Metal AM for Aerospace Sensor Housings
Obsah
Introduction: The Critical Role of Sensor Housings in Aerospace and the Metal AM Advantage
In the demanding realm of aerospace engineering, every component, no matter how seemingly small, plays a critical role in ensuring safety, reliability, and optimal performance. Among these essential parts are sensor housings – the protective enclosures that shield delicate sensing instruments from the extreme conditions encountered during flight and space exploration. These housings are far more than simple boxes; they are meticulously engineered components designed to maintain sensor integrity, ensure accurate data acquisition, and withstand G-forces, vibrations, extreme temperatures, corrosive environments, and potential impacts. From monitoring engine parameters and flight control surfaces to tracking structural health and cabin environment, sensors are the nerve endings of modern aircraft and spacecraft, and their housings are the vital armor that allows them to function flawlessly.
Traditionally, manufacturing these critical housings involved subtractive methods like CNC machining, where parts are carved from solid blocks of metal. While effective, machining often faces limitations, especially when dealing with highly complex internal geometries required for optimal sensor placement, cooling channels, or integrated mounting features. Furthermore, the drive for lightweighting – reducing component mass to improve fuel efficiency and payload capacity – pushes engineers to seek innovative manufacturing solutions that can produce strong yet lightweight structures, often involving intricate designs that are difficult or impossible to machine economically. This is where Výroba aditiv kovů (AM), běžně známý jako kov 3D tisk, emerges as a transformative technology.
Metal AM builds parts layer by layer directly from digital models using high-performance metal powders. This additive approach fundamentally changes the design and manufacturing paradigm. It allows engineers to:
- Create Complex Geometries: Internal cooling channels, conformal designs, integrated brackets, and complex lattice structures for weight reduction become feasible without the constraints of traditional tooling or machining access.
- Consolidate Parts: Multiple components of a sensor assembly (e.g., housing, bracket, connectors) can potentially be consolidated into a single, integrated 3D printed part, reducing assembly time, weight, and potential points of failure.
- Achieve Significant Weight Reduction: Techniques like topology optimization and the use of internal lattice structures allow for material placement only where structurally necessary, drastically reducing weight without compromising strength – a paramount goal in aerospace.
- Accelerate Prototyping and Production: Metal AM enables rapid iteration during the design phase and can be significantly faster for producing low-volume, highly complex parts compared to the tooling and setup required for traditional methods.
- Utilize Advanced Materials: AM processes work effectively with high-performance aerospace alloys like Titanium (e.g., Ti-6Al-4V) and high-strength Stainless Steels (e.g., 316L), ensuring the final part meets stringent material property requirements.
For procurement managers and engineers in the aerospace sector sourcing custom or low-volume sensor housings, metal AM offers a compelling value proposition. It opens doors to enhanced sensor performance through optimized housing design, contributes to overall platform efficiency via lightweighting, and can provide a faster route to market for new sensor integrations. Companies like Met3dp, specializing in industrial metal 3D printing solutions including advanced equipment and high-quality metal powders, are at forefront of enabling these advancements for demanding sectors like aerospace. Understanding the capabilities and nuances of metal AM is becoming increasingly crucial for staying competitive and innovative in aerospace component design and manufacturing.
What are Aerospace Sensor Housings Used For? Applications and Demands
Aerospace sensor housings are indispensable components found throughout virtually every system of an aircraft, spacecraft, drone, or missile. Their primary function is to protect sensitive electronic, optical, or mechanical sensors from the demanding and often brutal operating conditions inherent in aerospace environments, while simultaneously facilitating the sensor’s function – whether that’s measuring pressure, temperature, acceleration, strain, proximity, or electromagnetic fields. The specific design and material of a housing are dictated by the sensor type, its location, and the environmental hazards it must endure.
Key Application Areas and Associated Demands:
- Propulsion Systems (Engines, Rockets):
- Sensors: Temperature probes (EGT), pressure transducers, vibration sensors, speed sensors, flame detectors.
- Demands: Extreme temperatures (often exceeding 1000°C), high vibration levels, exposure to corrosive combustion byproducts, high pressures, thermal cycling, potential for foreign object damage (FOD). Housings must provide thermal insulation or facilitate cooling, withstand intense vibration without fatigue failure, and resist chemical attack. Material selection (often Nickel-based superalloys or specific Titanium grades) is critical.
- Flight Control Systems:
- Sensors: Position sensors (LVDTs, RVDTs) for actuators, angle of attack (AoA) sensors, pitot-static probes (airspeed, altitude), accelerometers, gyroscopes (inertial measurement units – IMUs).
- Demands: High reliability and accuracy are paramount for flight safety. Housings must maintain precise alignment for sensors, withstand aerodynamic loads and flutter, resist contamination (icing, dust, fluids), provide electromagnetic interference (EMI) shielding, and endure significant vibration and G-forces. Lightweighting is often a key consideration.
- Structural Health Monitoring (SHM):
- Sensors: Strain gauges, fiber optic sensors (FOS), acoustic emission sensors, crack detection sensors.
- Demands: Sensors are often embedded within or mounted directly onto critical structural components (wings, fuselage, landing gear). Housings must be low-profile, conform to complex surfaces, ensure intimate contact for accurate strain transfer, withstand fatigue loading cycles mirroring the airframe’s life, and resist environmental degradation (moisture, de-icing fluids). Part consolidation through AM can be highly beneficial here.
- Environmental Control Systems (ECS) & Cabin Monitoring:
- Sensors: Temperature sensors, pressure sensors, humidity sensors, air quality sensors (CO2, O2, ozone), smoke detectors.
- Demands: Long-term stability, resistance to cabin environments (cleaning agents, moisture), hermetic sealing in some cases, compliance with fire safety regulations (material flammability), and often aesthetic considerations for cabin-visible components. EMI shielding might be required to prevent interference with other aircraft systems.
- Avionics and Navigation Systems:
- Sensors: GPS antennas, proximity sensors (landing gear, doors), temperature sensors for cooling avionics bays, IMUs.
- Demands: EMI/RFI shielding is critical to prevent interference. Housings need to manage heat generated by electronics, withstand vibration and shock loads, and potentially meet specific radar cross-section (RCS) requirements for defense applications. Secure mounting and precise alignment are essential.
- Space Applications (Satellites, Launch Vehicles):
- Sensors: Star trackers, sun sensors, temperature sensors, pressure sensors, radiation detectors.
- Demands: Extreme temperature variations (deep space vs. solar exposure), vacuum conditions (outgassing constraints), radiation hardening, micrometeoroid/orbital debris (MMOD) protection, extreme vibration and acoustic loads during launch, and absolute minimum weight. Material selection is rigorously controlled.
Common Requirements Across Applications:
- Environmental Sealing: Protecting sensitive electronics from moisture, dust, de-icing fluids, fuel, hydraulic oils, and pressure differentials. Hermetic sealing is often required.
- Vibration and Shock Resistance: Withstanding high G-forces during maneuvers, launch, landing, and engine operation without mechanical failure or sensor damage.
- Tepelný management: Dissipating heat generated by the sensor or insulating it from external temperature extremes. AM allows for integrated cooling channels or heat sinks.
- EMI/RFI Shielding: Preventing electromagnetic interference from affecting sensor readings or other aircraft systems.
- Odolnost proti korozi: Withstanding exposure to atmospheric conditions, salt spray (marine environments), aviation fluids, and potential galvanic corrosion when interfacing with other materials.
- Odlehčení: Minimizing mass to improve fuel efficiency, increase payload capacity, or enhance vehicle agility.
- Precision Mounting: Ensuring the sensor is correctly positioned and oriented for accurate measurements.
- Durability and Longevity: Meeting the operational lifespan requirements of the aircraft or spacecraft, often spanning decades.
- Material Certification and Traceability: Adhering to stringent aerospace standards for materials and manufacturing processes (e.g., AS9100).
Sourcing these specialized housings B2B often involves providing detailed performance specifications, environmental requirements, and interface definitions. Manufacturers and suppliers must demonstrate capability in precision engineering, materials science, and quality assurance to meet the rigorous demands of the aerospace industry. Metal AM provides a powerful toolset to address many of these complex requirements simultaneously.
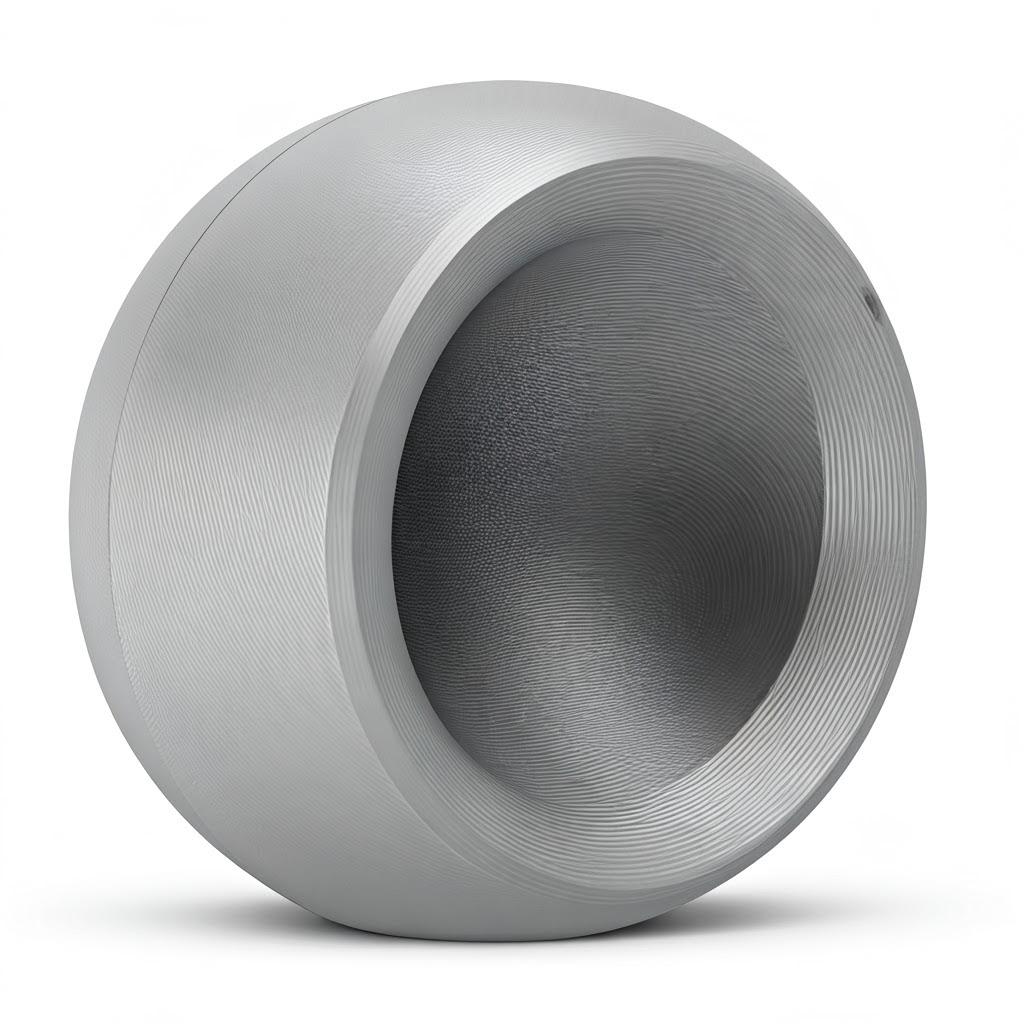
Why Use Metal 3D Printing for Aerospace Sensor Housings? Unlocking Performance
While traditional CNC machining has long been the standard for producing aerospace sensor housings, metal additive manufacturing offers a compelling suite of advantages, particularly when dealing with the complex requirements and performance demands characteristic of modern aerospace applications. Opting for metal AM is not merely about adopting a new technology; it’s about unlocking new levels of design freedom, performance optimization, and manufacturing agility specifically tailored to the challenges of protecting sensitive instruments in extreme environments. For engineers and procurement managers evaluating manufacturing routes, understanding these benefits is key to making informed decisions.
