High-Temperature Turbine Disks via 3D Printed Superalloys
Innehållsförteckning
Revolutionizing Aerospace Propulsion: High-Temperature Turbine Disks via 3D Printed Superalloys
The relentless pursuit of higher performance, greater efficiency, and access to space places extreme demands on aerospace propulsion systems. At the heart of many powerful rocket engines lies a component subjected to some of the most punishing conditions imaginable: the turbine disk. These critical rotating parts are the backbone of turbopumps, driving the flow of propellants at immense pressures and flow rates. Operating within searing temperatures exceeding 1000∘C (1832∘F) while spinning at tens of thousands of revolutions per minute, turbine disks must withstand incredible centrifugal forces, thermal gradients, high-cycle fatigue, and oxidative or corrosive environments created by combustion byproducts or propellants. Failure is not an option, as a compromised turbine disk can lead to catastrophic engine failure and loss of mission.
Traditionally, manufacturing these components involved complex forging and machining processes using high-performance nickel-based superalloys. While effective, these methods often face limitations in geometric complexity, lead times, and material utilization (the infamous buy-to-fly ratio in aerospace). However, a paradigm shift is underway, driven by the advancements in metalltillsatstillverkning (AM), more commonly known as metal 3D-utskrifter. This transformative technology offers engineers unprecedented design freedom and manufacturing agility, enabling the production of turbine disks with optimized geometries, enhanced performance, and potentially reduced weight and lead times.
Specifically, the application of pulverbäddfusion (PBF) techniques, such as Selective Laser Melting (SLM) or Laser Powder Bed Fusion (LPBF), and Electron Beam Melting (EBM), using specialized högtemperatursuperlegeringar, is unlocking new possibilities. Materials like IN738LC och Rene 41, renowned for their exceptional strength, creep resistance, and stability at extreme temperatures, are now being successfully processed via AM to create mission-critical turbine hardware. These are not just engineering materials; they are enabling materials, pushing the boundaries of what’s possible in rocket engine design and performance.
The challenge lies not just in printing these advanced materials but in ensuring the final component possesses the microstructural integrity, mechanical properties, and reliability demanded by the rigorous standards of the aerospace industry. This requires a deep understanding of material science, process parameter optimization, and sophisticated post-processing techniques.
This is where specialized expertise becomes paramount. Companies like Met3dp are at the forefront of this manufacturing revolution. Headquartered in Qingdao, China, Met3dp is a leading provider of comprehensive additive manufacturing solutions, specializing in state-of-the-art 3D printing equipment, including industry-leading Selective Electron Beam Melting (SEBM) systems, and the development and production of high-performance metal powders tailored for industrial applications. With decades of collective expertise in metal AM, Met3dp partners with aerospace leaders to navigate the complexities of printing demanding components like turbine disks, ensuring the highest levels of quality, accuracy, and reliability for mission-critical applications. As we delve deeper into the world of 3D printed superalloy turbine disks, we will explore the applications, the distinct advantages of AM, the critical role of material selection, and the essential considerations for successfully implementing this technology.
Critical Applications: Where are 3D Printed Superalloy Turbine Disks Utilized?
The primary and most demanding application for 3D printed superalloy turbine disks, particularly those made from IN738LC and Rene 41, is within the turbopumps of liquid-propellant rocket engines. These engines power launch vehicles carrying satellites, cargo, and humans into orbit and beyond.
- Liquid Rocket Engine Turbopumps:
- Function: Turbopumps are essentially high-speed rotating machinery consisting of a turbine driven by hot gas (either from a gas generator cycle, staged combustion cycle, or expander cycle) which, in turn, drives pumps. These pumps deliver fuel and oxidizer to the main combustion chamber at extremely high pressures (hundreds or even thousands of bars) and flow rates.
- Turbine Disk Role: The turbine disk is the central rotating component of the turbine section. It holds the turbine blades, which extract energy from the high-temperature, high-velocity gas flow. The disk must transmit the immense torque generated by the blades to the pump shaft while surviving the extreme thermal and mechanical loads.
- Why AM is Critical Here: The intricate internal passages for cooling, the complex blade attachment features (like fir-tree slots), and the desire for weight reduction make turbine disks ideal candidates for AM. 3D printing allows for geometries that are difficult or impossible to achieve through traditional forging and machining, potentially leading to more efficient cooling, lighter weight, and improved engine performance (e.g., higher thrust-to-weight ratios).
While liquid rocket engines represent the pinnacle application, the technology and materials find relevance in related high-temperature turbomachinery:
- Gas Turbines for Power Generation & Aviation: Land-based gas turbines for generating electricity and aero-derivative gas turbines used in aviation share similar operating principles and material challenges with rocket turbopumps, albeit often with different lifespan requirements (thousands of hours vs. minutes). AM is increasingly explored and adopted for turbine components in these sectors for performance upgrades, repair, and faster development cycles. Insights gained from aerospace AM often translate to these industries.
- Hypersonic Vehicle Propulsion Systems: Emerging concepts for hypersonic aircraft and missiles often rely on air-breathing engines (like scramjets) or combined-cycle engines that operate at extreme temperatures. Turbine components within certain engine architectures face conditions potentially exceeding even those in rockets, making AM with advanced superalloys a key enabling technology for realizing these futuristic systems.
B2B Supply Chain Implications:
The adoption of AM for critical components like turbine disks has significant implications for the aerospace supply chain:
- OEMs & Tier 1 Suppliers: Major aerospace original equipment manufacturers (OEMs) and their primary suppliers are increasingly integrating AM into their manufacturing strategies. They rely on specialized B2B partners who possess the validated processes, certified equipment, and materials expertise necessary for producing flight-critical hardware. Procurement managers within these organizations seek suppliers with proven track records in handling superalloys like IN738LC and Rene 41, robust quality management systems (QMS), and the capacity to scale production.
- Need for Specialized Expertise: Manufacturing aerospace-grade turbine disks via AM is not a commodity service. It requires deep domain knowledge spanning materials science, AM process physics, thermal engineering, non-destructive testing (NDT), and stringent quality control protocols (like AS9100 certification). Companies like Met3dp, with their focus on high-performance materials and advanced printing systems like SEBM, are crucial partners in this ecosystem.
- Shift in Supplier Landscape: AM enables a potential shift towards more agile and distributed manufacturing models. However, the high barrier to entry for producing certified, flight-ready superalloy parts means that established B2B suppliers with significant investment in technology, process validation, and quality assurance remain critical. Procurement strategies must focus on identifying and qualifying these capable partners who can guarantee the reliability and performance needed for components where failure margins are non-existent. Wholesale buyers are looking for consistency, traceability, and adherence to stringent aerospace specifications across potentially large batches of components.
In essence, 3D printed superalloy turbine disks are finding their niche in the most demanding corners of aerospace and energy, pushing the boundaries of performance where extreme heat and stress are the norms. Their successful implementation relies heavily on a sophisticated B2B ecosystem capable of delivering certified, high-integrity components.
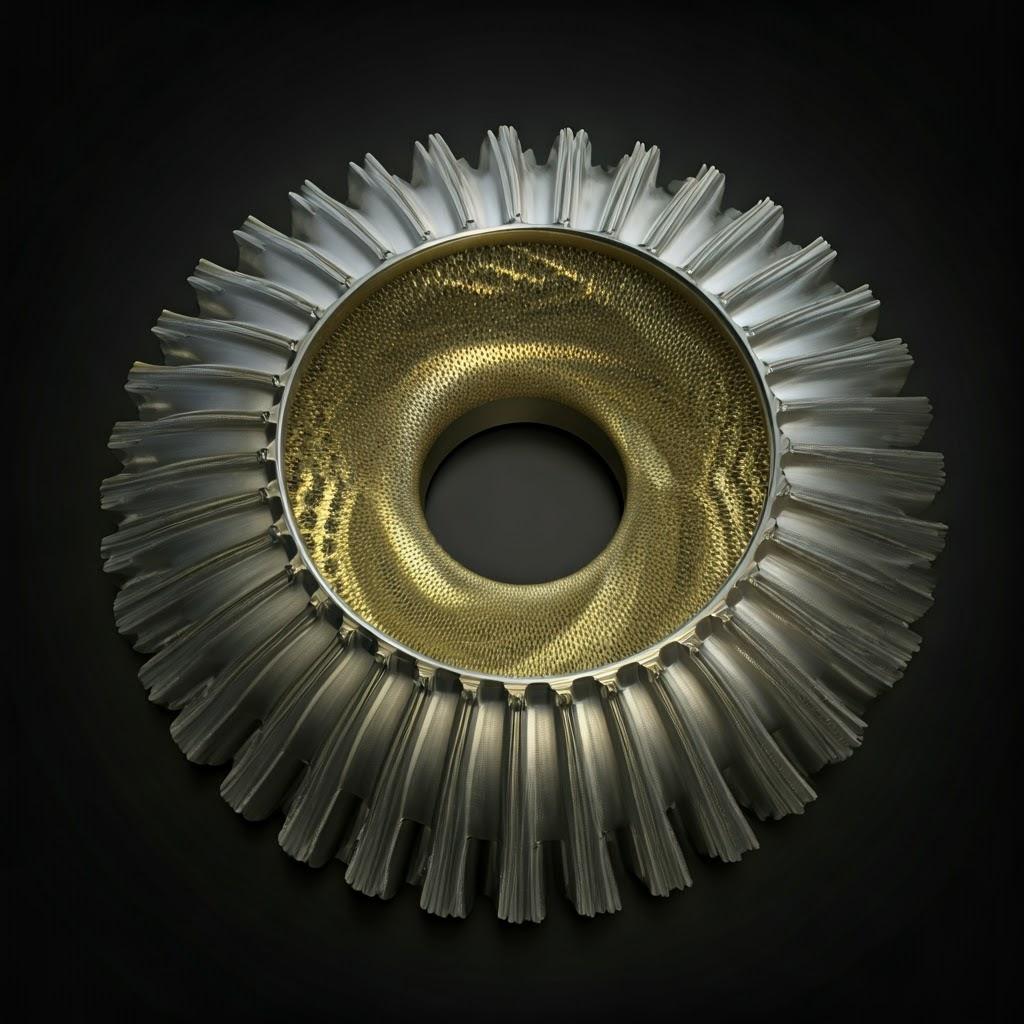
The Additive Advantage: Why Choose Metal 3D Printing for Turbine Disk Production?
