Doğrudan Metal Lazer Sinterlemeye (DMLS) Giriş
İçindekiler
3D Metal Baskının Büyüsü
Karmaşık metal parçaların bir toz yatağından, katman katman, lazer hassasiyetiyle üretildiği bir dünya hayal edin. Bu bilim kurgu değil; Doğrudan Metal Lazer Sinterleme (DMLS), metal bileşenleri tasarlama ve üretme şeklimizi dönüştüren devrim niteliğinde bir 3D baskı teknolojisi.
Seçici Lazer Eritme (SLM) veya Lazer Toz Yatağı Füzyonu (LPBF) olarak da bilinen DMLS, metalik parçacıkları seçici olarak eritmek ve birbirine kaynaştırmak için yüksek güçlü bir lazer kullanan ve dijital bir plandan 3D bir nesne oluşturan bir eklemeli üretim sürecidir. Bu teknoloji, tasarımda benzersiz bir özgürlük sunarak döküm veya işleme gibi geleneksel tekniklerle mümkün olmayan karmaşık geometrilerin ve iç özelliklerin oluşturulmasını sağlar.
Ancak DMLS sadece harika şekillerden ibaret değildir. Aşağıdakiler de dahil olmak üzere bir dizi faydaya sahiptir:
- Olağanüstü Güç ve Doğruluk: DMLS, geleneksel olarak üretilen bileşenlere rakip olan olağanüstü mekanik özelliklere sahip parçalar üretir. Ayrıca, katman katman yaklaşım olağanüstü boyutsal doğruluk sağlar.
- Hafifletme Potansiyeli: DMLS, iç kafesleri ve içi boş yapıları bir araya getirerek, havacılık ve otomotiv gibi sektörlerde büyük bir avantaj olan hafif ancak sağlam parçaların oluşturulmasına olanak tanır.
- Tasarım Özgürlüğü: Yaratıcılığınızı serbest bırakın! DMLS, geleneksel yöntemlerin sınırlamalarını ortadan kaldırarak, başka türlü elde edilmesi inanılmaz derecede zor ve hatta imkansız olan karmaşık geometrilerin ve iç özelliklerin üretilmesini sağlar.
- Hızlı Prototipleme: DMLS, işlevsel prototiplerin hızlı ve verimli bir şekilde oluşturulmasına olanak tanıyarak tasarım ve geliştirme sürecini hızlandırır.
- Toplu Özelleştirme: DMLS, düşük hacimli uygulamalar veya kişiselleştirilmiş ürünler için mükemmel olan küçük partiler halinde özelleştirilmiş parçalar üretmeyi mümkün kılar.
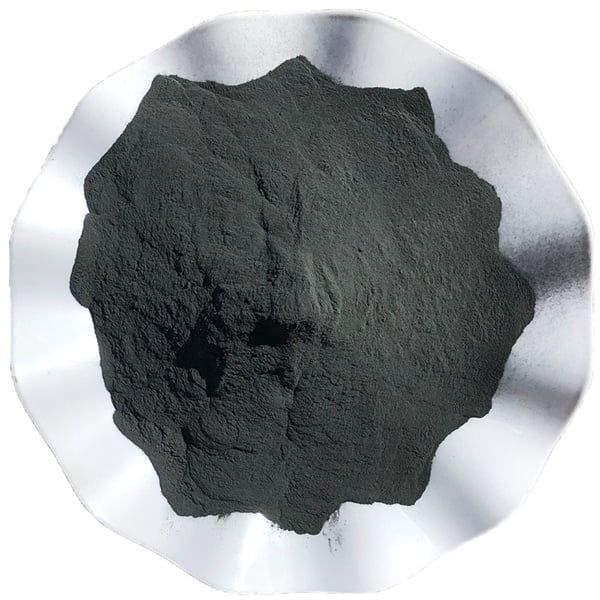
Yapı Taşları DMLS
DMLS sürecinin kalbi, kullanılan metal tozlarında yatmaktadır. Boyutları tipik olarak 20 ila 40 mikrometre arasında değişen bu ince metalik parçacıklar, nihai parçanın istenen özelliklerine göre titizlikle seçilir. İşte DMLS'de en yaygın kullanılan metal tozlarından bazılarına ve benzersiz özelliklerine daha yakından bir bakış:
Yaygın DMLS Metal Tozları:
Metal Tozu | Açıklama | Özellikler | Uygulamalar |
---|---|---|---|
Titanyum Alaşımları (Ti-6Al-4V, Ti-6Al-4V ELI) | Güç, ağırlık ve korozyon direnci arasında iyi bir denge sunan DMLS'nin beygiridir. | Yüksek mukavemet/ağırlık oranı, mükemmel biyouyumluluk (ELI sınıfı). | Havacılık ve uzay, tıbbi implantlar, spor malzemeleri |
