Precision Sensor Platforms for Aerospace Applications: The Metal 3D Printing Advantage
İçindekiler
The aerospace industry demands unparalleled precision, reliability, and performance from every component, and sensor platforms are no exception. These intricate systems serve as the nervous system of aircraft and spacecraft, collecting critical data for navigation, environmental monitoring, structural health assessment, and a multitude of other vital functions. Traditionally manufactured sensor platforms often face limitations in design complexity, material selection, and production efficiency. However, the advent of metal 3D baskı, also known as metal additive manufacturing, has ushered in a new era of possibilities, enabling the creation of highly customized, high-performance sensor platforms tailored precisely to the demanding needs of aerospace applications. At Metal3DP, we are at the forefront of this revolution, providing cutting-edge metal 3D printing solutions that empower aerospace engineers and procurement managers to reimagine the design and production of their sensor platforms. Our industry-leading print volume, accuracy, and reliability ensure that mission-critical parts meet the most stringent aerospace standards.
What are Custom Aerospace Sensor Platforms Used For?
Custom aerospace sensor platforms are integral to a wide array of critical functions within aircraft, spacecraft, satellites, and unmanned aerial vehicles (UAVs). Their versatility allows for the integration of various sensor types, including:
- Environmental Sensors: Measuring temperature, pressure, humidity, and air quality for cabin environment control and external atmospheric data collection.
- Position and Orientation Sensors: Housing accelerometers, gyroscopes, and magnetometers for inertial navigation systems (INS) and attitude control.
- Structural Health Monitoring (SHM) Sensors: Integrating strain gauges, acoustic emission sensors, and fiber optic sensors to detect and monitor structural integrity, fatigue, and potential damage in real-time.
- Fluid and Gas Flow Sensors: Providing platforms for sensors that measure fuel flow, hydraulic fluid pressure, and air intake for engine control and system monitoring.
- Optical Sensors: Supporting cameras, lidar, and other optical instruments for surveillance, remote sensing, and autonomous navigation.
- Communication and Radar Systems: Housing components for antennas, waveguides, and other elements of communication and radar arrays.
The ability to customize these platforms through metal 3D printing allows aerospace engineers to optimize sensor placement, reduce weight, improve aerodynamic profiles, and integrate multiple functionalities into a single, consolidated part. This design freedom is particularly valuable for specialized applications and the development of next-generation aerospace vehicles. Metal3DP’s advanced metal powders and printing processes are ideally suited for creating these complex geometries with the high precision required for aerospace applications.
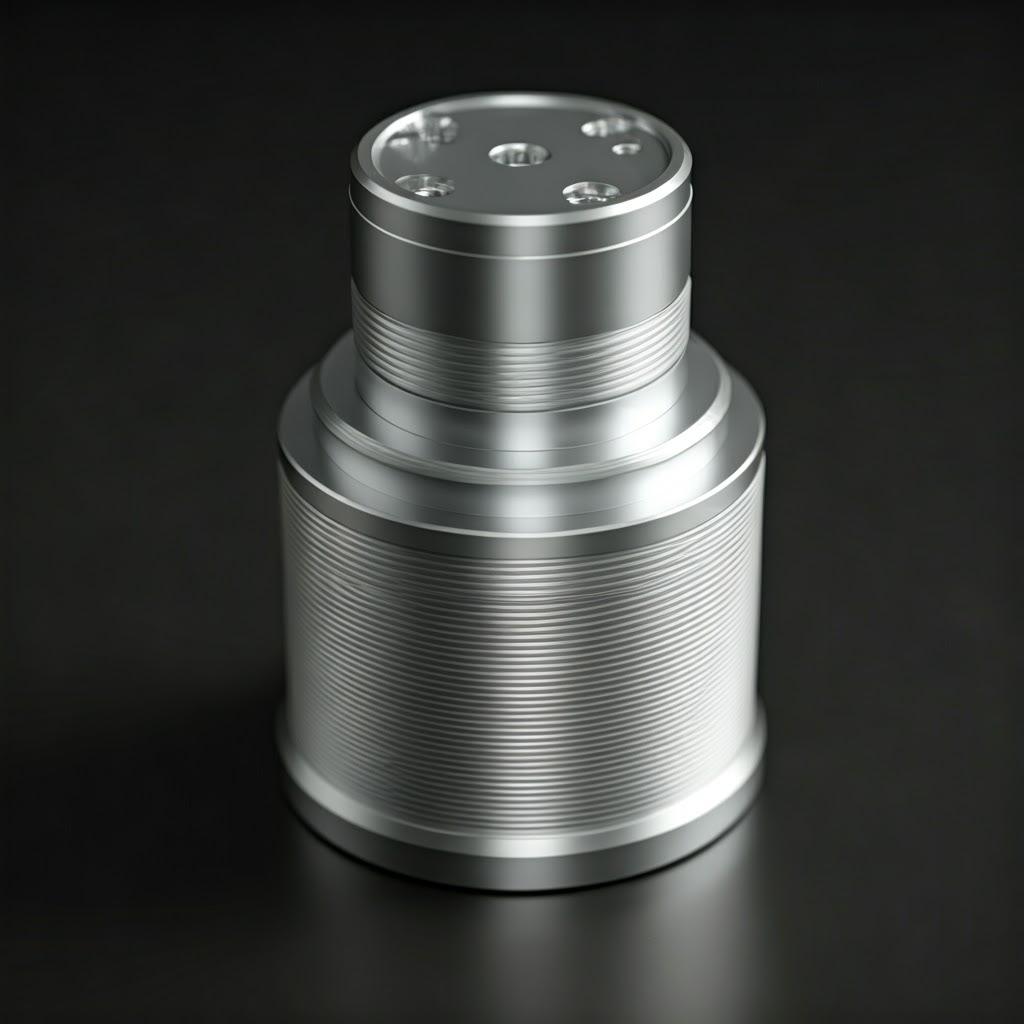
Why Choose Metal 3D Printing for Aerospace Sensor Platforms?
