Atomizasyon Sonrası Tedavi için Toz
İçindekiler
Bir heykeltıraşın bir mermer bloğundan titizlikle bir şaheser yarattığını düşünün. Ancak 3D baskı olarak da bilinen Katmanlı Üretim (AM) dünyasında hammadde o kadar yekpare değildir. Bunun yerine metal AM, nesneleri katman katman oluşturmak için küçük metalik parçacıkların - tozların - bir senfonisine dayanır.
Ancak hikaye bu metal tozlarının yaratılmasıyla bitmiyor. atomizasyon sonrası tedavi için toz bu metalik harikaların AM endüstrisinin titiz standartlarını karşılamasını sağlamada çok önemli bir rol oynamaktadır.
Bu makale, atomizasyon sonrası işleme yönelik tozların büyüleyici dünyasına girerek özelliklerini, uygulamalarını ve onları farklılaştıran faktörleri araştırıyor.
Atomizasyon Sonrası Tedavi için Tozlara Genel Bakış
Atomizasyon nedir? Bunu, erimiş metali ince bir parçacık sisine dönüştürme eylemi olarak düşünün. Gaz veya su atomizasyonu gibi çeşitli teknikler, sıvı metal akışını havada katılaşan küçük damlacıklar denizine ayırarak bunu başarır.
Ancak yolculuk burada bitmiyor. Ortaya çıkan metal tozu, görünüşte AM için hazır olsa da, bazı kusurlar barındırabilir. İşte burada atomizasyon sonrası işlem devreye giriyor. Bu özel prosesler toz özelliklerini rafine ederek Seçici Lazer Eritme (SLM) veya Elektron Işını Eritme (EBM) gibi AM tekniklerinin özel talepleri için optimize eder.
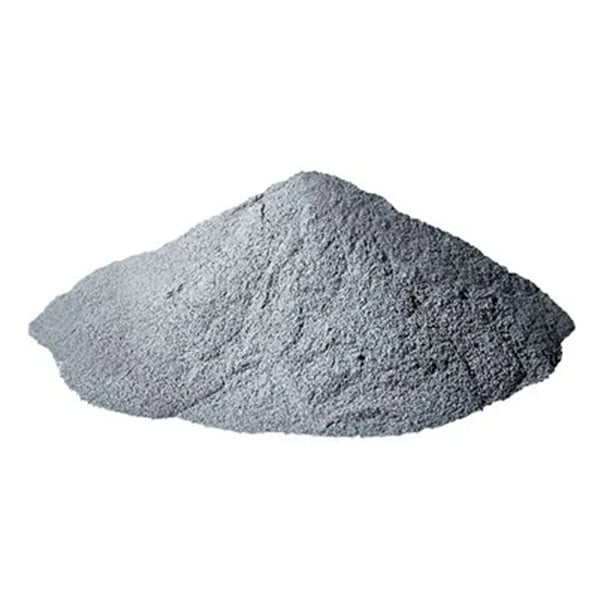
Atomizasyon Sonrası İşlem için Tozların Özellikleri
Bir fırıncının unu titizlikle elediğini ve mükemmel kek için partikül boyutunda tutarlılık sağladığını düşünün. Benzer şekilde, atomizasyon sonrası işlem için tozlar çeşitli özelliklerin kritik bir analizinden geçer:
- Partikül Boyutu ve Dağılımı: AM için tozlar sıkı bir şekilde kontrol edilen parçacık boyutu aralığı gerektirir. Çok büyük partiküller akışkanlığı engelleyebilir ve baskı sırasında düzensiz katman birikimine yol açabilir. Tersine, aşırı ince partiküller kullanımda zorluklara neden olabilir ve hatta AM işlemi sırasında lazer penetrasyonunu engelleyebilir.
- Parçacık Morfolojisi: Toz partiküllerinin şekli de hayati bir rol oynar. İdeal olarak, pürüzsüz yüzeylere sahip küresel partiküller en iyi akışkanlığı ve paketleme yoğunluğunu sunarak daha düzgün ve öngörülebilir bir yapı süreci sağlar.
