Thermal Insulation Plates for Space Systems via Metal AM
Innehållsförteckning
Introduction: The Critical Role of Thermal Insulation in Spacecraft
Spacecraft, whether orbiting Earth, traveling to distant planets, or docking with space stations, operate in one of the most extreme environments imaginable. They face a relentless barrage of challenges: the vacuum of space, intense solar radiation, micrometeoroid impacts, and extreme temperature fluctuations swinging hundreds of degrees Celsius between direct sunlight and shadow. Effectively managing these thermal loads isn’t just desirable; it’s fundamental to mission success. Every component, from sensitive electronics and propulsion systems to scientific instruments and structural elements, has specific operating temperature ranges. Deviations can lead to malfunction, reduced performance, shortened lifespan, or catastrophic failure. This is where spacecraft thermal management becomes paramount, and within this critical discipline, thermal insulation plates play an indispensable role.
Traditionally, spacecraft insulation relied on multi-layer insulation (MLI) blankets, specialized coatings, and passive thermal control elements. While effective, these methods often come with limitations in terms of geometric constraints, integration complexity, structural contribution, and susceptibility to handling damage or degradation over long missions. As spacecraft designs become more complex, miniaturized, and push the boundaries of exploration, the need for more integrated, robust, and geometrically optimized thermal solutions has grown significantly.
Skriva in additiv tillverkning av metall (metall AM), also known as metal 3D-utskrifter. This transformative technology is rapidly changing how engineers approach the design and production of complex komponenter för flyg- och rymdindustrin, including thermal insulation plates. Unlike traditional subtractive manufacturing (like CNC machining) which removes material from a solid block, or formative processes (like casting or forging), AM builds parts layer by layer directly from a digital model using specialized metal powders. This fundamental difference unlocks unprecedented design freedom, enabling the creation of intricate geometries, internal features, and optimized structures that were previously impossible or prohibitively expensive to manufacture.
For thermal insulation plates, metal AM offers a unique convergence of benefits. It allows engineers to:
- Integrate Functionality: Combine structural support with thermal insulation properties in a single component, reducing part count and assembly complexity.
- Optimize Geometry: Create complex shapes tailored precisely to the available volume and thermal requirements, including internal cavities, thin walls, and conformal designs that hug other components.
- Lightweight Structures: Employ topology optimization and lattice structures to significantly reduce mass – a critical factor in space missions where every gram saved translates to lower launch costs or increased payload capacity.
- Utilize Advanced Materials: Leverage high-performance metal alloys specifically chosen for their thermal properties, strength-to-weight ratio, and resistance to the harsh space environment.
- Accelerate Development: Rapidly iterate designs and produce prototypes or flight-ready parts much faster than traditional methods allow, crucial for demanding mission schedules.
Companies specializing in advanced manufacturing solutions are at the forefront of this revolution. Met3dp, a leading provider headquartered in Qingdao, China, exemplifies this shift. With expertise in both 3D-utskrift av metall equipment, specifically Selective Electron Beam Melting (SEBM), and the production of high-performance metal powders using advanced techniques like gas atomization and Plasma Rotating Electrode Process (PREP), Met3dp is enabling the aerospace industry to harness the full potential of AM. Their focus on industry-leading print volume, accuracy, and reliability ensures that mission-critical parts, such as thermal insulation plates, meet the stringent demands of space applications.
This article delves into the application of metal AM for producing advanced thermal insulation plates for space systems. We will explore the specific use cases, the compelling advantages over traditional methods, the recommended materials like IN625 and AlSi10Mg, crucial design considerations (DfAM), achievable precision, post-processing requirements, common challenges, supplier selection criteria, cost factors, and finally, answer some frequently asked questions. Our goal is to provide engineers, procurement managers, and decision-makers in the aerospace sector with a comprehensive understanding of how metal AM is reshaping spacecraft thermal management, offering solutions that are lighter, more efficient, and capable of meeting the challenges of next-generation space exploration. Whether you are involved in satellite manufacturing, launch vehicle development, or deep space probe design, understanding the capabilities of metal AM for thermal components is becoming increasingly vital.
Applications of Advanced Insulation Plates in Space Systems
The need for precise thermal control permeates nearly every aspect of spacecraft design and operation. Thermal insulation plates, especially those enhanced through the design freedom of metal additive manufacturing, find diverse and critical applications across various space systems. Their primary function is to control heat flow – either preventing sensitive components from overheating due to internal power dissipation or external radiation, or keeping critical systems within their operational temperature range in the cold vastness of space. The ability to tailor the geometry, material properties, and integrate features using AM significantly broadens their utility compared to traditional flat plates or simple standoffs.
Here’s a breakdown of key application areas:
1. Satellites (LEO, MEO, GEO, and Beyond):
- Electronics Housing Insulation: Sensitive electronic boxes containing processors, communication equipment, and sensor interfaces generate heat during operation and are simultaneously exposed to fluctuating external temperatures. Metal AM insulation plates can be designed conformally to these boxes, incorporating thin walls, internal reflective cavities, or even integrated heat pipes or vapor chambers (enabled by AM’s complexity) to efficiently isolate and manage thermal loads. They can act as structural mounts while providing thermal standoff.
- Battery Module Protection: Batteries have narrow optimal temperature ranges for performance and longevity. Insulation plates shield battery modules from extreme external temperatures and help manage heat generated during charge/discharge cycles, ensuring safety and reliability. Lightweight AlSi10Mg plates are often preferred here.
- Sensor and Instrument Isolation: Scientific instruments, cameras, and sensors often require extremely stable thermal environments to function correctly and achieve high precision. Custom-designed AM insulation plates can create thermally stable enclosures or mounting interfaces, minimizing thermal drift and noise. The low thermal conductivity combined with structural integrity makes materials like IN625 suitable for specific isolation needs.
- Propulsion System Components: Thrusters, fuel tanks, and associated plumbing operate at various temperatures, sometimes cryogenic, sometimes very high. Insulation plates help maintain fuel temperatures, protect adjacent structures from thruster plume heat, and ensure valves and lines operate correctly. High-temperature capable alloys like IN625 are essential here.
- Structural Interface Thermal Breaks: Where different structural elements meet, thermal bridges can form, allowing unwanted heat transfer. AM allows the design of complex interface plates with minimal contact area, thin sections, or integrated insulating features (like honeycombs or lattices) to act as effective thermal breaks while still carrying mechanical loads.
2. Launch Vehicles:
- Avionics and Guidance System Protection: During ascent, launch vehicles experience intense aerodynamic heating and vibrations. Insulation plates protect critical avionics, navigation, and control systems housed within the vehicle’s structure.
- Engine Compartment Shielding: Rocket engines generate enormous amounts of heat. Metal AM insulation plates, often using superalloys like IN625, are used as heat shields to protect surrounding structures, fuel lines, and actuators within the engine bay. Their complex shapes can be optimized for maximum coverage and minimal weight.
- Cryogenic Tank Insulation: While MLI is common, strategically placed AM structural/insulation plates can help manage boil-off and maintain structural integrity around cryogenic propellant tanks, particularly at mounting points or interfaces.
3. Space Stations and Habitats:
- Equipment Racks and Modules: Within pressurized modules, numerous experiments and subsystems generate heat. Integrated insulation plates help manage thermal loads locally, preventing hotspots and ensuring efficient operation of cooling systems.
- External Component Protection: Equipment mounted externally on space stations (like antennas, experiments, or robotic arms) is exposed to the full range of space thermal conditions. AM insulation plates provide durable, reliable thermal protection and structural mounting.
4. Deep Space Probes and Rovers:
- Extreme Temperature Survival: Probes traveling to the outer solar system or landing on planets like Mars or moons like Europa face extreme cold, while missions closer to the sun face intense heat. AM insulation plates, potentially using graded materials or complex internal structures, are critical for survival, maintaining operational temperatures for electronics and scientific payloads over decades-long missions.
- Radiator and Heat Pipe Integration: AM enables the direct integration of insulation features with components of the thermal control system, such as radiator panels or heat pipe mounting structures, optimizing heat rejection pathways while minimizing parasitic heat leaks.
Wholesale Aerospace Parts and Supply Chain Considerations:
För wholesale aerospace parts suppliers and manufacturers, metal AM offers a new paradigm. Procurement managers increasingly look for suppliers who can provide not just standard components, but highly optimized, application-specific parts. The ability to produce complex insulation plates on demand, potentially consolidating multiple functions into one part, offers significant advantages:
- Reducerad lagerhållning: Less need to stock numerous variations of standard insulation components.
- Kortare ledtider: AM enables faster turnaround from design finalization to part delivery compared to tooling-intensive traditional methods.
- Anpassning: Ability to provide bespoke insulation solutions tailored to specific mission requirements without significant NRE (Non-Recurring Engineering) costs associated with traditional manufacturing.
- Motståndskraft i leveranskedjan: Distributed AM capabilities can offer more resilient supply chains compared to geographically concentrated traditional manufacturing hubs.
Metal AM insulation plates represent a significant advancement, moving beyond simple barriers to become integrated, multi-functional components optimized for the demanding thermal and structural requirements of modern satellite thermal control, launch vehicle insulation, and deep space missions. As aerospace manufacturers seek lighter, more capable, and rapidly developed systems, the demand for advanced AM solutions from knowledgeable suppliers like Met3dp will only continue to grow.
