Högtemperaturlegering EP648
Innehållsförteckning
Översikt över högtemperaturlegering EP648
När det kommer till material designade för extrema miljöer utmärker sig högtemperaturlegeringar på grund av deras enastående förmåga att motstå tuffa förhållanden. Bland dessa, EP648 har framstått som en avgörande aktör inom olika industriella tillämpningar. Men vad exakt är Högtemperaturlegering EP648, och varför är det så högt uppskattat? Den här artikeln dyker djupt ner i sammansättningen, egenskaperna, tillämpningarna, fördelarna och nackdelarna med EP648, i syfte att ge en grundlig förståelse för detta unika material.
Vad är högtemperaturlegering EP648?
Högtemperaturlegering EP648 är en nickelbaserad superlegering, främst designad för applikationer som kräver exceptionellt motstånd mot höga temperaturer och mekanisk påfrestning. Superlegeringar som EP648 är konstruerade för användning i miljöer där vanliga metaller skulle misslyckas - tänk på flygmotorer, gasturbiner och kärnreaktorer. Med sin imponerande motståndskraft mot oxidation, korrosion och termisk krypning har EP648 blivit ett bra material i industrier där tillförlitlighet och prestanda är av största vikt.
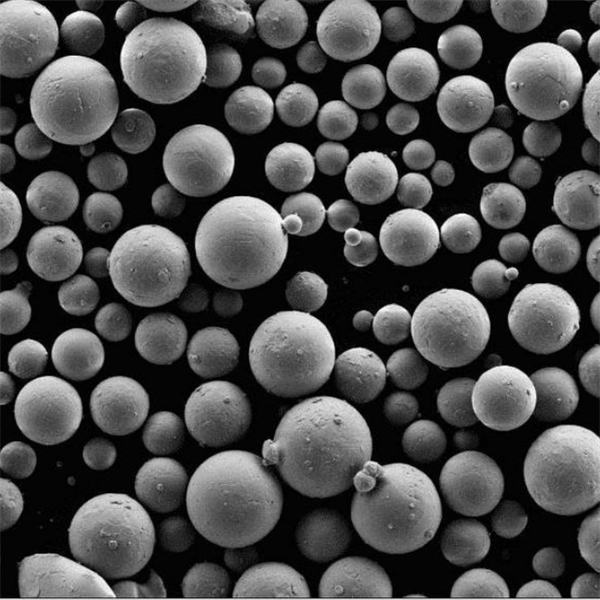
Sammansättning av högtemperaturlegering EP648
Magin med EP648 ligger i dess noggrant balanserade kemiska sammansättning, vilket ger den förmågan att prestera exceptionellt under extrema förhållanden. Här är en närmare titt på de primära elementen som utgör denna högpresterande legering:
Element | Procentuell andel (%) | Roll |
---|---|---|
Nickel (Ni) | 58-65 | Basmetall, ger utmärkt motståndskraft mot värme och korrosion. |
Krom (Cr) | 17-21 | Förbättrar oxidationsbeständigheten och bidrar till bildandet av ett skyddande oxidskikt. |
Kobolt (Co) | 10-15 | Förbättrar hållfasthet och stabilitet vid hög temperatur. |
Molybden (Mo) | 2.5-4.5 | Förbättrar styrkan vid höga temperaturer och motstår termisk krypning. |
Volfram (W) | 2.5-4.5 | Ökar hållfastheten och hårdheten, särskilt vid högbelastningsapplikationer. |
Aluminium (Al) | 0.5-1.5 | Bidrar till oxidationsbeständighet och hjälper till att bilda ett skyddande aluminiumoxidskikt. |
Titan (Ti) | 0.5-1.5 | Förbättrar den totala styrkan och motståndskraften mot termisk utmattning. |
Kol (C) | 0.03-0.10 | Ger solid lösningsförstärkning. |
Bor (B) | 0.001-0.005 | Förbättrar korngränsens styrka, minskar risken för sprickbildning. |
Zirkonium (Zr) | 0.03-0.10 | Förfinar kornstrukturen och förbättrar duktiliteten vid hög temperatur. |
Denna noggranna sammansättning är det som särskiljer EP648, vilket gör den mycket motståndskraftig mot de utmaningar som miljöer med hög temperatur innebär.
