Metal Enjeksiyon Kalıplama (MIM)
İçindekiler
Plastik enjeksiyon kalıplamanın karmaşık ayrıntılarını ve tasarım özgürlüğünü metalin benzersiz gücü ve dayanıklılığıyla birleştiren bir üretim süreci hayal edin. İşte bu sihirli Metal Enjeksiyon Kalıplama (MIM), metal işleme dünyasında oyunun kurallarını değiştiriyor.
Metal Enjeksiyon Kalıplama (MIM) nedir?
MIM, metal tozu ve polimerik bağlayıcının benzersiz bir karışımını kullanan ağ şekline yakın bir üretim tekniğidir. Hammadde olarak bilinen bu kombinasyon, kalıplanabilir bir macun gibi davranır. MIM süreci, bu hammaddeyi stratejik olarak yüksek basınç altında bir kalıp boşluğuna enjekte ederek istenen karmaşık geometriyi kopyalar. İşte MIM sürecinin temel aşamalarına ayrılması:
- Hammadde Hazırlama: İnce toz haline getirilmiş metal, tipik olarak paslanmaz çelik, çelik alaşımları ve hatta tungsten karbür gibi egzotik malzemeler, bir bağlayıcı sistemle titizlikle karıştırılır. Bu bağlayıcı, enjeksiyon kalıplama sırasında karışımın akışkanlığını sağlar.
- Kalıplama: Hazırlanan hammadde, yüksek basınç altında hassas şekilde tasarlanmış bir kalıp boşluğuna enjekte edilir. Bu, istenen metal bileşenin ağa yakın karmaşık şeklini kopyalar.
- Debinding: Kalıplamadan sonra, bağlayıcının kalıplanmış parçadan çıkarılması gerekir. Genellikle debinding olarak adlandırılan bu hassas süreç, seçilen bağlayıcı sistemine bağlı olarak termal teknikler (ısıtma) veya solvent debinding içerebilir.
- Sinterleme: Artık metal tozundan oluşan kırılgan bir yapıya sahip olan öğütülmüş parça, kontrollü bir atmosferde yüksek sıcaklıkta sinterleme işlemine tabi tutulur. Bu önemli adım, metal parçacıklarını birbirine kaynaştırarak nihai bileşen için istenen mukavemet ve yoğunluğu elde eder.
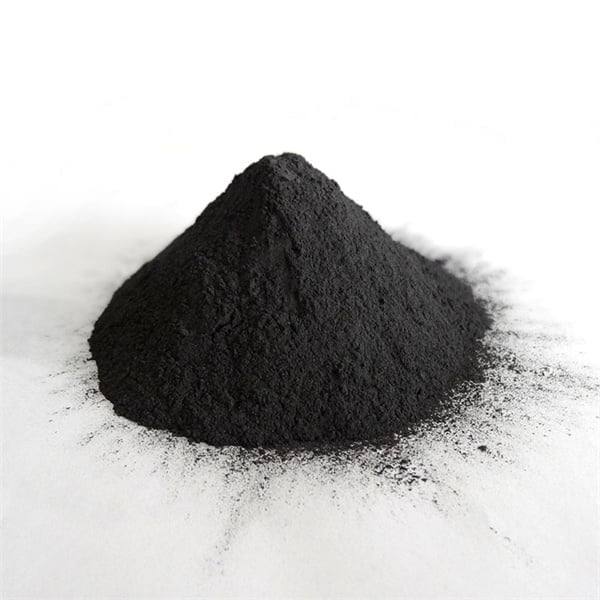
Avantajları Metal Enjeksiyon Kalıplama (MIM)
MIM, çeşitli endüstriler için oldukça rağbet gören bir süreç olmasını sağlayan bir dizi cazip avantaj sunmaktadır:
- Karmaşık Geometriler: Karmaşık şekillerle mücadele edebilen geleneksel işleme tekniklerinin aksine, MIM karmaşık özelliklere, dar toleranslara ve ince duvarlara sahip bileşenler üretmede mükemmeldir. Bu, daha önce geleneksel yöntemlerle elde edilmesi zor veya imkansız olan yenilikçi tasarımlar için kapıları açar.
