MIM İmalatı: Eksiksiz Bir Kılavuz
İçindekiler
Genel Bakış MIM Üretim
Metal enjeksiyon kalıplama (MIM), yüksek hacimlerde küçük, karmaşık metal parçalar üretmek için kullanılan bir toz metalurjisi üretim sürecidir.
MIM'deki kilit adımlar şunları içerir:
- Bir hammadde oluşturmak için ince metalik tozun bağlayıcı ile karıştırılması
- Hammaddenin plastik enjeksiyon kalıplama kullanılarak bir kalıba enjekte edilmesi
- Sadece metal tozu bırakarak bağlayıcıyı çıkarmak için bağlayıcı çözme
- Tozu yoğunlaştırarak katı bir metal bileşene dönüştürmek için sinterleme
MIM, plastik enjeksiyon kalıplamanın tasarım esnekliğini işlenmiş metallerin gücü ve performansı ile birleştirir. Küçük parçaların karmaşık, yüksek hacimli üretimi için uygun maliyetli bir süreçtir.
MIM Üretimi Nasıl Çalışır?
MIM üretim süreci şunları içerir:
- İnce metal tozunun polimer bağlayıcılarla karıştırılması ve peletlenmesi yoluyla bir hammaddenin formüle edilmesi
- Hammaddenin ısıtılması ve istenen şekilde enjeksiyonla kalıplanması
- Bağlayıcıyı çözücü veya termal çözme yoluyla kimyasal olarak çıkarma
- Tamamen yoğun bir parça üretmek için ayrıştırılmış metal bileşenin bir fırında sinterlenmesi
- Talaşlı imalat, delme, kaplama gibi isteğe bağlı ikincil bitirme işlemleri
MIM, karmaşık geometrilere, sıkı toleranslara ve mükemmel mekanik özelliklere sahip bileşenlerin ekonomik olarak üretilmesine olanak tanır.
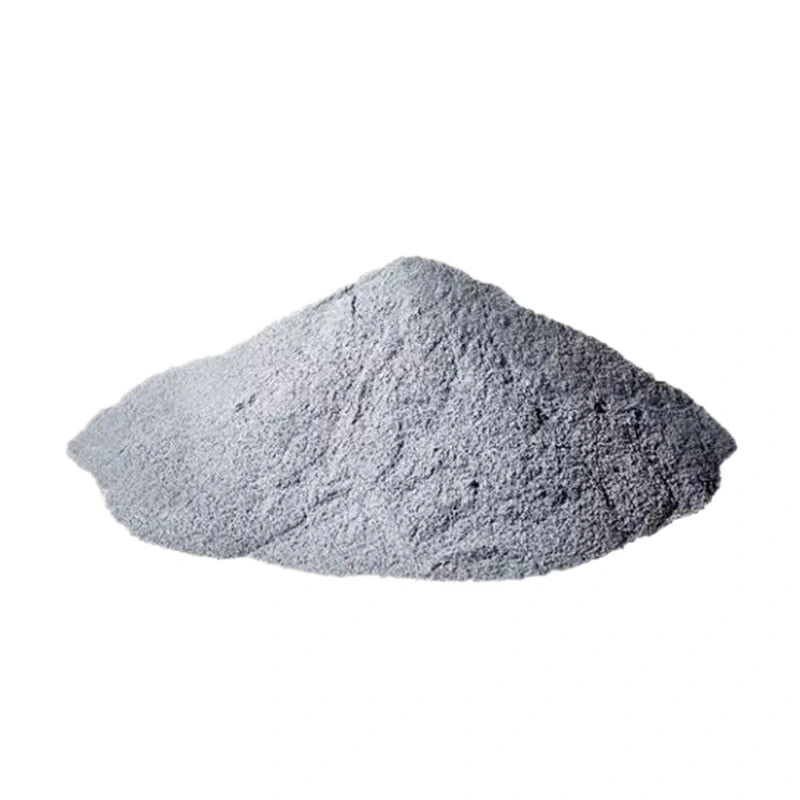
MIM'de Kullanılan Metal Türleri
MIM teknolojisi ile çok çeşitli metaller işlenebilir:
- Paslanmaz çelikler - 316L, 17-4PH, 410, 420
- Takım çelikleri - H13, P20, A2, D2
- Manyetik alaşımlar - Yumuşak ve sert ferritler
- Bakır alaşımları - Pirinç, bronz
- Düşük alaşımlı çelikler - 4100, 4600
- Süper alaşımlar - Inconel 625, 718
- Tungsten ağır alaşımları
- Titanyum alaşımları - Ti6Al4V, Ti6Al4V ELI
MIM genellikle yüksek yoğunluğa kadar sinterlenebilen herhangi bir malzeme için uygundur. Erime noktası 1000°C'nin altında olan metaller tercih edilir.