Opting for metal 3D printing for the production of aerospace sensor platforms offers a multitude of compelling advantages over traditional manufacturing methods:
- Tasarım Özgürlüğü ve Karmaşıklık: Additive manufacturing liberates engineers from the design constraints imposed by traditional techniques like machining or casting. Complex geometries, intricate internal channels for wiring or cooling, and optimized shapes for sensor integration can be achieved with ease. This allows for the creation of highly functional and space-efficient sensor platforms, crucial in weight-sensitive aerospace applications. Our baskı yöntemleri enable the realization of even the most challenging designs.
- Hafifletme: Metal 3D printing facilitates the creation of lightweight structures through topology optimization and the use of advanced materials. By strategically distributing material only where it’s needed for structural integrity, significant weight reductions can be achieved, leading to improved fuel efficiency and performance in aircraft and spacecraft.
- Malzeme Verimliliği: Additive manufacturing processes are inherently more material-efficient than subtractive methods, as material is only deposited where required. This reduces waste, lowers material costs, and is particularly beneficial when working with expensive aerospace-grade alloys.
- Hızlı Prototipleme ve Yineleme: Metal 3D printing significantly accelerates the prototyping process. Design modifications can be quickly implemented and new iterations produced in a fraction of the time compared to traditional methods. This agile approach allows for faster development cycles and quicker time-to-market for new aerospace technologies.
- Customization and Small Batch Production: Metal 3D printing is ideal for producing highly customized sensor platforms in small to medium volumes. Each platform can be tailored to specific mission requirements or sensor configurations without the need for expensive tooling or setup costs associated with traditional manufacturing.
- Integration of Features: Multiple components can be consolidated into a single 3D-printed part, reducing the number of assembly steps, fasteners, and potential failure points. This integrated approach enhances reliability and reduces overall system complexity. Metal3DP’s product portfolio showcases our ability to create such integrated solutions.
- Geliştirilmiş Performans: By optimizing designs and selecting appropriate materials, metal 3D printing can lead to sensor platforms with enhanced mechanical properties, thermal management capabilities, and overall performance characteristics tailored to the demanding aerospace environment.
Recommended Metal Powders for Aerospace Sensors: 316L and AlSi10Mg
At Metal3DP, we offer a range of high-performance metal powders specifically suited for the demanding requirements of aerospace applications. For custom aerospace sensor platforms, two materials stand out for their excellent combination of properties and processability: 316L stainless steel and AlSi10Mg aluminum alloy. Our company employs industry-leading gas atomization and PREP technologies to ensure the high sphericity and flowability of our yüksek kaliteli metal tozları.
316L Paslanmaz Çelik:
- Özellikler: 316L is an austenitic stainless steel known for its excellent corrosion resistance, high strength, good ductility, and weldability. The “L” designation indicates a low carbon content, which further enhances its resistance to sensitization (chromium carbide precipitation at grain boundaries) during welding or high-temperature exposure, crucial in many aerospace environments.
- Benefits for Sensor Platforms: Its corrosion resistance makes it ideal for platforms exposed to harsh atmospheric conditions or fluids. The high strength-to-weight ratio is beneficial for minimizing the overall weight of the sensor system. Its good weldability allows for easy integration with other components if needed.
- Uygulamalar: Suitable for structural components of sensor housings, mounting brackets, and platforms requiring high corrosion resistance and moderate weight.
AlSi10Mg Aluminum Alloy:
- Özellikler: AlSi10Mg is a widely used aluminum alloy in additive manufacturing, offering a good balance of strength, hardness, and thermal conductivity, combined with low density. It exhibits excellent processability with laser powder bed fusion (LPBF) and direct metal laser sintering (DMLS) techniques.
- Benefits for Sensor Platforms: Its primary advantage is its low density, which is critical for weight-sensitive aerospace applications. The good thermal conductivity can be beneficial for dissipating heat generated by electronic components within the sensor platform. It also offers good strength-to-weight ratio.
- Uygulamalar: Ideal for lightweight sensor housings, enclosures for electronic components, and platforms where thermal management is a consideration.
