3D Printing Lightweight Struts: Revolutionizing Automotive Performance with Metal Additive Manufacturing
Innehållsförteckning
Introduction – The Critical Role of Lightweight Struts in Modern Automotive Design
In the relentless pursuit of enhanced fuel efficiency, improved handling, and reduced emissions, the automotive industry is constantly innovating in material science and manufacturing processes. One critical component in achieving these goals is the automotive strut, a vital part of the suspension system. Traditionally manufactured using conventional methods, struts are now being reimagined through the lens of metal 3D-utskrifter. This advanced manufacturing technique offers unprecedented design freedom and the ability to create lightweight yet high-strength struts tailored for specific vehicle performance requirements. This blog post delves into the transformative potential of 3D-printed lightweight struts, exploring their applications, advantages, material considerations, and how partnering with a trusted supplier like Metall3DP can drive innovation in automotive manufacturing.
What is a Lightweight Automotive Strut Used For? – Enhancing Vehicle Dynamics and Efficiency
The automotive strut is a crucial structural element within the vehicle’s suspension system, primarily responsible for providing structural support and damping oscillations. Functionally, struts integrate the roles of a shock absorber and a spring mounting seat into a single unit. This compact design contributes to efficient packaging and weight reduction compared to traditional separate shock absorber and spring configurations.
Lightweight automotive struts play a pivotal role in several key areas:
- Improved Handling and Ride Comfort: By reducing unsprung mass – the weight of components not supported by the suspension springs, such as wheels, tires, and a portion of the struts – lightweight struts contribute to quicker suspension response. This translates to enhanced road holding, more precise steering, and a more comfortable ride, especially over uneven surfaces.
- Enhanced Fuel Efficiency: Lowering the overall weight of a vehicle is a direct pathway to improved fuel economy and reduced greenhouse gas emissions. Lightweight struts contribute to this overall weight reduction, making vehicles more efficient.
- Increased Performance: In performance vehicles, every kilogram saved translates to faster acceleration, improved braking, and enhanced agility. Lightweight struts, manufactured with optimized designs and materials through metal 3D printing, can significantly contribute to these performance gains.
- NVH (Noise, Vibration, and Harshness) Reduction: Optimized strut designs, achievable through additive manufacturing, can incorporate features that help dampen vibrations and reduce noise transmitted to the vehicle’s cabin, improving the overall driving experience.
- Space Optimization: The integrated nature of a strut, further enhanced by the design flexibility of 3D printing, allows for more compact suspension system designs, freeing up space for other critical components or increasing passenger/cargo area.
These benefits are particularly relevant across various automotive sectors, including:
- Passenger Vehicles: For everyday vehicles, lightweight struts offer a balance of improved fuel efficiency and ride comfort, appealing to a broad consumer base.
- High-Performance Vehicles: In sports cars and racing applications, the focus is on maximizing handling and acceleration, where the weight savings from 3D-printed struts can be a significant advantage.
- Electric Vehicles (EVs): Reducing weight is crucial for EVs to maximize range and efficiency, making lightweight 3D-printed struts an attractive solution.
- Commercial Vehicles: Even in trucks and buses, the benefits of reduced weight can lead to improved payload capacity and fuel economy.
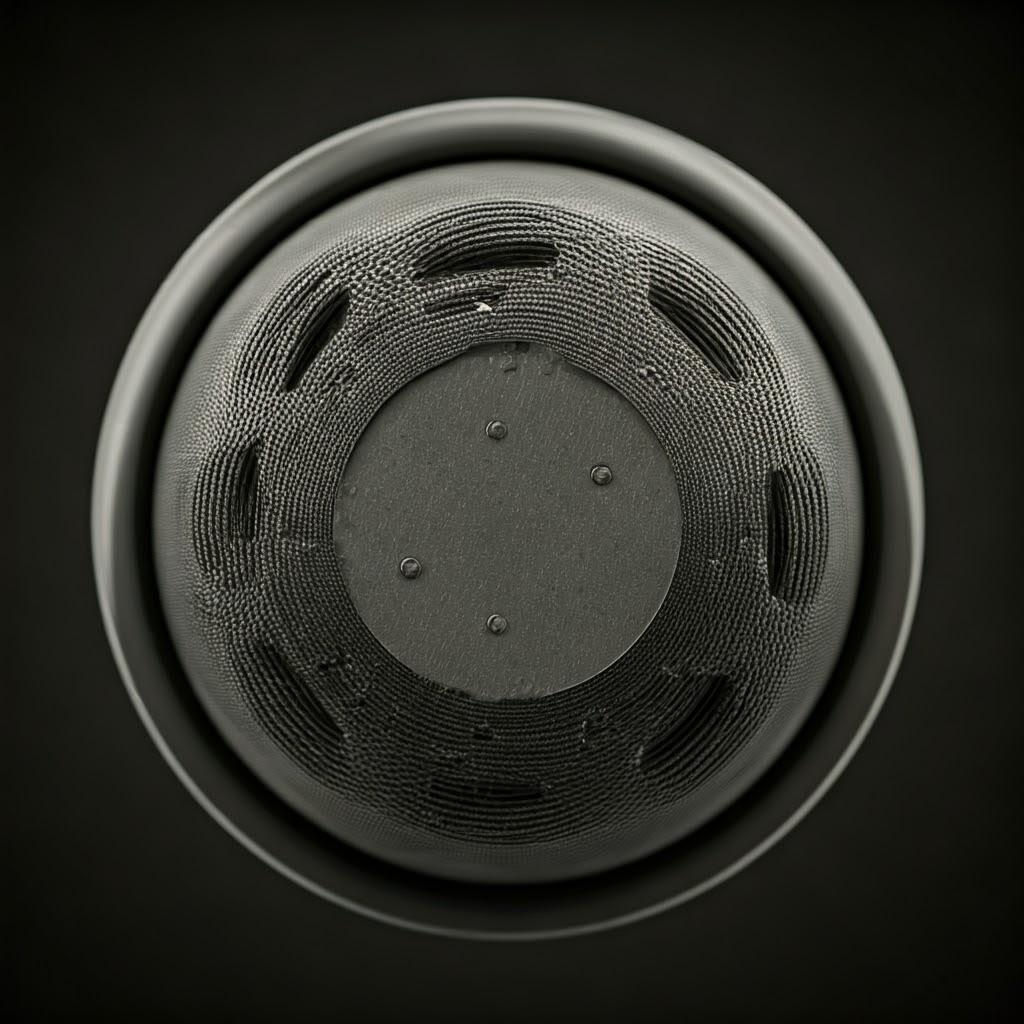
Why Use Metal 3D Printing for Lightweight Struts? – Unleashing Design Freedom and Performance Optimization
Adopting metal 3D printing for the manufacturing of lightweight automotive struts offers a compelling array of advantages over traditional manufacturing methods such as forging, casting, or machining:
- Design Freedom and Topology Optimization: Metal 3D printing, particularly processes like Selective Laser Melting (SLM) and Direct Metal Laser Sintering (DMLS), allows for the creation of complex geometries that are simply not achievable with conventional techniques. This enables engineers to employ topology optimization algorithms, which strategically remove material from low-stress areas while reinforcing high-stress zones. The result is a strut with an optimal strength-to-weight ratio, using only the necessary material.
