Rostfritt stål 316L Pulver
Innehållsförteckning
Rostfritt stål 316L pulver är ett populärt materialval för många applikationer på grund av dess utmärkta korrosionsbeständighet, mekaniska egenskaper och biokompatibilitet. Den här guiden ger en detaljerad översikt över 316L-pulver, inklusive dess egenskaper, produktionsmetoder, applikationer, leverantörer och mer.
Översikt över rostfritt stål 316L pulver
Rostfritt stål 316L pulver är en typ av rostfri stållegering som innehåller molybden för ökad korrosionsbeständighet. "L" hänvisar till den låga kolhalten, vilket förbättrar svetsbarheten.
Några viktiga egenskaper och kännetecken för 316L-pulver är
- Utmärkt korrosionsbeständighet, speciellt mot grop- och spaltkorrosion
- Hög hållfasthet och god duktilitet
- Enastående biokompatibilitet och lämplig för medicinska implantat
- Icke-magnetisk austenitisk struktur
- Hög oxidations- och krypmotstånd vid förhöjda temperaturer
- Finns i olika partikelstorlekar och morfologier
316L pulver kan framställas genom gasförstoftning, vattenförstoftning och andra metoder. Pulverproduktionsprocessen påverkar pulvrets egenskaper som partikelform, storleksfördelning, flytbarhet och mer.
Här är en jämförelse av olika 316L-pulvertyper och deras typiska tillämpningar:
Typ av pulver | Partikelstorlek | Morfologi | Tillämpningar |
---|---|---|---|
Atomiserad gas | 15-150 μm | Sfärisk | Additiv tillverkning, MIM |
Vatten som finfördelas | 10-300 μm | Oregelbunden, dendritisk | Formsprutning av metall |
Atomiserad plasma | <100 μm | Sfärisk | Additiv tillverkning |
Elektrolytisk | <150 μm | Dendritisk, spetsig | Additiv tillverkning, pressning |
Karbonyl | <10 μm | Sfärisk | Pulvermetallurgi, pressning |
316L-pulver värderas för sin kombination av styrka, korrosionsbeständighet och biokompatibilitet. Några av de stora applikationerna inkluderar:
- Additiv tillverkning – Selektiv lasersmältning, direkt metalllasersintring, bindemedelssprutning
- Formsprutning av metall – Små, komplexa delar som ortopediska implantat
- Press och sinter – Filter, porösa strukturer, självsmörjande lager
- Ytbeläggning – För att förbättra slitage- och korrosionsbeständigheten
- Hårdlödning och svetsning – Som tillsatsmaterial
Här är en översikt över hur 316L-pulver används i olika tillverkningsprocesser:
Tillverkningsprocess | Hur 316L pulver används |
---|---|
Additiv tillverkning | Pulverbädden smälts selektivt med laser för att bygga 3D-delar |
Formsprutning av metall | Pulver blandat med bindemedel, gjutet, sedan sintrat |
Pressa och sintra | Pulver pressas till form och sintras sedan |
Ytbeläggning | Sprayas eller smälts på ytan genom termisk sprutning, laserbeklädnad etc. |
Lödning och svetsning | Används som tillsatsmaterial för fogning |
Den ultrafina kornstrukturen och den homogena konsistensen som erhålls från pulver gör 316L till ett idealiskt material för kritiska applikationer inom rymd, medicinsk, kemisk bearbetning och mer.