The selection of the appropriate powder depends on the specific requirements of the sensor platform, including the operating environment, mechanical loads, and thermal considerations. Metal3DP’s team of experts can provide guidance on material selection to ensure optimal performance and reliability for your aerospace sensor applications. We are committed to providing comprehensive solutions, from advanced metal powders to application development services. Contact Metal3DP today to explore how our capabilities can power your organization’s additive manufacturing goals. Sources and related content
Design Optimization for Metal 3D Printed Aerospace Sensor Platforms
Designing for metal additive manufacturing requires a different mindset compared to traditional methods. To fully leverage the capabilities of 3D printing and achieve optimal performance for aerospace sensor platforms, several design considerations are crucial:
- Topology Optimization: This computational technique can identify areas of a design that are structurally critical and those that can be removed to reduce weight without compromising strength. For aerospace, where every gram counts, topology optimization can lead to significant weight savings in sensor platforms.
- Kafes Yapılar: Instead of solid infill, lattice structures can be incorporated into the design. These intricate, repeating patterns offer high strength-to-weight ratios and can be tailored to specific load-bearing requirements. They also improve airflow and heat dissipation, which can be beneficial for sensor electronics.
- Parçaların Birleştirilmesi: As mentioned earlier, metal 3D printing allows for the consolidation of multiple components into a single, integrated part. This reduces assembly time, the number of fasteners required, and potential points of failure, ultimately enhancing the reliability of the sensor platform. Consider integrating features like mounting points, cable channels, and even cooling fins directly into the design.
- Orientation and Support Structures: The orientation of the part during the printing process can significantly impact surface finish, dimensional accuracy, and the need for support structures. Careful consideration of the build orientation and the strategic placement of support structures are essential to minimize post-processing and ensure the integrity of critical features. Our expertise at Metal3DP ensures optimal part orientation for every build.
- Wall Thickness and Feature Size: While metal 3D printing offers great design freedom, there are still limitations regarding minimum wall thickness and feature size. These limitations depend on the chosen material and printing technology. Designing with these constraints in mind will ensure manufacturability and the structural integrity of the sensor platform.
- Internal Channels and Features: Complex internal channels for wiring, fluid flow (for cooling or sensing applications), or weight reduction can be easily incorporated into the design using metal 3D printing. These features would be difficult or impossible to achieve with traditional manufacturing methods.
- Surface Finish Considerations: The as-printed surface finish of a metal 3D printed part can vary depending on the material and printing process. If a smooth surface finish is required for aerodynamic performance or sensor integration, post-processing steps like polishing or machining should be planned for in the design phase.
By embracing these design principles, aerospace engineers can create highly optimized sensor platforms that are lighter, stronger, more functional, and tailored precisely to their specific application requirements.
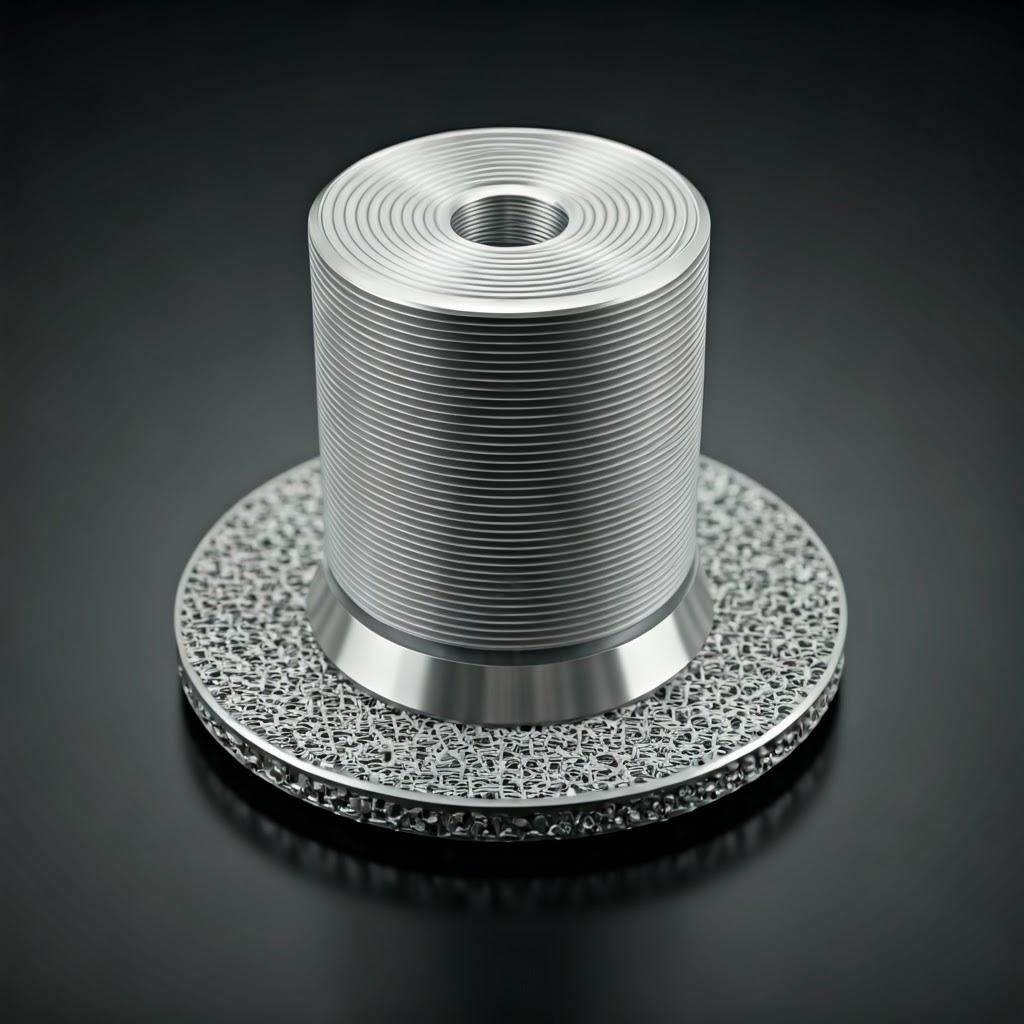
Achieving Tight Tolerances and Superior Surface Finish in 3D Printed Sensors
Aerospace applications often demand tight tolerances and specific surface finishes for proper functionality and integration of sensor platforms. Metal 3D printing technologies have made significant advancements in achieving these critical requirements:
- High-Precision Printing Technologies: At Metal3DP, we utilize Selective Electron Beam Melting (SEBM) and Laser Powder Bed Fusion (LPBF) technologies known for their high accuracy and ability to produce parts with fine details and tight tolerances. Our printers are engineered to deliver industry-leading accuracy, ensuring that your sensor platforms meet the most stringent specifications.