1. Unparalleled Design Freedom and Complexity:
- Challenge with Machining: Traditional subtractive methods are limited by tool access. Creating complex internal features like curved cooling channels, integrated sensor mounts within deep cavities, or conformal pathways for wiring often requires multiple setups, intricate tooling, or designing the part in multiple pieces to be assembled later, adding weight, cost, and potential failure points.
- AM Solution: Metal AM builds parts layer-by-layer, freeing designers from many traditional manufacturing constraints (DFM). This enables:
- Conformal Cooling/Heating Channels: Channels can precisely follow the contours of heat-generating components or the housing’s external shape for maximum thermal efficiency, which is nearly impossible to machine.
- Optimized Internal Structures: Sensor elements can be precisely positioned and secured using integrated mounting features within complex internal cavities, improving accuracy and simplifying assembly.
- Integrated Features: Brackets, connectors, flow straighteners, or even antenna elements can potentially be built directly into the housing structure, consolidating parts.
- Výhody: Enhanced sensor performance (better thermal management, more accurate positioning), reduced part count, simplified assembly, and reduced potential leak paths.
2. Significant Lightweighting Opportunities:
- Aerospace Imperative: Reducing weight is a constant driver in aerospace design to improve fuel efficiency, increase payload, or enhance maneuverability.
- AM Techniques:
- Optimalizace topologie: Software algorithms determine the most efficient load paths, removing material from non-critical areas while maintaining structural integrity. This often results in organic, bone-like structures that are highly efficient but difficult or impossible to machine.
- Mřížové struktury: Internal voids can be filled with engineered lattice structures (e.g., gyroids, honeycombs) that provide significant structural support with minimal mass. These can also enhance vibration damping or thermal dissipation.
- Thin Walls & Complex Shells: AM can produce parts with thinner, yet structurally sound, walls compared to the minimum thicknesses often required for robust machining setups.
- Výhody: Drastic weight reductions (often 20-60% or more compared to traditionally designed parts) without compromising strength or stiffness, directly contributing to platform efficiency.
3. Part Consolidation:
- Traditional Approach: Complex assemblies often consist of multiple machined components fastened or welded together (e.g., housing body, lid, mounting bracket, internal supports). Each interface represents a potential failure point, requires additional assembly labor, and adds tolerance stack-up issues.
- AM Advantage: Metal AM allows designers to redesign assemblies as a single, monolithic component. A housing and its mounting bracket, or multiple internal features, can be printed as one piece.
- Výhody: Reduced assembly time and cost, lower overall weight, improved structural integrity (no joints/fasteners), simplified supply chain management (fewer part numbers), and potentially enhanced sealing.
4. Rapid Prototyping and Accelerated Development Cycles:
- Výzva: Creating prototypes using traditional methods often requires dedicated tooling or significant machine setup time, leading to longer iteration cycles during the design and validation phase.
- AM Speed: Metal AM can produce functional metal prototypes directly from CAD data, often within days rather than weeks or months. This allows engineers to quickly test different design variations for fit, form, and function.
- Výhody: Faster design validation, reduced development costs, quicker time-to-market for new sensor technologies or aircraft programs. B2B suppliers offering rapid prototyping services via AM can significantly shorten development timelines for their clients.
5. Material Capabilities and Suitability:
- Aerospace Materials: Metal AM processes, such as Selective Laser Melting (SLM), Direct Metal Laser Sintering (DMLS), and Electron Beam Melting (EBM) – part of the broader 3D tisk z kovu landscape – are well-suited for processing standard high-performance aerospace alloys like Titanium Ti-6Al-4V and Stainless Steel 316L, as well as nickel superalloys and aluminum alloys.
- Kvalita: Reputable AM providers, like Met3dp, utilize high-quality, spherical metal powders produced using advanced methods like gas atomization, ensuring the final printed parts achieve dense, homogenous microstructures with mechanical properties comparable or even superior to wrought or cast materials after appropriate post-processing (like Hot Isostatic Pressing – HIP).
- Výhody: Enables the use of flight-proven materials while leveraging the geometric advantages of AM, ensuring parts meet stringent aerospace performance and certification requirements.
6. Suitability for Low-Volume, High-Complexity Production:
- Niche Applications: Aerospace often involves producing components, including specialized sensor housings, in relatively low volumes where the cost of creating dedicated tooling for casting or forging would be prohibitive.
- AM Economics: Metal AM is a tool-less process. While the per-part cost might be higher than mass-produced items, it can be highly cost-effective for low-to-medium production runs of complex parts, eliminating tooling investment and setup costs associated with traditional methods.
- Výhody: Provides an economically viable manufacturing route for custom or specialized sensor housings needed for specific platforms or missions, facilitating customization and on-demand manufacturing.
In summary, metal 3D printing offers a powerful alternative to traditional machining for aerospace sensor housings, enabling lighter, more complex, and potentially higher-performing designs. It facilitates part consolidation, accelerates development, and provides a cost-effective solution for low-volume production, making it a critical technology for aerospace manufacturers and their B2B component suppliers seeking a competitive edge.
Recommended Materials (316L & Ti-6Al-4V) and Why They Excel in Aerospace
Selecting the right material is paramount when designing any aerospace component, and sensor housings are no exception. The material must not only provide structural integrity and environmental protection but also be compatible with the sensor itself and the broader aerospace environment. Metal additive manufacturing processes work exceptionally well with several key aerospace alloys. Among the most versatile and frequently specified materials for 3D printed aerospace sensor housings are Nerezová ocel 316L a Titan Ti-6Al-4V. Understanding their properties explains their widespread adoption.
1. 316L Stainless Steel (UNS S31603): The Versatile Workhorse
316L is an austenitic chromium-nickel stainless steel containing molybdenum, which significantly enhances its corrosion resistance, particularly against chlorides and other industrial solvents. The “L” denotes low carbon content (typically <0.03%), which minimizes carbide precipitation during welding or stress relieving, thereby preserving corrosion resistance, especially in the heat-affected zones – a beneficial characteristic for AM parts that undergo thermal cycling during the build and subsequent heat treatments.
Key Properties and Aerospace Relevance:
- Vynikající odolnost proti korozi: This is arguably 316L’s most significant advantage. It exhibits outstanding resistance to atmospheric corrosion, various organic and inorganic chemicals, marine environments (salt spray), de-icing fluids, and other corrosive media commonly encountered in aerospace operations. This makes it ideal for housings exposed to external environments or internal corrosive fluids/gases.
- Good Strength and Ductility: 316L offers a good balance of moderate strength, high ductility, and toughness, even at cryogenic temperatures. While not as strong as titanium alloys or precipitation-hardened steels, its mechanical properties are sufficient for many housing applications that are not primary load-bearing structures. Its ductility allows it to absorb energy and resist cracking under vibration or impact.
- Weldability and Formability: Although less relevant for AM (which builds net shapes), its inherent weldability translates to good processability in Powder Bed Fusion (PBF) techniques like SLM/DMLS.
- Biocompatibility (for certain grades/finishes): While less critical for typical sensor housings, its use in medical implants highlights its inertness.
- Non-Magnetic (in annealed condition): Generally non-magnetic in the fully austenitic, annealed state, which can be important for housings near magnetically sensitive instruments. However, cold working or the delta ferrite present in AM microstructures can induce some magnetism.
- Efektivita nákladů: Compared to titanium or nickel superalloys, 316L is significantly more affordable, making it an attractive option for less demanding applications where extreme lightweighting or very high temperatures are not primary drivers.
- Dostupnost: 316L powder for AM is widely available from reputable suppliers.
Typical Aerospace Applications for 316L Housings:
- Housings for sensors in environmental control systems (ECS), cabin monitoring.
- Enclosures for non-critical avionics or ground support equipment sensors.
- Protective casings in cargo bays or less demanding external locations.
- Fluid handling system sensor interfaces.
- Prototyping housings before committing to more expensive materials.
Omezení:
- Hustota: Significantly denser than titanium or aluminum alloys (approx. 8.0 g/cm³), making it less suitable for applications where weight saving is paramount.
- Temperature Limit: Generally limited to service temperatures below ~425°C (800°F) for continuous service due to decreased strength and potential for sensitization (reduced corrosion resistance) at higher temperatures. Not suitable for engine hot sections.
- Mírná síla: Not ideal for housings subjected to very high structural loads.
Table: Typical Properties of AM 316L (Post-Stress Relief)
Vlastnictví | Typical Value (Varies with Process/Parameters) | Jednotka |
---|---|---|
Hustota | ~7.9 – 8.0 | g/cm³ |
Maximální pevnost v tahu | 500 – 650 | MPa |
Mez kluzu (0,2%) | 250 – 500 | MPa |
Prodloužení po přetržení | 30 – 50 | % |
Tvrdost | 70 – 95 | HRB / ~150-200 HV |
Modul pružnosti | ~190 | GPa |
Maximální provozní teplota | ~425 | °C |
Export do archů
2. Titanium Ti-6Al-4V (Grade 5, UNS R56400): The Aerospace Champion
Ti-6Al-4V (often abbreviated as Ti64) is the most widely used titanium alloy, accounting for more than 50% of all titanium tonnage worldwide. It’s an alpha-beta alloy offering an exceptional combination of high strength, low density, excellent corrosion resistance, and good performance at moderately elevated temperatures. Its properties make it a staple material in aerospace structures, engines, and components, including sensor housings.
Key Properties and Aerospace Relevance:
- Vynikající poměr pevnosti k hmotnosti: This is Ti64’s defining characteristic and primary advantage in aerospace. It offers strength comparable to many steels but at roughly 56% of the density (approx. 4.43 g/cm³ vs. ~7.9 g/cm³ for steel). This allows for significant weight savings in sensor housings without compromising structural integrity, directly impacting fuel efficiency and payload capacity.
- Vynikající odolnost proti korozi: Ti64 exhibits exceptional resistance to a wide range of corrosive environments, including seawater, marine atmospheres, oxidizing acids, chlorides, and many industrial chemicals. Its corrosion resistance often surpasses that of stainless steels, especially in chloride-containing environments.
