Ergonomic Medical Tool Handles via Metal AM
Innehållsförteckning
Introduction: Revolutionizing Surgical Precision with 3D Printed Ergonomic Medical Tool Handles
Imagine a surgical instrument handle perfectly contoured to an individual surgeon’s hand, reducing muscle strain during lengthy procedures. Picture a lightweight yet incredibly strong handle for an orthopedic drill, improving maneuverability and reducing operator fatigue. Envision tool handles with intricate internal channels for advanced cleaning protocols or integrated sensor pathways. This is no longer science fiction; it’s the reality enabled by metal AM. By building components layer by layer directly from digital designs using high-performance metal powders, manufacturers can now create complex geometries, personalized forms, and integrated features previously impossible or prohibitively expensive to produce. This capability is particularly transformative for ergonomic surgical grips, where the subtle nuances of shape, texture, and weight distribution can significantly enhance a surgeon’s tactile feedback and dexterity.
The importance of ergonomics in medical instrumentation cannot be overstated. Poor handle design can lead to:
- Increased Surgeon Fatigue: Repetitive strain injuries (RSIs) and musculoskeletal disorders are common among surgeons, often exacerbated by non-ergonomic tools used for extended periods.
- Reduced Precision and Control: Discomfort and fatigue can impair fine motor skills, potentially compromising the accuracy required in minimally invasive surgery, microsurgery, or complex dental procedures.
- Lower Efficiency: Awkward grips can slow down procedures and increase the cognitive load on the practitioner.
- Compromised Safety: In critical moments, a secure and comfortable grip is essential for preventing instrument slippage or mishandling.
Metal AM directly addresses these challenges by enabling true design freedom. Engineers and designers are no longer constrained by the limitations of subtractive machining (cutting material away) or molding (requiring expensive tooling). Instead, they can focus purely on function and ergonomics, creating handles that are:
- Customized: Tailored to specific surgical procedures, individual user preferences, or even patient anatomy for specialized instruments.
- Lättviktare: Utilizing topology optimization and lattice structures to remove unnecessary material without sacrificing strength, crucial for handheld devices.
- Complex: Incorporating internal channels, integrated features, varying wall thicknesses, and complex surface textures directly into the print.
- Consolidated: Reducing part count by integrating multiple components into a single printed piece, simplifying assembly and potentially improving structural integrity.
This technological shift is pivotal for advanced medical manufacturing, allowing device companies, hospitals, and research institutions to innovate faster, iterate designs rapidly, and produce highly optimized tools on demand. The ability to prototype a new handle design quickly, test it with surgeons, and refine it based on feedback accelerates the development cycle significantly compared to the lengthy tooling processes of traditional methods.
Leading this charge are companies like Met3dp, specializing in comprehensive metalladditiv tillverkningslösningar for demanding industries, including healthcare. Headquartered in Qingdao, China, Met3dp provides not only cutting-edge 3D-utskrifter equipment, renowned for its industry-leading print volume, accuracy, and reliability, but also a wide portfolio of high-performance metal powders specifically optimized for AM processes. Our expertise spans Selective Electron Beam Melting (SEBM) printers and advanced powder production using gas atomization and Plasma Rotating Electrode Process (PREP) technologies. This integrated approach ensures that clients receive not just hardware, but a complete solution tailored to producing mission-critical parts, including highly ergonomic and functional medical tool handles. By partnering with Met3dp, medical device manufacturers gain access to decades of collective expertise in metal AM, enabling them to leverage this transformative technology for next-generation surgical instruments and diagnostic tools, ultimately contributing to better patient care and enhanced surgical precision. The journey towards perfectly optimized medical tools has begun, and metal 3D printing is paving the way.
Applications Unveiled: Where are Custom Metal AM Tool Handles Making a Difference?
The versatility and design freedom offered by metal additive manufacturing have opened up a vast array of applications for custom tool handles across the medical spectrum. From the high-stakes environment of the operating room to diagnostic labs and dental clinics, 3D printed tool handles are enhancing performance, ergonomics, and functionality. These components are no longer just generic interfaces but are becoming highly specialized parts integral to the success of medical procedures. Procurement managers and medical device components suppliers are increasingly recognizing AM as a viable and often superior production method, particularly for complex or low-to-medium volume handle requirements. Let’s explore some key areas where these innovative handles are making a significant impact:
1. Surgical Instruments: This is perhaps the most prominent area benefiting from custom metal AM handles.
- Laparoscopic Surgery: Minimally invasive procedures rely on long, slender instruments manipulated remotely. Ergonomic handles are crucial for providing surgeons with precise control and tactile feedback while minimizing fatigue during often lengthy operations. Metal AM allows for:
- Customized Grips: Handles tailored to hand size, grip preference (pistol grip, inline grip), and specific procedural needs (e.g., graspers, scissors, dissectors).
- Lättviktsdesign: Reducing the overall weight of the instrument, improving balance and maneuverability. Topology optimization can create skeletal structures that maintain strength while shedding grams.
- Integrated Features: Incorporating ratcheting mechanisms, locking features, or channels for flushing and cleaning directly into the handle design, reducing assembly complexity and potential failure points.
- Enhanced Haptic Feedback: Designing handles with specific textures or lattice structures that can transmit subtle vibrations or resistance cues back to the surgeon’s hand.
- B2B Relevance: Efterfrågan på surgical instrument handles wholesale is growing, with AM offering efficient production for diverse, specialized handle designs required by laparoscopic instrument manufacturers.
- Orthopedic Surgery: Orthopedic procedures often involve significant force application (e.g., drilling, sawing, reaming) and require robust, durable, and ergonomic tools. Metal AM delivers:
- High-Strength Handles: Using materials like Ti-6Al-4V or high-strength stainless steels to withstand demanding loads.
- Vibration Dampening: Incorporating lattice structures or specific geometries within the handle to reduce the transmission of vibrations from power tools to the surgeon’s hand, mitigating fatigue and improving control.
- Optimized Grips for Torque: Designing handles that maximize grip security and leverage for high-torque applications.
- Integrated Cooling Channels: For powered instruments, internal channels can be designed for air or fluid cooling, improving performance and longevity.
- B2B Relevance: Suppliers catering to orthopedic device companies can leverage AM for rapid prototyping and production of handles for drills, saws, screwdrivers, and implant insertion tools.
- Microsurgery & Neurosurgery: These fields demand extreme precision and control. Handles must be perfectly balanced and facilitate minute movements.
- Fine-Tuned Ergonomics: AM allows for subtle adjustments to shape and balance to achieve optimal dexterity.
- Ultra-Lightweight Designs: Minimizing handle weight is paramount to reduce tremor and enhance fine motor control.
- Specialized Grips: Creating unique shapes for pencil grips or other specialized holding techniques common in these fields.
- Robotic Surgery: While the surgeon controls robotic arms remotely, the handles on the console interface are critical. AM can customize these interfaces for surgeon comfort and control efficiency.
2. Dental Instruments: Dentists and dental surgeons rely on a wide variety of handheld instruments requiring precision, durability, and excellent ergonomics.
- Scalers, Probes, and Explorers: AM can create lightweight, balanced handles with customized grips and textures for enhanced tactile sensitivity and reduced hand fatigue during delicate procedures.
- Extraction Forceps & Elevators: High-strength metal AM handles can be designed with optimized grip surfaces and leverage points for controlled force application.
- Implant Drivers & Handpieces: Custom handles for dental drills and implant placement tools can improve ergonomics and potentially integrate internal channels for irrigation or aspiration.
- Sterilizability: Materials like 316L stainless steel and Ti-6Al-4V are readily sterilizable via autoclaving, a critical requirement for dental tools.
- B2B Relevance: AM provides dental device handle manufacturers and suppliers with a flexible production method for both standard and customized instrument lines.
3. Diagnostic Tools: Even diagnostic procedures benefit from improved handle design.
- Otoscopes & Ophthalmoscopes: While often made of plastic, specialized or high-end diagnostic tools can utilize metal AM for durable, ergonomic handles with integrated features.
- Biopsy Instruments: Handles for biopsy needles or forceps can be optimized for single-handed operation, precise control, and comfortable grip during sample collection.
4. Medical Prototyping & Customization:
- Snabb iteration: Metal AM allows medical device companies to rapidly prototype different handle designs, get feedback from clinicians, and iterate quickly without the need for expensive tooling molds or complex machining setups. This accelerates the medical prototyping cycle significantly.
- Surgeon-Specific Tools: For complex or novel procedures, AM enables the creation of truly bespoke instruments with handles designed in collaboration with the surgeon who will use them.
- Produktion av små volymer: AM is economically viable for producing specialized tools needed in smaller quantities, where the cost of traditional tooling would be prohibitive.
5. Training and Simulation:
- Realistic Simulators: Creating anatomically accurate and functionally realistic training models often requires custom instruments. AM can produce handles that mimic the weight, balance, and feel of real surgical tools for enhanced training experiences.
The breadth of these 3D printed tool handles applications demonstrates the technology’s transformative potential. By enabling manufacturers to move beyond standardized designs and embrace customization and ergonomic optimization, metal AM is contributing directly to improved performance, reduced practitioner fatigue, and potentially enhanced patient outcomes across numerous medical and dental fields. Companies like Met3dp, as a specialized medical device components supplier focusing on AM powders and equipment, are crucial partners in realizing these advancements, providing the materials and technology needed to produce these next-generation tool handles reliably and efficiently.
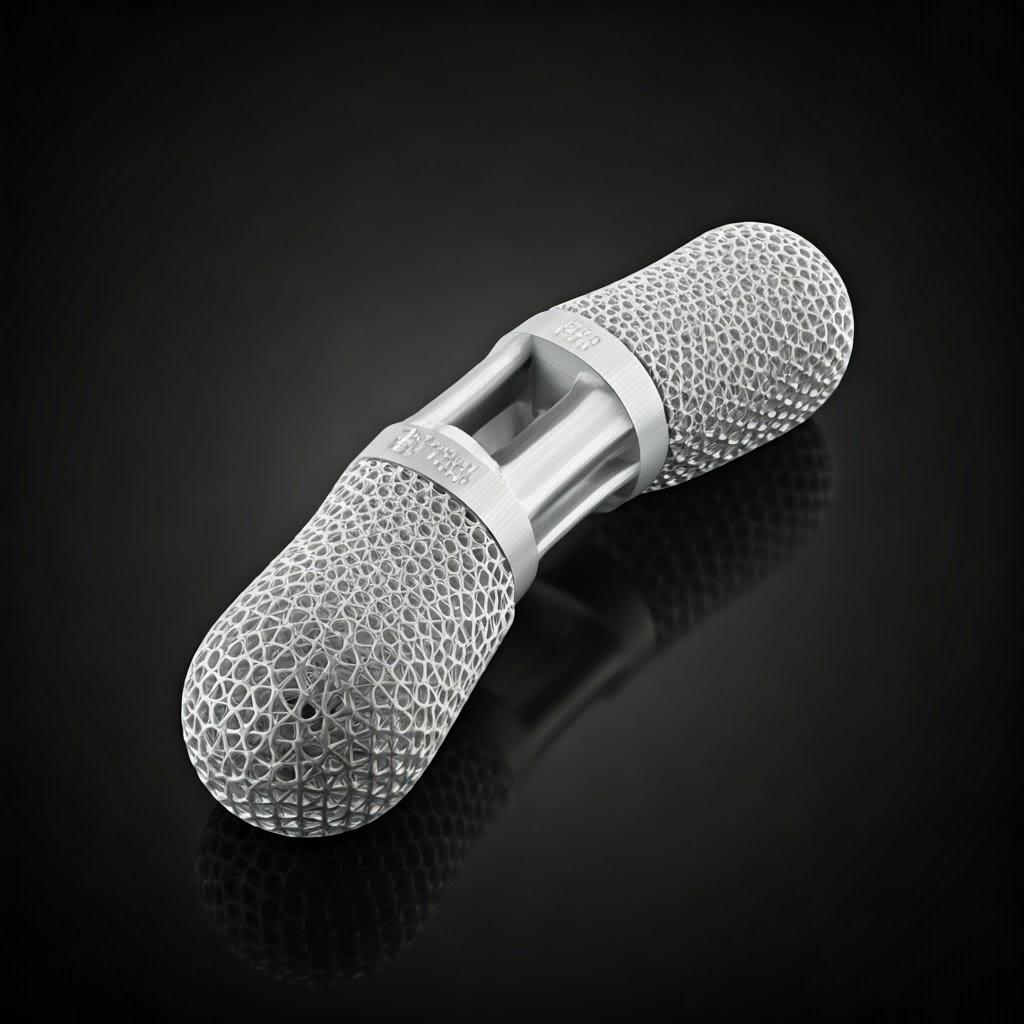
The Additive Advantage: Why Choose Metal 3D Printing for Your Medical Tool Handles?