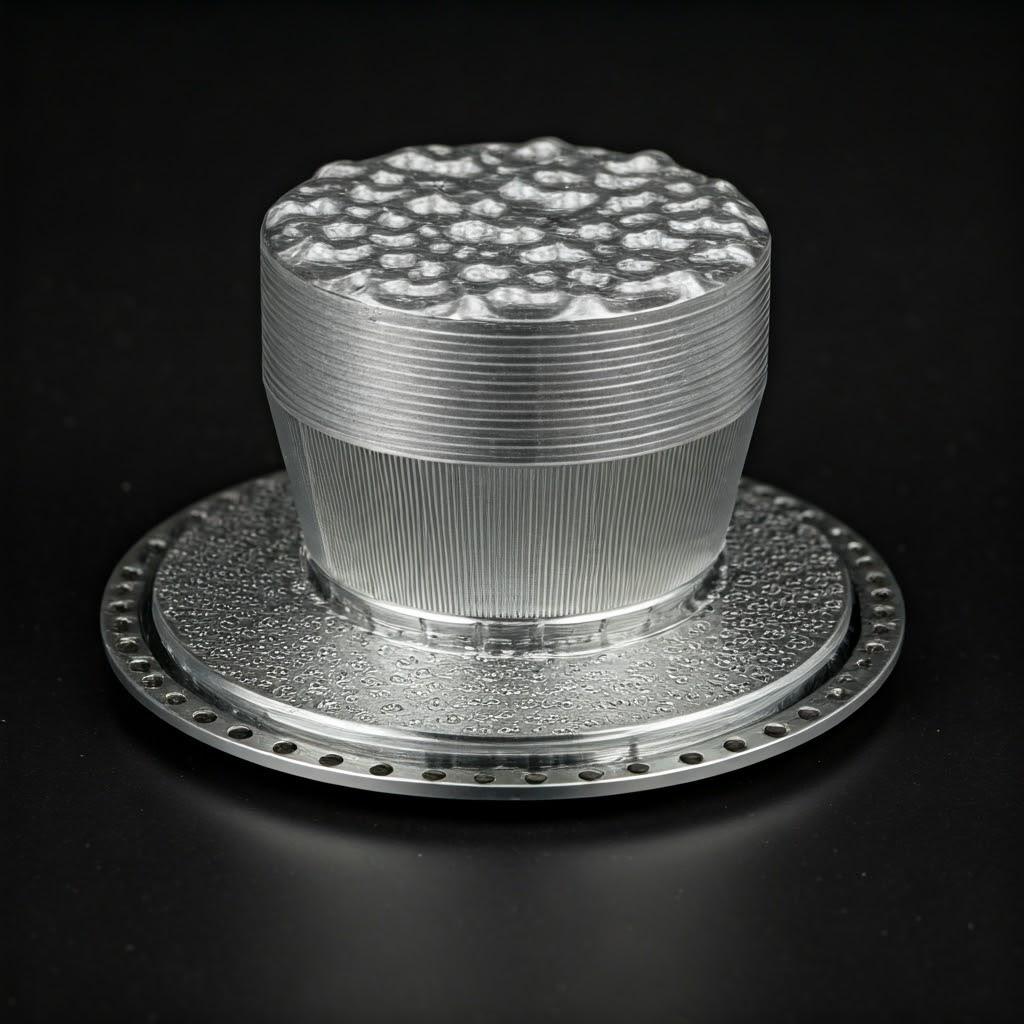
Why Metal Additive Manufacturing Excels for Spacecraft Insulation Plates
The harsh realities of the space environment – extreme temperatures, vacuum, radiation – combined with the relentless drive to reduce mass and increase performance, place extraordinary demands on spacecraft components. Thermal insulation plates are no exception. While traditional manufacturing methods like machining, casting, and sheet metal forming have served the aerospace industry for decades, metal additive manufacturing (AM) presents a suite of compelling advantages, particularly for complex components like optimized insulation plates. These benefits fundamentally change the design and production possibilities, making AM an increasingly preferred choice for mission-critical applications.
Let’s dissect the key reasons why metal AM is exceptionally well-suited for producing spacecraft insulation plates:
1. Unparalleled Design Freedom and Complexity:
- Geometric Sophistication: Traditional methods are inherently limited by tool access, mold constraints, or sheet formability. AM builds layer by layer, freeing designers to create virtually any shape imaginable. For insulation plates, this means:
- Conformal Designs: Plates can perfectly follow the contours of sensitive equipment, minimizing wasted volume and maximizing insulation coverage.
- Internal Features: Complex internal channels, cavities, or lattice structures can be designed directly into the plate. These can be optimized for minimal thermal conductivity, integrated cooling passages (if needed), or specific structural performance. Imagine an insulation plate with an internal honeycomb structure for stiffness and minimal heat conduction paths – easily achieved with AM.
- Organic Shapes: Topology optimization algorithms can be used to remove material strategically from low-stress areas, resulting in lightweight, organically shaped plates that efficiently meet both thermal and structural requirements.
- Traditional Constraints: Machining struggles with deep pockets, thin walls, and internal features. Casting requires complex molds and often results in thicker, heavier parts. Sheet metal forming is limited to relatively simple bends and forms.
2. Significant Lightweighting Potential:
- Mass is King: In aerospace, reducing mass is paramount. Every kilogram saved reduces launch costs significantly or allows for more payload (fuel, instruments, etc.).
- Topology Optimization: As mentioned, AM enables the use of software tools to optimize the plate’s structure based on applied loads and thermal constraints, placing material only where it’s needed. This routinely yields weight savings of 30-60% or more compared to traditionally designed parts.
- Gitterstrukturer: AM allows the incorporation of internal lattice or cellular structures. These metamaterials can be engineered to provide excellent stiffness-to-weight ratios and tailored thermal conductivity properties, creating highly efficient structural insulators.
- Thin Walls: Technologies like Selective Electron Beam Melting (SEBM), used by providers like Met3dp, excel at producing components with very thin, yet structurally sound, walls, further reducing weight compared to the minimum thicknesses achievable with casting or machining.
3. Part Consolidation and Integrated Functionality:
- Reducing Complexity: A traditional insulation assembly might consist of a structural bracket, a separate insulation plate, standoffs, and fasteners. Metal AM allows designers to consolidate these multiple components into a single, monolithic part.
- Benefits of Consolidation:
- Reduced Part Count: Simplifies inventory, logistics, and assembly.
- Lower Assembly Time & Cost: Fewer steps, less labor required.
- Improved Reliability: Eliminates potential failure points associated with joints and fasteners (e.g., loosening due to vibration, thermal cycling fatigue).
- Förbättrad prestanda: Eliminates thermal bridges often created by fasteners or joints, improving overall insulation effectiveness.
- Weight Savings: Often, the consolidated part is lighter than the sum of its original components.
4. Material Efficiency and Reduced Waste:
- Additive vs. Subtractive: Machining starts with a solid block and removes material, often generating significant waste (swarf), especially for complex aerospace parts where the final part volume is much smaller than the initial billet (high buy-to-fly ratio).
- Near-Net Shape: AM builds parts layer by layer, using primarily only the material needed for the final component and support structures. Unfused powder can typically be recycled and reused in subsequent builds.
- Sustainability and Cost: This near-net-shape process drastically reduces material waste, which is particularly important when working with expensive aerospace alloys like Inconel (IN625) or specialized Titanium grades. This contributes to lower material costs and a more sustainable manufacturing process.
5. Rapid Prototyping and Accelerated Development Cycles:
- Speed to First Part: AM does not require traditional tooling (molds, dies, fixtures), which can take weeks or months to design and manufacture. A design modification can be implemented in CAD and a new part printed relatively quickly (days or weeks, depending on complexity and size).
- Iterative Design: This speed enables rapid design iteration. Engineers can design, print, test, and refine insulation plate concepts much faster than traditional methods allow, leading to more optimized solutions within compressed project timelines.
- Tillverkning på begäran: AM facilitates the production of parts on demand, reducing the need for large inventories and enabling faster responses to unexpected needs or design changes late in a program.
6. Suitability for High-Performance Aerospace Materials:
- Processing Challenging Alloys: Metal AM processes, including SEBM and Laser Powder Bed Fusion (L-PBF), are well-suited for processing high-performance aerospace metal powders like Nickel superalloys (IN625) and specialized Aluminum or Titanium alloys (AlSi10Mg, Ti6Al4V). These materials often present challenges for traditional machining or casting due to their hardness, reactivity, or melting points.
- Optimized Microstructures: AM process parameters can be tuned to achieve specific microstructures and material properties, potentially enhancing performance characteristics relevant to thermal insulation and structural integrity in space environments.
Comparison Summary: Metal AM vs. Traditional Methods for Insulation Plates
Funktion | Additiv tillverkning av metall (AM) | Traditional Machining (CNC) | Traditionell gjutning | Sheet Metal Forming |
---|---|---|---|---|
Designens komplexitet | Very High (Internal features, lattices, conformal) | Moderate (Tool access limited) | Moderate (Mold limits) | Low (Bends, simple forms) |
Lättvikt | Excellent (Topology opt., lattices, thin walls) | Moderate (Material removal) | Fair (Often thicker walls) | Fair (Material choice) |
Konsolidering av delar | Excellent (Multiple parts into one) | Poor (Assembly required) | Poor (Assembly required) | Poor (Assembly required) |
Material Avfall | Low (Near-net shape, powder reuse) | High (Subtractive process) | Moderate (Gates, risers) | Moderate (Offcuts) |
Lead Time (Proto) | Fast (No tooling required) | Moderate (Programming, setup) | Slow (Tooling required) | Slow (Tooling required) |
Verktygskostnad | None / Minimal | Low (Standard tools) | High (Mold design/fab) | High (Die design/fab) |
Material lämplighet | Excellent (Superalloys, Ti, Al alloys) | Good (Depends on machinability) | Good (Depends on castability) | Fair (Depends on formability) |
Ideal Volume | Low to Medium, High Complexity | Low to High, Moderate Complexity | Medelhög till hög | High, Low Complexity |
Export to Sheets
In conclusion, the advantages of metal AM – unparalleled design freedom, significant lightweighting, part consolidation, material efficiency, rapid development, and suitability for advanced materials – make it a highly compelling technology for producing next-generation spacecraft insulation plates. While traditional methods still have their place, particularly for simpler designs or very high volumes, AM unlocks performance and integration possibilities crucial for pushing the boundaries of aerospace thermal management and enabling more ambitious space missions. Partnering with an experienced metal AM supplier like Met3dp, equipped with the right technology (e.g., SEBM) and material expertise, is key to realizing these benefits.
Material Focus: IN625 and AlSi10Mg for Extreme Environments
Selecting the right material is fundamental to the success of any spacecraft component, and thermal insulation plates are no exception. The material must not only provide the desired thermal properties (typically low thermal conductivity for insulation) but also possess adequate structural strength, low density, resistance to the space environment (radiation, atomic oxygen, thermal cycling), and compatibility with the chosen manufacturing process. Metal additive manufacturing opens the door to using high-performance alloys that might be difficult or costly to process using traditional methods. For spacecraft insulation plates, two materials frequently stand out due to their excellent balance of properties: Inconel 625 (IN625), a nickel-chromium superalloy, and Aluminum Silicon Magnesium (AlSi10Mg), a widely used aluminum casting alloy adapted for AM.
Understanding the characteristics of these aerospace metal powders and why they are suitable for AM-produced insulation plates is crucial for engineers and procurement managers.
1. Inconel 625 (IN625): The High-Temperature, High-Strength Workhorse
- Sammansättning: Primarily Nickel (Ni), with significant additions of Chromium (Cr), Molybdenum (Mo), and Niobium (Nb).
- Viktiga egenskaper:
- Excellent High-Temperature Strength: Retains significant strength and creep resistance at elevated temperatures (up to ~800-900°C or higher for short durations), crucial for applications near engines or facing direct solar radiation.
- Outstanding Corrosion Resistance: Highly resistant to oxidation and a wide range of corrosive environments, including resistance to atomic oxygen erosion in Low Earth Orbit (LEO).
- Good Fatigue Strength: Withstands cyclic loading and thermal fatigue resulting from extreme temperature swings in space.
- Good Fabricability (in AM): Generally exhibits good weldability, which translates to good processability in powder bed fusion AM processes like SEBM and L-PBF.
- Moderate Thermal Conductivity: While not as low as some ceramics or composites, its thermal conductivity is significantly lower than aluminum alloys, making it effective for thermal isolation applications where structural integrity at high temperatures is also required. (λ≈10−15 W/m·K depending on temperature).
