Prášek pro 3D tisk kovů
Obsah
Přehled
3D prášek pro tisk kovů, známá také jako aditivní výroba nebo přímé laserové slinování kovů, je revoluční výrobní technika, která umožňuje vytváření složitých kovových dílů přímo z digitálních návrhů. Laser selektivně taví jemný kovový prášek, vrstvu po vrstvě, dokud se neobjeví hotový 3D objekt.
Klíčovou složkou, která tuto transformační technologii umožňuje, je kovový prášek. Vlastnosti a kvalita prášku mají významný dopad na mechanické vlastnosti, přesnost, povrchovou úpravu a celkový výkon tištěných kovových dílů.
Tento článek poskytuje komplexní přehled kovových prášků pro 3D tisk. Zkoumáme typy prášků, složení, vlastnosti, specifikace, aplikace, výhody, omezení a další na základě nejnovějšího průmyslového výzkumu a standardů. Přečtěte si další informace o tomto fascinujícím materiálu, který je jádrem další průmyslové revoluce.
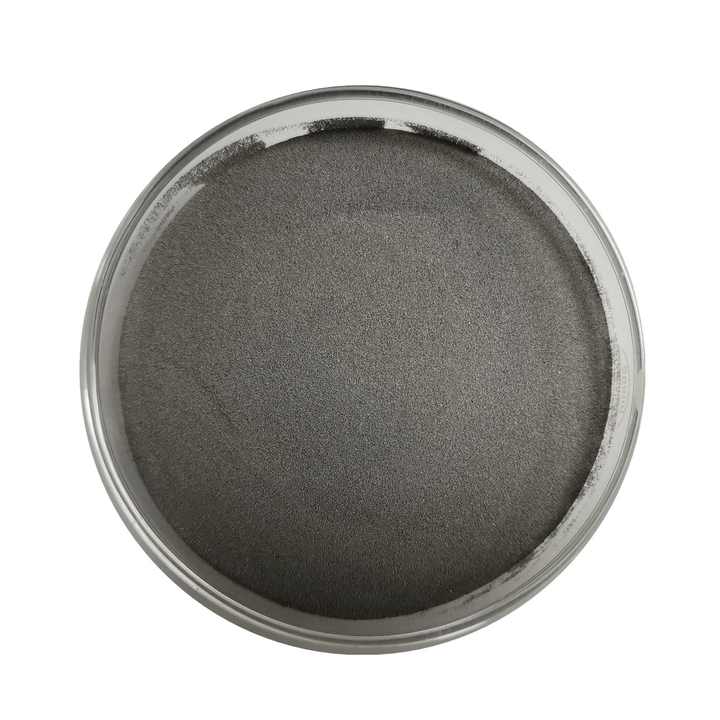
Typy 3D prášek pro tisk kovů
Pro 3D tiskový prášek lze použít několik slitin a kovových materiálů. Mezi nejběžnější možnosti patří:
Prášky z nerezové oceli
Nerezová ocel je jedním z nejoblíbenějších kovů pro 3D tisk díky své vysoké pevnosti, odolnosti proti korozi a schopnosti odolávat vysokým teplotám. Nejběžnější používané slitiny nerezové oceli jsou:
- Nerezová ocel 316L – Standardní slitina s vynikající odolností proti korozi a mechanickými vlastnostmi. 316L má nízký obsah uhlíku, aby se minimalizovalo zbytkové napětí během tisku.
- Nerezová ocel 17-4PH – Srážkově tvrzená nerezová ocel, která může dosáhnout velmi vysoké meze kluzu a pevnosti v tahu tepelným zpracováním po tisku.
- Nerezová ocel 15-5PH – Další srážkově tvrzená nerezová ocel schopná vysoké pevnosti a tvrdosti. 15-5PH nabízí lepší odolnost proti korozi než 17-4PH.
- Duplexní nerezové oceli – Slitiny se smíšenou feriticko-austenitickou mikrostrukturou. Duplexní oceli nabízejí vyšší mez kluzu a pevnost v tahu ve srovnání s austenitickou ocelí 316L. Mezi běžné duplexní slitiny patří 2205 a 2304.
