Enjeksiyonla Kalıplanabilir Toz
İçindekiler
Enjeksiyonla kalıplanabilir toz karmaşık ve yüksek hassasiyetli metal parçalar üretmek için endüstriyel bir üretim süreci olan toz enjeksiyon kalıplamada kullanılan bir tür hammadde malzemesini ifade eder. Bu toz, ince metal tozları ve polimer bağlayıcıların bir karışımı olup, yüksek hacimde karmaşık net şekilli parçalar halinde enjeksiyonla kalıplanabilir.
Enjeksiyonla Kalıplanabilir Toz Kullanmanın Avantajları
Avantaj | Açıklama | Fayda |
---|---|---|
Karmaşık Geometriler: IMP, geleneksel enjeksiyon kalıplama teknikleriyle elde edilmesi zor veya imkansız olan ince özelliklere sahip karmaşık şekillerin oluşturulmasına olanak tanır. Bu tasarım özgürlüğü, çeşitli sektörlerde yenilikçi bileşenler için kapılar açar. | Erimiş plastikler gibi geleneksel kalıplama malzemelerinin aksine IMP, kalıplama işlemi sırasında toz partiküllerini bir arada tutan bir bağlayıcı sistem kullanır. Bu da iç kanalları, alt kesimleri ve diğer karmaşık geometrileri olan parçaların oluşturulmasını sağlar. | |
Malzeme Verimliliği: IMP, net şekle yakın üretimi teşvik ederek talaşlı imalat gibi eksiltici tekniklere kıyasla malzeme israfını en aza indirir. Bu özellikle pahalı veya yüksek performanslı malzemeler için faydalıdır. | Enjeksiyon kalıplama sırasında toz dağılımı üzerindeki hassas kontrol, fazla malzeme kullanımını en aza indirir. Ayrıca, deneme çalışmaları sırasında hurda parçalar üreten geleneksel süreçlerin aksine, IMP minimum malzeme israfıyla daha hızlı tasarım yinelemelerine olanak tanır. | |
Geniş Malzeme Seçimi: IMP, geleneksel enjeksiyon kalıplamaya kıyasla daha geniş bir malzeme seçeneği yelpazesi sunar. Bu çok yönlülük, uygulamaya göre uyarlanmış belirli özelliklere sahip parçaların oluşturulmasına olanak tanır. | Enjeksiyon kalıplamada kullanılan standart polimerlerin ötesinde, IMP metal tozları, seramikler ve hatta kompozit malzemeler kullanabilir. Bu, benzersiz güç, iletkenlik veya biyouyumluluk kombinasyonlarına sahip parçaların yaratılması için kapılar açar. | |
Yüksek Performanslı Parçalar: IMP'de metal ve seramik tozlarının kullanılabilmesi, olağanüstü mukavemet, ısı direnci veya aşınma özelliklerine sahip yüksek performanslı parçaların üretilmesini sağlar. | Metal enjeksiyon kalıplı (MIM) bileşenler, işlenmiş (dökme) metallerle karşılaştırılabilir mekanik özellikler elde edebilir ve bu da onları zorlu uygulamalar için uygun hale getirir. Benzer şekilde, seramik IMP parçaları mükemmel aşınma direnci ve yüksek sıcaklık performansı sunar. | |
Seri Üretim Potansiyeli: Başlangıçta prototipleme için kullanılan IMP teknolojisi, karmaşık parçaların uygun maliyetli seri üretimini mümkün kılacak şekilde olgunlaşmıştır. | IMP süreçlerinde elde edilebilen yüksek otomasyon derecesi, tutarlı kalitede büyük miktarlarda parçanın verimli bir şekilde üretilmesini sağlar. Bu da onu yüksek hacimli uygulamalar için uygun bir seçenek haline getirir. | |
Geliştirilmiş Yüzey Kaplaması: Geleneksel metal döküm teknikleriyle karşılaştırıldığında, IMP bazen nihai parçalarda daha pürüzsüz bir yüzey kalitesi elde edebilir. | İnce tozların kullanımı ve kontrollü kalıplama süreci, yüzey kusurlarını en aza indirerek parlatma gibi kapsamlı işlem sonrası adımlara olan ihtiyacı potansiyel olarak azaltabilir. |
