Tillämpningar för 3D-utskrift med flera material
Innehållsförteckning
3D printing has revolutionized the manufacturing industry, offering unprecedented flexibility and efficiency. Among its most exciting advancements is multi-material 3D printing. This technology allows for the simultaneous use of different materials within a single print job, opening up new possibilities for creating complex and functional objects. In this article, we will explore the applications of multi-material 3D printing, focusing on its advantages, disadvantages, specific metal powder models, and more.
Overview of Multi-Material 3D Printing
Multi-material 3D printing involves the use of two or more materials in a single printing process. This capability allows for the creation of objects with varying properties, such as different colors, textures, mechanical strengths, and electrical conductivity. The technology is particularly useful in fields like aerospace, automotive, medical, and consumer products, where components often need to combine diverse material properties.
Key Details of Multi-Material 3D Printing
- Teknik: Uses multiple materials in one print job.
- Fördelar: Enhanced functionality, complex designs, improved product performance.
- Material: Metals, polymers, ceramics, composites.
- Industrier: Aerospace, automotive, medical, electronics, consumer goods.
Advantages of Multi-Material 3D Printing
- Flexibilitet i designen: Create complex geometries that are impossible with traditional manufacturing.
- Materialeffektivitet: Optimize material usage, reducing waste.
- Enhanced Product Functionality: Combine materials for superior mechanical, thermal, or electrical properties.
- Reduced Assembly: Print multi-material components in a single process, minimizing the need for assembly.
- Anpassning: Tailor products to specific needs and preferences.
Detailed Advantages of Multi-Material 3D Printing
- Komplexa geometrier: Enables intricate designs and internal structures.
- Materialoptimering: Utilizes the best material for each part of the component.
- Funktionell integration: Combines multiple functionalities in one component.
- Kostnadsbesparingar: Reduces the number of manufacturing steps and materials used.
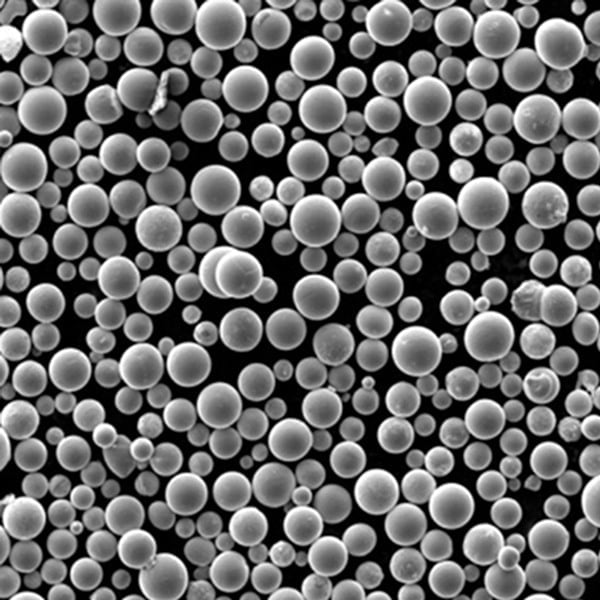
Disadvantages of Multi-Material 3D Printing
- Complexity in Process: Requires advanced software and expertise to manage different materials.
- Kostnad: High initial investment for multi-material printers and materials.
- Materialkompatibilitet: Not all materials can be combined due to differing properties.
- Printing Speed: Slower due to the need for multiple material changes.
- Efterbearbetning: May require additional steps to finish the printed parts.
Detailed Disadvantages of Multi-Material 3D Printing
- Technical Challenges: Managing different material properties can be difficult.
- Investment Costs: Expensive machinery and materials.
- Limited Material Combinations: Not all materials can be used together effectively.
- Produktionshastighet: Multi-material printing can be slower than single-material printing.
- Behov av efterbearbetning: Additional steps might be necessary to achieve the desired finish.
Tillämpningar av Multimaterial 3D-utskrift
Flyg- och rymdindustrin
In the aerospace industry, components must withstand extreme conditions and stresses. Multi-material 3D printing allows for the integration of lightweight materials with high-strength alloys, improving performance and reducing weight.
Example Applications:
- Turbine blades with thermal-resistant coatings.
- Lightweight structural components.
- Complex geometrical parts.
Fordon
Automotive manufacturers use multi-material 3D printing to produce parts that are lighter, stronger, and more efficient. This technology is pivotal in the development of electric vehicles and advanced driver-assistance systems (ADAS).