- Viktminskning: The ability to create intricate internal structures, such as lattices and honeycombs, within the strut body allows for significant weight reduction without compromising structural integrity. These internal features provide stiffness and support while minimizing material usage. Recent advancements in 3D printing of lattice metamaterials have even demonstrated strength levels exceeding conventional aerospace alloys at comparable densities.
- Materialeffektivitet: Additive manufacturing processes are inherently more material-efficient than subtractive methods like machining, where a significant portion of the raw material is removed as waste. 3D printing builds the part layer by layer, using only the material required for the final geometry.
- Customization and Performance Tailoring: 3D printing enables the production of struts with geometries and internal structures tailored to the specific performance requirements of a particular vehicle model or even individual wheel positions. This level of customization allows for fine-tuning the suspension characteristics for optimal handling and ride dynamics.
- Snabb prototypframtagning och iteration: The speed and flexibility of metal 3D printing significantly accelerate the prototyping process. Engineers can quickly design, print, and test different strut designs, allowing for rapid iteration and optimization of the component’s performance before mass production.
- Integration of Features: 3D printing allows for the integration of multiple functionalities into a single part. For example, cooling channels or sensor housings could be directly incorporated into the strut design, reducing the number of components and assembly steps.
- On-Demand Manufacturing and Reduced Tooling Costs: Unlike traditional manufacturing methods that often require expensive tooling (e.g., forging dies or casting molds), 3D printing eliminates or significantly reduces these costs, especially for low to medium production volumes or highly customized parts. This makes it economically viable to produce specialized lightweight struts for niche vehicle markets or aftermarket applications.
Recommended Materials and Why They Matter – AlSi10Mg and A7075 for Optimized Performance
The choice of metal powder is paramount in achieving the desired mechanical properties and lightweight characteristics of 3D-printed automotive struts. Metall3DP offers a range of high-performance metal powders, and for lightweight strut applications, AlSi10Mg och A7075 are particularly well-suited:
1. AlSi10Mg (Aluminum Silicon Magnesium):
- Egenskaper: AlSi10Mg is a widely used aluminum alloy in metal 3D printing due to its excellent combination of properties:
- Högt förhållande mellan styrka och vikt: It offers significant strength while being considerably lighter than steel, contributing directly to the lightweighting goals for automotive struts. Its density is approximately 2.67 g/cm³.
- Good Ductility and Impact Resistance: This ensures the strut can withstand the dynamic loads and impacts experienced during vehicle operation. AlSi10Mg typically exhibits an elongation at break of around 4-10%.
- Utmärkt värmeledningsförmåga: This property can be beneficial for heat dissipation in demanding driving conditions. Its thermal conductivity ranges from 130-150 W/m-K.
- God korrosionsbeständighet: Aluminum alloys naturally form a protective oxide layer, providing good resistance to environmental corrosion, which is crucial for long-lasting automotive components.
- Good Fatigue Strength: Essential for components subjected to cyclic loading, such as suspension struts.
- Weldability and Machinability: Post-processing, if required, is generally straightforward with AlSi10Mg.
- Why it Matters for Lightweight Struts: The high strength-to-weight ratio of AlSi10Mg allows for the creation of lighter struts without sacrificing structural integrity. Its good ductility and fatigue strength ensure durability under the stresses of driving. Furthermore, its thermal conductivity can aid in managing heat generated within the suspension system. Metall3DP provides AlSi10Mg powder specifically optimized for additive manufacturing processes, ensuring high-quality and consistent results.
2. A7075 (Aluminum 7075):
- Egenskaper: A7075 is known as one of the highest-strength aluminum alloys, making it ideal for applications where maximum strength is paramount while still aiming for weight reduction:
- Ultra-High Strength: In the T6 temper, A7075 can achieve ultimate tensile strengths of up to 572 MPa and yield strengths of up to 503 MPa, significantly higher than many other aluminum alloys.
- Excellent Fatigue Resistance: This is critical for the longevity and reliability of suspension components.
- Good Hardness and Wear Resistance: Important for the strut’s mounting points and areas of potential contact. Its Brinell hardness is typically around 150.
- Lättviktare: With a density of approximately 2.81 g/cm³, while slightly denser than AlSi10Mg, it is still considerably lighter than steel.
- Värmebehandlingsbar: Its strength properties are achieved through precise heat treatment processes.
- Why it Matters for Lightweight Struts: For high-performance vehicles or demanding applications where weight savings cannot compromise ultimate strength, A7075 offers an exceptional solution. Its superior strength allows for the design of thinner-walled and more aggressively topology-optimized struts, leading to significant weight reduction while maintaining or even exceeding the structural performance of traditionally manufactured, heavier components. Metall3DP offers high-quality A7075 powder suitable for various metal 3D printing techniques.
By leveraging the unique capabilities of metal 3D printing with materials like AlSi10Mg and A7075, automotive manufacturers can engineer and produce lightweight struts that offer superior performance, improved efficiency, and enhanced vehicle dynamics. Partnering with an experienced provider like Metall3DP ensures access to high-quality powders and the expertise needed to unlock the full potential of metal additive manufacturing for automotive applications.