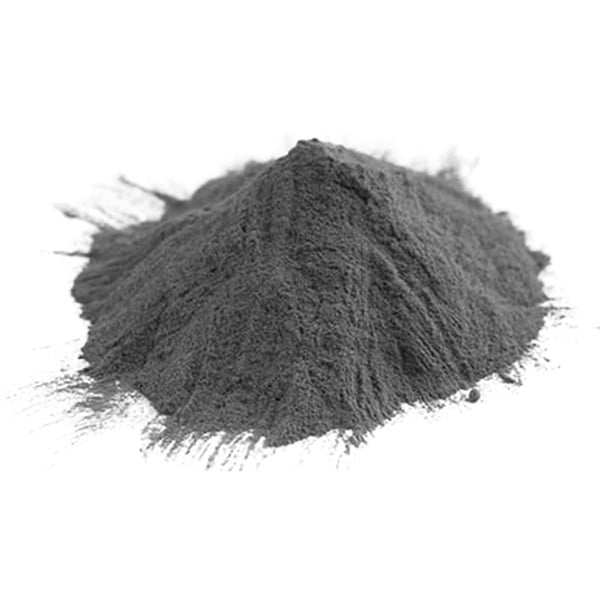
Enjeksiyonla Kalıplanabilir Toz Bileşimi
Bileşen | Açıklama | Fonksiyon |
---|---|---|
Baz Tozlar | Bunlar nihai parçanın birincil işlevsel malzemesini oluşturur ve üç ana tipte kategorize edilebilir: Metal Tozları: Paslanmaz çelik, takım çeliği veya süper alaşımlar gibi çeşitli alaşımların ince bölünmüş metalik parçacıkları. Seramik Tozları: Alümina, zirkonya veya toz halindeki silikon nitrür gibi seramik malzemeler. Polimer Tozları: Naylon veya polipropilen gibi enjeksiyon kalıplamada yaygın olarak kullanılan termoplastik polimerler. | Baz toz seçimi, kalıplanan parçanın mukavemet, aşınma direnci veya termal performans gibi nihai özelliklerini belirler. |
Bağlayıcı Sistem | Bu, kalıplama işlemi sırasında temel toz partiküllerini bir arada tutan geçici bir yapıştırıcı görevi gören çok önemli bir bileşendir. Bağlayıcı sistemi tipik olarak şunlardan oluşur: Termoplastik Polimer: Enjeksiyon kalıplama aşamasında eriyerek akışkanlık ve baz toz ile yapışma sağlayan termoplastik bir reçine. * Mumlar veya Katkı Maddeleri: Bunlar akış özelliklerini geliştirebilir, bağlama verimliliğini artırabilir veya bağlayıcı içinde toz dağılımına yardımcı olabilir. | Bağlayıcı sistemi, tozun enjeksiyon sırasında kalıplanabilir bir hammadde gibi davranmasını sağlar ve karmaşık şekillerin oluşturulmasına olanak tanır. |
Gözenek Oluşturucular | Bunlar, kalıplanmış parça içinde geçici gözenekler oluşturan isteğe bağlı katkı maddeleridir. Bunlar şunlar olabilir: * Organik Malzemeler: Bunlar, bağlayıcı sistemin çıkarılmasını kolaylaştıran bir gözenekler ağı bırakarak bağlayıcı çözme sırasında yanar. * Kimyasal Sızdırma Maddeleri: Bunlar, işlem sonrası bir adım sırasında belirli bir çözücü içinde çözünerek kontrollü bir gözenek yapısı oluşturur. | Gözenek oluşturucular, nihai parça içinde gözenekli yapıların oluşturulmasını sağlar; bu da filtreler veya kemik implantları gibi uygulamalar için faydalı olabilir. |
Kullanılan Metal Tozlarının Özellikleri
Karakteristik | Açıklama | MIM'deki Önemi |
---|---|---|
Partikül Boyutu ve Dağılımı | Metal tozu partiküllerinin boyutu ve dağılımı, MIM'in aşağıdaki yönlerini önemli ölçüde etkiler: Kalıp Dolgusu ve Yeşil Mukavemet: Daha ince tozlar genellikle daha iyi paketleme yoğunluğu sunar ve enjeksiyon sırasında kalıp dolumunu iyileştirebilir. Bununla birlikte, aşırı ince partiküller akışkanlığı engelleyebilir ve işleme sırasında zorluklara yol açabilir. Dar bir partikül boyutu dağılımı, tutarlı bir paketleme sağlar ve kalıplanmış parça içindeki boşlukları en aza indirerek iyi bir yeşil mukavemete (sinterlemeden önce parçanın mukavemeti) katkıda bulunur. Sinterleme Davranışı ve Nihai Özellikler: Partikül boyutu, partiküllerin katı bir yapı oluşturmak için birbirine bağlandığı sinterleme sürecini etkiler. Daha geniş bir boyut dağılımına sahip tozlar homojen olmayan sinterlemeye yol açabilir ve potansiyel olarak parçanın nihai mekanik özelliklerini etkileyebilir. | Partikül boyutu ve dağılımının dikkatli bir şekilde seçilmesi, iyi kalıp dolumu, yeşil mukavemet ve nihai sinterlenmiş bileşende optimum performans elde etmek için çok önemlidir. |
