3D tisk hliníkových kloubů řízení pro odlehčení
Obsah
Úvod: Revoluce v automobilových komponentech díky 3D tištěným hliníkovým kloubům řízení
Automobilový průmysl prochází neustálým vývojem, který je poháněn neustálými požadavky na lepší výkon, vyšší palivovou účinnost, přísné bezpečnostní normy a seismický posun směrem k elektrifikaci. Srdcem dynamiky vozidla je systém odpružení a řízení, jehož součásti musí s pečlivou přesností vyvažovat pevnost, odolnost a hmotnost. Mezi tyto kritické součásti patří kloub řízení, důležitý článek spojující řízení, odpružení a brzdový systém s nábojem kola. Klouby řízení, které se tradičně vyrábějí odléváním nebo kováním, čelí přirozeným omezením v oblasti složitosti konstrukce a optimalizace hmotnosti. S příchodem výroba aditiv kovů (AM), běžně známý jako kov 3D tisk, zahajuje novou éru takovýchto komponentů, zejména díky použití pokročilých hliníkových slitin. Tato technologie umožňuje konstruktérům nově pojímat konstrukci kloubů řízení a uvolňuje dosud nevídanou úroveň odlehčení a optimalizace výkonu, která byla dříve nedosažitelná.
Co je to kloub řízení?
Než se pustíme do transformačního potenciálu 3D tisku, uveďme základní roli kloubu řízení. Kloub řízení, označovaný také jako stojan nebo nosič náboje, je klíčovou součástí podvozkového systému vozidla. Mezi jeho základní funkce patří:
- Pouzdro náboje kola/nosiče: Poskytuje bezpečný montážní bod pro sestavu náboje kola a umožňuje volné otáčení kola.
- Spojovací součásti zavěšení: Slouží jako upevňovací bod pro horní a dolní řídicí ramena (nebo vzpěru MacPherson) a spojuje systém zavěšení se soustavou kol.
- Propojení součástí řízení: Koncovka spojovací tyče se připojuje k čepu řízení a převádí pokyny řidiče k řízení na úhlový pohyb kola.
- Montáž brzdových komponentů: Brzdový třmen a rotor se obvykle montují přímo na kloub řízení.
Vzhledem k těmto kritickým funkcím musí kloub řízení odolávat značnému dynamickému zatížení, včetně zatáčecích sil, brzdného momentu, nárazů od nerovností vozovky a statické hmotnosti vozidla. Proto jsou jeho strukturální integrita, tuhost a odolnost proti únavě nejdůležitější pro bezpečnost a jízdní vlastnosti vozidla.
Tradiční výroba: Výzvy a omezení
Po desetiletí se klouby řízení vyráběly převážně pomocí zavedených výrobních postupů:
- Obsazení: Roztavený kov (obvykle litina nebo slitina hliníku) se nalije do formy ve tvaru požadovaného kloubu. Odlévání je sice nákladově efektivní pro velkosériovou výrobu, ale často vede k těžším dílům kvůli konstrukčním omezením nutným pro naplnění a ztuhnutí formy. Dosažení složitých vnitřních struktur nebo vysoce optimalizovaných geometrií je obtížné a problémem může být pórovitost, která může mít vliv na pevnost.
- Kování: Kovový polotovar se zahřívá a tvaruje pod obrovským tlakem pomocí lisovacích forem. Kováním se obecně vyrábějí díly s vynikajícími pevnostními a únavovými vlastnostmi díky zjemněné struktuře zrn. Kovací nástroje jsou však drahé, takže jsou méně vhodné pro malosériovou až středně velkosériovou výrobu nebo časté iterace konstrukce. Tento proces také nabízí menší konstrukční volnost ve srovnání s odléváním nebo AM, často vyžaduje značné dodatečné obrábění pro dosažení konečných rozměrů a vlastností.
Obě tradiční metody se potýkají s problémy, pokud jde o odlehčení - kritický cíl v moderním automobilovém designu. Snížení neodpružené hmotnosti (hmotnost součástí, které nejsou neseny odpružením, včetně kol, pneumatik, brzd a kloubů) výrazně zlepšuje ovladatelnost vozidla, jízdní komfort, zrychlení a spotřebu paliva (nebo dojezd na baterie u elektromobilů). Každý ušetřený kilogram neodpružené hmoty se z hlediska dynamických vlastností může jevit jako několik kilogramů ušetřené odpružené hmoty. Dosažení výrazného snížení hmotnosti u konstrukčně kritického dílu, jako je kloub řízení, pomocí odlévání nebo kování však často vyžaduje kompromisy v pevnosti nebo vyžaduje použití dražších materiálů a složitých a nákladných kroků zpracování. Optimalizace konstrukce je omezena omezeními spojenými s tvorbou formy nebo zápustkovým kováním.
Příchod aditivní výroby (AM)
3D tisk kovů, zejména Laserová fúze v práškovém loži (LPBF) - známý také jako selektivní laserové tavení (SLM) - nabízí radikální odklon od těchto tradičních omezení. LPBF vytváří díly vrstvu po vrstvě přímo z digitálního modelu CAD selektivním tavením jemných částic kovového prášku pomocí vysoce výkonného laseru. Tento proces zásadně mění paradigma designu.
- Svoboda designu: Konstruktéři již nejsou vázáni omezeními forem nebo zápustek. Složité geometrie, složité vnitřní kanály (např. pro chlazení nebo hydraulické vedení) a vysoce optimalizované, topologicky řízené tvary se stávají proveditelnými.
- Potenciál odlehčení: AM umožňuje optimalizace topologie, kde softwarové algoritmy určují nejefektivnější rozložení materiálu pro splnění konkrétních požadavků na zatížení. To umožňuje vytvářet skeletové, organicky vypadající konstrukce, které minimalizují hmotnost při zachování nebo dokonce zvýšení tuhosti a pevnosti ve srovnání s jejich tradičně vyráběnými protějšky.
- Materiálové možnosti: AM otevírá dveře k použití pokročilých slitin, které by bylo obtížné nebo nemožné efektivně odlévat nebo kovat. Patří sem vysokopevnostní hliníkové slitiny speciálně navržené pro náročné aplikace.
- Rapid Prototyping & Iterace: Nové konstrukce kloubů řízení lze prototypovat a testovat mnohem rychleji a hospodárněji než tradičními metodami vyžadujícími nákladné nástroje. To urychluje vývojový cyklus a umožňuje větší zdokonalení konstrukce.
Zaměření na odlehčování hliníku
Hliníkové slitiny jsou pro klouby řízení obzvláště atraktivní díky vynikajícímu poměru pevnosti a hmotnosti. Ačkoli se hliníkové klouby již používají v mnoha vozidlech (často odlévané nebo kované), AM umožňuje ještě větší úsporu hmotnosti. Kombinací přirozené nízké hustoty hliníku s konstrukční svobodou 3D tisku a optimalizací topologie mohou konstruktéři dosáhnout snížení hmotnosti o 30-50 % nebo i více ve srovnání s tradičními ocelovými nebo dokonce optimalizovanými hliníkovými odlitky, aniž by byla ohrožena strukturální integrita. To má zásadní význam zejména pro:
- Elektrická vozidla (EV): Snížení celkové hmotnosti vozidla má zásadní význam pro maximalizaci dojezdu na baterie. Odlehčení komponentů, jako jsou klouby řízení, k tomuto cíli přímo přispívá.
- Výkonná vozidla: Snížení neodpružené hmotnosti výrazně zlepšuje odezvu při řízení, přilnavost a brzdný výkon.
- Motorsport: Každý gram se počítá a 3D tištěné hliníkové klouby nabízejí konkurenční výhodu díky optimalizované hmotnosti a přizpůsobené geometrii.
Společnosti, které stojí v čele aditivní výroby kovů, jako např Met3dp, hrají při tomto přechodu klíčovou roli. Díky zkušenostem s pokročilou práškovou výrobou i průmyslovými systémy 3D tisku poskytuje společnost Met3dp základní technologie nezbytné pro realizaci těchto automobilových komponent nové generace. Jejich zaměření na vysoce kvalitní sférické kovové prášky, vyráběné pomocí pokročilých technik plynové atomizace, zajišťuje konzistenci a vlastnosti materiálu, které jsou potřebné pro kritické díly, jako jsou například klouby řízení. Schopnost využívat slitiny, jako je AlSi10Mg a vysokopevnostní A7075, prostřednictvím procesů AM umožňuje automobilovým inženýrům a manažerům nákupu posouvat hranice výkonnosti a efektivity vozidel. Integrace AM do dodavatelského řetězce umožňuje distributorům a velkoobchodním dodavatelům automobilových součástek nabízet svým zákazníkům špičková, odlehčená řešení, která splňují vyvíjející se požadavky trhu.
Souhrnně lze říci, že použití kovového 3D tisku, konkrétně s využitím hliníkových slitin, jako jsou AlSi10Mg a A7075, představuje významný skok vpřed v konstrukci a výrobě kloubů řízení. Překračuje rámec postupných vylepšení, která nabízejí tradiční metody, a umožňuje vyrábět skutečně optimalizované, lehké součásti, které přímo přispívají k bezpečnějším, efektivnějším a výkonnějším vozidlům.
Základní aplikace: Kde jsou 3D tištěné klouby řízení hnacím motorem inovací?
Jedinečné výhody, které nabízí aditivní výroba kovů, zejména nízká hmotnost a svoboda designu, činí z hliníkových kloubů řízení vytištěných 3D tiskem přesvědčivé řešení pro různé segmenty automobilového průmyslu. Ačkoli zatím nejsou kvůli nákladům všudypřítomné v sériové výrobě, jejich uplatnění se rychle rozšiřuje v oblastech, kde je nejdůležitější výkon, přizpůsobení a rychlý vývoj. Tyto aplikace ukazují hmatatelné výhody a zdůrazňují trajektorii širšího přijetí, jak technologie dozrává a náklady se snižují. Mezi klíčové oblasti, které z této inovace těží, patří výkonná vozidla, elektromobily (EV), prototypy a vývoj a specializované nebo zakázkové stavby vozidel. Pochopení těchto aplikací je klíčové pro automobilové inženýry, kteří zkoumají pokročilé materiály, manažery nákupu, kteří hledají inovativní dodavatele komponentů, a dodavatele automobilového průmyslu prvního řádu, kteří usilují o integraci nejmodernějších technologií.
1. Vysoce výkonná vozidla a motoristický sport:
To je v současnosti pravděpodobně nejvýznamnější a nejvlivnější oblast použití 3D tištěných kloubů řízení. V motoristickém sportu a u vysoce výkonných silničních automobilů je snaha o dosažení nižších časů na kolo, lepší dynamiky řízení a konkurenční výhody ospravedlněním vyšších počátečních nákladů na komponenty AM.
- Extrémní odlehčení: Jak již bylo zmíněno, snížení neodpružené hmotnosti má zásadní význam pro jízdní vlastnosti. Topologicky optimalizované hliníkové klouby vytištěné na 3D tiskárně mohou výrazně snížit hmotnost ve srovnání i s těmi nejdokonalejšími kovanými hliníkovými díly, což vede k rychlejší odezvě odpružení, lepšímu kontaktu pneumatik s vozovkou, lepší přilnavosti v zatáčkách a účinnějšímu brzdění. Týmy a výrobci tak mohou získat měřitelnou výkonnostní výhodu.
- Geometrie na míru: Systém AM umožňuje přizpůsobit geometrii kloubu specifickým kinematickým vlastnostem zavěšení, rozměrům pneumatik, brzdovým sadám a aerodynamickým požadavkům. Body zdvihu zavěšení lze přesně umístit pro optimální nárůst odklonu, výšku středu náklonu a sklon osy řízení (SAI), čímž lze vyladit jízdní vlastnosti vozidla s takovou přesností, jaké lze obtížně dosáhnout metodami založenými na nástrojích.
- Integrované funkce: Chladicí kanály pro brzdy mohou být integrovány přímo do konstrukce kloubu, což zlepšuje výkon brzd a snižuje jejich ochabování při náročném používání na trati. Bezproblémově lze začlenit také montážní body snímačů.
- Rychlá iterace: Týmy motoristického sportu pracují v napjatých termínech. AM umožňuje rychlé změny designu a výrobu aktualizovaných kloubů mezi závody nebo testováním, což umožňuje neustálé zlepšování výkonu. Výrobce kloubů řízení specializující se na AM může dodat prototypy v řádu dnů, nikoli týdnů či měsíců.
Příklad scénáře: Závodní tým GT potřebuje optimalizovat geometrii předního zavěšení pro konkrétní trať. Pomocí softwaru pro optimalizaci topologie a tisku LPBF s vysokopevnostní hliníkovou slitinou, jako je A7075, navrhnou a vyrobí klouby, které jsou o 40 % lehčí než předchozí kované verze a mají upravené body zdvihu. Výsledkem je lepší přilnavost pneumatik a kratší časy na kolo.
2. Elektrická vozidla (EV): Dojezd a účinnost
Přechod na elektrickou mobilitu představuje jedinečné technické výzvy, které se soustředí především na hmotnost baterií a maximalizaci dojezdu. Odlehčení už není jen o výkonu, ale je základem životaschopnosti vozidla.
- Kompenzace hmotnosti baterie: Baterie jsou těžké. Snížení hmotnosti v jiných částech vozidla, zejména neodpružené hmotnosti, pomáhá kompenzovat hmotnost akumulátoru, zlepšuje celkovou účinnost a prodlužuje dojezd. Lehčí klouby přímo přispívají ke snížení spotřeby energie vozidla’(kWh/100 km nebo kWh/km).
- Vylepšená dynamika: I když je dojezd klíčový, elektromobily těží také z lepších jízdních vlastností. Okamžitý točivý moment elektromotorů vyžaduje systém odpružení, který dokáže účinně řídit síly. Lehčí klouby zlepšují dynamické reakce elektromobilů a přispívají k poutavějšímu zážitku z jízdy.
- Omezení při balení: Platformy pro elektromobily mají často jedinečné požadavky na balení kvůli umístění baterie a integraci elektromotoru. Volnost konstrukce AM umožňuje klouby tvarovat podle těchto omezení snadněji než tradiční komponenty.
- Úvahy o NVH: Lehčí součásti mohou někdy měnit charakteristiky hluku, vibrací a drsnosti (NVH). AM umožňuje konstrukce, které jsou optimalizovány nejen z hlediska hmotnosti a pevnosti, ale potenciálně i z hlediska specifických charakteristik tlumení nebo frekvenční odezvy, což pomáhá zvládat NVH u tichých elektrických pohonných jednotek.
Příklad scénáře: Výrobce elektromobilů vyvíjí novou platformu a usiluje o nejlepší dojezd ve své třídě. Použitím 3D tištěných kloubů řízení z AlSi10Mg (optimalizovaných na základě topologických studií) na celé platformě dosáhli výrazného snížení neodpružené hmotnosti, což přispělo k měřitelnému zvýšení dojezdu vozidla podle EPA nebo WLTP ve srovnání s použitím konvenčních litých hliníkových kloubů. To se stává klíčovým prodejním argumentem, který podporují jejich distributoři automobilových komponent.
3. Vývoj prototypů a vozidel:
Než se výrobci automobilů rozhodnou pro nákladné nástroje pro sériovou výrobu (odlévací formy nebo kovací formy), procházejí důkladnou fází prototypování a testování. AM je v této fázi neocenitelným nástrojem.
- Zrychlené vývojové cykly: Vytváření funkčních kovových prototypů kloubů řízení pomocí AM je výrazně rychlejší než tradiční metody prototypování zahrnující rozsáhlé obrábění nebo dočasné nástroje. Návrhy lze fyzicky realizovat a testovat na prototypech vozidel během několika dnů nebo týdnů.
- Nákladově efektivní iterace: Pokud testování odhalí potřebu úprav konstrukce (např. zesílení určité oblasti, úprava bodu zavěšení), lze provést změny v modelu CAD a relativně rychle a levně vytisknout nový prototyp. Tím se vyhnete utopeným nákladům spojeným s úpravou nebo vyřazením pevných nástrojů.
