3D-utskrift med pulverlaser för medicintekniska produkter
Innehållsförteckning
3D-utskrift med pulverlasersom omfattar tekniker som selektiv lasersintring (SLS) och direkt metallsintring (DMLS), håller snabbt på att förändra det medicintekniska landskapet. Dessa skrivare erbjuder oöverträffad designfrihet, komplexa geometrier och biokompatibla material, vilket gör det möjligt:
1. Patientspecifik anpassning:
1. Protetik och implantat av 3D-utskrift med pulverlaser
Proteser:
- Exakt skräddarsydd: Till skillnad från traditionella proteser möjliggör 3D-utskrifter anpassning utifrån den individuella anatomin. Detta innebär en bättre passform, förbättrad komfort och i slutändan, förbättrad funktion. Föreställ dig en armprotes som perfekt matchar din benstruktur och muskelrörelser, vilket ger en naturlig rörelsekänsla och ökad fingerfärdighet.
- Lätt och tålig: 3D-utskrivna proteser kan vara lättare än traditionella motsvarigheter, vilket minskar trötthet och förbättrar bärbarheten. Dessutom erbjuder avancerade material både styrka och flexibilitet, vilket leder till hållbara och långlivade proteser.
- Mer prisvärd: Även om de initiala kostnaderna kan vara jämförbara, kan möjligheten att skapa proteser på begäran minska de långsiktiga kostnaderna för justeringar och utbyten. Detta gör proteser mer tillgänglig till ett bredare spektrum av individer.
- Förbättrad estetik: Glöm det klumpiga, generiska utseendet. 3D-utskrifter gör det möjligt att införliva personliga mönster, färger och till och med mönstervilket gör proteserna mer estetiskt tilltalande och återspeglar bärarens individualitet.
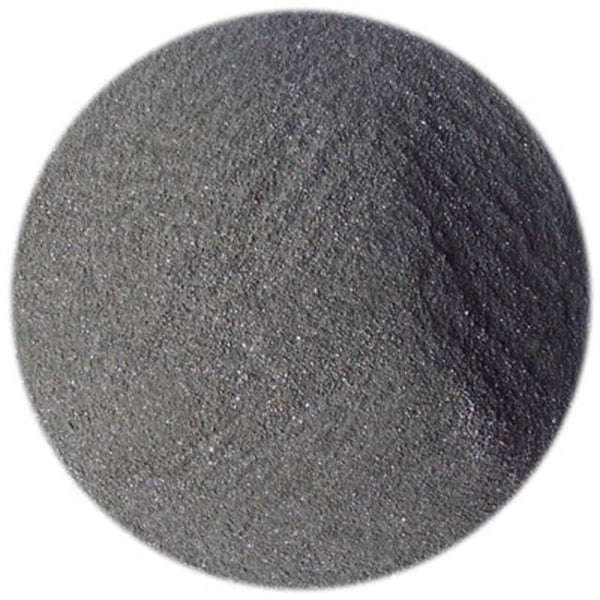
Implantat:
- Biokompatibla underverk: Specialdesignade implantat kan tillverkas av material med optimal biokompatibilitetDetta minskar risken för avstötning och säkerställer en bättre integration med kroppens vävnader. Detta är särskilt viktigt för implantat som höftledsproteser och tandkronor, där långsiktig framgång är beroende av sömlös integration.
- Förbättrad Osseointegration: 3D-printing gör det möjligt att skapa porösa strukturer som efterliknar naturligt ben, vilket främjar osseointegrationDetta är den process genom vilken benet växer runt och förenas med implantatet. Detta leder till ett starkare och stabilare implantat, vilket minskar smärtan och förbättrar funktionen.
- Komplexa och kundanpassade konstruktioner: 3D-printing gör det möjligt att skapa komplexa och patientspecifika implantat för komplicerade ingrepp. Föreställ dig en specialdesignad benställning som passar perfekt till patientens unika bendefekt och främjar optimal läkning och regenerering.
- Minskad operationstid och risk: Med exakt planering före operationen och patientanpassade implantat kan kirurgerna utföra minimalt invasiva ingrepp med kortare operationstider och potentiellt lägre risker. Detta leder till snabbare återhämtning och förbättrade patientresultat.
