Precision Instrument Housing 3D Printed in Invar
Innehållsförteckning
In the intricate world of advanced instrumentation, particularly radar systems deployed across aerospace, defense, automotive, and meteorological sectors, the housing is far more than a simple container. It’s a critical component ensuring the system’s accuracy, reliability, and longevity, often in challenging operational environments. Traditional manufacturing methods have long served this purpose, but they face limitations when dealing with complex geometries, rapid iteration needs, and the unique material properties required for peak performance. Enter metal additive manufacturing (AM), a transformative technology enabling the production of highly complex, precise, and functionally optimized components like radar housings. This post delves into the specifics of using metal 3D-utskrifter, particularly with materials like Invar (FeNi36), to manufacture precision instrument housings that meet and exceed the demanding requirements of modern radar systems. We’ll explore the applications, the distinct advantages AM offers, and the critical role material selection plays in achieving unparalleled performance.
Introduction: The Critical Role of Precision Radar Housings and Invar 3D Printing
Radar (Radio Detection and Ranging) systems operate by transmitting radio waves and analyzing the reflected signals to detect objects, determine their range, speed, and direction. The effectiveness of these systems hinges on the precise alignment and stability of their internal components – the transmitter, receiver, antenna, and processing units. The housing serves several crucial functions:
- Structural Integrity: It provides a robust framework holding sensitive components in precise alignment, resisting vibrations, shocks, and external forces encountered during operation (e.g., on aircraft, vehicles, or exposed installations).
- Environmental Protection: It shields delicate electronics from environmental factors like moisture, dust, temperature fluctuations, and electromagnetic interference (EMI).
- Termisk hantering: It often plays a role in dissipating heat generated by the electronics, preventing overheating that could degrade performance or cause failure.
- Maintaining Dimensional Stability: This is perhaps the most critical function for high-precision radar. Temperature changes cause materials to expand or contract. In a radar system, even minute dimensional changes in the housing can alter the alignment of antennas or reflectors, leading to signal degradation, pointing errors, and inaccurate measurements.
This is where the choice of material becomes paramount. For applications demanding exceptional dimensional stability across a wide range of operating temperatures, Invar (FeNi36) stands out. Invar is a nickel-iron alloy renowned for its uniquely low coefficient of thermal expansion (CTE). Its dimensions remain remarkably stable despite significant temperature swings, making it ideal for precision instruments like telescopes, measurement standards, and, critically, radar housings operating in environments with thermal variability – from the cold of high altitudes to the heat of engine compartments or direct sunlight.
Traditionally, manufacturing complex Invar components involved subtractive machining from solid blocks or casting, processes that can be costly, time-consuming, and generate significant material waste. Furthermore, these methods often struggle to create the highly intricate internal structures or optimized geometries that can enhance performance (e.g., conformal cooling channels, integrated mounting features, lightweight lattice structures).
Metal additive manufacturing solutions, particularly Powder Bed Fusion (PBF) techniques like Selective Laser Melting (SLM) or Electron Beam Melting (EBM), offer a revolutionary alternative. By building the housing layer by layer directly from fine metal powder, AM enables:
- Unprecedented Geometric Freedom: Creating complex internal features, thin walls, and organic shapes previously impossible or impractical to manufacture.
- Materialeffektivitet: Using only the material necessary for the part, minimizing waste.
- Rapid Prototyping and Iteration: Quickly producing and testing design variations.
- Del Konsolidering: Combining multiple components into a single, integrated printed part, reducing assembly time and potential failure points.
Företag gillar Met3dp, headquartered in Qingdao, China, are at the forefront of this technological shift. Specializing in advanced 3D-utskrift av metall equipment and high-performance metal powders, Met3dp provides the capabilities necessary to produce mission-critical parts like precision radar housings. Their expertise in both machine technology and material science, particularly with challenging alloys like Invar, makes them a valuable partner for industries seeking the highest levels of precision and reliability. Utilizing Invar powder via metal AM allows engineers to harness the material’s stability while leveraging the design freedom of 3D printing, resulting in radar housings optimized for performance in the most demanding applications.
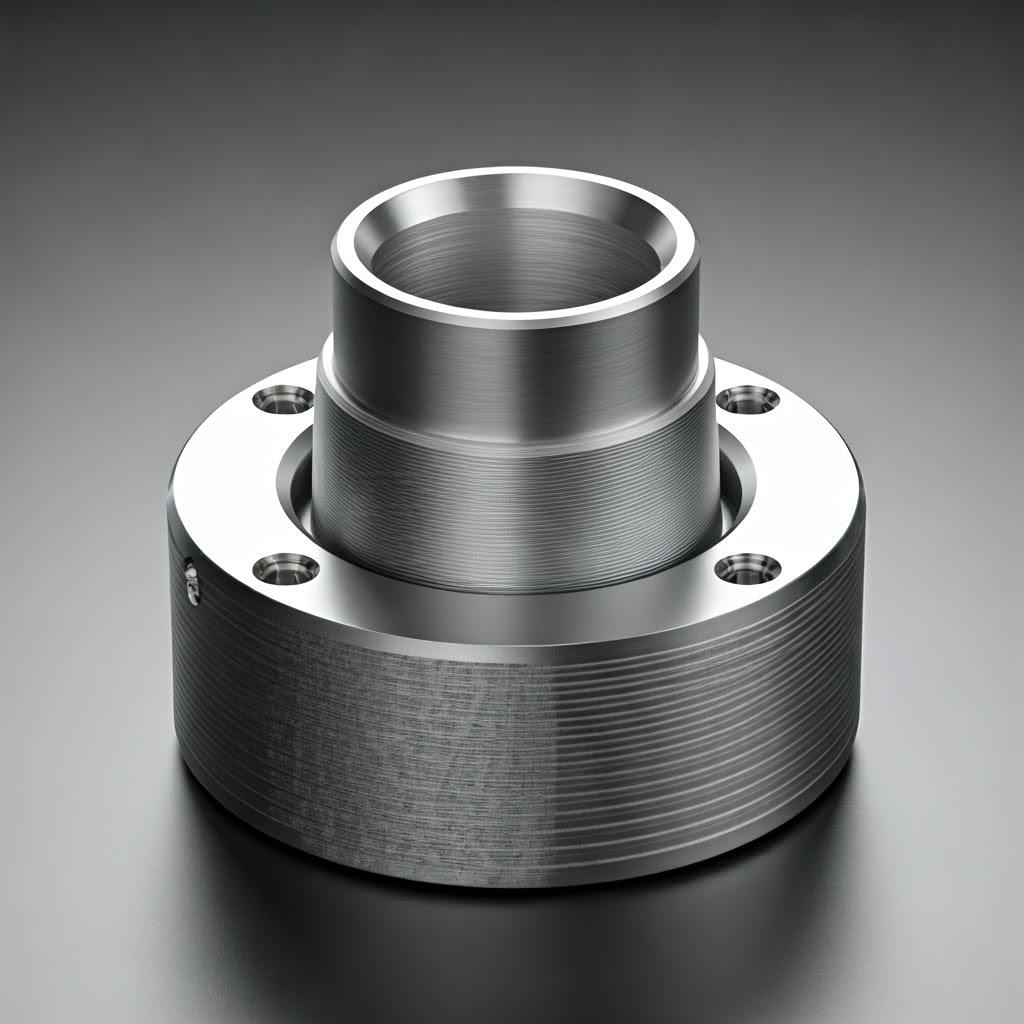
Applications: Where are 3D Printed Invar Radar Housings Utilized?
The unique combination of Invar’s thermal stability and the design flexibility offered by metal 3D printing makes these housings highly sought after in sectors where precision under varying temperatures is non-negotiable. Procurement managers, engineers, and system designers in these fields are increasingly specifying 3D printed Invar for critical applications:
- Flyg- och rymdindustrin samt försvarsindustrin:
- Airborne Radar Systems: Housings for fire-control radar, surveillance radar, and weather radar on military and commercial aircraft. These systems experience rapid temperature changes with altitude shifts and varying atmospheric conditions. Invar ensures the antenna arrays and sensitive optics maintain alignment for accurate targeting and navigation.