Parçacık Morfolojisi | Bu, metal tozu partiküllerinin şeklini ifade eder. İdeal olarak, MIM süreçleri küresel veya küresel morfolojiye yakın tozları tercih eder. | Küresel partiküller daha kolay akarak kalıp dolumunu ve paketleme yoğunluğunu iyileştirir. Düzensiz şekilli partiküller boşluklar oluşturabilir ve akışkanlığı engelleyerek kalıplanan parçada kusurlara yol açabilir. |
Görünür ve Dokunma Yoğunluğu | Bu özellikler, farklı koşullar altında tozun yığın yoğunluğunu temsil eder. Görünür Yoğunluk: Bu, partiküller arasındaki boşluklar dikkate alındığında, tozun hareketsiz haldeki yoğunluğunu ifade eder. Musluk Yoğunluğu: Bu, standartlaştırılmış bir kılavuz çekme işlemiyle elde edilen daha yoğun bir durumu yansıtmaktadır. | Daha yüksek kademe yoğunluğu genellikle MIM'de verimli malzeme kullanımı ve nihai parçada iyi boyutsal doğruluk için arzu edilir. Ayrıca kalıplama sırasında daha iyi paketlemeye katkıda bulunur ve sinterleme sırasında büzülmeyi en aza indirir. |
Kimyasal Bileşim | Metal tozunda kullanılan belirli elementler veya alaşımlar, sinterlenmiş parçanın nihai özelliklerini belirler. | Metal tozu bileşiminin seçimi, özel uygulama gereksinimlerini karşılamak için mukavemet, korozyon direnci veya aşınma direnci gibi özelliklerin uyarlanmasına olanak tanır. MIM paslanmaz çelik, takım çeliği ve hatta Inconel gibi yüksek performanslı alaşımlar dahil olmak üzere çeşitli metal alaşımları kullanabilir. |
Akışkanlık | Bu, tozun yerçekimi veya uygulanan kuvvetler altında akma kolaylığını ifade eder. | İyi akışkanlık, enjeksiyon kalıplama sırasında homojen toz dağılımı için gereklidir. Akışkanlığı zayıf olan tozlar, paketleme yoğunluğunda tutarsızlıklara ve nihai parçada potansiyel kusurlara yol açabilir. |
Metal Tozları için Standartlar
Kullanılan metal tozları bileşim ve tane standartlarını karşılamalıdır:
Standart Gövde | Standart | Açıklama | IMP'deki Önemi |
---|---|---|---|
ASTM Uluslararası (ASTM) | ASTM B930 - Metal Enjeksiyon Kalıplama (MIM) Hammaddesinin Toz Karakterizasyonu için Standart Kılavuz | Bu standart, MIM'de kullanılan metal tozlarının özelliklerini karakterize etmek için çeşitli test yöntemlerini özetlemektedir. | Partikül boyutu dağılımı, morfoloji, akışkanlık ve görünür yoğunluk gibi faktörleri değerlendirmek için bir çerçeve sağlar. Bu, IMP uygulamaları için kullanılan metal tozlarında tutarlılık ve kalite kontrolü sağlar. |
** | ** | * ASTM B783 - Metal Enjeksiyon Kalıplama (MIM) Uygulamaları için Paslanmaz Çelik Tozları için Standart Şartname | Bu standart, MIM'de kullanılan paslanmaz çelik tozlarının kimyasal bileşimi, parçacık boyutu dağılımı ve akışkanlığı için özel gereklilikleri tanımlar. |
** | ** | * ASTM D4000 - Plastik Malzemelerin Belirlenmesi için Standart Sınıflandırma Sistemi | IMP'ye özel olmamakla birlikte, bu standart IMP hammaddesinde potansiyel olarak bağlayıcı olarak kullanılanlar da dahil olmak üzere çeşitli plastik malzeme türleri için bir sınıflandırma sistemi sağlar. |
Uluslararası Standardizasyon Örgütü (ISO) | * ISO 3095 - Metalik tozlar - Hall akış ölçer ile akış hızının belirlenmesi | Bu standart, Hall akış ölçer kullanarak metalik tozların akışkanlığını ölçmek için bir yöntem belirler. | IMP'de iyi kalıp dolumu ve tutarlı parça kalitesi elde etmek için kritik bir özellik olan akışkanlığı değerlendirmek için standartlaştırılmış bir yaklaşım sağlar. |
