Sinter Sertleştirici Alaşım Tozu
İçindekiler
Sinterleme sertleştirme alaşım tozları, modern metalurji ve malzeme mühendisliğinin temel taşlarından biridir. Bu malzemeler, sinterleme ve sertleştirme süreçlerini tek bir adımda birleştirmenin benzersiz avantajını sunarak çeşitli endüstriyel uygulamalar için verimlilik ve performansta önemli iyileştirmeler sağlar. Bu kılavuz, sinterleme sertleştirme alaşım tozlarının dünyasına derinlemesine inerek türlerini, bileşimlerini, özelliklerini, uygulamalarını ve daha fazlasını inceler. İster deneyimli bir profesyonel olun ister meraklı bir öğrenci, bu makale bu büyüleyici konu hakkında değerli içgörüler sunacaktır.
Sinter Sertleştirici Alaşım Tozuna Genel Bakış
Sinterleme, metal tozunu istenen şekle sıkıştırmayı ve ardından parçacıklar arasında bağ oluşturmak için yüksek sıcaklıkta bir işleme tabi tutmayı içeren bir işlemdir ve katı bir parça ile sonuçlanır. Sinterleme ile sertleştirilen alaşım tozlarını farklı kılan şey, hem sinterleme hem de sertleştirmeyi aynı anda gerçekleştirebilmeleri ve ayrı bir ısıl işlem adımına gerek kalmamasıdır. Bu, gelişmiş mekanik özellikler ve boyut doğruluğu ile sonuçlanır ve bu malzemeleri otomotiv, havacılık ve üretim gibi endüstrilerde oldukça aranan hale getirir.
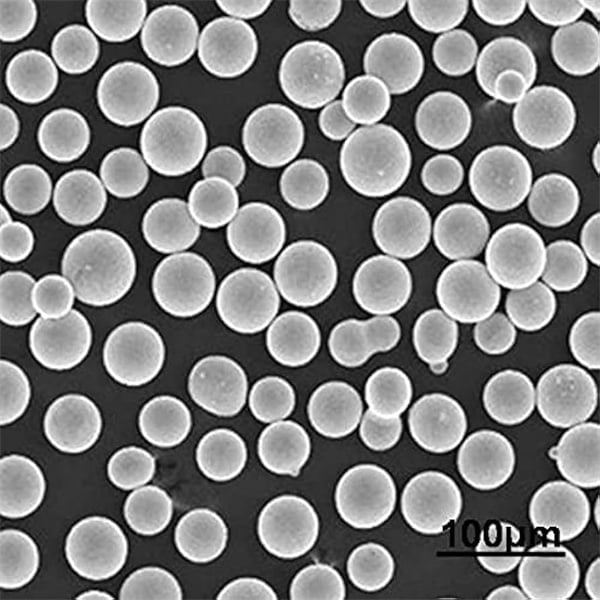
Sinterle Sertleşen Alaşım Tozlarının Türleri, Bileşimi ve Özellikleri
Sinter sertleştirme alaşım tozlarının belirli türlerini, bileşimlerini ve özelliklerini anlamak, uygulamanız için doğru malzemeyi seçmek açısından çok önemlidir. Aşağıda, sinter sertleştirme alaşım tozlarının temel modellerini, bileşimlerini ve özelliklerini özetleyen ayrıntılı bir tablo bulunmaktadır.