Nástrojové oceli
Nástrojové oceli mají velmi vysokou tvrdost, odolnost proti opotřebení a pevnost v tlaku. Mezi běžné kovové prášky v této skupině patří:
- Nástrojová ocel H13 – Extrémně univerzální nástrojová ocel pro práci za tepla Cr-Mo-V, která si zachovává vysokou tvrdost a stabilitu při zvýšených teplotách.
- Nástrojová ocel P20 – Univerzální nízkolegovaná ocel pro formy s dobrou obrobitelností a leštitelností. P20 se často používá jako levnější alternativa k nástrojové oceli H13.
- Maraging oceli – ‘Maraging’ znamená martenzitické stárnutí. Tyto oceli dosahují ultra vysoké pevnosti stárnutím tepelným zpracováním. Běžné maraging slitiny jsou 18Ni(350) a 18Ni(300).
Hliníkové slitiny
Lehkost hliníku, odolnost proti korozi a vysoká tepelná vodivost z něj činí oblíbenou volbu pro letecký, automobilový a vysokoteplotní průmysl. Mezi běžné hliníkové prášky patří:
- AlSi 10Mg – Nejpoužívanější hliníková slitina s vynikající tekutostí, stabilitou a mechanickými vlastnostmi. Si a Mg působí jako zpevňující činidla.
- AlSi7Mg – Velmi podobný AlSi10Mg. Nižší obsah křemíku zlepšuje tekutost prášku.
- Scalmalloy – Vysokopevnostní slitina Al-Mg-Sc, která získává výjimečnou mez kluzu z přídavku skandia.
Super slitiny kobaltu a niklu
Tyto pokročilé kovové prášky mají díky svému složitému složení extrémně vysokou odolnost vůči teplu a opotřebení. Mezi typické slitiny patří:
- Inconel 718 – Superslitina na bázi niklu a chromu s neuvěřitelnou vysokoteplotní pevností díky tepelnému zpracování s tuhým roztokem a srážkovým vytvrzováním.
- Inconel 625 – Vynikající odolnost proti oxidaci a korozi i při extrémních teplotách. Široce používané v leteckém, chemickém a námořním průmyslu.
- Kobalt-chrom (CoCr) – Kobalt zpevněný karbidy chromu vytváří biokompatibilní implantáty, jako jsou protézy a zubní korunky/můstky.
- Hastelloy – Niklové slitiny odolné proti korozi s přídavky jako molybden, chrom a wolfram.
Titan a slitiny titanu
Čistý titan nabízí dokonalou kombinaci vysoké pevnosti a nízké hustoty. Legující prvky jako hliník, vanad a železo poskytují další výhody:
- Ti6Al4V – Nejoblíbenější titanová slitina s hliníkem stabilizujícím fázi alfa a vanadem zpevňujícím fázi beta.
- TiAl6V4 – Vyšší obsah hliníku dále zlepšuje mechanické vlastnosti a odolnost proti oxidaci.
- Ti6Al4V ELI – ‘ELI’ znamená extra nízký intersticiální s nižším obsahem kyslíku, dusíku a uhlíku. Má zlepšenou odolnost proti lomu oproti běžnému Ti64.
Žáruvzdorné a intermetalické slitiny
Tyto pokročilé prášky odolávají extrémním teplotám nebo mají výjimečnou pevnost/tvrdost:
- Karbid wolframu (WC/Co) – Tvrdé karbidy wolframu spojené fází kobaltového pojiva činí tuto slitinu tužší než ocel při zachování houževnatosti.
- molybden (Mo) – Čistý prášek molybdenu vytváří díly s vysokou tepelnou odolností, které odolávají teplotám přesahujícím 750 °C.
- Inconel 625 – Prášek superslitiny na bázi niklu a chromu vytváří objekty, které si zachovávají vysokou pevnost v oxidačním prostředí až do 980 °C.
Drahé kovy
Jedinečné vlastnosti drahých kovů, jako je zlato, stříbro a platina, je také činí vhodnými pro 3D tisk:
- Stříbro (Ag) – Čistý stříbrný prášek zachovává vynikající elektrické a tepelné vodivé vlastnosti i ve složitých tištěných geometriích.
- Zlato (Au) – Většina tištěného zlata je ve skutečnosti slitina zlata s malým množstvím kovů, jako je stříbro, měď a palladium, pro zlepšení tvrdosti a optimalizaci vlastností.
- Platina (Pt) – Platinový prášek je biokompatibilní a odolný vůči korozi a chemickým vlivům. Používá se k výrobě lékařských implantátů a laboratorního vybavení.
