Jaké 3D tištěné kovové prášky lze použít při výrobě letadel?
Obsah
Svět letectví neustále posouvá hranice a hledá lehčí, pevnější a palivově účinnější letadla. Vstupte do 3D tisku, revoluční technologie, která transformuje způsob, jakým se letadla staví. Ale co pohání tuto transformaci? Odpověď spočívá v různých specializovaných 3D tištěný kovový prášek, z nichž každý má jedinečné vlastnosti, díky nimž jsou ideální pro specifické součásti letadel.
Tato komplexní příručka se ponoří hluboko do fascinujícího světa 3D tištěných kovových prášků používaných při výrobě letadel. Prozkoumáme různé typy prášků, jejich vlastnosti, aplikace a faktory, díky nimž se vznášejí nad konkurencí. Připoutejte se a připravte se na podrobný průzkum kovových zázraků, které se vznášejí v moderním leteckém průmyslu.
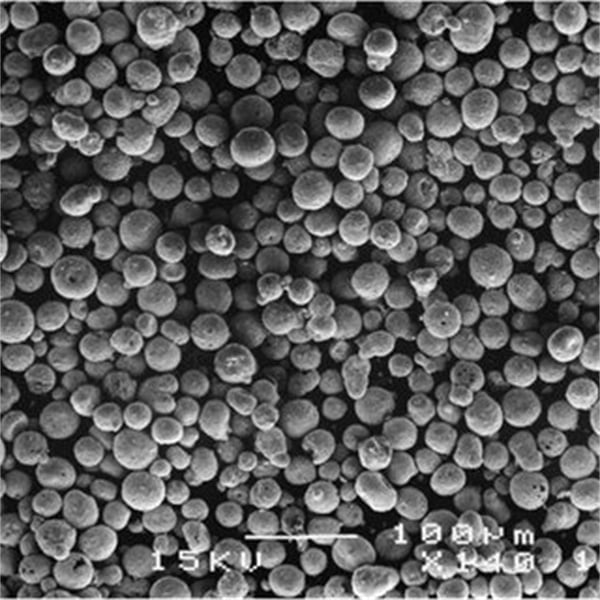
Pohled do světa 3D tištěné kovové prášky
Představte si, že stavíte složité součásti letadel vrstvu po vrstvě s bezkonkurenční přesností a minimálním odpadem. To je kouzlo 3D tištěných kovových prášků. Tyto jemnozrnné kovové částice se přivádějí do 3D tiskárny, kde je laser nebo elektronový paprsek selektivně roztaví dohromady a vytváří požadovaný tvar vrstvu po vrstvě.
Tato technologie nabízí několik výhod oproti tradičním výrobním metodám, jako je obrábění nebo odlévání. Zde jsou některé klíčové výhody:
- Svoboda designu: 3D tisk umožňuje složité geometrie, které by bylo nemožné nebo neuvěřitelně drahé vytvořit konvenčními metodami. Představte si lehké mřížkové struktury pro zlepšení spotřeby paliva nebo složité chladicí kanály pro teplejší motory.
- Snížení hmotnosti: V konstrukci letadel se počítá každý gram. Použitím lehkých kovových prášků, jako je titan, mohou výrobci výrazně snížit celkovou hmotnost letadla, což vede k lepší spotřebě paliva a zvýšené nosnosti.
- Snížení množství odpadu: Tradiční metody často generují spoustu kovového šrotu. 3D tisk používá pouze potřebný prášek, minimalizuje odpad a činí jej udržitelnější volbou.
- Konsolidace částí: Složité sestavy lze tisknout jako jednotlivé komponenty, což snižuje počet dílů a zjednodušuje výrobní proces.
Nyní se ponořme do konkrétních kovových prášků, které dělají vlny při výrobě letadel.
