Vlastní 3D tištěné tepelné štíty pro vozidla: Pokročilý tepelný management pomocí technologie AM s kovem
Obsah
Úvod: Revoluce v tepelném managementu automobilů s kovovými tepelnými štíty tištěnými na 3D tiskárně
Neustálá snaha o výkon, efektivitu a bezpečnost v automobilovém průmyslu neustále posouvá hranice inženýrství a výroby. Jedním z kritických, ale často přehlížených aspektů konstrukce vozidel je tepelný management. Účinná regulace tepla generovaného motory, výfukovými systémy, turbodmychadly, bateriemi a dalšími součástmi je nejdůležitější nejen pro ochranu citlivých součástí a zajištění pohodlí cestujících, ale také pro optimalizaci výkonu a životnosti vozidla. Tepelné štíty automobilů - primární komponenty, jejichž úkolem je tato tepelná regulace - se tradičně vyrábějí konvenčními metodami, jako je lisování a tváření plechů. Tyto techniky jsou sice efektivní pro hromadnou výrobu jednoduchých geometrií, ale často znamenají omezení pro složitost konstrukce, optimalizaci hmotnosti a rychlost vývoje, zejména pro specifické aplikace, výkonná vozidla nebo rychle se rozvíjející odvětví elektromobilů.
Vstupte kov 3D tisk, známé také jako aditivní výroba (AM). Tato transformační technologie rychle mění způsob navrhování a výroby složitých součástí v různých průmyslových odvětvích a automobilový průmysl není výjimkou. Konkrétně pro tepelné štíty pro automobilový průmysl, nabízí technologie metal AM změnu paradigmatu a umožňuje vytvářet vysoce přizpůsobená, komplexní a lehká řešení, která byla dříve neproveditelná nebo neúměrně drahá. Díky vytváření dílů vrstvu po vrstvě přímo z digitálních návrhů pomocí vysoce výkonných kovových prášků mohou nyní inženýři navrhovat tepelné štíty optimalizované přesně pro jejich specifické tepelné prostředí, integrovat složité prvky, konformní tvary a optimalizované kanály pro proudění vzduchu. Tato schopnost je klíčová pro řízení tepla v těsně uzavřených motorových prostorech, ochranu pokročilých bateriových systémů v elektromobilech a zvýšení výkonu přeplňovaných motorů.
Význam tohoto technologického pokroku nelze přeceňovat. S tím, jak se vozidla stávají sofistikovanějšími, obsahují hustší elektroniku, výkonné hybridní systémy a vysoce výkonná hnací ústrojí, nároky na systémy tepelného managementu se zvyšují. Tradiční tepelné štíty, které jsou často navrženy jako kompromis mezi cenou, vyrobitelností a výkonem, mají problém tyto rostoucí požadavky splnit. Aditivní výroba kovů poskytuje konstrukční svobodu, která je nezbytná k vytvoření na míru šitých řešení tepelného managementu přizpůsobené jedinečným výzvám moderních architektur vozidel. Od rychlé výroby prototypů během vývojových cyklů až po výrobu malých až středních sérií specializovaných výrobků zakázkové součásti vozidel, kovové AM nabízí nebývalou agilitu a výkonnostní potenciál.
Tento blogový příspěvek se zabývá světem 3D tištěné tepelné štíty pro vozidla. Prozkoumáme jejich použití, přesvědčivé výhody používání 3D tisk z kovu oproti tradičním metodám, doporučené materiály, jako je hliníková slitina AlSi10Mg a niklová superslitina IN625, zásadní konstrukční úvahy, dosažitelné ukazatele kvality, potřeby následného zpracování, potenciální problémy a faktory ovlivňující náklady a dobu realizace. Dále poradíme inženýrům a manažerům nákupu při výběru správné technologie aditivní výroba v automobilovém průmyslu partner.
V čele tohoto úsilí o pokročilá výrobní řešení stojí společnost Met3dp. Společnost Met3dp Technology Co., LTD se sídlem v čínském městě Qingdao se specializuje na nejmodernější technologie 3D tisk z kovu zařízení a výrobu vysoce výkonných kovových prášků, které jsou klíčové pro průmyslové aplikace. Naše odborné znalosti v oblasti práškové metalurgie, využívající pokročilé technologie plynové atomizace a plazmového rotačního elektrodového procesu (PREP), zajišťují nejvyšší kvalitu sférických kovových prášků - základ pro spolehlivé a vysoce výkonné 3D tištěné komponenty. Díky portfoliu zahrnujícímu inovativní slitiny a desítky let společných zkušeností poskytuje společnost Met3dp komplexní řešení, která umožňují průmyslovým odvětvím, jako je letecký, lékařský a zejména automobilový průmysl, plně využít potenciál aditivní výroby pro náročné aplikace, jako jsou například tepelné štíty na zakázku. Spolupracujeme s organizacemi po celém světě, abychom urychlili jejich transformaci digitální výroby a nabídli jim špičkový objem tisku, přesnost a spolehlivost.
Podívejte se s námi na to, jak technologie AM pro kovy nejen zlepšuje tepelné štíty automobilů, ale také mění přístup k tepelnému managementu ve vozidlech, čímž otevírá cestu k lehčím, efektivnějším a výkonnějším automobilům. Ať už jste automobilový inženýr, který hledá inovativní řešení, dodavatel Tier 1, který hledá pokročilé výrobní možnosti, nebo manažer nákupu, který hledá zdroje pro zakázkové automobilové komponenty, pochopení potenciálu tepelných štítů vytištěných na 3D tiskárně je v dnešním konkurenčním prostředí zásadní.
K čemu se používají tepelné štíty automobilů? Klíčové aplikace a odvětví
Tepelné štíty automobilů jsou základní pasivní tepelně izolační komponenty určené k ochraně součástí vozidla, cestujících a okolního prostředí před nadměrným teplem, které vzniká především v hnacím ústrojí a výfukovém systému. Jejich základní funkce tepelného štítu působí jako bariéra, která odráží sálavé teplo od citlivých oblastí a snižuje konvekční přenos tepla. Bez účinných tepelných štítů může dojít k řadě problémů, včetně degradace součástí, snížení výkonu, zvýšení emisí, potenciálního nebezpečí požáru a zhoršení komfortu cestujících v důsledku sálání tepla do kabiny. Strategické umístění a konstrukce těchto štítů jsou rozhodující pro celkovou spolehlivost a bezpečnost každého vozidla.
Použití tepelných štítů ve vozidle je rozmanité a řeší specifické tepelné problémy na různých místech:
- Tepelné štíty výfukového systému: Jedná se o pravděpodobně nejběžnější aplikaci. Výfukové potrubí, katalyzátory, tlumiče výfuku a výfukové trubky mohou dosahovat extrémně vysokých teplot (často přesahujících 600 °C nebo 1100 °C, zejména v blízkosti motoru nebo katalyzátoru). Tepelné štíty jsou zde klíčové pro:
- Chraňte součásti podvozku (palivové a brzdové vedení, kabelové svazky, palivovou nádrž).
- Zabraňte poškození nátěrů podvozku nebo konstrukčních prvků teplem.
- Snížení vyzařování tepla směrem k podlaze kabiny pro cestující.
- Chraňte okolní součásti během doby stání (např. zabraňte poškození asfaltu nebo vysychající vegetace).
- Klíčová slova: Tepelný štít výfuku, tepelný štít katalyzátoru, tepelný štít výfuku, tepelný štít podvozku.
- Stínění motorového prostoru: Motorový prostor je hustě zaplněné prostředí s mnoha zdroji tepla (blok motoru, turbodmychadlo, výfukové potrubí) a komponenty citlivými na teplo (elektronika, senzory, hadice, plastové díly). Tepelné štíty slouží k:
- Chrání specifické komponenty, jako je startér, alternátor, řídicí jednotka motoru a různé senzory, před přímým tepelným zářením.
- Chraňte plastové součásti (např. kryty motoru, sací potrubí) před deformací nebo roztavením.
- Řízení teplot pod kapotou zajišťuje optimální výkon motoru a zabraňuje tvorbě par v palivovém potrubí.
- Chraňte lak kapoty před nadměrným teplem.
- Klíčová slova: Stínění motorového prostoru, tepelný štít turbodmychadla, tepelný štít sběrného potrubí, izolace požární stěny.
- Tepelné štíty turbodmychadla: Turbodmychadla pracují při velmi vysokých teplotách, protože stlačují nasávaný vzduch a jsou poháněna horkými výfukovými plyny. Specifické tepelné štíty turbodmychadla (často nazývané “turbo deky” pokud jsou pružné, ale běžné jsou i pevné štíty) jsou nezbytné pro:
- Chraňte přilehlé součásti (kabeláž, hadice, pohony) před extrémním sálavým teplem.
- Udržují teplo uvnitř skříně turbíny, čímž zlepšují účinnost a odezvu turba (zkracují dobu roztáčení).
- Nižší celkové teploty pod kapotou.
- Klíčová slova: Tepelný štít turba, výkonné díly turba, tepelná izolace automobilů.
- Stínění baterií elektromobilů a hybridních vozidel: Elektromobily sice nemají horké výfukové systémy, ale jejich vysokonapěťové akumulátory jsou citlivé na extrémní teploty, a to jak na horko, tak na chlad. Tepelný management má zásadní význam pro výkon, životnost a bezpečnost baterií. Tepelné štíty mohou hrát roli při:
- Ochrana akumulátoru před vnějšími zdroji tepla (např. okolním teplem, teplem z blízkých motorů nebo výkonové elektroniky).
- Funguje jako součást rozsáhlejšího systému tepelného managementu, který udržuje optimální provozní teplotu baterie.
- Poskytuje ochranu proti tepelnému vyčerpání tím, že působí jako bariéra v případě selhání článku.
- Klíčová slova: Tepelný management baterií elektromobilů, tepelný štít baterií, součásti elektromobilů.
- Ochrana palivové nádrže: Mezi výfukový systém a palivovou nádrž se často umisťují tepelné štíty, aby se zabránilo přehřátí paliva, které by mohlo vést k nadměrnému odpařování, problémům s tlakem par nebo v extrémních případech k ohrožení bezpečnosti.
- Klíčová slova: Tepelný štít palivové nádrže, bezpečnostní součásti automobilů.
- Další aplikace: V závislosti na konstrukci vozidla se tepelné štíty mohou používat také v blízkosti brzd, převodovek, diferenciálů nebo specifických elektronických modulů vyžadujících tepelnou ochranu.
Odvětví, která z toho mají prospěch:
Potřeba účinného tepelného stínění se týká celého automobilového ekosystému:
- Automobiloví výrobci OEM (Original Equipment Manufacturers): Primárními spotřebiteli jsou výrobci automobilů, kteří tepelné štíty integrují do všech vyráběných vozidel, od ekonomických vozů až po luxusní sedany a těžké nákladní vozy. Vyžadují spolehlivá a cenově výhodná řešení, která splňují přísné normy pro výkon a životnost. Získávání Automobilové díly OEM jako jsou tepelné štíty, často zahrnuje spolupráci se specializovanými Dodavatelská řešení Tier 1.
- Výkonný trh s náhradními díly: Společnosti poskytující modernizace pro výkonná vozidla často vyvíjejí tepelné štíty na míru určené pro vyšší tepelné zatížení způsobené upravenými motory, většími turbodmychadly nebo výfukovými systémy s vysokým průtokem. Zde je často prioritou úspora výkonu a hmotnosti, což činí atraktivními pokročilé materiály a výrobní metody, jako je 3D tisk.
- Motorsport: V závodních aplikacích je tepelný management extrémně náročný. Týmy vyžadují vysoce optimalizované, lehké a extrémně odolné tepelné štíty, které jsou schopny odolávat intenzivním tepelným cyklům a vibracím. Přizpůsobení a rychlá iterace jsou klíčové, a proto je pro ně ideální technologie AM.
- Výrobci elektrických vozidel: Jak již bylo zmíněno, elektromobily mají jedinečné potřeby v oblasti tepelného managementu, zejména pokud jde o akumulátory a výkonovou elektroniku. V tomto rychle se rozvíjejícím odvětví jsou stále důležitější tepelné štíty navržené na míru.
- Speciální vozidla: Výrobci vozidel, jako jsou obytná vozidla, autobusy, zemědělské stroje a stavební stroje, rovněž používají tepelné štíty přizpůsobené jejich specifickému provoznímu prostředí a zdrojům tepla.
Pochopení těchto rozmanitých aplikací zdůrazňuje kritickou roli tepelných štítů a podtrhuje potenciál pokročilých výrobních technik, jako je 3D tisk kovů, poskytovat lepší řešení ve srovnání s tradičními metodami, zejména tam, kde je vyžadována složitost, přizpůsobení nebo optimalizace výkonu. Schopnost rychle navrhovat a vyrábět štíty specifické pro danou aplikaci nabízí významné výhody ve všech těchto segmentech automobilového průmyslu. Nalezení spolehlivého dodavatel tepelných štítů pro automobilový průmysl schopné využívat tyto pokročilé metody, je stále důležitější.
