Introduktion till HIP-teknik
Innehållsförteckning
Har du någonsin undrat hur till synes solida föremål som turbinblad eller konstgjorda höft hur kan fogar tillverkas med så invecklade detaljer och en sådan anmärkningsvärd styrka? Svaret ligger i en fascinerande teknik som kallas Het isostatisk pressning (HIP). Tänk dig att pressa ett material med ett intensivt tryck från alla håll samtidigt som det utsätts för brännande temperaturer - det är kärnan i HIP. Den här artikeln fördjupar sig i HIP-teknikens fängslande värld och utforskar dess komplikationer, tillämpningar och den fascinerande värld av metallpulver som den utnyttjar.
magin i HIP: En översikt
HIP är en efterbearbetningsteknik som omvandlar metallpulver eller tillverkade delar genom att tillföra extrem värme och enhetlig gas under högt tryck. Denna kraftfulla kombination tjänar flera syften:
- Eliminera interna defekter: Små hålrum eller porer som fångats i materialet pressas ihop av det enorma trycket, vilket resulterar i en tätare och mer robust struktur. Tänk dig en svamp som komprimeras - luftfickorna försvinner och lämnar en mer kompakt och solid form.
- Förbättring av materialegenskaper: Den intensiva värmen främjar atomdiffusion, vilket gör att atomerna kan omorganisera sig och stärka materialets inre bindningar. Tänk på det som att atomerna blir mysiga och håller varandra hårdare i handen.
- Förbättra ytfinishen: Trycket gör att materialet fyller varje skrymsle och vrå i formen, vilket ger en jämnare och mer konsekvent ytfinish. Föreställ dig en perfekt gjuten tårta utan ojämna kanter.
Resultatet? Metallkomponenter med exceptionell styrka, utmattningshållfasthet och måttnoggrannhet, vilket gör dem idealiska för krävande applikationer i olika branscher.
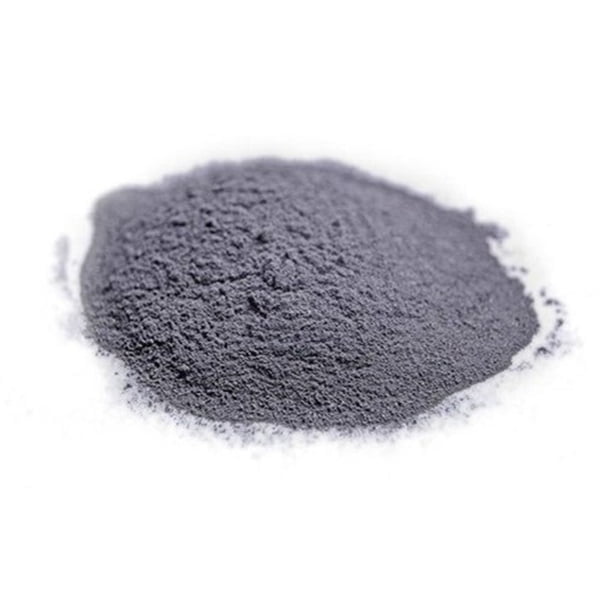
HIP:s byggstenar
Metallpulver är grunden för många HIP-applikationer. Dessa små, granulära partiklar, som vanligtvis är mellan mikrometer och millimeter stora, finns i en mängd olika varianter, var och en med unika egenskaper. Här är en närmare titt på några av de vanligaste metallpulvren i HIP:
- Gasatomerade pulver: Dessa pulver, som framställs genom att smälta metalldroppar snabbt stelnar i en ström av inert gas, har hög renhet, sfäriska former och utmärkta flödesegenskaper. Tänk dig små regndroppar av metall som stelnar till perfekta sfärer.
- Vattenatomerade pulver: Dessa pulver, som skapas genom att smält metall sprutas in i en högtrycksvattenstråle, är i allmänhet billigare men har en mer oregelbunden form jämfört med gasatomiserade varianter. Föreställ dig att smält metall träffar en kraftfull vattenstråle och skapar ett stänk av oregelbundna former.
- Järnpulver: Järnpulver är pulvervärldens arbetshäst och erbjuder en bra balans mellan kostnad, formbarhet och magnetiska egenskaper. De är det självklara valet för ett brett spektrum av applikationer, som kugghjul och maskinkomponenter.
- Pulver av rostfritt stål: Pulvren, som finns i olika kvaliteter, har utmärkt korrosionsbeständighet och används ofta i medicinska implantat, kemisk processutrustning och livsmedelsmaskiner. Föreställ dig en superstark, rostfri byggsten för krävande miljöer.
