3D-utskrift med pulverlaser för flyg- och rymdtillämpningar
Innehållsförteckning
Pulver Laser 3D-utskriftäven känd som Laser Powder Bed Fusion (LPBF), spelar en viktig roll inom flygindustrin och erbjuder flera fördelar jämfört med traditionella tillverkningstekniker.
1. Lättvikt, komplexa komponenter:
1. Tillverkning av flygplansdelar
Kan 3D-skrivare med pulverlaser användas för att tillverka motorkomponenter på flygplan?
Ja, absolut! 3D-skrivare med pulverlaser spelar en allt viktigare roll vid tillverkningen av komponenter till flygplansmotorer. Här’är varför:
Fördelar:
Komplex, lättviktig design: 3D-printing möjliggör intrikata konstruktioner med invändiga kanaler och gitter, vilket inte är möjligt med traditionella tekniker. Detta kan leda till lättare och starkare komponenter, vilket förbättrar bränsleeffektiviteten och prestandan.
Högpresterande material: LPBF-skrivare kan hantera avancerade metallegeringar som titan och Inconel, som är avgörande för att klara de höga temperaturerna och trycken i jetmotorer.
Minskat slöseri och kortare ledtider: 3D-printing använder ofta mindre material än traditionell subtraktiv tillverkning, vilket minimerar avfallet. Dessutom kan den effektivisera produktionen och minska ledtiderna jämfört med gjutning eller smide.
Exempel på detta:
Rolls-Royce: De använder LPBF för komplexa brännkammare i sin Pearl 10X-motor och hävdar en effektivitetsökning på 5%.
GE Aviation: De bygger världens största LPBF-skrivare för att tillverka strukturella komponenter till jetmotorer för enkelgångsflygplan.
Honeywell: De använder 3D-printing för bränslemunstycken och andra motorkomponenter i syfte att minska vikt och utsläpp.
Utmaningar:
Kostnad: LPBF-skrivare är för närvarande dyra, men kostnaderna sjunker.
Kvalifikationer: Omfattande tester och certifiering är nödvändiga för säkerhetskritiska delar som motorkomponenter.
Begränsad byggstorlek: Vissa skrivare har storleksbegränsningar, men större system håller på att utvecklas.
LPBF utmärker sig genom att skapa komplicerade lättviktsdelar med invändiga kanaler och gitter, vilket är omöjligt med konventionella metoder. Detta minskar vikten utan att kompromissa med hållfastheten, vilket är avgörande för bränsleeffektivitet och prestanda. Några exempel är:
Bränsleinsprutare: Komplexa inre geometrier för optimal bränsleblandning och förbränning.
Satellitfästen: Lätt och stark för minskad nyttolastvikt.
Värmeväxlare: Komplexa interna kanaler för effektiv värmeöverföring.
2. exempel på flygplanskomponenter
Bränslesystemets komponenter: Munstycken, injektorer och värmeväxlare kan 3D-printas med komplexa inre kanaler för förbättrat bränsleflöde och värmeöverföring.
Invändiga komponenter: Fästen, clips och andra icke-kritiska delar kan 3D-printas för viktminskning och kundanpassning.
Motorkomponenter: Vissa företag experimenterar med att 3D-printa vissa motorkomponenter, som t.ex. förbränningsugnar och turbinblad.
Obemannade flygfarkoster (UAV): På grund av sin lätta vikt och komplexa konstruktion är UAV:er en utmärkt kandidat för 3D-printade komponenter.
