fördelar med 3D-utskrift med pulverlaser vid tillverkning av bildelar
Innehållsförteckning
3D-utskrift med pulverlaser, även känd som Selective Laser Sintering (SLS), håller på att förändra fordonsindustrin genom att erbjuda en unik kombination av designfrihet, produktionsflexibilitet och lättviktskapacitet. Tekniken använder en högeffektslaser för att smälta och smälta samman pulveriserade metall- eller plastmaterial lager för lager, vilket skapar komplexa och funktionella delar direkt från digitala modeller.
1. Konstruktion av komplexa fordonskomponenter
3D-skrivare med pulverlaser bryter mot traditionell tillverkning genom att möjliggöra intrikata geometrier, gitterstrukturer och interna kanaler som tidigare var omöjliga.
1. Lättvikt:
Aerospace: Föreställ dig flygplansvingar med intrikata gitterstrukturer som är otroligt starka men ändå ultralätta, vilket maximerar bränsleeffektiviteten och räckvidden. Detta kan översättas till lättare rymdfarkoster, satelliter och till och med raketer, vilket möjliggör mer ambitiösa rymduppdrag.
Fordon: Komplexa motordelar med interna kanaler för effektiv kylning, lätta bilramar med överlägsen krocksäkerhet och anpassade, viktoptimerade komponenter för elfordon är alla möjliga med 3D-printning med pulverlaser.
Medicinska implantat: Föreställ dig proteser och implantat som är perfekt anpassade till en individs anatomi, vilket minskar vikten och förbättrar komfort och rörlighet.
2. Förbättrad funktionalitet:
Konsolidering av delar: Traditionellt sammansatta produkter kan skrivas ut som enskilda enheter, vilket minskar komplexiteten, monteringstiden och potentiella felpunkter. Föreställ dig en jetmotor med integrerade värmeväxlare eller ett kirurgiskt verktyg med inbyggda sensorer, allt utskrivet på en gång.
Prestandaoptimering: Interna kanaler för vätskeflöde, värmeavledning eller till och med luftcirkulation kan utformas och integreras på ett komplicerat sätt i en enda tryckt komponent, vilket leder till betydande prestandaförbättringar.
Arkitektur: Byggnader med komplexa bärande strukturer, intrikata fasader med integrerade funktioner eller till och med möbler med inbyggda funktioner kan skapas med hjälp av 3D-printade komponenter.
3. Anpassning:
Personanpassad medicin: Tänk dig proteser, implantat eller till och med kirurgiska verktyg som är perfekt anpassade till en individs anatomi och behov, vilket leder till förbättrade patientresultat och kortare återhämtningstider.
Konsumentvaror: Tillverkning på begäran av skräddarsydd sportutrustning, elektronik med personliga funktioner eller till och med reservdelar till vilken apparat som helst kan bli verklighet.
Massanpassning: Föreställ dig skor med specialanpassade sulor eller kläder med perfekt anpassad design, allt producerat effektivt genom 3D-printing.
4. Utöver dessa exempel:
3D-utskrift med pulverlaser öppnar dörrar för helt nya designmöjligheter som vi inte ens har kunnat föreställa oss ännu. Föreställ dig porösa material för avancerad filtrering, komplexa vätskekretsar för mikrofluidiska enheter eller intrikata metamaterial med unika egenskaper. Möjligheterna är verkligen oändliga.
