Pulver för behandling efter atomisering
Innehållsförteckning
Imagine a sculptor meticulously crafting a masterpiece from a block of marble. But in the world of Additive Manufacturing (AM), also known as 3D printing, the raw material isn’t quite as monolithic. Instead, metal AM relies on a symphony of tiny metallic particles – powders – to build objects layer by layer.
However, the story doesn’t end with the creation of these metal powders. pulver för behandling efter finfördelning plays a crucial role in ensuring these metallic marvels meet the exacting standards of the AM industry.
This article delves into the fascinating world of powders for post-atomization treatment, exploring their characteristics, applications, and the factors that differentiate them.
Overview of Powder for Post-Atomization Treatment
What is atomization? Think of it as the act of transforming molten metal into a fine mist of particles. Various techniques, like gas or water atomization, achieve this by breaking down the liquid metal stream into a sea of tiny droplets that solidify in mid-air.
But the journey doesn’t stop there. The resulting metal powder, while seemingly ready for AM, might harbor some imperfections. Here’s where post-atomization treatment steps in. These specialized processes refine the powder characteristics, optimizing them for the specific demands of AM techniques like Selective Laser Melting (SLM) or Electron Beam Melting (EBM).
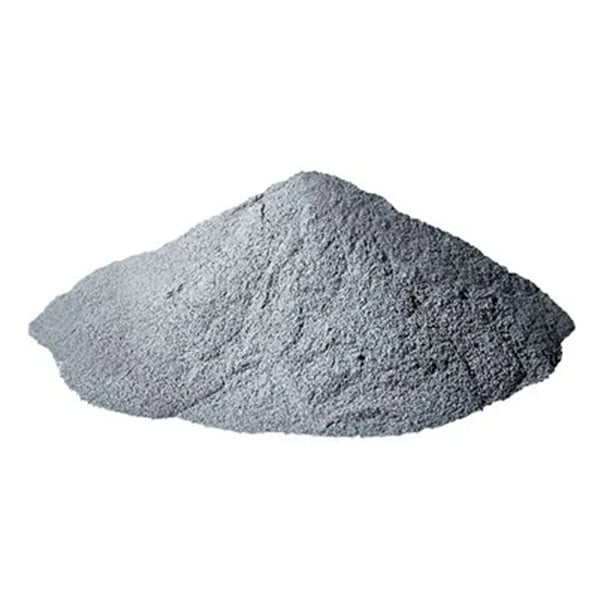
Characteristics of Powders for Post-Atomization Treatment
Imagine a baker meticulously sifting flour – ensuring consistency in particle size for that perfect cake. Similarly, powders for post-atomization treatment undergo a critical analysis of various characteristics:
- Partikelstorlek och fördelning: Powders for AM require a tightly controlled particle size range. Particles that are too large can hinder flowability and lead to uneven layer deposition during printing. Conversely, excessively fine particles can cause challenges in handling and might even impede laser penetration during the AM process.
- Partikelmorfologi: The shape of the powder particles also plays a vital role. Ideally, spherical particles with smooth surfaces offer the best flowability and packing density, leading to a more uniform and predictable build process.
- Kemisk sammansättning: Even the slightest variations in the chemical makeup of the powder can significantly impact the final properties of the printed part. Post-atomization treatments can help address issues like oxide formation or the presence of unwanted elements.
- Flytbarhet: Efficient flow of powder is essential for smooth AM operation. Powders with poor flowability create challenges in feeding mechanisms and can lead to inconsistencies in layer density.
Post-atomization treatments focus on optimizing these characteristics, ensuring the resulting powder is:
- Precisely sized and distributed: Think of it as having a uniform batch of flour, perfect for consistent baking results.
- Spherically shaped: Imagine round, smooth marbles – ideal for packing tightly and enabling seamless flow.
- Chemically pure: Just like following a recipe exactly, the powder needs the right ingredients for a successful print.
- Highly flowable: Imagine sand effortlessly pouring through an hourglass – that’s the desired flow characteristic for optimal AM performance.
Applications of Powders for Post-Atomization Treatment
Powders for post-atomization treatment cater to a diverse range of applications within the realm of AM. Here are some key areas:
- Aerospace: The AM industry is revolutionizing aerospace by creating lightweight, high-strength components. Powders with precise characteristics are crucial for building reliable parts for aircraft and spacecraft, where safety and performance are paramount.
