Lazer Seçici Ergitme (SLM) Çalışma Prensibi
İçindekiler
Karmaşık metal parçaların bir toz yatağından lazer hassasiyetiyle katman katman üretilebildiği bir dünya hayal edin. Bu bilim kurgu değil; Lazer Seçici Eritme (SLM), üretim ortamını dönüştüren devrim niteliğinde bir 3D baskı tekniği.
Peki SLM tam olarak nasıl çalışıyor? Kemerlerinizi bağlayın, çünkü lazerlerin, metal tozlarının ve eklemeli üretimin büyülü dünyasına dalmak üzereyiz.
Açığa Çıkarma SLM Süreç: Adım Adım Bir Döküm
Doğrudan Metal Lazer Sinterleme (DMLS) olarak da bilinen SLM, eklemeli üretim prensibine göre çalışır. İstenilen şekli oluşturmak için malzemeyi oyarak çıkaran talaşlı imalat gibi geleneksel eksiltici yöntemlerin aksine SLM, bir nesneyi her seferinde bir katman oluşturur. İşte sürecin bir dökümü:
- Dijital Tasarım: İlk adım, istenen nesnenin 3D bilgisayar destekli tasarım (CAD) modelini oluşturmaktır. Bu model SLM makinesi için bir plan görevi görür.
- Toz Yatağı Hazırlama: Tipik olarak 20 ila 100 mikron arasında değişen ince bir ince metal tozu tabakası, SLM makinesinin içindeki bir yapı platformuna eşit olarak yayılır. SLM'de kullanılan malzemeler arasında titanyum alaşımları, paslanmaz çelik, alüminyum ve hatta yüksek performanslı uygulamalar için Inconel gibi egzotik malzemeler yer alabilir.
- Lazer Işını Büyüsü: Yüksek güçlü bir lazer ışını, toz yatağının yüzeyini dijital tasarıma göre tarar. Lazer, toz partiküllerini belirli konumlarda eriterek nesnenin ilk katmanını oluşturmak için bir araya getirir.
- Katman Katman Oluşturma: İlk katman tamamlandıktan sonra, yapı platformu hafifçe alçalır ve yeni bir toz katmanı biriktirilir. Lazer ışını daha sonra bu yeni katmanı tarar, ikinci katmanı oluşturmak için toz parçacıklarını seçici olarak eritir ve kaynaştırır ve bu böyle devam eder. Bu işlem, nesnenin tamamı inşa edilene kadar katman katman devam eder.
- Destek Yapıları: Metal parçalar yüksek sıcaklıklar nedeniyle bükülebildiğinden veya deforme olabildiğinden, SLM genellikle geçici destek yapıları kullanır. Bu yapılar ana nesnenin yanında basılır ve yapım işlemi sırasında destek sağlar. Tamamlandıktan sonra, destek yapıları işleme, su jeti veya kimyasal aşındırma gibi çeşitli teknikler kullanılarak kaldırılır.
- İşlem sonrası: Yapı tamamlandıktan sonra, bitmiş parça yapı odasından çıkarılır ve gelişmiş mekanik özellikler için ısıl işlem veya estetik amaçlar için yüzey bitirme gibi ek işlem sonrası adımlardan geçebilir.
SLM'yi metaller için sofistike bir 3D yazıcı gibi düşünün. Plastik filament yerine metal tozu kullanır ve mürekkep püskürtme kafası yerine malzemeyi seçici olarak eritmek ve kaynaştırmak için yüksek güçlü bir lazer kullanır. Bu katman katman yaklaşım, geleneksel üretim yöntemleri kullanılarak elde edilmesi imkansız olmasa da zor olan inanılmaz derecede karmaşık geometrilerin oluşturulmasına olanak tanır.