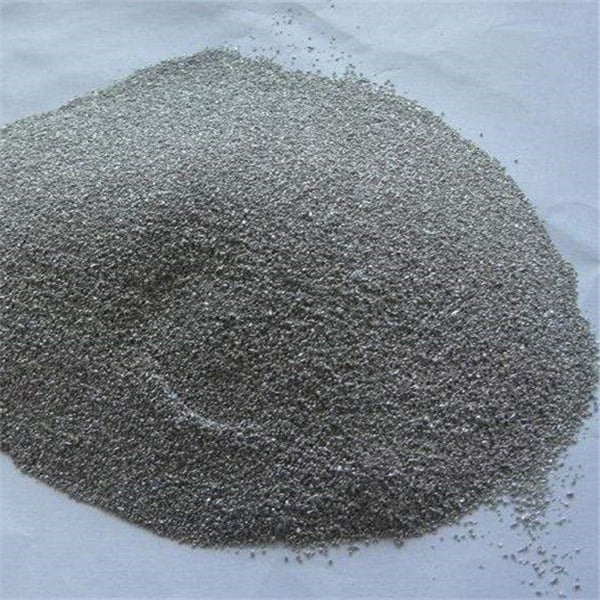
2. Specialtillverkade delar och tillverkning på begäran:
LPBF möjliggör snabb produktion av kundanpassade detaljer, vilket är viktigt för reparationer, prototyper och lågvolymstillämpningar. Detta minskar beroendet av storskalig tillverkning och möjliggör snabbare leveranstider. Exempel på detta är:
1. Hastighet och anpassning:
Snabbare handläggningstider: LPBF eliminerar traditionella verktyg och minskar drastiskt ledtiderna för specialtillverkade detaljer. Tänk dig att du behöver ett unikt fäste till ditt flygplan; istället för månader av väntan kan det skrivas ut på några dagar.
Oöverträffad anpassning: Komplexa geometrier och invecklade konstruktioner är en barnlek för LPBF. Tänk dig lättviktspaneler med interna gitterstrukturer för flygplan eller skräddarsydda beslag för rymdskeppsexperiment - möjligheterna är oändliga.
2. Fördelar för specifika tillämpningar:
Inredningskomponenter till flygplan: Tänk dig kundanpassade paneler med integrerad belysning eller fästen som passar perfekt i icke-standardiserade utrymmen. Detta sparar vikt, minskar monteringstiden och förbättrar estetiken.
Rymdfarkostens komponenter: LPBF är perfekt för unika, uppdragsspecifika delar som antenner, fästen eller till och med små motorkomponenter. Föreställ dig att du skriver ut en anpassad värmeväxlare för ett specifikt månuppdrag, skräddarsydd för miljön och uppdragskraven.
Ersättningsdelar: Inget mer väntande på föråldrade eller skadade delar! LPBF möjliggör utskrift på begäran, vilket minimerar stilleståndstiden och säkerställer en smidig drift. Föreställ dig att du skriver ut en sällsynt växel för ett veteranflygplan eller ett kritiskt sensorhus för en rymdfarkost i omloppsbana.
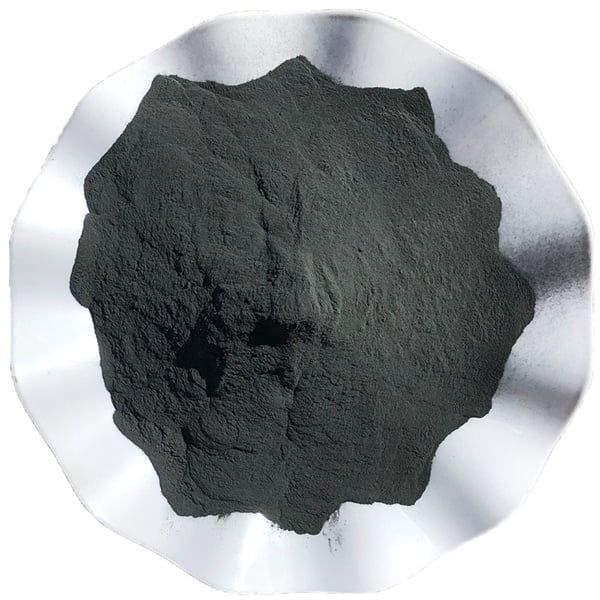
3. Avancerade material och prestanda av Pulver Laser 3D-utskrift
LPBF, eller Laser Powder Bed Fusion, handlar inte bara om att skapa kundanpassade delar; det frigör potentialen hos högpresterande material som tidigare var svåra eller omöjliga att använda i traditionell tillverkning. Låt oss dyka djupare in i hur LPBF möjliggör för industrier som flyg-, rymd-, raket- och turbinteknik:
1. Materiella underverk:
Titanlegeringar: Föreställ dig turbinblad som tål brännande temperaturer och intensivt tryck. LPBF gör det möjligt att trycka komplexa kylkanaler i dessa blad med hjälp av höghållfasta titanlegeringar, vilket maximerar prestanda och effektivitet.