** | ** | * ISO 4497 - Plastikler - Termoplastiklerin eriyik akış hızının (MFR) ve eriyik hacim-akış hızının (MVR) belirlenmesi | Bu standart, IMP hammaddesindeki bağlayıcı bileşenle ilgili olabilecek termoplastik malzemelerin eriyik akış hızını (MFR) ölçmek için bir yöntemi ana hatlarıyla belirtir. |
Üretim Sürecindeki Adımlar
Üretim süreci aşağıdaki temel adımlardan oluşmaktadır:
Adım | Açıklama | Önem |
---|---|---|
1. Toz Hazırlama ve Karıştırma | Temel toz (metal, seramik veya polimer) dikkatlice seçilir ve istenen nihai özelliklere göre ön işleme tabi tutulur. Gözenek oluşturucular veya yağlayıcılar gibi katkı maddeleri dahil edilebilir. Toz daha sonra hassas bir şekilde tartılır ve homojen bir besleme stoğu oluşturmak için bağlayıcı sistemle karıştırılır. | Bu adım, nihai parçanın özelliklerinin temelini oluşturur. Dikkatli seçim ve doğru karıştırma, işleme sırasında tutarlı malzeme davranışı sağlar. |
2. Enjeksiyon Kalıplama | Hazırlanan IMP hammaddesi yarı erimiş bir duruma kadar ısıtılır ve yüksek basınç altında kapalı bir kalıp boşluğuna enjekte edilir. Kalıp, nihai parçanın istenen şeklini kopyalar. | Bu aşama parçanın geometrisini tanımlar. Enjeksiyon sırasında tutarlı akış ve basınç, doğru parça boyutları ve minimum kusur elde etmek için çok önemlidir. |
3. Debinding | "Yeşil parça" olarak da adlandırılan kalıplanmış parça, bağlayıcı sistemi çıkarmak için bir bağlayıcı çözme işlemine tabi tutulur. Bu işlem şu yollarla gerçekleştirilebilir: * Çözücü Bağ Çözme: Parça, bağlayıcıyı çözen ve geride toz yapısını bırakan bir çözücüye daldırılır. * Termal Debinding: Parça, bağlayıcının termal olarak ayrıştığı ve gaz olarak dışarı çıktığı kontrollü bir ısıtma döngüsüne maruz bırakılır. | Hassas toz yapısına zarar vermeden istenen nihai şeklin ve gözenekliliğin elde edilmesi için etkili debinding kritik öneme sahiptir. |
4. Sinterleme | Öğütülmüş parça kontrollü bir atmosferde (genellikle vakum veya inert gaz altında) yüksek sıcaklıklara tabi tutulur. Bu işlem, toz parçacıkları arasında difüzyonu ve bağlanmayı teşvik ederek katı ve ağ şekline yakın bir bileşen elde edilmesini sağlar. | Sinterleme, parçanın mukavemet, yoğunluk ve boyutsal kararlılık gibi nihai mekanik özelliklerini belirler. Hassas sıcaklık kontrolü ve atmosfer yönetimi çok önemlidir. |
5. İşlem Sonrası | Uygulama gereksinimlerine bağlı olarak, sinterlenmiş parça aşağıdaki gibi ek son işlem adımlarından geçebilir: * İşleme veya Taşlama: Hassas boyut toleransları veya yüzey kalitesi elde etmek için. * Isıl İşlem: Mukavemet veya sertlik gibi belirli mekanik özellikleri geliştirmek için. * Kaplama veya Sızma: Aşınma direnci veya korozyon direnci gibi yüzey özelliklerini iyileştirmek için. | İşlem sonrası işlemler nihai IMP parçasının işlevselliğini ve estetiğini daha da geliştirebilir. |
