DMLS Teknolojisinin işlem adımları
İçindekiler
Hiç havadan karmaşık metal nesneler yaratmayı hayal ettiniz mi? Doğrudan Metal Lazer Sinterleme (DMLS) teknolojisi ile bu hayal gerçeğe dönüşüyor. Seçici Lazer Eritme (SLM) olarak da bilinen DMLS, karmaşık ve işlevsel metal parçalar oluşturmak üzere metal tozu parçacıklarını katman katman titizlikle birbirine kaynaştırmak için yüksek güçlü bir lazer kullanan devrim niteliğinde bir 3D baskı sürecidir.
Dijital bir dosyadan karmaşık bir dişli veya iç kanallara sahip hafif bir havacılık bileşeni oluşturduğunuzu hayal edin - işte DMLS'nin gücü budur. Peki ama bu sihir tam olarak nasıl gerçekleşiyor? Kemerlerinizi bağlayın, çünkü DMLS'nin büyüleyici dünyasını adım adım keşfetmek üzereyiz.
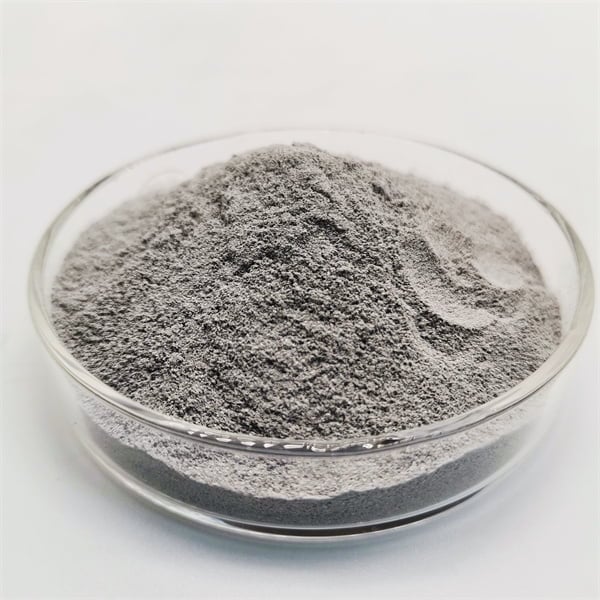
Yapı Taşları: Yapı Taşlarına Bir Bakış DMLS Metal Tozları
Herhangi bir DMLS oluşumunun temeli metal tozunun kendisinde yatar. Boyutları tipik olarak 15 ila 63 mikron arasında değişen (bu inanılmaz derecede küçük!) bu ince, metalik granüller, her biri belirli uygulamalar için benzersiz özellikler sunan çeşitli tatlarda gelir. İşte en popüler DMLS metal tozu seçeneklerinden bazılarına bir göz atın:
Metal Tozu | Kompozisyon | Özellikler | Uygulamalar |
---|---|---|---|
Paslanmaz Çelik 316L | 16-18% Krom, 10-14% Nikel, 2% Molibden | Mükemmel korozyon direnci, yüksek mukavemet, biyouyumlu | Tıbbi implantlar, havacılık ve uzay bileşenleri, mücevherat |
Titanyum 6Al-4V (Sınıf 23) | 90% Titanyum, 6% Alüminyum, 4% Vanadyum | Yüksek mukavemet/ağırlık oranı, iyi biyouyumluluk, mükemmel korozyon direnci | Havacılık ve uzay bileşenleri, tıbbi implantlar, spor malzemeleri |
Inconel 625 | Nikel-krom bazlı süper alaşım | Olağanüstü yüksek sıcaklık dayanımı, korozyon direnci | Türbin kanatları, ısı eşanjörleri, nükleer reaktörler |
Alüminyum AlSi10Mg | 10% Silikon ve 0,5% Magnezyum içeren alüminyum alaşım | Hafif, iyi korozyon direnci, yüksek termal iletkenlik | Otomotiv parçaları, ısı alıcıları, elektronik muhafazalar |
Bakır | 100% Bakır | Yüksek elektrik iletkenliği, iyi termal iletkenlik | Isı eşanjörleri, elektrikli bileşenler, dalga kılavuzları |
Takım Çeliği (H13) | Yüksek Krom içerikli alaşımlı çelik | Yüksek aşınma direnci, iyi termal stabilite | Kalıplar, kalıplar, kesici takımlar |
Nikel | 100% Nikel | Mükemmel korozyon direnci, iyi süneklik | Kimyasal işleme ekipmanları, elektrikli bileşenler, ısı eşanjörleri |
Kobalt Krom (CoCrMo) | Molibdenli kobalt-krom alaşımı | Yüksek mukavemet, aşınma direnci, biyouyumlu | Tıbbi implantlar, diş protezleri, aşınma parçaları |
Altın | 100% Altın | Yüksek süneklik, dövülebilirlik, mükemmel korozyon direnci | Takı, elektronik, dekoratif uygulamalar |
Bu tablo, DMLS metal tozlarının çeşitli dünyasına bir bakış sağlar. Her malzeme benzersiz güçlere sahiptir ve bu da onları çok çeşitli uygulamalar için uygun hale getirir. Bir metal tozu seçerken, istenen mekanik özellikler, korozyon direnci, ağırlık hususları ve biyouyumluluk (tıbbi uygulamalar için) gibi faktörlerin tümü çok önemli bir rol oynar.
