Lightweight Manifold Adapters via Metal AM
Innehållsförteckning
In the relentless pursuit of automotive performance, efficiency, and innovation, engineers constantly seek solutions that push the boundaries of design and manufacturing. One often overlooked yet critical component is the manifold adapter. These seemingly simple parts play a crucial role in optimizing engine airflow, enabling custom configurations, and ensuring seamless integration of performance upgrades. Traditionally crafted through casting or machining, the production of custom or low-volume manifold adapters often faces limitations in design complexity, tooling costs, and lead times. However, the advent of Metal Additive Manufacturing (Metal AM), specifically powder bed fusion technologies, is revolutionizing how these components are designed and produced, offering unprecedented opportunities for lightweighting, performance enhancement, and customization. This article delves into the world of metal 3D-utskriven automotive manifold adapters, exploring their applications, the compelling advantages of using AM, recommended materials like AlSi10Mg and A7075, and key considerations for engineers and procurement managers in the automotive, motorsport, and performance aftermarket sectors.
Introduction to Automotive Manifold Adapters: Performance Meets Precision
An automotive manifold adapter serves as a critical interface within an engine’s intake or exhaust system. Its primary function is to bridge the gap between components that were not originally designed to mate directly. Think of it as a specialized connector ensuring airtight and flow-efficient transitions.
- Intake System Adapters: These are commonly used to mount a different style or size of throttle body, adapt an aftermarket intake manifold to a specific cylinder head, or reposition components for better packaging or performance. For instance, adapting a larger throttle body requires an adapter that smoothly transitions the airflow from the new throttle body diameter to the intake manifold plenum entrance.
- Exhaust System Adapters: These might be used to connect aftermarket headers or turbochargers to the engine’s cylinder head or to adapt different flange types within an exhaust system. Ensuring a leak-free seal and maintaining exhaust gas velocity are paramount here.
The importance of these adapters extends far beyond simple connection:
- Prestanda: Properly designed adapters ensure smooth airflow or exhaust gas flow, minimizing turbulence and pressure drops. Poorly designed adapters can create restrictions, hindering engine breathing and robbing power. In forced induction applications (turbocharged or supercharged), the adapter’s design is critical for efficient delivery of pressurized air.
- Effektivitet: By enabling optimized airflow and component matching, adapters contribute to more complete combustion and overall engine efficiency, potentially improving fuel economy.
- Utsläpp: Ensuring leak-free connections in both intake and exhaust systems is vital for emissions control. Intake leaks can lead to lean running conditions, while exhaust leaks can disrupt oxygen sensor readings and allow harmful gases to escape before catalytic conversion.
- Packaging and Customization: In engine swaps or highly modified vehicles, space is often at a premium. Custom adapters allow engineers to relocate components, fit larger turbos, or integrate sensors in specific locations, enabling complex custom builds that would otherwise be impossible.
The modern automotive industry, driven by stringent emissions regulations, consumer demand for performance, and the shift towards electrification and complex powertrain configurations, increasingly requires components that are both highly complex and lightweight. Manifold adapters are no exception. Traditional manufacturing methods often struggle to produce the intricate internal geometries needed for optimal flow or the thin-walled, organically shaped structures desired for weight reduction without significant cost or time penalties. This is precisely where 3D-utskrift av metall emerges as a transformative technology.
Applications and Use Cases for Custom Manifold Adapters
The versatility of custom manifold adapters makes them indispensable in various automotive contexts, particularly where off-the-shelf solutions fall short. Metal AM allows for the cost-effective production of these specialized parts, even in single units or small batches.
Key Use Cases:
- Turbocharger Adaptation:
- Flange Conversion: Connecting a turbocharger with a T3 flange to an engine manifold designed for a T4 flange, or vice-versa. AM allows for smooth, blended transitions internally to maintain flow velocity.
- Relocation: Creating adapters that reposition the turbocharger for better clearance, heat management, or shorter charge piping routes.
- Twin-Scroll Conversions: Designing adapters that correctly divide exhaust pulses for optimal twin-scroll turbo performance on manifolds not originally designed for it.
- Throttle Body Adaptation:
- Size Increase: Mounting a larger diameter throttle body onto an existing intake manifold plenum for increased airflow potential. Adapters ensure a smooth bore transition.
- Different Bolt Patterns: Adapting throttle bodies with different mounting patterns (e.g., domestic vs. import).
- Drive-by-Wire (DBW) Conversions: Creating adapters that accommodate newer electronic throttle bodies onto older manifold designs.
- Intake Manifold Swaps:
- Adapting an intake manifold designed for one engine model onto a different cylinder head (common in engine hybrid builds or upgrades). This often requires complex port matching and angle corrections, achievable with AM.
- Sensor Integration:
- Designing adapters with integrated ports for additional sensors like MAP (Manifold Absolute Pressure), IAT (Intake Air Temperature), or auxiliary injectors (e.g., methanol injection). AM allows precise placement and orientation of these ports.
- Exhaust Manifold/Header Adaptation:
- Connecting custom headers to cylinder heads with unusual port shapes or bolt patterns.
- Adapting different exhaust component flanges (e.g., V-band to 2-bolt flange).
- Engine Swaps:
- Perhaps one of the most demanding applications, requiring adapters to mate intake/exhaust manifolds between entirely different engine architectures and chassis constraints. AM provides the geometric freedom necessary for these complex interfaces.
Industries Benefiting from AM Adapters:
- Performance Aftermarket: Suppliers and tuning shops require custom solutions for customers modifying vehicles for increased power and unique setups. Metal AM enables rapid development and delivery of niche adapters.
- Motorsport: Racing teams demand lightweight, highly optimized components. AM allows for topology-optimized adapters with integrated features, shaving precious grams and maximizing airflow for competitive advantage. The ability to quickly iterate designs based on track data is invaluable.
- Specialty Vehicle Manufacturing: Builders of kit cars, restored vehicles, or limited-production models often need bespoke adapters to integrate modern powertrains or specific components. AM provides a cost-effective route compared to traditional tooling for low volumes.
- OEM Prototyping: Major automotive manufacturers utilize metal AM for rapid prototyping of manifold and adapter designs during the R&D phase, allowing for functional testing long before expensive production tooling is created.
Procurement managers and engineers sourcing these parts often look for reliable custom manifold adapter manufacturers eller performance component suppliers capable of delivering high-quality, dimensionally accurate parts quickly. Metal AM service providers are increasingly filling this role, offering on-demand production capabilities.
