DED teknolojisi ile WAAM teknolojisinin karşılaştırılması
İçindekiler
Giriş
Kanca: Yüksek rüzgar türbini bileşenlerinden karmaşık tıbbi implantlara kadar her şeyi inşa etmek için titizlikle biriktirilen erimiş metal ile karmaşık metal nesneleri katman katman işlediğinizi hayal edin. Bu büyüleyici alan, Yönlendirilmiş Enerji Biriktirme (DED) ve Tel Ark Katmanlı Üretim (WAAM), iki devrim niteliğindeki metal eklemeli üretim (AM) tekniği.
Problem: DED ve WAAM arasında seçim yapmak göz korkutucu bir görev olabilir. Her ikisi de etkileyici yeteneklere sahiptir, ancak aralarındaki nüanslar proje sonuçlarını önemli ölçüde etkileyebilir.
Çözüm: Bu derinlemesine araştırma, DED ve WAAM'ı inceleyerek temel yönlerini, uygulamalarını ve çeşitli senaryolar için uygunluklarını karşılaştıracaktır.
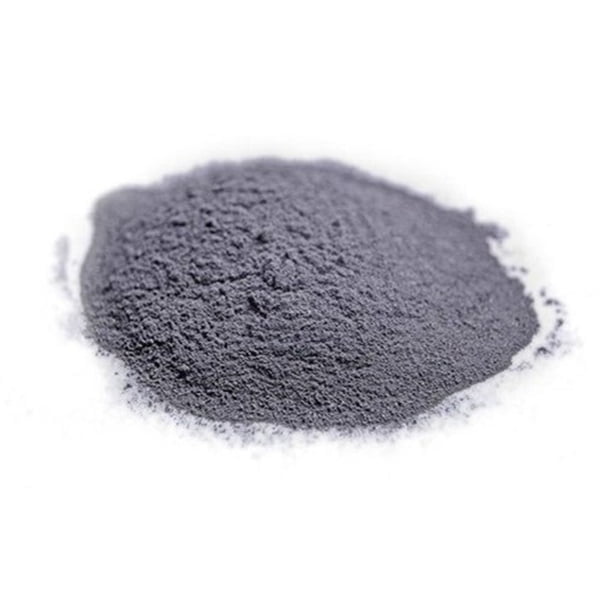
DED Teknolojisini Anlamak
Tanım: DED, malzemeyi (tipik olarak metal tozu) bir yapı platformu üzerinde eritmek ve kaynaştırmak için konsantre bir enerji kaynağı (lazer, elektron ışını, plazma arkı) kullanan ve katman katman bir 3B nesne oluşturan geniş bir AM süreci kategorisidir.
Isı Kaynakları:
Lazer DED: Yüksek güçlü lazerler hassas kontrol ve mükemmel çözünürlük sunarak karmaşık geometriler için idealdir. Popüler malzemeler arasında paslanmaz çelik, titanyum alaşımları ve Inconel bulunur.
Elektron Işını DED: Vakum odasında yüksek odaklı enerji ışınları üreterek üstün erime derinliği ve titanyum gibi reaktif metallerle uyumluluk sağlar.
Plazma Ark DED: Hammaddeyi eritmek için bir plazma torcu kullanır ve genellikle ortak kaynak telleri kullanarak daha büyük yapılar için daha hızlı biriktirme oranları ve maliyet etkinliği sunar.
