Lehké ramena brzdových pedálů pomocí aditivní výroby kovů
Obsah
Úvod: Revoluce v automobilových komponentech díky technologii AM pro kovy
Ve složitém systému, který tvoří moderní vozidlo, je jen málo součástí tak zásadně důležitých pro bezpečnost a ovládání řidiče jako ramena brzdového pedálu. Je to přímé rozhraní mezi pokyny řidiče a brzdovým systémem vozidla, které převádí tlak nohou na hydraulickou sílu, jež bezpečně zastaví tuny kovu. Po desetiletí se tyto součásti spolehlivě vyráběly tradičními metodami, jako je odlévání nebo kování, což často vedlo k výrobě robustních, ale poměrně těžkých dílů. Automobilový průmysl však prochází hlubokou proměnou, která je poháněna dvojím imperativem - elektrifikací a neustálým zvyšováním výkonu. V této nové éře, na každém gramu záleží. Odlehčování již není jen záležitostí špičkových závodních týmů, ale základním principem konstrukce, který je nezbytný pro prodloužení dojezdu elektromobilů, zlepšení jízdní dynamiky, snížení emisí a zvýšení celkové účinnosti.
Tato snaha o snížení hmotnosti v celém odvětví otevřela dveře převratným technologiím, které mohou změnit koncepci konstrukce a výroby součástí. Vstupte na výroba aditiv kovů (AM), běžně známý jako metal 3D tisk. Tato technologie rychle překračuje rámec prototypování a přechází do oblasti funkčních dílů pro konečné použití, přičemž nabízí nebývalou volnost návrhu a možnost vytvářet vysoce optimalizované, lehké struktury, které dříve nebylo možné vyrobit. Pro součásti, jako jsou ramena brzdových pedálů, představuje technologie AM transformační příležitost. Umožňuje konstruktérům vymanit se z omezení tradiční výroby a vytvářet organicky tvarované, topologicky optimalizované pedály, které zachovávají nebo dokonce překračují požadavky na pevnost a tuhost a zároveň výrazně snižují hmotnost. Tento posun má hluboké důsledky nejen pro výkonnost vozidel, ale také pro celý automobilový průmysl dodavatelský řetězec, která nabízí automobiloví výrobci OEM a Dodavatelé úrovně 1 nové úrovně agility a možností přizpůsobení. Když se ponoříme hlouběji, prozkoumáme, jak může využití pokročilých kovových prášků a tiskových procesů odemknout novou generaci součástí automobilových brzdových systémů.
Aplikace & Případy použití: Kde vynikají lehké brzdové pedály
Ačkoli koncept 3D tištěného kovového brzdového pedálu může znít futuristicky, jeho využití má hmatatelné technické výhody, které řeší konkrétní potřeby v automobilovém průmyslu. Díky výhodám odlehčení a optimalizace konstrukce, které nabízí technologie AM z kovu, jsou tyto komponenty obzvláště cenné v několika klíčových oblastech:
- Vysoce výkonné sportovní vozy a supersporty: U vozidel, u nichž je nejdůležitější výkon, je minimalizace neodpružené a celkové hmotnosti zásadní pro vynikající ovladatelnost, zrychlení a brzdění. Lehký brzdový pedál přispívá k citlivější odezvě a umožňuje konstruktérům přesněji vyladit dynamiku vozidla. Výrobci, kteří uspokojují potřeby tohoto exkluzivního trhu, často vyžadují vysoce technicky náročná řešení na míru, u nichž výhody AM převažují nad potenciálně vyššími náklady na jeden díl ve srovnání s masově prodávanými vozidly.
