Precision Steering Housing via Metal Additive Manufacturing
Innehållsförteckning
Introduction: The Critical Role of Missile Steering Housings and Advanced Manufacturing
In the high-stakes realm of aerospace and defense, precision and reliability are not just desirable attributes; they are absolute imperatives. Among the myriad of complex components that ensure the mission success of advanced missile systems, the steering mechanism housing plays a pivotal, albeit often unseen, role. This critical component serves as the protective enclosure and structural backbone for the sensitive actuators, sensors, and linkages responsible for guiding a missile towards its intended target with pinpoint accuracy. The failure of this single housing, whether due to structural compromise under extreme G-forces, thermal degradation during flight, or manufacturing defects, can lead to catastrophic mission failure. Therefore, the design, material selection, and manufacturing process for these housings are subject to the most stringent requirements demanding exceptional strength, durability, thermal stability, and geometric precision.
Traditionally, manufacturing such intricate components relied heavily on subtractive methods like multi-axis CNC machining from billet or investment casting, often involving complex tooling, significant material waste, and lengthy production cycles. While these methods have served the industry for decades, they increasingly face limitations when confronted with the escalating performance demands and geometric complexity required by next-generation missile systems. Engineers continually seek ways to reduce weight, enhance thermal management, integrate functionality, and shorten development timelines – goals that often push traditional manufacturing to its limits.
Det är här Additiv tillverkning av metall (AM), commonly known as metal 3D-utskrifter, emerges as a disruptive and transformative technology. Metal AM offers unprecedented design freedom, enabling the creation of highly complex, lightweight, and optimized structures that were previously impossible or prohibitively expensive to manufacture. By building parts layer by layer directly from digital models using high-performance metal powders, AM unlocks new possibilities for enhancing missile performance, reliability, and manufacturability. It allows for the integration of intricate internal features, conformal cooling channels, and topology-optimized geometries that minimize weight without compromising structural integrity. This paradigm shift is not merely an alternative manufacturing route; it represents a fundamental change in how critical defense components can be conceived, designed, and produced.
The successful implementation of metal AM for mission-critical applications like missile steering housings, however, necessitates a deep understanding of materials science, process physics, and stringent quality control. The choice of metal powder, the precision of the printing process, and the execution of post-processing steps are all crucial factors determining the final part’s performance and reliability. This is where specialized expertise and advanced technological capabilities become paramount.
At Met3dp, we stand at the forefront of this manufacturing revolution. Headquartered in Qingdao, China, Met3dp Technology Co., LTD specializes in providing comprehensive additive manufacturing solutions, encompassing industry-leading metal 3D printing equipment (utilizing technologies like Selective Electron Beam Melting – SEBM) and the production of high-performance, spherical metal powders optimized for AM processes. Our commitment to innovation is reflected in our advanced powder manufacturing systems, employing state-of-the-art gas atomization and Plasma Rotating Electrode Process (PREP) technologies to ensure exceptional powder quality – a critical foundation for printing dense, high-integrity metal parts with superior mechanical properties. We partner with leading organizations in aerospace, defense, medical, automotive, and industrial manufacturing to leverage the full potential of metal AM, transforming design possibilities into tangible, high-performance components. As we delve deeper into the specifics of manufacturing missile steering mechanism housings, we will explore how Met3dp’s expertise and capabilities provide a reliable pathway for producing these vital, precision-engineered parts.
What is a Missile Steering Mechanism Housing Used For? Applications and Demands
The missile steering mechanism housing is far more than just a simple container. It is a multi-functional, high-precision structural component engineered to perform reliably under some of the most demanding conditions imaginable. Its primary function is to securely house and protect the delicate and complex components of the missile’s guidance actuation system. This includes actuators (electro-mechanical, hydraulic, or pneumatic), position sensors, control electronics, and the mechanical linkages that translate guidance commands into physical movements of control surfaces like fins or canards. By providing a stable and protected environment, the housing ensures these critical elements can operate flawlessly throughout the missile’s flight trajectory.
Beyond protection, the housing serves as a critical structural element. It must withstand:
- Extreme G-forces: During launch and high-speed maneuvers, missiles experience immense acceleration and G-loads, potentially exceeding tens or even hundreds of Gs. The housing must maintain its shape and integrity without buckling or failing under these forces.
- Severe Vibration: The operational environment involves intense vibrations originating from the propulsion system, aerodynamic forces, and structural harmonics. The housing must dampen or withstand these vibrations to prevent damage to internal components and maintain alignment accuracy. Material selection and design play crucial roles in managing resonant frequencies.
- Thermal Stresses: Missiles encounter rapid and extreme temperature fluctuations. Aerodynamic heating at supersonic and hypersonic speeds can raise surface temperatures significantly, while internal electronics also generate heat. Simultaneously, components might be exposed to cryogenic temperatures before launch or at high altitudes. The housing material must possess excellent thermal stability, resisting expansion, contraction, and degradation across this wide temperature range. Effective thermal management, potentially involving integrated heat sinks or pathways designed into the housing itself, is often critical.
- Environmental Factors: Depending on the missile type and deployment, the housing might need to resist corrosion from saltwater exposure (naval applications), humidity, dust, and chemical agents.
The primary industries relying on these components are Flyg- och rymdindustrin samt försvar. Specific applications span a wide range of missile systems, each with its unique operational profile and performance requirements:
- Tactical Missiles: Air-to-air, air-to-ground, anti-tank, surface-to-air missiles (SAMs). These often require high maneuverability, rapid response times, and robust performance in challenging battlefield conditions. Weight and size are frequently critical constraints.
- Strategic Missiles: Ballistic missiles (ICBMs, SLBMs) require extreme reliability for long-duration flights, often involving high-altitude and re-entry phases with severe thermal loads.
- Cruise Missiles: Long-range subsonic or supersonic missiles require housings that can endure extended flight times and potentially harsh environmental exposure.
- Hypersonic Vehicles: Emerging hypersonic missiles and glide vehicles present extreme thermal and structural challenges, pushing material and design limits far beyond conventional systems.
These demanding applications translate into a stringent set of performance requirements for the steering mechanism housing:
- Högt förhållande mellan styrka och vikt: Minimizing weight is paramount in aerospace to increase range, payload capacity, and maneuverability. The housing must be as light as possible while retaining the necessary structural strength and stiffness.
- Geometric Complexity: Modern guidance systems often require intricate internal mounting points, complex passageways for wiring or cooling, and non-uniform shapes to conform to limited internal space within the missile airframe.
- Dimensional Accuracy and Stability: Precise tolerances are required for interfacing with actuators, sensors, and the missile body. The housing must maintain its dimensional stability across the full operational temperature range.
- Materialets prestanda: High tensile strength, fatigue resistance, fracture toughness, creep resistance (at elevated temperatures), and corrosion resistance are often essential material properties.
- Reliability and Consistency: Given the critical nature of the application, manufacturing processes must deliver consistent quality and predictable performance with zero defects.
För B2B procurement managers and supply chain specialists within the defense sector, sourcing these components presents unique challenges. Long development cycles, stringent qualification processes, managing obsolescence of older designs, ensuring supply chain security, and controlling costs while meeting escalating performance demands are constant pressures. Traditional manufacturing approaches can exacerbate these challenges, particularly with complex designs leading to high machining costs, significant material waste (buy-to-fly ratio), and long lead times for tooling and production setup. Additive manufacturing offers a compelling value proposition by directly addressing many of these pain points, enabling more agile development, efficient production of complex parts, and potentially simplifying the supply chain for specialized, low-to-medium volume components. The ability to digitally manufacture parts on demand also offers resilience against supply chain disruptions and facilitates rapid deployment of design upgrades.