While traditional manufacturing methods like CNC machining, metal injection molding (MIM), and investment casting have long served the medical device industry, Additiv tillverkning av metall (AM) offers a compelling suite of advantages specifically beneficial for producing custom medical tool handles. For engineers designing these critical components and procurement managers sourcing them, understanding these benefits of metal AM for surgical tools is key to leveraging this technology for a competitive edge. The decision to adopt AM often stems from its ability to overcome the inherent limitations of conventional processes, particularly concerning design complexity, customization, speed, and cost-effectiveness for certain production scales.
Let’s delve into the specific reasons why metal 3D printing stands out:
1. Unmatched Design Freedom & Complexity:
- Traditional Limitations: CNC machining is subtractive, meaning it starts with a block of material and cuts away until the final shape is achieved. This limits complex internal features, undercuts, and highly organic shapes. MIM and casting require expensive molds/tooling, which restricts design changes and makes highly intricate designs difficult or impossible to demold.
- AM Advantage: Metal AM builds parts layer-by-layer from metal powder. This additive approach liberates designers from traditional constraints. They can create:
- Highly Ergonomic Shapes: Handles perfectly contoured to the human hand, incorporating complex curves and variable cross-sections for optimal grip and comfort.
- Internal Channels: Complex, winding channels for cleaning, sterilization fluid flow, cooling, or housing sensors/electronics can be integrated directly into the handle during the printing process.
- Gitterstrukturer: Internal or external lattice structures can drastically reduce weight while maintaining structural integrity, or be tuned for specific vibration damping or haptic feedback properties.
- Consolidated Parts: Features previously requiring multiple machined or molded components (e.g., grips, buttons, ratchets) can potentially be integrated into a single printed handle, reducing assembly time, cost, and potential points of failure.
- Textured Surfaces: Intricate grip patterns, textures for enhanced tactile feel, or identification markings can be built directly into the surface.
2. Superior Ergonomics & Customization:
- The Ergonomic Imperative: As discussed, ergonomics are paramount for reducing surgeon fatigue and improving precision. Traditional methods often force compromises – standardized handles that fit “most” but are ideal for few.
- AM Advantage: Metal AM enables true customization and optimized ergonomics:
- Personalization: Handles can be tailored to individual surgeon’s hand sizes, grip preferences, or specific procedural requirements based on CAD models derived from scans or direct input.
- Procedure-Specific Designs: Create unique handle shapes optimized for the specific forces, movements, and access requirements of different surgical specialties (e.g., laparoscopic vs. orthopedic).
- Rapid Iteration for Optimal Feel: Easily print multiple design variations for surgeons to test and provide feedback, leading to a truly optimized ergonomic solution much faster than tooling modifications would allow.
3. Lightweighting:
- The Burden of Weight: Heavy surgical instruments contribute significantly to surgeon fatigue, especially during long procedures or when manipulating tools at awkward angles.
- AM Advantage: Genom topologioptimering software (which intelligently removes material from low-stress areas) and the incorporation of lattice structures, metal AM can produce handles that are significantly lighter than their solid, traditionally manufactured counterparts, without compromising necessary strength or stiffness. This directly translates to improved handling, reduced fatigue, and potentially greater dexterity for lightweight medical tools.
4. Rapid Prototyping & Accelerated Development:
- Traditional Bottlenecks: Creating prototypes with traditional methods often involves significant lead times for machining setups or creating prototype tooling for molding/casting, slowing down the design iteration cycle.
- AM Advantage: A new handle design can be printed directly from a CAD file, often within days or even hours, depending on the complexity and machine availability. This allows for:
- Fast Design Validation: Quickly produce physical prototypes for fit, form, and function testing.
- Clinical Feedback Integration: Get prototypes into the hands of surgeons early and often, incorporating their feedback into subsequent design iterations rapidly.
- Reduced Time-to-Market: Significantly shorten the overall product development lifecycle for new instruments. This capability for rapid prototyping medical handles is a major driver for AM adoption.
5. Material Options & Biocompatibility:
- AM Materials: Metal AM processes can utilize a range of medically relevant alloys, including the workhorses 316L rostfritt stål och Titanlegering Ti-6Al-4V, known for their excellent biocompatibility, corrosion resistance, and strength.
- Kvalitetssäkring: Reputable AM providers, like Met3dp metal 3D printing, utilize high-purity, tightly controlled metal powders and validated process parameters to ensure the final parts meet stringent medical requirements, including density and material properties comparable or superior to wrought materials.
6. Cost-Effectiveness for Complexity & Low Volumes:
- Traditional Cost Structures: Traditional methods often involve high upfront tooling costs (MIM, casting) or significant programming and machining time (CNC), making them less economical for complex designs or low-to-medium production volumes.
- AM Advantage: Metal AM typically has minimal tooling costs. The cost is primarily driven by material volume, machine time, and post-processing. This makes it highly cost-effective for:
- Highly Complex Geometries: Where machining would be extremely time-consuming or impossible.
- Customized/Personalized Parts: Producing unique designs without unique tooling for each.
- Low-to-Medium Volume Production: Bridging the gap between prototyping and mass production, or for specialized instruments with limited annual demand.
7. On-Demand Manufacturing & Supply Chain Flexibility:
- Digital Inventory: Designs exist as digital files, allowing parts to be printed as needed (on-demand manufacturing). This reduces the need for large physical inventories of diverse handle types.
- Motståndskraft i leveranskedjan: Reduces reliance on complex global supply chains and long lead times associated with traditional tooling and manufacturing, offering greater production flexibility.
Comparing AM with Traditional Methods for Handles:
Funktion | Metal AM (e.g., SLM/EBM) | CNC-bearbetning | Formsprutning av metall (MIM) | Investeringsgjutning |
---|---|---|---|---|
Designens komplexitet | Very High (Internal channels, lattices) | Moderate (Limited by tool access) | Moderate (Limited by demolding) | High (but requires tooling) |
Anpassning | Very High (Unique parts feasible) | Moderate (Programming required) | Low (Requires unique tooling) | Low (Requires unique tooling) |
Ergonomi | Highly Optimizable | Often Compromised | Standardized | Standardized |
Lättvikt | Excellent (Topology opt., lattices) | Limited (Material removal only) | Begränsad | Begränsad |
Verktygskostnad | None / Minimal | None (but programming time) | Mycket hög | Hög |
Unit Cost (Low Vol) | Konkurrenskraftig | High (esp. complex parts) | Very High (due to tooling) | Very High (due to tooling) |
Unit Cost (High Vol) | Högre | Lägre | Lägst | Lägre |
Lead Time (Proto) | Very Fast (Days) | Moderate (Days/Weeks) | Very Slow (Months – tooling) | Slow (Weeks/Months – tooling) |
Materialalternativ | Growing Range (Ti, SS, CoCr, etc.) | Wide Range | Specific Powder Blends | Wide Range |
Konsolidering av delar | High Potential | Låg | Låg | Låg |
Export to Sheets
While traditional methods remain optimal for high-volume production of simple, standardized handle designs, additive manufacturing medical devices like tool handles present clear advantages when complexity, customization, ergonomics, lightweighting, and speed are critical design drivers. Companies like Met3dp, with their advanced SEBM printers delivering industry-leading accuracy and reliability, are empowering medical device manufacturers to fully exploit these benefits, pushing the boundaries of surgical instrument design and performance. The transition isn’t just about a new manufacturing technique; it’s about enabling a new paradigm in how medical tools are conceived, designed, and produced for better healthcare outcomes.
Material Matters: Selecting the Right Biocompatible Metal Powders (316L & Ti-6Al-4V)
The success of any medical device, especially one that comes into direct or indirect contact with the human body or sterilization processes, hinges critically on the materials used in its construction. For metal 3D printed medical tool handles, selecting the appropriate metallpulver is paramount. The material must not only possess the required mechanical properties (strength, durability, fatigue resistance) but also meet stringent biological and chemical compatibility standards. Among the most widely adopted and trusted materials for such applications in the additive manufacturing space are 316L stainless steel (316L) och Ti-6Al-4V titanium alloy (Ti6Al4V). Understanding their properties and why they are preferred is crucial for engineers and procurement specialists sourcing these components.
Som ledande metal powder supplier for medical devices, Met3dp recognizes the critical importance of material quality. Utilizing advanced powder manufacturing techniques like vacuum gas atomization (VIGA) and the Plasma Rotating Electrode Process (PREP), Met3dp produces highly spherical, flowable metal powders with low oxygen content and controlled particle size distribution. This ensures optimal processing in AM systems (like SLM, DMLS, EBM) and results in printed parts with high density, excellent mechanical properties, and the purity required for demanding medical applications. Let’s examine the recommended powders, 316L and Ti-6Al-4V, in detail:
1. 316L Stainless Steel (Medical Grade Austenitic Stainless Steel):
- Sammansättning: Primarily iron, chromium (16-18%), nickel (10-14%), and molybdenum (2-3%), with low carbon content (<0.03%, denoted by the “L”). Molybdenum significantly enhances corrosion resistance, particularly against chlorides (like saline solutions).
- Key Properties & Benefits for Medical Handles:
- Utmärkt biokompatibilitet: 316L has a long history of safe use in medical implants and instruments. It generally meets ISO 10993 standards for biocompatibility, exhibiting low toxicity and minimal adverse tissue reaction. (Specific testing on final parts is still required).
- Överlägset korrosionsmotstånd: Highly resistant to corrosion in bodily fluids, cleaning agents, and sterilization environments (steam autoclaving, gamma, EtO). The passive chromium oxide layer protects the underlying metal. Passivation post-processing further enhances this layer.
- Good Mechanical Strength & Ductility: Offers a good balance of tensile strength, yield strength, and elongation, making it durable enough for most handle applications without being brittle.
- Ease of Sterilization: Readily withstands repeated cycles of standard sterilization methods, particularly autoclaving, without degradation.
- Kostnadseffektivitet: Generally more affordable than titanium alloys, making it a preferred choice when the absolute highest strength-to-weight ratio isn’t mandatory.
- Good Machinability & Polishability: Can be easily post-processed (machined, polished, electropolished) to achieve tight tolerances for mating features or very smooth, cleanable surfaces. Electropolishing significantly improves surface finish and corrosion resistance.
- AM Considerations: 316L processes well in Laser Powder Bed Fusion (L-PBF) systems like Selective Laser Melting (SLM) and Direct Metal Laser Sintering (DMLS). It requires careful control of process parameters (laser power, scan speed, layer thickness) to achieve full density and optimal mechanical properties. Post-print heat treatment (stress relief annealing) is typically required to reduce internal stresses built up during the rapid heating and cooling cycles.
- Typical Handle Applications: Surgical instrument handles (general surgery, laparoscopic), dental instrument handles, diagnostic tool components, orthopedic instrumentation (less commonly for implants themselves compared to Ti).