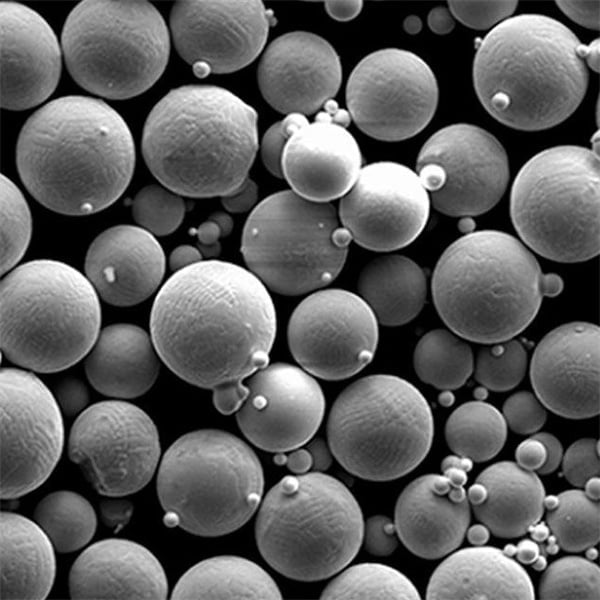
2. 3D-utskrift med pulverlaser Flexibilitet och smidighet i produktionen
Till skillnad från traditionella metoder kräver pulverlasertryck inga verktyg, vilket minskar ledtiderna och möjliggör snabb prototyptillverkning och iteration. Detta gör det möjligt:
1. Snabbare utvecklingscykler
- Snabb prototyptillverkning: Glöm veckor eller månader av väntan på maskinbearbetade prototyper. Med 3D-utskrift med pulverlaserkan du iterera på design snabbt och billigt, testa och förfina koncept på bara några dagar. Detta påskyndar forskning och utveckling inom olika branscher:
- Fordon: Konstruera och testa nya motorkomponenter, aerodynamiska former eller till och med kompletta bilkoncept inom veckor istället för månader.
- Sjukvård: Utveckla och testa anpassade proteser, kirurgiska verktyg eller till och med läkemedelstillförselanordningar med oöverträffad hastighet, vilket leder till snabbare medicinska framsteg.
- Konsumentelektronik: Experimentera med ny design, iterera på funktioner och få snabb feedback från användarna, vilket gör att innovativa produkter kommer ut på marknaden snabbare.
2. Reducerad lagerhållning:
- Skriv ut på begäran: Du behöver inte längre förutse efterfrågan och hålla stora lager av reservdelar. Skriv helt enkelt ut dem efter behov, minimera lagringskostnaderna och minska risken för föråldrade delar. Detta är särskilt fördelaktigt för:
- Aerospace: Skriv ut reservdelar till kritiska flygplanskomponenter på begäran vid underhållsanläggningar, vilket minskar stilleståndstiden och förbättrar den operativa effektiviteten.
- Tillverkning: Eliminera behovet av stora lager och förenkla leveranskedjorna genom att skriva ut verktyg, jiggar och fixturer efter behov på verkstadsgolvet.
- Militär: Skriv ut anpassade reservdelar för utrustning på avlägsna platser, vilket säkerställer uppdragsberedskapen och minskar logistiska utmaningar.
3. Lokaliserad produktion:
- Decentraliserad tillverkning: Sätt upp hubbar för 3D-printing närmare monteringslinjerna eller till och med hos slutanvändarna, vilket minskar transportkostnaderna, ledtiderna och koldioxidavtrycket. Detta är särskilt värdefullt för:
- Avlägsna platser: Skriv ut kritiska delar på plats för gruvdrift, offshore-plattformar eller till och med rymdstationer, vilket minimerar beroendet av långdistanslogistik.
- Personligt anpassade produkter: Skriv ut specialanpassade produkter som proteser, tandimplantat eller till och med kläder direkt på försäljningsstället för att tillgodose individuella behov och önskemål.
- Katastrofhjälp: Skriv ut viktiga verktyg, skyddsrum eller till och med medicinska förnödenheter på begäran i katastrofområden, vilket ger snabb och riktad hjälp.
4. Utöver dessa fördelar:
- Förbättrad lyhördhet: Anpassa dig snabbt till förändrade marknadskrav eller oväntade störningar i leveranskedjan genom att skriva ut delar på begäran.
- Minskat avfall: Eliminerar behovet av subtraktiva tillverkningsprocesser som genererar materialavfall, vilket bidrar till en mer hållbar tillverkningsmetod.