- Yüksek Hassasiyet ve Tekrarlanabilirlik: MIM, enjeksiyon kalıplamanın hassasiyetinden yararlanarak minimum boyutsal varyasyonlara sahip son derece tutarlı parçalar ortaya çıkarır. Bu da güvenilir performans ve daha az işlem sonrası ihtiyaç anlamına gelir.
- Seri Üretim: MIM, yüksek hacimli üretim çalışmaları için çok uygun bir süreçtir. Kalıp kurulduktan sonra, MIM çok sayıda aynı parçayı verimli bir şekilde üretebilir, bu da onu tutarlı kalite ve büyük miktarlar gerektiren uygulamalar için ideal hale getirir.
- Malzeme Çok Yönlülüğü: MIM, yaygın paslanmaz çelikler ve takım çeliklerinden titanyum ve inconel gibi egzotik seçeneklere kadar geniş bir uyumlu malzeme yelpazesine sahiptir. Bu, uygulamanın özel mukavemetine, korozyon direncine veya diğer performans gereksinimlerine göre en uygun malzemenin seçilmesine olanak tanır.
- Maliyet-Etkinlik: Geleneksel işleme teknikleriyle karşılaştırıldığında, özellikle karmaşık geometriler için, MIM önemli maliyet tasarrufları sağlayabilir. Nete yakın şekil kabiliyeti malzeme israfını en aza indirir ve kapsamlı işleme operasyonlarına olan ihtiyacı azaltır.
Metal Enjeksiyon Kalıplama (MIM) Uygulamaları
MIM'in çeşitli avantajları, onu geniş bir endüstri yelpazesinde popüler bir seçim haline getirmiştir. İşte öne çıkan bazı örnekler:
- Otomotiv: MIM, dayanıklılıkları ve boyutsal doğruluklarıyla bilinen dişliler, zincir dişlileri, valf bileşenleri ve yakıt sistemi parçaları gibi karmaşık bileşenleri üreterek otomotiv endüstrisinde parlıyor.
- Tıbbi Cihazlar: Bazı MIM malzemelerinin biyouyumlu yapısı, onu tıbbi uygulamalar için mükemmel hale getirir. MIM, çeşitli tıbbi cihazlar için karmaşık cerrahi aletler, implantlar ve bileşenler oluşturmak için kullanılır.
- Tüketici Elektroniği: Küçük, karmaşık parçaların yüksek hassasiyetle üretilebilmesi MIM'i tüketici elektroniği endüstrisi için ideal kılmaktadır. MIM, çeşitli elektronik cihazlar için konektörler, muhafazalar ve dahili bileşenlerde uygulama alanı bulmaktadır.
- Havacılık ve Savunma: Havacılık ve savunma sektörlerinin zorlu gereksinimleri MIM için çok uygundur. MIM, uçaklar, uzay araçları ve silah sistemleri için yüksek mukavemetli, hafif bileşenler üretir.
Faydaların Ötesinde: MIM için Dikkat Edilmesi Gerekenler
MIM çok sayıda avantaj sunsa da, özel uygulamanız için seçmeden önce bazı faktörleri göz önünde bulundurmanız önemlidir:
- Parça Boyutu Sınırlamaları: MIM şu anda üretebileceği maksimum parça boyutu konusunda sınırlamalara sahiptir. Belirli bir hacmi aşan parçalar geleneksel metal işleme teknikleri için daha uygun olabilir.
- Maddi Sınırlamalar: MIM geniş bir malzeme yelpazesi sunsa da, bazı egzotik veya özel alaşımlar MIM aracılığıyla kolayca bulunamayabilir veya uygun maliyetli olmayabilir.