2. Ti-6Al-4V Titanium Alloy (Grade 5 or Grade 23 – ELI):
- Sammansättning: Titanium alloyed with approximately 6% aluminum and 4% vanadium. Grade 23 (Extra Low Interstitial – ELI) has reduced oxygen, nitrogen, and iron content, improving ductility and fracture toughness, making it often preferred for medical applications.
- Key Properties & Benefits for Medical Handles:
- Exceptional Biocompatibility: Widely considered one of the most biocompatible metals, with excellent integration potential (osseointegration for implants) and extremely low reactivity with body tissues and fluids. Meets stringent ISO 10993 krav.
- Utmärkt korrosionsbeständighet: Forms a very stable and passive titanium dioxide (TiO2) layer, providing outstanding resistance to corrosion in harsh biological environments.
- Högt förhållande mellan styrka och vikt: Significantly lighter than steel (roughly 40-45% less dense) but offers comparable or even higher strength, particularly yield strength. This is a major advantage for reducing the weight of handheld instruments and minimizing surgeon fatigue.
- Good Fatigue Strength: Performs well under cyclic loading conditions, important for handles subjected to repetitive use or vibration.
- Icke-magnetisk: Suitable for use in environments where magnetic fields are present (e.g., MRI compatibility, though the entire instrument needs assessment).
- Good Sterilizability: Compatible with standard sterilization methods including autoclaving.
- AM Considerations: Ti-6Al-4V can be processed using both L-PBF (SLM/DMLS) and Electron Beam Melting (EBM) techniques. EBM, like the systems developed by pioneers in the field and related to Met3dp’s focus, often operates at higher temperatures in a vacuum, which can reduce residual stresses but may result in a rougher as-built surface finish. L-PBF achieves finer features and better surface finish but typically requires more significant stress relief heat treatments. Achieving optimal microstructure and mechanical properties requires precise control over the AM process and appropriate post-processing heat treatments (annealing, potentially Hot Isostatic Pressing – HIPing – to close internal porosity).
- Typical Handle Applications: Orthopedic instrument handles (drills, reamers, impactors – where high strength and low weight are critical), spinal surgery instruments, neurosurgery instruments, high-performance laparoscopic handles, dental implant drivers, components requiring MRI compatibility.
Choosing Between 316L and Ti-6Al-4V:
The selection often comes down to specific application requirements and cost considerations:
Faktor | 316L rostfritt stål | Ti-6Al-4V titanlegering | Consideration for Handles |
---|---|---|---|
Biokompatibilitet | Utmärkt | Exceptionell | Both generally suitable for handle contact; Ti often preferred for implantable components. |
Motståndskraft mot korrosion | Utmärkt | Exceptionell | Both excellent for sterilization & body fluids; Ti slightly superior in aggressive media. |
Täthet | ~7.9-8.0 g/cm³ | ~4.4-4.5 g/cm³ | Ti offers significant weight savings (~45% lighter). Key driver for Ti. |
Strength (Tensile) | Good (~500-700 MPa, annealed AM) | Very High (~900-1100 MPa, annealed AM) | Ti is significantly stronger. |
Stiffness (Modulus) | High (~190-200 GPa) | Moderate (~110-115 GPa) | Steel handles feel stiffer; Ti handles have more ‘flex’ (can be good or bad). |
Cost (Powder) | Lägre | Higher (2-5x or more) | Cost is a major factor favoring 316L if Ti properties aren’t strictly needed. |
Slitstyrka | Bra | Moderate (can gall) | Surface treatments might be needed for Ti in high-wear interfaces. |
Bearbetbarhet | Bra | Svårare | Post-print machining is easier for 316L. |
MRI Compatibility | No (Paramagnetic) | Yes (Non-magnetic) | Ti is necessary if MRI compatibility is required for the instrument. |
Export to Sheets
The Role of Powder Quality:
Regardless of the chosen alloy, the quality of the starting metallpulver directly impacts the final part’s integrity. Factors controlled by powder manufacturers like Met3dp high-quality metal powders are critical:
- Sfäricitet och flytbarhet: Ensures uniform powder bed layers in the AM machine, leading to consistent melting and part density. Met3dp’s gas atomization and PREP technologies excel here.
- Fördelning av partikelstorlek (PSD): Affects packing density, resolution, and surface finish. Tailored PSDs are needed for different AM processes and desired outcomes.
- Purity & Low Oxygen Content: Contaminants and excessive oxygen can lead to porosity, reduced mechanical properties, and compromised biocompatibility. Vacuum processing during powder production (VIGA) and handling is crucial.
- Batch Consistency: Ensuring minimal variation between powder batches is essential for repeatable manufacturing of medical devices.
In conclusion, both 316L stainless steel and Ti-6Al-4V titanium alloy are excellent candidate materials for metal 3D printed medical tool handles, each offering a unique set of properties. 316L provides a cost-effective, corrosion-resistant, and robust solution suitable for many applications. Ti-6Al-4V delivers exceptional biocompatibility, superior strength-to-weight ratio, and non-magnetic properties, making it ideal for lightweight, high-performance, or MRI-compatible handles. The choice depends on a careful analysis of the functional requirements, ergonomic goals, and budget constraints, underpinned by the selection of high-quality, medical-grade metal powders from a trusted supplier like Met3dp to ensure the safety, reliability, and performance of the final product.
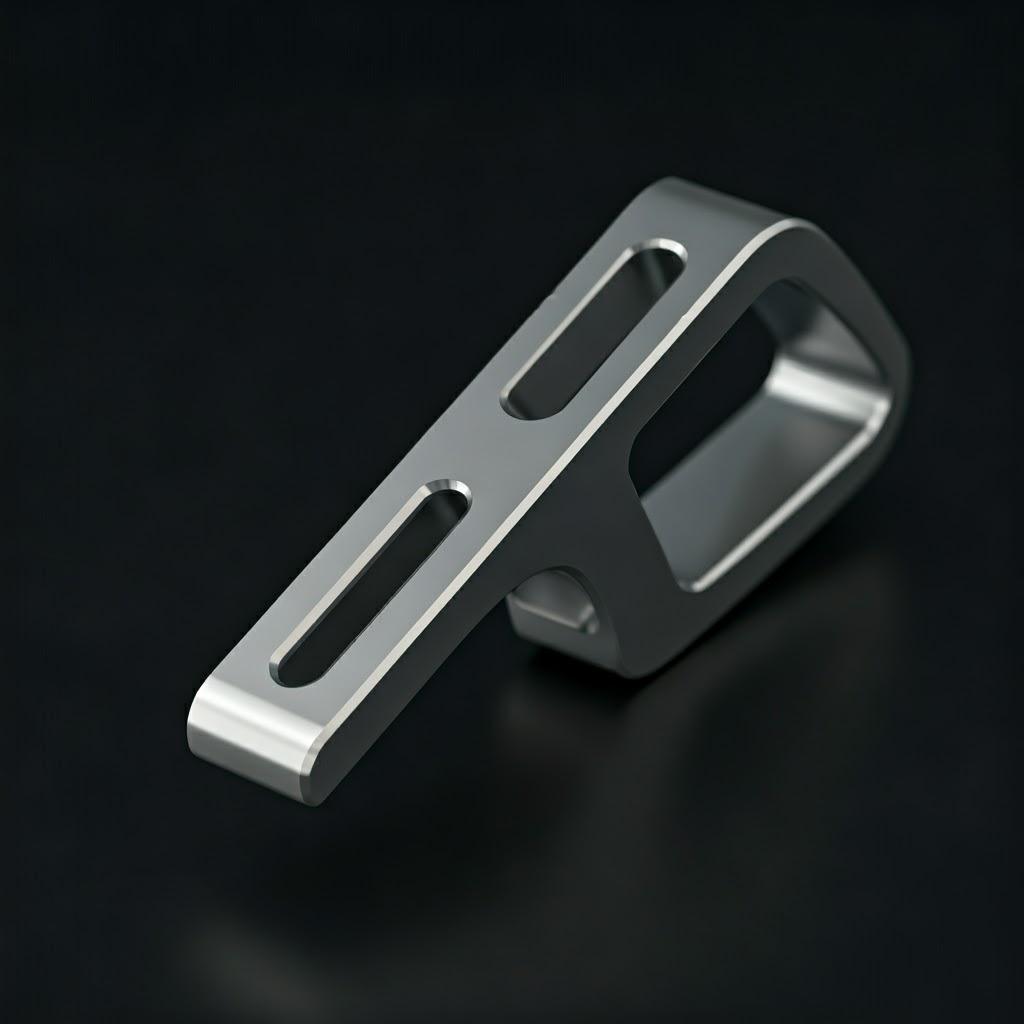
Designing for Success: DfAM Principles for Optimized Medical Tool Handles
Transitioning from traditional manufacturing paradigms to metal additive manufacturing (AM) requires more than just converting an existing CAD file. To truly unlock the potential of AM for creating superior custom medical tool handles, engineers must embrace Design för additiv tillverkning (DfAM) principles. DfAM is not merely a set of rules but a mindset shift, focusing on designing parts that leverage the unique capabilities of layer-by-layer fabrication while mitigating its inherent constraints. Applying DfAM effectively leads to handles that are not only functional and ergonomic but also optimized for printability, cost-effectiveness, and performance. For DfAM medical devices, this means considering factors beyond just the final form, including the build process itself, support structures, material properties, and post-processing requirements.
Let’s explore key DfAM principles crucial for designing optimized surgical tool handles using metal AM:
1. Leverage Geometric Freedom for Function & Ergonomics:
- Embrace Organic Shapes: Unlike the limitations of subtractive machining, AM excels at producing complex curves and freeform surfaces. Design handles that truly conform to the human hand, using ergonomic data or even 3D scans of users’ hands to create personalized grips.
- Topology Optimization: Utilize software tools to intelligently remove material from areas experiencing low stress during typical use. This creates lightweight, often organic-looking structures that maintain the required strength and stiffness, significantly reducing handle weight – a critical factor in reducing surgeon fatigue. This is central to optimizing tool handle design 3D printing.
- Gitterstrukturer: Incorporate internal or external lattice structures (e.g., gyroids, stochastic foams, trabecular patterns mimicking bone) for:
- Further Lightweighting: Achieving high stiffness-to-weight ratios.
- Vibration Dampening: Tuning lattice parameters to absorb vibrations from powered instruments.
- Enhanced Grip/Tactile Feedback: Using external lattices or textured surfaces generated through lattice patterns.
- Estetik: Creating unique and modern visual designs.
- Del Konsolidering: Analyze existing multi-part handle assemblies. Can components like triggers, buttons, ratchets, or covers be integrated into a single printed part? This reduces assembly time, cost, potential failure points, and inventory management complexity.
2. Design for Printability & Minimize Supports:
- Bygg orientering: The orientation of the handle on the build plate significantly impacts print time, support requirements, surface finish, and potentially anisotropic mechanical properties.
- Minimize Support Needs: Orient the part to maximize self-supporting angles (typically >45° from the horizontal for many metal L-PBF processes). Critical surfaces requiring high accuracy or smooth finishes should ideally be oriented upwards or vertically.
- Consider Anisotropy: Mechanical properties (especially fatigue strength and ductility) can vary slightly depending on the build direction (X, Y vs. Z). Orient critical stress paths optimally relative to the build layers, although this is often less pronounced with proper parameter optimization and post-print heat treatments.
- Support Structure Strategy: While minimizing supports is ideal, they are often necessary for overhangs, bridges, and anchoring the part to the build plate.
- Self-Supporting Features: Design overhangs with angles greater than the process-specific threshold. Use chamfers instead of sharp horizontal overhangs where possible.
- Design för Supports: When supports are unavoidable, design them for easy removal without damaging the part surface. Consider:
- Access: Ensure tools can reach support connection points.