Masanın Ötesinde: Metal Tozu Özelliklerine Daha Derin Bir Bakış
Bu metal tozlarının herhangi bir toz olmadığını anlamak önemlidir. DMLS işlemi sırasında optimum performans sağlamak için titizlikle tasarlanmışlardır. İşte dikkate alınması gereken bazı temel özellikler:
- Parçacık boyutu ve dağılımı: Tutarlı bir partikül boyutu ve dağılımı, düzgün toz akışı ve eşit lazer eritme için çok önemlidir.
- Küresellik: Küresel partiküller daha iyi akışkanlık ve paketleme yoğunluğu sunarak daha düzgün bir yapı süreci sağlar.
- Akışkanlık: Tozun DMLS makinesi içinde serbestçe akabilmesi, tutarlı katman oluşumu için gereklidir.
- Görünür yoğunluk: Bu, tozun kütlesinin toplam hacmine oranını ifade eder. Daha yüksek bir görünür yoğunluk, her katmana daha fazla malzemenin paketlenmesini sağlayarak daha yoğun bir nihai parça elde edilmesini sağlar.
- Lazer emiciliği: Metal tozunun lazer enerjisini verimli bir şekilde absorbe etme kabiliyeti, eritme sürecini ve genel yapı kalitesini belirler.
Üreticiler, DMLS metal tozlarının bu katı gereksinimleri karşıladığından emin olmak için büyük çaba harcarlar. Bu özellikleri dikkatlice kontrol ederek, optimum DMLS performansı için özel olarak tasarlanmış tozlar oluştururlar.
Dijital Hayallerden Metalik Gerçekliğe: Adım Adım DMLS Süreci
Yapı taşlarını incelediğimize göre şimdi de DMLS'nin büyüleyici dünyasına göz atalım. İşte adım adım sürecin bir dökümü:
1. Uygun metal tozunu seçin: Daha önce tartışıldığı gibi, doğru metal tozunun seçilmesi nihai parçada istenen özelliklerin elde edilmesi için kritik öneme sahiptir.
2. 3D modelleme yazılımı kullanarak bir 3D model oluşturun: DMLS'nin büyüsü, istenen nesnenin dijital bir temsiliyle başlar. Dijital çağ için bir heykeltıraşın keskisine benzeyen 3D modelleme yazılımı, mühendislerin geleneksel üretim yöntemleri kullanılarak oluşturulması imkansız olan karmaşık geometriler tasarlamasına olanak tanır. Bu 3D modeller, genel şeklinden iç kanallara ve karmaşık özelliklere kadar nihai parçanın her ayrıntısını belirler.
3. Yapı platformunu hazırlayın: Dijital bir tuvalin hayata geçtiğini hayal edin. DMLS makinesinin yapı platformu, metal nesnenin katman katman inşa edileceği temel görevi görür. Bu platform, yapım süreci için pürüzsüz ve tutarlı bir başlangıç noktası sağlamak amacıyla titizlikle temizlenir ve düzleştirilir.
4. Metal tozu baskı platformunun üzerine yerleştirin: Kalınlığı tipik olarak 20 ila 100 mikron arasında değişen ince bir metal tozu tabakası, yapı platformu boyunca eşit olarak biriktirilir. Bu katman, nesne için ilk yapı taşı görevi görür. Düzgün ve tutarlı bir toz tabakası elde etmek için bıçak kaplama sistemi veya silindir mekanizması gibi çeşitli teknikler kullanılabilir.