Kännetecken för Högtemperaturlegering EP648
Egenskaperna hos EP648 är direkt kopplade till dess sammansättning, och dessa egenskaper är det som gör den så värdefull i industriella applikationer. Här är en djupgående titt på de viktigaste egenskaperna:
1. Högtemperaturstyrka
EP648 kan bibehålla sina mekaniska egenskaper även vid temperaturer över 1 000°C (1 832°F). Detta är avgörande för applikationer som gasturbiner, där material utsätts för extrema termiska belastningar.
2. Oxidations- och korrosionsbeständighet
Tack vare sin höga krom- och aluminiumhalt bildar EP648 ett skyddande oxidskikt som skyddar den från oxidation och korrosion, även i de mest aggressiva miljöerna.
3. Termisk krypmotstånd
Termisk krypning, tendensen hos ett material att långsamt deformeras under konstant stress vid höga temperaturer, är ett betydande problem i många industriella tillämpningar. EP648s sammansättning är speciellt framtagen för att motstå detta fenomen, vilket säkerställer långsiktig tillförlitlighet.
4. Utmärkt svetsbarhet
Till skillnad från vissa högtemperaturlegeringar som kan vara utmanande att arbeta med, erbjuder EP648 god svetsbarhet, vilket gör det lättare att integrera i komplexa sammansättningar utan att kompromissa med prestanda.
5. Utmattningsmotstånd
I miljöer där komponenter utsätts för cykliska belastningar och påfrestningar säkerställer EP648:s motståndskraft mot utmattning att den kan bestå utan att spricka eller gå sönder.
Tillämpningar av högtemperaturlegering EP648
Med tanke på dess imponerande egenskaper kan EP648 användas i ett brett utbud av miljöer med hög stress och hög temperatur. Här är det mest sannolikt att du stöter på den här legeringen:
Tillämpning | Detaljer |
---|---|
Flygmotorer | Används i turbinblad, avgassystem och andra komponenter som utsätts för extrem värme och tryck. |
Gasturbiner | Integrerad i varma sektioner av landbaserade gasturbiner, vilket säkerställer effektivitet och livslängd. |
Kärnkraftsreaktorer | Appliceras i komponenter som kräver motståndskraft mot strålning och extrema temperaturer. |
Kemisk bearbetning | Används i utrustning som måste stå emot korrosiva miljöer vid höga temperaturer. |
Kraftgenerering | Viktigt i delar som värmeväxlare och högtemperaturfästen. |
Olje- och gasindustrin | Används i borrhålsverktyg och utrustning som utsätts för svåra förhållanden. |
Värmebehandlingsugnar | Komponenter gjorda av EP648 tål den intensiva värmen och cyklerna i industriella ugnar. |
Turboladdare för bilar | Ger hållbarhet och prestanda i högpresterande motorer. |
Marin teknik | Används i marina turbiner och avgassystem på grund av dess motståndskraft mot saltvattenkorrosion. |
Kryogen utrustning | Även om den är designad för höga temperaturer, gör EP648:s seghet den också lämplig för lågtemperaturapplikationer. |
Fördelar med högtemperaturlegering EP648
Varför välja EP648 framför andra högtemperaturlegeringar? Här är några viktiga fördelar:
1. Överlägsen prestanda under extrema förhållanden
EP648 överlever inte bara i höga temperaturer – den trivs. Dess förmåga att bibehålla styrka, motstå oxidation och förhindra termisk krypning gör den till det idealiska valet för krävande applikationer.
2. Långsiktig hållbarhet
I branscher där stillestånd är dyrt, säkerställer den långsiktiga hållbarheten hos EP648 att komponenter håller längre, vilket minskar behovet av frekventa byten och underhåll.
3. Mångsidighet
EP648 är ingen one-trick ponny. Dess mångsidighet inom olika branscher – från flyg till kraftproduktion – visar dess breda tillämpbarhet.
4. Svetsbarhet
Legeringens goda svetsbarhet förenklar tillverkningsprocesserna, vilket möjliggör mer komplexa konstruktioner och minskar den totala produktionskostnaden.
Nackdelar med Högtemperaturlegering EP648
Naturligtvis är inget material utan sina nackdelar. Här är några potentiella begränsningar för EP648:
1. Kostnad
Högpresterande legeringar som EP648 är dyra att tillverka, vilket kan vara ett viktigt övervägande i storskaliga applikationer.
2. Bearbetbarhet
Medan EP648 erbjuder god svetsbarhet, kan dess bearbetbarhet vara utmanande och kräver specialiserad utrustning och expertis.