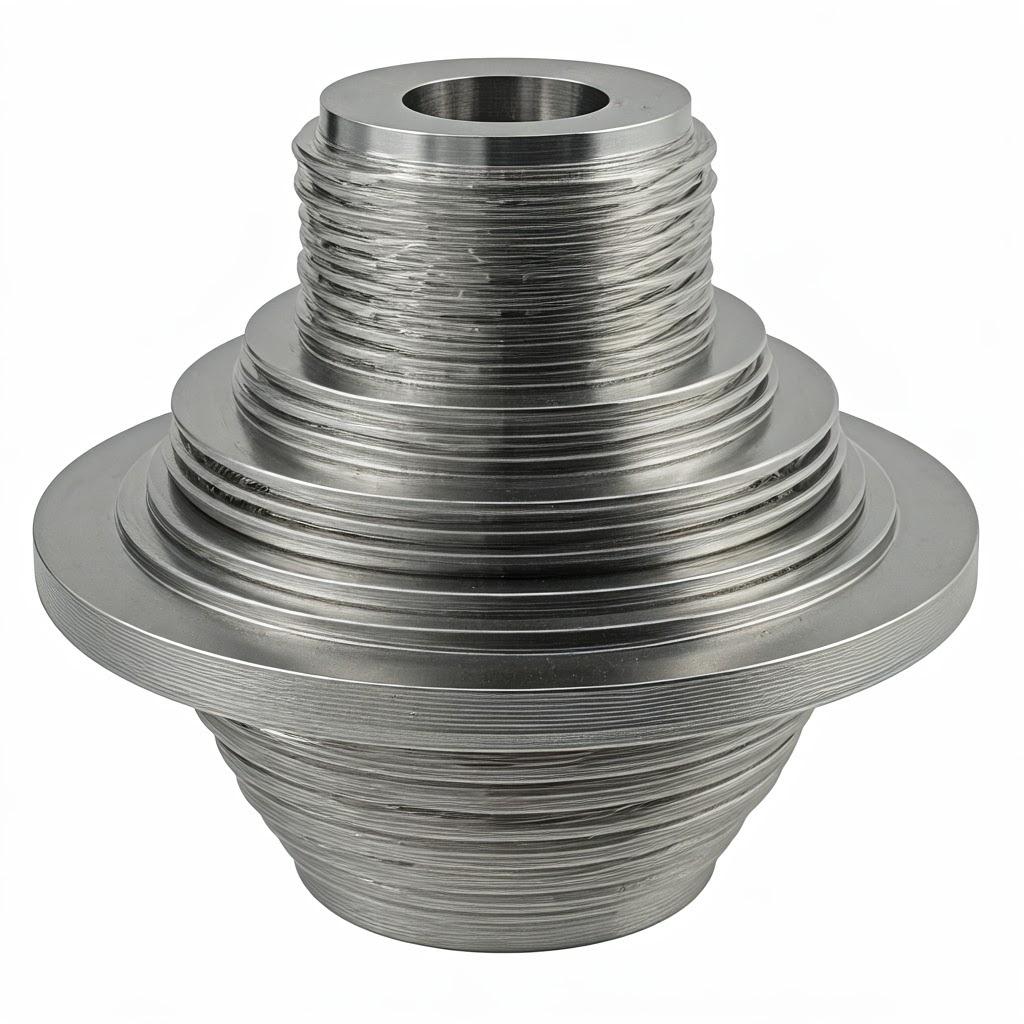
Design Considerations for Additive Manufacturing of Lightweight Struts – Optimizing Geometry for Performance and Printability
Designing lightweight automotive struts for metal 3D printing requires a shift in mindset compared to traditional manufacturing. The unique capabilities and limitations of additive manufacturing processes must be considered from the outset to achieve optimal performance, weight reduction, and manufacturability. Here are key design considerations:
- Topology Optimization: This computational design approach is particularly powerful in AM. By defining the load-bearing requirements and constraints, software algorithms can iteratively remove material from low-stress areas, resulting in an organic, highly efficient geometry that uses the minimum amount of material necessary. This is crucial for achieving significant weight reduction in struts.
- Lattice Structures and Internal Fill Patterns: Instead of solid infill, designers can utilize lattice structures or other internal fill patterns (e.g., gyroid, honeycomb). These structures provide significant stiffness and support while dramatically reducing weight. The density and cell size of the lattice can be tailored to specific load requirements within different sections of the strut.
- Optimering av väggtjocklek: AM allows for the creation of variable wall thicknesses. Highly stressed areas can have thicker walls, while less critical sections can be thinner, further contributing to weight savings. Careful analysis of stress distribution is essential to implement this effectively.
- Support Structure Minimization: Support structures are often required in metal 3D printing to prevent collapse or distortion during the build process, especially for overhanging features. Designing the strut with self-supporting angles (typically 45 degrees or greater) and minimizing overhangs can reduce the need for extensive support structures. This not only saves material but also reduces post-processing time and improves surface finish.
- Orientation Optimization: The orientation of the part on the build platform can significantly impact the need for supports, surface finish, and mechanical properties. Careful consideration of the loading direction and critical surfaces is necessary to choose the optimal build orientation. Simulation tools can help predict the impact of orientation on these factors.
- Feature Integration: AM enables the integration of multiple features into a single component. For example, cooling channels can be designed within the strut body to manage heat, or mounting features can be directly incorporated, reducing the need for separate parts and fasteners, thus saving weight and assembly time.
- Surface Finish Considerations: The layer-by-layer nature of AM can result in a stepped surface finish. The required surface finish for the strut’s functional surfaces (e.g., mounting points, bearing surfaces) should be considered during the design phase. Post-processing methods like machining or polishing might be necessary to achieve the desired smoothness and dimensional accuracy.
- Tolerance and Fit: Designing for the inherent tolerances of the chosen metal 3D printing process is crucial for ensuring proper fit and function within the suspension system. Critical interfaces and mating surfaces should have appropriate clearances or interference fits designed in.
- Design for Assembly (DfA): While AM can reduce the number of assembly steps by integrating features, the design should still consider how the strut will be integrated into the overall suspension system. Easy access for fasteners and proper alignment features should be incorporated.
- Material-Specific Design Rules: Different metal powders have different processing characteristics and achievable geometries in AM. Understanding the design rules specific to AlSi10Mg and A7075 (e.g., minimum feature size, aspect ratios) is essential for successful printing and optimal part performance. Metall3DP can provide valuable insights into material-specific design guidelines for their range of metal powders.
By thoughtfully addressing these design considerations, engineers can fully leverage the potential of metal 3D printing to create lightweight automotive struts with optimized performance, reduced material usage, and efficient manufacturability.