5. Lazer Büyüyü Eritir: Gerçek sihir burada gerçekleşir. Dijital 3D model tarafından titizlikle yönlendirilen yüksek güçlü bir lazer ışını, metal toz yatağı boyunca tarama yaparak parçacıkları seçici bir şekilde eritir. Lazerin güç yoğunluğu ve tarama yolu, her katman için istenen geometriyi oluşturmak üzere hassas bir şekilde kontrol edilir. Lazer tozu eritirken, parçacıkları katı bir kütle halinde birleştirir ve nesneyi her seferinde bir katman oluşturacak şekilde etkili bir şekilde inşa eder.
6. Katman Katman, Nesne Şekil Alıyor: DMLS süreci tekrarlayan bir döngüyü takip eder. İlk katman eritildikten sonra, üstüne yeni bir metal tozu katmanı bırakılır. Lazer daha sonra bu yeni katmanı tarayarak tozu eritir ve daha önce oluşturulmuş katmana kaynaştırır. Bu döngü, tüm tasarım tamamlanana kadar nesneyi aşağıdan yukarıya doğru titizlikle inşa ederek katman katman devam eder.
7. Soğuma: Son katman eritildikten sonra DMLS makinesi, üretilen nesnenin kontrollü bir atmosferde yavaşça soğumasını sağlar. Bu kontrollü soğutma işlemi, parça içindeki artık gerilmeleri ve bükülmeleri en aza indirmeye yardımcı olarak boyutsal doğruluğunu ve yapısal bütünlüğünü sağlar.
8. Desteğin Sökülmesi: Geleneksel inşaatlarda kullanılan iskelelere benzer şekilde, DMLS yapıları genellikle hassas özelliklerin baskı işlemi sırasında çökmesini önlemek için destek yapıları gerektirir. Bu destek yapıları tipik olarak aynı metal tozundan yapılır, ancak yapı tamamlandıktan sonra kolayca çıkarılacak şekilde tasarlanmıştır. Talaşlı imalat, su jeti kesimi veya mekanik sökme gibi teknikler, bu destek yapılarını ayırmak için kullanılabilir ve nihai metalik nesneyi tüm ihtişamıyla ortaya çıkarır.
9. DMLS teknolojisi işlem sonrası: Bazı durumlarda, DMLS ile üretilen nesne, istenen yüzey kalitesini veya mekanik özellikleri elde etmek için ek işlem sonrası adımlar gerektirebilir. Bu adımlar, gerilimin azaltılması veya mukavemetin artırılması için ısıl işlem, daha pürüzsüz bir yüzey kalitesi için kumlama veya daha yüksek boyutsal doğruluk için işleme içerebilir.
DMLS'nin Avantaj ve Sınırlamalarının Ortaya Çıkarılması
DMLS teknolojisi, geleneksel üretim yöntemlerine göre çok sayıda avantaj sunar:
- Tasarım özgürlüğü: DMLS, iç kanallar, kafesler ve geleneksel teknikler kullanılarak üretilmesi imkansız veya maliyetli olabilecek diğer karmaşık özellikler de dahil olmak üzere inanılmaz derecede karmaşık geometrilerin oluşturulmasına olanak tanır.
- Hızlı prototipleme: Doğrudan bir 3D modelden işlevsel parçalar oluşturma yeteneği, hızlı prototiplemeye olanak tanıyarak mühendislerin tasarımları hızlı ve verimli bir şekilde yinelemesine olanak tanır.
- Hafifletme: DMLS, yüksek mukavemet-ağırlık oranlarına sahip hafif yapıların oluşturulmasına olanak tanıyarak havacılık ve otomotiv endüstrilerindeki uygulamalar için idealdir.
- Özelleştirme: DMLS, özelleştirilmiş parçaların ve düşük hacimli partilerin üretimini kolayca kolaylaştırarak özel uygulamalar veya tek seferlik projeler için mükemmel hale getirir.
Ancak DMLS'nin de dikkate alınması gereken sınırlamaları vardır:
- Maliyet: DMLS makineleri ve metal tozları pahalı olabilir, bu da süreci yüksek hacimli üretim çalışmaları için daha az uygun hale getirir.
- Yapı boyutu sınırlamaları: DMLS makinelerinin üretim hacmi, geleneksel tekniklere kıyasla tipik olarak sınırlıdır.