- Malzeme Seçimi: The choice of metal powder also plays a crucial role in achieving the desired tolerances and surface finish. Fine, spherical powders with consistent particle size distribution, like those produced by Metal3DP’s advanced powder making system, contribute to smoother surfaces and more accurate part dimensions.
- Optimized Printing Parameters: Carefully controlled printing parameters, such as laser power, scan speed, layer thickness, and build environment, are essential for achieving dimensional accuracy and a good surface finish. Our experienced team at Metal3DP meticulously optimizes these parameters for each material and application.
- Build Orientation and Support Strategy: As mentioned in the design section, the orientation of the part during printing and the placement of support structures significantly impact surface quality. Strategically orienting the part to minimize downward-facing surfaces and optimizing support removal can lead to a smoother as-printed finish.
- Post-Processing Teknikleri: When extremely tight tolerances or specific surface finishes are required, various post-processing techniques can be employed. These include:
- CNC İşleme: For achieving very precise dimensions and smooth surfaces on critical interfaces.
- Grinding and Polishing: To improve surface roughness for aerodynamic performance or sensor integration.
- Yüzey Kaplaması: To provide specific surface properties, such as corrosion resistance or wear resistance, while also potentially improving surface finish.
By carefully considering the printing technology, material selection, design for additive manufacturing principles, and appropriate post-processing techniques, it is possible to achieve the tight tolerances and superior surface finishes required for demanding aerospace sensor platform applications.
Post-Processing for Aerospace-Grade Sensor Platforms
While metal 3D printing offers significant advantages in creating complex geometries, post-processing steps are often necessary to achieve the final desired properties, tolerances, and surface finish for aerospace-grade sensor platforms. Common post-processing requirements include:
- Destek Kaldırma: Support structures are often needed during the printing process to prevent warping and ensure the stability of overhanging features. These supports must be carefully removed after printing, which can involve manual breaking, cutting, or machining. The design of the supports and the part orientation can significantly impact the ease and quality of support removal.
- Stress Relief Heat Treatment: Metal 3D printed parts can sometimes contain residual stresses due to the rapid heating and cooling cycles during the printing process. Stress relief heat treatment is often performed to reduce these internal stresses, improving the dimensional stability and mechanical properties of the component, which is critical for aerospace applications.
- Sıcak İzostatik Presleme (HIP): HIP is a process that involves subjecting the printed part to high pressure and temperature in an inert atmosphere. This process helps to eliminate internal porosity, increase density, and improve the mechanical properties, particularly fatigue strength, which is crucial for aerospace components operating under cyclic loads.
- CNC İşleme: For achieving very tight tolerances on critical features, such as mounting interfaces or sensor cavities, CNC machining may be required as a secondary operation. This subtractive process can provide the precision needed for accurate assembly and functionality.
- Yüzey İşlemi: Depending on the application requirements, various surface finishing techniques may be employed, including:
- Media Blasting: To remove loose powder and provide a uniform surface texture.
- Grinding and Polishing: To achieve smoother surfaces for improved aerodynamics or aesthetics.
- Chemical Etching: To remove surface layers and reveal specific microstructures.
- Coating and Surface Treatments: To enhance corrosion resistance, wear resistance, or other specific surface properties, various coatings, such as anodizing, painting, or specialized aerospace coatings, may be applied.
- Inspection and Quality Control: Rigorous inspection and quality control procedures are essential to ensure that the final sensor platform meets the stringent requirements of the aerospace industry. This may involve dimensional measurements, non-destructive testing (NDT) methods like ultrasonic testing or X-ray inspection, and material property verification.
The specific post-processing steps required will depend on the material, the printing process, the design complexity, and the intended application of the aerospace sensor platform. Careful planning for post-processing is crucial in the overall manufacturing workflow.