Paslanmaz Çelik (316L, 17-4PH) | İyi mekanik özelliklere ve korozyon direncine sahip, çok yönlü ve uygun maliyetli. | Mükemmel korozyon direnci (316L), yüksek mukavemet ve sertlik (17-4PH). | Endüstriyel bileşenler, kimyasal işleme ekipmanları, mücevherat |
Alüminyum Alaşımları (AlSi10Mg, AlSi7Mg0.3) | Hafiftir ve sonradan işleme için iyi işlenebilirlik sunar. | Mükemmel mukavemet/ağırlık oranı, iyi dökülebilirlik (AlSi7Mg0.3). | Otomotiv parçaları, havacılık bileşenleri, ısı eşanjörleri |
Inconel (IN625, 718) | Yüksek sıcaklık dayanımı ve korozyon direnci ile tanınan süper alaşımlar. | Yüksek sıcaklıklarda olağanüstü performans, iyi oksidasyon direnci. | Gaz türbini bileşenleri, roket motorları, ısı eşanjörleri |
Kobalt Krom (CoCr) | Biyouyumlu ve aşınmaya dayanıklıdır, tıbbi implantlar için idealdir. | Mükemmel biyouyumluluk, yüksek mukavemet ve aşınma direnci. | Eklem replasmanları, diş implantları, cerrahi aletler |
Bakır (Cu) | Son derece iletken olduğundan elektrik uygulamaları için mükemmeldir. | Mükemmel termal ve elektriksel iletkenlik. | Isı alıcıları, elektronik bileşenler, dalga kılavuzları |
Nikel (Ni) | Saf Nikel, mukavemet, süneklik ve korozyon direncinin bir kombinasyonunu sunar. | Yüksek mukavemet, iyi süneklik ve korozyon direnci. | Elektrotlar, kimyasal işleme ekipmanları, sert lehim malzemeleri |
Takım Çeliği (H13, M2) | Yüksek aşınma direnci ve tokluk için tasarlanmıştır. | Mükemmel aşınma direnci, yüksek sertlik (H13), iyi tokluk (M2). | Kesici takımlar, kalıplar ve kalıplar, aşınma plakaları |
Değerli Metaller (Altın, Gümüş, Platin) | Estetik çekicilikleri ve benzersiz özellikleriyle ödüllendirilirler. | Yüksek değer, mükemmel elektrik iletkenliği (Altın, Gümüş), yüksek sıcaklık kararlılığı (Platin). | Takı, dekoratif parçalar, elektrik kontakları |
Refrakter Metaller (Tungsten, Tantal) | Olağanüstü yüksek sıcaklık dayanımı ve zorlu ortamlara karşı direnç sunar. | Çok yüksek erime noktaları, mükemmel aşınma direnci (Tungsten |
DMLS Süreç Akışı
DMLS'nin yapı taşlarını incelediğimize göre şimdi de büyüleyici sürecin kendisini inceleyelim. DMLS kullanarak metal bir parça oluşturmanın tipik iş akışının bir dökümünü burada bulabilirsiniz:
- Dijital Tasarım: Yolculuk, istenen parçanın 3D bilgisayar destekli tasarım (CAD) modeliyle başlar. Bu model, nihai bileşenin tam geometrisini, boyutlarını ve iç özelliklerini tanımlar. Modelin DMLS baskı için optimize edilmesini sağlamak için genellikle katmanlı üretim için özel olarak tasarlanmış yazılım kullanılır.