- Geliştirme Maliyetleri: Yeni bir bileşen için MIM sürecinin kurulması, kalıp geliştirme ve süreç optimizasyonu için ön yatırım gerektirir. Bu maliyet faktörünün, potansiyel üretim hacmi ve uzun vadeli faydalar karşısında tartılması gerekir.
MIM'i Anlamak: Teknik Bir Derin Dalış
MIM'in teknik incelikleriyle ilgilenenler için bazı temel hususlara daha yakından bir bakış:
Hammadde Seçimi: Başarılı bir MIM için doğru hammaddenin seçimi çok önemlidir. İşte dikkate alınması gereken bazı önemli hususlar:
- Metal Tozu:
- Partikül Boyutu ve Dağılımı: Metal tozunun boyutu ve dağılımı nihai parça özelliklerini önemli ölçüde etkiler. Daha ince tozlar genellikle daha sıkı toleranslar ve daha pürüzsüz yüzeyler sağlar, ancak akışkanlık sorunları nedeniyle işlenmeleri de daha zor olabilir. İyi dengelenmiş bir partikül boyutu dağılımı genellikle tercih edilir.
- Toz Morfolojisi: Metal parçacıkların şekli de bir rol oynar. Küresel tozlar daha iyi akma ve daha yoğun bir şekilde toplanma eğilimindedir, bu da daha iyi mukavemet ve boyutsal doğruluk sağlar.
- Cilt Sistemi: Bağlayıcı sistem geçici bir yapıştırıcı görevi görerek metal tozunu kalıplama ve bağlama sırasında bir arada tutar. Farklı bağlayıcı sistemleri, termal stabilite, bağlayıcı çözme davranışı ve seçilen bağlayıcı çözme işlemiyle uyumluluk gibi farklı özellikler sunar.
MIM için Kalıp Tasarımı:
MIM kalıpları plastik enjeksiyon kalıpları ile benzerlikler gösterir ancak metal tozu davranışı için özel hususlar gerektirir:
- Kapı Tasarımı: Hammaddenin kalıp boşluğuna giriş noktaları olan kapıların tasarımının uygun akışı sağlaması ve kusurlara yol açabilecek türbülansı en aza indirmesi gerekir.
- Havalandırma: Havalandırma kanalları, enjeksiyon sırasında sıkışan havanın dışarı çıkmasına izin vermek, boşlukları önlemek ve parçanın tamamen dolmasını sağlamak için çok önemlidir.
- Taslak Açıları: Kalıp duvarlarındaki çekim açıları, soğuduktan sonra kalıplanmış parçanın kolayca çıkarılmasını kolaylaştırmak için gereklidir.
MIM'de Bağ Çözme Teknikleri:
Daha önce de belirtildiği gibi, bağlayıcıyı kalıplanmış parçadan çıkarmak için kritik bir adımdır. İşte iki temel bağlayıcı çözme tekniğinin bir dökümü:
- Termal Debinding: Bu yöntem, kalıplanan parçanın kontrollü bir atmosferde kademeli olarak ısıtılmasını içerir. Sıcaklık yükseldikçe bağlayıcı bozunur ve ayrışarak metal toz yapısını geride bırakır. Hassas metal yapıya zarar vermeden bağlayıcının tamamen çıkarılmasını sağlamak için ısıtma profilinin dikkatlice tasarlanması gerekir.
- Çözücü Bağ Çözme: Bu teknikte bağlayıcı sistemi seçici olarak çözen bir çözücü kullanılır. Kalıplanmış parça çözücüye batırılır ve metal tozu bozulmadan kalırken bağlayıcının süzülmesine izin verilir. Solventle çözme işlemi termal çözme işleminden daha hızlı olabilir ancak kullanılan solvent için özel işlem ve bertaraf hususları gerektirebilir.
