3D tisk kovového prášku: mechanické legovací zařízení
Obsah
Svět 3D tiskový kovový prášek překonala sféru plastových cetek a figurek a vydala se do sféry robustních kovů, a to díky pokrokům, jako je mechanické slévání. Tento inovativní přístup odemyká potenciál pro navrhování materiálů nové generace s přizpůsobenými vlastnostmi a posouvá hranice toho, co je v aditivní výrobě možné. Ale v zákulisí orchestruje toto kovové stvoření symfonie specializovaného vybavení. Pojďme se ponořit do srdce tohoto procesu a prozkoumat základní nástroje, které dělají mechanické slévání 3D tisku kovového prášku realitou.
Zařízení pro výrobu mechanickou slitinou Kovové prášky pro 3D tisk
Představte si mikroskopický balet, kde jsou elementární částice pečlivě choreograficky uspořádány do soudržného celku. Zařízení pro mechanické slitiny ztělesňuje tento obraz, pečlivě manipuluje se surovinami, aby se dosáhlo požadovaného složení a mikrostruktury. Zde je rozdělení klíčových hráčů:
- Vysokorychlostní kulové mlýny: Představte si ocelovou komoru naplněnou koulemi, které se víří a srážejí silou miniaturního hurikánu. To je podstata vysokorychlostního kulového mlýna. Využitím kombinovaných účinků nárazu, tření a smykové síly tyto pracovní koně rozemelou a smíchají elementární prášky do jednotné směsi. Různé typy mlýnů, jako jsou planetové a attritorové mlýny, nabízejí variace ve zpracovatelském výkonu a charakteristikách prášku.
- Zařízení pro prosévání a klasifikaci: Ne všechny částice jsou stejné. Po vysokorychlostním tanci v kulovém mlýně nastupuje proces třídění. Síta s různými velikostmi ok fungují jako filtry a oddělují požadovaný rozsah velikosti částic od směsi. Tím se zajistí konzistence konečného prášku, což je zásadní pro úspěšný 3D tisk kovového prášku.
- Systémy pro manipulaci a skladování prášku: Představte si žonglování s jemným kovovým prachem. Přesně proto je správná manipulace a skladování životně důležité. Specializované systémy, jako jsou inertní plynové kryty a rukavicové boxy, zajišťují, že prášek zůstane bez kontaminace a vlhkosti, čímž se zachová jeho integrita a tisknutelnost.
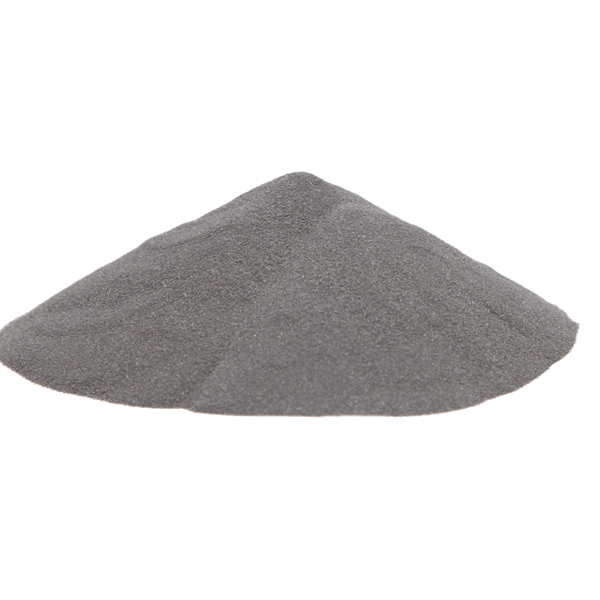
Porovnání výhod a nevýhod různých typů zařízení
Každé zařízení v orchestru mechanických slitin má své vlastní silné a slabé stránky. Pochopení těchto nuancí je zásadní pro informované rozhodování:
Zařízení | Výhody | Nevýhody |
---|---|---|
Vysokorychlostní kulové mlýny | Všestranný, škálovatelný pro různé objemy prášku, vhodný pro širokou škálu materiálů | Vysoká spotřeba energie, možnost kontaminace, pokud není řádně udržován |
Planetové kulové mlýny | Vysoká účinnost broušení, vhodné pro malovýrobu | Omezená kapacita ve srovnání s jinými typy mlýnů |
Attritorové mlýny | Vysoká smyková síla pro efektivní míchání, dobré pro dosažení jemnějších velikostí částic | Složitější konstrukce ve srovnání s jinými mlýny, potenciálně vyšší náklady na údržbu |
Zařízení pro prosévání a klasifikaci | Jednoduchá a spolehlivá metoda pro kontrolu velikosti prášku | Omezená účinnost separace pro velmi jemné prášky |
Inertní plynové kryty | Vynikající kontrola nad atmosférou prášku, minimalizuje rizika kontaminace | Vyžaduje další prostor a infrastrukturu |
V konečném důsledku závisí výběr zařízení na několika faktorech, včetně:
- Požadované složení a vlastnosti prášku: Různé kombinace zařízení by mohly být vhodnější pro dosažení specifických vlastností materiálu.