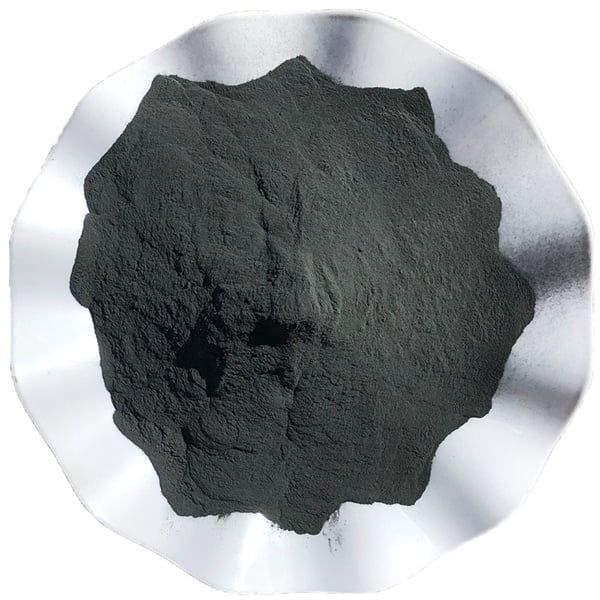
Egenskaper för 316L rostfritt stålpulver
Fastighet | Beskrivning | Inverkan på användbarhet |
---|---|---|
Kemisk sammansättning | Består huvudsakligen av järn (Fe), krom (Cr) (16-18%), nickel (Ni) (10-12%), molybden (Mo) (2-3%), med mindre tillsatser av kisel (Si), mangan (Mn), fosfor (P), kväve (N), kväve (N). Lågt kolinnehåll (mindre än 0,03%) | Det höga krominnehållet ger utmärkt korrosionsbeständighet, speciellt mot grop- och spaltkorrosion. Nickel förbättrar styrka och duktilitet, medan molybden förbättrar motståndskraften mot lokala attacker, särskilt av klorider. Låg kolhalt minimerar risken för karbidutfällning vid svetsning eller högtemperaturprocesser. |
Partikelstorlek och distribution | Mäts i mikrometer (µm), med ett typiskt intervall på 15-50 µm. Fördelningen av partikelstorlekar inom detta område är avgörande. | Partikelstorlek och fördelning påverkar avsevärt flytbarhet, packningsdensitet och slutproduktens mekaniska egenskaper. Finare partiklar ger i allmänhet bättre ytfinish men kan vara utmanande att hantera på grund av dålig flytbarhet. En välkontrollerad fördelning med en blandning av partikelstorlekar optimerar packningen och minimerar tomrum i slutprodukten. |
Skenbar densitet och tappdensitet | Skenbar densitet hänvisar till densiteten hos pulvret som löst hällt. Tappdensiteten mäts efter att man tappat på pulverbehållaren för att uppnå en tätare packning. Enheterna är vanligtvis g/cm³. | Skillnaden mellan skenbar och tappdensitet återspeglar pulvrets flytbarhet. En högre tappdensitet i förhållande till skenbar densitet indikerar bättre flödesegenskaper, väsentligt för effektiv pulverbäddsskapande i additiv tillverkningsprocesser. |
Flytbarhet | Lättheten med vilken pulver flyter under sin egen vikt. Mäts med tekniker som Hall Flowmeter eller Carr Index. | God flytbarhet möjliggör jämn pulverspridning och minimerar segregering (separering av olika partikelstorlekar) under hantering och deponering. Detta översätts till konsekvent densitet och egenskaper i slutprodukten. |
Sfäriskhet & morfologi | Sfäricitet hänvisar till hur mycket en partikel liknar en perfekt sfär. Morfologi beskriver partiklarnas övergripande form (sfärisk, kantig, oregelbunden). | Sfäriska partiklar flyter vanligtvis bättre och packas tätare jämfört med oregelbundna former. Vissa tillämpningar kan dock dra nytta av en specifik partikelmorfologi för att uppnå önskad yttextur eller sammanlåsning av partiklar. |
Smältpunkt och intervall | Runt 1400°C (2552°F). Smältområdet kan variera något beroende på den specifika pulversammansättningen. | Smältpunkten är avgörande för att bestämma lämpliga bearbetningstemperaturer i tekniker som sintring eller additiv tillverkning. |
Termisk konduktivitet | Cirka 16 W/mK. | Värmeledningsförmågan påverkar värmeöverföringen i pulverbädden under bearbetning. Detta kan påverka faktorer som kylningshastigheter, kvarvarande spänningar och bildandet av oönskade faser i slutprodukten. |
Sinterbeteende | Pulverpartiklarnas förmåga att binda samman under en högtemperaturuppvärmningsprocess (sintring) för att bilda ett fast föremål. | Sintringsbeteende beror på faktorer som partikelstorleksfördelning, pulverytkemi och sintringsparametrar. Välkontrollerad sintring möjliggör förtätning av pulverbädden, vilket uppnår de önskade mekaniska egenskaperna i slutprodukten. |
Motståndskraft mot korrosion | Ärver utmärkt korrosionsbeständighet från sin bulkmotsvarighet, 316L rostfritt stål. Ger motståndskraft mot ett brett spektrum av miljöer, inklusive oxiderande syror, reducerande syror och saltspray. | Molybdenhalten i 316L pulver ger överlägsen motståndskraft mot gropkorrosion, särskilt i kloridhaltiga miljöer, jämfört med 304L pulver av rostfritt stål. Detta gör den lämplig för applikationer som kräver hög korrosionsbeständighet. |
Produktionsmetoder för 316L pulver
Metod | Beskrivning | Partikelegenskaper | Fördelar | Nackdelar | Tillämpningar |
---|---|---|---|---|---|