- Veri Dilimleme: 3D CAD modeli daha sonra tipik olarak kalınlığı 20 ila 100 mikrometre arasında değişen bir dizi son derece ince kesit halinde dilimlenir. Her dilim, DMLS makinesinin üzerine inşa edeceği tek bir katmanı temsil eder. Her biri parçanın belirli bir katmanını detaylandıran dijital bir plan yığını düşünün.
- Toz Yatağı Hazırlama: DMLS makinesinin içinde, ince bir metal tozu tabakası bir yapı platformu boyunca eşit olarak biriktirilir. Bu katman dijital modelin ilk dilimine karşılık gelir. Platform hassas bir şekilde yukarı ve aşağı hareket ederek sonraki katmanların oluşturulmasına olanak tanır.
- Seçici Lazer Eritme: Tipik olarak bir fiber lazer olan yüksek güçlü bir lazer ışını, dilimlenmiş modelden gelen verilere göre toz yatağı boyunca tarama yapar. Lazer, belirlenen bölgelerdeki metalik parçacıkları eriterek bir araya getirir ve parçanın ilk katı katmanını oluşturur.
- Katman Katman Yapı: İşlem tekrarlanır - yeni bir toz katmanı biriktirilir ve lazer gerekli bölümleri seçici olarak eriterek bunları bir önceki katmana yapıştırır. Bu döngü, tüm nesne tamamlanana kadar parçayı her seferinde bir katman oluşturarak titizlikle devam eder.
- Destek Kaldırma: Baskı işlemi tamamlandığında, yapı platformu alçalarak yeni oluşan metal parçayı ortaya çıkarır. Bununla birlikte, parça, yapı sırasında herhangi bir sarkma veya deformasyonu önlemek için onunla birlikte basılan destek yapıları ile çevrili olabilir. Bu destek yapıları, talaşlı imalat veya su jeti kesimi gibi teknikler kullanılarak dikkatlice çıkarılır.
- İşlem sonrası: Uygulamaya ve istenen yüzey kalitesine bağlı olarak, DMLS parçası ısıl işlem, sıcak izostatik presleme (HIP) veya kumlama gibi ek işlem sonrası adımlardan geçebilir. Bu işlemler mekanik özellikleri iyileştirebilir, artık gerilmeleri azaltabilir ve nihai bileşenin yüzey kalitesini artırabilir.
Teknik Özellikleri DMLS
DMLS, onu çeşitli uygulamalar için güçlü bir araç haline getiren benzersiz bir dizi teknik özellik sunar. İşte dikkate alınması gereken bazı önemli hususlara daha yakından bir bakış:
- Çözünürlük ve Doğruluk: DMLS, tipik olarak 20 ila 100 mikrometre arasında değişen katman kalınlıkları ile olağanüstü çözünürlük ve boyutsal doğruluğa sahiptir. Bu, son derece karmaşık özelliklerin ve karmaşık geometrilerin oluşturulmasına olanak tanır.
- Yüzey İşlemi: DMLS parçalarının yüzey kalitesi, kullanılan metal tozuna ve kullanılan işleme sonrası tekniklere bağlı olarak değişebilir. Bununla birlikte, sürecin katman katman doğası, geleneksel işleme yöntemlerine kıyasla biraz kademeli bir yüzey kalitesi ile sonuçlanabilir.
- Malzeme Özellikleri: DMLS parçaları, genellikle geleneksel olarak üretilen bileşenlerle karşılaştırılabilir mükemmel mekanik özellikler sergiler. Spesifik metal tozu, yapı parametreleri ve işlem sonrası gibi faktörler parçanın nihai özelliklerini etkileyebilir.