- High Fatigue Strength: Critical for components subjected to cyclic loading and vibration, such as those mounted on engines or airframes. Proper processing (including HIP) is crucial to minimize defects and maximize fatigue life in AM Ti64 parts.
- Elevated Temperature Capability: Ti64 retains good strength and creep resistance up to temperatures around 315°C (600°F), with intermittent use possible up to ~400-500°C depending on the application and duration. This makes it suitable for housings located near engines or in hot zones where 316L would be inadequate.
- Biokompatibilita: Widely used for medical implants due to its excellent biocompatibility and inertness.
- Nízká tepelná roztažnost: Has a relatively low coefficient of thermal expansion, which can be advantageous for maintaining dimensional stability and minimizing stress when joined with other materials over temperature changes.
- Nemagnetické: Ti64 is non-magnetic, beneficial for applications near sensitive instruments.
Typical Aerospace Applications for Ti-6Al-4V Housings:
- Housings for sensors in engine environments (within temperature limits).
- Flight control system sensor enclosures (e.g., AoA sensors, actuator position sensors).
- Structural health monitoring sensor housings mounted on critical airframe parts.
- Avionics housings where lightweighting and EMI shielding are critical.
- Spacecraft sensor housings (low outgassing, radiation tolerance needs consideration).
- Any application where minimizing weight is a primary design driver.
Omezení:
- Náklady: Significantly more expensive than stainless steel or aluminum alloys, both in terms of raw material powder and processing.
- Reactivity at High Temperatures: Titanium reacts readily with oxygen, nitrogen, and hydrogen at elevated temperatures (above ~600°C), requiring controlled atmosphere or vacuum environments during AM processing and heat treatment.
- Obrobitelnost: Can be more challenging to machine during post-processing steps compared to steels, requiring specific tools and techniques.
- Galling Tendency: Titanium alloys have a tendency to gall (seize) when in sliding contact with other metals, requiring careful consideration for interfaces with moving parts or fasteners.
Table: Typical Properties of AM Ti-6Al-4V (Post-HIP and Heat Treatment)
Vlastnictví | Typical Value (Varies with Process/Parameters/Heat Treat) | Jednotka |
---|---|---|
Hustota | ~4.43 | g/cm³ |
Maximální pevnost v tahu | 900 – 1150 | MPa |
Mez kluzu (0,2%) | 830 – 1050 | MPa |
Prodloužení po přetržení | 10 – 18 | % |
Tvrdost | 32 – 38 | HRC / ~300-350 HV |
Modul pružnosti | ~110 – 115 | GPa |
Maximální provozní teplota | ~315 (Continuous), up to 500 (Intermittent) | °C |
Export do archů
Met3dp’s Role in Material Excellence:
Choosing the right material is only part of the equation; the quality of the metal powder used in the AM process is equally critical for achieving the desired performance and reliability in aerospace components. This is where specialized providers like Met3dp play a crucial role. Met3dp employs industry-leading powder production technologies, including Vacuum Induction Melting Gas Atomization (VIGA) a Proces plazmové rotující elektrody (PREP).
- Atomizace plynu: Molten metal is atomized using high-pressure inert gas jets, creating fine, spherical powder particles. Met3dp’s unique nozzle and gas flow designs optimize this process to yield powders with high sphericity, good flowability, low satellite content, and controlled particle size distribution – all essential for consistent PBF processing and achieving high density in the final part.
- PREP: A consumable electrode of the desired alloy is rotated at high speed while being melted by a plasma torch. Centrifugal force throws off molten droplets that solidify in flight into highly spherical powders with very few internal pores or satellites. PREP is particularly well-suited for reactive materials like titanium and refractory metals, producing exceptionally clean powders.
By leveraging these advanced manufacturing systems, Met3dp ensures its portfolio of metal powders, including aerospace grades like Ti-6Al-4V and various stainless steels (like 316L), meets the stringent quality requirements of the aerospace industry. High sphericity ensures good powder bed packing and flowability in the printer, while low porosity and high purity in the powder translate directly to superior mechanical properties (especially fatigue strength) and material integrity in the final 3D printed sensor housing. Partnering with a supplier that controls powder quality from atomization onwards provides greater assurance for demanding B2B aerospace applications.
In conclusion, both 316L Stainless Steel and Ti-6Al-4V Titanium offer unique advantages for metal 3D printed aerospace sensor housings. 316L provides excellent corrosion resistance and cost-effectiveness for less demanding applications, while Ti-6Al-4V delivers an unmatched combination of high strength, low weight, and good temperature capability, making it the preferred choice for performance-critical and weight-sensitive aerospace components. The ability to process these materials effectively via AM, using high-quality powders, unlocks significant potential for optimizing sensor protection and performance. Sources and related content
Design Considerations: Optimizing Sensor Housings for Metal Additive Manufacturing (DfAM)
Transitioning from traditional manufacturing methods like CNC machining to metal additive manufacturing isn’t just about swapping one machine for another; it requires a fundamental shift in design philosophy. To truly harness the power of metal AM for aerospace sensor housings, engineers must embrace Design pro aditivní výrobu (DfAM). DfAM is a set of principles and techniques aimed at optimizing a part’s design to leverage the unique capabilities and address the specific constraints of AM processes. Applying DfAM to sensor housings can lead to components that are lighter, stronger, more functional, and potentially more cost-effective to produce than their traditionally manufactured counterparts. Ignoring DfAM often results in parts that are difficult to print, require excessive post-processing, or fail to deliver the full performance benefits AM promises.
Key DfAM Principles for Aerospace Sensor Housings:
- Leverage Geometric Complexity:
- Mindset Shift: In traditional manufacturing, complexity often equates to higher cost and longer lead times due to intricate tooling or multiple machining setups. In AM, complexity is largely “free” – printing a highly intricate shape takes roughly the same time and material as printing a simple block of the same volume.
- Sensor Housing Application: This freedom allows for:
- Conformal Internal Features: Design internal cavities that perfectly match the sensor’s shape for optimal placement, support, and thermal contact.
- Integrated Channels: Incorporate winding internal channels for cooling fluids, purging gases, or routing wiring directly within the housing walls, eliminating the need for separate tubing or complex drilling/assembly.
- Optimized Mounting Interfaces: Create non-planar or complex mounting surfaces that conform perfectly to curved aircraft structures or integrate vibration-damping features.
- Bio-Inspired Designs: Mimic natural structures (like bone) for maximum strength with minimum material usage.
- Plánování strategické podpůrné struktury:
- Necessity: Most metal Powder Bed Fusion (PBF) processes require support structures for overhanging features (typically angles steeper than 45° relative to the build plate) and to anchor the part to the build plate, managing thermal stresses.
- DfAM Approach:
- Minimalizujte převisy: Orient the part on the build plate to reduce the number and extent of overhangs requiring support.
- Self-Supporting Angles: Design overhangs with angles less than 45° where possible, or use chamfers and fillets instead of sharp horizontal edges. Teardrop shapes are often preferred over simple circles for horizontal holes to make them self-supporting.
- Accessibility for Removal: This is CRITICAL. Supports must be removable without damaging the part. Consider tool access, especially for internal supports within cavities or channels. Design access ports if necessary, which might be sealed later. Avoid supports in areas with critical surface finish requirements if possible.
- Optimize Support Type: Utilize software to generate efficient support structures (e.g., lattice supports, thin-walled supports) that use less material, print faster, and are easier to remove. Consider break-away or stress-engineered supports.
- Sensor Housing Specifics: Supports inside deep sensor cavities or narrow cooling channels can be particularly challenging to remove; design these features with removal methods (e.g., machining access, soluble supports if available/compatible, flow-through design for flushing) in mind from the start.
- Optimize Wall Thickness:
- Minimum Limits: AM processes have minimum printable feature sizes, including wall thickness (often 0.3mm – 1.0mm depending on the process, material, and wall height). Design walls thick enough to be reliably printed and possess the necessary structural integrity.
- Maximum Limits (Thermal Management): Avoid overly thick, solid sections. Large solid volumes increase print time, material consumption, and susceptibility to residual stress and potential distortion. They can also hinder heat dissipation.
- Sensor Housing Application: Use thin walls where structurally permissible, potentially reinforced with internal ribs or lattices. Vary wall thickness strategically – thicker around mounting points or sealing interfaces, thinner elsewhere. Consider hollow sections or internal lattices instead of solid blocks.
- Design for Thermal Management:
- Sensor Heat: Many sensors generate heat, and aerospace environments can involve extreme external temperatures. Effective thermal management is crucial for sensor accuracy and lifespan.
- AM Solutions:
- Integrated Heat Sinks: Design fins, pins, or other extended surfaces directly into the housing exterior to maximize surface area for convective or radiative cooling.
- Konformní chladicí kanály: As mentioned earlier, route internal liquid or air cooling channels precisely where needed, following the contours of heat sources.
- Material Choice & Lattices: Select materials with appropriate thermal conductivity (e.g., certain aluminum alloys if suitable, though less common for housings than Ti or Steel) or utilize lattice structures which can influence thermal pathways.
- Výhody: AM allows thermal management features to be integrated seamlessly, often far more effectively than attaching separate heat sinks or routing external cooling lines.
- Embrace Lightweighting Strategies:
- Aerospace Priority: Reducing mass is always a goal.
- DfAM Techniques:
- Optimalizace topologie: Use software to identify and remove material from areas that do not contribute significantly to the load-bearing requirements, resulting in efficient, often organic-looking structures. Requires Finite Element Analysis (FEA) to define load cases accurately.
- Mřížové struktury: Replace solid volumes with internal lattice structures (e.g., cubic, gyroid, diamond). These can significantly reduce weight while maintaining considerable stiffness and strength. Lattice types can be chosen to optimize for properties like energy absorption (vibration damping) or permeability (for flow). Varying lattice density within a part allows for localized strengthening.
- Sensor Housing Example: A bulky, machined housing might be redesigned using topology optimization for its main structure and lattice infill for less critical volumes, achieving substantial weight savings while meeting mounting and protection requirements.
- Facilitate Part Consolidation:
- Concept: Redesign assemblies of multiple components into a single, monolithic printed part.
- Sensor Housing Opportunities:
- Integrate mounting brackets directly into the housing body.
- Combine housing halves or a body and lid into one piece (consider accessibility for sensor installation/maintenance).
- Incorporate cable guides, connector mounts, or flow conditioning features.
- Výhody: Reduced part count, eliminated assembly steps/costs, lighter weight (no fasteners), improved reliability (fewer joints), simplified inventory and logistics for B2B suppliers and customers.
- Plan for Post-Processing:
- Inevitability: Recognize that most aerospace AM parts require post-processing (see next section).
- DfAM Considerations:
- Machining Allowance: Add extra stock material (e.g., 0.5-1.0mm) specifically on surfaces that require tight tolerances or smooth finishes via CNC machining.
- Workholding: Design features (e.g., flat surfaces, temporary lugs) that can be used to securely hold the part during machining or other post-processing steps. These might be removed later.