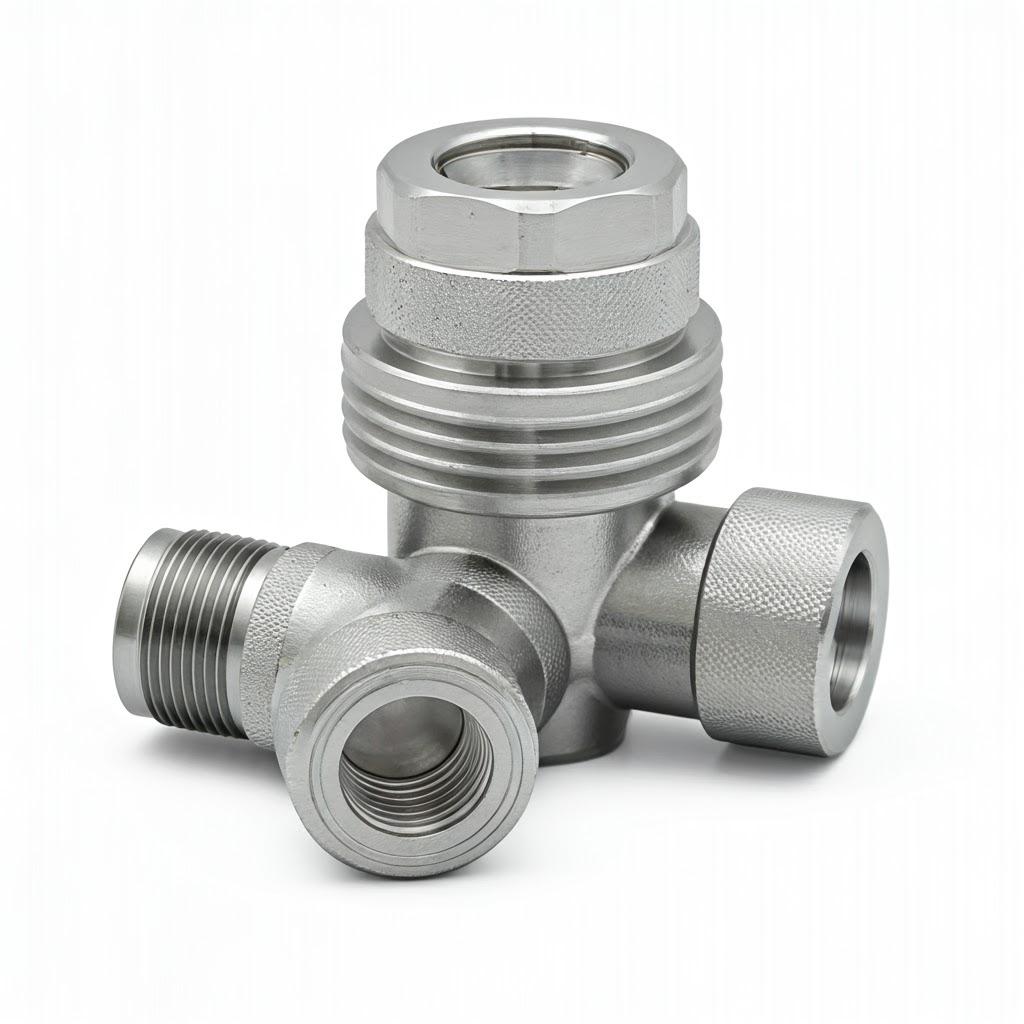
Why Choose Metal Additive Manufacturing for Manifold Adapters?
While traditional manufacturing methods like CNC machining from billet or casting have long been used for manifold adapters, they come with inherent limitations, especially for complex or low-volume parts. Metal AM offers compelling advantages that directly address these shortcomings.
Limitations of Traditional Methods:
- CNC Machining:
- Geometric Constraints: Difficult and expensive to machine complex internal channels with smooth curves or undercuts. Often requires multiple setups, increasing cost and potential for tolerance stack-up.
- Materialavfall: Subtractive process, starting with a solid block and removing material, leading to significant waste, especially for complex shapes.
- Tooling/Fixturing: Custom fixtures may be needed, adding to setup time and cost for low volumes.
- Casting:
- High Tooling Costs: Creating molds or patterns is expensive, making casting viable only for high production volumes.
- Design Limitations: Constraints related to draft angles, wall thickness, and achievable complexity. Internal channels often require complex cores.
- Long Lead Times: Tooling creation takes considerable time, delaying prototyping and production.
- Porosity Concerns: Can be an issue if not carefully controlled, potentially leading to leaks or weak points.
Advantages of Metal AM (specifically Laser Powder Bed Fusion – LPBF/SLM/DMLS):
- Oöverträffad designfrihet:
- Komplexa geometrier: AM builds parts layer-by-layer, enabling the creation of intricate internal channels, optimized flow paths, integrated features (sensor bosses, mounting points), and organic shapes that are impossible or prohibitively expensive to machine or cast. Internal support structures can be minimized with careful design (DfAM).
- Del Konsolidering: Multiple components can often be redesigned and printed as a single, monolithic part, reducing assembly time, weight, and potential leak paths. An adapter might integrate bracketry or sensor mounts directly.
- Lättviktspotential:
- Topology Optimization: Software can be used to remove material from low-stress areas, creating organically shaped, highly efficient structures that maintain strength while significantly reducing weight – crucial for automotive performance and efficiency.
- Gitterstrukturer: Internal lattice structures can be incorporated for further weight reduction while maintaining structural integrity, a feat unachievable with traditional methods.
- Rapid Prototyping and Iteration:
- Hastighet: Functional metal prototypes can be produced in days rather than weeks or months, dramatically accelerating the design validation and testing cycle.
- Flexibilitet: Design modifications can be implemented quickly by simply changing the digital CAD file, allowing for rapid iteration based on testing feedback without tooling changes.
- On-Demand Production & Customization:
- Tooling-Free: AM requires no part-specific tooling, making it economically viable for producing single custom parts, small batches, or replacement parts for obsolete vehicles.
- Massanpassning: Enables the production of unique adapters tailored to specific customer requirements or vehicle setups efficiently.
- Materialalternativ: A growing range of metal powders, including high-performance aluminum alloys ideal for manifold adapters, are available.
Företag gillar Met3dp specialize in providing comprehensive metalladditiv tillverkningslösningar, leveraging advanced printing technologies and high-quality metal powders to produce complex automotive components like manifold adapters, meeting the demands for precision, performance, and speed. Their expertise spans the entire process, from material selection to finished part.
Comparison Table: AM vs. Traditional Methods for Custom Manifold Adapters
Funktion | Metal AM (LPBF) | CNC Machining (Billet) | Gjutning |
---|---|---|---|
Designens komplexitet | Very High (Internal channels, organic) | Moderate (Limited by tool access) | Moderate (Limited by tooling) |
Lättvikt | Excellent (Topology opt., lattices) | Moderate (Pocketing) | Fair (Wall thickness limits) |
Verktygskostnad | Ingen | Low (Fixturing only) | Very High (Molds/Patterns) |
Lead Time (Proto) | Fast (Days) | Moderate (Days/Weeks) | Slow (Weeks/Months) |
Cost (Low Volume) | Konkurrenskraftig | Hög | Mycket hög |
Cost (High Volume) | Högre | Måttlig | Låg |
Material Avfall | Low (Powder recycling) | Hög | Måttlig |
Konsolidering av delar | Utmärkt | Dålig | Rättvist |
Export to Sheets
For engineers needing custom, lightweight, or complex manifold adapters, especially in low-to-mid volumes, the benefits of metal AM make it a highly attractive manufacturing route.
Recommended Materials: AlSi10Mg and A7075 for Optimal Performance
Selecting the right material is crucial for the performance and durability of an automotive manifold adapter. Aluminum alloys are often the primary choice due to their excellent balance of low weight, good thermal conductivity, corrosion resistance, and adequate strength for many adapter applications. Two common aluminum alloys successfully processed via metal AM are AlSi10Mg and A7075.
Material Properties Overview:
- Lättviktare: Aluminum’s low density (approx. 2.7 g/cm³) is a major advantage in reducing overall vehicle weight, contributing to better handling, acceleration, and fuel efficiency compared to steel alternatives.
- Termisk konduktivitet: Efficient heat dissipation is important, especially for exhaust adapters or intake adapters near hot engine components. Aluminum alloys conduct heat well.
- Motståndskraft mot korrosion: Aluminum naturally forms a protective oxide layer, offering good resistance to atmospheric corrosion.
- Bearbetbarhet: Post-processing steps like machining critical mating surfaces are easily performed on aluminum alloys.
AlSi10Mg:
- Sammansättning: An aluminum alloy containing silicon (around 10%) and magnesium (trace amounts). It’s closely related to common casting alloys like A360.
