Injektionsgjutbart pulver
Innehållsförteckning
Formsprutbart pulver avser en typ av råmaterial som används vid formsprutning av pulver, en industriell tillverkningsprocess för att tillverka komplexa metalldelar med hög precision. Pulvret är en blandning av fina metallpulver och polymerbindemedel som kan formsprutas till komplexa nätformade delar i stora volymer.
Fördelar med att använda formsprutningsbart pulver
Fördel | Beskrivning | Förmån |
---|---|---|
Komplexa geometrier: IMP gör det möjligt att skapa intrikata former med fina detaljer som är svåra eller omöjliga att uppnå med traditionella formsprutningstekniker. Denna designfrihet öppnar dörrar för innovativa komponenter inom olika branscher. | Till skillnad från traditionella gjutmaterial som smält plast, använder IMP ett bindemedelssystem som håller samman pulverpartiklarna under gjutningsprocessen. Detta gör det möjligt att skapa detaljer med invändiga kanaler, underskärningar och andra komplexa geometrier. | |
Materialeffektivitet: IMP främjar tillverkning nära nätform, vilket minimerar materialspillet jämfört med subtraktiva tekniker som maskinbearbetning. Detta är särskilt fördelaktigt för dyra eller högpresterande material. | Den exakta kontrollen över pulverfördelningen under formsprutningen minimerar överflödig materialanvändning. Till skillnad från traditionella processer som genererar skrotdelar under provkörningar, möjliggör IMP dessutom snabbare designupprepningar med minimalt materialspill. | |
Brett materialval: IMP erbjuder ett bredare utbud av materialalternativ jämfört med traditionell formsprutning. Denna mångsidighet gör det möjligt att skapa delar med specifika egenskaper som är skräddarsydda för applikationen. | Utöver standardpolymerer som används vid formsprutning kan IMP använda metallpulver, keramer och till och med kompositmaterial. Detta öppnar dörrar för skapandet av delar med unika kombinationer av styrka, ledningsförmåga eller biokompatibilitet. | |
Högpresterande delar: Möjligheten att använda metall- och keramikpulver i IMP gör det möjligt att tillverka högpresterande detaljer med exceptionell styrka, värmebeständighet eller slitageegenskaper. | Formsprutade komponenter av metall (MIM) kan uppnå mekaniska egenskaper som är jämförbara med smidda metaller (bulk), vilket gör dem lämpliga för krävande applikationer. På samma sätt erbjuder keramiska IMP-komponenter utmärkt slitstyrka och prestanda vid höga temperaturer. | |
Potential för massproduktion: IMP användes ursprungligen för prototyper, men tekniken har nu utvecklats till att möjliggöra kostnadseffektiv massproduktion av komplexa detaljer. | Den höga automatiseringsgrad som kan uppnås i IMP-processerna möjliggör effektiv produktion av stora mängder detaljer med jämn kvalitet. Detta gör IMP till ett bra alternativ för högvolymstillämpningar. | |
Förbättrad ytfinish: Jämfört med traditionella metallgjutningstekniker kan IMP ibland uppnå en jämnare ytfinish på de slutliga delarna. | Användningen av fina pulver och den kontrollerade gjutningsprocessen kan minimera ytfel, vilket potentiellt minskar behovet av omfattande efterbearbetningssteg som polering. |
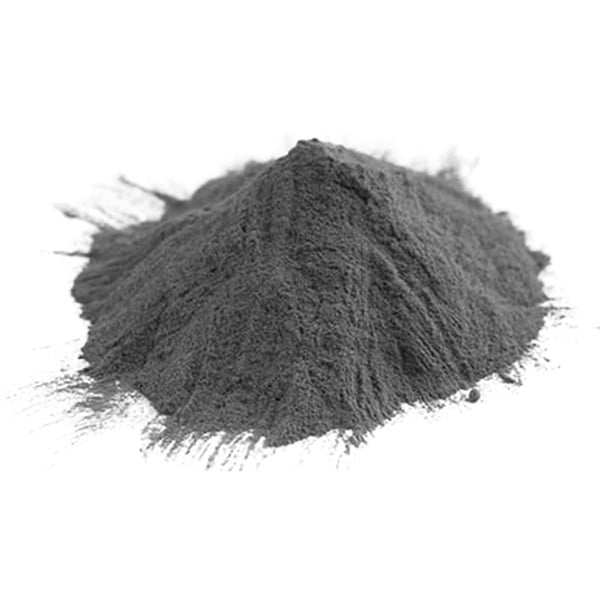
Sammansättning av formsprutbart pulver
Komponent | Beskrivning | Funktion |
---|---|---|
Baspulver | Dessa utgör det primära funktionella materialet i den slutliga delen och kan kategoriseras i tre huvudtyper: Metallpulver: Finfördelade metallpartiklar av olika legeringar, t.ex. rostfritt stål, verktygsstål eller superlegeringar. Keramiska pulver: Keramiska material som aluminiumoxid, zirkoniumoxid eller kiselnitrid i pulverform. Polymerpulver: Termoplastiska polymerer som ofta används vid formsprutning, t.ex. nylon eller polypropylen. | Valet av baspulver avgör de slutliga egenskaperna hos den gjutna delen, t.ex. styrka, slitstyrka eller termisk prestanda. |