- Yüzey kaplaması: Bazı DMLS parçaları iyi bir yüzey kalitesi elde edebilirken, diğerleri daha pürüzsüz bir estetik için ek işlem sonrası gerektirebilir.
- Malzeme sınırlamaları: DMLS için mevcut olan malzeme yelpazesi, sürekli genişlemesine rağmen hala gelişmektedir.
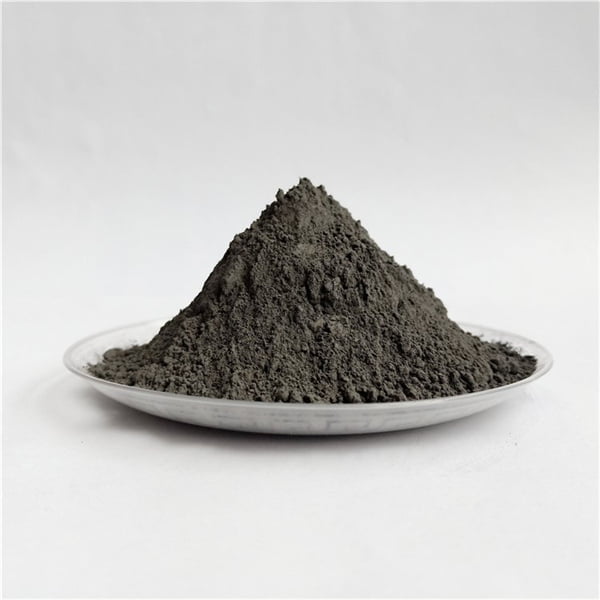
SSS
S: DMLS ve SLS arasındaki fark nedir?
C: Hem DMLS hem de Seçici Lazer Sinterleme (SLS), nesneleri katman katman oluşturmak için lazer kullanan 3D baskı süreçleridir. Bununla birlikte, kullandıkları malzemelerde önemli bir ayrım vardır. DMLS metal tozları ile çalışır ve katı bir nesne oluşturmak için bunları birlikte eritir. Buna karşılık, SLS tipik olarak plastik veya naylon tozları kullanır ve parçacıkları tamamen eritmeden sinterler (kaynaştırır). Bu fark, birkaç önemli varyasyonla sonuçlanır:
- Malzeme özellikleri: DMLS baskılı nesneler, plastiğe kıyasla metalin doğal özellikleri nedeniyle tipik olarak SLS parçalarından çok daha güçlü ve dayanıklıdır.
- Uygulamalar: DMLS, havacılık, otomotiv ve tıbbi uygulamalar için fonksiyonel metal parçalar oluşturmak için uygundur. SLS, prototip oluşturma ve iyi estetiğe sahip plastik parçalar üretme konusunda mükemmeldir.
- Maliyet: DMLS, metal tozlarının daha yüksek maliyeti ve daha karmaşık makineler nedeniyle genellikle SLS'ye kıyasla daha pahalı bir süreçtir.
S: DMLS baskılı parçalar ne kadar güçlüdür?
C: DMLS baskılı parçaların mukavemeti, kullanılan özel metal tozuna ve kullanılan işlem sonrası tekniklere bağlıdır. Bununla birlikte, DMLS parçaları inanılmaz derecede güçlü olabilir ve genellikle işlenmiş (geleneksel olarak üretilmiş) muadilleriyle karşılaştırılabilir mekanik özelliklere ulaşabilir. Isıl işlem gibi faktorenler nihai ürünün gücünü daha da artırabilir.
S: DMLS parçaları için yüzey kaplama seçenekleri nelerdir?
C: DMLS baskılı parçalar, sürecin katman katman doğası nedeniyle tipik olarak biraz pürüzlü bir yüzey kaplamasına sahiptir. Bununla birlikte, daha pürüzsüz bir yüzey elde etmek için çeşitli işlem sonrası teknikler kullanılabilir:
- İşleme: Frezeleme ve tornalama gibi geleneksel işleme teknikleri, pürüzsüz ve hassas bir yüzey kalitesi oluşturmak için kullanılabilir.
- Kumlama: Bu teknik, parçanın yüzeyini düzeltmek için bir aşındırıcı parçacık akışı kullanır.
- Parlatma: Yüksek oranda yansıtıcı bir yüzey elde etmek için mekanik veya kimyasal parlatma kullanılabilir.