- Elektrická vozidla (EV): Úzkost z dojezdu zůstává významným faktorem při zavádění elektromobilů. Snížení celkové hmotnosti vozidla je jedním z nejúčinnějších způsobů, jak maximalizovat dojezd na baterie. Ačkoli se může zdát, že úspora hmotnosti jednoho brzdového pedálu je izolovaně malá, přispívá ke kumulativnímu úsilí o snížení hmotnosti stovek komponentů. Volnost konstrukce navíc umožňuje potenciální integraci prvků nebo senzorů specifických pro rekuperační brzdové systémy. Zadávání zakázek v automobilovém průmyslu manažeři pracující na platformách pro elektromobily neustále hledají inovativní způsoby, jak ušetřit kilogramy.
- Motorsport &; Závodění: V ultrakonkurenčním světě závodů se týmy řídí přísnými předpisy, ale neustále usilují o marginální zisky. Technologie Metal AM umožňuje rychlý vývoj a výrobu vysoce optimalizovaných brzdových pedálů na míru konkrétním vozům nebo jezdcům. Schopnost rychlé iterace návrhů na základě údajů z trati nebo zpětné vazby od řidičů je neocenitelná a vynikající poměr pevnosti a hmotnosti je rozhodujícím faktorem pro odlišení výkonu.
- Pokročilé prototypování &; Niche Vehicles: Než se výrobci automobilů odhodlají k nákladnému odlévání nebo kování, mohou využít technologii AM pro výrobu funkčních prototypů nových konstrukcí brzdových pedálů. To umožňuje testování a ověřování v reálném prostředí mnohem dříve ve vývojovém cyklu, což snižuje rizika a zrychluje dobu uvedení na trh. Je také ideální pro nízkoobjemová vozidla, zakázkové stavby nebo renovace klasických automobilů, kde by vytvoření tradičních nástrojů bylo neúměrně nákladné.
- Optimalizace pocitu z pedálů a ergonomie: Kromě čistého odlehčení umožňuje konstrukční svoboda inženýrům experimentovat s konstrukcemi, které zvyšují tuhost pedálů a poskytují řidiči přímější a jistější pocit, což přispívá k vnímání kvality a sportovního charakteru vozidla.