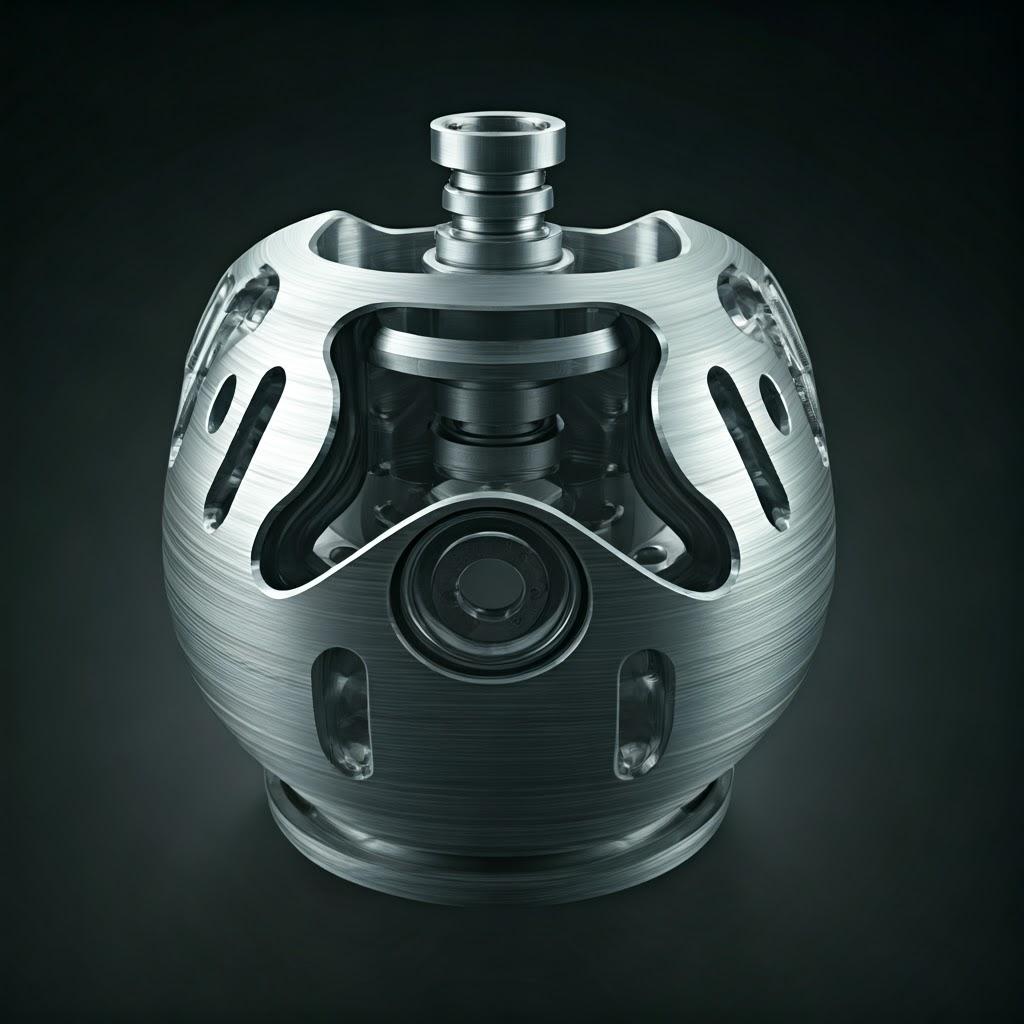
Why Use Metal 3D Printing for Missile Steering Housings? Advantages Over Traditional Methods
The decision to adopt metal additive manufacturing for a component as critical as a missile steering mechanism housing stems from the significant, tangible advantages AM offers over conventional manufacturing techniques like CNC machining and investment casting, particularly when dealing with the complexity and performance demands inherent in modern aerospace and defense applications. While traditional methods remain viable for simpler geometries or high-volume production, metal AM excels where complexity, weight reduction, and lead time are driving factors.
Let’s compare the approaches:
- CNC Machining: This subtractive process starts with a solid block (billet) of material and removes excess material to achieve the final shape.
- Begränsningar: Struggles with highly complex internal features, deep pockets, or undercuts. Can generate significant material waste (poor buy-to-fly ratio), especially with expensive aerospace alloys. Machining time, and thus cost, increases dramatically with complexity. Tool access limitations restrict design possibilities.
- Investeringsgjutning: This process involves creating a wax pattern, coating it with ceramic to form a mold, melting out the wax, and pouring molten metal into the cavity.
- Begränsningar: Requires expensive tooling (molds), making it less suitable for low volumes or prototypes. Achieving very thin walls or highly intricate internal details can be challenging. Porosity can be a concern requiring secondary processes like Hot Isostatic Pressing (HIP). Lead times for tooling development are often long. Design changes necessitate new tooling.
Metal 3D printing, typically using processes like Laser Powder Bed Fusion (LPBF) or Selective Electron Beam Melting (SEBM), builds the part layer by layer from metal powder, offering a fundamentally different approach with distinct benefits:
- Unmatched Geometric Complexity & Design Freedom: This is arguably the most significant advantage of AM. Engineers are no longer constrained by traditional manufacturing limitations like tool access or mold draft angles. This allows for:
- Highly Complex Internal Geometries: Integration of intricate cooling channels, internal structural reinforcements, complex sensor mounts, or convoluted wiring pathways directly into the housing structure.
- Topology Optimization: Using specialized software, designs can be algorithmically optimized to place material only where structurally necessary, resulting in organic-looking, highly efficient structures that minimize weight while meeting stiffness and strength requirements.
- Gitterstrukturer: Incorporating internal lattice structures can drastically reduce weight and potentially improve energy absorption or thermal dissipation characteristics.
- Significant Weight Reduction: Directly linked to design freedom, AM enables the creation of lighter housings through topology optimization and the ability to produce thin, yet strong, walls and internal features. Weight savings directly translate to improved missile performance (range, speed, maneuverability).
- Del Konsolidering: Complex assemblies previously requiring multiple machined or cast parts, fasteners, and seals can often be redesigned and printed as a single, monolithic component. This reduces:
- Assembly time and labor costs.
- Potential points of failure (joints, fasteners).
- Overall part count, simplifying inventory and logistics.
- Potential leak paths in sealed enclosures.
- Rapid Prototyping and Faster Iteration: AM allows designers to move from a digital model to a physical metal prototype in days rather than weeks or months. This accelerates the design validation process, enabling multiple iterations to be tested quickly and cost-effectively, leading to a more optimized final product. This agility is invaluable in the fast-paced defense development environment.
- Reduced Material Waste (Improved Buy-to-Fly Ratio): AM is an additive process, using only the material necessary to build the part and its supports. While some support material is used, the waste is significantly less compared to machining away large volumes of expensive billet material like titanium or high-nickel alloys. This results in better material utilization and lower raw material costs per part, especially for complex geometries.
- Shorter Lead Times (Especially for Low Volume & Development): By eliminating the need for custom tooling (molds, jigs, fixtures), AM significantly reduces the initial lead time for producing the first parts. This is highly advantageous for prototype runs, low-volume production typical of specialized defense systems, or producing replacement parts for legacy systems where original tooling may no longer exist.
- Potential for Enhanced Performance: The design freedom offered by AM can be leveraged to improve functional performance. For example, conformal cooling channels integrated directly into the housing walls can provide much more efficient thermal management for internal electronics compared to traditional solutions, allowing for higher power densities or improved reliability in extreme thermal environments.
For aerospace engineers and defense procurement managers, these advantages directly address key program goals: enhancing system performance, reducing lifecycle costs, shortening development and deployment schedules, and improving supply chain responsiveness. The ability to produce highly optimized, complex components like steering housings more efficiently and with potentially superior performance characteristics makes metal AM a compelling manufacturing solution for next-generation defense hardware. Partnering with an experienced provider like Met3dp ensures access to the necessary process controls and material expertise to realize these benefits reliably.
Recommended Materials (IN625, Ti-6Al-4V) and Why They Matter
Selecting the right material is fundamental to the success of any critical component, especially one subjected to the extreme operational environment of a missile steering mechanism housing. The material must not only withstand the mechanical loads, vibrations, and thermal excursions but also be amenable to the chosen manufacturing process – in this case, metal additive manufacturing. For such demanding applications, high-performance alloys are essential. Two standout candidates, widely used in aerospace and readily processable via metal AM, are the nickel-based superalloy Inconel 625 (IN625) and the titanium alloy Ti-6Al-4V (Grade 5 or Grade 23 ELI).
The choice between these materials often depends on the specific priorities of the application – primarily the balance between temperature resistance, weight, and cost.
Inconel 625 (IN625 / UNS N06625)
Inconel 625 is a nickel-chromium-molybdenum-niobium superalloy renowned for its exceptional combination of properties, making it a workhorse material in harsh environments.
- Viktiga egenskaper:
- High Strength & Toughness: Maintains excellent strength and toughness from cryogenic temperatures up to moderately high temperatures (around 800-900°C or 1500-1650°F).
- Outstanding Corrosion Resistance: Exhibits superb resistance to a wide range of corrosive media, including seawater, acids, and alkaline solutions. Particularly resistant to pitting and crevice corrosion.
- Utmärkt oxidationsbeständighet: Forms a protective oxide layer, providing resistance in high-temperature oxidizing environments.
- Utmattningshållfasthet: Possesses high fatigue and corrosion-fatigue strength.
- Weldability & Fabricability: Generally considered readily weldable and fabricable, which also translates well to AM processability.
- Relevance for Steering Housings: IN625 is an ideal choice when high-temperature performance and resistance to extremely corrosive environments are paramount. Its robustness makes it suitable for housings exposed to hot engine exhaust gases or deployed in harsh naval environments. While denser than titanium, its sheer strength and thermal stability can be enabling factors in certain designs, particularly where extreme temperatures preclude lighter alloys. It’s often specified for components requiring long service life under cyclic thermal and mechanical loads.
Titanium Alloy Ti-6Al-4V (Grade 5 / UNS R56400 or Grade 23 / UNS R56401 ELI)
Ti-6Al-4V is the most widely used titanium alloy, often referred to as the “workhorse” of the titanium industry, especially in aerospace. Grade 23 (Extra Low Interstitials – ELI) offers improved fracture toughness and fatigue strength compared to Grade 5.
- Viktiga egenskaper:
- Utmärkt förhållande mellan styrka och vikt: This is the hallmark property of Ti-6Al-4V. It offers high strength comparable to many steels but at roughly 40-45% lower density.
- Good High-Temperature Performance: Can be used for applications up to around 400°C (750°F), although its strength decreases significantly above this temperature compared to nickel superalloys like IN625.