- Medicinska implantat: Customized medical implants tailored to individual patients are becoming a reality thanks to AM. Here, biocompatible powders with exceptional purity are essential for creating implants that seamlessly integrate with the human body.
- Fordon: The automotive industry is increasingly leveraging AM for lightweight components and complex geometries. Powders with optimized flowability ensure consistent printing results, vital for mass production in the automotive sector.
- Konsumentvaror: From customized bike parts to intricate jewelry, AM is making its mark in the consumer goods space. Powders with a balance of aesthetics and functionality are necessary for creating visually appealing and durable consumer products.
Key Post-Atomization Treatment Processes
Several post-atomization treatments play a vital role in refining the characteristics of metal powders for AM:
- Siktning och klassificering: Similar to sifting flour, sieving separates powder particles into different size ranges. This helps achieve the desired particle size distribution for specific AM applications.
- Degassification: Metal powders might contain trapped gasses from the atomization process. Degassification techniques like vacuum drying remove these gasses, preventing them from causing voids or porosity in the final printed part.
- Spheroidization: Some post-atomization treatments, like plasma atomization, can inherently produce powders with a more spherical morphology. However, for powders generated through other techniques, additional processes like rotary atomization or chemical milling can help improve their sphericity.
- Surface Modification: Tailoring the surface chemistry of the powder particles can enhance their performance in the AM process. Techniques like carbonitriding or coating with lubricants can improve flowability and laser interaction during printing.
Att välja rätt Post-Atomization Treatment:
Selecting the most suitable post-atomization treatment depends on several factors:
- The desired characteristics of the final powder: Is a narrow particle size distribution or improved flowability the top priority?
- The type of metal powder: Different metals might respond better to specific post-atomization techniques.
- The intended AM application: The requirements for powders used in aerospace components might differ significantly from those for consumer goods.
Here’s a table summarizing the advantages and disadvantages of some common post-atomization treatments:
Behandling | Fördelar | Nackdelar |
---|---|---|
Sieving and Classification | Achieves precise particle size distribution | Can be time-consuming and might result in material loss |
Degassification | Reduces porosity and improves mechanical properties | May require specialized equipment and can be energy-intensive |
Sfäroidisering | Förbättrar flytbarhet och packningsdensitet | Can be an expensive process, and some techniques might introduce surface impurities |
Modifiering av ytan | Improves flowability and laser interaction | May alter the chemical composition of the powder and require stringent control |
It’s important to note that these treatments are often combined to achieve the optimal powder characteristics. For instance, sieving might be used in conjunction with degassing to ensure a precisely sized and gas-free powder.
Comparison of Powders for Post-Atomization Treatment
Metal powders can be broadly categorized into two types based on their origin:
- Virgin Powders: These powders are produced directly from primary metal sources and undergo post-atomization treatment for AM applications.
- Återvunnet pulver: With a growing focus on sustainability, recycled metal powders are gaining traction. These powders are derived from scrap metal and can be subjected to post-atomization treatments to meet AM quality standards.
Here’s a comparison of virgin and recycled powders for post-atomization treatment:
Parameter | Virgin Powders | Återvunna pulver |
---|---|---|
Kemisk sammansättning | Generally higher purity and consistency | Might contain trace elements or impurities from the source material |
Flytbarhet | Typically good flowability due to minimal handling | May require additional post-atomization treatment to improve flowability |
Kostnad | Generally more expensive due to the virgin material source | Can be a more cost-effective option |
Miljöpåverkan | Higher environmental footprint due to virgin metal extraction | Lower environmental impact due to material reuse |
The choice between virgin and recycled powders depends on the specific application and the desired balance between cost, performance, and sustainability.
Future of Powders for Post-Atomization Treatment
The realm of powders for post-atomization treatment is constantly evolving. Here are some exciting trends to watch for:
- Development of advanced post-atomization techniques: Researchers are exploring novel methods like microwave or ultrasonic treatment to further refine powder characteristics.
- Focus on sustainable practices: The use of recycled powders and the development of environmentally friendly post-atomization processes are gaining importance.
- Tailored powder design: The future might see powders specifically engineered with customized properties for unique AM applications.
In conclusion, powders for post-atomization treatment play a critical, yet often unseen, role in the success of Additive Manufacturing. By understanding their characteristics, applications, and the various treatment processes, we gain a deeper appreciation for the intricate world that builds the future, one tiny particle at a time.