Tolerance, Surface Finish, and Dimensional Accuracy of 3D-Printed Metal Struts – Achieving Precision for Critical Automotive Applications
In the automotive industry, particularly for safety-critical components like suspension struts, tolerance, surface finish, and dimensional accuracy are paramount. Metal 3D printing technologies have advanced significantly in their ability to produce parts with tight tolerances and acceptable surface finishes. However, it’s crucial for engineers and procurement managers to understand the capabilities and limitations of different metal AM processes and how they relate to achieving the required precision for lightweight struts.
- Process Dependence: The achievable tolerance, surface finish, and dimensional accuracy are highly dependent on the specific metal 3D printing process used (e.g., SLM/DMLS, Electron Beam Melting (EBM), Binder Jetting). Powder Bed Fusion (PBF) technologies like SLM/DMLS generally offer the highest accuracy and finest surface finishes among commercially available metal AM processes.
- Typical Tolerances: With optimized parameters and careful process control, SLM/DMLS can achieve dimensional accuracies in the range of ±0.05 to ±0.1 mm for smaller features and ±0.1 to ±0.2 mm for larger dimensions. However, it’s important to note that these are general guidelines, and tighter tolerances might be achievable with post-processing. Factors like part geometry, size, and build orientation also influence achievable tolerances.
- Ytjämnhet: The as-built surface finish in metal 3D printing typically has a higher surface roughness compared to machined surfaces. For SLM/DMLS, the average surface roughness (Ra) can range from 5 to 20 µm, depending on the layer thickness, powder particle size, and build orientation. Surfaces oriented at shallow angles to the build plate tend to have higher roughness due to the “stair-stepping” effect.
- Strategies for Improved Accuracy and Finish: Several strategies can be employed to enhance the tolerance, surface finish, and dimensional accuracy of 3D-printed metal struts:
- Optimized Build Parameters: Fine-tuning parameters such as laser power, scan speed, layer thickness, and powder particle size distribution can significantly impact the final part quality. Metall3DP possesses extensive expertise in optimizing these parameters for their range of metal powders and printing equipment.
- Support Structure Optimization: Minimizing the contact area and optimizing the design of support structures can reduce surface defects and improve the accuracy of supported surfaces.
- Build Orientation Selection: Choosing an orientation that minimizes the number of critical surfaces requiring support and aligns critical dimensions with the build direction can improve accuracy.
- Tekniker för efterbearbetning: For applications requiring tighter tolerances and smoother surface finishes, post-processing steps are often necessary. Common techniques include:
- CNC Machining: Precision machining can be used to achieve tight tolerances on critical features like mounting holes and bearing surfaces.
- Grinding and Polishing: These methods can significantly improve surface finish for enhanced performance or aesthetics.
- Ytbehandlingar: Techniques like shot peening can improve fatigue strength, while coatings can enhance corrosion resistance or wear properties.
- Chemical Etching: Can be used to smooth surfaces and remove partially sintered powder particles.
- Design for Post-Processing: When designing lightweight struts for metal 3D printing, it’s crucial to consider the required tolerances and surface finishes and plan for appropriate post-processing steps if necessary. Designing features that are easily accessible for machining or polishing can streamline the overall manufacturing process.
- Quality Control and Inspection: Robust quality control procedures, including dimensional measurements using Coordinate Measuring Machines (CMMs) and surface roughness testing, are essential to ensure that 3D-printed metal struts meet the required specifications.
By understanding the capabilities of metal 3D printing processes and implementing appropriate design and post-processing strategies, it is possible to achieve the necessary tolerance, surface finish, and dimensional accuracy for lightweight automotive struts used in demanding applications. Collaboration with experienced metal AM service providers like Metall3DP, who have expertise in process optimization and post-processing techniques, is crucial for ensuring the production of high-quality, precise components.
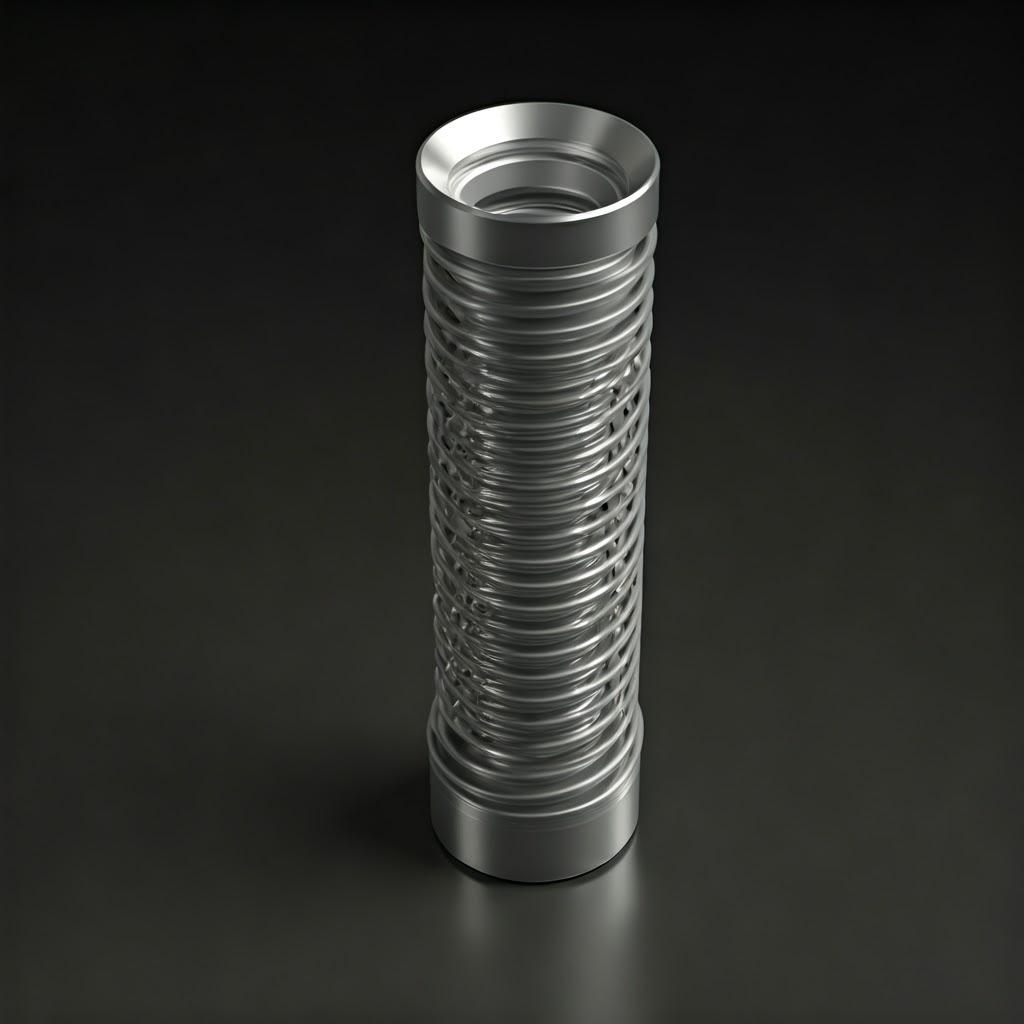
Post-Processing Requirements for 3D-Printed Lightweight Struts – Ensuring Optimal Performance and Finish
While metal 3D printing offers significant advantages in terms of design freedom and material efficiency, post-processing steps are often necessary to achieve the final desired properties, tolerances, and surface finish for lightweight automotive struts. The specific post-processing requirements depend on the application, the chosen metal powder, and the printing process. Here are common post-processing steps:
- Powder Removal: After the printing process, loose or partially sintered powder needs to be carefully removed from the build chamber and the internal channels or cavities of the strut. This is typically done using brushes, vacuums, and compressed air. For complex internal geometries, specialized powder removal techniques might be required.