- Break-off Points: Design support contact points (teeth) to be small and strategically located on non-critical surfaces where minor witness marks are acceptable or will be removed during post-processing.
- Sacrificial Material: In some cases, adding small amounts of extra material that will be machined away later can provide support or stability during printing.
- Internal Supports: Avoid complex internal supports where possible, as they are notoriously difficult to remove. Redesign internal channels to be self-supporting or utilize processes like EBM which may require fewer supports due to higher build temperatures.
3. Optimize Internal Channels:
- Cleanability & Sterilization: Internal channels design AM for medical tools must prioritize cleanability. Avoid sharp corners, dead-end cavities, and excessively long, narrow passages where debris or cleaning fluids could become trapped. Design smooth, sweeping bends. Consider Computational Fluid Dynamics (CFD) analysis to simulate fluid flow and ensure effective flushing.
- Functionality: Design channels with appropriate diameters and pathways for their intended purpose (e.g., irrigation, suction, housing fiber optics or wires). Ensure adequate wall thickness around channels for structural integrity.
- Powder Removal: Complex internal channels can trap unmelted metal powder. Design features or access points to facilitate powder removal after printing (e.g., using compressed air or vibration).
4. Adhere to Process Constraints:
- Minimum Wall Thickness: Understand the minimum printable wall thickness for the chosen material and AM process (typically 0.3-0.8 mm, but varies). Avoid designing features thinner than this limit. Ensure gradual transitions in wall thickness to minimize thermal stress.
- Feature Resolution: Be aware of the minimum feature size, hole diameter, and gap width the AM process can accurately reproduce. Small embossed text or intricate textures might need minimum feature sizes.
- Termisk hantering: Large, solid sections can accumulate heat and lead to warping or cracking. Consider hollowing parts or using internal lattices to reduce thermal mass. Ensure gradual transitions between thick and thin sections.
5. Design for Post-Processing:
- Machining Allowances: If certain surfaces require very tight tolerances, flatness, or specific finishes achievable only through machining, add sacrificial stock material (e.g., 0.5-1.0 mm) to those areas in the CAD model.
- Workholding: Consider how the complex, often organic shape of the AM handle will be securely held (fixtured) for subsequent machining or finishing operations. Designating specific flat surfaces or temporary fixturing features can be beneficial.
- Surface Finish Considerations: Understand the typical as-built surface roughness of the AM process and material. If a smoother finish is required, ensure the design allows access for polishing, blasting, or electropolishing. Critical internal channel surfaces might require specialized finishing like abrasive flow machining.
DfAM Workflow & Tools:
Implementing DfAM often involves:
- Collaboration: Close collaboration between design engineers, AM process engineers, and clinicians/end-users.
- Simulation: Using topology optimization, build process simulation (to predict distortion and stress), and potentially CFD software.
- Iterative Design: Leveraging the speed of AM for rapid prototyping and testing of different DfAM approaches.
- Guidelines: Following established DfAM guidelines provided by AM machine manufacturers or service providers like Met3dp, who possess deep expertise in optimizing designs for their specific equipment and processes.
By proactively incorporating these DfAM principles, manufacturers can move beyond simply replicating traditionally designed handles via AM. Instead, they can create truly innovative, next-generation custom medical tool handles that offer superior ergonomics, reduced weight, enhanced functionality, and improved overall performance, fully capitalizing on the transformative power of metal additive manufacturing.
Precision Engineered: Understanding Tolerance, Surface Finish, and Accuracy in Metal AM
While metal additive manufacturing unlocks unparalleled design freedom, a critical consideration for functional components like medical tool handles is the achievable level of precision. Engineers and procurement managers must understand the typical tolerance, ytfinish, och dimensionell noggrannhet capabilities of metal AM processes to set realistic expectations and ensure the final parts meet functional requirements, particularly for interfaces, mating parts, and surfaces requiring specific tactile properties or cleanability. Achieving the necessary precision often involves a combination of controlled printing processes and targeted post-processing steps.
1. Dimensional Accuracy:
- Definition: How closely the dimensions of the printed part conform to the original CAD model.
- Influencing Factors:
- AM System: Different technologies (L-PBF like SLM/DMLS vs. EBM) and specific machine models have varying inherent accuracy levels. Factors include laser/electron beam spot size, layer thickness control, and calibration. Companies like Met3dp invest in high-end systems known for their industry-leading print volume, accuracy and reliability.
- Process Parameters: Laser/beam power, scan speed, hatch spacing, layer thickness, and thermal management strategies significantly impact shrinkage, warping, and final dimensions. Optimized parameter sets are crucial.
- Materialegenskaper: Thermal expansion coefficient, conductivity, and shrinkage behavior of the metal powder (e.g., 316L vs. Ti-6Al-4V) affect dimensional stability during printing and cooling.
- Part Geometry & Size: Large or complex parts with varying cross-sections are more prone to thermal distortion and deviation than smaller, simpler geometries. Internal stresses can cause warping.
- Build Orientation & Supports: Orientation affects thermal gradients and support structures influence stability during the build, both impacting final accuracy.
- Typical Achievable Accuracy:
- As-Built: For well-controlled L-PBF processes, typical accuracy might fall within ±0.1 mm to ±0.3 mm or ±0.1-0.2% of the nominal dimension, whichever is larger. EBM might have slightly looser general tolerances due to higher process temperatures but can exhibit less internal stress. These values are general guidelines and highly dependent on the factors above.
- Targeted Machining: For critical features (e.g., connection points, assembly interfaces), post-print CNC machining is often employed to achieve much tighter tolerances, potentially down to ±0.01 mm or better, comparable to traditional machining.
- Verification: Dimensional accuracy is typically verified using calibrated metrology equipment like Coordinate Measuring Machines (CMMs), 3D laser scanners, or structured light scanners.
2. Geometric Tolerances (GD&T):
- Beyond Simple Dimensions: Geometric Dimensioning and Tolerancing (GD&T) defines allowable variations in form, orientation, location, and profile of features, which is often more critical than simple linear tolerances for functional parts.
- AM Considerations: Achieving tight GD&T specifications (e.g., flatness, perpendicularity, concentricity) directly from the AM process can be challenging due to potential warping and layer effects. While achievable tolerances are improving, critical GD&T requirements often necessitate post-machining operations on designated datum features and critical surfaces.
- DfAM for GD&T: Design parts with GD&T datums on surfaces that are easily accessible for machining or are inherently stable during the build process.
3. Surface Finish (Roughness):
- Definition: The measure of the fine-scale irregularities on a part’s surface, often quantified by the average roughness (Ra) in micrometers (µm) or microinches (µin).
- Importance for Medical Handles:
- Cleanability & Sterilization: Rougher surfaces have higher surface area and more crevices, potentially trapping contaminants and making cleaning/sterilization less effective. Smoother surfaces are generally preferred.
- Tactile Feel & Ergonomics: Surface finish contributes to the grip and feel of the handle. Specific textures might be desired for grip, while other areas need smoothness for comfort.
- Fatigue Life: Surface imperfections can act as stress concentrators, potentially reducing the fatigue life of the handle under cyclic loading. Smoother finishes generally improve fatigue performance.
- Estetik: Surface finish impacts the visual appearance of the tool.
- Influencing Factors:
- AM-process: EBM typically produces rougher as-built surfaces (Ra 20-40 µm) compared to L-PBF (Ra 6-15 µm), due to larger powder particles and sintering effects.
- Skiktets tjocklek: Thinner layers generally result in smoother surfaces, especially on angled or curved faces.
- Bygg orientering: Upward-facing surfaces tend to be smoother than downward-facing surfaces (which contact supports) or vertical walls (which show layer lines).
- Powder Particle Size: Finer powders can lead to smoother finishes but may pose challenges in handling and flowability.
- Process Parameters: Scan strategy, beam offset, and energy density influence melt pool stability and surface quality.
- Achievable Surface Finish (Ra):
Stat | Typical Ra (L-PBF: 316L/Ti6Al4V) | Typical Ra (EBM: Ti6Al4V) | Anteckningar |
---|---|---|---|
Som byggd | 6 – 15 µm | 20 – 40 µm | Varies significantly with orientation, parameters. Rough texture. |
Bead Blasted | 3 – 8 µm | 5 – 15 µm | Creates a uniform, matte finish. Improves aesthetics, removes loose powder. |
Tumbled / Vibro-Finished | 1 – 5 µm | 3 – 10 µm | Smoothens edges and surfaces through abrasive media. Cost-effective. |
CNC Machined | < 0.8 – 3.2 µm | < 0.8 – 3.2 µm | Used for specific features requiring high smoothness/accuracy. |
Manual Polishing | < 0.1 – 1.0 µm | < 0.4 – 2.0 µm | Labor-intensive. Can achieve mirror-like finishes. |
Electropolishing (316L) | < 0.2 – 0.8 µm | N/A | Excellent for smoothness, cleanability, corrosion resistance. |
Export to Sheets
- Internal Surfaces: Achieving smooth finishes inside complex internal channels is challenging. Techniques like abrasive flow machining (AFM) or electrochemical polishing might be required for critical applications.
Achieving Precision:
Reaching the required levels of tolerance, accuracy, and surface finish for demanding medical components often necessitates a holistic approach:
- Process Selection: Choose the AM technology best suited for the required precision and material (Met3dp Printing Methods offer insights into different approaches).
- Materialkvalitet: Use high-quality, consistent metal powders.
- Parameter Optimization: Develop and validate robust process parameters specific to the material, machine, and part geometry.
- DfAM: Design the part considering accuracy limitations and incorporating features for post-processing.
- Targeted Post-Processing: Implement necessary machining, polishing, or other finishing steps specifically on critical features.
- Kvalitetskontroll: Employ rigorous metrology and inspection throughout the process.
By understanding the interplay between the AM process, material choice, DfAM, and post-processing, manufacturers can confidently produce precision engineered metal AM medical tool handles that meet the exacting standards of the healthcare industry. Setting clear specifications for metal 3D printing tolerances och surface finish surgical instruments Ra early in the design phase is crucial for successful outcomes.