- Nickelbaserade superlegeringar: Dessa pulver är kända för sin exceptionella hållfasthet vid höga temperaturer och är avgörande för komponenter i jetmotorer, gasturbiner och raketframdrivningssystem. Tänk dig ett material som skrattar när det utsätts för extrem värme.
- Titanpulver: Pulvret är lätt, biokompatibelt och har ett högt förhållande mellan styrka och vikt, vilket gör det perfekt för delar inom flyg- och rymdindustrin, medicinska implantat och sportartiklar. Föreställ dig ett material som är starkt men samtidigt fjäderlätt.
- Aluminiumpulver: Aluminiumpulver har utmärkt formbarhet, ledningsförmåga och korrosionsbeständighet och används i kylflänsar, elektriska komponenter och lättviktskonstruktioner. Föreställ dig en metall som är lätt att forma, leder elektricitet väl och motstår rost.
- Kopparpulver: Kopparpulver är känt för sin höga termiska och elektriska ledningsförmåga och används i kylflänsar, elektriska kontakter och elektroder. Tänk på en metall som är mästare på att leda värme och elektricitet.
- Kobolt-krom-pulver: Dessa pulver är mycket biokompatibla och slitstarka och utgör ryggraden i konstgjorda höftleder, tandimplantat och andra ortopediska tillämpningar. Föreställ dig ett material som är snällt mot din kropp och som står emot slitage.
- Eldfasta metallpulver: Dessa pulver med hög smältpunkt, som volfram och tantal, används i ugnsdelar, raketmunstycken och andra applikationer som kräver extrem värmebeständighet. Föreställ dig ett material som förblir svalt som en gurka även i brännande temperaturer.
Valet av metallpulver för HIP beror på de önskade egenskaperna hos den slutliga komponenten. Det är en balansgång där faktorer som styrka, vikt, korrosionsbeständighet och kostnad måste beaktas.
Vänligen notera: Den här listan visar bara några av de många metallpulver som används i HIP. Med ständiga framsteg inom pulvermetallurgi utvecklas ständigt nya och innovativa material.
Tillämpningar av HIP
HIP-teknikens mångsidighet visar sig i dess olika tillämpningar inom många olika branscher. Här får du en inblick i några av de mest framträdande områdena där HIP gör avtryck:
- Aerospace: Flygindustrins ständiga strävan efter lätta men ändå robusta komponenter gör att HIP passar perfekt. Turbinblad, komponenter till landningsställ och delar till raketmotorer drar alla nytta av HIP:s förmåga att eliminera interna defekter och förbättra mekaniska egenskaper, vilket leder till ökad motoreffektivitet, bränslebesparingar och förbättrade övergripande flygplansprestanda. Föreställ dig en jetmotor där varje komponent är felfritt stark och lätt, vilket gör att planet kan flyga längre och mer effektivt.
- Medicinska implantat: För personer som är beroende av konstgjorda leder eller andra ortopediska implantat spelar HIP en avgörande roll. Tekniken säkerställer att implantaten är fria från inre hålrum, vilket leder till förbättrad livslängd, bättre lastbärande kapacitet och minskad risk för implantatfel. Tänk dig en höftledsprotes som är byggd för att hålla, som ger smärtfri rörelse och sinnesfrid.
- Produktion av energi: HIP förstärker kraftverkens hjärta - turbinblad och skivor. Genom att eliminera inre sprickor och förbättra krypmotståndet (förmågan att motstå deformation under stress vid höga temperaturer) säkerställer HIP att dessa kritiska komponenter fungerar effektivt och tillförlitligt under längre perioder. Föreställ dig ett kraftverk där turbinerna snurrar mjukt och effektivt tack vare den styrka och tillförlitlighet som HIP ger.
- Verktyg och pressgjutning: Tillverkningsindustrin är starkt beroende av slitstarka verktyg och matriser. HIP förstärker dessa verktyg genom att eliminera inre defekter och förbättra slitstyrkan. Detta leder till längre verktygslivslängd, färre underhållsstopp och i slutändan ökad produktivitet. Föreställ dig en fabrik där verktygen håller sig vassa och starka längre, vilket leder till en smidigare och effektivare produktionsprocess.
- Fordonsindustrin: Från lättviktskomponenter för bränsleeffektivitet till höghållfasta delar för prestandabilar, HIP hittar sin plats även inom fordonsindustrin. Motorblock, transmissionskomponenter och till och med komplexa bränsleinsprutare kan dra nytta av HIP:s förmåga att skapa delar som är nära nätformade med exceptionell styrka och måttnoggrannhet. Föreställ dig en bil som är både kraftfull och bränsleeffektiv, delvis tack vare användningen av HIP-teknik.