While traditional manufacturing methods like forging followed by extensive machining have long been the standard for producing turbine disks, metal additive manufacturing offers a compelling suite of advantages, particularly for the complex, high-value components operating in extreme environments. The choice to adopt AM is driven by tangible benefits impacting design, performance, cost, and lead time.
Let’s compare AM (specifically Powder Bed Fusion techniques like LPBF and EBM/SEBM) with traditional forging and machining for turbine disk production:
Funktion | Traditional Forging & Machining | Metal Additive Manufacturing (LPBF/SEBM) | Advantage of AM |
---|---|---|---|
Designfrihet | Limited by forging dies and subtractive constraints | Highly flexible; enables complex internal features | Significant: Allows for optimized cooling channels, integrated features, complex blade attachments (e.g., advanced fir-trees), topologically optimized shapes, and lightweight structures impossible to forge/machine. Enables performance-driven design. |
Material Avfall | High (Buy-to-Fly Ratio often >10:1) | Low (Near-net shape production, powder recycling) | Major: Drastically reduces expensive superalloy waste. Buy-to-fly ratios can potentially drop below 2:1 or 3:1, leading to substantial cost savings, especially for costly materials like IN738LC and Rene 41. Crucial for aerospace cost-efficiency. |
Ledtid | Long (Tooling design/manufacture, long machining) | Potentially shorter (Tooling-free, direct digital manuf.) | Significant: Eliminates the need for expensive and time-consuming forging dies. Enables rapid prototyping and faster design iteration cycles. Production lead times can be reduced, especially for complex or low-volume parts. |
Konsolidering av delar | Difficult; assemblies often required | Possible; multiple components can be printed as one | Moderate: Simplifies assembly, reduces part count, weight, and potential failure points (like joints or welds). Improves structural integrity. |
Complexity Handling | Expensive and challenging | Handles high complexity with little added cost | Major: The cost of AM is driven more by volume/time than complexity. Intricate internal passages or fine features don’t incur the same penalties as complex multi-axis machining setups. |
Performance Potential | Limited by manufacturability constraints | Higher potential via optimized design | Significant: Optimized cooling improves thermal management, allowing higher turbine entry temperatures or longer component life. Weight reduction improves thrust-to-weight ratios. Tailored microstructures (through process control) may offer property benefits. |
Verktygskostnad | Very High (Forging dies) | None (Digital manufacturing) | Major: Eliminates massive upfront investment and lead time associated with hard tooling, making it viable for lower volume production runs or customized designs. |
Materialegenskaper | Well-understood, established standards | Near-wrought or comparable properties achievable; requires process control & post-processing (HIP, HT) | Evolving: AM parts often require post-processing (HIP, heat treatment) to achieve properties equivalent to wrought materials. Anisotropy can be a factor requiring careful design and process control. However, AM allows for fine microstructural control. |
Export to Sheets
Delving Deeper into the AM Advantages:
- Unlocking Design Potential: Perhaps the most transformative aspect of AM is the liberation from traditional design-for-manufacturability constraints. Engineers can design turbine disks with incredibly complex internal cooling channels that follow curved paths, conform precisely to blade roots, or incorporate tripod structures for enhanced heat transfer. This level of cooling efficiency is simply unattainable with drilling or casting. Topology optimization algorithms can be used to remove material strategically from low-stress areas, significantly reducing rotational mass without compromising structural integrity – critical for improving the responsiveness and efficiency of the turbopump. Met3dp’s Selektiv smältning med elektronstråle (SEBM) technology, for instance, operates in a vacuum environment with higher process temperatures, which can be advantageous for processing crack-sensitive nickel superalloys and potentially reducing residual stress compared to some laser-based methods, further expanding the design possibilities.
- Tackling the Buy-to-Fly Ratio: In aerospace, the buy-to-fly ratio represents the weight of the raw material purchased (‘buy’) compared to the weight of the final component installed (‘fly’). Forgings often start as large billets, much of which is machined away. With superalloys costing hundreds of dollars per kilogram, this waste represents a significant portion of the final part cost. AM builds parts layer by layer, close to the final shape (near-net shape). While some support structures are needed and minor finishing machining is often required, the material utilization is vastly superior. Unfused powder can typically be sieved and reused, further improving material efficiency. This economic advantage is a major driver for AM adoption, particularly for wholesale B2B suppliers looking to offer competitive pricing on high-value components.
- Agility and Speed: The digital nature of AM eliminates the need for physical tooling. Design modifications can be implemented quickly in CAD and sent directly to the printer. This accelerates the development cycle dramatically, allowing for multiple design iterations and tests in the time it might take to procure a single set of forging dies. For industries requiring rapid innovation or facing uncertain demand, this agility is invaluable.
- Process Suitability (SEBM): Met3dp’s SEBM process, a type of EBM, uses an electron beam in a vacuum at elevated temperatures (typically 600−1000∘C). This high process temperature inherently anneals the part during the build, which can significantly reduce residual stresses – a major challenge when printing large, complex parts from crack-prone superalloys like Rene 41 or IN738LC. The vacuum environment also ensures high material purity, crucial for preventing contamination and ensuring optimal mechanical properties in reactive alloys.
While AM presents numerous advantages, it’s crucial to acknowledge that it requires significant expertise in process control, material science, and post-processing (like HIP and heat treatment) to achieve the demanding quality and performance standards of aerospace turbine disks. Partnering with knowledgeable providers like Met3dp, who possess both advanced equipment and deep material understanding, is key to successfully leveraging the additive advantage.
Material Excellence: IN738LC & Rene 41 Superalloys for Extreme Environments
The selection of materials for rocket engine turbine disks is dictated by the extreme operating conditions: high temperatures, high stresses (centrifugal and gas loads), potential for creep (time-dependent deformation under load at temperature), fatigue (from vibrations and thermal cycles), and oxidation/corrosion from hot gases. Nickel-based superalloys are the workhorses for these applications due to their ability to retain significant strength and stability at temperatures approaching their melting points. Among these, IN738LC (Inconel 738 Low Carbon) och Rene 41 are prominent choices, well-suited for additive manufacturing.
Understanding the Chosen Superalloys:
- IN738LC: This is a precipitation-hardenable nickel-based superalloy known for its excellent high-temperature creep strength, fatigue resistance, and good corrosion resistance, particularly against sulfidation. The “LC” designation indicates low carbon content, which improves weldability and, relevantly, processability in AM by reducing the risk of solidification cracking. Its strength comes primarily from gamma prime (γ′) precipitates within the nickel-chromium matrix.
- Why it Matters for Turbine Disks: Its exceptional creep resistance makes it suitable for components enduring sustained high loads at temperatures up to approximately 980∘C (1800∘F). Good fatigue life is critical for handling the cyclic stresses during engine start-up, operation, and shutdown.
- Rene 41 (Haynes R-41): Another precipitation-hardenable nickel-based superalloy, Rene 41 offers very high strength-to-weight ratio at temperatures up to 870∘C (1600∘F) and good oxidation resistance. It derives its strength from a significant volume fraction of coherent gamma prime (γ′) precipitates, along with solid solution strengthening from elements like molybdenum and cobalt. Traditionally, Rene 41 was known for being difficult to weld and forge due to its high gamma prime content and propensity for strain-age cracking.
- Why it Matters for Turbine Disks: Its high strength makes it attractive for highly stressed disks operating at slightly lower temperatures than the peak capabilities of IN738LC. AM offers a potential advantage here, as the layer-by-layer process with controlled thermal cycles can sometimes mitigate the weldability issues encountered in traditional fabrication, allowing complex Rene 41 parts to be produced more readily.