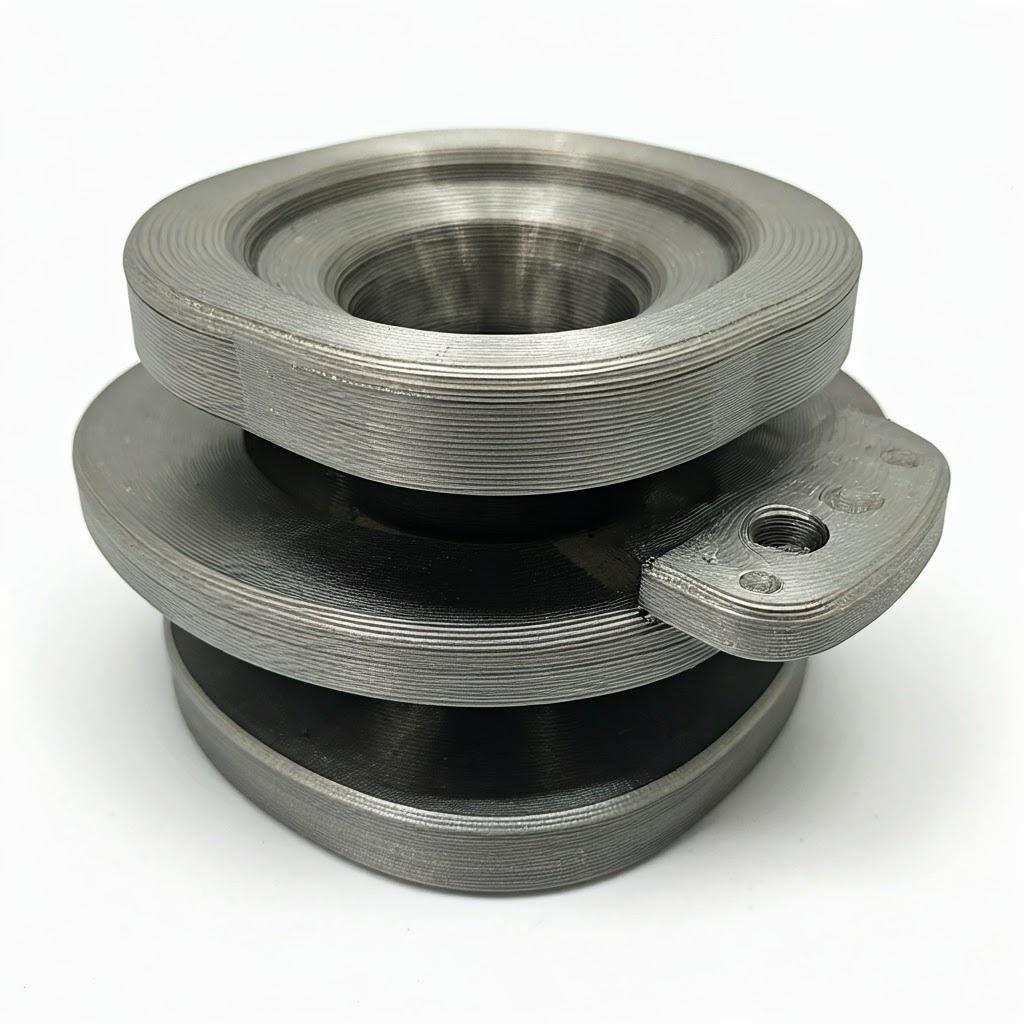
Proč používat 3D tisk z kovu pro tepelné štíty automobilů? Uvolnění svobody designu a výkonu
Zatímco tradiční výrobní metody, jako je lisování a hydroformování, dobře sloužily automobilovému průmyslu k výrobě velkých objemů relativně jednoduchých tepelných štítů, narážejí na omezení, když čelí rostoucí složitosti, požadavkům na výkon a přizpůsobení moderních vozidel. 3D tisk z kovu, zejména technologie PBF (Powder Bed Fusion), jako je selektivní laserové tavení (SLM) nebo přímé laserové spékání kovů (DMLS), nabízí přesvědčivou alternativu, která přináší významné výhody pro konstrukci a výrobu tepelných štítů. Na adrese výhody aditivní výroby v této souvislosti přímo řeší nedostatky konvenčních postupů.
Zde je podrobné srovnání a vysvětlení, proč aM vs. lisování kovů nebo tvarování je výhodné pro tepelné štíty:
- Bezkonkurenční volnost designu & Komplexnost:
- Tradiční: Lisování je omezeno omezeními nástrojů, úhly tahu a tvarovatelností plechu. Vytváření složitých křivek, integrovaných prvků nebo dutých struktur je obtížné, nákladné nebo nemožné. U složitých tvarů je často nutná montáž více vyražených kusů.
- Metal AM: Aditivní výroba vytváří díly vrstvu po vrstvě z digitálního souboru, což umožňuje prakticky neomezenou geometrickou složitost. To umožňuje:
- Tepelné štíty s komplexní geometrií: Štíty se mohou dokonale přizpůsobit okolním součástem, čímž se maximalizuje ochrana v těsných prostorech.
- Integrované funkce: Montážní body, držáky, upevňovací prvky, výztužná žebra a dokonce i kanály pro proudění vzduchu lze navrhnout přímo do tepelného štítu, čímž se sníží počet dílů, doba montáže a potenciální místa poruchy.
- Vnitřní struktury: Pro snížení hmotnosti při zachování tuhosti a tepelného výkonu lze použít duté profily nebo vnitřní mřížové/gyroidní struktury.
- Optimalizace topologie: Pomocí softwaru lze optimalizovat tvar štítu a odstranit materiál tam, kde není potřeba pro strukturální integritu nebo tepelný výkon, což vede k výrazné úspoře hmotnosti.
- Odlehčení:
- Tradiční: Plechové štíty mají často stejnou tloušťku a dosažení výrazného snížení hmotnosti vyžaduje použití tenčích rozměrů (což snižuje tuhost/odolnost) nebo přechod na dražší, hůře tvarovatelné materiály.
- Metal AM: Schopnost vytvářet optimalizované geometrie a vnitřní mřížkové struktury umožňuje drastické snížení hmotnosti bez ztráty výkonu. Použití lehkých kovových prášků, jako je AlSi10Mg, tuto výhodu dále zvyšuje. Lehké automobilové komponenty přímo přispívají ke zlepšení palivové účinnosti, lepší ovladatelnosti a zvýšení nosnosti.
- Rychlá tvorba prototypů a rychlost vývoje:
- Tradiční: Výroba raznic je časově i finančně náročná. Iterace návrhu vyžadují nákladné úpravy nástrojů nebo zcela nové nástroje, což výrazně zpomaluje vývojový cyklus.
- Metal AM: Prototypy lze vytisknout přímo z dat CAD během několika dnů, někdy i hodin, bez potřeby nástrojů. To umožňuje inženýrům rychle testovat různé návrhy, ověřovat výkon (tepelný a konstrukční) a provádět rychlé iterace. Tato schopnost pro tepelné štíty pro rychlé prototypování výrazně urychluje vývoj produktů a dobu jejich uvedení na trh.
- Přizpůsobení a výroba na vyžádání:
- Tradiční: Lisování je zaměřeno na hromadnou výrobu. Výroba malých sérií nebo zakázkových variant je ekonomicky nevýhodná kvůli vysokým nákladům na nástroje.
- Metal AM: Ideální pro malosériovou až středně velkou výrobu a přizpůsobení. Každý díl může být jedinečný bez nutnosti změny nástrojů. To umožňuje výroba tepelných štítů na vyžádání pro specifická vozidla, díly pro trh s náhradními díly, aplikace pro motorsport nebo náhradní díly pro starší modely, u nichž již neexistuje původní nářadí. Tato flexibilita dokonale odpovídá rostoucímu trendu personalizace vozidel a specializovaných modelů.
- Možnosti materiálu a výkon:
- Tradiční: Omezeno na plechy, které jsou snadno tvářitelné (různé oceli, slitiny hliníku). Použití výkonnějších slitin může být náročné a nákladné.
- Metal AM: Snadno lze zpracovávat širší škálu vysoce výkonných slitin, včetně niklových superslitin, jako je IN625 (ideální pro extrémní teplo), nebo specializovaných hliníkových slitin, jako je AlSi10Mg. Tyto materiály nabízejí vyšší tepelnou odolnost, odolnost proti korozi nebo poměr pevnosti a hmotnosti ve srovnání s běžnými možnostmi. Met3dp, jako specializovaný dodavatel kovového prášku, poskytuje vysoce kvalitní prášky AlSi10Mg a IN625 optimalizované pro procesy AM, které zajišťují spolehlivé vlastnosti materiálu.
- Konsolidace částí:
- Tradiční: Složité sestavy tepelných štítů se často skládají z více lisovaných dílů, které jsou k sobě přivařeny nebo připevněny.
- Metal AM: Svoboda návrhu umožňuje sloučit více součástí sestavy do jediného komplexního 3D tištěného dílu. To snižuje čas montáže, náklady na pracovní sílu, správu zásob a potenciální cesty úniku nebo místa poruch spojů.
Souhrnná tabulka: Kovové AM vs. tradiční výroba tepelných štítů
Vlastnosti | 3D tisk kovů (např. SLM/DMLS) | Tradiční lisování/formování | Výhody technologie Metal AM |
---|---|---|---|
Složitost návrhu | Prakticky neomezený počet; složité křivky, vnitřní prvky, mřížky | Omezeno nástroji, tvarovatelností materiálu; jednoduché tvary | Umožňuje vysoce optimalizované, konformní, integrované návrhy |
Odlehčení | Významný potenciál prostřednictvím optimalizace topologie, mřížové struktury | Omezené; často vyžaduje tenčí materiál (snižuje tuhost) | Možnost podstatného snížení hmotnosti při zachování nebo zvýšení výkonu |
Rychlost prototypování | Rychle (hodiny/dny); přímo z CAD, bez nástrojů | Pomalé (týdny/měsíce); vyžaduje vytvoření/modifikaci nástrojů | Výrazně zkracuje dobu vývoje (zkrácení dodací lhůty v automobilovém průmyslu) |
Náklady na nástroje | Žádný | Vysoká (formy a formy) | Úsporné pro prototypy, malosériové a zakázkové díly |
Přizpůsobení | Vysoká; snadná výroba jedinečných dílů nebo malých sérií | Nízká; ekonomicky životaschopná pouze pro hromadnou výrobu | Ideální pro specifické aplikace, trh s náhradními díly a motoristický sport, výroba na vyžádání |
Konsolidace částí | Vysoký potenciál; více částí integrovaných do jedné | Nízká; často vyžaduje montáž více komponentů | Snižuje náklady na montáž, její složitost a potenciální místa poruch |
Možnosti materiálu | Širší sortiment, včetně vysoce výkonných slitin (např. IN625) | Především tvářitelné plechy (ocel, hliník) | Přístup k materiálům s vynikajícími tepelně-mechanickými vlastnostmi pro náročné aplikace |
Vhodnost objemu | Prototypy, nízký až střední objem | Vysoký objem | Nákladově efektivní přemostění před sériovou výrobou nebo pro specializované díly |
Export do archů
Ačkoli v současné době může mít metoda AM pro velmi vysoké objemy vyšší náklady na jeden díl ve srovnání s lisováním, její výhody v oblasti flexibility konstrukce, zvýšení výkonu, snížení hmotnosti a rychlosti uvedení na trh nabízejí přesvědčivé hodnoty, zejména pro složité tepelné štíty, výkonné aplikace, elektromobily a situace vyžadující rychlý vývoj nebo přizpůsobení. Spolupráce se zkušenými služby kovového 3D tisku jako je Met3dp, který má hluboké odborné znalosti v oblasti tiskových metod a materiálů, umožňuje automobilovým společnostem plně využít těchto výhod pro jejich výzvy v oblasti tepelného managementu nové generace.
Doporučené materiály pro 3D tištěné tepelné štíty: AlSi10Mg vs. IN625
Výběr správného materiálu je zásadní pro výkon a životnost jakékoli součásti a tepelné štíty pro automobily vytištěné na 3D tiskárně nejsou výjimkou. Provozní prostředí - konkrétně špičkové a trvalé teploty, potenciál koroze, konstrukční zatížení a hmotnostní cíle - diktuje nejvhodnější kovový prášek. U mnoha aplikací tepelných štítů pro automobilový průmysl vyráběných prostřednictvím aditivní výroby kovů vynikají díky svým vlastnostem a zpracovatelnosti dva materiály: AlSi10Mg (slitina hliníku) a IN625 (superslitina niklu a chromu). Klíčem k výběru optimálního řešení je pochopení jejich vlastností.
Společnost Met3dp využívá své pokročilé možnosti výroby prášků, včetně plynové atomizace a technologie PREP, a vyrábí vysoce kvalitní sférické prášky kovový prášek pro 3D tisk v automobilovém průmyslu aplikací, čímž je zajištěna konzistentní kvalita a výkon. Jako spolehlivý Dodavatel prášku AlSi10Mg a Rozdělovač prášku IN625, Met3dp nabízí materiály ideální pro náročné úlohy tepelného managementu.
Porovnejme tyto dvě základní slitiny pro aplikace tepelných štítů:
1. Hliníková slitina – AlSi10Mg:
AlSi10Mg je široce používaná hliníková slitina v aditivní výrobě, která je známá pro svůj dobrý poměr pevnosti a hmotnosti, vynikající tepelnou vodivost, dobrou odolnost proti korozi a relativně snadnou zpracovatelnost pomocí metod laserové fúze v práškovém loži (L-PBF), jako je SLM/DMLS.
- Klíčové vlastnosti a výhody tepelných štítů:
- Nízká hustota (lehká): ~2,67 g/cm³. To je hlavní výhoda pro aplikace v automobilovém průmyslu, kde je snížení hmotnosti rozhodující pro úsporu paliva a výkon. Potisk lehkých kovů je klíčovou hnací silou pro přijetí AlSi10Mg.
- Vynikající tepelná vodivost: ~120-140 W/(m-K). Vysoká tepelná vodivost umožňuje stínění účinně odvádět teplo pryč od chráněných součástí nebo ho rozložit na větší plochu, což může být v určitých konstrukcích výhodné, ačkoli pro čistou izolaci může být žádoucí nižší vodivost (dosažitelná konstrukcí/povlaky).
- Dobrá pevnost & amp; Mechanické vlastnosti: Nabízí slušnou pevnost v tahu a tvrdost po vhodném tepelném zpracování, která je dostatečná pro mnoho konstrukčních požadavků tepelného štítu.
- Dobrá odolnost proti korozi: Obecně funguje dobře v typických automobilových prostředích.
- Zpracovatelnost: Dobře srozumitelný a široce dostupný materiál pro procesy L-PBF, umožňující jemné rysy a dobrou povrchovou úpravu.
- Efektivita nákladů: Obecně je cenově dostupnější než niklové superslitiny, jako je IN625, a to jak z hlediska ceny surového prášku, tak z hlediska doby tisku (díky nižšímu bodu tání).
- Omezení:
- Mírná teplotní odolnost: To je hlavní nevýhoda. AlSi10Mg výrazně ztrácí pevnost při teplotách nad přibližně 200-250 °C (392-482 °F). Je sice vhodný pro tepelné štíty na chladnějších místech (např. dále ve výfuku, ochrana elektroniky před mírným teplem, některé aplikace pod karoserií, některé scénáře stínění baterií elektromobilů), ale obecně je to ne vhodné pro aplikace v těsné blízkosti výfukového potrubí, katalyzátoru nebo skříně turbíny turbodmychadla, kde teploty běžně přesahují 500-600 °C (932-1112 °F) nebo vyšší.
- Typické aplikace tepelného štítu: Stínění podvozku od primárního tepla výfukových plynů, stínění elektroniky nebo senzorů, které jsou vystaveny mírnému tepelnému zatížení, některé aplikace baterií pro elektromobily, držáky nebo montážní komponenty spojené se systémy tepelného řízení.