Inconel: Denna nickel-kromlegering har exceptionell värmebeständighet och styrka, vilket gör den idealisk för komponenter i raketmotorer. LPBF möjliggör komplicerade konstruktioner som förbränningskammare och injektorer, vilket optimerar dragkraft och bränsleeffektivitet.
Aluminium-litium: Detta lättviktsunderverk minskar den värdefulla vikten i flyg- och rymdkonstruktioner. LPBF gör det möjligt att skriva ut komplexa ribbor, fackverk och bikakestrukturer, vilket skapar starka men ändå fjäderlätta komponenter för flygplan och rymdfarkoster.
2. Bortom exemplen:
Medicinska implantat: Biokompatibla titanlegeringar tryckta med LPBF skapar hållbara, lätta implantat som passar perfekt till patientens anatomi.
Tandprotetik: Starka, biokompatibla material som kobolt-krom används för LPBF-printade proteser och kronor, vilket ger överlägsen passform och funktion.
Avancerade verktyg: Föreställ dig kirurgiska instrument eller formar med invecklade detaljer, tryckta i slitstarka material som volframkarbid - LPBF gör det möjligt.
3. Låsa upp prestanda:
Förhållande mellan styrka och vikt: LPBF gör det möjligt att trycka lätta, komplexa strukturer som är otroligt starka, vilket är avgörande för att maximera prestandan inom flyg- och rymdindustrin och andra viktkänsliga applikationer.
Motståndskraft mot höga temperaturer: Material som Inconel tål extrem värme, vilket gör det möjligt för LPBF att skapa komponenter för jetmotorer, raketmotorer och andra miljöer med höga temperaturer.
Utmattningsegenskaper: LPBF-tryckta delar uppvisar utmärkt utmattningsbeständighet, vilket är viktigt för komponenter som utsätts för upprepad belastning i applikationer som turbiner och flygplansstrukturer.
Material | Viktiga egenskaper | Tillämpningar | Fördelar | Nackdelar | Kostnad | Efterbearbetning | Certifiering |
---|---|---|---|---|---|---|---|
Titanlegeringar | Högt förhållande mellan styrka och vikt, hög temperaturbeständighet, korrosionsbeständighet | Flyg- och rymdindustrin, medicinteknik, fordonsindustrin | Utmärkta mekaniska egenskaper, biokompatibilitet, låg vikt | Hög materialkostnad, komplex efterbearbetning | Hög | Värmebehandling, maskinbearbetning | Stränga regler |
Inconel | Beständighet mot höga temperaturer, hållfasthet, korrosionsbeständighet | Flyg- och rymdindustrin, energi, kemisk bearbetning | Utmärkt prestanda vid höga temperaturer, motståndskraft mot tuffa miljöer | Hög materialkostnad, komplex efterbearbetning | Hög | Värmebehandling, maskinbearbetning | Stränga regler |
Aluminium-Litium | Lättvikt, hög hållfasthet, god styvhet | Flyg- och rymdindustrin, fordonsindustrin, försvarsindustrin | Minskad vikt, förbättrad bränsleeffektivitet | Lägre hållfasthet än titanlegeringar, mer benägna att korrodera | Medium | Värmebehandling, maskinbearbetning | Mindre stränga regler |
Rostfritt stål | Hög hållfasthet, korrosionsbeständighet, biokompatibilitet | Medicin, fordonsindustri, industri | Bra kombination av egenskaper, kostnadseffektivt | Lägre styrka/vikt-förhållande än titanlegeringar, inte lika korrosionsbeständigt som Inconel | Låg | Värmebehandling, maskinbearbetning | Varierar beroende på applikation |
