metallpulver för fordonsindustrin
Innehållsförteckning
Föreställ dig en bil som är lättare än någonsin tidigare, men med överlägsen styrka och förbättrad bränsleeffektivitet. Det här är inte science fiction; det är verkligheten med metallpulverteknik inom bilindustrin. Metallpulver för bilindustrin är finmalda metallpartiklar som revolutionerar hur bilar designas och tillverkas.
Denna omfattande guide dyker djupt in i världen av metallpulver för fordonsindustrin applikationer. Vi kommer att utforska de olika typerna av metallpulver, deras egenskaper och hur de används för att skapa nästa generations bildelar. Vi kommer också att fördjupa oss i fördelarna och begränsningarna med metallpulver, jämföra specifika modeller och svara på vanliga frågor. Så, spänn fast dig och gör dig redo att utforska den fascinerande världen av metallpulver inom fordonsindustrin!
Typer, sammansättning, egenskaper och egenskaper hos metallpulver för fordonstillämpningar
Metallpulver finns i en mängd olika smaker, var och en med unika egenskaper som gör dem idealiska för specifika fordonstillämpningar. Här är en uppdelning av några av de vanligaste typerna:
Metallpulver Typ | Sammansättning | Fastigheter | Egenskaper |
---|---|---|---|
Järnbaserade pulver | Främst järn, med legeringselement som nickel, koppar eller molybden | Hög hållfasthet, bra slitstyrka, utmärkt bearbetningsförmåga | Mångsidig; används i ett brett utbud av bildelar |
Stålpulver | Järn och kol, med ytterligare legeringselement beroende på önskad ståltyp | Brett utbud av egenskaper beroende på det specifika stålet; generellt hög hållfasthet, god slitstyrka och utmärkt formbarhet | Erbjuder ett bredare spektrum av egenskaper jämfört med järnbaserade pulver |
Aluminiumbaserade pulver | Främst aluminium, med legeringselement som kisel, magnesium eller koppar | Låg vikt, god korrosionsbeständighet, hög värmeledningsförmåga | Idealisk för applikationer där viktminskning är avgörande |
Nickelbaserade pulver | Främst nickel, med legeringselement som krom, molybden eller volfram | Utmärkt hållfasthet vid höga temperaturer, god korrosionsbeständighet | Används i krävande applikationer som motorkomponenter som utsätts för höga temperaturer |
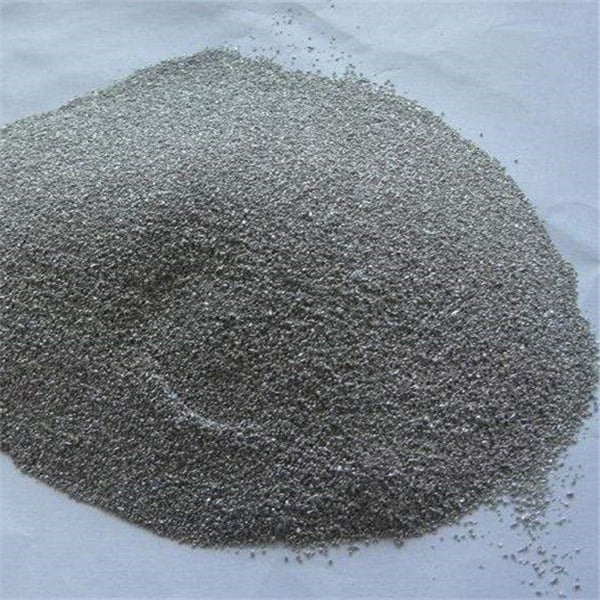
Utöver dessa grundläggande typer finns det många specialmetallpulver:
- Pulver av rostfritt stål: Erbjuder överlägsen korrosionsbeständighet för delar som utsätts för tuffa miljöer.
- Kopparpulver: Utmärkt elektrisk ledningsförmåga, vilket gör dem idealiska för elektriska komponenter.
- Titanpulver: Högt hållfasthet-till-viktförhållande och utmärkt korrosionsbeständighet, men tenderar att bli dyrare.
När du väljer ett metallpulver för en bilapplikation måste flera faktorer beaktas:
- Önskade egenskaper: Styrka, slitstyrka, vikt, korrosionsbeständighet och värmeledningsförmåga är alla avgörande faktorer.
- Delkomplexitet: Vissa metallpulver är bättre lämpade för intrikata former jämfört med andra.
- Kostnad: Metallpulverpriserna varierar beroende på pulvrets typ och komplexitet.
