3D Printed Thermocouple Housings for Jet Engines
Innehållsförteckning
The aerospace industry operates at the cutting edge of engineering, demanding components that meet extreme performance, reliability, and safety standards. Jet engines, the heart of modern aircraft, are marvels of complex machinery operating under intense heat, pressure, and vibration. Within this demanding environment, even seemingly small components play critical roles. One such crucial part is the thermocouple housing, responsible for protecting sensitive temperature sensors vital for monitoring engine health and optimizing performance. Traditionally manufactured through casting or complex machining, producing these housings involves significant challenges, including design limitations, long lead times, and material waste.
However, a transformative technology is reshaping how these critical components are designed and produced: Additiv tillverkning av metall (AM), commonly known as metal 3D-utskrifter. This innovative approach offers unprecedented design freedom, faster development cycles, and the ability to utilize advanced materials perfectly suited for the harsh conditions inside a jet engine. For engineers seeking performance improvements and procurement managers focused on efficient and reliable sourcing, metal AM presents a compelling value proposition.
This blog post delves into the specifics of using metal 3D printing for jet engine thermocouple housings. We will explore their critical function, the significant advantages AM offers over conventional methods, the ideal high-performance materials like IN718 and 316L, and crucial considerations for design, manufacturing, and supplier selection. Understanding these aspects is key for aerospace manufacturers, MRO (Maintenance, Repair, and Overhaul) providers, and component suppliers looking to leverage the power of additive manufacturing for next-generation aerospace hardware. As a leader in industrial metal AM solutions, Met3dp provides both advanced printing systems and high-quality metal powders, empowering companies to harness the benefits of this technology. We bring decades of collective expertise to help organizations implement 3D printing and accelerate their digital manufacturing transformations.
The Critical Role of Thermocouple Housings in Jet Engines: Function and Importance in Aerospace Safety and Performance
To appreciate the significance of leveraging advanced manufacturing for thermocouple housings, one must first understand their vital role within the complex ecosystem of a jet engine. A thermocouple itself is a sensor used to measure temperature. It typically consists of two dissimilar electrical conductors forming an electrical junction. The temperature change at the junction induces a voltage, which can be interpreted to read the temperature accurately. In a jet engine, precise temperature monitoring is not just beneficial – it’s absolutely critical for several reasons:
- Optimering av prestanda: Engine control systems rely on accurate temperature data from various stages (compressor, combustion chamber, turbine) to optimize fuel burn, thrust output, and overall efficiency. Maintaining temperatures within optimal ranges ensures the engine performs as designed.
- Safety and Engine Health Monitoring: Deviations from normal operating temperatures can indicate potential problems, such as combustion instabilities, cooling system malfunctions, or component degradation. Early detection through accurate thermocouple readings allows for timely maintenance interventions, preventing catastrophic failures. Monitoring Exhaust Gas Temperature (EGT) is particularly crucial.
- Component Lifespan Management: Many engine components have temperature limits. Consistently operating below these limits, verified by thermocouples, extends the life of expensive parts like turbine blades. Over-temperature conditions can drastically shorten component life.
- Efterlevnad av regelverk: Aviation authorities mandate strict monitoring and control of engine parameters, including temperature, to ensure flight safety.
Given the importance of the sensor, the thermocouple housing serves as its essential protector and interface. Its primary functions include:
- Environmental Protection: Shielding the delicate thermocouple junction and wiring from the extreme environment inside the engine – temperatures exceeding 1000∘C (1832∘F) in hot sections, high pressures, corrosive gases, and intense vibrations.
- Secure Mounting: Providing a stable and reliable mounting point to position the thermocouple sensor accurately within the gas path or on a specific engine casing. The mounting must withstand engine vibrations and thermal expansion/contraction.
- Sealing: Preventing gas path leaks where the housing penetrates engine casings, ensuring engine pressure and efficiency are maintained.
- Termisk hantering: In some designs, the housing might play a role in managing heat flow to or from the sensor itself, ensuring measurement accuracy.
- Electrical Isolation/Conduction: Depending on the design, ensuring proper electrical grounding or isolation.
The housing, therefore, is not merely a bracket; it’s an engineered component that must maintain its structural integrity, sealing capability, and mounting stability under some of the most demanding conditions found in modern engineering. Failure of the housing can lead to sensor damage, inaccurate readings, gas leaks, or even the housing itself becoming debris within the engine – all with potentially severe consequences. This underscores the need for robust design, high-quality materials, and advanced manufacturing processes capable of meeting these stringent requirements, making it a prime candidate for the capabilities offered by 3D-utskrift av metall.
Why Metal 3D Printing is Taking Flight for Thermocouple Housings: Advantages Over Traditional Manufacturing for Aerospace Suppliers
For decades, thermocouple housings were primarily produced using investment casting or extensive CNC machining from wrought billets. While proven, these traditional methods carry inherent limitations, particularly when addressing the aerospace industry’s push for lighter, more complex, and rapidly developed components. Metal additive manufacturing offers a paradigm shift, presenting significant advantages that are compelling for aerospace engineers, manufacturers, and suppliers:
Limitations of Traditional Methods:
- Design Constraints: Casting requires molds and patterns, limiting geometric complexity (e.g., internal channels, thin walls, intricate features). Machining, while precise, can struggle with complex internal features and generates significant material waste (buy-to-fly ratio).
- Tooling Costs & Lead Times: Investment casting requires expensive and time-consuming tooling creation. Machining complex parts may require multiple setups and specialized fixtures. This makes low-volume production or design iteration slow and costly.
- Part Consolidation Challenges: Housings often involve multiple brazed or welded sub-components (flanges, bosses, bodies), increasing manufacturing steps, weight, and potential failure points.
- Materialavfall: Subtractive manufacturing (machining) can waste a substantial amount of expensive aerospace-grade material.
Advantages of Metal Additive Manufacturing (AM):
Metal AM processes, such as Selective Laser Melting (SLM) or Electron Beam Melting (EBM), build parts layer by layer directly from metal powder, offering solutions to these challenges:
- Oöverträffad designfrihet:
- Komplexa geometrier: AM excels at creating intricate shapes, undercuts, and internal features that are difficult or impossible to cast or machine. This allows for optimized flow paths around the sensor, integrated mounting features, or conformal cooling channels if needed.
- Topology Optimization & Lightweighting: Engineers can use software tools to remove material from non-critical areas, creating lighter housings without compromising strength, contributing to overall aircraft fuel efficiency.
- Del Konsolidering: Multiple components of a traditional housing assembly can be redesigned and printed as a single, monolithic part. This reduces part count, eliminates brazing/welding steps, simplifies assembly, reduces weight, and potentially increases reliability by removing joints.
- Reduced Lead Times & Faster Iteration:
- Tooling Elimination: AM builds directly from a digital CAD file, eliminating the need for physical tooling. This dramatically cuts lead times, especially for prototypes, custom designs, or low-volume production runs.
- Snabb prototypframtagning: Design modifications can be implemented quickly by simply changing the CAD file and printing a new iteration, accelerating the development and qualification process.
- Materialeffektivitet: AM is an additive process, using only the material necessary to build the part and its supports. This significantly reduces material waste compared to subtractive machining, which is particularly beneficial when using expensive superalloys like IN718.
- Enhanced Performance Potential: Complex internal geometries enabled by AM can potentially improve the housing’s function, for example, by optimizing airflow around the sensor for faster response times or incorporating features that improve vibration damping.
- Flexibilitet i leveranskedjan:
- Tillverkning på begäran: Parts can be printed as needed, reducing inventory requirements for spares.
- Distributed Manufacturing: Digital part files can be sent electronically to certified AM facilities globally for localized production.