DED için Metal Tozları:
Metal Tozu | Açıklama | Avantajlar | Sınırlamalar |
---|---|---|---|
Paslanmaz Çelik 316L | Mükemmel korozyon direnci, biyouyumluluğu ve yüksek mukavemeti ile bilinen çok yönlü östenitik çelik. | Havacılık, tıbbi implantlar ve kimyasal işlemede yaygın olarak kullanılır. | Optimum yüzey kalitesi için son işlem gerektirebilir. |
Inconel 625 | Yüksek sıcaklık dayanımı, oksidasyon direnci ve sürünme direnci ile tanınan nikel-krom süper alaşım. | Zorlu havacılık, gaz türbini ve nükleer uygulamalarda kullanılır. | Yaygın çeliklerden daha pahalıdır. |
Titanyum Ti-6Al-4V | Güç, ağırlık ve korozyon direnci arasında iyi bir denge sunan iş gücü titanyum alaşımı. | Biyouyumluluğu nedeniyle havacılık, biyomedikal ve spor ürünlerinde popülerdir. | Baskı sırasında oksijen kontaminasyonuna yatkındır, dikkatli kullanım gerektirir. |
Alüminyum AlSi10Mg | İyi mukavemeti hafif özellikler ve gelişmiş dökülebilirlik ile birleştiren alaşım. | Ağırlık azaltma amacıyla otomotiv, havacılık ve denizcilik uygulamalarında kullanılır. | Yüksek oranda reaktiftir, baskı için inert gaz ortamları gerektirir. |
Takım Çeliği H13 | Mükemmel aşınma direnci ve sıcak mukavemeti ile bilinen sıcak iş takım çeliği. | Metal şekillendirme ve dövme işlemlerinde kullanılan kalıplar, kalıplar ve zımbalar için kullanılır. | Yüksek karbon içeriği nedeniyle baskı yapmak zor olabilir. |
Nikel Alaşım 718 | Yüksek sıcaklıklarda mükemmel mekanik özellikler sunan, yüksek mukavemetli, çökelme ile sertleşen nikel alaşımı. | Havacılık ve uzay bileşenlerinde mukavemeti ve sürünme direnci için kullanılır. | Diğer seçeneklere göre daha pahalı. |
Bakır | Termal ve elektrik uygulamaları ile yüksek iletken metal. | Elektrik iletkenlerinde, ısı eşanjörlerinde ve elektronik bileşenlerde kullanılır. | Baskı sırasında oksidasyona yatkındır, kontrol önlemleri gerektirir. |
Kobalt Krom (CoCr) | Aşınmaya dayanıklı tıbbi implantlar için kullanılan biyouyumlu alaşım. | Mükemmel aşınma direnci nedeniyle kalça ve diz protezlerinde kullanılır. | Biyouyumluluğu optimize etmek için özel kullanım ve son işlem gerektirebilir. |
Inconel 718C | Inconel 625'in geliştirilmiş döküm özellikleri ve kaynaklanabilirlik ile varyasyonu. | Türbin kanatları ve diğer yüksek sıcaklık uygulamalarında kullanılır. | Özellikleri ve sınırlamaları bakımından Inconel 625'e benzer. |
DED Uygulamaları: Havacılık ve uzay bileşenleri, tıbbi implantlar, yıpranmış parçaların onarımı, takımlar ve büyük ölçekli metal yapılar.
Gizemden Arındırma WAAM Teknoloji
Tanım: WAAM veya Tel Ark Katmanlı İmalat, malzemeyi eritmek ve biriktirmek için sürekli bir tel besleme stoğu ve bir elektrik arkı (tipik olarak gaz metal ark kaynağı) kullanan bir DED çeşididir.
Avantajlar:
Maliyet-Etkinlik: WAAM, mevcut ark kaynağı teknolojisinden ve kolayca temin edilebilen telden yararlanarak toz bazlı DED işlemlerine kıyasla daha uygun fiyatlı bir seçenek haline gelir.
Yüksek Birikim Oranları: WAAM, sürekli tel beslemesi ve arkın daha yüksek enerji yoğunluğu sayesinde daha hızlı biriktirme oranları sunarak büyük ölçekli projeler için uygun hale gelir.
Malzeme Uyumluluğu: WAAM, aşağıdakiler de dahil olmak üzere çeşitli yaygın kaynak telleri ile geniş malzeme uyumluluğu sunar:
Çelik: Yumuşak çelik, paslanmaz çelik kaliteleri (304L, 316L), dubleks paslanmaz çelik ve takım çelikleri.
Alüminyum: AlSi10Mg ve Al 6061 gibi alüminyum alaşımları.
Nikel Alaşımları: Inconel 625 ve Nikel Alaşım 718.
Diğer Metaller: Bakır, titanyum alaşımları (oksidasyon endişeleri nedeniyle sınırlı kullanım).
WAAM Uygulamaları: Gemi yapımı, inşaat (köprü bileşenleri, kirişler), büyük ölçekli basınçlı kaplar, ağır makinelerin onarımı ve büyük metal yapıların hızlı prototiplenmesi.