2. Nikl-chromová superslitina – IN625 (Inconel® 625):
IN625 je superslitina na bázi niklu, která je známá svou výjimečnou pevností při vysokých teplotách, vynikající odolností proti korozi a oxidaci a mimořádnou únavovou pevností. Je to materiál pro náročné aplikace v leteckém a automobilovém průmyslu, kde se vyskytuje extrémní teplo a drsné prostředí.
- Klíčové vlastnosti a výhody tepelných štítů:
- Vynikající odolnost při vysokých teplotách: Zachovává si značnou pevnost a strukturální integritu při velmi vysokých teplotách, až do ~800-900 °C (1472-1652 °F) nebo i vyšších při krátkých exkurzích v závislosti na zatížení. Díky tomu je ideální pro štíty v blízkosti nejžhavějších částí motoru a výfuku. Tepelná odolnost IN625 je jeho charakteristickým rysem.
- Vynikající odolnost proti korozi a oxidaci: Vysoce odolné vůči výfukovým plynům, silniční soli a dalším korozivním prvkům, které se vyskytují v automobilovém prostředí, což zajišťuje dlouhou životnost i v náročných podmínkách.
- Vysoká pevnost a odolnost: Má vynikající pevnost v tahu, únavě a tečení v širokém rozsahu teplot.
- Svařitelnost / tisknutelnost: Ačkoli je tisk IN625 náročnější než tisk AlSi10Mg (vyžaduje pečlivou kontrolu parametrů kvůli zbytkovým napětím), je snadno zpracovatelný pomocí L-PBF a tavení elektronovým svazkem (EBM - oblast schopností Met3dp, ačkoli L-PBF je běžnější pro tepelné štíty), což umožňuje získat husté a vysoce kvalitní díly.
- Omezení:
- Vyšší hustota: ~8,44 g/cm³. Výrazně hustší a těžší než hliníkové slitiny. I když optimalizace konstrukce (tenké stěny, mřížky) může tuto skutečnost zmírnit, štít IN625 bude obvykle těžší než štít AlSi10Mg podobných rozměrů.
- Nižší tepelná vodivost: ~9,8 W/(m-K). Tato nižší vodivost znamená, že IN625 je lepší izolant než AlSi10Mg, což je často žádoucí pro primární funkci tepelného štítu, kterou je blokování přenosu tepla.
- Vyšší náklady: Surový prášek i proces tisku jsou podstatně dražší než v případě AlSi10Mg, a to kvůli vysokým nákladům na nikl a legující prvky a vyššímu energetickému příkonu a pomalejšímu tempu tisku.
- Typické aplikace tepelného štítu: Štíty výfukového potrubí, štíty katalyzátoru, štíty turbodmychadla (na straně turbíny), výkonné součásti výfukového systému, štíty v extrémně horkých místech motorového prostoru, aplikace v motorsportu.
Souhrnná tabulka pro výběr materiálu:
Vlastnosti | AlSi 10Mg | IN625 (Inconel® 625) | Kritéria výběru |
---|---|---|---|
Primární výhoda | Lehký, cenově výhodný, dobrý tepelný K | Vynikající pevnost při vysokých teplotách & odolnost proti korozi. | Ovladač primární funkce (Hmotnost v závislosti na maximální teplotě) |
Hustota | Nízká (~2,67 g/cm³) | Vysoká (~8,44 g/cm³) | Citlivost aplikace na hmotnost |
Maximální provozní teplota (přibližně) | ~200-250°C (392-482°F) | ~800-900°C+ (1472-1652°F+) | Expozice maximální provozní teplotě |
Tepelná vodivost | Vysoká (~120-140 W/m-K) | Nízká (~9,8 W/m-K) | Rozptyl tepla vs. požadavek na izolaci (lze upravit podle konstrukce) |
Odolnost proti korozi | Dobrý | Vynikající | Závažnost provozního prostředí (výfukové plyny, sůl) |
Náklady | Dolní | Vyšší | Rozpočtová omezení vs. požadavky na výkon |
Typický případ použití | Oblasti s mírnou teplotou, štíty s kritickou hmotností | Extrémně zahřáté oblasti (výfukové potrubí, turbo) | Umístění ve vozidle |
Dodavatel | Met3dp (Dodavatel prášku AlSi10Mg) | Met3dp (Rozdělovač prášku IN625) | Zajištění vysoce kvalitního zdroje prášku pro spolehlivé výsledky |
Export do archů
Proč záleží na kvalitě prášku (Met3dp Advantage):
Výkon finálního tepelného štítu vytištěného na 3D tiskárně závisí do značné míry na kvalitě použitého kovového prášku. Faktory jako např:
- Sféricita: Vysoká sféricita zajišťuje dobrou tekutost prášku v tiskárně, což vede k rovnoměrným vrstvám prášku a konzistentnímu tavení. Proces plynové atomizace Met3dp’produkuje vysoce sférické prášky.
- Distribuce velikosti částic (PSD): Řízená PSD má zásadní význam pro dosažení vysoké hustoty balení a minimalizaci pórovitosti v konečném dílu.
- Čistota & amp; Chemie: Pro dosažení požadovaných mechanických a tepelných vlastností je nezbytná přísná kontrola složení slitiny a minimalizace nečistot (např. kyslíku nebo dusíku).
- Absence satelitů: Drobné částice navázané na větší částice (satelity) mohou zhoršovat tekutost a hustotu balení. Technologie PREP, kterou používá také společnost Met3dp, vyniká při výrobě prášků bez satelitů.
Využitím Met3dp kovové prášky, mohou mít konstruktéři a výrobci jistotu, že začínají s nejlepším možným základem pro výrobu odolných, vysoce výkonných tepelných štítů vytištěných 3D tiskem, které splňují náročné požadavky automobilového průmyslu. Přístup k rozsáhlým službám Met3dp’ produkt zajišťuje správnou volbu materiálu pro optimální výkon.
Volba mezi AlSi10Mg a IN625 nakonec závisí na pečlivé analýze tepelného zatížení, podmínek prostředí, cílové hmotnosti a rozpočtu konkrétní aplikace. Kovový 3D tisk poskytuje flexibilitu pro efektivní využití obou materiálů, což umožňuje řešení na míru pro optimalizovaný tepelný management automobilů.
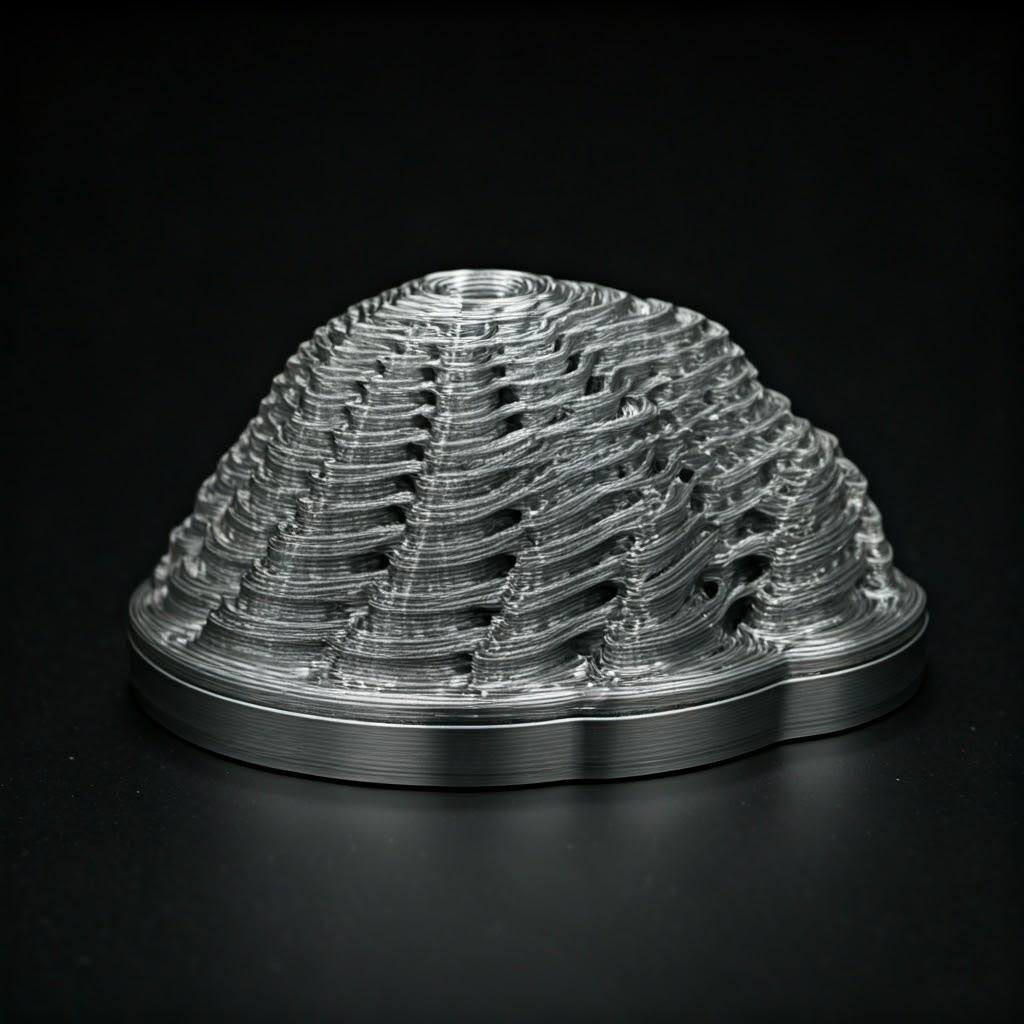
Úvahy o konstrukci aditivně vyráběných tepelných štítů: Optimalizace pro tisknutelnost a funkci
Jednou z nejvýznamnějších výhod aditivní výroby kovů pro tepelné štíty automobilů je nebývalá svoboda při navrhování. Tato svoboda je však spojena s odpovědností: konstruktéři musí přijmout Design pro aditivní výrobu (DfAM) principy, které umožňují vytvářet díly, jež jsou nejen funkčně dokonalejší, ale také optimalizované pro samotný proces tisku. Pouhý přenos návrhu určeného pro lisování z plechu do pracovního postupu AM pravděpodobně povede k neoptimálním výsledkům, což může zvýšit náklady, dobu výroby a riziko selhání tisku. Efektivní DfAM pro tepelné štíty zahrnuje holistický přístup, který současně zohledňuje geometrii, vlastnosti materiálu, podpůrné struktury, tepelný výkon a strukturální integritu. Spolupráce se zkušeným 3D tisk kovů servisní kancelář pro automobilový průmysl poskytovatel, jako je Met3dp, který může nabídnout podporu DfAM, je pro úspěch klíčový.
Zde jsou uvedeny klíčové konstrukční aspekty speciálně pro 3D tištěné tepelné štíty pro automobilový průmysl:
- Využití geometrické složitosti pro zvýšení výkonu:
- Konformní tvary: Navrhněte štíty, které přesně kopírují obrysy součástí, které chrání, nebo dostupný prostor v podvozku vozidla. Tím se maximalizuje pokrytí a účinnost tepelné ochrany, zejména v těsně zabalených motorových prostorech nebo kolem složitého vedení výfuků. Metal AM snadno vytváří tyto volné tvary, na rozdíl od omezení lisovacích forem.
- Integrované funkce: Eliminujte montážní kroky a potenciální místa poruch díky integraci funkcí přímo do konstrukce štítu. To zahrnuje:
- Montážní šrouby a držáky: Konstrukční upevňovací body přímo na těle štítu.
- Zpevnění žeber: Přidejte složité vzory žeber přesně tam, kde je to nutné pro podporu konstrukce, a minimalizujte spotřebu materiálu v jiných oblastech. Tato žebra mohou také ovlivnit proudění vzduchu a odvod tepla.
- Kanály pro proudění vzduchu: Začlenění kanálků nebo kanálků uvnitř nebo na povrchu štítu pro směrování chladicího vzduchu nebo řízení proudění horkého plynu, čímž se zvýší tepelný výkon aktivně, nikoli pouze pasivně blokováním tepla.
- Drátové/hadicové svorky: Integrujte příchytky nebo směrovací prvky pro zajištění blízkých součástí.
- Optimalizace topologie a odlehčení:
- Redukce materiálu: Pomocí softwaru pro optimalizaci topologie založeného na analýze konečných prvků (FEA) určete oblasti, kde lze materiál odstranit, aniž by byla narušena strukturální integrita nebo tepelná funkce štítu. Jedná se o výkonný nástroj pro vytváření lehké automobilové komponenty.
- Mřížové a gyroidní struktury: Nahraďte plné profily vnitřními mřížovými nebo gyroidními konstrukcemi. Tyto složité porézní geometrie přinášejí tepelným štítům několik výhod:
- Výrazné snížení hmotnosti: Dramaticky snižuje hmotnost dílu ve srovnání s pevnou konstrukcí.
- Zvýšený poměr tuhosti k hmotnosti: Může poskytnout vynikající konstrukční podporu s minimem materiálu.
- Lepší tepelná izolace: Vzduch zachycený v mřížkové/gyroidní struktuře může snížit přenos tepla vedením, což může zlepšit izolační vlastnosti štítu, zejména při použití materiálů s nižší vodivostí, jako je IN625. Konkrétní typ mřížky (např. otevřená vs. uzavřená buňka) lze vyladit pro požadované tepelné chování.
- Úvahy o návrhu: Vyžaduje pečlivou analýzu, aby byla zajištěna vyrobitelnost (odstranění prášku z vnitřních dutin) a pochopení dopadu na tepelnou vodivost a radiační vlastnosti. Minimální průměry vzpěr a uzlová spojení musí respektovat zvolený proces tisku a možnosti materiálu.
- Řízení podpůrných struktur:
- Minimalizace podpory: Podpěrné konstrukce jsou v procesech PBF často nezbytné k ukotvení dílu k sestavovací desce, k podpoře převislých prvků (obvykle úhly pod 45 stupňů od vodorovné roviny) a k odvodu tepla během tisku. Podpěry však zvyšují náklady na materiál, prodlužují dobu sestavení a vyžadují následné zpracování pro odstranění, které může být obtížné a zanechává stopy na povrchu (“witness marks”).
