introduktion till Wire Arc Additive Manufacturing
Innehållsförteckning
Föreställ dig att bygga stora, robusta metalldelar lager för lager, inte genom subtraktiva tillverkningstekniker som bearbetning, utan genom att lägga till material noggrant. Denna transformerande teknik är Tillverkning av trådbågetillsats (WAAM), redo att omforma hur vi skapar kritiska komponenter inom olika branscher.
Arbetsprincipen för wire Arc Additive Manufacturing
WAAM, även känd som Directed Energy Deposition-Arc (DED-Arc), faller under paraplyet Direct Energy Deposition (DED) 3D-utskriftsteknik. Den använder en kontrollerad elektrisk ljusbåge som en värmekälla för att smälta förbrukningsbar metalltråd. Denna smälta metall avsätts sedan noggrant, lager på lager, för att bygga den önskade 3D-strukturen.
Se det som en högteknologisk svetsprocess på steroider. Istället för att bara sammanfoga befintliga delar skapar WAAM helt nya objekt från grunden. En robotarm manövrerar trådmatningen och svetsbrännaren exakt, enligt en förprogrammerad digital ritning. När varje lager stelnar, läggs ett nytt ovanpå, vilket gradvis ger den digitala designen liv.
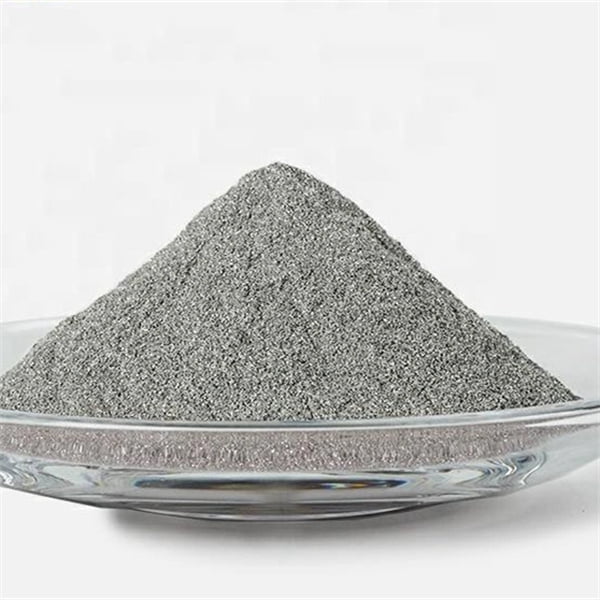
Processegenskaper hos Tillverkning av trådbågetillsats
WAAM erbjuder flera distinkta fördelar jämfört med traditionella tillverkningsmetoder:
- Hög avsättningshastighet: Jämfört med pulverbaserade 3D-utskriftstekniker av metall, har WAAM betydligt snabbare avsättningshastigheter. Detta leder till snabbare produktionstider, särskilt för storskaliga komponenter.
- Materialeffektivitet: WAAM använder tråd som råmaterial, vilket minimerar materialspill jämfört med subtraktiva tillverkningsprocesser som tar bort överskottsmaterial från ett massivt block.
- Tryckning i stor skala: WAAM utmärker sig på att skapa stora, komplexa metallstrukturer. Till skillnad från vissa pulverbaserade metoder som begränsas av byggkammarens storlek, kan WAAM-system fungera i öppna miljöer, vilket möjliggör tillverkning av massiva föremål.
- Materialets mångsidighet: WAAM är kompatibel med ett brett utbud av metallegeringar, inklusive stål, aluminium, nickellegeringar och titanlegeringar. Detta breda materialspektrum vänder sig till olika applikationer som kräver specifika mekaniska egenskaper.
Men WAAM har också begränsningar att ta hänsyn till:
- Ytfinish: Processen för deponering av smält metall i WAAM kan resultera i en grövre ytfinish jämfört med vissa pulverbaserade metoder. Efterbearbetningstekniker som slipning eller bearbetning kan vara nödvändiga för att uppnå en jämnare yta beroende på applikation.
- Återstående stress: De snabba uppvärmnings- och nedkylningscyklerna som är inneboende i WAAM kan införa restspänningar i den tryckta delen. Detta måste åtgärdas genom korrekt värmebehandling eller designöverväganden för att säkerställa dimensionsstabilitet och förhindra potentiell sprickbildning.
- Noggrannhet: Även om WAAM erbjuder imponerande upplösning, kanske det inte matchar de fina detaljer som kan uppnås med vissa puderbaserade tekniker. Valet beror på den specifika delens dimensionella toleranser och krav på komplexitet.