- Borttagning av stödstruktur: Support structures, which are often necessary to prevent distortion during printing, need to be removed. This can be done manually using cutting tools, pliers, or automated using CNC machining or wire Electrical Discharge Machining (EDM). The design of the supports should aim to minimize the effort and potential for surface damage during removal.
- Stress Relief Heat Treatment: Metal 3D-printed parts often contain residual stresses due to the rapid heating and cooling cycles during the printing process. Stress relief heat treatment is performed to reduce these internal stresses, which can improve dimensional stability and prevent warping or cracking during subsequent processing or service. The specific temperature and duration of the heat treatment depend on the material.
- Het isostatisk pressning (HIP): HIP is a process that applies high pressure and temperature simultaneously to consolidate the material and reduce internal porosity. This can significantly improve the density and mechanical properties (e.g., fatigue strength) of 3D-printed metal struts, especially for critical applications.
- Ytbehandling: As mentioned earlier, the as-built surface finish of 3D-printed metal parts can be rough. Depending on the application requirements, various surface finishing techniques can be employed:
- Media Blasting: Used to remove partially sintered particles and improve surface uniformity.
- Grinding and Polishing: To achieve smoother surface finishes for functional surfaces or aesthetic purposes.
- Vibratory Finishing (Tumbling): Suitable for deburring and achieving a consistent surface texture on complex geometries.
- Chemical Etching: Can smooth surfaces and reveal the material microstructure.
- CNC Machining: For achieving tight tolerances on critical dimensions, such as mounting holes, threads, and bearing surfaces, CNC machining is often employed as a post-processing step. This ensures precise fit and functionality within the suspension system.
- Surface Coatings: Depending on the application environment and performance requirements, surface coatings may be applied to enhance properties like corrosion resistance, wear resistance, or hardness. Common coatings include anodizing (for aluminum), hard chrome plating, or specialized thin-film coatings.
- Icke-förstörande testning (NDT): To ensure the structural integrity of the 3D-printed struts, NDT methods like ultrasonic testing, dye penetrant inspection, or X-ray radiography may be used to detect any internal defects or inconsistencies.
- Quality Control and Inspection: Final dimensional inspection using CMMs and surface roughness measurements are crucial to verify that the post-processed struts meet the required specifications.
The selection and sequence of post-processing steps are critical for achieving the desired performance and quality of 3D-printed lightweight automotive struts. Collaboration with an experienced metal AM service provider like Metall3DP is essential. They possess the knowledge and equipment to perform the necessary post-processing steps effectively and ensure that the final components meet the stringent requirements of the automotive industry. Their comprehensive solutions, spanning from high-quality metal powders to application development services, make them a valuable partner in realizing the benefits of metal additive manufacturing for automotive applications.
Common Challenges and How to Avoid Them in 3D Printing Lightweight Struts – Ensuring Successful Production
While metal 3D printing offers numerous advantages for manufacturing lightweight automotive struts, several challenges can arise during the process. Understanding these potential issues and implementing preventative measures is crucial for achieving successful and high-quality production.
- Warping and Distortion: Thermal stresses induced during the rapid heating and cooling cycles of the printing process can lead to warping or distortion of the strut geometry, particularly for large or complex parts.
- How to Avoid:
- Optimized Build Orientation: Orienting the part to minimize long, unsupported spans and reduce stress concentration can help.
- Support Structure Design: Properly designed support structures can anchor the part and prevent deformation.
- Processparameteroptimering: Fine-tuning laser power, scan speed, and layer thickness can minimize thermal gradients.
- Stress Relief Heat Treatment: As mentioned earlier, post-printing stress relief is essential to mitigate residual stresses.
- Build Plate Adhesion: Ensuring good adhesion to the build plate prevents the part from detaching and warping.
- How to Avoid:
- Support Removal Difficulties and Surface Damage: Aggressively attached or poorly designed support structures can be challenging to remove without damaging the strut’s surface.
- How to Avoid:
- Smart Support Generation: Utilizing software tools to optimize support placement, density, and interface with the part.
- Breakaway Supports: Designing supports with weaker connection points to the part for easier removal.
- Soluble Supports (for some processes): Although less common in metal PBF, soluble supports can be used in binder jetting processes.
- Careful Removal Techniques: Employing the correct tools and techniques for manual or automated support removal.
- How to Avoid:
- Porosity and Density Issues: Insufficient melting or sintering of the metal powder can result in internal porosity, which can compromise the mechanical strength and fatigue life of the strut.
- How to Avoid:
- Optimized Process Parameters: Ensuring appropriate laser power, scan speed, and powder bed temperature for complete melting/sintering.
- High-Quality Powder: Using metal powders with consistent particle size distribution and flowability, such as those offered by Metall3DP.
- Inert Atmosphere Control: Maintaining a pure inert gas environment during printing to prevent oxidation and ensure proper metallurgical bonding.
- Het isostatisk pressning (HIP): Post-processing with HIP can effectively eliminate internal porosity and increase density.
- How to Avoid:
- Surface Roughness Exceeding Requirements: The inherent layer-by-layer build process can result in a surface finish that is too rough for certain functional requirements.
- How to Avoid:
- Smaller Layer Thickness: Using thinner layers can improve surface finish but may increase build time.
