Tillämpningar av WAAM inom flyg- och rymdindustrin
Innehållsförteckning
Flyg- och rymdindustrin lever på innovation. Det är en ständig strävan att skapa lättare, starkare och effektivare fordon som kan erövra himlen och andra platser. Här kommer Wire Arc Additive Manufacturing (WAAM), en revolutionerande 3D-utskriftsteknik som snabbt förändrar hur vi bygger flygplan och rymdfarkoster.
Tänk dig att bygga komplexa, nästan nätformade komponenter lager för lager, med hjälp av en bågsvetsningsprocess för att smälta samman metalltråd. Det är det som är kärnan i WAAM. Denna teknik erbjuder en mängd fördelar för flyg- och rymdtillverkare, från kortare ledtider till skapandet av invecklade konstruktioner som tidigare var omöjliga.
Men vad exakt kan WAAM skapa i den vidsträckta rymdvärlden? Spänn fast dig när vi fördjupar oss i de spännande tillämpningarna av WAAM, utforskar de metalliska arbetshästarna som driver processen och svarar på några brännande frågor som du kanske har.
WAAM Kan tillverka flygplanskomponenter
Att skapa framtidens flyg börjar med själva byggstenarna i ett flygplan - dess komponenter. WAAM briljerar på denna arena och gör det möjligt att skapa ett brett utbud av delar:
- Vingar: Tänk dig att tillverka lätta, höghållfasta vingribbor med WAAM. Detta innebär bättre bränsleeffektivitet och ökad nyttolastkapacitet - en win-win för både kommersiella flygbolag och privata jetflygplan.
- Skrovsektioner: Borta är tiden för komplexa, flerdelade flygkroppsenheter. WAAM gör det möjligt att direkttrycka stora sektioner, vilket minskar vikten och förenklar tillverkningsprocessen.
- Landningsställ: Styrka och motståndskraft är av största vikt för landningsställ. WAAM kan skapa dessa kritiska komponenter med hjälp av robusta metallegeringar som titan, vilket garanterar säkra och smidiga landningar i många år framöver.
- Motordelar: Jetmotorernas invecklade värld kan dra nytta av WAAM:s förmåga att tillverka komplexa komponenter med hög tolerans. Tänk skräddarsydda värmeväxlare eller lätta turbinblad - allt för att tänja på gränserna för motorprestanda.
WAAM-fördelen: Jämfört med traditionell maskinbearbetning eller smide erbjuder WAAM betydande fördelar. Det gör det möjligt att skapa delar som är nära nätform, vilket minimerar materialspillet. Möjligheten att bygga komplexa geometrier öppnar dessutom upp för innovativa konstruktioner som tidigare begränsades av traditionella metoder.
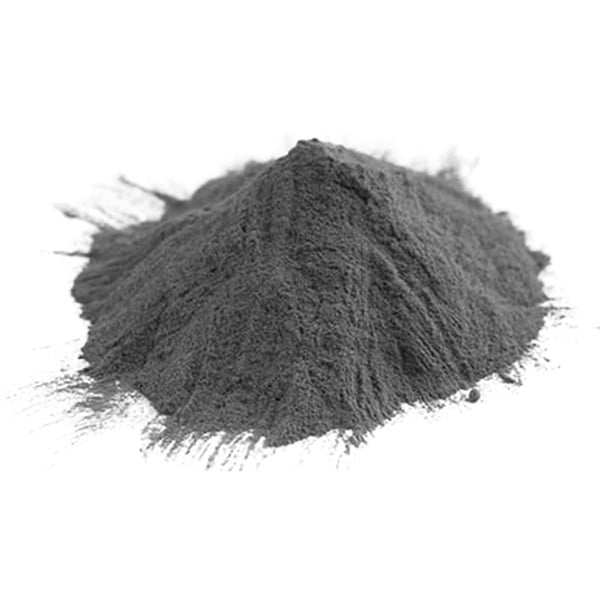
Metal Marvels: Kraftöverföring WAAM inom flyg- och rymdindustrin
Framgången för WAAM beror på de specifika metallegeringar som används. Här är 10 viktiga metallegeringar som spelar en avgörande roll i WAAM-applikationer inom flyg- och rymdindustrin:
Metallegering | Beskrivning | Fastigheter | Tillämpningar inom flyg- och rymdindustrin |
---|---|---|---|
Ti-6Al-4V (titan) | Den självklara metallen för höghållfasta lättviktstillämpningar. Motstår korrosion exceptionellt bra. | Utmärkt förhållande mellan styrka och vikt, god svetsbarhet. | Används ofta för vingkomponenter, delar till landningsställ och motorkomponenter. |
Aluminiumlegeringar (AA2xxx, AA6xxx, AA7xxx) | En familj av mångsidiga legeringar som erbjuder en rad olika hållfastheter och vikter. | Låg vikt, god korrosionsbeständighet (varierar beroende på legering), utmärkt formbarhet. | Idealisk för icke-kritiska strukturella komponenter som vingribbor, flygkroppspaneler och interna komponenter. |
Inconel 625 (nickel-kromlegering) | En mästare för applikationer med höga temperaturer. | Exceptionellt motståndskraftig mot värme, oxidation och korrosion. | Perfekt för jetmotorkomponenter som brännkammare, efterbrännkammare och avgaskanaler. |
Inconel 718 (nickel-kromlegering) | Erbjuder en balans mellan styrka, högtemperaturprestanda och god bearbetbarhet. | Hög hållfasthet, god krypbeständighet vid förhöjda temperaturer. | Används för strukturella komponenter i heta sektioner i jetmotorer och högpresterande flygplanskroppar. |