- Moderate Density: Relatively dense compared to Al or Ti alloys (ρ≈8.44 g/cm³). This is a trade-off for its high-temperature performance.
- Why it Matters for Insulation Plates:
- Värmesköldar: Ideal for insulation plates acting as heat shields near rocket engines, thrusters, or components exposed to intense radiative heating.
- Structural Thermal Breaks: Its combination of strength and moderate thermal conductivity makes it suitable for creating structural components that also serve as thermal breaks in high-temperature assemblies.
- Hållbarhet: Its robustness and resistance to the space environment ensure long-term performance for demanding missions.
- AM Considerations: IN625 can be processed effectively using both L-PBF and SEBM. SEBM, offered by providers like Met3dp, often requires fewer support structures due to the elevated build chamber temperatures reducing residual stress, which can be advantageous for complex plate geometries. Post-processing typically involves stress relief heat treatment.
2. Aluminum Silicon Magnesium (AlSi10Mg): The Lightweight Champion
- Sammansättning: Aluminum (Al) alloyed primarily with Silicon (Si) and a small amount of Magnesium (Mg). Originally a casting alloy, its properties make it highly suitable for AM.
- Viktiga egenskaper:
- Låg densitet: Significantly lighter than steel, titanium, or nickel alloys (ρ≈2.67 g/cm³). This is its primary advantage for mass-critical space applications.
- Bra förhållande mellan styrka och vikt: Offers good mechanical strength, particularly after appropriate heat treatment (e.g., T6).
- Good Thermal Conductivity: Possesses relatively high thermal conductivity (λ≈120−150 W/m·K). While this might seem counter-intuitive for insulation, it’s advantageous when the plate’s primary role is structural lightweighting, and thermal isolation is achieved through geometric design (thin walls, minimal contact area, integrated standoffs) rather than inherent material properties. It can also be beneficial if the plate needs to conduct heat away from a specific localized source to a radiator.
- Excellent Processability in AM: One of the most common and well-understood alloys for L-PBF, offering good surface finish and feature resolution.
- God korrosionsbeständighet: Exhibits good general corrosion resistance.
- Why it Matters for Insulation Plates:
- Lightweight Structural Components: Ideal when the primary goal is to create a lightweight structural mounting or enclosure with some thermal standoff achieved geometrically. Examples include electronics enclosures, battery mounts, and brackets where mass savings are paramount.
- Conformal Housings: Its ease of processing allows for complex, thin-walled conformal housings that provide structural support and environmental protection with minimal mass penalty.
- Kostnadseffektivitet: Generally less expensive than IN625 or Titanium alloys.
- AM Considerations: AlSi10Mg is predominantly processed using L-PBF. It typically requires stress relief and often a T6 heat treatment (solutionizing and artificial aging) to achieve optimal mechanical properties. Support structures are generally required and must be carefully considered during design.
Material Comparison Table:
Fastighet | IN625 | AlSi10Mg | Relevance to Insulation Plates |
---|---|---|---|
Primary Role | High-Temp Strength, Corrosion Res. | Lightweighting, Good Strength/Weight | Choose based on primary need: thermal barrier vs. lightweight structure |
Täthet | High (≈8.44 g/cm³) | Low (≈2.67 g/cm³) | AlSi10Mg heavily favored for mass-critical applications. |
Max Use Temp (Approx.) | High (≈800−900°C) | Low (≈150−200°C) | IN625 required for high-temperature zones (engines, etc.). |
Termisk konduktivitet | Moderate (≈10−15 W/m·K) | High (≈120−150 W/m·K) | IN625 provides better inherent insulation. AlSi10Mg relies on geometry. |
Styrka | Mycket hög | Good (esp. post-T6 heat treat) | Both offer structural capability, IN625 superior at temperature. |
AM Processability | Good (SEBM, L-PBF) | Excellent (L-PBF) | Both are readily processable via established AM methods. |
Relativ kostnad | Hög | Måttlig | Cost is a factor, balanced against performance needs. |
Export to Sheets
Met3dp’s Role in Material Excellence:
Choosing the right material is only part of the equation. The quality of the metal powder itself significantly impacts the final part’s properties and reliability. This is where specialized suppliers like Met3dp add considerable value. Met3dp employs industry-leading powder production technologies:
- Gas Atomization (GA): This process uses high-pressure inert gas jets to break up a stream of molten metal into fine droplets, which solidify into spherical powders. Met3dp’s unique nozzle and gas flow designs optimize this process to produce powders with high sphericity and good flowability – critical characteristics for uniform layer spreading and dense part consolidation in powder bed fusion AM.
- Process med roterande elektrod och plasma (PREP): PREP uses a rapidly rotating electrode bar made of the target alloy, which is melted at the tip by a plasma torch. Centrifugal force flings off molten droplets that solidify in flight into highly spherical powders with very low satellite content and high purity, often preferred for critical applications demanding superior material properties.
By controlling the powder production process, Met3dp ensures its metallpulver av hög kvalitet, including nickel superalloys like IN625 and aluminum alloys like AlSi10Mg (though their portfolio extends to Ti alloys, CoCrMo, steels, and innovative alloys like TiNi, TiTa, etc.), meet the stringent requirements of the aerospace industry. This commitment to powder quality translates directly into 3D printed components, like thermal insulation plates, with superior density, predictable mechanical properties, and enhanced reliability – essential for mission success in the extreme environment of space. Their expertise spans not just powder production but also the tryckmetoder themselves, ensuring optimal results from powder to part.
In summary, both IN625 and AlSi10Mg offer unique advantages for metal AM spacecraft insulation plates. IN625 excels in high-temperature, structurally demanding roles requiring inherent thermal isolation, while AlSi10Mg is the go-to for lightweight structural applications where thermal standoff is achieved primarily through design geometry. The choice depends heavily on the specific application requirements, operating environment, and performance trade-offs. Utilizing high-quality powders from expert suppliers ensures that the chosen material delivers its full potential in the final additively manufactured component.
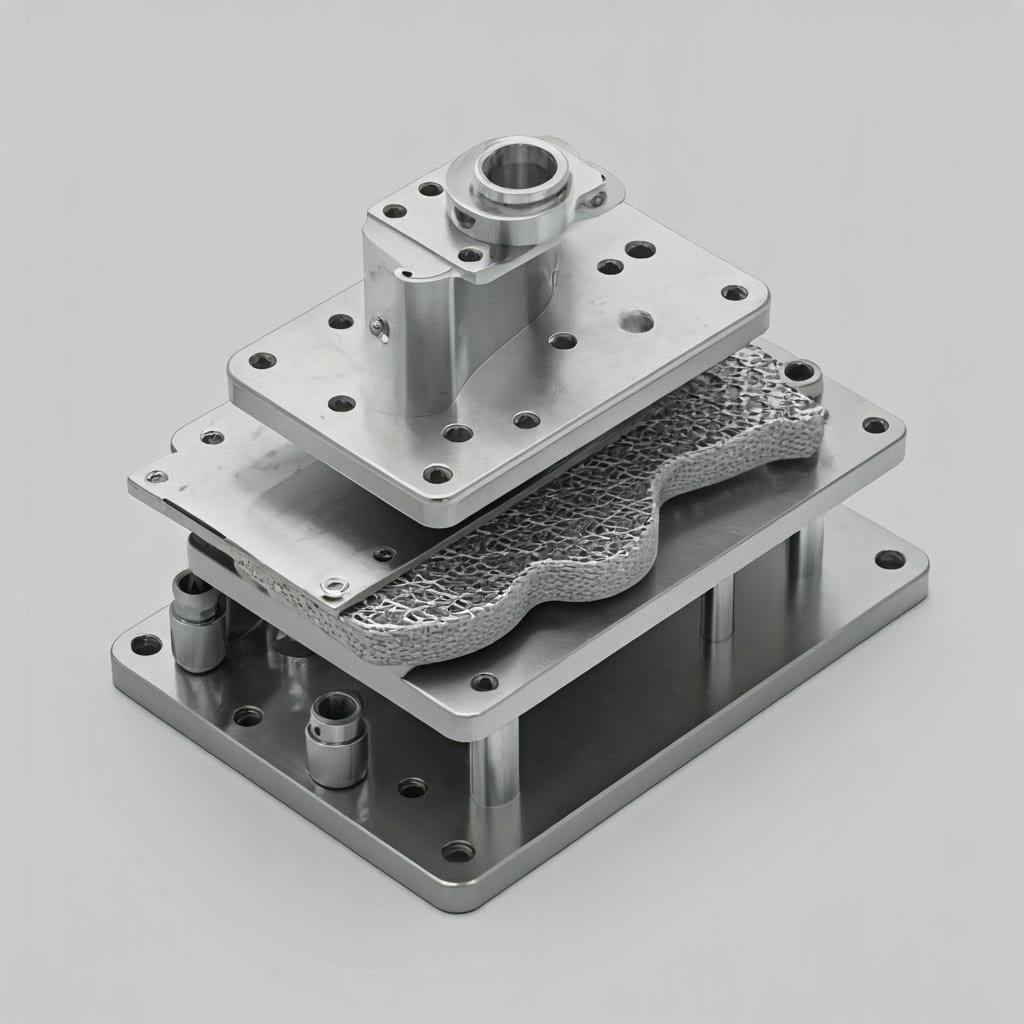
Design for Additive Manufacturing (DfAM) Principles for Thermal Plates
The transition from traditional manufacturing to metal additive manufacturing (AM) is not merely about swapping one production method for another. To truly harness the revolutionary potential of AM, particularly for complex components like spacecraft thermal insulation plates, requires a fundamental shift in design thinking. Simply replicating a design originally intended for machining or casting often fails to leverage AM’s unique strengths and can even introduce new challenges. This is where Design för additiv tillverkning (DfAM) becomes essential. DfAM aerospace principles guide engineers to create parts that are not only manufacturable using AM processes like Selective Electron Beam Melting (SEBM) or Laser Powder Bed Fusion (L-PBF) but are also optimized for performance, weight, cost, and reliability.
For thermal insulation plates destined for the demanding environment of space, applying DfAM principles is critical to achieving goals like maximum thermal isolation, minimum mass, structural integrity, and mission reliability. Let’s explore the key DfAM considerations:
1. Topology Optimization: Material Where It Matters
- Concept: Topology optimization is a computational design technique that optimizes material layout within a defined design space, subject to given loads, boundary conditions, and constraints (e.g., maximum stress, minimum stiffness, thermal performance targets). The software essentially “carves away” unnecessary material, leaving behind an often organic-looking, highly efficient load-bearing structure.
- Benefits for Insulation Plates:
- Mass Reduction: The primary driver. Topology optimization space parts can achieve significant weight savings (often 30-60%+) compared to conventional designs, directly impacting launch costs and payload capacity.
- Stiffness Enhancement: Optimized structures often exhibit higher stiffness-to-weight ratios.
- Thermal Path Control: Can be used implicitly or explicitly to influence heat flow paths, minimizing conduction through structural elements.