- Surface Accessibility: Ensure critical surfaces requiring finishing (polishing, machining) are accessible.
By thoughtfully applying these DfAM principles, engineers can move beyond simply replicating machined designs and start creating truly optimized aerospace sensor housings that fully exploit the advantages of metal additive manufacturing. This requires collaboration between design engineers, AM process experts, and stress analysts, often facilitated by specialized software tools.
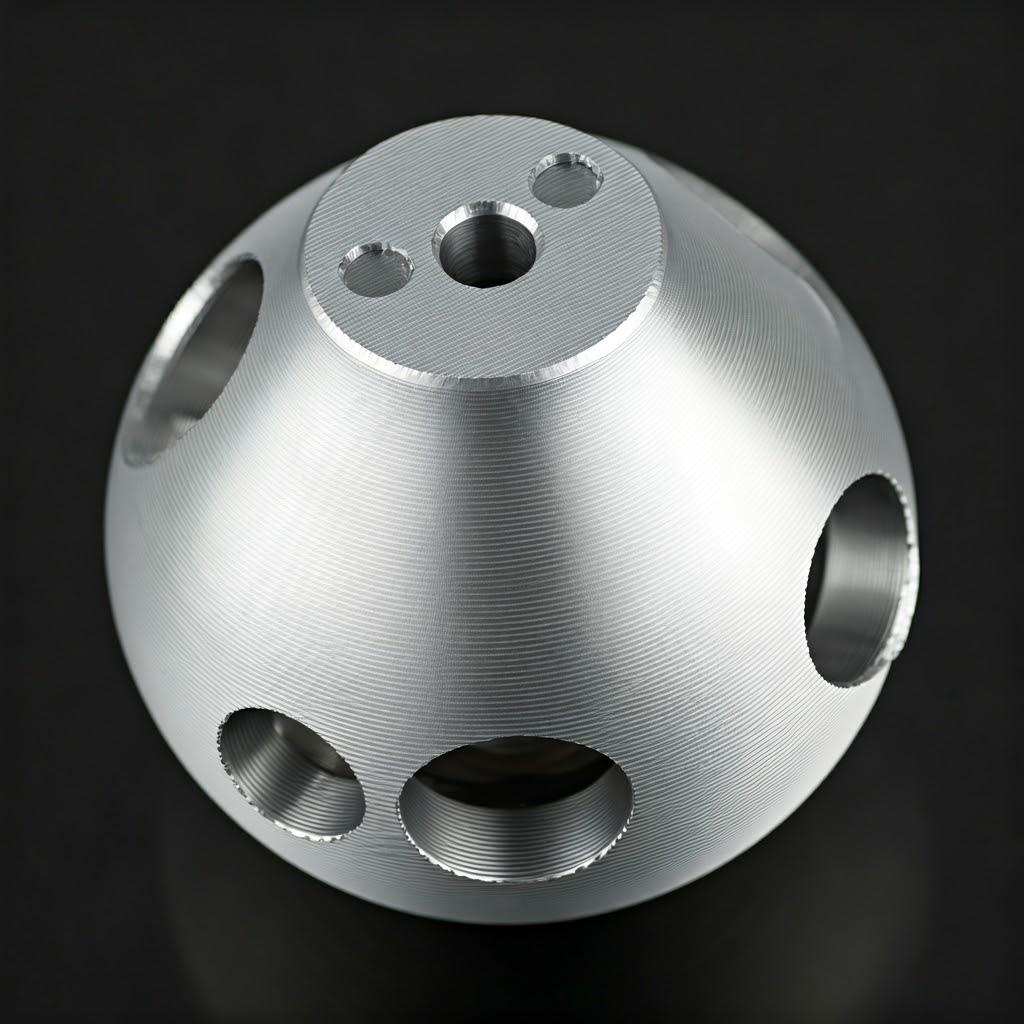
Achieving Precision: Tolerance, Surface Finish, and Dimensional Accuracy in Metal AM
While metal additive manufacturing unlocks incredible geometric freedom, a common question from engineers and procurement managers familiar with the tight precision of CNC machining revolves around the achievable tolerances, surface finish, and overall dimensional accuracy of 3D printed metal parts. Understanding these aspects is crucial for determining if metal AM is suitable for a specific aerospace sensor housing application and for planning necessary post-processing steps.
Typical Tolerances in Metal Powder Bed Fusion (PBF):
Metal PBF processes like Selective Laser Melting (SLM), Direct Metal Laser Sintering (DMLS), and Electron Beam Melting (EBM) – technologies central to industrial Způsoby tisku – offer good dimensional accuracy, but typically not matching the sub-millimeter precision of high-end CNC machining in their as-printed state.
- General Rule of Thumb: A widely cited tolerance range for as-printed metal AM parts is ±0.1 mm to ±0.2 mm for small features (e.g., up to 20-50 mm), and ±0.1% to ±0.2% of the nominal dimension for larger features.
- Influencing Factors: Actual achievable tolerances depend heavily on:
- Kalibrace stroje: Accuracy of the machine’s optics, scanners, and motion system.
- Parametry procesu: Laser/beam power, scan speed, layer thickness, hatch spacing. Optimized parameters lead to better accuracy.
- Materiál: Different materials exhibit varying shrinkage and thermal behavior.
- Part Geometry & Size: Larger parts and complex geometries are more prone to thermal distortion, potentially affecting accuracy.
- Orientace na stavbu: The direction a feature is built relative to the layers can impact its dimensional accuracy. Vertical walls are often more accurate than sloped or curved surfaces.
- Thermal Stresses: Residual stresses can cause warping, especially after removal from the build plate, impacting final dimensions. Stress relief protocols are critical.
- Kvalita prášku: Consistent particle size distribution and morphology contribute to stable melting and better accuracy. High-quality powders, like those produced by Met3dp using advanced atomization, promote process stability.
Povrchová úprava (drsnost):
The surface finish of as-printed metal AM parts is significantly rougher than typical machined surfaces. This is due to the layer-by-layer nature of the process and the partially melted powder particles adhering to the surface.
- Typical Ra Values:
- Laser Powder Bed Fusion (L-PBF – SLM/DMLS): Obvykle se pohybuje od 5 µm to 15 µm Ra (Roughness Average). Vertical walls are generally smoother than up-facing or down-facing horizontal surfaces or sloped surfaces. Down-facing surfaces directly above support structures tend to be the roughest.
- Tavení elektronovým svazkem (EBM): Often produces rougher surfaces than L-PBF, typically in the range of 20 µm to 35 µm Ra, due to higher process temperatures and larger powder particle sizes.
- Srovnání: For context, standard CNC machining can easily achieve finishes of 1.6 µm to 3.2 µm Ra, and grinding or polishing can reach below 0.8 µm Ra.
- Implications for Sensor Housings: As-printed surfaces may be acceptable for non-critical external surfaces or internal features. However, surfaces requiring sealing (e.g., O-ring grooves, mating flanges), precise sensor mounting, or smooth flow for internal channels will almost certainly require post-processing (machining, polishing). Rough surfaces can also be detrimental to fatigue life due to acting as stress concentrators.
Factors Affecting Surface Finish:
- Tloušťka vrstvy: Thinner layers generally result in smoother surfaces but increase build time.
- Velikost částic prášku: Finer powders tend to produce smoother finishes.
- Parametry procesu: Energy density (laser/beam power, speed) affects melt pool stability and surface quality.
- Orientace na stavbu: Surfaces parallel to the build direction (vertical walls) are usually the smoothest. Sloped and horizontal surfaces exhibit layer stepping effects. Down-facing surfaces are influenced by the supports used.
Achieving Critical Tolerances and Finishes:
For aerospace sensor housings, certain features demand high precision:
- Mounting Interfaces: Holes and surfaces for attaching the housing to the aircraft structure.
- Sealing Surfaces: Grooves for O-rings or flat surfaces for gasket seals to ensure hermeticity.
- Sensor Fitment Areas: Internal features ensuring precise positioning and alignment of the sensor element.
- Threaded Holes: For fasteners or connectors.
The standard approach to achieve the required precision for these critical features on AM parts is through post-print CNC machining. By incorporating machining allowances into the DfAM phase (adding extra material), these surfaces can be accurately machined to meet tight tolerance requirements (often in the range of ±0.01 mm to ±0.05 mm) and achieve smooth surface finishes (<1.6 µm Ra).
Geometric Dimensioning and Tolerancing (GD&T):
Applying GD&T principles is crucial when specifying requirements for AM parts, just as it is for machined components. GD&T allows designers to define not just size tolerances but also tolerances for form, orientation, location, and runout, ensuring functional requirements are met, especially when parts require post-machining on specific features.
Table: Typical As-Printed vs. Post-Machined Precision (Illustrative)
Vlastnosti | Parametr | Typical As-Printed (L-PBF) | Typical Post-Machined | Jednotka | Poznámky |
---|---|---|---|---|---|
Dimensional | General Tolerance | ±0.1 to ±0.2 / ±0.1-0.2% | ±0.01 to ±0.05 | mm / % | Machining needed for tight tolerances |
Povrchová úprava | Roughness (Ra) | 5 – 15 | < 1.6 (can be < 0.8) | µm | Significant improvement via machining/polishing |
Otvory | Diameter Tolerance | ±0.1 | ±0.01 to ±0.025 | mm | As-printed holes may not be perfectly round |
Flatness | Per 100mm | 0.1 – 0.3 | < 0.05 | mm | Dependent on size, orientation, stress relief |
Export do archů
Conclusion on Precision:
While as-printed metal AM parts may not match the inherent precision of CNC machining across all dimensions and surfaces, they offer sufficient accuracy for many features. For the critical interfaces and high-precision requirements typical of aerospace sensor housings, a hybrid approach combining the geometric freedom of AM with the precision of post-process machining is the standard and most effective strategy. Understanding the capabilities and limitations of as-printed accuracy allows for effective DfAM and process planning, ensuring the final component meets all functional requirements.
Beyond the Print: Essential Post-Processing for Aerospace Sensor Housings
A common misconception about metal 3D printing is that the part emerging from the machine is ready for immediate use. Especially in demanding sectors like aerospace, the reality is quite different. The “as-printed” component represents an intermediate stage, and a series of crucial post-processing steps are typically required to transform it into a functional, reliable, and certified aerospace sensor housing. These steps are essential for relieving stress, removing supports, achieving required tolerances and surface finishes, and ensuring the material possesses the necessary microstructure and mechanical properties for flight. Skipping or improperly executing these steps can compromise the part’s integrity and performance.
Common Post-Processing Workflow for AM Aerospace Components:
- Stress Relief Heat Treatment:
- Účel: The rapid heating and cooling cycles inherent in PBF processes create significant internal stresses within the printed part. These stresses can cause distortion or cracking, particularly when the part is removed from the rigid build plate. Stress relief is a thermal cycle performed before removing the part from the build plate (or immediately after) to reduce these internal stresses.
- Proces: The part, often still attached to the build plate, is heated in a furnace under a controlled atmosphere (inert gas like Argon, or vacuum, especially for Titanium) to a specific temperature below the material’s critical transformation point, held for a period, and then slowly cooled.
