The process flow of Material Jetting
Innehållsförteckning
Imagine a printer that doesn’t just lay down ink on paper, but builds intricate objects layer by layer, like a tiny sculptor wielding liquid building blocks. That’s the essence of material jetting, a revolutionary 3D printing technology that’s transforming design and manufacturing across industries.
Material Jetting: A Miniature Inkjet Revolution
Material jetting works similarly to your everyday inkjet printer. But instead of colored inks, it utilizes a dazzling array of materials like photopolymers, waxes, and even metals. These materials are deposited in tiny droplets from a printhead, solidifying rapidly under UV light or heat to create each layer of your desired object. Think of it as meticulously painting a 3D masterpiece, one layer at a time.
The Intricate Dance of Material Jetting
Now, let’s delve into the fascinating choreography that brings your 3D vision to life:
1. Prepping the Stage: Setting Up for Success
The journey begins with a virtual model sliced into thin digital layers. Imagine a loaf of bread meticulously cut into horizontal slices – each slice represents a layer your printer will build upon.
2. Material Selection: Choosing the Right Building Blocks
Next, comes the crucial selection of materials. The type of material you choose depends on the desired properties of your final product. Do you need a strong and durable object? Opt for metal powders. High detail and vibrant colors? Photopolymers are your pick.
3. Material Jetting in Action: Layering the Magic
The printhead, equipped with hundreds of tiny nozzles, precisely jets droplets of your chosen material onto the build platform. Just like an inkjet printer, it follows the digital blueprint, meticulously building each layer upon the previous one.
4. Solidification: Locking in the Form
As each layer is deposited, it undergoes a rapid transformation. Photopolymers are cured by UV light, while metal powders might be fused using heat or a combination of light and heat. This solidifies the material, locking in the desired shape.
5. The Grand Reveal: Post-Processing for Perfection
Once the final layer is complete, the build platform descends, revealing your newly created object bathed in a pool of unutilized material. This excess material will be removed through a post-processing stage, which might involve cleaning, support removal (for parts with overhangs), and additional finishing touches.
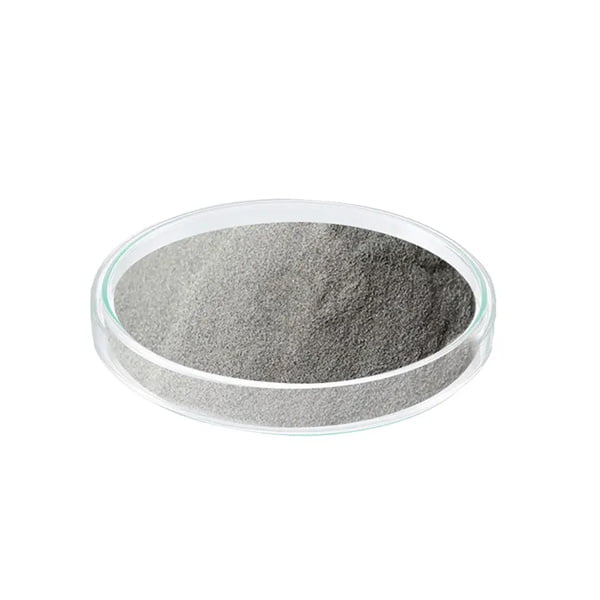
detailed introduction of Jetting av material Metallpulver
Material jetting’s ability to utilize metal powders opens doors to a whole new realm of possibilities. Here are some of the most popular metal powders used in this process, along with their key characteristics:
Material | Beskrivning | Fastigheter |
---|---|---|
Rostfritt stål 17-4 PH | A versatile and widely used option, offering good strength, corrosion resistance, and biocompatibility. | Ideal for functional prototypes, aerospace components, and medical devices. |
Inconel 625 | A high-performance nickel-chromium alloy boasting exceptional strength, heat resistance, and corrosion resistance. | Perfect for demanding applications like jet engine components and high-temperature tools. |
Titan 6Al-4V (klass 23) | A lightweight and biocompatible titanium alloy offering excellent strength-to-weight ratio. | Widely used in aerospace, medical implants, and sporting goods due to its lightweight and biocompatible nature. |
Koppar | A highly conductive metal perfect for applications requiring excellent electrical properties. | Used for creating electrical components, heat exchangers, and prototypes requiring high conductivity. |
Maråldrat stål | A family of steels known for their high strength and toughness achieved through a unique aging process. | Ideal for creating strong and lightweight tools, gears, and structural components. |
Nickel | A pure nickel powder offering good corrosion resistance and ductility. | Used for creating electroplating molds, electrodes, and components requiring good machinability. |
Guld | A precious metal prized for its aesthetics and electrical conductivity. | Often used for creating jewelry prototypes, decorative elements, and electrical contacts. |
Silver | Another precious metal known for its excellent electrical conductivity and reflectivity. | Used for creating electrical components, jewelry prototypes, and highly reflective surfaces. |
Aluminium | A lightweight and readily available metal offering good formability and machinability. | Ideal for creating lightweight prototypes, heat sinks, and non-critical structural components (compared to other metals on this list). |
Kovar | A controlled expansion alloy with a thermal expansion coefficient that closely matches glass. | Used for creating glass-to-metal seals in electronic devices and scientific instruments. |
Advantages and Considerations of Material Jetting
Material jetting boasts several advantages that make it a compelling choice for a variety of applications:
- High Resolution and Accuracy: Thanks to the precise jetting of materials, material jetting can produce parts with exceptional detail and dimensional accuracy. This makes it ideal for creating intricate prototypes, detailed models, and functional parts with tight tolerances.
- Brett utbud av material: As we’ve explored, material jetting offers a diverse selection of materials, from photopolymers with vibrant colors to robust metals for functional applications. This versatility allows you to create objects with the specific properties needed for your project.