Key Property Comparison (Typical Values – Can Vary with Processing & Heat Treatment):
Property (@ Temperature) | IN738LC | Rene 41 | Significance for Turbine Disks |
---|---|---|---|
Täthet | ~8.11 g/cm³ | ~8.25 g/cm³ | Lower density reduces centrifugal stresses at high RPMs. |
Utbyteshållfasthet (0,2% förskjutning) @ RT | ~760−850 MPa | ~900−1050 MPa | Resistance to permanent deformation under initial load. |
Ultimate draghållfasthet (UTS) @ RT | ~900−1000 MPa | ~1200−1350 MPa | Maximum stress the material can withstand before fracture. |
Utbyteshållfasthet (0,2% förskjutning) @ 870°C (1600°F) | ~550−650 MPa | ~700−800 MPa | Strength retention at high operational temperatures. |
Stress Rupture Life (e.g., @ 982°C/159 MPa) | > 100 hours | Shorter life at this temp/stress | Ability to withstand sustained load at high temp without failure (creep). |
Oxideringsbeständighet | Good to Excellent | Bra | Resistance to degradation from high-temperature gas exposure. |
Primary Strengthening Phase | Gamma Prime (γ′) Ni₃(Al, Ti) | Gamma Prime (γ′) Ni₃(Al, Ti) | Fine precipitates that impede dislocation movement. |
Export to Sheets
(Note: These are representative values. Actual properties of AM parts depend heavily on process parameters, build orientation, post-processing (HIP, Heat Treatment), and testing conditions.)
The Critical Role of Metal Powder Quality:
The success of producing high-integrity turbine disks via AM starts with the feedstock: the metal powder. The characteristics of the powder directly influence the printing process stability, the density of the final part, and its resulting mechanical properties. For demanding superalloys like IN738LC and Rene 41, powder quality is non-negotiable. Key powder characteristics include:
- Sfäriskhet: Ideally, powder particles should be highly spherical. Spherical powders flow easily and pack densely in the powder bed, leading to consistent layer spreading and uniform melting, minimizing the risk of porosity.
- Flytbarhet: Good flowability (measured by Hall flow rate or similar methods) ensures the recoater mechanism can spread thin, uniform layers of powder across the build platform consistently. Poor flowability can lead to uneven layers, voids, and build failures.
- Fördelning av partikelstorlek (PSD): The range and distribution of particle sizes are critical. A controlled PSD (e.g., 15-53 µm for LPBF, 45-106 µm for EBM) optimized for the specific AM machine ensures good powder bed density and melt pool stability. Fines (very small particles) can affect flowability and pose safety hazards, while excessively large particles may not melt completely.
- Purity & Chemistry: The powder chemistry must strictly adhere to the alloy specification. Contaminants (like oxygen, nitrogen, or inclusions) can severely degrade the mechanical properties, particularly fatigue life and creep resistance, which are critical for turbine disks. Low oxygen content is especially important.
- Absence of Satellites: Satellites are smaller particles attached to larger ones, which can hinder flowability and packing density. Powders with minimal satellites are preferred.
Met3dp’s Advantage in Powder Production:
Recognizing the paramount importance of powder quality, Met3dp employs industry-leading powder production technologies to manufacture its metallpulver av hög kvalitet.
- Gas Atomization (GA): This is a widely used method where a molten metal stream is disintegrated by high-pressure inert gas jets (typically Argon or Nitrogen). Met3dp utilizes advanced gas atomization equipment featuring unique nozzle and gas flow designs optimized to produce metallic spheres with high sphericity, good flowability, and controlled PSD, crucial for processing demanding alloys like IN738LC and Rene 41.
- Process med roterande elektrod och plasma (PREP): PREP involves rotating a consumable electrode made of the desired alloy at high speed in an inert atmosphere. A plasma torch melts the tip of the electrode, and centrifugal force flings off molten droplets that solidify in flight into highly spherical particles with very smooth surfaces and high purity, virtually free of satellites. PREP is particularly valued for producing ultra-clean powders required for the most critical aerospace and medical applications.
By leveraging these advanced powder-making systems, Met3dp ensures its customers receive superalloy powders (including IN738LC, Rene 41, and other innovative alloys like TiNi, TiTa, TiAl, CoCrMo, stainless steels, etc.) optimized for additive manufacturing processes like SEBM and LPBF. This control over the entire process, from powder production to printing systems, allows Met3dp to provide comprehensive, reliable solutions for manufacturing challenging components like high-temperature turbine disks, meeting the stringent demands of aerospace wholesale buyers and B2B suppliers.
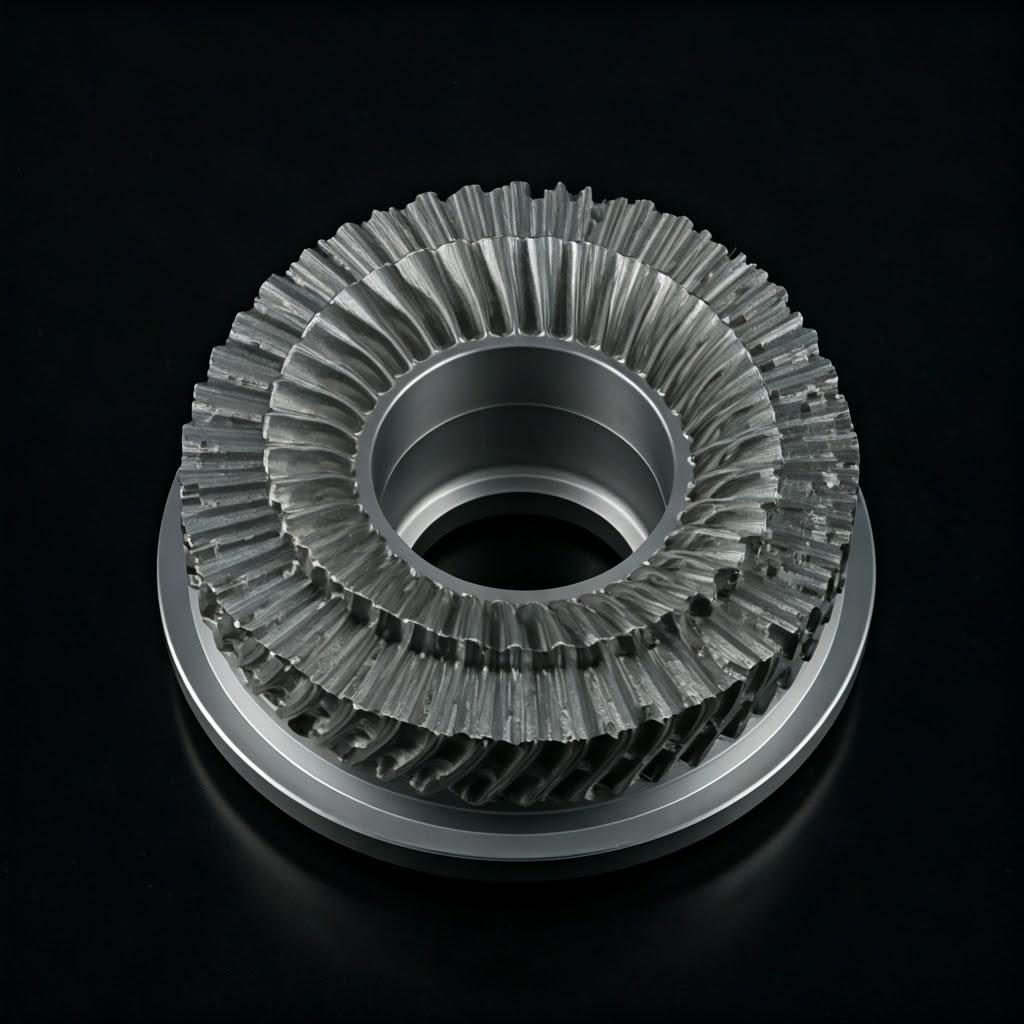
Design for Success: Optimizing Turbine Disks for Additive Manufacturing
Simply replicating a design intended for forging and machining onto a metal 3D printer rarely yields optimal results, especially for a component as complex and critical as a rocket turbine disk. To truly harness the power of additiv tillverkning, engineers must embrace Design för additiv tillverkning (DfAM) principles. DfAM is not just about ensuring a part burk be printed; it’s about leveraging AM’s unique capabilities to enhance performance, reduce weight, consolidate parts, and minimize manufacturing challenges and costs, particularly important considerations for B2B suppliers aiming for efficient production.
For high-temperature superalloy turbine disks made from IN738LC or Rene 41, DfAM involves several key considerations:
- Optimizing Internal Cooling Channels:
- Conformal Cooling: Unlike traditional methods limited to straight-line drilling, AM allows cooling channels to follow the complex contours of the turbine disk and blade roots. This conformal cooling places cooling fluids precisely where needed most, leading to more effective thermal management, potentially allowing higher turbine entry temperatures (improving engine efficiency) or extending the component’s life under extreme thermal loads.
- Komplexa geometrier: AM enables intricate channel designs, such as tripod or lattice structures within channels, to maximize surface area and enhance heat transfer rates.
- Design Constraints: Engineers must consider minimum printable channel diameters (dependent on the AM process and powder), aspect ratios, and ensuring channels are self-draining or accessible for post-print powder removal. Designing channels with self-supporting angles (typically >45 degrees from the horizontal) minimizes the need for internal supports that are difficult or impossible to remove.
- Minimizing Stress Concentrations:
- Smooth Transitions: Sharp corners and abrupt changes in geometry act as stress risers, potentially initiating cracks under high cyclic loads. DfAM emphasizes using generous fillets and smooth, tangential transitions between features (e.g., where the disk meets the shaft bore or blade attachments).
- Topology Optimization: This computational technique uses algorithms to strategically remove material from areas experiencing low stress while retaining material where needed for structural integrity. For a rotating component like a turbine disk, topology optimization can significantly reduce weight (lowering centrifugal forces) while maintaining or even increasing stiffness, guided by Finite Element Analysis (FEA) load cases. The resulting organic-looking shapes are often only manufacturable via AM.