- Včasné ověření výkonu: Prototypy AM, zejména ty vytištěné z cílového materiálu (např. AlSi10Mg nebo A7075), umožňují inženýrům ověřit výkonnostní charakteristiky (tuhost, kontroly vůlí, počáteční únavové zkoušky) v rané fázi vývojového procesu, čímž se snižují rizika předtím, než se přikročí k metodám sériové výroby.
- Testování více variant návrhu: AM umožňuje vyrábět a testovat několik konstrukčních variant kloubu řízení současně, což inženýrům umožňuje empiricky porovnat různé optimalizační strategie nebo kinematická řešení.
Příklad scénáře: Výrobce automobilů vyvíjí novou platformu pro SUV. Ve fázi vývoje podvozku používají LPBF k tisku několika iterací předního kloubu řízení z AlSi10Mg, přičemž testují různé vzory žeber a tloušťky stěn odvozené z optimalizace topologie. To jim umožňuje mnohem rychleji a s větší jistotou dokončit lehkou a zároveň robustní konstrukci pro sériovou výrobu (která může být nakonec odlévaná nebo kovaná, ale na základě optimální geometrie ověřené pomocí AM). Spolupracují s poskytovatelem služeb AM, který je schopen rychle dodat vysoce kvalitní prototypy.
4. Niche Vehicles, Custom Builds a Aftermarket:
Pro malosériovou výrobu, zakázková vozidla nebo trh s náhradními díly jsou náklady na tradiční nástroje často neúnosné. AM představuje životaschopné výrobní řešení.
- Výroba bez použití nástrojů: AM eliminuje potřebu drahých forem nebo lisovacích forem, takže je ekonomicky výhodné vyrábět malé série (desítky nebo stovky) kloubů řízení pro limitované edice vozidel, zakázkové stavby nebo modernizace pro trh s náhradními díly.
- Vysoká míra přizpůsobení: Systém AM umožňuje vytvářet jedinečné, na míru šité konstrukce kloubů přizpůsobené specifickým úpravám vozidla, jako je přizpůsobení větším brzdám, různým nastavením zavěšení nebo neobvyklým posunům kol, což vyhovuje potřebám výrobců speciálních vozidel a trhu výkonnostního tuningu.
- Výměna staršího dílu: U klasických nebo vzácných vozidel, u nichž již neexistuje původní nářadí, nabízí společnost AM možnost zpětného inženýrství a repasování zastaralých kloubů řízení, díky čemuž mohou tato vozidla nadále jezdit.
Příklad scénáře: Společnost specializující se na restaurování a modernizaci klasických sportovních vozů potřebuje silnější a lehčí klouby řízení, které by zvládly moderní přilnavost pneumatik a zvýšení výkonu motoru. Originální díly nejsou k dispozici nebo jsou nedostatečné. Spolupracuje se specialistou na zpracování kovů metodou AM, jako je Met3dp, který navrhuje a vyrábí topologicky optimalizované klouby A7075 v malých sériích a nabízí je svým zákazníkům jako prémiový balíček pro modernizaci. To je staví do pozice inovativního dodavatele na trhu restaurování.
Důsledky pro dodavatele a distributory automobilového průmyslu první úrovně:
Rozvoj AM v těchto aplikacích signalizuje změnu v dodavatelském řetězci automobilového průmyslu. Dodavatelé Tier 1 a distributoři automobilových komponentů si musí uvědomit potenciál AM:
- Nové nabídky služeb: Dodavatelé mohou využívat možnosti technologie AM pro rychlou výrobu prototypů, malosériovou výrobu a vysoce optimalizované lehké komponenty.
- Konkurenční výhoda: Nabídka dílů vyráběných metodou AM může dodavatele na trhu odlišit a přilákat zákazníky, kteří hledají špičková řešení, zejména v odvětví výkonných a elektrických vozidel.
- Přizpůsobení strategií získávání zdrojů: Manažeři veřejných zakázek v těchto společnostech musí najít spolehlivé partnery a spolupracovat s nimi poskytovatelé služeb kovového 3D tisku a dodavatelé vysoce kvalitního hliníkového prášku jako je Met3dp, které disponují potřebnými odbornými znalostmi, technologiemi (jako jsou pokročilé tiskárny LPBF) a systémy kontroly kvality (např. důkladná analýza prášku, monitorování procesů), které jsou nezbytné pro výrobu automobilových dílů kritických z hlediska bezpečnosti. Budování vztahů s velkoobchodní prodej 3D tištěných dílů poskytovatelé se stávají strategicky důležitými.
Závěrem lze říci, že aplikace 3D tištěných hliníkových kloubů řízení pokrývají kritické oblasti automobilového průmyslu, od náročného světa motoristického sportu přes trh s elektromobily zaměřený na efektivitu až po flexibilní potřeby prototypování a specializované výroby. S dalším rozvojem a rozšiřováním této technologie bude její úloha při utváření budoucnosti automobilových komponent jen růst, a proto je nezbytné, aby zúčastněné strany napříč hodnotovým řetězcem pochopily její možnosti a zapojily se do nich.
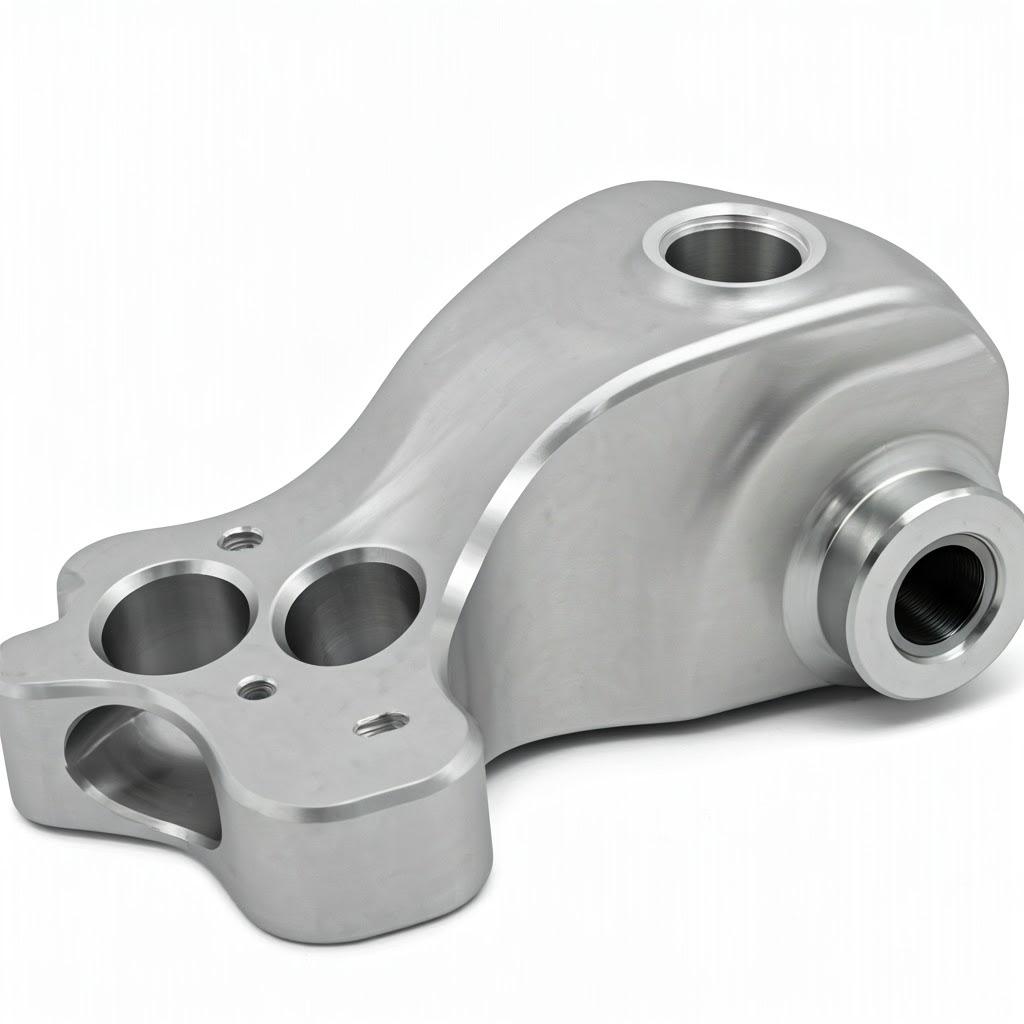
Výhoda AM: Proč zvolit 3D tisk kovů pro výrobu kloubů řízení?
Zatímco tradiční metody, jako je odlévání a kování, již dlouho slouží automobilovému průmyslu k výrobě kloubů řízení, aditivní výroba kovů (AM) představuje přesvědčivý soubor výhod, které přímo reagují na vyvíjející se požadavky na vyšší výkon, vyšší efektivitu a rychlejší vývojové cykly. Volba AM, konkrétně technologie Laser Powder Bed Fusion (LPBF), pro výrobu kloubů řízení neznamená pouze přijetí nové technologie, ale využití výrazných výhod, které se promítají do hmatatelného zlepšení konečného výrobku a výrobního procesu. Pochopení těchto výhod je zásadní pro konstruktéry navrhující vozidla nové generace, manažery nákupu, kteří vyhodnocují možnosti zásobování, a distributory automobilových součástek, kteří hledají inovativní výrobky.
Porovnejme AM s tradičním odléváním a kováním kloubů řízení a zdůrazněme hlavní důvody, proč AM vyniká:
1. Bezkonkurenční volnost designu & Komplexnost:
- Tradiční metody: Odlévání vyžaduje úhly tahu pro vyjmutí formy, omezení vnitřních prvků a relativně stejnou tloušťku stěn. Kování tvaruje kov pod tlakem a omezuje konstrukce na to, co lze prakticky vytvarovat mezi zápustkami, což často vede k jednodušším a objemnějším geometriím vyžadujícím rozsáhlé následné obrábění.
- AM (LPBF): Vytváří díly vrstvu po vrstvě, čímž osvobozuje konstruktéry od mnoha tradičních omezení. To umožňuje:
- Složité geometrie: Možné jsou složité vnitřní mřížky, duté struktury a organicky tvarované, topologicky optimalizované formy.
- Záporné úhly návrhu: Prvky, které by nebylo možné odlít při odlévání, lze snadno vytvořit.
- Podřezání & Vnitřní kanály: Složité vnitřní kanály pro chlazení, hydrauliku nebo integraci senzorů lze navrhnout přímo do dílu.
- Tenké stěny & amp; Jemné funkce: Větší přesnost při vytváření tenkých konstrukčních prvků a jemných detailů, což přispívá ke snížení hmotnosti.
- Výhoda: AM umožňuje inženýrům navrhovat optimální kloubu řízení na základě požadavků na výkon (napětí, tuhost, průběh zatížení), nikoliv na základě omezení výrobního procesu. To vede ke konstrukcím, které jsou skutečně optimalizované z hlediska funkce a hmotnosti.
2. Významné odlehčení pomocí optimalizace topologie:
- Tradiční metody: Snížení hmotnosti obvykle zahrnuje přechod na lehčí materiály (např. hliník místo železa) nebo rozsáhlé, často opakované obrábění po odlití/vykovení. Optimalizace je často založena na inženýrské intuici a standardní analýze konečných prvků (FEA), omezené výrobním procesem.
- AM (LPBF): Perfektně se hodí pro optimalizace topologie. Tento výpočetní proces využívá metodu konečných prvků pro simulaci zatížení dílu a poté inteligentně odstraní materiál z nekritických oblastí, čímž vznikne optimalizovaná nosná konstrukce.
- Organické struktury: Výsledky se často podobají přirozeným kostním strukturám - jsou vysoce účinné a lehké.
- Cílená tuhost: Materiál je umístěn přesně tam, kde je to potřeba k dosažení požadovaných hodnot tuhosti a pevnosti.
- Dramatická úspora hmotnosti: Jak již bylo uvedeno, ve srovnání s tradičními konstrukcemi lze dosáhnout snížení hmotnosti o 30-50 % nebo více, což má přímý dopad na neodpruženou hmotnost a výkon/účinnost vozidla.
- Výhoda: AM umožňuje matematicky optimalizované odlehčování, které je mnohem vyšší než u odlévání nebo kování, a přímo tak reaguje na klíčovou hnací sílu automobilového průmyslu. A výrobce kloubů řízení pomocí AM lze nabídnout výrazně lehčí díly, aniž by byla ohrožena bezpečnost.
3. Konsolidace částí:
- Tradiční metody: Složité sestavy často vyžadují výrobu několika jednotlivých součástí (odlitků, výkovků, obráběných dílů, konzol), které je třeba vyrobit odděleně a následně je spojit (svařením, šroubováním). Každý spoj zvyšuje hmotnost, potenciální místa poruchy a čas/náklady na montáž.
- AM (LPBF): Volnost konstrukce umožňuje konstruktérům sloučit více dílů do jediné monolitické součásti. Například montážní držáky pro senzory nebo brzdové vedení, které by za normálních okolností mohly být samostatnými díly, lze integrovat přímo do konstrukce 3D tištěného kloubu řízení.
- Snížený počet dílů: Zjednodušuje skladování, logistiku a montáž.
- Zvýšená strukturální integrita: Eliminuje spoje, které jsou často místem koncentrace napětí.
- Snížená hmotnost: Eliminuje spojovací prvky a překrývání materiálu ve spojích.
- Zjednodušený dodavatelský řetězec: Menší počet jednotlivých komponent, které je třeba zajistit a spravovat.
- Výhoda: AM zjednodušuje celý systém, což může snížit výrobní a montážní náklady, zvýšit spolehlivost a dále přispět ke snížení hmotnosti. To je významným přínosem pro výrobci automobilových dílů se snaží zefektivnit výrobu.
4. Rychlé prototypování a zrychlený vývoj:
- Tradiční metody: Vytváření prototypů často vyžaduje nákladné dočasné nástroje (měkké formy) nebo rozsáhlé CNC obrábění ze sochorů, což vyžaduje značný čas (týdny nebo měsíce) a náklady. Iterace návrhu vyžadují úpravu nebo znovuvytvoření tohoto nástroje/procesu.
- AM (LPBF): Prototypy lze vytisknout přímo z dat CAD během několika dní.
- Rychlost: Výrazně zkracuje dobu od návrhu konceptu k fyzickému, testovatelnému dílu.
- Nákladově efektivní iterace: Změny se provedou v systému CAD a nový díl se vytiskne bez nákladů na úpravu nástrojů. Lze rychle testovat více variant konstrukce.
- Funkční prototypy: Prototypy lze vytisknout z konečného zamýšleného materiálu (např. AlSi10Mg, A7075), což umožňuje reálné funkční testování v rané fázi vývojového cyklu.
- Výhoda: AM významně zkracuje časový plán vývoje vozidla, umožňuje důkladnější zkoumání a ověřování konstrukce a snižuje finanční rizika spojená s příliš brzkým závazkem k výrobě pevných nástrojů. Tato pružnost je v rychlém automobilovém průmyslu neocenitelná.
5. Eliminace/snížení nákladů na nástroje:
- Tradiční metody: Vyžadují značné počáteční investice do specializovaných nástrojů:
- Obsazení: Složité formy a jádra.
- Kování: Kalené ocelové matrice.
- Náklady na nástroje se mohou vyšplhat na desítky až stovky tisíc dolarů, což je pro malé objemy nebo časté změny designu neekonomické. Nástroje také vyžadují údržbu a skladování.
- AM (LPBF): Proces bez použití nástrojů”. Složitost je obsažena v souboru digitálního návrhu a v samotném stroji AM.
- Žádné vyhrazené nástroje: Eliminuje vysoké počáteční investice a dlouhé dodací lhůty spojené s výrobou forem nebo zápustek.
- Ekonomické pro malé až střední objemy: Umožňuje ekonomicky výhodnou výrobu specifických dílů, zakázkových komponent, prototypů a malých sérií.
- Flexibilita designu: Návrhy lze měnit bez jakýchkoli nákladů na nástroje.
- Výhoda: AM výrazně snižuje vstupní bariéru pro výrobu kloubů řízení na zakázku nebo v malých sériích a umožňuje finančně realizovat změny designu v průběhu celého životního cyklu výrobku. To přináší výhody velkoobchodní prodej 3D tištěných dílů dodavatelé a jejich zákazníci vyžadující flexibilitu.