Nejlepší kovové prášky pro výrobu letadel
Volba kovového prášku pro konkrétní součást letadla závisí na několika faktorech, včetně pevnosti, hmotnosti, odolnosti proti korozi a provozní teploty. Zde prozkoumáme deset nejoblíbenějších kovových prášků používaných při výrobě letadel, zdůrazňujících jejich jedinečné vlastnosti a aplikace:
1. Titanové slitinové prášky (Ti-6Al-4V)
- Složení: Primárně titan (Ti) se 6 % hliníku (Al) a 4 % vanadu (V).
- Vlastnosti: Vysoký poměr pevnosti k hmotnosti, vynikající odolnost proti korozi, dobrá biokompatibilita (důležitá pro lékařské aplikace v letadlech).
- Aplikace: Součásti podvozku, části draku letadla, úchyty motoru, součásti křídel.
- Specifikace: K dispozici v různých velikostech zrn a lze je dodatečně zpracovat pro zlepšení mechanických vlastností.
- Dodavatelé: AMPA Material, LPW Powder, EOS GmbH
- Cena: Relativně drahé ve srovnání s některými jinými prášky, ale úspora hmotnosti a výhody výkonu často ospravedlňují náklady.
- Klady: Lehký, pevný, odolný proti korozi.
- Nevýhody: Relativně drahé, může být náročné na tisk kvůli vysoké teplotě tání.
2. Hliníkové slitinové prášky (AlSi10Mg)
- Složení: Primárně hliník (Al) s 10 % křemíku (Si) a hořčíku (Mg) pro zlepšení pevnosti a slévatelnosti.
- Vlastnosti: Vynikající obrobitelnost, dobrý poměr pevnosti k hmotnosti, vysoká tepelná vodivost.
- Aplikace: Vnitřní součásti letadel, výměníky tepla, nestrukturální díly.
- Specifikace: K dispozici v různých velikostech zrn a lze je tepelně zpracovat pro vylepšené vlastnosti.
- Dodavatelé: SLM Solutions, ExOne, Höganäs AB
- Cena: Cenově dostupnější ve srovnání s titanovými prášky.
- Klady: Lehký, dobré tepelné vlastnosti, snadný tisk.
- Nevýhody: Nižší pevnost ve srovnání s titanovými slitinami.
3. Prášky z nerezové oceli (316L)
- Složení: Na bázi železa (Fe) s chromem (Cr), niklem (Ni), molybdenem (Mo) a dalšími prvky pro odolnost proti korozi.
- Vlastnosti: Vynikající odolnost proti korozi, dobrá pevnost a tažnost, snadno dostupné.
- Aplikace: Potrubí, trubky, součásti pro manipulaci s kapalinami, některé nestrukturální díly.
- Specifikace: K dispozici v různých třídách s různými úrovněmi odolnosti proti korozi a mechanických vlastností.
- Dodavatelé: Carpenter Additive Manufacturing, Oerlikon Metco, Sandvik Additive Manufacturing
- Cena: Cenově dostupný ve srovnání s titanem a některými slitinami na bázi niklu.
- Klady: Snadno dostupné, dobrá odolnost proti korozi, všestranné.
- Nevýhody: Relativně těžké ve srovnání s titanovými slitinami, může vyžadovat dodatečné zpracování pro optimální pevnost.
4. Inconel 625 (IN625)
- Složení: Superslitina na bázi niklu (Ni) s chromem (Cr), molybdenem (Mo) a niobem (Nb) pro vysokoteplotní pevnost.
- Vlastnosti: Výjimečná vysokoteplotní pevnost a odolnost proti oxidaci, dobrá odolnost proti tečení (odolnost proti deformaci při namáhání při vysokých teplotách).
- Aplikace: Součásti proudových motorů, jako jsou spalovací komory, lopatky turbín, součásti přídavného spalování.
- Specifikace: Přísná kontrola kvality vyžadovaná kvůli náročným požadavkům na výkon.
- Dodavatelé: Special Metals Corporation, Haynes International, Aubert & Duval
- Cena: Drahé kvůli složitému složení a vysokému výkonu.
