3D Printed Surgical Clamps with Stainless Steel
Innehållsförteckning
Inledning
In the demanding world of surgical instruments, precision, reliability, and biocompatibility are paramount. Traditional manufacturing methods for surgical clamps often involve complex machining processes, leading to longer lead times and potential limitations in design complexity. Enter metal 3D printing, a transformative technology that is revolutionizing the way these critical medical devices are conceived and produced. This blog post explores the significant advantages of utilizing metal additive manufacturing, specifically with materials like 316L stainless steel and Ti-6Al-4V titanium alloy, for the creation of high-performance surgical clamps. For businesses in the medical device industry, including wholesale buyers and suppliers, understanding the capabilities of metal 3D printing opens doors to innovation, improved functionality, and streamlined supply chains. At Metall3DP, we are at the forefront of this revolution, providing advanced 3D printing equipment and high-quality metal powders to empower the next generation of medical device manufacturing.
What are 3D Printed Surgical Clamps?
3D printed surgical clamps are medical instruments designed to grasp, hold, and manipulate tissues, vessels, or other structures during surgical procedures, manufactured using metal additive manufacturing techniques. Unlike conventionally manufactured clamps that are typically produced through subtractive methods like machining or casting, 3D printing builds the clamp layer by layer from a digital design. This process offers unparalleled design freedom, allowing for the creation of intricate geometries and customized features that were previously difficult or impossible to achieve.
These 3D printed clamps can be tailored for specific surgical applications, potentially incorporating features such as:
- Ergonomic handles: Optimized for surgeon comfort and grip.
- Specialized jaw designs: Featuring unique textures or profiles for enhanced tissue manipulation and reduced slippage.
- Integrated features: Such as locking mechanisms or sensors, directly incorporated during the printing process.
- Patient-specific customization: Adapting the clamp’s size and shape to individual patient anatomy for improved surgical outcomes.
The versatility of metal 3D printing allows for the production of a wide range of surgical clamp types, including:
- Hemostatic clamps: Used to control blood flow.
- Tissue grasping forceps: Designed for manipulating tissues.
- Retractors: Employed to hold tissues or organs out of the surgical field.
- Specialty clamps: Tailored for specific surgical disciplines like cardiovascular or neurosurgery.
As a leading provider of additive manufacturing solutions, Metal3DP Technology Co., LTD offers the expertise and technology to produce these advanced surgical instruments, catering to the stringent demands of the medical industry.
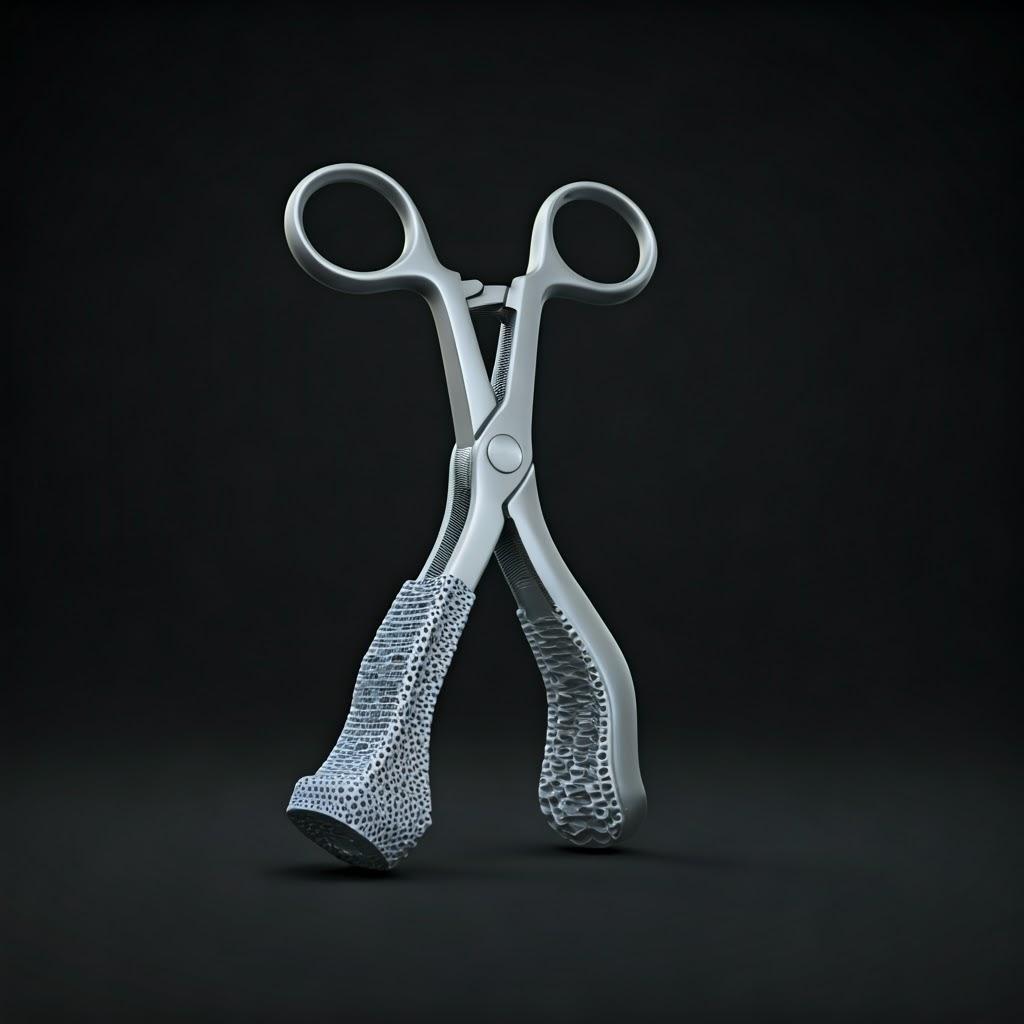
Why Choose Metal 3D Printing for Surgical Clamps?