- Kimyasal Bileşim: Tozun kimyasal yapısındaki en ufak değişiklikler bile basılan parçanın nihai özelliklerini önemli ölçüde etkileyebilir. Atomizasyon sonrası işlemler, oksit oluşumu veya istenmeyen elementlerin varlığı gibi sorunların giderilmesine yardımcı olabilir.
- Akışkanlık: Sorunsuz bir AM işlemi için tozun verimli bir şekilde akması şarttır. Akışkanlığı zayıf olan tozlar, besleme mekanizmalarında zorluklar yaratır ve katman yoğunluğunda tutarsızlıklara yol açabilir.
Atomizasyon sonrası işlemler, bu özellikleri optimize etmeye odaklanarak elde edilen tozun daha iyi olmasını sağlar:
- Tam olarak boyutlandırılmış ve dağıtılmıştır: Bunu, tutarlı pişirme sonuçları için mükemmel olan tek tip bir un yığınına sahip olmak gibi düşünün.
- Küresel şekilli: Yuvarlak, pürüzsüz mermerler hayal edin - sıkıca paketlemek ve kesintisiz akış sağlamak için idealdir.
- Kimyasal olarak saf: Tıpkı bir tarifi tam olarak takip etmek gibi, tozun da başarılı bir baskı için doğru malzemelere ihtiyacı vardır.
- Son derece akışkan: Kumun bir kum saatinden zahmetsizce aktığını hayal edin - optimum AM performansı için istenen akış karakteristiği budur.
Atomizasyon Sonrası İşlem için Toz Uygulamaları
Atomizasyon sonrası işleme yönelik tozlar, AM alanında çok çeşitli uygulamalara hitap eder. İşte bazı temel alanlar:
- Havacılık ve uzay: AM endüstrisi hafif, yüksek mukavemetli bileşenler yaratarak havacılıkta devrim yaratıyor. Hassas özelliklere sahip tozlar, güvenlik ve performansın çok önemli olduğu uçak ve uzay araçları için güvenilir parçalar oluşturmak için çok önemlidir.
- Tıbbi İmplantlar: Hastaya özel tıbbi implantlar AM sayesinde gerçeğe dönüşüyor. Burada, insan vücuduyla sorunsuz bir şekilde bütünleşen implantlar oluşturmak için olağanüstü saflığa sahip biyouyumlu tozlar gereklidir.
- Otomotiv: Otomotiv endüstrisi, hafif bileşenler ve karmaşık geometriler için AM'den giderek daha fazla yararlanıyor. Optimize edilmiş akışkanlığa sahip tozlar, otomotiv sektöründe seri üretim için hayati önem taşıyan tutarlı baskı sonuçları sağlar.
- Tüketim Malları: Özelleştirilmiş bisiklet parçalarından karmaşık mücevherlere kadar AM, tüketim malları alanına damgasını vuruyor. Estetik ve işlevsellik dengesine sahip tozlar, görsel olarak çekici ve dayanıklı tüketici ürünleri yaratmak için gereklidir.
Atomizasyon Sonrası Temel Arıtma Süreçleri
Atomizasyon sonrası çeşitli işlemler, AM için metal tozlarının özelliklerinin iyileştirilmesinde hayati bir rol oynamaktadır:
- Eleme ve Sınıflandırma: Unun elenmesine benzer şekilde, eleme toz partiküllerini farklı boyut aralıklarına ayırır. Bu, belirli AM uygulamaları için istenen partikül boyutu dağılımının elde edilmesine yardımcı olur.
- Gazdan arındırma: Metal tozları, atomizasyon işleminden kaynaklanan sıkışmış gazlar içerebilir. Vakumlu kurutma gibi gaz giderme teknikleri bu gazları gidererek nihai basılı parçada boşluklara veya gözenekliliğe neden olmalarını önler.
- Sferoidizasyon: Plazma atomizasyonu gibi bazı atomizasyon sonrası işlemler, doğal olarak daha küresel bir morfolojiye sahip tozlar üretebilir. Bununla birlikte, diğer tekniklerle üretilen tozlar için, döner atomizasyon veya kimyasal öğütme gibi ek işlemler küreselliklerini iyileştirmeye yardımcı olabilir.