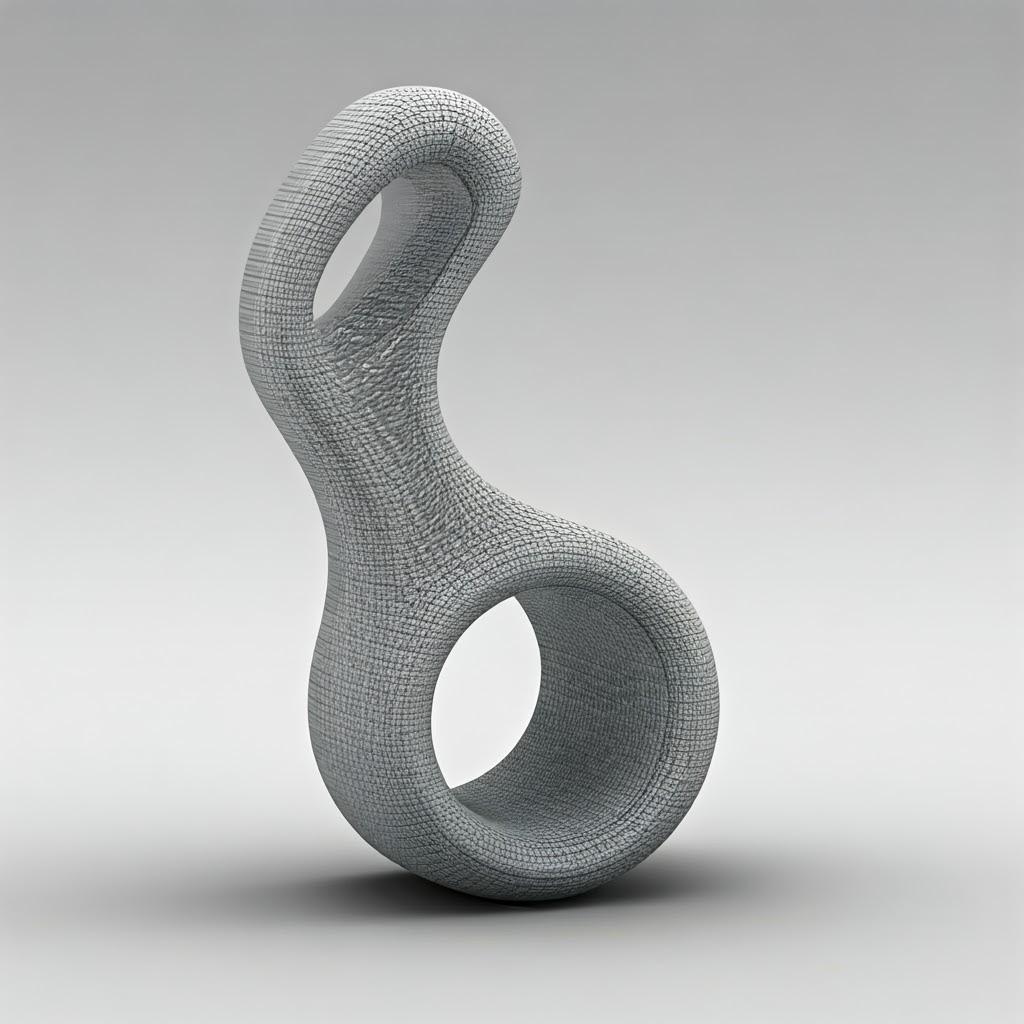
Beyond the Print: Essential Post-Processing for Functional Medical Tool Handles
Creating a medical tool handle using metal additive manufacturing doesn’t end when the part comes out of the printer. The as-built component, while geometrically complex, typically requires a series of post-processing metal AM medical parts steps to transform it into a functional, safe, and reliable medical device component. These steps are crucial for removing temporary structures, relieving internal stresses, achieving the required dimensional accuracy and surface finish, and ensuring the material possesses the optimal properties for its demanding application. Understanding these necessary steps is vital for accurately estimating costs, lead times, and ensuring the final handle meets all specifications.
The specific post-processing workflow can vary depending on the AM technology used (e.g., L-PBF vs. EBM), the material (316L vs. Ti-6Al-4V), the complexity of the handle design, and the specific requirements of the application. However, a typical sequence often includes:
1. De-powdering:
- Syfte: Removing unmelted metal powder trapped within the part (especially in internal channels or complex geometries) and surrounding the build.
- Metoder: Compressed air blow-off, brushing, vibration systems, ultrasonic cleaning baths (sometimes with specific solvents). Careful attention is needed for complex internal features to ensure all loose powder is removed, as trapped powder can pose a contamination risk or interfere with function. DfAM plays a role here in designing for effective powder removal.
2. Stress Relief Heat Treatment:
- Syfte: Reducing the significant internal stresses that build up during the rapid heating and cooling cycles inherent in powder bed fusion processes. These stresses can cause distortion during or after removal from the build plate, cracking, and reduced fatigue life. This is arguably the most critical post-processing step for ensuring part stability and performance.
- Metoder: Heating the parts (often while still attached to the build plate) in a controlled atmosphere (vacuum or inert gas like argon) furnace to a specific temperature below the material’s transformation point, holding for a period, and then cooling slowly.
- 316L rostfritt stål: Typical stress relief cycles involve temperatures between 550°C and 650°C, though higher temperature solution annealing (e.g., 1040-1150°C followed by rapid cooling) might be used to fully homogenize the microstructure and dissolve detrimental phases, improving corrosion resistance and ductility. The choice depends on the balance of properties required.
- Ti-6Al-4V: Stress relief is commonly performed at 600°C to 800°C in a vacuum or inert atmosphere. Higher temperature annealing or HIPing might follow for specific property optimization.
- Importance: Skipping or improperly performing stress relief can lead to dimensional instability and premature failure of the handle.
3. Part Removal from Build Plate:
- Syfte: Separating the printed handle(s) from the metal build plate they were fused to during the printing process.
- Metoder:
- Wire Electrical Discharge Machining (Wire EDM): Precise method, commonly used for cutting parts cleanly from the plate with minimal force.
- Bandsaw: Faster but less precise, requires careful handling.
- Maskinbearbetning: Milling or grinding away the base structure.
4. Support Structure Removal:
- Syfte: Removing the temporary support structures required during printing for overhangs and stability.
- Metoder:
- Manual Break-off: Supports are often designed with small contact points (‘teeth’) allowing them to be broken off by hand or with simple tools (pliers, cutters). This is common but leaves witness marks.
- Machining (CNC): Milling or grinding away supports, especially in accessible areas or when a cleaner finish is needed at the support interface.
- Hand Finishing: Using files, grinders, or rotary tools to manually smooth areas where supports were attached.
- Utmaningar: Removing supports from intricate internal channels or delicate features requires careful planning (DfAM) and execution.
5. Hot Isostatic Pressing (HIPing) – Optional but Recommended for Critical Applications:
- Syfte: Closing internal microscopic pores (porosity) that can sometimes remain after the AM process. This improves density, ductility, fatigue life, and overall material integrity.
- Method: Subjecting the parts to high temperature (just below melting point) and high inert gas pressure (typically Argon) simultaneously in a specialized HIP vessel.
- Relevance: Often recommended or required for critical medical components, especially Ti-6Al-4V parts used in high-stress applications, to ensure maximum material performance and reliability. It adds cost and lead time but significantly enhances material properties.
6. Machining for Critical Dimensions & Features:
- Syfte: Achieving tighter tolerances, specific surface finishes, or geometric features (like threads, O-ring grooves, precise mating surfaces) that cannot be achieved accurately enough by the AM process alone.
- Metoder: Standard CNC-bearbetning techniques (milling, turning, drilling, tapping, grinding).
- Överväganden: AM materials can sometimes be more challenging to machine than their wrought counterparts due to slightly different microstructures or hardness. Proper tooling, speeds, and feeds are required. DfAM should ensure parts can be fixtured effectively for machining.
7. Surface Finishing:
- Syfte: Achieving the desired surface roughness (Ra), texture, appearance, and cleanliness for the handle.
- Methods (can be combined):
- Bead Blasting/Sand Blasting: Creates a uniform matte finish, removes minor imperfections, and can improve fatigue life through compressive stress. Various media (glass beads, aluminum oxide) create different finishes.
- Tumbling/Vibratory Finishing: Uses abrasive media in a rotating or vibrating bowl to deburr edges and smooth surfaces. Cost-effective for batch processing.
- Manual Grinding/Polishing: Using belts, wheels, and polishing compounds to achieve smoother finishes, up to a mirror polish. Labor-intensive but highly controllable.
- Electropolishing (esp. for 316L): An electrochemical process that removes a microscopic layer of material, resulting in a very smooth, clean, passive, and corrosion-resistant surface. Excellent for electropolishing surgical tools and improving cleanability.
- Abrasive Flow Machining (AFM): Forcing an abrasive putty through internal channels to smooth their surfaces.
8. Passivation (for Stainless Steels like 316L):
- Syfte: Enhancing the natural corrosion resistance of stainless steel by removing free iron from the surface and thickening the protective chromium oxide layer. Critical for passivation stainless steel medical components per standards like ASTM A967.
- Method: Chemical treatment, typically using nitric acid or citric acid solutions.
9. Cleaning & Inspection:
- Syfte: Ensuring the final handle is free from contaminants (machining oils, polishing compounds, debris, residual powder) and meets all dimensional, surface, and material specifications before final packaging or assembly.
- Metoder: Validated cleaning protocols (aqueous, solvent, ultrasonic), visual inspection, dimensional metrology (CMM, scanning), surface roughness measurement, potentially material testing (density, tensile) on representative samples.
The complexity and rigor of these post-processing steps underscore why choosing an experienced metal AM service provider with comprehensive in-house or tightly managed external post-processing capabilities is crucial. Companies like Met3dp, with their focus on delivering end-to-end solutions, understand the critical interplay between printing and post-processing required to deliver functional, high-quality medical components like ergonomic tool handles. Neglecting or improperly executing these steps can compromise the performance, safety, and regulatory compliance of the final medical device.
Navigating Challenges: Overcoming Hurdles in Metal AM for Medical Handles
While metal additive manufacturing offers significant advantages for producing custom medical tool handles, the technology is not without its challenges. Understanding these potential metal 3D printing defects medical device manufacturers might encounter, and implementing strategies to mitigate them, is crucial for consistent, reliable production. Proactive problem-solving, rooted in robust process control, DfAM, and thorough post-processing, is key to success. Let’s explore some common hurdles and how to navigate them:
1. Warping and Distortion:
- Problem: Parts curling, lifting from the build plate, or deviating from their intended geometry due to the high thermal gradients and resulting residual stresses during the layer-by-layer melting and solidification process. This is one of the most common challenges 3D printing medical devices.
- Causes: Uneven heating/cooling, large thermal mass differences within the part, insufficient support, inadequate build plate heating.
- Mitigation Strategies:
- Thermal Simulation: Use build simulation software to predict areas prone to high stress and distortion before printing, allowing for design modifications or optimized orientation/supports.
- Optimized Build Orientation: Position the part to minimize large flat surfaces parallel to the build plate and reduce thermal gradients across layers.
- Robust Support Structures: Design supports not just for overhangs but also to anchor the part securely, conduct heat away, and counteract shrinkage forces. Consider solid “block” supports or reinforced lattice supports.
- Build Plate Heating: Utilize heated build platforms (common in L-PBF, inherent in EBM) to reduce the temperature differential between the molten material and the surrounding environment.
- Optimized Scan Strategies: Employ specific laser/beam scanning patterns (e.g., island scanning, alternating hatches) to distribute heat more evenly and reduce localized stress build-up.
- Immediate Stress Relief: Perform stress relief heat treatment immediately after printing, often before removing the part from the build plate, to relax internal stresses before they cause significant distortion.
2. Difficulty in Support Removal:
- Problem: Supports, especially those in complex internal geometries or attached to delicate features, can be difficult, time-consuming, or even impossible to remove without damaging the part. Residual support material can also compromise cleanability or function.
- Causes: Poor DfAM (inaccessible supports, overly strong connections), complex internal geometries, fragile part features.
- Mitigation Strategies:
- DfAM for Support Removal: Design parts to minimize the need for supports (e.g., self-supporting angles). When necessary, design supports for accessibility and easy breakage (optimized contact points, perforation). Consider adding features specifically to aid support removal access.
- Process Selection: EBM often requires fewer supports than L-PBF due to powder sintering providing some self-support.
- Optimized Support Design: Use specialized support generation software offering different support types (e.g., tree supports, block supports, lattice supports with specific densities) and connection parameters.
- Advanced Removal Techniques: Employ wire EDM, precise CNC machining, or specialized tools for removing challenging supports. For internal channels, abrasive flow machining (AFM) might be used to remove internal support remnants and smooth the surface simultaneously.
- Avoid Internal Supports Where Possible: Redesign internal channels to be self-supporting (e.g., teardrop shapes, diamond profiles) or consider designing the part in multiple pieces to be joined after printing if internal complexity is too high for reliable support removal.
3. Residual Stress Management:
- Problem: Even if significant warping doesn’t occur, high levels of residual stress can remain locked within the printed part, potentially leading to cracking during post-processing (e.g., machining) or reduced fatigue life and premature failure in service.
- Causes: Inherent rapid heating/cooling cycles of powder bed fusion.
- Mitigation Strategies:
- Mandatory Stress Relief: Implement appropriate stress relief heat treatment cycles as a standard procedure immediately after printing. This is non-negotiable for functional metal AM parts.
