3D Printed Marine Propellers with Bronze and Nickel Alloys
Innehållsförteckning
Introduction: The Next Wave in Marine Propulsion – Metal Additive Manufacturing
The relentless push for efficiency, performance, and sustainability in the maritime industry demands constant innovation. At the heart of vessel movement lies the propeller – a critical component translating engine power into thrust. For decades, the design and manufacture of marine propellers have relied heavily on traditional methods like casting and machining. While effective, these methods often face limitations in terms of design complexity, lead times, tooling costs, and material waste. Today, a new wave of technology is poised to redefine marine propulsion: Additiv tillverkning av metall (AM), commonly known as metal 3D-utskrifter.
Metal AM represents a paradigm shift, moving from subtractive processes (removing material) to additive ones (building layer by layer from metal powder). This fundamental difference unlocks unprecedented possibilities for creating highly optimized, complex, and customized components. Imagine propellers with intricate blade geometries perfectly tailored to a specific vessel’s hull form and operating profile, manufactured faster and potentially more cost-effectively, especially for unique or low-volume requirements. This is no longer science fiction; it’s the rapidly evolving reality enabled by advanced 3D-utskriftstekniker av metall.
This article delves into the exciting application of metal AM for manufacturing marine propellers, focusing specifically on the use of high-performance bronze and nickel alloys like Nickel-Aluminium Bronze (NAB – CuAl10Fe5Ni5) och Copper-Nickel (CuNi – CuNi30Mn1Fe). These materials are renowned for their exceptional performance in harsh marine environments, offering superior corrosion resistance, durability, and, in the case of CuNi alloys, excellent anti-biofouling properties.
Why does this matter to engineers and procurement managers in the aerospace, automotive, medical, and industrial manufacturing sectors, beyond the immediate maritime focus? The advancements and principles discussed here – design freedom, material optimization, supply chain disruption, performance enhancement – are relevant across industries seeking high-performance metal components. Understanding how AM is transforming a demanding application like marine propellers provides valuable insights into its potential for your own critical parts.
För engineers, metal AM opens a vast design space. It allows for the creation of biomimetic structures, complex internal channels for cooling or noise reduction, and variable pitch/camber distributions along the blade span that are simply not feasible or economical with traditional casting molds or multi-axis CNC machining. This translates directly into potential gains in hydrodynamic efficiency, fuel savings, reduced cavitation, and lower underwater radiated noise.
För procurement managers and those managing supply chains, metal AM offers compelling advantages. It facilitates on-demand production, significantly reducing the need for large inventories of spare parts, especially for older or less common vessels. Lead times for custom or replacement propellers can be dramatically shortened compared to the weeks or months often required for pattern making, casting, and machining. Furthermore, AM can enable localized manufacturing, strengthening supply chain resilience and potentially reducing logistical costs and complexities. Finding a reliable additive manufacturing solutions provider becomes key to harnessing these benefits.
På Met3dp, we stand at the forefront of this technological revolution. Headquartered in Qingdao, China, Met3dp specializes in industrial metal additive manufacturing systems and the production of high-performance metal powders essential for these advanced applications. Our industry-leading Selective Electron Beam Melting (SEBM) printers deliver exceptional accuracy, reliability, and build volume suitable for demanding components like marine propellers. Coupled with our expertise in powder metallurgy, utilizing advanced gas atomization and Plasma Rotating Electrode Process (PREP) technologies, we provide a comprehensive ecosystem for realizing the full potential of metal AM. We partner with organizations across demanding sectors to integrate 3D printing and accelerate their digital manufacturing transformations.
This article will explore the specific use cases where 3D printed propellers shine, detail the advantages over traditional methods, dive deep into the properties of CuAl10Fe5Ni5 and CuNi30Mn1Fe alloys in the context of AM, and guide you through the critical considerations for design, manufacturing, and partnering to successfully implement this technology. Join us as we navigate the currents of change in marine propulsion technology.
Applications & Use Cases: Where Do 3D Printed Propellers Excel?
While traditional manufacturing methods remain suitable for mass-produced, standardized propellers, metal additive manufacturing carves out significant advantages in specific niches and applications where its unique capabilities offer unparalleled value. The adoption of 3D printed propellers is gaining momentum across various segments of the marine industry, driven by the need for customization, speed, enhanced performance, and solutions for obsolescence. Here’s where AM propellers are making waves:
1. Custom and High-Performance Yachts:
- Need: Owners of superyachts and high-performance racing yachts demand peak efficiency and minimal vibration/noise. Propellers must be perfectly matched to the hull design and engine characteristics for optimal performance.
- AM Advantage: Metal AM allows for the creation of highly customized propeller geometries. Hydrodynamic optimization using computational fluid dynamics (CFD) can lead to designs with complex curves and blade profiles that are difficult or impossible to cast accurately. AM enables rapid iteration – printing and testing multiple design variations quickly to achieve the desired performance targets. The ability to produce one-off designs without dedicated tooling makes AM economically viable for this market.
2. Unmanned Surface Vehicles (USVs) and Autonomous Underwater Vehicles (AUVs):
- Need: These platforms often require compact, highly efficient, and sometimes acoustically stealthy propulsion systems. Designs are frequently iterated as sensor payloads and mission requirements evolve. Low production volumes are typical.
- AM Advantage: AM excels at producing complex, lightweight structures. Propeller-duct systems or integrated thrusters with intricate internal features can be printed as single units, reducing assembly complexity and potential leak paths. The rapid prototyping capability allows engineers to quickly adapt propulsion systems to new vehicle configurations or mission profiles. For military or research applications, AM enables the creation of propellers with specific acoustic signatures.
3. Specialized Workboats and Service Vessels:
- Need: Vessels designed for specific tasks (e.g., pilot boats, crew transfer vessels, research vessels, offshore support) often have unique operational profiles requiring optimized propulsion for efficiency, maneuverability, or low noise. Production volumes may be small series rather than mass production.
- AM Advantage: AM allows tailoring propellers to the specific duty cycle of the vessel – optimizing for high-thrust at low speed, maximizing fuel efficiency during transit, or minimizing noise for research activities. For research vessels needing ultra-low noise signatures, AM can produce complex blade shapes designed to reduce cavitation inception and tip vortex noise. The ability to print replacement blades or entire propellers quickly minimizes downtime for these critical assets.
4. Rapid Prototyping and Hydrodynamic Research:
- Need: Naval architects and marine engineers constantly seek to improve propeller designs. Testing new concepts requires accurate physical models.
- AM Advantage: Metal AM is an ideal tool for creating functional prototypes for tank testing or even limited sea trials. Designs can be taken directly from CAD models and printed in the target material (or a suitable proxy) far faster than traditional prototyping routes involving pattern making and casting. This accelerates the design-build-test cycle, fostering innovation in hydrodynamic efficiency, cavitation reduction, and noise suppression.
5. Replacement Parts for Legacy Systems and Obsolete Designs:
- Need: Maintaining older vessels can be challenging when original propeller designs are no longer manufactured, or the original tooling/patterns are lost or degraded. Sourcing replacements can involve long lead times and high costs.
- AM Advantage: If a 3D CAD model exists or can be created via reverse engineering (e.g., 3D scanning), metal AM allows for the on-demand production of replacement propellers or blades without needing the original tooling. This is invaluable for fleet operators, naval forces, and restoration projects. It ensures operational readiness and extends the service life of valuable assets. This capability is particularly interesting for marine parts distributors looking to offer solutions for hard-to-find components.
6. Niche Applications and Extreme Environments:
- Need: Certain applications might require propellers made from exotic alloys not typically available through standard casting foundries or propellers designed for extreme operating conditions (e.g., high-speed craft, polar operations).
- AM Advantage: AM service providers often work with a wider range of alloys, including specialized formulations. Companies like Met3dp, with expertise in powder development, can even explore custom alloy compositions if required. Furthermore, AM can create robust designs optimized to withstand specific environmental challenges like ice impact or severe cavitation.
Opportunities for the Supply Chain:
The rise of AM propellers creates new opportunities for businesses throughout the marine supply chain:
- Marine Parts Distributors: Can expand their portfolio to include custom or on-demand AM propellers, offering faster solutions for urgent needs and access to designs not available through traditional channels.
- Shipbuilding Suppliers: Can leverage AM for rapid prototyping during the vessel design phase or offer highly optimized propellers as a value-added component for new builds, differentiating their offerings.
- Repair Yards and Maintenance Providers: Can partner with AM service providers to offer rapid replacement solutions for damaged propellers, reducing vessel downtime significantly. This transforms the MRO (Maintenance, Repair, and Overhaul) landscape.
In summary, metal 3D printing is not necessarily aiming to replace all traditional propeller manufacturing overnight. Instead, it offers powerful solutions where customization, speed, complex geometries, low-volume production, and rapid innovation are paramount. As the technology matures, costs decrease, and awareness grows, the range of applications where 3D printed propellers excel will undoubtedly continue to expand, making it a crucial technology for forward-thinking marine engineers and procurement specialists.
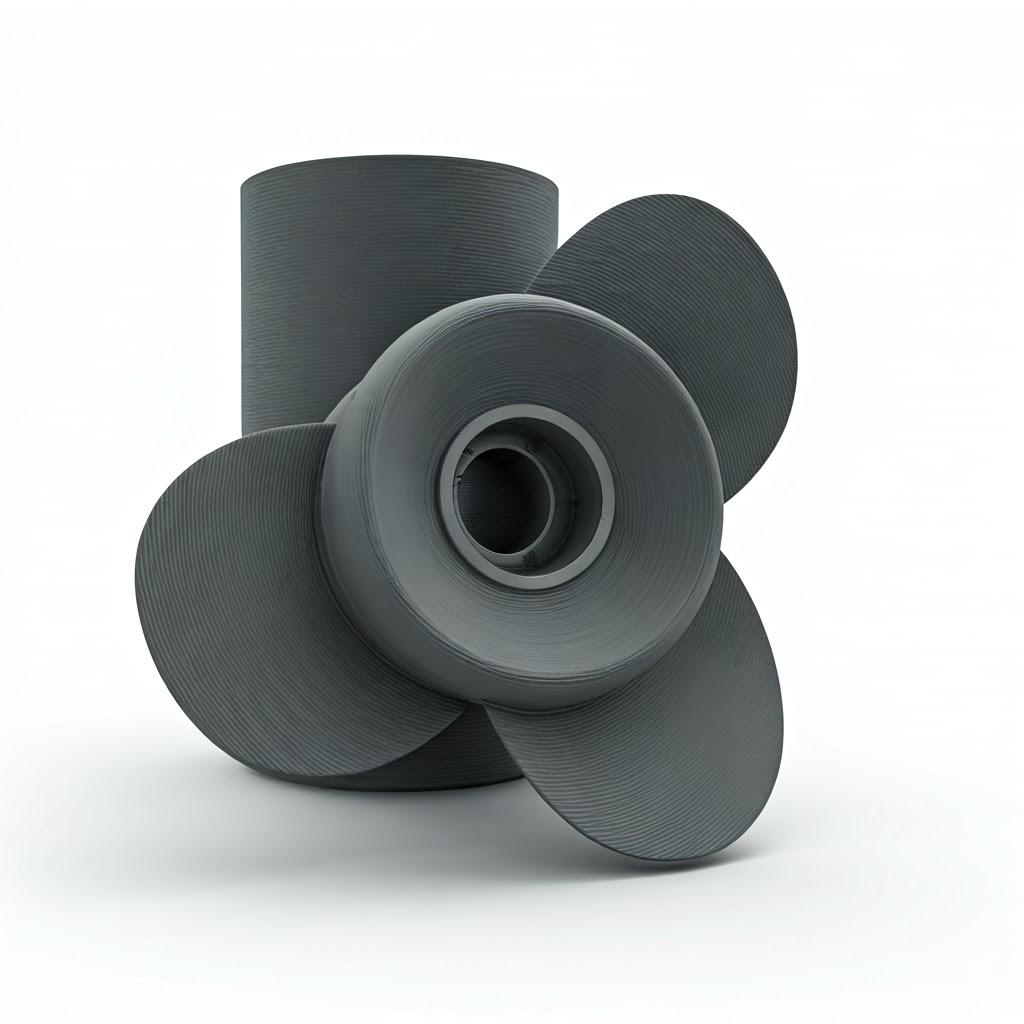
Why Metal 3D Printing? Advantages Over Traditional Propeller Manufacturing
For generations, marine propellers have been predominantly manufactured using casting (typically sand casting or investment casting) followed by extensive CNC machining and finishing. While these methods are mature and capable of producing reliable propellers, they inherently carry limitations that metal additive manufacturing can effectively overcome. Understanding these differences is key for engineers seeking optimal performance and procurement managers aiming for efficient and flexible sourcing.