Binder-system | Detta är en viktig komponent som fungerar som ett tillfälligt lim som håller ihop baspulverpartiklarna under gjutningsprocessen. Bindemedelssystemet består vanligtvis av: Termoplastisk polymer: Ett termoplastiskt harts som smälter under formsprutningsfasen, vilket möjliggör flytbarhet och vidhäftning med baspulvret. * Vaxer eller tillsatser: Dessa kan förbättra flödesegenskaperna, öka effektiviteten vid avbindning eller underlätta pulverdispersionen i bindemedlet. | Bindemedelssystemet säkerställer att pulvret beter sig som en formbar råvara under injektion och gör det möjligt att skapa komplexa former. |
Porbildande medel | Dessa är valfria tillsatser som skapar tillfälliga porer i den gjutna delen. De kan vara: * Organiska material: Dessa brinner ut under avbindningen och lämnar efter sig ett nätverk av porer som underlättar avlägsnandet av bindemedelssystemet. * Kemiska lakningsmedel: Dessa löses upp i ett specifikt lösningsmedel under ett efterbearbetningssteg, vilket skapar en kontrollerad porstruktur. | Porbildare gör det möjligt att skapa porösa strukturer i den slutliga detaljen, vilket kan vara fördelaktigt för tillämpningar som filter eller benimplantat. |
Egenskaper hos de använda metallpulvren
Karaktäristisk | Beskrivning | Betydelse i MIM |
---|---|---|
Partikelstorlek och distribution | Storleken och fördelningen av metallpulverpartiklarna har en betydande inverkan på följande aspekter av MIM: Formfyllnad och grön styrka: Finare pulver ger i allmänhet bättre packningstäthet och kan förbättra formfyllningen vid formsprutning. Alltför fina partiklar kan dock försämra flytbarheten och leda till utmaningar under bearbetningen. En smal partikelstorleksfördelning säkerställer konsekvent packning och minimerar hålrum i den gjutna delen, vilket bidrar till god grön styrka (styrkan hos delen före sintring). Sintringsbeteende och slutliga egenskaper: Partikelstorleken påverkar sintringsprocessen, där partiklar binds samman och bildar en solid struktur. Pulver med en bredare storleksfördelning kan leda till inhomogen sintring och potentiellt påverka de slutliga mekaniska egenskaperna hos detaljen. | Ett noggrant val av partikelstorlek och -fördelning är avgörande för att uppnå god formfyllnad, grön hållfasthet och optimal prestanda i den slutliga sintrade komponenten. |
Partikelmorfologi | Detta avser formen på metallpulverpartiklarna. Idealt sett gynnar MIM-processer pulver med sfärisk eller nästan sfärisk morfologi. | Sfäriska partiklar flyter lättare, vilket förbättrar formfyllnad och packningstäthet. Oregelbundet formade partiklar kan skapa hålrum och hindra flödesförmågan, vilket kan leda till defekter i den gjutna delen. |
Skenbar densitet och tappdensitet | Dessa egenskaper representerar pulvrets bulkdensitet under olika förhållanden. Skenbar densitet: Detta avser pulvrets densitet i vila, med hänsyn tagen till mellanrummen mellan partiklarna. Tap Density: Detta återspeglar ett tätare tillstånd som uppnåtts genom en standardiserad tappningsprocess. | Högre tappardensitet är generellt önskvärt i MIM för effektivt materialutnyttjande och god måttnoggrannhet i den slutliga detaljen. Det bidrar också till förbättrad packning under gjutning och minimerar krympning under sintring. |