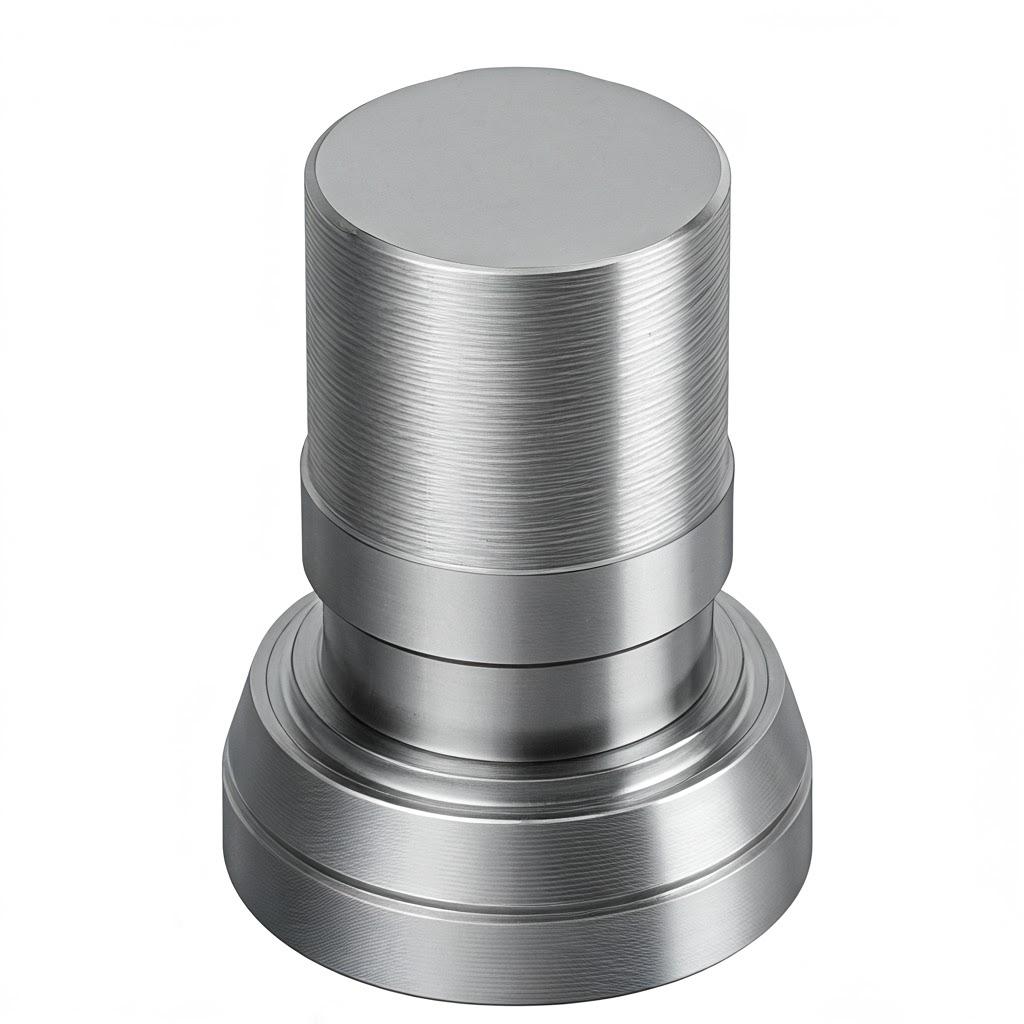
Overcoming Common Challenges in Metal 3D Printing of Sensor Components
While metal 3D printing offers numerous advantages, several challenges can arise during the fabrication of aerospace sensor components. Understanding these potential issues and implementing appropriate strategies to mitigate them is essential for successful outcomes:
- Çarpıtma ve Bozulma: Thermal gradients during the printing process can lead to internal stresses and subsequent warping or distortion of the part, particularly for large or complex geometries. Optimizing the build orientation, using support structures, and employing stress relief heat treatment can help minimize these issues.
- Destek Yapısının Kaldırılması: Removing support structures can sometimes be challenging, especially for intricate designs or delicate features. Careful design of support structures and the use of dissolvable supports (where applicable) can simplify this process.
- Gözeneklilik: Internal porosity can occur in metal 3D printed parts, which can negatively impact their mechanical properties and fatigue life. Optimizing printing parameters, material selection, and employing post-processing techniques like HIP can significantly reduce porosity. Metal3DP’s high-quality metal powders are designed to minimize porosity.
- Yüzey Kaplama Kalitesi: Achieving a smooth surface finish directly from the printing process can be challenging, especially on angled or overhanging surfaces. Optimizing build orientation and employing appropriate post-processing techniques like media blasting or polishing are often necessary.
- Boyutsal Doğruluk: While metal 3D printing offers good dimensional accuracy, achieving extremely tight tolerances may require careful process control and potentially post-processing machining. Understanding the capabilities and limitations of the chosen printing technology is crucial.
- Material Property Consistency: Ensuring consistent material properties throughout the printed part can be a challenge. Careful control of the printing environment, laser or electron beam parameters, and powder quality are essential for achieving homogeneous material properties.
- Cost and Lead Time: While metal 3D printing can be cost-effective for small to medium volumes and complex geometries, the initial investment in equipment and the cost per part can be higher than traditional methods for very high volumes or simple designs. Lead times can also vary depending on the complexity and size of the part. Careful consideration of these factors is necessary.
