Alüminyum Alaşımlı Toz
İçindekiler
Alüminyum alaşımlı toz alüminyum alaşımlarının toz metalurjisi formlarını ifade eder. Alüminyum tozları, hafiflikleri, yüksek mukavemetleri, korozyon dirençleri, termal iletkenlikleri ve elektrik iletkenlikleri nedeniyle çeşitli uygulamalarda kullanım alanı bulur.
Alüminyum Alaşım Tozuna Genel Bakış
Alüminyum alaşım tozu, erimiş alaşımların toz partikülleri halinde katılaşan ince damlacıklar halinde atomize edilmesiyle üretilir. Alaşım tozunun bileşimi ve özellikleri gereksinimlere göre uyarlanabilir.
Alüminyum alaşım tozu hakkında önemli detaylar:
- Alüminyum alaşımlarının atomize edilerek ince toz haline getirilmesiyle üretilir
- Partikül boyutu birkaç mikrondan milimetreye kadar değişir
- Küresel, düzensiz veya pul parçacık şekilleri
- Kullanılan alaşım elementlerinin çeşitliliği - Si, Mg, Zn, Cu vb.
- Alaşım bileşimine bağlı özellikler
- Hafif, yüksek mukavemetli, korozyon direnci
- Katmanlı imalat, termal sprey, MIM vb. için kullanılır.
Alüminyum Alaşımlı Toz Çeşitleri
Tip | Kompozisyon | Özellikler |
---|---|---|
Saf Al | 99%+ Al | Düşük mukavemet, yüksek elektrik iletkenliği |
1000 serisi | Al + Mn, Fe, Si | İşlenerek sertleştirilebilir, daha yüksek mukavemet |
2000 serisi | Al-Cu | Isıl işlem uygulanabilir, yüksek mukavemetli |
5000 serisi | Al-Mg | Orta ila yüksek mukavemet |
6000 serisi | Al-Mg-Si | Orta ila yüksek mukavemetli |
7000 serisi | Al-Zn | En yüksek güç |
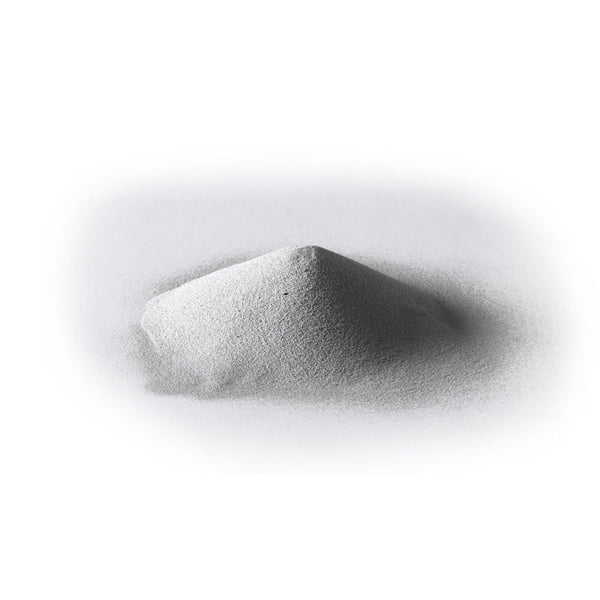
Alüminyum Alaşımlı Toz Kompozisyon
Alüminyum alaşım tozları, alaşım elementleri ile birlikte ana metal olarak alüminyum içerir. Bazı yaygın alaşım ilaveleri şunları içerir:
Alaşım Serisi | Birincil Alaşım Elementleri | Uygulamalar | Alaşım Elementleri ile Geliştirilmiş Özellikler |
---|---|---|---|
1XXX Serisi | > 99% Alüminyum (Al) | * Elektrik iletkenleri * Isı eşanjörleri * Gıda ambalajları | * Yüksek elektrik iletkenliği * Mükemmel şekillendirilebilirlik * Üstün korozyon direnci |
2XXX Serisi | Al + Bakır (Cu) (5,5%'ye kadar) | * Havacılık ve uzay bileşenleri * Baralar * Otomotiv parçaları | * Artırılmış mukavemet * Geliştirilmiş işlenebilirlik * İyi kaynaklanabilirlik |
3XXX Serisi | Al + Manganez (Mn) (1,3%'ye kadar) | * Bina ve inşaat malzemeleri * İşaretler ve paneller * Depolama tankları | * Gelişmiş iş sertleşmesi * Üstün şekillendirilebilirlik * Mükemmel sert lehimlenebilirlik |
4XXX Serisi | Al + Silikon (Si) (12%'ye kadar) | * Motor blokları * Silindir kafaları * Kaynak telleri | * Mükemmel döküm özellikleri * Düşük ısıl genleşme katsayısı * Aşınma direnci |
5XXX Serisi | Al + Magnezyum (Mg) (5,6%'ye kadar) | * Gemi yapımı * Basınçlı kaplar * Kimyasal depolama tankları | * Yüksek mukavemet/ağırlık oranı * Mükemmel korozyon direnci * İyi kaynaklanabilirlik |
6XXX Serisi | Al + Magnezyum (Mg) + Silikon (Si) (1 Mg ve 0,6 Si'ye kadar) | * Uçak yapıları * Köprüler * Ulaşım bileşenleri | * Mükemmel işlenebilirlik * İyi mukavemet * Üstün şekillendirilebilirlik |
7XXX Serisi | Al + Çinko (Zn) (6,5%'ye kadar) | * Uçak kanatları * Spor malzemeleri * Yüksek mukavemetli bağlantı elemanları | * Yüksek mukavemet * İyi yorulma direnci * Aşınma direnci (ilave alaşım elementleri ile) |
8XXX Serisi | Al + Lityum (Li) (12%'ye kadar) | * Çok düşük ağırlık gerektiren havacılık ve uzay bileşenleri * Yüksek performanslı araçlar | * Son derece düşük yoğunluk * Yüksek mukavemet/ağırlık oranı * Yüksek maliyet ve işleme zorlukları nedeniyle sınırlı uygulamalar |
Alüminyum Alaşımlı Toz Özellikleri
Alüminyum Alaşımlı Toz Özellikleri
Mülkiyet | Açıklama | Katmanlı Üretimde Faydalar |
---|---|---|
Partikül Boyutu ve Dağılımı | Alüminyum alaşım tozları, tipik olarak 10 ila 150 mikrometre arasında değişen çeşitli partikül boyutlarında mevcuttur. Bu partikül boyutlarının toz yatağı içindeki dağılımı da çok önemlidir. | Partikül boyutu ve dağılımı, katkılı olarak üretilen parçanın nihai özelliklerini önemli ölçüde etkiler. <br> - Daha ince parçacıklar genellikle daha pürüzsüz yüzeyler oluşturur, ancak artan akışkanlık sorunları ve oksidasyon için daha yüksek yüzey alanı nedeniyle işlenmesi daha zor olabilir. <br> - Daha büyük parçacıklar akışkanlığı artırır, ancak daha pürüzlü bir yüzey finişine ve bitmiş parça içinde potansiyel gözenekliliğe neden olabilir. <br> - A sıkı partikül boyutu dağılımı minimum varyasyon ile tutarlı paketleme yoğunluğu sağlar ve basılı parça içindeki iç gerilimleri en aza indirir. |