Kemisk sammansättning | De specifika element eller legeringar som används i metallpulvret bestämmer de slutliga egenskaperna hos den sintrade delen. | Valet av metallpulversammansättning gör det möjligt att skräddarsy egenskaper som styrka, korrosionsbeständighet eller slitstyrka för att uppfylla de specifika applikationskraven. MIM kan använda olika metallegeringar, inklusive rostfritt stål, verktygsstål och till och med högpresterande legeringar som Inconel. |
Flytbarhet | Detta avser hur lätt pulvret flyter under tyngdkraft eller pålagda krafter. | God flytbarhet är avgörande för en jämn pulverfördelning vid formsprutning. Pulver med dålig flytbarhet kan leda till inkonsekvenser i packningstätheten och potentiella defekter i den slutliga detaljen. |
Standarder för metallpulver
Metallpulver som används måste uppfylla standarder för sammansättning och kornstorlek:
Standard kropp | Standard | Beskrivning | Betydelse för IMP |
---|---|---|---|
ASTM International (ASTM) | ASTM B930 - Standardguide för pulverkarakterisering av råmaterial för metallinjektionsgjutning (MIM) | Denna standard beskriver olika testmetoder för att karakterisera egenskaperna hos metallpulver som används i MIM. | Ger ett ramverk för utvärdering av faktorer som partikelstorleksfördelning, morfologi, flytbarhet och skenbar densitet. Detta säkerställer konsekvens och kvalitetskontroll i de metallpulver som används för IMP-applikationer. |
** | ** | * ASTM B783 - Standardspecifikation för pulver av rostfritt stål för metallinjektionsgjutning (MIM) | Denna standard definierar specifika krav på kemisk sammansättning, partikelstorleksfördelning och flytbarhet hos pulver av rostfritt stål som används i MIM. |
** | ** | * ASTM D4000 - Standardklassificeringssystem för specificering av plastmaterial | Även om denna standard inte är exklusiv för IMP, innehåller den ett klassificeringssystem för olika typer av plastmaterial, inklusive sådana som potentiellt används som bindemedel i IMP:s råmaterial. |
Internationella standardiseringsorganisationen (ISO) | * ISO 3095 - Metallpulver - Bestämning av flödeshastighet med hjälp av en Hall-flödesmätare | Denna standard specificerar en metod för att mäta flytbarheten hos metallpulver med hjälp av en Hall-flödesmätare. | Ger ett standardiserat tillvägagångssätt för att bedöma flytbarhet, en kritisk egenskap för att uppnå god formfyllnad och jämn kvalitet på detaljerna i IMP. |
** | ** | * ISO 4497 - Plast - Bestämning av smältflödeshastighet (MFR) och smältvolymflödeshastighet (MVR) för termoplaster | Denna standard beskriver en metod för att mäta smältflödeshastigheten (MFR) för termoplastiska material, vilket kan vara relevant för bindemedelskomponenten i IMP-råvara. |
Steg i tillverkningsprocessen
Tillverkningsprocessen består av följande viktiga steg:
Steg | Beskrivning | Betydelse |
---|---|---|
1. Beredning och blandning av pulver | Baspulvret (metall, keramik eller polymer) väljs noggrant ut och förbehandlas utifrån de önskade slutliga egenskaperna. Tillsatser som porbildare eller smörjmedel kan ingå. Pulvret vägs sedan exakt och blandas med bindemedelssystemet för att bilda en homogen råvara. | Detta steg lägger grunden för den slutliga detaljens egenskaper. Noggrant urval och noggrann blandning säkerställer ett konsekvent materialbeteende under bearbetningen. |
2. Formsprutning | Det förberedda IMP-materialet värms upp till ett halvsmält tillstånd och injiceras i en sluten formkavitet under högt tryck. Formen replikerar den önskade formen på den slutliga delen. | I detta skede definieras detaljens geometri. Ett jämnt flöde och tryck under insprutningen är avgörande för att uppnå exakta detaljmått och minimala defekter. |