By understanding these potential challenges and working with an experienced metal 3D printing service provider like Metal3DP, which possesses the expertise, advanced equipment, and high-quality materials, aerospace engineers and procurement managers can effectively mitigate these issues and leverage the full potential of metal additive manufacturing for their sensor platform needs.
Selecting the Right Metal 3D Printing Partner for Aerospace Applications
Choosing the right metal 3D printing service provider is a critical decision for aerospace companies seeking to leverage the benefits of additive manufacturing for their sensor platforms. Given the stringent requirements of the aerospace industry, several key factors should be considered when evaluating potential partners:
- Aerospace Certifications and Standards: Ensure the service provider holds relevant aerospace certifications, such as AS9100, which demonstrates their commitment to quality management systems specific to the aerospace industry. Compliance with other relevant standards for materials and processes is also crucial.
- Material Capabilities: Verify that the provider offers a range of aerospace-grade metal powders, including the specific alloys required for your sensor platform (e.g., 316L, AlSi10Mg, and others like TiNi, TiAl, which Metal3DP also offers). Inquire about their material characterization and testing procedures.
- Printing Technology and Equipment: Understand the types of metal 3D printing technologies they employ (e.g., SEBM, LPBF, DMLS). Ensure they have well-maintained, high-precision equipment capable of meeting the dimensional accuracy and surface finish requirements of your application. Metal3DP’s industry-leading print volume, accuracy, and reliability are key advantages.
- Design for Additive Manufacturing (DfAM) Expertise: A knowledgeable partner should offer expertise in DfAM principles to help optimize your sensor platform design for metal 3D printing, maximizing performance and manufacturability.
- Post-Processing Capabilities: Inquire about their in-house post-processing capabilities, including support removal, heat treatment, HIP, CNC machining, surface finishing, and coating. A comprehensive suite of post-processing services can streamline the manufacturing process.
- Quality Control and Inspection: Understand their quality control procedures, including dimensional inspection, non-destructive testing (NDT), and material property verification. Robust quality assurance is paramount for aerospace components.
- Experience and Track Record: Evaluate their experience in serving the aerospace industry and their track record of successfully producing high-quality, mission-critical parts. Case studies and testimonials can provide valuable insights.
- Communication and Collaboration: A strong partnership requires clear communication and effective collaboration throughout the design, manufacturing, and post-processing stages. Assess their responsiveness and willingness to work closely with your team.
- Lead Times and Production Capacity: Discuss their typical lead times for similar projects and their production capacity to ensure they can meet your project timelines and volume requirements.
- Cost Structure and Transparency: Understand their pricing model and ensure transparency in their cost breakdown. Compare quotes from multiple providers, considering not just the printing cost but also post-processing, quality control, and other related services.
By carefully evaluating potential metal 3D printing service providers based on these criteria, aerospace companies can establish partnerships that ensure the successful production of high-performance, reliable sensor platforms.
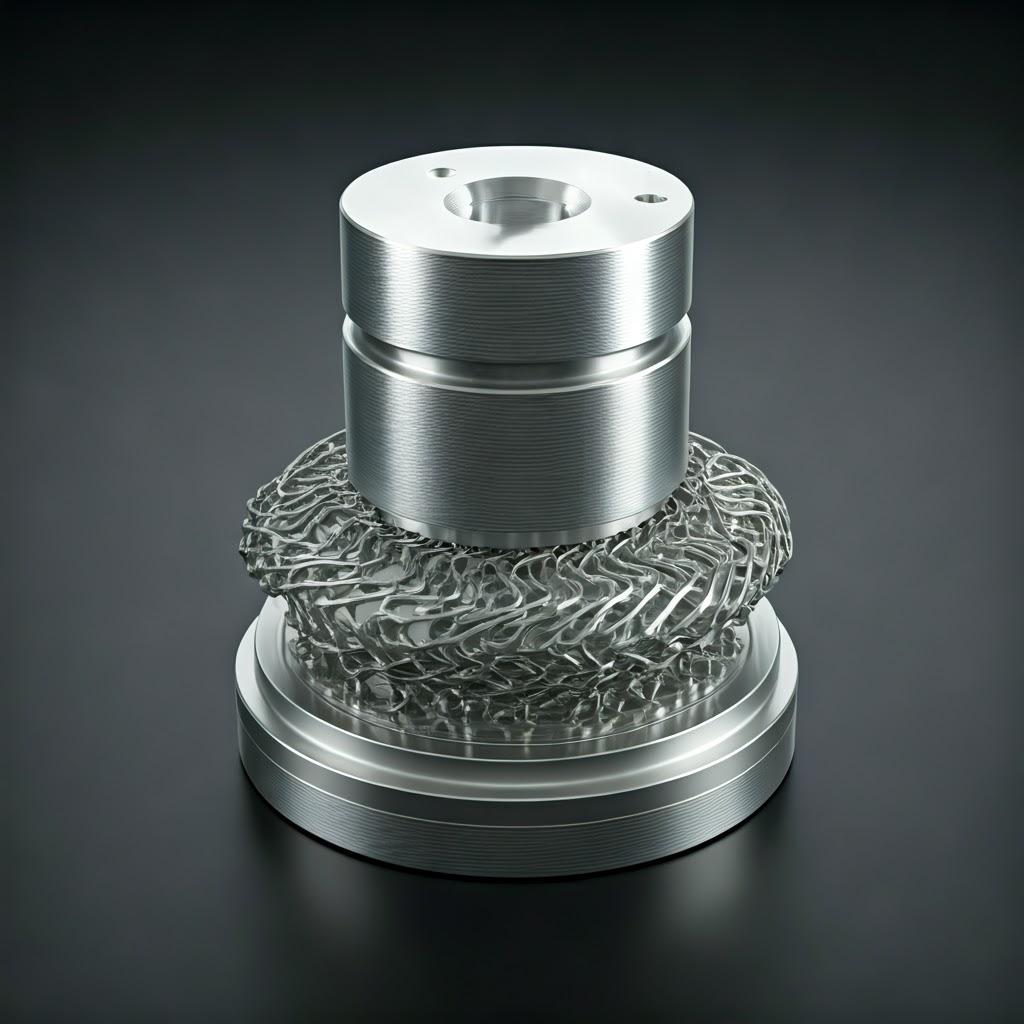
Cost Considerations and Lead Times for 3D Printed Aerospace Sensors
Understanding the cost factors and lead times associated with metal 3D printing of aerospace sensor platforms is crucial for effective project planning and budgeting:
Maliyet Faktörleri:
- Malzeme Maliyetleri: The cost of aerospace-grade metal powders can be significant and varies depending on the alloy and supplier. Material waste, although generally lower in additive manufacturing compared to subtractive methods, also contributes to the overall material cost. Metal3DP manufactures a wide range of high-quality metal powders, potentially offering cost advantages.
