3D Printed High-Load Robot Arm with Maraging Stee
Innehållsförteckning
Revolutionizing Robotics: The Power of 3D Printed High-Load Robot Arms in Maraging Steel
The landscape of industrial automation and robotics is undergoing a profound transformation, driven by the relentless pursuit of higher efficiency, greater precision, and enhanced capabilities. Central to this evolution is the robot arm – the workhorse of countless manufacturing lines, assembly cells, and complex operational environments. As demands intensify, particularly in sectors like aerospace, automotive, medical device manufacturing, and heavy industry, the need for robot arms capable of handling significant payloads with exceptional accuracy and reliability has become paramount. Traditional manufacturing methods, while established, often face limitations in producing the complex, lightweight, yet incredibly strong structures required for next-generation robotics. This is where the synergy between advanced materials like Maraging Steel (specifically grades like M300/1.2709) and the disruptive potential of 3D-utskrift av metall emerges as a game-changing solution.
High-strength robot arms are not merely about lifting heavier objects; they represent a leap forward in operational dynamics. Lighter, yet stronger arms allow for faster acceleration and deceleration, reduced inertia, improved positional accuracy, and lower energy consumption. They enable robots to perform more intricate tasks, operate in tighter spaces, and withstand more demanding duty cycles. Historically, achieving this combination of strength, stiffness, and low weight often involved complex assemblies of machined parts, leading to potential points of failure, longer assembly times, and design compromises. Additive Manufacturing (AM), commonly known as 3D-utskrifter, fundamentally alters this equation. By building parts layer by layer directly from digital models, metal AM allows for the creation of geometries previously impossible to manufacture. This includes intricate internal structures, topology-optimized designs that place material only where it’s structurally needed, and the consolidation of multiple components into a single, monolithic part.
Maraging steels, particularly the M300 (1.2709) grade, stand out as exceptional candidate materials for these demanding applications. These are ultra-high-strength steels characterized by their superior mechanical properties, including exceptional yield strength and tensile strength, combined with good toughness and ductility after a simple aging heat treatment. Unlike many other high-strength steels, they achieve their properties with very low carbon content, which contributes to their excellent machinability (in the annealed state) and weldability. When processed using metal AM techniques like Selective Laser Melting (SLM) or Direct Metal Laser Sintering (DMLS), maraging steel powders can produce near-net-shape parts with densities exceeding 99.9%, resulting in components that meet or even exceed the performance of traditionally manufactured counterparts.
The implications for B2B industries are significant. Procurement managers seeking reliable suppliers for high-performance robotic components can now look towards AM specialists capable of delivering customized, optimized robot arms with potentially shorter lead times for complex designs compared to traditional multi-part fabrication and assembly routes. Engineers are empowered with unprecedented design freedom, enabling them to create application-specific robot arms tailored for maximum performance and efficiency. Companies like Met3dp, headquartered in Qingdao, China, are at the forefront of this technological shift. Specializing in industrial 3D-utskrift av metall solutions, Met3dp provides not only advanced printing equipment known for its industry-leading print volume, accuracy, and reliability but also high-performance metal powders, including optimized maraging steel grades. Leveraging decades of collective expertise, Met3dp partners with businesses across aerospace, automotive, medical, and industrial sectors to accelerate their adoption of additive manufacturing, transforming how critical components like high-load robot arms are designed and produced. This fusion of advanced materials and manufacturing technology is not just an incremental improvement; it’s a fundamental revolutionizing force in robotics.
Unlocking Performance: Applications of 3D Printed High-Strength Robot Arms Across Industries
The unique combination of high strength, design freedom, and potential for weight optimization offered by 3D printed maraging steel robot arms unlocks a vast array of applications across numerous B2B sectors. These advanced components are not limited to niche uses; they are increasingly becoming critical enablers for enhanced productivity, precision, and capability in mainstream industrial operations. Procurement managers and engineers evaluating component suppliers should understand the breadth of these applications to appreciate the strategic value AM brings.
Key Application Areas:
- Automotive Manufacturing:
- High-Payload Assembly: Handling heavy components like engine blocks, transmissions, chassis parts, and battery packs for electric vehicles requires arms with exceptional strength and stiffness to maintain accuracy during movement. 3D printed maraging steel arms allow for optimized designs that handle these loads with minimal deflection.
- Automated Welding & Machining: Robot arms used for spot welding, laser welding, or robotic machining endure significant stress and vibration. The high fatigue strength and stiffness of AM maraging steel ensure longevity and precision in these demanding tasks. Lighter arms also enable faster positioning between operations.
- Press Tending & Material Handling: Moving large metal sheets or components in and out of stamping presses or CNC machines requires robust arms. Topology optimization via AM can create arms that are strong enough for the load but significantly lighter than traditional designs, improving cycle times.
- Flyg- och rymdindustrin:
- Component Handling & Assembly: Manipulating large, expensive, and often complex aerostructures (e.g., fuselage sections, wing components, engine parts) demands extreme reliability and precision. 3D printed arms offer high strength-to-weight ratios, crucial for the large-reach robots often used in aerospace assembly, reducing floor space requirements and potentially enabling gantry-less robotic systems.
- Drilling and Fastening: Robotic drilling and fastening systems exert considerable forces. Maraging steel arms provide the rigidity needed to maintain positional accuracy during these operations, ensuring compliance with strict aerospace tolerances. Design flexibility allows for integrated channels for cooling or sensor wiring.
- Automated Fiber Placement (AFP) & Automated Tape Laying (ATL): The end effectors and supporting arms for AFP/ATL systems must be incredibly stiff to apply composite materials accurately. AM allows for highly optimized, rigid structures tailored to these specific applications.
- Heavy Industry & Manufacturing:
- Foundry Operations: Robots operating in harsh foundry environments (heat, dust) need robust arms for tasks like casting extraction, mold handling, and fettling. Maraging steel offers good durability, and AM allows for designs that minimize dust ingress or incorporate cooling channels.
- Palletizing & Depalletizing: Handling heavy sacks, boxes, or other bulk items in logistics and warehousing benefits from strong, reliable robot arms capable of high speeds and continuous operation. Weight reduction through AM improves dynamic performance and reduces wear on the robot’s joints.
- Large-Scale Additive Manufacturing: Ironically, robot arms are increasingly used i large-scale AM processes (like Wire Arc Additive Manufacturing – WAAM or large format polymer extrusion). These often require large-reach, high-stiffness arms, where 3D printed maraging steel components can provide the necessary performance.
- Medical Device Manufacturing & Healthcare:
- Robotic Surgery Systems: While often smaller scale, surgical robot arms demand absolute precision and reliability. Certain components within the arm structure or setup systems might benefit from the high strength and stiffness of maraging steel, particularly where complex geometries or high dynamic stability are required. AM allows for intricate designs suitable for sterilization.
- Laboratory Automation: High-throughput screening and sample handling systems often utilize robotic arms. While payloads might be lower, the need for speed, precision, and reliability over millions of cycles makes optimized, durable components advantageous.
- Specialized & Emerging Applications:
- Construction Robotics: Robots used for tasks like bricklaying, welding structural steel, or 3D printing concrete require arms capable of handling significant loads and maintaining accuracy in less controlled environments.
- Remote Handling & Hazardous Environments: Operating in nuclear decommissioning, underwater exploration, or space requires highly reliable robotic systems. The strength and potential for complex, integrated designs make AM maraging steel arms suitable for these critical applications.
Why High Strength Matters in These Applications:
- Payload Capacity: Directly determines the weight the robot can manipulate effectively.
- Stiffness & Deflection: Crucial for maintaining positional accuracy under load, especially at the end of a long arm. Higher stiffness minimizes deflection and vibration.
- Dynamic Performance: Lighter, stiffer arms allow for faster acceleration/deceleration, leading to shorter cycle times.
- Fatigue Life: High-strength materials like maraging steel resist wear and fatigue over millions of operational cycles, increasing reliability and reducing downtime.
- Compactness: Higher strength allows for potentially smaller cross-sections for a given load, enabling operation in confined spaces.
By leveraging 3D printed maraging steel, manufacturers and system integrators can design and deploy robotic systems that push the boundaries of performance, addressing challenges that were previously difficult or impossible to overcome with traditional components. This capability is a key consideration for B2B buyers looking for wholesale robotic components or custom solutions that offer a competitive edge.
