Omvandlingen av SLM inom flyg- och rymdindustrin
Innehållsförteckning
The aerospace industry has always been a pioneer in pushing the boundaries of design and technology. Imagine a world where aircraft are lighter, stronger, and more fuel-efficient. This dream is becoming a reality thanks to Selective Laser Melting (SLM), a revolutionary 3D printing technique making waves in the field. SLM is transforming how aerospace components are manufactured, opening doors to innovative designs and performance optimization. But how exactly is SLM taking flight in the world of airplanes, rockets, and beyond? Let’s delve deeper and explore the specific applications of SLM in the aerospace industry.
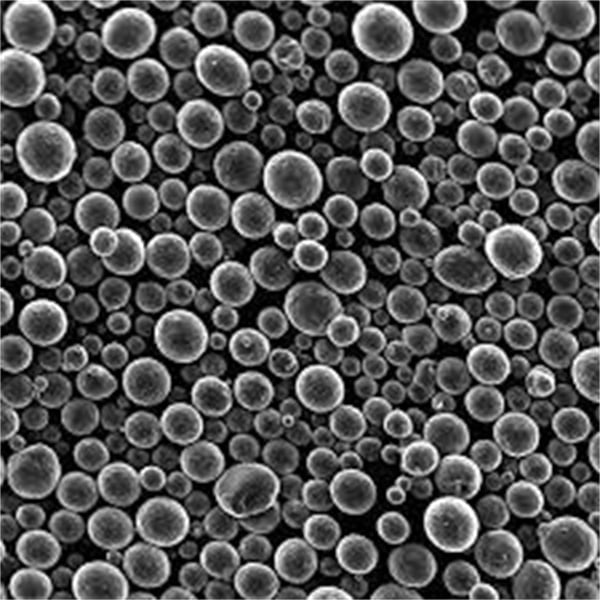
Metal Powders for Aerospace SLM
At the heart of SLM lies the magic of metal powders. These fine, metallic particles are meticulously layered and fused together by a high-powered laser, creating complex 3D structures on-demand. The specific metal powder used plays a crucial role in determining the final component’s properties and performance. Here’s a closer look at some of the key metal powders utilized in SLM for aerospace applications:
Metal Powders for Aerospace SLM
Metallpulver | Sammansättning | Fastigheter | Egenskaper | Tillämpningar inom flyg- och rymdindustrin |
---|---|---|---|---|
Titanium Alloys (Ti-6Al-4V, Ti-6Al-4V ELI) | Titan (Ti), aluminium (Al), vanadin (V) | Högt förhållande mellan styrka och vikt, utmärkt korrosionsbeständighet, biokompatibel | Powder particles are spherical for optimal flow and laser melting | Turbine blades, landing gear components, airframe structural components, |
Nickel-based Superalloys (Inconel 625, Inconel 718) | Nickel (Ni), Chromium (Cr), Cobalt (Co), Molybdenum (Mo), and other elements | Hållfasthet vid höga temperaturer, oxidationsbeständighet | More challenging to process compared to Titanium alloys | Turbine disks, combustor liners, afterburner components |
Aluminum Alloys (AlSi10Mg, Scalmalloy) | Aluminium (Al), kisel (Si), magnesium (Mg) | Lightweight, good strength, weldability | Offers high thermal conductivity compared to other alloys | Heat exchangers, wing components, fuselage components |
Kobolt Krom (CoCr) | Cobalt (Co), Chromium (Cr) | Hög slitstyrka, biokompatibel | Often used in medical applications, gaining traction in aerospace for specific wear parts | Bearings, gears, landing gear components |
Rostfritt stål (316L, 17-4 PH) | Järn (Fe), krom (Cr), nickel (Ni), molybden (Mo) | Korrosionsbeständighet, god hållfasthet | Relatively affordable compared to other metal powders | Fluid system components, structural components requiring good corrosion resistance |
Copper Alloys (CuNi) | Copper (Cu), Nickel (Ni) | Hög värmeledningsförmåga, bra elektrisk ledningsförmåga | Used for applications requiring efficient heat transfer | Heat sinks, busbars for electrical systems |
Tantal (Ta) | Tantal (Ta) | Hög smältpunkt, utmärkt korrosionsbeständighet | Relatively expensive metal powder | Crucible liners for high-temperature applications, heat shields |
Molybden (Mo) | Molybden (Mo) | Hög smältpunkt, god värmeledningsförmåga | Used in combination with other metals in superalloys | High-temperature components in rocket engines |
Volfram (W) | Volfram (W) | Mycket hög smältpunkt, utmärkt slitstyrka | Difficult to process due to high melting point | Nozzles for rocket engines, heat shields for re-entry vehicles |
Inconel additively manufactured (AM) | Nickel (Ni), Chromium (Cr), Cobalt (Co), Molybdenum (Mo), and other elements | Tailored properties through AM process | Allows for creation of unique microstructures with specific properties | High-performance turbine blades with optimized cooling channels |
As you can see, the selection of metal powders for SLM in aerospace is vast and carefully chosen based on the specific application’s requirements. From the robust strength of titanium alloys for turbine blades to the lightweight efficiency of aluminum for airframe components, SLM allows for the creation of parts with exceptional properties previously unattainable through traditional manufacturing methods.