Metallpulver för Tillverkning av trådbågetillsats
Medan WAAM använder kontinuerligt trådmaterial, är det viktigt att förstå egenskaperna hos motsvarande metallpulver som används för att skapa dessa trådar. Här är en uppdelning av några vanliga metallpulver i WAAM:
Material | Sammansättning | Fastigheter | Tillämpningar |
---|---|---|---|
Lågkolhaltigt stål (SAE 1005, AISI 1008) | Fe (Järn) med minimal kolhalt | Hög duktilitet, bra svetsbarhet, utmärkt bearbetningsförmåga | Allmänna konstruktionskomponenter, konsoler, kapslingar |
Höghållfast låglegerat (HSLA) stål (ASTM A514) | Fe med högre kolhalt och mikrolegeringselement som mangan, vanadin och niob | Förbättrat förhållande mellan styrka och vikt, bra seghet | Byggutrustning, transportkomponenter, tryckkärl |
Rostfritt stål (304L, 316L) | Fe med krom, nickel och molybden för korrosionsbeständighet | Utmärkt korrosionsbeständighet, god formbarhet | Utrustning för livsmedelsbearbetning, medicinsk utrustning, kemiska bearbetningstankar |
Aluminium (AA 5356, AA 6061) | Al (Aluminium) med magnesium för ökad styrka | Högt förhållande mellan styrka och vikt, god korrosionsbeständighet | Flyg- och rymdkomponenter, bildelar, marina applikationer |
Nickellegeringar (Inconel 625, Inconel 718) | Ni (nickel) med krom, molybden och andra element för prestanda vid hög temperatur | Exceptionell styrka och oxidationsbeständighet vid förhöjda temperaturer | Gasturbinkomponenter, värmeväxlare, tryckkärl för tuffa miljöer |
Titan (Ti-6Al-4V) | Ti (Titan) med aluminium och vanadin för ökad styrka | Högt förhållande mellan styrka och vikt, utmärkt biokompatibilitet | Flyg- och rymdkomponenter, biomedicinska implantat, sportartiklar |
Denna tabell ger en inblick i de olika metallpulver som används i WAAM trådmatningsmaterial. Det specifika materialvalet beror på önskade mekaniska egenskaper, korrosionsbeständighet och applikationskrav.
Ytterligare överväganden:
- Tråddiameter: Diametern på trådmatningsmaterialet spelar en avgörande roll i WAAM. Tjockare trådar möjliggör snabbare avsättningshastigheter men kan resultera i en grövre ytfinish. Omvänt ger tunnare trådar finare detaljer men leder till långsammare byggtider. Den optimala diametern beror på den önskade balansen mellan bygghastighet, upplösning och behov av efterbearbetning.
- Trådmaterialkvalitet: Konsekvent tråddiameter, minimala ytdefekter och korrekt kemisk sammansättning är avgörande för framgångsrik WAAM-utskrift. Högkvalitativt trådmaterial säkerställer jämn avsättning, minimerar stänk (smälta metalldroppar som sprutas ut under svetsning) och ger förutsägbara mekaniska egenskaper i den färdiga delen.
Utvecklingstrenderna för Tillverkning av trådbågetillsats
WAAM är en teknik som utvecklas snabbt. Här är några spännande trender som formar dess framtid:
- Hybrid WAAM-system: Att integrera WAAM med andra additiv tillverkningstekniker, som pulverbäddfusion, vinner dragkraft. Detta gör det möjligt att kombinera fördelarna med WAAM:s höga avsättningshastighet för stora funktioner med de finare detaljerna som kan uppnås genom pulverbaserade metoder för intrikata detaljer.
- Automation och styrsystem: Framsteg inom automations- och kontrollsystem förbättrar WAAMs processstabilitet och repeterbarhet. Detta inkluderar utveckling inom realtidsövervakning, sensorintegration och automatiserade processjusteringar, vilket leder till mer konsekvent och pålitlig detaljproduktion.
- Utveckling av material: Utforskningen av nya metallegeringar och kompositmaterial som är speciellt skräddarsydda för WAAM pågår. Detta öppnar dörrar för att skapa komponenter med ännu bättre mekaniska egenskaper, högtemperaturprestanda och skräddarsydda funktionaliteter.
Dessa framsteg banar väg för WAAM att bli ett ännu mer mångsidigt och kraftfullt verktyg inom olika branscher.
Tillämpningar av Wire Arc Additive Manufacturing
WAAMs unika kapacitet gör det till ett övertygande alternativ för ett brett utbud av applikationer, inklusive:
- Aerospace: Tillverkning av stora, lätta strukturella komponenter för flygplan och rymdfarkoster, som utnyttjar WAAMs förmåga att hantera höghållfast aluminium och titanlegeringar.