- Egenskaper:
- Excellent processability in Laser Powder Bed Fusion (LPBF).
- Good strength and hardness, suitable for many intake and moderate-temperature exhaust applications.
- Good thermal properties.
- Very good corrosion resistance.
- Can be heat-treated (typically T6) to significantly improve strength and hardness.
- AM Considerations: Prints relatively easily with well-established parameters. Exhibits good flowability as a powder. Post-print heat treatment is usually required to achieve optimal properties and relieve internal stresses built up during the layer-by-layer fusion process.
- Typiska tillämpningar: General-purpose intake adapters, throttle body adapters, sensor housings, brackets, components where moderate strength and good thermal properties are needed. Often seen as the ‘workhorse’ aluminum alloy for AM.
A7075:
- Sammansättning: An aluminum alloy with zinc as the primary alloying element, also containing magnesium and copper. It’s known as an aerospace-grade high-strength alloy.
- Egenskaper:
- Very high strength-to-weight ratio, significantly stronger than AlSi10Mg, especially after heat treatment. Comparable to some steels but at roughly one-third the weight.
- Excellent fatigue strength, crucial for components subjected to vibration and cyclic loading.
- Lower corrosion resistance compared to AlSi10Mg (due to copper content), may require protective coatings in harsh environments.
- Lower thermal conductivity compared to AlSi10Mg.
- AM Considerations: Traditionally considered very challenging to print via LPBF due to its wide freezing range and susceptibility to solidification cracking (hot cracking). However, advancements in machine technology, parameter optimization, and specialized powder chemistries have made reliable A7075 printing achievable. Requires precise control over the printing process and specific, often complex, heat treatment cycles (e.g., T6, T73) to achieve desired properties and mitigate stress. Printing crack-free, high-density A7075 requires significant process expertise.
- Typiska tillämpningar: High-performance intake/exhaust adapters where maximum strength and fatigue resistance are paramount, structurally critical lightweight components, motorsport applications, adapters subjected to high mechanical loads or vibrations.
Met3dp’s Role in Material Excellence:
Achieving the desired properties in AM parts starts with the powder. Met3dp använder branschledande gasatomisering och PREP-teknik to produce high-quality, spherical metal powders, including alloys like AlSi10Mg. Their advanced powder-making systems ensure:
- High Sphericity & Good Flowability: Critical for uniform powder bed layering in AM machines, leading to denser, more consistent parts.
- Controlled Particle Size Distribution (PSD): Optimized PSD for specific AM processes (LPBF, SEBM) ensures efficient melting and part quality.
- Low Impurity Levels: High purity minimizes defects and ensures predictable material properties.
While A7075 presents challenges, Met3dp’s deep expertise in metal powder production and additive manufacturing processes positions them well to support customers looking to leverage high-strength aluminum alloys. Their focus on research and development enables them to tackle demanding materials and applications.
Material Selection Table:
Funktion | AlSi10Mg | A7075 | Överväganden |
---|---|---|---|
Styrka | Bra | Mycket hög | Choose A7075 for highest load/fatigue requirements |
Vikt | Excellent (Low Density) | Excellent (Low Density) | Both offer significant weight savings |
Printability (LPBF) | Utmärkt | Challenging (Requires Expertise) | AlSi10Mg is easier/more common |
Värmebehandling | Required (e.g., T6) | Required & Complex (e.g., T6, T73) | A7075 requires specialized heat treat knowledge |
Motståndskraft mot korrosion | Mycket bra | Moderate (May need coating) | Environment dictates need for protection on A7075 |
Termisk konduktivitet | Bra | Rättvist | AlSi10Mg better for heat dissipation |
Kostnad | Måttlig | Higher (Powder & Processing) | Factor in material and specialized processing cost |
Export to Sheets
By carefully considering the application’s demands (load, temperature, environment) and understanding the properties and processing nuances of materials like AlSi10Mg and A7075, engineers can select the optimal alloy for their metal 3D printed manifold adapters, leveraging the unique benefits of AM for superior automotive components. Partnering with knowledgeable suppliers like Met3dp, who understand both materials science and additive manufacturing, is key to success.
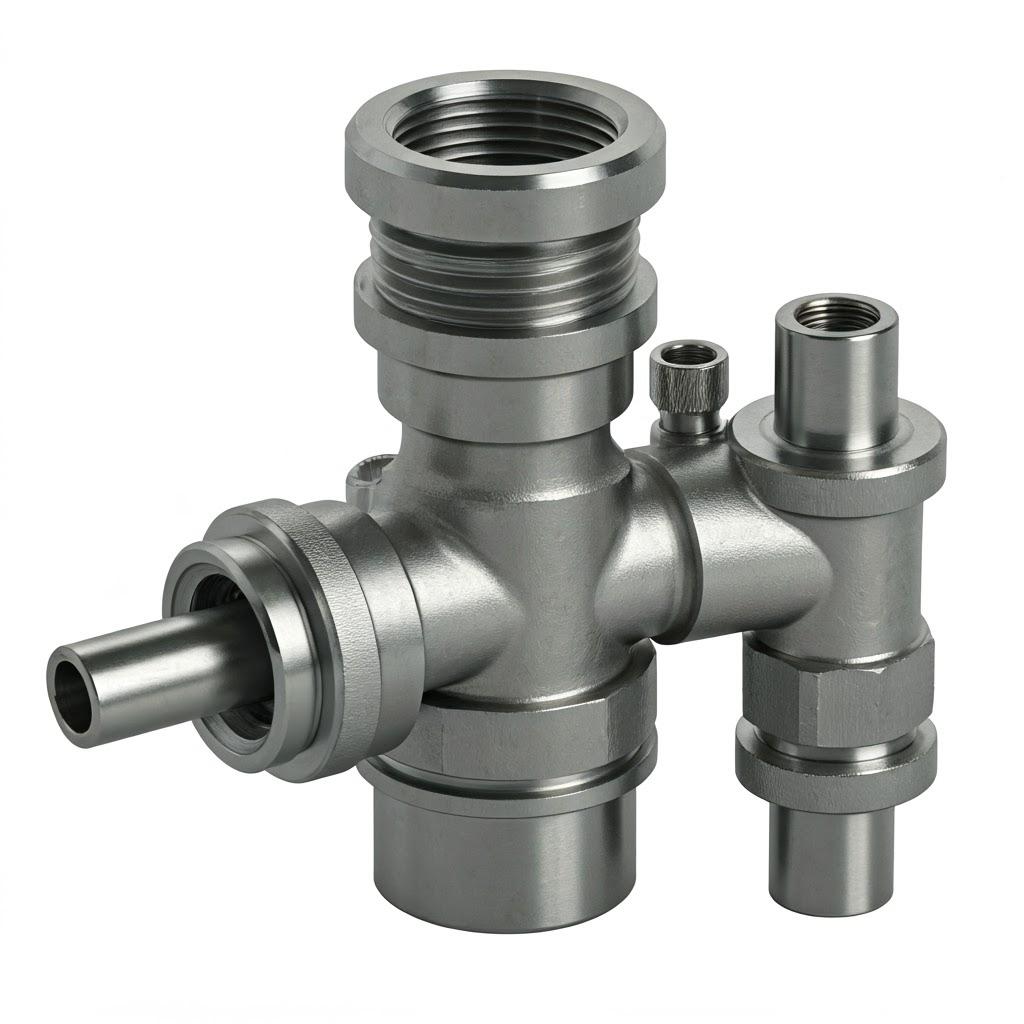
Design for Additive Manufacturing (DfAM) for Manifold Adapters
Simply replicating a design intended for machining or casting often fails to leverage the full potential of metal additive manufacturing. To truly benefit from AM’s capabilities for lightweighting, performance enhancement, and cost-effectiveness when producing manifold adapters, engineers must embrace Design för additiv tillverkning (DfAM) principles. DfAM involves rethinking the design from the ground up, considering the layer-by-layer build process, material properties, and post-processing requirements unique to AM.
