in718 pulver
Innehållsförteckning
Additive manufacturing, also known as 3D printing, has revolutionized the way we produce complex parts and components. One material that has gained significant traction in this field is IN718 pulver, a superalloy known for its exceptional strength, corrosion resistance, and high-temperature performance. This article delves into the world of IN718 powder, exploring its composition, properties, applications, and its role in the additive manufacturing industry.
IN718 Powder Composition and Properties
Fastighet | Värde/Beskrivning |
---|---|
Sammansättning | Nickel-based superalloy with chromium, iron, niobium, molybdenum, and other alloying elements |
Täthet | Approximately 8.19 g/cm³ |
Smältpunkt | 1260°C – 1336°C (2300°F – 2437°F) |
Draghållfasthet | Ultimate tensile strength up to 1240 MPa (180 ksi) |
Utbyteshållfasthet | Yield strength up to 1100 MPa (160 ksi) |
Töjning | Elongation between 12-21% |
Hårdhet | Rockwell C hardness up to 45 HRC |
Motståndskraft mot korrosion | Excellent resistance to oxidation and corrosion |
Hållfasthet vid höga temperaturer | Retains high strength up to 700°C (1292°F) |
IN718 powder is a nickel-based superalloy that derives its strength and corrosion resistance from a carefully balanced composition of chromium, iron, niobium, molybdenum, and other alloying elements. Its high melting point, tensile strength, and yield strength make it an ideal choice for applications requiring exceptional mechanical properties, particularly in high-temperature environments.
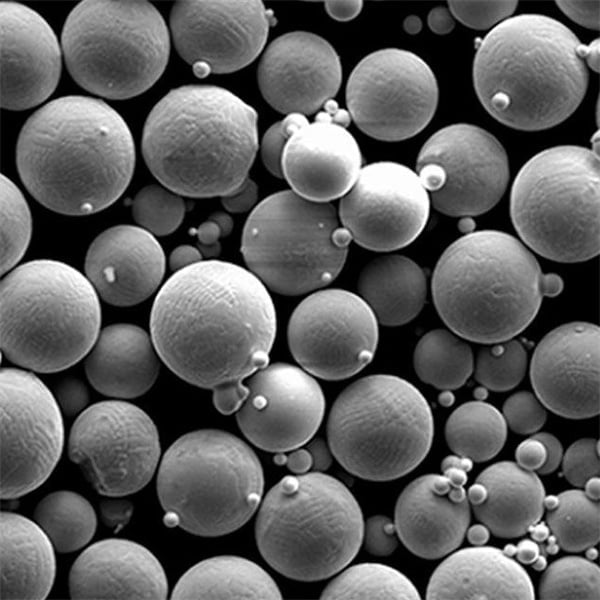
Industriella tillämpningar av IN718 Pulver
Tillämpning | Beskrivning |
---|---|
Flyg- och rymdindustrin | Used in turbine blades, discs, casings, and other hot section components of aircraft engines |
Kraftgenerering | Utilized in gas turbine components, valve components, and other high-temperature applications |
Olja och gas | Employed in downhole tools, valves, and components exposed to harsh environments |
Kemisk bearbetning | Used in pressure vessels, piping, and equipment for handling corrosive materials |
Additiv tillverkning | Widely used for 3D printing of intricate parts and prototypes across various industries |
The versatility of IN718 powder has made it a popular choice across numerous industries, particularly in aerospace, power generation, oil and gas, and chemical processing. Its ability to withstand extreme temperatures and corrosive environments makes it an invaluable material for critical components in these sectors. Additionally, the advent of additive manufacturing has further expanded the applications of IN718 powder, enabling the production of complex geometries and intricate parts that were previously difficult or impossible to manufacture using traditional methods.
IN718 Powder Specifications and Suppliers
Specifikation | Beskrivning |
---|---|
AMS 5662 | Specification for IN718 powder used in additive manufacturing processes |
AMS 5664 | Specification for IN718 powder used in hot isostatic pressing (HIP) processes |
AMS 5383 | Specification for wrought IN718 alloy products |
Leverantör | Plats | Pulverstorleksintervall | Certifiering |
---|---|---|---|
Snickare Tillsats | Förenta staterna | 15-53 μm | AMS 5662, ISO 9001 |
Sandvik Additiv tillverkning | Sverige | 10-45 μm | AMS 5662, ISO 9001 |
Höganäs AB | Sverige | 15-45 μm | AMS 5662, ISO 9001 |
Praxair Ytteknologi | Förenta staterna | 15-53 μm | AMS 5662, ISO 9001 |
LPW Technology Ltd. | Förenade kungariket | 15-53 μm | AMS 5662, ISO 9001 |
The quality and consistency of IN718 powder are crucial for ensuring the performance and reliability of the final components. Several specifications, such as AMS 5662 and AMS 5664, govern the production and quality control of IN718 powder for additive manufacturing and hot isostatic pressing applications. Major suppliers of IN718 powder include Carpenter Additive, Sandvik Additive Manufacturing, Höganäs AB, Praxair Surface Technologies, and LPW Technology Ltd., among others.
Fördelar och begränsningar med IN718 Pulver
Fördelar | Begränsningar |
---|---|
Högt förhållande mellan styrka och vikt | Begränsad duktilitet vid rumstemperatur |
Utmärkt korrosionsbeständighet | Känslig för sprickbildning på grund av belastningsålder |
Exceptional high-temperature performance | Difficult to machine in wrought form |
Versatility across various industries | High cost compared to some other alloys |
Capability for additive manufacturing | Potential for anisotropic properties in AM parts |
IN718 powder offers several advantages, including a high strength-to-weight ratio, excellent corrosion resistance, and exceptional high-temperature performance. These properties make it an ideal material for applications where strength, durability, and resistance to harsh environments are critical. Additionally, the ability to utilize IN718 powder in additive manufacturing processes opens up new possibilities for creating complex geometries and optimized designs.