Atomisering av gas | Smält 316L stål sprutas in i en höghastighets inert gasström och bryter den till fina droppar som snabbt stelnar till sfäriska partiklar. | – Sfärisk form – Tät storleksfördelning (15-45 mikron) – Utmärkt flytbarhet – Hög packningsdensitet | – Konsekvent kvalitet – Bra för Additive Manufacturing (AM) processer som Laser Beam Melting (LBM) och Electron Beam Melting (EBM) | – Hög energiförbrukning – Potential för syre- och kväveupptagning | – Flygkomponenter (turbinblad, värmeväxlare) – Medicinska implantat (på grund av biokompatibilitet) – Högpresterande bildelar |
Atomisering av vatten | Liknar gasatomisering, men använder en högtrycksvattenstråle för att bryta den smälta metallen. | – Oregelbunden form med vissa satelliter (smälta partiklar) – Bredare storleksfördelning (10-100 mikron) – Lägre flytbarhet jämfört med gasförstoftning | – Mer kostnadseffektiv än gasförstoftning – Lämplig för applikationer där sfärisk form är mindre kritisk | – Högre syrehalt på grund av vatteninteraktion – Kan kräva ytterligare efterbearbetning för AM | – Reaktorer med fluidiserad bädd (katalysatorbärare) – Metal Injection Molding (MIM) råmaterial |
Plasmaatomisering | Använder en plasmabrännare med hög temperatur och hög hastighet för att smälta och finfördela 316L stålråvaran. | – Mycket sfärisk form – Snäv storleksfördelning med finare partiklar möjlig (ned till 5 mikron) – Utmärkt flytbarhet | – Överlägsen kvalitet för krävande AM-applikationer – Kan uppnå finare puder för intrikata funktioner | – Högsta energiförbrukningen av de tre metoderna – Kräver specialutrustning | – Högpresterande turbinblad – Mikrofluidkomponenter – Biomedicinska implantat som kräver hög ytfinish |
Mekanisk legering | Fasta elementära eller förlegerade pulver blandas och mals tillsammans i en högenergikulkvarn för att uppnå en enhetlig 316L sammansättning. | – Oregelbunden form med kantiga facetter – Bred storleksfördelning – Lägre flytbarhet | – Mycket anpassningsbar för att skapa unika legeringskompositioner som inte kan uppnås med andra metoder | – Längre bearbetningstid jämfört med finfördelningstekniker – Kan kräva ytterligare steg för att förbättra flytbarheten för AM | – Specialiserade komponenter som kräver specifika materialegenskaper – Utveckling av nya legeringar för AM |
Elektrolys | En vattenbaserad process där en 316L anod löses upp i elektrolytlösningen och metalljonerna avsätts som pulver på katoden. | – Sfäriska eller dendritiska former – Bred storleksfördelning – Kan vara porösa | – Mycket rena pulver kan uppnås – Potential för tillverkning av nästan nettoform | – Begränsad produktionskapacitet – Relativt långsam process | – Biomedicinska implantat som kräver hög renhet – Katalysatorstöd – Specialiserade applikationer som kräver specifika pulveregenskaper |
Tillämpningar av 316L rostfritt stålpulver
Industri | Tillämpning | Fastigheter med hävstångseffekt | Ytterligare anmärkningar |
---|---|---|---|
Medicin & tandvård | * Implantat (knä, höft, dentala) * Kirurgiska instrument * Proteser | * Biokompatibel (säker för kroppskontakt) * Utmärkt korrosionsbeständighet * Hög hållfasthet * Formbarhet för komplexa konstruktioner | * 316L minimerar risken för avstötning och infektion. * Pulver möjliggör skapandet av porösa strukturer för beninväxt. * Kan steriliseras för säker kirurgisk användning. |
Livsmedelsbearbetning | * Kärl * Rör * Ventiler * Beslag * Fästelement | * Överlägsen korrosionsbeständighet mot matsyror och saltlösning * Lätt att rengöra och underhålla * Uppfyller hygien- och säkerhetsstandarder | * 316L säkerställer livsmedelskvalitet och förhindrar kontaminering. * Släta ytor minimerar bakteriella punkter. * Tål upprepade rengöringscykler. |
Marin | * Propelleraxlar * Dieselmotordelar * Däcksutrustning | * Exceptionell motståndskraft mot saltvattenkorrosion * Hög mekanisk hållfasthet * Hållbarhet i tuffa miljöer | * 316L förlänger livslängden för kritiska marina komponenter. * Upprätthåller strukturell integritet under stress och tunga belastningar. * Fungerar tillförlitligt i varierande temperaturer. |