Srovnávací souhrnná tabulka:
Vlastnosti | Aditivní výroba kovů (LPBF) | Tradiční casting | Tradiční kování |
---|---|---|---|
Svoboda designu | Velmi vysoká (složitá geometrie, vnitřní prvky) | Mírné (úhly ponoru, tloušťka stěny) | Nízká (jednodušší tvary, vyžaduje obrábění) |
Odlehčení | Vynikající (optimalizace topologie, mřížky) | Mírná (výběr materiálu, základní žebra) | Omezené (výběr materiálu, obrábění) |
Konsolidace částí | Vysoký potenciál | Omezený | Velmi omezené |
Rychlost prototypování | Velmi rychle (dny) | Pomalé (týdny/měsíce – obrábění/obrábění) | Pomalé (týdny/měsíce – obrábění/obrábění) |
Náklady na iteraci | Nízká (změny CAD) | Vysoký (úprava/přepracování nástrojů) | Velmi vysoká (nové matrice/modifikace) |
Náklady na nástroje | Žádné (digitální) | Vysoká (formy, jádra) | Velmi vysoká (Dies) |
Ekonomika svazku | Nejlepší pro malé až střední objemy, prototypy | Nejlepší pro velké objemy | Nejlepší pro velmi vysoké objemy (jednodušší díly) |
Materiálový odpad | Nízká (recyklace prášku) | Středně těžká (Běžci, brány) | Mírná (blesk, odpad z obrábění) |
Min. Velikost funkce | Vysoké rozlišení | Omezeno procesem odlévání | Omezeno procesem kování & obrábění |
Export do archů
Zvažování role Met3dp’:
Výběr AM vyžaduje spolupráci se schopným poskytovatelem. Společnost Met3dp se svými dvojími odbornými znalostmi v oblasti vysoce výkonných technologií 3D tisk z kovu systémy a výroba prémiových kovových prášků ztělesňuje výhodu AM. Jejich pokročilé tiskárny jsou navrženy pro přesnost a spolehlivost potřebnou pro kritické komponenty, jako jsou například klouby řízení. Kromě toho jejich vlastní výroba optimalizovaných hliníkových prášků (jako je AlSi10Mg a případně vlastní varianty) zajišťuje kvalitu materiálu nezbytnou pro dosažení požadovaných mechanických vlastností a výkonnostních výhod, které AM slibuje. Spolupráce s vertikálně integrovanou společností, jako je Met3dp, zefektivňuje proces od poradenství při výběru materiálu až po finální výrobu dílů, čímž zajišťuje plné využití všech výhod AM.
Závěrem lze říci, že zatímco odlévání a kování zůstávají relevantní pro určité velkoobjemové a zavedené konstrukce, AM z kovu nabízí transformační výhody v oblasti svobody konstrukce, odlehčení, konsolidace dílů, rychlosti vývoje a ekonomické flexibility, zejména u hliníkových kloubů řízení v aplikacích pro výkon, EV a prototypování. Tyto výhody jsou pro výrobce a dodavatele automobilů pádným důvodem, proč začlenit AM do svých výrobních strategií.
Zaměření materiálu: Výběr optimálních hliníkových slitin (AlSi10Mg & A7075) pro klouby řízení
Úspěch 3D tištěného kloubu řízení závisí především na volbě materiálu. Ačkoli aditivní výroba kovů otevírá dveře široké škále slitin, hliníkové slitiny pro tuto aplikaci vynikají díky své přirozené nízké hustotě a dobrým mechanickým vlastnostem. V rámci hliníkové rodiny se často uvažuje o dvou slitinách, které se používají pro náročné konstrukční součásti, jako jsou například klouby řízení, a to prostřednictvím laserové fúze v práškovém loži (LPBF): AlSi 10Mg a A7075 (často varianta zpracovaná AM). Pochopení specifických vlastností, silných a slabých stránek těchto materiálů a jejich zpracování je pro konstruktéry, kteří navrhují díl, a pro manažery nákupu, kteří nakupují z těchto materiálů, zásadní dodavatelé hliníkového prášku nebo poskytovatelé služeb AM.
Proč hliník? Nutnost odlehčení
Hlavní předností hliníku je jeho hustota, která je zhruba třetinová ve srovnání s ocelí, a přitom má stále slušnou pevnost, zejména v legovaných formách a po vhodném tepelném zpracování. Tato nízká hustota je základem snah o odlehčení, jejichž cílem je snížit neodpruženou hmotnost, zlepšit palivovou/energetickou účinnost a zlepšit dynamiku vozidla. Hliníkové slitiny také obecně nabízejí dobrou odolnost proti korozi a obrobitelnost.
AlSi10Mg: Hliníková slitina pro AM: pracovní kůň
AlSi10Mg je jednou z nejběžnějších a nejpoužívanějších hliníkových slitin používaných v kovové AM, zejména v LPBF. Je to v podstatě slitina odlitků upravená pro aditivní procesy. Její složení obvykle obsahuje ~9-11 % křemíku (Si) a 0,2-0,45 % hořčíku (Mg).
- Klíčové vlastnosti & Charakteristika:
- Vynikající zpracovatelnost: AlSi10Mg se během procesu LPBF chová velmi dobře. Obsah křemíku zlepšuje tekutost v bazénu taveniny a snižuje rozsah tuhnutí, čímž minimalizuje riziko vzniku trhlin za tepla během rychlých cyklů ohřevu a chlazení, které jsou pro AM typické. Díky tomu lze relativně snadno tisknout husté a vysoce kvalitní díly.
- Dobrý poměr pevnosti a hmotnosti: Ve stavu po vytištění vykazuje střední pevnost. Dobře však reaguje na tepelné zpracování (obvykle cyklus T6: tepelné zpracování roztokem a následné umělé stárnutí). Po tepelném zpracování T6 dosahuje AlSi10Mg mechanických vlastností (mez kluzu, mez pevnosti v tahu) srovnatelných nebo převyšujících vlastnosti běžných slitin A356/A357.
- Dobrá odolnost proti korozi: Vykazuje dobrou odolnost proti atmosférické korozi.
- Svařitelnost: Lze svařovat, ale doporučuje se zvláštní postup.
- Jemná mikrostruktura: Výsledkem rychlého tuhnutí při LPBF je velmi jemná dendritická mikrostruktura, která pozitivně přispívá k mechanickým vlastnostem ve srovnání se stejnou slitinou ve formě odlitku.
- Silné stránky pro klouby řízení:
- Osvědčené výsledky: Široce se používá v AM pro různé aplikace, včetně prototypů pro automobilový průmysl a některých funkčních dílů. O jeho vlastnostech a zpracování je k dispozici rozsáhlý výzkum a údaje.
- Spolehlivý tisk: Jeho dobrá zpracovatelnost vede k předvídatelnějším a opakovatelným výsledkům, což je zásadní pro kontrolu kvality v sériové výrobě.
- Dobrá vyváženost vlastností: Nabízí solidní kombinaci pevnosti, tažnosti (zejména po odlehčení napětí) a odolnosti proti korozi, která je po vhodném tepelném zpracování vhodná pro mnoho aplikací automobilových podvozků.
- Efektivita nákladů: Obecně je cenově výhodnější (cena prášku a snadnost tisku) ve srovnání se slitinami s vyšší pevností, jako je A7075 zpracovávaná AM.
- Slabé stránky / úvahy:
- Nižší absolutní síla: V porovnání s vysokopevnostními hliníkovými slitinami, jako je řada 7xxx (např. A7075) nebo oceli, jsou jejich absolutní meze pevnosti a únavy nižší. Konstrukce mohou být o něco objemnější (i když stále lehčí než ocel), aby se vyrovnaly ve vysoce namáhaných oblastech ve srovnání s tím, čeho by bylo možné dosáhnout s A7075.
- Požadováno tepelné zpracování: Pro dosažení optimálních mechanických vlastností (stav T6) je nutné po tisku provést tepelné zpracování, což zvyšuje časovou náročnost a náklady. Součásti vytištěné po tisku mají nižší pevnost a tažnost.
- Typické zpracování LPBF & amp; Vlastnosti (po tepelném zpracování T6): (Poznámka: Hodnoty jsou přibližné a do značné míry závisí na konkrétní kvalitě prášku, parametrech stroje, orientaci stavby a specifickém tepelném zpracování.) | Vlastnost | Rozsah typických hodnot (AlSi10Mg T6) | Jednotka | :————————– | :——————————– | :————— | Hustota | ~2.67 | g/cm³ | Mez kluzu (Rp0.2) | 230 – 300 | MPa | Mez pevnosti v tahu | 330 – 430 | MPa | Prodloužení při přetržení | 6 – 15 | % | Youngův modul | ~70 – 75 | GPa | Tvrdost | 100 – 120 | HV | Dosažená relativní hustota | > 99,5 | % |
A7075: Vysoce odolný soupeř
A7075 je známá vysokopevnostní tepaná slitina hliníku (součást řady 7xxx, obvykle legovaná zinkem, hořčíkem a mědí). Je ceněn v leteckém průmyslu a pro výkonné aplikace pro svůj výjimečný poměr pevnosti k hmotnosti, který výrazně převyšuje poměr pevnosti k hmotnosti AlSi10Mg nebo standardních slitin pro odlévání. Jeho přizpůsobení pro LPBF bylo náročné, ale je stále životaschopnější.
- Klíčové vlastnosti & Charakteristika:
- Velmi vysoká pevnost: Nabízí výrazně vyšší pevnost v tahu a mez kluzu ve srovnání s AlSi10Mg, blíží se pevnosti některých ocelí, ale při zlomku hmotnosti. To je jeho hlavní výhoda.
- Dobrá únavová pevnost: Obecně vykazuje dobrou odolnost proti únavovému selhání při cyklickém zatížení, což má zásadní význam pro součásti, jako jsou klouby řízení.
- Náročná zpracovatelnost: A7075 je notoricky známý tím, že se obtížně zpracovává pomocí metod AM založených na fúzi, jako je LPBF. Její široký rozsah tuhnutí a náchylnost k odpařování prvků s nízkým bodem varu (např. zinku) způsobují, že není-li zpracovávána za pečlivě kontrolovaných podmínek s optimalizovanými parametry a případně modifikovaným složením slitiny speciálně pro AM, je náchylná k defektům, jako je praskání při tuhnutí (trhání za tepla) a pórovitost.
- Složitost tepelného zpracování: Vyžaduje specifické, často vícestupňové tepelné zpracování (např. popouštění T6 nebo T7x), aby bylo dosaženo plného pevnostního potenciálu. Tyto úpravy musí být pečlivě kontrolovány, aby se předešlo problémům, jako je deformace nebo zhoršení vlastností.
- Nižší odolnost proti korozi: Obecně je méně odolný proti korozi než AlSi10Mg, zejména proti korozi pod napětím (SCC), ačkoli určité temperace (např. T73) zvyšují odolnost proti SCC za cenu mírného snížení maximální pevnosti. Často jsou nutné povrchové úpravy.
- Silné stránky pro klouby řízení:
- Maximální potenciál odlehčení: Jeho vynikající pevnost umožňuje agresivnější optimalizaci topologie a tenčí konstrukční části, což může vést k absolutně nejlehčí možné konstrukci hliníkového kloubu pro daný případ zatížení. Ideální pro aplikace v motorsportu a pro extrémní výkony.
- Vysoký výkon: Umožňuje součástem zvládat velmi vysoké zatížení a namáhání.
- Slabé stránky / úvahy:
- Obtížnost tisku & Kontrola kvality: Vyžaduje specializované odborné znalosti, přesně vyladěné parametry LPBF a případně upravené složení prášku specifické pro AM řady 7xxx, aby bylo možné spolehlivě vyrábět husté díly bez trhlin. Kontrola kvality a nedestruktivní testování (NDT) jsou rozhodující.
- Náklady: Prášek A7075 je obvykle dražší než AlSi10Mg a složitější procesy tisku a tepelného zpracování zvyšují další náklady.
- Možnost vzniku závad: Vyšší riziko tiskových vad, pokud není kontrola procesu přísná.
- Řízení koroze: V závislosti na provozním prostředí mohou vyžadovat ochranné nátěry nebo specifický výběr temperace.
- Typické zpracování LPBF & Vlastnosti (tepelně zpracované – např. T6): (Poznámka: Hodnoty jsou velmi závislé na dosažení vysoce kvalitního tisku bez vad a správném tepelném zpracování. Klíčová je zpracovatelnost.) | Vlastnost | Typický rozsah cílových hodnot (AM A7075 T6) | Jednotka | :————————– | :—————————————— | :——— | Hustota | ~2.81 | g/cm³ | Mez kluzu (Rp0.2) | 450 – 520 | MPa | Mez pevnosti v tahu| 520 – 590 | MPa | Prodloužení při přetržení | 4 – 10 | % | Youngův modul | ~71 – 73 | GPa | Tvrdost | 150 – 180 | HV | Dosažená relativní hustota| > 99,0 (vyžaduje odborné zpracování) | % |
Volba: AlSi10Mg vs. A7075
Výběr mezi AlSi10Mg a A7075 pro 3D tištěný kloub řízení závisí do značné míry na konkrétních požadavcích a omezeních aplikace:
- Zvolte AlSi10Mg, pokud:
- Hlavním faktorem jsou náklady.
- Nejdůležitější je prověřená spolehlivost a předvídatelnost procesu.
- Dobrá, ale ne extrémní pevnost a odlehčení jsou dostatečné.
- Je zapotřebí rychlejší vývoj/prototypování iterací s použitím osvědčeného materiálu.
- Odolnost proti korozi je významným faktorem, aniž by se muselo spoléhat na nátěry.
- Zvolte A7075 (nebo specifickou variantu AM), pokud:
- Primárním cílem je absolutně maximální poměr pevnosti a hmotnosti (např. motoristický sport, výkony na letecké úrovni).
- Je požadováno co nejvyšší odlehčení.
- Rozpočet umožňuje vyšší náklady na materiál a zpracování.
- Je možné navázat spolupráci s poskytovatelem AM s prokazatelnými zkušenostmi se zpracováním vysoce pevných hliníkových slitin citlivých na trhliny.
- Plánuje se odpovídající následné zpracování (tepelné zpracování, ochrana povrchu) a přísná kontrola kvality.
Důležitost kvality prášku a jeho získávání
Bez ohledu na zvolenou slitinu je kvalita kovového prášku zásadní pro úspěch procesu LPBF a integritu konečného dílu. Mezi klíčové vlastnosti prášku patří:
- Sféricita: Vysoce kulovité částice prášku zajišťují dobrou tekutost v systému přelakování tiskárny a rovnoměrnou hustotu nabalení na lůžku prášku, což vede ke konzistentnějšímu tavení a hustším dílům.
- Distribuce velikosti částic (PSD): Řízená PSD má zásadní význam pro dosažení vysoké hustoty balení a předvídatelného chování při tavení. Jemné částice mohou ovlivnit tekutost a představovat bezpečnostní riziko, zatímco nadměrné částice se nemusí zcela roztavit.
- Chemická čistota: Je nutné přísně dodržovat stanovené složení slitiny. Kontaminanty mohou výrazně ovlivnit mechanické vlastnosti a zpracovatelnost. Zvláště důležitý je nízký obsah kyslíku a vlhkosti.
- Absence satelitů: Malé částice navázané na větší částice (satelity) mohou zhoršovat tekutost a balení.
Zde se specializují dodavatelé kovových prášků jako je Met3dp, hrají zásadní roli. Met3dp využívá pokročilé výrobní techniky, jako je např Vakuová indukční tavicí plynová atomizace (VIGA) a Proces plazmové rotující elektrody (PREP). Tyto metody jsou určeny k výrobě prášků s:
- Vysoká sféricita: Zajištění vynikající tekutosti.
- Řízený PSD: Přizpůsobeno pro optimální výkon v systémech LPBF.
- Vysoká čistota: Minimalizace kontaminantů, jako je kyslík a dusík.
- Nízký obsah satelitu: Další zvýšení výkonu prášku.