Tip | Kompozisyon | Özellikler | Özellikler |
---|---|---|---|
Model A | Fe-Cu-Ni-Mo | Yüksek mukavemet, iyi aşınma direnci | Yapısal parçalar için idealdir |
B Modeli | Fe-Mn-Si | Mükemmel tokluk, orta sertlik | Dişliler ve yataklar için uygundur |
C Modeli | Fe-Ni-Mo-Cr | Üstün yorulma direnci, yüksek sertlik | Yüksek stresli uygulamalarda kullanılır |
D Modeli | Fe-Mo-C | İyi işlenebilirlik, dengeli özellikler | Çeşitli uygulamalar için çok yönlü |
E Modeli | Fe-Cr-Mn | Yüksek korozyon direnci, iyi tokluk | Deniz ortamları için mükemmel |
F Modeli | Fe-Ni-Mn | Mükemmel aşınma direnci, yüksek sertlik | Kesici takımlar için tercih edilir |
G Modeli | Fe-Mo-B | Yüksek sıcaklık kararlılığı, iyi aşınma direnci | Yüksek sıcaklık uygulamaları için uygundur |
H Modeli | Fe-Co-Ni | Üstün manyetik özellikler, iyi mukavemet | Elektrik ve manyetik uygulamalarda kullanılır |
Model I | Fe-Cu-Mo-Ni-Cr | Mükemmel genel performans, yüksek tokluk | Otomotiv bileşenleri için idealdir |
J Modeli | Fe-Mn-V | İyi süneklik, orta mukavemet | Karmaşık şekilli parçalarda kullanılır |
Belirli Modellerin Detaylı Açıklamaları
Model A: Fe-Cu-Ni-Mo
Model A, yüksek mukavemeti ve iyi aşınma direnciyle bilinen popüler bir sinter sertleştirme alaşım tozudur. Demir, bakır, nikel ve molibdenin birleşimi, yapısal parçalar yapmak için ideal olan bir malzemeyle sonuçlanır. Bu alaşım, mükemmelliği nedeniyle özellikle otomotiv endüstrisinde şanzıman dişlileri ve motor parçaları gibi bileşenler için tercih edilir.
boyutsal kararlılık ve mekanik performans.
Model B: Fe-Mn-Si
Model B'nin demir, manganez ve silikondan oluşan bileşimi ona mükemmel tokluk ve orta sertlik kazandırır ve onu dişliler ve yataklar için uygun bir seçim haline getirir. Bu alaşım tozu genellikle ağır makine ve inşaat ekipmanları gibi şok emilimi ve darbe direncinin kritik olduğu uygulamalarda kullanılır.
Model C: Fe-Ni-Mo-Cr
Model C, demir, nikel, molibden ve krom bileşimi sayesinde üstün yorulma direnci ve yüksek sertliğiyle öne çıkar. Bu, onu dayanıklılık ve güvenilirliğin en önemli olduğu havacılık bileşenleri ve yüksek performanslı otomotiv parçaları gibi yüksek stresli uygulamalar için ideal hale getirir.
Model D: Fe-Mo-C
Model D, iyi işlenebilirlik ve mekanik özelliklerin dengesini sağlayan dengeli bir demir, molibden ve karbon bileşimine sahiptir. Bu çok yönlülük, onu endüstriyel makine parçalarından tüketici ürünlerine kadar çok çeşitli uygulamalar için popüler bir seçim haline getirir.
Model E: Fe-Cr-Mn
Model E, demir, krom ve manganez bileşimi sayesinde yüksek korozyon direnci ve iyi tokluğuyla bilinir. Bu alaşım, özellikle deniz ortamlarında ve neme ve aşındırıcı elementlere maruz kalmanın endişe verici olduğu diğer ortamlarda kullanım için uygundur.
Model F: Fe-Ni-Mn
Mükemmel aşınma direnci ve yüksek sertliğiyle demir, nikel ve manganezden oluşan Model F, keskinliğin ve dayanıklılığın kritik önem taşıdığı kesme aletleri ve diğer uygulamalar için tercih edilir. Özellikleri, onu hem endüstriyel hem de tüketici kesme uygulamalarında kullanıma uygun hale getirir.
Model G: Fe-Mo-W
Model G, yüksek sıcaklık kararlılığı ve iyi aşınma direnci elde etmek için demir, molibden ve tungsteni birleştirir. Bu alaşım tozu, türbin motorları ve bozulmadan aşırı ısıya dayanması gereken diğer bileşenler gibi yüksek sıcaklık uygulamaları için idealdir.
Model H: Fe-Co-Ni
Model H, demir, kobalt ve nikel bileşimi sayesinde üstün manyetik özelliklere ve iyi mukavemete sahiptir. Bu, onu motorlar, transformatörler ve manyetik sensörler gibi elektrik ve manyetik uygulamalar için oldukça uygun hale getirir.