3. Avbindning | Den gjutna delen, även kallad den "gröna delen", genomgår en avbindningsprocess för att avlägsna bindemedelssystemet. Detta kan uppnås genom: * Avbindning med lösningsmedel: Delen sänks ned i ett lösningsmedel som löser upp bindemedlet och lämnar kvar pulverstrukturen. * Termisk avbindning: Delen utsätts för en kontrollerad värmecykel, där bindemedlet sönderdelas termiskt och avgår som gas. | Effektiv avbindning är avgörande för att uppnå den slutliga önskade formen och porositeten utan att skada den känsliga pulverstrukturen. |
4. Sintring | Den avgradade delen utsätts för höga temperaturer i en kontrollerad atmosfär (ofta under vakuum eller inert gas). Denna process främjar diffusion och bindning mellan pulverpartiklarna, vilket resulterar i en solid och nästan nätformad komponent. | Sintringen avgör de slutliga mekaniska egenskaperna hos detaljen, såsom hållfasthet, densitet och dimensionsstabilitet. Exakt temperaturkontroll och atmosfärhantering är avgörande. |
5. Efterbearbetning | Beroende på applikationskraven kan den sintrade delen genomgå ytterligare efterbehandlingssteg som t.ex: * Maskinbearbetning eller slipning: För att uppnå exakta dimensionstoleranser eller ytfinish. * Värmebehandling: För att förbättra specifika mekaniska egenskaper som styrka eller hårdhet. * Beläggning eller infiltration: För att förbättra ytegenskaper som slitstyrka eller korrosionsbeständighet. | Efterbehandlingsbehandlingar kan ytterligare förbättra funktionaliteten och estetiken hos den slutliga IMP-delen. |
Tillämpningar av formsprutade delar
Formsprutbart pulver kan användas för att tillverka olika komplicerade och högprecisionsdetaljer inom olika branscher:
Industri | Exempel på tillämpningar | Fördelarna med formsprutning |
---|---|---|
Fordon | Inredningskomponenter (instrumentbrädor, dörrpaneler, konsoler) Delar under motorhuven (fläktkåpor, insugningsrör) Funktionella komponenter (kugghjul, kedjehjul) | Högvolymsproduktion av komplexa former med exakta detaljer. Lättviktsdelar för förbättrad bränsleeffektivitet. Brett utbud av materialalternativ för olika prestandabehov (hållbarhet, värmebeständighet). |
Konsumentelektronik | Elektroniska höljen (telefoner, bärbara datorer, surfplattor) Anslutningar och knappar Interna komponenter (fästen, kugghjul) | Massproduktion av komplicerade detaljer med hög måttnoggrannhet. Slät ytfinish för estetik och användarvänlighet. Olika färger och texturer kan uppnås genom materialval och gjutningstekniker. |
Medicintekniska produkter | Kirurgiska instrument (handtag, grepp) Proteser (knäleder, tandimplantat) Medicinska komponenter för engångsbruk (sprutor, vialer) | Steriliserbara material för hygien och säkerhet. Biokompatibla material för användning i människokroppen (vissa polymerer och metallegeringar). Komplexa geometrier för exakt funktionalitet i medicinska applikationer. |
Flyg- och rymdindustrin samt försvar | Flygplanskomponenter (kanaler, delar till landningsställ) Satellitkomponenter (fästen, höljen) Försvarsutrustning (hjälmar, vapenkomponenter) | Lättvikts- och höghållfasta material för viktminskning inom flyg- och rymdindustrin. Flamskyddade eller värmebeständiga material för specifika krav. Slitstarka delar för tuffa miljöer och krävande driftsförhållanden. |
Konsumentvaror | Leksaker och spel Vitvaror (höljen, vred, rattar) Sportartiklar (hjälmar, cykeldelar) | Kostnadseffektiv produktion för konsumentprodukter i stora volymer. Stort utbud av färger och ytbehandlingar för visuell attraktionskraft. Slitstarka och funktionella delar för daglig användning. |
Fördelar med formsprutning för tillverkning av detaljer
Fördel | Beskrivning | Förmån |
---|---|---|
