MIM Teknolojisinin işlem adımları
İçindekiler
Hiç küçük bir dişliyi ya da karmaşık bir saat parçasını elinize alıp karmaşık detaylarına hayran kaldınız mı? Muhtemelen bu karmaşık metal parçası Metal Enjeksiyon Kalıplama (MIM). MIM sadece minyatür harikalar yaratmakla ilgili değildir; olağanüstü hassasiyet ve tekrarlanabilirlikle karmaşık, ağa yakın şekilli metal parçalar üretmek için güçlü bir tekniktir.
Peki MIM ince metal tozunu karmaşık metal bileşenlere tam olarak nasıl dönüştürüyor? Kemerlerinizi bağlayın, çünkü MIM teknolojisinin büyüleyici dünyasına doğru bir yolculuğa çıkmak, dört ana adımını incelemek ve bu süreci besleyen metal tozları dünyasını keşfetmek üzereyiz.
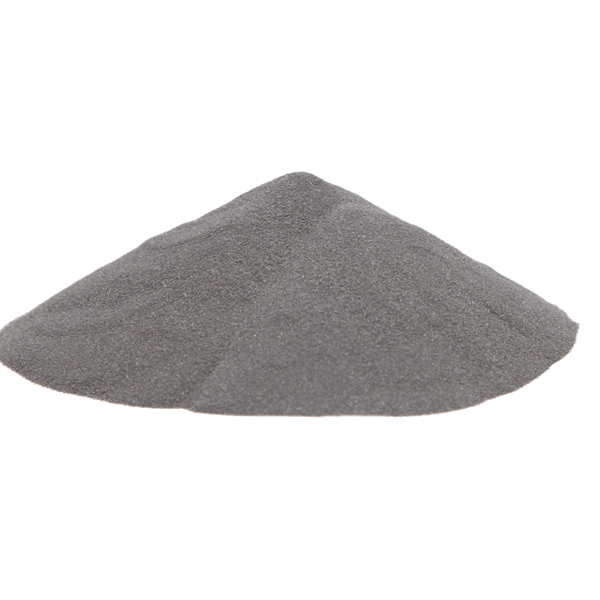
Dört Ana Adım MIM Teknoloji
MIM, iyi prova edilmiş bir oyun gibi, dört farklı perdede ortaya çıkıyor:
- Bileşik: Yetenekli bir fırıncının mükemmel bir hamur oluşturmak için un, şeker ve diğer malzemeleri titizlikle karıştırdığını düşünün. Benzer şekilde, MIM'de birleştirme işlemi metal tozunun özel bir bağlayıcı sistemle karıştırılmasını içerir. Tipik olarak termoplastikler ve mumlardan oluşan bu bağlayıcılar, kalıplama işlemi sırasında metal parçacıkları bir arada tutan tutkal gibi davranır.
Metal Toz Çılgınlığı:
MIM'in kalbi, kullanılan metal tozlarının çeşitliliğinde yatmaktadır. İşte en popüler metal tozlarından bazılarına ve benzersiz özelliklerine bir bakış:
Metal Tozu | Kompozisyon | Özellikler | Uygulamalar |
---|---|---|---|
316L Paslanmaz Çelik | Fe (Demir), Cr (Krom), Ni (Nikel), Mo (Molibden) | Mükemmel korozyon direnci, iyi mukavemet ve süneklik | Tıbbi cihazlar, havacılık ve uzay bileşenleri, otomotiv parçaları |
17-4 PH Paslanmaz Çelik | Fe (Demir), Cr (Krom), Ni (Nikel), Cu (Bakır) | Yüksek mukavemet, iyi süneklik, yaşla sertleştirilebilir | Dişliler, bağlantı elemanları, valfler, pompa bileşenleri |
Karbon Çelik | Kontrollü miktarda Karbon (C) içeren Fe (Demir) | Yüksek mukavemet, düşük maliyet, iyi işlenebilirlik | Rulmanlar, dişliler, kollar, yapısal bileşenler |
Nikel | Ni (Nikel) | Mükemmel korozyon direnci, yüksek termal ve elektriksel iletkenlik | Elektronik bileşenler, ısı eşanjörleri, kimyasal işleme ekipmanları |
Bakır | Cu (Bakır) | Yüksek elektrik ve ısı iletkenliği, iyi süneklik | Elektrik konnektörleri, ısı alıcıları, sert lehim malzemeleri |
Titanyum | Ti (Titanyum) | Yüksek mukavemet/ağırlık oranı, mükemmel korozyon direnci | Havacılık ve uzay bileşenleri, tıbbi implantlar, spor malzemeleri |
Inconel 625 | Ni (Nikel), Cr (Krom), Mo (Molibden) | Olağanüstü yüksek sıcaklık dayanımı ve oksidasyon direnci | Gaz türbini bileşenleri, roket motoru parçaları, ısı eşanjörleri |
Kovar | Fe (Demir), Ni (Nikel), Co (Kobalt) | Cam ve seramik ile mükemmel termal genleşme uyumu | Elektronik ambalajlar, optoelektronik cihazlar, vakum contaları |
Tungsten | W (Tungsten) | Çok yüksek erime noktası, mükemmel aşınma direnci | Kesme aletleri, elektrotlar, ısı kalkanları |
Molibden | Mo (Molibden) | Yüksek erime noktası, iyi termal iletkenlik | Fırın bileşenleri, elektrik kontakları, ısıtma elemanları |
Doğru metal tozunun seçimi, nihai parçanın mukavemet, korozyon direnci ve termal iletkenlik gibi istenen özelliklerine bağlıdır.