- Yapı Hacmi: Bir DMLS makinesinin yapı hacmi, tek bir yapıda basılabilecek parçanın maksimum boyutunu belirler. Yapı hacimleri birkaç santimetre küpten birkaç metre küpe kadar değişebilir ve geniş bir uygulama yelpazesine hitap eder.
- İnşa Hızı: Diğer bazı eklemeli üretim teknolojileriyle karşılaştırıldığında DMLS nispeten yavaş bir süreç olabilir. Oluşturma süreleri, parçanın boyutuna ve karmaşıklığına, ayrıca katman kalınlığına ve lazer gücü ayarlarına bağlıdır.
- Malzeme Atıkları: Önemli miktarda hurda malzeme üreten eksiltici üretim tekniklerinin aksine, DMLS minimum atık sunar. Kullanılmayan metal tozu geri dönüştürülebilir ve sonraki üretimlerde yeniden kullanılabilir, böylece malzeme tüketimi en aza indirilir.
DMLS'nin Uygulama Alanları
DMLS, benzersiz yetenekleri sayesinde çok çeşitli sektörleri hızla dönüştürmektedir. İşte DMLS'nin parladığı öne çıkan uygulama alanlarından bazıları:
- Havacılık ve uzay: DMLS, uçak ve uzay araçları için hafif ancak sağlam bileşenlerin oluşturulmasını sağlayarak havacılıkta oyunun kurallarını değiştiriyor. Karmaşık iç yapılar ve kafes tasarımları, performansı optimize etmek ve yakıt verimliliğinde çok önemli bir faktör olan ağırlığı azaltmak için dahil edilebilir.
- Tıbbi İmplantlar: Titanyum ve kobalt krom gibi bazı metal tozlarının biyouyumlu yapısı, DMLS'yi özelleştirilmiş tıbbi implantlar üretmek için ideal hale getirir. Bu implantlar hastanın anatomisine göre hassas bir şekilde uyarlanabilir, mükemmel bir uyum ve gelişmiş işlevsellik sunar.
- Otomotiv: (Devamı) Otomotiv endüstrisi, pistonlar, silindir kapakları ve dişli parçaları gibi yüksek performanslı bileşenler oluşturmak için DMLS'den yararlanıyor. Hafif ve karmaşık yapılar tasarlama yeteneği, günümüzün çevreye duyarlı pazarında büyük bir avantaj olan ağırlık azaltma ve gelişmiş yakıt verimliliği sağlar. Ayrıca DMLS, yarış uygulamaları veya sınırlı sayıda üretilen araçlar için özelleştirilmiş parçaların oluşturulmasını sağlar.
- Kalıp ve Kalıp Yapımı: DMLS, kalıplar içinde karmaşık ve konformal soğutma kanallarının üretimine izin vererek kalıp ve kalıp yapım endüstrisinde devrim yaratıyor. Bu kanallar, enjeksiyon kalıplama işlemi sırasında ısı transferini iyileştirerek daha hızlı döngü süreleri, daha iyi parça kalitesi ve daha düşük üretim maliyetleri sağlar.
- Tüketim Malları: DMLS, tüketim malları pazarına girerek mücevher, gözlük ve spor malzemeleri gibi benzersiz ve kişiselleştirilmiş ürünlerin yaratılmasını sağlıyor. Karmaşık geometriler üretme yeteneği yeni tasarım olanaklarının kilidini açarken, DMLS'nin talebe bağlı yapısı özelleştirme trendine hitap ediyor.
- Prototipleme: DMLS, hızlı prototipleme için güçlü bir araçtır ve mühendislerin ve tasarımcıların yeni ürünlerin işlevsel prototiplerini hızla oluşturmasına olanak tanır. Bu hızlı yineleme döngüsü, tasarım ve geliştirme sürecini hızlandırarak daha hızlı ürün yeniliği ve pazara sunma süresi sağlar.
