3D-skrivare med pulverbädd
Innehållsförteckning
Översikt
3d-skrivare med pulverbädd är en additiv tillverkningsteknik som lämpar sig väl för bearbetning av högpresterande tekniska termoplaster och metaller som inte enkelt kan tryckas med extruderingsbaserade metoder. En laser- eller elektronstråle smälter selektivt samman regioner i en pulverbädd lager för lager baserat på CAD-data för att konstruera komplexa 3D-objekt.
De viktigaste underkategorierna är:
Polymer pulverbäddsfusion (PBF) använder en CO2- eller IR-laser, och Fusion av metallpulverbäddar (MPBF) med hjälp av fiberlasrar eller elektronstrålar. Båda erbjuder konkurrenskraftiga funktioner som är omöjliga att uppnå med traditionella tillverkningstekniker när det gäller lättviktsdesign, konsolidering av montering, massanpassning och prestandaförbättring.
Den här guiden ger en teknisk översikt över olika 3D-printingtekniker och material med pulverbädd samt tillämpningar, systemöverväganden och framtida trender.
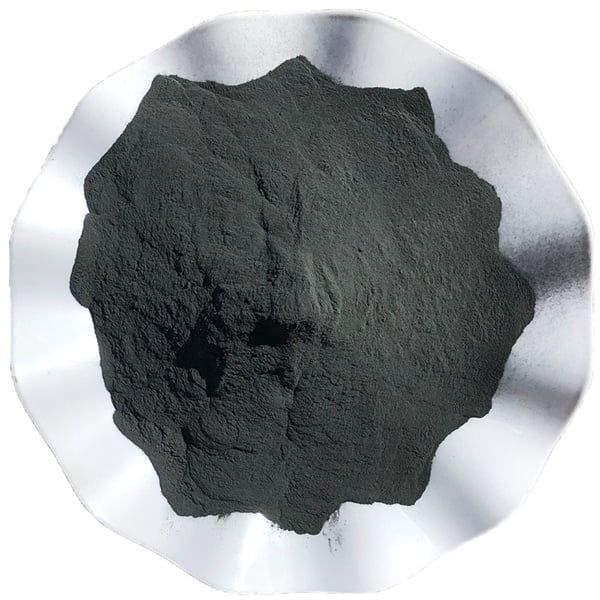
Typer av 3D-skrivare med pulverbädd
Det finns flera olika typer av utrustning för additiv tillverkning som utnyttjar pulverbäddsfusion:
Kategori | Beskrivning |
---|---|
Selektiv lasersintring (SLS) | Sintrar polymerpulver med hjälp av en CO2-laser |
Multi Jet Fusion (MJF) | Binder plastpulver med bläckstråleskrivna fixerings- och detaljmedel |
Selektiv lasersmältning (SLM) | Fullständig sammansvetsning av metallpulver med fiberlaser |
Direkt metallsintring med laser (DMLS) | Smälter samman metallpulver genom lasersmältning |
Smältning med elektronstråle (EBM) | Använder elektronstråle i vakuum för att smälta metallpulverbäddar |
Fusionsskrivare med polymerpulverbädd
Selektiv lasersintring (SLS) systemen fördelar ett tunt lager fint polymerpulver över en byggkammare och tillför värmeenergi från en CO2-laserstråle i enlighet med varje tvärsnitt från 3D CAD-modellen. Pulvret smälter eller sintrar ihop vid uppvärmning och stelnar under kylning för att bli objektet.
Populära material för SLS är bland annat
- Nylon (PA12, PA11, PA6)
- Termoplastiska elastomerer (TPE)
- TPU och andra avancerade flexibla hartser
Bland de ledande SLS-skrivarföretagen finns EOS, 3D Systems, Farsoon och Ricoh.
Multi Jet Fusion (MJF) använder sig också av polymerpulverbäddar, men ett smältmedel och ett detaljmedel deponeras selektivt av bläckstråleskrivhuvuden över lagren tillsammans med infraröd uppvärmning för att uppnå högupplösta utskrifter. Det möjliggör objekt av flera material och i flera färger. Vanliga MJF-hartser:
- HP 3D Hög återanvändbarhet PA12
- HP 3D Hög återanvändbarhet PA11
- HP 3D Hög återanvändbarhet TPA
HP är den främsta leverantören av MJF-teknik idag genom sin Jet Fusion-serie. Desktop Metal har också lanserat ett Fiber AM-system baserat på MJF.