- Låsa upp nya affärsmodeller: Utforska möjligheter som att erbjuda kundanpassning på begäran, distribuerade tillverkningsnätverk eller till och med 3D-utskrifter som en tjänst.
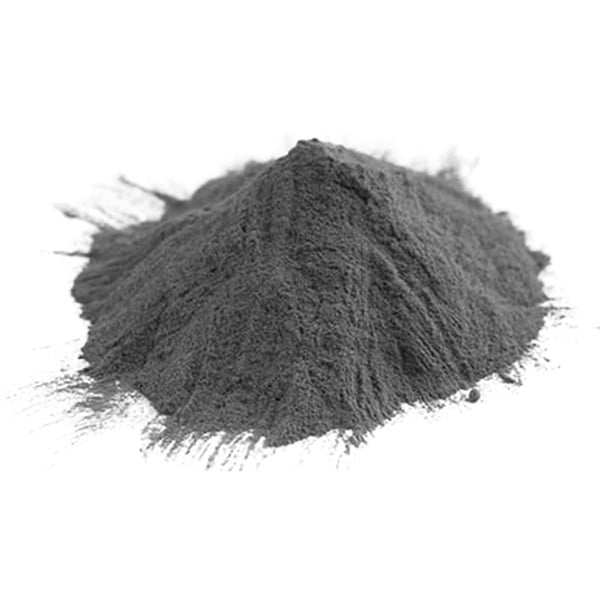
3. Materialdiversitet och resultat
Pulverlaserskrivare erbjuder ett brett utbud av material med olika egenskaper
1. Metaller: Oöverträffad styrka och hållbarhet:
- Aluminium: Lätt men ändå robust, perfekt för komponenter inom flyg- och rymdindustrin, värmeväxlare och till och med medicinska implantat. Dess tryckbarhet möjliggör intrikata konstruktioner som optimerar förhållandet mellan styrka och vikt.
- Titan: Känd för sin styrka, biokompatibilitet och korrosionsbeständighet, idealisk för krävande applikationer som flygplansdelar, medicinska implantat och proteser. 3D-utskrifter möjliggör komplexa gitterstrukturer som ytterligare förbättrar hållfastheten och minskar vikten.
- Stål och legeringar: Från höghållfast rostfritt stål för verktyg och matriser till maråldrat stål för högpresterande delar - 3D-printing öppnar upp för en mängd möjligheter. Föreställ dig jetmotorkomponenter, kirurgiska instrument eller till och med specialdesignade verktyg som skrivs ut med de perfekta egenskaperna för jobbet.
2. Nylon: Den mångsidiga arbetshästen:
- Nylon 12: Stark, flexibel och lätt, idealisk för funktionella delar som kugghjul, snäppfästen och till och med slitstarka komponenter. Den släta ytfinishen och tryckbarheten gör den till ett populärt val för många olika applikationer.
- Glasfylld nylon: Glasfylld nylon ger extra styrka och värmebeständighet och används i krävande applikationer som bildelar, bärande konstruktioner och till och med funktionella prototyper. Dess förmåga att motstå höga temperaturer gör den idealisk för komponenter under huven eller till och med steriliserbara medicintekniska produkter.
3. Bortom metaller och nylon:
- Polypropen (PP): PP är lätt, kemikaliebeständigt och har god flexibilitet och används i vätskehanteringsapplikationer, medicintekniska produkter och till och med i konsumentprodukter som anpassade telefonskal.
- Polymerer som är resistenta mot höga temperaturer (HTP): För applikationer som kräver hög termisk stabilitet, t.ex. motorkomponenter eller delar till flyg- och rymdindustrin, erbjuder HTP överlägsen prestanda jämfört med traditionella plaster.
4. Kom ihåg att materialutforskningen pågår hela tiden:
- Nya material: Forskning och utveckling utökar ständigt materialpaletten, med möjligheter som sträcker sig från biokompatibla polymerer för medicinska tillämpningar till ledande filament för elektronikintegration.