Kemi & Petrokemi | * Reaktionskärl * Rörsystem * Ventiler * Pumpar | * Ogenomtränglig för ett brett spektrum av kemikalier * Hög temperaturbeständighet * Trycktolerans | * 316L kan hantera aggressiva kemikalier utan nedbrytning. * Tål höga bearbetningstemperaturer för effektiva reaktioner. * Lämplig för högtrycksmiljöer i raffinaderier och anläggningar. |
Flyg- och rymdindustrin | * Flygplansmotorkomponenter * Vätskekontrollsystem * Strukturella delar | * Hög hållfasthet i förhållande till vikt * Utmärkta mekaniska egenskaper vid förhöjda temperaturer * Korrosionsbeständighet i utmanande miljöer | * 316L minskar vikten för förbättrad bränsleeffektivitet. * Upprätthåller prestanda under extrem värme och tryck. * Motstår korrosion från flygbränsle och andra flygvätskor. |
Fordon | * Avgaskomponenter * Motordelar * Trim och dekorativa element | * Högtemperaturbeständighet * Formbarhet för komplexa former * Korrosionsbeständighet för förlängd livslängd | * 316L klarar heta avgaser utan att bli skev. * Kan formas till invecklade avgasgrenrör och rör. * Motstår korrosion från vägsalt och tuffa väderförhållanden. |
Konsumentvaror | * Klockor * Smycken * Bestick * Hushållsapparater | * Estetisk tilltalande tack vare polerad finish * Hög hållfasthet och slitstyrka * Korrosionsbeständighet för enkel rengöring och hygien | * 316L erbjuder ett elegant, lyxigt utseende för exklusiva varor. * Redskap och apparater bibehåller skärpa och hållbarhet. * Lätt att hålla en ren och hygienisk yta. |
Konstruktion | * Arkitektonisk beklädnad * Fästelement * Räcken * Hårdvara | * Korrosionsbeständighet för utomhusapplikationer * Hög hållfasthet och väderbeständighet * Estetisk överklagande för modern design | * 316L tål hårda väderförhållanden utan att rosta. * Upprätthåller strukturell integritet och funktionalitet över tid. * Erbjuder en elegant, modern look för arkitektoniska element. |
Specifikationer och standarder
316L pulversammansättning, kvalitet och egenskaper styrs av olika internationella specifikationer och standarder.
ASTM-standarder
- ASTM A240 – Standard för plåt, plåt och band av krom och krom-nickel rostfritt stål för tryckkärl och allmänna applikationer. Definierar sammansättningsgränser och mekaniska egenskaper för 316L legering.
- ASTM B822 – Standardtestmetod för partikelstorleksfördelning av metallpulver och relaterade föreningar genom ljusspridning. Används för att karakterisera puderstorleksfördelning.
- ASTM F3055 – Standardspecifikation för additiv tillverkning av nickellegeringspulver avsett för användning i pulverbäddsfusionsapplikationer. Definierar stränga krav för AM nickellegeringspulver inklusive 316L.
- ASTM F3049 – Guide för karakterisering av egenskaper hos metallpulver som används för additiva tillverkningsprocesser. Ger vägledning om att mäta egenskaper som flöde, densitet, morfologi etc.
Andra standarder
- ISO 9001 – Kvalitetsledning för tillverkning av metallpulver
- ISO 13485 – Kvalitetsledning för metallpulver för medicinska tillämpningar
- ASME Boiler and Pressure Vessel Code – Materialkrav för tryckkärlapplikationer
Ansedda 316L-pulverleverantörer har kvalitetssystem certifierade enligt ISO- och ASTM-standarder. Lots spårbarhet och omfattande tester upprätthålls för att säkerställa efterlevnad.
316L pulver leverantörer
Några ledande globala leverantörer av 316L rostfritt stålpulver är bl.a:
Företag | Produktionsmetoder | Pulvertyper | Partikelstorlek |
---|---|---|---|
Sandvik | Atomisering av gas | Osprey® 316L | 15-45 μm |
LPW-teknik | Atomisering av gas | LPW 316L | 15-63 μm |
Snickare | Atomisering av gas | Snickare 316L | 15-150 μm |
Höganäs | Atomisering av vatten | 316L | 10-45 μm |
CNPC | Atomisering av gas och vatten | 316L | 10-150 μm |
Pometon | Atomisering av gas och vatten | 316L | 10-150 μm |
ATI | Atomisering av gas | 316L | 10-63 μm |
316L pulverpriset beror på faktorer som:
- Pulverkvalitet, sammansättning, partikelstorlek och morfologi
- Produktionsmetod
- Beställningskvantitet och partistorlek
- Nivå på kvalitetskontroll och testning
- Krav på förpackning och leverans
Indikativ prissättning för gasatomiserat 316L-pulver ligger i intervallet $50-100 per kg för standardbeställningar. Anpassade beställningar med speciella krav kan kosta mer.