Parçacık Şekli | Alüminyum alaşımı toz partiküllerinin şekli, paketleme yoğunluğunu, akışkanlığı ve katkılı olarak üretilen bileşenin nihai mikro yapısını etkileyebilir. | – Küresel parçacıklar daha verimli bir şekilde paketlenerek daha yüksek yoğunluk ve potansiyel olarak geliştirilmiş mekanik özellikler sağlar. <br> - Düzensiz şekilli parçacıklar katman yapışmasını iyileştiren birbirine kenetlenen özellikler oluşturabilir, ancak aynı zamanda daha yüksek iç gerilimlere ve potansiyel çatlamaya da yol açabilir. |
Toz Akışkanlığı | Toz akışkanlığı, toz partiküllerinin makinenin yapı haznesi içinde hareket edebilme ve yayılabilme kolaylığını ifade eder. | İyi akışkanlık, tutarlı katman birikimi ve doğru parça geometrisi sağlamak için gereklidir. <br> - Akışkanlığı zayıf olan tozlar düzensiz birikime, yoğunlukta tutarsızlıklara ve potansiyel baskı hatalarına yol açabilir. |
Görünür Yoğunluk | Bir alüminyum alaşım tozunun görünür yoğunluğu, parçacıklar arasındaki boşluklar dikkate alınarak birim hacim başına toz kütlesidir. | Görünür yoğunluk, belirli bir yapı hacmi için gereken malzeme miktarını belirlemede çok önemli bir faktördür ve baskı işlemi sırasında parçanın büzülmesini etkileyebilir. |
Paketleme Yoğunluğu | Paketleme yoğunluğu, toz partiküllerinin katı hacminin toz tarafından işgal edilen toplam hacme oranını ifade eder. | Paketleme yoğunluğu, partiküller arasındaki boşlukların varlığı nedeniyle tipik olarak görünür yoğunluktan daha düşüktür. Daha yüksek paketleme yoğunluğu genellikle nihai parçada gelişmiş mekanik özelliklere yol açar. |
Kimyasal Bileşim | Alüminyum tozunda bulunan belirli alaşım elementleri, katkılı olarak üretilen parçanın nihai özelliklerini önemli ölçüde etkiler. Yaygın alaşım elementleri arasında silikon, bakır, magnezyum, manganez ve çinko bulunur. | Uygun alüminyum alaşımlı tozun seçimi, bitmiş parçanın mukavemet, korozyon direnci ve ısı direnci gibi istenen özelliklerine bağlıdır. <br> Örneğin, bakır eklemek mukavemeti artırabilir ancak korozyon direncini azaltabilir. |
Yüzey Kimyası | Alüminyum alaşımı toz partiküllerinin yüzey kimyası, baskı işlemi sırasında akışkanlıklarını, reaktivitelerini ve bağlanmalarını etkileyebilir. | Alüminyum parçacıklarının yüzeyinde doğal olarak ince bir oksit tabakası oluşur. <br> - Yüzey modifikasyon teknikleri akışkanlığı artırmak ve eklemeli üretim süreci sırasında parçacıklar arası bağlanmayı teşvik etmek için kullanılabilir. |
Nem İçeriği | Alüminyum alaşım tozları higroskopiktir, yani çevrelerindeki ortamdan nemi kolayca emerler. | Tozdaki aşırı nem içeriği, katkılı olarak üretilen parça içinde hidrojen gözenekliliğine yol açarak mekanik özellikleri olumsuz etkileyebilir. <br> - Tozdaki düşük nem seviyelerini korumak için uygun depolama ve taşıma teknikleri çok önemlidir. |
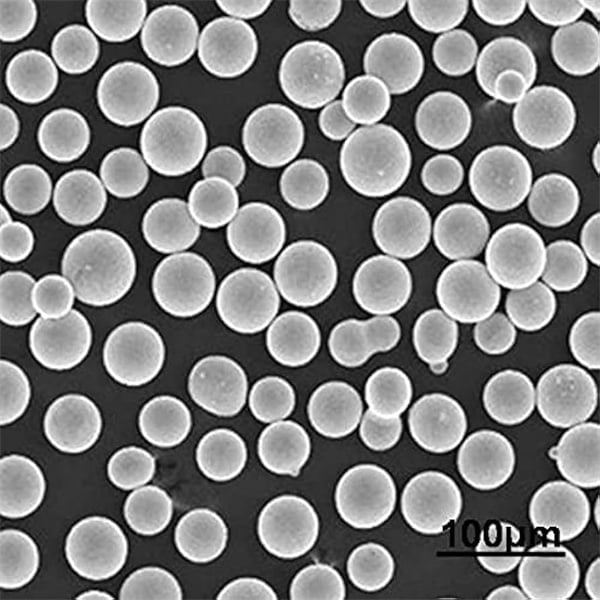
Alüminyum Alaşımlı Toz Uygulamaları
Uygulama | Açıklama | Alüminyum Alaşımlı Tozların Avantajları | Sınırlamalar |
---|---|---|---|
Havacılık ve Uzay Bileşenleri | Alüminyum alaşım tozları, mükemmel mukavemet-ağırlık oranları ve uygun mekanik özellikleri nedeniyle yüksek performanslı havacılık ve uzay bileşenlerinin katkılı üretimi (AM) için yaygın olarak kullanılmaktadır. Yaygın uygulamalar şunları içerir: - Uçak gövdeleri ve kanat bileşenleri - Motor bileşenleri - Uydu yapıları | – Hafif yapı: Alüminyum alaşımları, çelik gibi geleneksel malzemelere kıyasla ağırlıkta önemli ölçüde azalma sağlayarak havacılık araçlarında yakıt verimliliğinin ve yük taşıma kapasitesinin artmasına olanak tanır. – Tasarım özgürlüğü: AM, geleneksel üretim yöntemleriyle elde edilmesi zor veya imkansız olan iç kanallara ve kafeslere sahip karmaşık, hafif yapıların oluşturulmasına olanak tanır. – Performans terziliği: Yüksek mukavemet, iyi yorulma direnci ve mükemmel korozyon direnci gibi havacılık ve uzay uygulamalarının zorlu gereksinimlerini karşılamak için özel alüminyum alaşımları seçilebilir. | – Toz maliyeti: Alüminyum alaşım tozları, titanyum alaşımları gibi havacılıkta kullanılan bazı alternatif malzemelerden daha pahalı olabilir. – Yüzey pürüzlülüğü: AM süreçleri sürekli olarak gelişirken, katkılı olarak üretilen alüminyum bileşenler, işlenmiş parçalara kıyasla hala daha pürüzlü bir yüzey kalitesi sergileyebilir. Belirli uygulamalar için işleme veya parlatma gibi işlem sonrası teknikler gerekebilir. |