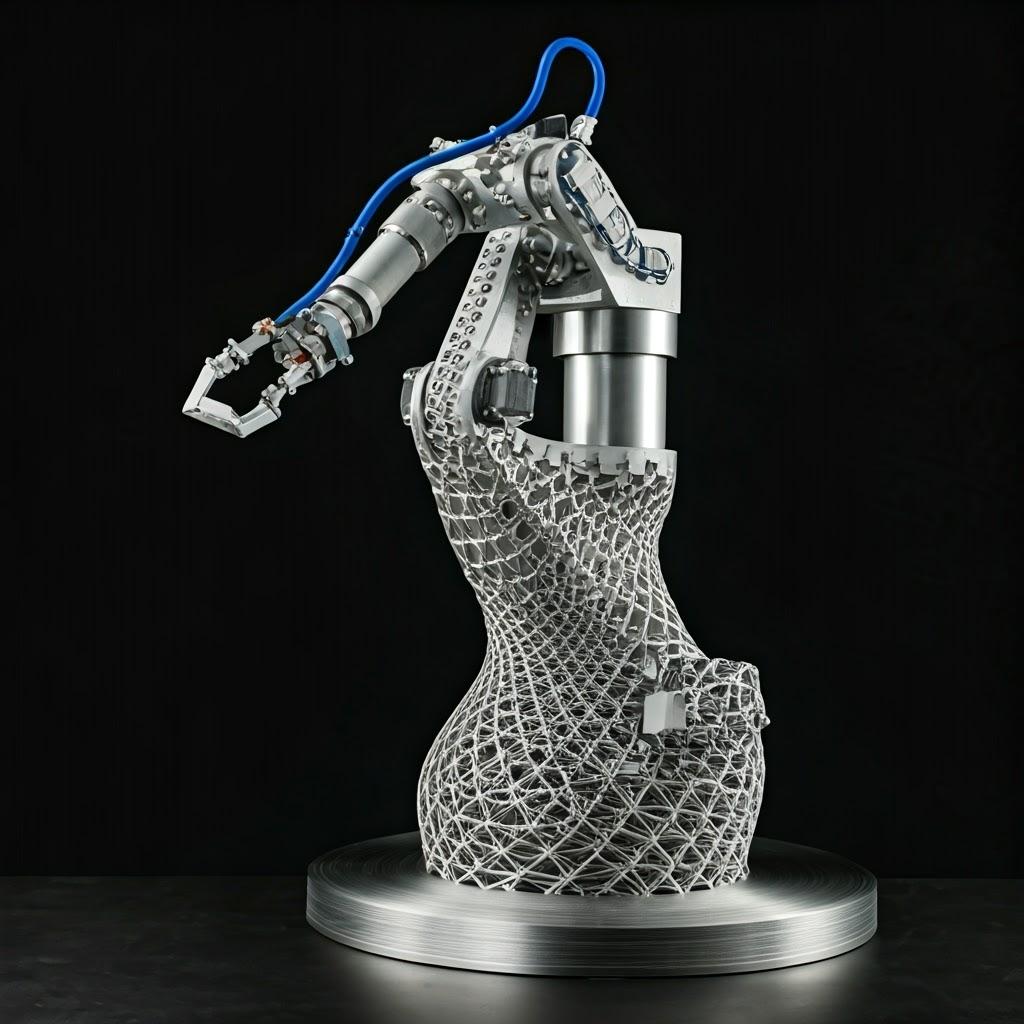
The Additive Advantage: Why Metal 3D Printing Outperforms for Complex Robot Arm Manufacturing
While traditional manufacturing methods like casting, forging, and CNC machining have served the robotics industry for decades, metal additive manufacturing presents a compelling suite of advantages, particularly for high-strength, high-performance robot arms made from materials like maraging steel. Understanding these benefits is crucial for engineers designing next-generation robotic systems and for procurement managers evaluating the most effective manufacturing routes and suppliers. Metal AM isn’t just a different way to make a part; it enables fundamentally better parts for complex applications.
Key Advantages of Metal AM for Robot Arms:
- Unprecedented Design Freedom & Complexity:
- Topology Optimization: This is arguably the most significant advantage. Software algorithms can optimize the material distribution within a design envelope, removing material where it’s not needed for structural integrity while maintaining strength and stiffness. This results in highly organic-looking, lightweight structures that are impossible to machine or cast efficiently. For a robot arm, this translates directly to lower inertia, faster movements, and reduced energy consumption.
- Gitterstrukturer: AM allows for the creation of internal lattice structures, further reducing weight while tailoring stiffness and vibration damping characteristics.
- Del Konsolidering: Multiple components of a traditional robot arm assembly (e.g., structural elements, mounting brackets, internal channels) can be consolidated into a single, monolithic 3D printed part. This reduces assembly time, eliminates potential points of failure (like fasteners or welds), simplifies inventory, and often improves overall structural integrity.
- Internal Channels & Conformal Cooling: Complex internal channels can be seamlessly integrated into the arm’s design. These can be used for routing hydraulic lines, electrical wiring, or fibre optics, protecting them from the external environment. Conformal cooling channels can also be designed close to heat sources (like motors or high-stress areas) for improved thermal management, enhancing performance and longevity.
- Enhanced Performance through Weight Reduction:
- As mentioned, topology optimization and lattice structures significantly reduce weight compared to solid machined or cast components designed for the same load.
- A lighter arm reduces the load on the robot’s own joints and actuators, potentially allowing for smaller, less expensive motors or enabling the robot to handle a larger external payload for the same overall system mass.
- Reduced inertia leads to faster acceleration and deceleration, shortening cycle times in repetitive tasks – a critical factor in high-volume manufacturing (e.g., automotive assembly lines).
- Material Efficiency & Reduced Waste:
- Traditional subtractive manufacturing (CNC machining) starts with a large block or billet of material and removes significant amounts, especially for complex geometries. This is particularly wasteful with expensive materials like maraging steel.
- Additive manufacturing, being an additive process, uses only the material necessary to build the part and its support structures. While powder management and recycling are essential, the overall material buy-to-fly ratio is often significantly better, reducing raw material costs and environmental impact.
- Rapid Prototyping & Iteration:
- Design changes can be implemented quickly by modifying the CAD file and printing a new iteration. This drastically speeds up the development cycle for new robot arm designs compared to the long lead times often associated with tooling for casting or complex multi-axis machining setups.
- Functional prototypes made from the final intended material (maraging steel) can be tested rigorously early in the design phase, reducing risks later in the project.
- Customization & On-Demand Manufacturing:
- AM is ideal for producing highly customized or application-specific robot arm designs without the need for expensive tooling changes. This allows manufacturers to offer tailored robotic solutions optimized for unique tasks or environments.
- Parts can be produced on-demand, potentially reducing the need for large inventories of spare parts, especially for older or highly specialized robot models.
- Potential for Improved Mechanical Properties:
- The rapid solidification rates inherent in processes like SLM can lead to fine microstructures in materials like maraging steel. When combined with appropriate post-process heat treatment (aging), 3D printed maraging steel can achieve mechanical properties (strength, hardness, toughness) that are comparable or even superior to wrought or cast counterparts.
Comparison Table: AM vs. Traditional Manufacturing for High-Strength Robot Arms
Funktion | Metal Additive Manufacturing (e.g., SLM) | Traditional (Casting/Machining) | Advantage of AM |
---|---|---|---|
Designens komplexitet | Very High (Organic shapes, lattices) | Moderate to High (Limited by tooling/access) | Enables topology optimization, part consolidation, internal features |
Viktminskning | Excellent potential | Limited (Often over-engineered) | Lower inertia, faster dynamics, higher payload-to-arm-weight ratio |
Konsolidering av delar | High (Multiple parts into one) | Low (Requires assembly) | Reduced assembly time, fewer failure points, improved integrity |
Material Avfall | Lower (Additive process) | Higher (Subtractive process) | Cost savings (especially with expensive alloys), more sustainable |
Verktygskostnad | None / Minimal | High (Molds, fixtures) | Economical for low-to-medium volumes and complex parts |
Lead Time (Complex) | Potentially Faster | Can be very long (Tooling, setup) | Faster design iteration, quicker delivery for intricate one-offs or small batches |
Anpassning | High (Digital file modification) | Low / Expensive | Ideal for application-specific designs and small batches |
Materialegenskaper | Excellent (Fine microstructure) | Good to Excellent (Established) | Can meet or exceed traditional methods with proper processing |
Export to Sheets
While traditional methods remain viable for simpler designs or very high-volume production runs where tooling costs can be amortized, metal 3D printing offers unparalleled advantages for creating the next generation of high-load, high-performance robot arms. Companies like Met3dp, with their expertise in both advanced powder production and industrial printing systems, are key partners in realizing this potential for B2B clients seeking superior robotic solutions. Their focus on avancerade utskriftsmetoder ensures that clients can fully leverage the benefits outlined above.
Material Excellence: Maraging Steel M300 (1.2709) – The Premier Choice for Demanding Robotic Applications
The performance of a high-load robot arm is fundamentally linked to the material from which it is constructed. While various alloys can be used in additive manufacturing, Maraging Steel, specifically the grade commonly designated as M300 (also known by Werkstoff number 1.2709 or classifications like MS1), stands out as a superior choice for applications demanding exceptional strength, high toughness, and dimensional stability. Understanding the properties and benefits of this remarkable alloy is crucial for engineers designing robotic systems and for procurement managers sourcing high-performance components.
What is Maraging Steel?
Maraging steels are a class of ultra-high-strength steels that differ significantly from conventional carbon steels. Their name derives from their strengthening mechanism: “martensite” (a very hard microstructure) combined with “aging” (a heat treatment process). Key characteristics include:
- Very Low Carbon Content: Typically less than 0.03% carbon. This distinguishes them from traditional high-strength steels and contributes to their good toughness and weldability.
- High Alloy Content: They contain high percentages of Nickel (typically 18%), Cobalt, and Molybdenum, along with additions of Titanium and Aluminum. These elements form intermetallic compounds during the aging process, which are responsible for the steel’s exceptional strength.
- Simple Heat Treatment: Unlike the complex quenching and tempering required for many carbon steels, maraging steels achieve their final properties through a relatively simple, low-temperature aging process (typically around 480-500°C) after being solution annealed. This process results in minimal distortion and predictable shrinkage, which is highly advantageous for complex 3D printed parts.
Why M300 (1.2709) is Ideal for 3D Printed Robot Arms:
- Exceptionellt förhållande mellan styrka och vikt:
- After aging, M300 achieves ultimate tensile strengths (UTS) typically exceeding 1900 MPa (often reaching over 2000 MPa) and yield strengths (YS) above 1800 MPa. This incredible strength allows designers to create significantly lighter robot arms for a given load capacity compared to using materials like aluminum, titanium, or conventional steels. As discussed earlier, reduced weight is critical for robot dynamics.
- Hög hårdhet och slitstyrka:
- The aged hardness of M300 typically reaches 50-55 HRC (Rockwell C scale). This high surface hardness provides excellent resistance to wear and abrasion, important for components that may experience contact or operate in demanding industrial environments.
- Good Toughness and Ductility:
- Despite its extreme strength and hardness, M300 retains good toughness (resistance to fracture) and reasonable ductility (ability to deform before breaking). This is crucial for robot arms that might experience unexpected impacts or shock loads, preventing catastrophic brittle failure. The low carbon content is a key factor in achieving this balance.
- Excellent Dimensional Stability During Aging:
- The aging heat treatment causes very predictable and uniform shrinkage with minimal distortion. This is a significant advantage for complex, near-net-shape parts produced by AM, ensuring that tight tolerances achieved during printing or subsequent machining are maintained after the final strengthening process.
- Good Machinability (in Annealed State):
- Before the aging treatment, M300 is relatively soft (around 30-35 HRC) and exhibits good machinability. This allows critical features, mounting surfaces, or bearing interfaces on the 3D printed arm to be easily finish-machined to very high precision before the final strengthening step.