- Strategic Use of Support Structures:
- Syfte: Support structures in Powder Bed Fusion (PBF) are necessary for two main reasons: anchoring overhanging features (typically those angled less than 45 degrees from the horizontal) to the build plate or underlying layers, and conducting heat away from the melt zone to prevent warping and ensure dimensional stability.
- Minimization Strategies: Excessive supports increase print time, material consumption, and post-processing effort (removal). DfAM strategies include:
- Optimizing build orientation to minimize the extent of overhangs.
- Using chamfers or fillets instead of sharp horizontal overhangs.
- Designing features to be self-supporting where possible.
- Process Differences: Laser PBF (LPBF/SLM) typically requires solid or sintered support structures directly fused to the part, which need mechanical removal. Electron Beam Melting (EBM/SEBM), like the systems offered by Met3dp, often benefits from the surrounding unfused powder acting as a partial support (powder cake support), potentially reducing the need for extensive directly sintered supports, especially for less severe overhangs. However, conductive supports are still crucial for thermal management.
- Designing for Removal: Supports should be designed with accessibility in mind, often incorporating weaker interface points or structures that are easier to break away or machine off without damaging the part surface.
- Feature Resolution and Wall Thickness:
- Process Limits: Every AM process has limitations on the minimum feature size it can accurately produce. This includes minimum wall thickness, hole diameter, and gap width. These limits depend on the beam spot size (laser or electron beam), layer thickness, and powder characteristics. Engineers must design features within these achievable limits (e.g., typical minimum wall thickness might be around 0.4−0.8 mm).
- SEBM vs LPBF: Generally, LPBF can achieve finer feature resolution and potentially better surface finish as-built compared to EBM/SEBM, though Met3dp’s advanced SEBM systems offer industry-leading accuracy. This needs consideration when designing very fine details.
- Simulation-Driven Design:
- Build Process Simulation: Software tools can simulate the layer-by-layer build process, predicting thermal gradients, residual stress accumulation, and potential distortion. This allows designers to optimize build orientation, support strategies, and even slightly modify the part geometry (compensating for predicted shrinkage/warpage) before committing to a costly print, especially vital for expensive superalloy parts.
- Performance Simulation: Computational Fluid Dynamics (CFD) is used to validate the effectiveness of designed cooling channels. FEA is crucial for analyzing stress distributions under mechanical and thermal loads, predicting fatigue life, and ensuring the topologically optimized design meets all structural requirements. These simulations are essential for validating the design’s integrity before manufacturing.
Integrating DfAM principles from the outset is crucial for aerospace manufacturers and their B2B suppliers. It ensures that the final 3D printed turbine disk not only meets the stringent performance requirements but is also manufacturable reliably and cost-effectively, leveraging the full potential of additive technology. Collaboration between design engineers and AM process experts, like the team at Met3dp, is often key to achieving DfAM success.
Precision Matters: Achieving Tight Tolerances and Surface Finish in 3D Printed Turbine Disks
While AM offers geometric freedom, achieving the tight tolerances and specific surface finishes required for aerospace components like turbine disks demands careful process control and often necessitates post-processing steps. Engineers and procurement managers must understand the realistic capabilities and limitations of AM processes like LPBF and SEBM when applied to superalloys such as IN738LC and Rene 41.
Defining the Terms:
- Dimensionell noggrannhet: How closely the dimensions of the printed part match the nominal dimensions specified in the CAD model.
- Tolerance: The permissible range of variation for a given dimension. Aerospace components often have very tight tolerances on critical features (e.g., ±0.05 mm or tighter).
- Surface Finish (Roughness): Measured typically as Ra (arithmetic average roughness), it quantifies the texture or smoothness of a surface. Lower Ra values indicate smoother surfaces.
Achievable Precision with AM Superalloys:
The achievable precision depends heavily on the specific AM process, machine calibration, part geometry and size, build orientation, material, and process parameters.
Funktion | As-Built (Typical Range – LPBF) | As-Built (Typical Range – SEBM) | Post-Processed (Machined/Polished) | Significance for Turbine Disks |
---|---|---|---|---|
General Tolerance | ±0.1 to ±0.3 mm (or ±0.1-0.3%) | ±0.2 to ±0.4 mm (or ±0.2-0.4%) | ±0.01 to ±0.05 mm (or tighter) | As-built tolerances often insufficient for critical interfaces (shaft fits, blade roots, sealing faces). Finish machining is usually required for these areas. |
Ytjämnhet (Ra) | 5 – 15 µm (Non-supported surfaces) | 20 – 40 µm (Due to larger powder/melt pool) | 0.4 – 1.6 µm (Machined) <br> <0.2 µm (Polished) | As-built roughness generally too high for fatigue-critical areas or sealing surfaces. Downward-facing surfaces are rougher due to support contact. |
Minsta funktionsstorlek | ~0.4 mm (Wall thickness) | ~0.8 mm (Wall thickness) | Governed by machining capability | Dictates the feasibility of fine cooling channels or thin walls directly from the AM process. |
Export to Sheets
(Note: These are general estimates. Specific capabilities vary significantly between machine manufacturers, material batches, and optimized parameter sets. Met3dp’s printers, for example, are designed for industry-leading accuracy and reliability within the SEBM process capabilities.)
Factors Influencing Precision:
- AM-process: LPBF generally offers slightly better dimensional accuracy and finer surface finish as-built compared to SEBM due to smaller beam spot size and layer thickness. However, SEBM’s higher processing temperature can reduce thermal stress and potential warping, aiding overall dimensional stability for certain large or complex parts.
- Machine Calibration & Condition: Regular calibration of the scanner system, beam focus, and mechanical axes is crucial. The overall health and reliability of the AM system, like the robust printers developed by Met3dp, play a significant role in achieving consistent results batch after batch – a key requirement for B2B production.
- Process Parameters: Laser/electron beam power, scan speed, layer thickness, hatch spacing, and scan strategy all impact melt pool dynamics, solidification behavior, and ultimately, dimensional accuracy and surface finish. Optimized parameters are alloy-specific.
- Termisk hantering: Controlling heat buildup and dissipation during the build is critical. Inconsistent thermal conditions can lead to warping and deviation from the intended geometry. Support structures play a key role here.
- Part Geometry & Orientation: Large, flat surfaces may be prone to warping. Tall, thin features can experience deviation. The orientation of the part in the build chamber affects support needs, surface finish on different faces, and potentially dimensional accuracy due to thermal gradients and shrinkage.
- Pulver Egenskaper: Powder size distribution and morphology can influence powder bed density and melt characteristics, subtly affecting final dimensions and surface quality.
Managing Expectations for Aerospace Quality:
Procurement managers and engineers must recognize that metal AM is typically a near-net-shape process, not a net-shape process for components with very high precision requirements. While AM excels at creating complex overall geometries, critical interfacing features, sealing surfaces, bearing journals, and high-fatigue areas on turbine disks almost always require finish machining after the AM build and subsequent heat treatments (which can also cause minor dimensional changes).
The typical workflow involves:
- Designing the part with AM capabilities and limitations in mind (DfAM).
- Printing the part using optimized processes on reliable machines (like Met3dp’s SEBM systems).
- Performing necessary post-processing like stress relief, HIP, and heat treatment.
- Using high-precision CNC machining to bring critical features into final tolerance and achieve the required surface finish.
Understanding this workflow and the achievable precision at each stage is vital for accurate quoting, production planning, and ensuring the final 3D printed superalloy turbine disk meets all demanding aerospace specifications.