- Design pro vlastní podporu: Pokud je to možné, navrhněte prvky tak, aby byly samonosné. Místo ostrých vodorovných převisů používejte zkosení nebo filamenty. Strategicky orientujte díl na konstrukční desce, abyste minimalizovali potřebu podpěr na kritických nebo těžko přístupných plochách. Snažte se o úhel přesahu větší než 45 stupňů.
- Přístupné podpory: Pokud jsou podpěry nevyhnutelné, navrhněte je tak, aby byly snadno přístupné a odstranitelné. Vyhněte se složitým vnitřním podpěrám v uzavřených dutinách, pokud to není nezbytně nutné a plánované (např. navrhování přístupových otvorů pro odstraňování prášku a vytahování podpěr). Zvažte frangibilní podpěrné konstrukce, které se snadněji odlamují.
- Vliv na tepelné štíty: U tenkostěnných tepelných štítů jsou podpěry rozhodující pro zabránění deformacím a ukotvení dílu. Umístění podpěr je třeba pečlivě zvážit, aby se zabránilo deformaci a zajistilo se snadné odstranění bez poškození tenké konstrukce.
- Tloušťka stěny a velikost prvků:
- Minimální tloušťka stěny: Dodržujte minimální tloušťky stěn pro tisk pro zvolený materiál (AlSi10Mg nebo IN625) a proces AM. Obvykle se pohybuje od 0,4 mm do 1,0 mm, ale závisí na konkrétním stroji, parametrech a délce nepodporovaného rozpětí. Tenčí stěny snižují hmotnost a náklady na materiál, ale mohou být náchylnější k deformaci nebo poškození při manipulaci a následném zpracování.
- Jednotnost: AM sice umožňuje proměnlivou tloušťku, ale náhlé velké změny průřezu mohou vést k rozdílnému chlazení a zvýšenému zbytkovému napětí. Tam, kde je změna tloušťky nutná, se snažte o plynulé přechody.
- Drobné funkce: Zvažte minimální rozlišitelnou velikost prvku (díry, drážky, kolíky) pro daný proces, která se obvykle pohybuje kolem 0,3-0,5 mm.
- Tepelná hlediska při navrhování:
- Dráha tepelného toku: Vědomě navrhněte štít tak, aby řídil tepelný tok. Použijte geometrii, která odvádí teplo z citlivých oblastí. Zvažte, jak mohou integrovaná žebra nebo prvky fungovat jako chladicí žebra nebo chladiče, což může, ale nemusí být žádoucí v závislosti na cíli.
- Vlastnosti povrchu: Uvědomte si, že drsnost povrchu ve stavu, v jakém je postaven, může ovlivnit sálavý přenos tepla. I když se často řeší až při následném zpracování (např. povlaky), může mít volba počáteční konstrukce vliv na konečné vlastnosti povrchu.
- Tepelná simulace: Využívejte software pro tepelnou simulaci již v rané fázi návrhu (tepelná simulace tepelného štítu) k předpovědi rozložení teplot, tepelného toku a účinnosti navržené konstrukce štítu. To umožňuje iterativní optimalizaci před se zavázat k tisku, což šetří čas i náklady. Simulace může pomoci optimalizovat rozmístění žeber, změny tloušťky stěn a účinnost kanálů pro proudění vzduchu nebo mřížových struktur pro tepelnou izolaci.
Souhrnná tabulka DfAM pro tepelné štíty:
Zásada DfAM | Aplikace na tepelné štíty | Klíčový(é) přínos(y) |
---|---|---|
Geometrická svoboda | Konformní tvary, integrované držáky/žebra/kanály | Vylepšené uložení, snížený počet dílů, lepší tepelné/strukturální vlastnosti |
Optimalizace topologie | Odběr materiálu na základě FEA | Maximální odlehčení, optimalizovaná tuhost |
Mřížové struktury | Nahrazení plných profilů vnitřními mřížkami/gyroidy | Výrazné snížení hmotnosti, možnost lepší izolace, vysoká tuhost |
Minimalizace podpory | Strategická orientace, samonosné úhly (45°), koutové lišty/výhybky | Kratší doba tisku/náklady, snadnější následné zpracování, lepší povrchová úprava |
Přístupné podpory | Konstrukce podpěr pro snadné vyjmutí, zamezení zachycení vnitřních podpěr | Snížení pracnosti následného zpracování/rizika poškození |
Tloušťka stěny | Dodržování minim (0,4-1,0 mm+), plynulé přechody | Možnost tisku, strukturální integrita, kontrolovaná hmotnost |
Tepelný design | Usměrňování tepelného toku s ohledem na povrchové efekty pomocí simulace | Optimalizovaná tepelná ochrana, předvídatelný výkon |
Export do archů
Promyšlenou aplikací těchto principů DfAM mohou konstruktéři plně využít možností aditivní výroby kovů k výrobě automobilových tepelných štítů, které jsou lehčí, účinnější a rychleji vyvinuté než jejich tradičně vyráběné protějšky. Spolupráce s odborníky na AM, jako je tým Met3dp, během fáze návrhu může poskytnout neocenitelné poznatky o optimalizaci dílů z hlediska funkčnosti i vyrobitelnosti.
Dosažitelná tolerance, povrchová úprava a rozměrová přesnost u kovových tepelných štítů tištěných 3D tiskem
Při specifikaci komponentů pro automobilové aplikace se konstruktéři a manažeři nákupu oprávněně zaměřují na přesnost. Otázky týkající se tolerance 3D tisku kovů, dosažitelné drsnost povrchu kovu AMa celkově rozměrová přesnost automobilových dílů jsou rozhodující. Ačkoli AM nabízí neuvěřitelnou svobodu při navrhování, je důležité pochopit, jaká je úroveň přesnosti tohoto procesu a jaká je v porovnání s konvenčními metodami, jako je obrábění nebo lisování. U tepelných štítů pro automobilový průmysl se požadovaná přesnost liší v závislosti na konkrétním prvku - například montážní body mohou vyžadovat přísnější tolerance než velké otevřené plochy.
Rozměrová přesnost a tolerance:
Procesy slučování kovů v práškovém loži (PBF), jako je SLM/DMLS, mohou dosáhnout poměrně dobré rozměrové přesnosti přímo ze stroje. Výslednou přesnost dílů však ovlivňuje několik faktorů:
- Kalibrace stroje: Pravidelná a přesná kalibrace laserů/elektronového paprsku, skenerů a pohybových systémů tiskárny je zásadní.
- Vlastnosti materiálu: Různé materiály se při ochlazování různě smršťují a deformují (např. AlSi10Mg vs. IN625). Podle toho je třeba vyladit procesní parametry.
- Tepelné namáhání: Rychlé zahřívání a ochlazování, které je pro PBF typické, vytváří vnitřní pnutí, které může způsobit deformaci nebo zkreslení a ovlivnit přesnost. Velkou roli při jejich zvládání hraje konstrukce dílu, orientace a strategie podpory.
- Velikost a geometrie dílu: Větší díly nebo složité geometrie s různými průřezy jsou obecně náročnější na tisk s vysokou přesností kvůli kumulovanému tepelnému napětí.
- Parametry sestavení: Tloušťka vrstvy, výkon laseru, rychlost skenování atd. ovlivňují konečné rozměry.
Typické tolerance:
- Tolerance podle stavu konstrukce: Pro dobře řízené procesy L-PBF se často uvádějí typické dosažitelné tolerance v rozmezí:
- ±0,1 mm až ±0,2 mm pro menší prvky (např. do 20-50 mm)
- ±0,1 % až ±0,2 % jmenovitého rozměru u větších prvků.
- Průmyslové normy, jako je řada ISO/ASTM 52900, poskytují rámec, ale konkrétní možnosti stroje/materiálu často určují dosažitelné limity.
- Tolerance po zpracování: Pokud jsou vyžadovány přísnější tolerance, zejména u styčných ploch, montážních otvorů nebo kritických rozhraní na tepelném štítu, obvykle se používá následné CNC obrábění. Obráběním lze dosáhnout tolerancí ±0,025 mm až ±0,05 mm nebo ještě těsnějších, srovnatelných s tradiční výrobou.
Povrchová úprava (drsnost):
Povrchová úprava kovových dílů vyrobených metodou AM je ze své podstaty drsnější než obráběné nebo dokonce lisované povrchy. To je způsobeno povahou procesu po vrstvách a částečně roztavenými částicemi prášku, které ulpívají na povrchu.
- Faktory ovlivňující drsnost:
- Tloušťka vrstvy: Silnější vrstvy mají zpravidla za následek drsnější povrch.
- Velikost částic prášku: Jemnější prášky mohou vést k hladším povrchovým úpravám, ale mohou představovat problém v tekutosti. Met3dp’se zaměřuje na optimalizované PSD, což pomáhá tuto skutečnost vyvážit.
- Orientace: Plochy rovnoběžné s konstrukční deskou (horní plochy) jsou obvykle hladší než svislé stěny. Povrchy směřující dolů (podepřené nebo téměř vodorovné) bývají nejhrubší v důsledku kontaktu s podpěrou nebo “efektu schodišťového kroku”. Zakřivené povrchy směřující nahoru mají obecně lepší povrchovou úpravu než povrchy směřující dolů.
- Parametry sestavení: Energie laseru/paprsku, strategie skenování a průtok plynu (v L-PBF) ovlivňují dynamiku taveniny a konsolidaci povrchu.
- Typické hodnoty Ra (ve výchozím stavu):
- AlSi10Mg (L-PBF): Hodnoty Ra se obvykle pohybují od 6 µm do 15 µm (240 µin až 600 µin).
- IN625 (L-PBF): Hodnoty Ra se často pohybují od 8 µm do 20 µm (320 µin až 800 µin).
- Tyto hodnoty jsou velmi závislé na zaměření a specifikách procesu.
- Zlepšení povrchové úpravy: U tepelných štítů může být pro nekritické povrchy přijatelná povrchová úprava podle stavu, ale často je požadována hladší povrchová úprava z estetických důvodů, z důvodu lepší únavové životnosti (méně míst pro vznik trhlin) nebo z důvodu přípravy pro nátěry. Běžné následné zpracování povrchu techniky zahrnují:
- Tryskání kuličkami / kuličkování: Vytváří rovnoměrný matný povrch, odstraňuje sypký pudr a může vytvářet příznivé tlakové napětí. Typické Ra se může zlepšit na 3-8 µm.
- Obrábění / vibrační úprava: Používá média k vyhlazení povrchů a hran, zvláště efektivní pro dávky menších dílů. Lze dosáhnout hodnot Ra až 1-3 µm.
- CNC obrábění: Poskytuje nejhladší povrchovou úpravu specifických prvků, ale pouze tam, kde je možný přístup nástroje.
- Elektrolytické leštění: Lze dosáhnout velmi hladkého, zrcadlového povrchu, zejména na materiálech jako IN625, ale vyžaduje specifické elektrolyty a zohlednění geometrie dílů.
Kontrola kvality a závazek společnosti Met3dp’:
Dosažení konzistentní rozměrové přesnosti a povrchové úpravy vyžaduje důslednou kontrolu kontrola kvality tisku na kov postupy. To zahrnuje:
- Pravidelná údržba a kalibrace stroje.
- Přísná kontrola kvality prášku a manipulace s ním (hlavní přednost společnosti Met3dp).
- Vývoj optimalizovaných parametrů procesu pro každý materiál (AlSi10Mg, IN625).
- Monitorování během procesu, pokud je k dispozici.
- Kontrola po výrobě pomocí technik, jako jsou souřadnicové měřicí stroje (CMM), 3D skenování a profilometrie povrchu.
Společnost Met3dp se zavázala dodávat díly s nejlepší přesností a spolehlivostí v oboru. Naše investice do pokročilých tiskových technologií a vysoce kvalitní práškové výroby zajišťují, že zákazníci obdrží tepelné štíty splňující jejich specifikace. Úzce spolupracujeme se zákazníky, abychom porozuměli požadavkům na tolerance a poradili jim, jaký přístup je nejlepší, ať už se spoléháme na přesnost při výrobě, nebo zahrnujeme sekundární obráběcí operace.
Souhrnná tabulka: Přesnost & povrchová úprava kovových tepelných štítů AM
Parametr | Typický rozsah ve stavu po dokončení (L-PBF) | Ovlivňující faktory | Možnosti dodatečného zpracování | Význam pro tepelné štíty |
---|---|---|---|---|
Rozměrová tolerance | ±0,1-0,2 mm nebo ±0,1-0,2 % | Stroj, materiál, tepelné namáhání, velikost, parametry | CNC obrábění | Kritické pro montážní body, rozhraní; méně kritické pro otevřené povrchy |
Drsnost povrchu (Ra) | AlSi10Mg: 6-15 µm; IN625: 8-20 µm | Tloušťka vrstvy, velikost prášku, orientace, parametry | Tryskání, otryskávání, obrábění | Ovlivňuje estetiku, přilnavost nátěru, případně únavu/proudění vzduchu |
Metoda kontroly | Kalibrace, optimalizace parametrů, kontroly kvality | Design (DfAM), Řízení procesu, Kvalita materiálu (Met3dp) | Sekundární operace | Zajišťuje, aby díly důsledně splňovaly technické specifikace |
Export do archů
Pochopení těchto dosažitelných ukazatelů umožňuje konstruktérům vhodně navrhnout tepelné štíty a stanovit realistická očekávání. Ačkoli se technologie AM pro kovy nemusí rovnat nejjemnějším tolerancím přesného obrábění přímo z konstrukční desky, kombinace volnosti návrhu s úctyhodnou přesností, často vylepšenou cíleným následným zpracováním, z ní činí mocný nástroj pro vytváření efektivních a komplexních tepelných řešení pro automobilový průmysl.