Získáním vysoce kvalitních, dávkově konzistentních prášků AlSi10Mg nebo specializovaných prášků A7075 od renomované společnosti distributor hliníkového prášku nebo výrobce, jako je Met3dp, mohou inženýři a manažeři nákupu výrazně zvýšit pravděpodobnost úspěšného tisku vysoce integrovaných a výkonných kloubů řízení, které splňují náročné specifikace automobilového průmyslu. Schopnosti společnosti Met3dp’přesahují rámec standardních slitin, včetně výzkumu inovativních složení, jako jsou TiAl, TiNbZr a další, což ukazuje jejich hluboké odborné znalosti materiálů relevantních pro budoucí pokrok v automobilovém průmyslu, které jsou k dispozici prostřednictvím jejich produkt nabídek.
Výběr správné hliníkové slitiny - vyvážení spolehlivé zpracovatelnosti slitiny AlSi10Mg a vysokopevnostního potenciálu slitiny A7075 - a zajištění použití vysoce kvalitního prášku optimalizovaného pro AM jsou prvními důležitými kroky při využívání 3D tisku pro pokročilé a lehké klouby řízení automobilů.
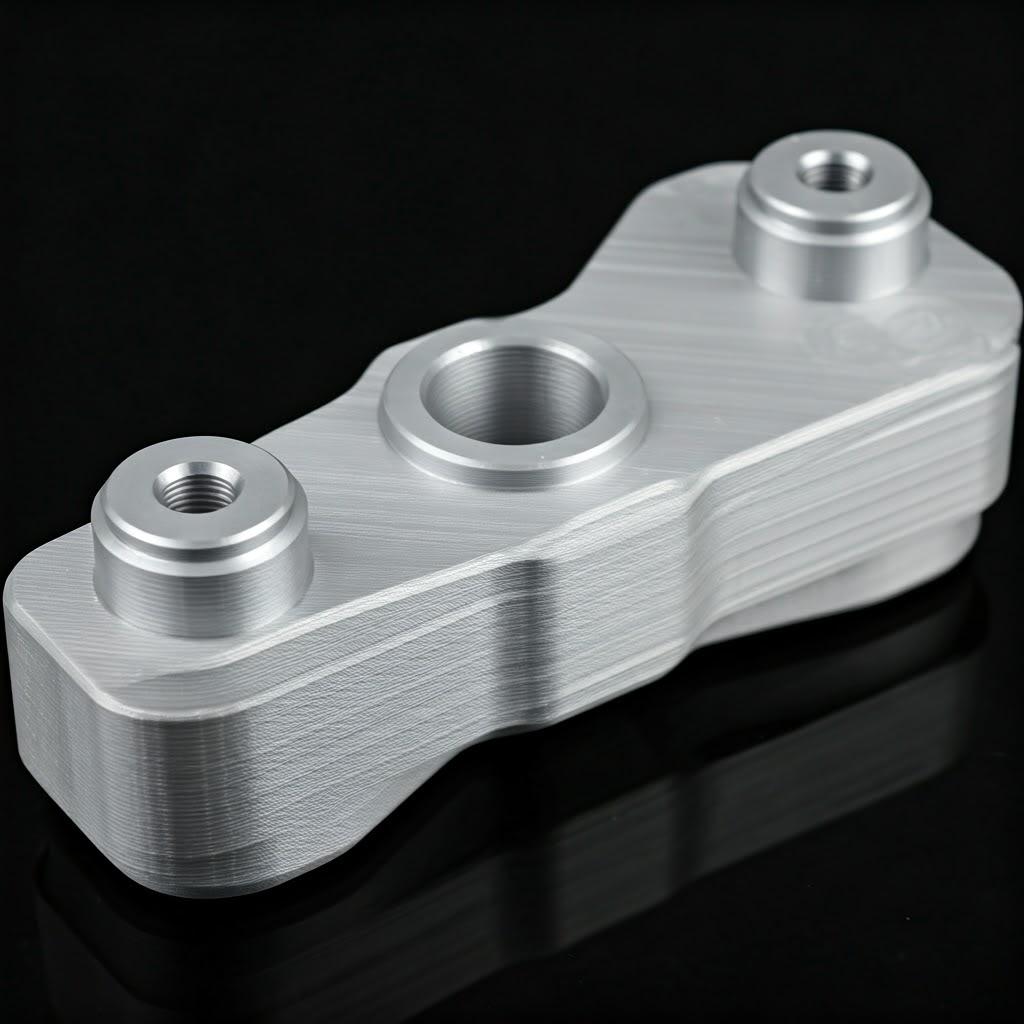
Design pro aditivní výrobu (DfAM): Optimalizace kloubů řízení pro 3D tisk
Vzít návrh určený k odlévání nebo kování a poslat ho do 3D tiskárny na kov je recept na zklamání. Aby inženýři skutečně využili potenciál aditivní výroby pro součásti, jako jsou například klouby řízení, musí se chopit Design pro aditivní výrobu (DfAM). DfAM není pouhý návrh, ale zásadní posun ve filozofii navrhování, který zohledňuje jedinečné možnosti a omezení stavebního procesu po vrstvách již ve fázi konceptu. Uplatňování zásad DfAM je nezbytné pro maximalizaci odlehčení, zajištění strukturální integrity, minimalizaci času a nákladů na tisk a snížení úsilí při následném zpracování. Pro výrobci automobilových dílů přechodu na AM je zvládnutí DfAM klíčové pro výrobu efektivních a spolehlivých komponent.
1. Optimalizace topologie: Navrhování podle cesty zatížení
To je často výchozím bodem a vizuálně nejvýraznějším aspektem DfAM pro konstrukční díly. Namísto toho, aby se začínalo s pevným blokem a odebíral se materiál (subtraktivní myšlení) nebo se vyplňoval předem definovaný tvar formy (licí myšlení), pracuje se při optimalizaci topologie jinak:
- Definujte prostor: Vycházejte z maximálního přípustného konstrukčního objemu kloubu řízení včetně všech připojovacích bodů (náboj kola, řídicí páky, spojovací tyč, držáky brzdových třmenů), které jsou pevně umístěny v prostoru.
- Použít zatížení a omezení: Definujte všechny předpokládané případy zatížení, kterým bude kloub během své provozní životnosti vystaven (síly v zatáčkách, brzdný moment, nárazy, omezení zdvihu zavěšení) pomocí analýzy konečných prvků (MKP). Definujte omezení, jako jsou ochranné zóny a pevné montážní body.
- Nastavení cílů optimalizace: Obvykle je cílem minimalizovat hmotnost (nebo objem) a zároveň splnit omezení týkající se maximálního přípustného napětí a průhybu (tuhosti).
- Spusťte algoritmus: Specializovaný software iterativně odstraňuje materiál z oblastí s nízkým namáháním a ponechává materiál pouze tam, kde je potřeba, aby efektivně přenášel definované zatížení.
- Interpretovat a upřesnit: Surovým výstupem optimalizace topologie je často organická, kostrbatá síť, kterou musí návrhář interpretovat a zdokonalit. To zahrnuje vyhlazení povrchů, zajištění vyrobitelnosti (s ohledem na omezení AM popsaná níže) a případné spuštění dalších analytických smyček.
Specifika kloubu řízení: Pro a optimalizace topologie kloubu řízení projektu je přesné definování více komplexních zatěžovacích stavů (kombinace brzdění, zatáčení a nárazového zatížení) velmi důležité. Cílem optimalizace by mělo být zachování tuhosti v kritických montážních bodech při současném výrazném snížení množství materiálu v jiných místech. Výsledné konstrukce často vypadají radikálně odlišně od svých tradičních protějšků a ukazují efektivní průběh zatížení.
2. Příhradové konstrukce a strategie vyplňování
Kromě odstranění objemového materiálu umožňuje DfAM strategické využití vnitřních mřížkových struktur:
- Další odlehčení: Nahrazení plných profilů pečlivě navrženými vnitřními mřížkami (např. gyroidy, diamantové, voštinové struktury) může dále snížit hmotnost při zachování významné strukturální podpory a tuhosti.
- Vlastnosti na míru: Různé typy a hustoty mřížek lze použít k vyladění specifických vlastností, jako je absorpce energie (pro odolnost proti nárazu) nebo tlumení vibrací.
- Tepelný management: Mřížky mohou potenciálně zlepšit odvod tepla, ačkoli je to u kloubů méně obvyklé jako primární hnací síla.
- Výzvy: Navrhování a ověřování vlastností mřížových konstrukcí vyžaduje pokročilý software a simulační schopnosti. Klíčovým aspektem je také zajištění odstranění prášku ze složitých vnitřních mřížek po tisku.
Specifika kloubu řízení: Mřížky lze selektivně použít v oblastech kloubu s nižším namáháním, které byly identifikovány během optimalizace topologie, a zajistit tak lokální tuhost s minimálními hmotnostními ztrátami.
3. Navrhování pro vlastní podporu a strategii podpůrné struktury
LPBF vyžaduje podpůrné konstrukce pro převislé prvky a pro ukotvení dílu ke stavební desce, aby se zabránilo jeho deformaci. Podpěry však zvyšují náklady na materiál, čas tisku a značné úsilí při následném zpracování při odstraňování, což může vést k poškození povrchu součásti. Cílem efektivního DfAM je minimalizovat závislost na podpěrách:
- Orientační strategie: Rozhodující je volba optimální orientace kloubu řízení na konstrukční desce. To ovlivňuje množství a umístění potřebných podpěr, kvalitu povrchu různých ploch, rozložení zbytkových napětí a dobu sestavení. Často se digitálně vyhodnocuje více orientací.
- Samonosné úhly: Konstrukce přesahů pod kritickým úhlem (obvykle kolem 45 stupňů od vodorovné roviny u hliníkových slitin, jako je AlSi10Mg, i když závisí na stroji a parametrech) umožňuje tisknout je bez podpěr. Konstruktéři mohou místo ostrých vodorovných převisů použít zkosení nebo filety.
- Interní kanály: Konstrukce vnitřních kanálů se samonosnými tvary (např. kosočtvercový nebo slzovitý průřez místo kruhového) může eliminovat potřebu obtížně odstranitelných vnitřních podpěr.
- Optimalizace podpory: Pokud jsou podpěry nevyhnutelné, zahrnuje DfAM jejich konstrukci pro snadné odstranění (např. použití minimálních kontaktních bodů, specifické vzory perforace) a jejich umístění na nekritické povrchy, kde jsou přijatelné stopy po odstranění nebo budou později opracovány. Specializovaný software může pomoci vygenerovat optimalizované podpůrné struktury.
Specifika kloubu řízení: Vzhledem ke složité geometrii kloubu s více rameny a montážními body je rozhodující orientace a strategie podpory. Minimalizace podpěr na funkčních rozhraních (otvory ložisek, montážní plochy) je zásadní pro snížení potřeby následného obrábění.
4. Řízení tepelného namáhání a deformace
Intenzivní lokalizovaný ohřev a rychlé ochlazení během LPBF vytváří v dílu značné tepelné gradienty a zbytková napětí. Pokud se tato napětí nezvládnou, mohou způsobit:
- Deformace/zkreslení: Díl se během tisku zkroutí nebo oddělí od konstrukční desky.
- Praskání: Zejména u citlivých slitin, jako je A7075.
- Snížený mechanický výkon: Vysoké zbytkové napětí může negativně ovlivnit únavovou životnost.
Strategie zmírnění dopadů DfAM: * Filetování: Vyhnutí se ostrým vnitřním rohům a použití velkorysých pilin snižuje koncentraci napětí. * Orientace: Stavba vysokých, tenkých úseků ve svislé poloze může někdy snížit napětí ve srovnání s jejich stavbou ve vodorovné poloze. * Tepelná kompenzace: Pokročilé techniky mohou zahrnovat jemné úpravy modelu CAD, které kompenzují předpokládané smrštění nebo zkreslení. * Strategická distribuce materiálu: Zamezení velkým, náhlým změnám průřezu může pomoci řídit nahromadění tepla a rychlost chlazení. * Robustní ukotvení: Zajištění dostatečné opory spojující díl s konstrukční deskou, zejména v počátečních vrstvách.
Specifika kloubu řízení: Různé tloušťky a složitý tvar činí klouby náchylnými k tepelnému namáhání. Důležité je pečlivé opilování spojů mezi rameny a hlavním tělesem a optimální orientace a podepření.
5. Minimální tloušťka stěny a rozlišení prvků
LPBF má omezení, pokud jde o to, jak tenkou stěnu nebo jak malý prvek lze spolehlivě vytisknout.
- Tloušťka stěny: U hliníkových slitin, jako jsou AlSi10Mg a A7075, se minimální dosažitelná tloušťka stěny obvykle pohybuje v rozmezí 0,4 mm až 1,0 mm v závislosti na stroji, parametrech a výšce/sklonění stěny. Konstruktéři musí zajistit, aby konstrukčně relevantní průřezy dodržovaly praktická minima.
- Rozlišení funkce: Velikost laserového bodu a velikost částic prášku omezují rozlišení jemných detailů, malých otvorů a ostrých hran. Velmi malé prvky nemusí být přesně rozlišeny nebo mohou být uzavřeny.
Specifika kloubu řízení: Zatímco optimalizace topologie může navrhovat extrémně tenké průřezy, konstruktéři musí prosazovat minimální tloušťky, které lze vyrobit. Malé nekritické otvory by bylo lepší vyvrtat během následného zpracování než je přímo vytisknout, pokud je potřeba vysoká přesnost.
6. Navrhování pro následné zpracování
Klíčovým aspektem DfAM, který je často opomíjen, je navrhování dílu s ohledem na následné kroky následného zpracování:
- Přídavky na obrábění: Povrchy vyžadující vysokou přesnost nebo specifickou povrchovou úpravu (např. otvory ložisek, uchycení brzdových třmenů, rozhraní řídicích ramen) by měly být navrženy s přídavným materiálem (“obráběcí materiál” nebo “odsazení”), který bude odstraněn během CNC obrábění.
- Obrábění: Zvažte, jak bude složitý tvar kloubu bezpečně držet během obrábění nebo dalších kroků následného zpracování. Možná bude nutné přidat dočasné přípravky nebo referenční prvky, které lze později snadno odstranit.
- Přístup k podpoře: Zajistěte, aby byly podpůrné konstrukce umístěny na místech, kde jsou fyzicky přístupné pro nástroje pro demontáž, aniž by došlo k poškození povrchu finálního dílu.
- Odstranění prášku: U dílů s vnitřními kanály nebo mřížkami zahrnuje konstrukce prvky nebo přístupová místa, která usnadňují odstranění nerozpuštěného prášku po tisku.
Specifika kloubu řízení: Běžnou praxí je přidání 0,5 až 1,5 mm materiálu na kritické styčné plochy a otvory ložisek. Zajištění volného přístupu pro nástroje k odstranění podpěr v okolí bodů zdvihu zavěšení je nezbytné.
Partnerství pro odbornost DfAM:
Úspěšná implementace DfAM, zejména u dílů kritických z hlediska bezpečnosti, jako jsou klouby řízení, vyžaduje odborné znalosti. Spolupráce se zkušeným poskytovatelem služeb AM, jako je Met3dp, nabízí významné výhody. Inženýři společnosti Met3dp’rozumějí nuancím LPBF s hliníkovými slitinami a mohou spolupracovat na optimalizaci návrhu, strategii podpory, analýze orientace a zajištění skutečné vyrobitelnosti návrhu. Jejich zkušenosti s automobilová součástka výroba poskytuje cenné poznatky o tom, jak převést požadavky na výkon do optimalizovaných, tisknutelných návrhů. Dodržování zavedených pokyny pro návrh aditivní výroby a zároveň využívat jedinečné možnosti technologie je klíčem k úspěchu.
DfAM v podstatě transformuje proces návrhu z přizpůsobení se výrobním omezením na využití výrobních možností. U hliníkových kloubů řízení vytištěných 3D tiskem je rozhodujícím prostředkem pro dosažení maximální lehkosti, výkonu a nákladové efektivity.