- Superb Corrosion Resistance: Exhibits outstanding resistance to corrosion in seawater, chloride solutions, and many industrial chemicals, due to the formation of a stable passive oxide layer.
- Biokompatibilitet: Widely used in medical implants (though not relevant for this specific application).
- Elasticitetsmodul: Lower than steel or nickel alloys, providing more “springiness,” which can be advantageous for fatigue or vibration damping in some designs.
- Relevance for Steering Housings: Ti-6Al-4V is the preferred choice when Viktminskning is the primary design driver, which is often the case for missile components to maximize range and maneuverability. Its excellent specific strength (strength divided by density) makes it highly efficient structurally. While its upper-temperature limit is lower than IN625, it is sufficient for many missile applications where extreme temperatures are localized or transient. Its corrosion resistance is also a significant benefit.
Material Properties Comparison (Typical Values at Room Temperature):
Fastighet | Enhet | Inconel 625 (Annealed) | Ti-6Al-4V (Annealed) | Anteckningar |
---|---|---|---|---|
Täthet | g/cm3 (lb/in3) | 8.44 (0.305) | 4.43 (0.160) | Significant weight advantage for Ti-6Al-4V |
Draghållfasthet | MPa (ksi) | ~830 (120) | ~950 (138) | Similar absolute strength |
Utbyteshållfasthet (0,2%) | MPa (ksi) | ~460 (67) | ~880 (128) | Higher yield strength for Ti-6Al-4V |
Styrka-till-vikt | Arbitrary Units | ~98 | ~215 | Ti-6Al-4V significantly superior |
Elasticitetsmodul | GPa (Msi) | ~207 (30) | ~114 (16.5) | IN625 is stiffer |
Max Use Temperature | °C (°F) | ~900+ (1650+) | ~400 (750) | IN625 excels at high temperatures |
Termisk expansion | µm/m⋅°C | ~12.8 | ~8.6 | Lower expansion for Ti-6Al-4V |
Export to Sheets
Note: Properties of AM materials can vary based on process parameters, build orientation, and post-processing (e.g., heat treatment, HIP). These are typical handbook values for wrought annealed material for comparison.
The Importance of Powder Quality:
Regardless of the chosen alloy, the quality of the metal powder used in the AM process is critical for achieving dense, defect-free parts with reliable and repeatable mechanical properties. Factors like:
- Sfäriskhet: Smooth, spherical powder particles ensure good flowability and uniform powder bed density.
- Fördelning av partikelstorlek (PSD): A controlled PSD is crucial for achieving high packing density and consistent melting behavior.
- Renhet: Low levels of impurities and contaminants (like oxygen, nitrogen) are essential, especially for reactive materials like titanium, to avoid embrittlement and ensure desired properties.
- Absence of Satellites: Small particles attached to larger ones can hinder flowability and packing.
This is where a provider’s control over powder production becomes a significant advantage. Met3dp leverages industry-leading Gas Atomization and PREP technologies to manufacture high-quality spherical metal powders. Our gas atomization systems utilize unique nozzle and gas flow designs engineered to produce metallic spheres with high sphericity and excellent flowability. Our rigorous quality control ensures low oxygen content and consistent PSD, tailored for optimal performance in demanding AM processes like SEBM and LPBF. Our comprehensive portfolio includes not only standard alloys like IN625 and Ti-6Al-4V but also innovative materials developed for specific customer needs. Access to this range of high-performance materials, all manufactured under stringent quality controls, is available through our produktutbud. Choosing a partner like Met3dp, with in-house expertise in both powder production and printing processes, provides greater assurance of material quality and traceability – essential elements when manufacturing mission-critical components like missile steering mechanism housings.
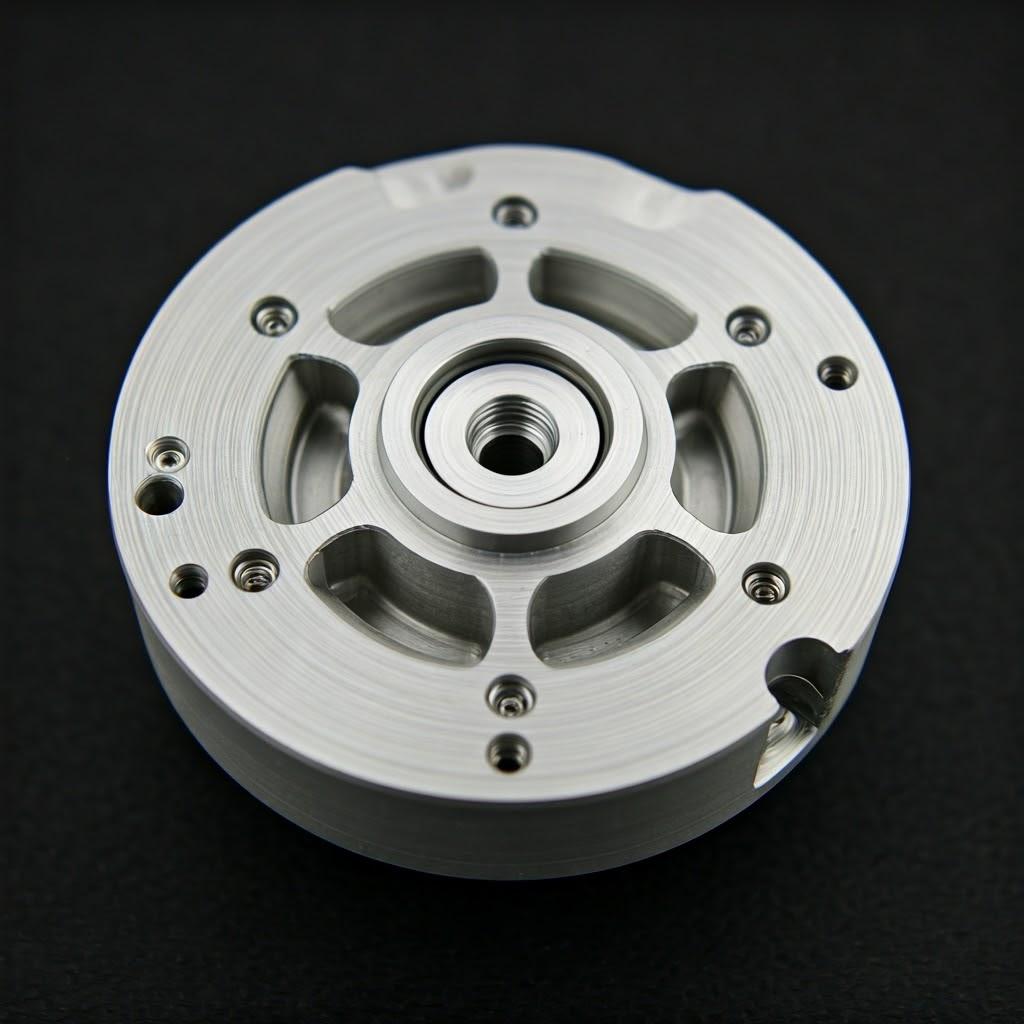
Design Considerations for Additive Manufacturing (DfAM) of Steering Housings
Transitioning the design of a complex component like a missile steering mechanism housing from traditional manufacturing methods to metal additive manufacturing is not simply a matter of converting a CAD file. To truly harness the power of AM and achieve optimal results in terms of performance, cost, and manufacturability, engineers must embrace the principles of Design för additiv tillverkning (DfAM). DfAM involves rethinking the design approach to leverage AM’s unique capabilities while mitigating its inherent constraints. It’s a crucial step that influences everything from print success and part quality to post-processing requirements and final performance. For critical defense components, applying rigorous DfAM principles is non-negotiable.
Here are key DfAM considerations specifically relevant to missile steering housings:
- Geometry Optimization for Printability:
- Overhangs and Support Structures: Metal AM processes like LPBF and SEBM build parts layer by layer. Features that overhang significantly from the main body without underlying support can warp, collapse, or exhibit poor surface quality due to insufficient heat dissipation and gravitational forces acting on the molten material. DfAM encourages designing with self-supporting angles (typically >45 degrees from the horizontal plane, though process-dependent) wherever possible. Where steep overhangs or horizontal ceilings are unavoidable, support structures must be strategically planned.
- Minimizing Supports: While necessary, supports add print time, consume material, and require post-processing steps for removal, which can be challenging and potentially damage the part surface, especially for internal features. DfAM focuses on minimizing the need for supports through clever orientation, incorporating fillets and chamfers instead of sharp horizontal edges, and designing features to be inherently self-supporting. Techniques like breaking down large overhangs into smaller, manageable steps or using diamond or teardrop shapes for horizontal holes can be effective.
- Topology Optimization and Generative Design:
- These computational tools are powerful allies in DfAM, especially for aerospace components where weight is critical. Topology optimization algorithms analyze the load paths and stress distributions within a defined design space and remove material from non-critical areas, resulting in highly efficient, often organic-looking structures.
- For a steering housing, this can lead to significant weight reduction compared to a conventionally designed counterpart, while maintaining or even increasing stiffness and strength. Generative design takes this further, exploring multiple design solutions based on performance constraints and manufacturing methods. Applying these techniques requires expertise in defining load cases, constraints, and manufacturing limitations accurately.