- Satellite Payloads: Housings for communication antennas, synthetic aperture radar (SAR) components, and optical benches within satellites. Space presents extreme thermal cycles (direct sunlight vs. shadow), demanding the utmost stability provided by Invar. AM allows for lightweighting, crucial for reducing launch costs.
- Missile Guidance Systems: Protecting and aligning critical seeker head components. Dimensional stability directly impacts targeting accuracy during flight through varying atmospheric layers.
- Ground-Based Defense Radar: Housings for phased array antennas and tracking systems exposed to harsh environmental conditions and requiring consistent performance.
- Fordon:
- Advanced Driver Assistance Systems (ADAS): Housings for high-resolution automotive radar sensors (e.g., 77 GHz, 79 GHz) used in adaptive cruise control, collision avoidance, and autonomous driving functions. These sensors are often mounted externally or near engines, subject to significant temperature variations, vibrations, and environmental exposure. Invar ensures consistent sensor performance regardless of weather or operating conditions.
- Lidar Systems: While often using different sensor types, the precision mounting structures and housings for Lidar can also benefit from Invar’s stability, especially in integrated sensor suites where thermal management across different sensor types is critical.
- Meteorology:
- Weather Radar Systems: Ground-based Doppler radar systems require extremely stable antenna mounts and enclosures to ensure accurate precipitation measurement and storm tracking over long periods and across seasons with wide temperature swings. Invar housings maintain the precise geometry needed for consistent beam forming and reception.
- Telekommunikation:
- High-Frequency Ground Antennas: Housings and mounting structures for millimeter-wave base station antennas (e.g., 5G and beyond) where precise beamforming is critical and environmental temperature changes can affect performance.
- Industrial Metrology and Scientific Instruments:
- Precision Measurement Equipment: Housings for laser trackers, interferometers, and other high-accuracy measurement devices used in manufacturing and scientific research, where ambient temperature fluctuations could introduce measurement errors.
- Optical Systems: Mounts and housings for large telescopes, optical benches, and laser systems where maintaining precise alignment of optical elements over temperature changes is paramount.
Why Invar is Critical in These Applications:
Feature Affected by Thermal Expansion | Consequence in Radar Systems | How Invar Mitigates the Issue |
---|---|---|
Antenna/Reflector Alignment | Beam pointing errors, reduced gain, inaccurate ranging/tracking | Maintains precise geometry, ensuring stable focus |
Resonant Cavity Dimensions | Frequency drift, reduced sensitivity | Keeps cavity dimensions stable, preserving frequency |
Electronic Component Mounting | Induced stress on solder joints, potential component failure | Reduces thermally induced mechanical stress |
Overall System Calibration | Need for frequent recalibration, reduced operational readiness | Enhances long-term calibration stability |
Export to Sheets
By leveraging 3D printed Invar, manufacturers and suppliers can deliver radar housings that offer superior performance and reliability compared to those made from materials with higher CTEs (like aluminum or standard steels) or those constrained by traditional manufacturing limitations. Met3dp’s capability to produce complex parts from these advanced materials supports innovation across these demanding B2B sectors.
Advantages of Metal Additive Manufacturing for Radar Housings
Choosing metal AM over conventional methods like CNC machining, casting, or sheet metal fabrication for producing radar housings, especially those requiring materials like Invar, offers compelling technical and business advantages. These benefits are driving adoption among engineers and procurement professionals looking for enhanced performance, faster development cycles, and optimized supply chains.
Viktiga fördelar:
- Unmatched Design Freedom & Complexity:
- Internal Features: AM allows for the seamless integration of complex internal structures like cooling channels that conform precisely to heat-generating components, waveguides, internal mounting bosses, and EMI shielding lattices directly into the housing design. This is extremely difficult or impossible with machining.
- Organic Shapes & Thin Walls: Designs are not limited by tool access or draft angle constraints. This enables the creation of highly optimized, curved, and thin-walled structures that minimize weight and material usage while maximizing structural integrity.
- Del Konsolidering: Multiple components that would traditionally be manufactured separately and then assembled (e.g., housing body, brackets, connectors, lids) can often be redesigned and printed as a single, monolithic part. This reduces assembly time, eliminates potential leak paths or points of failure at joints, simplifies inventory management, and lowers overall part count.
- Lightweighting through Optimization:
- Topology Optimization: Software tools can analyze load conditions and remove material from non-critical areas, creating highly efficient, organic-looking structures that meet strength requirements with significantly reduced mass. This is invaluable in aerospace and automotive applications where weight savings translate directly to fuel efficiency or payload capacity.
- Gitterstrukturer: Internal lattice or gyroid structures can be incorporated to provide structural support with minimal material, further reducing weight while maintaining stiffness.
- Accelerated Prototyping and Development Cycles:
- Snabb iteration: New design variations can be printed and tested in days rather than the weeks or months often required for tooling and setup in traditional manufacturing. This allows engineers to quickly validate performance, optimize designs, and get products to market faster.
- Tooling Elimination: AM builds parts directly from a digital file, eliminating the significant cost and lead time associated with creating molds (casting) or complex fixtures (machining).
- Material Efficiency and Sustainability:
- Near-Net Shape Production: AM processes typically use only the material needed for the part and temporary supports, resulting in significantly less material waste compared to subtractive machining, which starts with a larger block and removes material. This is particularly beneficial when working with expensive alloys like Invar or Titanium.
- Reduced Energy Consumption (Potentially): While the printing process itself is energy-intensive, eliminating tooling production and reducing material waste can lead to a lower overall energy footprint for the final part in some scenarios.
- On-Demand Manufacturing and Supply Chain Flexibility:
- Digital Inventory: Designs exist as digital files, allowing parts to be printed when needed, reducing the need for large physical inventories and associated storage costs.
- Distributed Manufacturing: Parts can potentially be printed closer to the point of use, streamlining logistics and reducing shipping times, especially for spare parts or replacements.
- Enhanced Thermal Management:
- Conformal Cooling: As mentioned, AM enables the creation of cooling channels that closely follow the contours of heat-generating components, providing much more efficient heat dissipation than traditional drilled channels or heat sinks. This is crucial for maintaining the stable operating temperature required by sensitive radar electronics.
Comparison: AM vs. Traditional Methods for Complex Invar Housings
Funktion | Metal Additive Manufacturing (PBF) | CNC Machining from Billet | Investeringsgjutning |
---|---|---|---|
Geometrisk komplexitet | Very High (Internal features, organics) | Moderate (Limited by tool access) | High (but requires tooling, draft angles) |
Konsolidering av delar | High potential | Low potential | Moderate potential |
Lättvikt | Excellent (Topology opt., lattices) | Moderate (Pocketing) | Moderate (Wall thickness limits) |
Material Avfall | Low (Powder recycle possible) | High (Significant chip generation) | Moderate (Gates, runners) |
Lead Time (Proto) | Fast (Days) | Moderate (Days/Weeks, requires setup) | Slow (Weeks/Months, requires mold) |
Verktygskostnad | Ingen | Low (Fixturing) | High (Mold production) |
Ideal Volume | Prototypes, Low-Mid Volume, Complex Parts | Prototypes, Mid-High Volume, Less Complex | Mid-High Volume |
Materialegenskaper | Near Wrought (with proper post-processing) | Wrought (Starts from solid) | Cast (Different grain structure) |
Termisk hantering | Excellent (Conformal cooling) | Limited (Drilled channels) | Limited (Design constraints) |
Export to Sheets
For demanding applications like radar housings requiring both the unique properties of Invar and complex, optimized designs, metal additive manufacturing, supported by experienced providers like Met3dp with their industry-leading print volume, accuracy and reliability, offers a compelling value proposition unmatched by traditional techniques.