Table: AM vs. Traditional Manufacturing for Thermocouple Housings
Funktion | Additiv tillverkning av metall (AM) | Traditional (Casting/Machining) | B2B Supplier Advantage (AM) |
---|---|---|---|
Designfrihet | High (complex geometries, internal channels, consolidation) | Moderate to Low (tooling/machining constraints) | Offer highly optimized, consolidated, lightweight solutions |
Verktyg | None (digital file-based) | Required (molds, patterns, complex fixtures) | Faster NPI (New Product Introduction), lower initial setup cost |
Ledtid | Short (especially for prototypes, low volume) | Long (tooling creation, multi-step processes) | Rapid response to customer needs, faster time-to-market |
Material Avfall | Låg (additiv process) | High (machining) or Moderate (casting feeders/gates) | Cost savings on expensive raw materials, greener process |
Konsolidering av delar | Excellent capability | Difficult / Requires assembly steps (brazing, welding) | Simpler BoM, reduced assembly risk, potential reliability gains |
Ideal Volume | Low to Medium, Complex Parts | High Volume (casting), Medium Volume (machining) | Competitive for specialized, high-value aerospace components |
Iteration Speed | Fast (modify CAD, reprint) | Slow (tooling modification or reprogramming) | Agile development, quick adaptation to design changes |
Export to Sheets
For wholesale buyers and procurement managers in the aerospace sector, partnering with an AM supplier like Met3dp means access to cutting-edge manufacturing capabilities that can deliver superior components faster and potentially more cost-effectively (especially when considering total lifecycle cost and performance benefits).
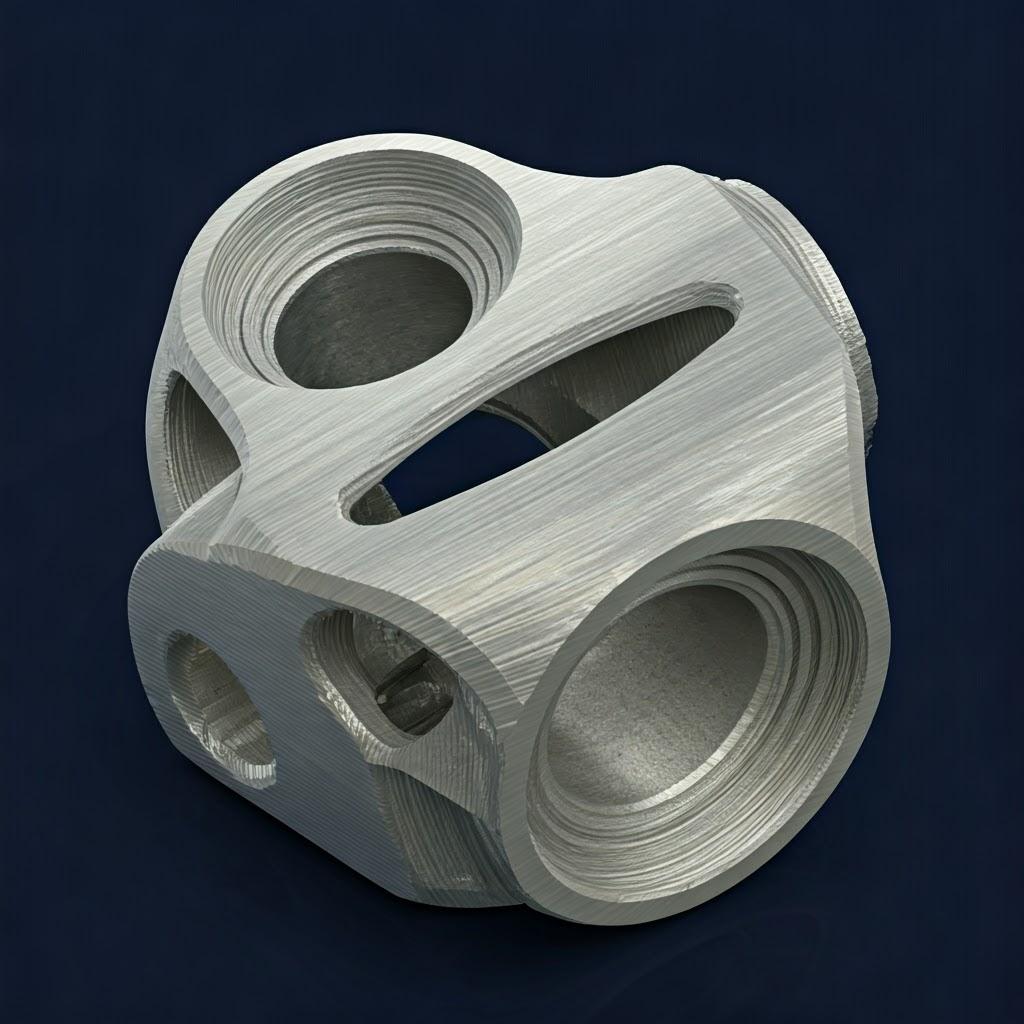
Material Selection Deep Dive: IN718 and 316L for Optimal Performance (Sourcing High-Quality Powders)
Choosing the right material is paramount for components operating within the extreme environment of a jet engine. The material must withstand high temperatures, resist oxidation and corrosion, maintain strength under stress and vibration, and be compatible with the surrounding engine components. For 3D printed thermocouple housings, two materials stand out due to their properties and established use in aerospace and demanding industrial applications: IN718 (Inconel 718) och 316L rostfritt stål. The suitability of each depends on the specific operating conditions and performance requirements of the housing’s location within the engine.
IN718 (Inconel 718): The High-Performance Workhorse
IN718 is a nickel-chromium-based precipitation-hardenable superalloy renowned for its exceptional combination of properties, making it a go-to material for demanding aerospace applications, including parts in the hot sections of jet engines.
- Viktiga egenskaper:
- High Temperature Strength: Maintains excellent tensile, fatigue, creep, and rupture strength at temperatures up to approximately 700∘C (1300∘F).
- Utmärkt korrosionsbeständighet: Resists oxidation and corrosion in aggressive environments, including combustion byproducts.
- God svetsbarhet: Compared to other nickel superalloys, IN718 exhibits relatively good weldability (important for traditional fabrication, less so for monolithic AM parts, but indicates good processing characteristics).
- Processability in AM: Well-characterized and widely used in metal AM processes like SLM and EBM, allowing for the production of dense, high-strength parts.
- Why it Matters for Thermocouple Housings: Its ability to withstand the high temperatures and stresses found in the turbine and exhaust sections of a jet engine makes it ideal for housings located in these critical hot zones. Its strength ensures structural integrity under aerodynamic loads and vibration, while its corrosion resistance protects it from the harsh chemical environment.
316L Stainless Steel: The Versatile and Reliable Option
316L is an austenitic chromium-nickel stainless steel containing molybdenum, which enhances its corrosion resistance, particularly against chlorides and other industrial solvents. It’s widely used across various industries, including aerospace, for components requiring good strength and excellent corrosion resistance at moderate temperatures.
- Viktiga egenskaper:
- Utmärkt korrosionsbeständighet: Superior resistance to general corrosion, pitting, and crevice corrosion compared to 304 stainless steel.
- Good Strength and Ductility: Offers a good balance of mechanical properties at room and moderately elevated temperatures (typically up to around 550∘C / 1022∘F, though strength decreases significantly above 425∘C / 800∘F).
- God formbarhet och svetsbarhet: Easily processed using various techniques.
- Kostnadseffektivitet: Generally less expensive than nickel-based superalloys like IN718.
- Well-Established in AM: Commonly used and well-understood in metal 3D printing processes.
