Vilket 3D-utskrivet nickelbaserat legeringspulver kan användas inom flyg- och rymdindustrin
Innehållsförteckning
Föreställ dig en fågel som utan ansträngning svävar genom skyn. Föreställ dig nu en jetmotor, det bultande hjärtat i ett modernt flygplan, som driver det över kontinenter i fenomenala hastigheter. Båda dessa tekniska underverk har ett gemensamt behov: lätta, otroligt starka material som kan stå emot extrema temperaturer och tuffa miljöer. Stig in i den fascinerande världen av 3D-tryckta nickelbaserade legeringspulveroch spelar en huvudroll i flygindustrins ständiga strävan efter innovation.
Nickelbaserade legeringar är en klass av metalliska superstjärnor. De har exceptionell hållfasthet vid höga temperaturer, korrosionsbeständighet och utmärkt krypbeständighet - förmågan att motstå deformation under konstant stress vid förhöjda temperaturer. Dessa egenskaper gör dem idealiska för de brutala driftsförhållanden som komponenter i jetmotorer utsätts för. Men vad är det som gör 3D-printning av dessa legeringar så revolutionerande?
Låt oss dyka djupare in i världen av 3D-utskrivna nickelbaserade legeringspulver och utforska de specifika typer som används i flyg- och rymdtillämpningar, deras unika egenskaper och de fördelar de erbjuder jämfört med traditionella tillverkningsmetoder.
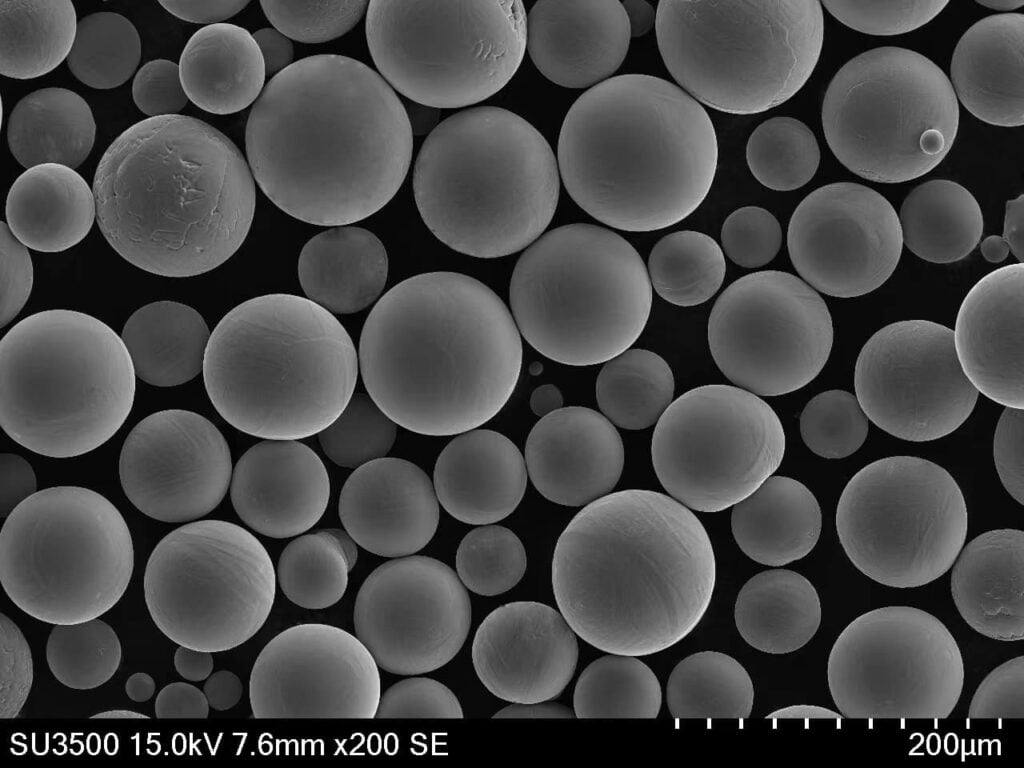
Vanlig Nickelbaserade legeringspulver för flyg- och rymdindustrin
3D-printade nickelbaserade legeringspulver är inte en värld som passar alla. Olika legeringar erbjuder distinkta fördelar beroende på den specifika applikationen. Här riktar vi strålkastarljuset mot tre av de mest framträdande utmanarna:
- Inconel 718: Denna kraftfulla legering är den obestridda mästaren för många flyg- och rymdtillämpningar. Dess exceptionella förhållande mellan styrka och vikt, utmärkta högtemperaturprestanda (upp till 700 °C) och goda svetsbarhet gör den till ett mångsidigt val för ett brett spektrum av komponenter. Se det som en "schweizisk armékniv" bland nickelbaserade legeringspulver, perfekt för allt från turbinskivor och skovlar till komponenter i landningsställ.
- Inconel 625: Denna legering har överlägsen korrosionsbeständighet jämfört med Inconel 718 och är en livräddare i miljöer som utsätts för starka kemikalier och oxidation. Tänk på brännheta avgassystem och delar som utsätts för saltvatten under långa perioder. Inconel 625 är inte riktigt lika stark som Inconel 718 vid höga temperaturer, men briljerar i tillämpningar där korrosionsbekämpning är av största vikt.