- Designing Complex Internal Features:
- AM excels at creating intricate internal channels and pathways that are impossible to machine or cast. This capability can be leveraged in steering housings for:
- Conformal Cooling: Integrating cooling channels that closely follow the contours of heat-generating internal components (electronics, actuators) for highly efficient thermal management.
- Integrated Wiring Channels: Designing pathways within the housing walls to route wiring, reducing clutter, protecting cables, and potentially simplifying assembly.
- Fluid Passages: For hydraulically or pneumatically actuated systems, internal passages can be integrated directly, eliminating joints and potential leak points.
- Design considerations include ensuring channels are large enough for effective powder removal after printing and potentially for flow requirements (coolant, hydraulic fluid). Smooth internal surfaces and avoidance of sharp turns are also important.
- AM excels at creating intricate internal channels and pathways that are impossible to machine or cast. This capability can be leveraged in steering housings for:
- Wall Thickness and Minimum Features:
- AM processes have limitations on the minimum wall thickness and feature size they can reliably produce. This varies depending on the machine, material, and process parameters but is typically in the range of 0.3-1.0 mm. Designers must ensure all features adhere to these minimums.
- Uniform wall thickness is generally preferred to promote consistent thermal behavior during printing, reducing the risk of warping and residual stress. Abrupt changes in thickness should be transitioned smoothly using fillets or chamfers.
- Support Structure Strategy:
- When supports are unavoidable, their design is critical. They must provide adequate anchoring and thermal conductivity during the build but also be relatively easy to remove without damaging the component.
- Considerations include support type (solid, lattice, conical), contact point density and size, and accessibility for removal tools. Supports on critical functional surfaces or difficult-to-reach internal areas should be avoided if possible through design changes or careful orientation. The impact of support contact points on surface finish must also be considered, as these areas will likely require secondary finishing.
- Part Orientation Planning:
- How a part is oriented on the build plate significantly impacts print time, support requirements, surface finish, and even mechanical properties (due to the anisotropic nature of AM parts).
- Orientation choices involve trade-offs: orienting for minimal supports might increase build height (and time) or place critical features on upward-facing surfaces (generally better finish) versus downward-facing surfaces (poorer finish, requires supports). Critical tolerances or features often dictate the optimal orientation. Anisotropy means properties like tensile strength or fatigue life can differ depending on whether they are measured parallel or perpendicular to the build layers; orientation should align the strongest direction with the primary load paths.
Effectively applying these DfAM principles requires not only sophisticated software tools but also deep process knowledge and experience. Collaborating with an AM service provider like Met3dp early in the design phase can be highly beneficial. Our team possesses decades of collective expertise in metal additive manufacturing and can provide crucial DfAM consultation, helping defense contractors and aerospace engineers optimize their steering housing designs for successful, efficient, and high-performance additive production, leveraging the full capabilities of our advanced SEBM printers and material portfolio.
Achievable Tolerance, Surface Finish, and Dimensional Accuracy in Metal AM
While metal additive manufacturing offers unparalleled design freedom, it’s crucial for engineers and procurement managers to understand the levels of dimensional accuracy and surface finish achievable directly from the printing process, and how these compare to the stringent requirements often needed for missile components. As-printed parts typically do not match the precision of multi-axis CNC machining, necessitating a clear understanding of achievable specifications and the role of post-processing.
Typical Tolerances:
The dimensional accuracy achievable with metal AM processes like Laser Powder Bed Fusion (LPBF) and Selective Electron Beam Melting (SEBM) depends on several factors but generally falls within certain ranges:
- General Tolerances: For well-controlled industrial systems, typical achievable tolerances are often cited in the range of ±0.1 mm to ±0.2 mm (±0.004″ to ±0.008″) for smaller dimensions (e.g., up to 100 mm), plus an additional tolerance percentage for larger dimensions (e.g., ±0.1% to ±0.2% of the dimension).
- Process Differences: EBM processes, like those used by Met3dp’s SEBM printers, typically operate at higher temperatures, which helps reduce residual stress but can sometimes lead to slightly lower as-built accuracy compared to LPBF for certain geometries. However, advancements in process control are continually improving EBM accuracy.
- Factors Influencing Accuracy:
- Machine Calibration: Regular and precise calibration of the printer’s laser/electron beam scanning system is critical.
- Materialegenskaper: Thermal conductivity, expansion coefficient, and melt pool behavior of the specific alloy (e.g., IN625 vs. Ti-6Al-4V) affect solidification and potential distortion.
- Thermal Stresses: The repeated heating and cooling cycles inherent in AM induce internal stresses that can cause warping or distortion, impacting final dimensions. Process parameters, scan strategies, and support structures are optimized to mitigate this.
- Part Geometry & Size: Larger parts and complex geometries with varying thicknesses are more prone to thermal distortion.
- Efterbearbetning: Stress relief heat treatments can cause minor dimensional changes that need to be accounted for.
Surface Finish (Roughness):
The surface finish of as-printed metal AM parts is inherently rougher than machined surfaces. The roughness depends on factors like layer thickness, powder particle size, beam parameters, and surface orientation relative to the build direction.
- Typical Ra Values: As-printed surface roughness (Ra) often ranges from 6 µm to 25 µm (240 µin to 1000 µin).
- Side Walls: Generally exhibit roughness related to the layer steps.
- Upward-Facing Surfaces: Tend to be smoother as they are directly formed by the melt pool.
- Downward-Facing Surfaces (Overhangs): Tend to be the roughest due to contact with support structures or the nature of solidifying over loose powder.
- Implications: This as-printed roughness may be acceptable for non-critical surfaces but is often insufficient for sealing faces, mating surfaces, bearing interfaces, or areas requiring specific aerodynamic or fluid dynamic properties.
Met3dp’s Contribution to Accuracy and Reliability:
Achieving consistent accuracy and reliable part properties hinges on the quality of the AM system and the robustness of process controls. Met3dp prides itself on printers that deliver industry-leading print volume, accuracy, and reliability. Our systems incorporate advanced monitoring and control features to ensure stable melt pool behavior, precise energy delivery, and controlled thermal management throughout the build process. This focus on equipment quality and process stability is fundamental to producing mission-critical parts, like steering housings, that meet demanding specifications. You can explore more about our cutting-edge 3D-utskrift av metall capabilities and how they translate to superior part quality.
The Role of Post-Processing:
For features requiring tolerances tighter than ±0.1 mm or surface finishes smoother than Ra 6 µm, post-processing is essential.
- CNC Machining: Critical features, mating surfaces, bearing bores, threaded holes, and sealing grooves are typically finish-machined after the AM build and necessary heat treatments. This allows tolerances comparable to fully machined parts (e.g., ±0.01 mm to ±0.05 mm or better) to be achieved where needed.
- Ytbehandling: Various techniques like abrasive blasting, tumbling, polishing, electro-polishing, or Extrude Hone AFM (Abrasive Flow Machining) can be used to improve the overall surface finish or target specific areas, reducing Ra values significantly.
Metrology and Quality Inspection:
Verifying the dimensional accuracy and integrity of AM parts, especially critical ones, requires rigorous inspection.
- Coordinate Measuring Machines (CMM): Used for high-precision measurement of specific geometric features and tolerances.
- 3D Scanning: Techniques like structured light or laser scanning provide a comprehensive comparison of the entire part geometry against the original CAD model, identifying deviations and verifying complex shapes.
- Icke-förstörande testning (NDT): As detailed later, NDT is crucial for internal integrity checks.
In summary, while metal AM provides immense design advantages, achieving the final required precision for missile steering housings often involves a hybrid approach, combining the geometric freedom of AM with the precision of targeted post-process machining and finishing. Understanding the as-printed capabilities and planning necessary secondary operations are key aspects of successfully implementing AM for these demanding applications.