Key DfAM Strategies for Manifold Adapters:
- Flow Path Optimization:
- Smooth Internal Geometries: AM excels at creating smooth, curved internal channels that minimize turbulence and pressure drop, unlike the often-sharp angles resulting from drilling or machining. Design transitions between different diameters or flange shapes to be gradual and aerodynamic.
- Computational Fluid Dynamics (CFD): Use CFD simulations early in the design phase to analyze airflow or exhaust gas flow through the adapter. Iterate the internal geometry based on simulation results to optimize velocity, reduce restriction, and ensure balanced flow distribution, especially in multi-port adapters.
- Avoid Abrupt Changes: Minimize sharp corners or sudden changes in cross-sectional area within the flow path, as these create efficiency losses.
- Part Consolidation & Feature Integration:
- Reduce Part Count: Identify opportunities to combine the adapter function with adjacent brackets, sensor mounts, or structural supports into a single printed component. This reduces assembly effort, potential leak points, weight, and overall system complexity.
- Integrated Mounts/Bosses: Design sensor bosses (for MAP, IAT, O2 sensors), mounting flanges, vacuum ports, or threaded inserts directly into the adapter body. AM allows precise placement and complex orientation of these features.
- Wire/Hose Routing: Consider integrating channels or clips for wiring harnesses or vacuum lines directly onto the adapter’s exterior.
- Designing for Self-Support & Reduced Print Time:
- Overhang Angles: Design features with overhang angles typically greater than 45 degrees relative to the build plate. Angles shallower than this usually require support structures, which add material cost, print time, and post-processing effort (removal and surface finishing). Orienting the part optimally on the build platform is crucial here.
- Internal Channels: Design internal channels to be as self-supporting as possible. Teardrop or diamond shapes are often better than purely circular horizontal channels, as the upper surfaces are self-supporting. Consider print orientation carefully.
- Minimize Support Contact Points: Where supports are unavoidable (e.g., critical sealing faces that must face downwards), design them strategically for easy removal and minimize the contact area (“witness marks”) on functional surfaces.
- Lightweighting Strategies:
- Topology Optimization: Utilize software tools that iteratively remove material from areas of low stress while maintaining structural integrity based on defined load cases and constraints. This often results in organic, bone-like structures that are significantly lighter than conventionally designed parts but equally strong or stiff.
- Gitterstrukturer: Replace solid sections with internal lattice structures (e.g., honeycomb, gyroid). These significantly reduce mass and material consumption while providing good stiffness and strength. They can also aid in vibration damping. Ensure adequate powder removal access from lattice-filled sections.
- Thin Walls (with caution): AM allows for thinner walls than casting might permit, but ensure walls meet minimum printable thicknesses (typically 0.4-0.8mm depending on material and machine) and can withstand operational pressures and temperatures. Ribbing or strategic thickening might be needed for reinforcement.
- Powder Removal Considerations:
- Access Holes: For complex internal channels or hollow sections, intentionally design strategically placed access holes to allow for effective removal of unfused powder after printing. These holes might be tapped and plugged later or integrated into non-critical areas of the design.
- Avoid Powder Traps: Design internal geometries to avoid features where powder can become easily trapped and difficult to remove, such as acute internal angles or very narrow, deep cavities.
Applying DfAM principles requires a shift in mindset but unlocks significant advantages. Collaborating with experienced AM service providers like Met3dp, who offer engineering support and DfAM expertise, can greatly accelerate the learning curve and ensure designs are optimized for successful, cost-effective production.
Achievable Tolerances, Surface Finish, and Dimensional Accuracy
Engineers and procurement specialists must understand the typical precision levels achievable with metal AM when specifying manifold adapters. While highly accurate, AM parts typically require post-processing machining for critical features demanding very tight tolerances.
Tolerances:
- General As-Built Tolerances: For Laser Powder Bed Fusion (LPBF) processes like DMLS or SLM, typical dimensional tolerances for well-calibrated machines and optimized processes are often in the range of ±0.1 mm to ±0.2 mm for smaller features (up to ~50mm), or ±0.1% to ±0.2% of the nominal dimension for larger features. However, this can vary significantly.
- Factors Influencing Tolerances:
- Machine Calibration & Condition: Regular calibration and maintenance are essential.
- Materialegenskaper: Different alloys exhibit varying shrinkage and thermal behavior during printing.
- Build Parameters: Laser power, scan speed, layer thickness, etc., affect melt pool stability and final dimensions.
- Part Geometry & Size: Large or complex parts are more prone to thermal distortion.
- Orientation & Supports: How the part is oriented on the build plate and the support strategy used significantly impact accuracy and potential distortion.
- Thermal Stresses: Residual stresses built up during printing can cause warping upon removal from the build plate if not managed correctly through design and process control.
- Critical Dimensions: For mating surfaces (flanges), sealing grooves (O-rings), or precise bore diameters, the as-built tolerances may not be sufficient. These features are typically designated on drawings for finishing via CNC machining in post-processing to achieve tolerances of ±0.025 mm or tighter, if required.
Surface Finish (Roughness):
- As-Built Surface Roughness (Ra): The surface finish of parts directly off the AM machine depends heavily on orientation, material, and parameters.
- Upward-facing surfaces: Generally smoother, potentially Ra $5 – 10 \mu$m.
- Side walls: Show layer lines, typically Ra $7 – 15 \mu$m.
- Downward-facing surfaces (supported): Roughest due to support structure contact, potentially Ra $15 – 25 \mu$m or more.
- Förbättra ytfinishen:
- Bead Blasting/Shot Peening: Common initial step, provides a uniform matte finish, typically Ra $5 – 10 \mu$m, and can improve fatigue life (shot peening).
- Tumbling/Vibratory Finishing: Smooths surfaces and edges, effective for batches of smaller parts.
- CNC Machining: Provides the smoothest finishes on specific features (Ra $1.6 \mu$m or lower).
- Polering: Manual or automated polishing can achieve very smooth, mirror-like finishes (Ra $< 0.8 \mu$m) if required for aesthetics or specific flow characteristics, but this is labor-intensive.
Dimensional Accuracy & Quality Control:
- Verification: Post-print and post-processing inspection are crucial. This typically involves CMM (Coordinate Measuring Machine) checks for critical dimensions, 3D scanning for overall geometric verification against the CAD model, and functional checks like leak testing.
- Processtyrning: Reliable AM providers utilize rigorous process monitoring and quality control procedures throughout the workflow, from powder management to final inspection. Understanding the various metall 3D-utskriftsmetoder and their inherent accuracy capabilities is important when selecting a supplier.
Summary Table: Tolerances & Surface Finish
Funktion | As-Built (LPBF) | After Bead Blasting | After CNC Machining | Anteckningar |
---|---|---|---|---|
Tolerans | $\pm 0.1-0.2$mm or ±0.1−0.2% | Unchanged | As specified ($\pm 0.025$mm+) | Machining required for tight-tolerance features |
Surface Ra (µm) | 5−25+ (Orientation dependent) | 5−10 (Uniform matte) | <1.6 (Feature specific) | Polishing can achieve <0.8 |
Export to Sheets
Clear communication between the designer and the AM service provider regarding critical dimensions, tolerances, and surface finish requirements is essential for ensuring the final manifold adapter meets all functional specifications.