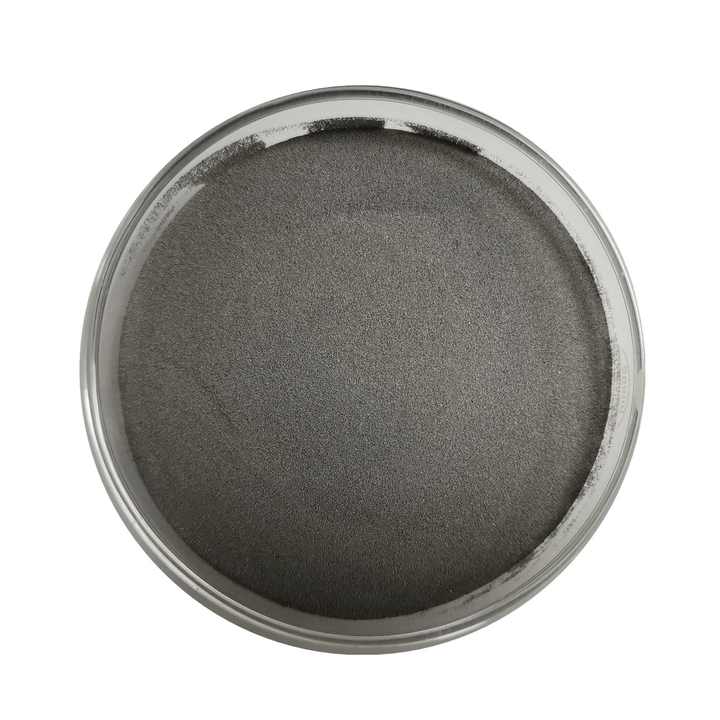
Sınırlamalar ve Dikkate Alınması Gereken Hususlar DMLS
DMLS çok sayıda avantaj sunsa da, sınırlamalarını ve dikkat edilmesi gereken hususları kabul etmek çok önemlidir:
- Maliyet: DMLS makineleri ve metal tozları, geleneksel üretim ekipmanı ve malzemelerine kıyasla pahalı olabilir. Bu da DMLS'yi basit parçaların yüksek hacimli üretimi için daha az uygun bir seçenek haline getirebilir.
- Yüzey İşlemi: Daha önce de belirtildiği gibi, DMLS'nin katman katman yapısı bir miktar kademeli yüzey kalitesi ile sonuçlanabilir. İşlem sonrası teknikler yüzey kalitesini artırabilirken, mükemmel pürüzsüzlükte bir yüzey elde etmek için ek işleme adımları gerekebilir ve bu da sürecin maliyetini ve karmaşıklığını artırır.
- Yapım süresi: DMLS, özellikle büyük veya karmaşık parçalar için yavaş bir süreç olabilir. Teslim süreleri ve üretim programları göz önünde bulundurulurken bunun hesaba katılması gerekir.
- Destek Yapıları: DMLS işlemi sırasında destek yapılarına duyulan gereksinim karmaşıklığı artırabilir ve potansiyel olarak işlem sonrası süreyi uzatabilir. Dikkatli tasarım değerlendirmeleri, karmaşık destek yapılarına olan ihtiyacı en aza indirebilir.
- Kısmi Yeterlilik: Havacılık ve tıp gibi sektörlerdeki kritik uygulamalar için DMLS parçaları, sıkı performans ve güvenlik standartlarını karşıladıklarından emin olmak için ek test ve yeterlilik prosedürleri gerektirebilir.
DMLS ve Diğer Katmanlı Üretim Teknolojileri
DMLS, 3D baskı oyunundaki tek oyuncu değil. İş için doğru aracı seçmenize yardımcı olmak için DMLS'nin diğer önde gelen katmanlı üretim teknolojileriyle hızlı bir karşılaştırmasını burada bulabilirsiniz:
- Stereolitografi (SLA): SLA, sıvı reçineyi katman katman katı bir nesneye dönüştürmek için bir lazer kullanır. DMLS ile karşılaştırıldığında, SLA daha yüksek çözünürlük ve daha pürüzsüz yüzey kaplamaları sunar, ancak başta plastikler olmak üzere daha küçük bir malzeme yelpazesiyle sınırlıdır.