Enjeksiyon Kalıplı Parça Uygulamaları
Enjeksiyonla kalıplanabilir toz endüstrilerdeki çeşitli karmaşık ve yüksek hassasiyetli parçaların üretiminde kullanılabilir:
Endüstri | Uygulama Örnekleri | Enjeksiyon Kalıplamanın Faydaları |
---|---|---|
Otomotiv | İç bileşenler (gösterge panelleri, kapı panelleri, konsollar) Kaput altı parçaları (fan davlumbazları, emme manifoldları) Fonksiyonel bileşenler (dişliler, zincir dişlileri) | Hassas özelliklere sahip karmaşık şekillerin yüksek hacimli üretimi. Gelişmiş yakıt verimliliği için hafif parçalar. Çeşitli performans ihtiyaçları için geniş malzeme seçenekleri (dayanıklılık, ısı direnci). |
Tüketici Elektroniği | Elektronik muhafazalar (telefonlar, dizüstü bilgisayarlar, tabletler) Konektörler ve düğmeler Dahili bileşenler (braketler, dişliler) | Yüksek boyutsal hassasiyete sahip karmaşık parçaların seri üretimi. Estetik ve kullanıcı konforu için pürüzsüz yüzeyler. Malzeme seçimi ve kalıplama teknikleriyle elde edilebilecek renk ve doku çeşitliliği. |
Tıbbi Cihazlar | Cerrahi aletler (saplar, tutamaklar) Protez bileşenleri (diz eklemleri, diş implantları) Tek kullanımlık tıbbi bileşenler (şırıngalar, flakonlar) | Hijyen ve güvenlik için sterilize edilebilir malzemeler. İnsan vücudunda kullanım için biyouyumlu malzemeler (belirli polimerler ve metal alaşımları). Tıbbi uygulamalarda hassas işlevsellik için karmaşık geometriler. |
Havacılık ve Savunma | Uçak bileşenleri (kanallar, iniş takımı parçaları) Uydu bileşenleri (braketler, muhafazalar) Savunma ekipmanları (kasklar, silah bileşenleri) | Havacılık ve uzay uygulamalarında ağırlık azaltımı için hafif ve yüksek mukavemetli malzemeler. Özel gereksinimler için alev geciktirici veya ısıya dayanıklı malzemeler. Zorlu ortamlar ve zorlu çalışma koşulları için dayanıklı parçalar. |
Tüketim Malları | Oyuncaklar ve oyunlar Aletler (muhafazalar, düğmeler, kadranlar) Spor malzemeleri (kasklar, bisiklet parçaları) | Yüksek hacimli tüketici ürünleri için uygun maliyetli üretim. Görsel çekicilik için çok çeşitli renk ve yüzeyler. Günlük kullanım için dayanıklı ve işlevsel parçalar. |
Parça İmalatı için Enjeksiyon Kalıplamanın Avantajları
Avantaj | Açıklama | Fayda |
---|---|---|
Yüksek Hacimli Üretim: Enjeksiyon kalıplama, büyük miktarlarda aynı parçaların verimli bir şekilde üretilmesinde mükemmeldir. Otomasyon yetenekleri ve hızlı döngü süreleri, uygun maliyetli seri üretime olanak tanır. | Bu, tüketici elektroniği veya otomotiv bileşenleri gibi milyonlarca birim gerektiren ürünler için özellikle avantajlıdır. Üretim süreci boyunca tutarlı kalite ve tekrarlanabilirlik sağlanır. | |
Tasarım Esnekliği: Enjeksiyon kalıplama, karmaşık şekiller, ince duvarlar ve iç özellikler de dahil olmak üzere çok çeşitli geometrik karmaşıklıkları barındırabilir. Bu tasarım özgürlüğü, işlevsel ve yenilikçi parçaların oluşturulmasını sağlar. | Bazı eksiltici üretim yöntemlerinin aksine, enjeksiyon kalıplama takım geometrisi ile sınırlı değildir. Alt kesimler, kanallar ve diğer karmaşık özellikler doğrudan parçaya kalıplanabilir. | |