- Hastelloy X: Föreställ dig ett material som trivs i miljöer som är så fientliga att till och med andra superlegeringar ryggar tillbaka. Hastelloy X kliver in i ringen. Denna mästare har fenomenal motståndskraft mot ett brett spektrum av korrosiva medier, inklusive heta klorvätesyror och svavelsyror. Tänk på den som den ultimata "korrosionskrigaren", perfekt för bränslesystem, värmeväxlare och andra komponenter som utsätts för aggressiva kemikalier.
Tabell 1: Jämförelse av viktiga egenskaper hos vanliga nickelbaserade legeringspulver
Fastighet | Inconel 718 | Inconel 625 | Hastelloy X |
---|---|---|---|
Hållfasthet vid höga temperaturer | Utmärkt (upp till 700°C) | Bra (upp till 675°C) | Måttlig |
Motståndskraft mot korrosion | Bra | Utmärkt | Exceptionell |
Svetsbarhet | Bra | Bra | Rättvist |
Typiska tillämpningar | Diskar och blad till turbiner, Komponenter till landningsställ | Avgassystem, Saltvattenexponerade komponenter | Bränslesystem, Värmeväxlare |
Tillämpningar av nickelbaserade legeringspulver inom flyg- och rymdindustrin
Möjligheten att skapa komplexa, lätta och otroligt starka komponenter med hjälp av 3D-printade nickelbaserade legeringspulver revolutionerar sättet att konstruera och tillverka flygplan. Låt oss utforska några av de mest spännande tillämpningarna:
- Turbindiskar och turbinblad: Dessa arbetshästar är hjärtat i en jetmotor, snurrar i svindlande hastigheter och tål extrema temperaturer. 3D-printad Inconel 718 erbjuder den perfekta blandningen av styrka och högtemperaturprestanda för dessa kritiska komponenter, vilket möjliggör lättare konstruktioner som förbättrar bränsleeffektiviteten.
- Eftermarknadsdelar och reparation: Tänk dig att snabbt och effektivt kunna byta ut ett skadat turbinblad. 3D-printning med nickelbaserade legeringspulver gör detta till verklighet. Komponenter kan specialutskrivas på begäran, vilket minimerar stilleståndstiden och underhållskostnaderna för flygbolagen.
- Värmeväxlare: Dessa viktiga komponenter överför värme till hela motorn. Hastelloy X:s exceptionella korrosionsbeständighet gör den idealisk för den här tillämpningen och säkerställer att växlaren fungerar felfritt i tuffa miljöer.
- Nästa generations motorkonstruktioner: Den designfrihet som 3D-printing erbjuder gör det möjligt för ingenjörer att skapa intrikata interna kylkanaler i motorkomponenter. Detta förbättrar inte bara effektiviteten utan gör det också möjligt att utforska helt nya motorarkitekturer och flytta fram gränserna för prestanda.
Fördelar med 3D-utskrifter Nickelbaserade legeringspulver
3D-printing med nickelbaserade legeringspulver erbjuder en rad fördelar jämfört med traditionella tillverkningstekniker som gjutning och smide:
- Designfrihet: Borta är begränsningarna med traditionella metoder som gjutning och smide. 3D-printing gör det möjligt att skapa komplexa geometrier med invecklade interna funktioner som tidigare varit omöjliga att åstadkomma. Detta öppnar dörrar för lättare och effektivare motorkonstruktioner som optimerar luftflöde och värmeöverföring. Föreställ dig ett turbinblad med interna kylkanaler som slingrar sig genom kärnan och maximerar värmeavledningen utan att öka volymen.
- Kortare ledtider: Traditionella tillverkningsprocesser kan vara tidskrävande, med långa ledtider för komplexa komponenter. 3D-printing ger en dramatisk minskning av ledtiderna. Komponenter kan skrivas ut på begäran, vilket avsevärt påskyndar design-, prototyp- och produktionscyklerna. Denna flexibilitet är avgörande i den snabbfotade flygindustrin och möjliggör snabbare svarstider på nya marknadskrav och tekniska framsteg.
- Materialeffektivitet: Traditionella tillverkningstekniker innebär ofta betydande materialspill under bearbetnings- och formningsprocesser. 3D-printing använder en laser för att selektivt smälta pulver endast där det behövs, vilket minimerar spill och gör det till ett mer hållbart tillverkningsalternativ. I en bransch som strävar efter att minska sitt miljöavtryck blir den här fördelen allt viktigare.
- Förbättrat förhållande mellan köp och flygning: Med "buy-to-fly ratio" avses den mängd råmaterial som behövs för att tillverka en färdig, flygfärdig komponent. Traditionell tillverkning kan resultera i en hög "buy-to-fly"-kvot på grund av materialspill. 3D-printingens inneboende effektivitet minskar detta förhållande avsevärt, vilket leder till lättare flygplan med förbättrad bränsleeffektivitet - en kritisk faktor i en bransch som är besatt av att minska driftskostnaderna och miljöpåverkan.