Tato tabulka shrnuje charakteristiky nejběžnějších kovových tiskových prášků:
Typ prášku | Složení | Klíčové vlastnosti |
---|---|---|
Nerezová ocel 316L | Fe/Cr18/Ni10/Mo3 | odolnost proti korozi, vysoká tažnost |
Nerezová ocel 17-4PH | Fe/Cr17/Ni4/Cu4 | Vysoká pevnost po srážkovém vytvrzování |
AlSi 10Mg | Al/Si10/Mg0.5 | Lehký, pevný, dobrá tepelná vodivost |
Inconel 718 | Ni/Cr18/Fe19/Nb5 | Zachovává vysokou pevnost při extrémních teplotách |
Ti6Al4V | Ti/Al6/V4 | Nízká hustota, biokompatibilní, vysoká pevnost |
Karbid wolframu | WC/Co | Extrémně tvrdý a tepelně odolný |
Silver | Ag > 99 % | Vynikající elektrická/tepelná vodivost |
Způsoby výroby kovového prášku
Pro dosažení vlastností nezbytných pro vysoce kvalitní 3D tisk musí mít kovové prášky určité specifické fyzikální vlastnosti a rozložení velikosti částic. Používá se několik technik výroby prášku:
Atomizace plynu
- Proud roztaveného kovu je rozprašován vysokotlakými tryskami inertního plynu
- Vytváří sférický prášek ideální pro tisk – vysoká tekutost, hustota zhutnění
- Nejběžnější metoda pro jemnější prášky z nerezové oceli, nástrojové oceli, superslitiny a titanu
Atomizace vody
- Používá vodní trysky k rozdělení roztaveného kovu na jemné kapičky
- Nepravidelný tvar prášku ovlivňuje tok, ale je levnější než plynová atomizace
- Obvykle se používá pro cenově dostupnější varianty, jako je hliník a hořčík
Plazmová atomizace
- Velmi vysokoenergetický plazmový oblouk taví a rozptyluje kov na jemné částice
- Generuje vysoce sférické prášky z reaktivních slitin, jako jsou titanové aluminidy
- Prášky mají vyšší čistotu a dokáží přesněji tisknout složité detaily
Elektrodová indukční atomizace tavicího plynu (EIGA)
- Kombinuje indukční tavení a plynovou atomizaci
- Výjimečná kontrola nad chemickým složením a čistotou
- Používá se pro speciální slitiny, jako jsou niklové superslitiny a drahé kovy
Mechanické legování
- Prášek vyrobený procesem vysoce energetického kulového mletí
- Používá se pro slitiny mědi CMD, hliníkové kompozity a intermetalické sloučeniny
- Generuje jemné homogenní kompozice ze směsí elementárních prášků
Správná technika výroby prášku je zásadní pro získání požadované chemie slitiny, tvarů částic, distribuce velikosti, úrovní čistoty a charakteristik toku, které jsou nezbytné pro vysoce kvalitní 3D tisk kovů.
Charakteristika kovového prášku
3D tiskové prášky musí splňovat přísné specifikace z hlediska chemie, distribuce velikosti částic, morfologie, mikrostruktury a dalších parametrů. Klíčové vlastnosti zahrnují:
Distribuce velikosti částic
Typický rozsah je 15 mikronů až 45 mikronů. Kritické faktory zahrnují:
- D10 – Velikost, pod kterou spadá 10 % částic
- D50 – Střední velikost částic s 50 % nad a pod tímto průměrem
- D90 – Velikost, kde je 90 % prášku pod tímto průměrem
Ideální hodnoty: D10: 20-25 μm ; D50: 30-35 μm ; D90: 40-45 μm
Tvar částic a povrchová morfologie
- Vysoce sférické částice s hladkými povrchy umožňují nejsnadnější rozprostírání prášku a nejlepší zhutňování.