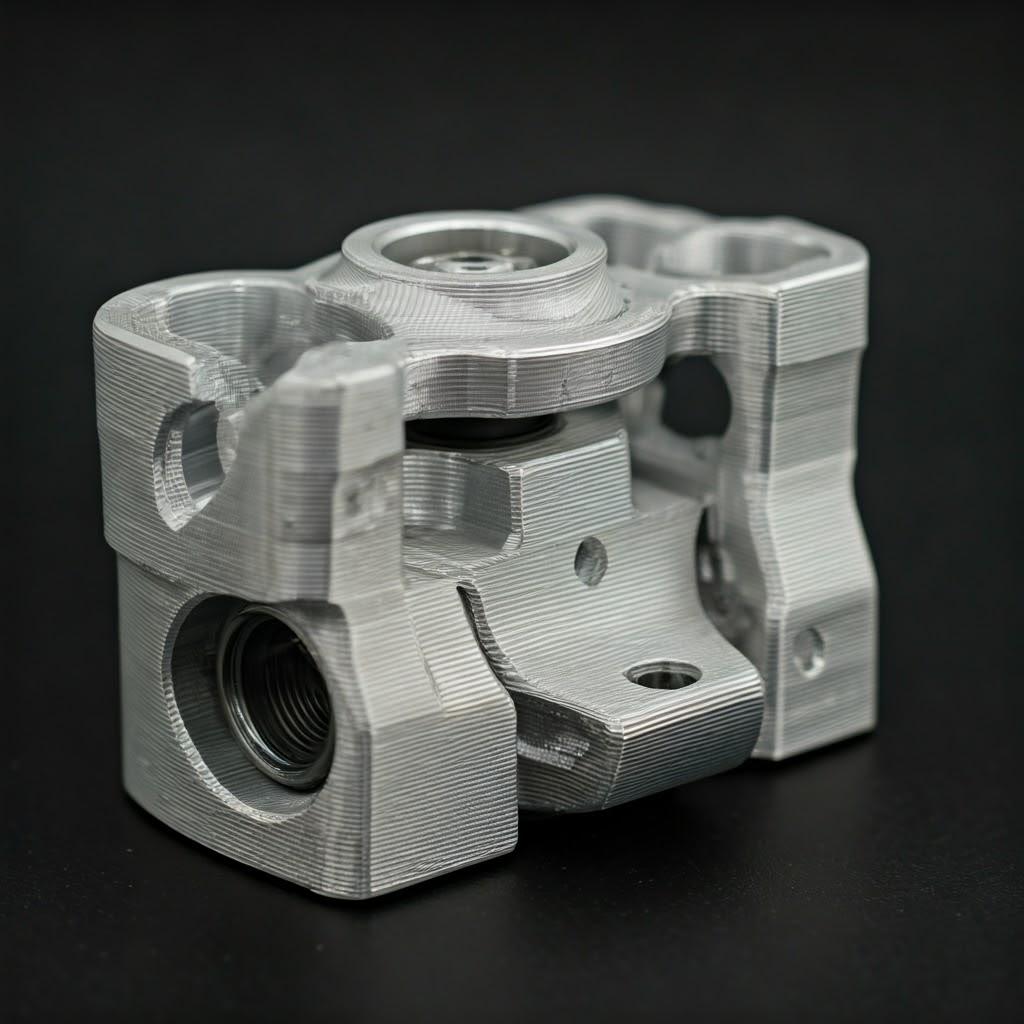
Post-Processing Requirements for Mission-Critical Housings
Producing a missile steering mechanism housing using metal additive manufacturing does not end when the printer stops. For components subjected to extreme operating conditions and requiring absolute reliability, a series of carefully controlled post-processing steps are almost always necessary. These steps are crucial for relieving internal stresses, achieving the desired material microstructure and mechanical properties, ensuring dimensional accuracy for critical features, obtaining the required surface finish, and verifying the overall integrity of the part. Skipping or improperly executing these steps can compromise the component’s performance and lead to failure. Planning for post-processing should be integral to the overall manufacturing strategy right from the design phase.
Common post-processing steps for critical AM components like steering housings include:
- Part Removal and Cleaning: Once the build cycle is complete and the chamber has cooled, the build plate with the printed housing(s) is removed. Excess powder surrounding the parts must be carefully removed and recovered (often for recycling). This can involve brushing, vacuuming, or using controlled inert gas jets, especially for complex internal channels where powder removal can be challenging.
- Stöd för borttagning: Structures printed to support overhangs and manage thermal stress must be removed. This can be done manually (using pliers, cutting tools) or through secondary processes like CNC machining or wire EDM (Electrical Discharge Machining), particularly for supports in hard-to-reach areas or made from very strong materials. The choice of support strategy during DfAM significantly impacts the ease and effectiveness of this step. Marks left by support contact points often require local finishing.
- Stress Relief / Heat Treatment: This is arguably one of the most critical post-processing steps for metal AM parts. The rapid heating and cooling cycles during layer-wise consolidation induce significant residual stresses within the material. These stresses can cause distortion (immediately or over time), reduce fatigue life, and potentially lead to cracking.
- Stressavlastning: Typically involves heating the part to a specific temperature below its critical transformation point, holding it for a defined period, and then slowly cooling it. This allows internal stresses to relax without significantly altering the microstructure. It’s often performed before removing the part from the build plate to minimize distortion during removal.
- Solution Annealing / Aging / Full Heat Treatments: Depending on the alloy (e.g., IN625, Ti-6Al-4V) and desired final properties, more comprehensive heat treatment cycles may be required to optimize the material’s microstructure, strength, ductility, and fatigue resistance. These cycles are specific to the alloy and application requirements.
- Het isostatisk pressning (HIP): This process combines high temperature and high inert gas pressure (typically Argon) to consolidate the material further. HIP is highly effective at closing internal microporosity (gas porosity or lack-of-fusion defects) that may be present after printing, significantly improving fatigue life, fracture toughness, and overall part density (approaching 100% theoretical density). For mission-critical components subjected to high cyclic loading, HIP is often mandated.
- CNC Machining: As discussed previously, AM parts often require finish machining to achieve tight tolerances on critical interfaces. This includes:
- Mating surfaces that connect to other components of the missile structure or guidance system.
- Bearing bores or mounting points for actuators and sensors.
- Sealing surfaces (e.g., O-ring grooves).
- Threading holes for fasteners. Machining strategies must account for the potentially complex geometry and workholding challenges of AM parts.
- Ytbehandling: Depending on the requirements, various surface treatments may be applied:
- Abrasive Blasting (Grit/Bead Blasting): Provides a uniform matte finish, removes minor surface imperfections, and can sometimes provide compressive residual stress benefits (shot peening).
- Tumbling/Vibratory Finishing: Can smooth surfaces and deburr edges, particularly for smaller components or batches.
- Polering: Manual or automated polishing can achieve very smooth, low Ra finishes for specific areas requiring low friction or specific reflective properties.
- Chemical Treatments/Coatings: Anodizing (for titanium), chemical conversion coatings (e.g., chromate or non-chromate alternatives for corrosion resistance), or specialized paints/coatings may be required for environmental protection or thermal control.
- Icke-förstörande testning (NDT): Given the criticality, rigorous inspection is essential to ensure the housing is free from internal defects that could compromise its integrity. Common NDT methods include:
- Computed Tomography (CT) Scanning: Provides a 3D X-ray view of the part’s internal structure, capable of detecting voids, inclusions, cracks, and verifying complex internal geometries. Often considered the gold standard for internal inspection of critical AM parts.
- X-ray Radiography: Traditional 2D X-ray inspection to detect internal flaws.
- Fluorescent Penetrant Inspection (FPI): Used to detect surface-breaking cracks or defects.
- Ultrasonic Testing (UT): Can detect subsurface flaws based on sound wave propagation.
Integrating these post-processing steps requires careful planning and coordination. The time and cost associated with these operations can be significant and must be factored into the overall production cost and lead time estimates. Working with a knowledgeable AM provider like Met3dp, who understands the intricacies of these downstream processes and can manage them effectively either in-house or through qualified partners, is crucial for delivering mission-ready components that meet all specifications.
Common Challenges in 3D Printing Steering Housings and How to Avoid Them
While metal additive manufacturing unlocks incredible potential for components like missile steering housings, the process is complex and not without its challenges. Achieving consistent, high-quality results requires careful control over design, materials, process parameters, and post-processing. Awareness of potential issues and proactive mitigation strategies are key to successfully implementing AM for such demanding applications. Here are some common challenges and how they can be addressed:
- Warping and Distortion:
- Utmaning: The significant thermal gradients generated during the layer-by-layer melting and solidification process create internal stresses. As these stresses accumulate, they can cause the part to warp or distort, pulling away from the build plate or deviating from the intended geometry. This is particularly prevalent in large parts or those with significant changes in cross-section.
- Mitigation:
- Process Simulation: Advanced simulation software can predict thermal behavior and distortion patterns, allowing for adjustments to orientation or support structures proactively.
- Optimized Part Orientation: Orienting the part to minimize large, flat surfaces parallel to the build plate and reduce residual stress accumulation in critical areas.
- Strategic Support Structures: Well-designed supports anchor the part securely to the build plate and act as heat sinks, helping to manage thermal gradients.
- Process Parameters: Fine-tuning laser/electron beam power, scan speed, and scan strategies (e.g., island scanning) can minimize localized overheating and stress buildup.
- Build Plate Heating: Maintaining an elevated temperature in the build chamber (especially common in EBM systems like Met3dp’s SEBM) significantly reduces thermal gradients and minimizes stress.
- Post-Build Stress Relief: Performing a stress relief heat treatment cycle, often while the part is still attached to the build plate, is crucial.
- Återstående stress:
- Utmaning: Even if macroscopic warping is controlled, significant residual stresses often remain within the as-built part. These stresses can reduce the component’s fatigue life, make it susceptible to stress corrosion cracking, and cause distortion during subsequent machining operations.
- Mitigation:
- Värmebehandling: Proper stress relief and annealing heat treatments are the primary methods for significantly reducing residual stresses to acceptable levels.
- Het isostatisk pressning (HIP): The high temperature involved in HIP also effectively relieves residual stress while simultaneously closing porosity.
- Processoptimering: As with warping, optimized process parameters and thermal management during the build help minimize the initial stress state.
- Porositet:
- Utmaning: Small voids or pores can form within the printed material due to trapped gas (gas porosity) or incomplete fusion between layers or scan tracks (lack-of-fusion porosity). Porosity acts as stress concentrators, significantly degrading mechanical properties, particularly fatigue strength and fracture toughness – critical factors for aerospace components.