MIM'de sinterleme:
Sinterleme, MIM sürecinin son aşamasıdır ve burada tozdan arındırılmış metal tozu katı, işlevsel bir bileşene dönüşür. Sinterleme sırasında parça kontrollü bir atmosferde yüksek sıcaklıklara (tipik olarak metalin erime noktasının 1/2 ila 2/3 aralığında) maruz bırakılır. Bu yüksek sıcaklık, metal parçacıkları arasında difüzyon bağını teşvik ederek yoğunlaşma ve mukavemet ile diğer mekanik özelliklerde önemli iyileşme sağlar.
MIM'de Kalite Kontrol:
MIM üretiminde tutarlı kaliteyi korumak çok önemlidir. İşte bazı temel kalite kontrol önlemleri:
- Hammadde Karakterizasyonu: Metal tozu boyutu dağılımı ve bağlayıcı içeriği gibi hammadde özelliklerinin düzenli olarak test edilmesi, işleme sırasında tutarlı malzeme davranışı sağlar.
- Boyutsal Muayene: Kalıplanan parçaların boyutları, tasarım özelliklerini karşıladıklarından ve sıkı toleransları koruduklarından emin olmak için titizlikle incelenir.
- Yoğunluk Ölçümü: Sinterlenmiş parçaların yoğunluğu, mukavemet ve performanslarının kritik bir göstergesidir. Yoğunluğu ölçmek için Arşimet prensibi veya piknometri gibi çeşitli teknikler kullanılabilir.
- Mikroyapı Analizi: Sinterlenmiş parçanın mikroyapısının mikroskobik incelemesi, tane boyutu, gözeneklilik ve potansiyel kusurlar hakkında bilgi verir.
Geleceği Metal Enjeksiyon Kalıplama
MIM, devam eden araştırma ve geliştirme çalışmaları ile sürekli gelişen bir teknolojidir:
- Genişleyen Malzeme Yelpazesi: MIM ile uyumlu yeni malzemelerin ve bağlayıcı sistemlerinin keşfedilmesi, bu çok yönlü proses için uygulama olanaklarını genişletmektedir.
- Geliştirilmiş Süreç Verimliliği: Araştırma, döngü sürelerini kısaltmak ve genel üretim verimliliğini arttırmak için debinding ve sinterleme aşamalarını optimize etmeyi amaçlamaktadır.
- Gelişmiş Parça Karmaşıklığı: Kalıp tasarımı ve malzeme bilimindeki gelişmeler, MIM aracılığıyla ulaşılabilir parça karmaşıklığının sınırlarını zorluyor.
Metal Enjeksiyon Kalıplama çok çeşitli endüstriler için tasarım özgürlüğü, malzeme çeşitliliği ve maliyet etkinliğinin benzersiz bir karışımını sunar. Teknoloji olgunlaşmaya devam ettikçe, MIM'in heyecan verici dünyasında daha da yenilikçi uygulamalar ve ilerlemeler bekleyebiliriz.