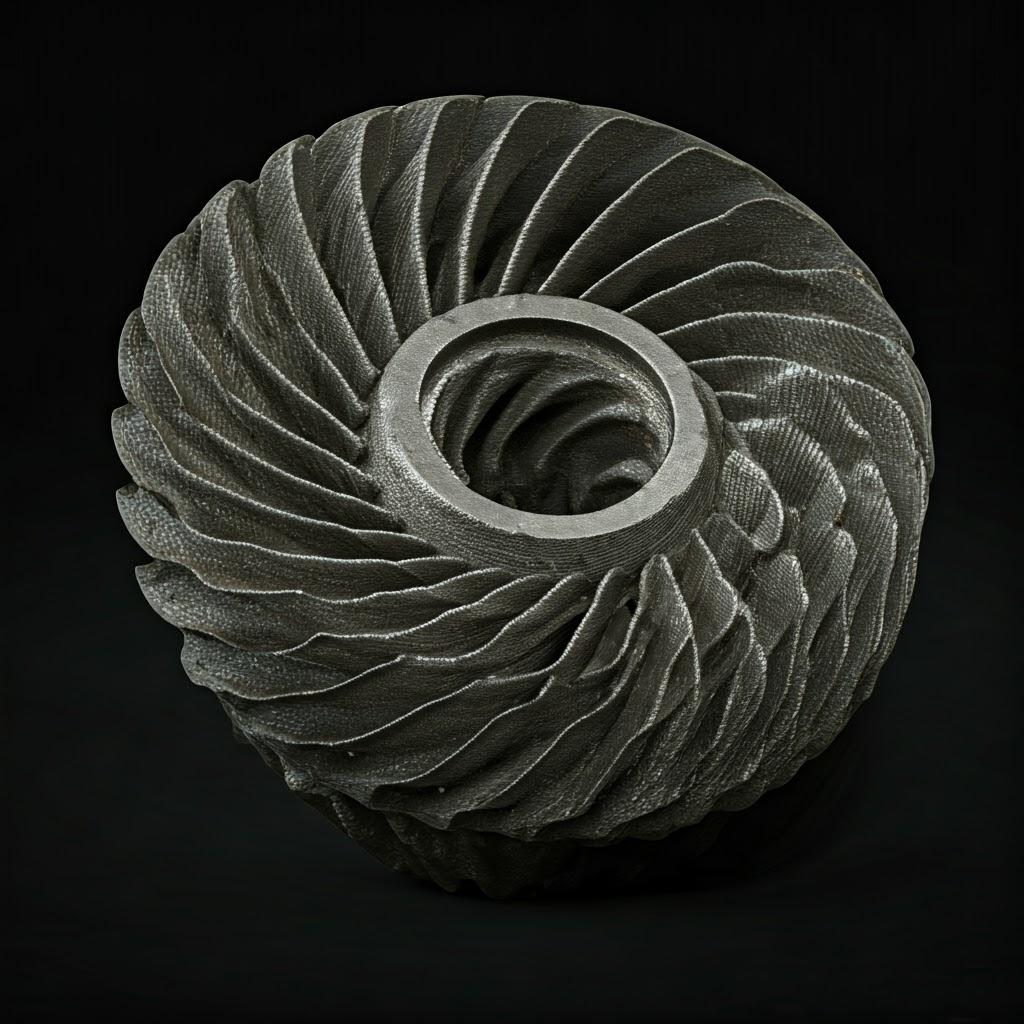
Beyond the Build: Essential Post-Processing for Mission-Critical Turbine Disks
Printing a superalloy turbine disk using IN738LC or Rene 41 is only the first manufacturing step. For these components to withstand the brutal environment inside a rocket engine turbopump, a series of crucial post-processing steps are mandatory. These steps are designed to relieve internal stresses, eliminate microscopic defects, optimize the material’s microstructure, achieve final dimensional tolerances, and verify the part’s integrity. Skipping or improperly performing these steps can compromise the part’s mechanical properties, particularly fatigue life and creep resistance, with potentially catastrophic consequences.
Here’s a breakdown of the essential post-processing sequence for AM superalloy turbine disks:
- Stressavlastning:
- Why: The rapid heating and cooling cycles inherent in powder bed fusion create significant residual stresses within the printed part. These stresses can cause distortion or warping, especially after the part is removed from the build plate, and can negatively impact mechanical performance.
- How: The part, often while still attached to the build plate (especially for LPBF), undergoes a furnace cycle at a specific temperature (below the aging temperature) for a set duration, followed by controlled cooling. This allows the microstructure to relax, reducing internal stresses. SEBM parts, built at higher temperatures, generally have lower residual stress but may still benefit from a stress relief cycle depending on the alloy and geometry.
- Importance: Prevents distortion during subsequent handling and machining, reduces susceptibility to cracking.
- Het isostatisk pressning (HIP):
- Why: Despite process optimization, microscopic internal pores (like gas porosity or small lack-of-fusion voids) can remain within the AM part. These act as stress concentrators and severely limit fatigue life and fracture toughness.
- How: Parts are subjected to high temperature (just below the alloy’s solidus temperature) and high-pressure inert gas (typically Argon, >100 MPa or 15,000 psi) in a specialized HIP vessel. The combination of heat and pressure causes the material to plastically deform on a micro-scale, diffusion bonding across internal void surfaces and effectively closing them.
- Importance: Crucial for aerospace-grade AM parts. HIP increases the density to virtually 100%, significantly improves fatigue strength, creep resistance, and overall material integrity, bringing AM part performance closer to that of traditionally wrought materials. It is often a mandatory requirement for flight-critical hardware.
- Borttagning av stödstruktur:
- Why: Supports used during the build process must be removed.
- How: Depending on the support design and material, removal can involve manual breaking (for easily accessible, weaker supports), cutting with saws or grinders, or more precise methods like Wire Electrical Discharge Machining (Wire EDM) for complex or hard-to-reach supports. Care must be taken to avoid damaging the part surface.
- Importance: Necessary step before subsequent machining and heat treatment. Design for support removal (DfAM) is key to making this step efficient and safe.
- Heat Treatment (Solution Annealing & Aging):
- Why: The as-built microstructure of an AM superalloy, even after HIP, may not be optimal for high-temperature performance. Heat treatment is required to homogenize the microstructure, dissolve any undesirable phases formed during printing, and then precipitate the fine, coherent gamma prime (gamma′) phase in the desired size and distribution, which provides the primary high-temperature strength and creep resistance in alloys like IN738LC and Rene 41.
- How: This typically involves two stages:
- Lösningsglödgning: Heating the part to a high temperature (e.g., 1120−1200circC) to dissolve existing precipitates and homogenize the matrix, followed by rapid cooling (quenching).
- Åldrande: Reheating the part to one or more lower temperatures (e.g., 840−900circC) for specific durations to allow the controlled precipitation and growth of the strengthening gamma′ phase. Specific cycles are alloy-dependent and dictated by aerospace material specifications.
- Importance: Develops the required mechanical properties (tensile strength, creep resistance, fatigue life) for the demanding operating conditions. Improper heat treatment leads to substandard performance.
- CNC Machining:
- Why: As discussed previously, AM processes typically cannot achieve the final, tight tolerances and fine surface finishes required on critical interfaces of a turbine disk.
- How: High-precision multi-axis CNC milling and turning centers are used to machine features like the shaft bore, blade attachment slots (e.g., fir-trees), sealing surfaces, and balancing features to the exact dimensions and surface finish (Ra) specified in the engineering drawing.
- Importance: Ensures proper fit, assembly, sealing, and aerodynamic/hydrodynamic performance. Critical for functionality and reliability.
- Icke-förstörande testning (NDT):
- Why: To verify the internal and external integrity of the final part without damaging it. Essential for quality assurance and certification in aerospace.
- How: A suite of NDT methods is typically employed:
- Computed Tomography (CT) Scanning: Provides a 3D X-ray view to detect internal voids, inclusions, or geometric deviations.
- Fluorescent Penetrant Inspection (FPI): Reveals surface-breaking cracks or porosity.
- Ultrasonic Testing (UT): Can detect subsurface flaws.
- Dimensionell inspektion: Using Coordinate Measuring Machines (CMMs) to verify final dimensions against the specification.
- Importance: Provides objective evidence that the part meets all quality requirements and is free from critical defects. Mandatory for flight hardware.
- Surface Finishing (Optional but Common):
- Why: Depending on the application, further surface treatments may be needed.
- How: Methods like shot peening can induce compressive residual stresses on the surface to improve fatigue life. Polishing might be used for specific aerodynamic or hydrodynamic surfaces. Thermal barrier coatings (TBCs) could potentially be applied, although less common on the disk itself compared to blades.
- Importance: Enhances specific performance characteristics like fatigue resistance or thermal insulation.
Successfully navigating this complex post-processing chain requires significant infrastructure, expertise, and rigorous process control. B2B suppliers specializing in aerospace AM components, like Met3dp, often develop integrated workflows and partnerships to manage these steps effectively, ensuring that the final turbine disk delivered to the customer is ready for its demanding mission.
Overcoming Hurdles: Common Challenges in 3D Printing Superalloy Turbine Disks & Solutions
Additive manufacturing of high-temperature superalloys like IN738LC and Rene 41 into complex geometries like turbine disks is a sophisticated process, not without its challenges. Understanding these potential hurdles and implementing effective mitigation strategies is key to achieving reliable, high-quality production. Here are some common challenges and solutions:
- Residual Stress and Distortion:
- Utmaning: The intense, localized heating from the laser or electron beam followed by rapid cooling creates steep thermal gradients, leading to the buildup of internal residual stresses as layers solidify and contract. Excessive stress can cause part distortion (warping), detachment from the build plate, or even cracking during or after the build.
- Solutions:
- Optimized Scan Strategies: Using techniques like island scanning, sector scanning, or rotating the scan vector between layers helps distribute heat more evenly and reduce stress buildup.
- Robust Support Structures: Well-designed supports anchor the part securely and help conduct heat away effectively.
- Process Simulation: Predicting stress buildup allows for design or parameter adjustments beforehand.
- Post-Build Stress Relief: Essential heat treatment step performed immediately after printing.
- Process Choice (SEBM Advantage): Met3dp’s SEBM process, operating at elevated temperatures (600circC), inherently reduces thermal gradients compared to the room-temperature start of LPBF, significantly lowering residual stress levels, which is a major advantage for large, complex superalloy parts prone to stress issues. Choosing appropriate tryckmetoder är avgörande.
- Cracking Susceptibility:
- Utmaning: Many high-strength nickel superalloys, especially those with high volume fractions of gamma prime (gamma′) like Rene 41, are susceptible to cracking during the AM process or subsequent heat treatments. This can manifest as solidification cracking (during cooling in the melt pool) or strain-age cracking (during post-weld or post-build heat treatment).
- Solutions:
- Careful Parameter Optimization: Fine-tuning energy input (power, speed) and thermal management to control cooling rates.
- Alloy Selection/Modification: IN738LC generally has better AM processability than Rene 41 due to its composition. Sometimes minor alloy modifications can improve printability.
- Het isostatisk pressning (HIP): Can help heal some micro-cracks, although preventing their formation is preferred.