- Objem výroby: Vysokorychlostní kulové mlýny se starají o větší výrobní potřeby, zatímco planetové mlýny jsou praktičtější pro malé dávky.
- Rozpočet: Složitost a funkčnost zařízení přímo ovlivňují jeho náklady.
Průvodce výběrem zařízení pro mechanické slitiny
Výběr správného zařízení je podobný výběru dokonalých nástrojů pro hudební skladbu. Zde je vodící melodie, která vám pomůže orientovat se v procesu výběru:
- Definujte požadované vlastnosti prášku: Jakého konkrétního složení, velikosti částic a tvaru se snažíte dosáhnout?
- Zvažte svůj objem výroby: Cílíte na maloprojekty nebo velkovýrobu?
- Zhodnoťte svá rozpočtová omezení: Buďte realističtí ohledně finančních prostředků dostupných pro pořízení zařízení.
- Konzultujte s odborníky: Vyhledejte radu zkušených inženýrů a výrobců zařízení, abyste se zorientovali v technických nuancích a zajistili kompatibilitu s vaším celkovým 3D tiskový kovový prášek nastavením.
Pečlivým zvážením těchto faktorů můžete zajistit, aby se výběr vašeho zařízení harmonizoval s vašimi celkovými výrobními cíli a přispěl k úspěšnému vytvoření vysoce výkonných kovových prášků.
Kovové prášky pro mechanické slitiny 3D tiskový kovový prášek
Nyní, když jsme prozkoumali zařízení, zaměřme se na hvězdu show: samotné kovové prášky. Zde je pohled do rozmanité krajiny materiálů, které čekají na odemknutí prostřednictvím mechanických slitin:
1. Prášky z nerezové oceli: Všestranný a široce používaný materiál, který nabízí vynikající odolnost proti korozi a mechanické vlastnosti. Mezi běžné třídy patří 316L a 17-4 PH.
2. Hliníkové slitiny: Lehké a pevné, tyto prášky jsou ideální pro aplikace vyžadující snížení hmotnosti a dobrou obrobitelnost. Mezi oblíbené možnosti patří AlSi10Mg a AlSi7Mg0.3.
3. Slitiny na bázi niklu: Tyto prášky, které nabízejí výjimečnou pevnost při vysokých teplotách a odolnost proti korozi, jsou ideální pro náročné letecké a energetické aplikace. Inconel 625 a Inconel 718 jsou významné příklady.
4. Slitiny kobaltu a chromu: Tyto prášky, známé svou biokompatibilitou a odolností proti opotřebení, se široce používají v lékařských implantátech a zubních aplikacích. CoCrMo a ASTM F75 jsou běžné volby.
6. Nástrojové oceli: Tyto prášky, které poskytují vynikající tvrdost a odolnost proti opotřebení, jsou vhodné pro vytváření odolných nástrojů a forem. H13 a AISI D2 jsou oblíbené možnosti.
7. Slitiny mědi: Tyto prášky, které nabízejí vynikající tepelnou a elektrickou vodivost, jsou vhodné pro aplikace ve výměnících tepla a elektrických součástkách. CuSn6 a CuZn15 jsou často používané příklady.
8. Prášky z žáruvzdorných kovů: Tyto prášky, které vykazují výjimečné vlastnosti při vysokých teplotách a odolnost proti oxidaci, se používají v aplikacích, jako jsou součásti pecí a části raketových motorů. Wolfram a tantal jsou hlavními příklady.
9. Prášky z drahých kovů: Prášky ze zlata, stříbra a platiny nabízejí jedinečné vlastnosti, jako je vysoká elektrická vodivost, odolnost proti korozi a biokompatibilita, díky čemuž jsou vhodné pro specializované aplikace v elektronice, šperkařství a lékařských zařízeních.
10. Amorfní kovové prášky: Tyto prášky, které mají jedinečné vlastnosti, jako je vysoká pevnost, vynikající elasticita a vynikající odolnost proti korozi, otevírají dveře inovativním aplikacím v oblastech, jako jsou transformátory, senzory a sportovní zboží.
Tento seznam pouze škrábe po povrchu obrovského potenciálu, který nabízejí kovové prášky v mechanických slitinách 3D tisku kovového prášku. Jak výzkum a vývoj pokračují v posouvání hranic, můžeme očekávat ještě širší spektrum materiálů, z nichž každý odemyká nové možnosti ve světě aditivní výroby.