Example Applications:
- Lightweight chassis components.
- Engine parts with thermal management features.
- Customized interior elements.
Medicinsk
The medical field benefits immensely from multi-material 3D printing, particularly in the production of prosthetics, implants, and surgical instruments. This technology enables the creation of patient-specific solutions with tailored mechanical and biological properties.
Example Applications:
- Biocompatible implants with varying stiffness.
- Custom-fit prosthetic limbs.
- Multi-functional surgical tools.
Konsumentvaror
In consumer goods, multi-material 3D printing allows for the creation of products with enhanced aesthetic and functional qualities. This includes wearable technology, customized accessories, and household items.
Example Applications:
- Smartwatches with integrated electronics.
- Customized smartphone cases.
- Functional prototypes for product development.
Elektronik
Multi-material 3D printing is transforming electronics manufacturing by enabling the integration of conductive and insulating materials. This allows for the production of complex electronic components and circuit boards.
Example Applications:
- Embedded sensors in structural components.
- Custom-designed circuit boards.
- Wearable electronics with integrated circuits.
Specifika metallpulvermodeller för Multimaterial 3D-utskrift
Here, we list some specific metal powders used in multi-material 3D printing, along with their descriptions:
Metallpulvermodell | Beskrivning |
---|---|
Inconel 718 | Nickel-based superalloy known for high strength and oxidation resistance at high temperatures. Ideal for aerospace and automotive applications. |
Ti-6Al-4V | Titanium alloy with excellent strength-to-weight ratio, used extensively in aerospace, medical implants, and high-performance automotive parts. |
316L rostfritt stål | Corrosion-resistant stainless steel with good mechanical properties, widely used in marine, medical, and food processing industries. |
AlSi10Mg | Aluminum alloy with high thermal conductivity and lightweight properties, suitable for automotive and aerospace applications. |
CoCr | Cobalt-chromium alloy known for wear resistance and biocompatibility, commonly used in medical implants and dental restorations. |
Koppar (Cu) | Highly conductive metal used for electrical components and heat exchangers. |
Maråldrat stål | High-strength steel alloy used in tooling, aerospace, and high-stress applications. |
Hastelloy X | Nickel-based alloy with excellent oxidation and corrosion resistance, suitable for high-temperature aerospace applications. |
Nickellegering 625 | Corrosion and oxidation-resistant nickel alloy, used in chemical processing, marine, and aerospace industries. |
Aluminium 7075 | High-strength aluminum alloy used in aerospace and automotive industries for its excellent mechanical properties and lightweight nature. |
Egenskaper och egenskaper hos metallpulver
Metallpulvermodell | Sammansättning | Fastigheter | Tillämpningar |
---|---|---|---|
Inconel 718 | Nickel, krom, järn | Hög hållfasthet, oxidationsbeständighet | Flyg- och rymdindustrin, fordonsindustrin |
Ti-6Al-4V | Titan, aluminium, vanadin | Högt förhållande mellan styrka och vikt | Flyg- och rymdindustrin, medicinska implantat |
316L rostfritt stål | Järn, krom, nickel | Korrosionsbeständighet, goda mekaniska egenskaper | Marine, medical, food processing |
AlSi10Mg | Aluminium, kisel, magnesium | Lätt, värmeledningsförmåga | Fordon, flyg- och rymdindustrin |
CoCr | Kobolt, krom | Slitstyrka, biokompatibilitet | Medicinska implantat, tandfyllningar |
Koppar (Cu) | Ren koppar | Hög elektrisk ledningsförmåga | Elektriska komponenter, värmeväxlare |