Otomotiv Bileşenleri | Alüminyum alaşım tozları, hafif ve karmaşık otomotiv bileşenlerinin üretimi için AM'de giderek daha fazla kullanım alanı bulmaktadır. Örnekler şunları içerir: - Braketler ve muhafazalar gibi yapısal bileşenler - Güç elektroniği için ısı alıcıları - Özelleştirilmiş motor bileşenleri | – Ağırlık azaltma: Alüminyum AM bileşenleri yakıt verimliliğinin ve genel araç performansının iyileştirilmesine katkıda bulunur. – Fonksiyonel entegrasyon: AM, entegre işlevlere sahip parçaların tasarlanmasına ve oluşturulmasına olanak tanıyarak bileşen sayısını azaltır ve montaj süreçlerini basitleştirir. – Performans optimizasyonu: Alüminyum alaşımları, yapısal bileşenler için yüksek mukavemet veya ısı alıcıları için iyi termal iletkenlik gibi belirli özellikler sağlamak üzere seçilebilir. | – Parça kalifikasyonu: AM ile üretilen güvenlik açısından kritik otomotiv parçaları için kapsamlı test ve sertifikasyon gerekebilir. – Üretim hacmi: AM, prototipleme ve kısa vadeli üretim için giderek daha fazla kullanılırken, yüksek hacimli otomotiv üretimi için ölçeklenebilirliği hala geliştirilme aşamasındadır. |
Tıbbi İmplantlar | Biyouyumlu özelliklere sahip alüminyum alaşım tozları, aşağıdaki gibi özelleştirilmiş tıbbi implantların AM'si için araştırılmaktadır: - Kemik onarım plakları ve vidaları - Diş implantları - Protez bileşenleri | – Biyouyumluluk: Bazı alüminyum alaşımları iyi biyouyumluluk sergileyerek insan vücudu tarafından reddedilme riskini en aza indirir. – Özelleştirme: AM, bireysel anatomiye mükemmel şekilde uyan hastaya özel implantların oluşturulmasını sağlayarak implant uyumunu ve işlevini iyileştirir. – Gözenekli yapılar: AM yoluyla oluşturulan gözenekli alüminyum yapılar kemik büyümesini teşvik edebilir ve implant osseointegrasyonunu (kemikle bağlanma) iyileştirebilir. | – Sınırlı biyouyumlu alaşım yelpazesi: Şu anda sadece birkaç alüminyum alaşımının tıbbi uygulamalar için biyouyumlu olduğu düşünülmektedir. – Mekanik özellikler: Bazı alüminyum alaşımları, belirli yüksek yük taşıyan implantlar için gerekli mukavemete veya yorulma direncine sahip olmayabilir. – Düzenleyici gereklilikler: AM yoluyla üretilen tıbbi cihazlar için sıkı düzenleyici onay süreçleri izlenmelidir. |
Tüketici Elektroniği | Alüminyum alaşım tozları, iyi termal iletkenlik ve hafiflik özellikleri nedeniyle tüketici elektroniğindeki çeşitli bileşenlerin AM'si için kullanılır. Örnekler şunları içerir: - Elektronik cihazlar için ısı alıcıları - Dizüstü bilgisayarlar ve cep telefonları için hafif muhafazalar | – Termal yönetim: Alüminyumun iyi termal iletkenliği, elektronik bileşenler tarafından üretilen ısının dağıtılmasına yardımcı olarak cihaz performansını ve güvenilirliğini artırır. – Hafif tasarım: Alüminyum AM bileşenleri, elektronik cihazların genel ağırlığının azaltılmasına katkıda bulunarak taşınabilirliği ve kullanıcı deneyimini geliştirir. | – Sınırlı güç: Saf alüminyum veya bazı alüminyum alaşımları, yüksek mukavemet gerektiren yapısal bileşenler için uygun olmayabilir. – Yüzey kaplaması: Diğer AM uygulamalarına benzer şekilde, yüzey pürüzlülüğü belirli estetik gereksinimler için ek işlem sonrası gerektirebilir. |
Alüminyum Alaşımlı Toz Kullanarak Katmanlı Üretim
Al alaşım tozu ile AM'nin bazı faydaları:
Fayda | Açıklama | Etki |
---|---|---|
Tasarım Özgürlüğü ve Karmaşıklığı | Katmanlı üretim (AM), talaşlı imalat veya döküm gibi geleneksel üretim teknikleriyle elde edilmesi zor veya imkansız olan girift ve karmaşık geometrilerin oluşturulmasına olanak tanır. Alüminyum alaşım tozları, akışkanlıkları ve seçici olarak eritilebilmeleri veya bağlanabilmeleri sayesinde bu tasarım özgürlüğünü daha da geliştirmektedir. | – Hafif yapılar: AM, havacılık ve otomotiv gibi uygulamalar için mukavemet-ağırlık oranlarını optimize ederek iç kafeslere ve kanallara sahip hafif bileşenlerin tasarlanmasını sağlar. – Fonksiyonel entegrasyon: Parçalar entegre işlevlerle tasarlanabilir, birden fazla bileşene olan ihtiyacı azaltır ve montaj süreçlerini basitleştirir. – Özelleştirme: AM, hastaya özel tıbbi implantlar veya ısmarlama tüketici elektroniği muhafazaları gibi özel ihtiyaçlara göre uyarlanmış özelleştirilmiş parçaların oluşturulmasına olanak tanır. |
Malzeme Verimliliği ve Azaltılmış Atık | Önemli miktarda hurda malzeme üreten geleneksel eksiltici üretim yöntemlerinin aksine, alüminyum alaşımlı toz ile AM daha sürdürülebilir bir yaklaşım sunar. Malzeme, katman katman inşa sürecinde yalnızca ihtiyaç duyulan yerlerde kullanılır ve atıkları en aza indirir. | – Azaltılmış çevresel etki: Daha düşük malzeme tüketimi, geleneksel üretim süreçlerine kıyasla daha küçük bir çevresel ayak izi anlamına gelir. – Talep üzerine üretim: AM, parçaların talep üzerine üretilmesine olanak tanıyarak büyük envanter ihtiyacını ortadan kaldırır ve nakliye gereksinimlerini potansiyel olarak azaltır. |