- Why it Matters for Thermocouple Housings: For housings located in cooler sections of the engine (e.g., compressor stages, bypass ducts, or external casings) where temperatures are less extreme but corrosion resistance and reliability are still crucial, 316L offers a robust and more economical solution compared to IN718.
Table: Material Comparison for Thermocouple Housings
Funktion | IN718 (Nickel Superalloy) | 316L rostfritt stål | Considerations for Sourcing |
---|---|---|---|
Max Operating Temp. | ~ 700∘C (1300∘F) | ~ 425−550∘C (800−1022∘F) | Match material to specific engine zone requirements |
High-Temp Strength | Utmärkt | Måttlig | Critical for hot section components |
Motståndskraft mot korrosion | Utmärkt | Excellent (especially chlorides) | Both offer good resistance; specific needs may vary |
Relativ kostnad | Hög | Måttlig | Budget implications for bulk procurement |
Täthet | ~ 8.19g/cm3 | ~ 8.0g/cm3 | Minor difference, but relevant for lightweighting |
AM Processability | Well-established | Well-established | Ensure supplier has proven parameters for chosen material |
Typical Engine Location | Turbine section, Combustor casing, Exhaust | Compressor section, Fan casing, Bypass duct | Select based on thermal and mechanical loads |
Export to Sheets
The Critical Importance of Powder Quality
Regardless of the chosen alloy, the quality of the metal powder used in the AM process is fundamental to achieving the desired mechanical properties and integrity of the final part. For aerospace applications, this is non-negotiable. Key powder characteristics include:
- Sfäriskhet: Highly spherical powder particles ensure good flowability and high packing density in the powder bed, leading to denser, stronger final parts with fewer voids or defects.
- Fördelning av partikelstorlek (PSD): A controlled PSD is crucial for consistent melting and layer deposition. Different AM machines are optimized for specific PSD ranges.
- Renhet: Low levels of impurities (like oxygen, nitrogen, carbon) and absence of contaminants are vital. Impurities can degrade mechanical properties and corrosion resistance.
- Flytbarhet: Powder must flow evenly and smoothly within the printer’s recoating system to create uniform layers.
Met3dp: Your Source for High-Quality Aerospace Powders
At Met3dp, we understand that exceptional parts start with exceptional materials. Our company employs industry-leading powder production technologies, including Atomisering av gas (GA) och Process med roterande elektrod och plasma (PREP), to manufacture high-quality spherical metal powders specifically optimized for additive manufacturing.
- Our advanced gas atomization equipment utilizes unique nozzle and gas flow designs to produce metallic spheres with high sphericity and excellent flowability, crucial for achieving superior part density and mechanical properties in demanding applications like jet engine components.
- We offer a comprehensive portfolio of high-performance metal powders, including IN718 och 316L, rigorously tested and quality-controlled to meet the stringent requirements of the aerospace industry.
- Beyond these, Met3dp also produces innovative alloys like TiNi, TiTa, TiAl, TiNbZr, CoCrMo, other stainless steels, and superalloys, showcasing our broad materials expertise.
Choosing a supplier like Met3dp ensures that the foundational element of your 3D printed thermocouple housing – the metal powder – meets the highest standards, enabling the production of reliable, high-performance components suitable for mission-critical aerospace use. Procurement managers and engineers can rely on Met3dp for consistent quality and supply of these advanced materials, backed by deep expertise in additive manufacturing processes and applications.
Design for Additive Manufacturing (DfAM): Optimizing Thermocouple Housing Geometry for Performance and Printability
One of the most compelling reasons aerospace manufacturers turn to metal additive manufacturing is the potential to radically rethink component design. Simply replicating a design originally intended for casting or machining often fails to leverage the full capabilities of AM. Design för additiv tillverkning (DfAM) is a crucial methodology that involves designing parts specifically for the layer-by-layer building process, unlocking benefits in performance, weight, and manufacturability. For jet engine thermocouple housings, applying DfAM principles can lead to significantly improved components.
Key DfAM Principles for Thermocouple Housings:
- Leveraging Geometric Complexity:
- Integrated Features: AM allows the seamless integration of features that would typically be separate parts or require complex machining. For a thermocouple housing, this could mean printing mounting flanges, sensor bosses, wire routing channels, or even anti-rotation features directly into the main body.
- Optimized Internal Structures: If required, complex internal channels for cooling airflow around the sensor or specific flow paths for calibration gases can be designed and printed – features often impossible with traditional methods.
- Thin Walls & Complex Curvatures: AM can produce parts with thinner walls (where structurally appropriate) and complex, organic shapes that follow stress lines, potentially reducing weight and improving aerodynamic interaction within the engine gas path.
- Del Konsolidering:
- Reducing Assembly Complexity: Traditional thermocouple housings might consist of a body, a flange, a threaded boss, and perhaps cover plates, often joined by brazing or welding. Each joint represents a potential failure point and adds manufacturing steps and tolerance stack-up.
- AM Advantage: DfAM encourages redesigning this assembly as a single, monolithic component. Printing the housing as one piece eliminates joining processes, reduces part count in the Bill of Materials (BOM), simplifies inventory and assembly, lowers overall weight, and inherently increases structural integrity by removing joints. This is a significant advantage for procurement seeking streamlined logistics and engineers aiming for enhanced reliability.
- Topology Optimization & Lightweighting:
- Intelligent Material Placement: Using specialized software, engineers can define load cases and boundary conditions for the housing. The software then iteratively removes material from areas experiencing low stress, leaving material only where it’s structurally necessary.
- Result: This often results in organic-looking, highly optimized structures that meet or exceed the strength requirements of the original design but with significantly less weight. Even small weight savings per component add up considerably across an entire engine, contributing to improved fuel efficiency and performance – key drivers in aerospace.
- Designing for Printability:
- Bygg orientering: How the part is oriented on the build plate significantly impacts support needs, surface finish, print time, and residual stress accumulation. DfAM involves considering the optimal orientation early in the design phase.
- Minimizing Supports: Support structures are often necessary for features overhanging the build plate at angles typically less than 45 degrees from horizontal. Supports consume extra material, add print time, require removal (post-processing), and can leave witness marks on the surface. Good DfAM practice involves:
- Designing features with self-supporting angles (>= 45 degrees) where possible.
- Using chamfers instead of sharp overhangs.
- Orienting the part to minimize critical surfaces facing downwards.
- Designing internal channels that are self-supporting or allow for easy powder removal.
- Planning for Post-Processing: Ensuring access for support removal tools and CNC machining fixtures if required. Designing sacrificial features that aid printing or post-processing but are removed later.
- Managing Thermal Stress:
- Feature Design: Sharp corners can concentrate stress during the rapid heating and cooling cycles of AM. Incorporating fillets and rounded edges can help distribute stress more evenly, reducing the risk of distortion or cracking.
- Material Distribution: Large, bulky sections connected to thin sections can exacerbate thermal stresses. DfAM encourages smoother transitions in material thickness.
Applying DfAM requires a different mindset than designing for traditional manufacturing. It necessitates close collaboration between design engineers and AM process experts. Partnering with a knowledgeable AM service provider who understands DfAM principles is crucial to fully realize the benefits of printing thermocouple housings and other critical components.