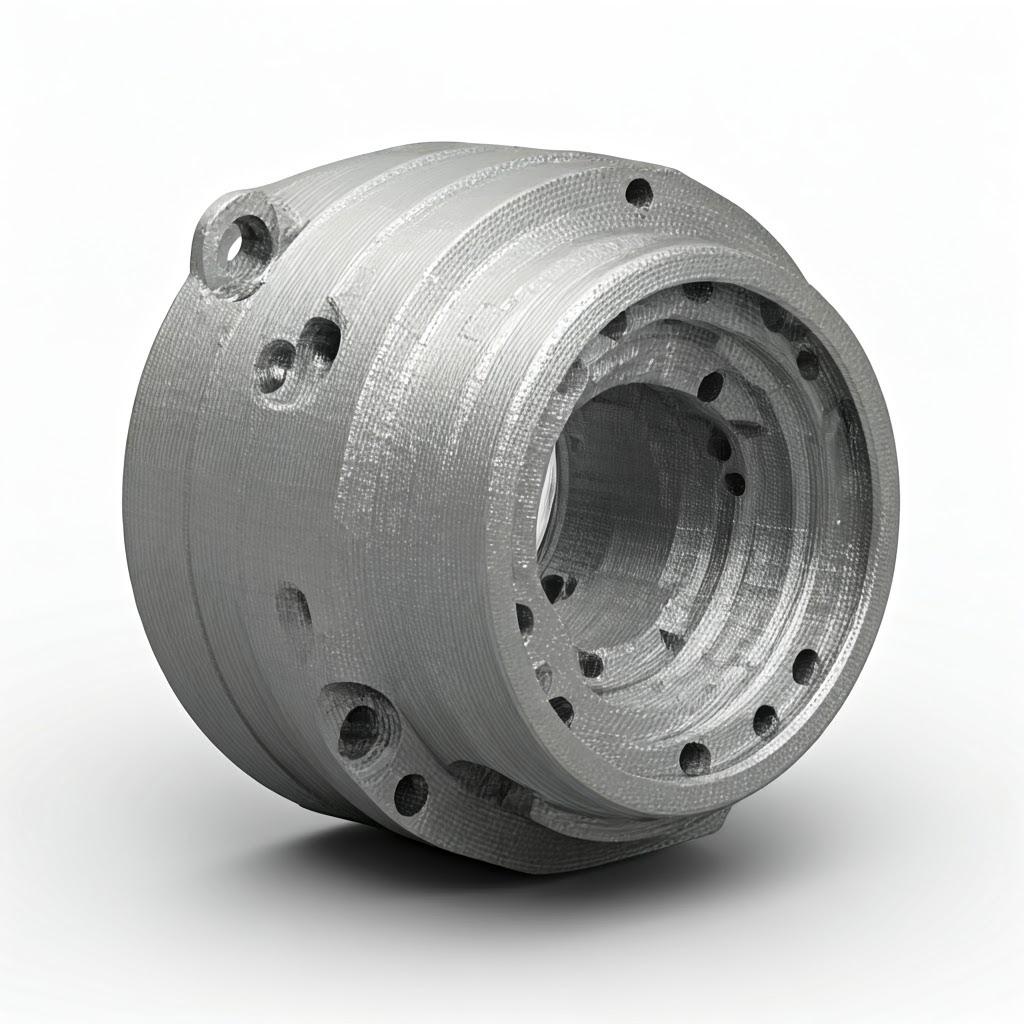
Material Deep Dive: Why Invar (FeNi36) and Ti-6Al-4V for Radar Housings?
The performance of a 3D printed radar housing is fundamentally tied to the material chosen. While various metals can be 3D printed, Invar (FeNi36) and Titanium alloys like Ti-6Al-4V are frequently selected for high-performance radar applications, albeit for different reasons. Understanding their distinct properties is crucial for material selection during the design phase.
Invar (FeNi36): The Champion of Stability
Invar, nominally an alloy of 36% Nickel and 64% Iron, is celebrated for one primary characteristic: its exceptionally low Coefficient of Thermal Expansion (CTE) around room temperature and extending over a moderate temperature range.
- Viktiga egenskaper:
- Ultra-Low CTE: Typically around 1.2 – 2.0 µm/(m·°C) near room temperature. This is roughly an order of magnitude lower than steels and aluminum alloys, and significantly lower than Titanium. This means its dimensions change very little with temperature fluctuations.
- Adequate Strength & Stiffness: While not as strong as high-strength steels or Titanium alloys, Invar possesses sufficient mechanical properties for housing applications where dimensional stability, not extreme load-bearing capacity, is the primary driver.
- Good Machinability (Relatively): Can be post-machined to achieve very tight tolerances if required.
- Magnetiska egenskaper: Invar is ferromagnetic, which may need consideration in applications sensitive to magnetic fields. Shielding might be necessary in some cases.
- Why it Matters for Radar Housings:
- Dimensional Precision: As discussed, maintaining the precise geometry and alignment of radar components (antennas, feeds, reflectors) is critical for signal integrity, beamforming accuracy, and overall system performance. Invar’s stability minimizes thermally induced misalignments.
- Calibration Stability: Systems housed in Invar require less frequent recalibration due to thermal drift, improving operational readiness and reducing maintenance costs.
- Performance in Variable Environments: Essential for aerospace, automotive, and outdoor applications where temperatures can swing significantly.
- Överväganden om 3D-utskrift:
- Printing Invar requires careful parameter control (laser power, scan speed, layer thickness) to manage internal stresses that can arise during the rapid heating and cooling cycles of PBF processes.
- Appropriate heat treatments (stress relief) after printing are often necessary to achieve optimal dimensional stability and mechanical properties.
- Support structures are required during printing and must be carefully designed for effective removal without damaging the part.
Ti-6Al-4V (Grade 5 Titanium): The Lightweight Powerhouse
Ti-6Al-4V (containing ~6% Aluminum, ~4% Vanadium) is the workhorse of the titanium alloys and one of the most common materials in metal AM. It offers a different set of advantages compared to Invar.
- Viktiga egenskaper:
- Högt förhållande mellan styrka och vikt: Ti-6Al-4V offers strength comparable to many steels but at nearly half the density. This makes it exceptionally attractive for weight-sensitive applications.
- Utmärkt korrosionsbeständighet: Forms a stable, passive oxide layer providing outstanding resistance to corrosion in various environments, including saltwater and many industrial chemicals.
- Good High-Temperature Performance: Retains its strength well at moderately elevated temperatures (up to ~300-400°C).
- Biokompatibilitet: Widely used in medical implants (though less relevant for typical radar housings).
- Moderate CTE: Its CTE is around 8.6 µm/(m·°C), significantly higher than Invar but lower than Aluminum alloys and many steels.
- Why it Might Be Chosen for Radar Housings:
- Viktminskning: In aerospace, defense, and potentially automotive applications, minimizing weight is paramount. If the absolute thermal stability of Invar isn’t strictly necessary, Ti-6Al-4V provides significant weight savings.
- Harsh Environments: If the primary challenge is corrosion rather than extreme thermal stability, Titanium’s resistance might be favored.
- Structural Demands: If the housing needs to withstand higher structural loads, Ti-6Al-4V’s superior strength-to-weight ratio can be advantageous.
- Broader Availability & Lower Cost (Relative to Invar): Ti-6Al-4V powder is generally more widely available and often less expensive than specialized Invar powder, although both are premium materials.
- Överväganden om 3D-utskrift:
- Ti-6Al-4V is well-understood in AM processes (SLM, EBM).
- It requires printing in an inert atmosphere (Argon) to prevent oxygen pickup, which can embrittle the material.
- Post-print heat treatments (stress relief, HIP – Hot Isostatic Pressing) are commonly used to optimize microstructure and mechanical properties, reducing residual stress and closing internal porosity.