- Implementation: Requires specialized software (e.g., Altair OptiStruct, ANSYS Mechanical, nTopology) and a clear definition of load cases (mechanical, thermal) and design constraints. The resulting geometry is often complex and ideally suited for AM.
2. Lattice Structures and Cellular Materials: Engineering Micro-Geometry
- Concept: AM allows the direct fabrication of intricate internal lattice structures thermal or cellular materials (like honeycombs, stochastic foams, or Triply Periodic Minimal Surfaces – TPMS). These are not just voids but engineered structures with tailored properties.
- Benefits for Insulation Plates:
- Further Lightweighting: Lattices offer extremely high porosity while maintaining structural integrity.
- Tunable Thermal Conductivity: The geometry, density, and material of the lattice can be designed to significantly reduce effective thermal conductivity compared to a solid block of the same material, enhancing insulation. TPMS structures, in particular, offer smooth surfaces and potentially excellent thermal properties.
- Multi-funktionalitet: Can provide energy absorption (vibration damping), fluid flow pathways (if designed for integrated cooling/heating), and acoustic insulation in addition to thermal and structural performance.
- Designöverväganden: Requires specialized design tools (nTopology, Materialise 3-matic, CAD add-ins). Need to consider minimum strut/wall thickness manufacturable by the AM process, powder removal from internal cells, and stress concentrations at nodes.
3. Feature Resolution and Minimum Feature Size:
- Process Limitations: Every AM process has limits on the minimum size of features it can accurately produce. This includes minimum wall thickness, minimum hole diameter, smallest achievable pin size, and the sharpness of corners.
- Typical Values: For powder bed fusion processes (L-PBF, SEBM), minimum wall thickness is often in the range of 0.3mm to 0.8mm, depending on the material, machine, and height of the wall. Small holes might be feasible down to 0.5mm, but accuracy decreases.
- DfAM Implications: Designers must ensure that critical features like thin insulating walls, small mounting holes, or fine details on the plate are designed within the achievable limits of the chosen AM process and material. Consulting with the AM service provider, like Met3dp, regarding their specific equipment capabilities (e.g., the precision achievable with their SEBM systems) is crucial. Designing features below the process capability will lead to print failures or parts not meeting specifications.
4. Support Structure Strategy: Building on Foundations
- Syfte: In powder bed fusion, support structures are often necessary for:
- Supporting Overhangs: Anchoring sections of the part that overhang the powder bed at angles below a certain threshold (typically < 45° from the horizontal, though process/material dependent).
- Heat Transfer: Conducting heat away from the fusion zone, preventing overheating and distortion, especially for delicate features or large masses.
- Anchoring: Preventing warping and securing the part to the build plate.
- DfAM Goal: Minimize the need for supports or design them for easy removal. Supports add material cost, increase build time, require post-processing effort, and can mar the surface finish where they connect.
- Strategies:
- Part Orientation: Carefully selecting how the part is oriented on the build plate can drastically reduce overhangs.
- Self-Supporting Angles: Designing overhangs to be above the critical self-supporting angle for the specific material and process (e.g., 45°).
- Chamfers/Fillets: Using chamfers instead of sharp horizontal overhangs can make features self-supporting.
- Designing for Removal: If supports are unavoidable, designing them with minimal contact points, break-off features, or ensuring access for removal tools is vital. This is especially critical for internal channels within insulation plates. SEBM often requires fewer supports than L-PBF due to the high build chamber temperature reducing stress, a notable advantage.
5. Part Orientation: Setting the Stage for Success
- Påverkan: The orientation of the insulation plate on the build platform significantly influences:
- Ytfinish: Upward-facing and downward-facing surfaces have different roughness characteristics compared to vertical walls due to layer stepping effects and support contact points.
- Support Requirements: As discussed above, orientation determines which features require support.
- Byggtid: Taller parts generally take longer to print. Orienting the shortest dimension vertically can sometimes speed up builds (though cross-sectional area also plays a role).
- Mekaniska egenskaper: AM parts can exhibit anisotropic properties (strength varying with direction) due to the layer-wise build process and thermal gradients. Orientation should consider the primary load directions.
- Återstående stress: Orientation can influence the build-up of thermal stress.
- Decision Process: Choosing the optimal orientation often involves balancing these competing factors, sometimes requiring simulation or empirical testing.
6. Thermal Management in Design:
- Beyond Structure: DfAM for thermal plates isn’t just about structure and manufacturability; it’s about designing for thermal performance from the outset.
- Techniques:
- Minimize Conductive Paths: Using thin walls, minimal contact areas, and materials with low thermal conductivity (like IN625 where appropriate).
- Incorporate Thermal Breaks: Designing deliberate gaps, slots, or low-conductivity lattice sections to impede heat flow.
- Radiation Control: Designing internal cavities with specific surface finishes (potentially requiring post-processing or coating) to control radiative heat transfer.
- Integrated Cooling/Heating: For active thermal management, designing internal channels for fluid flow or integration points for heating elements.
7. Consolidation Strategy: Simplifying Complexity
- Identifying Opportunities: Before starting detailed design, engineers should analyze the surrounding assembly to identify if the insulation plate can absorb the function of adjacent brackets, mounts, or structural elements.
- Benefits Review: Revisit the benefits of part consolidation (reduced count, weight, assembly time, improved reliability) to justify the design effort.
- Feasibility Check: Ensure the consolidated design remains manufacturable via AM and meets all functional requirements.
Met3dp’s Expertise: Effectively applying these DfAM principles requires not only the right software tools but also deep expertise in AM processes and materials science. Companies like Met3dp provide comprehensive solutions that extend beyond just printing. Their application development services involve working closely with customers to optimize designs for their specific AM processes (like SEBM), materials, and application requirements, ensuring that the final thermal insulation plates deliver maximum performance and reliability for demanding space missions. Understanding the nuances of different additive manufacturing methods is key to successful DfAM implementation.
By embracing DfAM, aerospace engineers can unlock the full potential of metal AM, creating spacecraft thermal insulation plates that are lighter, more efficient, and better integrated than ever before, pushing the boundaries of spacecraft design and exploration.
Achieving Precision: Tolerance, Surface Finish, and Accuracy in Metal AM
While metal additive manufacturing offers unprecedented design freedom, a common question from engineers and procurement managers, especially those accustomed to the high precision of CNC machining, revolves around the achievable levels of tolerance, surface finish, and overall dimensional accuracy. For mission-critical components like spacecraft insulation plates, understanding the precision capabilities and limitations of metal AM processes like SEBM and L-PBF is vital for managing expectations and ensuring parts meet stringent aerospace requirements.
1. Tolerances in Metal AM:
- Definition: Tolerance refers to the permissible limit or limits of variation in a physical dimension of a part.
- General Capabilities: Metal AM processes typically achieve tolerances comparable to investment casting or metal injection molding. As a general guideline, parts can often be produced to meet standards like ISO 2768-m (medium) or sometimes ISO 2768-f (fine) in the as-built state. However, achieving tighter tolerances comparable to machining (e.g., within tens of microns) usually requires secondary machining operations on critical features.
- Typical Ranges:
- For smaller parts (< 100 mm): Tolerances of ±0.1 mm to ±0.3 mm are often achievable.
- For larger parts (> 100 mm): Tolerances might range from ±0.2 mm to ±0.5 mm or potentially ±0.2% to ±0.5% of the nominal dimension.
- Influencing Factors:
- Machine Calibration: Accuracy depends heavily on the specific AM machine, its calibration status, laser/electron beam spot size, and layer thickness used.
- Materialegenskaper: Different materials exhibit varying degrees of shrinkage, expansion, and warping during the heating/cooling cycles inherent in AM.
- Part Geometry & Size: Larger parts and complex geometries with thin walls or large bulk sections are more prone to thermal distortion, affecting final tolerances.
- Thermal Stresses: Residual stresses built up during printing can cause warping upon removal from the build plate.
- Support Strategy: How the part is supported influences stability during the build and potential distortion.
- Efterbearbetning: Heat treatments (stress relief, annealing) can cause minor dimensional changes.
2. Surface Finish (Roughness):
- Definition: Surface finish, often quantified by the arithmetic average roughness (Ra), describes the texture of a part’s surface. AM parts inherently have a rougher surface finish than machined parts due to the layer-by-layer build process and partially melted powder particles adhering to the surface.
- As-Built Roughness:
- Typical Ra values for as-built metal AM parts (L-PBF/SEBM) range from 5 µm to 25 µm (micrometers), or approximately 200 to 1000 µin (microinches).
- Variations: Surface roughness depends significantly on:
- Orientation: Downward-facing surfaces (supported) are generally rougher than upward-facing surfaces or vertical walls. Stepped features on curved surfaces (“stair-stepping”) also contribute to roughness.
- Process Parameters: Layer thickness, beam power, scan speed influence melt pool dynamics and final surface texture.
- Material: Different metal powders can yield different surface characteristics.
- Powder Particle Size: Finer powders can sometimes lead to smoother finishes but may pose other process challenges.
- Achieving Smoother Finishes: For applications requiring smoother surfaces (e.g., sealing surfaces, specific thermal/optical properties, fatigue-critical areas), post-processing is necessary. Techniques like blasting, tumbling, machining, grinding, or polishing can significantly improve Ra values, potentially achieving finishes below 1 µm Ra with machining or polishing.
3. Dimensional Accuracy:
- Definition: Dimensional accuracy refers to the degree of conformity of a manufactured part to its specified dimensions in the CAD model. It encompasses both tolerance (variation) and systematic deviations (e.g., shrinkage).
- Factors Affecting Accuracy:
- Shrinkage Compensation: AM software typically includes algorithms to compensate for material shrinkage during solidification and cooling, but perfect prediction is difficult.
- Warping and Distortion: Uneven heating and cooling lead to residual stresses, which can warp the part, especially after removal from the build plate. This is more pronounced in L-PBF than SEBM due to the latter’s high build chamber temperature.
- Process Stability: Maintaining consistent beam power, spot size, powder layering, and chamber conditions throughout the build is critical.
- Part Removal: The process of removing the part from the build plate (e.g., wire EDM, sawing) must be done carefully to avoid distortion.
- Ensuring Accuracy: Achieving high dimensional accuracy aerospace parts requires meticulous process control, potentially build simulation to predict distortion, optimized support strategies, appropriate stress relief cycles, and often, final machining of critical interfaces and features.
Met3dp’s Commitment to Precision: Achieving reliable precision in metal AM requires more than just advanced machines; it demands rigorous process control and deep material understanding. Met3dp emphasizes industry-leading print volume, accuracy, and reliability. This is achieved through:
- Advanced Equipment: Utilizing state-of-the-art SEBM printers known for their ability to manage thermal stress effectively, leading to lower residual stress and potentially better dimensional stability, especially for large or complex parts compared to L-PBF in some cases.
- Processoptimering: Decades of collective expertise in metal AM allow Met3dp to optimize printing parameters for specific materials like IN625 and AlSi10Mg, ensuring consistent melt pool dynamics and part quality.