MIM Üretim Süreci Parametreleri
MIM'deki kritik süreç parametreleri şunları içerir:
Hammadde geliştirme:
- Toz morfolojisi, boyut dağılımı
- Bağlayıcı bileşimi
- Toz yüklemesi - tipik olarak 60-65 vol%
- Karıştırma işlemi - sıcaklık, zaman, atmosfer
Kalıplama:
- Kalıp malzemesi - P20 takım çeliği tercih edilir
- Enjeksiyon sıcaklığı, basıncı, hızı
- Kapı tasarımı
- Soğutma sistemi tasarımı
Debinding:
- Solvent, termal veya katalitik debinding
- Çözme sıcaklığı, zaman, atmosfer
Sinterleme:
- Sıcaklık profili - debinding, sinterleme adımları
- Isıtma hızı, sinterleme süresi, atmosfer
- Sinterleme sıcaklığı ve basıncı
MIM Tasarımı ve Parça Hususları
MIM süreci tasarım özgürlüğü sağlar, ancak bazı kurallara uyulması gerekir:
- Duvar kalınlığı: 0,3 - 4 mm aralığı mümkündür
- Yüzey kalitesi: As-sinterlenmiş Ra 1,5 μm civarındadır
- Boyutsal toleranslar: ±0,5% standarttır ancak ±0,1% elde edilebilir
- Sıkışmış tozu önleme: Tamamen kapalı iç boşluklar yok
- Çekim açıları: > 1°'den fazla çekim açısı tercih edilir
- Sinterleme büzülmesi: Yaklaşık 20% hacimsel büzülme
- Kusurların azaltılması: Geniş köşe yarıçapları çatlakları en aza indirir
Gelişmiş simülasyon araçları, deneme ve hatayı azaltmak için tasarım sırasında MIM sürecinin sanal optimizasyonuna olanak tanır.
Faydaları MIM Üretim
MIM kullanmanın temel avantajları şunlardır:
- Karmaşık geometriler ve dar toleranslar
- Mükemmel mekanik özellikler
- Geniş malzeme seçenekleri
- Düşük maliyetle yüksek üretim miktarları
- Atıkları en aza indirir - net şekle yakın süreç
- Azaltılmış işleme ve finisaj
- Bileşen entegrasyonu ve parça konsolidasyonu
- Işıklar kapalıyken çalışmaya uygun otomatik süreç
- Talaşlı imalattan daha çevre dostu
- Prototiplerden tam üretime kadar ölçeklenebilir
Bu avantajlar, MIM'i sektörler arasında yüksek hacimlerde hassas metal bileşenlerin uygun maliyetli bir şekilde üretilmesi için uygun hale getirmektedir.