Maråldrat stål | Järn, nickel, kobolt | Hög hållfasthet | Tooling, aerospace, high-stress applications |
Hastelloy X | Nickel, krom, järn | Oxidations- och korrosionsbeständighet | High-temperature aerospace applications |
Nickellegering 625 | Nickel, Krom, Molybden | Korrosions- och oxidationsbeständighet | Kemisk bearbetning, marin, flyg och rymd |
Aluminium 7075 | Aluminum, Zinc, Magnesium | Hög hållfasthet, låg vikt | Flyg- och rymdindustrin, fordonsindustrin |
Applications of Specific Metal Powders
Metallpulvermodell | Typiska användningsområden |
---|---|
Inconel 718 | Jet engines, gas turbines, high-performance automotive parts |
Ti-6Al-4V | Aircraft components, medical implants, high-performance sports equipment |
316L rostfritt stål | Marine hardware, surgical instruments, food processing equipment |
AlSi10Mg | Automotive parts, aerospace components, lightweight structural parts |
CoCr | Dental implants, orthopedic implants, wear-resistant components |
Koppar (Cu) | Electrical connectors, heat exchangers, conductive elements in electronics |
Maråldrat stål | High-strength tooling, aerospace components, high-stress mechanical parts |
Hastelloy X | Combustion chambers, high-temperature ducting, industrial furnace parts |
Nickellegering 625 | Chemical processing equipment, marine hardware, high-temperature aerospace parts |
Aluminium 7075 | Aircraft frames, automotive chassis, high-stress components in sports equipment |
Specifications and Standards of Metal Powders
Metallpulvermodell | Partikelstorlek | Densitet (g/cm³) | Smältpunkt (°C) | ASTM-standard |
---|---|---|---|---|
Inconel 718 | 15-45 µm | 8.19 | 1,350 | ASTM F3055 |
Ti-6Al-4V | 15-45 µm | 4.43 | 1,660 | ASTM F2924 |
316L rostfritt stål | 15-45 µm | 8.00 | 1,400 | ASTM F3184 |
AlSi10Mg | 20-63 µm | 2.68 | 660 | ASTM F3318 |
CoCr | 15-45 µm | 8.30 | 1,300 | ASTM F75 |
Koppar (Cu) | 15-45 µm | 8.96 | 1,083 | ASTM B213 |
Maråldrat stål | 15-45 µm | 8.00 | 1,410 | ASTM F3056 |
Hastelloy X | 15-45 µm | 8.22 | 1,350 | ASTM B435 |
Nickellegering 625 | 15-45 µm | 8.44 | 1,299 | ASTM F3056 |
Aluminium 7075 | 20-63 µm | 2.81 | 477 | ASTM B928 |
Leverantörer och prisuppgifter
Leverantör | Metallpulvermodell | Pris (per kg) | Kontaktuppgifter |
---|---|---|---|
Höganäs | Inconel 718 | $120 | [email protected] |
AP&C | Ti-6Al-4V | $200 | [email protected] |
Snickare | 316L rostfritt stål | $90 | [email protected] |
Eck Industries | AlSi10Mg | $70 | [email protected] |
Sandvik | CoCr | $180 | [email protected] |
Tekna | Koppar (Cu) | $60 | [email protected] |
Snickare | Maråldrat stål | $150 | [email protected] |
Haynes | Hastelloy X | $220 | [email protected] |
Snickare | Nickellegering 625 | $180 | [email protected] |
Rusal America | Aluminium 7075 | $50 | [email protected] |
Jämförelse av för- och nackdelar med Multimaterial 3D-utskrift
Aspekt | Fördelar | Nackdelar |
---|---|---|
Flexibilitet i designen | Allows complex geometries and custom designs. | Requires advanced design software and expertise. |
Materialeffektivitet | Reduces material waste by optimizing usage. | Material compatibility issues can arise. |
Enhanced Functionality | Combines multiple properties in one part (e.g., strength, conductivity). | Managing different material properties can be challenging. |
Reduced Assembly | Fewer components needed, simplifying the manufacturing process. | Printing speed may be slower due to multiple material changes. |
Anpassning | Easily tailor products to specific needs. | Higher costs for machinery and materials. |
Technical Challenges | Innovative solutions for combining materials. | Requires technical expertise to handle different materials. |