- Optimized Scan Strategies: Employing contour scans and other techniques to refine the outer surface.
- Efterbearbetning: Implementing appropriate surface finishing techniques like media blasting, grinding, polishing, or chemical etching.
- How to Avoid:
- Dimensional Inaccuracy and Tolerance Issues: Achieving tight tolerances can be challenging due to factors like thermal expansion/contraction and process variability.
- How to Avoid:
- Process Calibration and Control: Regularly calibrating the 3D printer and maintaining strict process control.
- Material Property Compensation: Accounting for material shrinkage during solidification in the design phase.
- Build Orientation Optimization: Choosing orientations that minimize the impact of thermal gradients on critical dimensions.
- Post-Processing Machining: Using CNC machining for critical features requiring tight tolerances.
- How to Avoid:
- Material Selection Incompatibility: Choosing a metal powder that is not well-suited for the application’s loading conditions or environmental factors can lead to premature failure.
- How to Avoid:
- Thorough Material Selection Process: Carefully evaluating the mechanical properties, corrosion resistance, and other relevant characteristics of potential materials like AlSi10Mg and A7075 based on the application requirements.
- Expert Consultation: Consulting with material scientists and additive manufacturing specialists, such as those at Metall3DP, to select the optimal powder for the application.
- How to Avoid:
- Cost Management: Metal 3D printing can be more expensive than traditional manufacturing methods for high volumes.
- How to Avoid:
- Design Optimization for AM: Designing parts specifically for additive manufacturing to reduce material usage and build time.
- Strategic Material Selection: Choosing cost-effective materials that still meet performance requirements.
- Processoptimering: Streamlining the printing and post-processing workflows to minimize costs.
- Volume Considerations: Evaluating the cost-effectiveness of AM versus traditional methods based on production volume.
- How to Avoid:
By proactively addressing these potential challenges through careful design, optimized process parameters, appropriate material selection, and effective post-processing, manufacturers can successfully leverage metal 3D printing to produce high-performance lightweight automotive struts. Partnering with a knowledgeable and experienced provider like Metall3DP can provide valuable guidance and support in navigating these complexities.
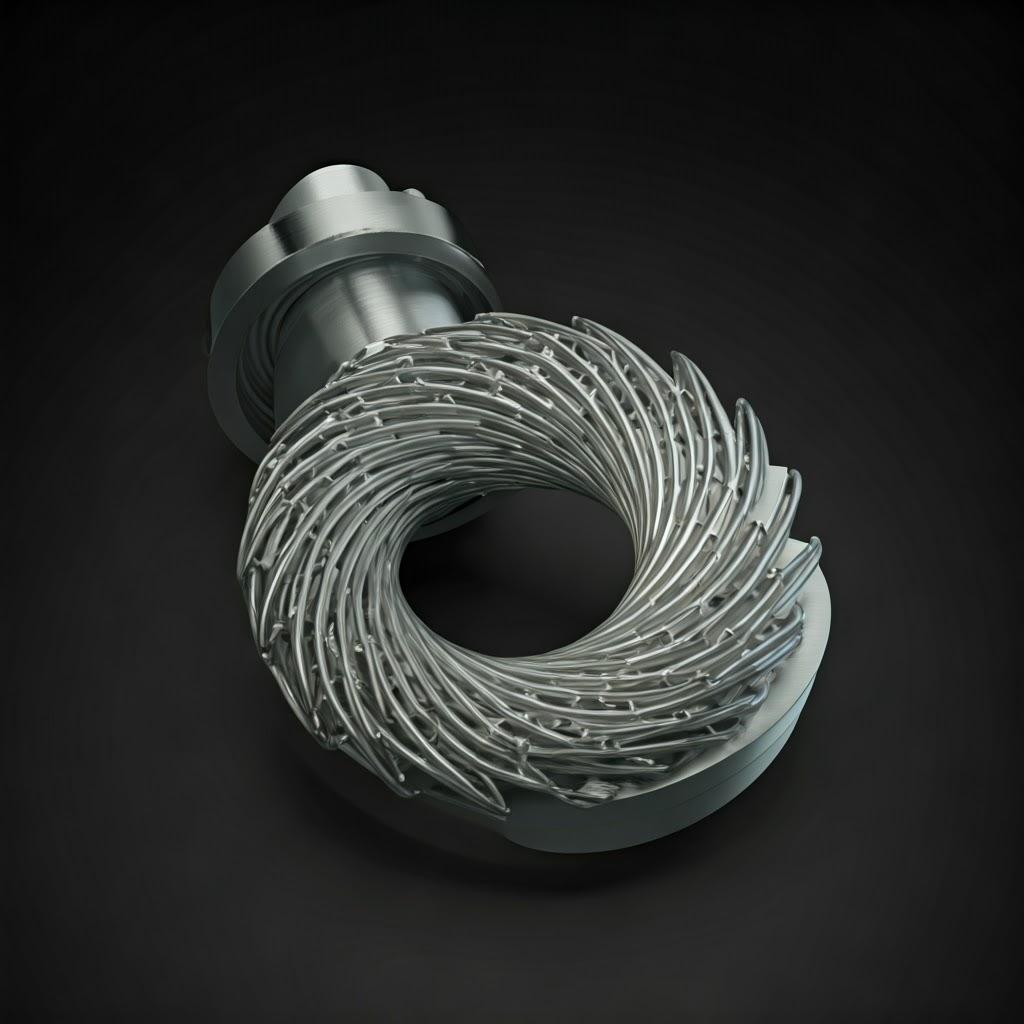
How to Choose the Right Metal 3D Printing Service Provider for Lightweight Struts – Key Considerations for Selection
Selecting the right metal 3D printing service provider is crucial for ensuring the successful production of high-quality, lightweight automotive struts that meet stringent performance and regulatory requirements. Here are key factors to consider when evaluating potential suppliers:
- Material Capabilities: Ensure the provider has experience working with the recommended metal powders for lightweight struts, such as AlSi10Mg and A7075. Verify their expertise in processing these materials to achieve the desired mechanical properties and density. Inquire about their material characterization and testing capabilities.
- Printing Technology and Equipment: Understand the types of metal 3D printing technologies the provider utilizes (e.g., SLM/DMLS, EBM). Different technologies offer varying levels of accuracy, surface finish, and build volume. Ensure their equipment is well-maintained and capable of producing parts with the required size and complexity. Metall3DP offers a range of advanced SEBM printers known for their accuracy and reliability.