- Försvar och militära tillämpningar: Militär utrustning kräver exceptionell styrka och tillförlitlighet. HIP används för att skapa komponenter till skjutvapen, pansarfordon och till och med delar till jetmotorer. Här säkerställer tekniken att dessa komponenter kan motstå tuffa miljöer och krävande driftsförhållanden. Föreställ dig ett militärfordon som kan ta sig fram i vilken terräng som helst och klara alla utmaningar, tack vare den orubbliga styrka som HIP ger.
Detta är bara några exempel på hur HIP-tekniken revolutionerar olika branscher. I takt med att forskning och utveckling fortsätter kan vi förvänta oss att se ännu fler innovativa tillämpningar växa fram i framtiden.
de tekniska specifikationerna för HIP Bearbetning
För den som vill fördjupa sig i de tekniska aspekterna av HIP följer här en sammanställning av några viktiga parametrar:
Tabell över parametrar för HIP-bearbetning
Parameter | Beskrivning |
---|---|
Temperatur | Vanligtvis mellan 700°C (1292°F) och 2400°C (4352°F), beroende på material och önskat resultat. |
Tryck | Ligger vanligtvis mellan 100 MPa (14.500 psi) och 300 MPa (43.500 psi), men kan nå ännu högre värden för specifika tillämpningar. |
Hålltid | Den tid under vilken materialet utsätts för hög temperatur och högt tryck. Den varierar beroende på materialtjocklek och önskad nivå av mikrostrukturell modifiering. |
Inert gas | En inert gas, t.ex. argon eller kväve, används för att skapa en tryckmiljö och förhindra oxidation av materialet under bearbetningen. |
Kylningshastighet | Den hastighet med vilken temperaturen sänks efter hålltiden. Detta kan styras för att påverka materialets slutliga mikrostruktur. |
Materialegenskaper som påverkas av HIP
Materialegenskaper | Hur HIP förbättrar den |
---|---|
Täthet | Eliminerar interna hålrum, vilket resulterar i en tätare och mer robust struktur. |
Mekanisk styrka | Förbättrar interatomär bindning, vilket leder till ökad styrka och utmattningshållfasthet. |
Duktilitet | Kan förbättra duktiliteten i vissa material genom att minska inre spänningskoncentrationer. |
Motståndskraft mot korrosion | Kan förbättra korrosionsbeständigheten i vissa material genom att eliminera porositet som kan fungera som vägar för korrosiva ämnen. |
Överväganden om HIP-behandling
HIP erbjuder många fördelar, men vissa faktorer kräver noggrant övervägande:
- Kostnad: De höga temperaturer och tryck som krävs kan göra HIP till en dyrare bearbetningsteknik jämfört med vissa konventionella metoder.
- Materialkompatibilitet: Alla material är inte lämpliga för HIP. Vissa material kan drabbas av oönskad korntillväxt eller andra negativa effekter vid de höga temperaturer som krävs.
- Delgeometri: Komplexa geometrier kan utgöra utmaningar vid HIP-bearbetning, eftersom det kan vara svårt att säkerställa en jämn tryckfördelning genom hela detaljen. Noggranna designöverväganden och processoptimering är avgörande för framgångsrik HIP av invecklade komponenter.
HIP Fördelar och begränsningar
HIP Fördelar Tabell
Fördel | Beskrivning |
---|---|
Eliminerar interna defekter | Stänger porositeten, vilket leder till en tätare och starkare slutprodukt. |
Förbättrar mekaniska egenskaper | Förbättrar hållfasthet, utmattningshållfasthet och dimensionsstabilitet. |
Förbättrar ytfinishen | Säkerställer att materialet formar sig perfekt efter formen, vilket ger en jämnare ytfinish. |
Nätformad tillverkning | Möjliggör skapandet av komplexa komponenter med nära nätform, vilket minimerar behovet av efterbearbetning. |
Bred materialkompatibilitet | Fungerar med ett brett urval av metaller, keramik och kompositer. |
Tabell över HIP-begränsningar