Material Comparison Summary:
Fastighet | Invar (FeNi36) | Ti-6Al-4V (klass 5) | Typical Use Case Driver for Radar Housing |
---|---|---|---|
Primary Advantage | Ultra-Low CTE | Högt förhållande mellan styrka och vikt | – |
Densitet (g/cm³) | ~8.1 | ~4.43 | Weight Sensitivity (Ti) |
CTE (µm/m·°C @ RT) | ~1.2 – 2.0 | ~8.6 | Thermal Stability (Invar) |
Tensile Strength (Typical) | Moderate (~500 MPa) | High (~950 MPa) | Structural Loads (Ti) |
Motståndskraft mot korrosion | Moderate (Requires protection) | Utmärkt | Corrosive Environment (Ti) |
Relativ kostnad | Hög | High (but often lower than Invar) | Cost (Potentially Ti, application dep.) |
Export to Sheets
Met3dp’s Role in Material Supply:
Choosing the right material is only part of the equation; sourcing high-quality, consistent powder optimized for AM is crucial. Met3dp excels in this area, utilizing industry-leading Gas Atomization and Plasma Rotating Electrode Process (PREP) technologies to produce spherical metal powders with high purity, excellent flowability, and controlled particle size distribution – essential characteristics for achieving dense, reliable parts in PBF systems. Their portfolio includes not only workhorse alloys like Ti-6Al-4V but also specialized materials such as Invar (FeNi36), alongside other advanced options like Nickel superalloys (Inconel), stainless steels, CoCrMo, and even developmental alloys like TiNi and TiTa, demonstrating their broad materials expertise. Partnering with a supplier like Met3dp ensures access to rigorously tested and qualified metallpulver av hög kvalitet suitable for printing demanding components like precision radar housings.
The choice between Invar and Ti-6Al-4V (or potentially other alloys) depends heavily on the specific performance requirements, operating environment, weight constraints, and budget of the radar system. Careful analysis during the design phase, often aided by simulation and consultation with AM experts, is key to selecting the optimal material.
Design for Additive Manufacturing (DfAM) for Optimal Radar Housing Performance
Design for Additive Manufacturing (DfAM) is a crucial methodology that moves beyond simply replicating a design intended for traditional manufacturing. It involves rethinking the component’s geometry to leverage the unique capabilities of AM, optimizing for performance, cost, and manufacturability within the additive process. For precision radar housings, applying DfAM principles is essential to maximize the benefits of using materials like Invar or Ti-6Al-4V.
Key DfAM Principles for Radar Housings:
- Strategic Build Orientation:
- Påverkan: The orientation of the housing on the build plate significantly affects support structure requirements, surface finish on different faces, residual stress accumulation, potential for distortion, and overall build time.
- Considerations for Housings: Critical mating surfaces, sealing faces, or features requiring the highest precision should ideally be oriented upwards or sideways (vertically) to minimize support contact and achieve better surface finish. However, this must be balanced against minimizing build height (which impacts time and cost) and managing thermal stresses. Simulation tools can help predict outcomes for different orientations.
- Optimized Support Structures:
- Necessity: Metal Powder Bed Fusion (PBF) requires support structures for overhangs (typically features angled less than 45° from the horizontal) and to anchor the part to the build plate, managing thermal stresses during printing.
- DfAM Approach: Design parts to be self-supporting where possible by using chamfers or fillets instead of sharp horizontal overhangs. Where supports are unavoidable, design them for easy and clean removal, minimizing witness marks on functional surfaces. Consider accessibility for tools post-print. Lightweight or tree-like supports can save material and print time.
- Feature Size and Resolution:
- Begränsningar: AM processes have minimum achievable feature sizes (e.g., wall thickness, hole diameter, pin size, channel width) dictated by the laser/electron beam spot size, powder particle size, and process parameters.
- Design Rules: Design walls, ribs, and channels above the minimum printable thickness (often ~0.4-0.8 mm, depending on the system and material). Ensure holes are large enough to allow for powder removal after printing. Very small features may require post-machining for accuracy.
- Del Konsolidering:
- Opportunity: AM excels at creating complex, monolithic parts. Analyze existing multi-part housing assemblies (e.g., body, lid, brackets, fasteners) and identify opportunities to redesign them as a single, integrated component.
- Fördelar: Reduces part count, eliminates assembly labor and potential tolerance stack-up issues, minimizes leak paths, and can improve structural integrity.
- Lightweighting Strategies:
- Topology Optimization: Use software to computationally remove material from non-critical areas while maintaining structural performance under defined load cases. This creates highly efficient, often organic-looking structures, ideal for weight saving in Ti-6Al-4V housings.
- Lattice/Gyroid Infill: Replace solid volumes with internal lattice or gyroid structures where appropriate. This drastically reduces weight and material consumption while maintaining significant stiffness and strength. Can also improve vibration damping or thermal performance.
- Integrated Thermal Management:
- Conformal Cooling/Heating Channels: Design channels that precisely follow the contours of heat-generating electronic components or areas requiring temperature stability. This allows for highly efficient fluid-based cooling or heating, far superior to traditional drilled channels. Ensure channels have smooth paths, appropriate diameters for flow, and well-placed inlet/outlet ports.
- Designing for Post-Processing:
- Machining Allowances: If certain surfaces require very tight tolerances or specific finishes achievable only by machining, add extra stock material (machining allowance, e.g., 0.5-1.0 mm) to those features in the CAD model before printing.
- Accessibility: Ensure features that need machining, polishing, or inspection are physically accessible after the part is printed and supports are removed.
- Fixturing Points: Consider adding temporary features or using robust existing features for securely holding the part during post-machining operations.
By applying these DfAM principles, engineers can unlock the full potential of metal AM for radar housings, moving beyond simple replacement towards truly optimized components. Engaging with experienced AM service providers like Met3dp, who offer application development support, can be invaluable. Their team understands the nuances of their advanced printing systems and materials like Invar and Ti-6Al-4V, helping clients translate functional requirements into optimized, printable designs that minimize cost and maximize performance.
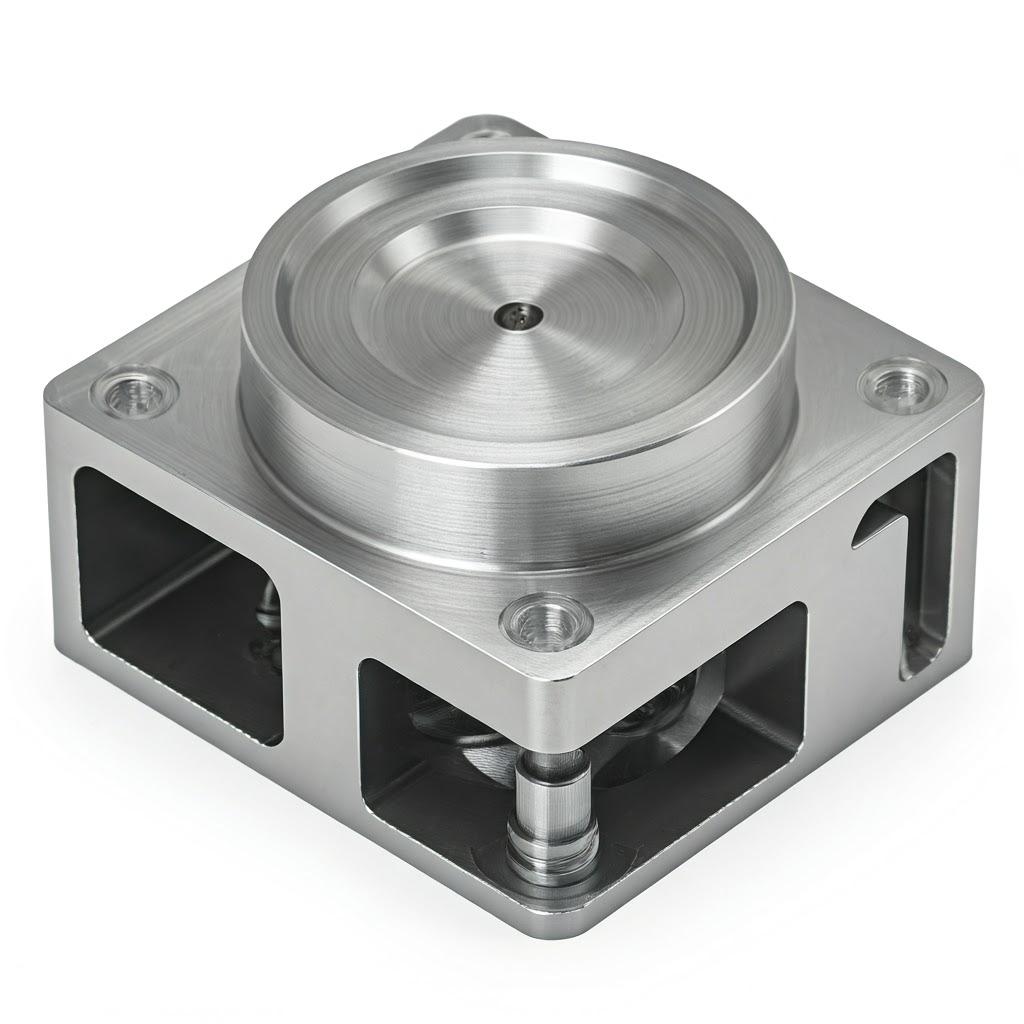
Achieving Precision: Tolerances, Surface Finish, and Accuracy in 3D Printed Housings
A primary reason for selecting metal AM for radar housings, particularly with Invar, is the pursuit of precision and stability. However, it’s crucial for engineers and procurement managers to understand the levels of precision achievable directly from the printing process (“as-printed”) versus what requires subsequent finishing operations.