- Klady: Vynikající vysokoteplotní výkon, dobrá odolnost proti tečení.
- Nevýhody: Drahé, náročné na tisk kvůli vysoké teplotě tání.
5. Haynes 282 (UNS N07282)
- Složení: Superslitina na bázi niklu (Ni) s chromem (Cr), molybdenem (Mo), wolframem (W) a dalšími prvky pro výjimečnou vysokoteplotní pevnost.
- Vlastnosti: Vynikající vysokoteplotní pevnost a odolnost proti oxidaci ve srovnání s Inconelem 625, vynikající odolnost proti tečení.
- Aplikace: Součásti horkého konce motoru, jako jsou lopatky turbín a lopatky v pokročilých proudových motorech.
- Specifikace: Vyžaduje pečlivou manipulaci a přísnou kontrolu kvality.
- Dodavatelé: Haynes International, Special Metals Corporation, ATI Allegheny Ludlum
- Cena: Velmi drahé kvůli složitému složení a vynikajícímu výkonu.
- Klady: Bezkonkurenční vysokoteplotní výkon, vynikající odolnost proti tečení.
- Nevýhody: Extrémně drahé, velmi náročné na tisk.
6. Hliníkové slitinové prášky (Scalmalloy)
- Složení: Vlastní slitina hliníku, hořčíku a skandia vyvinutá společností Airbus. Nabízí významné zlepšení oproti tradičnímu AlSi10Mg.
- Vlastnosti: Výjimečný poměr pevnosti k hmotnosti, překonávající i některé titanové slitiny, dobrá houževnatost a odolnost proti únavě.
- Aplikace: Vysoce namáhané součásti draku letadla, konstrukce křídel, potenciálně součásti trupu v budoucnu.
- Specifikace: Omezená dostupnost kvůli vlastnické povaze, vyžadují se specifické parametry tisku.
- Dodavatelé: Primárně Airbus (prostřednictvím partnerů jako SLM Solutions)
- Cena: Potenciálně dražší než tradiční hliníkové slitiny kvůli jeho jedinečnému složení.
- Klady: Výjimečný poměr pevnosti k hmotnosti, dobrá houževnatost a odolnost proti únavě.
- Nevýhody: Omezená dostupnost, vyžaduje specializované odborné znalosti tisku.
7. Slitiny mědi (CuNi2Si)
- Složení: Slitina mědi (Cu) s niklem (Ni) a křemíkem (Si) pro zlepšení pevnosti a tisknutelnosti.
- Vlastnosti: Vynikající tepelná a elektrická vodivost, dobrá odolnost proti korozi, relativně nízká teplota tání ve srovnání s jinými možnostmi.
- Aplikace: Výměníky tepla, elektrické součásti, potenciálně pro součásti vyžadující vysokou tepelnou vodivost.
- Specifikace: Může vyžadovat specifické dodatečné zpracování pro optimální vodivost.
- Dodavatelé: Höganäs AB, Carpenter Additive Manufacturing, ExOne
- Cena: Obecně cenově dostupný ve srovnání s vysoce výkonnými slitinami.
- Klady: Vynikající tepelná a elektrická vodivost, dobrá tisknutelnost.
- Nevýhody: Nižší pevnost ve srovnání s některými dalšími možnostmi.
8. Prášky ze slitin niklu (Rene 41)
- Složení: Superslitina na bázi niklu (Ni) s chromem (Cr), kobaltem (Co), molybdenem (Mo), hliníkem (Al) a dalšími prvky pro vysokoteplotní výkon.
- Vlastnosti: Vynikající pevnost při vysokých teplotách a odolnost proti oxidaci, dobrá odolnost proti tečení. Často se používá jako alternativa k Inconelu 625.
- Aplikace: Součásti proudových motorů, jako jsou turbínové disky a lopatky, vysokoteplotní konstrukční díly.
- Specifikace: Vyžaduje přísnou kontrolu kvality a pro optimální vlastnosti může vyžadovat dodatečné zpracování.