Model I: Fe-Cu-Mo-Ni-Cr
Model I, demir, bakır, molibden, nikel ve kromdan oluşan karmaşık bileşiminden kaynaklanan mükemmel genel performans ve yüksek tokluğa sahiptir. Genellikle, güç, tokluk ve aşınma direncinin bir kombinasyonunun gerekli olduğu tahrik milleri ve diferansiyel dişlileri gibi otomotiv bileşenlerinde kullanılır.
Model J: Fe-Mn-V
Demir, manganez ve vanadyum bileşimiyle Model J, iyi süneklik ve orta düzeyde dayanıklılık sunar. Bu, yapısal bütünlüğünden ödün vermeden belirli bir esneklik derecesi gerektiren karmaşık şekilli parçaların üretimi için uygun hale getirir.
Sinter Sertleştirici Alaşım Tozlarının Uygulamaları
Sinter sertleştirme alaşım tozlarının uygulamaları geniş ve çeşitlidir ve bu malzemelerin benzersiz özelliklerini yansıtır. Aşağıda farklı sinter sertleştirme alaşım tozları için birincil uygulamaları özetleyen bir tablo bulunmaktadır.
Uygulama | Uygun Alaşım Modelleri | Açıklama |
---|---|---|
Otomotiv Parçaları | Model A, Model I | Dişliler, motor parçaları ve tahrik milleri için yüksek mukavemet ve aşınma direnci |
Havacılık ve Uzay Bileşenleri | Model C, Model G | Yüksek stresli uygulamalar için üstün yorulma direnci ve yüksek sıcaklık kararlılığı |
Endüstriyel Makineler | Model B, Model D | Dişliler, yataklar ve diğer makine parçaları için iyi tokluk ve işlenebilirlik |
Deniz Ortamları | E Modeli | Nem ve aşındırıcı unsurlara maruz kalan bileşenler için yüksek korozyon direnci |
Kesici Takımlar | F Modeli | Keskinliği ve dayanıklılığı korumak için mükemmel aşınma direnci ve sertlik |
Elektrik ve Manyetik Uygulamalar | H Modeli | Motorlar, transformatörler ve sensörler için üstün manyetik özellikler |
Tüketici Ürünleri | Model D, Model J | Ev aletlerinden elektroniğe kadar çok çeşitli ürünler için çok yönlülük ve iyi süneklik |
Otomotiv Parçaları
Model A ve Model I gibi sinter sertleştirme alaşım tozları otomotiv endüstrisinde yaygın olarak kullanılır. Yüksek mukavemetleri ve aşınma dirençleri onları dişliler, motor parçaları ve tahrik milleri gibi kritik bileşenlerin üretimi için ideal hale getirir. Bu malzemeler parçaların yüksek yükler, sürtünme ve sıcaklık değişimleri dahil olmak üzere otomotiv uygulamalarının zorlu koşullarına dayanabilmesini sağlar.
Havacılık ve Uzay Bileşenleri
Havacılık ve uzay endüstrisi, Model C ve Model G'de bulunan olağanüstü yorulma direncine ve yüksek sıcaklık kararlılığına sahip malzemeler talep ediyor. Bu alaşım tozları, türbin kanatları, motor bileşenleri ve uçakların yapısal parçaları gibi aşırı gerilimlere ve sıcaklıklara dayanması gereken parçaların üretiminde kullanılıyor.
Endüstriyel Makineler
Endüstriyel makine uygulamaları, Model B ve Model D'nin dayanıklılığından ve işlenebilirliğinden faydalanır. Bu malzemeler, genellikle zorlu ortamlarda ağır yükler ve tekrarlayan hareketler altında güvenilir bir şekilde performans göstermesi gereken dişliler, yataklar ve diğer kritik parçaları üretmek için kullanılır.
Deniz Ortamları
Model E'nin yüksek korozyon direnci, onu deniz ortamlarında kullanılan bileşenler için mükemmel hale getirir. Pervaneler, şaftlar ve gemilerin ve denizaltıların yapısal elemanları gibi bu alaşım tozundan yapılan parçalar, deniz suyunun ve diğer deniz koşullarının aşındırıcı etkilerine dayanabilir.