- Kvalitetskontroll: Implementing robust quality checks throughout the process, from incoming powder inspection to final part validation using NDT and metrology.
Precision Summary Table:
Parameter | Typical As-Built Range (L-PBF/SEBM) | Post-Processed Potential | Key Influencing Factors |
---|---|---|---|
Tolerans | ISO 2768-m/f (±0.1 to ±0.5 mm+) | Machining Tolerances (<0.05mm) | Machine, Material, Size, Geometry, Thermal Stress, Supports |
Surface Finish (Ra) | 5 µm – 25 µm | < 1 µm (Machining/Polishing) | Orientation, Parameters, Material, Supports, Post-Processing |
Dimensionell noggrannhet | Good, but affected by distortion | High (with post-machining) | Shrinkage, Warping, Process Control, Part Removal, Heat Treat |
Export to Sheets
Conclusion on Precision: Engineers designing metal 3D printing tolerances into their spacecraft insulation plates must understand that while AM offers incredible geometric freedom, achieving machining-level precision typically requires post-processing steps for critical features. However, the “as-built” precision is often sufficient for many features, especially internal structures or non-critical interfaces. Effective communication with the AM service provider regarding critical dimensions, tolerances (quality control metal printing), and surface finish requirements is paramount. Leveraging the expertise and advanced capabilities of partners like Met3dp ensures that the final components meet the demanding precision standards required for reliable operation in space.
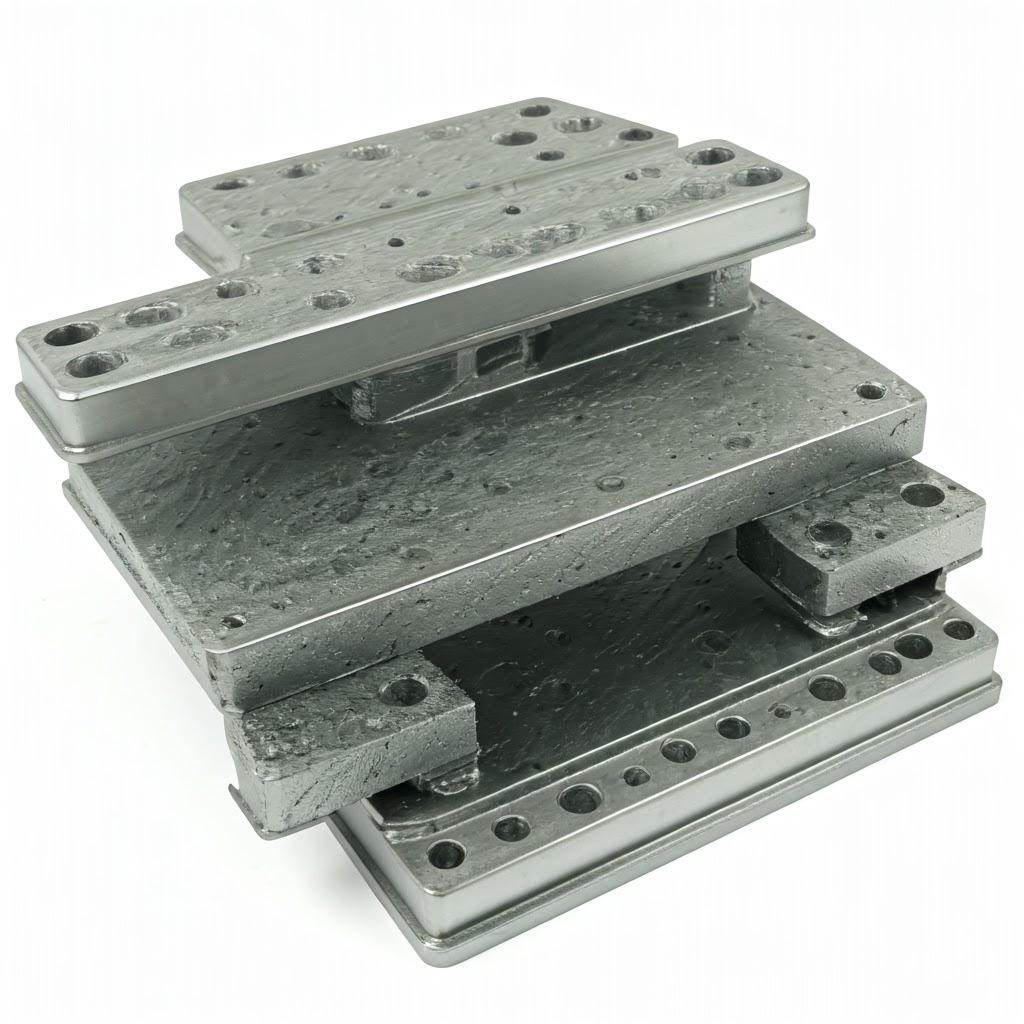
Essential Post-Processing for Mission-Critical Insulation Plates
A common misconception about metal additive manufacturing is that parts emerge from the printer ready for immediate use. While AM produces near-net-shape components, for demanding applications like mission-critical spacecraft insulation plates, the “as-built” part is merely the starting point. A series of essential efterbearbetning steps are typically required to transform the raw AM part into a flight-ready component that meets stringent aerospace requirements for mechanical properties, dimensional accuracy, surface finish, and overall reliability.
Understanding these post-processing stages is crucial for designers, engineers, and procurement managers to accurately budget time and cost, and to ensure the final part performs as intended. The specific steps depend on the material (e.g., IN625 vs. AlSi10Mg), the AM process used (SEBM, L-PBF), the complexity of the part, and the specific application requirements.
Common Post-Processing Steps for AM Thermal Insulation Plates:
1. Stress Relief / Heat Treatment:
- Syfte: The rapid heating and cooling cycles inherent in powder bed fusion AM create significant internal residual stresses within the part. These stresses can cause distortion upon removal from the build plate, lead to premature cracking, and negatively impact mechanical properties (especially fatigue life). Heat treatment is essential to alleviate these stresses and/or optimize the material’s microstructure for desired properties.
- Typical Cycles:
- Stressavlastning: Generally performed while the part is still attached to the build plate (especially for L-PBF) or immediately after removal. Involves heating the part to a specific temperature below its critical transformation point and holding it for a set duration, followed by controlled cooling. This relaxes internal stresses without significantly altering the microstructure. SEBM, operating at higher temperatures, inherently reduces stress build-up but may still benefit from a post-build stress relief cycle.
- Annealing (e.g., for IN625): A higher temperature treatment designed to relieve stress, improve ductility, and homogenize the microstructure. Specific temperatures and times depend on the desired properties.
- Solutionizing and Aging (e.g., T6 for AlSi10Mg): A multi-stage heat treatment for precipitation-hardening alloys like AlSi10Mg. Solutionizing dissolves alloying elements into the matrix, followed by quenching and then artificial aging (heating to a lower temperature) to precipitate fine particles that significantly increase strength and hardness.
- Importance: Heat treatment metal AM is arguably the most critical post-processing step for ensuring the structural integrity and dimensional stability of aerospace components.
2. Part Removal from Build Plate:
- Method: Parts are typically fused to a thick metal build plate during printing. Removal usually involves separating the part using wire Electrical Discharge Machining (EDM), sawing, or grinding.
- Överväganden: Care must be taken to avoid damaging the part during removal. The choice of method depends on the part geometry, material, and the required precision of the base surface. Wire EDM offers high precision but is slower.
3. Support Structure Removal:
- Necessity: As discussed in DfAM, support structures are often required but must be removed before the part can be used.
- Metoder:
- Manuell borttagning: Supports are often designed with weakened connection points and can be manually broken off or removed with hand tools (pliers, cutters).
- Maskinbearbetning: CNC machining or grinding can be used to remove support structures, especially in accessible areas or where a specific surface finish is required at the contact points.
- Wire EDM: Used for precise removal, especially for supports in intricate areas.
- Utmaningar: Removing supports from complex internal channels or delicate lattice structures can be extremely challenging and time-consuming. DfAM plays a critical role in designing supports for easy removal or avoiding them altogether. Support removal techniques must be considered early in the design phase.
4. Surface Finishing:
- Syfte: To improve the as-built surface roughness (Ra), remove partially melted powder particles, eliminate layer lines, and meet specific surface requirements for thermal, optical, sealing, or fatigue performance.
- **Techniques for Aerospace Surface Finishing:
- Abrasive Blasting (Sandblasting, Bead Blasting): Propels abrasive media (sand, glass beads, ceramic particles) against the surface to create a uniform, matte finish and remove loose powder. Effective for general surface cleanup but limited in improving Ra significantly.
- Tumbling/Vibratory Finishing: Places parts in a tub with media (ceramic, plastic) that vibrates or tumbles, causing the media to rub against the parts, smoothing edges and surfaces over time. Good for batch processing but less controlled.
- Machining/Grinding: Provides the highest level of precision and the smoothest finishes on specific features (e.g., mating surfaces, interfaces, sealing grooves). Often required for achieving tight tolerances.
- Polering: Achieves very smooth, mirror-like finishes for optical applications or where extremely low Ra is needed. Can be manual or automated.
- Electropolishing: An electrochemical process that removes a thin layer of material, smoothing surfaces and removing contaminants. Effective for complex shapes.
5. Inspection and Validation (NDT):
- Syfte: To ensure the part is free from critical defects (porosity, cracks, lack of fusion) and meets dimensional specifications. Crucial for metal AM part validation inom flyg- och rymdindustrin.
- Metoder:
- Visual Inspection: Basic check for obvious defects or inconsistencies.
- Dimensional Metrology: Using Coordinate Measuring Machines (CMMs), 3D scanners, or calipers to verify dimensions and tolerances against the CAD model.
- Icke-förstörande testning (NDT):
- Computed Tomography (CT) Scanning: X-ray based method providing detailed 3D images of the internal structure, highly effective for detecting internal porosity, cracks, and verifying complex internal features (like lattice structures or cooling channels). Often mandated for critical aerospace parts.
- Dye Penetrant Inspection (DPI): Detects surface-breaking cracks.
- Ultrasonic Testing (UT): Can detect subsurface flaws.
- Radiographic Testing (RT): Traditional X-ray for internal defect detection.
- Importance: Rigorös NDT inspection aerospace protocols are essential to guarantee the integrity and reliability of flight hardware.
6. Cleaning and Coating:
- Cleaning: Ensuring parts are free from powder residue, cutting fluids (from machining), and other contaminants before assembly or application of coatings.
- Thermal Control Coatings: Spacecraft insulation plates may require specialized coatings applied after other post-processing steps to achieve specific thermal properties (e.g., low solar absorptivity α, high thermal emissivity ϵ) for effective passive thermal control. These can include specialized paints (white, black), vapor-deposited layers (gold, silver, aluminum), or anodizing treatments.
Integrating Post-Processing into Design: Successful AM implementation requires thinking about post-processing from the very beginning. Designers should consider:
- Can features requiring tight tolerances or smooth finishes be easily accessed for machining?
- How will internal supports be removed?
- Will the chosen heat treatment cause acceptable levels of distortion?