V podstatě všude tam, kde je hmotnost vozidla kritickým konstrukčním parametrem, kde je zásadní rychlost vývoje nebo kde jedinečné konstrukční požadavky vylučují tradiční výrobu, nabízejí lehké kovové brzdové pedály AM přesvědčivé řešení pro progresivně smýšlející automobilové inženýry a dodavatelé komponentů.
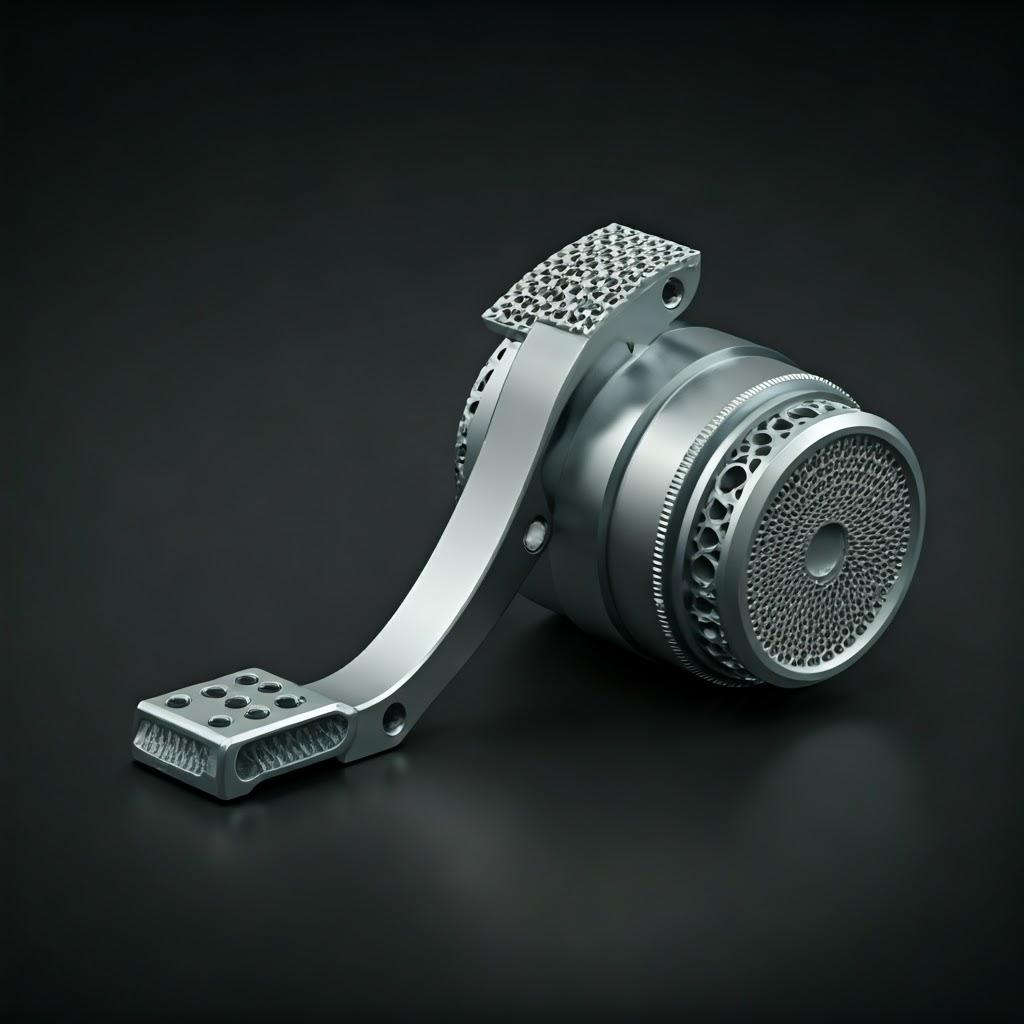
Proč 3D tisk z kovu pro ramena brzdových pedálů? Hlavní výhody
Volba aditivní výroby kovů namísto zavedených metod, jako je odlévání, kování nebo obrábění, u bezpečnostně důležitých součástí, jako je rameno brzdového pedálu, vyžaduje přesvědčivé zdůvodnění. Výhody, které nabízí AM, zejména laserová fúze v práškovém loži (L-PBF), jsou významné a řeší mnoho výzev moderního automobilového průmyslu:
- Bezkonkurenční volnost návrhu a optimalizace topologie: To je pravděpodobně nejvýznamnější přínos. Tradiční metody jsou ze své podstaty omezeny požadavky na nástroje (úhly ponoru pro odlévání, tvary zápustek pro kování, přístup k nástrojům pro obrábění). AM vytváří díly vrstvu po vrstvě, což konstruktérům umožňuje:
- Implementace optimalizace topologie: Pomocí softwaru analyzujte průběh zatížení a odstraňte materiál z nekritických oblastí, čímž získáte organické, skeletové konstrukce, které jsou optimálně pevné pouze tam, kde je to nutné. To může vést ke snížení hmotnosti o 30-60 % a více ve srovnání s tradičními konstrukcemi při zachování nebo dokonce zvýšení tuhosti.
- Vytváření složitých vnitřních geometrií: Začlenit vnitřní mřížkové struktury pro další snížení hmotnosti a vyladění tuhosti nebo v případě potřeby navrhnout vnitřní kanály pro senzory nebo jiné funkce - funkce, kterých nelze dosáhnout běžnými technikami.
- Realizace biomimetických návrhů: Inspirujte se přírodními strukturami (například kostmi), které se vyvinuly pro maximální efektivitu.
- Výrazné snížení hmotnosti: Jak bylo zdůrazněno, schopnost optimalizovat geometrii se přímo promítá do výrazných úspor hmotnosti. To má vliv na:
- Výkon vozidla: Nižší setrvačnost, lepší reakce na zrychlení/brzdění.
