Jämförelse mellan DED-teknik och WAAM-teknik
Innehållsförteckning
Inledning
Hook: Tänk dig att skapa komplexa metallföremål lager för lager, med smält metall som omsorgsfullt deponeras för att bygga allt från höga vindkraftverkskomponenter till komplicerade medicinska implantat. Denna fängslande värld hör till Directed Energy Deposition (DED) och Wire Arc Additive Manufacturing (WAAM), två revolutionerande tekniker för additiv tillverkning av metall (AM).
Problem: Att välja mellan DED och WAAM kan vara en skrämmande uppgift. Båda har imponerande egenskaper, men deras nyanser kan ha stor inverkan på projektresultaten.
Lösning: Denna djupgående undersökning kommer att dissekera DED och WAAM och jämföra deras centrala aspekter, tillämpningar och lämplighet för olika scenarier.
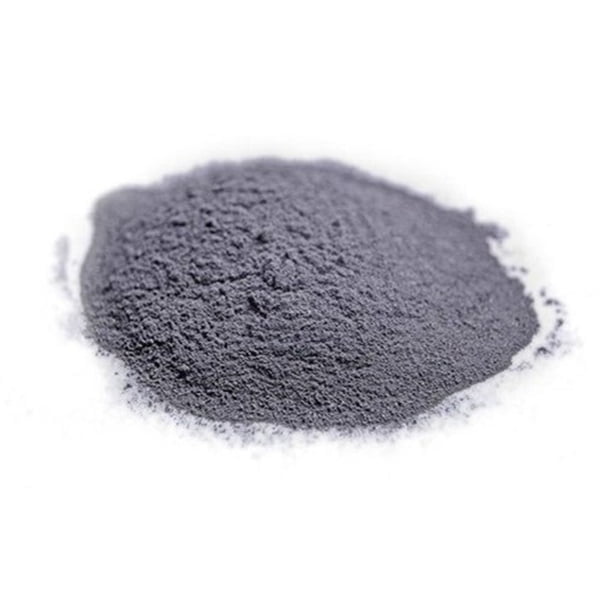
Förståelse för DED-teknik
Definition: DED är en bred kategori av AM-processer som använder en koncentrerad energikälla (laser, elektronstråle, plasmabåge) för att smälta och smälta samman material (vanligtvis metallpulver) på en byggplattform och skapa ett 3D-objekt lager för lager.
Värmekällor:
Laser DED: Högeffektslasrar ger exakt kontroll och utmärkt upplösning, vilket är perfekt för komplicerade geometrier. Populära material är bland annat rostfritt stål, titanlegeringar och Inconel.
Elektronstråle DED: Genererar högfokuserade energistrålar i en vakuumkammare, vilket möjliggör överlägset smältdjup och kompatibilitet med reaktiva metaller som titan.
Plasmabåge DED: Använder en plasmabrännare för att smälta råmaterialet, vilket ger snabbare deponeringshastigheter och kostnadseffektivitet för större strukturer, ofta med användning av vanliga svetstrådar.
Metallpulver för DED:
Metallpulver | Beskrivning | Fördelar | Begränsningar |
---|---|---|---|
Rostfritt stål 316L | Mångsidigt austenitiskt stål som är känt för sin utmärkta korrosionsbeständighet, biokompatibilitet och höga hållfasthet. | Används ofta inom flyg- och rymdindustrin, medicinska implantat och kemisk bearbetning. | Kan kräva efterbearbetning för optimal ytfinish. |
Inconel 625 | Nickel-krom-superlegering som är känd för sin högtemperaturhållfasthet, oxidationsbeständighet och krypbeständighet. | Används i krävande applikationer inom flyg- och rymdindustrin, gasturbiner och kärnkraft. | Dyrare än vanliga stål. |
Titan Ti-6Al-4V | Titanlegering som ger en bra balans mellan styrka, vikt och korrosionsbeständighet. | Populär inom flyg- och rymdindustrin, biomedicin och sportartiklar tack vare sin biokompatibilitet. | Riskerar att kontamineras av syre under tryckningen, vilket kräver noggrann hantering. |
Aluminium AlSi10Mg | Legering som kombinerar god hållfasthet med lättviktsegenskaper och förbättrad gjutbarhet. | Används inom bilindustrin, flygindustrin och marina applikationer för viktreduktion. | Mycket reaktiva, kräver miljöer med inert gas för tryckning. |
Verktygsstål H13 | Verktygsstål för varmbearbetning som är känt för sin utmärkta slitstyrka och varmhållfasthet. | Används för formar, matriser och stansar som används i metallformnings- och smidesprocesser. | Kan vara svårt att trycka på grund av den höga kolhalten. |
Nickellegering 718 | Höghållfast, utskiljningshärdande nickellegering med utmärkta mekaniska egenskaper vid förhöjda temperaturer. | Används i flyg- och rymdkomponenter för sin styrka och krypbeständighet. | Dyrare än andra alternativ. |