- Proven Additive Manufacturing Processability:
- M300 powder is well-characterized and widely used in laser powder bed fusion (L-PBF) processes like SLM and DMLS. Optimized process parameters exist to achieve high-density (>99.9%) parts with excellent microstructural integrity and mechanical properties that rival or exceed those of wrought material.
Material Properties Summary: M300 (1.2709) Maraging Steel (Typical Aged Values)
Fastighet | Typical Value Range | Enhet | Significance for Robot Arms |
---|---|---|---|
Slutlig draghållfasthet | 1900 – 2100+ | MPa | Ability to withstand maximum pulling forces |
Utbyteshållfasthet (0,2%) | 1800 – 2050+ | MPa | Point at which permanent deformation begins; key design metric |
Hardness (Aged) | 50 – 55 | HRC | Resistance to wear, indentation, and abrasion |
Töjning vid brott | 5 – 11 | % | Ductility; ability to deform before fracture |
Elasticitetsmodul | ~180 – 190 | GPa | Stiffness; resistance to elastic deformation under load |
Täthet | ~8.0 – 8.1 | g/cm³ | Needed for weight calculations; relatively dense |
Aging Temperature | 480 – 500 | °C | Relatively low temperature simplifies heat treatment |
Dimensional Change (Aging) | Minimal & Predictable Shrinkage | – | Crucial for maintaining tolerances in complex parts |
Export to Sheets
The Importance of Powder Quality:
Achieving these outstanding properties in a 3D printed component relies heavily on the quality of the metal powder feedstock. This is where suppliers like Met3dp play a critical role. Met3dp utilizes industry-leading powder production technologies, such as Vacuum Induction Melting Gas Atomization (VIGA) och Process med roterande elektrod och plasma (PREP), to manufacture high-quality M300 (1.2709) powders. Key powder characteristics ensured by these advanced processes include:
- Hög sfäriskhet: Smooth, spherical powder particles flow easily and pack densely in the powder bed, leading to more uniform layers and higher final part density.
- Low Satellite Content: Minimizing smaller particles attached to larger spheres improves flowability and reduces the risk of porosity.
- Controlled Particle Size Distribution (PSD): Optimizing the range of powder particle sizes ensures good powder bed density and efficient melting.
- High Purity & Controlled Chemistry: Strict control over the alloy composition and minimizing impurities (like oxygen and nitrogen) are essential for achieving the desired mechanical properties and preventing defects.
By utilizing premium M300 powder, such as that available in Met3dp’s extensive product portfolio, manufacturers can confidently print high-strength robot arms with superior performance and reliability. The selection of M300, combined with the design freedoms of AM and high-quality powder, represents the pinnacle of current technology for demanding robotic applications.
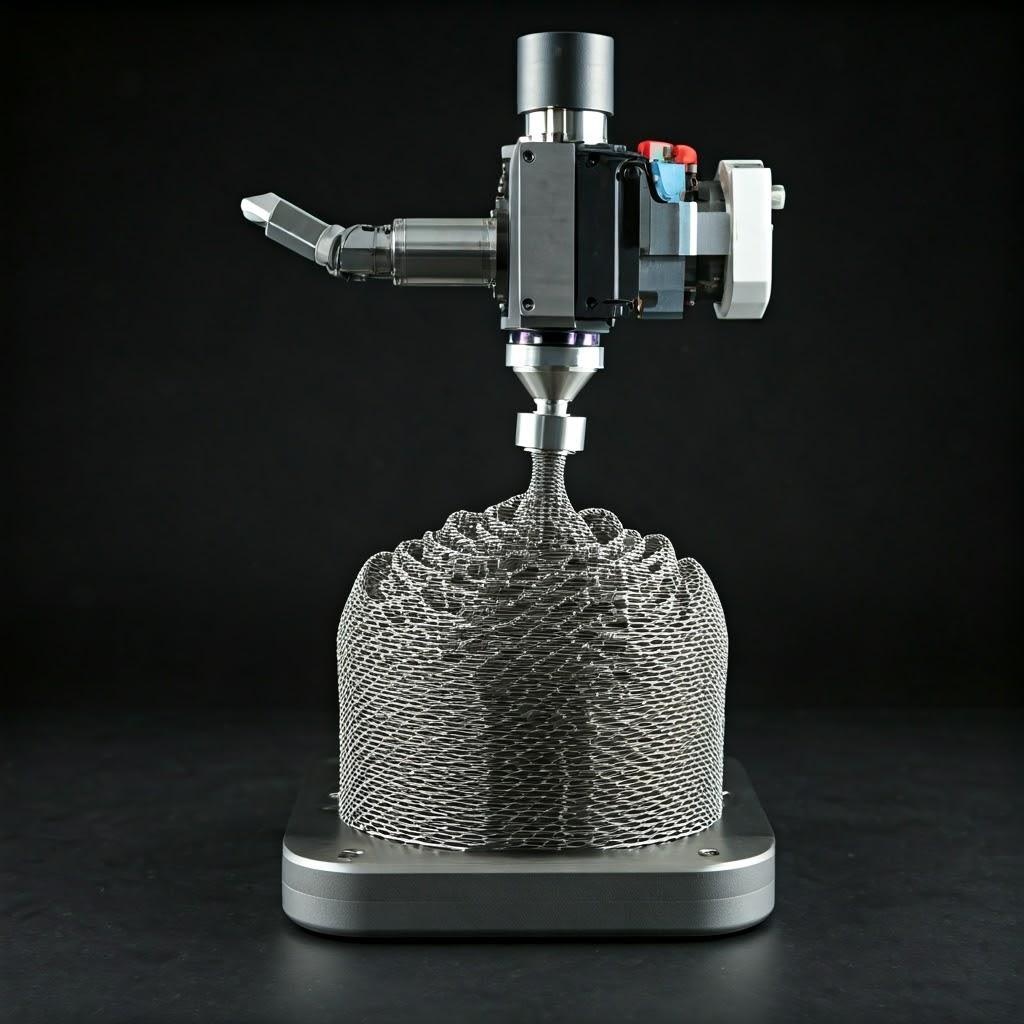
Design for Strength and Agility: Optimizing Robot Arm Geometry for Additive Manufacturing
The true potential of 3D printing high-load robot arms with Maraging Steel M300 is unlocked through intelligent design practices, specifically tailored for additive manufacturing (AM). Simply replicating a design intended for machining or casting often fails to leverage the unique capabilities of AM and may even introduce new challenges. Design for Additive Manufacturing (DfAM) is a critical methodology that engineers must embrace to create robot arms that are not only strong and precise but also lightweight, functionally integrated, and cost-effective to produce. For B2B clients and procurement managers, understanding these DfAM principles highlights the value proposition of partnering with an AM expert who can guide the design optimization process.
Core DfAM Principles for High-Strength Robot Arms:
- Topology Optimization: This is perhaps the most visually striking and impactful DfAM technique for robot arms.
- Concept: Utilizing specialized software (e.g., Altair Inspire, nTopology, Ansys Discovery, Generative Design in Fusion 360/Creo), engineers define the load cases (forces, moments, vibrations), design space (maximum allowable volume), constraints (mounting points, keep-out zones), and performance goals (minimize mass, maximize stiffness).
- Process: The software iteratively removes material from areas experiencing low stress, leaving behind an optimized, often organic-looking load path structure. This ensures that material is placed precisely where it’s needed to handle the applied loads.
- Benefit for Robot Arms: Drastic weight reduction (often 30-60% or more compared to traditional solid designs) while maintaining or even increasing stiffness. This leads to significantly lower inertia, enabling faster acceleration/deceleration, reduced energy consumption, and potentially higher payload capacity for the overall robotic system. The resulting designs are often impossible to manufacture using traditional subtractive methods.
- Lattice Structures and Infill Strategies:
- Concept: Instead of solid material, internal volumes can be filled with engineered lattice structures (e.g., strut-based like octet-truss, or surface-based like gyroids/TPMS – Triply Periodic Minimal Surfaces).
- Fördelar:
- Further Weight Reduction: Complements topology optimization by reducing mass in bulkier sections.
- Tailored Stiffness & Vibration Damping: Different lattice types offer varying mechanical responses. Engineers can select lattices to fine-tune the arm’s stiffness and damping characteristics, crucial for high-precision movements.
- Enhanced Thermal Management: Open-celled lattices can facilitate heat dissipation if internal components generate heat, or allow for conformal cooling channels to be integrated more easily.
- Increased Buckling Resistance: Certain lattice configurations can improve the stability of thin-walled structures.
- Överväganden: Requires careful analysis to ensure structural integrity, manufacturability (powder removal from complex lattices can be challenging), and appropriate stress distribution.
- Del Konsolidering:
- Concept: Redesigning assemblies to combine multiple individual components into a single, monolithic printed part.
- Example: A traditional robot arm segment might consist of a main structural beam, separate mounting flanges, brackets for sensors or cable management, and covers. An optimized AM design could integrate all these features into one complex component.
- Fördelar:
- Reduced Assembly Time & Cost: Eliminates fasteners, welding, or bonding operations.
- Improved Structural Integrity: No joints or interfaces that could represent weak points or potential failure modes.
- Simplified Supply Chain & Inventory: Fewer individual part numbers to manage.
- Förbättrad prestanda: Often results in a lighter and stiffer overall structure compared to the original assembly.
- Designing for Minimal Support Structures:
- Concept: Metal L-PBF processes require support structures for overhanging features (typically below 45 degrees from the horizontal) and to anchor the part to the build plate, managing thermal stresses. These supports consume material, add print time, and require post-processing effort for removal, potentially scarring surfaces.
- Strategies:
- Bygg orientering: Carefully selecting the orientation of the arm on the build platform can minimize the total area requiring support. This involves trade-offs with build time, surface finish on different faces, and potential anisotropy.
- Feature Design: Incorporating self-supporting angles (>= 45 degrees), designing smooth transitions (fillets) instead of sharp overhangs, and using diamond or teardrop shapes for horizontal holes can eliminate the need for internal supports.
- Sacrificial Features: Adding small features specifically designed to support a critical section, which are then easily machined away later.
- Benefit: Reduced print time, lower material consumption, less post-processing labor, and improved surface finish on down-facing surfaces.
- Internal Channels and Feature Integration:
- Concept: AM allows for the seamless creation of complex internal channels within the structure of the robot arm.