Adopting metal 3D printing for the manufacturing of surgical clamps offers a multitude of compelling advantages over traditional methods, making it an increasingly attractive option for medical device manufacturers, wholesale buyers, and suppliers. These benefits include:
- Designfrihet och komplexitet: Metal 3D printing enables the creation of intricate geometries and internal features that are difficult or impossible to achieve with conventional manufacturing. This allows for the optimization of clamp design for specific surgical tasks, potentially improving functionality and reducing invasiveness. For example, internal cooling channels or lattice structures for weight reduction can be easily integrated.
- Snabb prototypframtagning och iteration: The ability to quickly produce prototypes allows for rapid design iteration and testing. This accelerates the development cycle, enabling faster time-to-market for new and improved surgical instruments. Metal 3D printing services offered by companies like Metal3DP can significantly shorten this phase.
- Customization and Patient-Specific Solutions: 3D printing facilitates the production of surgical clamps tailored to individual patient anatomy or specific surgical requirements. This level of customization can lead to improved surgical precision and patient outcomes.
- Materialeffektivitet: Additive manufacturing processes can significantly reduce material waste compared to subtractive methods, as material is only deposited where needed. This can lead to cost savings, especially when working with expensive materials like titanium alloys.
- On-Demand Manufacturing and Reduced Inventory: 3D printing allows for on-demand production, eliminating the need for large inventories and reducing the risks associated with obsolescence. This agile manufacturing approach aligns well with the dynamic needs of the healthcare industry.
- Förbättrad funktionalitet: Integration of features like textured surfaces for better grip, internal channels for irrigation, or complex locking mechanisms can be directly incorporated during the printing process, enhancing the functionality of the surgical clamps.
- Lättvikt: Using advanced design techniques and materials like Ti-6Al-4V, 3D printing can produce lighter surgical clamps without compromising strength, potentially reducing surgeon fatigue during long procedures.
Recommended Materials for 3D Printed Surgical Clamps
The choice of material is critical for surgical clamps, as they must meet stringent requirements for biocompatibility, sterilizability, strength, and corrosion resistance. Metal 3D printing offers a range of high-performance materials suitable for these demanding applications. Two prominent materials recommended for 3D printed surgical clamps are 316L stainless steel and Ti-6Al-4V titanium alloy. Metal3DP tillverkar ett brett sortiment av högkvalitativa metallpulver optimized for additive manufacturing, including these essential materials.
316L rostfritt stål:
- Egenskaper: 316L is an austenitic stainless steel known for its excellent corrosion resistance, biocompatibility, and good mechanical properties. The “L” designation indicates low carbon content, which further enhances its resistance to sensitization (formation of chromium carbides at grain boundaries, leading to corrosion).
- Advantages in Surgical Clamps:
- Biokompatibilitet: Well-established biocompatibility makes it suitable for medical devices that come into contact with the human body.
- Sterilizability: Can withstand various sterilization methods, including autoclaving.
- Styrka och hållbarhet: Offers sufficient strength and toughness for most surgical applications.
- Kostnadseffektivt: Generally more cost-effective than titanium alloys.
- Applikationer: Widely used for various surgical instruments, including hemostatic clamps, tissue forceps, and retractors.
Ti-6Al-4V Titanium Alloy:
- Egenskaper: Ti-6Al-4V is a widely used titanium alloy known for its exceptional strength-to-weight ratio, excellent corrosion resistance, and high biocompatibility. It comprises approximately 6% aluminum and 4% vanadium.
- Advantages in Surgical Clamps:
- Högt förhållande mellan styrka och vikt: Results in lightweight yet strong instruments, reducing surgeon fatigue.