Let’s compare metal AM (specifically Powder Bed Fusion techniques like LPBF and SEBM, where Met3dp holds significant expertise with its advanced SEBM printers) against traditional casting and CNC machining for propeller production:
Comparison: Metal AM vs. Traditional Propeller Manufacturing
Funktion | Metal Additive Manufacturing (LPBF/SEBM) | Traditional Casting (+CNC) | Traditional CNC Machining (from Billet) |
---|---|---|---|
Designfrihet | Very High: Enables highly complex geometries, internal features, thin walls, optimized blade shapes, lattice structures. | Moderate: Limited by mold-making capabilities, draft angles, cooling rates. Complex internal features difficult/impossible. | High (External): Excellent for external surfaces, but limited for internal features. Deep pockets/complex internal work difficult. |
Lead Time (Prototype/Low Vol) | Short: Days to weeks. No tooling required. Direct from CAD. | Long: Weeks to months. Requires pattern/mold creation. | Moderate to Long: Depends on complexity and programming. Billet sourcing can add time. |
Verktygskostnad | None: Tool-less manufacturing. | High: Significant cost for patterns and molds, especially complex ones. | Low (Fixturing): Requires workholding fixtures, but no part-specific molds. |
Material Avfall | Low: Near-net-shape process. Unfused powder is largely recyclable. | Moderate: Requires risers, gates, runners (recycled but energy intensive). Significant machining allowance needed. | Very High: Subtractive process, often >50% of raw billet becomes chips (recyclable but inefficient). |
Complexity Handling | Excellent: Complexity often adds little to no extra cost or time. Enables part consolidation. | Challenging: Increased complexity drastically increases tooling cost and potential for casting defects. | Challenging/Costly: Very complex geometries require multi-axis machines, complex programming, and long cycle times. |
Minsta orderkvantitet (MOQ) | One: Ideal for single pieces, prototypes, and low volumes. | Moderate to High: Tooling costs necessitate batch production for economic viability. | One (Theoretically): But setup time makes single pieces expensive unless simple. |
Customization Potential | Very High: Each print can be unique without significant cost penalty. Mass customization feasible. | Low: Customization requires new or modified tooling, making it expensive and slow. | Moderate: Can customize features, but restricted by billet form and machining constraints. |
Materialegenskaper | Excellent: Often meets or exceeds cast/wrought properties due to rapid solidification. Fine grain structure. Potential for tailored microstructures. | Good: Well-understood properties, but prone to porosity, segregation, and coarser grain structures. | Excellent: Wrought material properties are typically the benchmark. Homogeneous structure. |
Export to Sheets
Elaborating on the Key Advantages of Metal AM:
- Oöverträffad designfrihet: This is arguably the most significant advantage of AM. Engineers are no longer constrained by the limitations of mold design or the accessibility of cutting tools.
- Hydrodynamic Optimization: Create blades with continuously varying pitch, skew, rake, and camber, precisely optimized using CFD for maximum efficiency and minimum cavitation across the vessel’s operating profile.
- Noise Reduction: Design complex tip geometries (e.g., winglets, non-planar shapes) or internal damping structures to minimize underwater radiated noise – critical for research vessels, naval applications, and passenger comfort.
- Viktminskning: Implement internal lattice structures or topology optimization to reduce propeller mass while maintaining structural integrity. Lighter propellers reduce shaftline stresses and can improve dynamic response.
- Del Konsolidering: Integrate features like rope guards or specialized hub attachments directly into the propeller print, reducing part count, assembly time, and potential failure points.
- Reduced Lead Times for Prototypes and Low Volumes: The ability to go directly from a digital CAD file to a physical metal part in days or weeks is transformative.
- Accelerated Innovation: Test multiple design iterations rapidly, allowing for faster convergence on an optimal solution.
- On-Demand Spares: Print replacement propellers or blades only when needed, drastically reducing inventory holding costs and minimizing vessel downtime. This is a game-changer for marine parts distributors and fleet operators dealing with diverse or aging fleets.
- Urgent Requirements: Address unforeseen damage or operational needs quickly without waiting for traditional casting and machining queues.
- Tool-less Manufacturing: Eliminating the need for expensive and time-consuming patterns and molds unlocks economic viability for:
- Anpassning: Producing one-off propellers for yachts or specialized vessels becomes affordable.
- Produktion av små volymer: Manufacturing small batches of propellers for niche applications or new vessel designs is cost-effective.
- Legacy Parts: Recreating obsolete propellers without investing in recreating lost tooling.
- Material Efficiency and Sustainability:
- Near-Net Shape: AM processes typically use only the material needed for the part and its support structures, significantly reducing waste compared to subtractive machining from large billets.
- Powder Recyclability: Unfused metal powder within the build chamber can usually be sieved and reused in subsequent prints, further improving material utilization. While recycling cast runners/gates and machining chips is possible, the AM process is inherently less wasteful at the primary manufacturing stage.
- Potential for Superior Material Properties: The layer-by-layer fusion process involves rapid heating and cooling, leading to fine-grained microstructures.
- Enhanced Strength & Fatigue Life: Fine grains generally correlate with higher strength and improved fatigue resistance compared to coarser-grained cast materials.
- Densitet: High-quality AM processes, like those employed by Met3dp using optimized parameters and high-quality powders, can achieve part densities exceeding 99.5%, minimizing porosity that can compromise cast parts.
While traditional methods have their place, especially for high-volume production of simple, standardized designs, metal additive manufacturing offers compelling technical and economic advantages for a growing range of marine propeller applications. It empowers engineers to design better-performing components and provides procurement managers with unprecedented flexibility and speed in sourcing critical marine hardware, positioning AM as a vital tool for industrial 3D printing service users in the maritime sector.
Material Focus: CuAl10Fe5Ni5 & CuNi30Mn1Fe Marine Alloys
The choice of material is absolutely critical for marine propellers, which operate in a uniquely challenging environment characterized by corrosive seawater, high mechanical loads, potential for cavitation erosion, and the persistent threat of biofouling. Traditional propeller materials like Manganese Bronze and Stainless Steel have limitations. Metal additive manufacturing opens the door to utilizing advanced alloys specifically chosen for their superior performance in these conditions. Two standout candidates readily processable via AM are Nickel-Aluminium Bronze (NAB, specifically CuAl10Fe5Ni5) and Copper-Nickel (CuNi, specifically CuNi30Mn1Fe). Understanding their properties is essential for selecting the right material for a 3D printed propeller.
1. Nickel-Aluminium Bronze (NAB) – CuAl10Fe5Ni5:
Often considered the workhorse material for high-performance marine propellers, NAB offers an excellent balance of strength, toughness, and corrosion resistance. The CuAl10Fe5Ni5 alloy (conforming to standards like ASTM B148 C95800 for casting, though AM properties can differ slightly) typically contains around 9-11% Aluminium, 3-5% Iron, and 4-5.5% Nickel, with Copper making up the remainder.
- Key Properties & Advantages for Marine Propellers:
- High Strength & Toughness: NAB exhibits significantly higher tensile and yield strength compared to manganese bronzes, allowing for thinner, more efficient blade designs or increased durability for demanding applications. Its good ductility and impact strength provide resistance to damage from debris or minor impacts.
- Excellent Seawater Corrosion Resistance: NAB forms a tenacious, complex protective oxide film (rich in aluminium oxide) when exposed to seawater. This film provides outstanding resistance to general corrosion, pitting, and crevice corrosion, even in polluted or stagnant waters.
- Superior Cavitation Erosion Resistance: Cavitation (the formation and collapse of vapor bubbles due to pressure changes on the blade surface) can rapidly destroy propeller materials. NAB is renowned for its excellent resistance to cavitation damage, significantly better than stainless steels or manganese bronzes. This is crucial for maintaining blade geometry and efficiency over time.
- Good Wear and Galling Resistance: The alloy’s microstructure provides good resistance to abrasive wear, beneficial in silty waters or during maneuvering.
- Svetsbarhet: While AM aims for monolithic parts, NAB generally offers fair weldability for potential repairs if necessary (though specific procedures for AM parts should be followed).
- AM Processability: NAB alloys like CuAl10Fe5Ni5 have demonstrated good processability with Powder Bed Fusion techniques (LPBF and SEBM), allowing for the creation of dense, high-integrity parts when using quality powder and optimized parameters.
- Överväganden:
- Biofouling: While corrosion resistant, NAB offers only moderate resistance to marine growth (biofouling) compared to CuNi alloys. Regular cleaning or anti-fouling coatings may still be required depending on the operational profile.
- Cost: Generally more expensive than manganese bronzes but often justified by its superior performance and longevity.
2. Copper-Nickel (CuNi) – CuNi30Mn1Fe:
Copper-Nickel alloys, particularly the 70/30 (CuNi 70/30) and 90/10 (CuNi 90/10) variants, are widely used in marine applications primarily for their outstanding resistance to biofouling and excellent general corrosion resistance. The CuNi30Mn1Fe alloy (similar to C71500) typically contains approximately 30% Nickel, 0.5-1.5% Manganese, and 0.4-1.0% Iron.
- Key Properties & Advantages for Marine Propellers:
- Exceptional Biofouling Resistance: This is the primary advantage of CuNi alloys. The surface naturally resists the settlement and growth of marine organisms like barnacles, algae, and mussels. This is due to the formation of a cuprite-rich film that is semi-adherent and inhibits biological attachment, possibly combined with a minimal release of copper ions. This property is highly valuable for maintaining propeller efficiency over long periods, reducing fuel consumption and the need for frequent cleaning.
- Very Good Seawater Corrosion Resistance: CuNi alloys form a stable, adherent protective film that provides excellent resistance to corrosion in flowing seawater. They are particularly resistant to impingement attack caused by turbulent flow or suspended solids.
- God duktilitet och formbarhet: These alloys are generally ductile, which can be advantageous for damage tolerance.
- AM Processability: CuNi alloys are also amenable to processing via metal AM technologies, allowing the creation of complex shapes while retaining their key material benefits.