- Palivo/energetická účinnost: Snížení celkové hmotnosti vozidla přímo přispívá ke snížení spotřeby paliva nebo prodloužení dojezdu elektromobilu.
- Úspora materiálu: Použití pouze nezbytného materiálu dlouhodobě snižuje množství odpadu a náklady na suroviny, zejména u cenných slitin.
- Konsolidace částí: Složité sestavy, které jsou často vyžadovány při tradiční výrobě (např. rameno pedálu přivařené nebo přišroubované k montážní konzole), lze potenciálně přepracovat a vytisknout jako jediný monolitický díl. To přináší několik výhod:
- Zkrácení doby montáže & Náklady: Menší počet komponentů znamená jednodušší a rychlejší montážní linky.
- Vylepšená strukturální integrita: Eliminuje potenciální místa poruch ve spojích nebo svárech.
- Zjednodušený dodavatelský řetězec: Méně jednotlivých čísel dílů, které je třeba spravovat, sledovat a hledat velkoobchodní nákupčí automobilového průmyslu a logistické týmy.
- Rapid Prototyping, Iteration & Rychlost vývoje: Cesta od modelu CAD k funkčnímu kovovému prototypu se může díky AM výrazně zkrátit.
- Eliminace nástrojů: AM nevyžaduje nákladné a časově náročné nástroje (formy, zápustky). Změny designu lze provádět digitálně a rychle je vytisknout znovu.
- Rychlejší ověřování: Funkční prototypy lze vyrobit během několika dnů nebo týdnů, což umožňuje rychlejší testovací cykly (fit, forma, funkce, dokonce i omezené testování na plošině). Tím se zrychluje celková doba vývoje vozidla.
- Flexibilita dodavatelského řetězce a výroba na vyžádání:
- Snížené zásoby: Díly lze tisknout podle potřeby, čímž se minimalizují náklady na skladování a rizika zastarávání, což je klíčová výhoda pro řízení dodavatel vztahy a úroveň zásob.
- Distribuovaná výroba: Umožňuje výrobu blíže k místu montáže, což může snížit náklady na přepravu a dodací lhůty.
- Přizpůsobení: Usnadňuje výrobu variant nebo vlastních návrhů bez větších investic do přestavby.
Zatímco tradiční metody jsou i nadále vhodné pro velkoobjemové standardní komponenty citlivé na náklady, AM zpracování kovů představuje výkonnou alternativu pro aplikace vyžadující odlehčení, složité geometrie, rychlost a přizpůsobení, a mění tak způsob, jakým inženýři a odborníci pracují specialisté na veřejné zakázky přístup k navrhování a získávání komponentů.
Zaměření materiálu: AlSi10Mg a A7075 pro automobilový průmysl
Úspěch každé kovové součásti AM závisí především na výběru správného materiálu. Pro lehké a vysoce výkonné automobilové aplikace, jako jsou ramena brzdových pedálů, jsou často hlavními kandidáty hliníkové slitiny díky své přirozené nízké hustotě a dobrým mechanickým vlastnostem. V této souvislosti vynikají dvě slitiny pro zpracování L-PBF: AlSi 10Mg a A7075. Výběr mezi nimi závisí do značné míry na konkrétních požadavcích na výkon, provozním prostředí a nákladových cílech aplikace.
AlSi10Mg: Jedná se o jednu z nejběžnějších a nejpoužívanějších hliníkových slitin používaných v aditivní výrobě. Je to v podstatě slitina odlitků upravená pro procesy L-PBF.
- Klíčové vlastnosti:
- Dobrý poměr pevnosti a hmotnosti: Nabízí dobré mechanické vlastnosti vhodné pro mnoho konstrukčních aplikací.
- Vynikající tisknutelnost: Relativně snadné zpracování pomocí L-PBF, s dobře zavedenými parametry vedoucími k hustým dílům.
- Dobré tepelné vlastnosti: Účinně odvádí teplo.