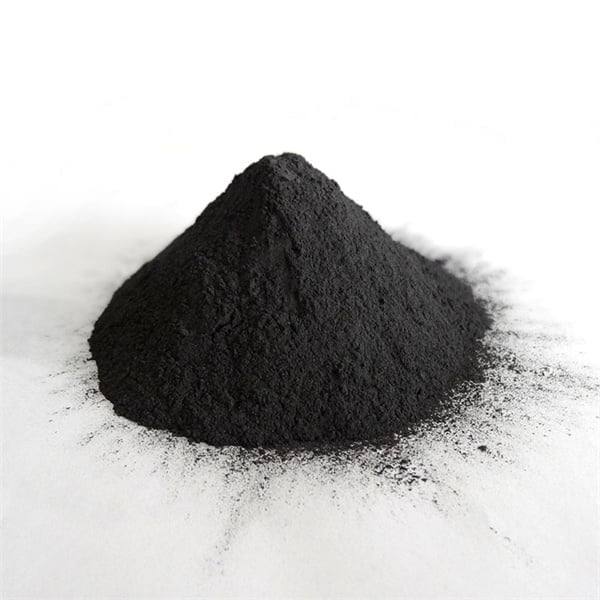
FAQ
1. Jaké jsou výhody mechanických slitin pro 3D tiskový kovový prášek?
Mechanické slitiny nabízejí několik výhod oproti tradičním metodám výroby prášku. Umožňuje:
- Vytváření nových materiálů: Smícháním různých elementárních prášků mohou inženýři vytvářet materiály s jedinečnými vlastnostmi, kterých nelze dosáhnout konvenčními metodami.
- Zlepšená uniformita prášku: Vysokorychlostní proces mletí zajišťuje rovnoměrnější rozložení prvků v částicích prášku, což vede ke konzistentním vlastnostem materiálu a zlepšené tisknutelnosti.
- Jemnější velikosti prášku: Mechanické slitiny mohou dosáhnout jemnějších velikostí prášku ve srovnání s jinými metodami, což může být výhodné pro určité techniky 3D tisku, jako je laserové tavení.
2. Jaká jsou omezení mechanických slitin pro 3D tisk kovových prášků?
Navzdory svým výhodám mají mechanické slitiny také určitá omezení:
- Vysoká spotřeba energie: Proces může být poměrně energeticky náročný, což může být problém pro velkovýrobu a z hlediska environmentální udržitelnosti.
- Možnost kontaminace: Pokud není mlecí zařízení řádně udržováno, může do prášku zavádět kontaminanty, což ovlivňuje jeho kvalitu a tisknutelnost.
- Omezená škálovatelnost: Zvýšení výroby pro velké množství prášku může být náročné a může vyžadovat specializované vybavení.
3. Jaké jsou některé faktory, které je třeba zvážit při výběru kovových prášků pro mechanické slitiny 3D tisku?
Několik faktorů ovlivňuje výběr kovových prášků pro mechanické slitiny:
- Požadované vlastnosti materiálu: Specifické složení a mikrostruktura prášku určí jeho konečné vlastnosti, jako je pevnost, odolnost proti korozi a tepelná vodivost.
- Velikost a morfologie prášku: Velikost a tvar částic prášku významně ovlivňují tisknutelnost a konečné vlastnosti 3D tištěného dílu.
- Náklady a dostupnost: Různé kovové prášky se liší cenou a dostupností, což je třeba zohlednit v celkových výrobních nákladech.
4. Jaká je budoucnost mechanických slitin pro 3D tisk kovových prášků?
Budoucnost mechanických slitin se jeví jako jasná, s probíhajícím výzkumem a vývojem zaměřeným na:
- Vývoj nových a účinnějších procesů mletí: To by mohlo zahrnovat zkoumání alternativních technik mletí nebo optimalizaci stávajících, aby se snížila spotřeba energie a zlepšila účinnost zpracování.
- Rozšíření rozsahu materiálů vhodných pro mechanické slitiny: Výzkumníci neustále zkoumají nové kombinace materiálů, aby odemkli nové vlastnosti a funkčnosti pro aplikace 3D tisku.
- Integrace s pokročilými technologiemi 3D tisku: Jak se techniky 3D tisku vyvíjejí, existuje potenciál pro ještě větší synergii mezi mechanickými slitinami a těmito technologiemi, což vede k vytvoření ještě složitějších a vysoce výkonných dílů.
Pečlivým zvážením těchto faktorů můžete zajistit, aby se výběr vašeho zařízení harmonizoval s vašimi celkovými výrobními cíli a přispěl k úspěšnému vytvoření vysoce výkonných kovových prášků.
Sdílet na
MET3DP Technology Co., LTD je předním poskytovatelem řešení aditivní výroby se sídlem v Qingdao v Číně. Naše společnost se specializuje na zařízení pro 3D tisk a vysoce výkonné kovové prášky pro průmyslové aplikace.
Dotaz k získání nejlepší ceny a přizpůsobeného řešení pro vaše podnikání!
Související články
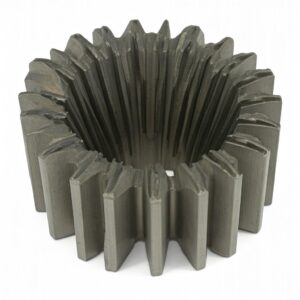
Vysoce výkonné segmenty lopatek trysek: Revoluce v účinnosti turbín díky 3D tisku z kovu
Přečtěte si více "O Met3DP
Nedávná aktualizace
Náš produkt
KONTAKTUJTE NÁS
Nějaké otázky? Pošlete nám zprávu hned teď! Po obdržení vaší zprávy obsloužíme vaši žádost s celým týmem.
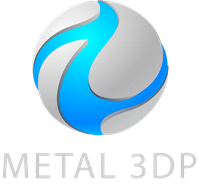
Kovové prášky pro 3D tisk a aditivní výrobu