2. Kirurgiska guider och modeller:
Tänk dig en kirurg som minutiöst planerar en komplex operation, inte bara utifrån 2D-bilder utan även utifrån en konkret, 3D-utskriven replika av patientens anatomi. Det är denna verklighet som 3D-printing för med sig till det kirurgiska fältet, vilket revolutionerar det sätt på vilket ingrepp utförs och förbättrar resultaten för patienterna.
Patientspecifik precision:
- Förplanera varje rörelse: Till skillnad från plana röntgenbilder eller CT-skanningar ger 3D-utskrivna modeller en realistiska och manipulerbara representation av patientens anatomi. Kirurgerna kan visualisera och öva på hela ingreppet i förväg, identifiera potentiella utmaningar och optimera sitt tillvägagångssätt. Detta leder till ökad precision och minskad risk för komplikationer under operationen.
- Minimalt invasiv magi: Med en detaljerad förståelse av patientens anatomi kan kirurgerna välja mellan minimalt invasiva teknikervilket minskar vävnadsskador, ärrbildning och postoperativ smärta. Detta kan översättas till kortare återhämtningstider och bättre patientupplevelser.
- Specialtillverkade guider: 3D-utskrivna kirurgiska guider fungerar som mallar under operationen, vilket säkerställer exakt placering av implantat, skruvar eller andra kirurgiska instrument. Detta minimerar antalet fel och säkerställer optimala resultat, särskilt vid komplexa ingrepp som ledproteser eller tumörborttagning.
Fördelar bortom operationssalen:
- Förbättrad kommunikation: 3D-utskrivna modeller kan användas för att förklara komplexa medicinska tillstånd till patienterna på ett tydligt och begripligt sätt, vilket främjar bättre kommunikation och informerat beslutsfattande.
- Kirurgisk utbildning: Läkarstudenter och ST-läkare kan använda 3D-utskrivna modeller för att öva kirurgiska tekniker i en säker och realistisk miljö, vilket förbättrar deras färdigheter och beredskap för verkliga scenarier.
- Forskning och utveckling: 3D-utskrivna modeller kan användas för att utveckla och testa nya kirurgiska tekniker och teknologiervilket påskyndar utvecklingen inom området och i slutändan förbättrar patientvården.
2. Avancerad funktionalitet och prestanda:
Porösa och lättviktiga konstruktioner
3D-utskrifter revolutionerar implantatområdet och gör det möjligt att skapa porösa och lätta strukturer som tidigare var omöjliga att tillverka med traditionella metoder. Dessa innovativa implantat erbjuder en rad fördelar, bland annat
Förbättrad beninväxt:
- Att efterlikna naturen: 3D-printing gör det möjligt att skapa porösa strukturer som efterliknar den naturliga trabekulära benstrukturen. Detta ger en gynnsam miljö för benceller att växa och infiltrera, vilket främjar osseointegration, den process genom vilken benet fäster vid implantatet.
- Förbättrad stabilitet: Den ökade ytarean hos porösa implantat främjar starkare bindning mellan ben och implantatvilket leder till förbättrad stabilitet och minskad risk för att implantatet lossnar eller går sönder.
- Snabbare läkning: De sammankopplade porerna i implantatet möjliggör näringsämnen och blodflödevilket underlättar bentillväxt och ger snabbare läkningstider.
Minskad vikt och förbättrad hållfasthet:
- Lättviktsunderverk: 3D-utskrivna implantat kan vara betydligt tändare än traditionella implantat, vilket minskar påfrestningarna på det omgivande benet och vävnaden. Detta är särskilt fördelaktigt för patienter med osteoporos eller andra tillstånd som försvagar benet.
- Starkare än någonsin: Trots sin lägre vikt kan 3D-utskrivna implantat vara lika starka, eller till och med starkare, än traditionella implantat. Detta beror på att 3D-utskrifter gör det möjligt att skapa optimerade strukturer som är skräddarsydda för varje patients specifika behov.
Patientspecifik anpassning:
- Perfekt passform: 3D-utskrivna implantat kan vara specialdesignad för att matcha den exakta storleken och formen på patientens anatomi. Detta ger en perfekt passform och optimal lastfördelning, vilket minskar risken för komplikationer och förbättrar resultatet på lång sikt.