- Applikationer:
- Cable/Hose Routing: Protects wiring, fiber optics, or pneumatic/hydraulic lines from external damage, snagging, or environmental factors.
- Conformal Cooling: Channels designed to follow the contours of heat-generating components (like motors or high-stress zones) for efficient thermal management.
- Fluid Flow: For potential hydraulic actuation integrated within the arm structure.
- Benefit: Increased robustness, improved performance, and cleaner overall robot design.
- Feature Resolution and Wall Thickness:
- Concept: AM processes have limitations on the minimum feature size, hole diameter, and wall thickness they can reliably produce. These depend on the specific machine, laser spot size, layer thickness, and powder characteristics.
- Considerations for M300 Arms: Ensure walls are sufficiently thick to handle loads and avoid buckling (especially after topology optimization). Design features like mounting holes or sensor pockets well above the minimum resolution limits. Thin, unsupported walls are prone to warping during printing due to thermal stress. Typical minimum wall thickness recommendations often range from 0.5mm to 1.0mm, but structural requirements will likely dictate much thicker sections for high-load arms.
- Stress Concentration Avoidance:
- Concept: Sharp internal corners or abrupt changes in geometry can act as stress concentrators, potentially leading to fatigue failure under cyclic loading, even if the overall stress levels are acceptable.
- Strategy: Incorporate generous fillets and radii at all geometric transitions, especially in highly stressed areas identified through Finite Element Analysis (FEA). Topology optimization software often naturally produces smooth, flowing shapes that minimize stress concentrations.
Partnering for DfAM Success:
Successfully implementing these DfAM principles requires expertise not only in CAD and simulation but also a deep understanding of the specific AM process (L-PBF) and material behavior (Maraging Steel M300). This is where partnering with an experienced AM service provider like Met3dp becomes invaluable. Met3dp’s team possesses decades of collective expertise in metal additive manufacturing and offers comprehensive application development services. They can collaborate with client engineering teams to:
- Analyze existing designs for AM suitability.
- Perform topology optimization and lattice structure design.
- Advise on optimal build orientation and support strategies.
- Ensure designs are compatible with Met3dp’s industry-leading printer capabilities and high-quality M300 powders.
- Validate designs through simulation (FEA, thermal analysis).
By leveraging DfAM and expert guidance, B2B clients can ensure their 3D printed maraging steel robot arms deliver maximum performance, reliability, and cost-effectiveness. Visiting the Om oss sida can provide further insight into Met3dp’s commitment to expertise and partnership in additive manufacturing.
Precision Engineering: Achieving Tight Tolerances and Superior Surface Finish on 3D Printed Arms
While the design freedom of additive manufacturing is a major draw, applications like high-load robot arms demand stringent levels of precision. Engineers and procurement managers need realistic expectations about the dimensional accuracy and surface finish achievable with 3D printed Maraging Steel M300 components, both in the as-printed state and after post-processing. Achieving the required precision involves careful control over the entire manufacturing workflow, from powder quality and printing parameters to post-processing techniques.
Understanding As-Printed Tolerances:
Metal Laser Powder Bed Fusion (L-PBF), the typical process for M300, can achieve good dimensional accuracy, but it’s not inherently as precise as high-precision CNC machining across all dimensions of a large part.
- General Tolerances: For overall part dimensions, typical achievable tolerances often fall within the range of ISO 2768-m (medium) or sometimes ISO 2768-f (fine). This generally translates to +/- 0.1mm to +/- 0.5mm or more, depending on the dimension’s size and the part’s geometry and orientation.
- Factors Influencing As-Printed Accuracy:
- Thermal Stresses & Shrinkage: The repeated heating and cooling cycles inherent in L-PBF cause internal stresses and material shrinkage, which can lead to distortion or deviation from the intended geometry. This is particularly relevant for large, complex parts like robot arms.
- Bygg orientering: The orientation on the build plate significantly impacts accuracy. Features built vertically tend to be more accurate than those built horizontally or on an angle.
- Stödstrukturer: How the part is supported affects thermal dissipation and stability during the build, influencing final dimensions. Support removal can also slightly affect nearby surfaces.
- Pulverkvalitet: Consistent particle size distribution, sphericity, and flowability (like that ensured by Met3dp’s advanced atomization) contribute to uniform melt pools and predictable shrinkage.
- Machine Calibration & Condition: Laser focus, scanner accuracy, recoater performance, and overall machine calibration are crucial. Met3dp’s focus on industry-leading, reliable printers helps ensure consistency.
- Skiktets tjocklek: Thinner layers generally allow for finer detail but increase build time.
Understanding Surface Finish (Roughness):
The surface finish of as-printed L-PBF parts is inherently rougher than machined surfaces due to the layer-by-layer process and partially melted powder particles adhering to the surface.
- As-Printed Surface Roughness (Ra):
- Top Surfaces: Generally the smoothest, often Ra 5-15 µm.
- Vertical Walls: Typically Ra 8-20 µm.
- Upward-Facing Angled Surfaces: Roughness increases slightly as the angle decreases.
- Downward-Facing (Overhanging) Surfaces: These are the roughest, often Ra 20-40 µm or more, as they rest on support structures or are formed by the limits of self-support angles. Surface quality depends heavily on support strategy and removal.
- Impact on Robot Arms: While internal surfaces might tolerate higher roughness, critical mating surfaces, bearing interfaces, mounting points, or areas requiring smooth aerodynamic/hydrodynamic flow will almost certainly require post-processing to improve the finish.
Achieving Tighter Tolerances and Improved Finish through Post-Processing:
For high-precision applications like robot arms, post-processing is nearly always essential to meet final tolerance and surface finish requirements.
- CNC Machining: This is the most common method for achieving tight tolerances on specific features.
- Process: The 3D printed M300 part (usually in the stress-relieved or annealed state for better machinability) is mounted in a CNC mill or lathe. Critical features like mating flanges, bearing bores, shaft interfaces, and mounting holes are machined to final dimensions.
- Achievable Tolerances: CNC machining can easily achieve tolerances of +/- 0.01mm to +/- 0.05mm or even tighter where required, far exceeding as-printed capabilities.
- Ytfinish: Machining produces much smoother surfaces, typically Ra 0.8-3.2 µm, depending on the operation and tooling.
- Surface Finishing Techniques:
- Bead Blasting / Sand Blasting: Provides a uniform, non-directional matte finish, removing loose powder and improving aesthetics. Doesn’t significantly improve dimensional accuracy but can achieve Ra values around 3-6 µm.
- Tumbling / Vibratory Finishing: Uses abrasive media in a vibrating tub to smooth surfaces and round edges. Effective for improving overall surface finish (potentially Ra 1-5 µm) but less precise than machining and can affect dimensional accuracy if not carefully controlled.
- Polering: Manual or automated polishing can achieve very smooth, mirror-like finishes (Ra < 0.1 µm) where required for low friction, sealing surfaces, or aesthetics.
- Electropolishing: An electrochemical process that removes a small amount of material, smoothing surfaces and improving corrosion resistance.
Comparison Table: As-Printed vs. Post-Processed M300
Funktion | As-Printed (L-PBF M300) | Post-Processed (Machined/Finished) | Significance for Robot Arms |
---|---|---|---|
General Tolerance | +/- 0.1 to 0.5mm+ (ISO 2768-m/f) | +/- 0.01 to 0.05mm (Feature specific) | Machining required for precise fits, alignments, interfaces. |
Ytjämnhet (Ra) | 5 – 40 µm (Varies by surface) | < 0.1 µm (Polished) to 3.2 µm (Machined) | Finishing needed for low friction, wear resistance, sealing. |
Feature Definition | Good, limited by process | Very High (Machined features) | Sharp edges, precise bores, threads require machining. |
Kostnad | Lower (Print cost only) | Higher (Additional steps) | Post-processing adds significant cost and lead time. |
Ledtid | Shorter (Print time) | Longer (Includes post-processing) | Must factor post-processing into project schedule. |
Export to Sheets
Quality Control & Inspection:
Ensuring final parts meet specification requires robust quality control:
- Dimensionell inspektion: Using Coordinate Measuring Machines (CMMs), 3D laser scanners, or traditional metrology tools to verify critical dimensions against the CAD model and drawings.
- Ytgrovhetsmätning: Using profilometers to quantify surface finish on critical areas.
- Icke-förstörande testning (NDT): Techniques like X-ray or Computed Tomography (CT) scanning may be used to detect internal porosity or defects if required for highly critical applications.
Achieving precision in 3D printed maraging steel robot arms is a multi-stage process requiring careful DfAM, optimized printing, and appropriate post-processing. Partnering with a provider like Met3dp, who controls the quality from powder production through printing on reliable machines, ensures a strong foundation for achieving the final necessary tolerances and finishes through well-managed post-processing steps. Their comprehensive approach helps B2B clients procure components that meet the demanding precision requirements of modern robotics.