MIM'in Sınırlamaları ve Zorlukları
MIM ile ilgili bazı sınırlamalar:
- Sınırlı boyut - tipik olarak parça başına <45 g bitmiş kütle
- Yüksek yoğunlukta sinterlenebilen metallerle sınırlıdır
- Hammadde formülasyonunda kapsamlı uzmanlık gereklidir
- Kalıp ve süreç geliştirme için ön maliyetler
- Çatlamaya eğilimli düz kesitler ve keskin köşeler
- Diğer süreçlere kıyasla daha uzun teslim süresi
- Nihai özelliklere ulaşmak için genellikle son işlem gerekir
- İplik gibi bazı özelliklerde tasarım özgürlüğü eksikliği
- Sinterlenmiş metallerde ikincil işleme zorlayıcı olabilir
Uygulamaya uygun hammadde ve proses tasarımı ile MIM teknolojisinin tüm potansiyelinden faydalanmak için bu zorlukların üstesinden gelinebilir.
MIM ile Üretilen Parçaların Uygulamaları
MIM aşağıdaki sektörlerde yaygın kullanım alanı bulmaktadır:
Otomotiv: Kilit donanımı, sensörler, yakıt sistemi ve motor bileşenleri
Havacılık ve Uzay: Çarklar, nozullar, valfler, bağlantı elemanları
Tıbbi: Diş implantları, neşter sapları, ortopedik aletler
Ateşli Silahlar: Tetikler, şarjörler, sürgüler, çekiçler
Saatler: Kılıflar, bilezik halkaları, kopçalar ve tokalar
Elektrik: Güvenilirlik için konektörler ve kurşun çerçeveler
Tipik parça boyutları 0,1 gram ile 110 gram arasında değişmektedir ve en büyük ticari üretim hacimleri konektörler, bağlantı elemanları, cerrahi aletler ve ortodontik diş tellerindedir.
MIM Üretiminin Maliyet Analizi
MIM üretim maliyetleri şunları içerir:
- Hammadde geliştirme - Formülasyon, karıştırma, karakterizasyon
- Kalıp imalatı - Yüksek hassasiyetli kalıp işleme
- MIM makinesi - Büyük sermaye ekipmanı yatırımı
- Operasyon - İşçilik, kamu hizmetleri, sarf malzemeleri
- İkincil operasyonlar - Debinding, sinterleme, finisaj
- Malzeme kullanımı - Metal tozu toplam maliyetin yaklaşık 60%'sini oluşturmaktadır
- Sarf malzemesi takımları - Yüksek hacim sağlamak için çoklu kalıp boşlukları
- Üretim hacmi - Toplam hacim üzerinden amorti edilen kurulum maliyetleri
- Uçmak için satın alma oranı - Diğer PM süreçlerine kıyasla sadece 2-4 kat
- Tasarım optimizasyonu - Minimum işleme ile basit geometriler
Büyük üretim hacimleri için MIM, mükemmel malzeme kullanımı ve net şekle yakın özellikleriyle yüksek üretim oranlarında çok uygun maliyet sunar.
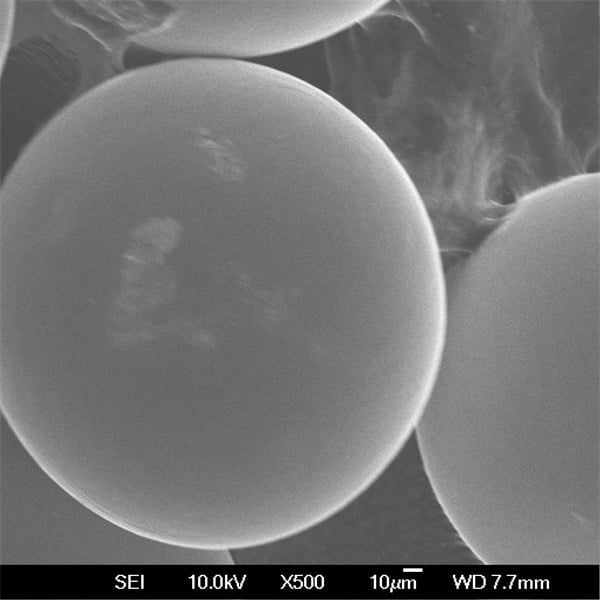
Bir seçim MIM Üretim Ortak
Bir MIM tedarikçisi seçerken temel faktörler:
- MIM ile kanıtlanmış uzmanlık ve yılların deneyimi
- Malzeme portföyü - paslanmaz çelik, takım çeliği, süper alaşım seçenekleri
- Kalite sertifikaları - ISO 9001, ISO 13485 tercihen
- İkincil işleme yetenekleri - işleme, ısıl işlem, yüzey bitirme
- Sıkı süreç ve ürün kalite kontrol prosedürleri
- Hammadde formülasyonu ve proses geliştirme için Ar-Ge yetenekleri
- Kalıp akış simülasyonu ve diğer tasarım analizi uzmanlığı
- Müşteri projelerini desteklemek için program yönetimi becerileri
- Üretim ihtiyaçları ile büyüyebilen ölçeklenebilir kapasite
- Çok yıllı anlaşmalarla rekabetçi fiyatlandırma
- Yakın işbirliği ve IP koruması sağlayan konum
Genel bir CNC metal işleme atölyesinin aksine, MIM'e odaklanan yerleşik bir MIM üreticisinin seçilmesi en iyi sonuçları sağlayacaktır.