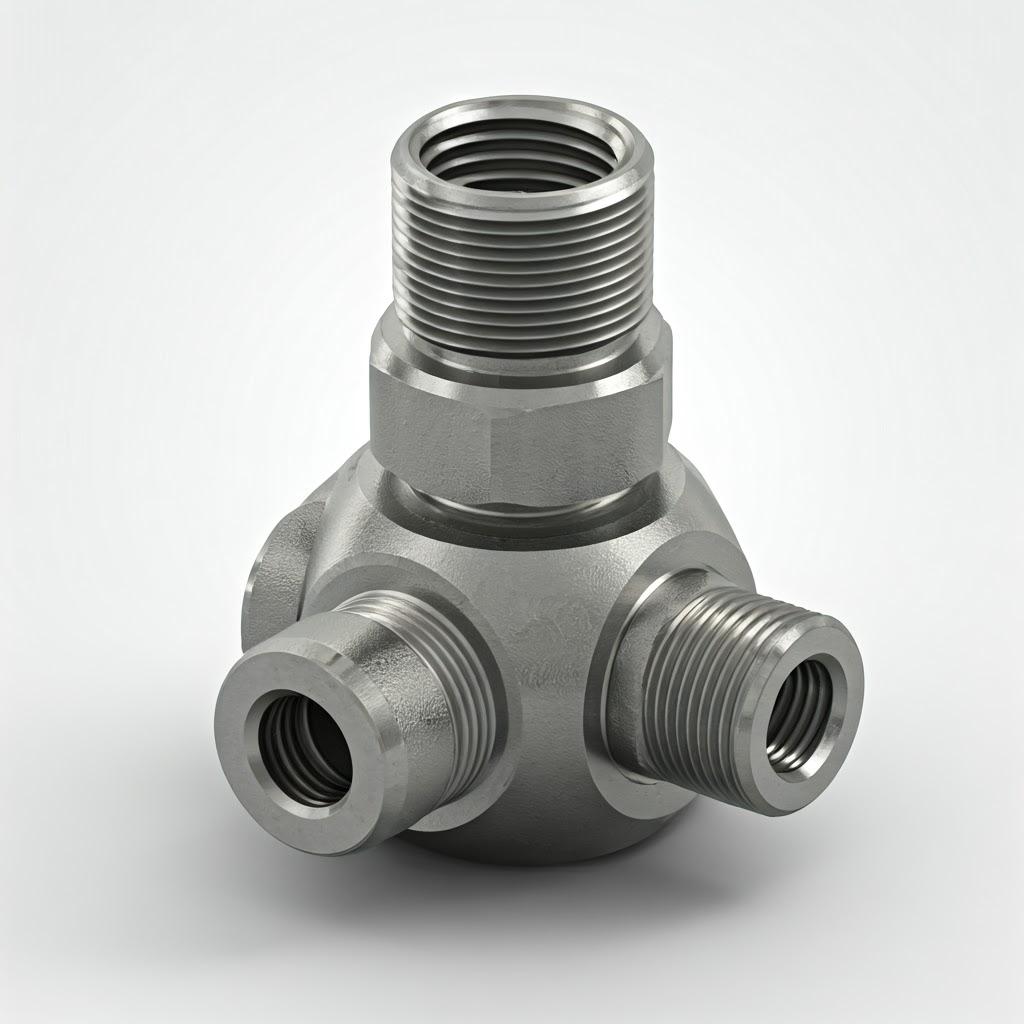
Essential Post-Processing Steps for AM Manifold Adapters
A metal 3D printed part is rarely ready for use immediately after it comes off the build plate. For functional components like automotive manifold adapters, several post-processing steps are typically required to achieve the necessary material properties, dimensional accuracy, surface finish, and overall quality.
Common Post-Processing Workflow:
- Stress Relief / Heat Treatment:
- Syfte: The rapid heating and cooling cycles inherent in LPBF create significant internal stresses within the printed part. Heat treatment relieves these stresses, preventing distortion or cracking after removal from the build plate and improving dimensional stability. It also homogenizes the microstructure and achieves the desired final material properties (strength, ductility, hardness).
- Förfarande: Typically performed while the part is still attached to the build plate. Specific temperature cycles (heating rate, soak time, cooling rate) depend heavily on the alloy (AlSi10Mg T6 vs. A7075 T6/T73 require different, precise cycles) and part geometry. Incorrect heat treatment can compromise mechanical properties.
- Necessity: Considered mandatory for almost all functional metal AM parts, especially aluminum alloys like AlSi10Mg and critically important for stress-sensitive, high-strength alloys like A7075.
- Removal from Build Plate:
- Metoder: Parts are typically cut from the build plate using wire EDM (Electrical Discharge Machining) or a bandsaw. Care must be taken to avoid damaging the part.
- Borttagning av stödstruktur:
- Syfte: Removing the temporary structures used to support overhangs and anchor the part during printing.
- Metoder: Can range from manual breakaway (for well-designed, minimal supports) to machining, grinding, or EDM, especially for supports in hard-to-reach internal areas or those attached to critical surfaces.
- Överväganden: This step can be labor-intensive and must be done carefully to avoid damaging the part surface. DfAM plays a crucial role in minimizing the need for and difficulty of removing supports.
- Ytbehandling:
- Syfte: Improve surface roughness, remove residual support marks, achieve desired aesthetics, or enhance flow characteristics.
- Common Methods:
- Abrasive Blasting (Bead/Sand Blasting): Provides a clean, uniform matte finish. Effective for removing loose powder and slight imperfections.
- Tumbling/Vibratory Finishing: Uses abrasive media in a vibrating bowl or barrel to smooth surfaces and edges, suitable for batches.
- Manual Finishing: Filing, grinding, or sanding specific areas.
- Polering: For achieving very smooth surfaces, often required inside flow paths or for aesthetic reasons.
- CNC Machining:
- Syfte: To achieve tight tolerances on critical features that cannot be met by the as-built AM process.
- Typical Features: Mating flanges (flatness, parallelism), sealing surfaces (O-ring grooves), threaded holes, precise bore diameters.
- Överväganden: Requires careful setup and fixture design to hold the potentially complex AM part geometry accurately.
- Cleaning & Inspection:
- Cleaning: Thoroughly cleaning the part to remove any remaining loose powder (especially from internal channels), machining fluids, or blasting media. Ultrasonic cleaning may be used.
- Inspection:
- Dimensional: Using CMM, calipers, gauges, or 3D scanning to verify critical dimensions against drawings/CAD models.
- Visual: Inspecting for surface defects, cracks, or incomplete support removal.
- Icke-förstörande testning (NDT): May include CT scanning (for internal defects/porosity), dye penetrant testing (surface cracks), or pressure/leak testing, especially critical for manifold integrity.
The specific post-processing steps and their sequence will depend on the adapter’s design complexity, material, and application requirements. Discussing these requirements upfront with the AM service provider is crucial for accurate quoting and lead time estimation.
Common Challenges in 3D Printing Manifold Adapters and Solutions
While metal AM offers significant advantages, producing high-quality manifold adapters is not without its challenges. Understanding these potential issues and how to mitigate them is key to successful implementation.
Challenge 1: Residual Stress and Warping
- Issue: The intense localized heating and rapid cooling during LPBF can cause internal stresses to build up. Upon removal from the build plate, these stresses can cause the part to warp or distort, especially for large or geometrically asymmetric parts.
- Solutions:
- Optimized Orientation: Orienting the part on the build plate to minimize large flat surfaces parallel to the plate and reduce thermal gradients.