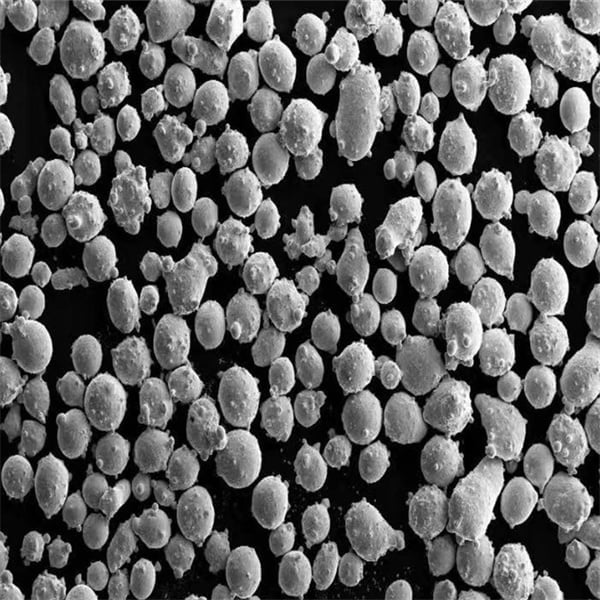
SSS
Tablo 1. Metal Enjeksiyon Kalıplama Metal Enjeksiyon Kalıplama (MIM) Hakkında Sıkça Sorulan Sorular
Soru | Cevap |
---|---|
MIM parçaları için tipik boyut sınırlamaları nelerdir? | MIM parçalarının maksimum boyutu genellikle birkaç inç küp ile sınırlıdır. Bu sınırlama, hammadde akışındaki zorluklardan ve daha büyük parçalarda homojen debileme sağlanmasından kaynaklanmaktadır. |
MIM prototipleme için kullanılabilir mi? | Evet, MIM, özellikle nihai tasarıma yüksek derecede doğruluk ve sadakat gerektiğinde, karmaşık metal parçaların prototipini oluşturmak için uygun bir seçenek olabilir. Ancak, kalıp geliştirmenin ön maliyetinin göz önünde bulundurulması gerekir. |
Geleneksel işlemeye kıyasla MIM'in avantajları nelerdir? | MIM, geleneksel işlemeye göre aşağıdakiler de dahil olmak üzere çeşitli avantajlar sunar: Karmaşık geometrileri dar toleranslarla üretme becerisi Karmaşık özellikler için daha fazla tasarım özgürlüğü Tutarlı parçalar için yüksek hassasiyet ve tekrarlanabilirlik Büyük miktarlar için seri üretim verimliliği Eksiltici tekniklere kıyasla daha az malzeme israfı |
Geleneksel işlemeye kıyasla MIM'in dezavantajları nelerdir? | MIM ile ilgili dikkate alınması gereken bazı sınırlamalar da vardır: Döküm veya dövme gibi tekniklere kıyasla parça boyutu sınırlamaları Belirli egzotik veya özel alaşımlar için malzeme sınırlamaları Kalıp geliştirme nedeniyle daha yüksek ön maliyetler Yüzey kalitesi, parlatma veya taşlama yoluyla elde edilebilecek son derece pürüzsüz yüzeylerle eşleşmeyebilir |
MIM ve geleneksel metal işleme arasında seçim yaparken göz önünde bulundurulması gereken bazı faktörler nelerdir? | İdeal seçim, özel uygulamanıza bağlıdır. İşte tartmanız gereken bazı temel faktörler: Parça geometrisi karmaşıklığı Üretim hacmi gereksinimleri Malzeme seçim ihtiyaçları Ön yatırım ve potansiyel tasarruflar dahil maliyet değerlendirmeleri Yüzey bitirme gereksinimleri |
MIM teknolojisinde gelecekteki bazı eğilimler nelerdir? | MIM'deki araştırma ve geliştirme çabaları, malzeme yelpazesini genişletmeye, daha hızlı döngü süreleri için süreç verimliliğini artırmaya ve ulaşılabilir parça karmaşıklığının sınırlarını zorlamaya odaklanmıştır. |
MIM'in bazı tipik uygulamaları nelerdir? | MIM, aşağıdakiler de dahil olmak üzere çok çeşitli sektörlerde uygulama alanı bulmaktadır: Otomotiv (dişliler, zincir dişlileri, valf bileşenleri) Tıbbi cihazlar (cerrahi aletler, implantlar) Tüketici elektroniği (konektörler, muhafazalar) Havacılık ve Savunma (yüksek mukavemetli, hafif bileşenler) |
MIM'de kullanılan farklı hammadde türleri nelerdir? | MIM hammaddesi tipik olarak polimerik bir bağlayıcı sistemle karıştırılmış bir metal tozundan (örneğin paslanmaz çelik, çelik alaşımları, titanyum) oluşur. Spesifik metal tozu ve bağlayıcı türü, parçanın istenen nihai özelliklerine bağlı olacaktır. |
MIM'de kullanılan farklı bağ çözme teknikleri nelerdir? | Başlıca iki bağ çözme tekniği vardır: Termal debinding: Bağlayıcıyı çıkarmak için kademeli ısıtma. Solventle bağlayıcı çözme: Bağlayıcıyı seçici olarak çözmek için bir çözücü kullanılması. |
Doğru Süreci Seçmek: MIM vs Geleneksel Metal İşleme
MIM ve geleneksel metal işleme teknikleri arasındaki karar, uygulamanıza özgü çeşitli faktörlere bağlıdır. İşte seçiminize rehberlik edecek bazı temel hususlar:
- Parça Geometrisi: Bileşeniniz karmaşık özelliklere, dar toleranslara ve karmaşık ayrıntılara sahipse, MIM önemli bir avantaj sunar.
