Sférický 3D tištěný kovový prášek
Obsah
Představte si, že stavíte složité budovy nebo složité pomůcky vrstvu po vrstvě, ne z cihel a malty, ale z ultrajemných kovových částic. To je kouzlo 3D tištěný kovový prášeka v srdci této revoluční technologie leží neopěvovaní hrdinové – sférické kovové prášky.
Tyto drobné, téměř dokonalé koule jsou stavebními kameny, které se transformují v ohromující a funkční kovové předměty. Ale co přesně jsou tyto sférické prášky a proč jsou tak zásadní pro 3D tisk? Připoutejte se, když se vydáme na cestu za poznáním fascinujícího světa těchto kovových divů!
Běžné sférické 3D tištěné kovové prášky
Svět 3D tisknutelných kovů je rozsáhlý, ale mezi nejoblíbenější volby pro sférické prášky patří:
- Nerezová ocel: Univerzální a široce používaný materiál, prášky z nerezové oceli nabízejí vynikající odolnost proti korozi a dobré mechanické vlastnosti, díky čemuž jsou ideální pro aplikace od lékařských implantátů po zařízení na zpracování potravin.
- Slitiny titanu: Slitiny titanu, jako je Ti6Al4V, známé pro svůj vysoký poměr pevnosti k hmotnosti a biokompatibilitu, jsou ideální pro letecké součásti, protetiku a sportovní zboží, kde je prvořadé snížení hmotnosti a odolnost.
- Slitiny niklu: Niklové slitiny, jako je Inconel 625, které nabízejí výjimečnou odolnost vůči teplu a korozi, jsou tou správnou volbou pro náročné prostředí, jako jsou proudové motory, závody chemického zpracování a součásti pro ropu a plyn.
- Slitiny hliníku: Lehké a snadno dostupné hliníkové slitiny, jako je AlSi10Mg, poskytují dobrou rovnováhu mezi pevností, tažností a cenovou dostupností, díky čemuž jsou vhodné pro automobilové díly, spotřební elektroniku a prototypové aplikace.
To je jen letmý pohled na rozmanitou škálu dostupných sférických kovových prášků. Konkrétní volba závisí na požadovaných vlastnostech konečného 3D tištěného objektu, přičemž se berou v úvahu faktory jako pevnost, hmotnost, odolnost proti korozi, biokompatibilita a tepelný výkon.
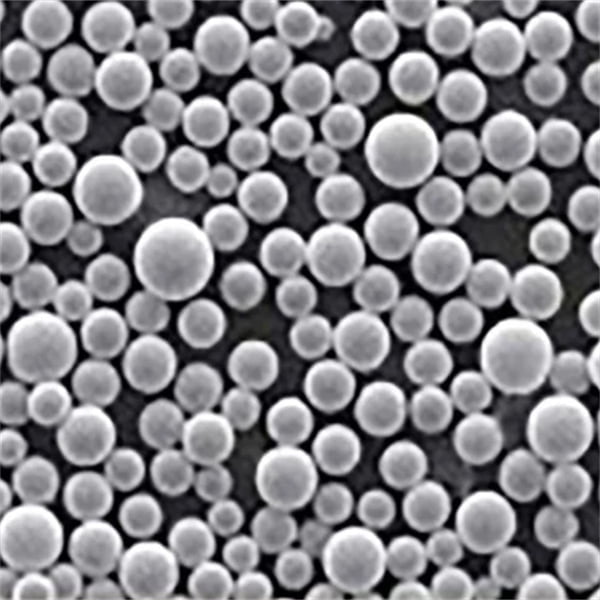
Způsoby výroby sférických 3D tištěné kovové prášky
Stejně jako sněhové vločky, žádné dva sférické kovové prášky nejsou přesně stejné. Způsoby používané k vytvoření těchto téměř dokonalých koulí však sdílejí některé společné rysy. Zde jsou dvě z nejrozšířenějších technik:
- Atomizace plynu: Tato metoda zahrnuje tavení cílového kovu pomocí vysokoteplotní pece. Roztavený kov je poté protlačován tryskou do vysokotlaké komory s inertním plynem. Plyn rychle ochlazuje a rozprašuje proud kovu na drobné kapičky, které se za letu ztuhnou do téměř dokonalých koulí.
- Plazmová atomizace: Podobně jako atomizace plynem využívá plazmová atomizace vysokoteplotní plazmový hořák k tavení kovu. Roztavený kov je poté vystaven vysokorychlostnímu proudu inertního plynu, což způsobí jeho rozpad na sférické částice. Ve srovnání s atomizací plynem nabízí plazmová atomizace jemnější kontrolu nad velikostí a morfologií částic.
Tyto procesy zajišťují vytvoření vysoce tekutých prášků s konzistentním sférickým tvarem. Tato konzistence je zásadní pro úspěšný 3D tisk, protože umožňuje rovnoměrné nanášení prášku a optimální tavení laserem během procesu tisku.