- Baskı Süresi: The build time for a sensor platform depends on its size, complexity, and the chosen printing technology. Longer build times translate to higher machine operating costs.
- Machine Operation and Maintenance: The costs associated with operating and maintaining the metal 3D printer, including energy consumption, consumables, and regular maintenance, are factored into the overall cost per part.
- İşlem Sonrası Maliyetler: The extent of post-processing required (support removal, heat treatment, machining, finishing, etc.) significantly impacts the final cost. Complex post-processing can add considerable expense.
- Design and Engineering Costs: The time and expertise required for designing the sensor platform for additive manufacturing, including topology optimization and support structure design, are part of the overall cost.
- Quality Control and Inspection Costs: Rigorous quality control procedures, including NDT and material testing, add to the manufacturing cost but are essential for aerospace applications.
- Parti Boyutu: While metal 3D printing is advantageous for low to medium volumes, the cost per part may not be competitive with traditional mass production methods for very high quantities. However, for customized aerospace sensors, the flexibility and design freedom often outweigh this factor.
Teslim Süreleri:
- Design and Optimization: The initial design and optimization phase for additive manufacturing can take time, depending on the complexity of the sensor platform and the level of customization required.
- Baskı Süresi: The actual printing duration is determined by the part’s geometry, size, and the chosen printing parameters.
- Post-Processing Time: The lead time for post-processing can vary significantly depending on the required steps. Complex machining or specialized coatings can extend the overall lead time.
- Quality Control and Inspection: Thorough quality checks can also add to the overall lead time.
- Malzeme Durumu: The availability of the specific aerospace-grade metal powder can sometimes impact lead times. Metal3DP’s advanced Powder Making System aims to ensure a consistent supply of high-quality powders.
It’s important to engage in detailed discussions with your metal 3D printing service provider to obtain accurate cost estimates and lead times based on your specific sensor platform requirements. Factors like design complexity, material selection, and the level of post-processing will all play a significant role.
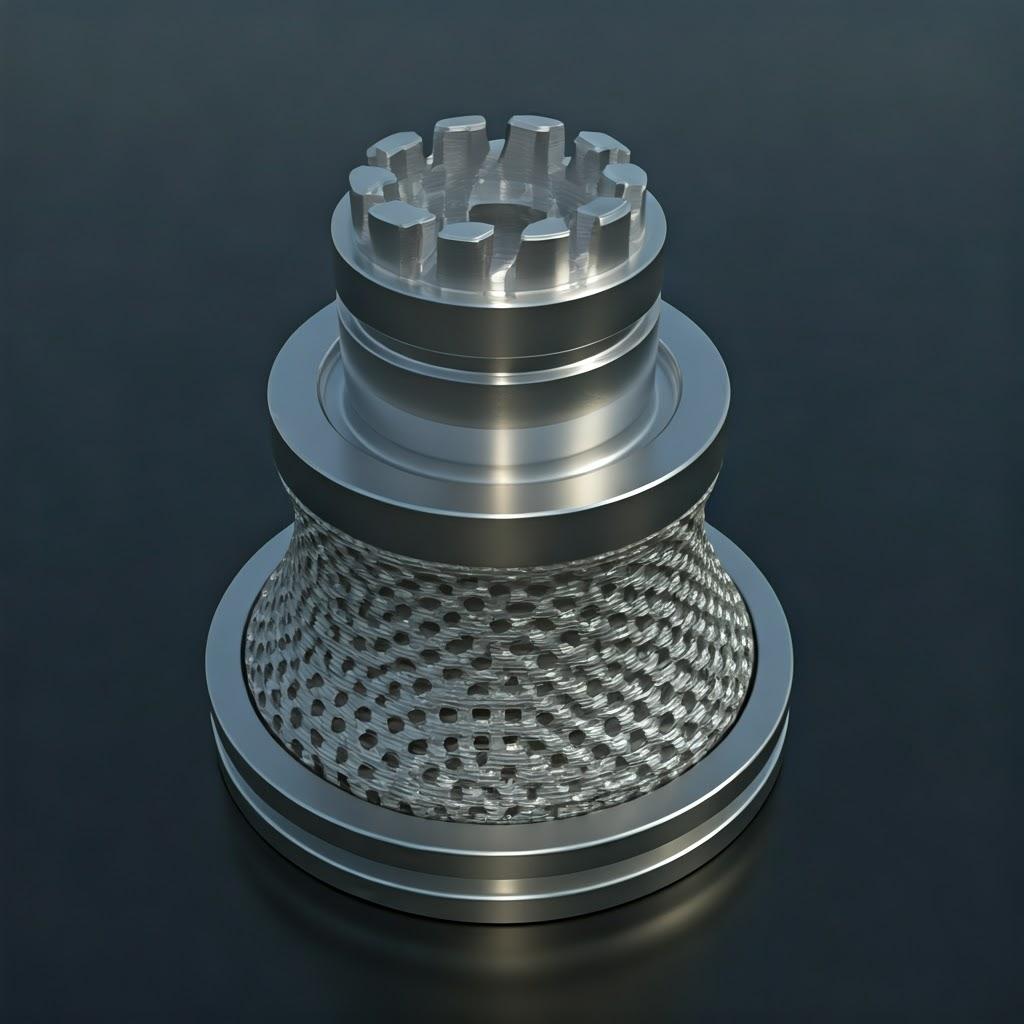
Sıkça Sorulan Sorular (SSS)
- What are the typical tolerances achievable with metal 3D printing for aerospace sensors?
- Metal 3D printing can achieve tolerances ranging from ±0.1 mm to ±0.05 mm, depending on the printing technology, material, and part geometry. Finer tolerances can be achieved through post-processing CNC machining. Metal3DP’s high-accuracy printers are designed to meet demanding aerospace requirements.