- Dodavatelé: Special Metals Corporation, ATI Allegheny Ludlum, Aubert & Duval
- Cena: Drahý kvůli složitému složení a vysokoteplotním schopnostem.
- Klady: Vynikající vysokoteplotní výkon, dobrá alternativa k Inconelu 625.
- Nevýhody: Drahý, vyžaduje pečlivé postupy tisku.
9. Prášky ze slitin titanu (Ti-6Al-4V ELI)
- Složení: Podobné jako Ti-6Al-4V, ale s ještě nižšími hladinami intersticiálních prvků, jako je kyslík a dusík, pro zlepšenou svařitelnost a odolnost proti únavě.
- Vlastnosti: Vynikající poměr pevnosti k hmotnosti, vynikající svařitelnost a odolnost proti únavě ve srovnání se standardním Ti-6Al-4V, dobrá biokompatibilita.
- Aplikace: Letecké díly vyžadující výjimečné svařování
- Nevýhody: Mírně nižší pevnost ve srovnání se standardním Ti-6Al-4V, může být dražší kvůli přísnějším výrobním požadavkům.
10. Slitiny kobaltu a chromu (CoCr)
- Složení: Slitina kobaltu (Co) a chromu (Cr), známá pro svou biokompatibilitu a odolnost proti opotřebení.
- Vlastnosti: Vynikající odolnost proti opotřebení, dobrá odolnost proti korozi, biokompatibilní (používá se v některých lékařských implantátech).
- Aplikace: Součásti podvozku, díly odolné proti opotřebení, potenciálně pro některé lékařské aplikace v letectví (např. protetické končetiny pro piloty).
- Specifikace: Může vyžadovat specifické parametry tisku pro optimální odolnost proti opotřebení.
- Dodavatelé: AMPA Material, LPW Powder, EOS GmbH
- Cena: Obecně se pohybuje ve středním rozsahu pro kovové prášky.
- Klady: Vynikající odolnost proti opotřebení, dobrá odolnost proti korozi, biokompatibilní.
- Nevýhody: Nemusí být ideální pro vysokozátěžové konstrukční aplikace kvůli svým vlastnostem.
Výběr správného kovového prášku
Jak vidíte, každý kovový prášek se může pochlubit jedinečnými silnými a slabými stránkami. Výběr toho správného závisí na několika faktorech specifických pro každou součást letadla:
- Požadavky na sílu: Vysoce namáhané součásti, jako jsou podvozky nebo turbínové lopatky, budou vyžadovat prášky s výjimečnou pevností, jako jsou titanové nebo niklové superslitiny.
- Zohlednění hmotnosti: U součástí, kde je zásadní snížení hmotnosti, se stávají výhodnými lehké varianty, jako jsou titanové nebo hliníkové slitiny.
- Provozní teploty: Součásti vystavené extrémnímu teplu, jako jsou díly proudových motorů, vyžadují prášky s vynikajícím vysokoteplotním výkonem, jako je Inconel 625 nebo Haynes 282.
- Odolnost proti korozi: Letadla provozovaná v drsných prostředích nebo vystavená slané vodě mohou těžit z prášků s vynikající odolností proti korozi, jako je nerezová ocel nebo některé niklové slitiny.
- Možnost tisku: U některých prášků, jako jsou titanové slitiny, může být tisk náročný kvůli jejich vysokému bodu tání. To je třeba zohlednit během návrhu a výrobního procesu.
Budoucnost 3D tisku kovových prášků ve výrobě letadel
Budoucnost 3D tisku kovových prášků ve výrobě letadel je zářivá. Zde je několik zajímavých trendů, které je třeba sledovat:
- Vývoj nových slitin: Výzkumníci neustále inovují a formulují nové kovové prášky s ještě lepšími vlastnostmi pro specifické aplikace. To povede k lehčím, pevnějším a tepelně odolnějším součástem.