Dimensional Tolerances:
Metal PBF processes like SLM and EBM can achieve good dimensional tolerances, but they are generally not as tight as high-precision CNC machining directly from the printer.
- Typical As-Printed Tolerances:
- For smaller features (e.g., < 100 mm): Often in the range of ±0.1 mm to ±0.2 mm.
- For larger dimensions: Tolerances may increase proportionally, often cited as ±0.1% to ±0.2% of the nominal dimension.
- These values depend heavily on the specific machine, calibration, material (Invar’s low CTE can be advantageous here), part geometry, orientation, and support strategy.
- Achieving Tighter Tolerances: For critical interfaces, mounting points, sealing surfaces, or features requiring tolerances tighter than ~±0.1 mm, post-print CNC machining is typically required. DfAM principles should incorporate necessary machining allowances on these features.
- Geometric Tolerances (GD&T): Specifying flatness, parallelism, perpendicularity, and position requires careful consideration of the AM process limitations and often necessitates post-machining for critical requirements.
Surface Finish (Roughness):
The as-printed surface finish of metal AM parts is inherently rougher than machined or polished surfaces due to the layer-by-layer fusion of powder particles.
- Typical As-Printed Surface Roughness (Ra):
- Upward-facing surfaces: Generally smoother, potentially 5-15 µm Ra.
- Vertical/Side walls: Moderate roughness, often 7-20 µm Ra. Influenced by layer thickness and contour scan parameters.
- Downward-facing (supported) surfaces: Typically the roughest due to support contact points, potentially 15-30 µm Ra or more, even after support removal.
- Förbättra ytfinishen:
- Orientation: Placing critical surfaces facing upwards or vertically improves the as-printed finish.
- Efterbearbetning: Various methods can significantly improve surface finish:
- Bead Blasting: Provides a uniform matte finish, slightly reducing Ra (e.g., 5-10 µm Ra).
- Tumbling/Vibratory Finishing: Smooths edges and can improve overall surface finish, especially on external surfaces.
- CNC Machining: Can achieve very smooth finishes (Ra < 1.6 µm or better) on specific features.
- Grinding/Polishing: Can achieve mirror-like finishes (Ra < 0.4 µm) for optical or sealing applications.
Dimensionell noggrannhet:
This refers to how closely the final part conforms to the intended dimensions specified in the CAD model. It’s influenced by multiple factors:
- Machine Calibration: Regular calibration of the AM system is essential.
- Process Parameters: Laser/beam power, scan speed, layer thickness, and scan strategy all impact accuracy.
- Thermal Stresses: Heating and cooling cycles induce stresses that can cause slight warping or deviation. Stress relief heat treatment is crucial for mitigating this.
- Materialegenskaper: The material’s thermal conductivity and CTE play a role.
- Part Geometry & Orientation: Complex geometries and suboptimal orientation can exacerbate inaccuracies.
- Pulverkvalitet: Consistent powder characteristics (particle size, flowability) contribute to stable printing.
- Efterbearbetning: Heat treatments can cause minor dimensional changes; machining brings features into final tolerance.
Met3dp’s Commitment to Accuracy:
Achieving consistent accuracy requires rigorous process control. Leading providers like Met3dp emphasize the “industry-leading print volume, accuracy and reliability” of their systems. This is achieved through advanced machine design, precise calibration routines, optimized process parameters developed through extensive testing, use of high-quality, internally produced powders, and robust quality management systems throughout the manufacturing process, including final inspection using tools like Coordinate Measuring Machines (CMMs).
Precision Expectations Summary:
Parameter | As-Printed (Typical PBF) | After Post-Processing (Machining/Polishing) | Key Influencing Factors |
---|---|---|---|
Tolerans | ±0.1 to ±0.2 mm (or ±0.1-0.2%) | < ±0.025 mm (or tighter) | Machine, Material, Geometry, Orientation, Heat Treat |
Surface Finish (Ra) | 5 – 30 µm | < 1.6 µm (Machined), < 0.4 µm (Polished) | Orientation, Supports, Post-Processing Method |
Noggrannhet | Good, but affected by stress | High, corrected by machining | Calibration, Process Control, Stress Relief, Inspection |
Export to Sheets
Engineers must design accordingly, specifying post-processing where needed and collaborating closely with their AM supplier to ensure the final radar housing meets all critical precision requirements.
Post-Processing Pathways for Metal 3D Printed Radar Housings
The journey of a metal 3D printed radar housing doesn’t end when the printer stops. A series of essential post-processing steps are typically required to transform the raw printed part into a functional, finished component meeting all specifications for performance, tolerance, and surface quality. The exact sequence and necessity of these steps depend on the material (Invar vs. Ti-6Al-4V), the application’s requirements, and the complexity of the part.
Typical Post-Processing Workflow:
- Stress Relief Heat Treatment:
- Syfte: To reduce the significant internal stresses built up during the rapid heating and cooling cycles inherent in PBF. This minimizes the risk of distortion or cracking during subsequent steps (like removal from the build plate) and improves long-term dimensional stability.
- Method: Performed in a controlled atmosphere furnace (inert gas like Argon, or vacuum) at specific temperatures and durations tailored to the alloy (e.g., Invar typically requires lower temperatures than Ti-6Al-4V). Often done while the part is still attached to the build plate.
- Criticality: Absolutely essential for dimensionally critical parts like Invar housings.
- Part Removal from Build Plate:
- Syfte: To separate the printed component(s) from the metal base plate they were built upon.
- Metoder: Commonly done using Wire Electrical Discharge Machining (Wire EDM) for a clean cut close to the part base, or sometimes band sawing for less critical applications.
- Borttagning av stödstruktur:
- Syfte: To remove the temporary structures that supported overhangs and anchored the part during printing.
- Metoder: Can range from simple manual break-off for well-designed supports to more involved processes like grinding, milling, or hand-finishing. Accessibility is key (a DfAM consideration). This can be one of the most labor-intensive steps.
- Further Heat Treatments (Optional but Common):
- Het isostatisk pressning (HIP): Combines high temperature and high pressure (using an inert gas like Argon) to close internal porosity (micropores) that might remain after printing. This improves density (approaching 100%), fatigue life, and overall mechanical integrity. Very common for critical aerospace and medical Ti-6Al-4V parts; can also benefit Invar components.
- Solution Annealing / Aging: Specific heat treatment cycles used for certain alloys (especially Titanium) to optimize microstructure and achieve desired mechanical properties (e.g., strength, ductility).
- Ytbehandling:
- Syfte: To achieve the required surface texture, remove contaminants, or prepare for coating.
- Methods (Progressive):
- Initial Cleaning: Grit blasting or bead blasting to remove loose powder and create a uniform matte finish.
- Bulk Deburring/Smoothing: Vibratory finishing or tumbling can smooth edges and slightly improve general surface roughness.