Koppar | Mycket ledande metall med termiska och elektriska tillämpningar. | Används i elektriska ledare, värmeväxlare och elektroniska komponenter. | Benägen att oxidera under tryckning, vilket kräver kontrollåtgärder. |
Kobolt Krom (CoCr) | Biokompatibel legering som används för slitstarka medicinska implantat. | Används i höft- och knäproteser tack vare sin utmärkta slitstyrka. | Kan kräva särskild hantering och efterbearbetning för att optimera biokompatibiliteten. |
Inconel 718C | Variation av Inconel 625 med förbättrade gjutegenskaper och svetsbarhet. | Används i turbinblad och andra applikationer med höga temperaturer. | Liknande egenskaper och begränsningar som Inconel 625. |
Tillämpningar av DED: Flyg- och rymdkomponenter, medicinska implantat, reparation av slitna delar, verktyg och storskaliga metallkonstruktioner.
Avmystifiering WAAM Teknik
Definition: WAAM, eller Wire Arc Additive Manufacturing, är en DED-variant som använder en kontinuerlig trådmatning och en elektrisk båge (vanligtvis gasmetallbågsvetsning) för att smälta och deponera materialet.
Fördelar:
Kostnadseffektivitet: WAAM utnyttjar befintlig bågsvetsteknik och lättillgänglig tråd, vilket gör den till ett mer prisvärt alternativ jämfört med pulverbaserade DED-processer.
Höga deponeringshastigheter: WAAM ger snabbare deponeringshastigheter tack vare den kontinuerliga trådmatningen och ljusbågens högre energitäthet, vilket gör den lämplig för storskaliga projekt.
Materialkompatibilitet: WAAM erbjuder bred materialkompatibilitet med olika vanliga svetstrådar, t.ex:
Stål: Mjukt stål, rostfria stålsorter (304L, 316L), duplex rostfritt stål och verktygsstål.
Aluminium: Aluminiumlegeringar som AlSi10Mg och Al 6061.
Nickellegeringar: Inconel 625 och Nickel Alloy 718.
Övriga metaller: Koppar- och titanlegeringar (begränsad användning på grund av oxidationsproblem).
Tillämpningar av WAAM: Skeppsbyggnad, konstruktion (brokomponenter, balkar), storskaliga tryckkärl, reparation av tunga maskiner och snabb prototyptillverkning av stora metallkonstruktioner.
Viktiga överväganden: DED kontra WAAM
Tryckhastigheten för DED-teknik och WAAM Tekniken är annorlunda
- DED: Erbjuder ett bredare utbud av utskriftshastigheter beroende på värmekälla och pulvermatningshastighet. Laser DED ger långsammare hastigheter för högprecisionsarbeten, medan plasma arc DED ger högre hastigheter för större konstruktioner.
- WAAM: Generellt sett har DED-processerna de snabbaste deponeringshastigheterna tack vare den kontinuerliga trådmatningen och ljusbågens högre energitäthet.
Materialkostnaderna för DED-teknik och WAAM-teknik skiljer sig åt
- DED: Kan vara dyrare, särskilt för processer som använder specialiserade metallpulver som Inconel eller reaktiva metaller som titan.
- WAAM: Vanligtvis mer kostnadseffektiva tack vare användningen av lättillgängliga och ofta billigare svetstrådar.
Ytfinishen för DED-teknik och WAAM-teknik är olika
- DED: Laser-DED ger den jämnaste ytfinishen tack vare den exakta kontrollen över laserstrålen. DED med elektronstråle ger också bra ytfinish. Plasmabåge-DED är visserligen snabbare, men kan kräva mer efterbearbetning för att uppnå önskad ytkvalitet.
- WAAM: Ger i allmänhet grövre ytfinish jämfört med laser-DED på grund av det stänk som uppstår i samband med bågsvetsningsprocessen. WAAM-ytor kan dock bearbetas eller slipas för önskad finish.