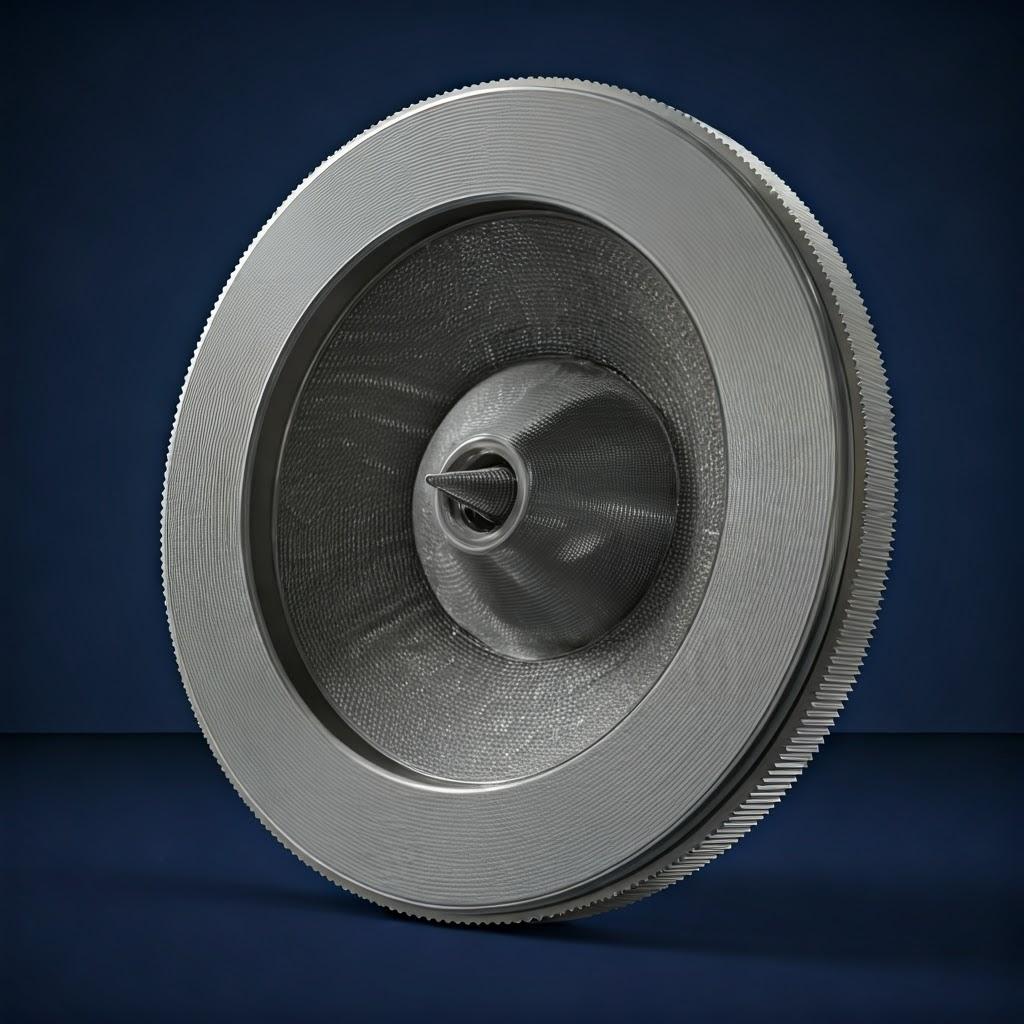
Achieving Precision: Tolerance, Surface Finish, and Dimensional Accuracy Standards in Metal AM
While AM offers design freedom, components destined for jet engines must meet stringent requirements for fit, form, and function. This means achieving specific levels of precision regarding tolerances, surface finish, and overall dimensional accuracy. Understanding the capabilities and limitations of metal AM in these areas is vital for engineers and procurement managers.
Tolerances:
- General Achievability: Typical “as-built” tolerances for metal AM processes like SLM and EBM are often in the range of ±0.1 mm to ±0.2 mm (±0.004″ to ±0.008″) for smaller features, potentially increasing slightly for larger dimensions due to thermal effects. However, this can vary significantly based on:
- AM System: The specific machine, its calibration, and beam focus quality.
- Material: Different alloys exhibit varying shrinkage and warping behavior.
- Part Geometry & Size: Larger parts or complex geometries are more prone to thermal distortion.
- Build Parameters: Laser/electron beam power, scan speed, layer thickness, etc.
- Efterbearbetning: Stress relief and HIP can cause minor dimensional changes.
- Critical Dimensions: For features requiring tighter tolerances – such as mounting interfaces, sealing surfaces, or precise internal diameters for sensor fit – post-process CNC machining is almost always necessary. AM is used to create the near-net shape efficiently, and machining provides the final precision.
- DfAM Consideration: Tolerances should be considered during the design phase. Identify critical features requiring tight tolerances and ensure the design allows for access for subsequent machining operations.
Surface Finish (Roughness):
- As-Built Finish: The surface finish of as-built metal AM parts is inherently rougher than machined surfaces. Typical Ra (average roughness) values can range from 6 µm to 20 µm (240 µin to 800 µin) or more, depending on:
- Bygg orientering: Top-facing surfaces (up-skins) tend to be smoother, while side walls show layer lines, and down-facing surfaces (down-skins) supported by structures are typically the roughest after support removal.
- Powder Size: Finer powders generally lead to smoother finishes but may process differently.
- Process Parameters: Layer thickness, energy input, and scan strategy influence the melt pool behavior and resulting surface.
- Importance for Housings: Rough surfaces can be problematic for sealing applications (e.g., flange faces) and may act as stress concentrators, potentially impacting fatigue life. Internal surfaces may require smoothness for flow or to prevent particle trapping.
- Förbättra ytfinishen: Post-processing steps like bead blasting, tumbling, polishing, or CNC machining are used to achieve the required surface finish on critical areas.
Dimensionell noggrannhet:
- Definition: How closely the final printed part conforms to the nominal dimensions specified in the CAD model.
- Influencing Factors: Similar to tolerance, accuracy is affected by machine calibration, material properties, thermal management during the build, support strategy, and post-processing steps (especially stress relief and HIP which can cause predictable shrinkage).
- Achieving Accuracy: Requires meticulous process control, well-characterized material parameters, and often, compensation factors built into the print file to account for expected thermal effects. Experienced AM providers utilize simulation tools and empirical data to maximize dimensional accuracy.
Met3dp’s Commitment to Precision:
At Met3dp, we recognize that precision is critical for aerospace components. Our industrial 3D printing systems are designed to deliver industry-leading accuracy and reliability. We employ rigorous process controls, machine calibration protocols, and optimized parameters developed through extensive testing for materials like IN718 and 316L. While we achieve excellent as-built precision, we also work closely with clients to integrate necessary post-processing steps, ensuring that critical tolerances and surface finishes on components like thermocouple housings meet the demanding specifications of the aerospace industry.
Beyond the Print: Essential Post-Processing Steps for Mission-Critical Jet Engine Housings
A common misconception about metal 3D printing is that parts are ready to use immediately after the build process finishes. For non-critical applications, this might sometimes be the case, but for high-performance, mission-critical components like jet engine thermocouple housings, the “as-built” part is merely an intermediate stage. A series of essential post-processing steps are required to ensure the part meets dimensional specifications, achieves the desired material properties, and is free from defects.
Common Post-Processing Workflow for AM Thermocouple Housings:
- Powder Removal:
- Process: Carefully removing unfused powder from the part surface and any internal channels or cavities, typically using compressed air, brushing, or specialized powder handling stations.
- Importance: Ensures no loose powder remains, which could contaminate engine systems or interfere with subsequent processes. DfAM plays a role here in designing easily clearable channels.
- Stress Relief Heat Treatment:
- Process: Heating the part (often while still attached to the build plate) in a controlled atmosphere furnace to a specific temperature below the aging or annealing temperature, holding it, and then slowly cooling it.
- Importance: The rapid heating and cooling during AM builds significant internal stresses. Stress relief reduces these stresses, preventing distortion during support removal or machining and improving dimensional stability and overall part integrity. This is a critical first step.