- Üretim Hacmi: Yüksek hacimli üretim çalışmaları için MIM'in verimliliği ve tekrarlanabilirliği onu cazip bir seçenek haline getirmektedir.
- Malzeme Seçimi: İhtiyacınız olan malzemenin MIM ile uyumlu olduğundan emin olun. MIM'de kolayca bulunmayan egzotik bir alaşıma ihtiyacınız varsa, geleneksel metal işleme yöntemi tercih edilebilir.
- Maliyet Değerlendirmeleri: Karmaşık parçalar için geleneksel tekniklerin potansiyel malzeme israfı ve daha uzun üretim sürelerine karşı MIM için kalıp geliştirmenin ön maliyetlerini hesaba katın.
- Yüzey İşlem Gereksinimleri: Kusursuz bir yüzey kalitesi çok önemliyse, cilalama gibi geleneksel teknikler gerekli olabilir.
Sonuç
Metal Enjeksiyon Kalıplama (MIM), geniş bir uygulama yelpazesi için tasarım özgürlüğü, malzeme seçenekleri ve maliyet etkinliğinin benzersiz bir kombinasyonunu sunan güçlü ve çok yönlü bir üretim süreci olarak öne çıkmaktadır. Avantajlarını, sınırlamalarını ve geleneksel metal işleme teknikleriyle karşılaştırmasını anlayarak, özel ihtiyaçlarınız için MIM'den yararlanmak üzere bilinçli kararlar verebilir ve yenilikçi ve yüksek performanslı metal bileşenlerin potansiyelini ortaya çıkarabilirsiniz.
Paylaş
MET3DP Technology Co, LTD, merkezi Qingdao, Çin'de bulunan lider bir katmanlı üretim çözümleri sağlayıcısıdır. Şirketimiz, endüstriyel uygulamalar için 3D baskı ekipmanları ve yüksek performanslı metal tozları konusunda uzmanlaşmıştır.
İşletmeniz için en iyi fiyatı ve özelleştirilmiş Çözümü almak için sorgulayın!
İlgili Makaleler
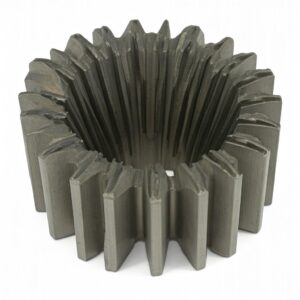
Yüksek Performanslı Nozul Kanat Segmentleri: Metal 3D Baskı ile Türbin Verimliliğinde Devrim
Daha Fazla Oku "Met3DP Hakkında
Son Güncelleme
Bizim Ürünümüz
BİZE ULAŞIN
Herhangi bir sorunuz var mı? Bize şimdi mesaj gönderin! Mesajınızı aldıktan sonra tüm ekibimizle talebinize hizmet edeceğiz.
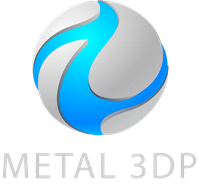
3D Baskı ve Katmanlı Üretim için Metal Tozları