- Fordon: Skapa komplexa motorkomponenter, anpassade fästen och lätta chassidelar och dra nytta av WAAMs hastighet och materialeffektivitet.
- Olja och gas: Utskrift av invecklade rörsystem, tryckkärl och reparationsdelar för tuffa miljöer, där WAAM:s materialmångsidighet och förmåga att hantera tjockväggiga strukturer spelar in.
- Konstruktion: Att bygga skräddarsydda arkitektoniska element, broar och storskaliga komponenter på plats, där WAAM:s förmåga att arbeta i öppna miljöer är fördelaktigt.
- Skeppsbyggnad: Tillverkar robusta fartygskomponenter, propellrar och reparationsdelar, dra nytta av WAAM:s lämplighet för arbete med stora stålkonstruktioner.
- Medicintekniska produkter: Skapa anpassade proteser, implantat och kirurgiska instrument med biokompatibla material som titan, vilket utnyttjar WAAMs förmåga att producera komplexa geometrier.
Detta är bara några exempel, och i takt med att WAAM-tekniken fortsätter att mogna förväntas dess tillämpningsområde att utökas ytterligare.
Fördelar och begränsningar med Tillverkning av trådbågetillsats
Fördelar:
- Hög avsättningshastighet: Möjliggör snabbare produktionstider, speciellt för storskaliga komponenter.
- Materialeffektivitet: Minimerar avfall jämfört med subtraktiv tillverkning.
- Tryckning i stor skala: Idealisk för att skapa stora, komplexa metallstrukturer.
- Materialets mångsidighet: Kompatibel med ett brett utbud av metallegeringar.
- Kostnadseffektivitet: Kan vara ett kostnadskonkurrenskraftigt alternativ för vissa applikationer jämfört med traditionella tillverkningsmetoder.
Begränsningar:
- Ytfinish: Kan kräva efterbearbetning för en jämn finish.
- Återstående stress: Kräver värmebehandling eller designöverväganden för att hantera.
- Noggrannhet: Får kanske inte de fina detaljerna i vissa pulverbaserade tekniker.
- Begränsad byggmiljö: Friluftssystem kan vara känsliga för miljöfaktorer som vind.
Noggrant övervägande av både fördelar och begränsningar är avgörande när man avgör om WAAM är den mest lämpliga tekniken för en viss applikation.
Jämförelse av WAAM med andra tillverkningstekniker för metalltillsats
WAAM är inte den enda spelaren i 3D-utskriftsspelet i metall. Här är en uppdelning av hur det står sig mot några andra framstående metoder:
Funktion | WAAM | Selektiv lasersmältning (SLM) | Smältning med elektronstråle (EBM) | Binder Jetting (BJ) |
---|---|---|---|---|
Depositionshastighet | Hög | Låg | Låg | Medelhög till hög |
Materialets mångsidighet | Brett utbud av metallegeringar | Begränsad till kompatibla legeringar | Begränsad till kompatibla legeringar | Brett utbud av metaller och keramik |
Ytfinish | Grovare, kan kräva efterbearbetning | Smidig | Smidig | Grovt, kräver efterbearbetning |
Bygg kuvertet | Stor, öppen miljö möjlig | Begränsad av kammarstorlek | Begränsad av kammarstorlek | Begränsad av kammarstorlek |
Material Avfall | Låg | Måttlig | Måttlig | Låg |
Kostnad per enhet | Kan vara kostnadseffektivt för stora delar | Hög | Hög | Måttlig till Låg |
Tillämpningar | Stora komponenter, olika industrier | Flyg-, medicinska, högvärdiga delar | Flyg-, medicinska, högvärdiga delar | Prototyper, verktyg, komplexa former |
Att välja rätt tillverkningsteknik för metalltillsats
Den optimala tillverkningstekniken för metalltillsats beror på olika faktorer, inklusive:
- Delstorlek och komplexitet: WAAM utmärker sig på storskaliga delar, medan SLM och EBM kan vara bättre lämpade för intrikata, mindre komponenter. BJ erbjuder en balans för medelstora detaljer med komplexa geometrier.
- Krav på material: Tänk på nödvändiga materialegenskaper och kompatibilitet med varje teknik. WAAM har en bred materialmångsidighet, medan SLM och EBM har begränsningar. BJ kan hantera ett brett utbud av metaller och även keramik.
- Ytbehandlingsbehov: Om en jämn finish är kritisk kan SLM eller EBM vara att föredra, medan WAAM kan kräva efterbearbetning. BJ kräver vanligtvis efterbearbetning för en jämn finish.