- Part Removal from Build Plate:
- Process: Separating the printed part(s) from the metal build plate, typically using wire EDM (Electrical Discharge Machining) or a bandsaw.
- Importance: Frees the part for subsequent handling and processing. Requires care to avoid damaging the part.
- Borttagning av stödstruktur:
- Process: Removing the support structures generated during the print, using manual methods (breaking, cutting, grinding), CNC machining, or sometimes electrochemical polishing.
- Importance: Supports are necessary for printing but are not part of the final component. Removal must be done carefully to avoid damaging the part surface, especially near critical features. The surface where supports were attached is typically rough and may require further finishing.
- Solution Annealing / Aging Heat Treatment (Material Specific, e.g., for IN718):
- Process: Subjecting the part to specific, tightly controlled thermal cycles (heating to high temperatures, quenching, then aging at intermediate temperatures).
- Importance: This develops the desired microstructure and precipitates (in the case of precipitation-hardenable alloys like IN718) required to achieve the final specified mechanical properties (hardness, tensile strength, creep resistance). Parameters are alloy-specific and critical for performance.
- Het isostatisk pressning (HIP):
- Process: Placing parts in a specialized vessel and subjecting them simultaneously to high inert gas pressure (e.g., 100-200 MPa) and elevated temperature (below melting point) for a set duration.
- Importance: This process effectively closes internal microporosity that can be present even in well-printed AM parts. Eliminating porosity significantly improves fatigue strength, ductility, and overall material integrity. HIP is often mandated by aerospace standards (like AS9100) for critical flight components.
- CNC Machining:
- Process: Using traditional subtractive machining (milling, turning, drilling, tapping) to achieve tight tolerances on critical dimensions, create precise sealing surfaces, machine threads, and improve surface finish on specific features.
- Importance: Bridges the gap between AM’s near-net shape capability and the final dimensional and surface finish requirements that AM alone cannot typically meet for critical interfaces.
- Ytbehandling:
- Process: Employing techniques like bead blasting, shot peening (can improve fatigue life), abrasive flow machining (AFM) for internal channels, polishing, or electropolishing.
- Importance: Improves overall surface quality, removes contaminants, achieves specific roughness values (Ra), and can prepare surfaces for subsequent coatings if required.
- Cleaning and Inspection:
- Process: Thoroughly cleaning the parts to remove any residual powder, machining fluids, or debris. Followed by rigorous inspection using various methods.
- Importance: Final verification before the part is certified for use. Inspection methods are discussed under “Challenges.”
The extent and sequence of these steps depend on the material, design complexity, and specific requirements of the thermocouple housing. Partnering with a full-service provider experienced in these post-processing techniques is crucial for obtaining flight-ready AM components.
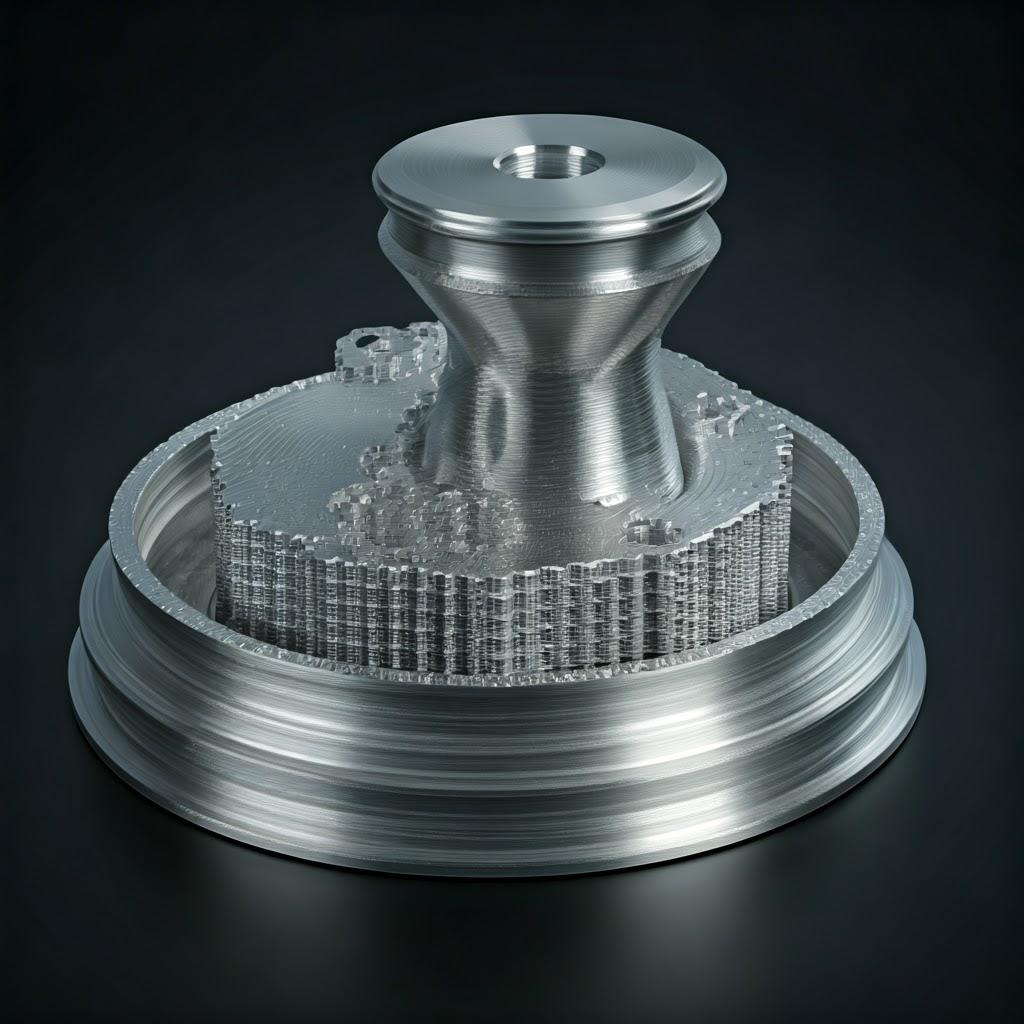
Navigating Challenges: Overcoming Potential Issues in 3D Printing Thermocouple Housings (Quality Control for Industrial Supply)
While metal AM offers numerous advantages, it’s also a complex process with potential challenges that must be understood and mitigated, especially when manufacturing parts for safety-critical aerospace applications. Ensuring consistent quality and reliability for industrial supply requires robust process control and effective solutions to common issues.
Common Challenges and Mitigation Strategies:
- Residual Stress, Warping, and Distortion:
- Cause: Uneven heating and cooling inherent in the layer-wise process creates internal stresses that can cause parts to warp or deviate from the intended geometry, especially after removal from the build plate.
- Mitigation:
- Process Simulation: Using software to predict stress accumulation and distortion before printing.
- Optimized Parameters: Fine-tuning laser/beam power, scan strategy, and potentially preheating the build chamber (common in EBM).
- Smart Support Strategy: Designing robust supports to anchor the part and dissipate heat effectively.
- DfAM: Designing parts with features that minimize stress concentration (e.g., fillets, gradual thickness changes).
- Mandatory Stress Relief: Performing stress relief heat treatment before removing the part from the build plate.
- Porositet:
- Cause: Small internal voids within the printed material, which can act as crack initiation sites and degrade mechanical properties (especially fatigue life). Caused by trapped gas, incomplete fusion between layers, or powder inconsistencies.
- Mitigation:
- High-Quality Powder: Using powder with high sphericity, controlled PSD, low gas content, and good flowability (like Met3dp’s GA/PREP powders). Proper powder handling to avoid moisture absorption.