Investment Costs | Potential for high returns on investment through advanced capabilities. | Initial setup costs can be prohibitive for some businesses. |
Produktionshastighet | Efficient for creating multifunctional parts in one go. | Can be slower compared to single-material printing. |
Behov av efterbearbetning | Offers high-quality, finished parts with fewer manufacturing steps. | Additional steps might be needed to achieve the desired finish. |
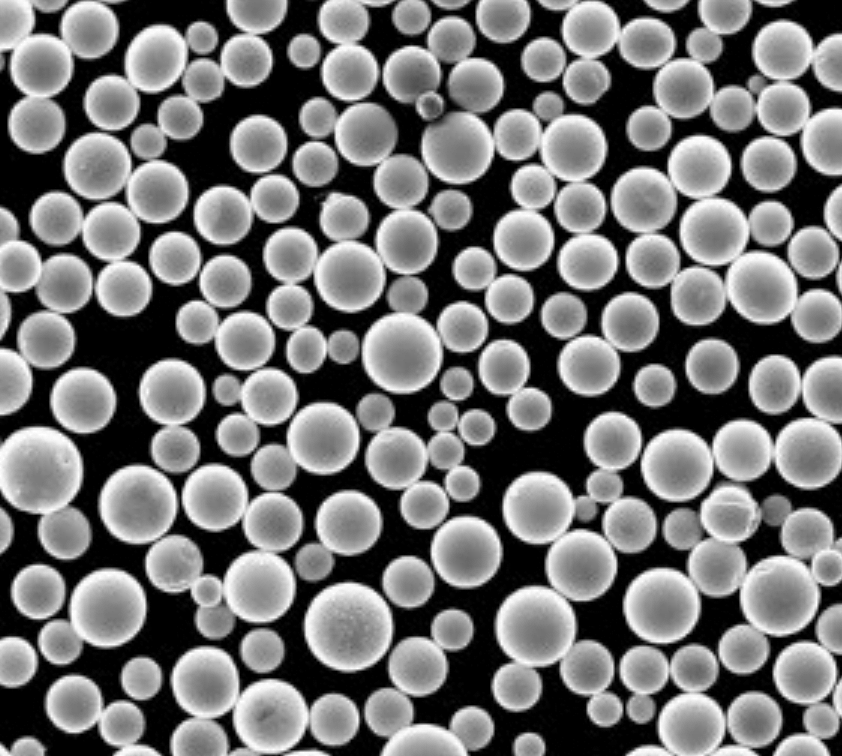
VANLIGA FRÅGOR
Fråga | Svar |
---|---|
What is multi-material 3D printing? | It is a 3D printing process that uses two or more different materials to create a single object with varied properties. |
What are the benefits of multi-material 3D printing? | Benefits include design flexibility, material efficiency, enhanced functionality, reduced assembly, and customization. |
What are the common materials used in multi-material 3D printing? | Common materials include metals (e.g., Inconel 718, Ti-6Al-4V), polymers, ceramics, and composites. |
Which industries benefit the most from multi-material 3D printing? | Aerospace, automotive, medical, consumer goods, and electronics industries benefit significantly from this technology. |
What are the challenges of multi-material 3D printing? | Challenges include managing different material properties, higher costs, technical complexity, slower printing speeds, and post-processing needs. |
How does multi-material 3D printing reduce assembly requirements? | It allows for the creation of multifunctional components in a single print, eliminating the need for assembling multiple parts. |
Can multi-material 3D printing be used for mass production? | It is generally more suited for low to medium volume production and highly customized or complex parts rather than mass production. |
What is the cost of multi-material 3D printers? | The cost can vary widely based on the capabilities and materials used, with high-end printers costing significantly more due to their advanced features. |
Are there any environmental benefits to multi-material 3D printing? | Yes, it can reduce material waste and energy consumption by optimizing the manufacturing process and minimizing the need for additional components. |
What future advancements are expected in multi-material 3D printing? | Future advancements may include improved material compatibility, faster printing speeds, and more accessible technology for a broader range of applications. |
Slutsats
Multi-material 3D printing is a groundbreaking technology that is transforming various industries by enabling the production of complex, multifunctional components. While it comes with certain challenges and costs, the benefits in terms of design flexibility, material efficiency, and enhanced functionality make it a valuable tool in modern manufacturing. As technology continues to advance, we can expect even more innovative applications and wider adoption across different sectors. Whether you are in aerospace, automotive, medical, or consumer goods, multi-material 3D printing offers exciting possibilities for creating the next generation of high-performance products.
Dela på
MET3DP Technology Co, LTD är en ledande leverantör av lösningar för additiv tillverkning med huvudkontor i Qingdao, Kina. Vårt företag är specialiserat på 3D-utskriftsutrustning och högpresterande metallpulver för industriella tillämpningar.
Förfrågan för att få bästa pris och anpassad lösning för ditt företag!
Relaterade artiklar
Om Met3DP
Senaste uppdateringen
Vår produkt
KONTAKTA OSS
Har du några frågor? Skicka oss meddelande nu! Vi kommer att betjäna din begäran med ett helt team efter att ha fått ditt meddelande.
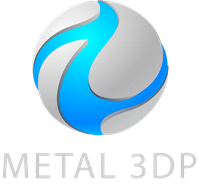
Metallpulver för 3D-printing och additiv tillverkning