Önemli Hususlar: DED ve WAAM
DED Teknolojisinin Baskı Hızı ve WAAM Teknoloji Farklıdır
- DED: Isı kaynağına ve toz besleme hızına bağlı olarak daha geniş bir baskı hızı aralığı sunar. Lazer DED yüksek hassasiyetli işler için daha düşük hızlar sağlarken, plazma ark DED daha büyük yapılar için daha yüksek hızlara ulaşır.
- WAAM: Sürekli tel beslemesi ve arkın daha yüksek enerji yoğunluğu sayesinde genellikle DED prosesleri arasında en hızlı biriktirme oranlarına sahiptir.
DED Teknolojisi ve WAAM Teknolojisinin Malzeme Maliyetleri Farklıdır
- DED: Özellikle Inconel gibi özel metal tozları veya titanyum gibi reaktif metaller kullanan prosesler için daha pahalı olabilir.
- WAAM: Kolayca bulunabilen ve genellikle daha ucuz kaynak tellerinin kullanılması nedeniyle tipik olarak daha uygun maliyetlidir.
DED Teknolojisi ve WAAM Teknolojisinin Yüzey İşlemi Farklıdır
- DED: Lazer DED, lazer ışını üzerindeki hassas kontrol sayesinde en pürüzsüz yüzey finişlerini sunar. Elektron ışını DED de iyi yüzey finisajları üretir. Plazma ark DED, daha hızlı olmakla birlikte, istenen yüzey kalitesini elde etmek için daha fazla işlem sonrası gerektirebilir.
- WAAM: Ark kaynağı işlemiyle ilişkili sıçrama nedeniyle genellikle lazer DED'ye kıyasla daha pürüzlü yüzeyler üretir. Bununla birlikte, WAAM yüzeyleri istenen yüzeyler için işlenebilir veya taşlanabilir.
Uygulama Alanları Farklıdır
- DED: Havacılık ve uzay parçaları, tıbbi implantlar ve kalıplar gibi mükemmel yüzey kalitesi gerektiren karmaşık, yüksek hassasiyetli bileşenler için çok uygundur.
- WAAM: Yüksek biriktirme oranları ve maliyet etkinliği nedeniyle büyük ölçekli metal yapılarda, hacimli parçaların hızlı prototiplemesinde, gemi inşa bileşenlerinde ve büyük makinelerin onarımında üstündür.
DED Teknolojisi ve WAAM Teknolojisinin Ekipman Maliyetleri
- DED: DED sistemleri, özellikle de lazer veya elektron ışını kullananlar, içerdikleri karmaşık teknoloji nedeniyle WAAM makinelerinden daha pahalı olma eğilimindedir.
- WAAM: WAAM sistemleri genellikle mevcut ark kaynağı teknolojisinden yararlanır ve bu da onları daha uygun fiyatlı bir DED seçeneği haline getirir.
Avantajlar ve Sınırlamalar Karşılaştırma Tablosu
Özellik | DED | WAAM |
---|---|---|
Isı Kaynağı | Lazer, Elektron Işını, Plazma Ark | Elektrik Ark (Gaz Metal Ark Kaynağı) |
Hammadde | Metal Tozu | Sürekli Tel |
Biriktirme Oranı | Değişir (Lazer DED: Yavaş, Plazma Ark DED: Daha Hızlı) | Yüksek |
Malzeme Uyumluluğu | Reaktif metaller de dahil olmak üzere daha geniş malzeme yelpazesi | Öncelikle yaygın kaynak teli malzemeleri |