Dosažení přesnosti: Tolerance, povrchová úprava a rozměrová přesnost u kloubů vytištěných na 3D tiskárně
Zatímco 3D tisk z kovu nabízí nebývalou svobodu při navrhování, častá otázka inženýrů a manažerů nákupu, zejména těch, kteří jsou zvyklí na vysokou přesnost CNC obrábění, se týká dosažitelné úrovně tolerance, kvality povrchu a celkové rozměrové přesnosti. Pro součást, jako je kloub řízení, kde jsou rozhodující přesná rozhraní s ložisky, rameny zavěšení a brzdami, je zásadní porozumět inherentní přesnosti laserové fúze v práškovém loži (LPBF) a faktorům, které ji ovlivňují. Spolehněte se na zkušené dodavatele, jako je společnost Met3dp, která je známá svými produkty špičkový objem, přesnost a spolehlivost tisku, je klíčem ke splnění přísných norem kvality v automobilovém průmyslu.
Typická rozměrová přesnost a tolerance v LPBF
Systém LPBF je schopen vyrábět kovové díly s dobrou rozměrovou přesností, ale obecně není tak přesný jako víceosé CNC obrábění.
- Obecné tolerance: U dobře kalibrovaných průmyslových systémů LPBF tisknoucích na hliníkové slitiny, jako je AlSi10Mg nebo A7075, se typické dosažitelné tolerance pro středně velké díly (např. kloub řízení) často pohybují v rozmezí:
- ±0,1 mm až ±0,3 mm pro menší rozměry (např. pod 100 mm).
- ±0,1 % až ±0,2 % jmenovitého rozměru u větších prvků.
- Normy ISO: Přesnost dílů AM lze klasifikovat podle norem, jako je řada ISO/ASTM 52900, nebo podle specifických procesních norem. Dosažitelná přesnost je však velmi závislá na konkrétním stroji, materiálu, geometrii dílu a řízení procesu.
- Kritické funkce: Je důležité si uvědomit, že tyto obecné tolerance nemusí být dostatečné pro všechny prvky na kloubu řízení, zejména pro otvory ložisek, přesné montážní plochy brzdových třmenů nebo kuželové otvory pro kulové čepy. Tyto prvky téměř vždy vyžadují dodatečné opracování, aby se dosáhlo potřebných těsných tolerancí (často v rozmezí ±0,01 mm až ±0,05 mm).
Faktory ovlivňující přesnost:
Dosažení co nejvyšší přesnosti v LPBF vyžaduje pečlivou kontrolu mnoha faktorů:
- Kalibrace stroje: Základem je pravidelná a přesná kalibrace laserů, skenerů (galvanometrů) a pohybových systémů tiskárny.
- Tepelné účinky: Zbytkové napětí, smršťování během chlazení a tepelná roztažnost/smršťování během sestavování významně ovlivňují konečné rozměry. Tepelnou historii ovlivňují faktory, jako je ohřev stavební desky, strategie laserového skenování a podpůrné konstrukce.
- Orientace na část: Orientace dílu na konstrukční desce ovlivňuje kumulaci tepelných napětí a může ovlivnit přesnost různých prvků v důsledku procesu vytváření vrstev (např. efekt “schodovitého pohybu” na šikmých plochách).
- Kvalita prášku: Konzistentní distribuce velikosti částic a morfologie hliníkového prášku přispívá k rovnoměrnému tavení a tuhnutí, což má vliv na přesnost. Výhodné je nakupovat od dodavatelů zaměřených na kvalitu, jako je Met3dp.
- Parametry laseru: Nastavení, jako je výkon laseru, rychlost skenování, rozteč šraf a tloušťka vrstvy, přímo ovlivňují velikost a stabilitu taveniny, což má vliv na přesnost rozměrů.
- Průtok plynu: Správný průtok inertního plynu (obvykle argonu nebo dusíku) v konstrukční komoře je nutný k odstranění vedlejších produktů zpracování a zajištění stálých podmínek tavení. Nerovnoměrné proudění může ovlivnit kvalitu a přesnost dílů.
- Následné zpracování: Tepelné zpracování s uvolněním napětí může způsobit mírné rozměrové změny (smrštění nebo nárůst), s nimiž je třeba počítat. Odstranění podpěr může ovlivnit i okolní povrchy.
Povrchová úprava (drsnost)
Povrchová úprava dílů z LPBF vytištěných po vyjmutí je ze své podstaty drsnější než u obráběných povrchů. Textura vzniká v důsledku částečně roztavených částic prášku ulpívajících na povrchu a vrstevnatého uspořádání.
- Typické hodnoty Ra: Drsnost povrchu (Ra – aritmetický průměr drsnosti) se u hliníkových slitin po tisku obvykle mění v závislosti na orientaci povrchu vzhledem ke směru sestavení:
- Plochy směřující vzhůru (nahoře): Obecně nejhladší, často Ra 5-10 µm.
- Svislé stěny: Střední drsnost, často Ra 8-15 µm.
- Plochy směřující dolů (podporované): Nejdrsnější povrchy v důsledku kontaktu s nosnými konstrukcemi a charakteru tvorby převisů, často Ra 15-25 µm nebo vyšší. Tam, kde byly podpěry odstraněny, může být povrch ještě drsnější a vykazovat stopy po svědcích.
- Svažité povrchy: Vykazují “schodovitý” efekt s drsností závislou na úhlu a tloušťce vrstvy.
- Ovlivňující faktory: Tloušťka vrstvy (tenčí vrstvy obecně poskytují lepší povrchovou úpravu), parametry laseru, velikost částic prášku a strategie skenování kontur - to vše ovlivňuje konečnou drsnost povrchu.
- Důsledky pro Knucklese: Zatímco obecná povrchová úprava může být přijatelná pro nekritické oblasti, povrchy vyžadující hladký chod (např. ložisková sedla) nebo těsnění budou vyžadovat následnou úpravu, jako je obrábění nebo případně leštění. Drsné povrchy mohou také působit jako koncentrátory napětí, což může mít vliv na únavovou životnost, pokud se neřeší (např. kuličkováním).
Splnění standardů kvality pro automobilový průmysl
Dosažení požadované přesnosti u automobilových součástí, jako jsou například klouby řízení, vyžaduje kombinaci řízeného tisku a cíleného následného zpracování:
- Řízení procesu během tisku: Použití vysoce kvalitních strojů LPBF s robustními systémy monitorování a řízení procesu. To zahrnuje sledování vlastností taveniny, výkonu laseru a atmosféry inertního plynu. Zaměření společnosti Met3dp’na spolehlivé a přesné tiskové systémy je v souladu s touto potřebou. Jejich odborné znalosti v oblasti 3D tisk z kovu zahrnuje pochopení a kontrolu těchto kritických procesních proměnných.
- DfAM pro přesnost: Zásadní je navrhování kritických prvků s vhodným obráběcím materiálem. Tolerance by měly být jasně specifikovány na výkresech, kde by mělo být uvedeno, které jsou dosažitelné “tak jak jsou vytištěny” a které vyžadují sekundární operace.
- Cílené následné obrábění: Pomocí víceosého CNC obrábění lze dokončit kritická rozhraní, otvory a montážní plochy s požadovanými přísnými tolerancemi a povrchovou úpravou.
- Důkladná kontrola: Použití souřadnicových měřicích strojů (CMM) a technologie 3D skenování k ověření přesnosti rozměrů podle modelu CAD a specifikací výkresu po tisku a po konečném obrábění. Pro sériovou výrobu lze zavést statistickou kontrolu procesu (SPC).
Souhrnná tabulka přesnosti:
Vlastnosti | LPBF (hliník) ve stavu po vytištění | Obrobený díl LPBF | Typický požadavek (kritická vlastnost kloubu řízení) |
---|---|---|---|
Obecná tolerance | ±0,1 až ±0,3 mm nebo ±0,1-0,2 % | Řízeno schopností obrábění | N/A (Specifické funkce) |
Kritická tolerance | Obvykle nedosažitelné | ±0,01 až ±0,05 mm | ±0,01 až ±0,05 mm |
Povrchová úprava (Ra) | 5 – 25+ µm (v závislosti na orientaci) | 0.4 – 3,2 µm (nebo lepší) | 0.8 – 1,6 µm (příklad otvoru ložiska) |
Export do archů
Závěrem lze říci, že ačkoli díly vytištěné metodou LPBF nabízejí dobrou základní přesnost, dosažení vysoké přesnosti požadované pro kritické prvky na hliníkovém kloubu řízení vyžaduje kombinaci odborného řízení procesu během tisku, principů DfAM (zejména přidání obráběného materiálu) a nezbytných operací po obrábění. Porozumění těmto možnostem a omezením umožňuje konstruktérům a manažerům nákupu stanovit realistická očekávání a efektivně naplánovat celý výrobní postup, čímž se zajistí, že výsledná součást splní přísné normy kvality pro automobilový průmysl pro rozměrová přesnost a povrchová úprava.
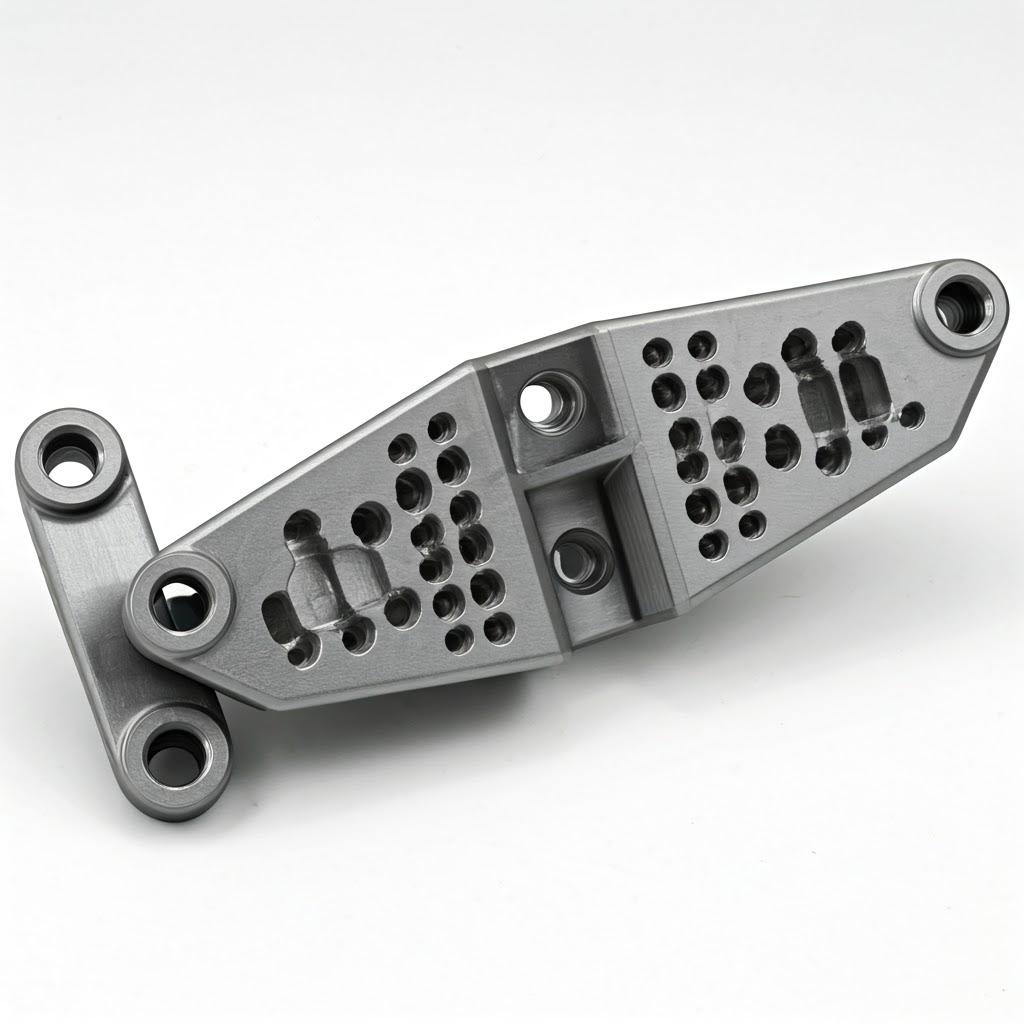
Kromě tisku: Základní kroky následného zpracování hliníkových kloubů řízení
Cesta hliníkového kloubu řízení vytištěného na 3D tiskárně nekončí, když stroj LPBF dokončí svůj stavěcí cyklus. Čerstvě vytištěný díl “zelený” vyžaduje několik zásadních kroků následného zpracování, aby se z něj stala funkční a spolehlivá automobilová součástka připravená k montáži. Tyto kroky nejsou volitelným doplňkem, ale nedílnou součástí pracovního postupu aditivní výroby, která je nezbytná k uvolnění napětí, odstranění dočasných struktur, dosažení kritických tolerancí, zlepšení povrchových vlastností a zajištění celkové kvality. Pochopení těchto kroků je zásadní pro přesný odhad nákladů, dodacích lhůt a zajištění toho, aby finální díl splňoval výkonnostní specifikace - což jsou klíčová hlediska pro velkoobchod s automobilovými součástkami dodavatelů a jejich zákazníků.
1. Tepelné ošetření proti stresu:
Jedná se pravděpodobně o nejdůležitější krok následného zpracování hliníkových dílů LPBF, zejména konstrukčních součástí, jako jsou klouby řízení vyrobené z AlSi10Mg nebo A7075.
- Proč je to potřeba: Rychlé zahřívání a ochlazování, které je vlastní LPBF, vytváří v tištěném dílu značná zbytková napětí. Tato vnitřní napětí mohou:
- Způsobit deformaci nebo pokřivení, zejména po vyjmutí dílu z konstrukční desky.
- Vede k předčasnému selhání při zatížení, zejména k únavovému praskání.
- Při následném obrábění je díl rozměrově nestabilní.
- Proces: Vytištěný díl, často ještě připevněný na konstrukční desce, se umístí do pece a podrobí pečlivě kontrolovanému tepelnému cyklu.
- Pro AlSi10Mg: Běžný cyklus uvolňování napětí může zahrnovat zahřívání na teplotu přibližně 300 °C po dobu 1-2 hodin a následné pomalé ochlazování. Tím se uvolní vnitřní napětí s minimálním dopadem na mikrostrukturu a pevnost.
- Pro A7075: Odlehčení od napětí může být začleněno jako první stupeň složitějšího tepelného zpracování (např. T6 nebo T7x).
- Výhody: Snižuje zbytkové napětí, zlepšuje rozměrovou stabilitu při obrábění a může mírně zlepšit tažnost. Je nezbytná pro předvídatelný výkon a prevenci deformace.
2. Vyjmutí dílu ze stavební desky:
Po uvolnění napětí (pokud se provádí na desce) je třeba díl oddělit od konstrukční desky.
- Metody: Obvykle se provádí pomocí:
- Drátové elektroerozivní obrábění (EDM): Přesnost, minimální síla, vhodné pro složité nebo křehké díly.
- Pásové řezání: Rychlejší a běžnější pro robustní díly, ale méně přesné a vyžadující plošší základnu/podpěrnou konstrukci.
- Obrábění: Frézování nebo soustružení základny.
- Úvahy: Zvolená metoda závisí na geometrii dílu, požadované přesnosti základního povrchu a konstrukci nosné konstrukce. Je třeba dbát na to, aby nedošlo k poškození dílu při demontáži.
3. Odstranění podpůrné konstrukce:
Dočasné podpůrné konstrukce vzniklé při tisku je třeba odstranit. To může být jeden z nejpracnějších a nejnáročnějších kroků následného zpracování.
- Metody:
- Ruční odstranění: Lámání nebo odřezávání podpěr pomocí ručního nářadí (kleště, štípačky, brusky). Vhodné pro přístupné podpěry, ale hrozí poškození povrchu dílu.
- CNC obrábění: Frézování nebo broušení podpěr, kontrolovanější a přesnější, zejména u podpěr na funkčních plochách.
- Drátové elektroerozivní obrábění: V některých případech lze použít k přesnému řezání podpěr.
- Výzvy:
- Přístupnost: Podpěry ve složitých vnitřních geometriích nebo v těžko přístupných oblastech lze jen velmi obtížně zcela odstranit. To posiluje význam DfAM pro minimalizaci vnitřních podpor.