Kesici Takımlar
Kesici takımlar, Model F'nin üstün olduğu keskinliği koruyan ve aşınmaya dirençli malzemeler gerektirir. Bu alaşım tozu, yoğun kullanımda bile zaman içinde tutarlı ve verimli bir şekilde performans göstermesi gereken bıçaklar, matkap uçları ve diğer kesme aletleri üretmek için kullanılır.
Elektrik ve Manyetik Uygulamalar
Model H'nin üstün manyetik özellikleri ve gücü onu elektrik ve manyetik uygulamalar için ideal hale getirir. Motorlar, transformatörler ve manyetik sensörler gibi bileşenler, bu alaşım tozunun manyetik alanlarla etkili bir şekilde etkileşime girme ve bu alanları iletme yeteneğinden faydalanır.
Tüketici Ürünleri
Model D ve Model J'nin çok yönlülüğü ve iyi sünekliği, onları çok çeşitli tüketici ürünleri için uygun hale getirir. Ev aletlerinden elektronik cihazlara kadar, bu malzemeler günlük kullanım için gereken güç, esneklik ve dayanıklılık dengesini sunar.
Spesifikasyonlar, Boyutlar, Kaliteler ve Standartlar
Doğru sinter sertleştirme alaşım tozunu seçmek, bu malzemelerle ilişkili özellikleri, boyutları, dereceleri ve standartları anlamayı gerektirir. Aşağıdaki tablo bu parametrelere ilişkin ayrıntılı bir genel bakış sağlar.
Parametre | Detaylar |
---|---|
Boyutlar | Tipik olarak 5 µm ile 150 µm parçacık boyutu aralığındadır |
Notlar | Standart endüstriyel sınıflar ve yüksek performanslı havacılık sınıfları dahil olmak üzere uygulamaya göre değişir |
Standartlar | Tutarlılık ve kalite güvencesi için ASTM, ISO ve DIN standartlarına uyun |
Teknik Özellikler | Belirli uygulamalara göre uyarlanmış kimyasal bileşim, mekanik özellikler ve fiziksel özellikler ekleyin |
Parçacık Boyutları
Sinter sertleştirme alaşım tozları, tipik olarak 5 mikrometre (µm) ila 150 µm arasında değişen çeşitli parçacık boyutlarında mevcuttur. Parçacık boyutu seçimi, uygulamanın özel gereksinimlerine bağlıdır; daha ince parçacıklar genellikle nihai üründe daha iyi yüzey kalitesi ve ayrıntı sağlarken, daha kaba parçacıklar iyileştirilmiş akışkanlık ve paketleme yoğunluğu sunabilir.
Notlar
Bu malzemeler farklı endüstrilerin ve uygulamaların ihtiyaçlarını karşılamak için çeşitli sınıflarda mevcuttur. Standart endüstriyel sınıflar genel üretim amaçları için uygundur, yüksek performanslı havacılık sınıfları ise daha yüksek mukavemet ve yorulma direnci gibi havacılık endüstrisinin sıkı gereksinimlerini karşılamak üzere tasarlanmıştır.
Standartlar
Sinter sertleştirme alaşım tozları, kalite ve tutarlılığı sağlamak için belirlenmiş standartlara uymalıdır. Ortak standartlar arasında ASTM (Amerikan Test ve Malzeme Topluluğu), ISO (Uluslararası Standardizasyon Örgütü) ve DIN (Deutsches Institut für Normung, Alman Standardizasyon Enstitüsü) tarafından belirlenenler yer alır. Bu standartlara uyulması, malzemelerin belirli kimyasal bileşim, mekanik özellik ve fiziksel özellik gereksinimlerini karşılamasını sağlar.
Teknik Özellikler
Sinter sertleştirme alaşım tozlarının teknik özellikleri, kimyasal bileşimleri, mekanik özellikleri (çekme dayanımı, sertlik ve uzama gibi) ve fiziksel özellikleri (yoğunluk ve ısıl iletkenlik gibi) hakkında ayrıntılı bilgiler içerir. Bu teknik özellikler, farklı uygulamaların özel ihtiyaçlarına göre uyarlanarak optimum performans ve güvenilirlik sağlar.