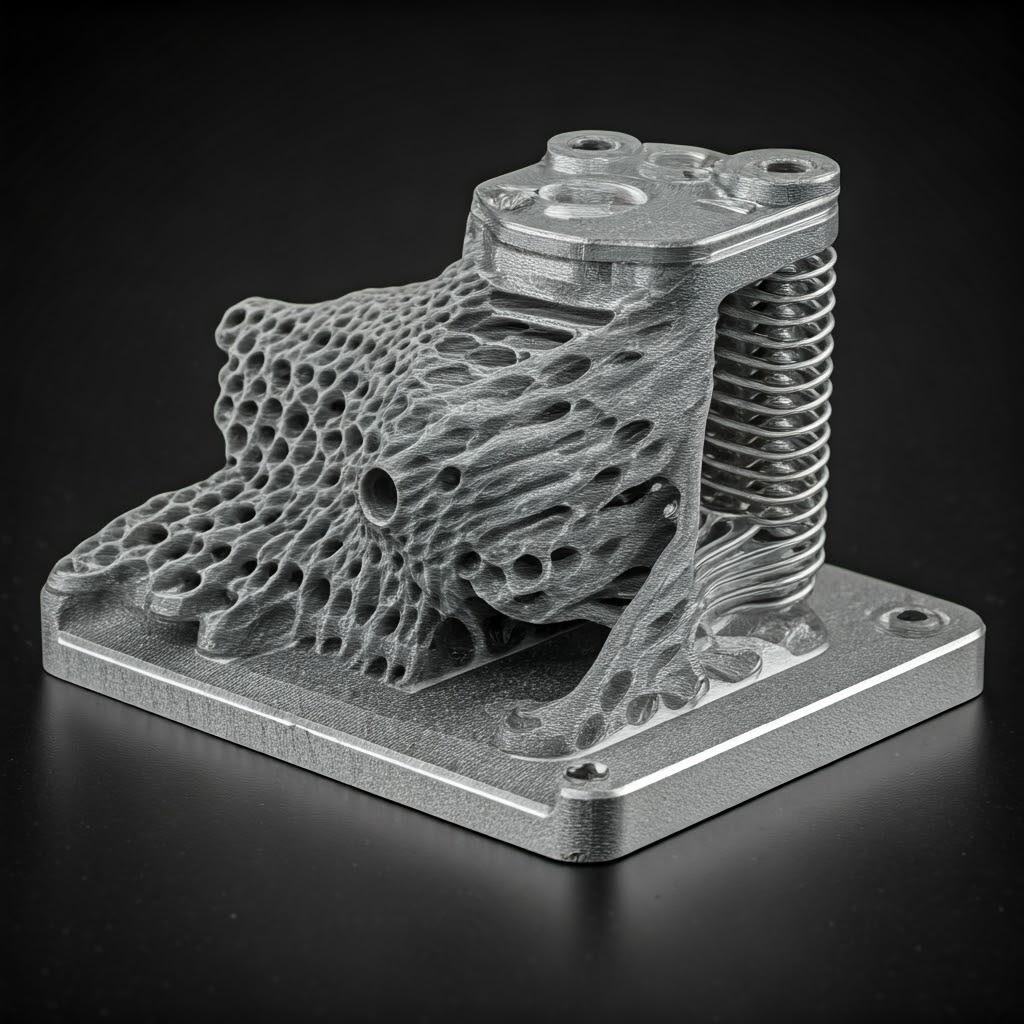
Požadavky na následné zpracování 3D tištěných tepelných štítů pro automobilový průmysl
Vytvoření funkčního tepelného štítu automobilu pomocí 3D tisku z kovu nekončí, když se tiskárna zastaví. Sestavený díl, čerstvě sundaný ze stavební desky, vyžaduje několik zásadních kroků následné zpracování kroky k dosažení konečných požadovaných vlastností, rozměrů, povrchové úpravy a nakonec i vhodnosti pro použití v náročném automobilovém prostředí. Tyto kroky jsou nezbytné pro zajištění spolehlivosti, trvanlivosti a výkonu součásti, ať už je vyrobena z AlSi10Mg, nebo z IN625 schopného pracovat při vysokých teplotách. Pokud tyto kroky neprovedete správně, může to ohrozit integritu tepelného štítu.
Mezi běžné požadavky na následné zpracování patří:
- Úleva od stresu / tepelné ošetření:
- Proč: To je pravděpodobně nejkritičtější krok následného zpracování kovových dílů PBF. Rychlé zahřívání a ochlazování během tisku vyvolává v materiálu značná zbytková napětí. Tato napětí mohou způsobit deformaci nebo zkreslení (zejména po vyjmutí z konstrukční desky), snížit únavovou životnost a dokonce vést k praskání v průběhu času nebo při následném obrábění. Tepelné zpracování kovů 3D tiskem je nezbytné pro uvolnění těchto napětí a stabilizaci mikrostruktury. U slitin, jako je AlSi10Mg, je navíc pro dosažení optimálních mechanických vlastností (pevnost, tvrdost) nutné tepelné zpracování (např. zpracování roztokem T6 a stárnutí). IN625 se obvykle podrobuje napěťovému odlehčení nebo žíhání, aby se zlepšila tažnost a zmírnilo napětí, aniž by se nutně zaměřovalo na precipitační kalení.
- Jak: Díly se umístí do pece s řízenou atmosférou (vakuum nebo inertní plyn, např. argon, aby se zabránilo oxidaci, což je zvláště důležité pro IN625 při vysokých teplotách) a podrobí se specifickým tepelným cyklům (rychlost zahřívání, teplota namáčení, doba namáčení, rychlost chlazení). Přesný cyklus závisí do značné míry na slitině a požadovaných konečných vlastnostech.
- AlSi10Mg: Často zahrnuje úpravu roztokem (např. ~530 °C) s následným ochlazením a umělým stárnutím (např. ~160 °C) pro stav T6. Jednoduché uvolnění napětí může zahrnovat nižší teploty (~300 °C).
- IN625: K uvolnění napětí obvykle dochází při vyšších teplotách, často v rozmezí 870 °C až 980 °C, po nichž následuje řízené ochlazení. K žíhání může docházet při ještě vyšších teplotách (~1100 °C+).
- Úvahy: Tepelné zpracování se musí často provádět před vyjmutí dílu ze stavební desky, zejména u velkých nebo tenkostěnných dílů náchylných k deformaci, jako je mnoho konstrukcí tepelných štítů. Atmosféra v peci musí být pečlivě kontrolována.
- Vyjmutí dílu ze stavební desky:
- Proč: Během tisku je díl nataven na silnou kovovou konstrukční desku.
- Jak: Obvykle se provádí pomocí elektroerozivního obrábění (EDM) nebo pásové pily. Při tomto procesu je třeba dbát na to, aby nedošlo k poškození dílu. Drátové elektroerozivní obrábění se často upřednostňuje kvůli přesnosti a minimálnímu mechanickému namáhání.
- Odstranění podpůrné konstrukce:
- Proč: Podpěry jsou sice nezbytné pro tisk, ale nejsou součástí finální součásti a musí být odstraněny.
- Jak: V závislosti na složitosti a umístění podpěr může jít o pracný proces. Mezi tyto metody patří:
- Ruční lámání/řezání: Pro přístupné podpěry lze použít kleště, štípací kleště nebo malé brusky. Vyžaduje zručnost, aby nedošlo k poškození povrchu dílu.
- CNC obrábění: Frézováním nebo broušením lze přesně odstranit nosné konstrukce, zejména kontaktní body (“svědecké stopy”).
- Drátové elektroerozivní obrábění: Pokud to přístup umožňuje, lze je použít pro složité nebo těžko přístupné podpěry.
- Úvahy: Podpora odstraňování dílů AM je klíčovou oblastí, ve které hraje DfAM roli - konstrukce pro snadné odstranění podpory výrazně snižuje čas a náklady na následné zpracování. Svědecké stopy, které zůstanou po odstranění, mohou vyžadovat další dokončovací práce.
- CNC obrábění (pokud je vyžadováno):
- Proč: Dosáhnout u kritických prvků (např. montážních otvorů, styčných ploch, těsnicích ploch) větších tolerancí, než umožňují možnosti konstrukce. Používá se také ke zlepšení kvality povrchu na specifických plochách.
- Jak: Standard CNC obrábění 3D výtisků (frézování, soustružení, vrtání). Upínání složité geometrie 3D tištěného dílu může být někdy náročné. Obrábění se obvykle provádí po tepelné zpracování pro zajištění rozměrové stability.
- Úvahy: Musí zohledňovat vlastnosti materiálu (AlSi10Mg se obrábí relativně snadno; IN625 je notoricky známý jako obtížný materiál kvůli kalení a houževnatosti, což vyžaduje specifické nástroje, rychlosti a posuvy). DfAM by měl zahrnovat přidání dodatečného zásobního materiálu (přídavek na obrábění) na povrchy určené k obrábění.
- Povrchová úprava:
- Proč: Pro zlepšení estetiky, odstranění volných částic prášku, dosažení jednotného vzhledu, přípravu na nátěry nebo někdy pro zlepšení únavové životnosti či vlastností proudění vzduchu.
- Jak: Různé techniky povrchové úpravy lze použít:
- Otryskávání kuliček / kuličkování: Běžně se používá pro jednotný matný povrch. Různá média (skleněné kuličky, keramika, ocelové broky) vytvářejí různé efekty. Kuličkování vyvolává příznivé tlakové napětí.
- Třískové/vibrační dokončování: Hodí se k odstraňování otřepů na hranách a vyhlazování povrchů na sériích dílů.
- Broušení/leštění: Ruční nebo automatizované postupy pro dosažení hladšího a jasnějšího povrchu na určitých plochách.
- Elektrolytické leštění: Elektrochemický proces pro velmi hladké a čisté povrchy, zvláště účinný u nerezových ocelí a niklových slitin, jako je IN625.
- Úvahy: Zvolená metoda závisí na požadované povrchové úpravě, geometrii dílu (přístupu), materiálu a nákladech. Agresivní metody mohou odstranit malé množství materiálu, což ovlivní konečné rozměry.
- Čištění a kontrola:
- Proč: K odstranění zbytků prášku (zejména z vnitřních kanálků nebo mřížkových struktur), obráběcích kapalin nebo tryskacích prostředků. Závěrečná kontrola zajišťuje, že díl splňuje všechny požadavky na rozměry, povrchovou úpravu a kvalitu.
- Jak: Čištění ultrazvukem, vyfukování stlačeným vzduchem. Kontrolní metody zahrnují vizuální kontrolu, souřadnicovou měřicí soustavu, 3D skenování, profilometrii a případně NDT (nedestruktivní testování), jako je CT skenování vnitřní integrity, pokud je to nutné.
- Povlak (volitelný):
- Proč: Zlepšení specifických vlastností, zejména tepelné izolace nebo odrazivosti. Povlakování 3D tištěných dílů je běžná pro optimalizaci výkonu.
- Jak: U tepelných štítů se často uvažuje o tepelně bariérových povlacích (TBC). Obvykle se jedná o povlaky na bázi keramiky (např. yttrií stabilizovaný zirkoničitan – YSZ), které se aplikují plazmovým nástřikem nebo jinými technikami. Vytvářejí vrstvu s velmi nízkou tepelnou vodivostí, což výrazně snižuje přenos tepla štítem. K odrazu sálavého tepla lze použít i reflexní povlaky (např. keramicko-metalické nebo specializované nátěry).
- Úvahy: Příprava povrchu je pro dobrou přilnavost nátěru rozhodující. Povlak zvyšuje tloušťku a může mít teplotní omezení.
Shrnutí pracovního postupu následného zpracování:
Typická posloupnost (i když existují i varianty) je:
- Zmírnění napětí / tepelné zpracování (často na stavební desce)
- Odstranění ze stavební desky (elektroerozivní obrábění / pila)
- Demontáž podpěr (ruční / obrábění)
- CNC obrábění (pokud je vyžadováno kvůli tolerancím/prvkům)
- Povrchová úprava (tryskání, otryskávání atd.)
- Čištění & amp; Inspekce
- Nátěr (pokud je vyžadován)
Pochopení těchto nezbytných normy pro povrchovou úpravu automobilových dílů a kroků je zásadní pro přesný odhad celkových nákladů a doby realizace 3D tištěných tepelných štítů. Každý krok přidává čas a náklady, což zdůrazňuje důležitost optimalizace návrhu (DfAM), aby se pokud možno minimalizovaly požadavky na následné zpracování, zejména odstranění podpěr a obrábění.
Běžné problémy při 3D tisku tepelných štítů a jejich řešení
Přestože aditivní výroba kovů nabízí významné výhody pro výrobu tepelných štítů pro automobily na zakázku, není tento proces bez potenciálních překážek. Jejich pochopení výzvy pro automobilový průmysl v oblasti AM aplikací, konkrétně v souvislosti s tepelnými štíty vyrobenými z AlSi10Mg nebo IN625, umožňuje konstruktérům a výrobcům aktivně zavádět strategie pro zmírnění dopadů a zajistit tak úspěšné výsledky a spolehlivé komponenty. Klíčem k překonání těchto složitostí je spolupráce se zkušeným poskytovatelem služeb.
Zde jsou některé běžné problémy a způsoby jejich řešení:
- Deformace a zkreslení (zbytkové napětí):
- Výzva: Vysoké teploty a rychlé ochlazování, které jsou pro PBF typické, vytvářejí v tištěném dílu značná zbytková napětí. Tato napětí mohou při sestavování dílu způsobit jeho deformaci, odklon od sestavovací desky nebo deformaci, zejména u tenkostěnných velkoplošných geometrií typických pro tepelné štíty. Tato stránka zvládání zbytkového stresu problém je výraznější u materiálů s vyššími koeficienty tepelné roztažnosti nebo u materiálů vyžadujících vyšší teploty zpracování (např. IN625).
- Zmírnění:
- DfAM: Konstrukční prvky pro minimalizaci koncentrace napětí. Místo ostrých rohů použijte koutové hrany. Snažte se o rovnoměrnější tloušťky stěn nebo postupné přechody.
- Orientace: Strategicky orientujte díl na konstrukční desce tak, abyste minimalizovali velké rovné plochy rovnoběžné s deskou a pokud možno snížili poměr výšky a šířky.
- Strategie podpory: Robustní podpůrné konstrukce mají zásadní význam pro pevné ukotvení dílu na konstrukční desce a jako chladiče. Klíčové je pečlivé umístění a hustota.
- Vytápění stavebních desek: Předehřívání stavební desky (běžné u mnoha strojů L-PBF, nezbytné u EBM) snižuje tepelný gradient a snižuje zbytkové napětí.
- Parametry procesu: Optimalizované parametry (strategie skenování, výkon laseru, rychlost) vyvinuté pro konkrétní materiál a geometrii mohou minimalizovat vznik napětí.
- Tepelné zpracování: Provádění tepelného ošetření pro uvolnění napětí před odstranění dílu z konstrukční desky je často nejúčinnějším způsobem, jak zabránit deformaci při uvolnění.
- Obtíže při odstraňování podpory:
- Výzva: Tepelné štíty mají často složité křivky a případně vnitřní kanály nebo dutiny. Umístění podpěr v těchto těžko přístupných místech znesnadňuje a prodlužuje demontáž a hrozí poškození dílu. U mřížkových konstrukcí může být odstranění vnitřních podpěr téměř nemožné, pokud se s ním nepočítá.