Maråldrat stål (18Ni250 Maråldrat) | Ett utskiljningshärdande stål som är känt för sin exceptionella hållfasthet. | Ultrahög hållfasthet, god seghet och dimensionsstabilitet. | Idealisk för komponenter till landningsställ och flygplansapplikationer med hög belastning. |
Rostfritt stål (316L) | En vanlig rostfri stålkvalitet med god korrosionsbeständighet. | God korrosionsbeständighet, svetsbarhet och formbarhet. | Används för icke-strukturella komponenter som fästen, höljen och inre delar som kräver korrosionsbeständighet. |
Kopparlegeringar (C175, C268) | Dessa legeringar har utmärkt elektrisk ledningsförmåga och termiska egenskaper. | Hög elektrisk ledningsförmåga, god värmeledningsförmåga och korrosionsbeständighet. | Används för värmeväxlare, elektriska komponenter och applikationer som kräver god värmeavledning. |
Hastelloy X (nickel-krom-molybdenlegering) | En mästare för extrema miljöer, med exceptionell motståndskraft mot ett brett spektrum av kemikalier. | Utmärkt korrosionsbeständighet, god mekanisk hållfasthet vid höga temperaturer. | Används för komponenter som utsätts för starka kemikalier, t.ex. bränslesystem och delar som hanterar korrosiva vätskor. |
Tantal (TA2) | En sällsynt |
WAAM kan tillverka komponenter till rymdfarkoster
Utforskning av rymden kräver ingenjörskonst på högsta nivå. WAAM antar utmaningen genom att göra det möjligt att skapa viktiga komponenter för rymdfarkoster:
- Bränsletankar: Tänk dig att konstruera lätta, höghållfasta bränsletankar för satelliter eller raketer. WAAM gör det möjligt att skriva ut komplexa former med minimala svetsningar, vilket minskar vikten och risken för läckage.
- Motordelar: I likhet med flygplansmotorer kan WAAM tillverka komplicerade komponenter med hög tolerans för framdrivningssystem till rymdfarkoster. Tänk dig skräddarsydda raketmunstycken eller lättviktsmotorfästen som flyttar fram gränserna för rymdfarkosters prestanda.
- Värmesköldar: Återinträdet i jordens atmosfär genererar brännande hetta. WAAM kan skapa värmesköldar med hjälp av legeringar som är särskilt utformade för att klara extrema temperaturer och skydda rymdfarkoster under deras brinnande nedstigning.
- Strukturella komponenter: Ramverket i en rymdfarkost måste vara starkt men ändå lätt. WAAM gör det möjligt att skriva ut skräddarsydda strukturelement och optimera vikt och styrka för ett framgångsrikt rymduppdrag.
WAAM-fördelen i rymden: Fördelarna med WAAM sträcker sig längre än bara till flygplan. I den oförlåtande rymdmiljön är WAAM:s förmåga att skapa komponenter med nära nettovorm och minimalt spill avgörande. Dessutom ger de kortare ledtiderna som erbjuds av WAAM kan påskynda utvecklingen och uppskjutningen av rymdfarkoster och förkorta den tid det tar att nå den sista gränsen.
WAAM Kan tillverka reparationsdelar
Flyg- och rymdindustrin är starkt beroende av att upprätthålla en välmående flygplansflotta. WAAM kan spela en viktig roll på detta område genom att möjliggöra utskrift av reservdelar på begäran:
- Komponenter till landningsställ: Mindre sprickor eller skador på landningsställ kan utgöra en betydande säkerhetsrisk. WAAM möjliggör snabb och effektiv reparation av sådana komponenter, vilket minimerar stilleståndstiden och säkerställer fortsatt säker drift av flygplanen.
- Motordelar: På samma sätt som man skapar nya delar kan WAAM användas för att reparera slitna eller skadade motorkomponenter. Detta förlänger livslängden på motorerna och minskar behovet av dyra utbyten.
- Skrovets paneler: Mindre bucklor eller sprickor på en flygkroppspanel kan enkelt repareras med WAAM. Detta minimerar stilleståndstiden och säkerställer flygplanets strukturella integritet.
WAAM-fördelen vid reparationer: Traditionella metoder för att reparera flygplansdelar kan vara tidskrävande och dyra. WAAM erbjuder en snabbare och mer kostnadseffektiv lösning. Möjligheten att skriva ut delar på begäran minskar dessutom behovet av omfattande lagerhantering, vilket effektiviserar reparationsprocessen.