Výhody sférických 3D tiskových kovových prášků
Proč tedy tolik povyku kolem sférických tvarů? Zde je důvod, proč tyto téměř dokonalé koule vládnou ve světě 3D tištěných kovů:
- Vynikající tekutost: Představte si, že sypete písek versus kuličková ložiska. Sférické prášky, jako kuličková ložiska, proudí volně a konzistentně, což zajišťuje rovnoměrné rozložení během procesu 3D tisku. To se promítá do lepšího vytváření vrstev a zlepšené kvality povrchu v konečném tištěném objektu.
- Zvýšená hustota balení: Přemýšlejte o balení pomerančů versus brambor nepravidelného tvaru. Sférické prášky se balí efektivněji, což vede k vyšší hustotě práškového lože. To se promítá do pevnějších a robustnějších 3D tištěných dílů s minimální vnitřní pórovitostí.
- Zlepšená absorpce laseru: Během 3D tisku laserový paprsek taví kovový prášek vrstvu po vrstvě. Sférický tvar umožňuje efektivnější absorpci laseru, což vede k přesnému tavení a minimalizaci tepelného zkreslení v okolním materiálu.
- Snížení množství odpadu: Prášky nepravidelného tvaru mají tendenci uvíznout v rozích nebo zanechat dutiny během tisku, což vede k plýtvání materiálem. Sférické prášky minimalizují takové výskyty, což vede k efektivnějšímu využití materiálu.
Tyto výhody společně přispívají k výrobě vysoce kvalitních, vysoce výkonných 3D tištěných kovových objektů s konzistentními vlastnostmi.
Aplikace sférických kovových prášků v 3D tisku
Aplikace sférických kovových prášků v 3D tisku jsou stejně rozmanité jako samotné materiály. Zde je jen několik příkladů:
- Letectví a obrana: Lehké, ale pevné slitiny titanu a hliníku se používají k vytváření složitých součástí letadel, částí raketových motorů a zakázkově navrženého obranného vybavení.
- Lékařství a zubní lékařství: Biokompatibilní prášky titanu a kobalt-chromu revolucionizují lékařskou oblast tím, že umožňují vytváření personalizované protetiky, zubních implantátů a chirurgických nástrojů.
- Automobilový průmysl: Hliníkové a niklové slitiny nacházejí
Technický průzkum sférických kovových prášků
Zatímco jsme prozkoumali běžné typy a aplikace sférických kovových prášků, existuje celý svět technických detailů, které čekají na odhalení. Pojďme se hlouběji ponořit do některých klíčových aspektů:
Vlastnosti a výkon prášku
Výkon 3D tištěných kovových objektů závisí na vlastnostech použitých sférických prášků. Zde jsou některé kritické faktory, které je třeba zvážit:
- Distribuce velikosti částic (PSD): To se týká kolísání velikosti částic prášku. Úzký PSD s minimálními odlehlými hodnotami zajišťuje konzistentní hustotu balení a optimální tavení laserem během tisku.
- Sféricita: Měřené odchylkou od dokonalé koule, vyšší hodnota sféricity indikuje lepší tekutost a hustotu balení.
- Morfologie povrchu: Povrchová textura částic prášku může ovlivnit absorpci laseru a vazbu mezi částicemi během tisku. Hrubší povrchy nabízejí lepší vazbu, zatímco hladší povrchy mohou nabídnout lepší tekutost.
- Chemie prášku: Přítomnost stopových prvků nebo nečistot v prášku může ovlivnit konečné vlastnosti tištěného objektu. Přísná kontrola kvality zajišťuje minimální nečistoty pro konzistentní výkon.
Tyto vlastnosti jsou pečlivě kontrolovány během výrobního procesu, aby se vytvořily prášky přizpůsobené pro specifické aplikace. Například jemnější prášky mohou být preferovány pro složité detaily, zatímco větší částice by mohly být ideální pro aplikace vyžadující vyšší pevnost.
Výzvy a úvahy při používání sférických kovových prášků
Zatímco sférické kovové prášky nabízejí nesporné výhody, je třeba zvážit výzvy:
- Náklady: Výroba vysoce kvalitních sférických prášků zahrnuje sofistikované procesy, které se mohou promítnout do vyšších nákladů na materiál ve srovnání s prášky nepravidelného tvaru.
- Bezpečnost: Kovové prášky, zejména ty jemnější, mohou představovat nebezpečí vdechování. Během skladování a manipulace jsou zásadní správné postupy manipulace a bezpečnostní vybavení.
- Dostupnost materiálu: Ne všechny kovy lze snadno vyrobit na vysoce kvalitní sférické prášky. Probíhá výzkum a vývoj s cílem rozšířit sortiment snadno dostupných materiálů.
Tyto výzvy jsou aktivně řešeny pokroky ve výrobních technikách a přísnějšími bezpečnostními předpisy. Jak technologie dozrává, můžeme očekávat cenově výhodnější a snadno dostupné sférické prášky pro širší škálu kovů.
Budoucnost sférických kovových prášků v 3D tisku
Budoucnost sférických kovových prášků v 3D tisku překypuje vzrušujícími možnostmi. Zde jsou některé trendy, které je třeba sledovat:
- Prášky nano-velikosti: Probíhá výzkum s cílem vyvinout ještě jemnější sférické prášky nano-velikosti. Tyto prášky mají obrovský potenciál pro vytváření mikro- a nano-měřítkových 3D tištěných struktur s výjimečnými vlastnostmi.