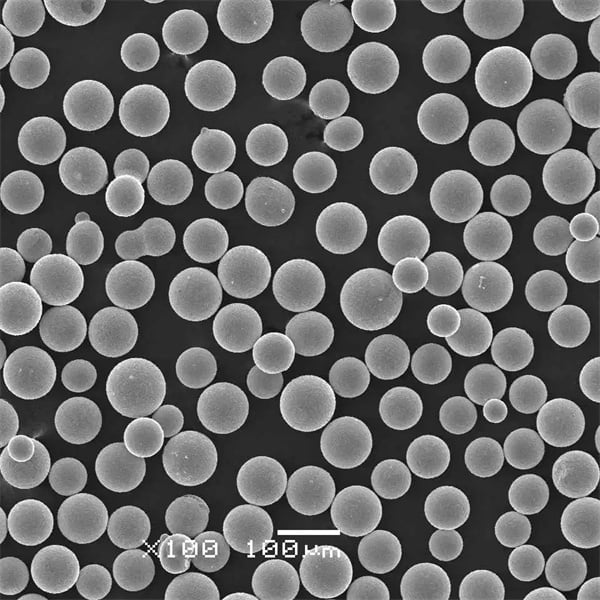
Tedarikçiler ve Fiyatlandırma Detayları
Sinter sertleştirme alaşım tozları için doğru tedarikçiyi seçmek, kalite ve tutarlılığı sağlamak için çok önemlidir. Aşağıda, fiyatlandırma ayrıntılarıyla birlikte bazı önemli tedarikçileri listeleyen bir tablo bulunmaktadır.
Tedarikçi | Konum | Fiyatlandırma (kg başına) | Uzmanlık Alanları |
---|---|---|---|
Höganäs AB | İsveç | $50 – $150 | Geniş alaşım tozları yelpazesi, mükemmel kalite kontrolü |
GKN Hoeganaes | ABD | $45 – $140 | Geniş ürün yelpazesi, ileri teknoloji |
Sandvik | İsveç | $55 – $160 | Yüksek performanslı tozlar, güçlü Ar-Ge odağı |
Marangoz Teknolojisi | ABD | $60 – $170 | Özel alaşımlar, özel çözümler |
Rio Tinto Metal Tozları | Kanada | $48 – $145 | Yüksek saflıkta tozlar, güvenilir tedarik zinciri |
Ametek Özel Metal Ürünleri | ABD | $52 – $155 | Özelleştirilebilir alaşım kompozisyonları, yüksek tutarlılık |
Sumitomo Elektrik Endüstrileri | Japonya | $50 – $150 | Yenilikçi malzemeler, gelişmiş üretim teknikleri |
Daido Çelik | Japonya | $55 – $160 | Yüksek kaliteli alaşımlar, kapsamlı uygulama uzmanlığı |
Mitsubishi Malzemeleri | Japonya | $50 – $150 | Geniş ürün portföyü, güçlü müşteri desteği |
Kennametal | ABD | $58 – $165 | Yüksek performanslı malzemeler, küresel varlık |
Tedarikçi Öne Çıkanlar
- Höganäs AB Geniş alaşım tozları yelpazesi ve mükemmel kalite kontrolüyle tanınan, birçok endüstri için tercih edilen bir seçimdir.
- GKN Hoeganaes geniş ürün yelpazesi ve ileri teknoloji sunarak yüksek performans ve güvenilirlik sağlar.
- Sandvik yüksek performanslı tozlara odaklanan ve güçlü bir Ar-Ge bölümüne sahip olan, sürekli olarak yenilik yapan
Sektörün ihtiyaçlarını karşılamak için çalışıyoruz.
- Marangoz Teknolojisi özel alaşımlarıyla müşterilerinin özel ihtiyaçlarına yönelik özel çözümler sunmada uzmanlaşmıştır.
- Rio Tinto Metal Tozları yüksek saflıkta tozlar ve güvenilir bir tedarik zinciri sunarak, tutarlı ürün bulunabilirliğini garanti eder.