Applikationsfälten är olika
- DED: Lämpar sig väl för komplicerade komponenter med hög precision som kräver utmärkt ytfinish, t.ex. flygplansdelar, medicinska implantat och formar.
- WAAM: Utmärkt för storskaliga metallkonstruktioner, snabb prototyptillverkning av skrymmande delar, skeppsbyggnadskomponenter och reparation av massiva maskiner tack vare sin höga deponeringshastighet och kostnadseffektivitet.
Utrustningskostnader för DED-teknik och WAAM-teknik
- DED: DED-system, särskilt de som använder laser eller elektronstrålar, tenderar att vara dyrare än WAAM-maskiner på grund av den komplexa tekniken.
- WAAM: WAAM-system utnyttjar ofta befintlig bågsvetsteknik, vilket gör dem till ett mer prisvärt DED-alternativ.
Fördelar och begränsningar Jämförelsetabell
Funktion | DED | WAAM |
---|---|---|
Värmekälla | Laser, elektronstråle, plasmabåge | Elektrisk bågsvetsning (gasmetallbågsvetsning) |
Råmaterial | Metallpulver | Kontinuerlig tråd |
Depositionshastighet | Varierande (Laser DED: Långsam, Plasma Arc DED: Snabbare) | Hög |
Materialkompatibilitet | Bredare utbud av material, inklusive reaktiva metaller | Främst vanliga material för svetstråd |
Ytfinish | Kan vara mycket smidig (Laser DED) | Generellt grövre |
Tillämpningar | Komplicerade komponenter, medicinska implantat, formar | Storskaliga strukturer, snabb prototyptillverkning, reparation |
Kostnad för utrustning | Generellt högre | Generellt lägre |
Materialkostnad | Kan vara högre för specialiserade pulver | Lägre för vanliga svetstrådar |
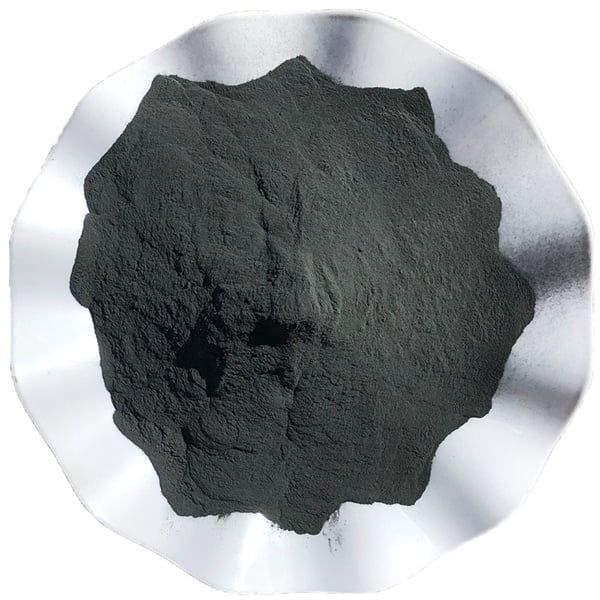
Att välja mellan DED och WAAM
Det optimala valet mellan DED och WAAM beror på dina specifika projektkrav:
För komplicerade detaljer med kritisk ytfinhet och ett bredare materialurval är DED (särskilt Laser DED) sannolikt det bättre valet.
För storskaliga, kostnadskänsliga tillämpningar där deponeringshastighet och lättillgängliga material är prioriterade, är WAAM en lysande lösning.
Ytterligare överväganden:
- Projektets komplexitet: DED utmärker sig i komplicerade geometrier.
- Krav på material: DED erbjuder bredare materialalternativ, inklusive reaktiva metaller.
- Produktionsvolym: WAAM:s snabbhet är en fördel för projekt med stora volymer.
- Budget: WAAM är i allmänhet mer kostnadseffektivt.
Framtiden för DED och WAAM
Både DED- och WAAM-teknikerna utvecklas snabbt. Vi kan förvänta oss framsteg inom:
- Kapacitet för flera material: DED och WAAM kan integrera funktioner för att deponera olika material i samma byggnad för kompositstrukturer.
- Hybrid DED/WAAM-system: Genom att kombinera DED och WAAM i en och samma maskin kan man få större flexibilitet när det gäller materialval och deponeringshastigheter.
- Förbättrad kontroll och automatisering: Förbättrad mjukvaru- och sensorintegration kommer att leda till mer exakt kontroll över tryckprocessen.