- Komplexa geometrier: 3D-printing gör det möjligt att skapa implantat med komplexa geometrier som skulle vara omöjliga att tillverka med traditionella metoder. Detta möjliggör behandling av komplexa fall som tidigare varit omöjliga att hantera.
Biokompatibla material
Ett brett utbud av biokompatibla material, som titan, koboltkrom och bioresorberbara polymerer, kan användas för att skapa enheter som integreras sömlöst med människokroppen.
Material som spelar roll:
- Titan: En stark, lätt och korrosionsbeständig metall som är mycket biokompatibel, vilket gör den idealisk för implantat som måste tåla höga belastningar, t.ex. höftledsproteser och tandimplantat.
- Cobalt Chrome: En annan stark och korrosionsbeständig metall som ofta används för implantat som måste vara starka och hållbara, t.ex. knäproteser och ryggradsimplantat.
- Bioresorberbara polymerer: Dessa material är utformade för att absorberas av kroppen över tid, vilket gör dem idealiska för tillfälliga implantat eller för användning i applikationer där långsiktig hållbarhet inte krävs.
Fördelar med biokompatibla material:
- Minskad risk för avstötning: Biokompatibla material är utformade för att accepteras av kroppen, vilket minskar risken för avstötning och komplikationer.
- Förbättrad Osseointegration: Biokompatibla material kan främja bentillväxt och integration med implantatet, vilket leder till förbättrad stabilitet och långsiktig framgång.
- Minskad smärta och inflammation: Biokompatibla material är mindre benägna att orsaka smärta och inflammation än traditionella implantatmaterial, vilket leder till en mer bekväm upplevelse för patienterna.
- Mångsidiga användningsområden: Biokompatibla material kan användas för att skapa ett brett utbud av implantat och anordningar, från enkla skruvar och plattor till komplexa skräddarsydda implantat.
Integrerad elektronik och sensorer
3D-utskrifter öppnar dörrar för att bygga in sensorer och elektronik direkt i enheter, vilket möjliggör övervakning i realtid och individanpassade behandlingar.
Sömlös integration:
- Direkt inbäddad: 3D-printing möjliggör exakt inbäddning av sensorer och elektronik i enhetens struktur, vilket eliminerar behovet av skrymmande externa komponenter. Detta leder till mer kompakta, bekväma och estetiskt tilltalande enheter.
- Optimerad funktionalitet: Integreringen av elektronik och sensorer kan skräddarsys efter varje patients specifika behov, vilket säkerställer optimal funktionalitet och prestanda.
- Mångsidiga användningsområden: Tekniken kan användas i en rad olika medicintekniska produkter, t.ex. pacemakers, insulinpumpar, system för läkemedelstillförsel och till och med konstgjorda organ.
Övervakning i realtid:
- Vitala hälsodata: Integrerade sensorer kan samla in realtidsdata om olika hälsoparametrar, t.ex. hjärtfrekvens, blodtryck, blodsockernivåer och syresättning av vävnader.
- System för tidig varning: Dessa data kan användas för att identifiera potentiella hälsoproblem i ett tidigt skede, vilket gör det möjligt att ingripa i tid och vidta förebyggande åtgärder.
- Personligt anpassad vård: Realtidsövervakning gör det möjligt för vårdgivare att skräddarsy behandlingsplaner efter varje patients individuella behov, vilket optimerar resultaten och förbättrar livskvaliteten.
Personligt anpassade behandlingar:
- Responsiva enheter: 3D-utskrivna enheter med integrerad elektronik och sensorer kan programmeras för att reagera på specifika förhållanden eller förändringar i patientens hälsa.
- Automatiska justeringar: En insulinpump kan t.ex. automatiskt justera mängden insulin som tillförs baserat på patientens blodsockernivåer.
- Förbättrade resultat: Individanpassade behandlingar kan leda till bättre kontroll av kroniska sjukdomar, minska risken för komplikationer och förbättra den allmänna hälsan och välbefinnandet.