Artıları ve Eksileri, Avantajları ve Sınırlamaları Karşılaştırma
Bilinçli bir karar vermek için, sinter sertleştirme alaşım tozlarının diğer malzemelere kıyasla avantajlarını ve dezavantajlarını anlamak önemlidir. Aşağıdaki tablo bu yönleri vurgulamaktadır.
Aspect | Sinter Sertleştirici Alaşım Tozları | Geleneksel Alaşım Tozları |
---|---|---|
Verimlilik | Tek adımda sinterleme ve sertleştirme, zamandan ve enerjiden tasarruf sağlar | Ayrı sinterleme ve ısıl işlem adımları gerektirir |
Mekanik Özellikler | Geliştirilmiş mukavemet, sertlik ve aşınma direnci | İyi özellikler ancak ek işleme gerektirebilir |
Boyutsal Doğruluk | Tek adımlı işlem sayesinde yüksek hassasiyet | Birden fazla işleme adımı sırasında boyutsal değişiklik potansiyeli |
Maliyet | Başlangıç maliyeti daha yüksek ancak süreç verimliliği nedeniyle genel olarak daha düşük | Daha düşük ilk maliyet ancak ek işleme adımları nedeniyle genel olarak daha yüksek |
Uygulamalar | Yüksek performanslı ve zorlu uygulamalar için uygundur | Genel ve bazı özel uygulamalar için uygundur |
Karmaşıklık | Gelişmiş ekipman ve kontrol sistemleri gerektirir | Daha basit ekipman ve süreçler, ancak ek adımlarla |
Özelleştirme | Son derece özelleştirilebilir kompozisyonlar ve özellikler | Özelleştirme mümkün ancak daha fazla işlem gerektirebilir |
Sinter Sertleştirici Alaşım Tozlarının Avantajları
- Verimlilik: Birincil avantajı, ayrı sinterleme ve ısıl işlem süreçleri gerektiren geleneksel yöntemlere kıyasla, tek adımda sinterleme ve sertleştirme yapılabilmesidir; bu da zamandan ve enerjiden tasarruf sağlar.
- Mekanik Özellikler: Sinterlenmiş alaşım tozları genellikle daha yüksek mukavemet, sertlik ve aşınma direnci gibi üstün mekanik özellikler sergiler ve bu da onları yüksek performanslı uygulamalar için ideal hale getirir.
- Boyutsal Doğruluk: Tek adımlı süreç, boyutsal değişiklik riskini en aza indirerek, nihai üründe yüksek hassasiyet ve tutarlılık sağlar.
- Özelleştirme: Bu tozlar, özel uygulama gereksinimlerini karşılamak için özel çözümlere olanak tanıyan son derece özelleştirilebilir bileşimler ve özellikler sunar.
Sinter Sertleştirmeli Alaşım Tozlarının Dezavantajları
- Maliyet: Toplam maliyet, proses verimliliği nedeniyle daha düşük olabilirken, sinterlenmiş alaşım tozlarının ilk maliyeti, geleneksel tozlara kıyasla daha yüksek olabilir.
- Karmaşıklık: Bu süreç, üretimin karmaşıklığını ve maliyetini artırabilen gelişmiş ekipman ve kontrol sistemleri gerektiriyor.
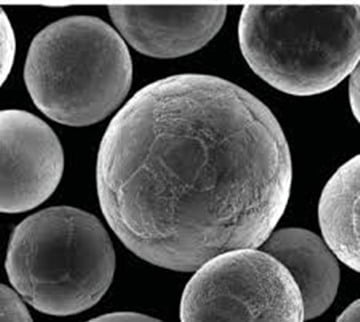
İçgörüler, Örnekler ve Karşılaştırmalar
Performans Bilgileri
Sinterlenmiş alaşım tozlarının avantajlarını göstermek için, Model A'dan (Fe-Cu-Ni-Mo) yapılmış bir bileşenin geleneksel bir çelik parçayla karşılaştırıldığı bir otomotiv uygulamasını ele alalım. Sinterlenmiş parça yalnızca daha yüksek mukavemet ve aşınma direnci sergilemekle kalmaz, aynı zamanda boyutsal doğruluğu da koruyarak işlem sonrası ayarlamalara olan ihtiyacı azaltır. Bu, daha verimli bir üretim süreci ve daha uzun ömürlü bir bileşenle sonuçlanır ve zamanla daha iyi değer sağlar.