3. Tillgänglighet
På grund av dess specifika sammansättning och tillverkningskrav kanske EP648 inte är lika lättillgänglig som andra vanligare material, vilket kan leda till längre ledtider.
Jämför högtemperaturlegering EP648 med andra legeringar
För att fullt ut uppskatta fördelarna med EP648 är det bra att jämföra den med andra högtemperaturlegeringar:
Fastighet | EP648 | Inconel 718 | Hastelloy X | Rene 41 |
---|---|---|---|---|
Maximal drifttemp | 1000°C | 700°C | 900°C | 980°C |
Oxideringsbeständighet | Utmärkt | Bra | Mycket bra | Utmärkt |
Termisk krypmotstånd | Utmärkt | Måttlig | Bra | Utmärkt |
Svetsbarhet | Bra | Utmärkt | Bra | Rättvist |
Kostnad | Hög | Måttlig | Hög | Mycket hög |
EP648 vs. Inconel 718
Medan både EP648 och Inconel 718 är nickelbaserade superlegeringar, erbjuder EP648 överlägsen prestanda vid högre temperaturer, vilket gör den till ett bättre val för extrema miljöer. Inconel 718 är dock billigare och lättare att bearbeta, vilket gör den att föredra för mindre krävande applikationer.
EP648 vs. Hastelloy X
Hastelloy X är känt för sin enastående oxidationsbeständighet, men EP648 överträffar den när det gäller termisk krypbeständighet och hög temperaturhållfasthet. Hastelloy X är dock lättare att svetsa, vilket kan göra det till ett bättre val i applikationer där detta är en prioritet.
EP648 vs. Rene 41
Rene 41 är en annan högtemperaturlegering med utmärkt hållfasthet och oxidationsbeständighet. Den är dock dyrare och svårare att svetsa än EP648, vilket kan begränsa dess användning i vissa applikationer.
Specifika metallpulvermodeller relaterade till EP648
När det gäller tillverkning av komponenter från högtemperaturlegeringar används ofta metallpulver, särskilt vid additiv tillverkning. Här är några specifika metallpulvermodeller relaterade till EP648:
Metallpulvermodell | Beskrivning |
---|---|
EP648-PM | En pulvermetallurgisk version av EP648, designad för precisionskomponenter inom flyg- och energiproduktion. |
EP648-AM | Optimerad för additiv tillverkning, erbjuder utmärkt flytbarhet och konsekvent partikelstorlek. |
EP648-HD | Pulver med hög densitet för applikationer som kräver maximal materialintegritet och minimal porositet. |
EP648-FG | Finkornigt pulver lämpligt för invecklade komponenter som kräver hög ytfinishkvalitet. |
EP648-HT | Speciellt utvecklad för högtemperaturapplikationer och erbjuder förbättrad termisk stabilitet. |
EP648-MC | Medelgrovt pulver designat för större komponenter, vilket ger en balans mellan flytbarhet och densitet. |
EP648-LC | Lågkolhaltig version av EP648, designad för att minska karbidutfällning och förbättra svetsbarheten. |
EP648-CR | Korrosionsbeständigt pulver, idealiskt för kemisk bearbetning och marina applikationer. |
EP648-RT | Snabbt stelningspulver, som erbjuder förbättrad mikrostrukturell kontroll för krävande applikationer. |
EP648-NP | Icke-poröst pulver designat för applikationer där materialintegriteten är kritisk. |
Dessa specifika modeller är skräddarsydda för olika tillverkningsprocesser och applikationskrav, vilket säkerställer att EP648 kan användas effektivt inom olika industrier.
Specifikationer, storlekar och standarder för Högtemperaturlegering EP648
När man väljer material för ett projekt är det avgörande att se till att de uppfyller specifika standarder och finns i de storlekar som behövs. Här är en uppdelning av specifikationerna, storlekarna och standarderna för EP648:
Specifikation | Detaljer |
---|---|
ASTM-standarder | ASTM B637, ASTM B829, ASTM F3055 |
Tillgängliga storlekar | Stavar, ark och pulver i olika diametrar och tjocklekar från 0,25 mm till 100 mm. |
ISO-standarder | ISO 15156, ISO 5832 |
Anpassade storlekar | Tillgänglig på begäran, beroende på applikation och tillverkningsprocess. |
Värmebehandling | Lösningen härdad vid 1 050°C följt av snabb släckning. |
Ytfinish | Finns i polerad, bearbetad eller gjuten finish. |
Dessa specifikationer säkerställer att EP648 kan skräddarsys för att möta de rigorösa kraven från olika industrier, oavsett om det är för flyg-, energiproduktion eller längre.