Produktion av stora volymer: Formsprutning är utmärkt för effektiv produktion av stora mängder identiska detaljer. Automatiseringsmöjligheterna och de snabba cykeltiderna möjliggör kostnadseffektiv massproduktion. | Detta är särskilt fördelaktigt för produkter som kräver miljontals enheter, t.ex. konsumentelektronik eller komponenter till fordonsindustrin. Konsekvent kvalitet och repeterbarhet säkerställs genom hela produktionskedjan. | |
Flexibilitet i utformningen: Formsprutning kan hantera ett brett spektrum av geometriska komplexiteter, inklusive intrikata former, tunna väggar och interna funktioner. Denna designfrihet gör det möjligt att skapa funktionella och innovativa delar. | Till skillnad från vissa subtraktiva tillverkningsmetoder begränsas formsprutning inte av verktygsgeometrin. Underskärningar, kanaler och andra komplexa detaljer kan gjutas in direkt i detaljen. | |
Dimensionell noggrannhet och repeterbarhet: Den exakta kontrollen över verktygskonstruktion och insprutningsparametrar ger konsekventa och exakta detaljdimensioner för höga produktionsvolymer. | Detta minimerar behovet av efterbearbetningssteg för dimensionskorrigering och säkerställer utbytbara delar vid montering. Repeterbarhet är avgörande för att upprätthålla konsekvent produktkvalitet och funktionalitet. | |
Brett materialurval: Ett stort antal material kan användas vid formsprutning, inklusive termoplaster, härdplaster, elastomerer och till och med vissa metallegeringar (genom Metal Injection Molding - MIM). | Denna mångsidighet gör det möjligt att välja det optimala materialet baserat på de önskade egenskaperna som styrka, värmebeständighet, kemisk beständighet eller flexibilitet. | |
Ytfinish och estetik: Formsprutning kan producera detaljer med jämn och högkvalitativ ytfinish, vilket ofta eliminerar behovet av omfattande efterbearbetningssteg som polering. Dessutom kan olika färgämnen och texturer införlivas under gjutningen. | Detta bidrar till att göra slutprodukten mer tilltalande och funktionell. Släta ytor kan vara avgörande för hygienen i medicintekniska produkter eller för enkel rengöring av konsumentvaror. | |
Materialeffektivitet: Formsprutning främjar tillverkning nära nettoform, vilket minimerar materialavfallet jämfört med subtraktiva tekniker som maskinbearbetning. Överskottsmaterial, så kallad gran och medbringare, kan ofta återvinnas och återanvändas i efterföljande produktionskörningar. | Detta är fördelaktigt ur ett kostnads- och hållbarhetsperspektiv. Genom att minimera avfallet minskar också tillverkningsprocessens miljöpåverkan. | |
Potential för automatisering: Formsprutningsprocessen kan automatiseras i hög grad, med minimal mänsklig inblandning i driften. Detta ger en jämn produktionskvalitet och sänker arbetskostnaderna. | Automatisering är särskilt fördelaktigt vid produktion av stora volymer och säkerställer en jämn produktkvalitet oavsett operatörens kompetensnivå. |
Begränsningar i tillverkningsprocessen
Det finns också vissa begränsningar:
- Delvikt begränsad till < 400 g
- Väggtjocklek > 0,4 mm
- Sammansättningar behövs för komplexa geometrier
- Dyra verktyg för gjutformar
- Dimensionsförändringar under sintring
Globala leverantörer av råmaterial
Många internationella företag levererar färdigt råmaterial för formsprutning:
Företag | Plats | Material |
---|---|---|
BASF | Tyskland | 316L rostfritt stål, titanlegeringar |
Sandvik | Sverige | Rostfria stål, verktygsstål |
GKN | STORBRITANNIEN | Aluminium- och magnesiumlegeringar |
Rio Tinto | Australien | Injekterade blandningar av metall och keramik |
Indikativ prissättning
Material | Prisintervall |
---|---|
Rostfritt stål | $50-70 per kg |
Verktygsstål | $45-65 per kg |
Tung legering av volfram | $130-170 per kg |
Priserna beror på ordervolymer, behov av kundanpassning och ekonomiska faktorer.