Utmaningar och överväganden
Även om 3D-utskrivna nickelbaserade legeringspulver erbjuder en enorm potential finns det utmaningar att ta hänsyn till:
- Kostnad: För närvarande är kostnaden för 3D-utskrifter nickelbaserade legeringspulver fortfarande högre jämfört med traditionell tillverkningsteknik för vissa applikationer. I takt med att tekniken utvecklas och användningsgraden ökar förväntas dock dessa kostnader sjunka.
- Pulverkvalitet: Pulvrets kvalitet och konsistens spelar en avgörande roll för den tryckta komponentens slutliga egenskaper. Strikta kvalitetskontroller är nödvändiga för att säkerställa att komponenterna uppfyller de stränga krav som ställs i flyg- och rymdapplikationer.
- Efterbearbetning: 3D-utskrivna komponenter kan kräva ytterligare efterbearbetningssteg som värmebehandling eller maskinbearbetning för att uppnå önskade slutliga egenskaper. Att optimera dessa efterbearbetningssteg är avgörande för att säkerställa komponentens prestanda och effektivitet.
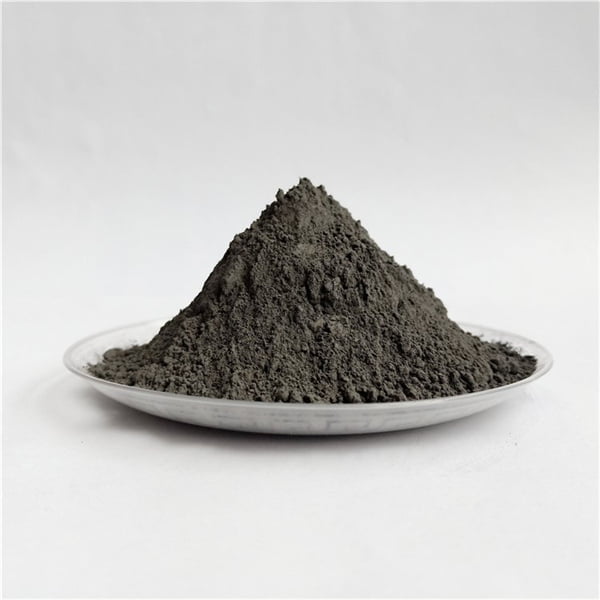
VANLIGA FRÅGOR
Här är några av de vanligaste frågorna om 3D-printade nickelbaserade legeringspulver inom flygindustrin:
Q: Vilka är fördelarna med att använda 3D-printade nickelbaserade legeringspulver jämfört med traditionella tillverkningsmetoder?
A: 3D-printing erbjuder fördelar som designfrihet, kortare ledtider, förbättrad materialeffektivitet och ett bättre förhållande mellan inköp och flygning.
F: Vilka nickelbaserade legeringspulver används oftast inom flyg- och rymdindustrin?
A: Inconel 718, Inconel 625 och Hastelloy X är några av de mest populära valen på grund av deras unika egenskaper som högtemperaturhållfasthet, korrosionsbeständighet och svetsbarhet.
Q: Vilka är utmaningarna med att använda 3D-printade nickelbaserade legeringspulver?
A: Kostnad, pulverkvalitet och behovet av efterbearbetning är några av de viktigaste utmaningarna som hanteras genom ständiga framsteg inom teknik och tillverkningsprocesser.
Q: Hur ser framtiden ut för 3D-printade nickelbaserade legeringspulver inom flygindustrin?
A: Framtiden ser ljus ut. I takt med att tekniken utvecklas, kostnaderna sjunker och pulverkvaliteten förbättras kommer 3D-printing att spela en allt viktigare roll i konstruktionen och tillverkningen av nästa generations flygplan och flytta fram gränserna för prestanda och effektivitet.
Slutsats
Kombinationen av 3D-printingteknik och nickelbaserade legeringspulver är en gamechanger för flygindustrin. Det öppnar upp för nya möjligheter till designinnovation, lättare och effektivare flygplan samt snabbare produktionscykler. Även om utmaningarna kvarstår är de potentiella fördelarna obestridliga. När vi blickar mot framtidens himmel kommer 3D-tryckta nickelbaserade legeringspulver säkert att spela en viktig roll för att driva oss mot en ny era av utforskning och prestationer inom flygindustrin.
Dela på
MET3DP Technology Co, LTD är en ledande leverantör av lösningar för additiv tillverkning med huvudkontor i Qingdao, Kina. Vårt företag är specialiserat på 3D-utskriftsutrustning och högpresterande metallpulver för industriella tillämpningar.
Förfrågan för att få bästa pris och anpassad lösning för ditt företag!
Relaterade artiklar
Om Met3DP
Senaste uppdateringen
Vår produkt
KONTAKTA OSS
Har du några frågor? Skicka oss meddelande nu! Vi kommer att betjäna din begäran med ett helt team efter att ha fått ditt meddelande.
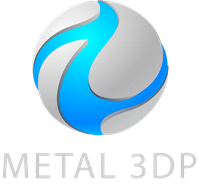
Metallpulver för 3D-printing och additiv tillverkning