- Povrchové značky: Při odstraňování podpěr často zůstávají na povrchu dílu v místě jejich upevnění stopy po svědcích nebo drsné skvrny (“nubs”). Ty mohou vyžadovat další úpravu.
- Choulostivé funkce: Při odstraňování podpěr je třeba dbát na to, aby nedošlo k porušení tenkých stěn nebo křehkých prvků.
- DfAM Impact: Konstrukce podpěr s minimálním počtem kontaktních bodů, specifickými odlamovacími prvky a jejich umístění na nekritické povrchy výrazně usnadňuje demontáž.
4. Žíhání roztokem a stárnutí Tepelné zpracování (např. temperace T6)
Aby slitiny jako AlSi10Mg a A7075 dosáhly optimální pevnosti a tvrdosti, je obvykle zapotřebí celý cyklus tepelného zpracování, který přesahuje pouhé uvolnění napětí. Pro hliníkové slitiny je běžný temperační stupeň T6.
- Proces (zjednodušený příklad T6):
- Tepelné zpracování roztoku: Zahřívání dílu na vysokou teplotu (např. ~520-540 °C pro AlSi10Mg, ~470-490 °C pro A7075) po určitou dobu, aby se legující prvky rozpustily do pevného roztoku.
- Kalení: Rychlé ochlazení dílu (obvykle ve vodě), aby se prvky udržely v roztoku.
- Umělé stárnutí: Opětovné zahřátí dílu na nižší teplotu (např. ~160-180 °C pro AlSi10Mg, ~120-150 °C pro A7075) po dobu několika hodin, aby bylo možné řízené vysrážení zpevňujících fází v kovové matrici.
- Výhody: Výrazně zvyšuje mez kluzu, pevnost v tahu a tvrdost ve srovnání se stavem po vytištění nebo po uvolnění napětí. To má zásadní význam pro dosažení potřebných mechanických vlastností kloubu řízení.
- Úvahy: Tepelné zpracování vyžaduje přesnou kontrolu teploty a času. Kalení může vyvolat deformace, které může být nutné řešit pomocí přípravků nebo následným rovnáním/obráběním. Různé temperace (např. T7x pro A7075) mohou nabízet různou rovnováhu mezi pevností a odolností proti koroznímu praskání. Provádění tepelné zpracování AlSi10Mg T6 správné použití je pro výkonnost dílu zásadní.
5. CNC obrábění:
Jak je uvedeno v části ‘Přesnost’, obrábění je téměř vždy nutné pro kritické prvky.
- Účel: Dosažení přísných rozměrových tolerancí, specifických geometrických tolerancí (např. kolmost, soustřednost) a požadovaných povrchových úprav na funkčních rozhraních.
- Obráběné oblasti: Obvykle zahrnuje:
- Montážní otvor ložiska kola.
- Montážní plochy pro brzdový třmen a opěrnou desku.
- Kuželové otvory pro kulové čepy vahadel a spojovacích tyčí.
- Ostatní kritické styčné plochy nebo rozhraní.
- Proces: Využívá víceosé (často pětiosé) CNC frézky. Vyžaduje pečlivý návrh upínacích přípravků kvůli složitým, často organickým tvarům, které vznikají optimalizací topologie. CNC obrábění 3D tištěných dílů vyžaduje odborné znalosti při zpracování potenciálně složitých geometrií a zajištění správného upnutí obrobku.
6. Povrchová úprava:
V závislosti na požadavcích lze použít další povrchové úpravy:
- Zpevňování povrchu: Bombardování povrchu malými kulovými médii (broky) vnáší do povrchové vrstvy tlaková zbytková napětí. To je velmi výhodné pro zvýšení únavové životnosti, což je důležité zejména u cyklicky namáhaných součástí, jako jsou například klouby řízení.
- Třískové/vibrační dokončování: Použití brusných médií v rotující nebo vibrující misce k odstranění otřepů, vyhlazení povrchů a dosažení rovnoměrného matného povrchu. Účinné pro odstranění drobných podpěrných vrypů a zlepšení celkové estetiky povrchu.
- Leštění: Lze dosáhnout velmi hladkého, zrcadlového povrchu, pokud je to požadováno pro specifické aplikace (méně obvyklé pro klouby, pokud se nejedná o výstavní vozidla).
- Eloxování/povlakování: Nanášení ochranných nebo kosmetických povrchových vrstev. Eloxování zvyšuje odolnost hliníku proti korozi a opotřebení. Specifické barvy nebo nátěry mohou být použity z důvodu ochrany životního prostředí nebo značky.
7. Kontrola a řízení kvality:
V celém řetězci následného zpracování má kontrola zásadní význam.
- Rozměrová kontrola: CMM nebo 3D skenování po tisku, po tepelném zpracování (pro kontrolu deformace) a po konečném obrábění.
- Nedestruktivní zkoušení (NDT):
- Vizuální kontrola: Základní kontrola zjevných závad.
- Dye Penetrant Inspection (DPI): Detekuje trhliny porušující povrch.
- Rentgenová počítačová tomografie (CT): Zásadní pro detekci vnitřních vad, jako je pórovitost nebo nedostatečné spojení, což je důležité zejména pro ověřování integrity dílů důležitých z hlediska bezpečnosti. Poskytuje úplný 3D pohled na vnitřní strukturu.
- Ověřování vlastností materiálu: Zkouška tvrdosti, případně tahová zkouška reprezentativních vzorků vytištěných vedle hlavního dílu, pro potvrzení úspěšného tepelného zpracování a vlastností materiálu.
Shrnutí pracovního postupu následného zpracování:
Build Plate -> Stress Relief -> Part Removal -> Support Removal -> Heat Treatment (T6) -> CNC Machining -> Surface Finishing (e.g., Shot Peening) -> Final Inspection (CMM, NDT) -> Ready for Assembly
Každý krok prodlužuje celkový výrobní proces o čas a náklady. Efektivní integrace těchto kroků vyžaduje pečlivé plánování a odborné znalosti poskytovatele AM služeb. Společnosti jako Met3dp, které nabízejí komplexní řešení, rozumí tomuto integrovanému pracovnímu postupu od výroby prášku až po hotový díl a zajišťují kvalitu v každé fázi.
Zvládání výzev: Běžné problémy při 3D tisku řídicích kloubů a strategie jejich řešení
Ačkoli aditivní výroba kovů, zejména LPBF, nabízí významné výhody při výrobě lehkých hliníkových kloubů řízení, není tento proces bez problémů. Dosažení konzistentních a vysoce kvalitních výsledků, zejména u složitých geometrií a náročných materiálů, jako je A7075, vyžaduje hluboké pochopení potenciálních problémů a robustní strategie jejich zmírnění. Povědomí o těchto problémech je klíčové pro inženýry, kteří zadávají díly, a pro manažery nákupu, kteří vybírají schopné dodavatele, kteří mají potřebné řízení procesu a odborné znalosti. Mnohé z těchto výzev jsou aktivně řešeny pokrokem v technologii strojů, monitorování procesů a materiálových věd, jehož průkopníky jsou často společnosti zaměřené na průmyslová AM řešení, jako je Met3dp.
1. Pórovitost:
Pórovitost znamená malé dutiny nebo póry uvnitř tištěného materiálu, které mohou výrazně zhoršit mechanické vlastnosti, zejména únavovou pevnost.
- Typy:
- Pórovitost plynu: Způsobeno plynem (často vodíkem u hliníkových slitin) zachyceným v tavenině během tuhnutí. Může vzniknout z kontaminovaného prášku (vlhkost) nebo nedostatečného množství stínicího plynu.
- Pórovitost LoF (Lack-of-Fusion): Nepravidelně tvarované dutiny způsobené neúplným tavením a tavením mezi sousedními skenovacími stopami nebo následnými vrstvami. Často je to důsledek nedostatečného příkonu energie (příliš nízký výkon laseru, příliš vysoká rychlost skenování) nebo špatného překrytí vrstvy prášku.
- Detekce: Vizuálně obtížně zjistitelné na povrchu. Nejlépe se zjišťuje uvnitř pomocí rentgenového CT vyšetření.
- Zmírnění:
- Vysoce kvalitní prášek: Použití čistého, suchého, sférického prášku s kontrolovaným PSD, jako jsou prášky vyráběné pomocí pokročilých atomizačních procesů společnosti Met3dp, minimalizuje zdroje plynů. Zásadní je správná manipulace s práškem a jeho skladování.
- Optimalizované parametry: Vývoj a ověřování robustních parametrů tisku (výkon laseru, rychlost, rozteč šraf, tloušťka vrstvy) specifických pro slitinu a stroj, aby bylo zajištěno úplné roztavení a tavení. Klíčový je rozsáhlý vývoj procesu.
- Účinný stínicí plyn: Zajištění průtoku vysoce čistého inertního plynu (argonu) pro ochranu bazénu taveniny před kontaminací atmosférou.
- Monitorování procesů: Pokročilé systémy mohou v reálném čase monitorovat emise nebo teplotu v bazénu taveniny a odhalit tak anomálie svědčící o možném vzniku pórů.
- Izostatické lisování za tepla (HIP): Krok následného zpracování zahrnující vysokou teplotu a tlak, který může uzavřít vnitřní pórovitost. Tento postup však zvyšuje náklady a čas a je obvykle vyhrazen pro nejkritičtější aplikace (např. v letectví a kosmonautice).
2. Cracking:
Během procesu tisku nebo po něm mohou vznikat trhliny, které představují kritické vady ohrožující integritu konstrukce.
- Typy:
- Praskání při tuhnutí (trhání za tepla): Vzniká během tuhnutí u slitin se širokým rozsahem tuhnutí (jako je A7075) v důsledku tepelných napětí, která rozrušují polotuhou strukturu. Často se vyskytuje mezi hranicemi zrn.
- Praskání zbytkovým napětím (praskání za studena): Může se vyskytnout po ochlazení v důsledku vysokého vnitřního napětí, které překračuje pevnost nebo tažnost materiálu.
- Detekce: Někdy může být viditelný na povrchu, ale může být i vnitřní (zjistitelný pomocí CT nebo případně penetrací barviva, pokud je porušen povrch).
- Zmírnění:
- Výběr/úprava slitiny: AlSi10Mg je výrazně méně náchylný k praskání při tuhnutí než A7075. Při potřebě vysoké pevnosti může pomoci použití variant řady 7xxx specifických pro AM s modifikovaným složením nebo zušlechtěním zrna.
- Optimalizace parametrů: Vyladěním parametrů laseru (např. předehřev, hustota měrné energie) lze ovlivnit tepelné gradienty a mikrostrukturu a snížit tak náchylnost k praskání. Výzkum optimalizovaných Výzvy pro tisk A7075 probíhá.
- Strategie skenování: Použití specifických vzorů skenování (např. ostrovní skenování, šachovnicové vzory) může pomoci rovnoměrněji rozložit tepelné namáhání.
- Úleva od stresu: Pro snížení zbytkových napětí, která by mohla vést k praskání za studena, je zásadní včasné a vhodné tepelné zpracování.
- Strategie podpory: Správná konstrukce podpěr pomáhá zvládat tepelné namáhání během sestavování.
3. Deformace a zkreslení:
Nerovnoměrné smršťování a vznik zbytkových napětí mohou způsobit deformaci nebo zkroucení dílu během tisku nebo po vyjmutí z konstrukční desky.
- Příčiny: Především díky tepelným gradientům mezi horkou taveninou a chladnějším okolním materiálem/podkladem. Zvláště náchylné jsou velké, ploché úseky nebo náhlé změny tloušťky.
- Detekce: Vizuální kontrola, souřadnicový měřicí přístroj nebo 3D skenování.
- Zmírnění:
- Vytápění stavebních desek: Předehřátí konstrukční desky snižuje tepelný gradient mezi prvními vrstvami a substrátem.
- Robustní podpůrné struktury: Bezpečné ukotvení dílu ke stavební desce, zejména velkých nebo převislých částí, pomáhá odolávat deformačním silám.
- Optimalizovaná orientace: Orientace dílu tak, aby se minimalizovaly velké rovné plochy rovnoběžné s konstrukční deskou nebo dlouhé nepodporované přesahy.
- Strategie skenování: Stejně jako v případě prasklin mohou i při zvládání nahromaděného stresu pomoci specifické strategie skenování.
- Promptní úleva od stresu: Tepelné zpracování na uvolnění napětí před vyjmutím součásti z konstrukční desky (pokud je to možné) nebo bezprostředně po něm pomáhá stabilizovat součást.
- Modifikace designu (DfAM): Přidání žeber nebo mírná změna geometrie pro zvýšení tuhosti proti deformačním silám.
4. Obtíže při odstraňování podpory a kvalita povrchu:
Podpěrné konstrukce jsou sice nezbytné, ale představují problém při odstraňování a ovlivňují kvalitu povrchu.
- Výzvy: Přístup k vnitřním podpěrám, porušení jemných prvků při demontáži, časové/pracovní náklady, zanechání stop/jizviček na povrchu dílu.
- Zmírnění:
- DfAM: Navrhování samonosných podpěr, optimalizace orientace, používání snadno demontovatelných typů podpěr (např. stromové podpěry, kuželové podpěry), umisťování podpěr na nekritické povrchy.
- Optimalizované parametry podpory: Doladění spojovacích bodů mezi podpěrou a dílem pro snadnější odpojení.
- Vhodné techniky odstraňování: Použití správných nástrojů a metod (ruční, obrábění, elektroerozivní obrábění) pro konkrétní typ podpěry a umístění.
- Povrchová úprava po odstranění: Plánování následného obrábění nebo povrchové úpravy (tupování, kuličkování) pro odstranění stop na kritických místech.
5. Správa a recyklace prášku:
Manipulace s jemnými kovovými prášky vyžaduje opatrnost a opětovné použití nespékaného prášku je důležité z hlediska hospodárnosti, ale vyžaduje kontrolu.
- Výzvy:
- Bezpečnost: Kovové prášky (zejména hliník) mohou být hořlavé nebo mohou představovat nebezpečí pro dýchací cesty, pokud se s nimi nezachází správně (vyžaduje správné osobní ochranné prostředky, uzemnění, manipulaci v inertní atmosféře).
- Degradace prášku: Opakované vystavení teplu ve stavební komoře nebo manipulace s ním může způsobit oxidaci prášku nebo změny v PSD, což ovlivňuje zpracovatelnost a kvalitu dílů při následných sestaveních.
- Křížová kontaminace: Zajistěte, aby se typy prášků nemíchaly.
- Zmírnění:
- Správné manipulační postupy: Používání uzavřených systémů manipulace s prášky, prostředí s inertním plynem, vhodné osobní ochranné pomůcky.
- Monitorování kvality prášku: Pravidelné testování recyklovaného prášku (např. chemická analýza, PSD, tekutost), aby se zajistilo, že stále splňuje specifikace.
- Strategie řízené recyklace: Míchání recyklovaného prášku s původním práškem v kontrolovaných poměrech, stanovení limitů počtu cyklů opakovaného použití.
- Kvalita dodavatele: Začněte s vysoce kvalitním, konzistentním práškem od dodavatelů, jako je Met3dp, a minimalizujte počáteční variabilitu. Jejich zkušenosti s výrobou prášku zajišťují spolehlivý výchozí materiál. Porozumění společnosti Met3dp’s tiskových metod a jejich vztah k interakci s práškem je přínosný.
Zvládnutí těchto výzev vyžaduje kombinaci pokročilé strojní technologie, optimalizovaných a ověřených procesních parametrů, vysoce kvalitních materiálů, přísné kontroly procesu a kvalifikované obsluhy a inženýrů. Spolupráce s poskytovatelem AM služeb nebo dodavatelem technologií, jako je Met3dp, který investuje do výzkumu, vývoje procesů a systémů kvality, výrazně zvyšuje pravděpodobnost úspěšného překonání těchto překážek a výroby spolehlivých, vysoce výkonných hliníkových kloubů řízení vytištěných 3D tiskem.