Hızlı Prototipleme ve Kısa Süreli Üretim | Alüminyum alaşımlı toz ile AM, hızlı prototiplemede üstünlük sağlayarak tasarım doğrulama ve test için işlevsel prototiplerin hızlı bir şekilde oluşturulmasını sağlar. Ayrıca AM, pahalı takımlara ihtiyaç duymadan karmaşık parçaların kısa süreli üretimini kolaylaştırarak düşük hacimli uygulamalar için idealdir. | – Daha hızlı ürün geliştirme döngüleri: Hızlı prototipleme, daha hızlı tasarım yinelemelerine ve geri bildirim döngülerine olanak tanıyarak ürün geliştirme sürecini hızlandırır. – Azaltılmış pazara sunma süresi: AM, geleneksel üretim yöntemleriyle ilişkili uzun teslim sürelerini ortadan kaldırarak parçaların talep üzerine üretilmesini sağlar. – Düşük hacimler için uygun maliyetli: Düşük hacimli üretim çalışmaları için, alüminyum alaşımlı toz ile AM maliyeti, takım yatırımı gerektiren geleneksel yöntemlere kıyasla rekabetçi olabilir. |
Performans Uyarlama ve Hafifletme | Her biri mukavemet, korozyon direnci ve termal iletkenlik gibi farklı özellikler sunan çok çeşitli alüminyum alaşımları toz formunda mevcuttur. Bu, belirli bir uygulama için istenen performans özelliklerini elde etmek için en uygun alüminyum alaşım tozunun seçilmesine olanak tanır. | – Performans için hafifletme: Alüminyumun doğası gereği hafif olması, AM'nin tasarım özgürlüğü ile birleştiğinde, araçlarda yakıt verimliliğini veya havacılık uygulamalarında yük taşıma kapasitesini artıran daha hafif bileşenlerin oluşturulmasını sağlar. – Fonksiyonel optimizasyon: Bir uygulamanın performans taleplerini karşılamak için belirli alüminyum alaşımları seçilebilir. Örneğin, yüksek mukavemetli alaşımlar yapısal bileşenler için kullanılabilirken, iyi termal iletkenliğe sahip alaşımlar ısı alıcıları için idealdir. |
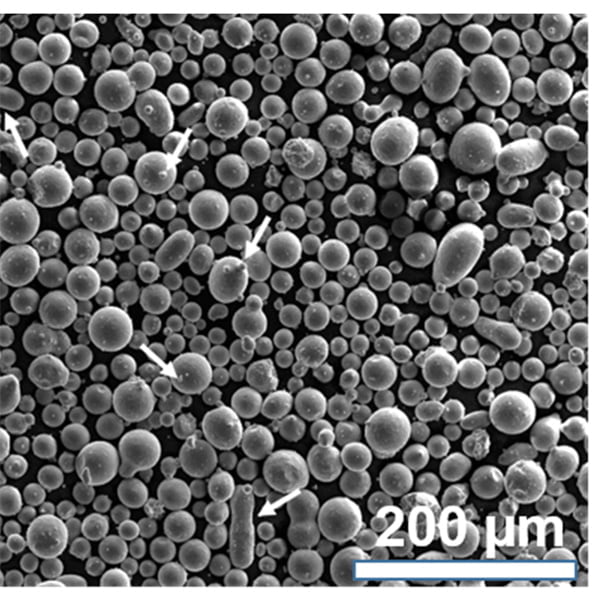
Al Tozu Kullanan AM'de Mevcut Sınırlamalar
Aspect | Sınırlama | Etki | Potansiyel Çözümler |
---|---|---|---|
Toz özellikleri | Düzensiz partikül şekli ve boyut dağılımı | Tutarsız lazer emilimi, zayıf akışkanlık, nihai parçalarda artan gözeneklilik | Küresel tozlar için daha verimli atomizasyon tekniklerinin geliştirilmesi, partikül boyutu dağılımı üzerinde daha sıkı kontrol |
Toz akışkanlığı | Zayıf akış düzgün yayılmayı engelleyebilir | Tutarsız katman yoğunluğu, zayıf katmanlar arası bağ | Toz yayılımını iyileştirmek için akışkanlık ajanları veya titreşimli sistemlerin kullanılması, bağlayıcı püskürtme gibi alternatif toz yatağı füzyon tekniklerinin araştırılması |
Toz geri dönüştürülebilirliği | Oksidasyon ve kirlenme nedeniyle sınırlı yeniden kullanım döngüleri | Artan malzeme maliyeti, çevresel etki | Entegre temizleme ve eleme süreçlerine sahip kapalı döngü toz yönetim sistemlerinin geliştirilmesi, oksidasyona daha az duyarlı Al alaşımlarının araştırılması |
Yüzey kalitesi | Erimemiş partiküller nedeniyle yüksek yüzey pürüzlülüğü | İşlem sonrası adımlar gerekli, yorulma çatlağı başlatma potansiyeli | Gelişmiş eritme verimliliği için lazer parametre optimizasyonu, bilyeli çekiçleme veya elektro-parlatma gibi alternatif sonlandırma tekniklerinin araştırılması |
Mekanik özellikler | Gözeneklilik mukavemet ve sünekliğin azalmasına neden olabilir | Parçalar tasarım gereksinimlerini karşılamayabilir | Gözeneklerin kapatılması için sıcak izostatik preslemenin (HIP) kullanılması, eriyik havuzu arıtma gibi lazer son işlem tekniklerinin araştırılması |
Artık stres | Hızlı katılaşma yüksek artık gerilime neden olabilir | Eğilme ve çatlama riskinde artış | Toz yatağının ön ısıtılması, termal gradyanları en aza indirmek için lazer tarama stratejilerinin optimize edilmesi, gerilim giderme ısıl işlemlerinin kullanılması |
Maliyet | Yüksek Al tozu üretim maliyeti | Belirli uygulamalar için ekonomik uygulanabilirliği sınırlar | Daha enerji verimli atomizasyon tekniklerinin geliştirilmesi, daha basit geometriler için alternatif üretim yöntemlerinin araştırılması |
Çevresel etki | Toz üretimi sırasında yüksek enerji tüketimi | Artan karbon ayak izi | Su bazlı bağlayıcılarla soğuk sprey veya bağlayıcı püskürtme gibi yeşil AM tekniklerinin araştırılması, geri dönüştürülmüş alüminyum kaynaklarının kullanımının incelenmesi |
Parça boyutu sınırlamaları | AM makinelerinin yapı hacmi kısıtlamaları | Büyük ölçekli alüminyum bileşenler kolaylıkla üretilemez | Daha yüksek üretim hacimlerine sahip daha büyük AM makinelerinin geliştirilmesi, işlevleri birleştirmek için hibrit AM tekniklerinin araştırılması |
Tasarımla ilgili hususlar | AM için tasarım optimizasyonu ihtiyacı | Geleneksel tasarım kuralları doğrudan tercüme edilemeyebilir | Al bileşenlerin AM'sine özel tasarım kılavuzlarının ve yazılım araçlarının geliştirilmesi, AM topluluğu içinde bilgi paylaşımının ve en iyi uygulamaların teşvik edilmesi |
Alüminyum Alaşımlı Toz ile Metal Enjeksiyon Kalıplama
Metal enjeksiyon kalıplama (MIM), nispeten düşük maliyetlerle alüminyum alaşımlı toz hammadde kullanarak karmaşık, sıkı toleranslı, net şekilli metalik bileşenler üretebilir.