- Kalıplama: Şimdi, fırıncının istenen şekli oluşturmak için hazırlanan hamuru bir kalıba döktüğünü hayal edin. MIM'de, birleştirilmiş hammadde (metal tozu ve bağlayıcı karışımı) yüksek basınç altında hassas bir şekilde tasarlanmış çelik bir kalıba enjekte edilir. Bu enjeksiyon kalıplama işlemi, kalıp boşluğunun karmaşık ayrıntılarını, sonraki işlemlerden önce yeni oluşturulan bileşen için teknik terim olan yeşil parça üzerine kopyalar.
- Debinding: Fırıncının keki kalıptan dikkatlice çıkardığını ve geride güzel bir eser bıraktığını hayal edin. MIM'de bağlayıcı çözme, bağlayıcının yeşil kısımdan kademeli olarak çıkarıldığı kontrollü bir süreçtir. Bu, termal veya solvent bazlı tekniklerle gerçekleştirilebilir. Bağlayıcının uzaklaştırılması, metal parçacıkların birbirine yaklaşmasını sağlayarak son aşamanın yolunu açtığı için çok önemlidir.
- Sinterleme: MIM oyununun son perdesi pastayı pişirmek gibidir. Sinterleme, kabuğu soyulmuş parçanın kontrollü bir atmosferde metal tozunun erime noktasına yakın ancak bunun altında bir sıcaklığa kadar ısıtılmasını içerir. Bu yüksek sıcaklık, metal parçacıklar arasında tane büyümesini ve bağlanmayı teşvik ederek mükemmel mekanik özelliklere sahip, ağa yakın şekilli, yüksek yoğunluklu bir metal bileşen elde edilmesini sağlar.
Avantajları MIM Teknoloji
MIM, onu oldukça rağbet gören bir üretim tekniği haline getiren bir dizi cazip avantaj sunmaktadır:
- Karmaşık Geometriler: Geleneksel işlemenin aksine MIM, dar toleranslara sahip karmaşık şekiller üretmede mükemmeldir.
- Nete Yakın Şekilde Üretim: MIM, geleneksel işlemeye kıyasla kapsamlı işlem sonrası adımlara olan ihtiyacı en aza indirir. Parçalar sinterleme işleminden nihai boyutlarına yakın bir şekilde çıkarak malzeme israfını ve üretim süresini azaltır.
- Yüksek Hassasiyet ve Tekrarlanabilirlik: MIM, boyutsal doğruluk ve parçadan parçaya tutarlılık üzerinde olağanüstü kontrol sunar. Bu, özellikle büyük miktarlarda özdeş bileşenler gerektiren uygulamalar için faydalıdır.
- Malzeme Çok Yönlülüğü: Daha önce de incelediğimiz gibi, MIM çok çeşitli metal tozlarıyla uyumluluğa sahiptir ve özel ihtiyaçlara uygun farklı özelliklere sahip parçaların oluşturulmasını sağlar.
- Maliyet-Etkinlik: Karmaşık, yüksek hacimli üretim çalışmaları için MIM, geleneksel işlemeye göre uygun maliyetli bir alternatif olabilir. Azaltılmış malzeme israfı ve minimum işlem sonrası süreç, ekonomik uygulanabilirliğine katkıda bulunur.
- Tasarım Özgürlüğü: MIM, geleneksel tekniklerle elde edilmesi zor veya imkansız olabilecek yenilikçi tasarımlara kapı açar. Bu tasarım özgürlüğü, mühendisleri ürün işlevselliğinin sınırlarını zorlama konusunda güçlendirir.
MIM Teknolojisinin Dezavantajları
MIM güçlü bir teknoloji olsa da sınırlamaları da yok değil:
- Yüksek İlk Yatırım: Bir MIM üretim hattı kurmak, ekipman ve takım için önemli ön maliyetler gerektirir. Bu, daha küçük şirketler veya sınırlı üretim hacmine sahip olanlar için bir engel olabilir.