- Does the design allow for effective NDT inspection of critical areas?
Post-processing adds time and cost to the overall manufacturing workflow, but it is indispensable for producing high-quality, reliable metal AM components for space applications. Understanding these steps allows for better planning, costing, and design optimization, ensuring the final insulation plate meets all mission requirements.
Overcoming Common Challenges in Metal AM for Thermal Components
While metal additive manufacturing unlocks significant potential for creating advanced thermal insulation plates, the technology is not without its challenges. Producing complex, mission-critical aerospace components requires careful management of the process to avoid potential defects and ensure consistent quality. Awareness of these common challenges and the strategies to mitigate them is crucial for successful implementation.
1. Residual Stress, Warping, and Cracking:
- Utmaning: The extreme thermal gradients experienced during powder bed fusion (rapid melting and solidification) inevitably lead to the build-up of internal residual stress metal printing. If these stresses exceed the material’s yield strength, they can cause warping (distortion of the part geometry) or even cracking, either during the build or after removal.
- Mitigation Strategies:
- Process Simulation: Using Finite Element Analysis (FEA) tools specifically designed for AM simulation can predict thermal gradients, stress accumulation, and potential distortion, allowing for design or parameter adjustments before utskrift.
- Optimized Scan Strategies: Tailoring the laser or electron beam path (e.g., island scanning, alternating directions) can help distribute heat more evenly and reduce localized stress peaks.
- Effective Support Structures: Well-designed supports anchor the part firmly to the build plate and act as heat sinks, helping to manage thermal gradients and prevent warping during the build.
- Appropriate Heat Treatment: Post-build stress relief cycles are essential for relaxing internal stresses and stabilizing the part’s geometry.
- Process Choice (SEBM Advantage): Processes like Selective Electron Beam Melting (SEBM), which operate with the powder bed held at elevated temperatures (several hundred °C), significantly reduce the thermal gradients during the build compared to L-PBF. This results in much lower residual stress, minimizing the risk of warping and cracking, especially for large parts or crack-sensitive alloys like IN625. This is a key advantage of the technology used by providers like Met3dp.
2. Porosity:
- Utmaning: Porosity refers to small voids or pores within the finished part. These act as stress concentrators and can significantly degrade mechanical properties, particularly fatigue strength and fracture toughness – unacceptable for critical components. Porosity can arise from two main sources:
- Gas Porosity: Trapped gas (e.g., Argon used as shielding gas in L-PBF, or dissolved gases within the powder) forming bubbles that get frozen into the solidifying metal.
- Lack-of-Fusion Porosity: Insufficient energy input or improper overlap between scan tracks leading to incomplete melting and bonding between layers or adjacent melt pools.
- Mitigation Strategies:
- High-Quality Powder: Använder metallpulver with high sphericity, controlled particle size distribution, low internal porosity, and low dissolved gas content is crucial. Met3dp’s advanced powder production methods (Gas Atomization, PREP) are designed to ensure such metallpulver av hög kvalitet. Regular powder sieving and careful handling/recycling protocols are also vital to prevent contamination and degradation.
- Optimized Process Parameters: Dialing in the correct beam power, scan speed, layer thickness, and hatch spacing is critical to ensure complete melting and fusion without excessive energy input that could vaporize material or increase gas pickup.
- Het isostatisk pressning (HIP): A post-processing step where the part is subjected to high temperature and high inert gas pressure. This can effectively close internal voids (both gas and lack-of-fusion porosity), significantly improving density and mechanical properties. Often required for fatigue-critical aerospace parts.
- NDT Inspection: CT scanning is particularly effective for detecting and characterizing internal porosity control additive manufacturing.
3. Support Removal Difficulties:
- Utmaning: While DfAM aims to minimize supports, complex internal geometries like lattice structures or cooling channels within an insulation plate can make support removal extremely difficult or impossible without damaging the part.
- Mitigation Strategies:
- DfAM Focus: Prioritize self-supporting designs, orient parts strategically, use soluble or easily breakable support materials/structures where possible (though less common in metal AM).
- Design for Access: Ensure tools or fluids (for chemical etching, though less common) can reach internal supports.
- Process Simulation: Predict areas needing support and try to redesign them.
- Acceptance: In some cases, internal supports may need to be left in place if they do not critically impact performance and cannot be removed – this must be carefully evaluated.
4. Achieving Tight Tolerances and Surface Finish:
- Utmaning: As discussed previously, the as-built tolerances and surface finish of AM parts may not meet the requirements for all features, particularly critical interfaces or sealing surfaces.
- Mitigation Strategies:
- Hybridtillverkning: Design the part for AM, leveraging its geometric freedom, but include extra material (machining allowance) on critical surfaces that will be finished using conventional CNC machining.
- Targeted Post-Processing: Apply specific finishing techniques (blasting, polishing, grinding) only to the areas requiring improved surface quality or tolerance.
- Realistic Expectations: Understand the inherent capabilities of the AM process and avoid specifying unnecessarily tight tolerances or finishes where they are not functionally required.
5. Material Contamination and Powder Management:
- Utmaning: Metal powders, especially reactive ones like Aluminum and Titanium alloys, can be easily contaminated by oxygen, nitrogen, or moisture from the atmosphere, or cross-contaminated if multiple materials are processed on the same machine without meticulous cleaning. Contamination degrades powder quality and final part properties.
- Mitigation Strategies:
- Inert Atmosphere: Processing within a tightly controlled inert gas environment (Argon or Nitrogen for L-PBF, vacuum for SEBM).
- Strict Powder Handling Protocols: Dedicated equipment for specific materials, proper storage conditions (sealed containers, controlled humidity), regular sieving to remove degraded particles, and controlled powder recycling procedures.
6. Anisotropy:
- Utmaning: Due to the layer-wise build and directional solidification, AM parts can exhibit anisotropic mechanical properties (different strength/ductility in the build direction (Z) vs. the build plane (X-Y)).
- Mitigation Strategies:
- Bygg orientering: Orient the part such that the primary load paths align with the directions of optimal material properties.
- Processparameteroptimering: Fine-tuning parameters can influence the microstructure (e.g., grain structure) and reduce the degree of anisotropy.
- Post-Processing Heat Treatments: Certain heat treatments can help homogenize the microstructure and reduce anisotropy.
- Design Allowances: Account for potential anisotropy in design calculations using direction-specific material property data.
Overcoming these common challenges requires a combination of robust DfAM practices, meticulous process control, high-quality materials, appropriate post-processing, and rigorous inspection. Partnering with experienced metal AM troubleshooting experts and service providers like Met3dp, who possess deep knowledge across materials, processes (including the specific benefits of SEBM for managing stress), and quality control, significantly increases the likelihood of successfully producing reliable, high-performance thermal insulation plates for the demanding environment of space. Addressing aerospace component validation requires tackling these challenges head-on.
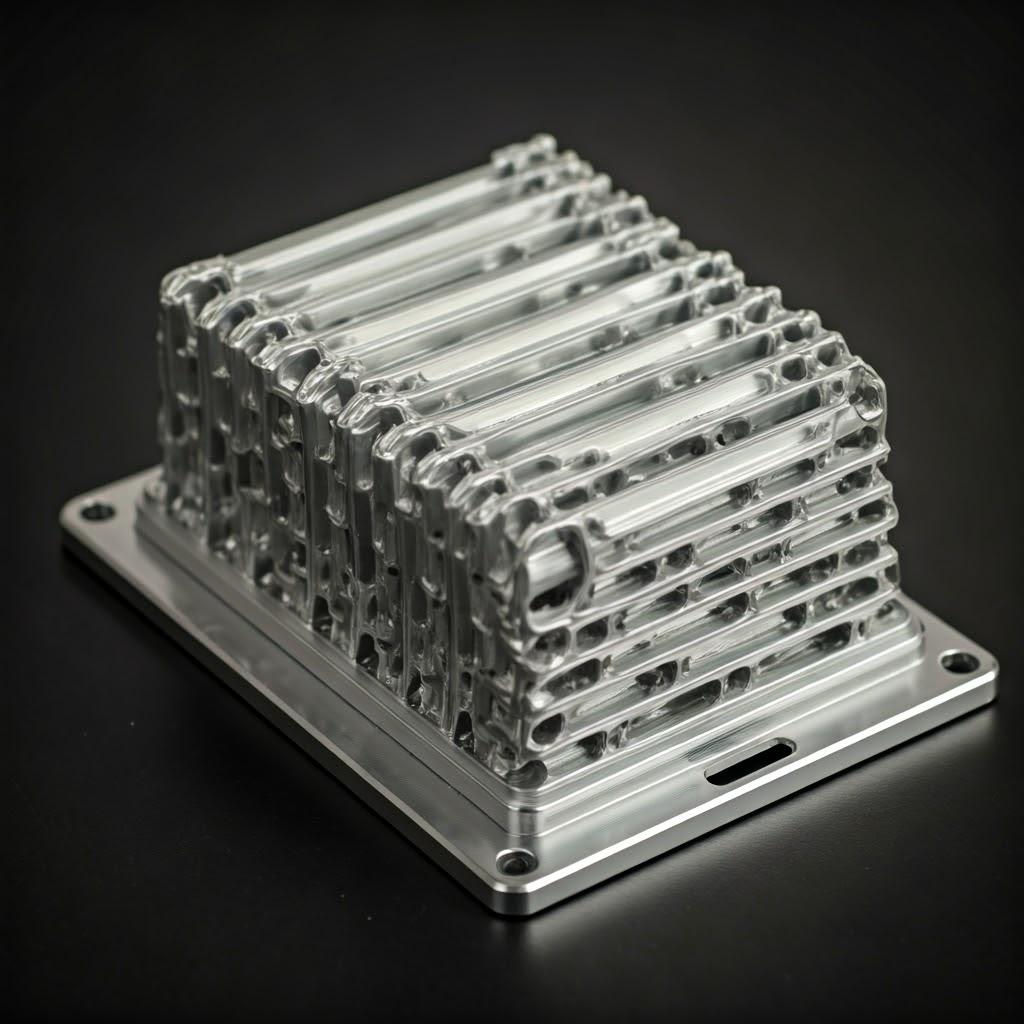
Selecting Your Strategic Partner: Choosing a Metal AM Service Provider
The journey from a thermal insulation plate concept to a flight-qualified component relies heavily not just on the technology itself, but on the expertise and capabilities of the chosen metal additive manufacturing service provider. For aerospace applications, where safety, reliability, and performance are non-negotiable, selecting the right partner is a critical strategic decision. The supplier landscape varies widely, from small job shops to large, vertically integrated manufacturers. Procurement managers and engineering teams need a robust framework for aerospace AM supplier evaluation to ensure their chosen partner can meet the rigorous demands of the space industry.
Here are key criteria to consider when evaluating additive manufacturing vendors for producing spacecraft thermal insulation plates:
1. Quality Management System (QMS) and Certifications:
- AS9100: This is the internationally recognized QMS standard for the aerospace industry. Certification to AS9100 demonstrates a provider’s commitment to quality, traceability, risk management, and continuous improvement specific to aerospace requirements. It is often a mandatory prerequisite for suppliers of flight hardware.