MIM ve CNC İşlemenin Artıları ve Eksileri
MIM'in Avantajları:
- Mükemmel boyutsal doğruluk ve tekrarlanabilirlik
- Talaşlı imalatla elde edilemeyen karmaşık geometriler
- Minimum malzeme israfı ile net şekle yakın
- Çok yüksek üretim hacimlerine verimli bir şekilde ölçeklenir
- Otomatik süreç 7/24 çalışma sağlar
- Kurulumdan sonra daha kısa teslim süreleri
- Yüksek hacimlerde önemli ölçüde daha düşük parça maliyetleri
- Özellikler işlenmiş metallerle eşleşir veya aşar
MIM'in Dezavantajları:
- Hammadde ve kalıp için yüksek ilk kurulum maliyetleri
- Sınırlı boyut yetenekleri
- Bazı özelliklerde kısıtlı tasarım özgürlüğü
- Düşük başlangıç üretim miktarları verimsiz
- Hammadde formülasyonunda kapsamlı uzmanlık gereklidir
- İkincil bitirme işlemlerine hala ihtiyaç duyulabilir
- İlk prototipler için daha uzun teslim süreleri ve daha düşük kalite
Çok yüksek hacimlerde üretilen küçük ve karmaşık metal parçalar için MIM, zaman ve maliyet açısından en verimli üretim yöntemi haline gelmektedir.
MIM ve Metal 3D Baskı Arasındaki Karşılaştırma
MIM ile 3D baskı arasındaki temel farklar:
Parametre | MIM | 3D Baskı |
---|---|---|
Süreç | Bağlayıcı enjeksiyon kalıplama + sinterleme | Toz yatağı füzyonu veya bağlama |
Malzemeler | Geniş alaşım yelpazesi | Sınırlı malzeme seçenekleri |
Parça boyutu | < 45 gram | Birkaç kg'a kadar |
Doğruluk | Mükemmel, ±0,5% | Orta, ±1% |
Yüzey kaplaması | Çok iyi | Orta ila zayıf |
Üretim ölçeği | 10.000'lerden milyonlara | Orta hacimlere kadar prototipleme |
Parça başına maliyet | Çok düşük | Orta ila yüksek |
İkincil bitirme | Gerekli olabilir | Genellikle gerekli |
Teslim süresi | Süreç geliştirme için daha uzun | Daha hızlı prototipler ancak daha yavaş seri üretim |
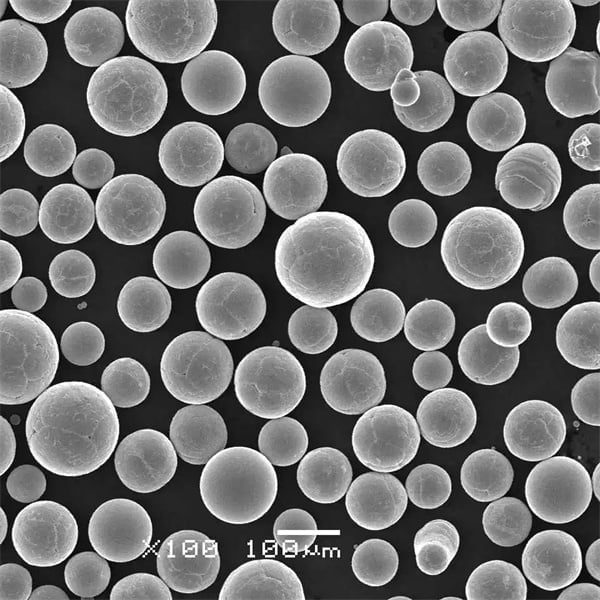
SSS
MIM üretimi için tipik tolerans kapasitesi nedir?