- Parça Boyutu Sınırlamaları: MIM parçalarının boyutu, enjeksiyon kalıplama sürecindeki sınırlamalar ve debinding ve sinterleme sırasındaki potansiyel zorluklar nedeniyle genellikle kısıtlıdır.
- Yüzey İşlemi: MIM parçaları, talaşlı imalat veya diğer tekniklerle üretilenlerle aynı yüzey kalitesi seviyesine ulaşamayabilir. Ancak, parlatma veya tamburlama gibi işlem sonrası teknikler yüzey estetiğini iyileştirebilir.
- Tasarım Hususları: MIM parçalarının tasarımında malzeme özellikleri, çekim açıları ve potansiyel hata ayıklama zorlukları gibi faktörlerin dikkate alınması gerekir. Tasarım aşamasında deneyimli MIM mühendislerine danışmak çok önemlidir.
MIM Teknolojisi Uygulamaları
MIM, karmaşık, yüksek hassasiyetli metal parçalar üretme kabiliyeti nedeniyle çok çeşitli sektörlerde uygulama alanı bulmaktadır. İşte öne çıkan bazı örnekler:
- Tıbbi Cihazlar: MIM, stentler, implantlar ve cerrahi aletler gibi karmaşık tıbbi bileşenlerin üretiminde yaygın olarak kullanılmaktadır. Belirli metal tozlarının biyouyumluluğu ve MIM'in yüksek hassasiyeti onu bu kritik uygulamalar için ideal kılmaktadır.
- Havacılık ve Savunma: Havacılık ve savunma endüstrileri, yüksek mukavemet-ağırlık oranları, mükemmel ısı direnci ve sıkı toleranslar gerektiren bileşenler için MIM'den yararlanır. Örnekler arasında jet motoru bileşenleri, füze parçaları ve ateşli silah bileşenleri yer almaktadır.
- Otomotiv: MIM, otomotiv endüstrisinde karmaşık dişlilerin, şanzıman parçalarının ve yakıt sistemi bileşenlerinin üretimi için giderek daha fazla kullanılmaktadır. MIM'in net şekle yakın kabiliyeti ve malzeme çok yönlülüğü, bu sektörde giderek daha fazla benimsenmesine katkıda bulunmaktadır.
- Elektronik: MIM, konektörler, muhafazalar ve ısı alıcıları gibi karmaşık özelliklere sahip minyatür elektronik bileşenlerin oluşturulmasında rol oynar. MIM ile elde edilebilen yüksek iletkenlik ve boyutsal doğruluk, onu bu uygulamalar için uygun hale getirir.
- Tüketim Malları: MIM, saat bileşenlerinden spor malzemelerine kadar çeşitli tüketici ürünlerinde kendine yer buluyor. İyi bir estetiğe sahip karmaşık şekiller üretme yeteneği, MIM'i belirli tüketim malları uygulamaları için cazip bir seçenek haline getirmektedir.
Seçim için Dikkat Edilmesi Gerekenler MIM
MIM güçlü bir teknolojidir, ancak herkese uyan tek bir çözüm değildir. MIM'in uygulamanız için doğru seçim olup olmadığına karar verirken göz önünde bulundurmanız gereken bazı temel faktörleri aşağıda bulabilirsiniz:
- Parça Karmaşıklığı: Tasarımınız karmaşık şekiller, ince duvarlar veya iç özellikler içeriyorsa, MIM mükemmel bir uyum olabilir.
- Üretim Hacmi: MIM, maliyet etkinliğinin parladığı yüksek hacimli üretim çalışmalarında öne çıkmaktadır.
- Malzeme Gereksinimleri: MIM ile uyumlu bir metal tozu seçerken mukavemet, korozyon direnci ve termal iletkenlik gibi istenen özellikleri göz önünde bulundurun.
- Parça Boyutu: Parça tasarımınızın MIM teknolojisinin boyut sınırlamaları içinde kaldığından emin olun.
- Bütçe: Aşağıdakilerle ilişkili ön yatırım maliyetleri MIM kurulumunun kararınıza dahil edilmesi gerekir.
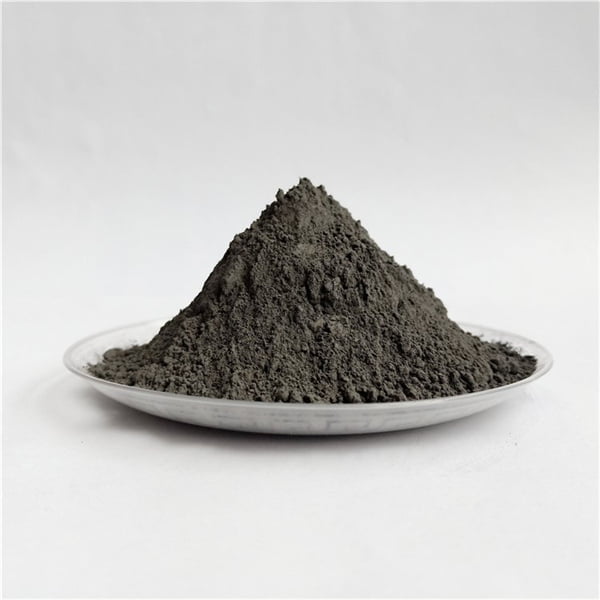
SSS
S: MIM ile geleneksel işleme arasındaki fark nedir?