Yüzey İşlemi | Çok pürüzsüz olabilir (Lazer DED) | Genellikle daha pürüzlü |
Uygulamalar | Karmaşık bileşenler, tıbbi implantlar, kalıplar | Büyük ölçekli yapılar, hızlı prototipleme, onarım |
Ekipman Maliyeti | Genel olarak daha yüksek | Genellikle daha düşük |
Malzeme Maliyeti | Özel tozlar için daha yüksek olabilir | Yaygın kaynak telleri için daha düşük |
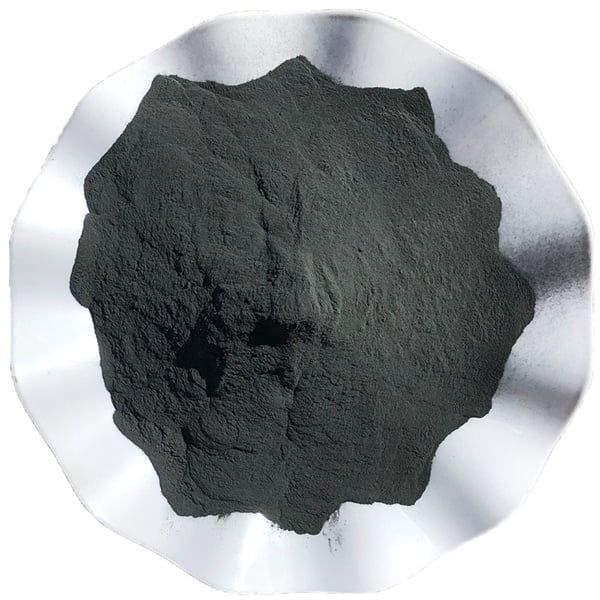
DED ve WAAM
DED ve WAAM arasındaki en uygun seçim, özel proje gereksinimlerinize bağlıdır:
Kritik yüzey işlemlerine ve daha geniş bir malzeme seçimine sahip karmaşık parçalar için DED (özellikle Lazer DED) muhtemelen daha iyi bir seçimdir.
Biriktirme hızının ve kolayca bulunabilen malzemelerin öncelikli olduğu büyük ölçekli, maliyete duyarlı uygulamalar için WAAM parlıyor.
Ek Hususlar:
- Proje karmaşıklığı: DED karmaşık geometrilerde mükemmeldir.
- Malzeme gereksinimleri: DED, reaktif metaller de dahil olmak üzere daha geniş malzeme seçenekleri sunar.
- Üretim hacmi: WAAM'ın hızı, yüksek hacimli projeler için avantajlıdır.
- Bütçe: WAAM genellikle daha uygun maliyetlidir.
DED ve WAAM'ın Geleceği
Hem DED hem de WAAM teknolojileri hızla gelişmektedir. Şu konularda ilerlemeler bekleyebiliriz:
- Çoklu malzeme yetenekleri: DED ve WAAM, kompozit yapılar için aynı yapı içinde farklı malzemeleri biriktirmek üzere işlevleri entegre edebilir.
- Hibrit DED/WAAM sistemleri: DED ve WAAM'ın tek bir makinede birleştirilmesi, malzeme seçimi ve biriktirme oranlarında daha fazla esneklik sunabilir.
- Geliştirilmiş kontrol ve otomasyon: Geliştirilmiş yazılım ve sensör entegrasyonu, baskı süreci üzerinde daha hassas kontrol sağlayacaktır.
SSS
S: Hangi teknoloji daha hızlı, DED mi WAAM mı?
C: WAAM genellikle DED süreçleri arasında en hızlı biriktirme oranlarına sahiptir. WAAM'daki sürekli tel beslemesi ve arkın daha yüksek enerji yoğunluğu, DED'e, özellikle de toz bazlı DED yöntemlerine kıyasla daha hızlı malzeme biriktirmeye olanak tanır. Bununla birlikte, lazer DED, yüksek hassasiyet gerektiren karmaşık işler için orta hızlara ulaşabilir.
S: DED mi yoksa WAAM mı daha pahalı?
C: WAAM genellikle daha uygun maliyetli bir seçenektir. İşte bir döküm:
- Ekipman: WAAM sistemleri mevcut ark kaynağı teknolojisinden yararlanarak, özellikle lazer veya elektron ışını kullanan DED makinelerinden daha uygun fiyatlı hale gelir.
- Malzeme: Inconel gibi özel metal tozlarına veya titanyum gibi reaktif metallere ihtiyacınız varsa DED daha pahalı olabilir. WAAM, kolayca bulunabilen ve genellikle daha ucuz kaynak tellerini kullanır.
S: Hangi teknoloji daha iyi bir yüzey kalitesi sunar?