Průtok a zdánlivá hustota
- Průtok určuje snadnost rozprostírání prášku během tisku
- Zdánlivá hustota udává, jak hustě se prášek balí dohromady v pevném objemu
- Hodnoty závisí na faktorech, jako je tvar částic, distribuce velikosti, povrchová struktura
- Prášky atomizované plynem mají nejvyšší tekutost a hustotu balení
Klepněte na položku Hustota
- Maximální hustota dosažená po mechanickém poklepávání/agitaci
- Vyšší hustota poklepávání zlepšuje hustotu konečného dílu
Hausnerův poměr
- Poměr mezi hustotou poklepávání a zdánlivou hustotou
- Nižší poměry ~1,1 naznačují dobrou tekutost
- Vyšší poměry ~1,4 naznačují soudržnost a špatný tok
Zbytkové oxidy a nečistoty
- Čistota je kritická, kyslík a dusík mohou způsobit defekty pórovitosti
- Chemické složení se musí shodovat se specifikacemi slitin
- Atomizace plynem, plazmou a EIGA nabízí nejčistší prášky
Vnitřní mikrostruktura
- Záleží na složení, rychlosti tuhnutí během výroby prášku
- Pro optimální vrstvené spojování jsou požadována jednofázová, ekviaxiální zrna
- Některé slitiny záměrně vytvářejí duální fáze pro jedinečné vlastnosti
Tvrdost částic
- Ovlivňuje výkonnost hotových dílů
- Pro kvantifikaci se používá číslo pyramidky podle Vickerse (HV)
- Tvrdé částice odolávají deformaci při rozprostírání prášku
Vytváření satelitů
- Menší částice se mohou vázat na větší částice během výroby prášku
- Satelity mohou ovlivnit tvorbu tavné lázně během tisku
- Prášky atomizované plynem mají minimální satelity
Povrchová chemie
- Povrchové funkční skupiny ovlivňují rozprostírání a spojování prášku
- Atmosféra a teplota během výroby mají vliv
- Zpracování v inertní atmosféře generuje čisté chemické složení prášku bez oxidů
Udržování přísné kontroly kvality nad těmito charakteristikami prášku je zásadní pro úspěšný vysoce kvalitní 3D tisk.
Specifikace kovového prášku
Výrobci 3D tiskáren a organizace jako ISO a ASTM standardizovaly specifikace pro většinu kovových tiskových prášků. Typické parametry zahrnují:
Distribuce velikosti
- Hodnoty D10, D50, D90 podle doporučených rozsahů
- Maximální obsah satelitů < 1 %
Shoda chemického složení
- Elementární složení splňující publikované rozsahy složení slitin
- Nízké hladiny kyslíku a dusíku (<1000 ppm)
- Zbytkové množství uhlíku a síry v závislosti na slitině
Zdánlivá a kohoutková hustota
- Zdánlivá hustota 2,5-4,5 g/cm3
- Sypná hustota až o 65 % vyšší než zdánlivá hustota
Průtok
- Zkouška Hallovým průtokoměrem > 15 s/50 g
Obsah vlhkosti
- Vysoká vlhkost způsobuje aglomeraci prášku
- Maximální obsah vlhkosti < 0,02 %
Povrchové oxidy
- Oxidy a kontaminanty mohou způsobit defekty pórovitosti
- Snímkování SEM pro kontrolu povrchů částic
Renomovaní výrobci prášků testují každou šarži a poskytují úplné údaje o analýze, jakož i poměry MLS, Hausnerovy poměry, Carrův index a výsledky pyknometru a Hallova průtokoměru, aby kvalifikovali prášek podle stanovených norem.
Aplikace kovových tiskových prášků
3D tisk kovů transformuje výrobu v různých průmyslových odvětvích. Typické aplikace zahrnují:
Aerospace
- Součásti leteckých a raketových motorů – turbíny, trysky, palivové systémy
- Konstrukční části draku a podvozku letadla z titanu, hliníku, Inconelu
- Významná úspora hmotnosti, konsolidace dílů, zlepšení výkonu
Lékařské a zubní služby
- Implantáty pro rekonstrukci kloubů, jako jsou kolena, kyčle, ramena
- Zubní implantáty, korunky a můstky
- Lebeční desky, chirurgické nástroje, vodítka a nástroje přizpůsobené pacientovi
- Biokompatibilní chromkobalt, titan, nerezová ocel a drahé slitiny
Automobilový průmysl
- Lehké prototypy a výrobní díly automobilů – podvozek, hnací ústrojí
- Konformní chladicí nástroje pro vstřikování
- Vlastní přípravky, upínací přípravky pro montážní linky
- Certifikace pro konstrukční komponenty z nerezové oceli v procesu
Průmyslová výroba
- Kovové nástroje – vstřikování, tváření za tepla, tváření plechu
- Lisovací a razicí matrice z kalených nástrojových ocelí
- Konformní chladicí kanály minimalizují doby cyklu nástrojů
- Rychlá realizace krátkodobých výrobních nástrojů
Ropa a plyn
- Ventily, čerpadla, potrubí z nerezové oceli a Hastelloye pro výrobu
- Komponenty z Inconelu odolné proti korozi pro pobřežní oblasti
- Konformní kanály minimalizují ztráty poklesem tlaku
Spotřební elektronika
- Přizpůsobené kryty, štíty, rámy z nerezové oceli nebo hliníku
- Zařízení pro tepelný management pro odvod tepla
- Komponenty elektromagnetického stínění
- Špičkové designérské šperky – zlato, stříbro, platina
Rychlé výrobní techniky, jako je 3D tisk, odemykají funkčnost, výkon a svobodu designu, které mění hru. Jedinečné vlastnosti kovových tiskových prášků umožňují výrobu hotových dílů pro konečné použití téměř ve všech průmyslových odvětvích.