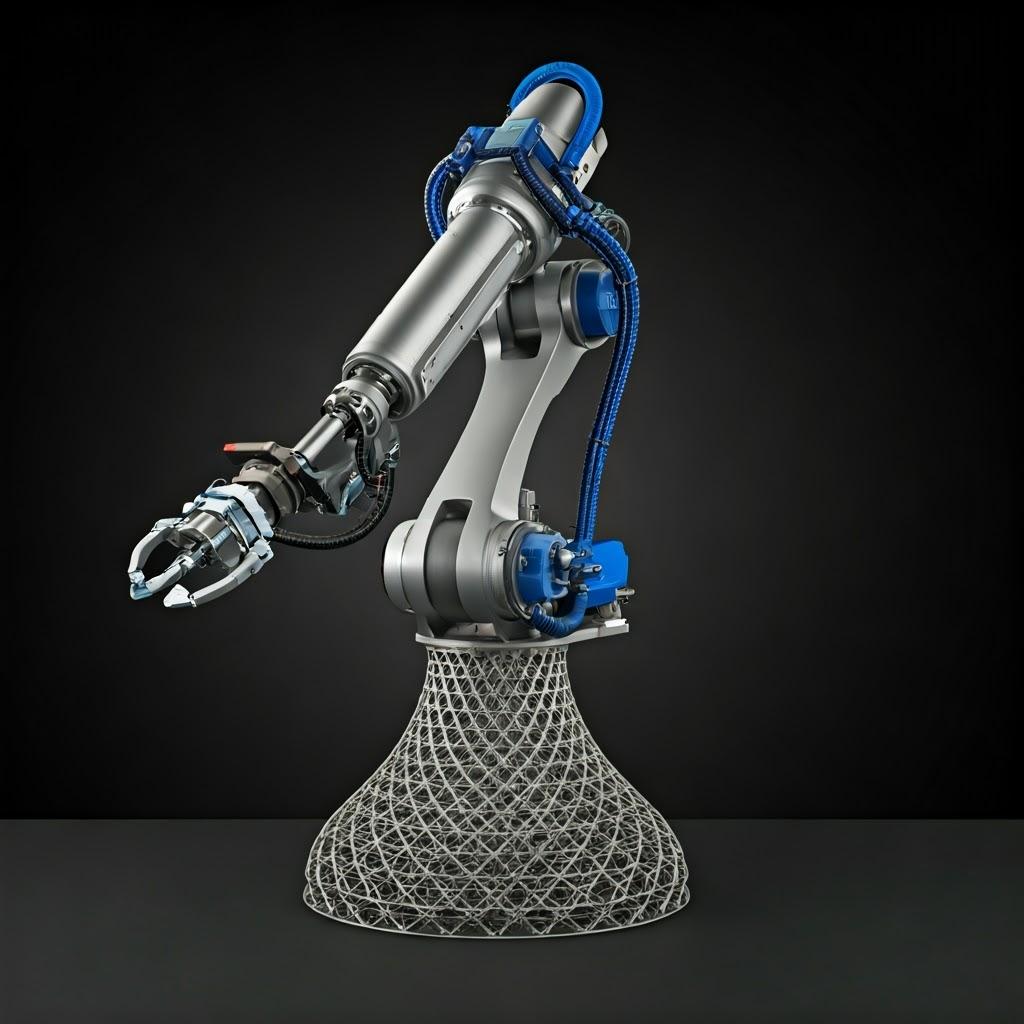
Beyond the Print: Essential Post-Processing Steps for Maraging Steel Robot Arms
Producing a high-quality Maraging Steel M300 robot arm component via additive manufacturing does not end when the printer stops. A series of critical post-processing steps are required to transform the as-printed part into a functional, reliable, high-performance component ready for assembly and deployment. Understanding this workflow is vital for engineers specifying requirements and for procurement managers evaluating supplier capabilities and project timelines. Each step plays a crucial role in achieving the desired material properties, dimensional accuracy, and surface characteristics.
Typical Post-Processing Workflow for AM M300 (1.2709):
- Stressavlastning:
- Syfte: The rapid heating and cooling cycles during the L-PBF process induce significant residual stresses within the printed part. These stresses can cause distortion during subsequent steps (like removal from the build plate or machining) and potentially compromise the part’s fatigue life. Stress relief heat treatment reduces these internal stresses without significantly altering the microstructure.
- Process: Typically performed while the part is still attached to the build plate, in an inert atmosphere furnace (Argon or Nitrogen). The part is heated to a specific temperature (often around 650-850°C, below the aging temperature range but high enough to allow stress relaxation), held for a period (e.g., 1-4 hours), and then slowly cooled. Exact parameters depend on part size and geometry.
- Importance: A crucial first step to ensure dimensional stability in subsequent operations.
- Part Removal from Build Plate:
- Syfte: Separating the printed component(s) from the metal build plate they were fused to during printing.
- Metoder: Commonly done using Wire Electrical Discharge Machining (Wire EDM) or a band saw. Wire EDM offers higher precision and a cleaner cut, often preferred for complex or delicate parts. Sawing is faster but less precise and may require more finishing on the base surface.
- Överväganden: Must be done carefully to avoid damaging the part. The removal method can influence subsequent machining steps if the base surface is critical.
- Borttagning av stödstruktur:
- Syfte: Removing the scaffold-like structures that were printed to support overhangs and anchor the part.
- Metoder: Can range from manual breaking (for easily accessible, lightly sintered supports) to extensive machining (milling, grinding) or specialized tools (e.g., dental drills for intricate areas). Support removal from complex internal channels can be particularly challenging and time-consuming.
- Påverkan: This step significantly impacts labor costs and lead time. Poor removal can leave witness marks or scarring on the part surface, potentially requiring further finishing. DfAM plays a huge role here – minimizing supports simplifies this step.
- (Optional) Solution Annealing:
- Syfte: To fully dissolve precipitates and create a uniform martensitic structure before aging. In L-PBF, the as-built state is often already close to a solutionized condition due to the rapid cooling. However, a separate solution annealing step might be specified for certain applications or if extensive machining is required before aging, as it ensures maximum softness (around 30-35 HRC) for machinability.
- Process: Heating to a higher temperature (e.g., 820-900°C), holding, and then rapidly cooling (air cool or faster).
- Machining (Subtractive Finishing):
- Syfte: To achieve tight dimensional tolerances, create specific features (threads, precise bores, O-ring grooves), and obtain smooth surface finishes on critical mating or functional surfaces.
- Process: Performed using CNC milling machines, lathes, or grinders. As noted, M300 is best machined in the annealed or as-printed/stress-relieved state (before aging). Designing the AM part with sufficient machining stock (e.g., 0.5-2mm) on critical surfaces is essential.
- Omfattning: Typically applied to mounting flanges, bearing seats, interface points, and any dimension requiring accuracy beyond as-printed capabilities.
- Aging Heat Treatment (Precipitation Hardening):
- Syfte: This is the critical step that develops the ultra-high strength and hardness of Maraging Steel M300. It causes the precipitation of fine intermetallic compounds within the martensitic matrix.
- Process: Performed in a precisely controlled vacuum or inert atmosphere furnace. Parts are heated to the aging temperature (typically 480-500°C for M300), held for a specific duration (commonly 3-6 hours), and then typically air-cooled.
- Critical Controls: Accurate temperature control (+/- 5°C or better), uniform heating/cooling, and controlled atmosphere are paramount to achieve consistent and optimal mechanical properties throughout the part. Dimensional changes (predictable shrinkage) occur during aging.
- Result: Hardness increases significantly (to 50-55 HRC), along with yield and tensile strength reaching their peak values.
- Ytbehandling:
- Syfte: To achieve the final desired surface texture, remove machining marks, improve fatigue life, or enhance aesthetics.
- Methods (Post-Aging):
- Bead Blasting: Often used for a uniform cosmetic finish.
- Tumbling/Vibratory Finishing: Can smooth surfaces but must be carefully controlled after aging due to the high hardness.
- Polering: For mirror finishes on specific areas.
- Slipning: Can be used for final dimensional adjustments on hardened parts, but it’s slower and more expensive than machining before aging.
- Överväganden: Aggressive methods post-aging can be difficult due to the material’s hardness.
- Final Cleaning and Inspection:
- Syfte: Removing any residual oils, debris, or media from previous steps. Performing final quality assurance checks.
- Metoder: Cleaning using appropriate solvents or aqueous methods. Final dimensional inspection (CMM, scanning), surface roughness checks, visual inspection, and any required NDT (Non-Destructive Testing).
Supplier Capability:
Successfully executing this multi-stage post-processing workflow requires significant infrastructure (furnaces, CNC machines, finishing equipment) and expertise. When selecting an AM supplier for high-strength robot arms, procurement managers must verify their capabilities not just in printing but also in managing or performing these critical post-processing steps to the required standards. A vertically integrated provider or one with strong partnerships for these services, like Met3dp, can offer a more streamlined and reliable path to obtaining finished, application-ready components. Their understanding of the entire process chain, from powder to finished part, ensures better control over the final quality and performance.
Navigating Complexity: Overcoming Common Challenges in 3D Printing High-Strength Robot Arms
Additive manufacturing of large, complex, high-strength components like robot arms using Maraging Steel M300 is a sophisticated process, and like any advanced technology, it comes with potential challenges. Awareness of these issues and the strategies to mitigate them is essential for both engineers designing the parts and B2B clients procuring them. Partnering with an experienced AM provider is key to navigating this complexity successfully.
Common Challenges and Mitigation Strategies:
- Thermal Stress, Warping, and Distortion:
- Utmaning: The intense, localized heat of the laser followed by rapid cooling creates significant temperature gradients within the part during the build. This generates internal stresses that can cause the part to warp, distort, or even crack, especially in large or geometrically complex structures like robot arms. Distortion can also occur upon removal from the build plate if stresses are not properly managed.
- Mitigation Strategies:
- Optimized Build Orientation: Selecting an orientation that minimizes large, flat surfaces parallel to the build plate and reduces thermal gradients.
- Effective Support Structures: Well-designed supports anchor the part securely, conduct heat away effectively, and resist deformation forces during the build. Simulation tools can help optimize support placement and density.
- Build Plate Heating: Heating the build plate (common in many L-PBF machines) reduces the temperature difference between the solidified material and the surrounding powder bed, lowering residual stress accumulation.
- Optimized Scan Strategies: Using specific laser scanning patterns (e.g., island scanning, rotating scan vectors between layers) helps distribute heat more evenly and reduce localized stress peaks.
- Stress Relief Heat Treatment: Performing this step (ideally before plate removal) is crucial for relaxing accumulated stresses and ensuring dimensional stability.
- Process Simulation: Advanced simulation software can predict thermal behavior and distortion, allowing for pre-compensation in the build file or adjustments to the support strategy before printing.
- Residual Stress Management:
- Utmaning: Even if catastrophic warping is avoided, high residual stresses remaining in the part can negatively impact its fatigue life, fracture toughness, and dimensional accuracy during machining or service life.
- Mitigation Strategies: Primarily addressed by the Stressavlastning heat treatment described previously. Careful process parameter optimization during printing also plays a role. For highly critical components, techniques like Laser Shock Peening (LSP) could potentially be used post-process to introduce beneficial compressive stresses, though this adds significant cost.
- Support Structure Design and Removal:
- Utmaning: Designing supports that are robust enough to prevent distortion and ensure good surface quality on overhangs, yet are easy and cost-effective to remove without damaging the part. Supports in complex internal channels or hard-to-reach areas present significant difficulties. Removal can be labor-intensive and leave witness marks.