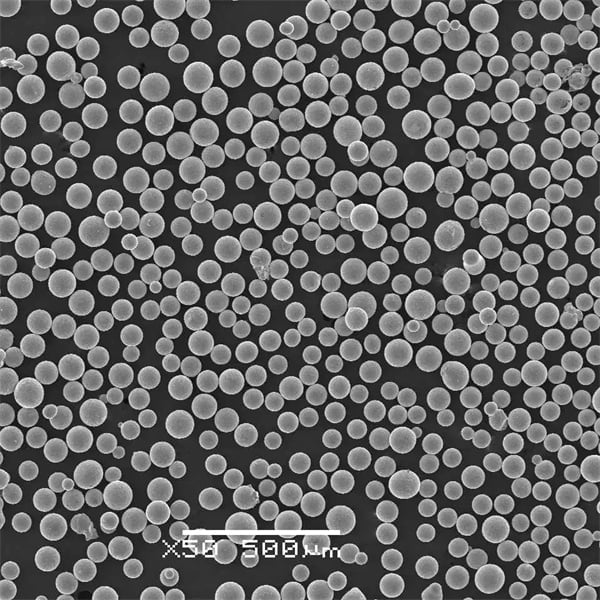
3. Förbättrad effektivitet och tillgänglighet:
Kortare ledtider för tillverkning
3D-utskrifter eliminerar behovet av komplexa verktyg, vilket leder till snabbare produktionstider och snabbare patienttillgång till anpassade enheter.
Utmaningar inom traditionell tillverkning:
Traditionell tillverkning av medicintekniska produkter innebär komplexa och tidskrävande processer som formkonstruktion, tillverkning och testning. Detta kan leda till långa ledtider, höga kostnader och begränsade möjligheter till kundanpassning.
Fördelar med 3D-utskrift:
3D-printing eliminerar behovet av komplexa verktyg, vilket effektiviserar tillverkningsprocessen och avsevärt minskar ledtiderna. Detta gör det möjligt för:
- Snabbare produktion: 3D-printing kan producera enheter på några timmar eller dagar, jämfört med veckor eller månader med traditionell tillverkning.
- Minskade kostnader: 3D-printing kan minska tillverkningskostnaderna genom att eliminera behovet av dyra formar och verktyg.
- Anpassning: 3D-printing gör det möjligt att skapa skräddarsydda enheter som är anpassade till varje patients specifika behov.
Fördelar för patienterna:
- Snabbare tillgång till vård: 3D-printing kan minska den tid det tar för patienter att få skräddarsydda enheter, vilket förbättrar deras livskvalitet och minskar belastningen på sjukvårdssystemen.
- Förbättrade resultat: Anpassade produkter kan ge bättre passform, funktion och komfort, vilket leder till förbättrade patientresultat.
- Stärkta patienter: 3D-printing gör det möjligt för patienterna att vara mer delaktiga i utformningen och utvecklingen av sina apparater, vilket ger dem större kontroll över sin vård.
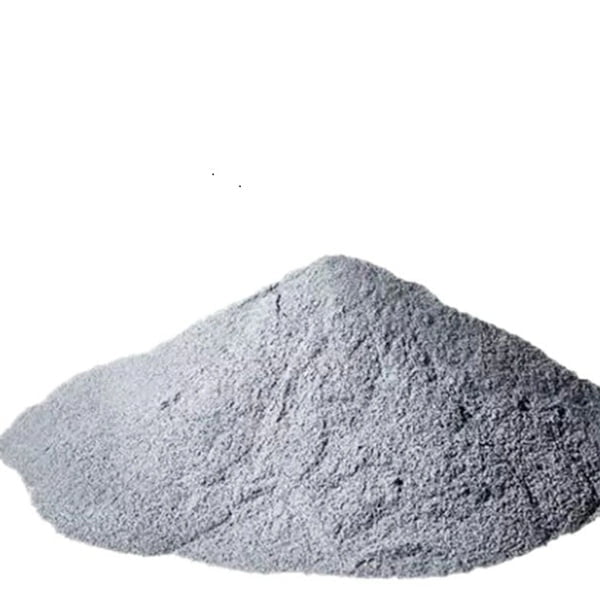
On-Demand-tillverkning
3D-skrivare kan installeras på sjukhus eller kliniker, vilket möjliggör lokal produktion av utrustning och minskar kostnaderna och de logistiska utmaningarna.