- Överväganden:
- Lower Strength: Compared to NAB, CuNi30Mn1Fe has significantly lower tensile and yield strength. This means propeller blades might need to be thicker or designs adapted to manage the higher stresses, potentially impacting peak hydrodynamic efficiency compared to a slimmer NAB design.
- Cavitation Resistance: While offering good general corrosion resistance, its resistance to cavitation erosion is generally considered lower than that of NAB. Design considerations to minimize cavitation are even more critical.
- Kostnad: High nickel content makes these alloys relatively expensive.
Material Comparison for 3D Printed Propellers:
Fastighet | CuAl10Fe5Ni5 (Nickel-Aluminium Bronze) | CuNi30Mn1Fe (Copper-Nickel 70/30) | Importance for Propellers |
---|---|---|---|
Draghållfasthet | High (~585+ MPa / 85+ ksi typical cast) | Moderate (~380+ MPa / 55+ ksi typical annealed) | High (Blade loading) |
Utbyteshållfasthet | High (~240+ MPa / 35+ ksi typical cast) | Low (~150+ MPa / 22+ ksi typical annealed) | High (Resisting deformation) |
Motståndskraft mot korrosion | Utmärkt | Mycket bra | Kritisk |
Cavitation Resistance | Utmärkt | Fair to Good | Mycket hög |
Biofouling Resistance | Måttlig | Exceptionell | High (Efficiency/Maint.) |
Täthet | ~7,6 g/cm³ | ~8,9 g/cm³ | Moderate (Inertia) |
Printability (LPBF/SEBM) | Bra | Bra | Grundläggande |
Relativ kostnad | Hög | Mycket hög | Moderate (Lifecycle cost) |
Export to Sheets
Note: Specific properties of AM parts depend heavily on process parameters, powder quality, and post-processing (e.g., heat treatment) and may differ from typical cast or wrought values.
The Crucial Role of Metal Powder Quality – Met3dp’s Contribution:
Achieving the desired mechanical properties and corrosion performance in a 3D printed propeller is not just about choosing the right alloy designation; it is critically dependent on the quality of the metal powder used in the AM process. This is where specialized powder manufacturers like Met3dp play a vital role as a trusted metal powder supplier.
Met3dp employs industry-leading powder production technologies:
- Gas Atomization (GA): This process uses high-pressure inert gas jets to break up a stream of molten metal into fine droplets, which solidify into spherical powders. Met3dp utilizes unique nozzle and gas flow designs to optimize this process, yielding powders with:
- Hög sfäriskhet: Spherical particles flow easily and pack densely in the powder bed, which is crucial for achieving high-density (>99.5%) printed parts with minimal porosity.
- Low Satellite Content: Minimizes fine, irregular particles attached to larger spheres, further improving flowability and packing density.
- Controlled Particle Size Distribution (PSD): Tailoring the PSD for specific AM machines (like SEBM or LPBF) ensures consistent melting and layer formation.
- Process med roterande elektrod och plasma (PREP): Particularly suited for producing highly spherical powders from reactive or refractory metals (like Titanium alloys, also relevant in some marine contexts), PREP involves rotating a consumable electrode rod while melting its tip with a plasma torch. Centrifugal force disperses the molten metal into droplets that solidify in flight. This method typically produces powders with exceptional sphericity and very high purity, free from gas porosity within the particles.
Why Met3dp’s Powder Quality Matters for Propellers:
- Förutsägbar prestanda: High-purity, spherical powders with consistent PSD lead to reliable melting and solidification, resulting in printed propellers with predictable mechanical properties (strength, ductility, fatigue life) and consistent corrosion resistance, meeting stringent marine requirements.
- Minskade defekter: Poor powder quality (irregular shapes, internal porosity, impurities, uncontrolled PSD) can lead to defects in the final part, such as porosity, lack of fusion, or cracking, which could compromise the structural integrity and performance of a critical component like a propeller.
- Optimized Printing: High-quality powders enable smoother processing, potentially allowing for faster build speeds and reducing the likelihood of print failures.
By leveraging advanced powder manufacturing techniques and rigorous quality control, Met3dp ensures that the CuAl10Fe5Ni5 and CuNi30Mn1Fe powders supplied meet the demanding specifications required for 3D printing high-integrity marine propellers. Our comprehensive portfolio of metal powders, detailed on our website (see Met3dp’s material offerings), provides engineers and procurement managers with the foundation needed to confidently adopt additive manufacturing for challenging marine applications. Choosing the right alloy is the first step; ensuring it’s produced from premium, AM-optimized powder is paramount for success.
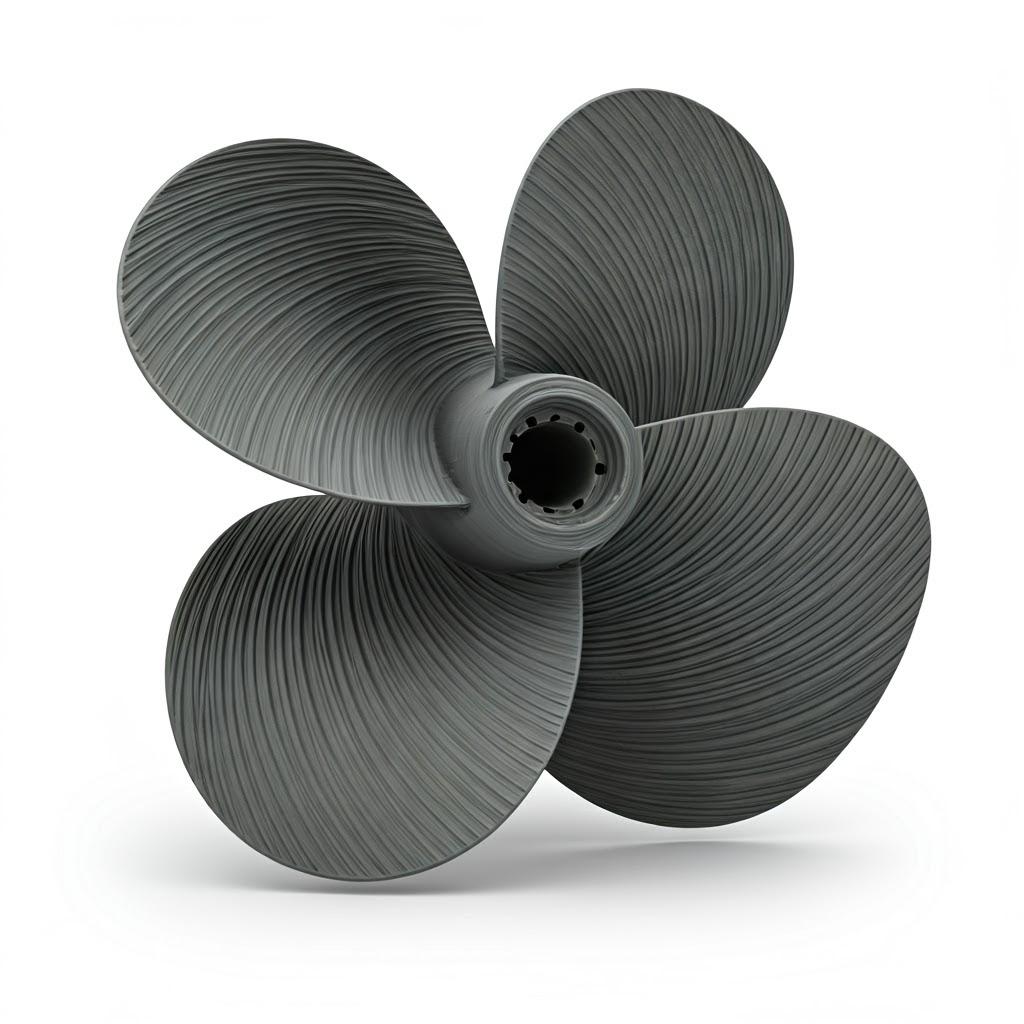
Design for Additive Manufacturing (DfAM): Optimizing Propellers for 3D Printing
One of the most profound shifts introduced by metal additive manufacturing is the need to rethink design itself. Simply taking a propeller design optimized for casting or CNC machining and sending it to a 3D printer will rarely unlock the full potential of AM, and may even lead to suboptimal results or print failures. Design för additiv tillverkning (DfAM) is a methodology that integrates knowledge of the AM process, materials, and post-processing steps directly into the design phase. For marine propellers, applying DfAM principles is crucial for maximizing performance, minimizing cost, and ensuring manufacturability.
Why DfAM Matters for Propellers:
- Exploiting Geometric Freedom: AM removes many traditional manufacturing constraints, allowing for complex shapes that can enhance hydrodynamic performance.
- Minimizing Supports: Support structures are often necessary but add material cost, print time, and significant post-processing effort. DfAM aims to minimize their use.
- Managing Thermal Stresses: The layer-by-layer fusion process inherently creates thermal gradients and residual stresses. DfAM can help mitigate these.
- Ensuring Printability: Designing with AM limitations in mind (e.g., minimum feature size, overhang angles) prevents issues during the build.
- Optimizing for Post-Processing: Considering how the part will be heat-treated, finished, and inspected during the design phase can simplify these downstream steps.
Key DfAM Principles for 3D Printed Propellers:
- Leverage Geometric Complexity for Performance:
- Advanced Blade Profiles: Move beyond simple P/D ratios and standard sections. Implement continuously varying pitch, skew, rake, and camber distributions optimized via CFD analysis for specific flow conditions. Design blades with non-planar shapes or winglets to reduce tip vortex cavitation and induced drag.
- Leading/Trailing Edge Optimization: AM allows for sharper, more defined edges than typically achievable with casting (though extreme sharpness might require post-machining or pose durability/printability challenges). Design edge profiles carefully to balance efficiency gains with structural integrity and manufacturing constraints. Consider biomimetic edge designs inspired by nature (e.g., tubercles like on humpback whale fins) if analysis suggests benefits.
- Hub Integration: Design integrated features like rope cutters, specialized fairings, or sensor mounts directly into the hub structure, consolidating parts and improving flow.
- Strategic Support Structure Minimization:
- Self-Supporting Angles: Design features to adhere to the self-supporting angle limits of the chosen AM process (typically 45° or greater from the horizontal for LPBF/SEBM, though material dependent). Orienting the propeller in the build chamber strategically is key.
- Avoid Horizontal Surfaces: Large, flat downward-facing surfaces require extensive support. Modify designs to use chamfers or curves where possible.
- Accessible Supports: Where supports are unavoidable (e.g., under the hub, steep blade overhangs), design them for easy access and removal. Use perforations or specific structures that break away cleanly or are easily reached with tools. Consider using different support types (e.g., block vs. lattice) depending on the location and function.
- Process-Specific Supports: Understand the support strategies common to the specific AM process (e.g., SEBM often requires fewer, more robust supports than LPBF due to the higher process temperature reducing thermal gradients). Collaborating with an AM service provider like Met3dp, with deep knowledge of their SEBM systems, is invaluable here.
- Optimize Wall Thickness and Feature Sizes:
- Minimum Wall Thickness: Adhere to the minimum printable wall thickness for the chosen material (CuAl10Fe5Ni5 or CuNi30Mn1Fe) and process (typically around 0.4-1.0 mm, but thicker is often safer for structural integrity and printability). Avoid overly thin trailing edges that can warp or be difficult to print accurately.