- Zmírnění:
- DfAM pro přístup: Navrhněte díl s ohledem na odstranění podpěr. Orientujte se tak, abyste minimalizovali vnitřní podpěry. Pokud jsou vnitřní podpěry nutné (např. pro vnitřní kanály v mřížce), navrhněte přístupové otvory pro nástroje na odstraňování nebo odsávání prášku.
- Typy podpory: Používejte optimalizované podpěrné konstrukce (např. tenkostěnné, kvádrové nebo kuželové podpěry se specifickými kontaktními body) určené pro snadnější odpojení. Některé softwary umožňují generovat snadno rozlomitelné nebo rozpustné podpěry (méně obvyklé u AM kovů).
- Techniky odstraňování: V závislosti na dostupnosti a požadavcích na přesnost použijte k odstranění podpěr vhodné techniky, jako je pečlivé ruční lámání, obrábění na CNC nebo elektroerozivní obrábění.
- Pórovitost:
- Výzva: Drobné dutiny nebo póry uvnitř potištěného materiálu (pórovitost kovu AM) může zhoršit mechanické vlastnosti (zejména únavovou pevnost) a potenciálně vytvořit netěsnosti, pokud je třeba štít utěsnit. Pórovitost může vznikat v důsledku zachyceného plynu, neúplného spojení mezi vrstvami nebo keyholingu (propadání parních prohlubní).
- Zmírnění:
- Vysoce kvalitní prášek: Zásadní význam má použití vysoce kvalitního sférického prášku s kontrolovaným PSD a nízkým obsahem plynu, jaký vyrábí společnost Met3dp pomocí pokročilých atomizačních technik. Špatná kvalita prášku je častým zdrojem pórovitosti.
- Optimalizované parametry: Vývoj a přísná kontrola parametrů tisku (výkon laseru, rychlost skenování, rozteč šraf, tloušťka vrstvy, průtok plynu) jsou rozhodující pro zajištění úplného roztavení a splynutí.
- Stav stroje: Dobrá údržba tiskárny a kontrola atmosféry v konstrukční komoře (kvalita inertního plynu) zabraňuje kontaminaci a podporuje stabilní tavení.
- Izostatické lisování za tepla (HIP): U kritických aplikací, které vyžadují téměř nulovou pórovitost, lze HIP použít jako následný krok zpracování. Zahrnuje použití vysoké teploty a izostatického tlaku plynu k uzavření vnitřních dutin. To sice zvyšuje náklady a čas, ale výsledkem jsou plně hutné díly.
- Povrchová úprava a vady:
- Výzva: Dosažení požadované povrchové úpravy, zejména u povrchů směřujících dolů nebo u složitých vnitřních prvků, může být obtížné. Mohou se vyskytnout vady, jako je “schodovitost” na mělkých úhlech, tvorba strusky nebo částečně roztavené částice ulpívající na povrchu (“rozstřik”).
- Zmírnění:
- Orientace: Optimalizujte orientaci dílu tak, aby kritické povrchy byly pokud možno umístěny ve svislé poloze nebo směrem nahoru.
- Parametry: Dolaďte parametry obrysů a případně použijte specifické strategie skenování pro definici hranic.
- Následné zpracování: Pro dosažení požadované konečné povrchové úpravy se po odstranění hlavních stop po podepření spolehněte na techniky povrchové úpravy (tryskání, otryskávání, leštění).
- Kvalita prášku: Vysoce kvalitní prášek snižuje rozstřikování a podporuje hladší chování taveniny.
- Dosažení požadavků na interní kanály:
- Výzva: Pokud konstrukce tepelného štítu obsahuje vnitřní kanály pro chladicí nebo konstrukční účely (např. v mřížových konstrukcích), může být náročné zajistit, aby tyto kanály neobsahovaly prášek a měly přijatelnou povrchovou úpravu. Odstranění prášku z klikatých cest může být obtížné a vnitřní povrchy jsou ze své podstaty drsnější.
- Zmírnění:
- DfAM: Navrhněte kanály s dostatečným průměrem a hladkými ohyby, které usnadňují odstraňování prášku. Včetně strategicky umístěných odtokových/přístupových otvorů. Zvažte návrh samonosných kanálů, abyste minimalizovali vnitřní podpěry.
- Odstranění prášku: Využívejte vibrace, stlačený vzduch a případně specializované stanice pro odstraňování prášku po montáži.
- Volba procesu: Některé procesy mohou být vhodnější pro vnitřní kanály (např. EBM často produkuje méně hustě zabalený prášek).
- Kontrola: K ověření úplného odstranění prášku a vnitřní integrity může být nutné provést CT vyšetření.
- Zajištění konzistence a kvality:
- Výzva: Udržení konzistentní kvality dílů (rozměrová přesnost, vlastnosti materiálu, úroveň vad) v různých sestavách a na různých strojích vyžaduje robustní systém zajištění kvality aditivní výroby protokoly.
- Zmírnění:
- Standardizované postupy: Zavedení přísných procesních kontrol, standardizovaných parametrů sestavování a přísných plánů údržby strojů.
- Sledovatelnost materiálu: Udržujte úplnou sledovatelnost šarží prášku použitých pro každou sestavu. Pravidelně testujte kvalitu prášku.
- Monitorování během procesu: Využijte dostupné nástroje pro monitorování taveniny nebo zobrazování vrstev k odhalení případných anomálií během sestavování.
- Kvalifikace po dokončení stavby: Zavedení konzistentních kontrolních protokolů (CMM, skenování, NDT) a testování mechanických vlastností (pomocí svědeckých kupónů vytištěných spolu s díly) pro ověření kvality.
Řešení těchto problémů vyžaduje kombinaci chytrého návrhu (DfAM), pečlivé kontroly procesu, vysoce kvalitních materiálů, vhodného následného zpracování a důsledného zajištění kvality. Partnerství s vertikálně integrovaným a zkušeným poskytovatelem, jako je Met3dp, který kontroluje vše od výroby prášku až po finální kvalifikaci dílu, tato rizika výrazně minimalizuje. Jejich hluboká znalost materiálových věd, tiskových procesů a složitostí následného zpracování zajišťuje, že jsou potenciální problémy předvídány a řešeny proaktivně. Pro společnosti, které hledají spolehlivé 3D tištěné tepelné štíty na zakázku, je výběr partnera s prověřenými odbornými znalostmi zásadní pro zvládnutí složitostí technologie AM pro zpracování kovů. Více informací o komplexních schopnostech společnosti Met3dp’ a jejím závazku ke kvalitě v celé škále služeb se dozvíte na jejích webových stránkách https://met3dp.com/.
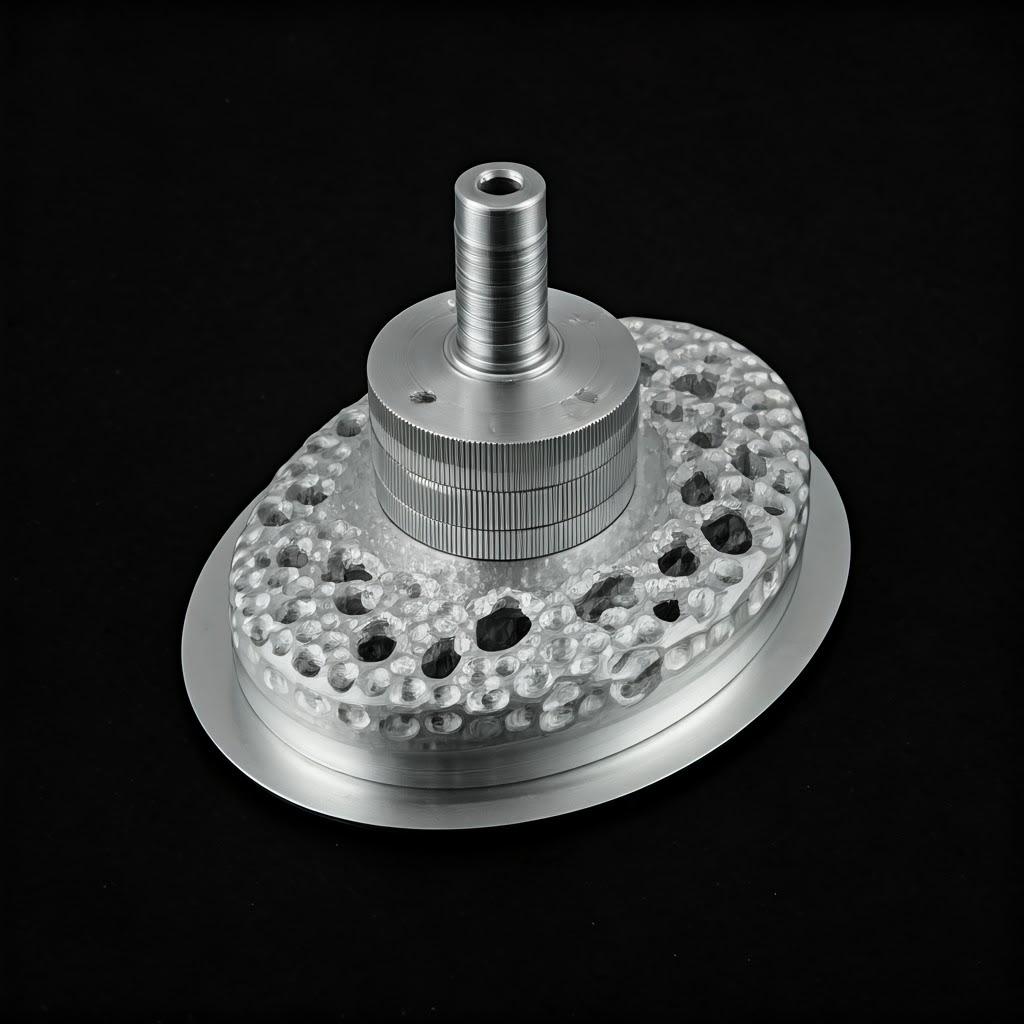
Jak vybrat správného poskytovatele služeb 3D tisku kovů pro tepelné štíty automobilů
Výběr správného výrobního partnera je stejně důležitý jako zdokonalení samotného návrhu, zejména pokud se pouštíte do pokročilých technologií, jako je aditivní výroba kovů pro náročné automobilové aplikace, jako jsou tepelné štíty. Kvalita, spolehlivost a výkonnost finální součásti do značné míry závisí na schopnostech, odborných znalostech a systémech kvality vybraného výrobce 3D tisk kovů servisní kancelář pro automobilový průmysl poskytovatele. Inženýři a manažeři veřejných zakázek, kteří se v tomto prostředí pohybují, musí při hodnocení potenciálních dodavatelů zohlednit nejen cenu, ale i řadu technických a provozních faktorů. Nalezení skutečného odborník na výrobu tepelných štítů který rozumí jak AM, tak i nuancím požadavků automobilového průmyslu.
Zde je komplexní průvodce tím, na co se zaměřit při výběru partnera pro výrobu tepelného štítu na zakázku:
- Technické znalosti a materiálové schopnosti:
- Příslušné materiály: Ujistěte se, že dodavatel má prokazatelné zkušenosti s tiskem na specifické materiály, které jsou pro váš tepelný štít potřeba - především na AlSi 10Mg a IN625. Vyžádejte si doklady o úspěšných výtiscích, katalogové listy materiálů založené na jejich postupu a případně vzorky dílů. Měli by rozumět jedinečným výzvám a optimálním parametrům pro každou slitinu.
- Znalost procesů: Ověřte si jejich odborné znalosti v příslušné technologii AM, nejčastěji laserové fúze v práškovém loži (L-PBF, včetně SLM/DMLS) pro tepelné štíty díky její schopnosti vyrábět jemné prvky a složité geometrie. Pokud se uvažuje o tavení elektronovým svazkem (EBM) (třeba pro specifické aplikace IN625), ujistěte se, že disponují touto schopností.
- Technická podpora (DfAM): Nabízí poskytovatel konzultace v oblasti designu pro aditivní výrobu (DfAM)? Dobrý partner bude spolupracovat s vaším konstrukčním týmem na optimalizaci návrhu tepelného štítu pro tisk, funkčnost, nákladovou efektivitu a minimalizaci následného zpracování. Tento přístup založený na spolupráci je neocenitelný.
- Systém řízení kvality (QMS) a certifikace:
- ISO 9001: Jedná se o základní požadavek, který naznačuje robustní systém řízení jakosti pro obecnou kvalitu výroby.
- Automobilové normy (IATF 16949): Přestože ne všechny servisní kanceláře AM mají certifikaci IATF 16949 specifickou pro automobilový průmysl (je přísná a často zaměřená na větší objem výroby), informujte se o jejich znalosti požadavků automobilového průmyslu a o tom, zda jejich systém řízení jakosti zahrnuje příslušné zásady (např. APQP, PPAP, sledovatelnost). Poskytovatelé sloužící leteckému průmyslu (např. držitelé AS9100) mají často velmi přísné systémy kvality použitelné pro náročné potřeby automobilového průmyslu.
- Sledovatelnost: Poskytovatel musí prokázat úplnou sledovatelnost materiálu - od šarže surového prášku (Dodavatel prášku AlSi10Mg, Rozdělovač prášku IN625) přes tisk, následné zpracování a konečnou kontrolu. To je u kritických automobilových dílů neoddiskutovatelné. Společnost Met3dp, která vyrábí vlastní prášky, nabízí výjimečnou kontrolu nad tímto aspektem.
- Zkušenosti v oboru:
- Záznamy z automobilového průmyslu: Pracoval poskytovatel již dříve na projektech v automobilovém průmyslu, konkrétně na komponentech tepelného managementu? Zkušenosti s náročnými požadavky, validačními procesy a běžnými problémy v automobilovém průmyslu jsou významnou výhodou. Požádejte o relevantní případové studie nebo reference (při respektování dohod o zachování důvěrnosti).
- Porozumění aplikacím: Rozumí funkčním požadavkům na tepelný štít - tepelná izolace/odraz, odolnost proti vibracím, trvanlivost, montážní omezení?
- Vybavení a zařízení:
- Machine Park: Zhodnoťte jejich nabídku a počet průmyslových tiskáren AM pro kovy. Mají dostatečné množství Výrobní kapacita AM zvládnout potřeby prototypů a případně je rozšířit na malosériovou až středně velkosériovou výrobu? Jsou stroje dobře udržované a kalibrované?