Yüzey kaplamasının seçimi, nihai parçanın istenen estetiğine ve işlevsel gereksinimlerine bağlıdır.
S: DMLS ile ilgili çevresel hususlar nelerdir?
C: DMLS, her üretim süreci gibi bazı çevresel etkilere sahiptir. İşte dikkate alınması gereken bazı temel faktörler:
- Enerji tüketimi: DMLS makineleri, yüksek güçlü lazeri çalıştırmak ve kontrollü bir atmosferi korumak için önemli miktarda enerji gerektirir.
- Malzeme atıkları: Parça geometrisine ve destek yapısı tasarımına bağlı olarak, DMLS işlemi sırasında bir miktar metal tozu israf edilebilir. Bununla birlikte, bazı makineler atıkları en aza indirmek için toz geri dönüşüm özellikleri sunar.
- Emisyonlar: DMLS süreci, basılan malzemeye bağlı olarak az miktarda toz ve duman üretebilir. Bu emisyonları azaltmak için uygun havalandırma sistemleri çok önemlidir.
Üreticiler sürekli olarak DMLS teknolojisinin verimliliğini ve sürdürülebilirliğini iyileştirmeye çalışmaktadır. Daha enerji verimli makineler geliştirmek ve atık oluşumunu en aza indirmek için araştırmalar devam etmektedir.
DMLS'nin Geleceği: Yarının İnovasyonlarına Bir Bakış
DMLS teknolojisi hızla gelişen ve sürekli olarak mümkün olanın sınırlarını zorlayan bir alandır. İşte DMLS'nin geleceğini şekillendiren bazı heyecan verici trendler:
- Çok malzemeli DMLS: Aynı yapı içinde birden fazla metal tozu kullanarak nesneleri basma yeteneği, benzersiz özellik kombinasyonlarına sahip parçalar oluşturmak için kapılar açar.
- Daha büyük yapı hacimleri: Daha büyük ve daha karmaşık metalik nesnelerin oluşturulmasına olanak tanıyan daha büyük yapı zarflarına sahip DMLS makineleri geliştirilme aşamasındadır.
- Daha yüksek baskı hızları: Lazer teknolojisi ve toz işleme mekanizmalarındaki gelişmeler daha hızlı baskı sürelerine yol açarak DMLS'yi üretim uygulamaları için daha verimli hale getirmektedir.
- Yeni malzemeler: DMLS ile uyumlu malzeme yelpazesi, yeni alaşımlar ve hatta titanyum alüminid (TiAl) gibi egzotik malzemeler de dahil olmak üzere sürekli genişlemektedir.
DMLS teknolojisi gelişmeye devam ettikçe, havacılık ve otomotivden tıbba ve ötesine kadar çeşitli sektörlerde devrim yaratma potansiyeline sahiptir. Karmaşık, işlevsel ve hafif metal parçalar yaratma kabiliyetiyle DMLS, üretimin geleceğini şekillendirmede önemli bir rol oynamaya hazırlanıyor.
Paylaş
MET3DP Technology Co, LTD, merkezi Qingdao, Çin'de bulunan lider bir katmanlı üretim çözümleri sağlayıcısıdır. Şirketimiz, endüstriyel uygulamalar için 3D baskı ekipmanları ve yüksek performanslı metal tozları konusunda uzmanlaşmıştır.
İşletmeniz için en iyi fiyatı ve özelleştirilmiş Çözümü almak için sorgulayın!
İlgili Makaleler
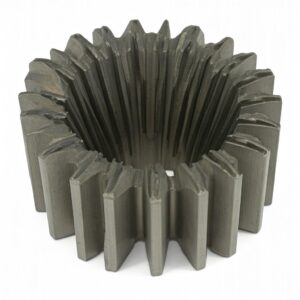
Yüksek Performanslı Nozul Kanat Segmentleri: Metal 3D Baskı ile Türbin Verimliliğinde Devrim
Daha Fazla Oku "Met3DP Hakkında
Son Güncelleme
Bizim Ürünümüz
BİZE ULAŞIN
Herhangi bir sorunuz var mı? Bize şimdi mesaj gönderin! Mesajınızı aldıktan sonra tüm ekibimizle talebinize hizmet edeceğiz.
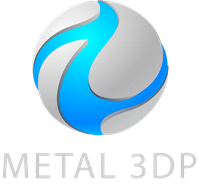
3D Baskı ve Katmanlı Üretim için Metal Tozları