- Small Feature Resolution: Understand the limits on resolving very small holes, pins, or intricate details. If high precision is needed for small features, plan for post-machining.
- Internal Channels: If designing internal channels (e.g., for damping or future sensor integration), ensure they are self-supporting or design access points for powder removal. Powder removal from complex internal channels can be extremely challenging.
- Design for Stress Management:
- Orientation Impact: The orientation of the propeller in the build chamber significantly affects support needs, surface finish, dimensional accuracy, and residual stress patterns. Simulate or work with experts to determine the optimal orientation. Building blades vertically might minimize supports but could increase build height and time. Building horizontally might require more supports but could reduce height.
- Thermal Considerations: Avoid abrupt changes in cross-section, which can concentrate stress. Use generous fillets and radii at junctions (e.g., blade root to hub) to distribute stress more evenly.
- Simulation-Driven Design: Utilize thermal and structural Finite Element Analysis (FEA) calibrated for AM processes to predict stress concentrations and potential distortion hotspots before printing. Modify the design based on simulation results.
- Consider Lightweighting (with Caution):
- Topology Optimization: Use software tools to remove material from low-stress regions (primarily the hub, potentially thicker sections of blades) while maintaining performance targets.
- Gitterstrukturer: Incorporate internal lattice structures for significant weight reduction. However, for propellers, consider the implications for fatigue life under cyclic loading, potential for internal corrosion if not fully sealed, and difficulty in cleaning/inspecting internal surfaces exposed to the marine environment. Often, solid blades are preferred for robustness and reliability.
The Importance of Collaboration:
Effective DfAM is rarely done in isolation. It requires close collaboration between the component designer (who understands the functional requirements) and the AM process expert (who understands the manufacturing capabilities and limitations). Engaging with a knowledgeable additive manufacturing solutions provider like Met3dp early in the design cycle is highly recommended. Met3dp’s team brings decades of collective expertise in metal AM, material science, and process optimization using their advanced SEBM printers and high-quality powders. This collaboration ensures that the propeller design is not only innovative but also manufacturable, reliable, and cost-effective. By embracing DfAM, engineers can truly leverage the transformative power of 3D printing to create next-generation marine propellers.
Achievable Precision: Tolerance, Surface Finish, and Dimensional Accuracy
While metal additive manufacturing offers incredible design freedom, it’s essential for engineers and procurement managers to have realistic expectations regarding the achievable precision, surface finish, and overall dimensional accuracy of 3D printed marine propellers “as-built.” Understanding these aspects is crucial for determining necessary post-processing steps and ensuring the final component meets functional requirements. The precision achievable depends on the specific AM process (e.g., LPBF vs. SEBM), machine calibration, material used, part size and complexity, build orientation, and thermal management during the print.
1. Dimensional Tolerances:
- General Tolerances: As a rule of thumb, metal Powder Bed Fusion (PBF) processes like Laser PBF (LPBF/SLM) and Selective Electron Beam Melting (SEBM) can typically achieve general dimensional tolerances in the range of ISO 2768-m (medium) or sometimes -f (fine) for as-printed parts. This translates to roughly ±0.1 mm to ±0.5 mm or more, depending on the dimension size.
- LPBF: Often capable of slightly tighter tolerances and finer feature resolution due to the smaller laser spot size compared to an electron beam.
- SEBM: Operates at higher temperatures, which helps reduce residual stress but can sometimes lead to slightly lower as-built dimensional accuracy compared to LPBF, though excellent results are achievable with well-calibrated machines like those utilized by Met3dp. Met3dp’s focus on industry-leading accuracy and reliability ensures their SEBM systems perform optimally.
- Factors Influencing Tolerance:
- Delstorlek: Larger parts generally exhibit greater absolute deviation due to accumulated thermal effects and potential distortion.
- Geometry: Complex geometries with thin walls or large overhangs are more challenging to hold tight tolerances on.
- Material: Different alloys exhibit varying degrees of shrinkage and warp potential.
- Orientation: The direction of build significantly impacts accuracy on different features.
- Termisk hantering: Process parameters and machine stability play a critical role.
- Critical Tolerances: Dimensions requiring high precision – such as the propeller bore diameter, keyway geometry, shaft taper interface, and mounting faces – almost always require post-machining (e.g., CNC turning, milling, grinding) to achieve the necessary tight tolerances (often in the range of ±0.01 mm to ±0.05 mm) for proper fit and function. DfAM should account for adding sufficient machining stock (e.g., 0.5 mm to 2 mm) on these critical surfaces.
2. Surface Finish (Roughness):
- As-Printed Roughness (Ra): The surface finish of as-printed metal AM parts is significantly rougher than machined or even cast surfaces.
- LPBF: Typically achieves Ra values between 5 µm and 20 µm (micrometers).
- SEBM: Generally results in a rougher surface, often between 20 µm and 40 µm Ra, sometimes higher. This is partly due to the larger beam spot size and higher energy input leading to more particle sintering on the surface.
- Surface Texture:
- Layer Lines: The inherent layer-by-layer nature creates visible lines, especially on vertical walls.
- Stair-Stepping: Curved or angled surfaces exhibit a “stair-step” effect, where the layer edges approximate the smooth curve. The severity depends on the layer thickness and the angle of the surface relative to the build plate. Shallower angles result in more pronounced stepping.
- Up-skin vs. Down-skin: Surfaces facing upwards during the build (up-skins) generally have a better finish than surfaces facing downwards (down-skins), which are influenced by the support structures or powder interaction below them.
- Implications for Propellers: The as-printed surface roughness of AM propellers is typically too high for optimal hydrodynamic performance, as it increases frictional drag and can promote early cavitation inception. Therefore, significant surface finishing is usually required, especially on the pressure and suction faces of the blades, as detailed in the next section. Procurement managers should ensure that quotations from industrial 3D printing service providers clearly specify the target surface finish and the methods used to achieve it.
3. Dimensional Accuracy and Warping:
- Overall Accuracy: Beyond tolerances on specific features, the overall geometric fidelity of the part compared to the original CAD model is crucial. Thermal cycles during printing can cause warping and distortion, particularly in large, thin, or asymmetrically designed parts like propeller blades.
- Mitigation Strategies:
- Simulation: Predictive modeling helps anticipate distortion.
- Orientation & Supports: Strategic placement minimizes stress and anchors the part.
- Process Parameters: Optimized energy input and scanning strategies reduce thermal gradients.
- Machine Stability & Calibration: High-quality, well-maintained machines like Met3dp’s SEBM printers provide the stable processing environment needed for accuracy. Their commitment to reliability translates into more predictable dimensional outcomes.
- Stressavlastning: Post-print heat treatment is vital for relieving internal stresses that could otherwise cause distortion upon removal from the build plate or during machining.
- Balancing Requirement: Even with excellent dimensional accuracy achieved through AM and post-machining, minor mass imbalances inherent in any manufacturing process (AM or traditional) necessitate final static and dynamic balancing. This ensures the propeller rotates smoothly without inducing vibrations in the shaft line and hull, which is critical for performance, comfort, and longevity of drivetrain components.
In conclusion, while metal AM offers the ability to create complex propeller geometries, it’s not inherently a ‘perfect precision’ process straight out of the machine. Engineers must design with achievable tolerances and surface finishes in mind, and procurement managers must budget for the necessary post-processing steps, particularly machining and surface finishing, to meet the final functional requirements. Partnering with an experienced AM provider who understands these nuances and possesses the right equipment and process controls, like Met3dp, is key to achieving the desired precision for demanding marine applications.
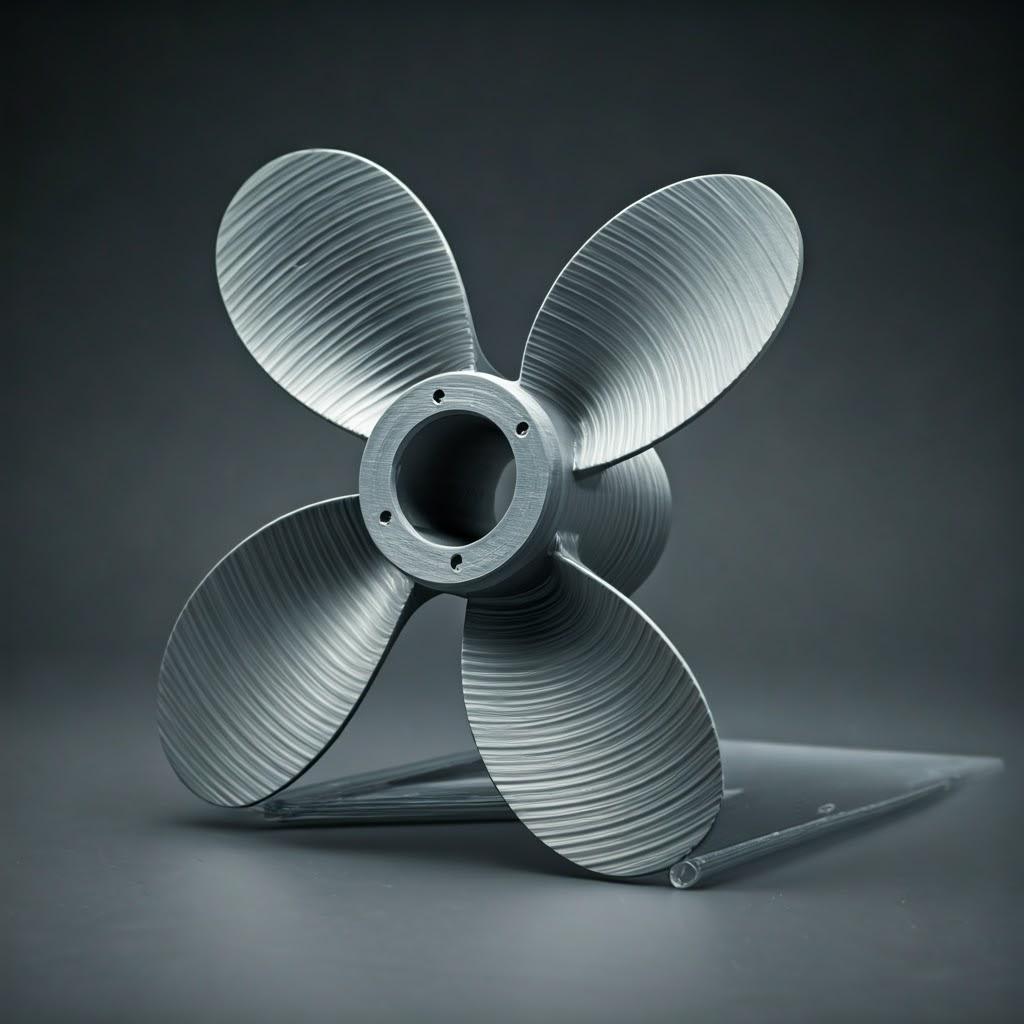
Post-Processing Pathway: From Printed Part to Finished Propeller
The journey of a 3D printed metal propeller doesn’t end when the printer stops. In fact, the “printing” is often just the first major step in a comprehensive manufacturing workflow. Post-processing is not merely an afterthought; it’s an essential sequence of steps required to transform the raw, as-printed component into a functional, reliable, and finished marine propeller ready for installation and operation. The specific steps and their order can vary depending on the AM process used (LPBF vs. SEBM), the material (NAB vs. CuNi), the propeller’s design complexity, and the final performance requirements.