- Manipulace s práškem: Vyhodnoťte jejich postupy pro skladování prášku, manipulaci s ním, recyklaci a testování kvality, abyste zabránili kontaminaci a zajistili konzistenci materiálu. Poskytovatelé, jako je společnost Met3dp, kteří vyrábějí vlastní prášky pomocí pokročilých metod, jako je plynová atomizace a PREP, prokazují vynikající kontrolu nad tímto kritickým vstupem.
- Možnosti následného zpracování: Nabízejí základní kroky následného zpracování přímo ve firmě (tepelné zpracování, odstranění podpěr, základní povrchová úprava)? Nebo se spoléhají na outsourcing? Vlastní kapacity obecně umožňují lepší kontrolu kvality, dodacích lhůt a komunikace. Ověřte si jejich odborné znalosti v oblasti správného tepelného zpracování AlSi10Mg a IN625 a bezpečného odstraňování podpěr ze složitých geometrií. Posuďte jejich schopnosti pro CNC obrábění nebo specializované povrchové úpravy, pokud jsou vyžadovány.
- Řízení projektů a komunikace:
- Jasná komunikace: Je poskytovatel vstřícný, transparentní a snadno se s ním komunikuje? Stanovte jasná kontaktní místa a struktury podávání zpráv.
- Řízení projektů: Mají strukturovaný proces řízení projektů, od nabídky a kontroly návrhu až po plánování výroby, kontroly kvality a dodání?
- Detail nabídky: Prověřte jejich postup tvorby cenových nabídek. Jsou v něm jasně rozděleny náklady (materiál, strojní čas, práce, následné zpracování)? Jsou v něm uvedeny dodací lhůty a dodací podmínky?
- Náklady a doba realizace:
- Konkurenční ceny: Zatímco náklady by neměly být pouze faktor, získat nabídky od více kvalifikovaných dodavatelů. Ujistěte se, že porovnáváte podobné materiály, standardy kvality a zahrnuté následné zpracování.
- Reálná doba dodání: Diskutujte o dodacích lhůtách pro prototypy a výrobní série. Ujistěte se, že poskytovatel má zkušenosti s dodržováním závazků týkajících se dodávek. Pochopte faktory, které ovlivňují dobu realizace (dostupnost stroje, složitost následného zpracování).
Hodnocení potenciálních dodavatelů: Klíčové otázky, které je třeba položit
- Můžete uvést příklady podobných tepelných štítů nebo složitých automobilových komponent, které jste vytiskli pomocí AlSi10Mg / IN625?
- Jaký je váš postup pro zajištění kvality a sledovatelnosti materiálu? Odkud získáváte prášky? (Odpověď společnosti Met3dp’zde zdůrazňuje jejich vertikální integraci).
- Jakou podporu DfAM můžete nabídnout pro optimalizaci konstrukce tepelného štítu?
- Jaké jsou vaše standardní rozměrové tolerance a dosažitelné povrchové úpravy pro tyto materiály ve stavu po zabudování?
- Popište své vlastní možnosti následného zpracování (tepelné zpracování, obrábění, dokončovací práce).
- Jaké máte certifikáty kvality (ISO 9001, IATF 16949, AS9100)? Dokážete v případě potřeby vyhovět požadavkům PPAP?
- Jaká je obvyklá doba realizace prototypu tepelného štítu této složitosti? Pro sérii X kusů?
- Jak řídíte kontrolu kvality během celého výrobního procesu? Jaké kontrolní metody používáte?
Proč uvažovat o Met3dp?
Společnost Met3dp vyniká jako potenciální partner tím, že splňuje mnoho z těchto kritických kritérií výběru:
- Vertikální integrace: Jako výrobce pokročilých tiskáren AM pro kovy a vysoce kvalitních sférických kovových prášků (včetně AlSi10Mg, IN625 a inovativních slitin) nabízí společnost Met3dp bezkonkurenční kontrolu nad celým procesním řetězcem.
- Materiálové znalosti: Hluboké znalosti práškové metalurgie a chování materiálu při AM zajišťují optimální výsledky.
- Pokročilé technologie: Využití špičkových tiskových zařízení a technik výroby prášku (plynová atomizace, PREP).
- Komplexní řešení: Nabídka tiskáren, prášků a služeb vývoje aplikací poskytuje komplexní přístup.
- Zakázkové chirurgické nástroje Zkušenosti s náročnými průmyslovými odvětvími, jako je letecký, lékařský a automobilový průmysl.
Výběr správného Dodavatel AM je strategické rozhodnutí. Pečlivým vyhodnocením potenciálních partnerů podle těchto kritérií mohou automobilové společnosti navázat pevné vztahy, které jim umožní úspěšně využít sílu kovového 3D tisku pro inovativní a vysoce výkonná řešení tepelných štítů.
Nákladové faktory a dodací lhůty pro 3D tepelné štíty na zakázku
I když jsou technické výhody 3D tisku kovů pro tepelné štíty automobilů přesvědčivé, pochopení souvisejících náklady na 3D tisk kovů v automobilovém průmyslu faktorů a typických výrobních lhůt je zásadní pro plánování projektu, sestavování rozpočtu a porovnávání AM s tradičními metodami. Konečná cena a harmonogram dodání tepelného štítu vytištěného 3D tiskem na zakázku závisí na složité souhře volby designu, výběru materiálu, kroků zpracování a objemu zakázky.
Klíčové hnací síly nákladů:
- Typ a objem materiálu:
- Výběr materiálu: To je často hlavní příčinou nákladů. Vysoce výkonné niklové superslitiny, jako např IN625 jsou v přepočtu na kilogram výrazně dražší než hliníkové slitiny, např AlSi 10Mg, vzhledem k nákladům na suroviny a náročnosti zpracování.
- Část Objem/hmotnost: Samotné množství spotřebovaného kovového prášku přímo ovlivňuje náklady. Větší a hustší díly jsou přirozeně dražší. Techniky DfAM, jako je optimalizace topologie a mřížkové struktury, jsou klíčem k minimalizaci spotřeby materiálu při zachování funkčnosti.
- Čas stroje (čas sestavení):
- Velikost dílu (ohraničující rámeček): Větší díly zabírají stavební komoru po delší dobu. Vliv má zejména celková výška dílu, protože tisk probíhá po jednotlivých vrstvách.
- Část Složitost: Složité geometrie mohou vyžadovat nižší rychlost tisku nebo složitější strategie skenování, což prodlužuje strojní čas.
- Podpůrné struktury: Objem potřebného podpůrného materiálu zvyšuje spotřebu materiálu i dobu sestavení, protože tyto konstrukce je třeba také vytisknout. Optimalizovaná orientace a DfAM pomáhají snížit potřebu podpůrných materiálů.
- Hnízdění/dávkování: Tisk více dílů současně v jednom sestavení (nesting) může výrazně snížit efektivní časové náklady stroje na jeden díl díky maximálnímu využití stroje. To je klíčové pro dosažení lepší ekonomiky při velkoobchodní služby 3D tisku nebo malosériová výroba.
- Práce a nastavení:
- Příprava souborů: Příprava souboru CAD pro tisk (orientace, generování podkladů, řezání) vyžaduje kvalifikovanou práci.
- Nastavení/rozborka stroje: Vkládání prášku, nastavení sestavy a následné vyjmutí dílů a čištění stroje vyžadují pracovní čas. Tyto náklady na seřízení se amortizují na počet dílů v sestavě; proto jsou náklady na seřízení jednotlivých prototypů vyšší než náklady na sériovou výrobu.
- Práce po zpracování: To může představovat významnou složku nákladů. Ruční odstranění podpěr, nastavení a obsluha obrábění, dokončovací práce a kontrola vyžadují čas kvalifikovaných techniků. Tyto náklady přímo ovlivňuje složitost dílu a požadavky na jeho následné zpracování.
- Intenzita následného zpracování:
- Tepelné zpracování: Je nutná prakticky pro všechny kovové díly AM, náklady závisí na době cyklu pece, požadavcích na atmosféru (vakuum/inertní plyn je dražší) a velikosti dávky.
- Odstranění podpory: Složité nebo nedostupné podpěry zvyšují náklady na pracovní sílu.
- CNC obrábění: Pokud jsou u některých prvků nutné přísné tolerance nebo specifické povrchové úpravy, zvyšuje obrábění značné náklady na strojní čas, nástroje, programování a práci. Obrábění IN625 je výrazně dražší než obrábění AlSi10Mg.
- Povrchová úprava: Náklady se značně liší v závislosti na metodě (jednoduché tryskání vs. vícestupňové leštění nebo elektrolytické leštění) a požadované úrovni kvality.
- Povlaky: Aplikace TBC nebo jiných povlaků zvyšuje náklady na materiál a proces.
- Zajištění kvality a kontrola:
- Základní kontrola kvality: Obvykle jsou součástí standardní rozměrové kontroly a vizuální kontrola.
- Pokročilá kontrola kvality: Vyžadování protokolů ze souřadnicových měřicích strojů, porovnání 3D skenování, nedestruktivního zkoušení (např. CT skenování pro zjištění vnitřní pórovitosti) nebo zkoušení vlastností materiálu (tahové zkoušky na svědeckých kuponech) zvyšuje náklady, ale může být nezbytné pro kritické aplikace. Náklady vznikají také s dokumentací PPAP.
- Objednávkové množství:
- Prototypy: Jednotlivé díly nebo velmi malé série mají nejvyšší náklady na jeden díl, protože náklady na seřízení se neamortizují.
- Nízký až střední objem: S rostoucím množstvím (např. desítky až stovky kusů) se náklady na jeden díl snižují díky úsporám z rozsahu při přípravě, sériovém zpracování (tisk, tepelné zpracování, dokončovací práce) a možnosti vyjednávání velkoobchodní služby 3D tisku sazby.
- Vysoký objem: U velmi vysokých objemů (tisíce nebo desetitisíce kusů) jsou pro jednodušší konstrukce tepelných štítů obvykle cenově výhodnější tradiční metody, jako je lisování. U velmi složitých nebo přizpůsobených štítů však může AM zůstat konkurenceschopná i při vyšších objemech, než se původně očekávalo.
Faktory doby realizace:
Doba realizace se vztahuje k celkové době od zadání objednávky do dodání dílu. Pro doba výroby tepelného štítu při použití kovu AM jsou typickými faktory:
- Cenová nabídka a kontrola návrhu: Počáteční komunikace, kontrola spisu, konzultace s DfAM (pokud je potřeba) a tvorba nabídky zaberou určitý čas (obvykle několik dní).
- Čas fronty / dostupnost stroje: Servisní kanceláře fungují podle jízdních řádů. Vaše úloha musí počkat na volný stroj vhodně nakonfigurovaný pro váš materiál. V závislosti na poptávce to může být několik dní až týdnů.
- Doba tisku: Skutečná doba, kterou díl stráví tiskem ve stroji. Může se pohybovat od hodin u malých dílů až po několik dní u velkých, složitých dílů nebo celých konstrukčních desek.
- Doba chlazení: Díly musí před manipulací vychladnout ve stroji nebo po vyjmutí.
- Následné zpracování: To často představuje významnou část celkové doby realizace.
- Cykly tepelného zpracování mohou trvat 8-24 hodin nebo déle (včetně náběhu/ochlazení).
- Odstranění podpory a základní dokončovací práce mohou v závislosti na složitosti trvat hodiny až dny.
- CNC obrábění přidává značný čas na programování, seřizování a obráběcí cykly (hodiny/dny).
- Externě zajišťované kroky (např. specializované nátěry, HIP) prodlužují dobu přepravy a dobu realizace externího dodavatele.
- Kontrola kvality: Potřebný čas závisí na úrovni potřebné kontroly.
- Doprava: Doba přepravy do vašeho zařízení.
Typické odhady doby realizace:
- Prototypy: Často 5-15 pracovních dnů, ve velké míře v závislosti na složitosti, následném zpracování a aktuálních strojových frontách. Zrychlené služby mohou být k dispozici za příplatek.
- Malosériová výroba (např. 10-100 kusů): Obvykle 3-6 týdnů, což umožňuje dávkové zpracování a efektivitu plánování.
- Vyšší objemy: Doba realizace se zvyšuje s množstvím a složitostí, což vyžaduje pečlivé plánování a případně vyhrazení strojního času.
Strategie zkrácení dodací lhůty:
- DfAM: Zjednodušení návrhu a minimalizace podpěr zkracuje dobu tisku a následného zpracování.
- Čiré specifikace: Předložením úplných a přesných požadavků předem se vyhnete zpoždění.
- Komunikace s partnery: Úzká spolupráce s pohotovým poskytovatelem služeb, jako je Met3dp, pomáhá tento proces zefektivnit.
- Realistická očekávání: Uvědomte si, že proces AM s kovem, zejména s rozsáhlým následným zpracováním, není pro složité díly typicky procesem na jednu noc.
Pochopením této dynamiky nákladů a doby realizace mohou inženýři a manažeři nákupu činit informovaná rozhodnutí o využití AM kovů pro tepelné štíty v automobilovém průmyslu, a to při porovnání technických výhod s rozpočtovými a časovými omezeními.