- Mitigation:
- High-Quality Powder: Using high-purity, spherical metal powders with controlled particle size distribution and low gas content is fundamental. This is where Met3dp’s advanced powder production using Gas Atomization and PREP technologies provides a distinct advantage, ensuring optimal powder characteristics.
- Optimized Process Parameters: Developing and validating robust parameter sets (power, speed, layer thickness, hatch spacing, gas flow) specific to the material and machine ensures complete melting and fusion.
- Inert Atmosphere Control: Maintaining a high-purity inert gas atmosphere (Argon or Nitrogen) in the build chamber minimizes oxidation and gas pickup by the melt pool. EBM processes operate under high vacuum, inherently offering excellent protection against contamination.
- Het isostatisk pressning (HIP): HIP is extremely effective at closing and eliminating both gas and lack-of-fusion porosity, significantly enhancing material integrity.
- Support Removal Difficulty:
- Utmaning: Removing support structures, especially from complex internal channels or delicate features of a steering housing, can be time-consuming, costly, and risks damaging the part. Inaccessible internal supports may be impossible to remove completely.
- Mitigation:
- DfAM: Designing for minimal support requirements from the outset is the best strategy (self-supporting angles, optimizing orientation).
- Support Design: Using specialized support structures (e.g., thin-walled, easily breakable, or lattice supports) where necessary can ease removal.
- Advanced Removal Techniques: Utilizing CNC machining, wire EDM, or abrasive flow machining for support removal in challenging areas.
- Material Choice: Some materials are inherently easier or harder to remove supports from.
- Surface Finish Limitations:
- Utmaning: The as-printed surface roughness may not meet the requirements for certain functional surfaces (sealing, mating, aerodynamic). Downward-facing surfaces and areas affected by support structures typically have the poorest finish.
- Mitigation:
- Orientation Planning: Position critical surfaces optimally (e.g., upward-facing or vertical) during build planning.
- Process Parameter Tuning: Smaller layer thicknesses and optimized beam parameters can improve finish, though often at the cost of increased build time.
- Secondary Finishing Operations: Implementing appropriate post-processing steps like machining, polishing, blasting, or AFM is usually necessary to achieve demanding surface finish specifications.
- Material Property Consistency:
- Utmaning: Ensuring that the mechanical properties (strength, ductility, fatigue life) are consistent throughout the part and repeatable from build to build is critical for certification and reliability in defense applications. Variations can arise from inconsistencies in powder quality, process parameters, or thermal history.
- Mitigation:
- Rigorous Process Control: Implementing strict quality management systems covering powder handling, machine calibration, parameter validation, atmosphere control, and post-processing. Understanding the specific tryckmetoder and their control parameters is key.
- Powder Quality Management: Ensuring consistent, high-quality powder feedstock through rigorous testing and supplier qualification (or in-house production like Met3dp’s). Batch traceability is essential.
- Homogenization Heat Treatments: Appropriate heat treatments (annealing, HIP) help homogenize the microstructure and properties.
- Extensive Testing: Implementing a robust testing plan, including tensile testing, fatigue testing, and microstructural analysis on witness coupons printed alongside the parts, verifies that properties meet specifications for each build.
Addressing these challenges requires a combination of design expertise (DfAM), material science knowledge, precise process control, and diligent post-processing and quality assurance. Partnering with an experienced AM provider like Met3dp, equipped with advanced technology and a deep understanding of these potential pitfalls and their solutions, significantly de-risks the adoption of metal 3D printing for mission-critical components like missile steering mechanism housings.
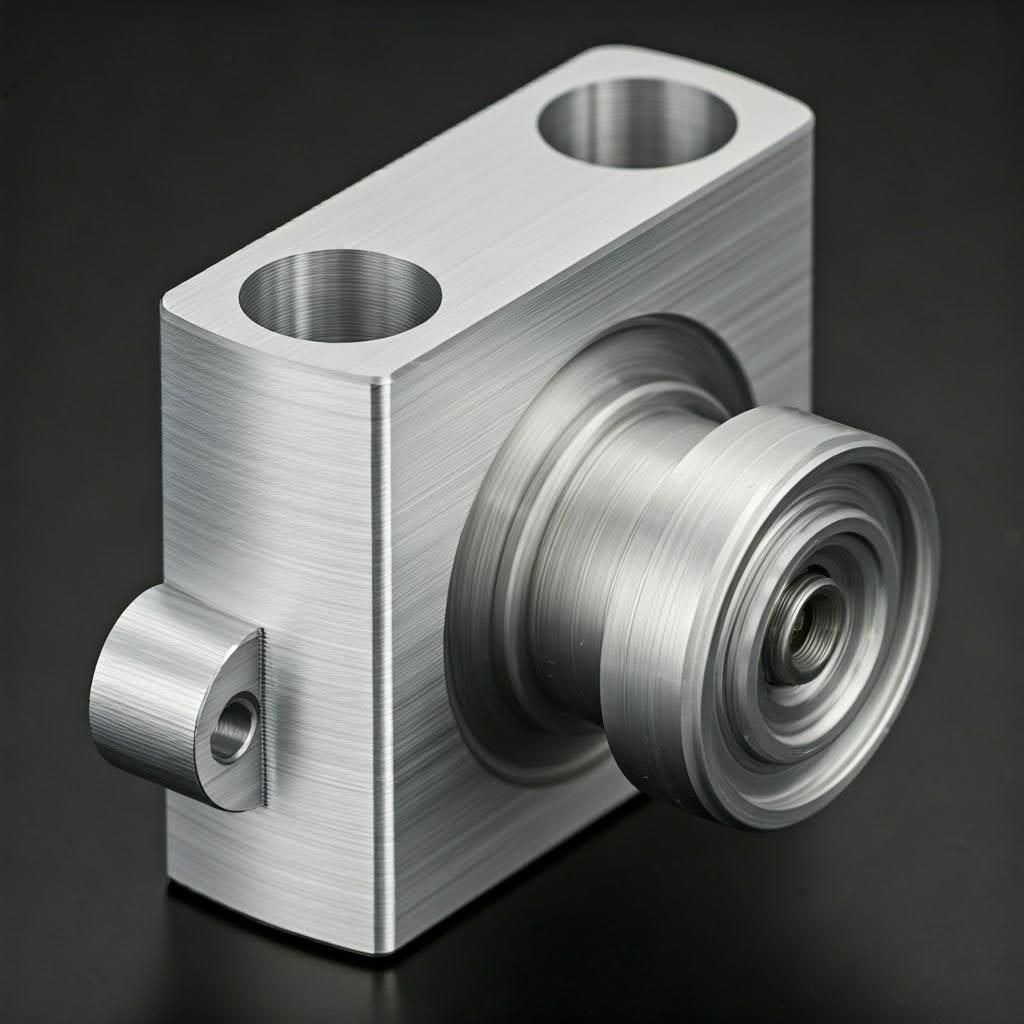
How to Choose the Right Metal 3D Printing Service Provider for Defense Components
Selecting the right manufacturing partner is always critical, but when sourcing flight-critical components like missile steering mechanism housings using advanced technologies like metal additive manufacturing, the stakes are exceptionally high. The unique complexities of AM, combined with the stringent requirements of the aerospace and defense sector, necessitate a rigorous evaluation process for potential suppliers. Choosing an unqualified or inexperienced provider can lead to project delays, cost overruns, substandard parts, and potentially catastrophic failures. Procurement managers and engineers must look beyond just price and evaluate suppliers based on a comprehensive set of technical capabilities, quality systems, and industry-specific credentials.
Here are key criteria to evaluate when selecting a metal AM service provider for defense applications:
- Industry-Specific Certifications: These demonstrate a provider’s commitment to quality and process control relevant to the sector.
- AS9100: The standardized quality management system (QMS) for the aerospace industry. Certification indicates robust processes for traceability, risk management, configuration management, and quality assurance crucial for flight hardware.
- ITAR Compliance: For projects involving U.S. defense articles or technical data, the supplier must be registered and compliant with the International Traffic in Arms Regulations to handle sensitive information and components legally and securely.
- ISO 9001: A fundamental QMS certification, indicating established processes for quality, but AS9100 is generally preferred for aerospace/defense work.
- Material Expertise and Control: The provider must have proven experience printing the specific alloys required (e.g., IN625, Ti-6Al-4V) and demonstrate control over their materials.
- Alloy Experience: Demonstrated track record with the required high-performance alloys, including established and validated process parameters.
- Powder Quality & Traceability: Access to high-quality, aerospace-grade metal powders with documented chemistry and characteristics. Robust procedures for powder handling, storage, testing, and batch traceability are essential. Providers like Met3dp, who manufacture their own high-performance powders using advanced Gas Atomization and PREP technologies, offer a significant advantage in controlling and verifying powder quality from the source.
- Utveckling av material: Capability to work with specialized or custom alloys if required.
- Equipment Capabilities and Technology: The provider should utilize industrial-grade AM systems suitable for producing high-quality, consistent parts.
- Printer Technology: Appropriate technology (e.g., LPBF, SEBM) for the material and application. Met3dp’s focus on advanced systems, including SEBM technology known for producing low-stress parts in materials like Ti-6Al-4V, ensures access to state-of-the-art capabilities.