Here’s a typical post-processing pathway for a 3D printed marine propeller using CuAl10Fe5Ni5 or CuNi30Mn1Fe:
1. Stress Relief Heat Treatment:
- Why: This is arguably the most critical initial post-processing step. The rapid heating and cooling cycles inherent in PBF processes create significant residual stresses within the printed part. These stresses can cause distortion or cracking during subsequent steps (like removal from the build plate or machining) or compromise the part’s performance and fatigue life in service.
- How: The part, often while still attached to the build plate, is heated in a controlled atmosphere furnace (e.g., inert gas like Argon, or vacuum) to a specific temperature below the alloy’s critical transformation point, held for a defined period, and then slowly cooled.
- Typical for NAB (CuAl10Fe5Ni5): Temperatures might range from 300°C to 650°C depending on the desired balance between stress relief and maintaining strength. Time varies based on part thickness.
- Typical for CuNi (CuNi30Mn1Fe): Annealing/stress relief temperatures might be in the 550°C to 750°C range.
- Outcome: Significantly reduces internal stresses, stabilizes the microstructure, and improves ductility. Careful planning is needed as parts can still distort slightly during this process if not properly supported.
2. Part Removal from Build Plate:
- Why: The propeller is fused to a thick metal build plate during printing. It needs to be separated for further processing.
- How: Vanliga metoder inkluderar:
- Wire Electrical Discharge Machining (Wire EDM): Precise method, good for complex interfaces, minimal force applied to the part.
- Bandsågning: Faster and lower cost for simpler interfaces, but applies more mechanical force.
- Maskinbearbetning: Milling or grinding away the base/support interface.
- Consideration: The chosen method depends on the part geometry, required precision at the base, and cost factors.
3. Bulk Powder Removal and Cleaning:
- Why: Unfused metal powder remains on the part surface and within any internal cavities or support structures. This needs to be thoroughly removed.
- How:
- Manual Brushing/Vacuuming: For accessible surfaces.
- Compressed Air Blowing: Effective but requires containment to manage airborne powder.
- Bead Blasting (Gentle): Can help dislodge trapped powder but must be done carefully to avoid damaging delicate features.
- Ultrasonic Cleaning: Sometimes used with appropriate solvents for intricate parts.
- Utmaning: Removing powder completely from complex internal channels or dense lattice structures (if used) can be very difficult and requires careful design consideration (DfAM). Incomplete powder removal is a contamination risk and adds dead weight.
4. Support Structure Removal:
- Why: Supports are temporary structures essential for the build process but are not part of the final propeller design.
- How: This is often a labor-intensive step:
- Manual Breaking/Cutting: For easily accessible, frangible supports. Pliers, chisels, grinders may be used.
- Machining (CNC or Manual): Milling or grinding away support structures, especially at the interface points (“witness marks”).
- Wire EDM: For precise removal in tight areas.
- Utmaning: Support removal can leave witness marks or slight imperfections on the part surface that require blending. Accessing supports within intricate blade geometries can be difficult. DfAM plays a huge role in designing supports for easier removal. This step significantly impacts the final cost and lead time, especially for complex parts requiring extensive support. Procurement managers evaluating quotes from wholesale 3D printed propeller suppliers should inquire about the time and methods allocated for support removal.
5. Solution Annealing / Strengthening Heat Treatments (Optional but Common):
- Why: Beyond stress relief, additional heat treatments may be needed to optimize the final mechanical properties (e.g., increase strength, improve corrosion resistance further, homogenize the microstructure). The specific treatment depends heavily on the alloy and desired properties.
- NAB: May involve higher temperature treatments (e.g., >800°C) followed by controlled cooling or quenching and potentially tempering to achieve specific phases and hardness levels.
- CuNi: Typically used in the annealed state after stress relief for optimal corrosion resistance and biofouling properties.
- How: Performed in controlled atmosphere furnaces following precise temperature and time profiles defined by material specifications or application requirements.
6. Hot Isostatic Pressing (HIP) (Optional):
- Why: To eliminate any remaining internal microporosity left over from the AM process. Porosity can act as an initiation site for fatigue cracks, reducing the component’s lifespan under cyclic loading (very relevant for propellers).
- How: The part is subjected to high temperature (below melting point) and high isostatic pressure (using an inert gas like Argon) simultaneously in a specialized HIP vessel. The pressure collapses internal voids, diffusion bonding the material across the void interfaces.
- When: Recommended for critical applications demanding maximum fatigue life and structural integrity. Adds cost and lead time but provides the highest material quality. Met3dp can advise on whether HIP is beneficial based on the application and their process capabilities.
7. Machining for Critical Dimensions and Features:
- Why: As discussed under ‘Precision’, AM tolerances are often insufficient for critical interfaces.
- How: Using CNC lathes, mills, or grinders to achieve final tolerances on:
- Propeller bore (diameter, taper, keyway)
- Mounting faces
- Blade tips or edges requiring specific profiles/sharpness.
- Any surfaces requiring a very specific, smooth finish for hydrodynamic seals or fits.
8. Surface Finishing:
- Why: To improve hydrodynamic efficiency (reduce drag), minimize cavitation inception, enhance fatigue life (smooth surfaces have fewer stress risers), and improve aesthetics.
- How: Various methods can be employed, often in combination:
- Grinding/Sanding: Manual or robotic processes using abrasive belts or discs to smooth blade surfaces and blend support witness marks. Progressively finer grits are used.
- Polering: Using polishing compounds and buffing wheels to achieve very low Ra values (mirror-like finish if required), typically focused on blade pressure and suction faces.
- Mass Finishing (Tumbling/Vibratory): Can be used for smaller components or to achieve a uniform satin finish, potentially using abrasive or non-abrasive media. Less common for large propellers.
- Electropolishing: An electrochemical process that removes a thin layer of material, preferentially from peaks, resulting in a very smooth and clean surface. Can be effective for complex shapes but requires specific electrolytes for copper alloys.
9. Non-Destructive Testing (NDT) and Quality Assurance:
- Why: To verify the integrity of the finished propeller and ensure it meets all specifications before delivery. Essential for quality control and certification.
- How: A combination of methods:
- Visual Inspection: Thorough check for surface defects, cracks, incomplete support removal.
- Dimensionell inspektion: Using Coordinate Measuring Machines (CMM), 3D scanners, or traditional metrology tools to verify critical dimensions and overall geometry against the CAD model and drawings.
- Dye Penetrant Testing (DPT): To detect surface-breaking cracks or porosity.
- Radiographic Testing (X-ray) or Computed Tomography (CT) Scanning: To detect internal defects like porosity or inclusions. CT scanning provides a full 3D view of internal structures.
- Material Certification: Verifying powder batch traceability and conformance to material specifications.
10. Balancing:
- Why: To ensure smooth, vibration-free operation.
- How: Placing the finished propeller on a balancing machine to detect mass imbalances. Material is then carefully removed (usually by grinding) from specific locations on the hub or blades until the propeller meets the required balancing grade (e.g., ISO 1940 G6.3 or better). Both static and dynamic balancing are typically performed.
This comprehensive post-processing pathway highlights that 3D printing is part of an integrated manufacturing chain. Each step requires expertise, specialized equipment, and careful quality control. Companies like Met3dp, offering end-to-end additiv tillverkningslösningar, understand this intricate process, ensuring that the final 3D printed propeller delivered to the customer meets the demanding requirements of the marine environment.
Navigating Challenges: Common Hurdles in 3D Printing Propellers & Solutions
While the potential of 3D printed marine propellers is immense, realizing this potential requires navigating several inherent challenges associated with metal additive manufacturing, particularly when dealing with complex geometries and demanding materials like NAB and CuNi. Awareness of these potential hurdles allows engineers, manufacturers, and procurement specialists to implement mitigation strategies proactively, often in collaboration with experienced AM service providers.
1. Warping and Distortion:
- Utmaning: The intense, localized heating and rapid cooling during PBF processes create steep thermal gradients. As layers solidify and cool, they contract, inducing internal stresses. Uneven stress distribution, especially in large parts or those with varying cross-sections like propeller blades, can cause the part to warp or distort from its intended shape, both during the build and after removal from the build plate.
- Solutions:
- Thermal Simulation: Use FEA software to predict temperature distributions and resulting stresses/distortion based on part geometry, material properties, and scan strategy. Allows for design or process adjustments pre-emptively.
- Optimized Part Orientation: Selecting the build orientation that minimizes large overhangs, balances thermal masses, and potentially reduces build height can significantly impact distortion.
- Robust Support Structures: Supports act not only to anchor overhangs but also as heat sinks and mechanical restraints against warping. Intelligent support design is crucial.
- Optimized Scan Strategies: Techniques like island scanning, sectoring, or adjusting laser/beam parameters can help manage heat accumulation and reduce stress.
- Process Temperature (SEBM Advantage): SEBM operates with the powder bed at elevated temperatures (several hundred °C). This reduces the thermal gradient between the molten pool and surrounding material, inherently lowering residual stresses compared to room-temperature LPBF processes, making it potentially advantageous for large or complex parts prone to warping. Met3dp’s expertise in SEBM leverages this benefit.
- Mandatory Stress Relief: Performing stress relief heat treatment immediately after printing and before support removal is non-negotiable.
2. Residual Stress Management:
- Utmaning: Even if macroscopic warping is controlled, high residual stresses can remain locked within the part. These stresses can:
- Cause unexpected distortion during post-machining as material layers are removed.
- Lead to premature cracking or failure in service, especially under fatigue loading.
- Make support removal difficult or cause the part to spring back upon support removal.
- Solutions:
- DfAM: Designing with stress mitigation in mind (fillets, avoiding sharp corners, gradual thickness changes).
- Processoptimering: As mentioned above (orientation, scan strategy, SEBM).
- Effective Heat Treatment: Proper stress relief cycles are paramount. Solution annealing or HIP can further homogenize the microstructure and reduce stress variation.
3. Porosity:
- Utmaning: Small voids or pores can form within the printed material due to several reasons:
- Gas Porosity: Trapped shielding gas (Argon in LPBF) or dissolved gases in the powder released during melting.
- Lack of Fusion Porosity: Insufficient energy input or improper beam/laser overlap leading to incomplete melting between layers or scan tracks.
- Powder Quality Issues: Hollow powder particles or contaminants.
- Påverkan: Porosity reduces the effective cross-sectional area, degrades mechanical properties (especially fatigue strength and ductility), and can act as corrosion initiation sites.
- Solutions:
- Optimized Process Parameters: Ensuring correct energy density, scan speed, layer thickness, and gas flow (for LPBF).
- High-Quality Powder: Using powder with high sphericity, controlled PSD, low internal gas content, and high purity is critical. This underscores the importance of sourcing from reputable suppliers like Met3dp, who utilize advanced atomization techniques (Gas Atomization, PREP) and rigorous quality control. Learn more about Met3dp’s commitment to quality.
- Het isostatisk pressning (HIP): The most effective way to eliminate internal porosity post-print.
4. Achieving Desired Surface Finish:
- Utmaning: As-printed surfaces are inherently rough (see previous section). Achieving the smooth finish required for hydrodynamic efficiency (typically Ra < 3-6 µm, or even lower for high-performance applications) requires significant post-processing effort, especially on the complex, doubly-curved surfaces of propeller blades.