- Mitigation Strategies:
- DfAM: Designing parts with self-supporting angles (>45°) wherever possible is the most effective strategy. Using features like teardrop-shaped holes avoids internal supports.
- Support Optimization Software: Tools that automatically generate supports optimized for minimal contact points, easy break-off, or specific structural requirements.
- Material Choice for Supports: Some systems allow using slightly different parameters or structures for supports to make them weaker and easier to remove.
- Access Planning: Designing parts such that support removal access is considered.
- Post-Processing Expertise: Skilled technicians using appropriate tools (manual, machining, EDM) are essential for effective and clean support removal.
- Porositet:
- Utmaning: Small voids or pores within the printed material can act as stress concentrators and reduce the part’s density, strength, ductility, and fatigue resistance. Porosity can arise from several sources:
- Lack-of-Fusion: Insufficient energy density fails to fully melt powder particles, leaving gaps between layers or scan tracks.
- Keyhole Porosity: Excessive energy density causes metal vaporization and instabilities in the melt pool, trapping gas.
- Gas Porosity: Gas trapped within the powder particles (especially lower-quality powder) or dissolved in the melt pool can form pores upon solidification.
- Mitigation Strategies:
- Optimized Process Parameters: Developing and strictly controlling laser power, scan speed, layer thickness, and hatch spacing tailored for M300 to ensure complete melting without vaporization.
- High-Quality Powder: Using powder with high sphericity, good flowability, controlled particle size distribution, and low internal gas content is critical. Met3dp’s focus on premium powder production using advanced atomization (VIGA, PREP) directly addresses this, minimizing the risk of powder-related porosity.
- Inert Atmosphere Control: Maintaining a high-purity inert gas environment (Argon) in the build chamber prevents oxidation and minimizes gas pickup by the melt pool.
- NDT Inspection: For critical parts, CT scanning can detect internal porosity to ensure components meet quality standards.
- Utmaning: Small voids or pores within the printed material can act as stress concentrators and reduce the part’s density, strength, ductility, and fatigue resistance. Porosity can arise from several sources:
- Anisotropi:
- Utmaning: Mechanical properties (especially ductility and fatigue strength) can sometimes vary depending on the direction relative to the build layers (Z-axis vs. XY plane). This is due to the layer-wise solidification and columnar grain growth typical in AM.
- Mitigation Strategies:
- Build Orientation Optimization: Orienting the part so that critical stresses are aligned with the direction of optimal properties (often the XY plane).
- Parameter Optimization: Fine-tuning parameters can influence microstructure and reduce anisotropy.
- Post-Processing Heat Treatments: Appropriate heat treatments (annealing, aging) help homogenize the microstructure and reduce anisotropic effects.
- Design Allowances: Accounting for potential directional property variations in the design calculations (using lower allowable values if necessary).
- Cost and Lead Time:
- Utmaning: Maraging steel powder is expensive. L-PBF machine time is costly. Complex post-processing adds significant time and expense. While AM can be faster for initial prototypes or highly complex single parts, the overall cost and lead time for production-ready components need careful evaluation against traditional methods.
- Mitigation Strategies:
- DfAM for Efficiency: Topology optimization reduces material use and print time. Designing for minimal supports reduces post-processing.
- Nesting & Build Optimization: Printing multiple parts simultaneously on the build plate can improve machine utilization.
- Supplier Efficiency: Partnering with an experienced and efficient AM provider like Met3dp, who has optimized workflows and potentially amortized machine costs over higher volumes, can help manage costs.
- Realistic Expectations: Understanding that high-performance components made with advanced materials and processes inherently involve significant investment. Focus on the total value proposition (performance gains, assembly reduction) rather than just piece price.
By anticipating these challenges and working with knowledgeable partners who employ robust mitigation strategies – from powder quality control and DfAM expertise to meticulous process control and post-processing management – B2B clients can confidently leverage the power of 3D printed Maraging Steel M300 for their most demanding high-strength robot arm applications.
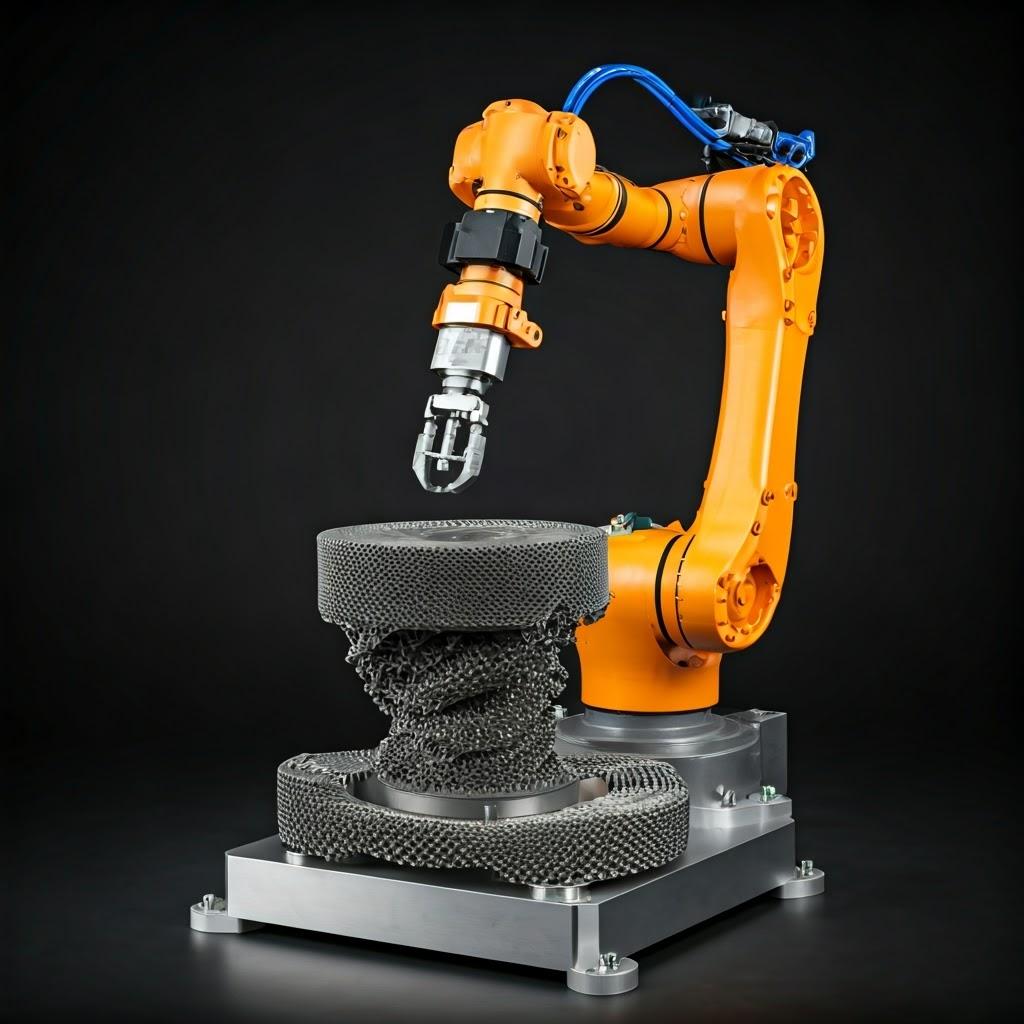
Partnering for Success: How to Select the Right Metal Additive Manufacturing Supplier for Robotic Components
Choosing the right additive manufacturing partner is as critical as the design and material selection when developing high-strength robot arms from Maraging Steel M300. The unique demands of this material and the complexity of the L-PBF process, coupled with essential post-processing, require a supplier with deep expertise, robust processes, and capable technology. For procurement managers and engineering leads navigating the AM landscape, evaluating potential suppliers requires a systematic approach focused on key capabilities. Making the right choice ensures reliable component quality, adherence to specifications, and ultimately, the success of the robotic application.
Key Criteria for Evaluating Metal AM Suppliers for M300 Robot Arms:
- Proven Maraging Steel (M300/1.2709) Expertise:
- Specific Experience: Does the supplier have a demonstrated track record of successfully printing M300 parts, particularly complex or large ones? Ask for case studies or examples relevant to robotics or similar high-stress applications.
- Parameter Development: Have they developed and validated their own robust printing parameters for M300 on their specific machines to achieve optimal density (>99.9%), microstructure, and mechanical properties? Or do they rely solely on generic machine manufacturer parameters?
- Material Property Validation: Can they provide data demonstrating the typical mechanical properties (strength, hardness, ductility) they achieve for M300 after printing and post-processing?
- Powder Handling & Management: What are their processes for qualifying incoming powder, storing it correctly (M300 powder can be sensitive to moisture), handling it safely, and managing recycling/refreshing to maintain quality? Suppliers like Met3dp, who manufacture their own high-quality spherical powders using advanced atomization, inherently have greater control and expertise in this area.
- Appropriate Equipment and Technology:
- Printer Capabilities: Do they operate industrial-grade L-PBF machines suitable for M300? Consider build volume (Met3dp offers industry-leading volume, essential for larger robot arm segments), laser power, inert atmosphere control quality, and in-process monitoring capabilities (e.g., melt pool monitoring, thermal imaging) which enhance quality assurance.
- Machine Maintenance & Calibration: Are their machines well-maintained and regularly calibrated to ensure consistent performance?
- Capacity & Redundancy: Do they have sufficient machine capacity to meet potential production demands and offer redundancy in case of machine downtime?
- Comprehensive Post-Processing Capabilities:
- In-House vs. Managed Services: Does the supplier perform critical post-processing steps like stress relief, aging heat treatment, and precision CNC machining in-house, or do they manage a network of qualified subcontractors? In-house capabilities often offer better control and potentially shorter lead times.
- Heat Treatment Expertise: Do they have furnaces with the required temperature uniformity (+/- 5°C) and atmosphere control (vacuum or high-purity inert gas) specifically validated for M300 aging cycles? Improper heat treatment is a common failure point.
- Machining Precision: Can their machining capabilities meet the tight tolerance requirements for robot arm interfaces? Do they have experience machining hardened M300 if required (though machining before aging is preferred)?