När du väljer en leverantör av 316L pulver, inkluderar några viktiga överväganden:
- Pulveregenskaper – partikelstorleksfördelning, morfologi, flytbarhet etc. bör matcha applikationsbehov
- Konsekvent kvalitet och sammansättning enligt specifikationer
- Pålitlig försörjningskedja och logistik
- Överensstämmelse med internationella standarder och certifieringar
- Teknisk expertis och kundservice
- Prissättning och minsta orderkvantitet
Ledande 316L-pulvertillverkare har årtionden av erfarenhet av att producera pulver som är skräddarsydda för AM, MIM och andra applikationer med sträng kvalitetskontroll.
Designöverväganden för 316L pulver
Designöverväganden för 316L rostfritt stålpulver
Aspekt | Övervägande | Inverkan på tryckt del | Rekommendationer |
---|---|---|---|
Väggens tjocklek | Minsta tjocklek bör vara 0,8-1 mm | Delar med tunnare väggar kan vara svaga och benägna att spricka. | * Designa väggar minst 1 mm tjocka för optimal styrka. * Överväg att använda invändiga ribbor eller galler för förstärkning i tunna sektioner. * För delar som kräver minimal väggtjocklek, utforska alternativa AM-processer med högre upplösning. |
Överhäng & vinklar | Skarpa hörn och ostödda överhäng kan leda till skevhet och delaminering. | * Minimera skarpa hörn genom att införliva filéer och kurvor. * Designa överhäng med vinklar mellan 30-45 grader för bättre stöd. * Använd strategiskt placerade stödstrukturer under utskrift för att förhindra hängande. | |
Ytfinish & Orientering | Pulveregenskaper och lagerorientering kan påverka ytstrukturen. | * Förstå hur pulverstorlek och morfologi påverkar ytjämnheten. * Överväg delorientering för att minimera lagersynlighet på kritiska ytor. * Efterbehandlingstekniker som polering eller blästring kan förbättra ytfinishen. | |
Porositet | Luftfickor instängda i delen kan äventyra mekaniska egenskaper. | * Optimera utskriftsparametrar som laserkraft och skanningshastighet för att uppnå hög densitet. * Utforska tekniker som Hot Isostatic Pressing (HIP) för att ytterligare minimera porositeten. * Designa interna kanaler eller ventilationshål för att underlätta borttagning av pulver under utskrift. | |
Stresshantering | Kvarvarande spänningar från tryckprocessen kan leda till skevhet eller sprickbildning. | * Använd stödstrukturer strategiskt för att minimera stresskoncentrationspunkter. * Designfunktioner som filéer och gradvisa övergångar för att minska stressuppbyggnad. * Överväg värmebehandling efter tryck för avspänningsglödgning. | |
Dimensionell noggrannhet | Pulverstorleksfördelning och krympning under sintring kan påverka slutdimensionerna. | * Ta hänsyn till krympningshastigheter (vanligtvis runt 20%) när du designar modellen. * Använd design för additiv tillverkning (DfAM) principer för att optimera tryckbarheten och minimera dimensionella avvikelser. * Skriv ut testdelar för att kalibrera utskriftsparametrar och säkerställa dimensionsnoggrannhet. | |
Stödstrukturer | Tillfälliga strukturer som behövs för komplexa geometrier kan lämna spår. | * Designa stödstrukturer med minimal kontaktyta för att minimera borttagningsmärken. * Utforska upplösbart stödmaterial för enklare efterbearbetning. * Optimera designen av stödstrukturen för effektiv materialanvändning och enkel borttagning. | |
Avlägsnande av pulver | Oavlägsnat pulver som fångas inuti håligheter kan påverka funktionaliteten. | * Designa interna kanaler eller dräneringshål för att underlätta borttagning av pulver. * Använd vinklade funktioner och ventilationsstrategier för att förhindra att pulver fastnar. * Optimera utskriftsparametrar för att minimera pulver som fastnar och förbättra flytbarheten. |
Efterbearbetning av 316L delar
Efterbearbetning av 316L delar av rostfritt stål
Process | Beskrivning | Fördelar | Överväganden |
---|---|---|---|
Borttagning av stöd | Ta bort tillfälliga strukturer som används under utskrift. | * Viktigt för att uppnå slutlig detaljgeometri. * Ger tillgång till interna funktioner. | * Val av borttagningsmetod beror på typ av stödmaterial (manuell, mekanisk, kemisk upplösning). * Försiktig hantering krävs för att undvika att skada delen. |