- Solutions:
- Orientation Strategy: Orienting critical surfaces (like blade faces) optimally relative to the build direction can minimize stair-stepping, though trade-offs exist (e.g., increased support needs).
- Advanced Post-Processing: Utilizing multi-axis CNC machining, robotic grinding/polishing, or potentially electropolishing.
- Budgeting Time & Cost: Recognizing that achieving a high-quality surface finish is a major component of the overall manufacturing time and cost.
5. Support Removal Difficulties:
- Utmaning: Removing potentially extensive and complex support structures without damaging the part can be time-consuming, costly, and requires skilled labor. Accessing internal supports or those on delicate features is particularly challenging. Support witness marks always require cosmetic finishing.
- Solutions:
- DfAM for Minimal Support: The primary strategy is to design the part and select the orientation to minimize the need for supports in the first place.
- Smart Support Design: Using structures that are strong enough during the build but designed to break away easily or be accessed for cutting/machining.
- Appropriate Removal Techniques: Using the right tools (manual, CNC, EDM) for the specific support type and location.
- Experienced Technicians: Relying on skilled personnel for manual support removal and finishing.
6. Material Consistency and Qualification:
- Utmaning: Ensuring that every printed propeller exhibits consistent material properties (strength, ductility, corrosion resistance) that meet specifications requires tight control over the entire process chain, from raw powder to finished part. Batch-to-batch variation in powder or deviations in print parameters can affect outcomes. Qualifying the process for marine applications, potentially requiring certification by classification societies (e.g., DNV, ABS, LR), adds another layer of complexity.
- Solutions:
- Rigorous Powder QA/QC: Sourcing powder from suppliers with robust quality management systems (like Met3dp, adhering to standards like ISO 9001) who provide detailed batch certifications (chemistry, PSD, morphology, flowability).
- Process Validation & Monitoring: Establishing qualified, locked-down printing parameters for specific material/machine combinations. Implementing in-situ monitoring where possible to track build consistency.
- Standardized Post-Processing: Using consistent, documented procedures for heat treatment, machining, and finishing.
- Comprehensive NDT: Employing thorough testing to verify the integrity and properties of each finished part.
- Collaboration for Certification: Working closely with classification societies from the outset if formal certification is required, involving material testing, process qualification, and part inspection according to their rules. This is crucial for wholesale marine component suppliers aiming for broad market acceptance.
7. Cost-Effectiveness:
- Utmaning: Compared to mature casting technology for standard, high-volume propellers, metal AM can still have higher upfront costs per part, driven by expensive machinery, specialized materials, and extensive post-processing.
- Solutions:
- Focus on Value, Not Just Cost: Emphasize applications where AM provides unique value (customization, speed, performance gains, obsolescence solutions) that outweigh the potentially higher piece price.
- Optimize for AM: Use DfAM to reduce material usage, minimize supports, and potentially consolidate parts, lowering overall manufacturing cost.
- Total Cost of Ownership (TCO): Analyze the full lifecycle cost, including potential fuel savings from higher efficiency, reduced maintenance from better materials (e.g., CuNi biofouling resistance), and minimized downtime from on-demand spares.
- Technological Advancement: Costs are continuously decreasing as AM technology matures, machines become faster, and materials become more available.
By understanding these challenges and working with knowledgeable partners equipped with the right technology and expertise, such as Met3dp, the maritime industry can successfully harness the power of metal additive manufacturing to produce innovative, high-performance marine propellers.
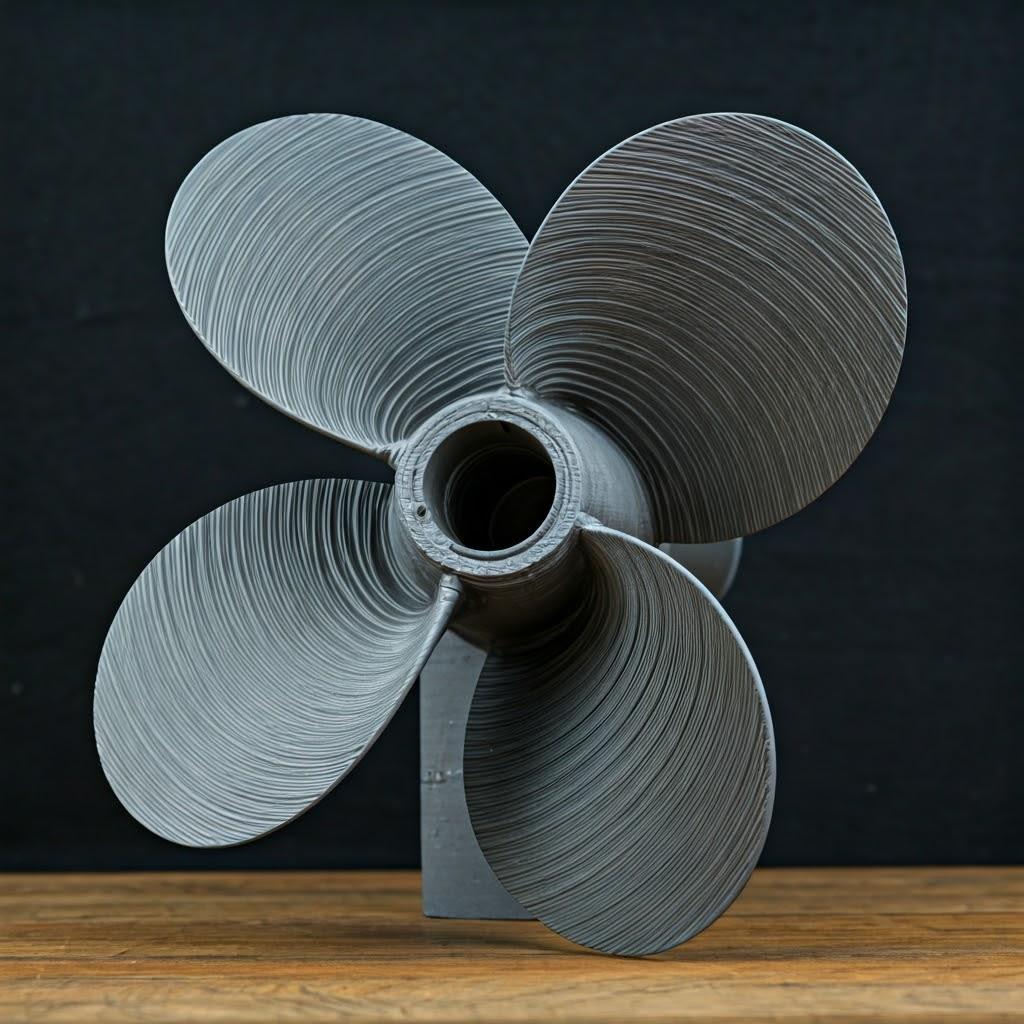
Choosing Your Partner: Selecting the Right Metal AM Service Provider
Successfully implementing 3D printed marine propellers requires more than just advanced technology; it demands a strong partnership with a capable and experienced metal additive manufacturing service provider. The right partner acts as an extension of your engineering and procurement teams, offering expertise, reliability, and quality assurance throughout the entire process, from design optimization to final part qualification. Choosing incorrectly can lead to project delays, cost overruns, subpar component quality, and ultimately, failure to realize the benefits of AM.
For engineers and procurement managers evaluating potential industrial 3D printing service providers for marine propeller projects using specialized materials like CuAl10Fe5Ni5 (NAB) or CuNi30Mn1Fe, here are critical criteria to consider:
1. Proven Expertise and Relevant Experience:
- Marine Application Focus: Does the provider have documented experience with marine components? Do they understand the harsh operating environment, corrosion challenges, and performance requirements specific to the maritime industry? Ask for case studies or examples of similar projects (while respecting NDAs).
- Material Specialization: Have they successfully printed parts using NAB, CuNi, or other relevant high-performance copper alloys? These materials can be more challenging to print than common steels or titanium. Verify their experience with the specific alloy you intend to use.
- Size and Complexity: Does their prior work include parts of comparable size and geometric complexity to your propeller design? Printing large, intricate shapes requires specific machine capabilities and process control expertise.
2. Appropriate Technology and Equipment:
- AM Process Suitability: Do they offer the right technology? For robust, medium-to-large propellers in NAB or CuNi, Selective Electron Beam Melting (SEBM) often offers advantages in managing residual stress due to its high processing temperatures. Laser Powder Bed Fusion (LPBF) might be suitable for smaller parts or those requiring finer features. Understand the provider’s rationale for recommending a specific process. Met3dp’s specialization in industry-leading SEBM printers makes them a strong candidate for demanding propeller applications.
- Machine Capability: Does their equipment fleet have the necessary build volume (X, Y, Z dimensions) to accommodate your propeller size? Are their machines well-maintained and calibrated for accuracy and repeatability?
- Pulverhantering: Do they have robust procedures for storing, handling, sieving, and recycling metal powders to prevent contamination and ensure consistency? Do they use dedicated machines for reactive or sensitive alloys if necessary?
3. Material Quality Assurance:
- Powder Sourcing: Where do they source their NAB and CuNi powders? Do they work with reputable metal powder suppliers? Do they perform incoming quality checks (e.g., chemistry, PSD, morphology)?
- In-House Powder Production: Providers like Met3dp, who manufacture their own high-quality spherical metal powders using advanced gasatomisering och PREP-teknik, offer a significant advantage. This ensures full traceability, optimized powder characteristics for their machines, and greater control over material quality – a critical factor for demanding applications.
4. Comprehensive Post-Processing Capabilities:
- Integrated Services: Does the provider offer a full suite of necessary post-processing steps in-house or through tightly managed, qualified partners? This includes:
- Controlled atmosphere heat treatment (stress relief, annealing, etc.)
- Precise part removal (Wire EDM capability?)
- Thorough powder removal and cleaning
- Skilled support structure removal
- CNC machining (multi-axis capabilities for complex blade surfaces and features)
- Surface finishing (grinding, polishing to meet hydrodynamic requirements)
- Hot Isostatic Pressing (HIP) availability if required
- Non-Destructive Testing (NDT) facilities (Visual, Dimensional/CMM, DPT, X-ray/CT)
- Dynamic balancing capabilities
- Streamlined Supply Chain: An integrated service offering simplifies project management, reduces logistical complexity, and ensures accountability throughout the manufacturing process.
5. Robust Quality Management System (QMS) and Certifications:
- ISO 9001 Certification: This should be considered a minimum requirement, demonstrating a commitment to standardized processes and quality control.
- Traceability: Can they provide full traceability from the raw powder batch to the final shipped part?
- Marine Classification Experience: If your propeller requires certification by bodies like DNV, ABS, Lloyd’s Register, etc., does the provider have experience with the required qualification procedures, documentation, and testing protocols? Met3dp’s experience in aerospace, medical, and automotive fields demonstrates their capability in handling stringent quality requirements and their readiness to engage in qualification processes for marine applications. Learn about Met3dp’s commitment to quality on their ‘About Us’ page.
- Audits and Transparency: Are they open to customer audits or facility visits for significant projects?
6. Technical Support and Collaboration:
- DfAM Expertise: Do they offer Design for Additive Manufacturing support to help optimize your propeller design for printability, performance, and cost-effectiveness?
- Engineering Access: Are their engineers and technical staff accessible to discuss design challenges, material selection, process parameters, and post-processing strategies?
- Communication: Do they have clear communication protocols and provide regular project updates?