Gerçek Dünya Örneği
Havacılık endüstrisinde, türbin kanatlarında Model G (Fe-Mo-W) kullanımı, malzemenin yüksek sıcaklık kararlılığını ve aşınma direncini gösterir. Geleneksel alaşım tozları, benzer özelliklere ulaşmak için ek ısıl işlem gerektirir ve bu da hem zamanı hem de maliyeti artırır. Sinterleme sertleştirme işlemi, kanatların performanstan ödün vermeden aşırı koşullara dayanabilmesini sağlayarak üretimi kolaylaştırır.
Karşılaştırmalı Analiz
Sinter sertleştirme alaşım tozları geleneksel alaşım tozlarıyla karşılaştırıldığında, birincisinin verimlilik, mekanik özellikler ve boyutsal doğruluk açısından önemli avantajlar sağladığı açıktır. Ancak, özellikle maliyet ve basitliğin birincil hususlar olduğu her uygulama için en iyi seçim olmayabilirler. Genel üretim ihtiyaçları için geleneksel alaşım tozları yeterli olabilir, ancak yüksek performanslı, zorlu uygulamalar için sinter sertleştirme alaşımları eşsiz avantajlar sağlar.
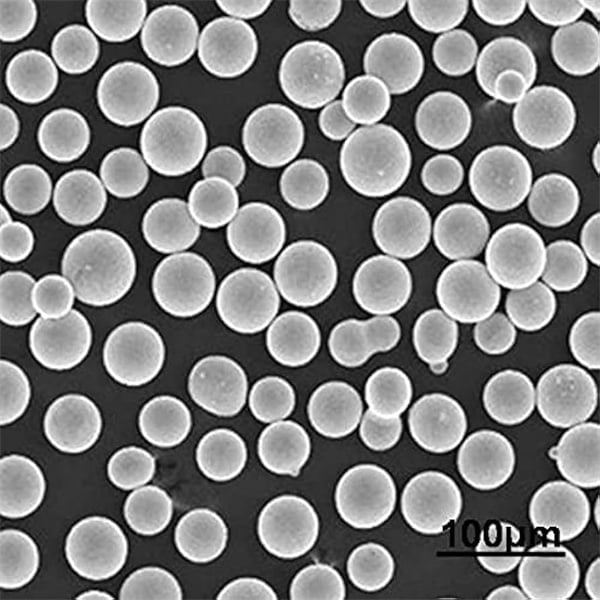
SSS
Sinter sertleştirme nedir?
Sinter sertleştirme sinterleme ve sertleştirmeyi tek bir adımda birleştiren bir işlemdir. Metal tozu istenen şekle sıkıştırılır ve daha sonra aynı anda bağlanma ve sertleşmeyi sağlamak için yüksek bir sıcaklığa ısıtılır, bunun sonucunda gelişmiş mekanik özelliklere sahip sağlam bir parça elde edilir.
Sinter sertleştirme alaşım tozları neden kullanılır?
Sinterleme sertleştirme alaşım tozları, iyileştirilmiş mukavemet, sertlik, aşınma direnci ve boyutsal doğruluk gibi çeşitli avantajlar sunar. Ayrıca, sinterleme ve sertleştirmeyi tek bir adımda birleştirerek üretim sürecini hızlandırır, zamandan ve enerjiden tasarruf sağlar.
Sinterlenmiş alaşım tozlarından hangi endüstriler faydalanır?
Otomotiv, havacılık, endüstriyel makine, denizcilik ve elektrik uygulamaları gibi endüstriler, üstün özellikleri ve üretimdeki verimlilikleri nedeniyle sinter sertleştirme alaşım tozlarının kullanımından önemli ölçüde yararlanmaktadır.
Sinterlenmiş alaşım tozları geleneksel alaşım tozlarıyla karşılaştırıldığında nasıldır?