- Finishing & Inspection: Do they offer the required surface finishing options (blasting, polishing) and possess advanced metrology equipment (CMM, 3D scanners) for thorough quality inspection?
- Robust Quality Management System (QMS):
- Certifieringar: Do they hold relevant certifications? ISO 9001 is a baseline expectation for quality management. Depending on the end application, certifications like AS9100 (Aerospace) or ISO 13485 (Medical Devices) might be necessary and indicate a higher level of process control and traceability.
- Processtyrning: Can they demonstrate rigorous process control throughout the entire workflow, from powder batch tracking to final inspection reporting?
- Traceability: Is there full traceability of materials, processes, and parameters used for each part?
- Engineering and DfAM Support:
- Collaborative Approach: Are they willing and able to work collaboratively with your engineering team to optimize the robot arm design for additive manufacturing (DfAM)?
- Simulation Capabilities: Can they perform FEA or thermal simulations to predict performance and optimize the build strategy?
- Applikationsexpertis: Do they understand the specific functional requirements and challenges of robotic components? Met3dp emphasizes its role in providing comprehensive solutions, including application development services.
- Track Record and Industry Experience:
- Relevant Projects: Have they successfully completed projects in robotics, automation, aerospace, automotive, or other industries with similarly demanding requirements?
- Client References: Can they provide references from satisfied B2B clients?
- Stability & Reliability: Is the supplier financially stable and likely to be a reliable long-term partner?
- Communication, Project Management, and Logistics:
- Responsiveness: Are they responsive to inquiries and requests for quotation (RFQs)?
- Project Management: Do they have clear processes for managing projects, providing updates, and meeting agreed-upon timelines?
- Logistics: Consider their location (e.g., Met3dp in Qingdao, China) and their experience with shipping, customs, and logistics, especially for international clients.
Why Met3dp Stands Out:
Met3dp positions itself strongly against these criteria:
- Material Control: As a manufacturer of high-quality metal powders using advanced VIGA and PREP technologies, Met3dp has fundamental control over the starting material quality for M300.
- Advanced Equipment: They utilize printers offering industry-leading print volume, accuracy, and reliability.
- Omfattande lösningar: Met3dp provides end-to-end solutions spanning printers, powders, and crucial application development services, assisting clients with DfAM and process optimization.
- Expertis: Decades of collective expertise in metal AM underpin their ability to tackle complex projects.
- Fokus på branschen: They actively partner with organizations in demanding sectors like aerospace, medical, and automotive.
By carefully evaluating potential suppliers against these criteria, businesses can select a partner capable of delivering high-quality, reliable 3D printed Maraging Steel M300 robot arms that meet the rigorous demands of modern industrial automation. Exploring the supplier’s main website, such as Met3dp’s homepage, often provides a good starting point for understanding their capabilities and focus.
Understanding Investment: Key Cost Factors and Lead Time Considerations for 3D Printed Robot Arms
Additive manufacturing of high-performance components like Maraging Steel M300 robot arms represents a significant technological capability, but it also involves considerable investment. Procurement managers and project leaders need a clear understanding of the factors driving cost and lead time to make informed decisions, manage budgets effectively, and set realistic project timelines. While AM can offer unparalleled design benefits, appreciating the cost structure is crucial for evaluating its economic viability compared to traditional methods for a specific application.
Key Cost Drivers for 3D Printed M300 Robot Arms:
- Material Cost:
- Powder Price: Maraging Steel M300 powder is inherently expensive due to its high alloy content (Nickel, Cobalt, Molybdenum, Titanium) and complex manufacturing process (atomization). The cost per kilogram is significantly higher than common steels or even many titanium alloys.
- Material Consumption: This includes the material in the final part plus the material used for support structures and any potential losses during handling. Topology optimization and minimizing supports directly reduce material consumption.
- Powder Refresh/Recycling: Unused powder in the build chamber can often be recycled, but it typically requires sieving and potentially mixing with virgin powder (refreshing) to maintain quality, adding process complexity and cost.
- AM Machine Time:
- Byggtid: This is often the largest single contributor to print cost. It depends directly on:
- Part Volume: Larger parts take longer to print.
- Part Height: Taller parts require more layers.
- Support Volume: Printing support structures adds time.
- Skiktets tjocklek: Thinner layers improve detail but significantly increase build time.
- Scan-strategi: Complex scanning patterns can take longer.
- Machine Hourly Rate: This rate includes machine depreciation, energy consumption, inert gas usage, maintenance, facility overheads, and operator time. Industrial L-PBF machines represent a major capital investment for suppliers.
- Byggtid: This is often the largest single contributor to print cost. It depends directly on:
- Kostnader för arbetskraft:
- Pre-Processing: CAD preparation, DfAM consultation, simulation work, build file setup.
- Machine Operation: Setting up the build, monitoring the print process, initial part breakout.
- Post-Processing (Significant Driver):
- Stöd för borttagning: Can be highly labor-intensive, especially for complex geometries or hard-to-reach supports.
- Maskinbearbetning: Skilled machinist time on CNC equipment.
- Värmebehandling: Furnace loading/unloading and monitoring (though often automated, it requires skilled oversight).
- Manual Finishing: Polishing, deburring, surface treatments.
- Inspection: Technician time for CMM, scanning, NDT, and documentation.
- Post-Processing Consumables and Energy:
- Värmebehandling: Energy costs for furnaces, consumption of inert gas or vacuum pump operation.
- Maskinbearbetning: Cutting tool wear (M300 can be demanding), cutting fluids.
- Efterbehandling: Abrasive media (blasting, tumbling), polishing compounds.
- Inspection: CMM probe wear, NDT consumables.
- Quality Assurance and Documentation:
- The level of required documentation (material certifications, process logs, inspection reports) adds administrative overhead and labor cost. More stringent requirements (e.g., for aerospace) increase costs.
- Supplier Overheads and Profit:
- Includes general business costs, facility costs, R&D investment, and the supplier’s profit margin.
- Order Volume:
- Prototypes vs. Production: One-off prototypes typically have a higher per-part cost as setup and engineering effort are not amortized.
- Batch Production: For larger quantities (relevant for wholesale buyers or distributors), per-part costs can decrease due to better machine utilization (nesting multiple parts), amortized setup, and potentially negotiated volume discounts.
Key Lead Time Considerations:
Lead time is the total time from order placement to final part delivery. It’s often as critical as cost, especially in fast-paced development cycles.
- Design Finalization & Engineering: Initial DfAM, simulation, and design freeze. (Variable: days to weeks)
- Quotation & Order Processing: Supplier review, costing, and order confirmation. (Variable: days)
- Build Preparation & Scheduling: Generating the final build file, optimizing orientation/supports, and scheduling the job on an available machine. Print queues can significantly impact lead time. (Variable: days to weeks)
- Printing Time: The actual time the part spends printing in the machine. (Variable: hours to many days, depending on size/complexity)
- Cool Down & Part Removal: Allowing the build chamber and part to cool before safe removal. (Variable: hours to a day)
- Post-Processing (Often the Longest Phase):
- Stress Relief: ~1 day (including furnace cycle)
- Part Removal/Support Removal: Highly variable (hours to days)
- Machining: Depends on complexity and machine shop queue (days to weeks)
- Aging Heat Treatment: ~1 day (including furnace cycle)
- Finishing: Variable (hours to days)
- Inspection: Variable (hours to days)
- Frakt: Depends on supplier location and shipping method. (Variable: days to weeks)
Typical Estimated Lead Times (Rough Guide):
- Functional Prototype: 2 – 6 weeks
- Small Batch Production (e.g., 5-20 units): 6 – 12 weeks+
- Larger Production Runs: Requires careful planning and dedicated capacity; lead times negotiated based on volume and schedule.
Optimizing Cost & Lead Time:
- DfAM: Designing for reduced material usage and minimal supports has the biggest impact.
- Clear Specifications: Providing complete and clear drawings and requirements reduces ambiguity and delays.
- Supplier Collaboration: Working closely with an experienced supplier like Met3dp early in the process allows for optimization and realistic scheduling.
- Volume Planning: Discussing potential future volumes can sometimes lead to better pricing structures.
Understanding these cost and lead time factors allows B2B clients to budget appropriately, set realistic project schedules, and appreciate the value derived from the high performance and design freedom offered by 3D printed Maraging Steel M300 robot arms.
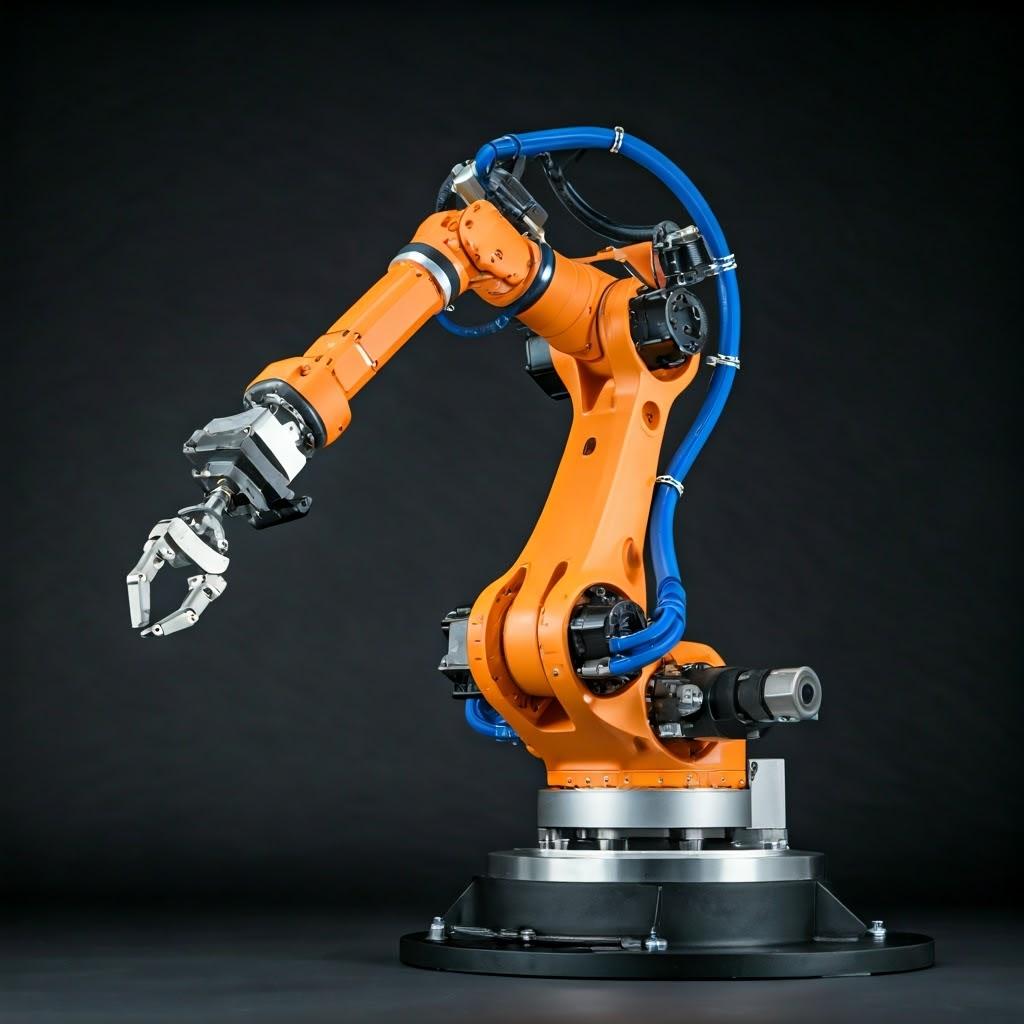
Frequently Asked Questions (FAQ) about 3D Printed Maraging Steel Robot Arms
Here are answers to some common questions engineers and procurement managers may have when considering 3D printed Maraging Steel M300 (1.2709) for high-strength robot arm applications:
Q1: What are the typical mechanical properties achieved for 3D printed M300 compared to wrought (traditionally manufactured) M300?