- ISO 9001: A foundational QMS standard, indicating robust general quality processes.
- Nadcap Accreditation: While AS9100 covers the overall system, Nadcap provides accreditation for specific special processes critical to aerospace, such as heat treatment, non-destructive testing (NDT), welding (relevant to AM), and materials testing. A provider holding relevant Nadcap accreditations offers additional assurance of process control in these specific areas.
- Verification: Always verify the status and scope of certifications.
2. Material Expertise and Handling:
- Proven Experience: The provider must have demonstrable experience working with the specific aerospace metal powders required (e.g., IN625, AlSi10Mg, Titanium alloys). This includes understanding their processing nuances, required heat treatments, and potential challenges.
- Powder Quality Control: Rigorous procedures for incoming powder inspection (chemistry, particle size distribution, morphology, flowability), secure storage, controlled handling (preventing contamination), traceability by batch, and powder rejuvenation/recycling protocols are essential. Ask about their powder sourcing – vertically integrated suppliers like Met3dp, who manufacture their own metallpulver av hög kvalitet using advanced methods like Gas Atomization and PREP, offer greater control and traceability.
- Material Characterization: Does the provider have capabilities (in-house or via partners) to characterize powder and final part material properties (tensile strength, microstructure, density, etc.) to ensure they meet specifications?
3. Equipment, Technology, and Capacity:
- Appropriate Technology: Does the provider operate the right type of AM machines (e.g., L-PBF, SEBM) suitable for the material and application? For instance, Met3dp’s focus on SEBM skrivare can offer advantages in reduced residual stress for complex IN625 parts.
- Machine Condition and Calibration: Are the machines well-maintained, regularly calibrated, and equipped with necessary process monitoring capabilities (e.g., melt pool monitoring, oxygen sensors)?
- Byggvolym: Can their machines accommodate the size of the required insulation plates?
- Capacity and Redundancy: Do they have sufficient capacity to meet required lead times, especially if moving from prototype to low-volume production? Do they have multiple machines to offer redundancy?
4. Process Control and Quality Assurance:
- Documented Procedures: Robust, documented procedures for every step, from build preparation and parameter settings to post-processing and inspection.
- Traceability: End-to-end traceability linking the final part back to the specific machine, build parameters, powder batch, operator, and post-processing steps is crucial for aerospace.
- Pågående övervakning: Utilization of available tools to monitor build stability and detect potential issues in real-time.
- NDT Capabilities: In-house or certified third-party capabilities for required NDT methods (CT scanning, DPI, UT, etc.) are essential for part validation.
5. Engineering Support and DfAM Expertise:
- Collaboration: A true strategic partner collaborates with your engineering team, not just takes orders. Look for providers offering applikationsutvecklingstjänster.
- DfAM Guidance: Can they provide expert advice on optimizing the insulation plate design for AM (topology optimization, support strategy, feature resolution, material selection)?
- Simulation Capabilities: Do they utilize build simulation tools to predict and mitigate potential issues like distortion or thermal stress?
- Problem Solving: Do they have experienced engineers who can help troubleshoot issues and find solutions? Met3dp prides itself on decades of collective expertise in metal AM to support customer projects. Learn more about Met3dp’s capabilities.
6. Aerospace Industry Track Record:
- Proven Performance: Have they successfully produced parts for similar space or demanding aerospace applications? Can they provide (non-confidential) case studies or references?
- Understanding Requirements: Are they familiar with the specific documentation, testing, and quality requirements typical of aerospace programs?
7. Lead Time, Responsiveness, and Communication:
- Realistic Timelines: Can they provide accurate lead time estimates and consistently meet delivery schedules?
- Communication: Clear, proactive communication throughout the project lifecycle is vital.
- Flexibilitet: Ability to accommodate potential design changes or expedited requests (within reason).
8. Cost Transparency and Value:
- Clear Quoting: Providing detailed quotes that break down costs (material, machine time, labor, post-processing, QA) allows for better evaluation.
- Value Proposition: Consider the overall value, not just the lowest price. Expertise, quality, reliability, and engineering support contribute significantly to the total value and risk mitigation.
Att hitta rätt passform: Choosing a metal AM service provider for procurement metal AM services requires due diligence beyond a simple price comparison. It involves assessing their technical capabilities, quality systems, material expertise, engineering support, and track record. Companies like Met3dp, offering comprehensive solutions from avancerade metallpulver produced via state-of-the-art techniques to cutting-edge SEBM skrivare and dedicated application support, represent the type of vertically integrated, expert partner needed to successfully implement metal AM for mission-critical spacecraft components like thermal insulation plates. A strong partnership built on trust, transparency, and technical excellence is fundamental to leveraging AM effectively for the challenges of space exploration.
Understanding Cost Dynamics and Lead Times for AM Insulation Plates
One of the key considerations for adopting any manufacturing technology is its economic viability and production speed. While metal additive manufacturing offers compelling technical advantages for spacecraft insulation plates, understanding the associated metal 3D printing cost factors and typical additive manufacturing lead times is crucial for project planning, budgeting, and comparing AM against traditional alternatives like CNC machining. The cost structure and timeline drivers for AM differ significantly from subtractive or formative methods.
Cost Factors Breakdown:
The final price of an AM-produced thermal insulation plate is influenced by a complex interplay of factors:
- Material Cost:
- Powder Price: The raw material cost per kilogram varies significantly between alloys. High-performance aerospace metal powders like IN625 or specialized Titanium alloys are considerably more expensive than AlSi10Mg or stainless steels.
- Powder Consumption: This includes the material making up the final part och the support structures. Designs requiring extensive supports will consume more powder.
- Recycling Efficiency: While unfused powder can be recycled, there are limits and associated costs (sieving, testing, potential degradation over cycles). The provider’s efficiency in powder reuse impacts overall material cost attribution.
- Maskintid:
- Byggtid: This is often the largest cost component. It’s primarily driven by the height of the part (number of layers) and the volym eller cross-sectional area per layer (influencing scan time). Complex geometries or dense lattice structures require more scanning per layer.
- Machine Hourly Rate: This rate incorporates machine depreciation, energy consumption, maintenance, inert gas usage (Argon/Nitrogen for L-PBF, vacuum system for SEBM), and facility overheads. High-end industrial metal AM systems represent a significant capital investment.
- Kostnader för arbetskraft:
- Pre-Processing: File preparation, build layout optimization, support structure generation, and process parameter selection require skilled technicians or engineers.
- Machine Operation: Setup, monitoring the build process, and initial part removal.
- Efterbearbetning: Significant labor is involved in part removal from the plate, support removal (often manual or semi-automated), heat treatment setup, surface finishing, and inspection. This can sometimes exceed the actual printing time cost for complex parts.
- Kostnader för efterbearbetning:
- Specific Processes: Each post-processing step (stress relief/heat treatment, HIP, machining, blasting, polishing, NDT) has associated equipment, consumables, and labor costs.
- Komplexitet: Parts requiring extensive support removal, multi-axis machining for tight tolerances, or advanced NDT (like CT scanning) will incur higher post-processing costs.
- Quality Assurance and Certification:
- Inspection: The level of required inspection (visual, dimensional, NDT) directly impacts cost. Comprehensive NDT like CT scanning is expensive but often necessary for aerospace component validation.
- Documentation: Generating the detailed documentation, material certifications, and traceability records required for aerospace significantly adds to the overhead cost.
- Design Complexity and Part Volume:
- Komplexitet: While AM enables complexity, features like very thin walls, intricate internal channels, or extensive lattice structures can increase build time and post-processing difficulty, thus impacting cost.
- Part Volume: Refers to the overall size of the part, influencing material consumption and machine time.
- Build Density: Printing multiple parts in a single build (nesting) can amortize setup time and potentially reduce the cost per part compared to printing individually, though this depends on part geometry and height consistency.
Lead Time Considerations:
Additive manufacturing lead times for metal parts are typically shorter than traditional methods involving tooling (like casting or injection molding), especially for prototypes and low volumes. However, it’s not an instantaneous process.
- Typical Phases:
- Quoting & Order Confirmation: (1-5 days) Depends on complexity and supplier responsiveness.
- Design Review & Preparation: (1-3 days) DfAM checks, build file setup, simulation (if needed).
- Queueing & Scheduling: (Variable) Depends on machine availability and supplier workload.
- Tryckning: (1-7+ days) Highly dependent on part height, volume, and complexity. Runs can take multiple days for large/complex parts.
- Cool Down & Depowdering: (0.5-1 day)
- Efterbearbetning: (2-10+ days) Heat treatment cycles, support removal, machining, finishing, NDT all add significant time. Can be the longest phase.
- Final Inspection & Shipping: (1-3 days)
- Influencing Factors:
- Part Complexity/Size: Larger, more complex parts take longer to print and post-process.
- Machine Availability: High demand can lead to longer queue times.
- Krav på efterbearbetning: Extensive machining or specialized NDT adds significantly to the timeline.
- Material Choice: Some materials may require longer heat treatment cycles.
- Kvantitet: Printing larger batches takes longer but may be more efficient overall than multiple small builds.
- General Comparison: For a single complex prototype or a small batch (1-10) of spacecraft insulation plates, AM lead times might range from 1 to 4 weeks, depending heavily on the factors above. This is often significantly faster than the months it might take to get first articles from casting or tooling-intensive processes.
Return on Investment (ROI):
While the per-part cost of metal AM might sometimes be higher than traditional methods (especially compared to high-volume processes or simple machined parts), the ROI additive manufacturing calculation for aerospace often looks favorable when considering:
- Reduced Development Time: Faster iterations lead to quicker project completion.
- Weight Savings: Lower launch costs or increased payload capacity provide substantial economic benefits.
- Performance Improvements: Enhanced thermal management can improve mission reliability and lifespan.
- Del Konsolidering: Reduced assembly time, complexity, and inventory costs.
- Tooling Elimination: Avoids high upfront tooling costs, making low-volume production economically feasible.
Understanding the specific cost drivers and realistic lead times associated with metal AM for components like thermal insulation plates allows aerospace companies to make informed decisions, budget accurately, and fully appreciate the broader value proposition beyond just the component price tag. Engaging with knowledgeable suppliers who provide transparent aerospace component pricing and realistic timelines is key to successful project execution.