C: Geleneksel işleme, istenen şekli oluşturmak için katı bir bloktan malzeme çıkarmayı içerir. MIM ise metal tozu ve bir bağlayıcı sistem kullanarak parçayı katman katman oluşturur. MIM karmaşık geometriler, net şekle yakın üretim ve yüksek hacimli üretim için avantajlar sunar.
S: MIM'de kullanılan farklı metal tozu türleri nelerdir?
C: Paslanmaz çelikler, karbon çelikleri, nikel, bakır, titanyum ve çeşitli alaşımlar dahil olmak üzere çok çeşitli metal tozları MIM ile uyumludur. Metal tozu seçimi, nihai parçanın istenen özelliklerine bağlıdır.
S: MIM parçalarının yüzey kalitesi sınırlamaları nelerdir?
C: MIM parçaları, işlenmiş bileşenlere kıyasla biraz daha pürüzlü bir yüzey kalitesine sahip olabilir. Ancak parlatma, tamburlama veya vibrofinishing gibi işlem sonrası teknikler yüzey estetiğini önemli ölçüde iyileştirebilir.
S: MIM çok malzemeli parçalar için kullanılabilir mi?
C: MIM tipik olarak tek malzemeli parçalarla sınırlıdır. Bununla birlikte, metal ve plastik elemanlar içeren hibrit bileşenler oluşturmak için metal ekleme kalıplama gibi teknikler kullanılabilir.
S: MIM'in çevresel hususları nelerdir?
C: MIM'deki bağ çözme işlemi, çevresel etkiyi en aza indirmek için uygun kullanım ve bertaraf gerektiren çözücüler içerebilir. Üreticiler, bu endişeyi gidermek için giderek daha fazla çevre dostu bağ çözme teknikleri benimsemektedir.
S: MIM teknolojisinin geleceği nedir?
C: MIM teknolojisi sürekli gelişiyor. Metal tozu geliştirme, kabuk soyma teknikleri ve sinterleme süreçlerindeki ilerlemeler MIM yeteneklerinin sınırlarını zorluyor. Gelecekte MIM kullanılarak daha da karmaşık ve yüksek performanslı parçaların üretilmesini bekleyebiliriz.
Sonuç
MIM teknolojisi, karmaşık, ağa yakın şekilli metal bileşenlerin üretimi için tasarım özgürlüğü, yüksek hassasiyet ve maliyet etkinliğinin benzersiz bir kombinasyonunu sunar. Artan çok yönlülüğü ve sürekli ilerlemeleriyle MIM, önümüzdeki yıllarda çeşitli sektörlerde daha da önemli bir rol oynamaya hazırlanıyor. İster tasarımcı, ister mühendis olun, ister yenilikçi üretim tekniklerini merak ediyor olun, MIM'in potansiyelini anlamak metal parça üretimi dünyasında heyecan verici olasılıklara kapı açabilir.
Paylaş
MET3DP Technology Co, LTD, merkezi Qingdao, Çin'de bulunan lider bir katmanlı üretim çözümleri sağlayıcısıdır. Şirketimiz, endüstriyel uygulamalar için 3D baskı ekipmanları ve yüksek performanslı metal tozları konusunda uzmanlaşmıştır.
İşletmeniz için en iyi fiyatı ve özelleştirilmiş Çözümü almak için sorgulayın!
İlgili Makaleler
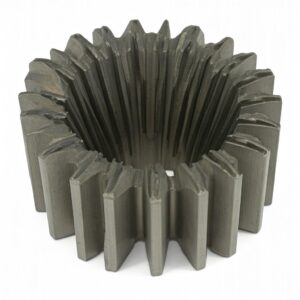
Yüksek Performanslı Nozul Kanat Segmentleri: Metal 3D Baskı ile Türbin Verimliliğinde Devrim
Daha Fazla Oku "Met3DP Hakkında
Son Güncelleme
Bizim Ürünümüz
BİZE ULAŞIN
Herhangi bir sorunuz var mı? Bize şimdi mesaj gönderin! Mesajınızı aldıktan sonra tüm ekibimizle talebinize hizmet edeceğiz.
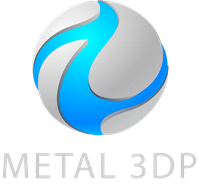
3D Baskı ve Katmanlı Üretim için Metal Tozları