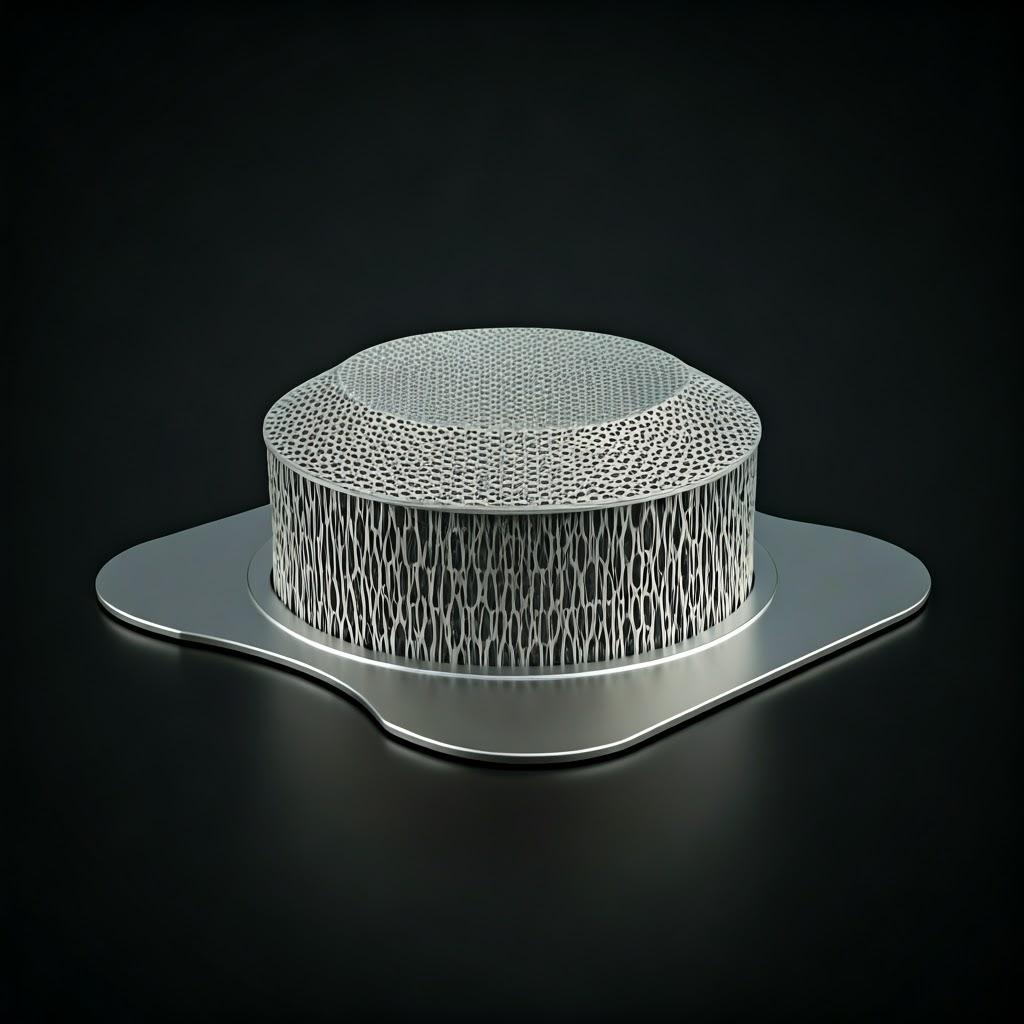
Často kladené otázky (FAQ) o 3D tištěných tepelných štítech pro automobilový průmysl
S tím, jak se v automobilovém průmyslu rozšiřuje aditivní výroba kovů, mají konstruktéři a designéři často konkrétní dotazy ohledně jejího použití pro komponenty, jako jsou tepelné štíty. Zde jsou odpovědi na některé časté dotazy:
1. Jak odolné jsou 3D tištěné kovové tepelné štíty ve srovnání s tradičními lisovanými?
- Odpověď: Trvanlivost tepelného štítu vytištěného na 3D tiskárně je vynikající a často lepší než u tradičních lisovaných dílů, pokud je zvolen správný materiál a díl je správně navržen a zpracován.
- Vlastnosti materiálu: Kovový AM využívá robustní konstrukční materiály, jako je AlSi10Mg, a vysoce výkonné slitiny, jako je IN625. Při tisku s vysokou hustotou (>99,5 %) a správném tepelném zpracování vykazují tyto materiály mechanické vlastnosti (pevnost, odolnost proti únavě, odolnost proti tečení) srovnatelné nebo lepší než jejich protějšky zhotovené z kovu nebo odlitky, zejména při zvýšených teplotách (v případě IN625). Tepelná odolnost IN625 je výjimečný.
- Optimalizace designu: Technologie AM umožňuje vytvářet konstrukce optimalizované pro dlouhou životnost. Funkce, jako jsou integrovaná výztužná žebra, optimalizované tloušťky stěn a eliminace svarů nebo spojovacích prvků (potenciální místa poruch u lisovaných sestav), mohou zvýšit integritu konstrukce a únavovou životnost.
- Potenciální problémy: Stejně jako u každého výrobního procesu mohou mít potenciální vady (např. pórovitost, zbytkové napětí, pokud nejsou správně řízeny) vliv na trvanlivost. To podtrhuje důležitost výběru dodavatele kvality s důkladnou kontrolou procesu a odbornými znalostmi v oblasti následného zpracování, jako je Met3dp.
- Srovnání: Dobře navržený a vyrobený tepelný štít IN625 vytištěný na 3D tiskárně, který pracuje v prostředí s vysokými teplotami (např. v blízkosti turbodmychadla), obvykle nabízí výrazně lepší dlouhodobou životnost a odolnost proti tepelné únavě než srovnatelný štít vyražený z konvenční oceli nebo hliníkové slitiny. Štít AlSi10Mg, používaný v rámci svých teplotních limitů, nabídne vynikající odolnost srovnatelnou s tradičními hliníkovými štíty, ale s větší konstrukční flexibilitou a potenciálně nižší hmotností.
2. Je kovový 3D tisk pro velkosériovou výrobu tepelných štítů rentabilní?
- Odpověď: Obecně platí, že pro velmi vysoké objemy výroba (desítky až stovky tisíc kusů ročně) jednoduchý konstrukce tepelného štítu, zůstává tradiční lisování nákladově efektivnější díky nižším nákladům na jeden díl po amortizaci nástrojů. Nicméně porovnání nákladů na tepelný štít AM vs. tradiční je diferencovaný:
- Silné stránky AM: Technologie AM je vysoce nákladově efektivní pro:
- Prototypování a vývoj: Eliminuje náklady na nástroje, což umožňuje rychlou iteraci při nižších celkových nákladech na vývoj.
- Výroba v malém až středním objemu: Pro objemy, kde jsou náklady na lisování nástrojů neúměrně vysoké (např. specifická vozidla, díly pro trh s náhradními díly, počáteční náběh výroby).
- Vysoká složitost: Pokud je konstrukce tepelného štítu velmi složitá (konformní tvary, vnitřní prvky, integrované prvky), může lisování vyžadovat více nástrojů a montážních kroků, čímž se AM může stát nákladově konkurenceschopným i při středních objemech.
- Přizpůsobení: U štítů na zakázku nebo vysoce přizpůsobených (např. v motoristickém sportu) je AM často jedinou schůdnou možností.
- Na vyžádání / Náhradní díly: Tisk dílů podle potřeby zamezuje nákladům na skladování a je ideální pro výměnu starších komponent.
- Bod zlomu: Přesný objem, při kterém se lisování stává levnějším, závisí do značné míry na složitosti dílu, materiálu a nákladech na nástroje. U složitých štítů IN625 může AM zůstat konkurenceschopná při překvapivě vysokých objemech ve srovnání s vícestupňovým tvářením a výrobou stejného designu.
- Celkové náklady na vlastnictví: Zvažte i další faktory než jen cenu za díl: zkrácení doby montáže (konsolidace dílů), nižší hmotnost (úspora paliva), potenciálně delší životnost (lepší materiály/konstrukce).
- Silné stránky AM: Technologie AM je vysoce nákladově efektivní pro:
3. Jaká je typická teplotní odolnost tepelných štítů vyrobených 3D tiskem z AlSi10Mg a IN625?
- Odpověď: Teplotní odolnost je klíčovým rozlišovacím prvkem:
- AlSi10Mg: Tato hliníková slitina má mírná teplotní odolnost. Jeho mechanické vlastnosti se výrazně zhoršují nad přibližně 200-250°C (392-482°F). Je vhodný pro tepelné štíty umístěné dále od extrémních zdrojů tepla, jako jsou spodní části výfuku, součásti podvozku vzdálené od katalyzátoru nebo stínění elektroniky před mírným teplem v motorovém prostoru.
- IN625 (Inconel® 625): Tato niklová superslitina nabízí vynikající pevnost při vysokých teplotách a odolnost proti oxidaci. Udržuje si užitečnou pevnost až do 800-900°C (1472-1652°F) nebo krátkodobě i vyšší, v závislosti na podmínkách zatížení. To z něj činí ideální nejlepší materiál pro tepelný štít výfuku aplikace v blízkosti rozdělovačů, katalyzátorů, turbodmychadel a vysoce výkonných výfukových systémů, kde jsou extrémní teploty.
4. Lze přímo na tepelný štít vytisknout složité integrované montážní prvky?
- Odpověď: Rozhodně. To je jedna z klíčových výhod kovového 3D tisku tepelných štítů. Prvky, jako jsou montážní šrouby, závitové otvory (často vytištěné s mírně zmenšenými rozměry a následně opatřené závitem), polohovací čepy, držáky a svorky, lze navrhnout přímo do modelu tepelného štítu a vytisknout jako jediný monolitický díl.
- Výhody:
- Konsolidace částí: Snižuje počet jednotlivých komponent, čímž zjednodušuje montáž a inventarizaci.
- Zkrácení doby montáže/nákladů: Eliminuje svařování, nýtování nebo upevňování.
- Vylepšená pevnost/spolehlivost: Integrované prvky mohou být pevnější než připojené, čímž se eliminují potenciální místa poruch v místech spojů.
- Flexibilita designu: Umožňuje optimalizovat umístění a geometrii montážních prvků bez omezení tradiční výroby.
- Úvahy: Zásady DfAM by měly být použity k zajištění toho, aby tyto prvky byly tisknutelné (např. v případě potřeby podepřené, vhodné minimální rozměry prvků) a funkční (např. návrh dostatečného množství materiálu kolem otvorů se závitem). Pro přesná rozhraní může být nutné následné zpracování, jako je závitování nebo vystružování.
- Výhody:
Závěr: Budoucnost tepelné ochrany automobilů je aditivní
Cesta spletitostí 3D tištěné tepelné štíty pro vozidla odhaluje přesvědčivý příběh: aditivní výroba kovů není pouhou alternativou, ale transformační silou, která mění přístup k tepelnému managementu automobilů. Tím, že se vymaňuje z geometrických omezení tradičního lisování a tváření, umožňuje AM zpracování kovů inženýrům navrhovat a vyrábět pokročilá řešení tepelných štítů které jsou lehčí, složitější, vysoce přizpůsobené a často vykazují vynikající výkon, zejména v náročných vysokoteplotních prostředích.
Prozkoumali jsme kritické funkce tepelných štítů v různých automobilových aplikacích, od zmírnění tepla z výfuku po ochranu citlivých baterií elektromobilů. Výrazné výhody použití AM kovů - bezkonkurenční volnost designu umožňující konformní tvary a integrované prvky, významný potenciál odlehčení díky optimalizaci topologie a mřížkovým strukturám, rychlé prototypování urychlující vývojové cykly a možnost výroby na zakázku a přizpůsobení - představují jasnou nabídku hodnoty pro Automobilové díly OEM dodavatelé, specialisté na náhradní díly a týmy motoristického sportu.
Strategický výběr materiálů, jako je lehký AlSi 10Mg pro mírné teplotní zóny a robustní, žáruvzdorný IN625 pro extrémní prostředí ve spojení s vysoce kvalitními prášky, jako jsou prášky vyráběné společností Met3dp, tvoří základ spolehlivého výkonu. Pochopení a uplatnění principů DfAM, rozpoznání dosažitelných tolerancí a povrchových úprav a provedení nezbytných kroků následného zpracování - to vše jsou klíčové prvky pro využití plného potenciálu této technologie. Ačkoli existují problémy, partnerství se zkušenou a vertikálně integrovanou firmou je velmi důležité poskytovatel služeb 3D tisku kovů jako je Met3dp, který má hluboké odborné znalosti od prášku až po hotový díl, účinně snižuje rizika a zajišťuje úspěšné výsledky.
Schopnost rychle a efektivně vytvářet optimalizované komponenty tepelného managementu specifické pro danou aplikaci dokonale zapadá do trajektorie automobilového průmyslu směrem ke složitějším pohonným jednotkám, elektrifikaci, vyšším nárokům na výkon a rostoucí personalizaci. 3D tisk kovů je klíčovým faktorem umožňujícím digitální výroba v automobilovém průmyslu strategie, které nabízejí dříve nedosažitelnou agilitu a inovace.
S výhledem do budoucnosti bude role aditivní výroby při výrobě kritických součástí, jako jsou tepelné štíty, nadále růst. Nabízí cestu ke zvýšení účinnosti vozidel, zlepšení bezpečnosti, rychlejším inovacím a udržitelnějším výrobním postupům díky optimalizaci materiálů a snížení množství odpadu.
Jste připraveni prozkoumat, jak může 3D tisk z kovu změnit vaše problémy s tepelným managementem v automobilovém průmyslu?
Společnost Met3dp Technology Co., LTD, se svými špičkovými tiskárnami SEBM, pokročilými systémy plynové atomizace a výroby prášků PREP a rozsáhlým portfoliem vysoce výkonných kovových prášků, včetně AlSi10Mg a IN625, je ideálním řešením Met3dp partner pro aditivní výrobu. Náš tým má desítky let společných zkušeností, které vám pomohou od konzultace návrhu až po finální výrobu dílů.
Kontaktujte Met3dp ještě dnes a prodiskutovat s vámi vaše konkrétní požadavky na tepelný štít nebo jiné dodavatel automobilových komponentů na zakázku potřeby. Pomůžeme vám využít sílu aditivní výroby k urychlení vašich inovací a k budoucímu zvýšení výkonu a efektivity vozidel. Navštivte naše webové stránky nebo se obraťte na náš tým odborníků a začněte rozhovor.
Sdílet na
MET3DP Technology Co., LTD je předním poskytovatelem řešení aditivní výroby se sídlem v Qingdao v Číně. Naše společnost se specializuje na zařízení pro 3D tisk a vysoce výkonné kovové prášky pro průmyslové aplikace.
Dotaz k získání nejlepší ceny a přizpůsobeného řešení pro vaše podnikání!
Související články
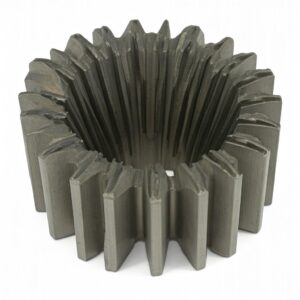
Vysoce výkonné segmenty lopatek trysek: Revoluce v účinnosti turbín díky 3D tisku z kovu
Přečtěte si více "O Met3DP
Nedávná aktualizace
Náš produkt
KONTAKTUJTE NÁS
Nějaké otázky? Pošlete nám zprávu hned teď! Po obdržení vaší zprávy obsloužíme vaši žádost s celým týmem.
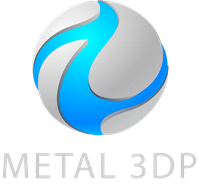
Kovové prášky pro 3D tisk a aditivní výrobu