C: DED, özellikle lazer DED, lazer ışını üzerindeki hassas kontrol nedeniyle pürüzsüz yüzeyler üretmede mükemmeldir. Elektron ışını DED de iyi sonuçlar verir. Plazma ark DED, daha hızlı olmakla birlikte, istenen yüzey kalitesi için daha fazla işlem sonrası gerektirebilir. WAAM, ark kaynağı işlemiyle ilişkili sıçrama nedeniyle lazer DED'ye kıyasla genellikle daha pürüzlü yüzeyler üretir. Bununla birlikte, WAAM yüzeyleri daha pürüzsüz bir yüzey için işlenebilir veya taşlanabilir.
S: DED ve WAAM ne tür parçalar için uygundur?
C: DED ve WAAM farklı uygulama alanlarına hitap etmektedir:
- DED: Mükemmel yüzey kalitesi gerektiren karmaşık, yüksek hassasiyetli bileşenler için idealdir, örneğin:
- Havacılık ve uzay parçaları (türbin kanatları, motor bileşenleri)
- Tıbbi implantlar (kalça protezleri, diş protezleri)
- Kalıplar ve takım uçları
- WAAM: Büyük ölçekli metal yapılarda ve uygulamalarda üstünlük sağlar:
- Yüksek biriktirme oranları çok önemlidir (gemi inşa bileşenleri, köprü kirişleri)
- Hacimli parçaların hızlı prototiplenmesi gereklidir
- Maliyet-etkinlik önemli bir husustur (büyük makinelerin onarımı)
S: DED mi yoksa WAAM mı daha çevre dostu?
C: Hem DED hem de WAAM, talaşlı imalat gibi geleneksel eksiltici imalat tekniklerine kıyasla çevre dostu olarak kabul edilebilir. İşte nedeni:
- Azaltılmış Malzeme Atığı: DED ve WAAM, fazla malzemeyi ortadan kaldıran talaşlı imalatla karşılaştırıldığında minimum malzeme israfı ile parçaları katman katman inşa eden eklemeli süreçleri kullanır.
- Geri Dönüşüm Potansiyeli: DED'de kullanılan metal tozları potansiyel olarak geri dönüştürülebilir ve gelecekteki yapılarda yeniden kullanılabilir, böylece çevresel etki en aza indirilebilir.
Sonuç olarak, DED ve WAAM, farklı güçlü yönleri ve uygulamaları olan güçlü metal katkılı üretim teknolojileridir. Temel ilkelerini, malzeme uyumluluğunu ve çeşitli proje gereksinimlerine uygunluğunu anlayarak, hangi teknolojinin ihtiyaçlarınıza en uygun olduğu konusunda bilinçli bir karar verebilirsiniz. Bu teknolojiler gelişmeye devam ettikçe, çeşitli sektörlerde daha da büyük yetenekler ve daha geniş bir benimseme bekleyebiliriz.
Paylaş
MET3DP Technology Co, LTD, merkezi Qingdao, Çin'de bulunan lider bir katmanlı üretim çözümleri sağlayıcısıdır. Şirketimiz, endüstriyel uygulamalar için 3D baskı ekipmanları ve yüksek performanslı metal tozları konusunda uzmanlaşmıştır.
İşletmeniz için en iyi fiyatı ve özelleştirilmiş Çözümü almak için sorgulayın!
İlgili Makaleler
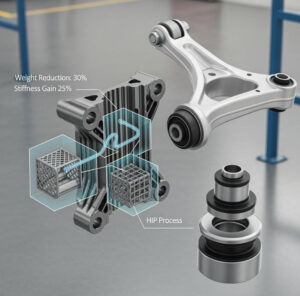
Metal 3D Printed Subframe Connection Mounts and Blocks for EV and Motorsport Chassis
Daha Fazla Oku "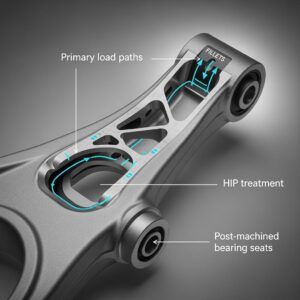
Metal 3D Printing for U.S. Automotive Lightweight Structural Brackets and Suspension Components
Daha Fazla Oku "Met3DP Hakkında
Son Güncelleme
Bizim Ürünümüz
BİZE ULAŞIN
Herhangi bir sorunuz var mı? Bize şimdi mesaj gönderin! Mesajınızı aldıktan sonra tüm ekibimizle talebinize hizmet edeceğiz.