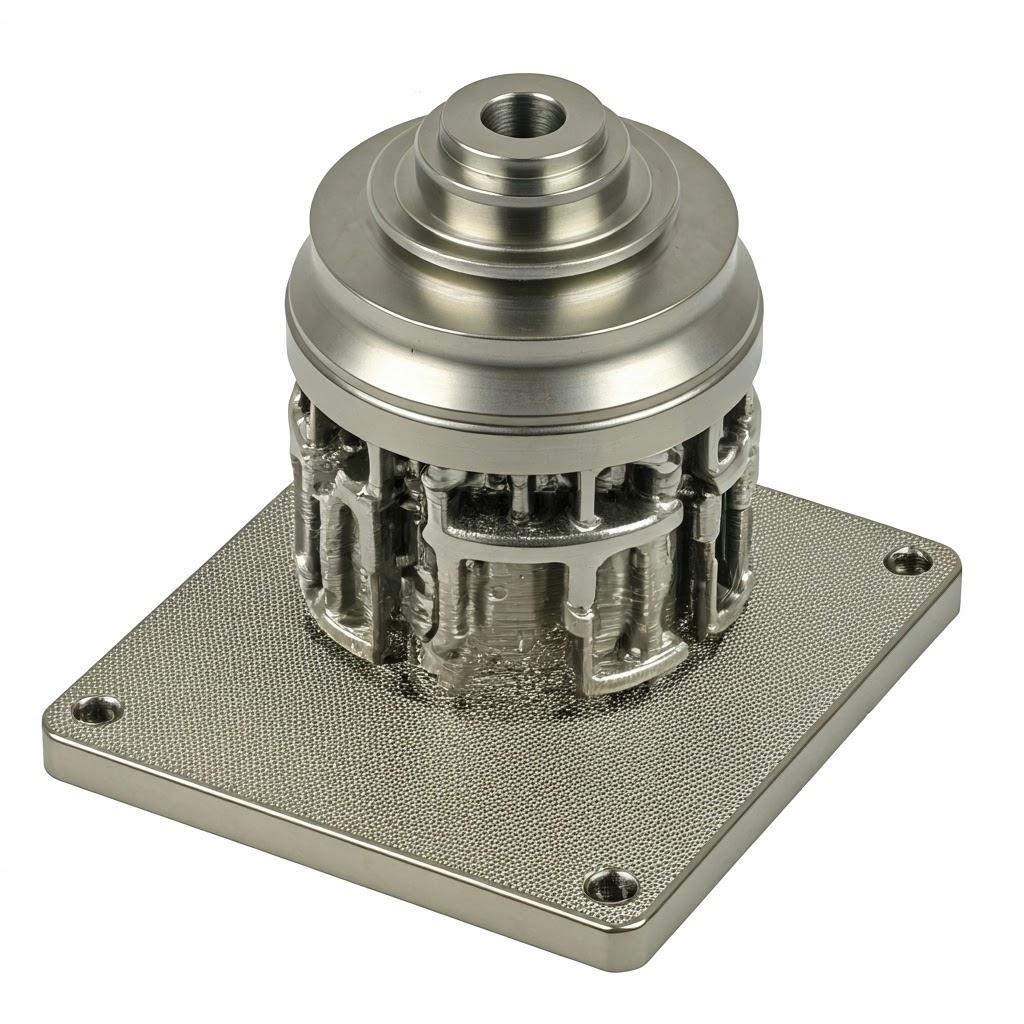
Frequently Asked Questions (FAQ) about Metal AM for Space Insulation
As metal additive manufacturing becomes more prevalent in the aerospace industry, engineers, designers, and procurement specialists often have specific questions about its application for components like thermal insulation plates. Here are answers to some common queries:
1. What are the typical thermal conductivity values achievable with AM IN625 and AlSi10Mg insulation plates, especially considering lattice structures?
- Base Material Properties: The inherent thermal conductivity (λ) of the base material remains the primary factor. As mentioned earlier, wrought IN625 typically has λ≈10−15 W/m·K, while AlSi10Mg has λ≈120−150 W/m·K at room temperature. AM versions generally exhibit similar conductivity, though minor variations can occur due to microstructure differences.
- Impact of Lattice Structures: Incorporating lattice structures thermal is a key strategy to significantly reduce the effektiv thermal conductivity of a component made from a relatively conductive material like AlSi10Mg, or to further enhance the insulating properties of IN625. By replacing solid material with a network of thin struts and voids, the path for heat conduction becomes much more tortuous, and radiation/convection within the lattice pores also plays a role.
- Achievable Reduction: The exact reduction depends heavily on the lattice topology (e.g., Octet, Kelvin Cell, TPMS Gyroid), relative density (percentage of solid material), strut thickness, and material. Reductions in effective thermal conductivity by factors of 5, 10, or even more compared to the solid material are possible, potentially bringing the effective λ of an AlSi10Mg lattice structure down significantly, while still retaining useful structural properties.
- Verification: Predicting the precise effective thermal conductivity requires thermal simulation (FEA) of the specific lattice geometry or, ideally, experimental testing of representative coupons manufactured using the same AM process and parameters as the final part. Suppliers with strong engineering support may assist with this analysis.
2. Can complex internal features, like cooling channels or heat pipes, be reliably integrated and verified in AM insulation plates?
- AM Capability: Yes, integrating complex cooling channels AM or designing cavities for later insertion of heat pipe wicks/envelopes is one of the major strengths of metal additive manufacturing. AM allows for smooth, organically shaped channels that follow optimal paths, which are often impossible to create with traditional drilling or machining. This enables highly efficient, localized thermal management integrated directly within the insulation plate structure.
- Designöverväganden: Key design challenges include ensuring self-supporting channel geometries (or designing effective internal supports) and, critically, ensuring that all unfused powder can be removed from these channels after the build. Design rules often involve minimum channel diameters (e.g., >1-2 mm), smooth curves, avoiding sharp corners where powder can get trapped, and designing access ports for powder removal (e.g., using compressed air, vibration).
- Verification: Ensuring channels are clear and dimensionally accurate is paramount. NDT inspection aerospace methods, particularly industrial CT scanning, are invaluable for this. CT scans can visualize the internal channels in 3D, confirm they are free of powder, measure critical dimensions, and detect any potential defects like cracks or porosity along the channel walls. Functional flow tests may also be required depending on the application.
3. How does the cost of metal AM compare to traditional CNC machining for low-volume, complex spacecraft insulation plates?
- Complexity is Key: Den cost comparison AM vs CNC space parts hinges heavily on part complexity and production volume.
- High Complexity / Low Volume (1-50 parts): For highly complex insulation plates involving topology optimization, internal lattices, conformal shapes, or integrated features, metal AM is often more cost-effective than CNC machining. This is because AM avoids the high cost and lead time of specialized tooling/fixtures, minimizes material waste (CNC has high buy-to-fly ratios for complex parts), and enables part consolidation, reducing assembly costs. Machining such complex geometries from a solid block would require multi-axis machines, extensive programming time, and generate significant scrap.
- Simple Geometry / Low Volume: For relatively simple plate geometries that can be easily machined from standard stock, CNC machining might be cheaper per part, even at low volumes, due to lower machine hour rates and potentially less expensive raw material forms (billet vs. powder).
- Higher Volumes: As production volume increases, the per-part cost of CNC machining typically drops more significantly than AM due to economies of scale and amortization of programming/setup time. AM costs decrease less dramatically with volume. The crossover point depends entirely on the specific part geometry and complexity.
- Other Factors: Consider the total cost of ownership, including development time (AM is faster for iterations), potential weight savings (launch cost reduction), and performance gains enabled by AM’s design freedom. For many advanced spacecraft applications where complexity, weight, and performance are critical, AM provides superior value despite potentially comparable or even higher initial per-part costs in some scenarios. Exploring a supplier’s product offerings, including various materials and printing options, can help determine the best approach.
Answering these FAQ about Metal AM for Space Insulation highlights the nuanced considerations involved in applying this technology. Consulting with experienced AM providers is crucial for navigating material choices, design optimization, verification strategies, and cost-benefit analyses specific to your application.
Conclusion: Advancing Space Exploration with Metal AM Thermal Solutions
The hostile environment of space demands relentless innovation in spacecraft design, particularly in the critical area of thermal management. As we’ve explored throughout this discussion, metal additive manufacturing has emerged as a powerful enabling technology, fundamentally changing how engineers approach the design and production of essential components like thermal insulation plates for space systems. By moving beyond the constraints of traditional manufacturing, metal AM offers a compelling suite of advantages perfectly aligned with the needs of the aerospace industry.
The ability to leverage avancerade material like the high-temperature resilience of IN625 or the lightweight efficiency of AlSi10Mg is just the starting point. The true transformative power of metal AM lies in its unparalleled design freedom. Engineers can now create highly komplexa geometrier, including conformal shapes, internal cavities, and sophisticated lattice structures thermal, optimizing plates for both thermal insulation and structural performance simultaneously. This capability, combined with topologioptimering, facilitates significant lättviktande – a paramount objective in reducing launch costs and maximizing mission capability. Furthermore, the potential for delkonsolidering, merging brackets, standoffs, and insulation into single, monolithic components, enhances reliability while reducing assembly time and complexity.
However, realizing these benefits requires more than just access to a 3D printer. It demands a holistic approach encompassing Design för additiv tillverkning (DfAM) principles, meticulous process control, appropriate efterbearbetning techniques (including heat treatment and surface finishing), and rigorous kvalitetssäkring incorporating NDT methods like CT scanning. Overcoming inherent challenges such as residual stress, porosity, and achieving tight tolerances necessitates deep expertise and advanced technological capabilities.
This underscores the critical importance of strategic supplier selection. Partnering with a knowledgeable and experienced metal AM provider, one that possesses not only state-of-the-art equipment (like SEBM skrivare known for managing thermal stress) but also profound material expertise, robust quality systems (like AS9100 certification), and comprehensive engineering support, is fundamental to success. Companies like Met3dp, which offer end-to-end solutions encompassing the production of metallpulver av hög kvalitet, advanced printing technologies, and dedicated application development services, are positioned as key enablers for aerospace companies seeking to harness the full potential of metal AM innovation aerospace.
Den future of space manufacturing will undoubtedly see increasing adoption of additive manufacturing. For thermal insulation plates and countless other spacecraft components, metal AM provides a pathway to creating lighter, more efficient, more reliable systems, faster than ever before. It allows engineers to design for optimal function, unbound by many traditional manufacturing limitations, ultimately contributing to more ambitious and successful space exploration missions. By embracing metal AM and collaborating with expert partners, the aerospace industry can continue to push the boundaries of what’s possible, reaching further into the cosmos with systems built upon the foundation of additive innovation. To begin exploring how these advanced capabilities can benefit your next aerospace project, contact Met3dp today.
Dela på
MET3DP Technology Co, LTD är en ledande leverantör av lösningar för additiv tillverkning med huvudkontor i Qingdao, Kina. Vårt företag är specialiserat på 3D-utskriftsutrustning och högpresterande metallpulver för industriella tillämpningar.
Förfrågan för att få bästa pris och anpassad lösning för ditt företag!
Relaterade artiklar
Om Met3DP
Senaste uppdateringen
Vår produkt
KONTAKTA OSS
Har du några frågor? Skicka oss meddelande nu! Vi kommer att betjäna din begäran med ett helt team efter att ha fått ditt meddelande.
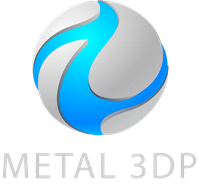
Metallpulver för 3D-printing och additiv tillverkning