- Superior Biocompatibility: Exhibits excellent tissue compatibility and osseointegration properties.
- Utmärkt korrosionsbeständighet: Provides long-term reliability in the demanding surgical environment.
- Icke-magnetisk: Important for procedures involving sensitive electronic equipment.
- Applikationer: Ideal for surgical clamps requiring high strength and low weight, such as specialized retractors and certain types of grasping forceps.
The selection between 316L and Ti-6Al-4V depends on the specific requirements of the surgical clamp, including the intended application, mechanical load, weight considerations, and budget. Metal3DP’s advanced powder making system ensures the production of high-quality spherical powders of both 316L and Ti-6Al-4V, optimized for consistent and reliable 3D printing outcomes.
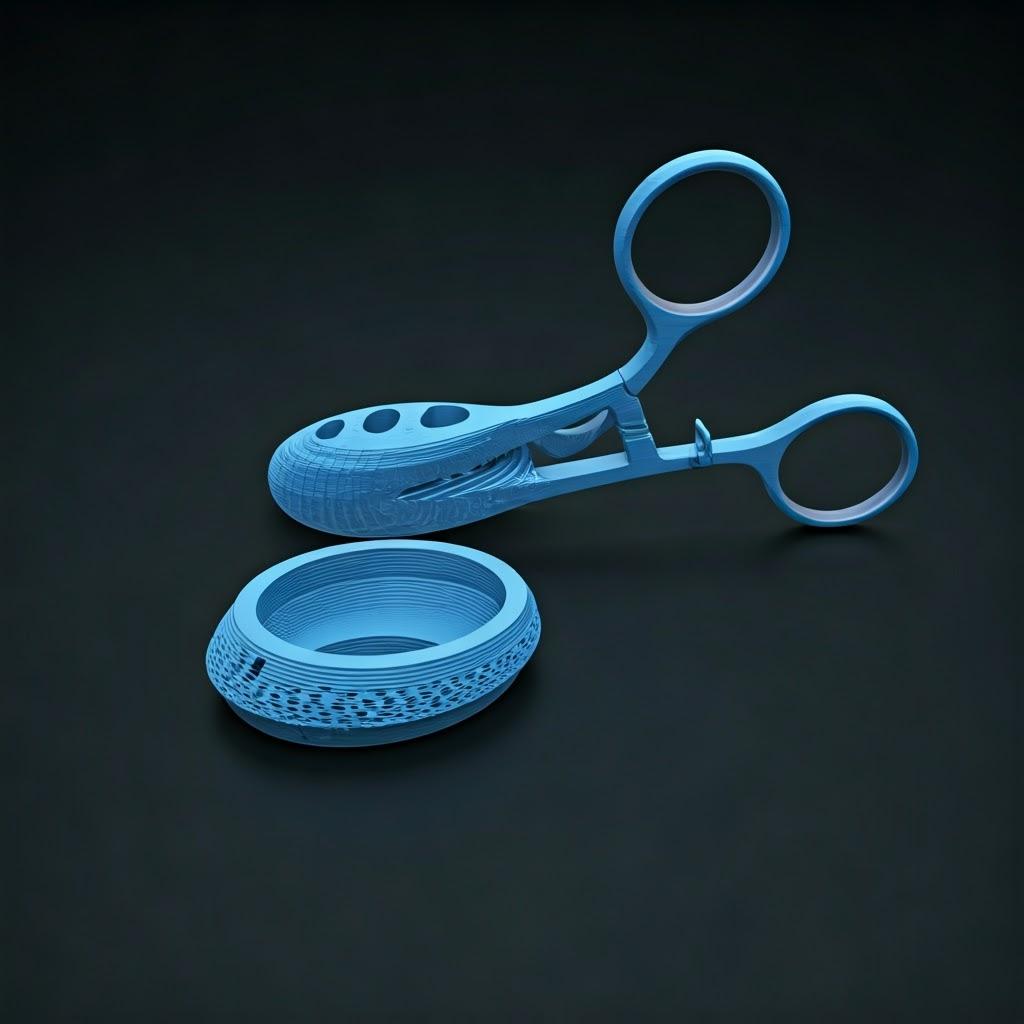
Design Optimization for Metal 3D Printed Surgical Clamps
Optimizing the design of surgical clamps for metal 3D printing is crucial to fully leverage the capabilities of additive manufacturing and achieve the desired functional and performance characteristics. Unlike traditional manufacturing methods with their inherent design constraints, 3D printing offers a high degree of freedom, allowing engineers to create innovative and efficient clamp designs. Here are some key considerations for design optimization:
- Topology Optimization: This computational technique can be employed to identify the most efficient material distribution for a given set of loads and constraints. By removing unnecessary material, it’s possible to create lighter clamps with equivalent or even enhanced strength. This is particularly beneficial for reducing surgeon fatigue during lengthy procedures.