- Multi-Material Capability: Some advanced material jetting systems can even utilize multiple materials within a single build. Imagine creating a part with a rigid metal core and a flexible, rubber-like outer layer – all printed in one go! This opens doors for innovative designs with complex functionalities.
- Fast Turnaround Times: Compared to traditional manufacturing methods, material jetting allows for rapid prototyping and creation of small-batch production runs. This can significantly accelerate your design and development process.
- Smooth Surface Finishes: Material jetting often produces parts with smooth surface finishes, reducing the need for extensive post-processing. This can be a major advantage for applications where aesthetics are important.
However, like any technology, material jetting comes with its own set of considerations:
- Build Volume Limitations: Material jetting printers typically have smaller build volumes compared to some other 3D printing technologies. This might limit the size of parts you can create.
- Kostnader för material: Metal powders and some high-performance photopolymers can be relatively expensive compared to materials used in other 3D printing methods. This can factor into the overall cost of your project.
- Krav på efterbearbetning: While material jetting often produces parts with good surface finishes, some post-processing like support removal and cleaning might still be necessary, depending on the complexity of your design.
- Stödstrukturer: For parts with overhangs or complex geometries, support structures might be required during printing. These temporary structures need to be removed after printing, which can add time and complexity to the process.
Tillämpningar av Jetting av material
Material jetting finds applications across a diverse range of industries, each leveraging its unique capabilities:
- Aerospace: Prototyping lightweight and high-strength components for aircraft, satellites, and spacecraft.
- Fordon: Creating functional prototypes and end-use parts for cars, motorcycles, and other vehicles.
- Medicinsk: Manufacturing biocompatible implants, dental prosthetics, and surgical instruments.
- Konsumentvaror: Developing prototypes and producing small-batch runs of jewelry, eyewear, and other consumer products.
- Elektronik: Creating intricate electrical components, circuit boards, and connectors.
Material Jetting vs. Other 3D Printing Methods
When choosing a 3D printing technology, it’s crucial to understand how material jetting stacks up against its competitors. Here’s a quick comparison:
- Fused Deposition Modeling (FDM): FDM is a popular and affordable technology that uses filament to create parts layer by layer. However, FDM generally offers lower resolution and a more limited material selection compared to material jetting.
- Selektiv lasersintring (SLS): SLS utilizes a laser to sinter powdered materials together. It can create strong and functional parts, but often with a rougher surface finish compared to material jetting.
- Stereolitografi (SLA): Similar to material jetting, SLA uses a laser to cure liquid photopolymers. However, SLA printers typically have smaller build volumes and might require more extensive post-processing steps.
The Future of Material Jetting
Material jetting is a rapidly evolving technology. Here are some exciting trends to keep an eye on:
- Development of New Materials: Researchers are constantly developing new materials for material jetting, including biocompatible options for advanced medical applications and even conductive materials for creating functional electronics directly from the printer.
- Increased Build Volumes: As technology advances, we can expect to see material jetting printers with larger build volumes, opening doors for creating even bigger and more complex objects.
- Multi-Material Advancements: Expect to see even more sophisticated multi-material capabilities, allowing for the creation of parts with a wider range of functionalities and properties within a single build.
VANLIGA FRÅGOR
A: Material jetting offers high resolution and accuracy, a wide range of materials, multi-material capability, fast turnaround times, and smooth surface finishes.
Q: What are some limitations of material jetting?
A: Material jetting typically has smaller build volumes compared to other technologies, and some materials can be expensive. Additionally, post-processing might be required, support structures can add complexity, and material jetting may not be suitable for large-scale production runs.
Q: What industries use material jetting?
A: Material jetting finds applications in aerospace, automotive, medical, consumer goods, electronics, and many more.
Q: Hur är materialjetting jämfört med andra 3D-utskriftstekniker?
A: Compared to FDM, material jetting offers higher resolution and more material options. It provides smoother finishes than SLS and can be faster than SLA, though SLA printers might have higher resolution in some cases.
Q: What’s the future outlook for material jetting?
A: The future of material jetting is bright, with advancements in material development, increased build volumes, and even more sophisticated multi-material capabilities on the horizon.
Slutsats
Material jetting stands as a powerful tool for designers, engineers, and innovators across industries. Its ability to produce high-resolution, multi-material parts with diverse properties makes it ideal for prototyping, creating functional end-use parts, and even pushing the boundaries of design. As the technology continues to evolve, we can expect even more exciting possibilities to emerge, transforming the way we design and manufacture objects in the years to come.
So, if you’re looking for a 3D printing technology that offers exceptional detail, versatility, and speed, material jetting might be the perfect fit for your next project. With its ever-expanding capabilities, material jetting is poised to play a pivotal role in shaping the future of manufacturing and product development.
Dela på
MET3DP Technology Co, LTD är en ledande leverantör av lösningar för additiv tillverkning med huvudkontor i Qingdao, Kina. Vårt företag är specialiserat på 3D-utskriftsutrustning och högpresterande metallpulver för industriella tillämpningar.
Förfrågan för att få bästa pris och anpassad lösning för ditt företag!
Relaterade artiklar
Om Met3DP
Senaste uppdateringen
Vår produkt
KONTAKTA OSS
Har du några frågor? Skicka oss meddelande nu! Vi kommer att betjäna din begäran med ett helt team efter att ha fått ditt meddelande.
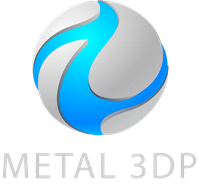
Metallpulver för 3D-printing och additiv tillverkning
FÖRETAG
PRODUKT
cONTACT INFO
- Qingdao City, Shandong, Kina
- [email protected]
- [email protected]
- +86 19116340731