- Optimized Process Parameters: Ensuring sufficient energy density and appropriate scan strategies for full melting and fusion.
- Controlled Atmosphere: Maintaining a high-purity inert gas environment (Argon or Nitrogen) in the build chamber to minimize oxidation and gas pickup.
- Het isostatisk pressning (HIP): As mentioned, HIP is highly effective at closing internal gas porosity and improving density. Often required for critical parts.
- Support Removal Issues:
- Cause: Supports necessary for printing overhangs or complex features can be difficult to remove, especially from internal channels or delicate areas, potentially damaging the part or leaving undesirable surface artifacts.
- Mitigation:
- DfAM: Designing parts to be self-supporting where possible, minimizing the need for supports. Orienting the part strategically. Designing supports for easier removal (e.g., with specific interface points).
- Advanced Support Strategies: Using specialized support types (e.g., tree supports, conical supports) that offer stability with easier removal.
- Skilled Technicians: Employing experienced technicians with appropriate tools (hand tools, micro-machining, EDM) for careful support removal.
- Ytjämnhet:
- Cause: Inherent nature of layer-wise fusion, stair-stepping effect on curved surfaces, partially melted powder particles adhering to the surface, support contact points.
- Mitigation:
- Processoptimering: Using finer layer thicknesses (at the cost of build time), optimizing contour scan parameters.
- Bygg orientering: Positioning critical surfaces optimally (e.g., upwards or vertically) for better finish.
- Efterbearbetning: Utilizing machining, polishing, blasting, or AFM as needed to meet surface finish requirements.
- Consistency and Repeatability:
- Utmaning: Ensuring that parts printed in different builds, on different machines, or at different times meet the same specifications consistently – crucial for industrial supply and aerospace qualification.
- Mitigation:
- Robust Quality Management System (QMS): Implementing and adhering to strict quality standards (e.g., AS9100 for aerospace).
- Process Monitoring & Control: Real-time monitoring of key process parameters (laser power, melt pool characteristics, oxygen levels, temperature).
- Machine Calibration: Regular and thorough calibration of AM systems.
- Powder Management: Strict control over powder sourcing, testing, storage, handling, and traceability. Batch testing and recycling protocols.
- Standardized Procedures: Documented procedures for build setup, printing, post-processing, and inspection.
- Inspection and Quality Control (QC):
- Utmaning: Verifying the internal integrity and dimensional accuracy of complex AM parts.
- Metoder:
- Dimensional: Coordinate Measuring Machines (CMM), 3D scanning.
- Materialegenskaper: Tensile testing, hardness testing (often on witness coupons printed alongside the parts).
- Internal Defects (Porosity, Cracks): X-ray Computed Tomography (CT scanning) is invaluable for non-destructively inspecting the internal structure of complex AM parts. Dye penetrant testing (PT) and Magnetic Particle testing (MT) can be used for surface-breaking defects.
- Mikrostruktur: Metallographic analysis of sectioned samples or witness coupons.
Overcoming these challenges requires deep process knowledge, advanced equipment, rigorous quality control, and a commitment to continuous improvement. Aerospace procurement managers should prioritize suppliers like Met3dp who demonstrate expertise in managing these complexities and possess the necessary certifications (e.g., AS9100 or readiness for it) to ensure the delivery of reliable, high-quality thermocouple housings suitable for flight.
Selecting Your Partner: How to Choose the Right Metal 3D Printing Service Provider (Evaluating Suppliers for Aerospace Components)
The success of implementing 3D printed thermocouple housings, or any critical aerospace component, hinges significantly on selecting the right manufacturing partner. The stakes are high in aerospace; therefore, choosing a metal additive manufacturing service provider requires rigorous evaluation beyond just comparing price quotes. Procurement managers and engineers need to assess potential suppliers based on their technical capabilities, quality systems, materials expertise, and understanding of aerospace requirements.
Key Criteria for Evaluating Metal AM Suppliers for Aerospace:
- Aerospace Expertise & Certifications:
- Industry Knowledge: Does the supplier understand the specific demands, regulations (FAA, EASA), and quality expectations of the aerospace industry?
- AS9100 Certification: This is the internationally recognized Quality Management System standard for the Aviation, Space, and Defense industries. Certification (or demonstrable compliance and path towards certification) is often a prerequisite for manufacturing flight hardware. It ensures robust processes for traceability, configuration management, risk management, and more.
- Technical Capabilities & Process Control:
- Appropriate Technology: Do they operate the relevant AM technologies (e.g., SLM, EBM) suitable for IN718 or 316L?
- Equipment Quality & Maintenance: Are their machines well-maintained and regularly calibrated to ensure consistent performance?
- Process Monitoring: Do they employ in-situ monitoring or other techniques to track build consistency?
- Parameter Development: Do they have established, validated build parameters for the specific alloys required?
- Materials Expertise & Quality:
- Proven Material Experience: Demonstrated success printing with aerospace-grade alloys like IN718 and 316L.
- Powder Quality Control: Stringent processes for incoming powder inspection, storage, handling, and traceability. How do they manage powder reuse/recycling to maintain quality? (A supplier like Met3dp, manufacturing its own high-quality powders using advanced GA and PREP methods, offers significant advantages here).
- Material Certification: Ability to provide full material certifications tracing back to the original powder batch.
- Comprehensive Post-Processing Capabilities:
- In-House vs. Managed Services: Do they offer the necessary post-processing steps (stress relief, heat treatment specific to the alloy, HIP, precision machining, NDT) in-house, or do they manage these through a network of qualified and preferably aerospace-certified vendors?
- Integrated Workflow: How seamlessly are these steps integrated into their production process and quality system?
- Robust Quality Management System (QMS):
- Beyond Certification: Look for evidence of a mature QMS in practice – documented procedures, rigorous inspection protocols (including appropriate NDT methods like CT scanning for internal inspection), process validation, statistical process control (SPC) where applicable, and effective handling of non-conformances.
- Engineering & DfAM Support:
- Collaboration: Can their engineering team collaborate effectively on Design for Additive Manufacturing (DfAM) to optimize the housing design for performance and printability?
- Simulation Capabilities: Do they offer simulation services for predicting thermal stress or print outcomes?
- Qualification Support: Can they assist with developing test plans and providing data required for component qualification?
- Capacity, Scalability & Track Record:
- Produktionsvolym: Can they meet your volume requirements, from prototypes to potential series production or bulk orders for MRO spares?
- Reliability: Do they have a proven track record of delivering high-quality parts on time? Request case studies or references, especially within the aerospace or similarly demanding sectors.
Finding the Ideal Partner Profile:
The ideal partner is not just a print bureau but a solutions provider. They possess the certifications, technical expertise, robust quality systems, and collaborative approach necessary to navigate the complexities of aerospace manufacturing. They understand the critical nature of components like thermocouple housings and have the infrastructure to deliver reliable, flight-worthy parts. Companies like Met3dp embody this profile, combining advanced printing technology with in-house production of high-performance metal powders and decades of collective expertise in metal additive manufacturing, ready to partner with organizations to achieve their AM goals.