- Appropriate Heat Treatment Cycles: Designing stress relief and aging cycles carefully to avoid temperatures/hold times known to promote strain-age cracking.
- SEBM Process: The high, uniform temperature and vacuum environment of SEBM can be beneficial in mitigating some cracking mechanisms compared to LPBF for certain sensitive alloys.
- Porositetskontroll:
- Utmaning: Internal pores are detrimental defects. They can arise from gas trapped within the powder or dissolved in the melt (gas porosity) or from incomplete melting and fusion between layers or scan tracks (lack-of-fusion porosity).
- Solutions:
- High-Quality Powder: Using powder with low internal gas content, high sphericity, and controlled PSD (like those produced by Met3dp’s GA and PREP systems) is fundamental. Proper powder storage and handling to prevent moisture pickup is also key.
- Optimized Process Parameters: Ensuring sufficient energy density (beam power, speed, layer thickness) to achieve complete melting and fusion without overheating (which can increase gas porosity).
- Vacuum Environment (SEBM): The vacuum in SEBM helps minimize gas pickup from the atmosphere during printing.
- Het isostatisk pressning (HIP): The most effective way to eliminate remaining microscopic porosity after printing.
- Support Structure Removal Difficulties:
- Utmaning: Supports made from the same strong superalloy can be very difficult and time-consuming to remove, especially if they are in complex internal channels or tightly integrated with the part. Removal processes risk damaging the part surface.
- Solutions:
- DfAM: Designing parts to be self-supporting where possible, optimizing build orientation, and designing supports for easier access and removal (e.g., using weaker interface layers if the process allows).
- Specialized Removal Techniques: Utilizing tools like multi-axis Wire EDM for precise, non-contact cutting of supports.
- Process Considerations: The powder cake support in SEBM can sometimes reduce the need for extensive fused supports compared to LPBF.
- Anisotropy in Mechanical Properties:
- Utmaning: Due to the directional nature of solidification along the build direction (typically Z-axis), AM parts often exhibit anisotropy – their mechanical properties (e.g., tensile strength, ductility, fatigue life) can vary depending on the direction of testing relative to the build direction. This is related to elongated grain structures and microstructural texture.
- Solutions:
- Build Orientation Optimization: Orienting the part such that the most critical load paths align with the direction of optimal properties.
- Process Parameter Adjustment: Some studies show possibilities to influence grain structure through scan strategy manipulation.
- Post-Processing (HIP & Heat Treatment): These steps help homogenize the microstructure and can reduce, but not always eliminate, anisotropy.
- Designöverväganden: Engineering analysis must account for potential anisotropy by using directional property data in simulations and applying appropriate safety factors.
- Powder Handling, Recycling, and Safety:
- Utmaning: Fine metal powders, especially reactive alloys, can pose safety risks (flammability, inhalation). Maintaining powder purity during handling and recycling is critical, as contamination degrades properties. Tracking powder batches and reuse cycles is essential for aerospace traceability.
- Solutions:
- Controlled Environments: Using inert gas atmospheres (e.g., Argon) for powder handling and machine operation.
- Proper PPE: Operators require appropriate respiratory and personal protective equipment.
- Hantering av livscykeln för pulver: Implementing strict protocols for powder sieving, quality testing (chemistry, PSD, morphology), blending, and tracking the number of reuse cycles. Documented procedures are essential for B2B suppliers serving aerospace.
- Supplier Expertise: Relying on experienced providers like Met3dp who have robust powder handling and quality control systems in place.
By proactively addressing these challenges through careful design, process optimization, meticulous post-processing, and partnering with experienced AM providers, manufacturers can successfully produce high-integrity, mission-capable superalloy turbine disks like those from IN738LC and Rene 41, fully realizing the benefits of additive manufacturing for demanding aerospace applications.
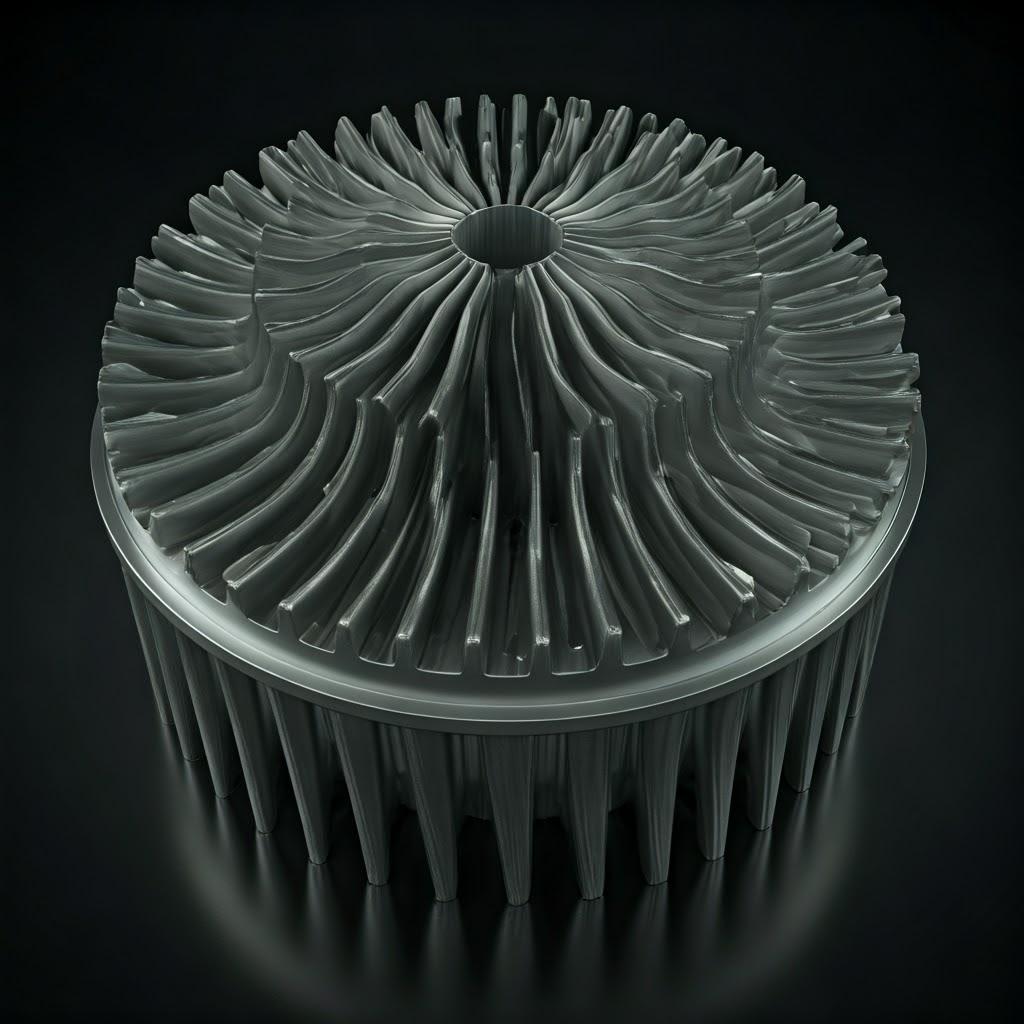
Partnering for Propulsion: Selecting the Right Metal AM Service Provider
The journey from a digital design file to a flight-certified, 3D printed superalloy turbine disk is complex and requires a manufacturing partner with exceptional capabilities and rigorous quality standards. Choosing the right metal additive manufacturing service provider is arguably as critical as the design and material selection itself, especially for demanding aerospace applications involving materials like IN738LC and Rene 41. Procurement managers and engineers in aerospace OEMs and Tier 1 suppliers must evaluate potential B2B partners based on a stringent set of criteria.
Here’s what to look for when selecting a metal AM service provider for mission-critical turbine components:
- Demonstrated Material Expertise:
- Superalloy Experience: The provider must have proven, hands-on experience printing the specific superalloy required (e.g., IN738LC, Rene 41) and understand its unique behavior during the AM process (melt pool dynamics, solidification, response to heat treatment). Ask for evidence of successful projects with these materials.
- Powder Knowledge: Ideally, the partner understands powder metallurgy deeply. Do they have robust procedures for powder sourcing, testing, handling, storage, and recycling to maintain purity and traceability? Partners like Met3dp, who manufacture their own metallpulver av hög kvalitet using advanced techniques like Gas Atomization and PREP, offer an integrated advantage, ensuring optimal powder characteristics tailored for their printing processes.
- Process Specialization and Control:
- Technology Fit: Does the provider specialize in the most suitable AM process for your application? For high-stress superalloys prone to cracking, the high-temperature vacuum environment of Electron Beam Melting (EBM/SEBM) can offer advantages, a technology where Met3dp provides industry-leading printers and expertise. For finer features, Laser Powder Bed Fusion (LPBF) might be considered, but the provider must demonstrate mastery over controlling residual stress.
- Parameter Optimization: The provider should possess validated, optimized process parameter sets for the specific alloy and machine combination, ensuring dense, defect-free builds with predictable microstructures.
- Industrial-Grade Equipment and Capacity:
- Machine Quality & Maintenance: Are they using well-maintained, industrial-grade AM systems specifically designed for reactive, high-temperature alloys? Consistent machine calibration and performance are vital. Met3dp’s focus on developing printers with industry-leading print volume, accuracy, and reliability ensures a stable production platform.