Löftet om tillverkning på beställning:
3D-printing har potential att revolutionera sättet på vilket medicintekniska produkter tillverkas och distribueras genom att möjliggöra produktion på begäran vid vårdplatsen. Det innebär att sjukhus och kliniker kan ha sina egna 3D-skrivare för att tillverka utrustning efter behov, vilket eliminerar behovet av centraliserade tillverknings- och distributionsanläggningar.
Fördelar med tillverkning på begäran:
- Minskade kostnader: On-demand-tillverkning kan minska kostnaderna genom att eliminera behovet av dyra lager och transporter.
- Snabbare leverans: Enheterna kan produceras på begäran, vilket eliminerar väntetiderna för patienterna.
- Ökad anpassningsförmåga: 3D-printing gör det möjligt att skapa skräddarsydda enheter som är anpassade till varje patients specifika behov.
- Förbättrad hållbarhet: On-demand-tillverkning kan minska avfallet genom att producera enheter endast när de behövs.
Utmaningar att övervinna:
- Initial investering: Den initiala investeringen i 3D-skrivare och utbildning kan vara hög.
- Efterlevnad av regelverk: 3D-utskrivna produkter måste uppfylla samma lagstadgade standarder som traditionellt tillverkade produkter.
- Kvalitetskontroll: Att säkerställa kvaliteten på 3D-utskrivna produkter är avgörande för patientsäkerheten.
Ökad innovation och experimenterande
Att 3D-printing är enkelt och prisvärt främjar snabb prototyptillverkning och innovation, vilket leder till utveckling av nya och förbättrade medicintekniska produkter.
Innovationsmotorn:
3D-utskrifter revolutionerar den medicintekniska industrin genom att göra det enklare och billigare att skapa prototyper och experimentera med nya idéer. Detta har lett till en explosion av innovation inom området, med nya och förbättrade enheter som utvecklas hela tiden.
Fördelarna med 3D-utskrifter för innovation:
- Snabb prototypframtagning: Med 3D-printing kan designers snabbt och enkelt skapa fysiska prototyper av sina konstruktioner, vilket gör att de kan testa och förfina sina idéer innan de investerar i dyra verktyg och tillverkning.
- Kostnadseffektiva experiment: 3D-printing är ett relativt billigt sätt att experimentera med nya material, konstruktioner och tillverkningstekniker. Det gör att företag kan utforska nya möjligheter utan att riskera stora finansiella investeringar.
- Ökat samarbete: 3D-utskrifter gör det enkelt att dela med sig av design och prototyper till andra, vilket underlättar samarbetet mellan designers, ingenjörer och läkare.
Exempel på 3D-utskriftsdriven innovation:
- Anpassade implantat: 3D-printing används för att skapa anpassade implantat som är skräddarsydda efter varje patients specifika behov. Detta kan leda till bättre passform, förbättrad funktion och ökad komfort för patienterna.
- Biotryckta vävnader: 3D-printing används för att skapa bio-printade vävnader som kan användas för transplantation eller forskning. Detta har potential att revolutionera vårt sätt att behandla skador och sjukdomar.
- Bärbara enheter: 3D-printing används för att skapa bärbara enheter som kan övervaka patienters hälsa och ge individanpassade behandlingar. Detta har potential att förbättra patientresultaten och minska kostnaderna för hälso- och sjukvården.
Dela på
MET3DP Technology Co, LTD är en ledande leverantör av lösningar för additiv tillverkning med huvudkontor i Qingdao, Kina. Vårt företag är specialiserat på 3D-utskriftsutrustning och högpresterande metallpulver för industriella tillämpningar.
Förfrågan för att få bästa pris och anpassad lösning för ditt företag!
Relaterade artiklar
Om Met3DP
Senaste uppdateringen
Vår produkt
KONTAKTA OSS
Har du några frågor? Skicka oss meddelande nu! Vi kommer att betjäna din begäran med ett helt team efter att ha fått ditt meddelande.
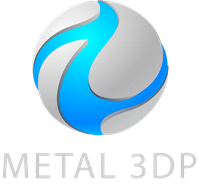
Metallpulver för 3D-printing och additiv tillverkning