Fusionskrivare med metallpulverbädd
Selektiv lasersmältning (SLM) utrustningen fokuserar extremt exakt fiberlaserenergi i en miljö med inert gas över tunna lager av metallpulver för att helt smälta och smälta samman partiklar till täta strukturer lager för lager baserat direkt på CAD-geometrier.
Smältning med elektronstråle (EBM) använder en kraftfull elektronstråle som värmekälla för konsolidering för att smälta metallpulverpartiklar över varje lager i en vakuumatmosfär. Den snabba bearbetningen leder till komponenter med egenskaper som närmar sig gjutna material.
Vanliga legeringar för MPBF inkluderar:
- Rostfritt stål (316L, 17-4PH, 15-5)
- Verktygsstål (H13, S7)
- Titanlegeringar (Ti-6Al-4V)
- Aluminiumlegeringar (AlSi10Mg)
- Superlegeringar av nickel (Inconel 718)
- Koboltkrom (CoCr)
Alla ledande leverantörer av utrustning för metall-AM som EOS, Renishaw, 3D Systems, GE och SLM Solutions erbjuder maskiner för pulverbäddsfusion.
Utskriftsprocess för 3d-skrivare med pulverbädd
Det generiska arbetsflödet för additiv tillverkning som är gemensamt för alla varianter av pulverbäddfusion:
- Importera CAD-modell och orientera detaljen optimalt
- Virtuellt skära och generera laserskanningsbanor
- Fördela den uppmätta mängden pulver jämnt över byggytan
- Selektiv smältning av material enligt sektionsritning med laser eller ebeam
- Sänk byggplattan och lägg på nytt pulverskikt
- Upprepa skiktningscykeln tills hela objektet och stöden är byggda
- Ta bort objektet från pulverkakan och återställ osmälta regioner
- Efterbearbetning av delar – rengöring, värmebehandling, maskinbearbetning etc.
Alla pulverbäddsprocesser kräver omfattande efterbearbetning som borttagning av stöd, ytbearbetning och behandlingar före funktionell användning.
Material för 3d-skrivare med pulverbädd
Egenskaper för polymerpulver
Material | Täthet | Draghållfasthet | Förlängning % | Användningsområden |
---|---|---|---|---|
PA12 | 0.9-1,1 g/cm3 | 45-65 MPa | 15-50% | Polymer för SLS-prototyptillverkning för allmänt bruk |
TPU 92A | 1.1-1,3 g/cm3 | 6 MPa | 220-240% | Flexibla, gummiliknande delar via SLS |
PEEK | 1.3-1,4 g/cm3 | 100 MPa | 30-60% | Delar av höghållfast konstruktionsplast |
Typer av metallpulver
Legering | Täthet | Smältpunkt | Användningsområden |
---|---|---|---|
Aluminium AlSi10Mg | 2,7 g/cm3 | 600°C | Lättviktskomponenter för flyg- och bilindustrin |
Titan Ti-6Al-4V | 4,4 g/cm3 | 1655°C | Implantat och höghållfasta strukturer |
Verktygsstål H13 | 7.7 g/cm3 | 1320°C | Hållbara verktyg för gjutning och extrudering |
Rostfritt stål 316L | 8,0 g/cm3 | 1375°C | Korrosionsbeständiga kärl, ventiler, hårdvara |
Inconel 718 | 8,2 g/cm3 | 1260-1336°C | Värme- och krypresistenta flygmotordelar vid höga temperaturer |
Tillämpningar av 3d-skrivare med pulverbädd
Polymera delar