Boyutsal Doğruluk ve Tekrarlanabilirlik: Kalıp tasarımı ve enjeksiyon parametreleri üzerindeki hassas kontrol, yüksek üretim hacimlerinde tutarlı ve doğru parça boyutları sağlar. | Bu, boyutsal düzeltme için işlem sonrası adımlara olan ihtiyacı en aza indirir ve montaj için değiştirilebilir parçalar sağlar. Tekrarlanabilirlik, tutarlı ürün kalitesini ve işlevselliğini korumak için çok önemlidir. | |
Geniş Malzeme Seçimi: Enjeksiyon kalıplamada termoplastikler, termosetler, elastomerler ve hatta bazı metal alaşımları (Metal Enjeksiyon Kalıplama - MIM yoluyla) dahil olmak üzere çok çeşitli malzemeler kullanılabilir. | Bu çok yönlülük, mukavemet, ısı direnci, kimyasal direnç veya esneklik gibi istenen özelliklere göre en uygun malzemenin seçilmesine olanak tanır. | |
Yüzey İşlemi ve Estetik: Enjeksiyon kalıplama, pürüzsüz ve yüksek kaliteli yüzey kaplamalarına sahip parçalar üretebilir ve genellikle parlatma gibi kapsamlı işlem sonrası adımlara olan ihtiyacı ortadan kaldırır. Ayrıca, kalıplama sırasında çeşitli renklendiriciler ve dokular dahil edilebilir. | Bu, nihai ürünün görsel çekiciliğine ve işlevselliğine katkıda bulunur. Pürüzsüz yüzeyler tıbbi cihazlarda hijyen veya tüketim mallarında kolay temizlik için gerekli olabilir. | |
Malzeme Verimliliği: Enjeksiyon kalıplama, net şekle yakın üretimi teşvik ederek talaşlı imalat gibi eksiltici tekniklere kıyasla malzeme israfını en aza indirir. Yolluk ve yolluk olarak adlandırılan fazla malzeme genellikle geri dönüştürülebilir ve sonraki üretim çalışmalarında yeniden kullanılabilir. | Bu, maliyet ve sürdürülebilirlik açısından faydalıdır. Atıkların en aza indirilmesi, üretim sürecinin çevresel etkisini de azaltır. | |
Otomasyon Potansiyeli: Enjeksiyon kalıplama süreci, operasyon için minimum insan müdahalesi gerektirecek şekilde yüksek oranda otomatikleştirilebilir. Bu, tutarlı üretim kalitesi sağlar ve işçilik maliyetlerini azaltır. | Otomasyon özellikle yüksek hacimli üretim çalışmaları için avantajlıdır ve operatör beceri seviyesinden bağımsız olarak tutarlı ürün kalitesi sağlar. |
Üretim Sürecinin Sınırlamaları
Bazı sınırlamalar da vardır:
- Parça ağırlığı <400 g ile sınırlıdır
- Duvar kalınlığı > 0,4 mm
- Karmaşık geometriler için gerekli montajlar
- Kalıplar için pahalı takımlar
- Sinterleme sırasında boyutsal değişiklikler
Küresel Hammadde Tedarikçileri
Birçok uluslararası şirket enjeksiyon kalıplama için hazır hammadde tedarik etmektedir:
Şirket | Konum | Malzemeler |
---|---|---|
BASF | Almanya | 316L paslanmaz çelik, titanyum alaşımları |
Sandvik | İsveç | Paslanmaz çelikler, takım çelikleri |
GKN | BIRLEŞIK KRALLIK | Alüminyum ve magnezyum alaşımları |
Rio Tinto | Avustralya | Metal ve seramik enjeksiyonlu karışımlar |
Gösterge Niteliğinde Fiyatlandırma
Malzeme | Fiyat Aralığı |
---|---|
Paslanmaz Çelik | $50-70 kg başına |
Takım Çeliği | $45-65 kg başına |
Tungsten Ağır Alaşım | $130-170 kg başına |
Fiyatlandırma sipariş hacimlerine, özelleştirme ihtiyaçlarına ve ekonomik faktörlere bağlıdır.