- Design Optimization Expertise: A good service provider should offer design consultation services to help optimize the strut design for additive manufacturing. This includes guidance on topology optimization, lattice structure implementation, support structure design, and orientation for optimal printability and performance.
- Post-Processing Capabilities: Determine if the provider offers the necessary post-processing services in-house or has trusted partners. This includes powder removal, support removal, stress relief heat treatment, HIP, surface finishing (machining, polishing, coating), and non-destructive testing. A comprehensive suite of post-processing capabilities streamlines the production process and ensures quality.
- Quality Assurance and Certifications: Inquire about the provider’s quality management system and relevant certifications (e.g., ISO 9001, AS9100 for aerospace). Robust quality control procedures, including dimensional inspection and material testing, are essential for ensuring the reliability and safety of automotive components.
- Experience in the Automotive Industry: Prior experience working with automotive clients and understanding the specific demands of the industry (e.g., material traceability, regulatory compliance) is a significant advantage. Ask for case studies or references from automotive projects.
- Lead Times and Production Capacity: Discuss the provider’s typical lead times for similar projects and their production capacity to meet your volume requirements, whether for prototyping or serial production.
- Cost Structure and Transparency: Obtain a clear and detailed breakdown of the pricing, including printing costs, material costs, design fees, and post-processing charges. Understand the factors that influence the cost and ensure transparency in their pricing 1 model. 1. ominfowave.com ominfowave.com
- Communication and Collaboration: Effective communication and a collaborative approach are crucial for a successful partnership. The provider should be responsive, proactive in addressing concerns, and willing to work closely with your engineering team.
- Location and Logistics: Consider the provider’s location and its impact on shipping times and logistics, especially for serial production. Metall3DP, headquartered in Qingdao, China, offers international shipping and support.
- Confidentiality and Intellectual Property Protection: Ensure the provider has robust policies and agreements in place to protect your intellectual property and maintain the confidentiality of your designs.
By carefully evaluating potential metal 3D printing service providers based on these criteria, automotive manufacturers can select a partner that aligns with their specific needs and ensures the successful production of high-performance, lightweight struts. Metall3DP stands out as a leading provider with comprehensive capabilities in metal AM equipment, high-quality powders, and application development services, making them a strong contender for automotive applications.
Cost Factors and Lead Time for 3D-Printed Lightweight Struts – Understanding the Economics of Additive Manufacturing
Understanding the cost factors and lead times associated with 3D-printed lightweight automotive struts is essential for making informed decisions about adopting this advanced manufacturing technology. While the initial perception might be of high costs, a nuanced analysis reveals the economic viability for specific applications and production volumes.
Kostnadsfaktorer:
- Kostnader för material: The cost of the metal powder (e.g., AlSi10Mg, A7075) is a significant factor. Specialty alloys and smaller batch orders tend to have higher per-kilogram costs. Metall3DP manufactures its own high-quality metal powders, potentially offering cost advantages.
- Utskriftstid: The build time depends on the part’s size, complexity, and the chosen layer thickness. Longer print times translate to higher machine operational costs (energy consumption, maintenance) and potentially higher per-part costs, especially for machine hourly rates.
- Machine Depreciation and Operational Costs: The cost of the metal 3D printer itself, along with its maintenance, calibration, and energy consumption, contributes to the overall cost per part.
- Support Material and Removal: The volume and complexity of support structures influence material usage and the labor or time required for removal. Optimized designs can minimize these costs.
- Kostnader för efterbearbetning: The extent of post-processing required (e.g., heat treatment, HIP, machining, polishing, coating) significantly impacts the final cost. Parts requiring extensive post-processing will be more expensive.
- Design and Engineering Costs: Initial design optimization for additive manufacturing and any subsequent design iterations can incur engineering costs. However, these upfront costs can lead to long-term savings through material efficiency and improved performance.
- Quality Control and Inspection Costs: Thorough quality checks, including dimensional measurements and material testing, add to the overall cost but are crucial for ensuring the reliability of automotive components.
- Produktionsvolym: The cost per part in additive manufacturing often decreases with increasing production volume due to economies of scale in material procurement and process optimization. However, for very high volumes, traditional manufacturing methods might still be more cost-effective.
Lead Time Factors:
- Design and Optimization: The initial design phase, including topology optimization and design for AM, can take time depending on the complexity of the strut and the level of customization.
- Material Procurement: Lead times for acquiring the specific metal powder can vary depending on availability and supplier lead times. Working with a provider like Metall3DP that manufactures its own powders can potentially reduce material lead times.
- Utskriftstid: As mentioned earlier, the build duration is a direct contributor to the lead time.
- Post-Processing Time: The time required for each post-processing step (e.g., heat treatment cycles, machining time, coating application) adds to the overall lead time.
- Quality Control and Inspection: Thorough inspection processes can also contribute to the lead time.
- Scheduling and Capacity: The service provider’s current workload and machine availability will influence the lead time.
Economic Considerations:
While the per-part cost of 3D-printed struts might be higher than traditionally manufactured struts for very high volumes, additive manufacturing offers economic advantages in several scenarios:
- Low to Medium Volume Production: For smaller production runs or niche vehicle models, the absence of tooling costs in AM can make it more cost-effective.
- Complex Geometries and Customization: The ability to create highly optimized and customized strut designs without significant cost penalties can lead to performance advantages that justify the cost.
- Lightweighting Benefits: The fuel efficiency gains and performance enhancements resulting from lightweight 3D-printed struts can lead to long-term cost savings.
- Rapid Prototyping and Reduced Time-to-Market: The speed of AM in producing prototypes accelerates the development cycle, potentially leading to faster time-to-market and a competitive edge.
- On-Demand Manufacturing and Reduced Inventory: AM allows for the production of parts only when needed, reducing the need for large inventories and associated costs.
By carefully analyzing the cost factors and lead times in the context of the specific application requirements and production volume, automotive manufacturers can make strategic decisions about when and how to leverage the benefits of 3D-printed lightweight struts. Engaging with experienced service providers like Metall3DP can provide valuable insights into cost optimization and realistic lead times for specific projects.