Sinter sertleştirme alaşım tozları, geleneksel alaşım tozlarına kıyasla daha iyi mekanik özellikler, daha yüksek verimlilik ve daha büyük boyutsal doğruluk sağlar. Ancak, başlangıçta daha pahalı olabilirler ve işleme için gelişmiş ekipman gerektirebilirler.
Sinter sertleştirme alaşım tozlarının bazı yaygın bileşimleri nelerdir?
Yaygın bileşimler arasında demirin bakır, nikel, molibden, manganez, silikon, krom ve tungsten gibi elementlerle kombinasyonları bulunur. Her kombinasyon belirli uygulamalar için uygun benzersiz özellikler sunar.
Sinter sertleştirme alaşım tozları özelleştirilebilir mi?
Evet, sinter sertleştirme alaşım tozları belirli uygulama gereksinimlerini karşılamak için oldukça özelleştirilebilir. Kompozisyondaki ayarlamalar, mukavemet, sertlik, aşınma direnci ve korozyon direnci gibi özellikleri özelleştirebilir.
Sinter sertleştirme alaşım tozlarını nereden satın alabilirim?
Sinter sertleştirme alaşım tozları Höganäs AB, GKN Hoeganaes, Sandvik, Carpenter Technology, Rio Tinto Metal Powders, Ametek Specialty Metal Products, Sumitomo Electric Industries, Daido Steel, Mitsubishi Materials ve Kennametal gibi tedarikçilerden satın alınabilir.
Sinter sertleştirme alaşım tozu seçerken hangi faktörleri göz önünde bulundurmalıyım?
Sinter sertleştirme alaşım tozu seçerken, belirli uygulama, gerekli mekanik özellikler, boyutsal doğruluk, maliyet ve tedarikçi güvenilirliği gibi faktörleri göz önünde bulundurun. Malzemenin sektörünüz için ilgili standartları ve özellikleri karşıladığından emin olmak da önemlidir.
Sonuç
Sinterleme sertleştirme alaşım tozları, tek bir adımda sinterleme ve sertleştirmenin benzersiz bir kombinasyonunu sunarak malzeme mühendisliğinde önemli bir ilerlemeyi temsil eder. Farklı endüstrilerin ihtiyaçlarını karşılamak üzere tasarlanmış çeşitli bileşimlerle, bu malzemeler üstün mekanik özellikler, verimlilik ve hassasiyet sağlar. Otomotiv üretimi, havacılık mühendisliği veya başka herhangi bir yüksek performanslı uygulamayla ilgileniyor olun, sinterleme sertleştirme alaşım tozlarını anlamak ve kullanmak, ürün kalitesinin ve üretim verimliliğinin artmasına yol açabilir.
Paylaş
MET3DP Technology Co, LTD, merkezi Qingdao, Çin'de bulunan lider bir katmanlı üretim çözümleri sağlayıcısıdır. Şirketimiz, endüstriyel uygulamalar için 3D baskı ekipmanları ve yüksek performanslı metal tozları konusunda uzmanlaşmıştır.
İşletmeniz için en iyi fiyatı ve özelleştirilmiş Çözümü almak için sorgulayın!
İlgili Makaleler
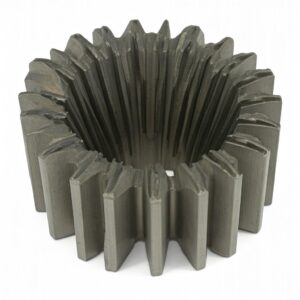
Yüksek Performanslı Nozul Kanat Segmentleri: Metal 3D Baskı ile Türbin Verimliliğinde Devrim
Daha Fazla Oku "Met3DP Hakkında
Son Güncelleme
Bizim Ürünümüz
BİZE ULAŞIN
Herhangi bir sorunuz var mı? Bize şimdi mesaj gönderin! Mesajınızı aldıktan sonra tüm ekibimizle talebinize hizmet edeceğiz.
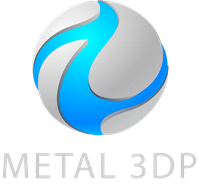
3D Baskı ve Katmanlı Üretim için Metal Tozları