Tillämpningar av metallpulver i biltillverkning
Metallpulver letar sig in i ett ständigt ökande antal bildelar. Här är några av de vanligaste applikationerna:
Fordonskomponent | Metallpulvertyp(er) | Fördelar |
---|---|---|
Motorkomponenter | Järnbaserad, stål, nickelbaserad | Lättare vikt förbättrar bränsleeffektiviteten; hög hållfasthet säkerställer hållbarhet |
Växellådans växlar | Järnbaserad, stål | Hög hållfasthet och slitstyrka för smidiga växlingar |
Bromskomponenter | Järnbaserad, stål | Hög slitstyrka för längre bromslivslängd |
Upphängningsdelar | Järnbaserad, aluminiumbaserad | Lättare vikt minskar ofjädrad massa för bättre hantering |
Kroppsdelar | Aluminiumbaserad | Lättviktskonstruktion förbättrar bränsleeffektiviteten |
Elektriska komponenter | Koppar, järnbaserad | Förbättrad ledningsförmåga för bättre elektrisk prestanda |
Användningen av metallpulver i biltillverkning erbjuder flera fördelar:
- Viktminskning: Metallpulver kan avsevärt minska vikten på bildelar, vilket leder till förbättrad bränsleeffektivitet och hantering.
- Designflexibilitet: Metallpulver möjliggör skapandet av komplexa former som är svåra eller omöjliga att uppnå med traditionella tillverkningsmetoder.
- Materialeffektivitet: Metallpulverprocesser genererar minimalt med avfall, vilket gör dem till ett miljövänligt alternativ.
- Hög precision: Metallpulverdelar kan tillverkas med hög dimensionsnoggrannhet.
- Förbättrad prestanda: Metallpulver kan ge överlägsen styrka, slitstyrka och andra prestandaegenskaper jämfört med traditionella material.
Men metallpulverteknik har också några begränsningar:
- Kostnad: Metallpulver kan vara dyrare än traditionella material, även om kostnaden minskar när tekniken mognar.
- Begränsad delstorlek: Nuvarande teknik har begränsningar för storleken på delar som kan tillverkas med metallpulver.
- Ytfinish: Metallpulverdelar kan kräva ytterligare efterbehandlingsprocesser för att uppnå önskad ytkvalitet.
Specifika metallpulvermodeller för fordonstillämpningar
Med en uppsjö av metallpulveralternativ tillgängliga, här är en närmare titt på tio specifika modeller som vanligtvis används inom bilindustrin:
- Höganäs Atomized AM 301: Detta järnbaserade pulver från Höganäs AB är ett arbetshästmaterial för fordonsapplikationer. Den har utmärkt kompressibilitet och flytbarhet, vilket gör den idealisk för komplexa former i stora produktionsserier. AM 301 erbjuder god grönstyrka för enkel hantering och minimal delförvrängning under sintring. Typiska applikationer inkluderar strukturella komponenter, växlar och motordelar.
- AMPO CP-1: Detta vattenatomiserade järnpulver från AMPO ger en hög renhetsgrad och en sfärisk partikelform. Den sfäriska formen förbättrar packningsdensiteten, vilket leder till förbättrade mekaniska egenskaper i den sista delen. CP-1 är känt för sin utmärkta bearbetbarhet, vilket gör den lämplig för delar som kräver efterbearbetning för snäva toleranser. Tillämpningar inkluderar växlar, kedjehjul och kopplingskomponenter.
- Snickare Invar® AM 360: Detta specialmetallpulver från Carpenter Additive Division är en nickel-järnlegering känd för sin exceptionella dimensionsstabilitet. Invar® AM 360 har en mycket låg termisk expansionskoefficient, vilket innebär att den expanderar eller drar ihop sig minimalt med temperaturförändringar. Detta gör den idealisk för motorkomponenter som upplever betydande temperaturfluktuationer under drift.
- BASF Aluminium SC1: Detta aluminiumlegeringspulver från BASF erbjuder en bra balans mellan styrka och duktilitet. SC1-beteckningen hänvisar till närvaron av kisel och koppar som legeringselement, vilket ökar styrkan och gjutbarheten. SC1 är ett populärt val för lätta strukturella komponenter som fästen och höljen på grund av dess utmärkta vikt-till-hållfasthet-förhållande.
- LPW Titanium Ti-6Al-4V ELI: Detta gasatomiserade titanpulver från LPW är industristandarden för additiv tillverkning av högpresterande titandelar. Ti-6Al-4V ELI (Extra Low Interstitials) erbjuder exceptionellt förhållande mellan styrka och vikt, utmärkt korrosionsbeständighet och biokompatibilitet. Tillämpningar inkluderar krävande komponenter som flygdelar, motorkomponenter och proteser.