Värmebehandling | * Avspänningsglödgning: Minskar kvarvarande spänningar från utskrift för att förbättra dimensionsstabiliteten och förhindra sprickbildning. * Lösningsglödgning: Förfinar mikrostrukturen för förbättrade mekaniska egenskaper och korrosionsbeständighet. | * Optimerar prestandan och livslängden för delen. * Möjliggör överensstämmelse med specifika materialspecifikationer. | * Kräver exakt kontroll av temperatur och tid baserat på delens geometri och önskat resultat. * Snabba kylningstekniker som härdning kan vara nödvändiga för lösningsglödgning. |
Shot Peening | Bombardera ytan med små metallkulor för att skapa ett tryckspänningsskikt. | * Förbättrar utmattningshållfasthet och slitstyrka. * Förbättrar motståndet mot spänningskorrosionssprickor. | * Val av skottmedia och blästringsparametrar beror på önskad ytfinish och effektdjup. * Överdriven blästring kan skapa ytjämnhet. |
Betning & Passivering | Kemisk rengöringsprocess för att avlägsna ytföroreningar och förbättra korrosionsbeständigheten. | * Viktigt för delar som utsätts för tuffa miljöer. * Skapar ett passivt oxidskikt för förbättrat korrosionsskydd. | * Val av betnings- och passiveringslösningar beror på materialkvalitet och yttillstånd. * Felaktig hantering av kemikalier kräver lämpliga säkerhetsåtgärder. |
Bearbetning & Finishing | Traditionella subtraktiva tekniker för att uppnå exakta dimensioner, toleranser och ytfinish. | * Möjliggör skapandet av funktioner som inte kan uppnås med AM. * Förbättrar ytestetik och funktionalitet. | * Kräver ytterligare bearbetningsexpertis och utrustning. * Kan införa värme och stress som kräver ytterligare efterbearbetning. |
Polering | Mekaniska eller kemiska metoder för att uppnå en slät, reflekterande yta. | * Förbättrar estetiskt tilltalande för dekorativa applikationer. * Förbättrar ythygienen för medicinsk utrustning. * Minskar ytjämnheten för förbättrad slitstyrka. | * Val av poleringsmetod beror på önskad finishnivå. * Överdriven polering kan ta bort material och ändra delars dimensioner. |
Elektroplätering | Lägg ett tunt lager av en annan metall på ytan för förbättrade egenskaper. | * Förbättrar elektrisk ledningsförmåga, slitstyrka eller korrosionsbeständighet. * Erbjuder dekorativa ytskikt som krom eller guldplätering. | * Kräver specialiserad utrustning och expertis för galvanisering av bad. * Platttjockleken måste kontrolleras noggrant för att undvika delaminering. |
Vanliga defekter i 316L delar
Defekt | Beskrivning | Orsak | Påverkan | Strategier för begränsning |
---|---|---|---|---|
Porositet | Luftfickor fångade i delen under utskrift. | * Suboptimal laserkraft eller skanningshastighet. * Otillräcklig pulverflytbarhet. * Felaktig gasrening. | * Minskad mekanisk hållfasthet, utmattningslivslängd och korrosionsbeständighet. * Kan skapa läckagevägar i vätskeapplikationer. | * Optimera utskriftsparametrar för korrekt smältning och densitet. * Förvärm pulverbädden för att förbättra flödet. * Använd inertgasrening för att minimera instängd luft. * Överväg efterbehandlingstekniker som Hot Isostatic Pressing (HIP) för ytterligare förtätning. |
Brist på fusion | Ofullständig smältning mellan intilliggande pulverlager. | * Otillräcklig lasereffekttäthet. * Inkonsekvent tjocklek på pulverskiktet. * Kontaminering på pulverytan. | * Svag bindning mellan skikten, vilket leder till potentiell sprickbildning och delfel. | * Kalibrera laserkraft och skanningshastighet för rätt smältdjup. * Säkerställ konsekvent tjocklek på pulverskiktet genom lämpliga övermålningsmekanismer. * Håll en ren pulverbädd fri från fukt eller föroreningar. |
Ballongning | Smält metall ackumuleras till överdrivna pärlor på den övre ytan. | * Överdriven lasereffekttäthet. * Felaktig skanningshastighet. * Felaktig pulverstorleksfördelning. | * Grov ytfinish med dålig estetik. * Potential för stänk och processinstabilitet. | * Minska lasereffekten eller öka skanningshastigheten för att förhindra överhettning. * Optimera skanningsmönster för att undvika överdriven uppehållstid på ett enda område. * Använd en mer enhetlig pulverstorleksfördelning för konsekvent smältbeteende. |
Sprickor | Sprickor i delen på grund av kvarvarande spänningar eller termisk chock. | * Snabb kylning under utskrift. * Otillräcklig stressavlastning efterbearbetning. * Skarpa hörn eller designfunktioner som koncentrerar stress. | * Äventyrad strukturell integritet och potential för delfel. | * Implementera långsammare kylningshastigheter under utskrift för att minimera termiska gradienter. * Utför avspänningsglödgning för att minska kvarvarande spänningar. * Designfunktioner med mjuka övergångar och undvik skarpa hörn. |