Verktygsstål | Hög hårdhet, slitstyrka och seghet | Verktyg, tillverkning, fordonsindustrin | Utmärkt slitstyrka, lång verktygslivslängd | Hög materialkostnad, komplex efterbearbetning | Medium | Värmebehandling, maskinbearbetning | Varierar beroende på applikation |
Nylon | Lätt, stark och flexibel | Fordon, konsumentvaror, medicinteknik | Lätt, kostnadseffektiv och biokompatibel | Lägre hållfasthet och temperaturbeständighet än metaller | Låg | Minimal efterbearbetning | Varierar beroende på applikation |
Polypropylen | Lättvikt, kemikaliebeständighet, låg kostnad | Konsumentvaror, förpackningar, medicinteknik | Lätt, kostnadseffektiv, god kemisk beständighet | Lägre hållfasthet och temperaturbeständighet än metaller | Låg | Minimal efterbearbetning | Varierar beroende på applikation |
4. Designfrihet och optimering:
LPBF, eller Laser Powder Bed Fusion, handlar inte bara om att skriva ut komplexa former; det handlar också om att konstruerar delar som tänjer på gränserna för vad som är möjligt. Till skillnad från traditionell tillverkning med dess begränsningar erbjuder LPBF oöverträffad designfrihet och optimeringvilket leder till lättare, starkare och mer effektiva komponenter. Låt oss utforska de spännande möjligheterna:
1. Släppa loss kreativiteten:
Bikakestrukturer: Föreställ dig lätta men ändå otroligt starka flygplansvingar eller paneler till rymdfarkoster, som åstadkoms genom intrikata, LPBF-tryckta bikakestrukturer. Dessa konstruktioner minimerar materialanvändningen samtidigt som de maximerar styrka och styvhet, vilket leder till betydande viktminskningar och förbättrad bränsleeffektivitet.
Topologiskt optimerade delar: Säg adjö till skrymmande, ineffektiva konstruktioner! LPBF gör det möjligt att skriva ut delar som är optimerade utifrån specifika belastnings- och spänningskrav. Föreställ dig en bilfjädringskomponent som utformats med hjälp av topologioptimering och uppnår optimal styrka med minimalt material, vilket sparar vikt och förbättrar prestandan.
Biomimetisk design: Hämta inspiration från naturen! LPBF gör det möjligt att trycka komponenter som är inspirerade av biologiska strukturer, som fågelben eller spindelväv. Föreställ dig ett turbinblad med inre kanaler som efterliknar en fågelvinge, vilket ger överlägsen värmeöverföring och effektivitet.
2. Bortom exemplen:
Medicinska implantat: LPBF gör det möjligt att skriva ut implantat med komplexa, porösa strukturer som efterliknar naturligt ben, vilket främjar bentillväxt och osseointegration.
Konsumentvaror: Föreställ dig lätta, ergonomiskt utformade cyklar eller sportutrustning, tryckta med intrikata interna strukturer för optimal prestanda och komfort.
Arkitektur: LPBF öppnar dörren för att skriva ut komplicerade byggnadskomponenter med minskad materialanvändning och förbättrad styrka, vilket banar väg för hållbar och innovativ arkitektur.
3. Frigörande av potential:
Viktminskning: Genom att skapa lättviktsstrukturer med minimalt med material leder LPBF till betydande viktbesparingar i kritiska applikationer som flyg, fordon och medicinteknik.
Förbättrad prestanda: Optimerad design och biomimetisk inspiration kan leda till förbättrad prestanda inom områden som värmeöverföring, vätskeflöde och strukturell styrka.
Hållbarhet: Minskad materialanvändning och lättare komponenter ger lägre miljöpåverkan under produktens hela livscykel.