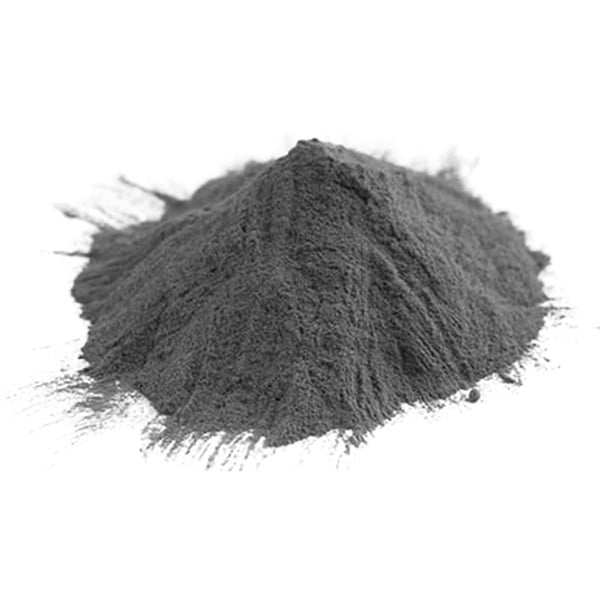
Avantajları SLM Süreç
SLM, geleneksel tekniklere kıyasla çok sayıda cazip avantaj sunmaktadır:
- Tasarım Özgürlüğü: SLM, geleneksel yöntemlerle elde edilemeyen iç kanallar, kafesler ve diğer özelliklerle karmaşık geometrilerin oluşturulmasına olanak tanır. Bu da havacılık, otomotiv ve tıbbi uygulamalarda hafif, yüksek mukavemetli bileşenler için bir olasılıklar dünyasının kapılarını açıyor.
- Hızlı Prototipleme: Doğrudan dijital bir modelden karmaşık parçalar oluşturma yeteneği, SLM'yi hızlı prototipleme için ideal hale getirir. Bu, tasarımcıların tasarımları hızlı ve verimli bir şekilde yinelemesine olanak tanıyarak geliştirme süresini ve maliyetlerini azaltır.
- Toplu Özelleştirme: SLM'nin talep üzerine benzersiz parçalar üretme yeteneği, onu kitlesel özelleştirme için mükemmel hale getirir. Bu, özellikle parçaların hastalara göre uyarlanması gereken tıbbi implantlar gibi sektörler için değerlidir.
- Malzeme Verimliliği: SLM nispeten atık yoğun olmayan bir süreçtir. Yapı haznesindeki kullanılmayan toz geri dönüştürülebilir ve sonraki yapılarda yeniden kullanılabilir, böylece malzeme israfı en aza indirilir.
- Hafifletme: SLM, karmaşık iç yapılar oluşturarak geleneksel olarak üretilen bileşenlerden önemli ölçüde daha hafif parçalar üretebilir. Bu, havacılık ve otomotiv gibi ağırlık azaltmanın kritik olduğu uygulamalar için büyük bir avantajdır.
SLM Sürecinin Dezavantajları
SLM birçok avantaj sunarken, bazı sınırlamaları da beraberinde getirmektedir:
- Yüksek Maliyet: SLM makineleri pahalıdır ve sürecin kendisi de yoğun emek gerektirebilir. Bu da SLM'yi yüksek hacimli üretim çalışmaları için geleneksel yöntemlere kıyasla daha az maliyetli bir seçenek haline getirebilir.
- Yüzey İşlemi: SLM parçaları, sürecin katman katman doğası nedeniyle pürüzlü bir yüzey kalitesine sahip olabilir. Bu durum, pürüzsüz bir yüzey kalitesi gerektiren uygulamalar için işleme gibi ek işlem sonrası adımları gerektirebilir.
- Maddi Sınırlamalar: Tüm metaller SLM için uygun değildir. SLM'de söz konusu olan yüksek sıcaklıklar bazı malzemelerin çatlamasına veya eğilmesine neden olabilir. Ayrıca, bazı malzemeler bitmiş parça içinde performansı etkileyebilecek artık gerilmelere duyarlı olabilir.
- Parça Boyutu Sınırlamaları: SLM karmaşık geometriler oluşturabilirken, üretilebilecek parçaların boyutunda sınırlamalar vardır. Makinenin yapı haznesi boyutu, maksimum parça boyutlarını belirler.