- Materialkombinationer: Tryckning av flera material gör det möjligt att skapa objekt med olika egenskaper i en och samma del, vilket öppnar upp för nya designmöjligheter. Föreställ dig ett verktyg med ett slitstarkt handtag och ett flexibelt grepp, eller ett medicinskt implantat med en biokompatibel kärna och ett starkare yttre skal.
4. Utmaningar och överväganden
Även om det är lovande, 3D-utskrift med pulverlaser står inför vissa utmaningar:
1. Viktiga utmaningar
Utmaning | Beskrivning | Påverkan | Strategier för begränsning |
---|---|---|---|
Kostnad | 3D-skrivare och högpresterande material kan vara dyra, särskilt när det gäller stora delar. | Högre produktionskostnader, begränsad tillgänglighet för småföretag. | Forskning och utveckling för att sänka kostnaderna och optimera tryckprocesserna. |
Efterbearbetning | Tryckta delar kräver ofta rengöring, värmebehandling och efterbehandling. | Ökade ledtider, extra arbetskostnader, potentiella kvalitetsproblem. | Utveckling av automatiserade tekniker för efterbearbetning, värmebehandling på plats. |
Kvalitetskontroll | Att säkerställa en jämn kvalitet och uppfylla stränga fordonsstandarder är en utmaning. | Risk för defekter, bristande efterlevnad av föreskrifter. | Rigorösa rutiner för kvalitetskontroll, branschgemensamma standarder och certifieringar. |
2. Materialöverväganden
Material | Fastigheter | Tillämpningar | Utmaningar |
---|---|---|---|
Metaller (Aluminium, titan, stål, legeringar) | Hög hållfasthet, värmebeständighet och hållbarhet | Motorkomponenter, fästen, fjädringssystem | Materialtillgång, kostnad, efterbearbetning. |
Nylon (Nylon 12, glasfylld nylon) | Stark, lätt och slittålig | Kugghjul, bussningar, inre komponenter | Materialegenskaperna kan skilja sig från motsvarande produkter i bulk. |
Polypropylen (PP) | Lätt, kemikalieresistent, flexibel | Vätskehanteringsapplikationer, medicintekniska produkter, konsumentvaror | Begränsad tillgång till högpresterande material. |
Högtemperaturbeständiga polymerer (HTP) | Hög termisk stabilitet | Motorkomponenter, delar till flyg- och rymdindustrin | Hög kostnad, komplex efterbearbetning. |
3. Överväganden om design
Designfunktion | Fördelar | Utmaningar |
---|---|---|
Intrikata geometrier | Lättvikt, förbättrad funktionalitet, kundanpassning | Komplex designprocess, kräver specialiserad expertis. |
Gitterstrukturer | Förbättrat förhållande mellan styrka och vikt, minskad materialåtgång | Komplex tillverkning, utmaningar med kvalitetskontroll. |
Interna kanaler | Optimerat vätskeflöde, värmeavledning och luftcirkulation | Designkomplexitet, kräver specialiserad programvara. |
Dela på
MET3DP Technology Co, LTD är en ledande leverantör av lösningar för additiv tillverkning med huvudkontor i Qingdao, Kina. Vårt företag är specialiserat på 3D-utskriftsutrustning och högpresterande metallpulver för industriella tillämpningar.
Förfrågan för att få bästa pris och anpassad lösning för ditt företag!
Relaterade artiklar
Om Met3DP
Senaste uppdateringen
Vår produkt
KONTAKTA OSS
Har du några frågor? Skicka oss meddelande nu! Vi kommer att betjäna din begäran med ett helt team efter att ha fått ditt meddelande.
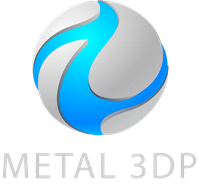
Metallpulver för 3D-printing och additiv tillverkning