- Gitterstrukturer: Incorporating lattice structures within the clamp body can significantly reduce weight without sacrificing structural integrity. These intricate internal networks can be tailored to provide specific stiffness or energy absorption properties.
- Ergonomics and Handling: Design should prioritize surgeon comfort and ease of use. This includes optimizing handle shapes, incorporating textured grips for secure handling, and ensuring a balanced weight distribution.
- Integration of Features: 3D printing allows for the direct integration of features such as locking mechanisms, ratchets, or even sensors into the clamp design. This can simplify assembly, improve functionality, and potentially reduce the overall size of the instrument.
- Minimizing Support Structures: While support structures are often necessary during metal 3D printing to prevent collapse or distortion, their design and placement should be carefully considered to minimize post-processing effort and ensure optimal surface finish. Design features like self-supporting angles and strategic part orientation can help reduce the need for extensive supports.
- Channeling and Fluidics: For specialized clamps requiring irrigation or suction, internal channels can be designed and printed directly within the instrument. This eliminates the need for separate tubing and simplifies the overall design.
- Surface Texture Optimization: The surface texture of the clamp jaws can be tailored to enhance grip on specific tissues or vessels. This can be achieved through strategically designed surface patterns at the CAD level.
By considering these design optimization principles, medical device manufacturers can create 3D printed surgical clamps that offer superior performance, enhanced functionality, and improved ergonomics. Metal3DP’s expertise in application development services can assist organizations in optimizing their designs for metal additive manufacturing.
Achieving Precision: Tolerance, Surface Finish, and Dimensional Accuracy
In the realm of surgical instruments, precision is non-negotiable. Metal 3D printing has advanced significantly in its ability to produce parts with tight tolerances, good surface finishes, and high dimensional accuracy. However, understanding the factors that influence these aspects is crucial for achieving the desired results in 3D printed surgical clamps.
- Tolerance: Tolerance refers to the allowable variation in a specified dimension. Metal 3D printing processes, particularly Powder Bed Fusion (PBF) technologies like Selective Laser Melting (SLM) and Electron Beam Melting (EBM) offered by Metal3DP’s industry-leading printers, can achieve tolerances in the range of ±0.05 mm to ±0.1 mm, depending on the material, part geometry, and process parameters. Critical dimensions may require post-processing, such as CNC machining, to achieve tighter tolerances.
- Ytfinish: The surface finish of a 3D printed part is influenced by the powder particle size, laser/electron beam parameters, and layer thickness. Typically, as-printed metal parts have a surface roughness that may require post-processing to meet the requirements for surgical instruments. Techniques like polishing, bead blasting, and electrochemical polishing can be employed to achieve smoother surfaces, which are important for hygiene and reducing tissue adhesion.
- Dimensionell noggrannhet: Dimensional accuracy refers to how closely the printed part matches the intended CAD model. Factors affecting dimensional accuracy include material shrinkage during solidification, thermal gradients, and calibration of the 3D printer. Careful process control, optimized build parameters, and appropriate support structure design are essential for achieving high dimensional accuracy.
Factors Influencing Precision:
Faktor | Beskrivning | Impact on Precision |
---|---|---|
Utskriftsteknik | SLM and EBM generally offer higher precision compared to Binder Jetting or Directed Energy Deposition for intricate parts. | Higher precision with PBF technologies. |
Material | Different metal powders exhibit varying shrinkage rates and thermal behavior, affecting final dimensions. | Material-specific adjustments to process parameters are necessary. |
Build Orientation | The orientation of the part on the build platform can influence dimensional accuracy and surface finish on different surfaces. | Strategic orientation can minimize support needs and improve critical surface quality. |
Processparametrar | Laser power, scan speed, layer thickness, and powder bed temperature significantly impact the melting and solidification process. | Optimized parameters are crucial for minimizing errors and achieving desired properties. |
Efterbearbetning | Techniques like CNC machining, grinding, and polishing can significantly improve tolerance and surface finish. | Essential for achieving stringent requirements for surgical instruments. |
Export to Sheets
Understanding these factors and leveraging the advanced capabilities of metal 3D printing technologies offered by Metall3DP are key to producing surgical clamps with the required precision and quality.