- Optimized Parameters & Scan Strategies: As mentioned for warping, process parameters and scan strategies influence heat input and stress accumulation.
- Build Simulation: Predict stress hotspots and adjust design or process accordingly.
- HIPing: Can help relieve stress while also closing pores, though primarily used for porosity reduction.
4. Achieving Required Surface Finish and Cleanliness:
- Problem: As-built surfaces are typically rough (especially EBM) and may not meet requirements for cleanability, tactile feel, or fatigue resistance. Internal channels are particularly challenging to finish and clean. Trapped powder poses a contamination risk.
- Causes: Layer-wise building process, partially melted powder particles adhering to surfaces, support contact marks, limitations of finishing techniques for internal features.
- Mitigation Strategies:
- Appropriate Post-Processing: Select and implement the right combination of surface finishing techniques (blasting, tumbling, polishing, electropolishing, AFM) based on requirements for different part areas.
- DfAM for Finishing: Design parts with access for finishing tools and processes. Optimize internal channel design for cleanability and potential finishing (smooth bends, sufficient diameter).
- Validated Cleaning Protocols: Develop and rigorously validate cleaning procedures to ensure removal of all processing residues (powder, oils, polishing compounds) according to medical device standards (e.g., ISO 19227).
- Powder Quality & Handling: Use high-quality powder with good flowability and minimize contamination during handling to reduce powder adherence issues. Met3dp’s advanced powder production systems contribute here.
5. Porosity Control:
- Problem: Small voids or pores within the printed material can compromise mechanical properties (especially fatigue strength and ductility) and act as potential initiation sites for cracks or corrosion.
- Causes: Incorrect process parameters (energy density too low/high), unstable melt pool, gas trapped during melting, poor powder quality (internal gas porosity, satellites).
- Mitigation Strategies:
- Processparameteroptimering: Develop robust parameter sets (laser/beam power, scan speed, layer thickness, hatch spacing) validated through density testing (e.g., Archimedes method, metallographic analysis) to achieve >99.5% relative density (often >99.9%).
- Powder Quality Control: Utilize high-purity, gas-atomized powders with controlled size distribution and low internal porosity, like those produced by Met3dp. Ensure proper powder storage and handling to prevent moisture absorption or contamination.
- HIPing: Highly effective at closing internal gas porosity, often used for critical applications to guarantee maximum density and properties.
- In-situ Monitoring: Advanced AM systems may incorporate melt pool monitoring to detect instabilities that could lead to porosity in real-time.
6. Ensuring Biocompatibility:
- Problem: While materials like 316L and Ti-6Al-4V are inherently biocompatible, the AM process or post-processing steps could potentially introduce contaminants or alter surface chemistry in a way that affects biological response. Ensuring biocompatibility 3D printed parts requires rigorous control.
- Causes: Process contaminants (e.g., from handling, machine environment), residues from supports or cleaning agents, unintended surface oxides or phases.
- Mitigation Strategies:
- Material Certification: Use certified medical-grade powders from reputable suppliers.
- Process Validation & Control: Maintain a clean build environment, use validated process parameters, and control post-processing steps carefully.
- Validated Cleaning: Implement rigorous, validated cleaning procedures to remove all residues.
- Passivation (316L): Ensure proper passivation to optimize the surface chemistry.
- Biocompatibility Testing: Conduct necessary biocompatibility tests (per ISO 10993) on final, processed parts or representative coupons as part of the device validation process. Partnering with an AM provider experienced in the medical field, potentially with relevant certifications like ISO 13485, is crucial.
By anticipating these common utmaningar and implementing robust mitigation strategies grounded in sound engineering principles, DfAM, meticulous process control, and thorough post-processing, manufacturers can successfully leverage metal AM to produce high-quality, reliable, and safe custom medical tool handles. Partnering with experienced AM solution providers like Met3dp, who understand these nuances and possess the technology and expertise to overcome them, significantly de-risks the adoption process and accelerates the path to innovative medical devices.
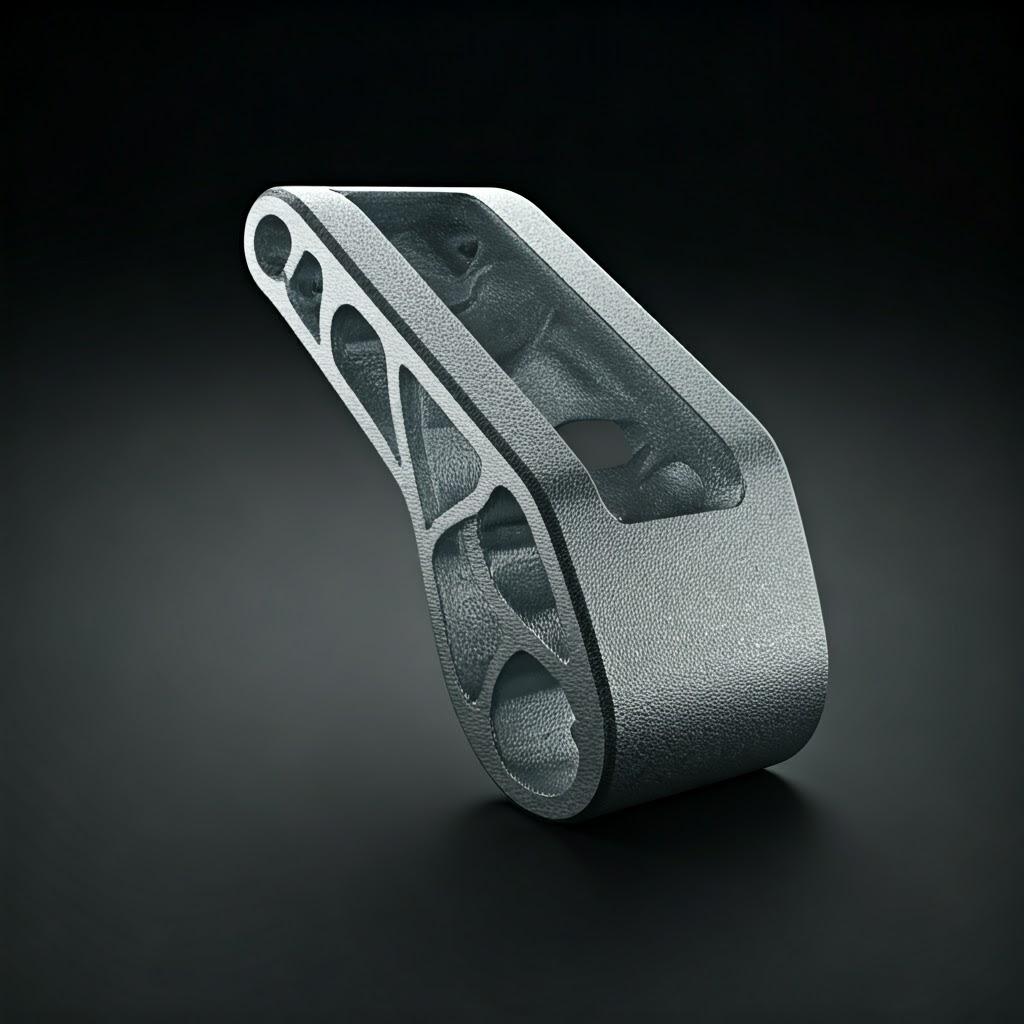
Partnering for Progress: How to Choose the Right Metal 3D Printing Service Provider
Selecting the right manufacturing partner is a critical decision when adopting metal additive manufacturing for medical components like custom tool handles. The quality, reliability, and regulatory compliance of your final product depend heavily on the expertise, processes, and quality systems of your chosen metal AM service bureau. While numerous providers offer metal 3D printing, not all possess the specific capabilities and rigorous controls required for the demanding medical device sector. A thorough medical device 3D printing supplier evaluation process is essential for engineers and procurement managers to ensure a successful partnership and a safe, effective end product.
Making the right choice involves looking beyond just price and technical specifications. It requires assessing the provider’s holistic capabilities, quality commitment, and experience within the healthcare landscape. Here’s a comprehensive guide on how to choose the right metal 3D printing service provider for your ergonomic medical tool handles:
1. Demonstrated Medical Device Expertise & Experience:
- Track Record: Does the provider have a proven history of manufacturing components for the medical industry? Can they share (non-confidential) case studies or examples relevant to surgical instruments, handles, or similar components?
- Regulatory Understanding: Are they familiar with medical device regulations (e.g., FDA requirements in the US, MDR in Europe)? Do they understand the importance of process validation, traceability, and documentation required for regulatory submissions?
- Application Knowledge: Do they understand the specific functional requirements, sterilization methods, and biocompatibility needs associated with medical tool handles? Can they offer insights or suggestions based on their experience?
2. Quality Management System & Certifications:
- ISO 13485 Certification: This is arguably the most crucial criterion. ISO 13485 additive manufacturing certification signifies that the provider operates under a quality management system specifically designed for medical device manufacturing. It demonstrates a commitment to risk management, traceability, process validation, and documented controls essential for medical components. Ask for their certificate and understand its scope.
- ISO 9001 Certification: While more general, ISO 9001 indicates a baseline commitment to quality management principles.
- Robust QMS in Practice: Beyond certifications, evaluate their actual quality management system. How do they handle material receiving inspection, powder traceability, process monitoring, equipment calibration, non-conformance reporting, corrective/preventive actions (CAPA), and final inspection? Request documentation examples or an audit if feasible.
3. Technological Capabilities & Capacity:
- Relevant AM Technology: Do they operate the appropriate metal AM technology (e.g., L-PBF like SLM/DMLS, or EBM) suitable for your handle’s material (316L, Ti-6Al-4V) and design complexity?
- Machine Fleet & Condition: What specific machine models do they use? Are they well-maintained and calibrated? What is their build envelope size – can it accommodate your handle size and potential batch quantities?
- Processtyrning: What measures are in place for monitoring and controlling critical process parameters (e.g., laser power, atmosphere purity, temperature)? Do they utilize any in-situ monitoring capabilities?
- Capacity & Scalability: Can they meet your volume requirements, from initial prototypes to potential low-to-medium volume production runs? What are their typical lead times, and do they have mechanisms to handle urgent requests?
4. Material Expertise & Handling:
- Medical-Grade Materials: Do they have validated experience printing with the specific medical-grade alloys you require (e.g., 316L, Ti-6Al-4V ELI)?
- Powder Sourcing & Quality: Where do they source their metal powders? Do they use certified medical-grade powders? What are their incoming powder inspection and testing procedures? Companies like Met3dp, which manufacture their own high-quality metal powders using advanced atomization techniques, offer a distinct advantage in controlling material quality from the source.
- Powder Management: How do they handle, store, track (batch traceability), and recycle metal powders to prevent contamination and ensure consistency? Cross-contamination between alloys is a significant risk that must be strictly controlled.
5. Comprehensive Post-Processing Capabilities:
- Integrated Services: Does the provider offer the necessary post-processing steps in-house (stress relief, support removal, machining, finishing, cleaning, passivation)? In-house capabilities generally allow for better process control, shorter lead times, and clearer accountability.
- Validated Processes: Are their post-processing steps, especially heat treatment, cleaning, and passivation, properly validated?
- Finishing Expertise: Can they achieve the specific surface finishes (Ra values, polished, matte, textured) required for different areas of your handle? Do they have experience with techniques like electropolishing for stainless steel?
- Metrology & Inspection: What equipment do they have for dimensional inspection (CMM, 3D scanners) and surface roughness measurement? What are their standard inspection procedures?
6. Engineering & Technical Support:
- DfAM Expertise: Can their engineering team provide expert advice on optimizing your handle design for additive manufacturing (DfAM)? Can they assist with topology optimization, support strategy, or internal channel design?
- Simulation Capabilities: Do they offer build simulation services to predict potential issues like warping or stress concentrations?