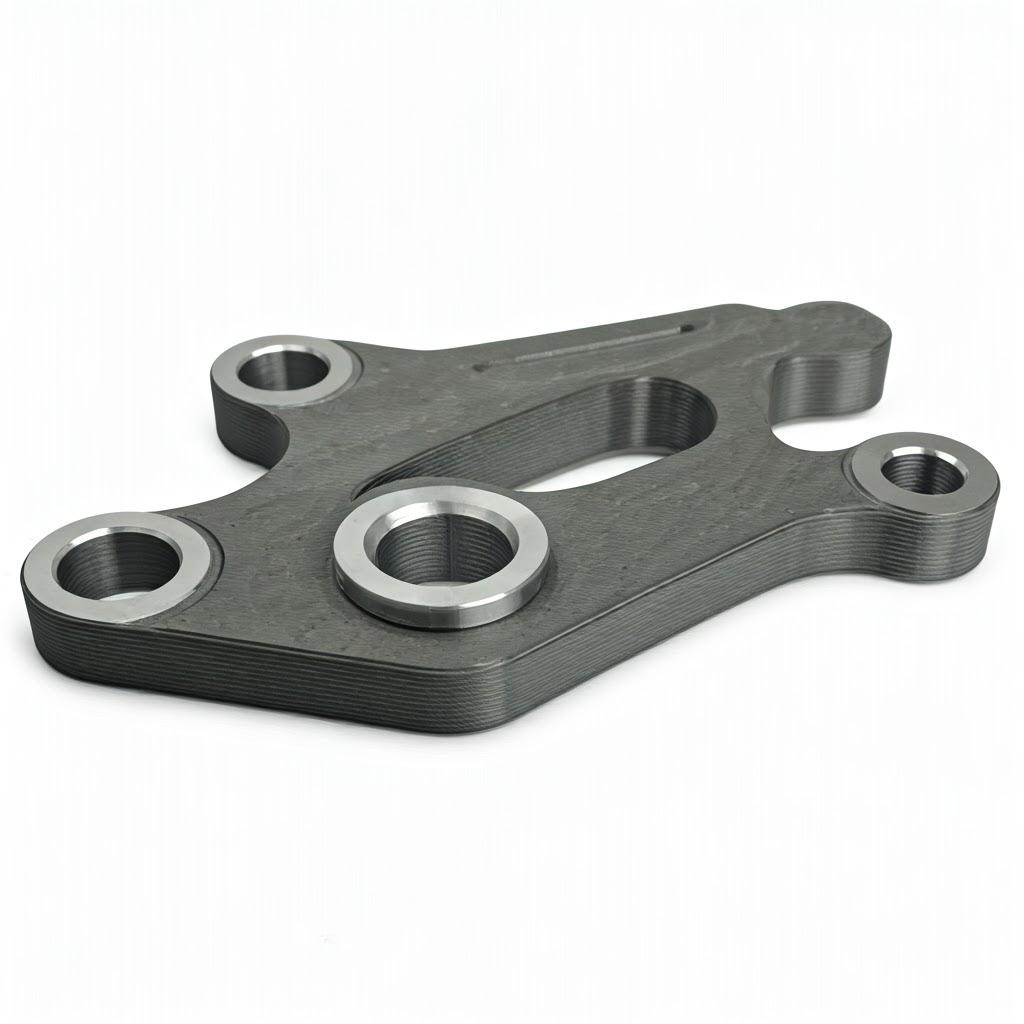
Výběr dodavatele: Výběr správného partnera pro 3D tisk kovů pro automobilové komponenty
Přechod na aditivní výrobu kritických součástí, jako je kloub řízení, je významným krokem. Úspěch tohoto přechodu závisí nejen na konstrukci a materiálu, ale také na schopnostech a spolehlivosti vámi zvoleného zařízení poskytovatel služeb 3D tisku kovů. Výběr správného partnera má zásadní význam, zejména v náročném automobilovém průmyslu, kde je kvalita, opakovatelnost a sledovatelnost neoddiskutovatelná. Pro manažery nákupu a inženýrské týmy, které prověřují potenciální dodavatele, je zásadní důkladný hodnotící proces založený na klíčových kritériích. Ne všichni dodavatelé AM jsou si rovni a partnerství s dodavatelem, který má hluboké odborné znalosti v oblasti automobilových aplikací, hliníkových slitin a robustních systémů kvality, je rozhodující pro zmírnění rizik a dosažení požadovaných výsledků.
Zde jsou uvedeny klíčové faktory, které je třeba zvážit při hodnocení a výběru dodavatel aditivní výroby pro automobilový průmysl:
1. Systémy řízení kvality a certifikace:
- ISO 9001: Jedná se o základní požadavek, který prokazuje závazek k dokumentovaným procesům a neustálému zlepšování řízení kvality.
- IATF 16949: Ačkoli se plná certifikace IATF mezi poskytovateli zaměřenými na AM stále ještě objevuje, prokázání dodržování jejích zásad nebo zkušeností s dodávkami do dodavatelských řetězců v souladu s IATF je významnou výhodou. Prokazuje to pochopení požadavků automobilového průmyslu týkajících se řízení procesů, řízení rizik (FMEA), sledovatelnosti a dokumentace (PPAP - prvky procesu schvalování výrobních dílů).
- Certifikace pro letectví a kosmonautiku (AS9100): Pokud je poskytovatel držitelem certifikátu AS9100, často to znamená vysoce vyspělé systémy kvality a řízení procesů, což může být výhodné i pro aplikace v automobilovém průmyslu.
2. Technická odbornost a technická podpora:
- Věda o materiálech: Klíčová je hluboká znalost konkrétních hliníkových slitin (AlSi10Mg, A7075), včetně jejich chování během LPBF, požadovaných tepelných úprav a dosažitelných mechanických vlastností. Zeptejte se na jejich zkušenosti s těmito specifickými materiály.
- Schopnost DfAM: Dodavatel by neměl být jen “tiskárnou”, ale skutečným partnerem, který rozumí a může aktivně přispívat k designu pro aditivní výrobu (DfAM). Měl by být schopen poskytnout zpětnou vazbu ohledně tisknutelnosti návrhu, navrhnout optimalizace pro odlehčení nebo snížení podpory a spolupracovat na vývoji optimální geometrie.
- Porozumění procesní fyzice: Důkladné pochopení procesu LPBF, včetně tepelného managementu, interakce laseru s materiálem, vývoje parametrů a strategií pro zmírnění vad.
- Znalosti následného zpracování: Odborné znalosti požadované posloupnosti kroků následného zpracování (uvolnění napětí, tepelné zpracování, strategie obrábění dílů AM, dokončovací práce) a jejich vliv na konečnou součást.
3. Technologie a schopnosti stroje:
- Zařízení průmyslové třídy: Ujistěte se, že poskytovatel používá moderní, dobře udržované průmyslové stroje LPBF, které jsou speciálně uzpůsobeny pro spolehlivé zpracování hliníkových slitin. Klíčové vlastnosti zahrnují dostatečný stavební objem, řízení inertní atmosféry a potenciální možnosti monitorování procesu in-situ.
- Přesnost a spolehlivost: Vyhledejte důkazy o kalibračních postupech stroje a údaje dokládající tvrzení o přesnosti a opakovatelnosti. Poskytovatelé jako Met3dp zdůrazňují, že jejich tiskárny’ špičkový objem, přesnost a spolehlivost tisku, což jsou kritické metriky pro součásti vyžadující přesnost.
- Kapacita: Zhodnoťte kapacitu a vytížení jejich strojů, abyste se ujistili, že jsou schopni dodržet požadované dodací lhůty pro prototypy a případné malé série.
4. Získávání a kontrola materiálu:
- Kvalita prášku: Jak dodavatel získává a kvalifikuje svůj hliníkový prášek? Má přísné postupy vstupní kontroly? Jaké jsou jejich protokoly pro manipulaci s práškem a recyklaci, aby se zabránilo kontaminaci a degradaci?
- Sledovatelnost materiálu: Mohou poskytnout úplnou sledovatelnost šarže prášku použitého pro vaše konkrétní díly s odkazem na původní certifikát shody výrobce prášku?
- Vlastní výroba prášku: Společnosti jako Met3dp, které vyrábějí tiskárny i vysoce kvalitní sférické kovové prášky pomocí pokročilých metod, jako je plynová atomizace a PREP, nabízejí výraznou výhodu. Tato vertikální integrace poskytuje větší kontrolu nad kvalitou a konzistencí materiálu, což má přímý dopad na integritu konečného dílu. Jejich O nás na stránce najdete podrobnosti o jejich zázemí a závazku ke komplexním řešením AM.
5. Komplexní možnosti následného zpracování:
- Integrovaný pracovní postup: V ideálním případě by měl poskytovatel nabízet bezproblémový pracovní postup, který zahrnuje nezbytné kroky následného zpracování buď přímo u něj, nebo prostřednictvím přísně kontrolovaných kvalifikovaných partnerů. To zahrnuje:
- Pece s řízenou atmosférou pro uvolňování napětí a tepelné zpracování (s kalibračními záznamy).
- Víceosé CNC obrábění vhodné pro složité geometrie AM dílů.
- Odborné znalosti v oblasti odstraňování podpory.
- Možnosti povrchové úpravy (např. kuličkování, bubnování).
- Komplexní možnosti kontroly a nedestruktivního zkoušení.
- Řízení dodavatelského řetězce: Pokud zadáváte následné zpracování externím dodavatelům, zhodnoťte jejich procesy řízení a kontroly kvality pro tyto externí kroky.
6. Důkladná kontrola kvality a inspekce:
- Monitorování procesů: Využívají při stavbě nějaký monitoring in-situ? Jaké jsou jejich standardní postupy pro kontrolu protokolů o sestavení a ověřování parametrů?
- Rozměrová kontrola: Záznamy o dostupnosti a kalibraci souřadnicových měřicích strojů a/nebo 3D skenerů. Standardní formáty inspekčních zpráv.
- Nedestruktivní zkoušení (NDT): Rozhodující pro díly důležité z hlediska bezpečnosti, jako jsou klouby řízení. Zhodnoťte jejich schopnosti a zkušenosti s:
- CT vyšetření: Doporučuje se pro detekci vnitřních defektů (pórovitost, praskliny).
- Dye Penetrant Inspection (DPI): Pro detekci povrchových trhlin.
- Další metody podle potřeby (např. ultrazvukové zkoušky, radiografické zkoušky).
- Testování materiálů: Schopnost provádět zkoušky tvrdosti, tahové zkoušky (na reprezentativních vzorcích) nebo metalografickou analýzu k ověření vlastností materiálu a úspěšnosti tepelného zpracování.
7. Dosavadní výsledky, případové studie a reference:
- Relevantní zkušenosti: Podařilo se jim úspěšně vyrobit podobné díly z hlediska složitosti, materiálu a kritičnosti? Konkrétní zkušenosti s automobilovými součástmi jsou velmi žádoucí.
- Případové studie: Vyžádejte si příklady nebo případové studie prokazující jejich schopnosti a dovednosti při řešení problémů.
- Odkazy: Vyžádejte si reference zákazníků, zejména z automobilového průmyslu nebo podobně náročných odvětví.
8. Náklady, doba realizace a komunikace:
- Transparentní citování: Poskytuje podrobné cenové nabídky s uvedením všech složek nákladů (materiál, doba výroby, práce, následné zpracování, NDT).
- Reálná doba dodání: Sděluje jasné a dosažitelné doby realizace pro různé fáze (prototypování, výroba).
- Komunikace & Řízení projektů: Jasná kontaktní místa, pravidelné aktualizace a schopnost reagovat na dotazy.
Shrnutí kontrolního seznamu hodnocení:
Kritéria | Klíčové otázky | Důležitost (kloub řízení) |
---|---|---|
Certifikáty kvality (ISO/IATF) | Jaké certifikáty máte? Jak jste v souladu s automobilovými standardy? | Velmi vysoká |
Technické znalosti | Jaké jsou vaše zkušenosti s AlSi10Mg/A7075? Podporujete DfAM? Jak optimalizujete parametry tisku? | Velmi vysoká |
Schopnosti stroje | Jaké stroje používáte? Jaký je jejich stavební objem/přesnost? Jak jsou udržovány/kalibrovány? | Vysoký |
Kontrola materiálu | Kde získáváte prášek? Jak ho kvalifikujete, zpracováváte a recyklujete? Dokážete zajistit sledovatelnost? | Velmi vysoká |
Následné zpracování | Jaké kroky jsou prováděny interně a jaké externě? Jak kontrolujete kvalitu tepelného zpracování/obrábění/NDT? | Velmi vysoká |
Kontrola kvality/NDT | Jaké jsou vaše standardní kontrolní postupy? Nabízíte CT vyšetření? Jak zajišťujete integritu dílů? | Velmi vysoká |
Záznamy o činnosti | Můžete se podělit o případové studie nebo odkazy na podobné automobilové/kritické díly? | Vysoký |
Náklady a dodací lhůta | Můžete poskytnout podrobné nabídky? Jaké jsou vaše obvyklé dodací lhůty? Jak probíhá komunikace v rámci projektu? | Vysoký |
Export do archů
Výběr správného partner pro kovový 3D tisk je investicí do kvality a spolehlivosti. Provedení hloubkové kontroly podle těchto kritérií vám pomůže zajistit výběr dodavatele, jako je společnost Met3dp, který je schopen dodávat vysoce výkonné a lehké hliníkové klouby řízení splňující přísné požadavky automobilového průmyslu.
Analýza nákladů a dodací lhůty: Pochopení ekonomiky 3D tištěných kloubů řízení
Technické výhody 3D tištěných hliníkových kloubů řízení jsou přesvědčivé, manažeři nákupu v automobilovém průmyslu a inženýři musí také pečlivě zvážit ekonomickou životaschopnost a časový plán výroby. Struktura nákladů a dodací lhůty aditivní výroby se výrazně liší od tradičního odlévání nebo kování. Pochopení těchto rozdílů je klíčem k informovanému rozhodování o tom, kdy a kde implementovat AM pro komponenty, jako jsou například klouby řízení.
Klíčové faktory ovlivňující náklady na 3D tištěné klouby řízení (LPBF):
Na rozdíl od tradičních metod, kterým dominují náklady na nástroje při nízkých objemech, jsou náklady na AM přímo vázány na samotný díl a čas potřebný k jeho výrobě.
- Náklady na materiál:
- Typ prášku: Náklady na suroviny se u jednotlivých slitin výrazně liší. Vysokopevnostní slitiny, jako je A7075, jsou obecně dražší než standardní AM slitiny, jako je AlSi10Mg.
- Část Objem: Samotný objem materiálu ve finálním dílu, včetně všech potřebných podpůrných konstrukcí, přímo ovlivňuje náklady. To podtrhuje ekonomický přínos optimalizace topologie a DfAM - snížení spotřeby materiálu šetří přímé náklady.
- Využití/recyklace prášku: Účinné strategie manipulace s práškem a recyklace používané poskytovatelem služeb mohou ovlivnit efektivní náklady na materiál, které se přenášejí na zákazníka. Neefektivní využití nebo nadměrný odpad zvyšují náklady.
- Čas stroje (čas sestavení):
- Primární nákladový faktor: Často se jedná o největší jednotlivou složku nákladů. Je závislá na tom, jak dlouho stroj LPBF tiskne díl(y).
- Ovlivňující faktory:
- Část Objem & Výška: Větší a vyšší díly se tisknou vrstvu po vrstvě déle.
- Část Složitost: Složitější geometrie mohou vyžadovat nižší rychlost skenování nebo složitější dráhy laserového skenování.
- Počet dílů na sestavení (Nesting): Tisk více dílů současně v jedné sestavovací úloze optimalizuje využití stroje a může snížit náklady na strojní čas na jeden díl. Efektivní vkládání je klíčové pro malosériovou výrobu.
- Tloušťka vrstvy: Tenčí vrstvy zlepšují kvalitu povrchu, ale výrazně prodlužují počet vrstev, a tím i dobu výroby.
- Hodinová sazba stroje: Tato sazba zahrnuje odpisy stroje, spotřebu energie, spotřebu inertního plynu, údržbu a režijní náklady zařízení. Sazby se liší v závislosti na složitosti stroje a struktuře nákladů poskytovatele.