- Targeted Machining: CNC milling or turning to achieve tight tolerances and fine finishes on specific features (mating faces, sealing grooves, mounting holes).
- Manual Grinding/Polishing: For achieving very smooth, mirror-like finishes (Ra < 0.4 µm) if required for optical or specific RF functions.
- Cleaning and Inspection:
- Syfte: Ensure the part is free from contaminants (e.g., machining fluids, debris) and meets all specifications.
- Metoder: Ultrasonic cleaning, thorough visual inspection, dimensional inspection using CMMs or laser scanners, surface roughness measurements. Non-Destructive Testing (NDT) like X-ray or CT scanning may be used for critical parts to verify internal integrity and check for defects or residual powder in internal channels.
- Coating or Plating (If Required):
- Syfte: To add corrosion protection (especially if Invar is used in a corrosive environment), improve wear resistance, provide specific electrical properties (e.g., conductivity), or for cosmetic reasons (e.g., painting).
- Metoder: Anodizing (for Ti), painting, powder coating, electroplating (e.g., nickel, gold), conversion coatings. Surface preparation before coating is critical.
The specific combination and execution of these steps require expertise. Providers like Met3dp, offering heltäckande lösningar, often manage these post-processing supply chains or provide detailed guidance to ensure the final radar housing fully meets the demanding requirements of the application. Understanding these necessary steps helps procurement managers and engineers accurately estimate total costs and lead times.
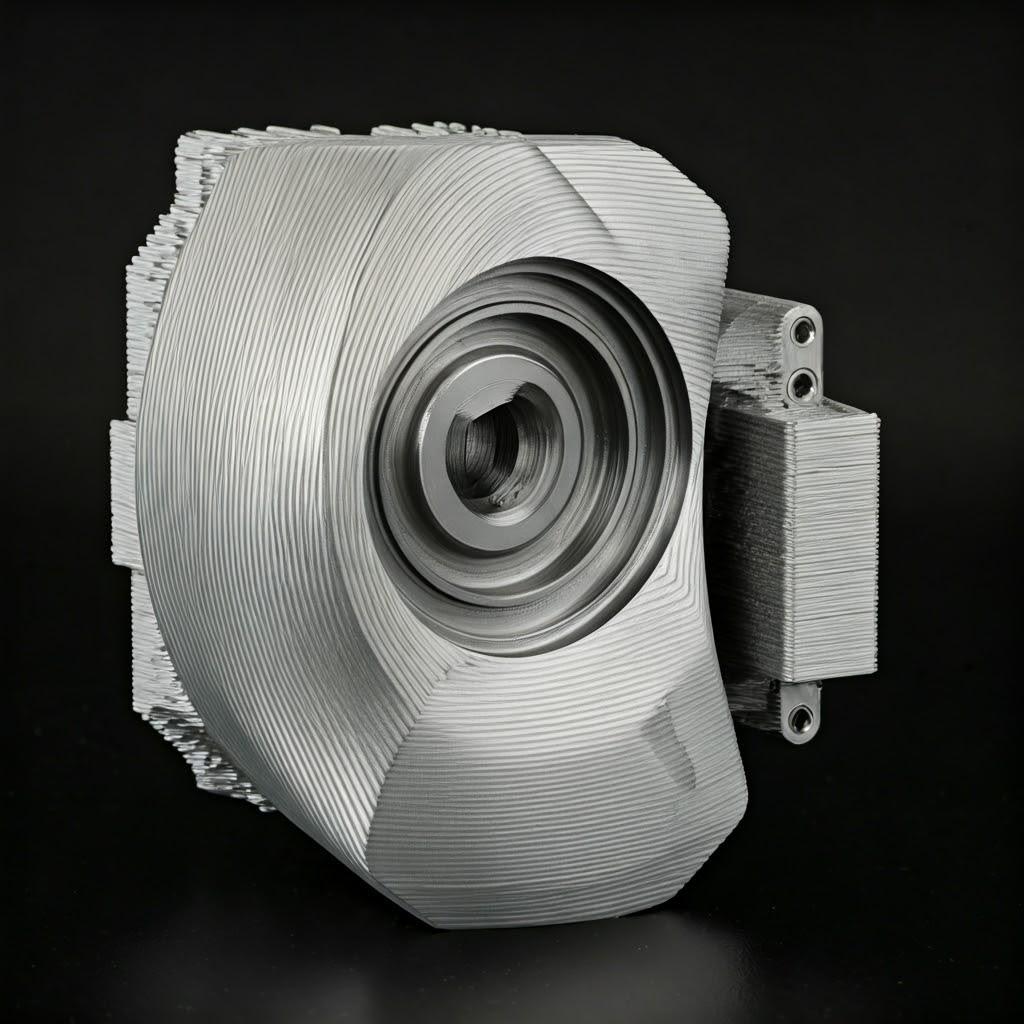
Overcoming Challenges in 3D Printing Precision Instrument Housings
While metal AM offers significant advantages, producing high-precision instrument housings like those for radar systems is not without its challenges. Awareness of these potential issues and collaboration with experienced providers are key to successful implementation.
Common Challenges and Mitigation Strategies:
- Warping and Distortion:
- Cause: Uneven heating and cooling leads to internal stresses that can cause the part to warp during or after printing, especially thin-walled or large structures.
- Mitigation:
- Simulation: Using process simulation software to predict thermal behavior and stress distribution.
- Optimized Orientation: Choosing a build orientation that minimizes large flat areas parallel to the build plate and manages heat accumulation.
- Robust Supports: Designing effective support structures to anchor the part securely and conduct heat away.
- Optimized Parameters: Fine-tuning laser/beam parameters (scan strategy, power, speed) to reduce thermal gradients.
- Prompt Stress Relief: Performing stress relief heat treatment immediately after printing.
- Support Removal Difficulty & Damage:
- Cause: Supports in inaccessible areas, supports fused too strongly to the part, damage caused during manual removal.
- Mitigation:
- DfAM: Designing for self-supporting angles, minimizing overhangs, ensuring access for support removal tools.
- Specialized Supports: Using support structures designed for easier removal (e.g., perforations, specific geometries).
- Careful Removal: Utilizing appropriate tools and techniques (manual, machining) to minimize damage to the part surface. Witness marks may need polishing or machining.
- Internal Porosity:
- Cause: Incomplete melting of powder particles or trapped gas bubbles can lead to small internal voids, potentially affecting density, strength, and fatigue life.
- Mitigation:
- Optimized Print Parameters: Ensuring sufficient energy density for complete melting.
- High-Quality Powder: Using powder with consistent morphology, size distribution, and low gas content (Met3dp’s Gas Atomization/PREP powders excel here).
- Inert Atmosphere: Maintaining a high-purity inert gas environment during printing (especially critical for Ti).
- HIP Post-Processing: Hot Isostatic Pressing is highly effective at closing internal pores.
- Återstående stress:
- Cause: Inherent consequence of the rapid solidification process. Can affect dimensional accuracy and mechanical performance if not managed.
- Mitigation:
- Stress Relief Heat Treatment: The primary method for reducing residual stress.
- Optimized Scan Strategies: Using techniques like island scanning or checkerboard patterns to distribute heat more evenly.
- Process Simulation: Predicting and compensating for stress-induced distortions.
- Achieving Desired Surface Finish and Tolerances:
- Cause: As-printed limitations of the AM process.
- Mitigation:
- Realistic Expectations: Understanding what is achievable as-printed vs. what needs post-processing.
- Strategic Orientation: Placing critical surfaces optimally during build setup.
- Targeted Post-Processing: Incorporating necessary machining, grinding, or polishing steps into the manufacturing plan.
- DfAM: Adding machining allowances where needed.
- Överväganden om kostnader:
- Cause: High machine investment, expensive specialized powders (like Invar), potentially lengthy print times for large/complex parts, required post-processing steps.
- Mitigation:
- DfAM for Efficiency: Optimizing designs to reduce print time and material usage (part consolidation, lightweighting).