- Typical Parameters:
- Ti-6Al-4V: ~650°C – 800°C for 1-4 hours.
- Nerezová ocel 316L: ~550°C – 650°C (though sometimes higher, up to 900°C depending on desired properties, but care needed to avoid sensitization).
- Důležitost: This is arguably the most critical first step to ensure dimensional stability and prevent part failure.
- Part Removal from Build Plate:
- Účel: Separating the printed sensor housing(s) from the base plate they were built upon.
- Metody: Commonly done using wire Electrical Discharge Machining (EDM), band sawing, or sometimes milling/grinding. Wire EDM is often preferred for its precision and minimal mechanical stress induction.
- Úvaha: The interface between the part and the build plate (often involving support structures) needs to be accounted for in the design and removal planning.
- Odstranění podpůrné konstrukce:
- Účel: Removing the temporary structures used to support overhangs and anchor the part during printing.
- Metody: This can be one of the most labor-intensive steps. Methods include:
- Manual Breaking: For easily accessible, frangible supports.
- Hand Tools: Pliers, grinders, chisels (use with caution to avoid damaging the part).
- Obrábění: Milling or grinding away support structures. Often required for robust supports or precise interface cleanup.
- Wire EDM: Can be used for intricate or hard-to-reach supports.
- Výzvy: Accessing and removing internal supports within cavities or channels requires careful DfAM planning. Residual “witness marks” where supports attached may need further finishing.
- Further Heat Treatment (Beyond Stress Relief):
- Izostatické lisování za tepla (HIP):
- Účel: To eliminate internal microporosity (caused by trapped gas or lack-of-fusion defects) inherent in the AM process. HIP significantly improves density (approaching 100% theoretical), ductility, fatigue strength, and fracture toughness – properties critical for aerospace reliability.
- Proces: Parts are heated to high temperatures (e.g., ~900-950°C for Ti64, ~1100-1150°C for 316L) under high isostatic pressure (100-200 MPa) using an inert gas (typically Argon) for several hours. The combination of heat and pressure causes internal voids to collapse and diffusion bond closed.
- Důležitost: Often considered mandatory for fatigue-critical aerospace components, especially those made from Ti-6Al-4V.
- Solution Annealing & Aging (If Applicable):
- Účel: To achieve specific target mechanical properties (e.g., optimizing strength, ductility, hardness) by controlling the material’s microstructure.
- Relevance: More common for precipitation-hardening steels or certain titanium alloys (like heat-treated Ti64 variants) than for standard 316L. The specific cycles depend heavily on the alloy and desired properties.
- Izostatické lisování za tepla (HIP):
- Povrchová úprava:
- Účel: To improve the as-printed surface roughness for functional or aesthetic reasons.
- Metody:
- Abrasive Blasting: Using media like glass beads, aluminum oxide, or ceramic beads to create a uniform matte finish, remove loose powder, and slightly smooth the surface. Can improve fatigue life by inducing compressive stresses but must be controlled.
- Tumbling/Vibratory Finishing: Parts are tumbled with abrasive media to deburr edges and improve surface finish, especially for batches of smaller parts.
- Grinding/Polishing: Manual or automated processes to achieve very smooth, mirror-like finishes on specific surfaces. Often used after machining.
- Electropolishing: An electrochemical process that removes a thin layer of material, smoothing peaks and valleys, enhancing corrosion resistance (for stainless steels), and deburring.
- CNC obrábění:
- Účel: To achieve tight dimensional tolerances, precise geometric features (GD&T), and smooth surface finishes on critical interfaces.
- Applications on Sensor Housings: Machining mounting holes and surfaces, O-ring grooves, sealing faces, connector interfaces, sensor alignment features, and any threads.
- Requirement: Requires careful DfAM planning to include machining stock and workholding features.
- Cleaning and Inspection:
- Cleaning: Thoroughly cleaning the parts to remove any trapped powder (especially from internal channels), machining fluids, or debris. Ultrasonic cleaning baths are often used.
- Inspection: Verifying dimensional accuracy (CMM, laser scanning), surface finish, and material integrity.
- Nedestruktivní zkoušení (NDT): Crucial for aerospace validation. Common methods include:
- Computed Tomography (CT) Scanning: Provides detailed 3D visualization of internal structures to detect voids, inclusions, or geometric deviations within complex housings.
- Dye Penetrant Inspection (DPI): Detects surface-breaking cracks or porosity.
- Ultrazvukové testování (UT): Can detect subsurface flaws.
- Visual Inspection: Magnified visual checks.
- Destructive Testing: Often performed on representative “witness coupons” printed alongside the main parts to verify material properties (tensile strength, yield strength, elongation, hardness) meet specifications.
- Nedestruktivní zkoušení (NDT): Crucial for aerospace validation. Common methods include:
The specific sequence and necessity of these steps depend on the application requirements, material choice, and the AM process used. For a B2B supplier providing aerospace components, having robust, well-documented, and certified post-processing capabilities is as important as the printing process itself.
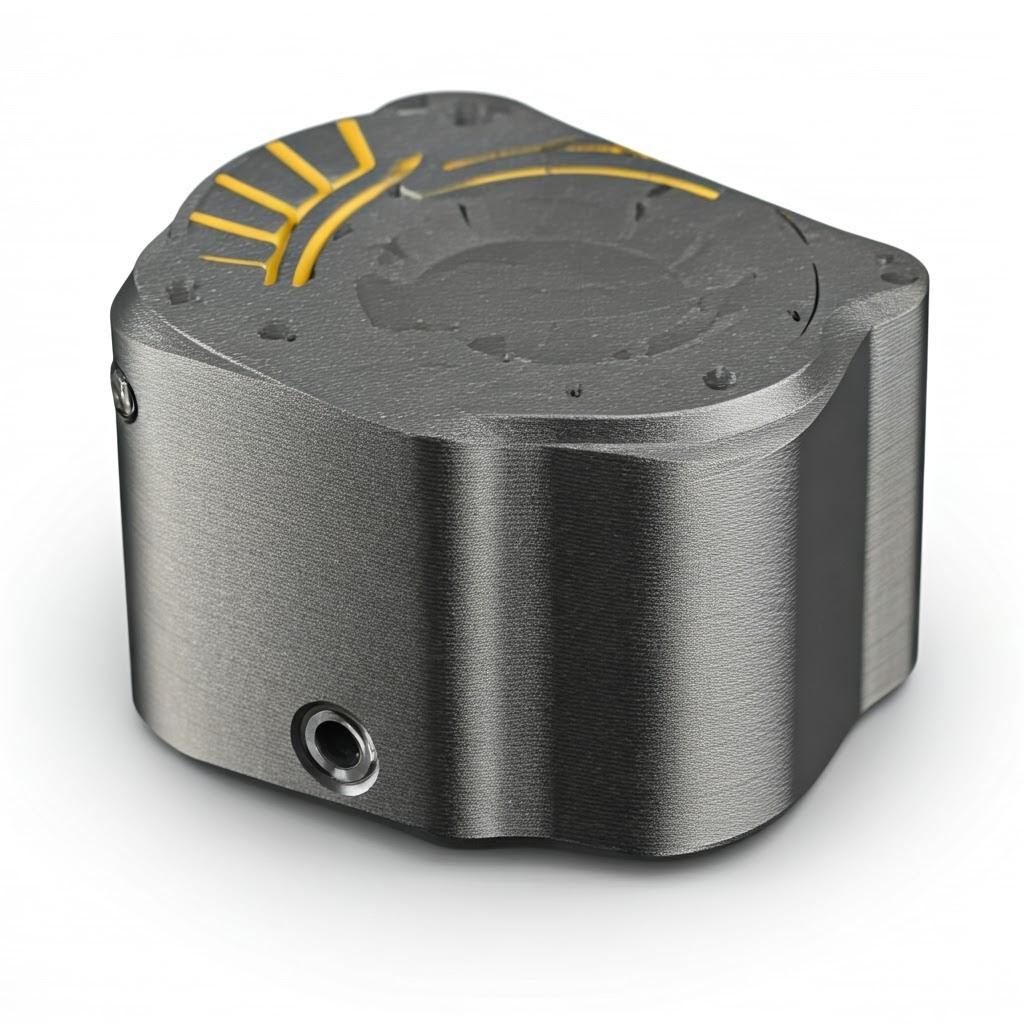
Navigating Challenges in Metal AM for Sensor Housings and Mitigation Strategies
While metal additive manufacturing offers significant advantages for producing complex aerospace sensor housings, the technology is not without its challenges. Achieving consistent, high-quality, flight-ready components requires a deep understanding of potential issues and the implementation of effective mitigation strategies throughout the design, printing, and post-processing phases. Proactively addressing these challenges is key to successfully leveraging AM in the demanding aerospace sector.
Common Challenges and How to Address Them:
- Zbytkové napětí a deformace:
- Výzva: The intense, localized heating and rapid cooling inherent in PBF cause thermal gradients, leading to internal stresses. These stresses can cause parts to warp or distort during the build, upon removal from the build plate, or during post-processing, leading to dimensional inaccuracies or even cracking. Complex geometries and large thermal masses exacerbate this.
- Strategie zmírnění dopadů:
- Optimized Build Orientation: Orienting the part to minimize large flat surfaces parallel to the recoater and reduce thermal gradients across layers.
- Robustní podpůrné struktury: Designing supports not just for overhangs but also to act as heat sinks and anchors, resisting thermal stresses during the build. Simulation tools can help optimize support placement and density.
- Process Parameter Control: Fine-tuning laser/beam power, scan speed, and scan strategies (e.g., island scanning, checkerboard patterns) to manage heat input and reduce temperature gradients.
- Platform Heating: Preheating the build platform (common in L-PBF, inherent in EBM) reduces the temperature difference between the solidified material and the surrounding powder bed.
- Mandatory Stress Relief: Performing a proper stress relief heat treatment before removing the part from the build plate is essential.
- Simulation: Using process simulation software to predict stress accumulation and potential distortion, allowing for design or process adjustments before printing.
- Pórovitost:
- Výzva: Small voids or pores can form within the printed material due to trapped gas (from the powder or shielding gas) or incomplete melting/fusion between layers or scan tracks (lack-of-fusion defects). Porosity degrades mechanical properties, particularly fatigue strength, and can be detrimental in aerospace applications.
- Strategie zmírnění dopadů:
- Vysoce kvalitní prášek: Using powder with low internal gas content, high sphericity, good flowability, and controlled particle size distribution is critical. Sourcing from reputable suppliers like Met3dp, who utilize advanced atomization techniques (VIGA, PREP) and rigorous quality control, minimizes powder-related porosity.
- Optimalizované parametry procesu: Ensuring sufficient energy density (power, speed, layer thickness combination) to achieve complete melting and fusion, while avoiding excessive energy that can cause keyhole porosity (vapor depression collapse). Parameter development is crucial for each material and machine.
- Controlled Atmosphere: Maintaining a high-purity inert gas atmosphere (Argon or Nitrogen for L-PBF) or vacuum (EBM) to prevent oxidation and minimize gas pickup during melting.