- Collaboration & Communication: Are they responsive, easy to communicate with, and willing to collaborate closely throughout the project lifecycle? Do they provide clear project management and reporting?
7. Cost, Value, and Transparency:
- Clear Quoting: Is their pricing structure transparent? Does the quote clearly break down costs associated with materials, printing, supports, post-processing, and quality assurance?
- Value Proposition: Consider the total value offered, not just the piece price. Factor in expertise, quality assurance, reliability, lead time, and support. A slightly higher price from a highly qualified medical AM provider often represents lower overall risk and better long-term value.
Supplier Evaluation Checklist:
Kriterier | Viktiga frågor | Ideal Response / Evidence |
---|---|---|
Medical Experience | Years serving medical? Relevant project examples? Understanding of medical regulations? | >5 years, similar component examples, demonstrates regulatory awareness (ISO 13485 focus) |
ISO 13485 Certification | Certified? Scope covers relevant processes? | Yes, certificate provided, scope includes metal AM & post-processing for medical. |
Technology Fit | Right AM process (L-PBF/EBM)? Suitable machines/build size? | Yes, modern calibrated machines appropriate for material & size. |
Material Expertise (316L/Ti6Al4V) | Specific experience? Medical-grade powder sourcing? Powder QC & handling procedures? | Yes, validated parameters, certified powder source, robust handling/traceability protocols. |
Efterbearbetning | In-house capabilities (Heat Treat, Machining, Finish, Clean)? Validated processes? | Primarily in-house, validated key processes (esp. heat treat, cleaning). |
Quality Management System | Traceability? Process validation approach? Inspection methods? Metrology equipment? | Documented QMS, batch traceability, process validation records, CMM/Scanner reports. |
Teknisk support | DfAM review offered? Simulation? Collaborative approach? | Yes, dedicated engineering support, DfAM consultation standard. |
Capacity & Lead Time | Meets volume needs? Stated lead times reliable? | Yes, clear capacity info, track record of on-time delivery. |
Cost & Transparency | Detailed quote breakdown? Competitive pricing relative to value/quality? | Transparent quote, justifies cost based on quality/services provided. |
Export to Sheets
Att välja rätt metal 3D printing partner selection is a strategic decision. Thoroughly vetting potential suppliers against these criteria will help ensure you partner with a provider, like Met3dp, that possesses the necessary technical capabilities, quality commitment exemplified by their advanced powder making systems and reliable printers, and medical industry focus to successfully produce your ergonomic medical tool handles, ultimately contributing to better surgical tools and improved patient outcomes.
Decoding Investment: Cost Factors and Lead Times in Metal AM for Medical Handles
One of the primary considerations for adopting any manufacturing technology is understanding the associated costs and production timelines. While metal additive manufacturing offers significant advantages in design freedom and customization for medical tool handles, it’s essential to have a clear picture of the metal 3D printing cost medical devices involve and the factors influencing lead time 3D printed surgical tools. This knowledge allows engineers and procurement managers to make informed decisions, manage budgets effectively, and plan project timelines accurately.
Key Cost Drivers for Metal AM Medical Tool Handles:
The final price of a 3D printed metal handle is influenced by a complex interplay of factors. Unlike traditional high-volume methods where tooling amortization is dominant, AM costs are more closely tied to the specific part design and process parameters.
- Material Type & Volume:
- Kostnad för pulver: The raw material powder is a significant cost component. Ti-6Al-4V is considerably more expensive (often 2-5x or more) than 316L rostfritt stål.
- Part Volume: The actual volume of the handle itself directly consumes material.
- Support Structure Volume: Material used for support structures also adds to the cost. Efficient DfAM aims to minimize this.
- Återvinning av pulver: While providers recycle unused powder, there are costs associated with sieving, testing, and managing recycled powder batches, which is factored into overall pricing.
- Designkomplexitet:
- Geometric Intricacy: Highly complex geometries with intricate details, thin walls, or extensive internal channels can increase print time and complexity, potentially requiring more support and more intensive post-processing (e.g., cleaning, finishing).
- Topology Optimization/Lattices: While these reduce material volume (saving material cost), they can sometimes increase print time slightly due to complex scan paths. The net effect on cost depends on the balance.
- Machine Time (Build Time):
- Part Height (Z-Height): Build time is primarily determined by the number of layers required, meaning taller parts take longer to print, irrespective of their volume per layer.
- Part Volume & Cross-Section: The amount of material melted per layer (related to the cross-sectional area) also influences the time taken for each layer.
- Nesting Efficiency: How many handles can be efficiently arranged (nested) onto a single build plate affects the per-part machine time allocation. Skilled providers optimize nesting.
- Machine Hourly Rate: Different AM machines have varying capital costs, operating expenses, and associated hourly rates charged by the service provider.
- Support Structure Requirements:
- Volume & Complexity: As mentioned, support material adds to cost. Complex support structures also require more time for generation in software and significantly more labor for removal during post-processing.
- Removal Effort: The difficulty of accessing and removing supports directly impacts labor costs. Internal supports are particularly costly to remove.
- Post-Processing Intensity:
- This is often a MAJOR cost driver. The extent and complexity of required post-processing steps significantly impact the final price.
- Värmebehandling: Standard stress relief is necessary. More complex cycles (annealing, HIPing) add cost due to furnace time and energy. HIPing is a particularly expensive step.
- Maskinbearbetning: The amount of CNC machining needed for tolerances or features, and the complexity of setups, adds considerable cost.
- Ytbehandling: Basic bead blasting or tumbling is relatively low-cost. Achieving very smooth finishes (low Ra) through manual polishing or electropolishing requires significant labor or specialized equipment, increasing costs substantially.
- Cleaning & Passivation: Validated cleaning processes and chemical passivation add time and cost.
- Quality Assurance & Inspection:
- Level of Inspection: Basic dimensional checks vs. comprehensive CMM reports, surface roughness measurements, material density tests, or Positive Material Identification (PMI) add varying levels of cost.
- Documentation: Extensive documentation packages required for medical device traceability and validation contribute to overhead costs.
- Quantity & Batch Size:
- Stordriftsfördelar: While AM avoids tooling costs, some economies of scale exist. Larger batch sizes allow for more efficient machine utilization (nesting), and potentially more efficient batch post-processing (e.g., heat treatment, tumbling). However, the per-part cost reduction with quantity is generally less dramatic than in traditional high-volume methods like MIM.
- Setup Costs: There are still setup costs associated with preparing the build file, loading the machine, and initial process checks, which are amortized over the batch.
Illustrative Cost Breakdown Structure (Example – May Vary Greatly):
Kostnadskomponent | Potential % of Total Cost (Illustrative) | Anteckningar |
---|---|---|
Material Powder | 15-30% | Higher % for Ti-6Al-4V, large/solid parts |
Machine Time | 20-40% | Driven by Z-height, volume, nesting efficiency |
Support Removal Labor | 5-15% | Highly dependent on support complexity & DfAM |
Värmebehandling | 5-10% | Standard stress relief; higher for HIPing |
CNC-bearbetning | 0-30% | Depends heavily on tolerance/feature requirements |
Ytbehandling | 5-25% | Basic finish vs. extensive polishing/electropolishing |
QA & Inspection | 5-10% | Based on required level of scrutiny & documentation |
Setup & Overheads | 5-10% | Amortized over batch size |
Export to Sheets
Lead Time Considerations:
Lead time refers to the total time from order placement to receiving the finished parts. For metal AM handles, it typically involves several stages:
- Order Processing & File Prep (1-3 days): Final CAD checks, build file preparation, support generation, scheduling.
- Machine Queue Time (1 day – 2 weeks): Waiting for an available machine slot. Can vary significantly based on provider workload. Expedited options may be available at higher cost.
- Printing Time (1 – 5+ days): Depends primarily on build height, volume, and nesting. Complex or tall builds take longer.
- Post-Processing (3 days – 3 weeks): This is often the longest and most variable part of the lead time. Includes cooling, de-powdering, stress relief (furnace cycles take time), part removal, support removal, potential HIPing (can add a week+), machining, finishing, cleaning, inspection. The complexity of these steps dictates the time needed.
- Shipping (1-5 days): Depends on location and shipping method.
Typical Lead Time Ranges:
- Prototyper: Often 5-15 working days, depending on complexity and provider backlog.
- Produktion av små volymer: Typically 3-6 weeks, influenced heavily by batch size and post-processing intensity.
Key Takeaways for Cost & Lead Time:
- DfAM is Crucial: Optimizing the design to minimize volume, height, supports, and post-processing needs is the most effective way to control both cost and lead time.
- Post-Processing Matters: Don’t underestimate the time and cost impact of post-processing steps required to meet functional requirements.
- Material Choice Impact: Ti-6Al-4V is significantly more expensive than 316L.
- Clear Specifications: Provide clear drawings and specifications, including tolerances, surface finishes, and critical features, to get accurate quotes and timelines.
- Provider Partnership: Work closely with your chosen AM provider to understand trade-offs between design features, cost, and lead time. An experienced provider can offer valuable guidance on achieving cost-effective metal AM production för dina specifika behov.
By understanding these additive manufacturing pricing factors and lead time components, medical device manufacturers can better evaluate the ROI additive manufacturing medical offers and integrate this powerful technology into their product development and supply chain strategies effectively.
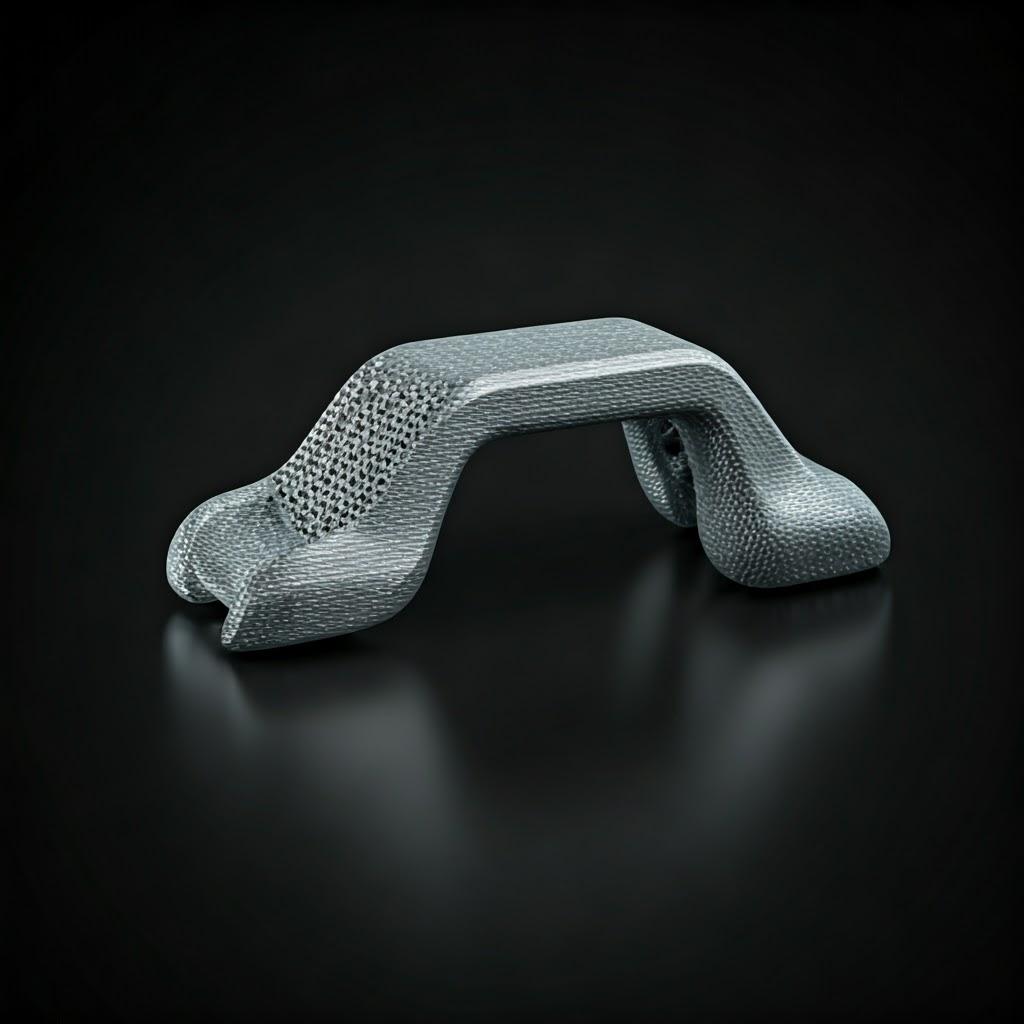
Frequently Asked Questions (FAQ) about Metal 3D Printed Medical Tool Handles
As metal additive manufacturing becomes more prevalent in the medical device industry, engineers, designers, and procurement managers often have specific questions regarding its application for components like tool handles. Here are answers to some frequently asked questions:
1. Q: Are 3D printed metal tool handles (using 316L or Ti-6Al-4V) sterilizable?
A: Yes, absolutely. Both 316L stainless steel and Ti-6Al-4V titanium alloy, when processed correctly via metal AM and properly post-processed, are fully compatible with standard medical sterilization methods.