- Güvenlik Hususları: SLM, güvenlik tehlikeleri oluşturabilecek yüksek güçlü lazerler ve metal tozları içerir. Operatörleri toz solumaktan ve lazer radyasyonundan korumak için uygun havalandırma ve güvenlik protokolleri şarttır.
Bu sınırlamalara rağmen SLM, bu zorlukları ele alan devam eden araştırma ve geliştirme çalışmaları ile hızla gelişen bir teknolojidir. Teknoloji olgunlaştıkça, malzeme uyumluluğu, yüzey kalitesi ve maliyet etkinliği konularında ilerlemeler görmeyi ve SLM'nin üretim alanındaki uygulamalarını daha da genişletmeyi bekleyebiliriz.
Uygulamaları SLM Süreç
SLM'nin benzersiz yetenekleri, onu çeşitli sektörlerde değerli bir araç haline getirmektedir:
- Havacılık ve uzay: SLM, uçaklar, uydular ve uzay araçları için hafif, yüksek mukavemetli bileşenler oluşturmak için kullanılır. Karmaşık iç yapıları tasarlama yeteneği, gelişmiş performans ve yakıt verimliliğine sahip parçalara olanak tanır.
- Otomotiv: SLM, otomobiller ve motosikletler için özel motor parçaları ve braketler gibi hafif bileşenlerin üretiminde uygulama alanı bulmaktadır. Bu, genel araç ağırlığının azaltılmasına ve yakıt ekonomisinin iyileştirilmesine katkıda bulunur.
- Tıbbi: SLM, bir hastanın anatomisine mükemmel şekilde uyan karmaşık özelliklere sahip özel protezlerin, diş implantlarının ve cerrahi aletlerin oluşturulmasını sağlayarak tıbbi implant alanını dönüştürüyor. Bu düzeyde bir kişiselleştirme hasta sonuçlarını önemli ölçüde iyileştirebilir.
- Tüketim Malları: SLM, mücevherat, spor malzemeleri ve hatta müzik aletleri gibi üst düzey tüketim mallarının üretimine giriyor. Benzersiz ve karmaşık tasarımlar yaratma yeteneği, yenilikçi ürün geliştirme için kapılar açıyor.
- Aletler: SLM, çeşitli endüstriler için karmaşık kalıplar ve takımlar oluşturmak için kullanılır. Bu, özelleştirilmiş araçların hızlı prototiplenmesine ve üretilmesine olanak tanıyarak teslim sürelerini ve geliştirme maliyetlerini azaltır.
Potansiyel uygulamaları SLM çok geniş ve sürekli genişliyor. Teknoloji daha erişilebilir ve uygun maliyetli hale geldikçe, farklı sektörlerde daha da yenilikçi kullanımların ortaya çıkmasını bekleyebiliriz.