Kullanmanın Artıları ve Eksileri Enjeksiyonla Kalıplanabilir Tozlar
Avantajlar | Dezavantajlar |
---|---|
Karmaşık ve karmaşık şekiller | Sınırlı boyut ve ağırlık |
Daha yakın toleranslar | Pahalı araç ve gereçler |
İnce yüzey kalitesi | Sinterleme sırasında boyutsal değişiklikler |
Malzeme çeşitliliği | İşlem sonrası genellikle gereklidir |
Yüksek üretim, parça başına düşük maliyet | Kırılgan malzemeler çatlama eğilimindedir |
Azaltılmış atık | Malzeme seçimini kısıtlar |
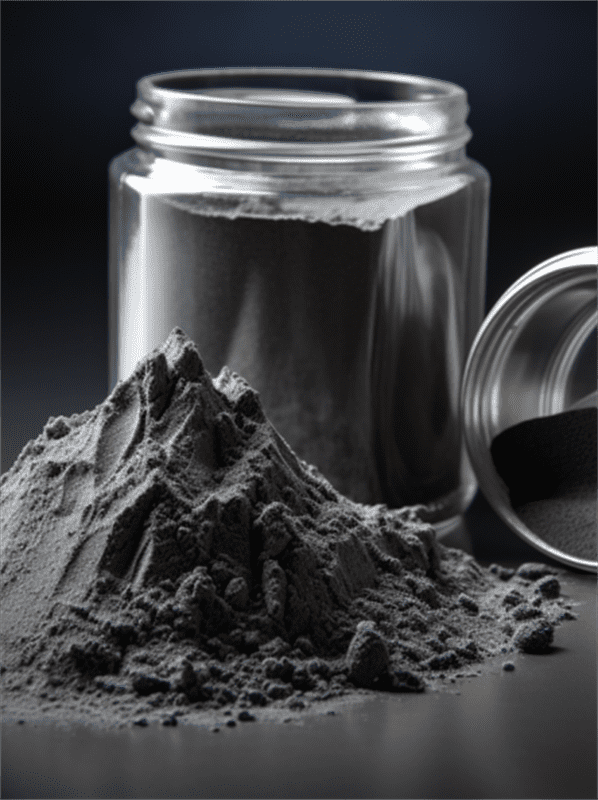
SSS
S: Enjeksiyonla kalıplanabilir tozların tipik bileşimi nedir?
C: Ağırlık olarak 80-90% metal tozu, 8-20% bağlayıcı ve 1-2% yağlayıcı içerirler. Yaygın bağlayıcılar balmumu, PP, PE ve PEG'dir.
S: Hangi boyut aralığında tozlar kullanılıyor?
C: 1-20 mikron arasında tozlar kullanılır. Daha ince tozlar yoğunluğu artırır ancak topaklanmaya eğilimli olabilir.
S: Sinterleme sırasında ne kadar büzülme meydana gelir?
C: Sıvı faz sinterleme sırasında parçalarda 20%'ye kadar doğrusal büzülme meydana gelir. Takım tasarımında ödenekler yapılmalıdır.
S: Sinterlenmiş metal enjeksiyon kalıplı parçalarda çatlaklara ne sebep olur?
C: Fırınlarda homojen olmayan ısıtma, sinterlemeden sonra hızlı soğutma kullanımı, zayıf toz karışımı ve kırılgan alaşımların seçimi.
S: Enjeksiyonla kalıplanabilir tozlar için hangi malzeme seçenekleri mevcut?
C: Paslanmaz çelikler, takım çelikleri, tungsten ağır alaşımları, bakır alaşımları, titanyum ve titanyum alaşımları ve diğerleri.
Paylaş
MET3DP Technology Co, LTD, merkezi Qingdao, Çin'de bulunan lider bir katmanlı üretim çözümleri sağlayıcısıdır. Şirketimiz, endüstriyel uygulamalar için 3D baskı ekipmanları ve yüksek performanslı metal tozları konusunda uzmanlaşmıştır.
İşletmeniz için en iyi fiyatı ve özelleştirilmiş Çözümü almak için sorgulayın!
İlgili Makaleler
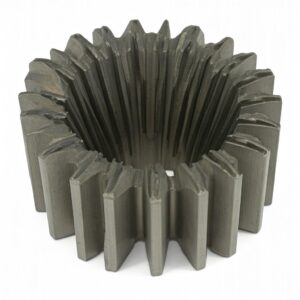
Yüksek Performanslı Nozul Kanat Segmentleri: Metal 3D Baskı ile Türbin Verimliliğinde Devrim
Daha Fazla Oku "Met3DP Hakkında
Son Güncelleme
Bizim Ürünümüz
BİZE ULAŞIN
Herhangi bir sorunuz var mı? Bize şimdi mesaj gönderin! Mesajınızı aldıktan sonra tüm ekibimizle talebinize hizmet edeceğiz.
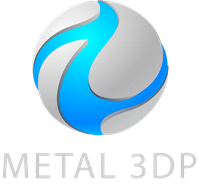
3D Baskı ve Katmanlı Üretim için Metal Tozları