- Överväganden om kostnader: WAAM kan vara kostnadseffektivt för stora delar, medan SLM och EBM generellt har högre kostnader. BJ erbjuder ett mellanklassalternativ.
Genom att noggrant utvärdera dessa faktorer och styrkorna och begränsningarna för varje teknik, kan du fatta ett välgrundat beslut om den mest lämpliga metoden för din specifika tillämpning.
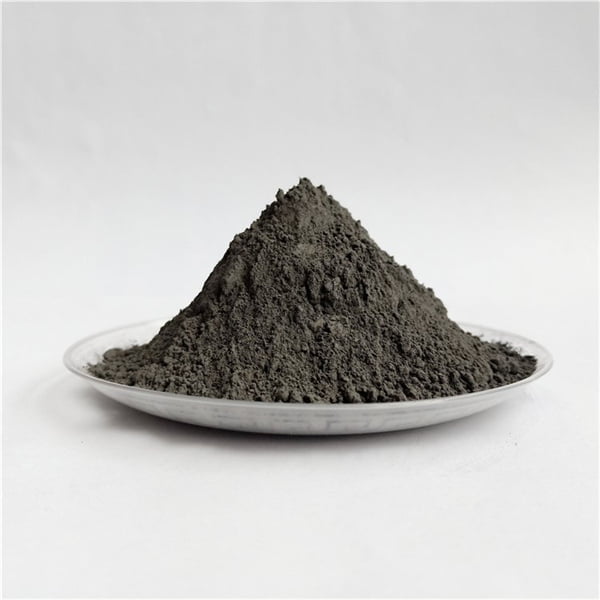
VANLIGA FRÅGOR
F: Vilka är säkerhetsaspekterna för WAAM?
WAAM involverar höga temperaturer, smält metall och elektriska strömmar. Korrekt säkerhetsprotokoll är viktigt, inklusive att bära lämplig personlig skyddsutrustning (PPE) som svetshjälmar, handskar och brandsäkra kläder. Att använda systemet i en välventilerad miljö och följa rekommenderade säkerhetsriktlinjer är avgörande.
F: Hur starka är delar tillverkade med WAAM?
Styrkan hos WAAM-tryckta delar beror på den valda metallegeringen, korrekta processparametrar och värmebehandling (om tillämpligt). WAAM kan producera komponenter med utmärkta mekaniska egenskaper jämförbara med traditionellt tillverkade motsvarigheter.
F: Kan WAAM skriva ut i färg?
För närvarande erbjuder WAAM inte direkt flerfärgsutskrift. Däremot kan efterbearbetningstekniker som målning eller anodisering användas för att lägga till färg till de färdiga delarna.
F: Vad är framtiden för WAAM?
Som diskuterats tidigare är framtiden för WAAM ljus. Framsteg inom automation, kontrollsystem och materialutveckling är redo att driva WAAMs kapacitet ytterligare. Hybrid WAAM-system som kombinerar WAAM med andra additiva tillverkningsmetoder lovar ännu större mångsidighet. Utforskningen av nya applikationer inom olika branscher förväntas accelerera när WAAM-tekniken mognar.
Sammanfattningsvis, Wire Arc Additive Manufacturing (WAAM) presenterar en revolutionerande metod för 3D-utskrift av metall. Dess höga avsättningshastighet, materialeffektivitet och förmåga att hantera storskaliga strukturer gör det till ett övertygande alternativ för olika industrier. Även om faktorer som ytfinish och restspänning måste beaktas, positionerar WAAM:s fördelar och pågående utveckling det som ett kraftfullt verktyg för att forma framtiden för metalltillverkning.
Dela på
MET3DP Technology Co, LTD är en ledande leverantör av lösningar för additiv tillverkning med huvudkontor i Qingdao, Kina. Vårt företag är specialiserat på 3D-utskriftsutrustning och högpresterande metallpulver för industriella tillämpningar.
Förfrågan för att få bästa pris och anpassad lösning för ditt företag!
Relaterade artiklar
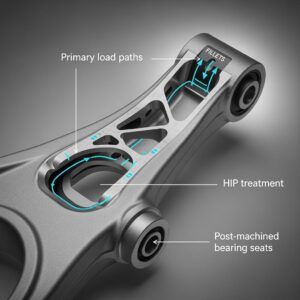
Metal 3D Printing for U.S. Automotive Lightweight Structural Brackets and Suspension Components
Läs mer "Om Met3DP
Senaste uppdateringen
Vår produkt
KONTAKTA OSS
Har du några frågor? Skicka oss meddelande nu! Vi kommer att betjäna din begäran med ett helt team efter att ha fått ditt meddelande.