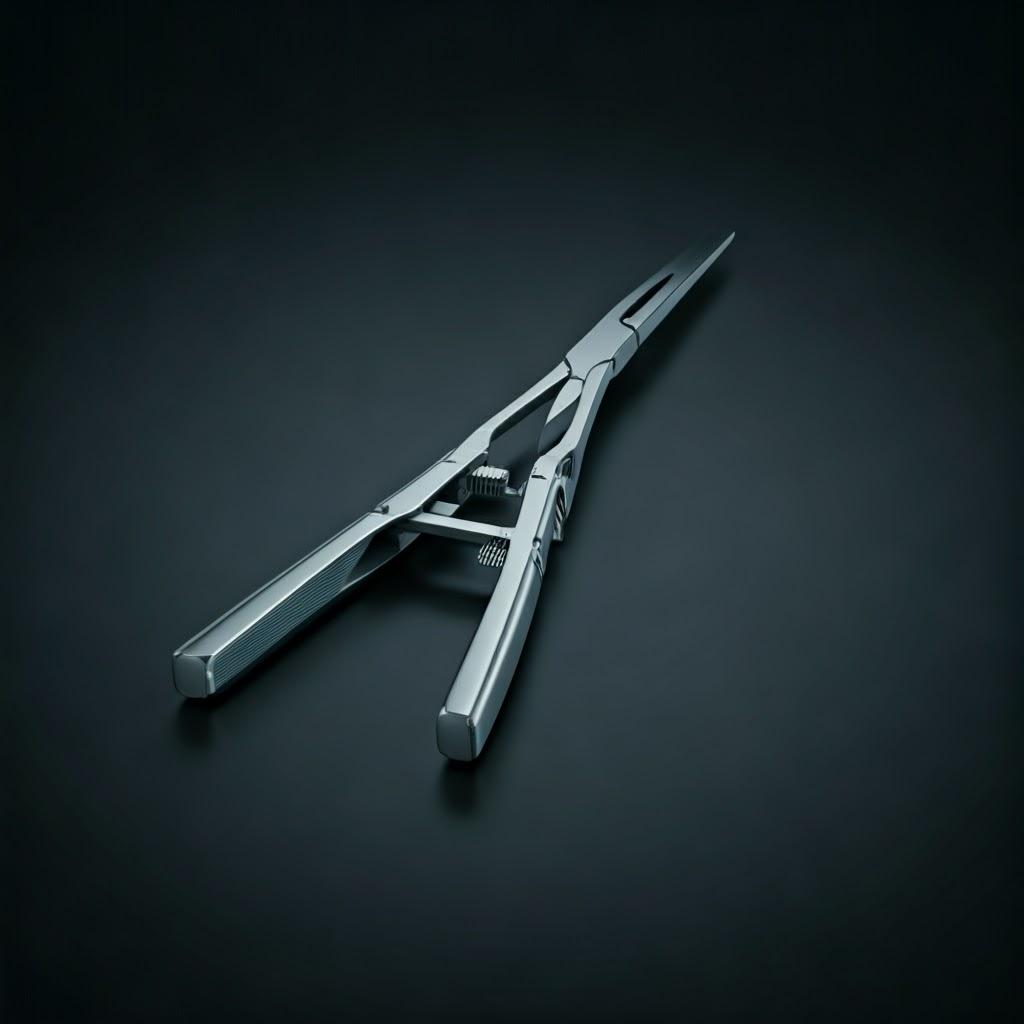
Post-Processing of 3D Printed Surgical Clamps
While metal 3D printing offers significant advantages in creating complex geometries, post-processing steps are often necessary to achieve the final functional and aesthetic requirements for surgical clamps. These steps can include:
- Stöd för borttagning: Metal 3D printed parts typically require support structures to prevent deformation during the printing process. These supports need to be carefully removed, often using specialized tools or machining techniques. The design of the supports and the part orientation can significantly impact the ease of removal and the surface finish of the supported areas.
- Värmebehandling: To relieve internal stresses developed during the rapid heating and cooling cycles of the 3D printing process and to achieve the desired mechanical properties (e.g., hardness, tensile strength), heat treatment is often required. The specific heat treatment cycle depends on the material and the intended application.
- Ytbehandling: As-printed metal surfaces can be rough and may not meet the hygienic or aesthetic requirements for surgical instruments. Various surface finishing techniques can be employed:
- Media Blasting: Using abrasive media to remove surface oxides and improve surface uniformity.
- Polering: Mechanical or chemical polishing to achieve a smooth, reflective surface, which is important for cleanability and reducing tissue adhesion.
- Electropolishing: An electrochemical process that smooths the surface and enhances corrosion resistance, particularly beneficial for stainless steel components.
- CNC Machining: For critical features requiring very tight tolerances or specific surface finishes, CNC machining can be used as a secondary process. This can include machining of threads, precise mating surfaces, or fine details.
- Cleaning and Sterilization Preparation: Thorough cleaning is essential to remove any residual powder or processing agents. The clamps must also be prepared for sterilization, which may involve passivation for stainless steel to enhance corrosion resistance.