- Can metal 3D printed sensors withstand harsh aerospace environments?
- Yes, with the appropriate material selection and post-processing, metal 3D printed sensors can be designed to withstand extreme temperatures, vibrations, corrosion, and other harsh conditions encountered in aerospace applications. Materials like 316L offer excellent corrosion resistance, and HIP can enhance mechanical properties for demanding environments.
- Is metal 3D printing cost-effective for producing small batches of customized aerospace sensors?
- In many cases, yes. For small to medium volumes of highly customized or complex sensor platforms, metal 3D printing can be more cost-effective than traditional methods that require expensive tooling. The ability to consolidate parts and reduce assembly steps can also lead to cost savings.
Conclusion: The Future of Aerospace Sensor Platforms with Metal 3D Printing
Metal 3D printing is revolutionizing the design and manufacturing of custom aerospace sensor platforms. Its ability to enable complex geometries, lightweight designs, material efficiency, rapid prototyping, and customization offers significant advantages over traditional manufacturing methods. By leveraging advanced materials like 316L and AlSi10Mg, and partnering with experienced providers like Metal3DP, aerospace engineers and procurement managers can create high-performance, reliable sensor platforms tailored precisely to their demanding application requirements. As the technology continues to advance, metal additive manufacturing will play an increasingly vital role in shaping the future of aerospace innovation, enabling the development of next-generation aircraft, spacecraft, and unmanned systems. Contact Metal3DP to explore how our cutting-edge systems and powders can empower your organization’s additive manufacturing goals.
Paylaş
MET3DP Technology Co, LTD, merkezi Qingdao, Çin'de bulunan lider bir katmanlı üretim çözümleri sağlayıcısıdır. Şirketimiz, endüstriyel uygulamalar için 3D baskı ekipmanları ve yüksek performanslı metal tozları konusunda uzmanlaşmıştır.
İşletmeniz için en iyi fiyatı ve özelleştirilmiş Çözümü almak için sorgulayın!
İlgili Makaleler
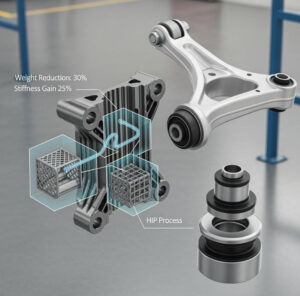
Metal 3D Printed Subframe Connection Mounts and Blocks for EV and Motorsport Chassis
Daha Fazla Oku "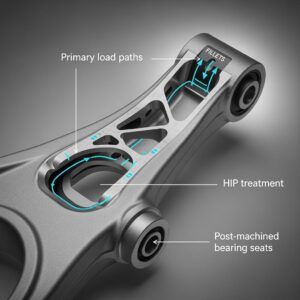
Metal 3D Printing for U.S. Automotive Lightweight Structural Brackets and Suspension Components
Daha Fazla Oku "Met3DP Hakkında
Son Güncelleme
Bizim Ürünümüz
BİZE ULAŞIN
Herhangi bir sorunuz var mı? Bize şimdi mesaj gönderin! Mesajınızı aldıktan sonra tüm ekibimizle talebinize hizmet edeceğiz.