- Seçici Lazer Sinterleme (SLS): SLS, DMLS'ye benzer şekilde çalışır ancak plastik toz parçacıklarını sinterlemek için bir lazer kullanır. SLS genellikle plastik parçalar üretmek için DMLS'den daha hızlı ve daha uygun maliyetlidir, ancak metal uygulamalar için DMLS'ye kıyasla daha düşük mukavemet ve sınırlı malzeme seçenekleri sunar.
- Kaynaşmış Biriktirme Modellemesi (FDM): FDM, nesneyi katman katman oluşturmak için erimiş plastik filamenti ekstrüde ederek çalışır. FDM yaygın olarak kullanılan ve nispeten ucuz bir teknolojidir ancak DMLS'ye kıyasla daha düşük çözünürlük ve güç sunar.
- Elektron Işınıyla Eritme (EBM): DMLS'ye benzer şekilde EBM de metal tozunu eritmek için bir elektron ışını kullanır. EBM, titanyum gibi reaktif metalleri işlemede mükemmeldir, ancak vakum ortamı gerektirir, bu da onu aşağıdakilere kıyasla daha karmaşık ve pahalı bir süreç haline getirir DMLS.
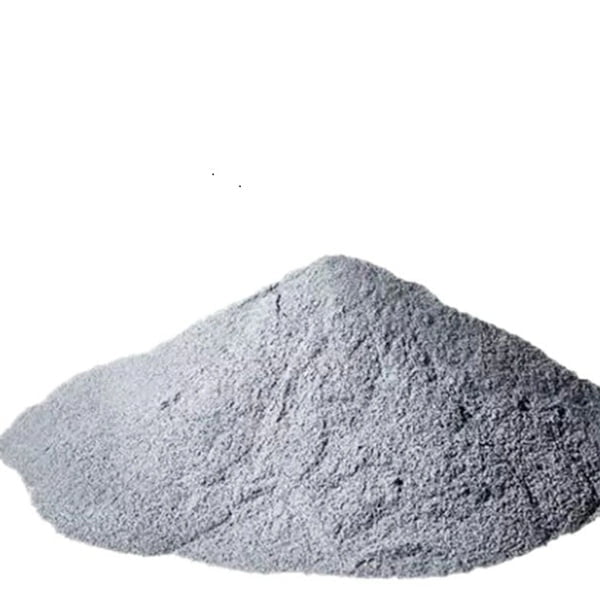
SSS
DMLS hakkında en sık sorulan sorulardan bazılarını burada bulabilirsiniz:
S: DMLS'nin avantajları nelerdir?
C: DMLS, olağanüstü tasarım özgürlüğü, yüksek mukavemet ve parça doğruluğu, hafifletme potansiyeli, hızlı prototipleme yetenekleri ve minimum malzeme israfı gibi çeşitli avantajlar sunar.
S: DMLS'nin sınırlamaları nelerdir?
C: DMLS'nin sınırlamaları arasında geleneksel üretime kıyasla nispeten yüksek maliyeti, yüzey kalitesi ile ilgili potansiyel zorluklar, diğer bazı 3D baskı teknolojilerine kıyasla daha yavaş yapım süreleri ve belirli uygulamalar için destek yapıları ve parça kalifikasyonu gibi ek hususlara duyulan ihtiyaç yer almaktadır.
S: DMLS ile hangi malzemeler kullanılabilir?
C: DMLS ile titanyum alaşımları, paslanmaz çelik, alüminyum alaşımları, Inconel, kobalt krom, bakır, nikel, takım çeliği, değerli metaller ve refrakter metaller dahil olmak üzere çok çeşitli metal tozları kullanılabilir.