- Yüzey Modifikasyonu: Toz partiküllerinin yüzey kimyasının uyarlanması, AM sürecindeki performanslarını artırabilir. Karbonitrürleme veya yağlayıcılarla kaplama gibi teknikler, baskı sırasında akışkanlığı ve lazer etkileşimini iyileştirebilir.
Doğru Seçimi Yapmak Atomizasyon Sonrası Tedavi:
En uygun atomizasyon sonrası tedavinin seçilmesi çeşitli faktörlere bağlıdır:
- Nihai tozun istenen özellikleri: Dar bir partikül boyutu dağılımı mı yoksa gelişmiş akışkanlık mı en önemli öncelik?
- Metal tozu türü: Farklı metaller, belirli atomizasyon sonrası tekniklere daha iyi yanıt verebilir.
- Amaçlanan AM uygulaması: Havacılık ve uzay bileşenlerinde kullanılan tozlar için gereklilikler, tüketim malları için olanlardan önemli ölçüde farklı olabilir.
İşte bazı yaygın atomizasyon sonrası tedavilerin avantaj ve dezavantajlarını özetleyen bir tablo:
Tedavi | Avantajlar | Dezavantajlar |
---|---|---|
Eleme ve Sınıflandırma | Hassas partikül boyutu dağılımı sağlar | Zaman alıcı olabilir ve malzeme kaybına yol açabilir |
Gazdan Arındırma | Gözenekliliği azaltır ve mekanik özellikleri iyileştirir | Özel ekipman gerektirebilir ve enerji yoğun olabilir |
Sferoidizasyon | Akışkanlığı ve paketleme yoğunluğunu artırır | Pahalı bir süreç olabilir ve bazı teknikler yüzey kirliliğine yol açabilir |
Yüzey Modifikasyonu | Akışkanlığı ve lazer etkileşimini geliştirir | Tozun kimyasal bileşimini değiştirebilir ve sıkı kontrol gerektirir |
Optimum toz özelliklerini elde etmek için bu işlemlerin genellikle birleştirildiğini unutmamak önemlidir. Örneğin, tam olarak boyutlandırılmış ve gazsız bir toz sağlamak için eleme, gaz giderme ile birlikte kullanılabilir.
İçin Tozların Karşılaştırılması Atomizasyon Sonrası Tedavi
Metal tozları, kökenlerine göre genel olarak iki türe ayrılabilir:
- Bakir Tozlar: Bu tozlar doğrudan birincil metal kaynaklarından üretilir ve AM uygulamaları için atomizasyon sonrası işleme tabi tutulur.
- Geri Dönüştürülmüş Tozlar: Sürdürülebilirlik konusuna giderek daha fazla odaklanılmasıyla birlikte, geri dönüştürülmüş metal tozları ilgi görmeye başlamıştır. Bu tozlar hurda metalden elde edilir ve AM kalite standartlarını karşılamak için atomizasyon sonrası işlemlere tabi tutulabilir.
Atomizasyon sonrası işlem için işlenmemiş ve geri dönüştürülmüş tozların bir karşılaştırması:
Parametre | Bakir Tozlar | Geri Dönüştürülmüş Tozlar |
---|---|---|
Kimyasal Bileşim | Genel olarak daha yüksek saflık ve tutarlılık | Kaynak malzemeden eser elementler veya safsızlıklar içerebilir |
Akışkanlık | Minimum elleçleme nedeniyle tipik olarak iyi akışkanlık | Akışkanlığı iyileştirmek için atomizasyon sonrası ek işlem gerektirebilir |
Maliyet | İşlenmemiş malzeme kaynağı nedeniyle genellikle daha pahalıdır | Daha uygun maliyetli bir seçenek olabilir |
Çevresel Etki | İşlenmemiş metal çıkarımı nedeniyle daha yüksek çevresel ayak izi | Malzemenin yeniden kullanımı sayesinde daha düşük çevresel etki |
İşlenmemiş ve geri dönüştürülmüş tozlar arasındaki seçim, özel uygulamaya ve maliyet, performans ve sürdürülebilirlik arasında istenen dengeye bağlıdır.