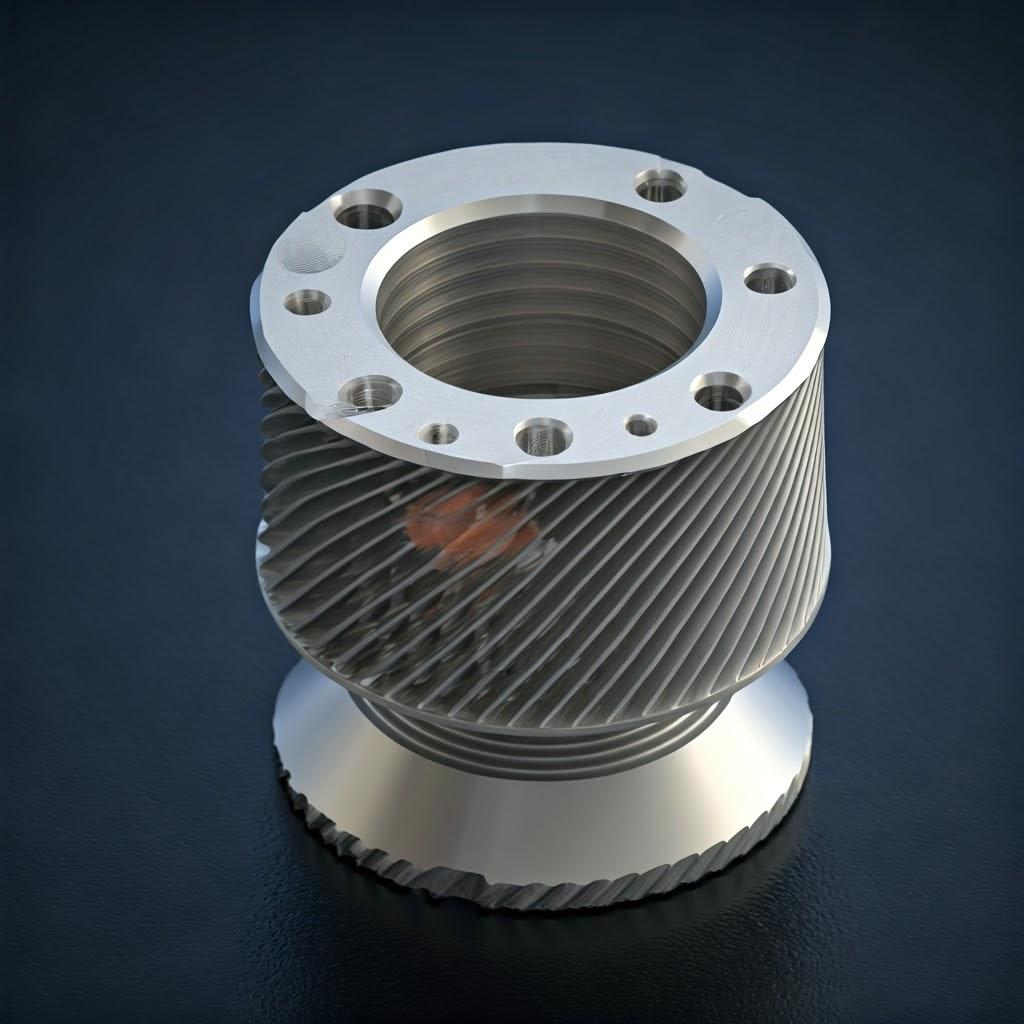
Understanding the Investment: Cost Factors and Lead Times for Industrial Orders and Bulk Procurement
While metal AM offers compelling technical benefits, understanding the cost structure and expected lead times is crucial for project planning and procurement decisions. The economics of AM differ significantly from traditional manufacturing.
Key Cost Drivers for 3D Printed Thermocouple Housings:
- Material Cost:
- Alloy Type: Aerospace-grade powders are expensive. IN718 is substantially more costly than 316L.
- Consumption: Includes the material in the final part plus the material used for support structures. Part design (density, size) directly impacts this.
- Powder Condition: Virgin powder vs. properly recycled powder (which can offer cost savings if managed under strict quality control).
- AM Machine Time:
- Build Duration: A primary cost factor, determined by part volume, height, layer thickness, scan speed, and the number of parts nested onto a single build plate. Larger or more complex parts take longer.
- Machine Hourly Rate: Reflects the capital investment, maintenance, operational costs (power, gas), and operator time.
- Kostnader för arbetskraft:
- Setup & Teardown: Preparing the build file, setting up the machine, and removing the build plate/parts.
- Efterbearbetning: Labor involved in powder removal, support removal, heat treatments, machining setups, finishing, and inspection. Support removal and machining can be labor-intensive.
- Kostnader för efterbearbetning:
- External Services: Costs associated with specialized processes like HIP, specific heat treatments, NDT (especially CT scanning), or advanced machining if outsourced.
- Consumables: Materials used in finishing, cleaning, etc.
- Quality Assurance & Inspection:
- NDT: Non-destructive testing methods add cost but are essential for verifying integrity. CT scanning, while thorough, is more expensive than methods like dye penetrant testing.
- Dimensionell inspektion: CMM or 3D scanning time.
- Documentation: Generating compliance reports and certifications.
- Design & Engineering:
- Initial DfAM: Engineering time required to optimize the design for AM, especially if converting from a traditional design or performing part consolidation.
- Order Volume:
- Amortization: Setup costs (file prep, machine setup) are amortized over the number of parts in a build. Larger batches generally have a lower per-part cost for these fixed elements.
- Nesting: Printing multiple parts simultaneously in one build job optimizes machine time and reduces per-part cost compared to printing single units. Bulk procurement allows for better build planning.
Typical Lead Time Considerations:
Lead times for fully processed and inspected aerospace-grade AM parts are typically measured in weeks, not days. The total time includes:
- Pre-Processing: Order review, DfAM consultation (if needed), build file preparation, job scheduling (1-5 days).
- Tryckning: Dependent on part size, complexity, and quantity per build (1-7 days).
- Efterbearbetning: This is often the most time-consuming phase.
- Stress Relief & Cooldown: (1-2 days)
- Support Removal/Basic Finishing: (1-3 days)
- Heat Treatment / Aging (e.g., IN718): Requires specific furnace cycles (2-5 days including ramp/soak/cool).
- HIP: Requires scheduling at a specialized facility, cycle time itself can be ~1 day, plus transit (3-10 days total).
- CNC Machining: Depends heavily on complexity and shop availability (2-10 days).
- Inspection (NDT, Dimensional): (1-5 days).
- Frakt: (1-5 days depending on location/method).
Total Estimated Lead Time: Typically 3 to 8 weeks, highly variable based on the specific part and required processing steps. Expedited options may be available at a higher cost, but critical processes like heat treatment and HIP have minimum cycle times. Clear communication with the supplier is essential for managing expectations.