7. Capacity, Lead Times, and Logistics:
- Realistic Timelines: Can they provide and adhere to realistic lead time estimates, considering the entire workflow from order to delivery?
- Capacity Planning: Do they have sufficient machine and personnel capacity to handle your project without significant delays, especially if considering wholesale marine component orders?
- Shipping Expertise: Do they have experience packaging and shipping large, relatively delicate components internationally? (Met3dp’s location in Qingdao, a major port city, is advantageous for global logistics).
Evaluation Checklist Summary:
Criterion | Viktiga överväganden |
---|---|
Erfarenhet | Marine relevance, specific alloy experience (NAB/CuNi), similar part size/complexity |
Teknik | Suitable AM process (SEBM/LPBF), adequate build volume, machine condition |
Materialkvalitet | Reputable powder source (in-house like Met3dp is a plus), QA procedures, handling protocols |
Efterbearbetning | Comprehensive in-house/managed capabilities (Heat Treat, Machining, Finishing, NDT, Balancing) |
Quality System | ISO 9001, traceability, marine certification experience (if needed), audit readiness |
Teknisk support | DfAM services, engineering collaboration, communication clarity |
Capacity & Lead Time | Realistic timelines, adequate capacity, proven delivery performance |
Logistics & Cost | Shipping experience, clear quotation structure, competitive overall value |
Export to Sheets
Choosing the right AM partner is a strategic decision. Thorough vetting using these criteria will help ensure you select a provider like Met3dp, who possesses the technical prowess, quality commitment, and collaborative spirit necessary to successfully deliver high-performance 3D printed marine propellers.
Economic Considerations: Cost Factors and Lead Time Analysis
While the technical advantages of 3D printed marine propellers are compelling, understanding the economic implications – specifically the cost drivers and expected lead times – is crucial for making informed decisions, particularly for procurement managers and project leaders. Metal additive manufacturing presents a different cost structure compared to traditional casting or machining, offering benefits in some scenarios while potentially being more expensive in others.
Key Cost Factors for 3D Printed Propellers:
The final price of a 3D printed propeller is influenced by a complex interplay of factors. A clear understanding of these components is essential when evaluating quotes from additive manufacturing service providers.
- Kostnader för material:
- Powder Price: The cost per kilogram of the chosen metal powder (e.g., CuAl10Fe5Ni5, CuNi30Mn1Fe). Copper alloys, especially high-nickel ones like CuNi30Mn1Fe, tend to be more expensive than standard steels or aluminum alloys.
- Part Volume: The amount of material directly making up the propeller geometry.
- Support Volume: The amount of material used for support structures, which can be significant depending on the design and orientation. DfAM aims to minimize this.
- Återvinning av pulver: While unfused powder is largely recyclable, there are associated costs for sieving, testing, and refreshing the powder stock. Reputable providers factor this efficiency into their pricing.
- AM Machine Time:
- Byggtid: Primarily determined by the height of the build and the volume of material being fused per layer. Factors include layer thickness, scanning speed, and the number of parts nested in a single build.
- Machine Hourly Rate: Covers machine depreciation, energy consumption, inert gas (for LPBF), vacuum systems (for SEBM), maintenance, and operator time. Higher-end industrial machines have higher hourly rates.
- Kostnader för arbetskraft:
- Pre-Processing: CAD file preparation, build simulation, support design, machine setup.
- Machine Operation: Monitoring the build process.
- Post-Processing Labor (Often Significant):
- Part removal from build plate.
- Bulk powder removal and cleaning.
- Support structure removal: This can be highly labor-intensive, especially for complex geometries.
- Manual grinding, sanding, and polishing for surface finishing.
- Inspection and quality control labor.
- Post-Processing Costs (Non-Labor):
- Värmebehandling: Furnace time, energy, controlled atmosphere gases/vacuum.
- Het isostatisk pressning (HIP): Specialized equipment and process cost; can be a significant addition if required.
- CNC Machining: Machine time for achieving critical tolerances and specific surface features. Multi-axis machining adds cost.
- Consumables: Abrasives for finishing, coolants for machining, NDT materials (dyes, films).
- Balancing: Equipment time and skilled labor.
- Quality Assurance and Testing:
- NDT Services: Cost associated with performing DPT, X-ray/CT scans, etc.
- Dimensionell inspektion: CMM machine time, metrology labor.
- Documentation: Generating compliance reports, material certifications, inspection records.
- Overhead and Profit:
- The service provider’s operational overheads (facility, administration, etc.) and profit margin.
- Orderkvantitet:
- Low Volumes (1-10): AM often shines here due to the absence of tooling costs. Setup costs are amortized over fewer parts.
- Medium Volumes: Cost per part decreases as setup costs are spread, and efficiencies might be found in batch post-processing.
- High Volumes: Traditional casting typically becomes more cost-effective per part, though AM costs are continuously improving.
- Wholesale Pricing: For repeat orders or larger batches, suppliers may offer volume discounts or negotiated grossistpriser structures.
Lead Time Analysis:
One of the most significant advantages of AM is often the reduction in lead time compared to traditional methods, especially for custom or low-volume parts.
- Jämförelse:
- Traditional Casting: Requires pattern/mold making (weeks/months), casting (days/weeks), machining/finishing (weeks). Total: Often 8-16 weeks or more.
- Metal AM: Design prep/simulation (days), printing (days to 1-2 weeks depending on size), full post-processing (1-4 weeks depending on complexity). Total: Often 3-8 weeks.
- Typical AM Workflow & Time Estimates (Example – Medium Size Propeller):
- Order Processing & Print Prep: 1-3 days
- Printing (SEBM/LPBF): 3-10 days (highly size/complexity dependent)
- Cooldown & Depowdering: 1 day
- Stress Relief Heat Treatment: 1-2 days (including furnace time)
- Part/Support Removal: 1-3 days
- HIP (if needed): 3-5 days (including logistics to/from HIP provider if outsourced)
- CNC Machining: 2-5 days
- Surface Finishing: 2-7 days (highly dependent on required Ra)
- NDT & Inspection: 1-3 days
- Balancing: 1 day
- Total Estimated: ~3 to 8 weeks
- Factors Influencing AM Lead Time:
- Part Size & Complexity: Larger, more complex parts take longer to print and post-process.
- Machine Availability: Scheduling on appropriate machines.
- Post-Processing Intensity: Extensive machining or polishing significantly adds time. HIP adds significant time.
- QA Requirements: Rigorous NDT and documentation add time.
- Provider’s Workflow Efficiency: How streamlined are their operations?
Total Cost of Ownership (TCO):
It’s crucial to look beyond the initial purchase price. The TCO perspective considers lifetime costs and benefits:
- Potential Savings with AM Propellers:
- Fuel Efficiency: Optimized designs can lead to significant fuel savings over the vessel’s life.
- Reduced Maintenance: Superior materials like CuNi reduce the need for frequent cleaning due to biofouling resistance. Better cavitation resistance (NAB) extends blade life.
- Lower Inventory Costs: On-demand printing of spares eliminates the need to hold expensive physical inventory.
- Minimized Downtime: Faster replacement of damaged propellers gets vessels operational again sooner.
- Calculating TCO: While complex, estimating these lifetime benefits is essential for justifying the investment in potentially higher-cost AM components, particularly for commercial or naval operators and discerning yacht owners.
In conclusion, the economics of 3D printed propellers are favorable for prototypes, custom designs, low-volume production, and situations where speed or unique performance characteristics enabled by AM provide significant value. While material and post-processing costs are key drivers, the dramatically reduced lead times and potential TCO benefits often make AM a compelling economic choice for specific marine applications. Obtaining detailed quotes from experienced providers like Met3dp, outlining all cost components and realistic lead times, is the first step towards making an informed economic evaluation.
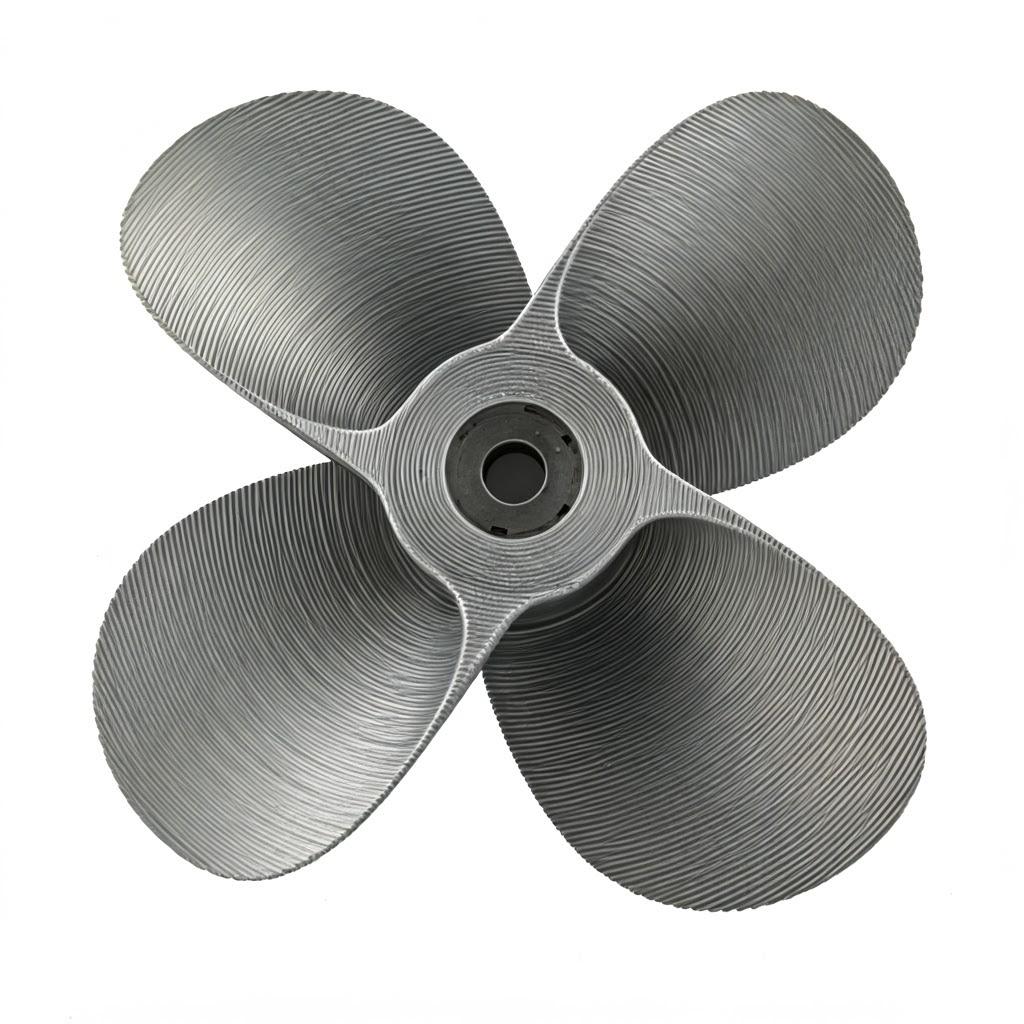
Frequently Asked Questions (FAQ) about 3D Printed Marine Propellers
As metal additive manufacturing gains traction in the maritime industry, engineers, designers, procurement managers, and vessel operators often have questions about the capabilities, limitations, and practicalities of 3D printed propellers. Here are answers to some frequently asked questions:
Q1: Are 3D printed propellers as strong and durable as traditionally cast propellers?