- Byggvolym: Sufficient build chamber size to accommodate the housing dimensions.
- Accuracy & Reliability: Proven machine accuracy and repeatability, backed by calibration records and process monitoring data. Met3dp printers are designed for industry-leading accuracy and reliability.
- Process Monitoring: In-situ monitoring capabilities (e.g., melt pool monitoring, thermal imaging) can provide valuable data for quality assurance.
- Technical Expertise and Support: The supplier should function as a partner, offering technical guidance beyond just printing.
- DfAM Support: Experienced engineers who can assist with optimizing the housing design for additive manufacturing, minimizing risks and maximizing performance.
- Process Engineering: Deep understanding of process parameters and their impact on material properties and part quality.
- Metallurgical Knowledge: Expertise in materials science, heat treatment, and failure analysis relevant to the chosen alloys and application.
- Comprehensive Post-Processing Capabilities: As discussed, post-processing is critical. The ideal provider should have robust capabilities, either in-house or through a tightly managed network of qualified partners.
- Värmebehandling: Controlled furnaces with proper calibration and atmosphere control for stress relief, annealing, HIP.
- Precision Machining: Multi-axis CNC capabilities for achieving tight tolerances on critical features.
- Ytbehandling: Various methods to meet specified roughness or treatment requirements.
- NDT & Inspection: Certified NDT capabilities (CT scanning, X-ray, FPI) and advanced metrology equipment (CMM, 3D scanners).
- Robust Quality Management System (QMS): Beyond certifications, the QMS should be demonstrably effective.
- Processtyrning: Standardized operating procedures for all manufacturing stages.
- Inspection & Testing: Clear protocols for dimensional inspection, material testing (e.g., witness coupons), and NDT.
- Traceability: Full traceability of materials, process data, and inspection results for each part.
- Configuration Management: Processes to control design revisions and ensure the correct version is manufactured.
- Lead Time, Responsiveness, and Capacity: The provider must demonstrate the ability to meet project timelines and communicate effectively. Evaluate their current workload, machine availability, and project management approach.
- Security and Confidentiality: Especially crucial for defense projects. The provider must have secure facilities and IT systems, along with procedures to protect sensitive design data and intellectual property, adhering to requirements like CMMC (Cybersecurity Maturity Model Certification) if applicable.
Questions Procurement Managers Should Ask:
- Can you provide evidence of your AS9100 certification and ITAR registration (if applicable)?
- Describe your experience printing [specific alloy, e.g., Ti-6Al-4V ELI] for aerospace/defense applications.
- How do you control and validate the quality of your incoming metal powders? Do you manufacture your own, like Met3dp?
- What AM systems would you use for this project, and what process monitoring is employed?
- Can your team provide DfAM consultation for our steering housing design?
- Detail your in-house and outsourced post-processing capabilities (heat treatment, machining, NDT). How do you qualify external partners?
- Walk us through your quality assurance process, from order receipt to final inspection and shipment. How is traceability maintained?
- What are your procedures for handling sensitive/export-controlled data?
- What is your typical lead time for a part of this complexity and material?
Choosing the right supplier is a critical risk mitigation step. A thorough evaluation based on these criteria will help ensure that your missile steering housings are manufactured to the highest standards of quality, reliability, and performance. Exploring potential partners, including learning more om oss at Met3dp, provides insight into the capabilities and commitment required for success in this demanding field.
Cost Factors and Lead Time for Additively Manufactured Steering Housings
Understanding the cost structure and typical lead times associated with producing missile steering mechanism housings via metal additive manufacturing is crucial for budgeting, project planning, and managing expectations within B2B procurement cycles. While AM can offer cost savings compared to traditional methods, particularly for complex, low-volume parts, it’s essential to recognize the various factors that influence the final price and delivery schedule.
Key Cost Factors:
- Materialkostnad:
- Powder Type: High-performance alloys like aerospace-grade IN625 and Ti-6Al-4V ELI are inherently expensive raw materials. The cost per kilogram can vary significantly.
- Part Volume & Weight: The amount of powder consumed directly impacts cost. Larger or denser parts require more material. DfAM techniques like topology optimization are key to minimizing material usage.
- Support Structure Volume: Material used for supports also adds to the cost, reinforcing the need for support minimization during design.
- Återvinning av pulver: Efficient powder recovery and recycling processes employed by the service provider can help mitigate raw material costs over time, although stringent quality control on recycled powder is necessary for critical applications.
- Maskintid:
- Byggtid: This is often a primary cost driver. It’s determined by the part’s volume (total height and cross-sectional area per layer), complexity, the number of parts nested on a build plate, and the specific process parameters (layer thickness, scan speed). Larger and more complex housings naturally take longer to print.
- Machine Depreciation & Operational Costs: The hourly rate charged for machine time reflects the high capital investment in industrial metal AM systems, maintenance, energy consumption, inert gas usage, and facility overheads.
- Kostnader för arbetskraft:
- Design & Preparation (NRE): Non-recurring engineering costs associated with DfAM consultation, build preparation (orientation, support generation, slicing), and process simulation can be significant, especially for initial runs.
- Machine Setup & Operation: Skilled technicians are required to prepare the machine, load powder, oversee the build, and remove parts.
- Post-Processing Labor: Manual tasks like powder removal, support removal, basic finishing, inspection, and packaging contribute to the overall cost.
- Post-Processing Complexity & Costs:
- Värmebehandling: Costs vary depending on the cycle complexity (simple stress relief vs. full anneal + age vs. HIP), furnace time, and whether HIP is required (HIP is a relatively expensive batch process).
- Maskinbearbetning: The extent of required CNC machining (number of features, tolerance requirements, setup complexity) significantly impacts cost. Machining AM parts can sometimes be more challenging than machining wrought materials due to geometry or hardness.
- Surface Finishing & Coating: Costs depend on the specific processes employed (blasting, polishing, anodizing, painting) and the surface area treated.
- NDT & Inspection: Rigorous inspection using CT scanning, CMM, etc., adds cost based on the level of inspection required and the time involved.
- Quality Assurance & Testing: Costs associated with implementing and maintaining a robust QMS, material testing (e.g., analyzing witness coupons from each build), documentation, and certification requirements.
Factors Influencing Lead Time:
- Part Complexity and Size: Larger volume and more intricate geometries directly translate to longer print times.
- Print Time & Machine Availability: The actual time spent printing the part(s) is often the longest single step. Supplier machine availability and scheduling queues heavily influence the start time.
- Number of Post-Processing Steps: Each required step (stress relief, HIP, machining, finishing, inspection) adds sequential time to the overall workflow. Some steps, like HIP, often involve batching and have their own scheduling lead times.
- Quantity Ordered: While AM setup times are low compared to tooling-based methods, printing larger quantities still takes proportionally longer. Post-processing may also become a bottleneck for larger batches.
- Supplier Capacity and Backlog: The chosen provider’s current workload and overall capacity will impact how quickly they can start and complete a project.
- Initial Setup & Qualification: For first-time production of a critical part, additional time may be needed for DfAM iterations, process validation, and first article inspection (FAI).
Managing Expectations (B2B):
For procurement managers, it’s important to understand that while AM excels at snabb prototyptillverkning, den produktionsledtid for qualified, mission-critical metal parts involving extensive post-processing can still be substantial – potentially weeks or even months, depending on the factors above. However, this may still be significantly faster than the months or even years required for traditional casting tooling development and qualification.
Met3dp Value Proposition: By integrating advanced, reliable printing systems with in-house expertise in materials (including powder production) and process optimization, Met3dp aims to provide competitive value. Our focus on efficiency, process control, and comprehensive solutions helps streamline the manufacturing workflow, manage costs effectively, and provide realistic, reliable lead time estimates for our B2B clients in demanding sectors like aerospace and defense.