Alüminyum alaşımlı toz ile MIM'in faydaları
Özellik | Fayda | Örnek Uygulama |
---|---|---|
Karmaşık Geometriler | Alüminyum alaşımlı MIM, dar toleranslara sahip karmaşık şekiller üretmede mükemmeldir. Geleneksel döküm yöntemlerinin aksine, MIM kalıp ayırma çizgileri ile sınırlı değildir, alttan kesmelere, ince duvarlara ve iç kanallara izin verir. | Birbirine kenetlenen dişlere ve dahili yağlama kanallarına sahip tıbbi bir cihazdaki minyatür dişliler. |
Yüksek Hacimli Üretim | MIM, küçük metal parçaların yüksek hacimli üretimi için uygun maliyetli bir çözüm sunar. Enjeksiyon kalıplama süreci, hızlı döngü sürelerine ve minimum son işleme olanak tanıyarak karmaşık bileşenlerin işlenmesine kıyasla önemli maliyet tasarrufu sağlar. | Büyük miktarlarda üretilen, karmaşık pin konfigürasyonlarına sahip tüketici elektroniği için elektrik konektörleri. |
Malzeme Çok Yönlülüğü | MIM'de her biri benzersiz özellikler sunan çok çeşitli alüminyum alaşımları kullanılabilir. Bu, yüksek mukavemet (örn. Al7075), iyi korozyon direnci (örn. Al5052) veya mükemmel termal iletkenlik (örn. Al6061) gibi uygulamanın özel ihtiyaçlarına göre seçim yapılmasına olanak tanır. | Verimli ısı dağıtımı için Al6061 kullanan, elektronik cihazlar için hafif ısı alıcıları. |
Ağ Şeklinde Üretim | MIM parçaları sinterlemeden sonra minimum işlem sonrası gerektirir. Neredeyse nihai boyutlar doğrudan kalıptan elde edilir ve ek işleme veya son işlem adımlarına olan ihtiyacı en aza indirir. | Biyouyumluluk için yüksek hassasiyet ve minimum işlem sonrası gerektiren entegre mikroakışkan kanallara sahip biyosensör bileşenleri. |
Hafifletme | Alüminyum alaşımları doğası gereği hafiftir, bu da MIM'i ağırlık azaltmanın kritik olduğu uygulamalar için ideal hale getirir. Bu özellikle havacılık, otomotiv ve tüketici elektroniği sektörlerinde faydalıdır. | MIM ile üretilen Al alaşımlarının yüksek mukavemet/ağırlık oranından yararlanarak insansız hava araçlarındaki yapısal bileşenler. |
Tasarım Özgürlüğü | MIM, birden fazla özelliğin tek bir bileşene entegre edilmesine olanak tanır. Bu, montaj karmaşıklığını azaltır, parça işlevselliğini geliştirir ve potansiyel olarak genel üretim maliyetlerini düşürür. | Akış kontrol elemanları, filtreler ve basınç düzenleme özelliklerini birleştiren akışkan sistemler için çok fonksiyonlu valf bileşenleri. |
Geliştirilmiş Yüzey İşlemi | MIM parçaları tipik olarak pürüzsüz bir yüzeye sahiptir ve ek parlatma veya son işlem adımlarına olan ihtiyacı azaltır. Bu, tıbbi implantlar veya optik bileşenler gibi yüksek derecede yüzey kalitesi gerektiren uygulamalar için çok önemli olabilir. | Doku entegrasyonunu desteklemek ve enfeksiyon risklerini en aza indirmek için pürüzsüz bir yüzey kaplamasına sahip biyouyumlu kemik vidaları. |
Malzeme Verimliliği | MIM, geleneksel işleme tekniklerine kıyasla malzeme israfını en aza indiren net şekle yakın bir üretim süreci kullanır. Bu fayda, sürdürülebilir üretim uygulamalarıyla uyumludur. | Karmaşık dişlilerin ve zincir dişlilerinin minimum hurda malzeme ile üretilmesi, kaynakların korunmasını teşvik eder. |
Alüminyum tozları kullanan MIM için sınırlamalar
Faktör | Sınırlama | Etki |
---|---|---|
Sinterleme Zorlukları | Alüminyumun oksijen ile yüksek reaktivitesi, sinterleme işlemi sırasında yüzey oksitlerinin oluşmasına yol açabilir. Bu oksitler parçacıkların birbirine bağlanmasını engelleyerek çelik gibi diğer malzemelerden yapılan MIM parçalara kıyasla daha düşük mekanik mukavemet ve daha fazla gözeneklilikle sonuçlanır. | Yüksek yapısal bütünlük veya basınç direnci gerektiren bileşenler, potansiyel mukavemet sınırlamaları nedeniyle alüminyum MIM için uygun olmayabilir. |
Toz Özellikleri | MIM'de kullanılan alüminyum tozları tipik olarak diğer metaller için kullanılanlardan daha incedir. Bu ince partikül boyutu, hammaddede iyi akışkanlık elde etmeyi zorlaştırabilir ve potansiyel olarak yüzey pürüzlülüğü veya eksik parça dolumu gibi enjeksiyon kalıplama kusurlarına yol açabilir. | Toz özellikleri üzerinde sıkı kontrol ve hammadde reçetesinin dikkatli optimizasyonu, başarılı parça üretimini sağlamak için gereklidir. |
Parça Boyutu Kısıtlamaları | Sinterleme sırasında meydana gelen yüksek büzülme nedeniyle (alüminyum için 20%'ye kadar), alüminyum MIM kullanılarak etkili bir şekilde üretilebilecek parçaların boyutu ve karmaşıklığı sınırlıdır. Büyük veya karmaşık bileşenler çatlamaya veya eğilmeye eğilimli olabilir. | Alüminyum MIM, nispeten basit geometrilere sahip küçük ve orta ölçekli parçalar için en uygunudur. |
Maliyet Değerlendirmeleri | MIM yüksek hacimli üretim için maliyet avantajları sunarken, kalıplama ve toz geliştirme ile ilgili ön maliyetler önemli olabilir. Ayrıca, MIM için alüminyum tozları tipik olarak diğer bazı metal tozlarından daha pahalıdır. | Düşük hacimli uygulamalar için geleneksel işleme veya alternatif üretim teknikleri daha uygun maliyetli olabilir. |
İşlem Sonrası Gereksinimler | Nete yakın şekiller elde edilebilse de, alüminyum MIM parçaları, özel uygulama gereksinimlerine bağlı olarak çapak alma, ısıl işlem veya yüzey bitirme gibi bazı işlem sonrası adımlar gerektirebilir. | Bu ek adımlar toplam üretim süresini ve maliyetini artırabilir. |
Malzeme Özellik Sınırlamaları | MIM için uygun olan diğer bazı metallerle karşılaştırıldığında, alüminyum alaşımları genellikle daha düşük mukavemet ve aşınma direncine sahiptir. Bu durum, zorlu çalışma koşulları altında yüksek mekanik performans gerektiren uygulamalarda kullanımlarını kısıtlayabilir. | Alüminyum MIM parçalar yüksek yükler, aşırı sıcaklıklar veya aşındırıcı ortamlar gerektiren uygulamalar için uygun olmayabilir. |
Yüzey Pürüzlülüğü | MIM alüminyum parçalar iyi yüzey kalitesi elde edebilse de, diğer bazı metal işleme teknikleriyle elde edilebilenler kadar pürüzsüz olmayabilir. Bu, estetik veya işlevsel nedenlerle olağanüstü yüzey kalitesi gerektiren uygulamalar için bir sınırlama olabilir. | Bazı uygulamalar için düzleştirme veya parlatma adımları gerekli olabilir. |
Sınırlı Alaşım Seçimi | MIM için mevcut alüminyum alaşımları yelpazesi, bu süreçte yaygın olarak kullanılan diğer metallere kıyasla şu anda daha küçüktür. Bu durum, özel performans ihtiyaçları için malzeme özelliklerini uyarlama becerisini kısıtlamaktadır. | Devam eden araştırma ve geliştirme çalışmaları, MIM için uygun alüminyum alaşımlarının seçimini genişletmektedir, ancak seçenekler diğer malzemelere kıyasla hala sınırlı olabilir. |