- Ytbeläggning (tillval): In some cases, coatings may be applied to enhance biocompatibility, wear resistance, or provide specific surface properties.
The specific post-processing steps required will depend on the material, the 3D printing process used, and the final application of the surgical clamp. Medical device manufacturers must establish robust post-processing protocols to ensure the safety and efficacy of their 3D printed instruments. Metal3DP’s comprehensive solutions encompass not only advanced printing equipment and materials but also expertise in post-processing considerations.
Overcoming Challenges in 3D Printing Surgical Clamps
While metal 3D printing offers numerous benefits, there are also potential challenges that need to be addressed to ensure the successful production of high-quality surgical clamps:
- Warping and Distortion: Thermal stresses during the printing process can lead to warping or distortion of the part, especially for complex geometries or large parts. Optimized build parameters, support structure design, and stress-relieving heat treatments are crucial for mitigating these issues.
- Porositet: Internal voids or porosity can compromise the mechanical strength and fatigue resistance of the printed part. Careful selection of process parameters, high-quality metal powders from reputable suppliers like Metall3DP, and optimized powder bed preparation are essential to minimize porosity.
- Ytjämnhet: Achieving a smooth surface finish directly from the 3D printing process can be challenging. As discussed earlier, post-processing techniques are often required to meet the stringent surface requirements for surgical instruments.
- Borttagning av stödstruktur: Removing support structures can be time-consuming and may leave surface marks. Designing self-supporting geometries and optimizing support placement can help minimize these issues.
- Material Property Consistency: Ensuring consistent mechanical properties throughout the printed part and across different builds is critical for medical applications. This requires well-controlled printing processes, high-quality and consistent metal powders, and thorough testing. Metal3DP’s advanced powder making system focuses on producing powders with high sphericity and flowability, contributing to consistent printing outcomes.
- Efterlevnad av regelverk: Medical devices are subject to stringent regulatory requirements. Manufacturers must ensure that their 3D printing processes and materials meet the necessary biocompatibility, sterility, and performance standards.
- Cost and Scalability: While 3D printing can be cost-effective for prototyping and low-volume production, the cost per part and scalability for high-volume manufacturing need to be carefully considered. Optimizing designs for efficient printing and exploring hybrid manufacturing approaches may be necessary for larger-scale production.
By understanding these potential challenges and implementing appropriate strategies and best practices, medical device manufacturers can effectively leverage metal 3D printing to produce high-quality surgical clamps that meet the demanding requirements of the medical field.
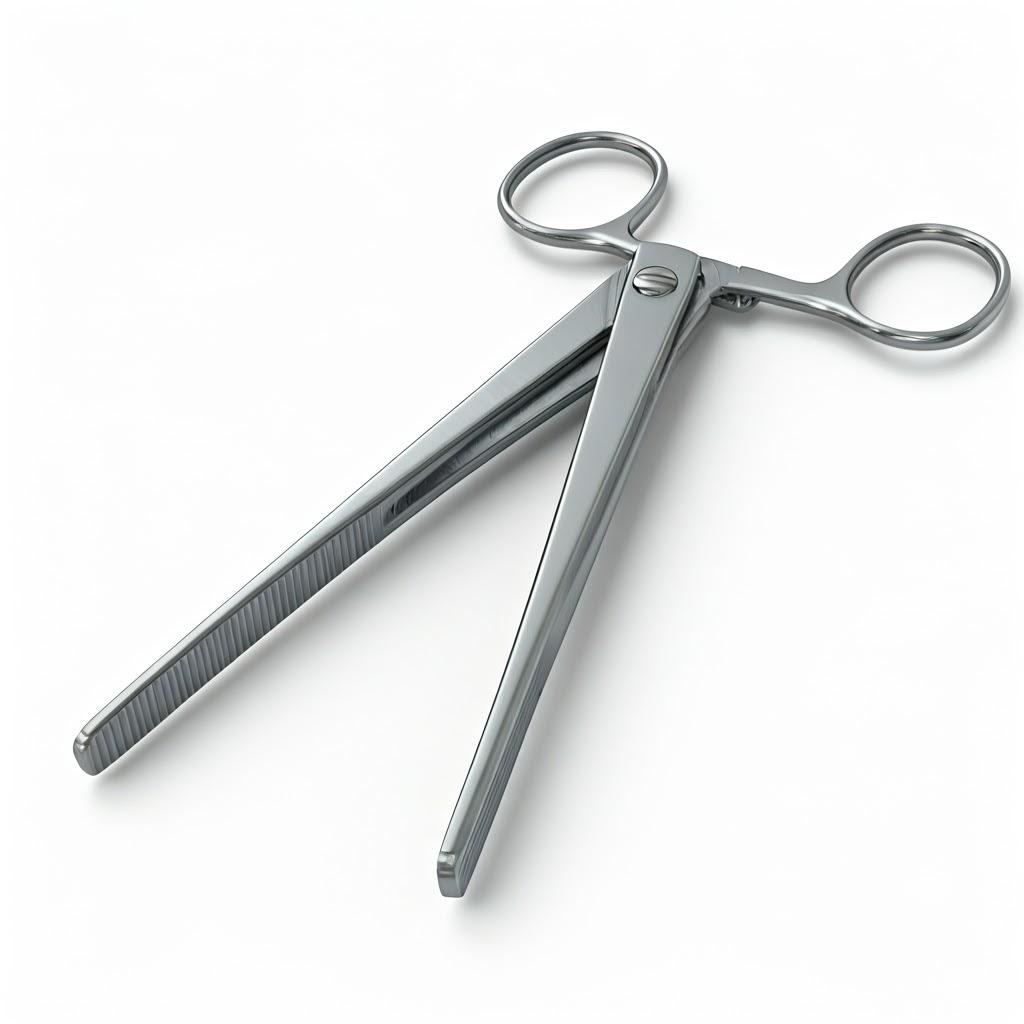
How to Choose the Right Metal 3D Printing Service Provider
Selecting the right metal 3D printing service provider is a critical decision for medical device companies looking to manufacture surgical clamps using additive manufacturing. The choice of supplier can significantly impact the quality, cost, and lead time of the final product. Here are key factors to consider when evaluating potential providers:
- Material Capabilities: Ensure the provider has experience working with the specific metal powders required for your application, such as 316L stainless steel and Ti-6Al-4V titanium alloy. They should be knowledgeable about the material properties and processing parameters relevant to medical devices.