För- och nackdelar med att använda Formsprutningsbara pulver
Fördelar | Nackdelar |
---|---|
Invecklade och komplexa former | Begränsad storlek och vikt |
Snävare toleranser | Dyra verktyg och utrustning |
Fin ytfinish | Dimensionsförändringar under sintring |
Utbud av material | Efterbearbetning behövs ofta |
Hög produktion, låg kostnad per del | Sköra material tenderar att spricka |
Minskat avfall | Begränsar val av material |
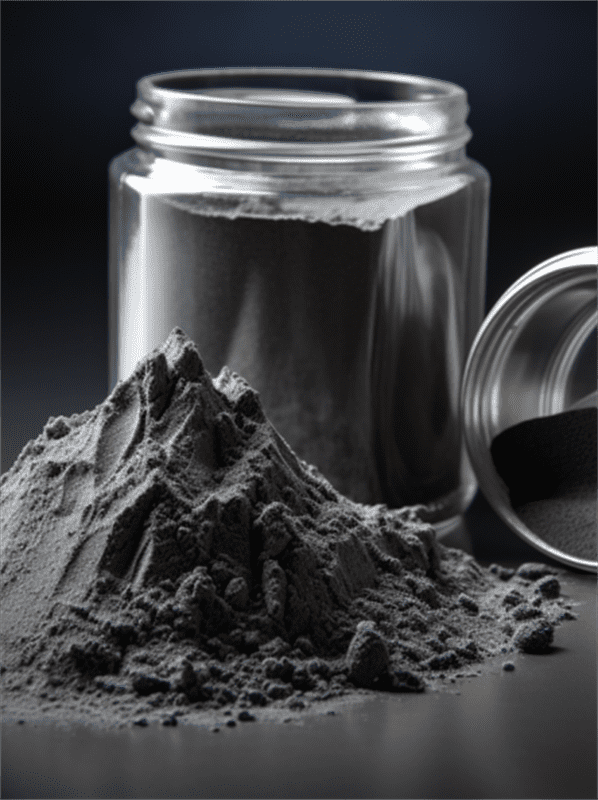
VANLIGA FRÅGOR
F: Vilken är den typiska sammansättningen av formsprutningsbara pulver?
A: De innehåller 80-90% metallpulver, 8-20% bindemedel och 1-2% smörjmedel efter vikt. Vanliga bindemedel är vax, PP, PE och PEG.
F: Vilken storlek på pulver används?
S: Pulver mellan 1-20 mikrometer används. Finare pulver förbättrar densiteten men kan vara benägna att agglomerera.
F: Hur mycket krympning sker under sintring?
A: Upp till 20% linjär krympning av detaljer sker under sintring i vätskefas. Hänsyn måste tas till detta vid verktygskonstruktionen.
F: Vad orsakar sprickor i formsprutade delar av sintrad metall?
A: Ojämn uppvärmning i ugnar, användning av snabb kylning efter sintring, dålig pulverblandning och val av spröda legeringar.
F: Vilka materialalternativ finns det för formsprutningsbara pulver?
A: Rostfria stål, verktygsstål, tunga volframlegeringar, kopparlegeringar, titan och titanlegeringar m.fl.
Dela på
MET3DP Technology Co, LTD är en ledande leverantör av lösningar för additiv tillverkning med huvudkontor i Qingdao, Kina. Vårt företag är specialiserat på 3D-utskriftsutrustning och högpresterande metallpulver för industriella tillämpningar.
Förfrågan för att få bästa pris och anpassad lösning för ditt företag!
Relaterade artiklar
Om Met3DP
Senaste uppdateringen
Vår produkt
KONTAKTA OSS
Har du några frågor? Skicka oss meddelande nu! Vi kommer att betjäna din begäran med ett helt team efter att ha fått ditt meddelande.
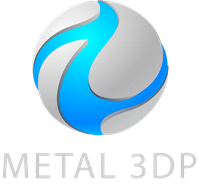
Metallpulver för 3D-printing och additiv tillverkning