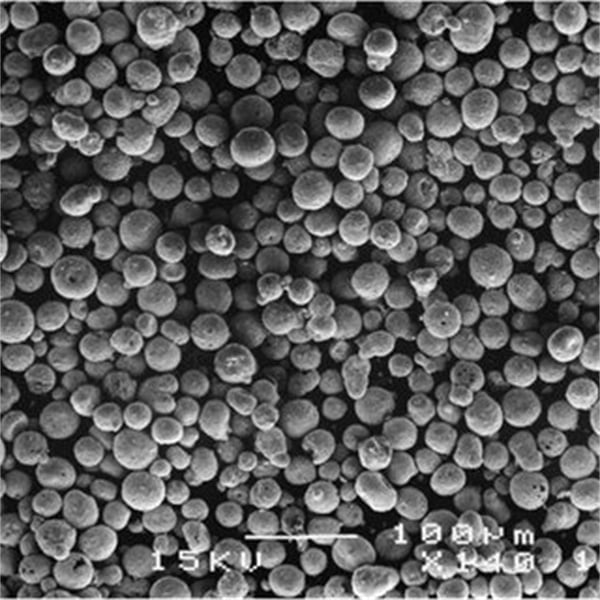
Termal Sprey için Alüminyum Alaşımlı Toz
Mülkiyet | Açıklama | Avantajlar | Dezavantajlar |
---|---|---|---|
Alaşım Bileşimi | Alüminyum alaşım tozları, her biri farklı özellikler sunan çeşitli bileşimlerde gelir. Yaygın alaşım elementleri arasında silikon (Si), magnezyum (Mg), bakır (Cu) ve manganez (Mn) bulunur. | – Si: Aşınma direncini ve dökülebilirliği artırır. - Mg: Ağırlığı azaltır ve korozyon direncini artırır. – Cu: Mukavemeti ve ısı iletkenliğini artırır. – Mn: İşlenebilirliği ve yüksek sıcaklık dayanımını artırır. | - Seçim büyük ölçüde kaplamanın istenen nihai özelliklerine bağlıdır. - Optimum seçim için özel alaşım bilgisi gereklidir. |
Partikül Boyutu ve Morfolojisi | Toz partiküllerinin boyutu ve şekli kaplama özelliklerini önemli ölçüde etkiler. Tozlar, küresel veya düzensiz morfolojilerle 10 mikrondan daha inceden 100 mikronu aşan irilere kadar değişir. | – İnce Tozlar (<45 mikron): Aşınma direnci ve korozyon koruması gerektiren uygulamalar için ideal olan daha pürüzsüz yüzeylere sahip daha yoğun kaplamalar üretin. – Daha Kaba Tozlar (> 45 mikron): Aşınmış bileşenlerin yeniden inşası için uygun olan daha hızlı biriktirme oranları ve gelişmiş bağlanma gücü sunar. – Küresel Tozlar: Akışkanlığı ve paketleme verimliliğini artırarak daha homojen kaplamalar elde edilmesini sağlar. – Düzensiz Tozlar: Daha pürüzlü bir yüzey oluşturabilir ancak kaplama içindeki mekanik kenetlenmeyi iyileştirebilir. | - Daha ince tozlar, doğru besleme için özel termal püskürtme ekipmanı gerektirir. - Daha iri tozlar kaplama içinde daha yüksek gözenekliliğe neden olabilir. |
Termal Püskürtme Tekniği | Farklı termal sprey prosesleri, farklı etkinlik derecelerine sahip alüminyum alaşım tozlarını kullanır. Yaygın teknikler şunları içerir: - Yüksek Hızlı Oksi-Yakıt (HVOF) - Plazma Sprey (PS) - Soğuk Sprey (CS) | – HVOF: Yüksek partikül hızları sağlayarak mükemmel aşınma ve korozyon direncine sahip yoğun kaplamalar oluşturur. Si- ve Cu alaşımlı tozlar için çok uygundur. – PS: Daha geniş bir yelpazedeki alüminyum alaşım tozları için proses çok yönlülüğü sunar. – CS: Daha düşük partikül sıcaklıkları kullanır, tozdaki metalurjik değişiklikleri en aza indirir ve kaplamadaki artık gerilimi azaltır. Mg alaşımlı tozlar için daha uygundur. | - Seçim, tozun erime noktasına ve istenen kaplama özelliklerine bağlıdır. - Her tekniğin biriktirme hızı, kaplama kalınlığı ve maliyet açısından kendi sınırlamaları vardır. |
Yüzey Hazırlığı | Alt tabakanın yüzey durumu, termal sprey kaplamanın yapışmasını ve performansını önemli ölçüde etkiler. | - Optimum mekanik yapıştırma için temiz ve pürüzlendirilmiş bir yüzey sağlar. - Kum püskürtme veya kum aşındırma gibi teknikler yaygın olarak kullanılmaktadır. | - Yanlış yüzey hazırlığı zayıf yapışmaya ve erken kaplama hatasına yol açabilir. |
Kaplama Özellikleri | Alüminyum alaşımlı termal sprey kaplamalar benzersiz bir özellik kombinasyonu sunar: – Elektriksel İletkenlik: Alaşım bileşimine bağlı olarak değişir. Saf alüminyum en yüksek iletkenliği sunarken, Si ve Mg ilaveleri iletkenliği azaltabilir. – Termal İletkenlik: Genellikle yığın alüminyumdan daha düşüktür ancak Cu gibi bazı alaşım elementleri ile iyileştirilebilir. – Korozyon Direnci: Alüminyumun kendisi iyi bir korozyon direnci sergiler ve Mg ilaveleri ile daha da geliştirilir. – Aşınma Direnci: Si ve Cu ilaveleri ile geliştirilmiş kaplama, aşınma uygulamaları için uygun hale getirilmiştir. | - Alaşım seçimi ve proses optimizasyonu yoluyla özel uygulama gereksinimlerini karşılamak üzere uyarlanmıştır. - Farklı özellikler arasında ödünleşimler mevcuttur; örneğin, aşınma direncini en üst düzeye çıkarmak elektrik iletkenliğinden ödün verebilir. | |
Uygulamalar | Alüminyum alaşımlı termal sprey kaplamalar, çok yönlülükleri nedeniyle çeşitli endüstrilerde kullanım alanı bulmaktadır: – Otomotiv: Pistonlar, silindir kapakları, fren kaliperleri (aşınma direnci ve ısı dağılımı için). – Havacılık ve uzay: İniş takımı bileşenleri, uçak gövdesi bileşenleri (korozyon koruması ve ağırlık azaltma için). – Elektronik: Isı alıcıları, elektrik baraları (iletkenlik için seçilen alaşıma bağlı olarak). – Kimyasal İşleme: Kimyasal kaplar, borular (korozyon direnci için). | - Bileşen onarımı, performans geliştirme ve hizmet ömrünü uzatma için uygun maliyetli bir çözüm sunar. - Malzeme seçimi ve proses kontrolü, her uygulamada istenen sonuçların elde edilmesi için çok önemlidir. |
Alüminyum Alaşımlı Toz Özellikleri
Alüminyum alaşım tozları, kabul edilebilir bileşim limitlerini, partikül boyutu aralıklarını, şekil kontrolünü vb. tanımlayan çeşitli standart spesifikasyonlara göre üretilir.
Standart | Açıklama |
---|---|
AMS 4200 | Atomize Al alaşım tozu için havacılık ve uzay malzemesi spesifikasyonu |
ASTM B602 | Al alaşım tozları için standart spesifikasyon |
EN 1706 | Atomize Al tozları için Avrupa standart spesifikasyonu |
ISO 13318 | Gaz ve su atomize Al tozları için uluslararası standart |
DIN 50125 | Atomize Al tozları için Alman ulusal standardı |
Spesifikasyonlar, müşterilerin özel uygulama ve proses gereksinimlerine uygun toz tedarik etmelerini sağlar.
Alüminyum Alaşımlı Toz Boyutları
Son kullanıma bağlı olarak çeşitli boyut aralıklarında alüminyum alaşım tozu üretilmektedir:
- Reaktif uygulamalar için ultra ince toz < 10 mikron
- Genellikle termal sprey için 15 - 45 mikron ince toz
- Orta toz 45 - 100 mikron yaygın olarak kullanılan boyut
- Özel uygulamalar için 150 mikrona kadar kaba toz
Daha kalın kaplamalar için soğuk sprey proseslerinde 180 mikronun üzerindeki daha büyük partiküller kullanılır. Partikül boyutu dağılımının kontrolü de bazı uygulamalar için önemlidir.
Alüminyum Alaşımlı Toz Kaliteleri
Alüminyum alaşım tozu, alaşım türüne bağlı olarak farklı yerleşik kalitelerde üretilir:
- 1xxx serisi tozlar - AA1100, AA1350
- 2xxx serisi tozlar - AA2014, AA2024, AA2219, AA2519
- 5xxx serisi tozlar - AA5083, AA5654
- 6xxx serisi tozlar - AA6061, AA6082
- 7xxx serisi tozlar - AA7050, AA7075
Daha yüksek sayı serileri daha yüksek alaşım seviyelerini ve mukavemeti gösterir. Tescilli kaliteler için özel alaşım bileşimleri de mümkündür.