- Equipment and Technology: Inquire about the types of metal 3D printers they utilize. Powder Bed Fusion (PBF) technologies like SLM and EBM are often preferred for high-precision medical components. The provider should have well-maintained equipment and demonstrate expertise in operating it.
- Quality Management Systems and Certifications: Verify if the provider has relevant certifications, such as ISO 13485 for medical device quality management. This indicates their commitment to quality and regulatory compliance.
- Post-Processing Capabilities: Understand the in-house post-processing services offered, including support removal, heat treatment, surface finishing, and cleaning. A provider with comprehensive post-processing capabilities can streamline the manufacturing process.
- Design Optimization and Engineering Support: A valuable service provider will offer expertise in design optimization for additive manufacturing, helping you to refine your surgical clamp designs for optimal printability and performance. Metal3DP provides comprehensive solutions spanning SEBM printers, advanced metal powders, and application development services.
- Tolerance and Accuracy Capabilities: Discuss the achievable tolerances and dimensional accuracy with the provider and ensure they align with the requirements of your surgical clamps. Ask for examples of their work with similar medical devices.
- Ledtider: Understand the typical lead times for manufacturing and delivery. Discuss their capacity and ability to meet your production timelines.
- Cost Structure: Obtain a clear breakdown of the costs involved, including printing, materials, post-processing, and any additional services. Compare pricing models from different providers.
- Communication and Customer Support: Assess the provider’s responsiveness, communication clarity, and willingness to collaborate throughout the project.
- Confidentiality and Intellectual Property Protection: Ensure the provider has robust measures in place to protect your intellectual property and maintain confidentiality.
By carefully evaluating these factors, medical device companies can select a metal 3D printing service provider that meets their specific needs and contributes to the successful manufacturing of high-quality surgical clamps.
Cost Factors and Lead Time for 3D Printed Surgical Clamps
The cost and lead time for producing surgical clamps using metal 3D printing are influenced by several factors. Understanding these elements is crucial for budgeting and project planning:
Kostnadsfaktorer:
- Kostnader för material: The cost of the metal powder (e.g., 316L stainless steel, Ti-6Al-4V) is a significant factor. Specialty alloys or custom blends will generally have higher material costs.
- Build Volume and Part Size: Larger parts or those that occupy a significant portion of the printer’s build volume will typically cost more due to increased material usage and longer print times.
- Complexity of Design: Intricate designs with fine features or complex internal structures may require more support material and longer printing times, increasing costs.
- Krav på efterbearbetning: The extent of post-processing needed (e.g., support removal, heat treatment, machining, polishing) will add to the overall cost.
- Labor and Machine Time: The time required to set up the print job, monitor the printing process, and perform post-processing tasks contributes to the overall cost. Machine time is also a key factor, as longer prints consume more resources.
- Quantity and Scale: While 3D printing can be cost-effective for low to medium volumes and customization, the cost per part may not always be competitive with traditional high-volume manufacturing methods for very large quantities without design optimization for scalability.
- Service Provider Margins: Different service providers will have varying pricing structures and profit margins.
Lead Time Factors:
- Part Complexity and Size: More complex and larger parts generally require longer print times.