- Autoclaving (Steam Sterilization): This is the most common method, and both materials withstand the typical temperatures (e.g., 121°C or 134°C) and pressures without degradation of mechanical properties or corrosion.
- Ethylene Oxide (EtO) Gas Sterilization: Both materials are compatible with EtO sterilization.
- Gamma Radiation Sterilization: Ti-6Al-4V generally shows good stability under gamma radiation. 316L is also commonly sterilized this way, although very high doses could potentially affect material properties minimally – typically not a concern for handle applications.
- Sterilant Chemistries (e.g., Peracetic Acid, Hydrogen Peroxide): Both materials exhibit excellent corrosion resistance to common chemical sterilants.
- Critical Considerations:
- Ytfinish: Smoother surfaces achieved through post-processing (e.g., polishing, electropolishing) are easier to clean thoroughly prior to sterilization, reducing bioburden risk. Rough as-built surfaces require more rigorous cleaning validation.
- Cleaning Validation: Regardless of the material, the cleaning process before sterilization must be validated to ensure removal of manufacturing residues and contaminants. Trapped residues could shield microorganisms during sterilization.
- Design for Cleanability (DfAM): Handles, especially those with internal channels, must be designed to facilitate effective cleaning to ensure successful sterilization. Avoid dead-end cavities or features that trap debris.
2. Q: How does the strength and durability of 3D printed metal handles compare to traditionally machined ones?
A: When manufactured using optimized process parameters and appropriate post-processing (especially stress relief and potentially HIPing), metal AM components can achieve mechanical properties (like tensile strength, yield strength, elongation) that are comparable, and sometimes even superior, to those of traditionally wrought or machined materials.
- Materialegenskaper: High-quality metal powders (like those from Met3dp) combined with well-controlled melting processes (L-PBF, EBM) can produce fully dense parts (>99.5%) with fine-grained microstructures.
- Post-Processing Impact: Heat treatments (stress relief, annealing, HIPing) are crucial for homogenizing the microstructure, relieving internal stresses, and optimizing properties like ductility and fatigue strength.
- Anisotropi: There can be slight variations in properties depending on the build direction (Z vs. XY plane) due to the layered structure. Good design practice (DfAM) and process control aim to minimize this effect or orient the part such that critical stresses are aligned with the strongest build direction. For most handle applications, this is manageable.
- Fatigue Life: Surface finish plays a significant role in fatigue performance. A smooth, post-processed surface generally yields better fatigue life than a rough, as-built surface. HIPing can also significantly improve fatigue properties by eliminating internal pores.
- Designoptimering: AM allows for topology optimization, creating designs that are structurally efficient, placing material only where needed. This can result in handles that are lighter yet meet or exceed the strength requirements of bulkier machined designs.
- Outcome: With proper engineering and manufacturing control, strength 3D printed vs machined components can be equivalent or better for handle applications. Rely on data sheets from reputable AM providers based on tested material properties according to relevant standards (e.g., ASTM, ISO).
3. Q: Can I get custom textures, complex grip patterns, or integrated markings on my tool handles using metal 3D printing?
A: Yes, this is a major advantage of metal AM. Unlike traditional methods where adding textures or complex patterns often requires separate, costly processes (e.g., specialized machining, etching, overmolding), additive manufacturing allows intricate surface features to be built directly into the handle design.
- Designfrihet: CAD software allows designers to apply virtually any texture map, grip pattern (e.g., knurling, dimples, complex lattices), or ergonomic feature directly onto the handle’s surface model.
- Integrated Features: Logos, identification numbers, depth markings, or other symbols can be embossed or engraved directly during the printing process.
- Gitterstrukturer: External lattice structures can serve as functional grip elements, providing texture, compliance, and ventilation.
- Resolution Limits: There are limits to the fineness of features that can be reliably reproduced, depending on the AM process, machine resolution, and powder size. Very fine textures might require specific parameter tuning or might be better achieved through post-processing like laser texturing if extreme precision is needed.
- Benefit: This capability allows for highly customized, ergonomic grips tailored to user preference or specific procedural requirements, enhancing comfort, control, and potentially safety, all integrated within a single manufacturing step. Custom textures AM handles are a key differentiator.
4. Q: What is the typical Minimum Order Quantity (MOQ) for custom metal AM handles? Is it suitable for low-volume production?
A: Metal AM is exceptionally well-suited for low-to-medium volume production and prototyping, primarily because it does not require expensive tooling (like molds for MIM or casting).
- No Tooling Cost Barrier: The absence of tooling costs makes AM economically viable for producing even single, unique prototypes or very small batches of custom handles.
- MOQ: Many metal AM service providers do not have a strict MOQ. You can often order quantities from one single unit upwards. The per-part cost will generally be higher for single pieces or very small batches due to setup costs being amortized over fewer parts, but it’s still feasible.
- Sweet Spot: The technology is often most cost-competitive in the range from prototypes up to hundreds or sometimes low thousands of parts per year, especially for complex or customized designs where traditional tooling would be prohibitive or machining excessively time-consuming.
- Bridge Production: AM can serve as “bridge production” – producing initial market launch quantities while high-volume tooling is being prepared (if transitioning to methods like MIM later for very high volumes).
- Tillverkning på begäran: Enables production of specialized handles on an as-needed basis, reducing inventory requirements for diverse but low-demand instrument variations.
5. Q: What are the key regulatory considerations when using metal AM for medical tool handles?
A: While a tool handle itself might be considered lower risk than an implant, using AM necessitates careful consideration within your device’s overall regulatory strategy (e.g., FDA submission, CE marking under MDR).
- Process Validation: Regulatory bodies expect manufacturing processes for medical devices to be validated. This includes validating the AM printing process itself (IQ/OQ/PQ – Installation/Operational/Performance Qualification) and critical post-processing steps like heat treatment and cleaning. Partnering with an ISO 13485 certified provider experienced in validation is highly advantageous.
- Material Equivalency: You may need to demonstrate that the AM material (e.g., AM Ti-6Al-4V) has properties equivalent or superior to the traditionally processed material specified in predicate devices or standards.
- Biokompatibilitet: Although using known biocompatible materials (316L, Ti-6Al-4V), biocompatibility testing (per ISO 10993) on final, processed parts (including worst-case sterilization exposure) is typically required as part of the device’s biological safety assessment.
- Cleaning Validation: Demonstrating effective removal of manufacturing residues (powder, supports, processing fluids) is critical.
- Sterilization Validation: The chosen sterilization method must be validated for the final device configuration, including the AM handle.
- Supplier Controls: Your quality system must include controls for selecting and monitoring your AM supplier, especially if they are considered a critical supplier (which is likely for medical components).
- Documentation & Traceability: Robust documentation covering material sourcing, process parameters, post-processing, inspection results, and batch traceability is essential for regulatory submissions and audits.
Navigating the regulatory landscape is crucial. Engaging with regulatory consultants and choosing an AM partner with strong medical device experience and a robust quality system (like ISO 13485) is highly recommended.
Conclusion: Embracing the Future of Ergonomic Medical Tools with Metal Additive Manufacturing
The journey through the intricacies of metal additive manufacturing for custom medical tool handles reveals a technology poised to redefine standards in surgical instrumentation. We’ve explored the compelling reasons – from achieving unparalleled ergonomic design freedom och significant lightweighting to enabling rapid Anpassning och accelerated prototyping – that position metal AM not just as an alternative, but often as a superior manufacturing solution compared to traditional methods for specific applications. The ability to craft handles perfectly contoured to a surgeon’s hand, integrate complex internal features for enhanced functionality or cleaning, and consolidate multiple components into a single, robust part offers tangible benefits for both practitioners and patients.
Material som 316L rostfritt stål och Titanlegering Ti-6Al-4V, pillars of medical device manufacturing, find new potential through AM, allowing their inherent biocompatibility, corrosion resistance, and strength to be molded into forms previously unattainable. Leveraging high-quality powders, such as those produced using advanced gas atomization and PREP technologies by specialists like Met3dp, ensures the foundational material integrity required for these critical applications.
However, unlocking these benefits requires a deliberate and informed approach. Success hinges on embracing Design för additiv tillverkning (DfAM) principles, meticulously controlling the printing process to achieve desired tolerances and surface finishes, implementing essential efterbearbetning steps like heat treatment and finishing, and proactively navigating potential utmaningar like residual stress and support removal.
Critically, the journey requires collaboration with the right manufacturing partner. Selecting a metal AM service provider involves rigorous evaluation, prioritizing medical device expertise, ISO 13485 certification, robust quality systems, validated processes, and comprehensive capabilities spanning design support through to final inspection. Understanding the nuances of cost factors and lead times allows for realistic project planning and budgeting, highlighting AM’s economic viability, particularly for complex, custom, or low-to-medium volume components where tooling costs are eliminated.
Den future of surgical instrument manufacturing is increasingly intertwined with digital technologies like additive manufacturing. Metal AM empowers medical device companies to innovate faster, create more effective and user-centric tools, and potentially improve surgical outcomes. It offers a pathway to enhanced performance, reduced surgeon fatigue, and greater design possibilities, ultimately contributing to the advancement of healthcare.
For engineers and procurement managers looking to leverage this transformative technology for their next medical tool handle project, the time to explore metal AM is now. By partnering with knowledgeable and capable providers, you can harness the full potential of additive manufacturing to gain a competitive edge and contribute to metal AM medical innovation.
We invite you to explore how Met3dp’s comprehensive solutions – encompassing industry-leading SEBM printers, high-performance metal powders, and deep application expertise – can power your organization’s additive manufacturing goals. Visit our website or contact us today to discuss your specific requirements and discover how we can help you manufacture the next generation of ergonomic medical tools.
Ready to revolutionize your medical tool design? Contact Met3dp today!
Dela på
MET3DP Technology Co, LTD är en ledande leverantör av lösningar för additiv tillverkning med huvudkontor i Qingdao, Kina. Vårt företag är specialiserat på 3D-utskriftsutrustning och högpresterande metallpulver för industriella tillämpningar.
Förfrågan för att få bästa pris och anpassad lösning för ditt företag!
Relaterade artiklar
Om Met3DP
Senaste uppdateringen
Vår produkt
KONTAKTA OSS
Har du några frågor? Skicka oss meddelande nu! Vi kommer att betjäna din begäran med ett helt team efter att ha fått ditt meddelande.
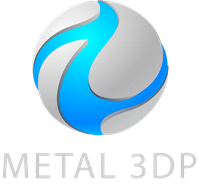
Metallpulver för 3D-printing och additiv tillverkning