A: When processed correctly using optimized L-PBF parameters and appropriate post-processing (stress relief and aging), 3D printed M300 can achieve mechanical properties that are highly comparable, and in some cases potentially slightly superior in terms of yield and tensile strength, to wrought M300.
- Strength & Hardness: Yield strength (>1800 MPa), tensile strength (>1900 MPa), and hardness (50-55 HRC) are typically achieved and meet or exceed standard specifications for wrought M300.
- Ductility & Toughness: Elongation at break might be slightly lower or exhibit more anisotropy (variation with build direction) compared to wrought material, typically ranging from 5-11%. Careful design, parameter control, and heat treatment help optimize these properties. Fatigue properties are also comparable but can be sensitive to surface finish and internal defects, highlighting the importance of quality control. Partnering with a supplier like Met3dp, who controls powder quality and process parameters, is key to consistently achieving excellent, near-isotropic properties.
Q2: What is the maximum size robot arm segment that can be realistically 3D printed in Maraging Steel M300?
A: The maximum printable size is primarily limited by the build volume of the L-PBF machine used by the supplier. Modern industrial metal printers are continuously increasing in size.
- Typical Large Format Machines: Build envelopes can range up to 400mm x 400mm x 400mm, 500mm x 280mm x 365mm, or even larger specialized systems reaching 800mm or more in one dimension.
- Practical Considerations: Printing very large, monolithic parts pushes the boundaries of thermal stress management and can lead to extremely long print times and high costs. For very large robot arms, it might be more practical to print segments and join them using M300’s good weldability (followed by post-weld heat treatment) or mechanical fastening, leveraging AM for the most complex or highly loaded sections.
- Supplier Capability: It’s crucial to confirm the specific build volume capabilities of your chosen supplier. Met3dp emphasizes its industry-leading print volume, suggesting capabilities suitable for substantial robotic components.
Q3: How does the cost of a complex, topology-optimized 3D printed M300 robot arm compare to one CNC machined from a solid M300 billet?
A: The cost comparison is highly dependent on the specific geometry and, to some extent, the production volume.
- Simple Geometries: For relatively simple, blocky shapes that don’t require significant material removal, CNC machining from a standard billet might be less expensive than AM, especially at higher volumes where programming and setup costs are amortized.
- Complex & Optimized Geometries: For highly complex, topology-optimized, or lattice-filled designs that AM excels at, the comparison shifts significantly. Machining such a shape from a solid billet would involve immense material waste (very poor buy-to-fly ratio for M300), extremely long machining times, and might be practically impossible. In these cases, AM becomes the enabling technology and is often more cost-effective despite the high process costs, especially when considering the performance benefits (weight reduction, part consolidation).
- Overall: AM is generally favored when design complexity is high, weight reduction is critical, part consolidation offers assembly savings, or rapid iteration/customization is needed. Traditional machining is favored for simpler shapes in higher volumes where AM’s specific advantages aren’t fully leveraged.
Q4: Can internal channels for cooling, hydraulics, or sensor wiring be reliably printed and made functional in M300 arms?
A: Yes, this is one of the significant advantages of metal AM. Internal channels can be designed directly into the CAD model and printed integrally. However, there are considerations:
- Design Rules: Channels need minimum diameters (typically >0.5-1.0mm) to be reliably printed and for powder removal. Smooth bends are preferred over sharp corners. Self-supporting channel shapes (e.g., diamond or teardrop cross-sections for horizontal runs) can minimize the need for internal supports, which are extremely difficult to remove.
- Powder Removal: Ensuring all unmelted powder is removed from complex internal networks after printing is critical. This usually involves designing access ports and using compressed air, vibration, or flushing techniques.
- Ytfinish: The internal surface finish will be as-printed (relatively rough) unless secondary processes like abrasive flow machining or chemical polishing are employed, which adds complexity and cost.
- Inspection: Verifying channel clearance and integrity might require methods like flow testing, endoscopy, or CT scanning.
- Functionality: With proper design and post-processing, these channels are highly reliable for routing wires, carrying cooling fluids, or low-to-medium pressure hydraulic lines.
Q5: What quality control measures and certifications should I expect from a supplier providing critical M300 robot arms?
A: For critical components like high-load robot arms, robust quality control is non-negotiable. You should expect:
- Material Certification: Traceability and certification for the M300 powder batch used.
- Processtyrning: Documented procedures and control over printing parameters, machine calibration, and post-processing steps (especially heat treatment).
- Dimensionell inspektion: CMM reports or 3D scan data verifying critical dimensions against drawings.
- Mechanical Property Testing: Often performed on representative samples printed alongside the main parts to verify strength, hardness, and potentially ductility meet specifications.
- NDT (Optional but Recommended): Non-Destructive Testing like CT scanning for internal defect detection, especially for fatigue-critical applications.
- QMS Certification: ISO 9001 certification is a minimum expectation. AS9100 or ISO 13485 may be required depending on the industry. Suppliers like Met3dp, focused on industrial applications, typically operate under stringent quality management systems.
Conclusion: Embracing Additive Manufacturing for the Next Generation of High-Performance Robotics
The integration of metal additive manufacturing, specifically using high-performance materials like Maraging Steel M300 (1.2709), represents a pivotal advancement in the field of robotics. As industries ranging from automotive and aerospace to heavy manufacturing and medical technology continue to push the boundaries of automation, the demand for robot arms that are stronger, lighter, faster, and more precise is intensifying. 3D printed M300 components are not just meeting these demands; they are enabling entirely new levels of performance and design possibilities.
Throughout this exploration, we’ve seen how AM overcomes the limitations of traditional manufacturing for complex robotic structures. The ability to leverage topologioptimering och lattice structures facilitates dramatic weight reductions without compromising strength, leading to superior dynamic performance and efficiency. Konsolidering av delar simplifies designs, reduces assembly costs, and enhances reliability by eliminating potential failure points. The capacity to integrate complex internal channels offers functional advantages for cooling, wiring, or hydraulics, creating cleaner and more robust robotic systems.
Maraging Steel M300 itself proves to be an exceptional material choice, offering an unparalleled combination of ultra-high strength, good seghet, high Hårdhet, and remarkable dimensionsstabilitet through its straightforward aging heat treatment. When processed using optimized L-PBF techniques and high-quality powders, the resulting components exhibit properties suitable for the most demanding load-bearing robotic applications.
However, unlocking this potential requires navigating the complexities of DfAM, meticulous process control during printing, and essential, carefully managed post-processing steps including stress relief, machining, and critical aging heat treatment. Overcoming challenges related to thermal stress, support structures, and ensuring precision necessitates a deep understanding of the technology and a commitment to quality at every stage.
This underscores the importance of selecting the right manufacturing partner. Companies like Met3dp stand at the forefront of this technological wave, offering not just access to industry-leading printing equipment and advanced powder manufacturing capabilities, but also the crucial expertise in materials science, application development, and process optimization. Their comprehensive approach, from producing high-sphericity M300 powders to providing DfAM support and ensuring reliable printing, empowers businesses to confidently adopt AM for their critical robotic components.
For engineers seeking to design lighter, faster, stronger robots, and for procurement managers looking for reliable suppliers of next-generation components, the message is clear: Metal additive manufacturing with Maraging Steel M300 is a transformative technology. By embracing this approach and partnering with knowledgeable experts, businesses can gain a significant competitive advantage, driving innovation and efficiency in the rapidly evolving world of robotics.
Ready to revolutionize your robotic applications with the strength and design freedom of 3D printed Maraging Steel? Contact Met3dp today to discuss your high-strength robotic application requirements and explore how our additive manufacturing solutions can elevate your performance.
Dela på
MET3DP Technology Co, LTD är en ledande leverantör av lösningar för additiv tillverkning med huvudkontor i Qingdao, Kina. Vårt företag är specialiserat på 3D-utskriftsutrustning och högpresterande metallpulver för industriella tillämpningar.
Förfrågan för att få bästa pris och anpassad lösning för ditt företag!
Relaterade artiklar
Om Met3DP
Senaste uppdateringen
Vår produkt
KONTAKTA OSS
Har du några frågor? Skicka oss meddelande nu! Vi kommer att betjäna din begäran med ett helt team efter att ha fått ditt meddelande.
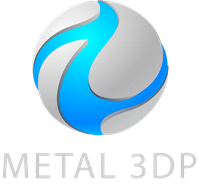
Metallpulver för 3D-printing och additiv tillverkning