- Nesting Parts: Printing multiple parts simultaneously on the build plate to improve machine utilization.
- Materialval: Choosing the most cost-effective material that meets requirements (e.g., Ti-6Al-4V might be sufficient if Invar’s extreme stability isn’t needed).
- Total Cost Perspective: Considering savings from reduced assembly, faster time-to-market, and improved performance against the initial printing cost.
Successfully navigating these challenges requires a combination of smart design, process control, materials science knowledge, and robust post-processing capabilities. Partnering with an experienced metal AM provider like Met3dp, who possesses deep expertise across equipment, materials (including their own advanced powders), and application engineering, significantly increases the likelihood of producing high-quality, reliable precision radar housings efficiently. Their comprehensive approach helps clients anticipate and overcome these hurdles.
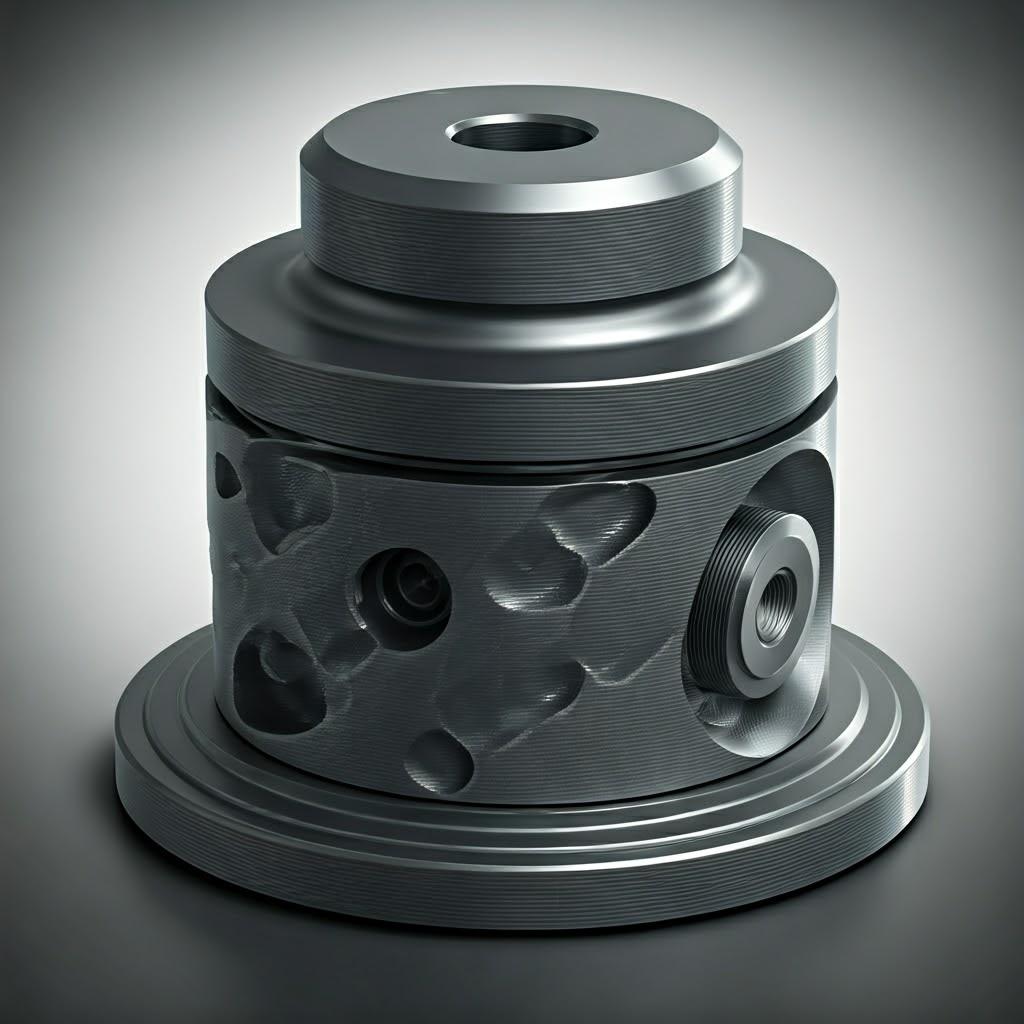
Selecting Your Metal AM Partner: Finding the Right Supplier for Radar Housings
Choosing a metal additive manufacturing service provider is a critical decision that significantly impacts the quality, cost, and delivery time of your precision radar housings. Procurement managers and engineers should evaluate potential partners based on a comprehensive set of criteria beyond just quoted price.
Key Evaluation Criteria for Metal AM Suppliers:
- Technical Expertise and Proven Experience:
- Material Specialization: Does the provider have demonstrable experience printing successfully with the specific alloy required (Invar FeNi36, Ti-6Al-4V)? Ask for case studies or examples, particularly with challenging materials like Invar.
- Fokus på branschen: Experience in demanding sectors like aerospace, defense, or medical indicates familiarity with stringent requirements and quality expectations.
- Engineering Support: Does the provider offer DfAM consultation, simulation services, or application engineering support to help optimize your design for additive manufacturing? This collaborative approach is often invaluable.
- Equipment, Technology, and Processes:
- AM Technology: Do they operate the appropriate PBF technology (SLM, EBM) best suited for your material and part requirements? Met3dp, for instance, specializes in advanced systems including SEBM (Selective Electron Beam Melting) printers, known for producing low-stress parts, particularly beneficial for materials like Titanium.
- Maskinens kapacitet: Assess their printer fleet’s build volume, accuracy, laser/beam power, and monitoring capabilities. Are their machines well-maintained and regularly calibrated?
- Processtyrning: Do they have established, documented procedures for build setup, execution, monitoring, and powder handling?
- Material Quality and Handling:
- Powder Sourcing & Qualification: How do they source, test, and qualify their metal powders? Do they offer material certifications and traceability? Providers like Met3dp, who manufacture their own high-quality spherical powders using advanced Gas Atomization and PREP technologies, offer a distinct advantage in controlling material consistency from the source.
- Powder Management: Proper storage, handling, sieving, and recycling procedures are critical to prevent contamination and ensure consistent part quality.
- Comprehensive Post-Processing Capabilities:
- Integrated Services: Does the provider offer necessary post-processing steps (stress relief, HIP, machining, finishing, inspection) in-house, or do they manage a qualified network of subcontractors? A single point of contact for the entire workflow simplifies project management.
- Expertis: Ensure they (or their partners) have specific expertise in the required post-processing for your chosen material (e.g., vacuum heat treatment for Invar, HIP for Ti-6Al-4V, precision 5-axis machining).
- Quality Management System (QMS) and Certifications:
- Base Certification: ISO 9001 certification is a minimum standard for a reliable supplier.
- Industry-Specific Certifications: Depending on the application, certifications like AS9100 (Aerospace), ISO 13485 (Medical Devices), or IATF 16949 (Automotive) may be required, demonstrating adherence to higher levels of process control, traceability, and risk management.
- Inspection Capabilities: Do they have calibrated CMMs, scanners, surface measurement tools, and potentially NDT capabilities (X-ray, CT) appropriate for verifying your part’s specifications?
- Capacity, Lead Times, and Communication:
- Produktionskapacitet: Can they handle your required volume, from prototypes to potential series production?
- Transparent Quoting: Do they provide clear, detailed quotes outlining costs and estimated lead times for each stage (printing, post-processing, inspection)?
- Project Management & Communication: Look for responsive communication, a dedicated point of contact, and proactive updates throughout the manufacturing process.
Selecting a partner like Met3dp offers significant advantages. Their position as both an equipment manufacturer and a producer of high-performance metal powders, combined with their focus on demanding industries and commitment to providing comprehensive solutions, makes them a highly capable and reliable partner for producing critical components like precision radar housings.
Understanding Cost Drivers and Lead Times for 3D Printed Radar Housings
While metal AM enables incredible technical achievements, it’s essential to have realistic expectations regarding costs and lead times, especially for complex parts made from premium materials like Invar.
Major Cost Drivers:
- Material Type and Volume: This is often the most significant cost factor.