- Produktionskapacitet: Can the provider handle your required volume, from prototypes to potential series production for wholesale B2B orders? Assess their machine availability, operational shifts, and workflow efficiency.
- Robust Quality Management System (QMS):
- Aerospace Certification (AS9100): For flight-critical components, AS9100 certification (or equivalent aerospace QMS) is often non-negotiable. This demonstrates adherence to rigorous quality processes, risk management, configuration control, and traceability requirements specific to the aerospace industry.
- Process Documentation: Expect comprehensive documentation covering every step, from powder batch tracking to build logs, post-processing records, NDT reports, and final inspection data.
- End-to-End Material Traceability:
- Powder to Part: The provider must demonstrate an unbroken chain of custody and traceability for the metal powder, linking specific powder batches to specific parts and builds. This includes tracking powder reuse cycles and performing regular quality checks on recycled powder.
- Comprehensive Post-Processing Capabilities:
- Integrated Workflow: Does the provider offer critical post-processing steps like stress relief, HIP, alloy-specific heat treatment, precision CNC machining, and relevant NDT methods either in-house or through tightly controlled, qualified external partners? An integrated workflow minimizes logistical complexity and ensures process continuity.
- Engineering and Technical Support:
- DfAM Expertise: Can their engineering team provide valuable input on optimizing the design for additive manufacturing (DfAM)? This collaboration can significantly improve manufacturability, reduce cost, and enhance performance.
- Simulation Capabilities: Access to build process simulation or performance analysis tools can de-risk the manufacturing process and validate design choices.
- Problem Solving: Aerospace AM often involves unique challenges. A partner with deep technical expertise can effectively troubleshoot issues that may arise during production.
- Proven Track Record and Reputation:
- Case Studies & References: Look for evidence of successful projects involving similar materials, complexities, and industry standards. Customer testimonials or references within the aerospace sector are valuable indicators.
- Industry Standing: Choose a provider recognized for quality and reliability in the demanding field of industrial metal AM.
Why Met3dp Excels as a Partner:
Met3dp Technology Co., LTD stands out as a premier partner for organizations seeking to leverage additive manufacturing for high-performance components like rocket turbine disks. As detailed further About Met3dp, the company provides a unique synergy of capabilities:
- Avancerade material: In-house production of high-sphericity, high-purity superalloy powders (including IN738LC, Rene 41, and others) using state-of-the-art Gas Atomization and PREP technology.
- Cutting-Edge Equipment: Development and supply of SEBM printers known for their large build volumes, precision, and reliability, ideal for processing challenging superalloys.
- Integrated Solutions: Offering comprehensive support spanning materials, equipment, process optimization, and application development.
- Deep Expertise: Decades of collective experience within the team focused specifically on metal additive manufacturing for demanding industrial sectors like aerospace, medical, and automotive.
Choosing a partner like Met3dp, with end-to-end control over critical inputs like powder and deep expertise in the SEBM process, significantly de-risks the adoption of AM for challenging aerospace components and provides a solid foundation for B2B supply chain relationships demanding quality and consistency.
Understanding Investment: Cost Drivers and Lead Times for AM Turbine Disks
While offering significant advantages, additive manufacturing of aerospace-grade superalloy turbine disks represents a considerable investment. Understanding the factors that drive cost and influence lead times is crucial for project planning, budgeting, and managing expectations within the B2B supply chain.
Key Cost Drivers:
The final price per part for a 3D printed IN738LC or Rene 41 turbine disk is influenced by a combination of factors:
- Material Cost:
- Powder Price: Nickel-based superalloys like IN738LC and Rene 41 are inherently expensive raw materials due to their elemental composition (high Ni, Cr, Co, Mo, etc.) and complex production processes. Powder pricing is typically per kilogram.
- Consumption: This includes the volume of the final part, the volume of support structures needed, and any powder lost during handling or deemed unsuitable for recycling after multiple uses. Efficient DfAM and nesting strategies aim to minimize overall consumption.
- AM Machine Time:
- Build Duration: This is often the largest cost component. It’s determined by the total volume of material being fused (part + supports), the height of the build (number of layers), the complexity requiring specific scan strategies, and the machine’s deposition rate.
- Machine Depreciation & Operation: The cost reflects the high capital investment in industrial AM systems and their operational expenses (power, inert gas, maintenance).
- Kostnader för arbetskraft:
- Skilled Operators: Significant skilled labor is involved in build preparation (loading powder, setting up the job file), machine monitoring, part removal (depowdering), support removal, and managing post-processing steps.
- Post-Processing Intensity:
- HIP: Hot Isostatic Pressing requires specialized equipment and is a relatively expensive batch process, adding a significant cost per part, especially for smaller batches.
- Värmebehandling: Complex, multi-stage heat treatment cycles for superalloys require specialized vacuum furnaces and long cycle times.
- CNC Machining: Precision machining of critical features using multi-axis machines adds considerable cost, dependent on the extent of machining required and the tolerances specified.
- NDT & Inspection: Rigorous non-destructive testing (CT, FPI, UT) and dimensional inspection using CMMs contribute significantly to the quality assurance cost component.
- Development and Engineering:
- DfAM & Simulation: Initial design optimization, simulation work, and process development efforts represent upfront engineering costs, which may be amortized over the production run.
- Order Volume (Economies of Scale):
- Setup Costs: Machine setup and preparation costs are amortized over the number of parts in a build.
- Nesting Efficiency: Printing multiple parts simultaneously in a single build (nesting) improves machine utilization and reduces the cost per part.
- Batch Post-Processing: HIP and heat treatment costs are often more economical for larger batches.
- Wholesale Advantage: Consequently, unit costs for larger B2B wholesale orders are typically lower than for single prototypes or very small batches.
Typical Lead Times:
Lead time refers to the total duration from order placement (or final design approval) to delivery of the finished, inspected component. It’s crucial to understand that while AM eliminates tooling lead time, the overall process for a certified aerospace part remains substantial.
- Prototyping: For initial prototypes (potentially with less stringent QA), lead times might range from 2 till 6 veckor, depending on complexity, machine availability, and basic post-processing needs.
- Production Parts (Certified): For fully processed and certified turbine disks, lead times are significantly longer, typically ranging from 8 to 20 weeks or more. This extended duration accounts for:
- Detailed production planning and scheduling.
- Print time (can be many days for large/complex builds).
- Queueing time for specialized post-processing like HIP and heat treatment (often performed by external certified facilities).
- Multi-stage precision machining.
- Comprehensive NDT and final inspection reporting.
- Potential iterations if any non-conformances are found.
Factors influencing lead time include part complexity, the specific AM process used, machine availability, the efficiency and capacity of the post-processing supply chain, the required level of quality assurance documentation, and the overall quantity ordered. Clear communication with the AM service provider is essential to establish realistic lead time expectations for B2B procurement planning.
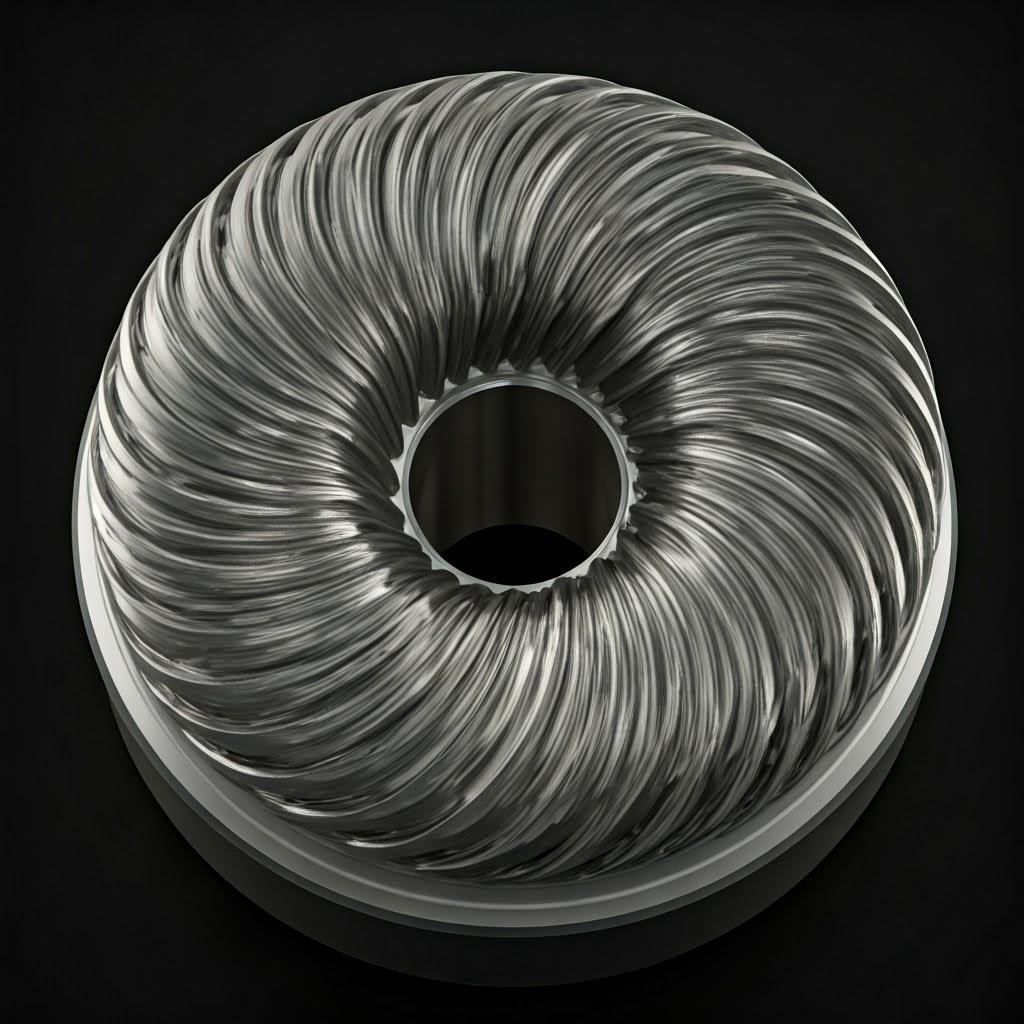
Frequently Asked Questions (FAQ) about 3D Printed Superalloy Turbine Disks
Here are answers to some common questions regarding the additive manufacturing of high-temperature turbine disks using superalloys like IN738LC and Rene 41:
1. What are the main advantages of 3D printing turbine disks over traditional forging?
Additive Manufacturing (AM) offers several key advantages compared to traditional forging and machining for turbine disks:
- Designfrihet: AM enables highly complex internal cooling channels (conformal cooling) and optimized geometries (topology optimization) that are impossible or impractical to achieve via forging/machining. This can lead to significantly improved cooling efficiency, reduced weight, and potentially higher engine performance.