However, IN718 powder also has some limitations. Its limited ductility at room temperature and susceptibility to strain-age cracking can pose challenges in certain applications. Furthermore, the material can be difficult to machine in its wrought form, and its high cost compared to some other alloys may be a consideration in cost-sensitive projects. Additive manufacturing with IN718 powder can also result in anisotropic properties, where the mechanical properties may vary depending on the build direction.
IN718 Powder Pricing and Cost Considerations
The cost of IN718 powder can vary depending on factors such as supplier, quantity, and powder size distribution. Generally, IN718 powder is more expensive than some other commonly used metal powders due to its specialized composition and processing requirements. Here are some approximate pricing ranges for IN718 powder:
Pulverstorlek | Prisintervall (USD/kg) |
---|---|
15-45 μm | $150 – $300 |
45-105 μm | $120 – $250 |
105-150 μm | $100 – $220 |
It’s important to note that these prices are subject to change based on market conditions and should be verified with suppliers for accurate quotes. Additionally, factors such as transportation costs, import duties, and minimum order quantities may impact the overall cost.
When considering the use of IN718 pulver for additive manufacturing or other applications, it’s essential to weigh the cost against the performance requirements and benefits offered by the material. While IN718 powder may be more expensive than some alternatives, its exceptional properties and versatility often justify the higher cost in applications where performance and reliability are paramount.
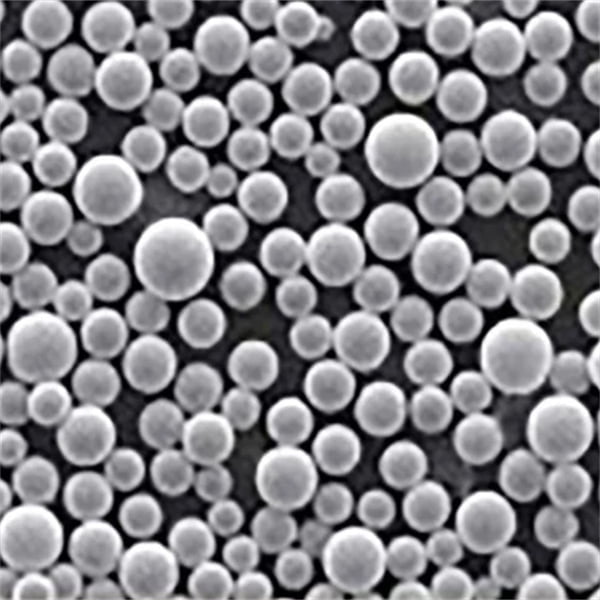
VANLIGA FRÅGOR
Fråga | Svar |
---|---|
What makes IN718 powder suitable for additive manufacturing? | IN718 powder’s high strength, corrosion resistance, and high-temperature performance make it an ideal choice for producing parts using additive manufacturing techniques like powder bed fusion or directed energy deposition. Its weldability and ability to maintain mechanical properties after post-processing also contribute to its suitability for AM. |
How does the powder size distribution affect the properties of additively manufactured parts? | The powder size distribution can influence factors such as surface finish, density, and mechanical properties of the final part. Smaller powder sizes generally result in smoother surface finishes and higher densities, but may also increase the risk of agglomeration and processing challenges. Larger powder sizes can improve flowability but may lead to rougher surfaces and lower densities. Selecting the appropriate powder size distribution is crucial for optimizing the additive manufacturing process and achieving the desired part properties. |
What are the typical post-processing steps for IN718 powder parts produced through additive manufacturing? | Common post-processing steps for IN718 powder parts include stress relief heat treatment, hot isostatic pressing (HIP), solution annealing, and age hardening. These processes help mitigate residual stresses, improve density and microstructural homogeneity, and enhance mechanical properties. The specific post-processing steps and parameters may vary depending on the application and desired properties. |
How does the build orientation affect the mechanical properties of additively manufactured IN718 parts? | The build orientation can influence the mechanical properties of additively manufactured IN718 parts due to the anisotropic nature of the material. Parts built in the vertical orientation typically exhibit higher strengths in the build direction, while those built horizontally may have higher ductility and fracture toughness in the transverse direction. Careful consideration of the build orientation and its impact on the final part properties is essential. |
What are the potential limitations or challenges associated with using IN718 powder in additive manufacturing? | Some challenges with using IN718 powder in additive manufacturing include its high cost, potential for anisotropic properties, susceptibility to cracking or defects, and the need for precise process control and optimization. Additionally, post-processing steps like HIP and heat treatments may be required to achieve desired mechanical properties, adding to the overall complexity and cost. Proper material handling, storage, and process monitoring are crucial to mitigate these challenges. |
Dela på
MET3DP Technology Co, LTD är en ledande leverantör av lösningar för additiv tillverkning med huvudkontor i Qingdao, Kina. Vårt företag är specialiserat på 3D-utskriftsutrustning och högpresterande metallpulver för industriella tillämpningar.
Förfrågan för att få bästa pris och anpassad lösning för ditt företag!
Relaterade artiklar
Om Met3DP
Senaste uppdateringen
Vår produkt
KONTAKTA OSS
Har du några frågor? Skicka oss meddelande nu! Vi kommer att betjäna din begäran med ett helt team efter att ha fått ditt meddelande.
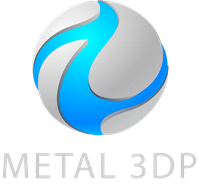
Metallpulver för 3D-printing och additiv tillverkning