- Náklady na pracovní sílu:
- Předběžné zpracování: Čas inženýrů na konzultace DfAM, přípravu sestavení (orientace, generování podpory), krájení a nastavení stroje.
- Následné zpracování: Může se jednat o velmi významnou složku práce, včetně:
- Vyjmutí dílu ze stavební desky.
- Ruční nebo poloautomatické odstraňování podpěr (u složitých dílů může být časově náročné).
- Seřizování a obsluha CNC strojů.
- Ruční dokončování, odstraňování otřepů nebo povrchová úprava.
- Postupy kontroly a řízení kvality.
- Náklady na následné zpracování (kromě mzdových nákladů):
- Tepelné zpracování: Doba pece, spotřeba energie, náklady na řízenou atmosféru.
- CNC obrábění: Čas stroje, opotřebení nástrojů, náročnost programování. Obrábění složitých, topologicky optimalizovaných tvarů může být náročnější než obrábění jednoduchých bloků.
- Povrchové úpravy: Náklady spojené s kuličkováním, bubnováním, eloxováním nebo povlakováním.
- NDT: Náklady na specializované kontroly, jako je CT skenování, včetně času stráveného na zařízení a práce na analýze.
- Zajištění kvality & Dokumentace:
- Úroveň požadovaných kontrol, zkoušek a dokumentace (např. podrobné kontrolní zprávy, certifikace materiálů, záznamy o sledovatelnosti) zvyšuje celkové náklady. Požadavky na výrobu v automobilovém průmyslu (i v malých sériích) jsou obvykle vyšší než u běžných průmyslových prototypů.
Srovnání nákladů: AM vs. tradiční metody (odlévání/kovení)
- Nízké objemy (prototypy, zakázkové díly, ~100-500 kusů): AM je často nákladově efektivnější. Eliminace vysokých počátečních nákladů na nástroje (desítky až stovky tisíc dolarů za formy/lisy) činí AM vysoce konkurenceschopným. Změny konstrukce jsou v AM také levné, zatímco úpravy nástrojů jsou drahé.
- Střední objemy (~500 – ~5 000 kusů): Často se jedná o šedou zónu. Náklady na jeden díl u AM zůstávají relativně stabilní, zatímco amortizované náklady na nástroje pro odlévání/kovení výrazně klesají. Bod přechodu do značné míry závisí na složitosti dílu, materiálu a specifických nákladech na výrobu nástrojů v porovnání s výrobou AM. AM může být stále životaschopný, pokud jeho jedinečné výhody (odlehčení, konsolidace) poskytují významnou hodnotu v navazujícím řetězci.
- Vysoké objemy (> ~5 000 – 10 000+ kusů): Tradiční odlévání nebo kování se obvykle stává výrazně levnější na díl, protože vysoké investice do nástrojů se amortizují na mnoho jednotek a doba cyklu na jeden díl je obecně mnohem kratší než doba výroby AM.
Souhrnná tabulka nákladových faktorů:
Nákladový faktor | Klíčové vlivy | Typický dopad na náklady na AM | Poznámky |
---|---|---|---|
Materiál | Typ slitiny (A7075 > AlSi10Mg), Objem dílu (Topology Opt. helps) | Vysoký | Cena prášku za kg |
Strojový čas | Výška/objem dílu, efektivita hnízdění, tloušťka vrstvy | Velmi vysoká | Často největší složka nákladů |
Porod (před/po porodu) | Úsilí DfAM, nastavení sestavení, odstranění podpory, nastavení obrábění, kontrola | Vysoký | Odstranění podpory & obrábění může být velmi pracné |
Následné zpracování | Tepelné zpracování, čas CNC, volba povrchové úpravy, požadavky NDT | Mírná až vysoká | NDT (zejména CT) může výrazně zvýšit náklady |
Zajištění kvality | Úroveň dokumentace, testování, potřeby certifikace | Nízká až střední | Vyšší pro automobilovou výrobu |
VS. Tradiční | Žádné náklady na nástroje | Hlavní výhoda (nízký objem) | Odlévací/kovací nástroje = vysoké počáteční náklady |
VS. Tradiční | Pomalejší doba cyklu | Nevýhoda (vysoký objem) | Odlévání / kování = rychlé časy cyklů, jakmile je nástroj připraven |
Export do archů
Dodací lhůty pro 3D tištěné klouby řízení:
Dodací lhůty v AM jsou také strukturovány jinak než u tradičních metod.
- Vytváření prototypů:
- AM: Výrazně rychlejší. Po dokončení návrhu může být tisk často zahájen během několika dní. Včetně doby tisku (která může být 1-3 dny v závislosti na velikosti/složitosti) a nezbytného následného zpracování (odlehčení napětí, odstranění základních podpěr, případně rychlé obrábění jednoho prvku) lze funkční prototypy často dodat za několik dní 1 až 3 týdny.
- Tradiční: Nejprve je nutné navrhnout a vyrobit nástroje, což může trvat 6-12 týdnů nebo déle. Celková doba výroby prvních odlitých/kovaných prototypů se často počítá na měsíce.
- Malosériová výroba (např. 10-100 kusů):
- AM: Doba realizace do značné míry závisí na dostupnosti stroje, celkové době sestavení (lze vnořit více sestavení?) a na úplném pracovním postupu následného zpracování. Typická doba realizace se může pohybovat od 4 až 8 týdnů, případně déle, pokud je vyžadováno rozsáhlé obrábění nebo složité NDT. Výroba může být často zahájena relativně rychle po potvrzení objednávky.
- Tradiční: Po schválení nástrojů (po zdlouhavé prototypové fázi) může být výroba dílů rychlá (např. stovky za týden). Počáteční doba přípravy nástrojů však dominuje celkovému časovému plánu projektu.
- Faktory ovlivňující dobu dodání AM:
- Složitost dílu & Velikost: Přímo ovlivňuje dobu tisku.
- Požadavky na následné zpracování: Rozsáhlé obrábění nebo specializované úpravy prodlužují čas. Samotné cykly tepelného zpracování trvají hodiny nebo dny.
- Kapacita dodavatele: Dostupnost a počet nevyřízených zakázek u vybraného poskytovatele služeb.
- Objednané množství: Větší dávky mohou vyžadovat více tisků.
- Požadavky na kvalitu: Přísná kontrola a dokumentace prodlužují čas.
Souhrnně lze říci, že analýza nákladů na 3D tisk kovů odhaluje, že silnou stránkou AM’ je eliminace nákladů na nástroje, což z něj činí ideální řešení pro prototypy a malosériovou výrobu, kde je nejdůležitější flexibilita a rychlost. Náklady na jeden díl jsou sice vyšší než u tradičních sériově vyráběných komponent, ale hodnota plynoucí z odlehčení, zvýšení výkonu a urychlení vývoje často ospravedlňuje investici. Pochopení doba realizace aditivní výroby výhody pro výrobu prototypů a počátečních sérií jsou pro plánování projektů v rychle se rozvíjejícím automobilovém průmyslu zásadní.

Závěr: Budoucnost je lehká - využití AM pro pokročilou konstrukci kloubů řízení
Cesta za složitostí 3D tisku hliníkových kloubů řízení odhaluje technologii, která je připravena změnit aspekty konstrukce a výroby automobilových komponent. Využitím síly technologie Laser Powder Bed Fusion (LPBF) s pokročilými hliníkovými slitinami, jako je AlSi10Mg a vysokopevnostní A7075, se konstruktéři mohou osvobodit od omezení tradičního odlévání a kování. Na stránkách výhody lehkých kloubů řízení realizované aditivní výrobou jsou nepopiratelné: výrazné snížení neodpružené hmotnosti vedoucí k lepší dynamice vozidla, lepší palivová/energetická účinnost, která je pro elektromobily zásadní, a bezkonkurenční konstrukční svoboda umožňující optimalizaci topologie a konsolidaci dílů.
Prozkoumali jsme klíčovou roli návrhu pro aditivní výrobu (DfAM), dosažitelné úrovně přesnosti a zásadní povahu následných kroků zpracování, jako je tepelné zpracování a CNC obrábění. Také jsme se seznámili s běžnými problémy a zdůraznili, že s odbornými znalostmi, řízením procesu a vysoce kvalitními materiály jsou tyto překážky překonatelné. Ekonomická analýza zdůrazňuje jasné výhody AM’v oblasti rychlé výroby prototypů a malosériové výroby, což urychluje vývojové cykly a umožňuje individuální řešení, která byla dříve nedostupná.
The budoucnost automobilových komponentů, zejména ve výkonnostních segmentech, u elektrických vozidel a ve výklenkových aplikacích, bude stále více zahrnovat aditivní výrobu. Klouby řízení slouží jako názorný příklad toho, jak může AM přinést hmatatelné výkonnostní výhody díky výrobě složitých, vysoce optimalizovaných a lehkých struktur, které dříve jednoduše nebyly proveditelné.
Využití tohoto potenciálu však vyžaduje spolupráci a odborné znalosti. Výběr správného partnera pro AM - partnera s prokazatelnými schopnostmi v oblasti materiálů, řízení procesů, zajištění kvality a hlubokým porozuměním požadavkům automobilového průmyslu - je pro úspěch klíčový.
Met3dp je připraven být tímto partnerem. Díky našim integrovaným schopnostem, které zahrnují pokročilou výrobu kovových prášků pomocí špičkových technik atomizace a výrobu vysoce výkonných tiskáren SEBM a LPBF, známých svou přesností a spolehlivostí, nabízíme komplexní řešení. Náš tým disponuje desítkami let společných zkušeností v oblasti aditivní výroby kovů a je připraven vám pomoci při zkoumání možností AM pro vaše automobilové komponenty.
Jste připraveni prozkoumat, jak mohou 3D tištěné hliníkové komponenty změnit váš příští automobilový projekt? Ať už jste inženýr, který se snaží posouvat hranice výkonnosti, nebo manažer nákupu, který hledá inovativní a agilní výrobní řešení, zveme vás, abyste se s námi spojili.
Navštivte naše webové stránky na adrese https://met3dp.com/ a dozvíte se více o našich technologiích a službách, nebo nás kontaktujte přímo a prodiskutujte s námi vaše konkrétní potřeby. Met3dp vám pomůže odhalit budoucnost lehké a vysoce výkonné výroby automobilů.
Často kladené otázky (FAQ)
Otázka 1: Jsou 3D tištěné hliníkové klouby řízení dostatečně pevné a bezpečné pro použití v automobilovém průmyslu?
A: Ano, rozhodně, pokud jsou správně navrženy, vyrobeny a ověřeny. Bezpečnost a pevnost závisí na několika faktorech:
- Správný návrh (DfAM): Využití optimalizace topologie a metody konečných prvků pro zajištění toho, aby konstrukce odolala všem provozním zatížením s odpovídajícími bezpečnostními faktory.
- Výběr materiálu: Výběr správné slitiny (např. AlSi10Mg nebo A7075) pro požadované pevnostní a únavové vlastnosti.
- Kvalitní tiskový proces: Použití průmyslových strojů LPBF s ověřenými parametry pro výrobu plně hustých dílů (>99,5 %) s minimem vad (pórovitost, trhliny). To vyžaduje vysoce kvalitní prášek a přísnou kontrolu procesu.
- Správné následné zpracování: Provedení nezbytného uvolnění napětí a tepelného zpracování (např. temperace T6) pro dosažení optimálních mechanických vlastností.
- Důkladné testování & Validace: Provádění důkladných mechanických zkoušek (tahových, únavových) a NDT (zejména CT skenování) s cílem ověřit strukturální integritu a zajistit, aby díl splňoval nebo překračoval výkonnostní normy OEM nebo regulační normy. Pokud jsou tyto kroky pečlivě dodržovány zkušenými poskytovateli, mohou být 3D tištěné klouby stejně bezpečné a pevné, nebo dokonce silnější, pokud jde o měrnou pevnost (poměr pevnosti k hmotnosti), jako tradičně vyráběné protějšky.
Otázka 2: Je 3D tisk pro klouby řízení nákladově efektivní ve srovnání s odléváním nebo kováním?
A: Nákladová efektivita je velmi závislá na objemu výroby:
- Prototypy & Velmi nízký objem (< 10-50 kusů): AM je obecně vysoce nákladově efektivní protože se zcela vyhýbá masivním počátečním investicím do odlévacích forem nebo kovářských zápustek.
- Nízký až střední objem (~50 – ~1000 jednotek): AM zůstává konkurenceschopná a často představuje ekonomicky nejvýhodnější volbu, zejména pokud vezmeme v úvahu výhody rychlosti a flexibility konstrukce. Bod přechodu se liší v závislosti na složitosti.
- Velký objem (>> 1000 kusů): Tradiční odlévání nebo kování je obvykle výrazně levnější na díl díky úsporám z rozsahu a rychlejším časům cyklů za předpokladu stabilní konstrukce, kdy lze náklady na nástroje amortizovat na mnoho jednotek. Nicméně i při vyšších objemech může být AM opodstatněná, pokud umožňuje konstrukci, která poskytuje podstatné odlehčení nebo výkonnostní výhody nedosažitelné tradičními prostředky, což vede k vyšší celkové hodnotě systému (např. výrazně prodloužený dojezd elektromobilu).
Otázka 3: Lze u hliníkového kloubu vytištěného na 3D tiskárně dosáhnout stejné únavové životnosti jako u kovaného kloubu?
A: Dosažení srovnatelné nebo potenciálně i vyšší únavové životnosti je možné pomocí 3D tištěných hliníkových kloubů, ale vyžaduje to pečlivou pozornost věnovanou detailům v celém procesu:
- Optimalizace designu: Optimalizace topologie může vytvořit konstrukce s plynulejším tokem napětí, což může snížit koncentraci napětí ve srovnání s některými tradičními konstrukcemi.
- Integrita materiálu: Minimalizace vnitřních defektů, jako je pórovitost, prostřednictvím optimalizovaného tisku je velmi důležitá, protože póry slouží jako iniciační místa únavy. Klíčové jsou vysoce kvalitní prášek a kontrola procesu.
- Povrchová úprava: Povrchy vytištěné as tiskem mohou být drsné, což může mít vliv na únavu. Kroky následného zpracování, jako např kuličkování jsou velmi účinné při zavádění příznivých tlakových napětí na povrchu, což výrazně zvyšuje únavovou odolnost, často nad rámec odolnosti neleštěných kovaných dílů. Obráběním kritických oblastí se také odstraňují potenciálně drsné povrchy po otisknutí.
- Výběr materiálu & Tepelné zpracování: Použití vysokopevnostních slitin, jako je A7075 (správně zpracovaných), a zajištění správného tepelného zpracování přispívá k lepší únavové výkonnosti. Zatímco kované díly těží z kované mikrostruktury, dobře navržený, s minimem vad a vhodně dodatečně zpracovaný AM díl může splnit nebo překročit požadavky na únavu pro náročné aplikace. Zásadní je ověření pomocí důkladných únavových zkoušek.
Sdílet na
MET3DP Technology Co., LTD je předním poskytovatelem řešení aditivní výroby se sídlem v Qingdao v Číně. Naše společnost se specializuje na zařízení pro 3D tisk a vysoce výkonné kovové prášky pro průmyslové aplikace.
Dotaz k získání nejlepší ceny a přizpůsobeného řešení pro vaše podnikání!
Související články
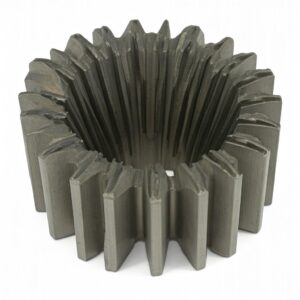
Vysoce výkonné segmenty lopatek trysek: Revoluce v účinnosti turbín díky 3D tisku z kovu
Přečtěte si více "O Met3DP
Nedávná aktualizace
Náš produkt
KONTAKTUJTE NÁS
Nějaké otázky? Pošlete nám zprávu hned teď! Po obdržení vaší zprávy obsloužíme vaši žádost s celým týmem.
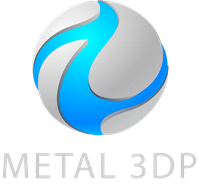
Kovové prášky pro 3D tisk a aditivní výrobu