3D prášek pro tisk kovů Dodavatelé
Většina hlavních konglomerátů pro výrobu kovů nyní vyrábí specializované prášky určené pro aditivní výrobu. Mezi některé z předních globálních dodavatelů patří:
Společnost | Klíčové produkty | Popis |
---|---|---|
Sandvik | Osprey Nerezová ocel, nástrojová ocel, vysoce legované prášky | Lídr v oboru atomizace nerezové oceli, vysoce legované oceli a nástrojové oceli s globálními technickými centry |
Přísada pro tesaře | 17-4PH, 304L, Slitina 625, Chromkobalt, Titanové třídy | Široké portfolio včetně nízkolegovaných ocelí, nerezových ocelí, niklových slitin, titanu a chromkobaltu |
Praxair | TAFA Metal Printability Powders | Úzké distribuce velikosti a sférické morfologie optimalizované pro tisk |
Höganäs | Digitální kovové třídy | Vysoce kvalitní atomizované prášky z nerezové oceli, nástrojové oceli, chromkobaltu a niklové slitiny |
Technologie LPW | LPW Powder Solutions | Specializuje se na plazmovou atomizaci pro reaktivní materiály, jako jsou slitiny titanu a hliníku |
Arcast | Arcast Metal 3D Printing Powders | Kapacita atomizace v komerčním měřítku napříč řadou nerezových ocelí, nástrojových ocelí, niklových superslitin atd. |
Metal Powders Industries Federation | Standard MPIF 35 | Globální federace stanovující akceptované standardy specifikací pro kovové prášky |
Renomovaní dodavatelé poskytují komplexní údaje o složení a vlastnostech svých prášků podložené intenzivním výzkumem a vývojem a přísnou kontrolou kvality. Mnozí nabízejí také služby vývoje slitin na míru. Globální logistika dodavatelského řetězce zajišťuje spolehlivou dostupnost na hlavních trzích.
Ceny prášků pro 3D tisk kovů
Nerezová ocel 316L – 50–100 USD za kg
Maraging Steel (třída 300) – 100–200 USD za kg
Hliník AlSi10Mg – 30–60 USD za kg
Titan Ti6Al4V (třída 5) – 200–400 USD za kg
Inconel 718 – 100–200 USD za kg
Kobaltový chrom F75 – 100–250 USD za kg
Ceny se liší podle:
- Úrovně čistoty
- Rozložení velikosti
- Minimální množství objednávky
- Poplatky za vývoj slitin na míru
- Dovozní cla/daně
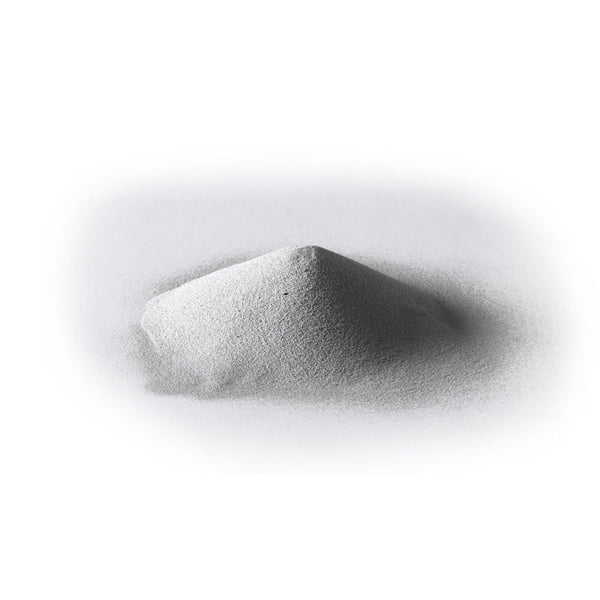
Proti a proti 3D tisku kovů
Výhody
- Volnost návrhu pro složité geometrie
- Konsolidace dílů do jedné součásti
- Snížení hmotnosti z optimalizace topologie
- Snížená montáž z menšího počtu součástí
- Možnosti vysoce pevných slitin
- Funkční integrace – např. konformní chladicí kanály
- Rychlá realizace pro iterace a přizpůsobení
- Výroba zastaralých/starších náhradních dílů na vyžádání