A: Yes, and potentially even stronger and more durable, provided they are designed, manufactured, and post-processed correctly. Here’s why:
- Materialegenskaper: Metal AM processes like SEBM and LPBF, when properly controlled using high-quality powders (like those produced by Met3dp), result in fine-grained microstructures. Fine grains generally lead to higher tensile strength, yield strength, and fatigue strength compared to the coarser grains typical of sand castings.
- Densitet: High-integrity AM processes can achieve part densities exceeding 99.5%, often reaching near 100% density, especially if Hot Isostatic Pressing (HIP) is employed. This minimizes porosity, which can be a weak point in cast components.
- Alloy Performance: Using high-performance alloys like NAB (CuAl10Fe5Ni5) or CuNi (CuNi30Mn1Fe) inherently provides excellent strength, toughness, and resistance to corrosion and cavitation.
- Design Optimization (DfAM): AM allows designs to be optimized for stress distribution, potentially reducing peak stresses compared to designs constrained by casting limitations.
- Critical Factor: The key is rigorous process control, validated material properties, appropriate post-processing (especially heat treatment and potentially HIP), and thorough Non-Destructive Testing (NDT) to ensure the absence of critical defects. When these steps are followed by experienced providers, AM propellers can meet or exceed the performance of their cast counterparts and conform to relevant marine standards.
Q2: What is the maximum size of a propeller that can be 3D printed?
A: This is constantly evolving as AM technology advances.
- Current PBF Limits: Most current industrial metal PBF machines (LPBF and SEBM) have build envelopes typically ranging up to roughly 500mm x 500mm x 500mm, with some larger frame machines reaching towards 800mm or even 1000mm in one dimension. This allows for the production of propellers suitable for many small-to-medium sized vessels, USVs, AUVs, and yacht applications. Met3dp offers industry-leading print volumes within the SEBM category, pushing these boundaries.
- Very Large Propellers: Propellers for large commercial ships (often several meters in diameter) are generally still beyond the practical size limits of single-piece PBF printing.
- Alternative Methods:
- Directed Energy Deposition (DED) / Wire Arc Additive Manufacturing (WAAM): These AM processes are not confined by a powder bed and can theoretically produce much larger parts, though typically with lower resolution and potentially requiring more final machining. They are actively being explored for large marine components.
- Sectional Printing: Printing a large propeller in multiple sections and then joining them (e.g., via welding) is another potential approach, although this introduces complexities related to joint integrity and qualification.
- Outlook: The trend is towards larger AM machine build volumes, so the maximum printable size will likely continue to increase.
Q3: Can existing propeller designs originally made for casting be easily adapted for 3D printing?
A: While technically possible to print a propeller directly from an existing CAD model (or one created by reverse-engineering/3D scanning an existing part), it’s often not the optimal approach.
- Missed Opportunities: Simply replicating a cast design fails to leverage the key advantages of AM, such as geometric freedom for hydrodynamic optimization, lightweighting potential, or integrated features.
- Potential Issues: Designs optimized for casting might include features (like large flat sections or specific draft angles) that are difficult or inefficient to print using AM or may require excessive support structures.
- Recommendation: Redesign (DfAM): The best practice is to use the existing design as a baseline but then re-evaluate and optimize it using Design for Additive Manufacturing (DfAM) principles. This involves collaborating with AM experts to tailor the geometry for better performance, reduced weight, minimized supports, and improved printability. This unlocks the true value of adopting AM.
Q4: How does the cost of 3D printing compare to traditional casting for propellers?
A: There’s no single answer; it depends heavily on several factors:
- Prototypes, One-Offs, Custom Designs: For single pieces or very small quantities (<5-10), AM is almost always snabbare och mer kostnadseffektivt because it eliminates the high upfront cost and long lead time associated with creating patterns and molds for casting.
- Komplexa geometrier: If the propeller design is highly complex (e.g., intricate blade shapes, internal features), AM can be more economical than casting and extensive multi-axis machining, as complexity adds relatively little cost to the AM process itself (though it may increase post-processing needs).
- Low-to-Medium Volume (e.g., 10-100 units): This is a gray area where the cost comparison depends heavily on the part’s size, complexity, material, and the specific casting method being compared. A detailed cost-benefit analysis is needed.
- High Volume (>100s or 1000s) & Simple Designs: For large quantities of relatively simple, standardized propeller designs, traditional casting methods generally remain more cost-effective per part due to well-established economies of scale.
- TCO Matters: Remember to consider the Total Cost of Ownership (TCO). Higher initial AM cost might be offset by lifetime benefits like fuel savings or reduced maintenance.
Q5: Can 3D printed propellers receive classification society approval (e.g., from DNV, ABS, Lloyd’s Register)?
A: Yes, achieving class approval for 3D printed marine components, including propellers, is becoming increasingly feasible, though it requires a rigorous process.
- Guidelines Exist: Major classification societies have published guidelines and frameworks for qualifying AM parts, materials, and manufacturers (e.g., DNVGL-CG-0197, ABS Guide for Additive Manufacturing).
- Rigorous Qualification: The process typically involves:
- Manufacturer Qualification: Auditing the AM service provider’s facilities, QMS, processes, and personnel competence.
- Material Specification: Defining and testing the properties of the specific powder batch used.
- Processkvalificering: Qualifying the specific AM machine and locked-down parameters used for production.
- Part Qualification: Extensive NDT and mechanical testing (tensile, fatigue, impact, corrosion) on witness coupons printed alongside the part and potentially on the part itself.
- Documentation: Comprehensive records tracking the entire process from powder to finished part.
- Collaboration is Key: Achieving class approval requires close collaboration between the designer, the AM provider (like Met3dp, who is experienced with stringent quality demands), and the classification society from the early stages of the project. It adds time and cost but is essential for ensuring the highest levels of safety and reliability for critical applications.
Q6: How does the biofouling resistance of a 3D printed Copper-Nickel (CuNi) propeller compare to a traditional cast or wrought CuNi part?
A: The inherent biofouling resistance of CuNi alloys stems from their chemical composition and the way they interact with seawater to form a specific protective copper-oxide surface layer. Therefore, a 3D printed CuNi propeller should exhibit comparable excellent biofouling resistance to its traditionally manufactured counterparts, assuming:
- Correct Alloy Composition: The AM powder (e.g., CuNi30Mn1Fe) meets the required chemical specifications.
- Dense Microstructure: The AM process achieves a fully dense part without significant porosity that could alter surface chemistry or provide attachment points.
- Appropriate Surface Condition: The final surface finish after post-processing is suitable. Extremely rough surfaces might initially offer more texture for settlement, but the fundamental material property should dominate.
- Potential for Enhancement? AM might even offer future possibilities to create specific micro-textures on the surface during printing, potentially further enhancing biofouling resistance, although this is an area of ongoing research.
Having these questions answered should provide greater clarity and confidence for organizations considering the adoption of 3D printed marine propellers using advanced alloys like NAB and CuNi.
Conclusion: Charting the Future of Marine Propulsion with Met3dp
The adoption of metal additive manufacturing marks a significant inflection point in the evolution of marine propulsion technology. As we’ve explored throughout this discussion, 3D printing, particularly using high-performance alloys like Nickel-Aluminium Bronze (CuAl10Fe5Ni5) and Copper-Nickel (CuNi30Mn1Fe), offers a powerful suite of advantages that directly address the ongoing demands for higher efficiency, greater customization, reduced environmental impact, and more resilient supply chains within the maritime industry.
För engineers and naval architects, metal AM unlocks an unprecedented level of design freedom. It liberates propeller design from the constraints of traditional casting molds and machining access, enabling the creation of highly optimized, complex geometries tailored to specific vessel hydrodynamics. This translates into tangible benefits: improved fuel efficiency through advanced blade profiles, reduced cavitation and noise via sophisticated edge and tip designs, and the potential for lighter, integrated propulsion components. The ability to rapidly prototype and test functional designs accelerates innovation cycles, pushing the boundaries of what’s possible in marine propulsion performance.
För procurement managers, shipyards, and fleet operators, metal AM presents compelling strategic advantages. The tool-less nature of the technology dramatically reduces lead times for custom or low-volume propellers, transforming the economics of niche applications and bespoke vessel construction. On-demand manufacturing capabilities allow for the production of spare parts precisely when needed, minimizing costly inventory and reducing vessel downtime significantly – a critical factor for operational readiness and profitability. This technology empowers a more agile and responsive supply chain, capable of addressing obsolescence challenges for legacy systems and enabling localized production. Evaluating the Total Cost of Ownership (TCO), including performance gains and maintenance reductions, often reveals a strong value proposition for AM beyond the initial part cost, especially when dealing with suppliers focused on wholesale marine components.
However, successfully harnessing this transformative potential requires navigating the complexities of DfAM, material science, process control, and extensive post-processing. This underscores the critical importance of choosing the right manufacturing partner.
Met3dp stands ready to be that strategic partner. We offer more than just printing services; we provide comprehensive additiv tillverkningslösningar built on a foundation of deep expertise and cutting-edge technology. Our strengths align perfectly with the demands of producing high-quality marine propellers:
- Advanced SEBM Technology: Our industry-leading Selective Electron Beam Melting printers are ideally suited for producing robust, low-stress parts from challenging materials like NAB and CuNi, delivering exceptional accuracy and reliability.
- High-Performance Metal Powders: As a producer of our own powders using state-of-the-art Gas Atomization and PREP technologies, we ensure the highest quality, consistency, and traceability for materials critical to marine performance.
- Material & Application Expertise: With decades of collective experience, our team collaborates with clients on DfAM, material selection, process optimization, and navigating qualification pathways.
- Integrated Approach: We understand the entire manufacturing workflow, from powder to finished, balanced, and inspected propeller, ensuring quality and accountability at every stage.
The future of marine propulsion is undoubtedly intertwined with the advancement of digital manufacturing technologies like metal AM. By embracing this innovation, stakeholders across the maritime sector can achieve new levels of performance, efficiency, and operational flexibility.
Are you ready to explore how 3D printed propellers can revolutionize your marine application? Whether you are designing a custom yacht, developing advanced USVs, seeking performance upgrades for workboats, or needing solutions for obsolete parts, Met3dp has the expertise and technology to help you succeed.
Contact Met3dp today to discuss your project requirements with our additive manufacturing specialists and discover how our capabilities can power your organization’s journey into the next generation of marine propulsion. We welcome inquiries from engineers, procurement managers, shipyards, marine propeller suppliers, och marine parts distributors looking to leverage the power of metal 3D printing.
Dela på
MET3DP Technology Co, LTD är en ledande leverantör av lösningar för additiv tillverkning med huvudkontor i Qingdao, Kina. Vårt företag är specialiserat på 3D-utskriftsutrustning och högpresterande metallpulver för industriella tillämpningar.
Förfrågan för att få bästa pris och anpassad lösning för ditt företag!
Relaterade artiklar
Om Met3DP
Senaste uppdateringen
Vår produkt
KONTAKTA OSS
Har du några frågor? Skicka oss meddelande nu! Vi kommer att betjäna din begäran med ett helt team efter att ha fått ditt meddelande.
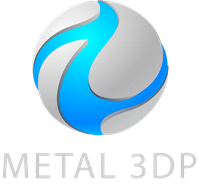
Metallpulver för 3D-printing och additiv tillverkning