- Thermal Engineering: Using build plate heating (common in many LPBF machines).
- Optimized Support Structures: Strategically placed supports anchor the part firmly during the build and help conduct heat away.
- Processparameteroptimering: Fine-tuning laser power, scan speed, and scan strategy to manage heat input.
- Mandatory Stress Relief: Performing a proper stress relief heat treatment cycle before removing the part from the build plate is the most critical step.
Challenge 2: Powder Removal from Internal Channels
- Issue: Manifold adapters often feature complex internal flow paths. Ensuring all unfused metal powder is removed from these channels after printing is critical for functionality and preventing contamination. Trapped powder can obstruct flow or become dislodged during operation.
- Solutions:
- DfAM for Access: Designing dedicated powder removal access holes at strategic locations (can be plugged later). Designing channels with smooth curves and avoiding powder traps.
- Optimized Orientation: Printing the part so internal channels have clear drainage paths.
- Thorough Post-Processing: Utilizing compressed air, vibration, and potentially ultrasonic cleaning methods specifically designed for powder removal from AM parts.
- Inspection: Using borescopes or CT scanning to verify complete powder removal from critical internal passages.
Challenge 3: Porosity
- Issue: Small voids or pores can sometimes form within the printed material due to trapped gas or incomplete fusion between layers. Excessive porosity can compromise the adapter’s mechanical strength and lead to leaks under pressure.
- Solutions:
- High-Quality Powder: Using high-quality, spherical powders with low gas content and optimized particle size distribution, such as those developed by Met3dp för deras product line. Powder quality is fundamental.
- Optimized Print Parameters: Developing and using validated process parameters (laser power, speed, layer thickness, hatch spacing, gas flow) specific to the material and machine to ensure complete melting and fusion.
- Controlled Atmosphere: Maintaining a high-purity inert gas atmosphere (Argon or Nitrogen) in the build chamber to minimize oxidation and gas pickup.
- Het isostatisk pressning (HIP): For critical applications demanding maximum density (>99.9%), HIP can be used as a post-processing step to close internal pores through high temperature and pressure. This adds cost and time but guarantees density.
Challenge 4: Support Structure Removal & Surface Quality
- Issue: Supports are often necessary but can be difficult to remove, especially from internal channels or delicate features. Removal can leave witness marks on the surface, affecting aesthetics or potentially sealing performance if on a critical face.
- Solutions:
- DfAM for Self-Support: Designing parts to minimize the need for supports by respecting overhang angle limits.
- Smart Support Strategies: Using optimized support structures (e.g., thin tips, conical supports, tree supports) that provide adequate anchoring but are easier to remove and leave minimal marking. Software tools and provider expertise are key.
- Efterbearbetning: Combining careful manual removal with machining or appropriate surface finishing techniques (blasting, tumbling) to smooth support contact points. Planning for machining allowance on supported critical surfaces.
Challenge 5: Material-Specific Issues (e.g., A7075 Cracking)
- Issue: Certain alloys, like high-strength A7075 aluminum, are inherently more prone to cracking during the rapid solidification of the AM process due to their chemical composition and wide freezing range.
- Solutions:
- Specialized Parameters: Requires highly optimized, often proprietary, build parameters (e.g., specific thermal management strategies, scan patterns) developed through extensive R&D.
- Powder Chemistry Control: Using powders with slightly modified compositions or specific characteristics designed for better AM processability.
- Advanced Machine Capabilities: Utilizing machines with precise thermal control and monitoring.
- Expertis: Partnering with an AM provider with proven experience and success in printing challenging alloys like A7075 is crucial.
By anticipating these challenges and implementing appropriate DfAM strategies, process controls, and post-processing steps, manufacturers can reliably produce high-quality, functional metal 3D printed manifold adapters. Collaboration with experienced partners like Met3dp, who possess deep knowledge in materials science, process optimization, and application engineering, can significantly de-risk the adoption of AM for these critical automotive components.
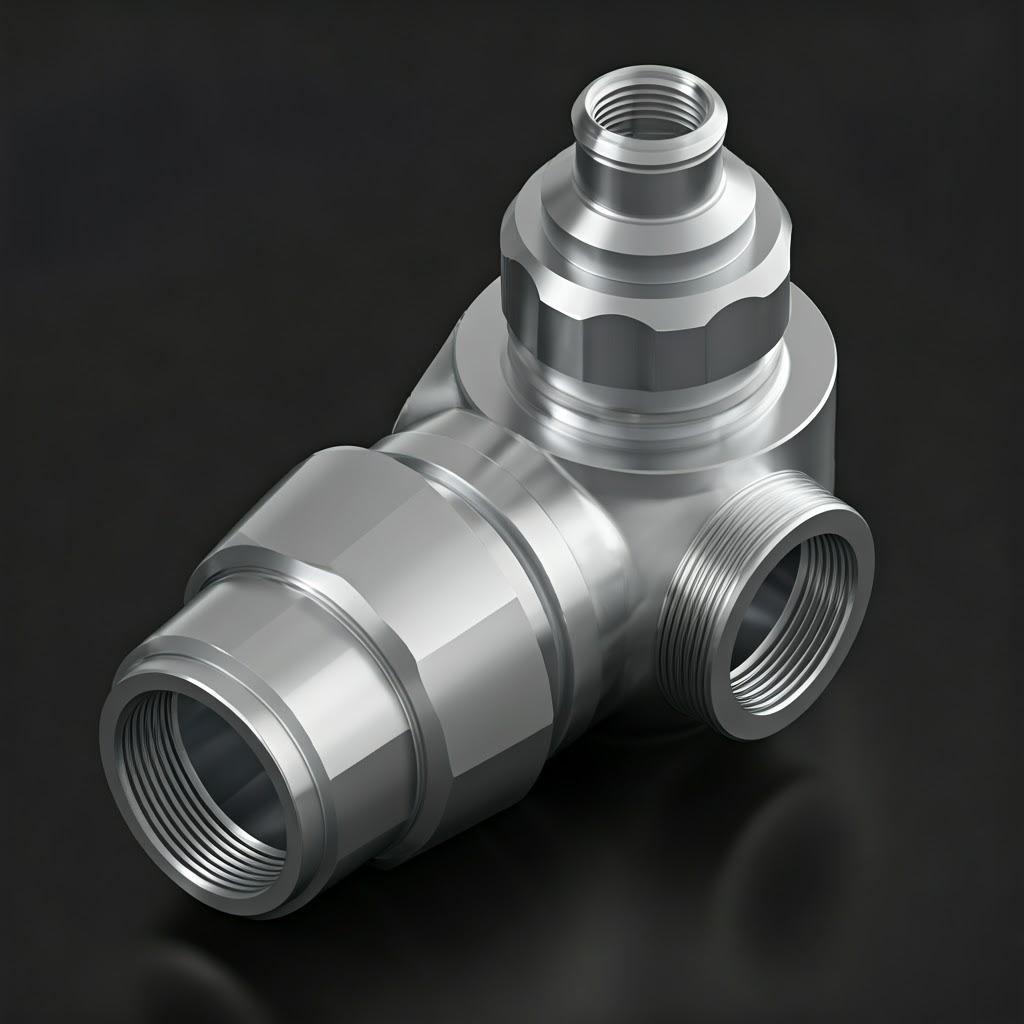
Selecting the Right Metal 3D Printing Service Provider
Choosing the right manufacturing partner is as critical as optimizing the design itself when implementing metal additive manufacturing for automotive manifold adapters. The quality, reliability, and performance of the final component depend heavily on the provider’s expertise, technology, and processes. For engineers and procurement managers evaluating potential metal AM service bureau partners, here are key criteria to consider:
- Material Expertise & Availability:
- Relevant Alloys: Does the provider have proven experience and validated processes for the specific aluminum alloys required (e.g., AlSi10Mg, A7075)? Ask for material datasheets based on their printed and post-processed samples.