Tillämpningar av SLM inom flyg- och rymdindustrin
The impact of SLM in aerospace extends far beyond just the materials used. This technology is revolutionizing the way aircraft components are designed and manufactured, leading to a new era of innovation. Here are some of the key applications of SLM in the aerospace field:
SLM Applications in Aerospace
Tillämpning | Fördelar | Exempel |
---|---|---|
Turbinblad | Complex internal cooling channels for improved efficiency, reduced weight, ability to create intricate blade geometries for better performance | High-pressure turbine blades, low-pressure turbine blades, blisks (integrated turbine blade and disk) |
Landningsställskomponenter | Lighter weight for improved fuel efficiency, design freedom for complex lattice structures for better shock absorption | Landing gear brackets, struts, structural components |
Airframe Structural Components | Topology optimization for weight reduction, ability to manufacture complex shapes difficult with traditional methods | Ribs, stringers, longerons (structural elements) |
Combustion Liners | Conformal cooling channels for improved thermal management, ability to create intricate surface features for better fuel-air mixing | Combustor liners for improved efficiency and reduced emissions |
Värmeväxlare | Lightweight designs with high surface area for efficient heat transfer | Air-to-air heat exchangers, oil coolers |
Satellitkomponenter | Reduced weight for increased payload capacity, ability to manufacture intricate structures for specific functionalities | Brackets, antennas, structural components |
Rocket Engine Components | High-temperature resistant materials for extreme environments, ability to create complex cooling channels for heat management | Nozzles, combustion chambers, thrust chambers |
The benefits of utilizing SLM in these applications are numerous. For instance, the ability to create intricate internal cooling channels within turbine blades allows for more efficient heat management, leading to increased engine performance and fuel efficiency. Similarly, SLM enables the design and manufacture of lightweight components for airframes and landing gear, directly contributing to reduced fuel consumption and extended aircraft range. Furthermore, SLM empowers engineers to create complex geometries that were previously impossible with traditional manufacturing techniques, unlocking new possibilities for design optimization and performance enhancement.
Challenges and Considerations for SLM inom flyg- och rymdindustrin
While SLM offers tremendous potential for the aerospace industry, there are still challenges to overcome. Here are some key considerations for utilizing SLM in aerospace applications:
- Machine and Powder Costs: SLM machines are currently high-priced, and metal powders specifically designed for aerospace applications can be expensive.
- Process Control and Qualification: SLM is a complex process requiring strict control over parameters to ensure consistent and reliable part quality. Qualification of the SLM process for aerospace components demands rigorous testing and certification procedures.
- Ytjämnhet: SLM parts can exhibit a rougher surface finish compared to traditionally manufactured components. Post-processing techniques like machining or polishing might be necessary depending on the application.
- Begränsningar av delstorleken: Current SLM machines have limitations on the size of parts they can produce. Manufacturing larger aerospace components might require segmentation and assembly of multiple SLM-printed parts.
Despite these challenges, the potential benefits of SLM are undeniable. As the technology matures and production costs decrease, SLM is poised to become a mainstream manufacturing method for the aerospace industry. Research and development efforts are continuously improving machine capabilities, powder quality, and process control, paving the way for wider adoption of SLM in the years to come.