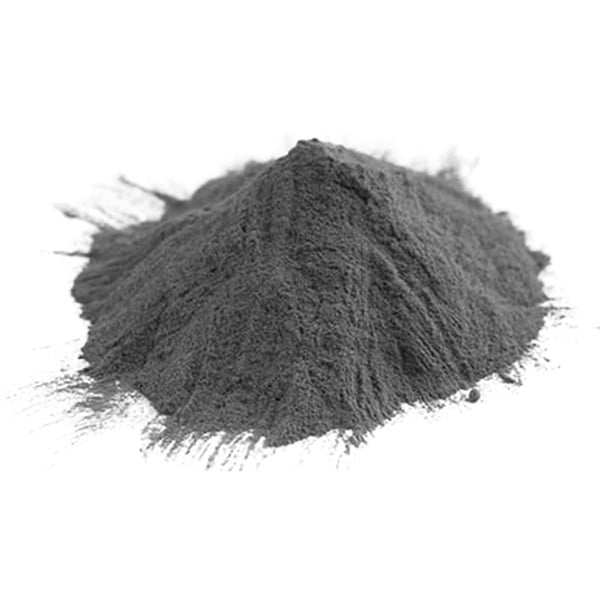
VANLIGA FRÅGOR
What are the typical sizes of powders used in AM?
The particle size range for powders used in AM can vary depending on the specific application. Typically, powders range from 10 to 150 micrometers in diameter.
Tillämpning | Typical Particle Size Range (micrometers) |
---|---|
Flyg- och rymdindustrin | 20-60 |
Medicinska implantat | 40-100 |
Fordon | 50-120 |
Konsumentvaror | 70-150 |
How does the quality of the powder impact the final printed part?
The quality of the powder has a significant influence on the properties of the final printed part. Powder characteristics like size, shape, and chemical composition can affect factors like:
- Mekanisk hållfasthet: Inclusions, voids, or impurities in the powder can compromise the mechanical strength of the printed part.
- Ytfinish: The surface roughness of the powder particles can translate to a rougher surface finish on the printed part.
- Dimensionell noggrannhet: Inconsistent particle size distribution can lead to dimensional inaccuracies in the printed part.
What are some of the challenges associated with using recycled powders for AM?
While recycled powders offer a sustainable alternative, they do come with some challenges:
- Kemisk sammansättning: Recycled powders might contain trace elements or impurities from the source material. These need to be carefully monitored and controlled to ensure the final part meets performance specifications.
- Flytbarhet: Recycled powders might have undergone multiple processing steps, potentially impacting their flowability. Additional post-atomization treatment might be necessary to achieve optimal flow characteristics.
- Sorting and Segregation: Recycled powders might require more rigorous sorting and classification processes to ensure consistent particle size distribution.
What are the benefits of using spherical powders in AM?
Spherical powders offer several advantages in AM:
- Förbättrad flytbarhet: Spherical particles with smooth surfaces flow more easily, leading to smoother layer formation during printing.
- Förbättrad packningstäthet: Spherical particles pack more tightly, minimizing voids and improving the overall density of the printed part.
- Minskad porositet: Minimized voids translate to reduced porosity, leading to stronger and more consistent mechanical properties.
How can users ensure they are selecting the right powder for their AM application?
Here are some tips for selecting the right powder for your AM application:
- Rådgör med en materialleverantör: Material suppliers can offer expert advice on powder selection based on your specific needs and the intended application.
- Consider the desired properties of the final part: Factors like mechanical strength, surface finish, and dimensional accuracy should guide your powder selection.
- Evaluate the cost vs. performance trade-off: Virgin powders might offer superior performance, but recycled powders can be a more cost-effective option.
By understanding the intricacies of powders for post-atomization treatment, users can make informed decisions that contribute to successful and high-quality Additive Manufacturing projects.
Dela på
MET3DP Technology Co, LTD är en ledande leverantör av lösningar för additiv tillverkning med huvudkontor i Qingdao, Kina. Vårt företag är specialiserat på 3D-utskriftsutrustning och högpresterande metallpulver för industriella tillämpningar.
Förfrågan för att få bästa pris och anpassad lösning för ditt företag!
Relaterade artiklar
Om Met3DP
Senaste uppdateringen
Vår produkt
KONTAKTA OSS
Har du några frågor? Skicka oss meddelande nu! Vi kommer att betjäna din begäran med ett helt team efter att ha fått ditt meddelande.
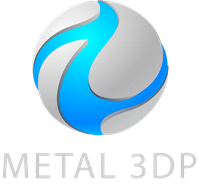
Metallpulver för 3D-printing och additiv tillverkning