- Pulverkvalitet: Inquire about their powder sourcing and quality control procedures. Do they use powders optimized for AM from reputable suppliers, or even produce their own high-quality powders, like Met3dp does with its advanced atomization techniques? Consistent powder quality is fundamental to part quality.
- Broader Portfolio: While you might need aluminum now, does the provider offer other relevant materials (e.g., Titanium alloys, Stainless Steels) for future projects?
- Technology and Equipment:
- Process Capability: Do they utilize industrial-grade Laser Powder Bed Fusion (LPBF/SLM/DMLS) machines known for accuracy and reliability? Understand the specific machine models they operate and their capabilities (build volume, laser power, monitoring features).
- Machine Maintenance & Calibration: Are machines regularly maintained and calibrated to ensure consistent results?
- Environment Control: Is the build environment (inert gas quality, temperature) properly controlled?
- Technical & Engineering Support:
- DfAM Expertise: Can they offer guidance on Design for Additive Manufacturing to help optimize your adapter design for printability, performance, and cost-effectiveness?
- Process Simulation: Do they utilize simulation tools to predict potential build failures or distortions, especially for complex parts?
- Application Knowledge: Do they have experience specifically with automotive components and understand the typical requirements and challenges?
- Post-Processing Capabilities:
- In-House vs. Outsourced: Does the provider offer essential post-processing steps like heat treatment, support removal, CNC machining, and surface finishing in-house, or do they outsource? In-house capabilities often lead to better control, accountability, and potentially faster turnaround times.
- Range of Services: Ensure they can perform all necessary steps to meet your specified tolerances and finish requirements.
- Quality Management & Certifications:
- QMS: Is the provider certified to relevant quality management systems, such as ISO 9001? This indicates a commitment to standardized processes and quality control.
- Industry-Specific Certifications: While not always required for adapters, certifications like AS9100 (Aerospace) demonstrate a higher level of process rigor and traceability, which can be beneficial for demanding automotive applications.
- Inspection Capabilities: What tools and methods do they use for dimensional inspection (CMM, 3D scanning) and material verification? Can they provide detailed inspection reports?
- Track Record & Communication:
- Case Studies/Examples: Can they provide examples of similar automotive parts they have successfully produced?
- Project Management: How do they handle project communication, progress updates, and documentation? Clear and timely communication is vital.
- Lead Times & Reliability: What are their typical lead times, and do they have a track record of on-time delivery?
Choosing a partner like Met3dp, som erbjuder heltäckande lösningar spanning high-performance metal powders, advanced SEBM and LPBF printing equipment, and application development services, can provide significant advantages. An integrated approach ensures seamless transitions between material science, printing, and post-processing, backed by decades of collective expertise in metal additive manufacturing. Evaluating potential suppliers based on these criteria will help ensure you select a partner capable of delivering high-quality, reliable manifold adapters that meet your specific automotive needs.
Cost Factors and Lead Time Estimation for AM Manifold Adapters
Understanding the factors that influence the cost and lead time of metal 3D printed manifold adapters is crucial for budgeting, project planning, and determining the economic viability of AM compared to traditional methods, especially for procurement managers and project engineers.
Key Cost Drivers:
- Part Volume & Material Consumption:
- Material Cost: The amount of metal powder consumed directly impacts the price. More complex or larger adapters naturally cost more. High-performance alloys like A7075 are generally more expensive than standard AlSi10Mg powder.
- Stödstrukturer: Material used for support structures also adds to the cost. Optimized DfAM to minimize supports is key.
- Machine Build Time:
- Part Height: The taller the part is oriented in the build chamber, the longer it takes to print (more layers).
- Part Density/Complexity: Densely packed build chambers or very complex geometries requiring intricate laser scanning patterns increase build time. Machine time on industrial metal AM systems is a significant cost component.
- Part Complexity & Design:
- Internal Channels/Features: Highly complex internal geometries might require more intricate support strategies or extensive powder removal efforts, increasing labor costs.
- Thin Walls/Fine Features: Printing very fine details may require specific parameters or slower print speeds, impacting time and cost.
- Krav på efterbearbetning:
- Värmebehandling: Standard stress relief adds cost; complex cycles for alloys like A7075 add more.
- Stöd för borttagning: Labor-intensive removal for complex parts increases cost.
- CNC Machining: The extent of machining required for tight tolerances significantly impacts the final price. More features requiring machining equals higher cost.
- Ytbehandling: Basic bead blasting is relatively inexpensive; extensive polishing is costly.
- Inspection: Advanced inspection like CT scanning adds cost but may be necessary for critical applications.
- Orderkvantitet:
- Setup Costs: There are fixed costs associated with setting up each build (machine preparation, powder loading). These costs are amortized over the number of parts in a build. Therefore, the per-part cost generally decreases with larger batch sizes, although AM remains competitive even for single units compared to tooling-based methods.
- Arbete: Includes build setup, machine operation monitoring, part removal, post-processing tasks, and quality inspection.
Lead Time Estimation:
Lead time refers to the total time from order placement to receiving the finished part.
- Prototyping: For single parts or very small batches (1-5 units) with standard post-processing, lead times typically range from 5 to 15 business days. This includes printing, stress relief, basic support removal, and potentially bead blasting. Adding complex machining will extend this.
- Low-Volume Production: For small batches (10-100 units), lead times can range from 2 till 6 veckor, depending heavily on part complexity, total build time required (multiple machine runs may be needed), and the extent of post-processing.
- Factors Influencing Lead Time:
- Machine Availability: Current workload and queue at the service provider.
- Byggtid: As discussed under cost factors.
- Post-Processing Complexity: Extensive machining or specialized finishing adds significant time.
- Kvalitetssäkring: Detailed inspection requirements add time.
- Materialets tillgänglighet: Ensuring the required powder is in stock.
It’s crucial to get detailed quotes from potential providers that break down costs and provide realistic lead time estimates based on the specific design and requirements of the manifold adapter.