- Izostatické lisování za tepla (HIP): The most effective way to close internal porosity post-print, significantly improving density and mechanical properties. Often mandatory for critical parts.
- Cracking:
- Výzva: Cracks can form during printing (solidification cracking) or cooling (liquation or strain-age cracking), especially in alloys susceptible to hot tearing or those with wide freezing ranges. High residual stresses also contribute.
- Strategie zmírnění dopadů:
- Alloy Selection: Some alloys are inherently more crack-prone in AM than others. Choose materials known to have good AM processability where possible.
- Optimalizace parametrů procesu: Controlling heat input and cooling rates through parameter adjustments.
- Geometry Design (DfAM): Avoiding sharp internal corners or abrupt changes in cross-section, which act as stress concentrators. Using generous fillets and radii.
- Úleva od stresu: Prompt and effective stress relief minimizes the driving force for stress-related cracking.
- Preheating: Elevated build platform temperatures can reduce thermal gradients.
- Support Structure Removal Difficulties:
- Výzva: Supports, while necessary, can be difficult, time-consuming, and costly to remove, especially from complex internal geometries like sensor cavities or cooling channels. Incomplete removal can compromise function, and aggressive removal can damage the part surface.
- Strategie zmírnění dopadů:
- DfAM for Support Minimization: Designing self-supporting features, choosing optimal build orientation.
- DfAM for Accessibility: Designing access ports or pathways for tools or flushing to reach internal supports.
- Optimized Support Design: Using software to generate easily removable support types (e.g., conical, perforated, lattice supports).
- Advanced Removal Techniques: Investigating wire EDM, electrochemical machining (ECM), or abrasive flow machining (AFM) for challenging internal supports, though these add cost and complexity.
- Material Choice: Some materials allow for chemical etching of supports, but this is less common for typical aerospace alloys like Ti64 and 316L.
- Surface Roughness and Feature Definition:
- Výzva: As-printed surfaces are inherently rough, and small features (thin walls, sharp edges, small holes) may lack definition or accuracy compared to machining.
- Strategie zmírnění dopadů:
- Orientation and Parameter Optimization: Fine-tuning parameters (e.g., contour scans) and orientation can improve surface finish on critical faces.
- DfAM: Designing features slightly larger or smaller to account for process capabilities (e.g., minimum printable hole size).
- Následné zpracování: Relying on machining, polishing, or blasting to achieve the required surface finish and feature definition on critical areas. Planning for these steps is essential.
- Material Qualification and Process Consistency:
- Výzva: Ensuring that the AM material and process consistently deliver the required mechanical properties and microstructure, meeting stringent aerospace standards (e.g., AMS specifications) from build to build and machine to machine. Variability in powder batches, machine calibration, or process parameters can affect outcomes.
- Strategie zmírnění dopadů:
- Robustní systém řízení kvality (QMS): Implementing and adhering to aerospace standards like AS9100.
- Strict Powder Control: Sourcing powder from qualified suppliers with strong batch traceability and quality control. Performing incoming powder inspection.
- Process Parameter Validation: Developing and locking down optimized process parameters based on rigorous testing (e.g., building test coupons with varying parameters and performing mechanical/metallurgical analysis).
- Machine Calibration and Monitoring: Regular calibration of lasers/beams, scanners, gas flow, thermal sensors. In-situ process monitoring (e.g., melt pool monitoring) can help detect anomalies during the build.
- Witness Coupon Testing: Including standardized test specimens (tensile bars, fatigue specimens, density cubes) on each build plate for destructive testing to verify mechanical properties and material integrity for that specific build.
- Comprehensive NDT: Utilizing methods like CT scanning to verify internal soundness and geometric conformance of final parts.
- Dokumentace: Maintaining thorough records of powder batches, process parameters, post-processing steps, and test results for full traceability.
Successfully navigating these challenges requires expertise in materials science, AM process physics, DfAM, and rigorous quality control methodologies. Partnering with an experienced metal AM service provider equipped with advanced technology and a strong aerospace quality mindset is crucial for producing reliable sensor housings.
Choosing Your Partner: How to Select the Right Metal 3D Printing Service Provider for Aerospace
The decision to utilize metal additive manufacturing for aerospace sensor housings brings immense potential, but realizing this potential hinges critically on selecting the right manufacturing partner. Unlike commodity components, aerospace parts demand the highest levels of precision, reliability, and traceability. The service provider you choose must possess not only the right equipment but also the specialized expertise, robust processes, and stringent quality certifications required to operate in this demanding sector. Choosing inadequately can lead to parts that fail to meet performance specifications, costly delays, or even safety risks. For procurement managers and engineers sourcing these critical components, a thorough evaluation process is essential.
Key Criteria for Evaluating Metal AM Service Providers for Aerospace:
- Aerospace Certifications (Non-Negotiable):
- AS9100: This is the internationally recognized Quality Management System (QMS) standard specific to the aerospace industry. Certification to AS9100 demonstrates the provider has implemented rigorous processes covering traceability, configuration management, risk management, process control, and continuous improvement tailored to aerospace requirements. This should be considered a mandatory requirement.
- ISO 9001: A foundational QMS standard, but insufficient on its own for aerospace work. AS9100 incorporates ISO 9001 and adds aerospace-specific requirements.
- NADCAP Accreditation: While AS9100 covers the overall system, NADCAP (National Aerospace and Defense Contractors Accreditation Program) provides specific accreditation for special processes like heat treatment, non-destructive testing (NDT), welding, and materials testing. If your provider performs these critical post-processing steps in-house, NADCAP accreditation adds significant assurance of process control and competence.
- Demonstrated Technical Expertise and Experience:
- Deep AM Process Knowledge: Proficiency in the specific AM technology being used (e.g., L-PBF, EBM), including parameter development, optimization for different materials (Ti64, 316L, Inconel, etc.), and understanding the physics behind the process.
- Materials Science Acumen: Expertise in metallurgy, particularly concerning the specified aerospace alloys. Understanding phase transformations during printing and heat treatment, microstructure-property relationships, and defect mitigation is crucial.
- DfAM Proficiency: The ability to actively collaborate with your design team, providing expert guidance on designing parts optimized for additive manufacturing, including support strategy, feature integration, and lightweighting.
- Post-Processing Mastery: In-depth knowledge and proven capability in necessary post-processing steps like stress relief, HIP, precision machining of AM parts, surface finishing techniques, and NDT interpretation.
- Aerospace Track Record: Proven experience in successfully delivering parts for aerospace or similarly demanding industries (e.g., medical implants, high-performance automotive). Ask for case studies or references relevant to sensor housings or similar components. Companies like Met3dp pride themselves on decades of collective expertise in metal additive manufacturing, providing a strong foundation for tackling complex aerospace projects.
- Advanced Equipment and Comprehensive Capabilities:
- Industrial-Grade Printers: Access to reliable, well-maintained, industrial-grade metal AM systems with appropriate build volumes for your sensor housings. Features like in-situ monitoring capabilities (melt pool monitoring, thermal imaging) can provide valuable process data. Met3dp, for example, emphasizes printers delivering industry-leading print volume, accuracy, and reliability.
- Řízení procesu: Evidence of robust machine calibration schedules, environmental controls (humidity, temperature), and controlled atmosphere management (oxygen levels in L-PBF, vacuum levels in EBM).
- Manipulace s práškem: Strict procedures for storing, handling, sieving, blending, and testing metal powders to prevent contamination and ensure consistency.
- In-House Post-Processing: While outsourcing is possible, providers with vertically integrated capabilities (in-house heat treatment furnaces, HIP units, multi-axis CNC machining centers, NDT labs) generally offer better process control, traceability, and potentially shorter lead times. Assess the quality and calibration of this equipment.
- Software Ecosystem: Utilization of advanced build preparation software, simulation tools (for predicting stress/distortion), and potentially CAM software optimized for machining AM parts.
- Material Sourcing, Quality Control, and Traceability:
- Qualified Powder Supply Chain: Using powders sourced from reputable suppliers who provide batch certifications and meet relevant aerospace material specifications (AMS). Ideally, the provider has strong relationships with powder producers or, like Met3dp, possesses advanced in-house powder manufacturing capabilities (e.g., VIGA, PREP) ensuring tight control over powder quality (sphericity, flowability, purity, particle size distribution).
- Rigorous Powder Management: Documented procedures for incoming powder inspection, storage in controlled environments, recycling/reconditioning protocols (if used, with strict quality checks), and batch traceability linking powder to specific builds and parts.
- Material Testing: Capability to perform or manage required material testing on witness coupons (tensile, hardness, density, microstructure analysis) to verify that each build meets specifications.
- Robust Quality Management System (QMS) Implementation:
- Dokumentace: Clear, accessible documentation for all procedures, work instructions, and specifications.
- Traceability: End-to-end traceability from raw powder batch to final shipped part, including all processing steps, parameters used, operator logs, inspection results, and certifications.
- Řízení procesu: Statistical Process Control (SPC) methods may be used to monitor key process parameters. Defined workflows for build setup, execution, and post-processing.
- Inspection and NDT: Calibrated inspection tools (CMMs, scanners), qualified NDT personnel (e.g., Level II/III certified inspectors), and documented inspection procedures.
- Non-Conformance Management: A clear process for identifying, documenting, segregating, and dispositioning non-conforming parts or process deviations.
- Průběžné zlepšování: Evidence of systems for analyzing quality data, implementing corrective actions, and driving ongoing process improvements.
- Capacity, Lead Time, and Communication:
- Produkční kapacita: Ensure the provider has sufficient machine and personnel capacity to meet your volume requirements within acceptable lead times, considering potential fluctuations in demand.
- Realistic Lead Time Quoting: Transparency in quoting lead times, accounting for build queues, actual print times, post-processing durations (HIP and machining can add significant time), and quality checks.
- Communication and Collaboration: Responsive customer service, clear communication channels, willingness to provide progress updates, and a collaborative approach to problem-solving. A true partner works with you to achieve the best outcome.
Selecting a metal AM service provider for aerospace sensor housings is a strategic decision. Look beyond just price and evaluate potential partners holistically against these criteria. A technically proficient, quality-focused, and certified provider like Met3dp can be an invaluable asset, transforming the potential of AM into reliable, high-performance aerospace components. Visiting facilities, conducting audits, and having detailed technical discussions are highly recommended steps in the selection process.