Tozların Geleceği için Atomizasyon Sonrası Tedavi
Atomizasyon sonrası tedavi için tozlar alanı sürekli gelişiyor. İşte izlenmesi gereken bazı heyecan verici trendler:
- İleri atomizasyon sonrası tekniklerin geliştirilmesi: Araştırmacılar, toz özelliklerini daha da iyileştirmek için mikrodalga veya ultrasonik işlem gibi yeni yöntemler araştırıyor.
- Sürdürülebilir uygulamalara odaklanın: Geri dönüştürülmüş tozların kullanımı ve çevre dostu atomizasyon sonrası proseslerin geliştirilmesi önem kazanmaktadır.
- Özel pudra tasarımı: Gelecekte, benzersiz AM uygulamaları için özelleştirilmiş özelliklerle özel olarak tasarlanmış tozlar görülebilir.
Sonuç olarak, atomizasyon sonrası işlem için kullanılan tozlar, Katmanlı İmalatın başarısında kritik, ancak genellikle görünmeyen bir rol oynamaktadır. Özelliklerini, uygulamalarını ve çeşitli işlem süreçlerini anlayarak, her seferinde küçük bir parçacık olmak üzere geleceği inşa eden karmaşık dünya hakkında daha derin bir takdir kazanıyoruz.
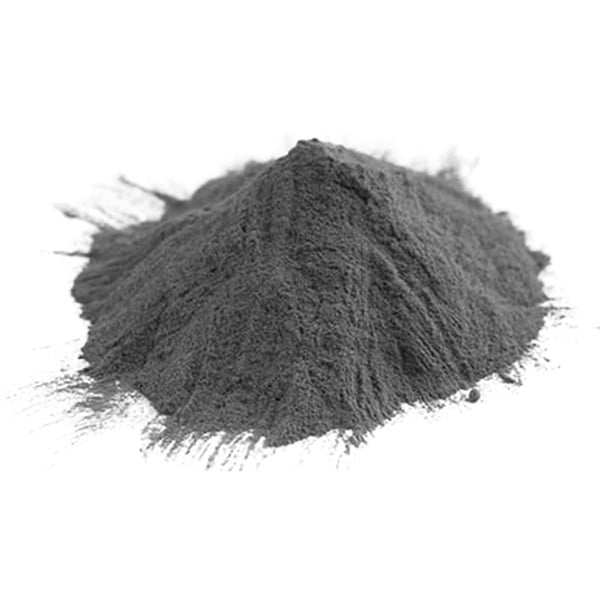
SSS
AM'de kullanılan tozların tipik boyutları nelerdir?
AM'de kullanılan tozlar için parçacık boyutu aralığı belirli uygulamaya bağlı olarak değişebilir. Tipik olarak, tozların çapı 10 ila 150 mikrometre arasında değişir.
Uygulama | Tipik Partikül Boyutu Aralığı (mikrometre) |
---|---|
Havacılık ve Uzay | 20-60 |
Tıbbi İmplantlar | 40-100 |
Otomotiv | 50-120 |
Tüketim Malları | 70-150 |
Tozun kalitesi nihai basılı parçayı nasıl etkiler?
Tozun kalitesi, nihai basılı parçanın özellikleri üzerinde önemli bir etkiye sahiptir. Boyut, şekil ve kimyasal bileşim gibi toz özellikleri aşağıdaki gibi faktörleri etkileyebilir:
- Mekanik Dayanım: Tozdaki inklüzyonlar, boşluklar veya safsızlıklar basılı parçanın mekanik mukavemetini tehlikeye atabilir.
- Yüzey İşlemi: Toz partiküllerinin yüzey pürüzlülüğü, basılı parça üzerinde daha pürüzlü bir yüzey finişine dönüşebilir.
- Boyutsal Doğruluk: Tutarsız partikül boyutu dağılımı, basılı parçada boyutsal yanlışlıklara yol açabilir.
AM için geri dönüştürülmüş tozların kullanılmasıyla ilgili bazı zorluklar nelerdir?