- Snížení materiálového odpadu ve srovnání se subtraktivními technikami
Omezení
- Vyšší náklady na díly ve srovnání s konvenční výrobou ve velkém objemu
- Omezená kapacita velikosti na základě objemu sestavení zařízení
- Omezená rozmanitost možností slitin, které jsou v současnosti certifikovány a kvalifikovány
- Nižší rozměrová přesnost a jemnější povrchové úpravy vyžadují sekundární obrábění
- Mechanická anizotropie, protože vlastnosti se liší v závislosti na orientaci sestavení
- Dodatečné zpracování, jako je horké izostatické lisování, potřebné pro plnou konsolidaci hustoty
- Nedostatek průmyslových standardů pro některé aplikace
Rozsah kovů, které lze tisknout, se exponenciálně rozšiřuje spolu s kvalitou a opakovatelností, protože technologie a věda o materiálech neustále rychle pokročí.
FAQ
Jaký rozsah velikosti částic potřebují kovové prášky pro 3D tisk?
- Typický rozsah velikostí je 15–45 mikronů
- Křivky distribuce specifikují průměry částic D10, D50 a D90
- Hodnoty závisí na požadovaném rozlišení vrstvy, ale běžně 20–45 mikronů
Jaký je rozdíl mezi prášky z nerezové oceli 316L a 17-4PH?
- Obě slitiny železa/chromu/niklu. 316L má lepší odolnost proti korozi.
- 17-4PH má vyšší pevnost a tvrdost po tepelném zpracování vytvrzováním srážením
- 316L se používá více v námořních, chemických a biomedicínských aplikacích, které vyžadují odolnost proti korozi
- 17-4PH se hodí pro aplikace nástrojů vyžadujících vysokou odolnost proti opotřebení
Proč je tvar důležitý pro kovové prášky pro 3D tisk?
- Vysoce sférické částice mají lepší tok a vysokou hustotu slinování
- Hladká povrchová morfologie bez satelitů zajišťuje optimální tavení
- Prášky atomizované plynem poskytují nejkvalitnější výtisky.
Sdílet na
MET3DP Technology Co., LTD je předním poskytovatelem řešení aditivní výroby se sídlem v Qingdao v Číně. Naše společnost se specializuje na zařízení pro 3D tisk a vysoce výkonné kovové prášky pro průmyslové aplikace.
Dotaz k získání nejlepší ceny a přizpůsobeného řešení pro vaše podnikání!
Související články
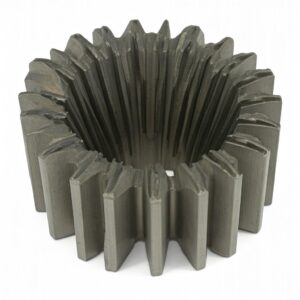
Vysoce výkonné segmenty lopatek trysek: Revoluce v účinnosti turbín díky 3D tisku z kovu
Přečtěte si více "O Met3DP
Nedávná aktualizace
Náš produkt
KONTAKTUJTE NÁS
Nějaké otázky? Pošlete nám zprávu hned teď! Po obdržení vaší zprávy obsloužíme vaši žádost s celým týmem.
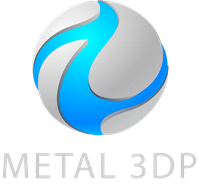
Kovové prášky pro 3D tisk a aditivní výrobu