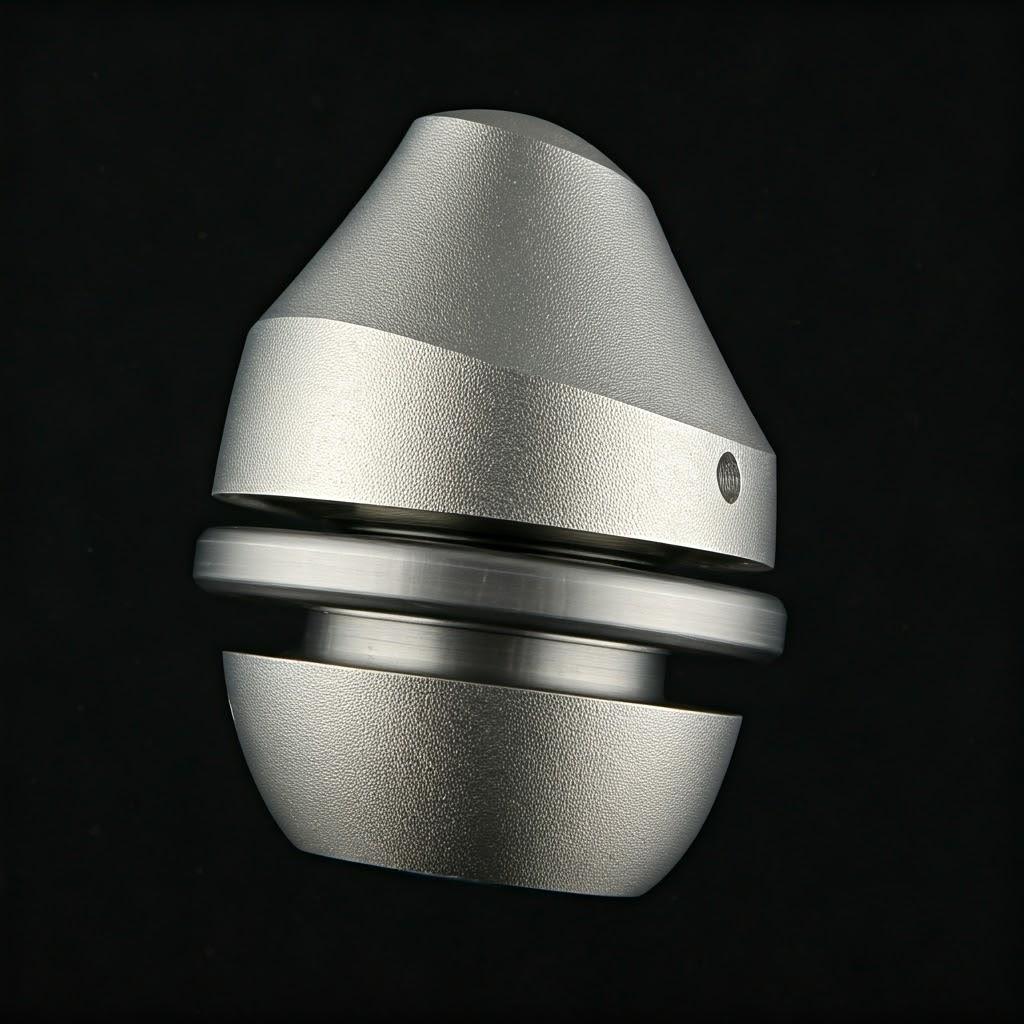
Understanding the Investment: Cost Factors and Lead Times for AM Sensor Housings
While metal additive manufacturing offers compelling technical advantages for aerospace sensor housings, understanding the associated costs and typical lead times is crucial for project planning, budgeting, and comparing AM against traditional manufacturing methods. The cost structure of AM differs significantly from machining or casting, and lead times can vary based on several factors.
Key Cost Drivers for Metal AM Sensor Housings:
The final price of a 3D printed metal sensor housing is influenced by a complex interplay of factors:
- Náklady na materiál:
- Powder Price: This is a significant factor. High-performance aerospace powders like Ti-6Al-4V or nickel superalloys are considerably more expensive than 316L stainless steel or aluminum alloys. Cost is typically measured per kilogram.
- Part Volume & Density: The actual volume of the printed part directly impacts the amount of powder consumed. Lightweight designs using topology optimization or lattices not only improve performance but also reduce material cost.
- Objem podpůrné struktury: Material used for support structures also adds to the cost. Optimized designs minimize support needs.
- Powder Waste/Recycling: Inefficient powder handling or recycling processes can increase effective material costs.
- Strojový čas:
- Doba výstavby: The time taken to print the part(s) on the AM machine. This is influenced by:
- Part Height (Z-axis): Build time is primarily driven by the number of layers, hence taller parts take longer.
- Part Volume/Area per Layer: The area that needs to be scanned by the laser/electron beam on each layer impacts layer time.
- Tloušťka vrstvy: Thinner layers improve resolution but significantly increase the number of layers and thus build time.
- Scan Strategy & Parameters: Optimized parameters aim for a balance between speed, quality, and stability.
- Machine Depreciation & Operating Costs: The high capital cost of industrial metal AM systems, along with maintenance, consumables (filters, inert gas), and energy consumption, are factored into hourly machine rates.
- Doba výstavby: The time taken to print the part(s) on the AM machine. This is influenced by:
- Náklady na pracovní sílu:
- Pre-Processing: CAD file preparation, build layout optimization (nesting multiple parts), support structure generation, and slicing. Requires skilled technicians/engineers.
- Machine Operation: Setting up the build, monitoring the process, and removing the build plate.
- Post-Processing (Often Significant): This can be a major labor component. Includes part removal from the plate, manual or automated support removal, surface finishing (blasting, tumbling, polishing), inspection, and potentially significant CNC machining time for critical features.
- Zajištění kvality: Labor associated with inspection, NDT, documentation, and certification.
- Post-Processing Costs (Beyond Labor):
- Tepelné zpracování: Costs associated with running furnace cycles for stress relief and/or solution annealing/aging (energy, inert gas/vacuum).
- Izostatické lisování za tepla (HIP): HIP is a specialized process often outsourced if not available in-house. It adds a significant cost component but is frequently essential for aerospace part integrity.
- CNC obrábění: Costs associated with machine time, tooling, and programming if extensive machining is required for tolerances or features.
- Povrchové úpravy: Costs for specific finishing processes like electropolishing or specialized coatings if required.
- NDT: Costs associated with running CT scans, DPI, UT, etc., and professional interpretation of results.
- Part Complexity & Geometry:
- While AM handles complexity well, extremely intricate designs might necessitate more extensive support structures, potentially increasing print time, material usage, and post-processing labor for support removal. Thin, delicate features might require slower printing parameters.
- Build Nesting & Quantity:
- Build Plate Density: The number of parts that can be printed simultaneously on a single build plate significantly impacts per-part cost. Setup time, build initiation/completion time, and some post-processing steps (like heat treatment) can be amortized across more parts. Higher quantities generally lead to lower per-part costs, although AM economics differ from the steep volume discounts seen in mass production methods like casting.
- Quality and Certification Requirements:
- The stringent testing, inspection (especially NDT), documentation, and certification requirements inherent in aerospace add overhead and direct costs compared to industrial or consumer parts. Witness coupon testing, detailed reports, and AS9100 compliance all contribute to the final cost.
Typical Lead Times:
Lead time is the duration from order placement to part delivery. For metal AM sensor housings, it comprises several stages:
- Order Processing & Pre-Processing: File check, quoting, build preparation, scheduling (Can range from 1-5 days).
- Tisk: Actual machine time. Can range from several hours for small, simple parts to multiple days for large, complex parts or dense build plates (Hours to Days).
- Cool Down & Part Removal: Allowing the build chamber to cool before safely removing the powder and build plate (Several hours to 1 day).
- Následné zpracování: This often constitutes the largest portion of the lead time.
- Stress Relief: ~1 day (including furnace cycle and cooling).
- Part/Support Removal & Basic Finishing: 1-3 days (depending on complexity).
- HIP: If required, can add 3-7 days (including shipping to/from HIP provider if outsourced, plus the cycle time).
- CNC Machining: Highly variable, from 1 day to over a week depending on the extent and complexity of machining required.
- NDT & Inspection: 1-3 days (depending on methods required and reporting).
- Doprava: Standard shipping times.
Overall Estimated Lead Times:
- Prototypy: For relatively simple housings requiring minimal post-processing beyond stress relief and support removal, lead times might be 1-3 týdny.
- Production Parts (Aerospace Certified): For parts requiring HIP, extensive machining, full NDT, and certification, lead times are typically much longer, potentially ranging from 4 to 8 weeks or more, depending heavily on the specific post-processing requirements and batch size.
AM vs. Traditional Methods Comparison (Simplified):
Faktor | Metal AM | CNC obrábění | Investiční odlévání |
---|---|---|---|
Náklady na nástroje | Žádný | Low (fixtures) | High (mold/die) |
Per-Part Cost | High (especially low volume) | Medium-High (depends on complexity/material) | Low (high volume), High (low volume) |
Složitost | High capability | Limited by tool access | High capability |
Lead Time (1st Part) | Fast (no tooling) | Moderate (programming/setup) | Slow (tooling required) |
Lead Time (Production) | Moderate-Slow (print + post-processing) | Moderate (machining time) | Fast (once tooling exists) |
Best Fit | Complex, low-medium volume, custom, rapid | Moderate complexity, various volumes | High volume, complex shapes |
Export do archů
Understanding these cost drivers and lead time components allows for more accurate budgeting and realistic scheduling when considering metal AM for aerospace sensor housings. Engaging potential suppliers early for quotes based on detailed part requirements is essential.
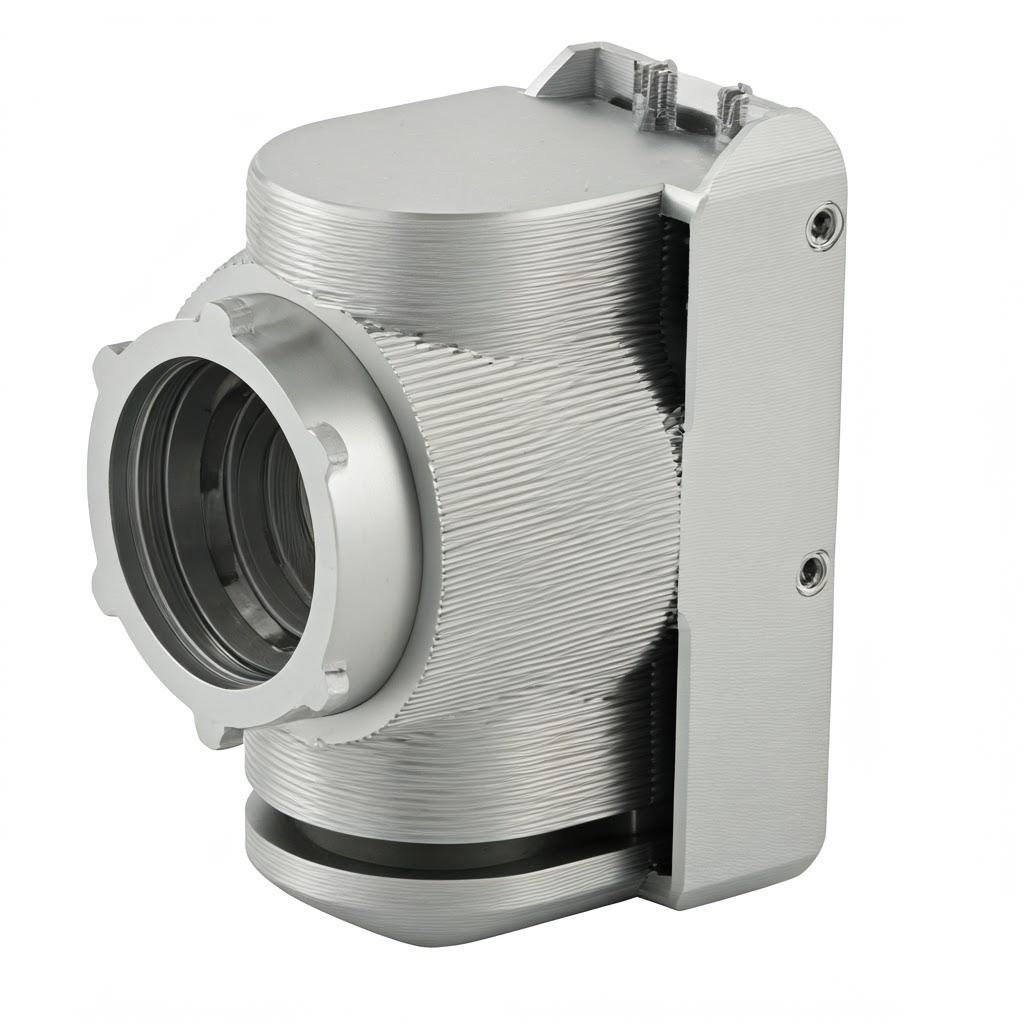
Frequently Asked Questions (FAQ) about Metal AM for Aerospace Sensor Housings
Here are answers to some common questions engineers and procurement managers have when considering metal 3D printing for aerospace sensor housings:
Q1: Is metal 3D printing suitable and approved for flight-critical sensor housings?