- Funktionella prototyper med egenskaper som liknar verkliga plastmaterial
- Kundanpassade konsumentvaror som mobilskal eller skor
- Fordonsinteriörer och belysningskomponenter
- Induktionsformar och jiggar & fixturer
- Formar för höga temperaturer och kanaler för kemikalier
Metallkomponenter
- Prototyper av turbinblad och bränsleinsprutare för flyg- och rymdindustrin
- Biokompatibla titanimplantat för knä, höft, kranie- och ryggkirurgi
- Lättviktsdelar till chassi, bromsar och drivlina för racerbilar och flygplan
- Konforma kylkanaler integrerade i formsprutningsverktyg
- Specialanpassade tandproteser, substruktioner och broar
- Värmebeständiga avgasgrenrör och verktygsinsatser
Köparens’guide för 3D-skrivare med pulverbädd
Valet av ett idealiskt fusionssystem för pulverbäddar beror på:
Kriterier | Viktiga överväganden |
---|---|
Bygg kuvertet | Maximalt möjliga dimensioner på detaljerna. Från 5 tum till 500 mm+ |
Material | Tillgängliga hartser från polymerer till reaktiva metaller som uppfyller applikationsbehoven |
Precision | X-Y-upplösning från ~100 mikrometer ner till 5 mikrometer för fina detaljer |
Ytfinish | Sidoväggarnas kvalitet varierar från 15 mikrometer till 150+. Kan kräva efterbearbetning. |
Automatisering | Manuell eller automatiserad pulverhantering. Bearbetning i slutna kretsar föredras. |
Programvara | Generativ designintegration för topologioptimering. Snabb skivning. |
Prisintervall | Systemkostnader i förskott från 100 000 dollar till över 1 miljon dollar. Tänk också på driftskostnaderna. |
Ledande tidningar | Installations- och leveransscheman. Utbildningslängd för operatörer. |
Några ledande modeller span:
Start – EOS Formiga P110 SLS-system, $100K
Professionell – 3D Systems DMP Factory 500, 400 000 dollar
Industriell – GE Additive X Line 2000R, >$1M
Framtidsutsikter
Pulverbäddsfusionssystem kommer att fortsätta att utvecklas med:
- Större byggkuvert över 500 mm långa
- Ytterligare polymermaterial som PEKK och PPSF
- Legeringar med högre mekanisk prestanda
- Förbättrad återvinningsbarhet för pulver och slutna kretslopp
- Banbrytande ytfinhet utan maskinbearbetning
- Integrerad övervakning och justering av smältbadet i realtid
- Ytterligare hybridsystem med inbyggd kvalitetssäkring
- Dramatiskt ökad produktivitet genom högre lasereffekt och snabbare skanningshastigheter
I takt med att tekniska hinder övervinns och produktionskostnaderna optimeras kommer AM att förändra tillverkningen inom allt från flyg, medicinteknik och fordon till konsumentprodukter genom att möjliggöra distribuerad och decentraliserad tillverkning av slutanvändarkomponenter i kommersiella volymer.
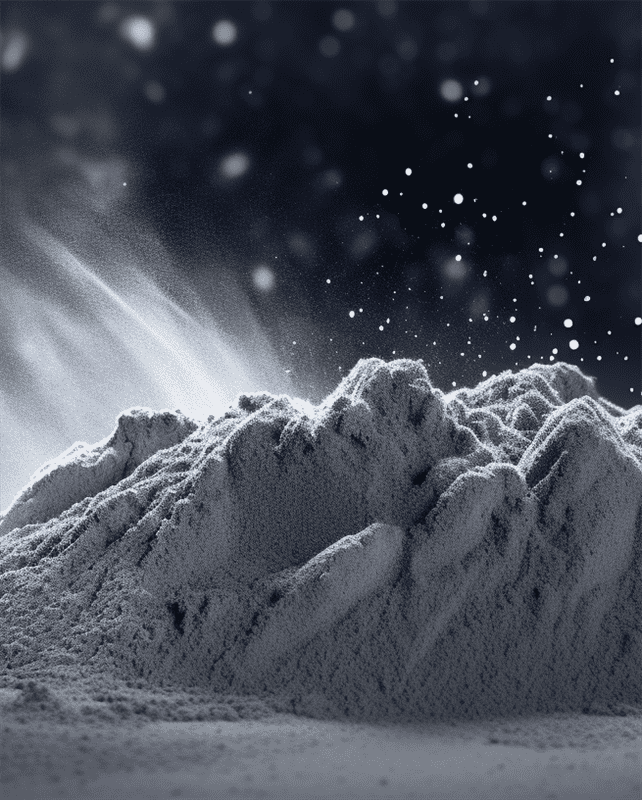
Vanliga frågor
F: Hur dyra är 3D-utskriftsmaskiner för metall med pulverbäddfusion jämfört med plastsystem?