- Prášky z různých materiálů: Vývoj kompozitních prášků se směsí různých materiálů by mohl vydláždit cestu pro 3D tištěné objekty s přizpůsobenými funkcemi, jako je vynikající pevnost a vodivost v rámci jednoho výtisku.
- Recyklované prášky: Udržitelnost je rostoucí obavou. Pokroky v technologiích recyklace prášků by mohly umožnit opětovné použití kovových prášků ze zbylého materiálu nebo podpůrných struktur, čímž by se minimalizoval odpad a dopad na životní prostředí.
Tyto pokroky slibují rozšíření možností 3D tisku a posouvají hranice toho, co je možné s kovovýrobou. Sférické kovové prášky nepochybně zůstanou v popředí této revoluční technologie, budou hnacím motorem inovací a utvářet budoucnost výroby.
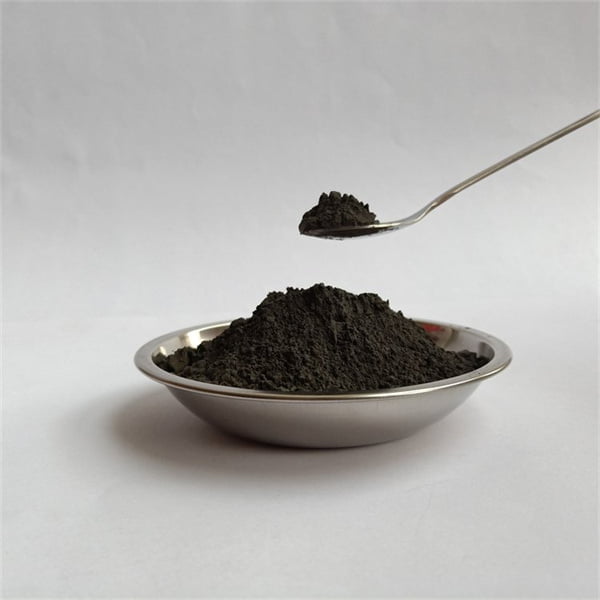
Nejčastější dotazy
Zde je rychlý přehled některých často kladených otázek o sférických kovových prášcích pro 3D tisk, prezentovaný v tabulkovém formátu pro snadnou orientaci:
Otázka | Odpovědět |
---|---|
Jaké jsou výhody používání sférických kovových prášků při 3D tisku? | Sférické prášky nabízejí ve srovnání s nepravidelnými tvary vynikající tekutost, hustotu balení, absorpci laseru a minimalizují odpad, což vede k vyšší kvalitě a výkonu 3D tištěných objektů. |
Jaké jsou některé běžné typy sférických kovových prášků používaných při 3D tisku? | Nerezová ocel, slitiny titanu, slitiny niklu a slitiny hliníku jsou oblíbenou volbou díky svým rozmanitým vlastnostem a rozšířeným aplikacím. |
Jak se vyrábějí sférické kovové prášky? | Atomizace plynem a plazmová atomizace jsou přední techniky, obě zahrnují vysokoteplotní tavení a rychlé chlazení kovu do téměř dokonalých koulí. |
Jaké jsou některé aplikace sférických kovových prášků při 3D tisku? | Aplikace jsou rozsáhlé, včetně leteckých komponentů, lékařských implantátů, automobilových dílů a zakázkově navržených nástrojů pro různá průmyslová odvětví. |
Existují nějaké problémy spojené s používáním sférických kovových prášků? | Náklady, bezpečnostní obavy u jemných prášků a omezená dostupnost určitých materiálů jsou některé z problémů, které se řeší prostřednictvím probíhajícího výzkumu a vývoje. |
Sdílet na
MET3DP Technology Co., LTD je předním poskytovatelem řešení aditivní výroby se sídlem v Qingdao v Číně. Naše společnost se specializuje na zařízení pro 3D tisk a vysoce výkonné kovové prášky pro průmyslové aplikace.
Dotaz k získání nejlepší ceny a přizpůsobeného řešení pro vaše podnikání!
Související články
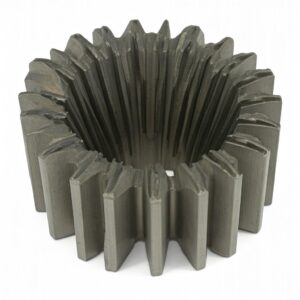
Vysoce výkonné segmenty lopatek trysek: Revoluce v účinnosti turbín díky 3D tisku z kovu
Přečtěte si více "O Met3DP
Nedávná aktualizace
Náš produkt
KONTAKTUJTE NÁS
Nějaké otázky? Pošlete nám zprávu hned teď! Po obdržení vaší zprávy obsloužíme vaši žádost s celým týmem.
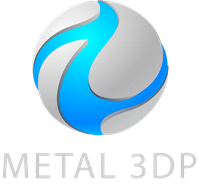
Kovové prášky pro 3D tisk a aditivní výrobu