A: Yes, metal additive manufacturing is increasingly being used for flight-critical components, including sensor housings, in the aerospace industry. However, its suitability depends on rigorous adherence to established processes and standards. Key requirements include:
- Mature Process Control: Utilizing validated and locked-down printing parameters on qualified machines.
- Kvalifikace materiálu: Using aerospace-grade powders (e.g., Ti-6Al-4V, 316L, Inconel) that meet relevant AMS specifications, with full batch traceability.
- Mandatory Post-Processing: Implementing essential steps like stress relief and, crucially for fatigue-critical parts (especially Titanium), Hot Isostatic Pressing (HIP) to eliminate internal porosity and improve material properties.
- Thorough NDT: Employing non-destructive testing methods (like CT scanning) to verify internal integrity.
- Mechanical Testing: Verifying properties using witness coupons from each build.
- Certifikace: Manufacturing under a certified Quality Management System, specifically AS9100. When these conditions are met, AM parts can offer performance comparable or even superior (due to design optimization) to traditionally manufactured components for critical applications.
Q2: What are the main advantages of using metal AM for sensor housings compared to traditional CNC machining?
A: While CNC machining remains excellent for many parts, metal AM offers distinct advantages, particularly for complex sensor housings:
- Svoboda designu: AM excels at creating intricate internal features (e.g., conformal cooling channels, optimized sensor mounts, integrated cable routing) and complex external shapes that are difficult or impossible to machine.
- Odlehčení: Enables significant weight reduction through topology optimization and the use of internal lattice structures, crucial for aerospace efficiency, without compromising strength.
- Konsolidace částí: Allows multiple components of a sensor assembly (e.g., housing body, lid, bracket) to be combined into a single printed part, reducing assembly time, weight, fasteners, and potential failure points.
- Rychlé prototypování: Enables faster iteration cycles during design by producing functional metal prototypes quickly without needing dedicated tooling.
- Využití materiálu: Often generates less material waste (buy-to-fly ratio) compared to subtractive machining, especially for complex parts carved from large blocks.
Q3: How does the fatigue life of AM sensor housings compare to those made from wrought or cast materials?
A: The fatigue performance of metal AM parts is highly dependent on process quality and post-processing.
- Porosity is Key: As-printed parts often contain microporosity, which acts as initiation sites for fatigue cracks, leading to significantly lower fatigue life compared to wrought material.
- HIP is Crucial: Hot Isostatic Pressing (HIP) is extremely effective at closing internal pores. Properly HIPed AM components (especially Ti-6Al-4V) can achieve fatigue properties that are comparable to, and sometimes even exceed, those of cast materials, approaching the levels of wrought materials.
- Surface Finish Matters: The inherent roughness of as-printed surfaces can also negatively impact fatigue life by creating stress concentrations. Post-process machining or polishing of critical surfaces is often necessary to achieve optimal fatigue performance comparable to smooth, machined wrought components.
- Závěr: With appropriate process control, mandatory HIP treatment, and suitable surface finishing, metal AM sensor housings can meet demanding aerospace fatigue life requirements.
Q4: Can metal AM produce sensor housings that are hermetically sealed?
A: Metal AM processes can produce fully dense parts capable of forming a hermetic barrier. However, achieving a reliable hermetic seal typically depends on the quality of the sealing interface (e.g., O-ring groove, mating flange).
- As-Printed Limitations: The as-printed surface roughness (typically 5-20 µm Ra or more) is generally too rough to guarantee a reliable, long-term hermetic seal with standard elastomers (like O-rings) or metal gaskets.
- Post-Machining is Required: To ensure hermeticity, the sealing surfaces on the AM housing must almost always be post-machined to achieve the necessary smooth finish (e.g., <1.6 µm Ra, often smoother) and precise dimensional tolerances required for the specific seal type.
- Design for Sealing: DfAM principles should incorporate allowances for machining these critical sealing features.
- Závěr: Yes, hermetically sealed housings can be achieved using metal AM, but it requires a hybrid approach combining AM for the complex overall shape with precision machining for the sealing interfaces.
Q5: What information does a service provider need to provide an accurate quote for a 3D printed aerospace sensor housing?
A: To receive a comprehensive and accurate quote from a metal AM service provider like Met3dp, you should provide as much detail as possible, typically including:
- 3D model CAD: A high-quality model in a standard format (e.g., STEP, Parasolid).
- Specifikace materiálu: Clearly defined material (e.g., Ti-6Al-4V, 316L) and the relevant aerospace standard (e.g., AMS 4928, AMS 5643).
- Technical Drawing (Highly Recommended): A 2D drawing defining critical dimensions, tolerances (using GD&T), required surface finishes for specific features (especially sealing or mating surfaces), and any threads or special features.
- Požadavky na následné zpracování: Specify required heat treatments (stress relief, HIP, annealing/aging cycles), surface finishes (Ra values for critical areas), and any required coatings.
- Testing and Certification: Clearly state required NDT methods (CT, DPI, UT), any destructive testing needs (witness coupons), and required certifications (e.g., AS9100 compliance, Certificate of Conformance, material certs).
- Množství: Number of parts required (for prototypes and/or production runs).
- Požadovaná doba dodání: Your required delivery schedule.
- Application Context (Optional but helpful): Briefly describing the sensor type and operating environment can sometimes help the provider offer DfAM suggestions.
Providing this level of detail enables the service provider to accurately assess the manufacturing complexity, required process steps, quality assurance effort, and ultimately provide a realistic quote and lead time.
Conclusion: Elevating Aerospace Sensing Capabilities with Metal Additive Manufacturing
The aerospace industry operates at the confluence of extreme performance requirements and relentless innovation. In this environment, the ability to protect sensitive instruments while optimizing for weight, complexity, and reliability is paramount. Metal additive manufacturing has decisively moved beyond being a mere prototyping tool to become a powerful manufacturing solution capable of producing flight-ready components, including sophisticated aerospace sensor housings.
As we’ve explored, leveraging metal AM with materials like robust Nerezová ocel 316L and the high-performance Ti-6Al-4V Titanium alloy allows engineers to break free from the constraints of traditional manufacturing. The unparalleled svoboda designu enables the creation of housings with integrated thermal management features, complex internal geometries for optimal sensor placement, and topology-optimized structures that significantly snížit hmotnost – a critical factor in enhancing aircraft fuel efficiency and payload capacity. Furthermore, the ability to consolidate multiple parts into a single, monolithic component simplifies assembly, reduces potential failure points, and streamlines logistics.
However, harnessing these benefits requires more than just access to a 3D printer. A successful implementation relies on a holistic approach encompassing:
- Design for Additive Manufacturing (DfAM): Rethinking design strategies to maximize AM’s strengths and mitigate its constraints.
- Rigorous Process Control: Utilizing high-quality powders, optimized printing parameters, and meticulous machine operation.
- Essential Post-Processing: Implementing critical steps like stress relief, Hot Isostatic Pressing (HIP) for material integrity, and precision machining for functional interfaces.
- Stringent Quality Assurance: Adhering to aerospace standards like AS9100 and employing thorough NDT methods.
Perhaps most importantly, success hinges on choosing the right manufacturing partner. A provider with proven aerospace expertise, robust quality systems, advanced equipment, deep material knowledge, and a collaborative approach is essential for transforming innovative designs into reliable, certified hardware.
Metal additive manufacturing is not just changing how sensor housings are made; it’s enabling the development of next-generation sensing capabilities. By allowing sensors to be housed in lighter, more complex, and better-integrated enclosures, AM contributes directly to the advancement of flight control, structural health monitoring, propulsion efficiency, and overall aerospace safety and performance. As the technology continues to mature, its role in producing critical aerospace components will only grow, further accelerating the digital transformation of manufacturing.
Companies like Met3dp, with their focus on providing comprehensive solutions spanning advanced SEBM and L-PBF printers, high-performance metal powders manufactured via cutting-edge VIGA and PREP technologies, and deep application development expertise, are enabling organizations worldwide to embrace the power of metal AM. Contacting such knowledgeable partners is the first step towards exploring how additive manufacturing can elevate your aerospace sensing applications and broader manufacturing goals.
Sdílet na
MET3DP Technology Co., LTD je předním poskytovatelem řešení aditivní výroby se sídlem v Qingdao v Číně. Naše společnost se specializuje na zařízení pro 3D tisk a vysoce výkonné kovové prášky pro průmyslové aplikace.
Dotaz k získání nejlepší ceny a přizpůsobeného řešení pro vaše podnikání!
Související články
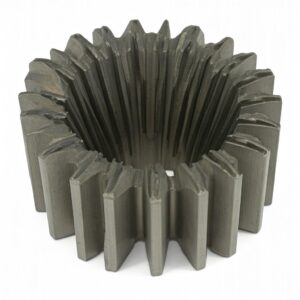
Vysoce výkonné segmenty lopatek trysek: Revoluce v účinnosti turbín díky 3D tisku z kovu
Přečtěte si více "O Met3DP
Nedávná aktualizace
Náš produkt
KONTAKTUJTE NÁS
Nějaké otázky? Pošlete nám zprávu hned teď! Po obdržení vaší zprávy obsloužíme vaši žádost s celým týmem.
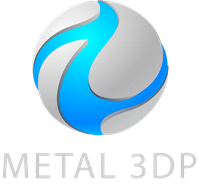
Kovové prášky pro 3D tisk a aditivní výrobu
SPOLEČNOST
PRODUKT
kontaktní informace
- Město Qingdao, Shandong, Čína
- [email protected]
- [email protected]
- +86 19116340731