Leverantörer och prisuppgifter för högtemperaturlegering EP648
Att hitta rätt leverantör är nyckeln till att säkerställa kvaliteten och tillgängligheten av EP648. Här är en lista över några leverantörer tillsammans med prisinformation:
Leverantör | Plats | Produktsortiment | Uppskattat pris (per kg) |
---|---|---|---|
ATI Metals | USA | Stavar, lakan, pulver | $150 – $250 |
Special Metals Corporation | STORBRITANNIEN | Stavar, barer, puder | $160 – $270 |
VDM Metals | Tyskland | Plåtar, spolar, stavar | $145 – $240 |
Snickeriteknik | USA | Stavar, pulver, trådar | $155 – $260 |
Sandvik Materialteknik | Sverige | Rör, stavar, pulver | $170 – $280 |
Haynes International | USA | Stavar, plattor, trådar | $160 – $275 |
Aperam legeringar | Frankrike | Stavar, ark, spolar | $150 – $265 |
Valsade legeringar | USA | Plåt, stänger, plattor | $140 – $250 |
VDM-legeringar | Tyskland | Pulver, tråd, stavar | $165 – $260 |
Allegheny Technologies | USA | Stavar, trådar, lakan | $155 – $265 |
Priset kan variera beroende på storlek, form och kvantitet som krävs, så det är viktigt att få en exakt offert baserad på dina specifika behov.
För- och nackdelar med högtemperaturlegering EP648
Att fatta ett välgrundat beslut kräver att man väger för- och nackdelar med EP648 mot andra material. Här är en jämförande översikt:
Aspekt | Proffs | Nackdelar |
---|---|---|
Hållfasthet vid höga temperaturer | Exceptionell, bibehåller integriteten vid 1 000°C | Dyrare än andra legeringar |
Oxideringsbeständighet | Utmärkt, bildar ett skyddande oxidskikt | Kan vara utmanande att bearbeta |
Termisk krypmotstånd | Enastående, idealisk för långtidsapplikationer | Längre ledtider på grund av tillgänglighet |
Svetsbarhet | Bra, förenklar tillverkningsprocesser | Specialiserade svetstekniker krävs |
Hållbarhet | Långvarig, minskar underhållskostnaderna | Initialkostnaden är högre jämfört med alternativ |
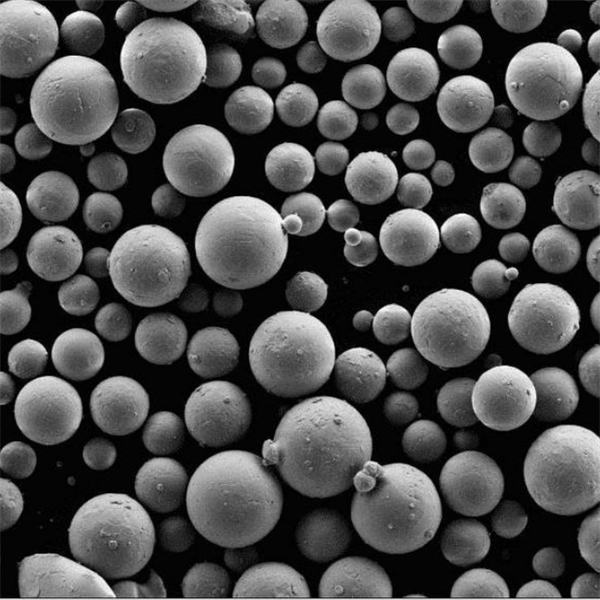
Vanliga frågor
F1: Vad gör EP648 bättre för högtemperaturapplikationer?
A1: EP648 är speciellt framtagen för att tåla extrema temperaturer, upp till 1 000°C, utan att förlora sina mekaniska egenskaper. Dess unika sammansättning, särskilt det höga nickel- och krominnehållet, ger exceptionellt motstånd mot oxidation, termisk krypning och korrosion, vilket gör den idealisk för krävande miljöer som flygmotorer och gasturbiner.
F2: Hur jämför EP648 med andra högtemperaturlegeringar?