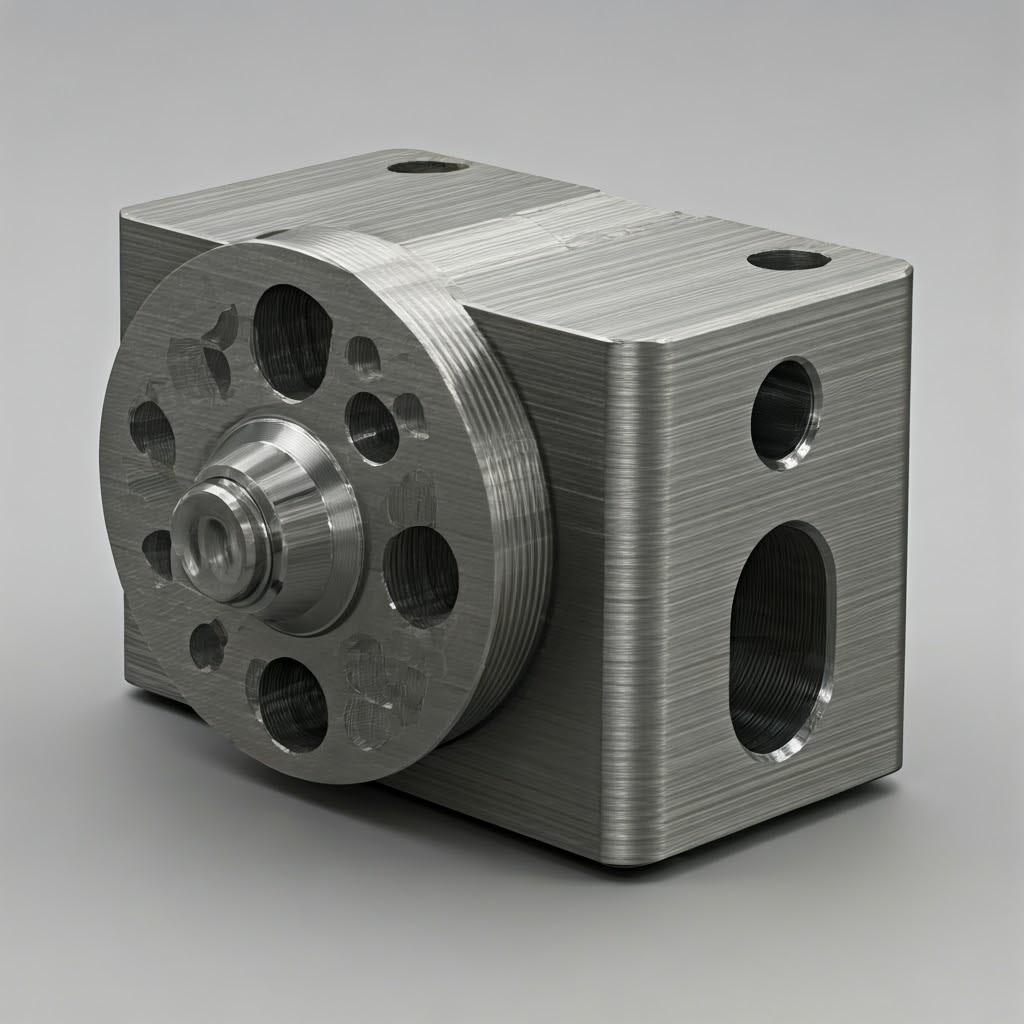
Vanliga frågor och svar (FAQ)
Q1: What level of detail and complexity can be achieved for internal features in a missile steering housing using metal AM?
A1: Metal AM excels at creating highly complex internal geometries that are often impossible with traditional methods. Features like conformal cooling channels following component contours, intricate lattice structures for weight reduction, integrated wiring pathways, and complex internal mounting bosses can be readily produced. The minimum feature size and wall thickness depend on the specific AM process (LPBF/SEBM), machine resolution, and material, but are typically in the range of 0.3 mm to 1.0 mm. Careful DfAM is required to ensure internal powder removal is possible and that features are self-supporting or adequately supported during the build.
Q2: How does the cost of metal 3D printing a steering housing compare to traditional CNC machining from billet?
A2: The cost comparison depends heavily on part complexity and production volume. * For highly complex geometries: AM is often more cost-effective, especially at low-to-medium volumes, because it avoids the exponential increase in machining time and potential for significant material waste associated with complex CNC paths from expensive billets (poor buy-to-fly ratio). * For simpler geometries: Traditional CNC machining may remain more cost-effective, particularly at higher volumes where machining processes are highly optimized and material waste is less of a factor. * Delkonsolidering: If AM allows multiple machined parts to be consolidated into one printed component, the savings in assembly labor and reduced part count can significantly favor AM, even if the printing cost itself is comparable. A detailed cost analysis considering design complexity, material, volume, buy-to-fly ratio, and post-processing is needed for a specific case.
Q3: What quality control measures are essential when sourcing 3D printed missile components?
A3: Essential QC measures for critical 3D printed missile parts include: * Powder Control: Strict control and testing of incoming powder chemistry, particle size distribution, morphology, and flowability; rigorous management of recycled powder. * Process Monitoring & Control: Real-time monitoring (where available) and tight control over critical process parameters (e.g., beam power, speed, layer thickness, chamber atmosphere/vacuum). * Witness Coupons: Printing standardized test specimens alongside the actual parts in each build for destructive testing (tensile, fatigue, density, microstructure analysis) to verify material properties. * Dimensionell inspektion: Using CMM and/or 3D scanning to verify conformance to drawing tolerances. * Icke-förstörande testning (NDT): CT scanning is highly recommended for detecting internal defects (porosity, inclusions, cracks) and verifying internal geometries. FPI for surface defects may also be required. * Traceability: Comprehensive documentation linking powder batches, process data, NDT results, and dimensional reports to each specific part serial number. * Supplier Audits & Certifications: Ensuring the supplier holds relevant certifications (e.g., AS9100) and undergoes regular audits.
Q4: Can existing housing designs originally made for machining or casting be directly printed, or do they need modification for AM?
A4: Directly printing a design optimized for traditional manufacturing is generally not recommended and often fails to leverage AM’s benefits or account for its constraints. Existing designs should undergo a DfAM review and likely modification. This involves optimizing for printability (reducing supports, ensuring minimum feature sizes), potentially applying topology optimization for weight reduction, consolidating parts if applicable, and adding features only possible with AM (like internal channels). Attempting a direct print often results in excessive support needs, longer print times, higher costs, and potentially suboptimal performance compared to a redesigned AM-native part.
Q5: What is the typical turnaround time for prototyping vs. production runs of these components using metal AM?
A5: Turnaround times vary significantly based on complexity, size, material, quantity, post-processing, and supplier capacity. * Prototyping: For a single, relatively complex housing prototype requiring basic stress relief and minimal machining, lead times might range from 1-4 weeks, focusing on rapid iteration. * Production Runs (Qualified Parts): For low-volume production runs requiring full heat treatment (including potential HIP cycles), extensive machining, rigorous NDT, surface finishing, and full documentation/certification, lead times are typically much longer, potentially ranging from 6-16 weeks or more. The extensive post-processing and quality assurance steps required for flight-qualified hardware add substantially to the overall timeline compared to simple prototypes.
Conclusion: Advancing Missile Technology with Precision Metal AM
The relentless pursuit of higher performance, increased reliability, and greater efficiency in missile technology demands continuous innovation in design and manufacturing. As we’ve explored, the missile steering mechanism housing, a component critical to guidance accuracy and mission success, stands to benefit immensely from the capabilities of Additiv tillverkning av metall. By transcending the limitations of traditional manufacturing, metal AM empowers engineers to create housings that are lighter, more complex, and potentially offer enhanced thermal management and structural integrity.
The ability to leverage topologioptimering och generative design allows for significant weight reduction without compromising strength – a crucial advantage in aerospace applications. The freedom to design intricate interna kanaler and consolidate multiple components into a single printed part simplifies assembly, reduces potential failure points, and unlocks new functional possibilities. Utilizing high-performance alloys like the robust, high-temperature resistant IN625 or the lightweight, high-strength Ti-6Al-4V ensures that these advantages are built upon a foundation of proven material performance capable of withstanding extreme operational environments.
However, realizing the full potential of metal AM for such critical applications requires more than just access to a printer. It demands a deep understanding of Design för additiv tillverkning (DfAM) principles, meticulous control over the printing process, rigorous efterbearbetning (including heat treatment, HIP, machining, and NDT), and unwavering commitment to kvalitetssäkring. Common challenges like warping, residual stress, and porosity must be proactively managed through expertise and advanced technology.
This underscores the critical importance of selecting the right manufacturing partner. A provider like Met3dp brings together the essential elements for success:
- Industry-leading AM systems designed for accuracy and reliability.
- Metallpulver av hög kvalitet, produced in-house using advanced Gas Atomization and PREP technologies, ensuring optimal material characteristics for demanding applications.
- Decades of collective expertise in metal AM, materials science, and application development across critical industries.
- Heltäckande lösningar spanning equipment, materials, and expert support to navigate the complexities of producing mission-critical components.
Metal additive manufacturing is no longer a future concept; it is a present-day reality enabling next-generation aerospace and defense systems. For engineers and procurement managers seeking to push the boundaries of missile performance and reliability, metal AM offers a powerful pathway. By partnering with a knowledgeable and capable provider, the intricate challenges of manufacturing precision steering mechanism housings can be transformed into opportunities for innovation and enhanced mission capability.
Ready to explore how Metal Additive Manufacturing can elevate your aerospace and defense components? Contact Met3dp today to discuss your specific requirements and learn how our cutting-edge systems, advanced materials, and expert support can power your organization’s additive manufacturing goals. Visit our website at https://met3dp.com/ to learn more.
Dela på
MET3DP Technology Co, LTD är en ledande leverantör av lösningar för additiv tillverkning med huvudkontor i Qingdao, Kina. Vårt företag är specialiserat på 3D-utskriftsutrustning och högpresterande metallpulver för industriella tillämpningar.
Förfrågan för att få bästa pris och anpassad lösning för ditt företag!
Relaterade artiklar
Om Met3DP
Senaste uppdateringen
Vår produkt
KONTAKTA OSS
Har du några frågor? Skicka oss meddelande nu! Vi kommer att betjäna din begäran med ett helt team efter att ha fått ditt meddelande.
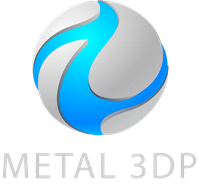
Metallpulver för 3D-printing och additiv tillverkning