WAAM:s framtid inom flyg- och rymdindustrin
WAAM:s potential inom flyg- och rymdindustrin sträcker sig långt utöver de tillämpningar som anges ovan. I takt med att tekniken mognar kan vi förvänta oss att se ännu fler innovativa användningsområden växa fram:
- Anpassning: WAAM:s förmåga att skapa komplexa geometrier öppnar dörrar för mycket kundanpassade komponenter till flygplan och rymdfarkoster. Föreställ dig att skapa skräddarsydda vingar för ökad bränsleeffektivitet eller lätta motorfästen som är optimerade för ett specifikt uppdrag.
- Tillverkning på begäran: Framtiden för flygplanstillverkning kan innebära att delar skrivs ut på begäran vid reparationsanläggningar eller till och med direkt på flygplatser. Detta skulle avsevärt minska ledtiderna och effektivisera underhållsprocessen.
- Hybridtillverkning: WAAM kan integreras med andra tillverkningstekniker för att skapa ännu mer komplexa och högpresterande komponenter. Tänk dig att kombinera WAAM med traditionell maskinbearbetning för detaljer som kräver en blandning av olika funktioner.
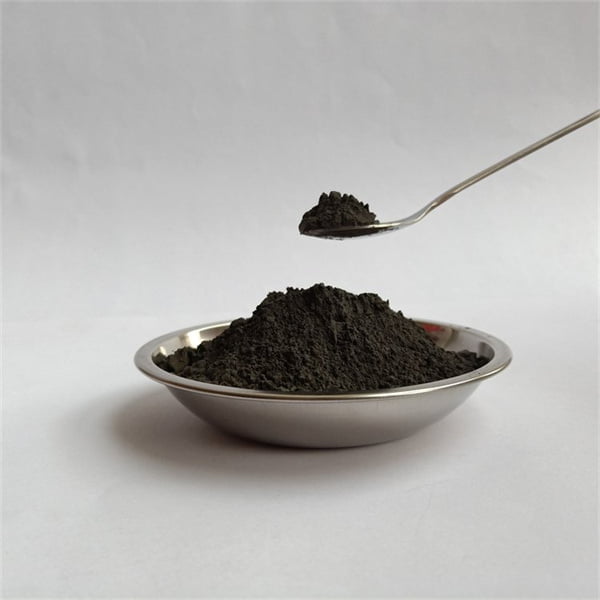
VANLIGA FRÅGOR
Här följer några vanliga frågor om WAAM och dess tillämpningar inom flyg- och rymdindustrin:
Q: Vilka är begränsningarna med WAAM inom flyg- och rymdindustrin?
S: Även om WAAM erbjuder många fördelar finns det begränsningar att ta hänsyn till. Ytkvaliteten på WAAM-tryckta delar kan vara grövre jämfört med traditionellt maskinbearbetade delar. Dessutom är tekniken fortfarande under utveckling, och utbudet av kvalificerade material för flyg- och rymdtillämpningar utvecklas.
F: Är WAAM säkert för användning i kritiska komponenter inom flyg- och rymdindustrin?
Svar: WAAM-komponenter kan vara säkra för kritiska tillämpningar, men det krävs noggranna test- och kvalificeringsförfaranden. Regleringsorgan inom flygindustrin har fastställt standarder för WAAM-komponenter som används i flygkritiska applikationer.
F: Hur ser kostnaden ut för WAAM jämfört med traditionella tillverkningsmetoder?
S: Kostnaden för WAAM kan variera beroende på hur komplex detaljen är och vilka material som används. WAAM kan dock ge betydande kostnadsbesparingar i det långa loppet tack vare minskat spill och kortare ledtider.
F: Vilka är miljöfördelarna med att använda WAAM inom flyg- och rymdindustrin?
S: WAAM ger miljöfördelar genom att minimera materialavfallet jämfört med traditionella bearbetningsmetoder. Dessutom kan möjligheten att skapa lättare flygplanskomponenter bidra till förbättrad bränsleeffektivitet och minskade utsläpp.
Slutsats
WAAM revolutionerar det sätt på vilket vi bygger och underhåller flygplan och rymdfarkoster. Från komplexa komponenter med nära nätform till reparationer på begäran erbjuder WAAM en skattkista av fördelar för flygindustrin.
Dela på
MET3DP Technology Co, LTD är en ledande leverantör av lösningar för additiv tillverkning med huvudkontor i Qingdao, Kina. Vårt företag är specialiserat på 3D-utskriftsutrustning och högpresterande metallpulver för industriella tillämpningar.
Förfrågan för att få bästa pris och anpassad lösning för ditt företag!
Relaterade artiklar
Om Met3DP
Senaste uppdateringen
Vår produkt
KONTAKTA OSS
Har du några frågor? Skicka oss meddelande nu! Vi kommer att betjäna din begäran med ett helt team efter att ha fått ditt meddelande.
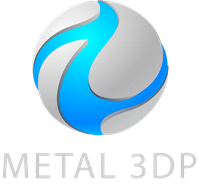
Metallpulver för 3D-printing och additiv tillverkning