Warpage | Förvrängning av delen från dess avsedda geometri. | * Ojämn termisk expansion och sammandragning under utskrift. * Otillräckliga stödstrukturer för komplexa geometrier. * Restspänningar låsta i delen. | * Dimensionella felaktigheter och risk för funktionsfel. | * Optimera utskriftsparametrar för att minimera termiska gradienter. * Använd strategiskt placerade stödstrukturer för korrekt stöd under utskrift. * Implementera avspänningsglödgning för att minska snedvridningstendenser. |
Delaminering | Separering av lager inom delen. | * Svag bindning mellan skikten på grund av bristande sammansmältning. * För hög fukthalt i pulvret. * Kontaminering på pulverbädden. | * Förlust av strukturell integritet och potential för delaminering av delar. | * Säkerställ korrekt sammansmältning mellan lager genom att optimera utskriftsparametrar. * Bibehåll låg pulverfuktighet genom korrekt förvaring och hantering. * Använd en ren pulverbädd fri från föroreningar. |
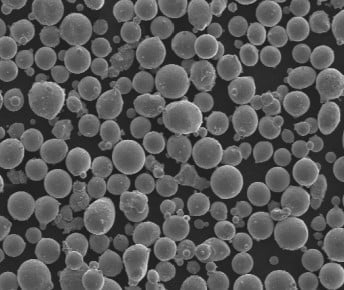
Hur man väljer en 316L pulverleverantör
Här är en steg-för-steg-guide för att välja leverantör för 316L rostfritt stålpulver:
Steg 1: Bestäm applikationskrav
- Fundera på vilken tillverkningsprocess som kommer att användas – AM, MIM etc.
- Identifiera de kritiska pulveregenskaperna som behövs som partikelstorlek, form, renhet etc.
- Tänk på detaljspecifikationerna - mekaniska egenskaper, noggrannhet, ytfinish etc.
Steg 2: Undersök potentiella leverantörer
- Sök efter ledande 316L pulvertillverkare med lång erfarenhet
- Kontrollera kapacitet – produktionsmetoder, pulversorter, QC-testning etc.
- Granska fallstudier och kundrecensioner som är relevanta för din ansökan
Steg 3: Utvärdera tekniska förmågor
- Kan de anpassa 316L pulver till dina applikationsbehov?
- Har de expertis inom AM, MIM eller andra pulverteknologier?
- Vilken är deras nivå av vertikal integration och kvalitetskontroll?
Steg 4: Bedöm tjänsteerbjudanden
- Teknisk support vid pulverval, applikationsutveckling
- Provtester, testtjänster
- Lyhördhet för förfrågningar, ledtidsflexibilitet
Steg 5: Granska certifieringar och efterlevnad
- Internationella kvalitetscertifieringar – ISO 9001, ISO 13485 etc.
- Överensstämmelse med pulversammansättningsstandarder som ASTM
- Partispårbarhet, omfattande tester och dokumentation
Steg 6: Jämför priser
- Pris per kg för önskad partikelstorlek, kvalitetsnivå, kvantitet
- Minsta orderkvantitet och krav på partistorlek
- Frakt/logistikkostnader
Steg 7: Kontrollera tillgänglighet och tillförlitlighet
- Stadig lagertillgång och förmåga att möta efterfrågefluktuationer
- Orderspårning och övervakning, transparenta ledtider
- Bevisat leveransrekord i tid
Att välja en leverantör med applikationsexpertis, konsekvent produktkvalitet och lyhörd service säkerställer en smidig upphandlingsupplevelse.
Hur man optimerar 316L pulver för AM
Matcha partikelstorleken till AM-processen
- Använd 10-45 μm partiklar för pulverbäddfusion som DMLS, SLM
- Optimera storleksfördelningen – för bred kan orsaka packningsproblem
- Finare 1-10 μm partiklar bättre lämpade för bindemedelssprutning
Uppnå hög sfäricitet och flytbarhet
- Flytbarheten påverkar direkt pulverspridningen och skiktlikheten
- Gasatomisering ger sfäriska, friflytande pulver
- Testa pulverflöde enligt ASTM B213 standard
Minimera satellitpartiklar
- Använd siktning, klassificering för att ta bort satelliter och böter
- Satelliter kan orsaka agglomeration och defekter
Kontrollkompositionstolerans
- Tätt kontroll av elementär sammansättning inom ASTM specificerat område
- Begränsa föroreningar som O, N, C som påverkar egenskaperna
Minska porositeten
- Optimera processparametrar och skanningsmönster
- Använd varm isostatisk pressning för att minimera porositeten
- Bibehåll >99% densitet för hög prestanda
Minimera kvarstående spänningar
- Optimera termiska gradienter i byggprocessen
- Använd lämpliga värmebehandlingar för att lindra påfrestningar
Uppnå mål för mekaniska egenskaper
- Lösningsglödgning och åldring förbättrar styrkan
- Bibehåll enhetliga egenskaper i alla byggriktningar
Noggrann pulverkarakterisering, parameteroptimering och efterbearbetning är nyckeln för att uppnå defektfria 316L-delar med AM.