VANLIGA FRÅGOR
Fråga: Vilken teknik är snabbast, DED eller WAAM?
S: WAAM har i allmänhet de snabbaste deponeringshastigheterna bland DED-processerna. Den kontinuerliga trådmatningen och den högre energitätheten hos ljusbågen i WAAM möjliggör snabbare materialdeponering jämfört med DED, särskilt pulverbaserade DED-metoder. Laser-DED kan dock uppnå måttliga hastigheter för komplicerade arbeten som kräver hög precision.
F: Är DED eller WAAM dyrare?
S: WAAM är vanligtvis det mer kostnadseffektiva alternativet. Här är en uppdelning:
- Utrustning: WAAM-system utnyttjar befintlig bågsvetsteknik, vilket gör dem mer prisvärda än DED-maskiner, särskilt de som använder laser eller elektronstrålar.
- Material: DED kan bli dyrare om du behöver specialiserade metallpulver som Inconel eller reaktiva metaller som titan. WAAM använder lättillgängliga och ofta billigare svetstrådar.
Q: Vilken teknik ger en bättre ytfinish?
S: DED, särskilt laser-DED, utmärker sig genom att ge en jämn ytfinish tack vare den exakta kontrollen över laserstrålen. DED med elektronstråle ger också bra resultat. DED med plasmabåge är visserligen snabbare, men kan kräva mer efterbearbetning för att uppnå önskad ytkvalitet. WAAM ger i allmänhet en grövre yta jämfört med laser-DED på grund av det sprut som uppstår i samband med bågsvetsningsprocessen. WAAM-ytor kan dock bearbetas eller slipas för att få en jämnare finish.
Q: Vilken typ av delar är DED och WAAM lämpliga för?
S: DED och WAAM vänder sig till olika tillämpningsområden:
- DED: Idealisk för invecklade komponenter med hög precision som kräver utmärkt ytfinish, t.ex:
- Delar till flyg- och rymdindustrin (turbinblad, motorkomponenter)
- Medicinska implantat (höftledsproteser, tandproteser)
- Gjutformar och verktygsinsatser
- WAAM: Utmärker sig i storskaliga metallstrukturer och applikationer där:
- Höga deponeringshastigheter är avgörande (komponenter för skeppsbyggnad, brobalkar)
- Behov av snabb prototyptillverkning av skrymmande delar
- Kostnadseffektivitet är en viktig faktor (reparation av stora maskiner)
F: Är DED eller WAAM mer miljövänligt?
S: Både DED och WAAM kan betraktas som miljövänliga jämfört med traditionella subtraktiva tillverkningstekniker som maskinbearbetning. Här är varför:
- Minskat materialavfall: DED och WAAM använder additiva processer som bygger delar lager för lager med minimalt materialspill jämfört med maskinbearbetning, där överflödigt material tas bort.
- Potential för återvinning: Metallpulver som används i DED kan potentiellt återvinnas och återanvändas i framtida konstruktioner, vilket minimerar miljöpåverkan.
Sammanfattningsvis, DED och WAAM är kraftfulla tekniker för additiv tillverkning av metall med olika styrkor och användningsområden. Genom att förstå deras grundläggande principer, materialkompatibilitet och lämplighet för olika projektkrav kan du fatta ett välgrundat beslut om vilken teknik som bäst passar dina behov. I takt med att dessa tekniker fortsätter att utvecklas kan vi förvänta oss ännu större kapacitet och bredare användning inom olika branscher.
Dela på
MET3DP Technology Co, LTD är en ledande leverantör av lösningar för additiv tillverkning med huvudkontor i Qingdao, Kina. Vårt företag är specialiserat på 3D-utskriftsutrustning och högpresterande metallpulver för industriella tillämpningar.
Förfrågan för att få bästa pris och anpassad lösning för ditt företag!
Relaterade artiklar
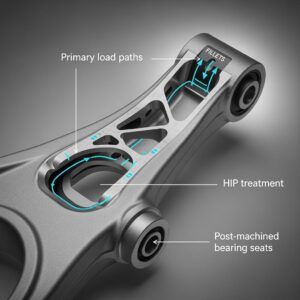
Metal 3D Printing for U.S. Automotive Lightweight Structural Brackets and Suspension Components
Läs mer "Om Met3DP
Senaste uppdateringen
Vår produkt
KONTAKTA OSS
Har du några frågor? Skicka oss meddelande nu! Vi kommer att betjäna din begäran med ett helt team efter att ha fått ditt meddelande.