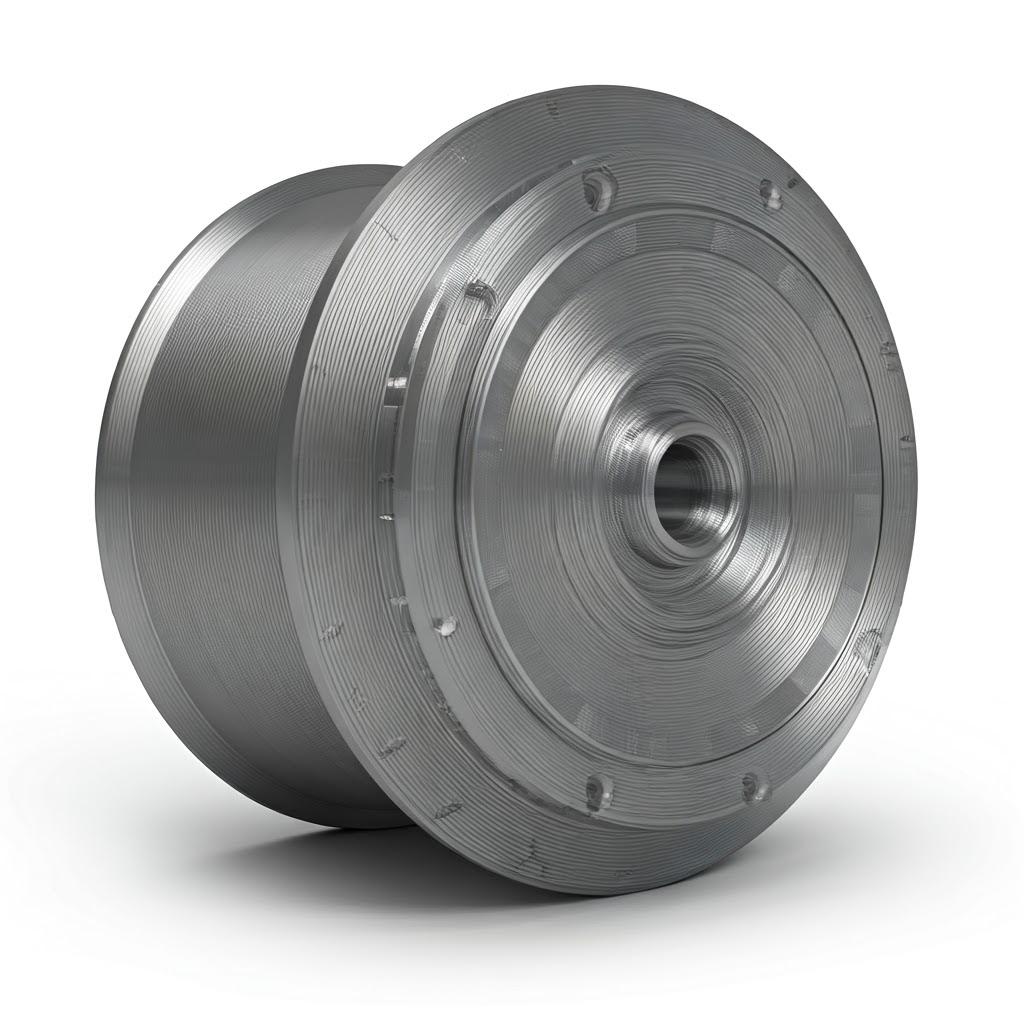
Conclusion: The Future of Aerospace Components is Additive – Partnering with Met3dp for Success
Metal additive manufacturing represents a significant leap forward in the production of complex, high-performance components for demanding environments like jet engines. For thermocouple housings, AM offers compelling advantages over traditional methods, including unprecedented design freedom enabling part consolidation and lightweighting, the ability to utilize advanced high-temperature superalloys like IN718, and the potential for reduced development cycles.
However, realizing these benefits requires more than just access to a 3D printer. It demands a holistic approach encompassing rigorous Design for Additive Manufacturing (DfAM) principles, careful material selection underpinned by exceptional powder quality, meticulous process control during printing, and comprehensive post-processing steps including heat treatment, HIP, and precision machining to meet final specifications. Furthermore, robust quality assurance and inspection protocols are non-negotiable for ensuring the reliability and safety demanded by the aerospace industry.
Choosing the right manufacturing partner – one with deep aerospace expertise, proven technical capabilities, a mature quality management system, and proficiency across the entire AM workflow from powder to finished part – is paramount.
Met3dp stands ready to be that partner. As a leader in metal AM, we provide comprehensive solutions that span our own advanced Selective Electron Beam Melting (SEBM) printers, meticulously produced high-quality metal powders optimized for additive manufacturing (including IN718, 316L, Ti-alloys, CoCrMo, and more), and expert application development services. Our commitment to quality, driven by industry-leading powder atomization technologies and decades of collective expertise, ensures we can deliver components meeting the stringent requirements of aerospace and other critical industries.
The future of aerospace manufacturing is increasingly additive. By leveraging the power of metal 3D printing, companies can create lighter, stronger, and more efficient components faster than ever before. Partner with Met3dp to explore how our cutting-edge systems, advanced materials, and application knowledge can accelerate your digital manufacturing transformation and power your organization’s additive manufacturing goals for thermocouple housings and beyond. Contact us today to start the conversation.
Frequently Asked Questions (FAQ): Your Questions Answered on 3D Printed Thermocouple Housings
Q1: Is 3D printed IN718 as strong as wrought or cast IN718?
A: With appropriate process optimization and post-processing, particularly Hot Isostatic Pressing (HIP) to eliminate internal porosity and specific heat treatments to achieve the desired microstructure, the mechanical properties (tensile strength, yield strength, elongation) of AM IN718 can be highly comparable to cast IN718. Achieving properties equivalent to wrought IN718, especially in fatigue strength, is challenging but possible in certain orientations and with rigorous process control and post-processing. For critical applications, properties are verified through extensive testing according to aerospace standards.
Q2: What level of detail and minimum feature size can be achieved on a 3D printed thermocouple housing?
A: The achievable level of detail depends on the specific metal AM process (SLM generally offers finer resolution than EBM), the machine’s capabilities, and the powder particle size. Minimum printable feature sizes are typically around 0.4-0.5 mm (0.016″-0.020″). However, for features requiring high precision or very sharp edges (like threads or critical sealing surfaces), post-process CNC machining is usually employed to achieve the final tolerances and definition.
Q3: How does the cost of a 3D printed thermocouple housing compare to a traditionally manufactured one?
A: The cost comparison is complex and depends heavily on factors like part geometry, order volume, material, and the specific traditional method (casting vs. machining).
- AM can be more cost-effective for: Highly complex geometries, consolidated parts (reducing assembly), low-to-medium production volumes (no tooling costs), and rapid prototyping/development. Material savings from reduced waste (vs. machining) can also be significant with expensive alloys.
- Traditional methods may be cheaper for: Very simple geometries produced in very high volumes where tooling costs are amortized significantly. A total cost of ownership analysis, considering factors like weight savings, reduced assembly time, and potentially improved performance, often favors AM for suitable aerospace components.
Q4: What information does Met3dp need to provide a quote for a 3D printed thermocouple housing?
A: To provide an accurate quote, we typically require the following information:
- 3D CAD model of the part (STEP format is preferred).
- Specified material (e.g., IN718, 316L).
- Required quantity (including anticipated future volumes, if applicable).
- Technical drawings indicating critical dimensions, tolerances, and required surface finishes.
- Details on necessary post-processing (heat treatments, HIP, machining requirements, surface treatments).
- Any specific testing, inspection (e.g., CT scanning), or certification requirements (e.g., material certs, certificate of conformance).
Q5: Are 3D printed thermocouple housings automatically flight-certified?
A: No, parts are not automatically certified simply because they are 3D printed. Any component intended for flight hardware, regardless of manufacturing method, must undergo a rigorous qualification and certification process defined by the engine or aircraft manufacturer and aviation authorities (like the FAA or EASA). This involves extensive material testing, process validation (proving consistency and repeatability), and part-level testing (functional, environmental, fatigue, etc.). Working with a supplier like Met3dp, who operates under stringent quality controls (aligned with AS9100 principles) and provides full traceability and process documentation, is a critical enabler for achieving eventual part certification by the customer.
Dela på
MET3DP Technology Co, LTD är en ledande leverantör av lösningar för additiv tillverkning med huvudkontor i Qingdao, Kina. Vårt företag är specialiserat på 3D-utskriftsutrustning och högpresterande metallpulver för industriella tillämpningar.
Förfrågan för att få bästa pris och anpassad lösning för ditt företag!
Relaterade artiklar
Om Met3DP
Senaste uppdateringen
Vår produkt
KONTAKTA OSS
Har du några frågor? Skicka oss meddelande nu! Vi kommer att betjäna din begäran med ett helt team efter att ha fått ditt meddelande.
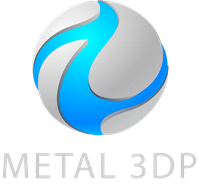
Metallpulver för 3D-printing och additiv tillverkning