Geri dönüştürülmüş tozlar sürdürülebilir bir alternatif sunarken, bazı zorlukları da beraberinde getirmektedir:
- Kimyasal Bileşim: Geri dönüştürülmüş tozlar, kaynak malzemeden eser elementler veya safsızlıklar içerebilir. Nihai parçanın performans spesifikasyonlarını karşıladığından emin olmak için bunların dikkatle izlenmesi ve kontrol edilmesi gerekir.
- Akışkanlık: Geri dönüştürülmüş tozlar, akışkanlıklarını potansiyel olarak etkileyen birden fazla işleme aşamasından geçmiş olabilir. Optimum akış özelliklerini elde etmek için atomizasyon sonrası ek işlem gerekli olabilir.
- Ayıklama ve Ayrıştırma: Geri dönüştürülmüş tozlar, tutarlı partikül boyutu dağılımı sağlamak için daha titiz ayırma ve sınıflandırma işlemleri gerektirebilir.
AM'de küresel tozlar kullanmanın faydaları nelerdir?
Küresel tozlar AM'de çeşitli avantajlar sunar:
- Geliştirilmiş Akışkanlık: Pürüzsüz yüzeylere sahip küresel partiküller daha kolay akar ve baskı sırasında daha düzgün katman oluşumuna yol açar.
- Geliştirilmiş Paketleme Yoğunluğu: Küresel partiküller daha sıkı paketlenerek boşlukları en aza indirir ve basılı parçanın genel yoğunluğunu artırır.
- Azaltılmış Gözeneklilik: Minimize edilen boşluklar, gözenekliliğin azalması anlamına gelir ve bu da daha güçlü ve daha tutarlı mekanik özellikler sağlar.
Kullanıcılar AM uygulamaları için doğru tozu seçtiklerinden nasıl emin olabilirler?
İşte AM uygulamanız için doğru tozu seçmeye yönelik bazı ipuçları:
- Bir malzeme tedarikçisine danışın: Malzeme tedarikçileri, özel ihtiyaçlarınıza ve amaçlanan uygulamaya göre toz seçimi konusunda uzman tavsiyesi sunabilir.
- Nihai parçanın istenen özelliklerini göz önünde bulundurun: Mekanik mukavemet, yüzey kalitesi ve boyutsal doğruluk gibi faktörler toz seçiminize rehberlik etmelidir.
- Maliyet ve performans arasındaki dengeyi değerlendirin: İşlenmemiş tozlar üstün performans sunabilir, ancak geri dönüştürülmüş tozlar daha uygun maliyetli bir seçenek olabilir.
Kullanıcılar, atomizasyon sonrası işlem için tozların inceliklerini anlayarak, başarılı ve yüksek kaliteli Katmanlı Üretim projelerine katkıda bulunan bilinçli kararlar verebilirler.
Paylaş
MET3DP Technology Co, LTD, merkezi Qingdao, Çin'de bulunan lider bir katmanlı üretim çözümleri sağlayıcısıdır. Şirketimiz, endüstriyel uygulamalar için 3D baskı ekipmanları ve yüksek performanslı metal tozları konusunda uzmanlaşmıştır.
İşletmeniz için en iyi fiyatı ve özelleştirilmiş Çözümü almak için sorgulayın!
İlgili Makaleler
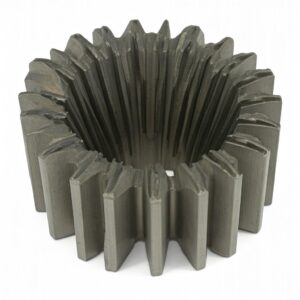
Yüksek Performanslı Nozul Kanat Segmentleri: Metal 3D Baskı ile Türbin Verimliliğinde Devrim
Daha Fazla Oku "Met3DP Hakkında
Son Güncelleme
Bizim Ürünümüz
BİZE ULAŞIN
Herhangi bir sorunuz var mı? Bize şimdi mesaj gönderin! Mesajınızı aldıktan sonra tüm ekibimizle talebinize hizmet edeceğiz.
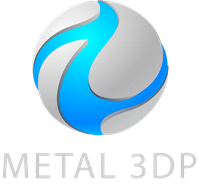
3D Baskı ve Katmanlı Üretim için Metal Tozları