Alüminyum Alaşımlı Toz Karşılaştırması
Parametre | Soğuk Gaz Atomizasyonu | Su Atomizasyonu |
---|---|---|
Parçacık şekli | Son derece küresel | Daha düzensiz, uydular |
Parçacık boyutu aralığı | 15 - 180 mikron | 5 - 350 mikron |
Boyut dağılımı | Daha sıkı kontrol | Daha geniş dağıtım |
Görünür yoğunluk | Daha yüksek | Daha düşük |
Üretim oranı | Daha düşük | Daha yüksek |
Maliyet | Daha yüksek | Daha düşük |
Su atomize tozlar maliyet avantajına sahiptir, ancak gaz atomize alüminyum alaşımlı tozlara kıyasla daha az küresellik ve daha geniş partikül dağılımlarından muzdariptir.
Alüminyum Alaşımlı Toz Standartları
Alüminyum alaşımlı toz için temel standartlar:
Standart | Organizasyon | Açıklama |
---|---|---|
AMS4200 | SAE | Havacılık ve uzay malzeme spesifikasyonu |
ASTM B602 | ASTM | Kimyasal bileşimler ve elek boyutları |
EN1706 | CEN | Avrupa standardı spesifikasyonu |
ISO13318 | ISO | Gaz atomize ve su atomize formlar için uluslararası standart |
Çeşitli ulusal ve organizasyonel standartlar, alüminyum alaşımlı toz tedarikinin kalitesini ve tutarlılığını sağlamaya yardımcı olur.
Küresel Alüminyum Alaşımlı Toz Tedarikçileri
Tedarikçi | Konum | Yetenekler |
---|---|---|
Valimet A.Ş. | ABD | Geniş atomizasyon aralığı, büyük kapasite |
Sandvik Osprey | BIRLEŞIK KRALLIK | Kontrollü tozların lider tedarikçisi |
TLS Technik GmbH | Almanya | Gaz ve su atomize tozlar konusunda uzman |
Fukuda Metal Folyo ve Toz Co. | Japonya | Geniş alaşım teklifleri |
SCM Metal Ürünleri | Singapur | Alüminyum ve bakır alaşımlarına odaklanın |
Alüminyum Alaşımlı Tozlar için Fiyatlandırma
Alüminyum alaşımlı toz için fiyat bağlı olarak değişir:
- Alaşım sınıfı ve özellikleri
- Partikül şekli ve boyutu özellikleri
- Satın alma miktarı ve lot büyüklüğü
- Bölgesel tarifeler ve ulaşım
Tip | Fiyat Aralığı |
---|---|
1xxx serisi | $5 - $15 kg başına |
2xxx serisi | $10 - $30 kg başına |
5xxx serisi | $15 - $35 kg başına |
6xxx serisi | $20 - $40 kg başına |
7xxx serisi | $30 - $60 kg başına |
Yukarıdaki fiyatlar sadece referans amaçlı yaklaşık aralıklardır. Özel ihtiyaçlarınıza göre tam güncel fiyatlandırma için tedarikçilerle iletişime geçin.
Avantajları ve Sınırlamaları Alüminyum Alaşımlı Toz
Avantajlar | Sınırlamalar |
---|---|
Yüksek Mukavemet-Ağırlık Oranı | Toz İşleme |
Alüminyum alaşımlı toz, ağırlığına göre olağanüstü bir mukavemet sunar. Bu da onu havacılık ve uzay bileşenleri, otomotiv parçaları ve protezler gibi ağırlık azaltmanın kritik olduğu uygulamalar için ideal hale getirir. Çelik gibi geleneksel metallerle karşılaştırıldığında, alüminyum alaşımlı toz parçalar toplam ağırlığı önemli ölçüde azaltırken benzer mukavemet seviyelerine ulaşabilir. | Alüminyum alaşım tozu, özellikle daha ince kaliteler, akışkanlığı ve toz patlaması potansiyeli nedeniyle kullanımı zor olabilir. Depolama, nakliye ve katkılı üretim süreçleri sırasında güvenli ve verimli toz yönetimi sağlamak için özel taşıma ekipmanları ve önlemleri gereklidir. |
Karmaşık Geometriler | Yüzey Pürüzlülüğü |
Alüminyum alaşım tozu, 3D baskı gibi eklemeli üretim (AM) tekniklerinde gelişir. İstenen şekli oluşturmak için malzemeyi kaldıran geleneksel eksiltici üretim yöntemlerinin aksine, AM parçaları tozdan katman katman oluşturur. Bu, geleneksel yöntemlerle elde edilmesi zor veya imkansız olan karmaşık geometrilere sahip karmaşık, hafif bileşenlerin oluşturulmasına olanak tanır. | Alüminyum alaşımlı toz kullanılarak üretilen parçalar, işlenmiş bileşenlere kıyasla biraz daha pürüzlü bir yüzey kalitesi sergileyebilir. Parlatma veya kumlama gibi işlem sonrası teknikler yüzey dokusunu iyileştirebilirken, bu adımlar genel üretim süresine ve maliyetine katkıda bulunur. |
Malzeme Çok Yönlülüğü | Malzeme Maliyeti |
Her biri kendine özgü özelliklere sahip çok çeşitli alüminyum alaşımları toz formunda kullanılabilir. Bu, mühendislerin malzeme seçimini uygulamanın özel gereksinimlerine göre uyarlamasına olanak tanır. Örneğin, bazı alaşımlar yüksek mukavemete öncelik verirken, diğerleri üstün korozyon direnci veya imalattan sonra gelişmiş işlenebilirlik sunar. | Alüminyum alaşım tozu, geleneksel alüminyum külçelerinden veya dövme ürünlerden daha pahalı olabilir. Bunun nedeni kısmen toz üretiminde yer alan ek işleme adımları ve özel kullanım gereksinimleridir. Bununla birlikte, AM'nin azaltılmış malzeme atığı ve net şekle yakın üretim gibi faydaları, bazı uygulamalarda daha yüksek malzeme maliyetini dengeleyebilir. |
Nete Yakın Şekilde Üretim | İzotropik Özellikler |