VANLIGA FRÅGOR
F: Vad används 316L rostfritt stålpulver vanligtvis till?
S: 316L pulver används mest för additiv tillverkning, metallformsprutning och press- och sinterapplikationer på grund av dess utmärkta korrosionsbeständighet i kombination med goda mekaniska egenskaper och biokompatibilitet. Vanliga applikationer inkluderar implantat, flygkomponenter, bildelar, biomedicinsk utrustning och verktyg.
F: Vilken partikelstorlek rekommenderas för laserbaserade AM-processer?
S: Ett partikelstorleksintervall på 10-45 mikron rekommenderas vanligtvis för laserpulverbäddfusionsprocesser som DMLS och SLM. Finare partiklar under 10 mikron kan orsaka problem med flöde och spridning. Partikelstorleksfördelning bör också kontrolleras väl.
F: Hur påverkar pulvermorfologi egenskaperna?
S: Mycket sfäriskt, fritt flytande pulver är önskvärt för AM-applikationer. Oregelbundet, taggigt pulver är lämpligt för press- och sintringsmetoder. Satellitpartiklar och fina partiklar påverkar pulverflödet negativt och kan skapa defekter. Att kontrollera pulvermorfologi är nyckeln för optimal prestanda.
F: Vilka är några viktiga skillnader mellan gas atomiserat kontra vatten atomiserat 316L pulver?
S: Gasatomiserat 316L-pulver har mer sfärisk morfologi och bättre flytbarhet. Vattenatomiserat pulver uppvisar mer oregelbundna former men ger högre kompressibilitet som önskas för press- och sinterapplikationer. Gasatomiserat pulver har lägre syrehalt.
F: Vilka efterbearbetningsmetoder används på 316L AM-delar?
S: Vanlig efterbearbetning inkluderar värmebehandling, varm isostatisk pressning, ytbehandling genom slipning/bearbetning, beläggning och kvalitetskontrolltestning. Detta hjälper till att uppnå målegenskaper, dimensionsnoggrannhet, estetik och defektdetektering.
F: Vilka är några vanliga 316L-pulverdefekter och hur kan de undvikas?
S: Potentiella defekter är porositet, sprickbildning, dålig ytfinish, brist på smältning och kvarvarande spänningar. Noggrann processparameteroptimering, pulverkvalitetskontroll, byggorientering och efterbearbetning kan minimera dessa defekter i 316L delar.
F: Vilka standarder gäller för 316L-pulver för AM och andra applikationer?
S: Nyckelstandarder är ASTM F3055 för AM-pulver, ASTM B822 för pulverkarakterisering, ASTM A240 för legeringssammansättning och ISO-standarder för kvalitetsstyrning. Ledande 316L pulverleverantörer är certifierade enligt dessa standarder.
F: Vilka faktorer avgör priset för 316L pulver?
S: Huvudfaktorer som påverkar 316L-pulverprissättningen är kvalitetsnivå, partikelstorlek och distribution, produktionsmetod, orderkvantitet, köparens krav på testning/QC, förpackning och leverans. Strängare behov ökar prissättningen.
F: Hur kan korrosionsbeständigheten hos 316L AM-delar optimeras?
S: Lösningar inkluderar kontroll av föroreningsnivåer genom snäva kemiska sammansättningstoleranser, användning av varm isostatisk pressning för att öka densiteten och minska porositeten, tillämpning av passiveringsbehandlingar och lösningsglödgning för att förbättra korrosionsbeständigheten.
Dela på
MET3DP Technology Co, LTD är en ledande leverantör av lösningar för additiv tillverkning med huvudkontor i Qingdao, Kina. Vårt företag är specialiserat på 3D-utskriftsutrustning och högpresterande metallpulver för industriella tillämpningar.
Förfrågan för att få bästa pris och anpassad lösning för ditt företag!
Relaterade artiklar
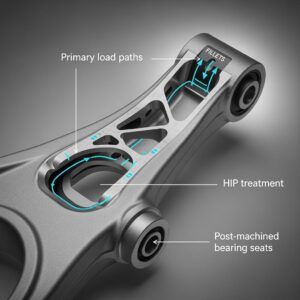
Metal 3D Printing for U.S. Automotive Lightweight Structural Brackets and Suspension Components
Läs mer "Om Met3DP
Senaste uppdateringen
Vår produkt
KONTAKTA OSS
Har du några frågor? Skicka oss meddelande nu! Vi kommer att betjäna din begäran med ett helt team efter att ha fått ditt meddelande.