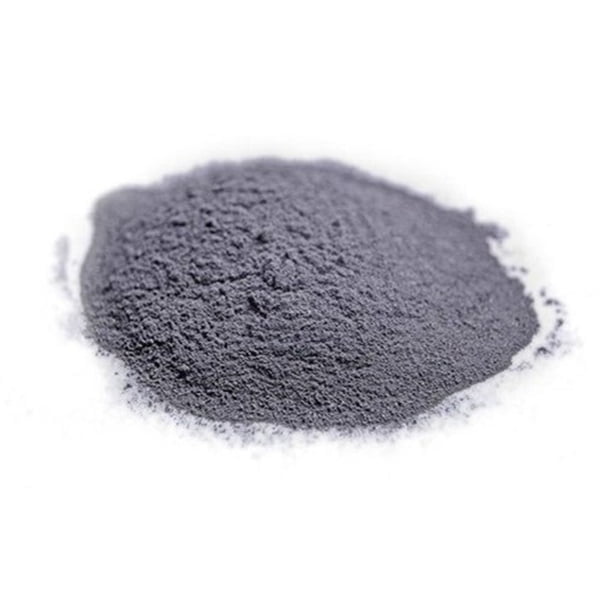
5. Utmaningar och överväganden:
LPBF erbjuder spännande möjligheter, men det är viktigt att vara medveten om de utmaningar som följer med denna teknik:
1. Kostnad:
Maskinkostnad: Jämfört med traditionell tillverkningsutrustning kan LPBF-maskiner vara betydligt dyrare, särskilt för högpresterande skrivare. Detta begränsar tillgängligheten och ökar kostnaden per detalj.
Materialkostnad: Högpresterande material som titanlegeringar och Inconel är i sig dyra, och pulverformen som används i LPBF medför ytterligare kostnader jämfört med bulkmaterial.
2. Efterbearbetning:
Stöd för borttagning: LPBF kräver ofta att man trycker stödstrukturer för komplexa geometrier. Att ta bort dessa stöd kan vara tidskrävande och kräva specialteknik, vilket ökar den totala kostnaden och komplexiteten.
Efterbehandling: Beroende på användningsområde kan delarna behöva värmebehandling, maskinbearbetning eller andra efterbehandlingssteg för att uppnå önskade egenskaper, vilket ytterligare ökar bearbetningstiden och kostnaden.
3. Certifiering:
Stränga regler: För tillämpningar inom kritiska branscher som flyg- och rymdindustrin eller medicinteknik måste komponenterna uppfylla strikta regler och säkerhetsstandarder. Detta innebär ofta omfattande test- och kvalificeringsprocesser, vilket kan vara tidskrävande och dyrt.
Begränsade standarder: Även om standarderna för LPBF utvecklas är de inte lika mogna som de för traditionella tillverkningsmetoder. Detta kan skapa osäkerhet och ytterligare hinder för certifiering.
4. Ytterligare överväganden:
Designkompetens: För att effektivt utnyttja LPBF krävs specialkunskaper om teknikens möjligheter och begränsningar, vilket ökar projektets totala komplexitet.
Kvalitetskontroll: Att säkerställa en jämn kvalitet och repeterbarhet på detaljerna kan vara en utmaning på grund av faktorer som pulveregenskaper, laserparametrar och maskinkalibrering.
Miljöpåverkan: Även om LPBF kan ge materialbesparingar jämfört med traditionella metoder, måste energiförbrukningen och hanteringen av pulveravfall beaktas för ett hållbart införande.
Dela på
MET3DP Technology Co, LTD är en ledande leverantör av lösningar för additiv tillverkning med huvudkontor i Qingdao, Kina. Vårt företag är specialiserat på 3D-utskriftsutrustning och högpresterande metallpulver för industriella tillämpningar.
Förfrågan för att få bästa pris och anpassad lösning för ditt företag!
Relaterade artiklar
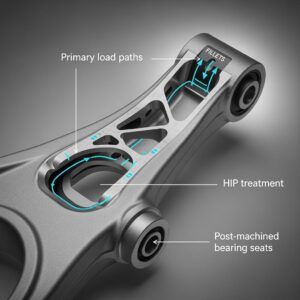
Metal 3D Printing for U.S. Automotive Lightweight Structural Brackets and Suspension Components
Läs mer "Om Met3DP
Senaste uppdateringen
Vår produkt
KONTAKTA OSS
Har du några frågor? Skicka oss meddelande nu! Vi kommer att betjäna din begäran med ett helt team efter att ha fått ditt meddelande.