S: DMLS'nin bazı uygulamaları nelerdir? (Devamı)
C: DMLS, havacılık, tıbbi implantlar, otomotiv, kalıp ve kalıp yapımı, tüketim malları, prototipleme ve daha fazlası dahil olmak üzere çeşitli endüstrilerde uygulama alanı bulmaktadır.
S: Bir DMLS makinesinin maliyeti nedir?
C: Bir DMLS makinesinin maliyeti, üretim hacmine, yeteneklerine ve markasına bağlı olarak büyük ölçüde değişebilir. Fiyatlar, daha küçük makineler için on binlerce dolardan, üst düzey endüstriyel sistemler için milyonlarca dolara kadar değişebilir.
S: DMLS'yi evde kullanabilir miyim?
C: Metal için masaüstü 3D yazıcılar ortaya çıkarken, endüstriyel sınıf DMLS makineleri karmaşıklıkları, maliyetleri, güvenlik hususları ve özel toz işleme gereksinimleri nedeniyle genellikle ev kullanımı için uygun değildir.
S: DMLS'nin geleceği nedir?
C: DMLS'nin geleceği parlak. Teknoloji ilerledikçe, daha uygun fiyatlı DMLS makineleri, daha geniş bir uyumlu metal tozu yelpazesi ve daha da yüksek baskı hızları görmeyi bekleyebiliriz. DMLS, çeşitli sektörlerde yenilikçi ve yüksek performanslı parçaların oluşturulmasını sağlayarak üretimde giderek daha önemli bir rol oynamaya hazırlanıyor.
Sonuç
DMLS, benzersiz tasarım özgürlüğü ve olağanüstü güç ve doğrulukla karmaşık metal parçalar oluşturma yeteneği sunarak üretimde devrim niteliğinde bir sıçramayı temsil ediyor. DMLS, hafif havacılık bileşenlerinden özelleştirilmiş tıbbi implantlara kadar geniş bir ürün yelpazesini tasarlama ve üretme şeklimizi yeniden şekillendiriyor. Maliyet ve yapım süresi gibi dikkate alınması gereken sınırlamalar olsa da DMLS gelişmeye ve daha erişilebilir hale gelmeye devam ederek onu mühendisler, tasarımcılar ve üreticiler için güçlü bir araç haline getiriyor. DMLS teknolojisi olgunlaştıkça ve yetenekleri genişledikçe, önümüzdeki yıllarda daha da çığır açan uygulamaların ortaya çıkmasını bekleyebiliriz.
Paylaş
MET3DP Technology Co, LTD, merkezi Qingdao, Çin'de bulunan lider bir katmanlı üretim çözümleri sağlayıcısıdır. Şirketimiz, endüstriyel uygulamalar için 3D baskı ekipmanları ve yüksek performanslı metal tozları konusunda uzmanlaşmıştır.
İşletmeniz için en iyi fiyatı ve özelleştirilmiş Çözümü almak için sorgulayın!
İlgili Makaleler
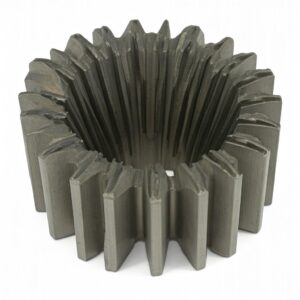
Yüksek Performanslı Nozul Kanat Segmentleri: Metal 3D Baskı ile Türbin Verimliliğinde Devrim
Daha Fazla Oku "Met3DP Hakkında
Son Güncelleme
Bizim Ürünümüz
BİZE ULAŞIN
Herhangi bir sorunuz var mı? Bize şimdi mesaj gönderin! Mesajınızı aldıktan sonra tüm ekibimizle talebinize hizmet edeceğiz.
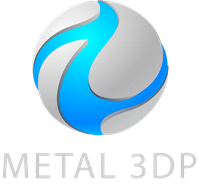
3D Baskı ve Katmanlı Üretim için Metal Tozları