Begränsning | Beskrivning |
---|---|
Kostnad | Kan vara en dyrare bearbetningsmetod jämfört med vissa konventionella tekniker. |
Materialkompatibilitet | Inte lämplig för alla material; vissa kan uppleva negativa effekter vid höga temperaturer. |
Begränsningar för delgeometri | Komplexa geometrier kan vara en utmaning eftersom det är svårt att säkerställa en jämn tryckfördelning. |
Begränsningar i storlek | Stora komponenter kan kräva specialiserad HIP-utrustning. |
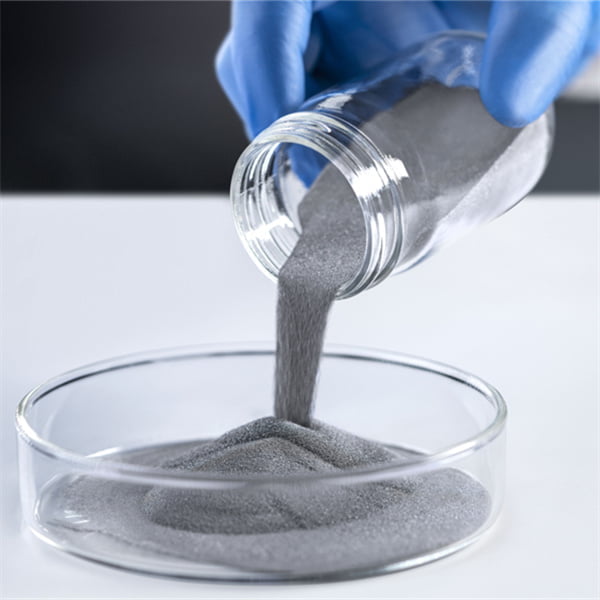
Den framtida utvecklingen av HIP-tekniken
Framtiden för HIP-tekniken är fylld av spännande möjligheter. Här är några viktiga trender att hålla ögonen på:
- Framsteg inom pulvermetallurgi: Utvecklingen av nya och innovativa metallpulver med skräddarsydda egenskaper kommer att fortsätta att flytta fram gränserna för vad som är möjligt att åstadkomma med HIP.
- Lägre kostnad för bearbetning: Forskningsinsatser pågår för att utveckla mer kostnadseffektiva HIP-tekniker, vilket gör tekniken tillgänglig för ett bredare spektrum av tillämpningar.
- Större HIP-enheter: Utvecklingen av större HIP-enheter kommer att göra det möjligt att bearbeta ännu större komponenter, vilket öppnar dörrar för nya tillämpningar inom sektorer som skeppsbyggnad och tunga maskiner.
- Integration med additiv tillverkning: Möjligheten att kombinera HIP med additiv tillverkning (3D-printing) är mycket lovande för att skapa komplexa, högpresterande komponenter med överlägsna egenskaper.
Som HIP tekniken fortsätter att utvecklas kan vi förvänta oss att den kommer att spela en ännu viktigare roll när det gäller att forma framtiden för olika branscher, från flyg och medicin till fordons- och energiproduktion.
VANLIGA FRÅGOR
Fråga | Svar |
---|---|
Vad är skillnaden mellan HIP och Hot Pressing? | Vid varmpressning används endast tryck, medan HIP kombinerar tryck med hög temperatur. |
Kan HIP användas för att reparera delar? | I vissa fall kan HIP användas för att reparera sprickor eller andra defekter i metallkomponenter. |
Vilka är säkerhetsaspekterna för HIP-bearbetning? | HIP-kärl arbetar under högt tryck och hög temperatur, så det är viktigt med lämpliga säkerhetsprotokoll och utbildad personal. |
Hur står sig HIP jämfört med andra konsolideringstekniker för metallpulver? | HIP erbjuder flera fördelar jämfört med andra tekniker som sintring, t.ex. högre densitet och eliminering av inre porositet. |
Var kan jag få mer information om HIP-teknik? | Många resurser finns tillgängliga online och i tekniska bibliotek, inklusive branschpublikationer och forskningsrapporter. |
Genom att fördjupa oss i HIP-teknikens värld upptäcker vi en fascinerande process som omvandlar metallpulver eller tillverkade delar till högpresterande komponenter. Från dess olika tillämpningar inom olika branscher till dess potential för framtida framsteg, står HIP-tekniken som ett bevis på mänsklig uppfinningsrikedom och dess obevekliga strävan efter att skapa starkare, mer tillförlitliga material för en bättre morgondag.
Dela på
MET3DP Technology Co, LTD är en ledande leverantör av lösningar för additiv tillverkning med huvudkontor i Qingdao, Kina. Vårt företag är specialiserat på 3D-utskriftsutrustning och högpresterande metallpulver för industriella tillämpningar.
Förfrågan för att få bästa pris och anpassad lösning för ditt företag!
Relaterade artiklar
Om Met3DP
Senaste uppdateringen
Vår produkt
KONTAKTA OSS
Har du några frågor? Skicka oss meddelande nu! Vi kommer att betjäna din begäran med ett helt team efter att ha fått ditt meddelande.
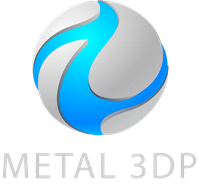
Metallpulver för 3D-printing och additiv tillverkning