Alüminyum alaşımlı toz ile katmanlı üretim, net şekle yakın üretim sağlar. Bu, nihai bileşen şeklinin minimum işlem sonrası atıkla elde edildiği anlamına gelir. Bu, malzeme tüketimini azaltır ve genellikle önemli miktarda malzeme çıkarılmasını gerektiren geleneksel yöntemlere kıyasla üretim sürecini kolaylaştırır. | Alüminyum alaşımlı tozdan imal edilen parçalar hafif anizotropik özellikler sergileyebilir, yani mekanik mukavemetleri yapım yönüne bağlı olarak değişebilir. Bunun nedeni, toz partiküllerinin AM işlemi sırasında yapım yönü boyunca hizalanma eğiliminde olmasıdır. Ancak, toz teknolojisi ve AM tekniklerindeki gelişmeler alüminyum alaşımlı bileşenlerin izotropisini sürekli olarak iyileştirmektedir. |
Geri Dönüştürülebilirlik | Çevresel Etki |
Alüminyum alaşım tozu mükemmel geri dönüştürülebilirlik sunar. Geleneksel alüminyum hurdasına benzer şekilde, kullanılmış toz yeniden işlenebilir ve AM süreçlerinde yeniden kullanılabilir, atıkları en aza indirir ve sürdürülebilir üretim uygulamalarını teşvik eder. | Alüminyum alaşımlı toz üretimi enerji yoğun olabilir ve kullanılan enerji kaynağına bağlı olarak, geleneksel üretim yöntemlerine kıyasla daha yüksek bir çevresel ayak izine sahip olabilir. Ancak devam eden araştırmalar, çevresel etkiyi azaltmak için daha enerji verimli toz üretim teknikleri geliştirmeye odaklanmaktadır. |
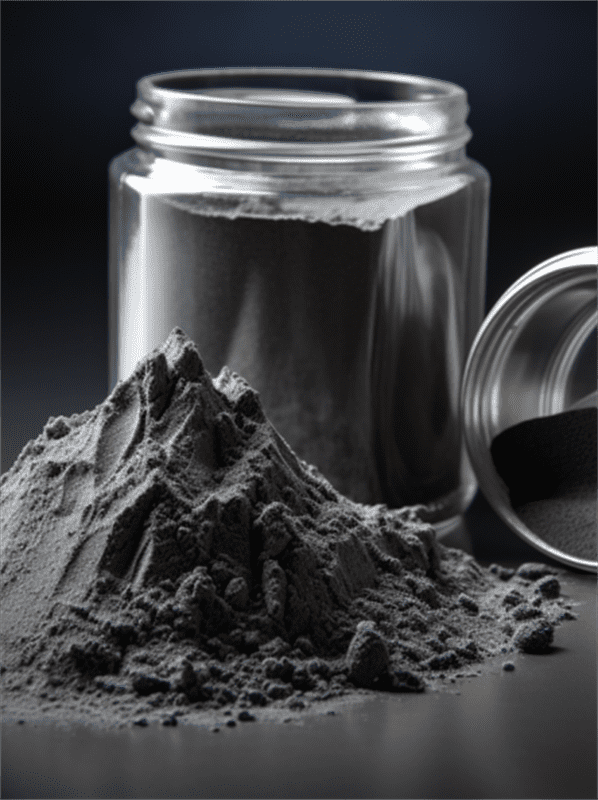
SSS
Alüminyum alaşım tozu olarak kullanılan en yaygın alaşımlar nelerdir?
En yaygın alaşım tozları şunlardır: 2014 ve 2024 gibi 2xxx serisi, 5083 gibi 5xxx alaşımları, 6061 ve 6082 dahil 6xxx alaşımları ve 7050 ve 7075'in popüler olduğu 7xxx alaşımları.
Alüminyum tozları kullanarak metal enjeksiyon kalıplama için en iyi partikül boyutu hangisidir?
Alüminyum alaşımlı tozların kullanıldığı metal enjeksiyon kalıplama için tipik olarak 15-45 mikron arasında bir partikül boyutu aralığı önerilir.
Ne tür atomizasyon işlemleri alüminyum alaşım tozu üretebilir?
Gaz atomizasyonu ve su atomizasyonu kullanılan iki ana endüstriyel işlemdir. Döner disk atomizasyon yöntemi de alüminyum tozları üretebilir.
Termal püskürtme için 5xxx serisi alüminyum alaşımları kullanmanın faydası nedir?
5083 gibi 5xxx serisi Al alaşımları, yüksek sıcaklıklarda boyutsal olarak stabil kalırken mükemmel korozyon direncine sahiptir ve bu da onları deniz ve kimyasal maruziyetler için termal sprey kaplamalar için uygun hale getirir.
Alüminyum alaşım tozunun fiyatını ne etkiler?
Alaşım bileşimi, boyut ve şekil gibi parçacık özellikleri, sipariş hacmi, bölgesel tarifeler ve nakliye maliyetleri, farklı alüminyum tozu tedarikçilerinden alınan nihai fiyatları belirler.
Katmanlı üretim kullanımları için alüminyum alaşım tozları için hangi standartlar geçerlidir?
Temel standartlar arasında ASTM B602, AMS4200, EN1706 ve ISO 13318 bulunmaktadır. Süreçle ilgili gereklilikleri ele almak için AM'ye özgü ek standartlar geliştirilmektedir.
Alüminyum alaşım tozu tekrar kullanılabilir mi?
Alüminyum tozunun yeniden kullanılması genellikle kritik uygulamalar için önerilmez. Saklama koşulları nem toplanmasına ve toz performansını sınırlayan oksidasyona izin verebilir. Kritik olmayan uygulamalarda uygun testlerle küçük çaplı yeniden kullanım mümkün olabilir.
Yüksek numaralı alüminyum alaşımları her zaman düşük numaralı alaşımlardan daha mı güçlüdür?
Genel olarak, daha yüksek numaralı 2xxx, 6xxx ve 7xxx serisi tozlar, 1xxx veya 5xxx alaşımlarından daha yüksek mukavemete sahiptir, ancak tam bileşime, toz özelliklerine ve işleme geçmişine bağlı olarak önemli örtüşmeler olabilir. Garantili toz özellikleri için daima tedarikçi verilerini kontrol edin.
Gözeneklilik ve anizotropi, AM yapımı alüminyum bileşenler için neden bir endişe kaynağıdır?
Lazer veya e-ışın eritme sırasında hızlı katılaşma ile birlikte alüminyumun yüksek termal iletkenliği ve yansıtıcılığı, optimum füzyonu ve kusurlara yol açan gaz kabarcığı kaçışını engeller. Yapı katmanlarına paralel ve enine farklı mekanik özellikler de ortaya çıkar.
Özel kaliteler oluşturmak için farklı alüminyum alaşım tozlarını karıştırabilir miyim?
Parça üretimi sırasında eksik karıştırma, alaşım reaksiyonları veya yetersiz partikül bağlanması riskleri nedeniyle ara veya özel alaşımlar oluşturmak için tozların karıştırılması genellikle tavsiye edilmez. Özellik kombinasyonlarını araştırırken toz tedarikçinize yakından danışın.
Paylaş
MET3DP Technology Co, LTD, merkezi Qingdao, Çin'de bulunan lider bir katmanlı üretim çözümleri sağlayıcısıdır. Şirketimiz, endüstriyel uygulamalar için 3D baskı ekipmanları ve yüksek performanslı metal tozları konusunda uzmanlaşmıştır.
İşletmeniz için en iyi fiyatı ve özelleştirilmiş Çözümü almak için sorgulayın!
İlgili Makaleler
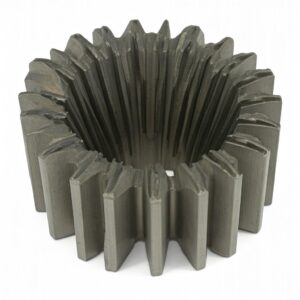
Yüksek Performanslı Nozul Kanat Segmentleri: Metal 3D Baskı ile Türbin Verimliliğinde Devrim
Daha Fazla Oku "Met3DP Hakkında
Son Güncelleme
Bizim Ürünümüz
BİZE ULAŞIN
Herhangi bir sorunuz var mı? Bize şimdi mesaj gönderin! Mesajınızı aldıktan sonra tüm ekibimizle talebinize hizmet edeceğiz.
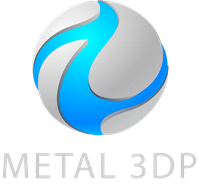
3D Baskı ve Katmanlı Üretim için Metal Tozları