MIM, küçük hassas bileşenler için ±0,1% tolerans kapasitesine sahip gelişmiş süreçlerle ±0,5%'lik boyut toleranslarını güvenilir bir şekilde elde edebilir.
Yaygın MIM hammadde bileşimleri nelerdir?
Tipik MIM hammaddeleri, polipropilen, polietilen ve polistiren gibi polimerlerden oluşan 35-40% bağlayıcı ile 60-65% metal tozu yüklemesinden oluşur. Mumlar toz akışını iyileştirmeye yardımcı olur.
MIM birden fazla malzemeden parça üretebilir mi?
Evet, MIM her kalıp boşluğuna farklı hammaddeleri enjeksiyonla kalıplayarak veya farklı erime noktalarına sahip bağlayıcılar kullanarak kompozit ve dereceli yapılar üretebilir.
MIM ile hangi kalıplanmış parça boyutu elde edilebilir?
MIM kalıpları tipik olarak kütle olarak 45 gramdan küçük parçalarla ve 50 mm'den küçük boyutlarla sınırlıdır. Daha büyük veya daha ağır bileşenlerin yeterince doldurulması ve yoğunlaştırılması zorlaşır.
MIM, küçük metal bileşenler için basınçlı dökümle nasıl karşılaştırılır?
MIM daha yüksek boyutsal doğruluk ve malzeme mukavemeti sağlar, ancak basınçlı döküm daha hızlı döngü sürelerine sahiptir. MIM karmaşık geometriler için daha uygunken, basınçlı döküm daha basit formlar için tercih edilir.
Paylaş
MET3DP Technology Co, LTD, merkezi Qingdao, Çin'de bulunan lider bir katmanlı üretim çözümleri sağlayıcısıdır. Şirketimiz, endüstriyel uygulamalar için 3D baskı ekipmanları ve yüksek performanslı metal tozları konusunda uzmanlaşmıştır.
İşletmeniz için en iyi fiyatı ve özelleştirilmiş Çözümü almak için sorgulayın!
İlgili Makaleler
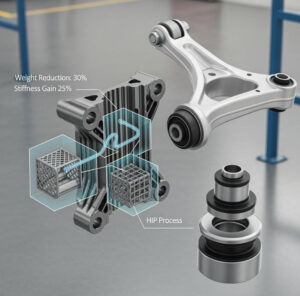
Metal 3D Printed Subframe Connection Mounts and Blocks for EV and Motorsport Chassis
Daha Fazla Oku "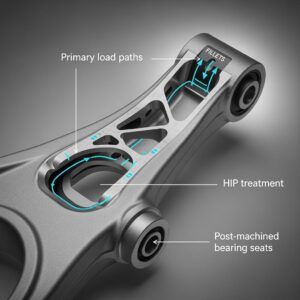
Metal 3D Printing for U.S. Automotive Lightweight Structural Brackets and Suspension Components
Daha Fazla Oku "Met3DP Hakkında
Son Güncelleme
Bizim Ürünümüz
BİZE ULAŞIN
Herhangi bir sorunuz var mı? Bize şimdi mesaj gönderin! Mesajınızı aldıktan sonra tüm ekibimizle talebinize hizmet edeceğiz.