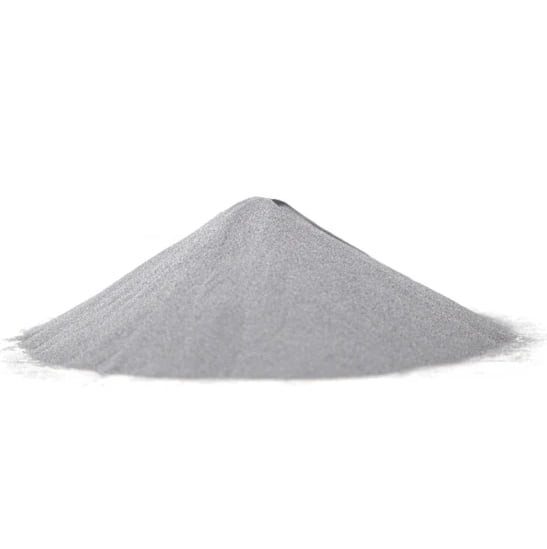
VANLIGA FRÅGOR
Q: What are the advantages of using SLM for aerospace components?
A: SLM offers several advantages, including:
- Lätta delar: SLM enables the creation of lighter components compared to traditional manufacturing methods, leading to improved fuel efficiency and increased aircraft range.
- Designfrihet: SLM allows for the design and manufacture of complex geometries previously impossible with traditional techniques, unlocking new possibilities for performance optimization.
- Materialegenskaper: SLM parts can be made from high-performance materials with exceptional properties like high strength-to-weight ratio and high-temperature resistance.
- Minskat avfall: SLM is a more efficient process compared to traditional methods, generating less material waste.
Q: What are the limitations of using SLM for aerospace components?
A: Some limitations of SLM in aerospace include:
- Machine and powder costs: SLM machines and metal powders can be expensive, impacting production costs.
- Process control and qualification: SLM requires strict control over parameters and rigorous qualification procedures for aerospace applications.
- Ytjämnhet: SLM parts might require post-processing for smoother surface finishes depending on the application.
- Part size limitations: Current SLM machines have limitations on the size of parts they can produce.
Q: What are some future advancements expected in SLM for aerospace applications?
A: The future of SLM in aerospace is bright, with several advancements expected:
- Reduced machine and powder costs: As the technology matures, production costs for both SLM machines and metal powders are expected to decrease, making SLM more accessible for wider adoption.
- Större byggvolymer: Development of larger SLM machines with increased build volumes will enable the production of bigger aerospace components, eliminating the need for segmentation and assembly.
- Multi-material SLM: Advancements in SLM technology might allow for the printing of parts using multiple materials within a single build, creating components with graded properties for optimal performance.
- In-situ process monitoring and control: Real-time monitoring and control of the SLM process will ensure consistent part quality and reduce the risk of defects.
- Automation and integration: Increased automation and integration of SLM with other manufacturing processes will streamline production workflows and improve efficiency.
Q: Is SLM the future of aerospace manufacturing?
A: While SLM is not likely to replace all traditional manufacturing methods in aerospace, it is undoubtedly revolutionizing the industry. SLM’s ability to create lightweight, high-performance components with intricate designs makes it ideal for a wide range of aerospace applications. As the technology continues to develop and overcome its limitations, SLM is poised to become a dominant force in shaping the future of aerospace manufacturing.
Slutsats
Selective Laser Melting (SLM) is transforming the way aircraft are designed and manufactured. This innovative 3D printing technology offers a unique combination of design freedom, material properties, and weight reduction capabilities, pushing the boundaries of what’s possible in the aerospace industry. From lighter, more fuel-efficient airplanes to rockets capable of reaching new heights, SLM is playing a crucial role in shaping the future of flight. As the technology matures and overcomes its challenges, the sky’s the limit for the transformative power of SLM in aerospace.
Dela på
MET3DP Technology Co, LTD är en ledande leverantör av lösningar för additiv tillverkning med huvudkontor i Qingdao, Kina. Vårt företag är specialiserat på 3D-utskriftsutrustning och högpresterande metallpulver för industriella tillämpningar.
Förfrågan för att få bästa pris och anpassad lösning för ditt företag!
Relaterade artiklar
Om Met3DP
Senaste uppdateringen
Vår produkt
KONTAKTA OSS
Har du några frågor? Skicka oss meddelande nu! Vi kommer att betjäna din begäran med ett helt team efter att ha fått ditt meddelande.
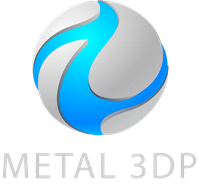
Metallpulver för 3D-printing och additiv tillverkning