S: Industriella metallpulverbäddsskrivare sträcker sig från $ 300.000 till över $ 1 miljon medan polymerbaserad utrustning börjar på $ 100.000. Driftskostnaderna är också 5-10X högre för metallmaterial och inert bearbetning.
F: Hur stora delar kan 3D-printas med pulverbäddsfusionsteknik?
A: Metallmaskinerna klarar byggvolymer på upp till 500 x 500 x 500 mm kuber, medan polymererna klarar dimensioner på upp till 800 x 500 x 375 mm. Större kuvert som är över en meter långa är också tillgängliga.
F: Vilka material kan bearbetas med 3D-utskrift med pulverbädd?
A: Alla högpresterande och tekniska termoplaster som PEEK, ULTEM, PPSF kan tryckas som är svåra för FDM-extrudering. På metaller kan rostfritt stål, titan- och nickellegeringar, verktygsstål, koboltkrom och mer kvalificeras.
F: Hur bra är noggrannheten och ytfinishen hos en pulverbäddsskrivare innan någon efterbearbetning?
A: Måttnoggrannheten efter efterbearbetning är cirka ±0,1-0,3% medan toleranser under 50 mikrometer är möjliga. Den tryckfärdiga ytjämnheten varierar avsevärt mellan 15-150 mikrometer före eventuell efterbehandling.
F: Vilken pulverbäddsfusionsprocess ger de snabbaste bygghastigheterna: SLS, DMLS eller EBM?
S: Elektronstrålesmältning (EBM) ger extremt höga bygghastigheter på upp till 40 cm3/timme, vilket möjliggör mycket hög produktivitet. DMLS erbjuder måttliga hastigheter medan SLS är jämförelsevis ganska långsam.
Q: Hur hållbar är pulverbädds-AM jämfört med bearbetning av metaller och plaster?
S: Alla pulverbäddstekniker återanvänder över 90% av det osmälta pulvret efter byggnation för återvinning. Lättviktsoptimerade geometrier sparar också material. Energianvändningen är ett fortsatt fokusområde.
F: Vilka faktorer leder till prissättning av utskriftstjänster för pulverbäddsfusion?
A: Materialkostnader, byggtid, arbetskraft, efterbehandling, 3D-skrivarmodell, produktionsvolym och köparens applikationssektor styr i hög grad prisnivåerna för industriella AM-delar idag.
Q: Vilka branscher är ledande inom additiv tillverkning med pulverbäddfusion idag?
A: Företag inom flyg-, medicin-, fordons- och maskinkonstruktion med fokus på jiggar, fixturer och verktyg utgör över 60% av de kommersiella kunder som utforskar AM-produktionsapplikationer med polymerer och metaller.
Q: Vilken specialprogramvara krävs för att förbereda och skriva ut 3D CAD-modeller på bästa sätt?
S: Skivningsprogram som Materialise Magics och SLM Build Processor orienterar automatiskt delarna för bästa geometri och egenskaper och anpassar skanningsparametrarna. Vissa skrivarleverantörer levererar egenutvecklade programvaruverktyg.
Dela på
MET3DP Technology Co, LTD är en ledande leverantör av lösningar för additiv tillverkning med huvudkontor i Qingdao, Kina. Vårt företag är specialiserat på 3D-utskriftsutrustning och högpresterande metallpulver för industriella tillämpningar.
Förfrågan för att få bästa pris och anpassad lösning för ditt företag!
Relaterade artiklar
Om Met3DP
Senaste uppdateringen
Vår produkt
KONTAKTA OSS
Har du några frågor? Skicka oss meddelande nu! Vi kommer att betjäna din begäran med ett helt team efter att ha fått ditt meddelande.
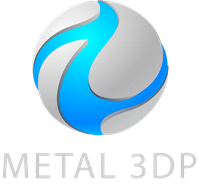
Metallpulver för 3D-printing och additiv tillverkning