A2: Jämfört med andra högtemperaturlegeringar som Inconel 718 eller Hastelloy X erbjuder EP648 överlägsen termisk krypmotstånd och kan arbeta vid högre temperaturer. Det är dock dyrare och kan vara mer utmanande att bearbeta, vilket kan begränsa dess användning i vissa applikationer.
F3: Kan EP648 användas i additiv tillverkning?
A3: Ja, EP648 finns tillgänglig i pulverform speciellt designad för additiv tillverkning. Modeller som EP648-AM är optimerade för denna process och erbjuder utmärkt flytbarhet och konsekvent partikelstorlek, vilket gör den lämplig för att producera komplexa, högpresterande komponenter.
F4: Vilka industrier använder vanligtvis EP648?
A4: EP648 används ofta i industrier som kräver material som tål extrema temperaturer och påfrestningar. Detta inkluderar flyg (turbinblad, avgassystem), kraftgenerering (gasturbiner, värmeväxlare), kemisk bearbetning (korrosiva miljöer) och olje- och gasindustrin (borrhålsverktyg).
F5: Är EP648 svår att bearbeta?
A5: Medan EP648 erbjuder god svetsbarhet, kan dess bearbetbarhet vara utmanande på grund av dess hårdhet och styrka. Specialiserade verktyg och tekniker krävs ofta för att bearbeta EP648 effektivt, vilket kan öka tillverkningskostnaderna.
F6: Finns det några alternativ till EP648?
A6: Alternativ som Inconel 718, Hastelloy X och Rene 41 används ofta i högtemperaturapplikationer. Men var och en av dessa legeringar har olika styrkor och svagheter jämfört med EP648. Till exempel är Inconel 718 lättare att bearbeta och billigare men fungerar inte lika bra vid mycket höga temperaturer.
F7: Hur är kostnaden för EP648 jämfört med andra legeringar?
A7: EP648 är i allmänhet dyrare än andra högtemperaturlegeringar som Inconel 718 eller Hastelloy X på grund av dess överlägsna prestanda och mer komplexa sammansättning. Dess långvariga hållbarhet och motståndskraft mot extrema förhållanden kan dock kompensera för den högre initiala kostnaden.
F8: Kan EP648 lätt svetsas?
A8: EP648 erbjuder god svetsbarhet jämfört med många andra högtemperaturlegeringar, vilket gör den lättare att integrera i komplexa sammansättningar. Svetsning bör dock utföras av skickliga fackmän för att säkerställa att materialets integritet bibehålls.
F9: Vilka former finns EP648 tillgänglig i?
A9: EP648 finns i olika former, inklusive stavar, ark, pulver och trådar. Den kan även specialbeställas i olika storlekar och ytbehandlingar för att möta specifika projektkrav.
F10: Är EP648 lämplig för kryogena tillämpningar?
A10: Även om EP648 i första hand är designad för högtemperaturmiljöer, gör dess seghet och hållbarhet den också lämplig för vissa kryogena applikationer, där material utsätts för extremt låga temperaturer.
Slutsats
Högtemperaturlegering EP648 är ett anmärkningsvärt material designat för att möta utmaningarna i extrema miljöer. Oavsett om det är den brännande värmen från en gasturbin eller den frätande atmosfären i en kemisk anläggning, erbjuder EP648 den styrka, hållbarhet och motståndskraft som krävs för att säkerställa tillförlitlig prestanda. Även om det kan komma med en högre prislapp och vissa bearbetningsutmaningar, uppväger de långsiktiga fördelarna med att använda EP648 ofta dessa nackdelar. För industrier där prestanda inte går att kompromissa med, framstår EP648 som ett toppval, och erbjuder den motståndskraft och tillförlitlighet som modern ingenjörskonst kräver.
Dela på
MET3DP Technology Co, LTD är en ledande leverantör av lösningar för additiv tillverkning med huvudkontor i Qingdao, Kina. Vårt företag är specialiserat på 3D-utskriftsutrustning och högpresterande metallpulver för industriella tillämpningar.
Förfrågan för att få bästa pris och anpassad lösning för ditt företag!
Relaterade artiklar
Om Met3DP
Senaste uppdateringen
Vår produkt
KONTAKTA OSS
Har du några frågor? Skicka oss meddelande nu! Vi kommer att betjäna din begäran med ett helt team efter att ha fått ditt meddelande.
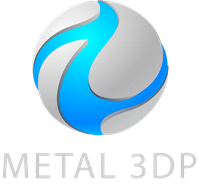
Metallpulver för 3D-printing och additiv tillverkning