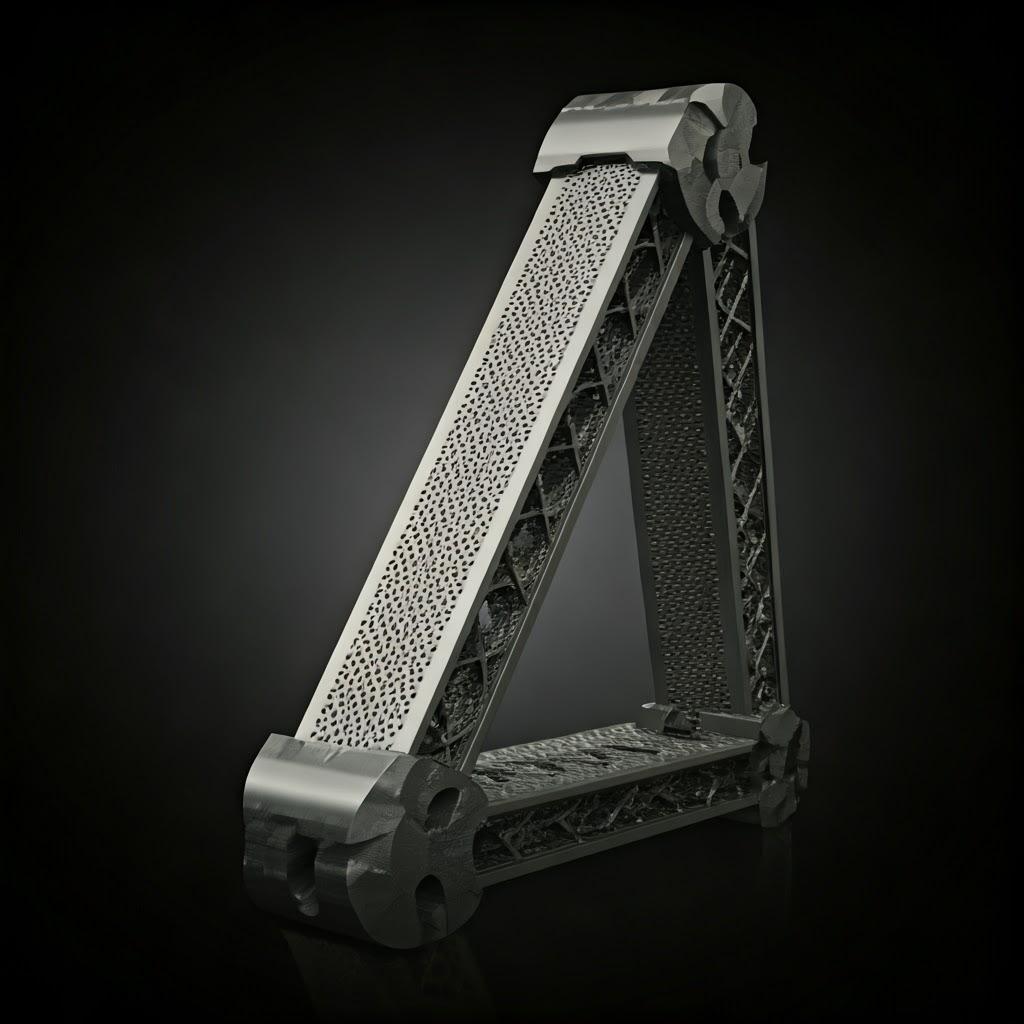
Vanliga frågor och svar (FAQ)
- Q: Can 3D-printed metal struts meet the strength and durability requirements of automotive applications?
- A: Yes, when the appropriate metal powder (e.g., AlSi10Mg, A7075) is used and the printing process is optimized, 3D-printed metal struts can achieve mechanical properties comparable to or even exceeding those of traditionally manufactured parts. Post-processing techniques like HIP can further enhance density and strength. Rigorous testing and validation are essential to ensure they meet automotive safety and performance standards.
- Q: What is the typical weight reduction achievable with 3D-printed struts compared to traditional ones?
- A: The weight reduction achievable depends heavily on the design optimization and the specific application. However, through topology optimization and the use of lattice structures, weight reductions of 20-50% or more are often possible without compromising structural integrity.
- Q: Are 3D-printed metal struts cost-effective for mass production in the automotive industry?
- A: While the per-part cost of 3D-printed metal parts can be higher for very high volumes compared to traditional methods, it can be cost-effective for low to medium volumes, complex geometries, and customized parts. The benefits of lightweighting, rapid prototyping, and on-demand manufacturing can also contribute to overall cost savings. As the technology matures and production volumes increase, the cost-effectiveness for mass production is expected to improve.
Conclusion – Driving Automotive Innovation with Lightweight Metal 3D-Printed Struts
The advent of metal 3D printing has opened up exciting new possibilities for the design and manufacturing of lightweight automotive struts. The ability to create complex, topology-optimized geometries using high-performance materials like AlSi10Mg and A7075 offers significant advantages in terms of weight reduction, performance enhancement, and design flexibility. While challenges exist in terms of achieving tight tolerances and managing costs for very high volumes, the benefits of rapid prototyping, customization, and material efficiency make metal AM a compelling solution for various automotive applications, particularly in performance vehicles, electric vehicles, and niche markets.
Partnering with a leading provider like Metall3DP, with their expertise in advanced metal powders, cutting-edge printing equipment, and comprehensive application development services, is crucial for automotive manufacturers looking to harness the transformative potential of metal additive manufacturing. By embracing this innovative technology, the automotive industry can continue to push the boundaries of vehicle performance, efficiency, and sustainability, paving the way for the next generation of automotive design and manufacturing. Contact Metall3DP today to explore how their capabilities can power your organization’s additive manufacturing goals in the automotive sector.
Dela på
MET3DP Technology Co, LTD är en ledande leverantör av lösningar för additiv tillverkning med huvudkontor i Qingdao, Kina. Vårt företag är specialiserat på 3D-utskriftsutrustning och högpresterande metallpulver för industriella tillämpningar.
Förfrågan för att få bästa pris och anpassad lösning för ditt företag!
Relaterade artiklar
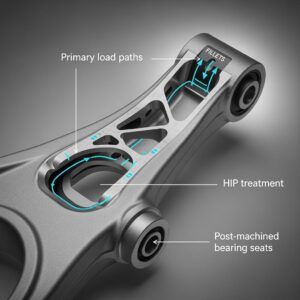
Metal 3D Printing for U.S. Automotive Lightweight Structural Brackets and Suspension Components
Läs mer "Om Met3DP
Senaste uppdateringen
Vår produkt
KONTAKTA OSS
Har du några frågor? Skicka oss meddelande nu! Vi kommer att betjäna din begäran med ett helt team efter att ha fått ditt meddelande.