- ExOne M2 Bronze C834: Detta koppar-tennlegeringspulver från ExOne är ett mångsidigt alternativ för bussningar, lager och slitplattor. Tillsatsen av tenn till koppar förbättrar slitstyrkan och smörjigheten. M2 Bronze C834 delar kan vara självsmörjande, vilket minskar behovet av externa smörjmedel, vilket är ett plus för miljövänliga applikationer.
- Sandvik Osprey® 250: Detta kväveatomiserade rostfria stålpulver från Sandvik erbjuder överlägsen korrosionsbeständighet jämfört med vanliga rostfria stål. Kväveatomiseringsprocessen minimerar syrehalten, vilket leder till förbättrad övergripande delprestanda. Osprey® 250 används för delar som utsätts för tuffa miljöer, såsom avgaskomponenter och underredeskomponenter.
- GKN Hoeganaes AMBase 100: Detta järn-nickellegeringspulver från GKN Hoeganaes är designat speciellt för tillsatstillverkning med laserstrålesmältning (LBM). AMBase 100 erbjuder hög hållfasthet och god duktilitet, vilket gör den lämplig för ett brett utbud av strukturella komponenter. Den höga nickelhalten förbättrar korrosionsbeständigheten, vilket gör den till ett bra val för delar som utsätts för fukt eller vägsalt.
- Momentiv MX1: Detta specialmetallpulver från Momentive är ett råmaterial för bunden metallformsprutning (MIM). MIM möjliggör skapandet av komplexa, nästan nätformade delar med god dimensionell noggrannhet. MX1 är en förblandad blandning av metallpulver och ett polymert bindemedel, vilket förenklar MIM-processen för högvolymproduktion. Tillämpningar inkluderar kugghjul, fästelement och små elektroniska komponenter.
- Merck SCC mjuka metallpulver: Detta sortiment av metallpulver från Merck inkluderar koppar-, silver- och tennalternativ. Dessa mjuka metallpulver används ofta för elektriska applikationer på grund av deras utmärkta ledningsförmåga. I bilapplikationer kan SCC Soft Metal Powders hittas i kopplingar, borstar och kylflänsar.
Att välja rätt metallpulver för en specifik fordonstillämpning kräver noggrant övervägande av de önskade egenskaperna, delens komplexitet och kostnadsfaktorer. Genom att förstå de tillgängliga alternativen och deras unika egenskaper kan ingenjörer utnyttja metallpulverteknik för att skapa nästa generations fordonskomponenter som är lättare, starkare och mer effektiva.
Fördelar och begränsningar med Metallpulver för bilar Tillämpningar
Fördelar:
- Viktminskning: Metallpulver kan avsevärt minska komponentvikten, vilket leder till förbättrad bränsleeffektivitet och hantering. En studie av Aluminum Manufacturers Association: visade att utbyte av stålkomponenter med aluminiumekvivalenter i en bil kan leda till en viktminskning på upp till 400 pund, vilket översätter till betydande bränslebesparingar.
- Designflexibilitet: Tillverkning av metallpulvertillsatser möjliggör skapandet av komplexa former som är svåra eller omöjliga att uppnå med traditionella tillverkningsmetoder. Detta öppnar dörrar för innovativ lättviktsdesign och förbättrad delfunktionalitet.
- Materialeffektivitet: Metallpulverprocesser genererar minimalt avfall jämfört med traditionella subtraktiva tillverkningstekniker som bearbetning. Detta leder till lägre materialkostnader och en mer miljövänlig produktionsprocess.
- Hög precision: Tillverkning av metallpulvertillsatser kan producera delar med hög dimensionsnoggrannhet och utmärkt ytfinish, vilket minskar behovet av efterbearbetningssteg.
- Förbättrad prestanda: Metallpulver kan erbjuda överlägsna egenskaper jämfört med traditionella material. Till exempel har vissa metallpulver högre styrka-till-vikt-förhållanden, bättre slitstyrka eller förbättrad värmeledningsförmåga, vilket leder till förbättrad prestanda i den slutliga komponenten.