- Tisk z více materiálů: Zkoumá se možnost tisku s více kovovými prášky ve stejné součásti. To otevírá dveře pro díly s přizpůsobenými vlastnostmi v různých oblastech.
- Snížené náklady na prášek: Jak technologie 3D tisku dospívá a objemy výroby se zvyšují, očekává se, že se náklady na kovové prášky sníží, čímž se tato technologie stane dostupnější.
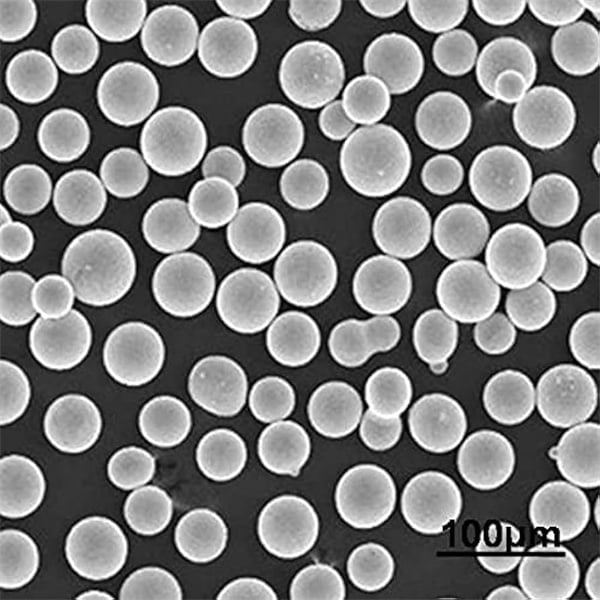
FAQ
Otázka: Jaké jsou výhody použití kovových prášků pro 3D tisk ve výrobě letadel?
Odpověď: 3D tisk nabízí několik výhod, včetně svobody designu, snížení hmotnosti, snížení odpadu a konsolidace dílů. To se promítá do lehčích, palivově účinnějších letadel s potenciálně nižšími výrobními náklady.
Otázka: Jaké jsou některé z problémů spojených s 3D tiskem kovových prášků?
Odpověď: Mezi problémy patří vysoké náklady na některé prášky, tisknutelnost určitých materiálů a potřeba dodatečného zpracování pro optimální výkon v některých případech. Kromě toho je v celém procesu nezbytná přísná kontrola kvality.
Otázka: Jaký je budoucí výhled pro 3D tisk kovových prášků ve výrobě letadel?
Budoucnost vypadá slibně. S probíhajícím výzkumem a vývojem můžeme očekávat ještě lepší kovové prášky, možnosti tisku z více materiálů a snížené náklady, což dále revolučně změní způsob, jakým jsou letadla navrhována a vyráběna.
Sdílet na
MET3DP Technology Co., LTD je předním poskytovatelem řešení aditivní výroby se sídlem v Qingdao v Číně. Naše společnost se specializuje na zařízení pro 3D tisk a vysoce výkonné kovové prášky pro průmyslové aplikace.
Dotaz k získání nejlepší ceny a přizpůsobeného řešení pro vaše podnikání!
Související články
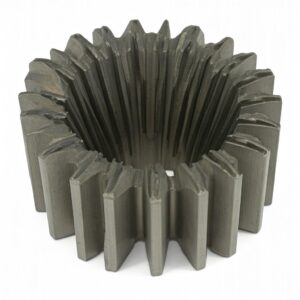
Vysoce výkonné segmenty lopatek trysek: Revoluce v účinnosti turbín díky 3D tisku z kovu
Přečtěte si více "O Met3DP
Nedávná aktualizace
Náš produkt
KONTAKTUJTE NÁS
Nějaké otázky? Pošlete nám zprávu hned teď! Po obdržení vaší zprávy obsloužíme vaši žádost s celým týmem.
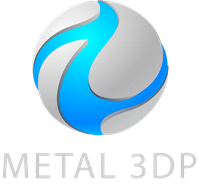
Kovové prášky pro 3D tisk a aditivní výrobu