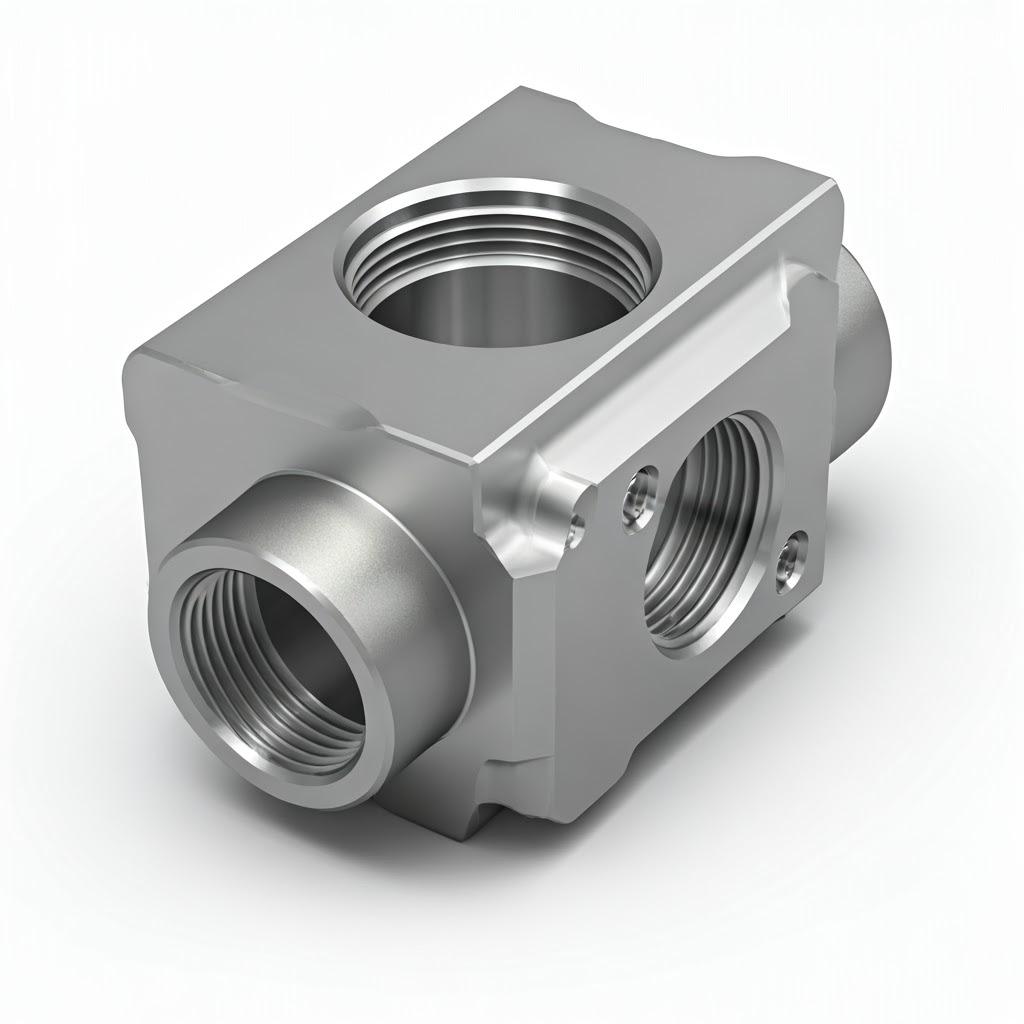
Frequently Asked Questions (FAQ) about AM Manifold Adapters
Here are answers to some common questions engineers and designers have about using metal AM for automotive manifold adapters:
Q1: How does the strength of 3D printed AlSi10Mg or A7075 compare to traditionally manufactured parts (cast or billet)?
- A: Properly processed and heat-treated metal AM parts can achieve mechanical properties (tensile strength, yield strength, elongation) that are comparable to or even exceed those of cast parts, especially for AlSi10Mg which mimics casting alloys. For AlSi10Mg, properties can be similar to A356-T6 castings. High-strength alloys like A7075, when printed using optimized parameters and correct heat treatments, can approach the strength levels of wrought A7075-T6/T73 billet, offering significant strength-to-weight advantages. However, properties can be slightly anisotropic (varying with build direction). Always refer to the provider’s material datasheets based on printed specimens for specific values.
Q2: Can 3D printed manifold adapters handle typical automotive under-hood temperatures and pressures?
- A: Yes. Aluminum alloys like AlSi10Mg and A7075 offer good performance at typical automotive operating temperatures. AlSi10Mg retains useful strength up to around 150−200∘C (300−390∘F). A7075 can generally handle slightly higher temperatures depending on the heat treatment state but may see strength reduction above 120−150∘C (250−300∘F). Both materials, when printed to full density (>99.5%), can easily withstand typical intake manifold pressures (vacuum and boost up to several bar) and moderate exhaust temperatures/pressures, especially for adapters placed further downstream. Design considerations (wall thickness) and material choice should factor in the specific thermal and pressure environment.
Q3: What is the typical cost saving when using AM for custom adapters compared to CNC machining from billet?
- A: For single units or very low volumes (e.g., 1-10 parts) of complex adapters, AM is often mer kostnadseffektivt than CNC machining. This is because AM avoids the high programming and setup costs per part associated with CNC for complex geometries, and it generates less material waste. For simpler adapters or larger quantities (e.g., 50+), CNC machining may become more economical. The breakeven point depends heavily on part complexity – the more complex the adapter, the more advantageous AM becomes at lower volumes. Topology-optimized, lightweight designs that are difficult or impossible to machine often heavily favor AM regardless of quantity if performance is key.
Q4: Are there specific design rules I need to follow for internal channels in AM adapters?
- A: Yes, DfAM principles are crucial. Key rules include:
- Smooth Bends: Use gradual curves instead of sharp angles to optimize flow.
- Self-Supporting Shapes: Design channels with teardrop or diamond cross-sections where possible to avoid the need for internal supports, which are very difficult to remove. Circles are acceptable if oriented vertically.
- Minimum Channel Diameter: Ensure channels are large enough for effective powder removal (typically > 1-2 mm diameter, larger is better).
- Powder Escape Holes: Include access holes for powder removal if channels are fully enclosed or very complex.
- Väggens tjocklek: Maintain appropriate minimum wall thickness for printability and pressure handling. Consult your AM provider for specific guidelines based on their process and material.
Conclusion: Accelerating Automotive Innovation with Metal AM Adapters
The automotive landscape demands continuous innovation, pushing engineers to find solutions that enhance performance, improve efficiency, and reduce weight. Metal additive manufacturing has firmly established itself as a powerful tool in this pursuit, particularly for components like custom manifold adapters.
By leveraging the unparalleled designfrihet of AM, engineers can create adapters with highly optimized internal flow paths, integrate multiple features to reduce part count, and achieve significant viktbesparingar through topology optimization and lightweight materials like AlSi10Mg and A7075. The ability to move from design to functional metal prototype in days enables rapid iteration and validation, accelerating development cycles for performance tuning, engine swaps, and specialty vehicle builds. Furthermore, the tooling-free nature of AM makes customization and low-volume production economically viable, opening doors for niche applications and aftermarket solutions previously limited by traditional manufacturing costs.
While challenges related to design optimization, process control, and post-processing exist, they are addressable through DfAM principles, careful material selection, and collaboration with knowledgeable service providers. Companies with deep expertise across the AM ecosystem, from powder production to printing and finishing, are crucial partners in successfully implementing this technology. Met3dp, with its focus on high-quality metal powders, advanced printing systems, and comprehensive application support, exemplifies the type of partner needed to navigate the complexities and unlock the full potential of metal AM. You can learn more about their integrated approach by visiting their Om oss sida.
For engineers and procurement managers in the automotive sector seeking solutions for complex component integration, performance enhancement, or lightweighting challenges, metal additive manufacturing offers a compelling pathway. Specifically for manifold adapters, AM transitions from a prototyping technology to a viable manufacturing solution for delivering high-performance, customized parts on demand. Exploring the possibilities of metal AM for your next project could be the key to accelerating innovation and achieving competitive advantage.
Dela på
MET3DP Technology Co, LTD är en ledande leverantör av lösningar för additiv tillverkning med huvudkontor i Qingdao, Kina. Vårt företag är specialiserat på 3D-utskriftsutrustning och högpresterande metallpulver för industriella tillämpningar.
Förfrågan för att få bästa pris och anpassad lösning för ditt företag!
Relaterade artiklar
Om Met3DP
Senaste uppdateringen
Vår produkt
KONTAKTA OSS
Har du några frågor? Skicka oss meddelande nu! Vi kommer att betjäna din begäran med ett helt team efter att ha fått ditt meddelande.
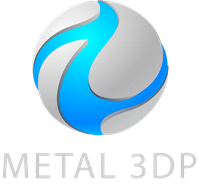
Metallpulver för 3D-printing och additiv tillverkning