- Minskat materialavfall: AM is a near-net-shape process, drastically reducing the amount of expensive superalloy material wasted compared to the subtractive nature of machining large forgings. This significantly lowers the buy-to-fly ratio, resulting in substantial cost savings on raw materials.
- Elimination of Tooling: AM does not require expensive and time-consuming forging dies. This dramatically reduces upfront costs and lead times, making it suitable for rapid prototyping, faster design iterations, and economically viable low-to-mid volume production.
- Del Konsolidering: AM allows features previously manufactured as separate components and then assembled (e.g., blades integrated with the disk – a ‘blisk’, though challenging) to potentially be printed as a single unit, reducing part count, weight, and potential failure points.
- Faster Development Cycles: The ability to move directly from CAD to part allows for quicker testing and refinement of new turbine disk designs, accelerating innovation in propulsion systems.
2. How does the performance of 3D printed IN738LC/Rene 41 compare to wrought counterparts?
Achieving performance parity with established wrought (forged) superalloys is a primary goal for aerospace AM. With optimized process control and mandatory post-processing, AM superalloys can exhibit comparable properties:
- Densitet: After Hot Isostatic Pressing (HIP), AM parts typically achieve full density (>99.9%), eliminating porosity concerns.
- Static Properties: Tensile strength (yield and ultimate) at room and elevated temperatures can often meet or exceed the specifications for wrought or cast equivalents after appropriate heat treatment (solution annealing and aging) develops the optimal microstructure.
- Motstånd mot krypning: With proper heat treatment to precipitate the strengthening gamma prime phase correctly, AM IN738LC and Rene 41 can demonstrate excellent creep resistance comparable to traditional forms.
- Fatigue Life: This is often the most critical property for turbine disks. While as-built AM parts typically have lower fatigue life due to surface roughness and potential minor defects, HIP is essential for closing internal pores. Combined with appropriate surface finishing (machining, polishing, shot peening) and heat treatment, the fatigue performance of AM superalloys can be brought into line with wrought material requirements, though extensive testing and characterization are always necessary for certification.
- Anisotropi: AM parts can exhibit directionality in properties. Understanding and accounting for this potential anisotropy through design, testing, and build orientation is crucial. Post-processing steps like HIP and heat treatment help homogenize the microstructure, reducing anisotropy.
In summary, while requiring careful process control and extensive post-processing, AM can produce IN738LC and Rene 41 turbine disks with mechanical properties suitable for demanding aerospace applications, often meeting or exceeding the performance of cast equivalents and approaching wrought levels for many critical metrics.
3. What quality control measures are essential for aerospace-grade AM turbine disks?
Ensuring the quality and reliability of flight-critical AM components like turbine disks requires a multi-faceted approach throughout the entire manufacturing process:
- Powder Control: Strict control and traceability of powder chemistry, particle size distribution (PSD), morphology, flowability, and gas content. Testing of virgin and recycled powder batches is mandatory.
- Process Monitoring: In-situ monitoring (where available) of melt pool characteristics, layer consistency, and thermal conditions during the build. Comprehensive logging of all process parameters.
- Post-Processing Verification: Confirmation that stress relief, HIP, and heat treatment cycles were performed correctly according to validated specifications (e.g., furnace charts, pressure logs).
- Dimensionell inspektion: Using CMMs or structured light scanning to verify that all geometric dimensions and tolerances meet drawing requirements after printing and final machining.
- Icke-förstörande testning (NDT):
- Computed Tomography (CT): Crucial for detecting internal defects (pores, inclusions, cracks) and verifying internal channel geometry.
- Fluorescent Penetrant Inspection (FPI): Essential for detecting surface-breaking defects.
- Other methods (e.g., Ultrasonic Testing – UT) may be used depending on specific requirements.
- Material Property Testing: Destructive testing of representative samples built alongside the main component (or cut from it) to verify tensile strength, stress rupture life, fatigue properties, and microstructure meet specifications.
- Full Traceability: Maintaining complete documentation linking the final part back to specific powder batches, machine used, build file, process parameters, post-processing records, NDT results, and operator logs, often managed through an AS9100 certified QMS.
4. Can Met3dp handle production volumes for turbine disk components?
Yes, Met3dp is structured to support industrial production requirements, moving beyond just prototyping.
- Industrial Focus: Met3dp specializes in providing additive manufacturing solutions specifically for industrial applications in demanding sectors like aerospace, medical, and automotive.
- Reliable Equipment: Their SEBM printers are designed for robust, continuous operation, featuring industry-leading print volume and reliability crucial for series production.
- Powder Supply: As a manufacturer of high-performance metal powders, Met3dp can ensure a consistent and high-quality supply of materials like IN738LC and Rene 41 needed for ongoing production runs.
- Omfattande lösningar: By offering integrated solutions covering printers, advanced metal powders, and application development services, Met3dp partners with organizations like aerospace B2B suppliers and OEMs to implement AM efficiently and scale production. Their expertise supports customers in transitioning from R&D to qualified serial manufacturing.
Companies looking for a reliable B2B partner capable of producing certified superalloy turbine disks in production volumes should consider Met3dp’s proven capabilities.
Conclusion: The Future of Aerospace Propulsion Forged with Additive Manufacturing
The landscape of aerospace propulsion is undergoing a significant transformation, and metal additive manufacturing is undeniably a key catalyst. The ability to produce complex, high-performance components like rocket turbine disks from advanced nickel-based superalloys such as IN738LC and Rene 41 using techniques like Selective Electron Beam Melting (SEBM) and Laser Powder Bed Fusion (LPBF) marks a pivotal shift from traditional methods.
We’ve explored how AM unlocks unprecedented design freedom, enabling optimized cooling strategies and lightweight structures that push the boundaries of engine efficiency and performance. We’ve highlighted the critical importance of material quality, starting with meticulously produced powders, and the necessity of rigorous post-processing steps – including stress relief, Hot Isostatic Pressing (HIP), specific heat treatments, and precision machining – to ensure the final component meets the extreme demands and non-negotiable reliability standards of the aerospace industry. Embracing Design for Additive Manufacturing (DfAM) principles and understanding how to navigate challenges like residual stress, porosity, and tolerance achievement are essential for success.
The journey requires not just advanced technology but deep expertise. Selecting the right manufacturing partner – one with proven experience in superalloys, robust quality systems (like AS9100 certification), advanced equipment, comprehensive post-processing capabilities, and end-to-end traceability – is paramount for aerospace OEMs and B2B suppliers aiming to integrate AM into their supply chains effectively.
As a leader providing synergistic solutions encompassing advanced SEBM printers, high-quality metal powders produced via Gas Atomization and PREP, and decades of collective application expertise, Met3dp stands ready to empower organizations in their additive manufacturing journey. We partner with aerospace innovators to turn complex designs into flight-ready hardware, accelerating the development and production of next-generation propulsion systems.
The future of aerospace propulsion is intricately linked with the advancements in additive manufacturing. By leveraging the capabilities of AM and partnering with knowledgeable providers, the industry can continue to reach new heights in performance, efficiency, and exploration.
Ready to explore how Met3dp’s additive manufacturing solutions can elevate your aerospace components? Contact us today to discuss your project requirements with our technical experts.
Dela på
MET3DP Technology Co, LTD är en ledande leverantör av lösningar för additiv tillverkning med huvudkontor i Qingdao, Kina. Vårt företag är specialiserat på 3D-utskriftsutrustning och högpresterande metallpulver för industriella tillämpningar.
Förfrågan för att få bästa pris och anpassad lösning för ditt företag!
Relaterade artiklar
Om Met3DP
Senaste uppdateringen
Vår produkt
KONTAKTA OSS
Har du några frågor? Skicka oss meddelande nu! Vi kommer att betjäna din begäran med ett helt team efter att ha fått ditt meddelande.
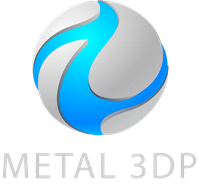
Metallpulver för 3D-printing och additiv tillverkning