- Kostnad för pulver: Specialized alloys like Invar (FeNi36) are inherently more expensive than more common alloys like Ti-6Al-4V or stainless steels.
- Part Volume: The amount of powder consumed, including support structures, directly impacts cost. DfAM techniques like topology optimization and lattice structures can help reduce material usage.
- Print Time: Determined by:
- Part Height: Taller parts require more layers, significantly increasing print time.
- Part Volume/Density: Larger or denser parts take longer to scan.
- Skiktets tjocklek: Thinner layers improve resolution but increase print time.
- Machine Operating Costs: These high-value machines have significant hourly operating costs.
- Part Complexity and Size: Intricate geometries may require more complex support structures and potentially longer scan times for fine features. Very large parts occupy the machine for extended periods.
- Stödstrukturer: The volume of support material adds to cost (material consumption, print time) and requires labor for removal, which can be substantial for complex internal supports.
- Krav på efterbearbetning: Each step adds cost and time:
- Heat Treatments (Stress Relief, HIP): Require specialized furnaces and long cycle times. HIP is particularly costly but often necessary for critical parts.
- Maskinbearbetning: Setup time, machining time (especially for hard materials or multi-axis work), and programming contribute significantly.
- Ytbehandling: Manual polishing or complex finishing operations can be labor-intensive.
- Quality Assurance and Inspection: Tighter tolerances necessitate more precise (and expensive) machining and inspection methods (e.g., CMM verification, NDT). Documentation requirements also add overhead.
- Order Volume: While AM doesn’t scale like traditional mass production, some cost savings per part may be realized on larger batches due to amortization of setup and programming efforts.
Factors Influencing Lead Times:
- Design Finalization & Preparation: Initial file checks, potential DfAM iterations, build simulation, and nesting parts on the build plate take time.
- Machine Queue: Service providers have finite machine capacity; your job must wait its turn in the queue.
- Tryckning: As noted, this can range from hours to many days.
- Efterbearbetning: This often constitutes the largest portion of the total lead time. Heat treatment cycles are long, machining requires setup and execution, and finishing can be manual. Coordinating external suppliers adds complexity.
- Inspection & Quality Control: Thorough inspection and documentation take time.
- Shipping & Logistics: Transit time to your facility.
Typical Lead Time Range: For a complex metal radar housing, expect lead times anywhere from 1-3 veckor for a relatively simple prototype needing minimal post-processing, up to 6-12 weeks or more for production-quality parts requiring extensive heat treatment (like HIP), multi-axis machining, detailed inspection, and potentially coating.
Engaging with potential suppliers early, providing clear requirements, and being receptive to DfAM suggestions can help optimize both cost and lead time. Experienced providers like Met3dp can provide accurate quotes based on finalized designs and required specifications.
Frequently Asked Questions (FAQ) about 3D Printed Invar Housings
Here are answers to some common questions regarding 3D printed Invar and precision housings:
- How does the performance of 3D printed Invar (FeNi36) compare to traditional wrought Invar?
- With optimized printing parameters and appropriate post-processing, particularly stress relief heat treatment and potentially HIP, the mechanical properties (strength, stiffness) of 3D printed Invar can closely approach those of wrought Invar. Critically, its defining characteristic – the low coefficient of thermal expansion (CTE) – is well-preserved in the AM process, making it excellent for applications demanding dimensional stability. Material testing specific to the application environment is always recommended for validation.
- What is the typical cost difference between printing a housing in Invar versus Ti-6Al-4V?
- Invar powder is generally significantly more expensive per kilogram than Ti-6Al-4V powder. Additionally, Invar’s higher density (~8.1 g/cm³ vs. ~4.4 g/cm³) means more material mass is required for the same volume part. While print parameters and post-processing might differ slightly, the material cost usually makes Invar parts considerably more expensive than identical Ti-6Al-4V parts. However, the cost must be weighed against the performance requirement – if Invar’s unique thermal stability is essential, the higher cost is often justified. Always obtain specific quotes based on your geometry.
- Can complex internal channels or features be reliably cleaned of unfused powder?
- Yes, but it requires careful planning during the design phase (DfAM). Channels need sufficient diameter (typically > 1-2 mm) and strategically placed access ports for powder removal (using vibration, compressed air, or specialized flushing). Designing channels with smooth curves and avoiding sharp corners helps. For critical applications, non-destructive testing methods like X-ray or CT scanning can be used to verify complete powder removal. Experienced AM providers have established protocols for powder removal and cleaning.
- What level of detail is achievable for features like mounting threads or sealing grooves?
- Metal AM can print fine details, including thread-like structures and grooves. However, for optimal performance and strength, threads are typically recommended to be printed slightly undersize and then tapped or thread-milled during post-processing. This ensures a clean, precise thread form. Similarly, sealing grooves often require post-machining to achieve the necessary tight tolerances and smooth surface finish (Ra) for effective sealing. Design these features with machining allowances in mind.
- Is 3D printed Invar suitable for space applications requiring vacuum stability and radiation resistance?
- Yes, 3D printed Invar is increasingly used in space applications for optical benches, satellite structures, and instrument housings where thermal stability is paramount. Key considerations include ensuring high density and minimizing internal porosity (HIP is highly recommended) to reduce outgassing potential in vacuum environments. Material properties under expected radiation levels should also be considered, but Invar generally performs well. As with any space-grade component, rigorous material testing and qualification specific to the mission profile are essential.
Conclusion: Leveraging Metal 3D Printing for Advanced Radar Housing Solutions
The convergence of advanced materials like Invar (FeNi36) and Ti-6Al-4V with the design freedom and precision of metal additive manufacturing represents a significant leap forward for radar technology and other precision instrumentation. As we’ve explored, metal AM enables the creation of radar housings that are not only dimensionally stable or lightweight but also highly optimized for thermal management, structural efficiency, and system integration through complex geometries and part consolidation – capabilities often unattainable with traditional manufacturing methods.
Harnessing these benefits requires a holistic approach, encompassing strategic material selection, dedicated Design for Additive Manufacturing (DfAM) principles, a thorough understanding of achievable tolerances and surface finishes, meticulous post-processing, and careful navigation of potential challenges.
Critically, success hinges on selecting the right manufacturing partner – one with deep technical expertise, robust quality systems, advanced equipment, mastery over materials like Invar, and comprehensive capabilities spanning the entire production workflow. Companies like Met3dp, with their foundation in both cutting-edge AM systems and high-performance powder production, embody the type of partner needed to realize the full potential of this technology for demanding applications. Their commitment to industry-leading accuracy, reliability, and providing comprehensive solutions positions them to help organizations accelerate their adoption of additive manufacturing.
By embracing metal 3D printing, engineers and manufacturers can push the boundaries of radar system performance, enabling next-generation capabilities across aerospace, defense, automotive, and industrial sectors. The path involves careful planning and collaboration, but the rewards – enhanced precision, reduced weight, improved thermal control, and faster innovation cycles – are transforming how critical components are designed and produced.
Ready to explore how metal additive manufacturing can elevate your precision instrument or radar housing project? Contact Met3dp today to discuss your requirements and discover how their expertise and advanced capabilities can power your organization’s additive manufacturing goals and contribute to your digital manufacturing transformation.
Dela på
MET3DP Technology Co, LTD är en ledande leverantör av lösningar för additiv tillverkning med huvudkontor i Qingdao, Kina. Vårt företag är specialiserat på 3D-utskriftsutrustning och högpresterande metallpulver för industriella tillämpningar.
Förfrågan för att få bästa pris och anpassad lösning för ditt företag!
Relaterade artiklar
Om Met3DP
Senaste uppdateringen
Vår produkt
KONTAKTA OSS
Har du några frågor? Skicka oss meddelande nu! Vi kommer att betjäna din begäran med ett helt team efter att ha fått ditt meddelande.
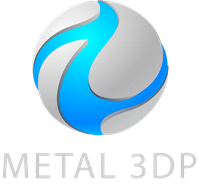
Metallpulver för 3D-printing och additiv tillverkning