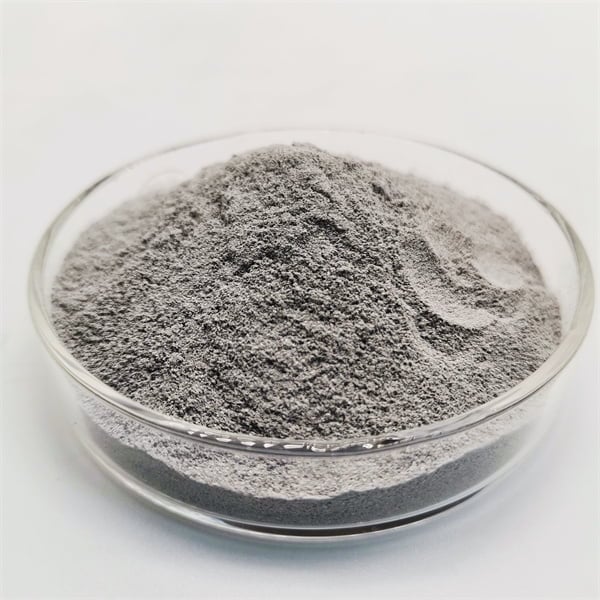
Begränsningar:
- Kostnad: Metallpulver kan vara dyrare än traditionella material, särskilt för stora produktionsserier. Kostnaden för metallpulver i sig kan vara högre, och additiv tillverkningsutrustning kan också vara en betydande investering.
- Begränsad delstorlek: Den nuvarande tekniken för tillverkning av metallpulvertillsatser har begränsningar för storleken på de delar som kan produceras. Detta begränsar tillämpningen av metallpulverteknik för större bilkomponenter som chassi eller karosspaneler.
- Ytfinish: Även om metallpulverdelar kan uppnå god ytkvalitet, kan vissa applikationer kräva ytterligare efterbehandlingsprocesser för att uppfylla specifika estetiska eller funktionella krav. Detta ökar den totala produktionstiden och kostnaden.
- Processbegränsningar: Tillverkningsprocesser för metallpulvertillsats kan vara långsammare än traditionella produktionstekniker med hög volym. Dessutom utvecklas kvalitetskontrollprocedurer för tillverkning av metallpulvertillsatser fortfarande för att säkerställa konsekvent detaljkvalitet.
Trots dessa begränsningar går metallpulverteknologin snabbt framåt, och kostnaden minskar stadigt. När tekniken mognar kan vi förvänta oss att se en bredare användning av metallpulver inom biltillverkning, vilket leder till lättare, starkare och effektivare fordon.
VANLIGA FRÅGOR
F: Vilka är miljöfördelarna med att använda metallpulver i biltillverkning?
S: Metallpulverprocesser genererar minimalt avfall jämfört med traditionella tillverkningsmetoder. Detta minskar bilproduktionens miljöpåverkan. Dessutom kan viktminskningen som uppnås med metallpulver leda till förbättrad bränsleeffektivitet, vilket minskar CO2-utsläppen under fordonsdrift.
F: Är metallpulver säkert att använda vid biltillverkning?
S: Metallpulver i sig kan utgöra vissa hälsorisker om de andas in. Men korrekta säkerhetsprotokoll och ventilationssystem implementeras i tillverkningsanläggningar för metallpulvertillsats för att skydda arbetarna. De slutliga metalldelarna som produceras är i allmänhet säkra för användning i bilar.
F: Hur starka är metallpulverdelar jämfört med traditionellt tillverkade delar?
S: Styrkan hos metallpulverdelar kan vara lika med eller till och med överstiga den hos traditionellt tillverkade delar, beroende på det specifika metallpulver och tillverkningsprocess som används. Metallpulverdelar kan uppnå hög densitet och utmärkt bindning mellan partiklar, vilket leder till överlägsna hållfasthetsegenskaper.
F: Kommer metallpulverbilar att bli mainstream i framtiden?
S: När metallpulvertekniken utvecklas och kostnaderna blir mer konkurrenskraftiga är det troligt att metallpulver kommer att spela en betydande roll i framtiden för biltillverkning. Potentialen för viktminskning, designflexibilitet och förbättrad prestanda gör metallpulver till ett attraktivt alternativ för att skapa nästa generations fordon.
Dela på
MET3DP Technology Co, LTD är en ledande leverantör av lösningar för additiv tillverkning med huvudkontor i Qingdao, Kina. Vårt företag är specialiserat på 3D-utskriftsutrustning och högpresterande metallpulver för industriella tillämpningar.
Förfrågan för att få bästa pris och anpassad lösning för ditt företag!
Relaterade artiklar
Om Met3DP
Senaste uppdateringen
Vår produkt
KONTAKTA OSS
Har du några frågor? Skicka oss meddelande nu! Vi kommer att betjäna din begäran med ett helt team efter att ha fått ditt meddelande.
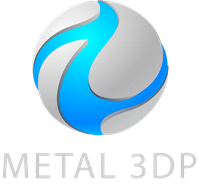
Metallpulver för 3D-printing och additiv tillverkning