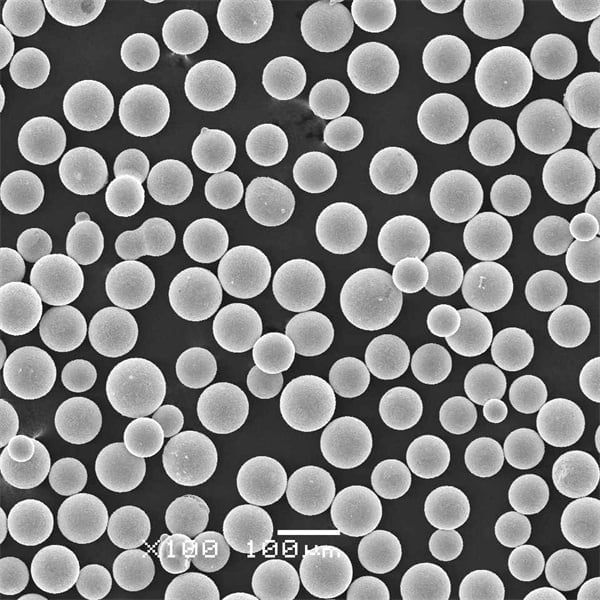
SSS
SLM hakkında sıkça sorulan bazı soruların bir dökümünü burada bulabilirsiniz:
Soru | Cevap |
---|---|
SLM'de hangi malzemeler kullanılabilir? | SLM'de titanyum alaşımları, paslanmaz çelik, alüminyum, Inconel ve hatta altın ve platin gibi değerli metaller de dahil olmak üzere çok çeşitli metaller kullanılabilir. |
SLM parçaları ne kadar güçlüdür? | SLM parçaları, geleneksel olarak üretilen parçalarla karşılaştırılabilir mekanik özelliklerle inanılmaz derecede güçlü olabilir. Güç, kullanılan özel malzemeye ve yapı parametrelerine bağlıdır. |
SLM ve SLS (Seçici Lazer Sinterleme) arasındaki fark nedir? | SLM özellikle metal tozları için kullanılırken, SLS plastikler, seramikler ve hatta naylon dahil olmak üzere daha geniş bir malzeme yelpazesi için kullanılabilir. Ayrıca, SLM toz parçacıklarını tamamen eritirken, SLS bunları kısmen kaynaştırır. |
SLM yüksek hacimli üretim için iyi bir seçim mi? | Şu anda SLM prototipleme, düşük hacimli üretim çalışmaları veya tasarım karmaşıklığının çok önemli olduğu uygulamalar için daha uygundur. Ancak teknoloji olgunlaştıkça, gelecekte yüksek hacimli üretim için maliyet açısından daha rekabetçi hale gelebilir. |
SLM'nin gelecekteki beklentileri nelerdir? | SLM'nin geleceği parlak. Devam eden araştırma ve geliştirmelerle malzeme uyumluluğu, yüzey kalitesi ve maliyet etkinliği konularında ilerlemeler bekleyebiliriz. Bu, SLM uygulamalarını daha da genişletecek ve karmaşık metal parçaları üretme şeklimizde devrim yaratacaktır. |
Umarım bu kapsamlı açıklama Lazer Seçici Eritme'nin (SLM) çalışma prensibi, avantajları, dezavantajları, uygulamaları ve gelecekteki beklentileri hakkında net bir anlayış sağlar. Bu yenilikçi 3D baskı teknolojisi, çeşitli sektörlerde üretimi yeniden şekillendirme potansiyeline sahip ve gelecek için heyecan verici olanaklar sunuyor.
Paylaş
MET3DP Technology Co, LTD, merkezi Qingdao, Çin'de bulunan lider bir katmanlı üretim çözümleri sağlayıcısıdır. Şirketimiz, endüstriyel uygulamalar için 3D baskı ekipmanları ve yüksek performanslı metal tozları konusunda uzmanlaşmıştır.
İşletmeniz için en iyi fiyatı ve özelleştirilmiş Çözümü almak için sorgulayın!
İlgili Makaleler
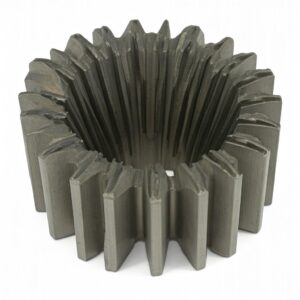
Yüksek Performanslı Nozul Kanat Segmentleri: Metal 3D Baskı ile Türbin Verimliliğinde Devrim
Daha Fazla Oku "Met3DP Hakkında
Son Güncelleme
Bizim Ürünümüz
BİZE ULAŞIN
Herhangi bir sorunuz var mı? Bize şimdi mesaj gönderin! Mesajınızı aldıktan sonra tüm ekibimizle talebinize hizmet edeceğiz.
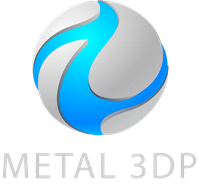
3D Baskı ve Katmanlı Üretim için Metal Tozları
ÜRÜN
cONTACT BİLGİLERİ
- Qingdao Şehri, Shandong, Çin
- [email protected]
- [email protected]
- +86 19116340731