- Materialets tillgänglighet: The availability of the specific metal powder can impact lead times. Metal3DP tillverkar ett brett sortiment av högkvalitativa metallpulver, potentially offering shorter lead times for certain materials.
- Machine Availability and Capacity: The service provider’s current workload and the availability of suitable 3D printers will affect lead times.
- Post-Processing Duration: The time required for post-processing steps like heat treatment and surface finishing will add to the overall lead time.
- Förfaranden för kvalitetskontroll: Thorough quality checks and inspections can also influence the total lead time.
- Shipping and Logistics: The time taken for shipping the finished parts to the customer needs to be considered.
It’s essential to discuss these factors with potential metal 3D printing service providers to obtain accurate cost estimates and lead times for your specific surgical clamp requirements.

Vanliga frågor och svar (FAQ)
Here are some frequently asked questions about using metal 3D printing for surgical clamps:
Q: Are 3D printed metal surgical clamps biocompatible? A: Yes, when manufactured using biocompatible materials like 316L stainless steel and Ti-6Al-4V titanium alloy and following proper post-processing and sterilization procedures, 3D printed metal surgical clamps can be fully biocompatible. It’s crucial to choose materials and processes that meet relevant medical device standards.
Q: Can metal 3D printed surgical clamps be sterilized? A: Absolutely. Materials like 316L stainless steel and Ti-6Al-4V are compatible with common sterilization methods used for surgical instruments, such as autoclaving, chemical sterilization, and radiation sterilization. The chosen post-processing and cleaning procedures must ensure that the clamps can be effectively sterilized.
Q: What level of precision can be achieved with metal 3D printed surgical clamps? A: Metal 3D printing technologies like SLM and EBM can achieve tolerances in the range of ±0.05 mm to ±0.1 mm. For critical dimensions requiring tighter tolerances, post-processing with CNC machining can be employed. Surface finishes can also be improved through various post-processing techniques to meet the requirements for surgical instruments.
Q: Is metal 3D printing cost-effective for producing surgical clamps? A: Metal 3D printing can be cost-effective for prototyping, low to medium volume production, and for creating complex or customized designs. The cost-effectiveness depends on factors like material costs, part size, design complexity, and post-processing requirements. For very high volumes, traditional manufacturing methods may still be more economical, but 3D printing offers advantages in flexibility and customization.
Q: What are the typical applications for 3D printed metal surgical clamps? A: 3D printed metal surgical clamps can be used in a wide range of surgical specialties, including general surgery, cardiovascular surgery, neurosurgery, and orthopedics. They can be tailored for specific tasks such as hemostasis, tissue manipulation, retraction, and specialized procedures, potentially offering improved functionality and patient outcomes.
Conclusion: The Future of Surgical Clamps with Metal 3D Printing
Metal 3D printing is poised to play an increasingly significant role in the design and manufacturing of surgical clamps. The technology offers unparalleled design freedom, the ability to create customized and patient-specific instruments, and the potential for enhanced functionality through integrated features and optimized geometries. Materials like 316L stainless steel and Ti-6Al-4V provide the necessary biocompatibility, strength, and corrosion resistance for demanding surgical applications.
While challenges such as achieving tight tolerances and smooth surface finishes require careful consideration and often necessitate post-processing, advancements in metal 3D printing technology and techniques are continuously improving these aspects. By partnering with experienced and reliable metal 3D printing service providers like Metall3DP, medical device manufacturers can leverage the benefits of additive manufacturing to innovate, accelerate product development, and ultimately deliver superior surgical instruments to healthcare professionals. The future of surgical clamps is increasingly being shaped by the transformative capabilities of metal 3D printing, promising a new era of precision, customization, and improved patient care.
Dela på
MET3DP Technology Co, LTD är en ledande leverantör av lösningar för additiv tillverkning med huvudkontor i Qingdao, Kina. Vårt företag är specialiserat på 3D-utskriftsutrustning och högpresterande metallpulver för industriella tillämpningar.
Förfrågan för att få bästa pris och anpassad lösning för ditt företag!
Relaterade artiklar
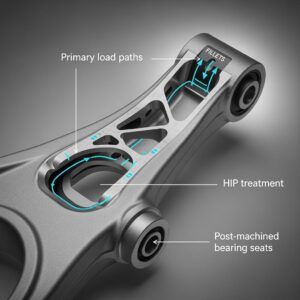
Metal 3D Printing for U.S. Automotive Lightweight Structural Brackets and Suspension Components
Läs mer "Om Met3DP
Senaste uppdateringen
Vår produkt
KONTAKTA OSS
Har du några frågor? Skicka oss meddelande nu! Vi kommer att betjäna din begäran med ett helt team efter att ha fått ditt meddelande.