- Dobrá odolnost proti korozi: Dobře funguje v typických automobilových prostředích.
- Svařitelnost: V případě potřeby lze svařovat, ačkoli konsolidace dílů tuto potřebu často minimalizuje.
- Vhodnost pro brzdové pedály: AlSi10Mg představuje robustní a cenově výhodné řešení pro mnoho lehkých konstrukcí brzdových pedálů, zejména tam, kde není primárním faktorem extrémní zatížení nebo kde nahrazuje standardní hliníkový odlitek. Umožňuje výraznou úsporu hmotnosti díky optimalizaci topologie ve srovnání s tradičními konstrukcemi.
- Kvalita prášku Met3dp: Dosažení požadovaných mechanických vlastností vyžaduje kvalitní vstupní materiál. Společnosti jako např Met3dp se specializují na výrobu kovové prášky pomocí pokročilých technik rozprašování plynu. To zajišťuje, že jejich prášek AlSi10Mg vykazuje vysokou sféricitu, dobrou tekutost a kontrolovanou distribuci velikosti částic - což jsou všechno rozhodující faktory pro dosažení hustých, spolehlivých dílů s předvídatelnými vlastnostmi v náročných podmínkách 3D tisk z kovu procesy.
A7075 (hliníková slitina 7075): Jedná se o vysoce pevný hliník legovaný zinkem, který se hojně používá v letectví a ve vysoce výkonných aplikacích. Tradičně je k dispozici jako kovaný výrobek (plechy, desky, výlisky), jeho přizpůsobení pro AM představuje výzvu, ale nabízí významné výkonnostní výhody.
- Klíčové vlastnosti:
- Velmi vysoká pevnost: Jedna z nejpevnějších dostupných hliníkových slitin, která se pevností blíží některým ocelím, ale má zhruba třetinovou hustotu.
- Vynikající únavová pevnost: To je zásadní pro součásti vystavené cyklickému zatížení, jako je brzdový pedál.
- Dobrá lomová houževnatost (při správném tepelném zpracování).
- Výzvy & Řešení v AM: A7075 může být náchylná k praskání za tepla během rychlých cyklů tání a tuhnutí L-PBF. Úspěšný tisk vyžaduje pečlivou optimalizaci parametrů (výkon laseru, rychlost skenování, šrafovací vzory), případně upravené složení slitiny speciálně pro AM a pečlivé tepelné zpracování po procesu (obvykle temperace T6), aby se dosáhlo optimálních vlastností. Zásadní význam má spolupráce s poskytovatelem služeb AM, který má zkušenosti s vysoce pevnými hliníkovými slitinami.
- Vhodnost pro brzdové pedály: A7075 je preferovanou volbou v případech, kdy je rozhodující maximální pevnost a odolnost proti únavě, například u vysoce výkonných závodních aplikací nebo u vozidel s extrémními požadavky na životnost. Vyšší náklady na materiál a zpracování jsou ospravedlněny vynikajícími vlastnostmi a potenciálem ještě větší úspory hmotnosti díky přirozené pevnosti materiálu.
Srovnání výběru materiálu:
Vlastnosti | AlSi 10Mg | A7075 (zpracováno AM) | Význam pro rameno brzdového pedálu |
---|---|---|---|
Primární legování | Křemík (Si), hořčík (Mg) | Zinek (Zn), Hořčík (Mg), Měď (Cu) | Ovlivňuje mechanické vlastnosti jádra. |
Typická mez kluzu (tepelně zpracovaná) | ~230-280 MPa | ~450-520 MPa | Odolnost proti trvalé deformaci při zatížení. Kritické. |
Typická pevnost v tahu (tepelně zpracovaná) | ~330-430 MPa | ~500-580 MPa | Maximální napětí před zlomením. Kritické pro bezpečnostní rezervu. |
Hustota | ~2,67 g/cm³ | ~2,81 g/cm³ | Klíč k odlehčení. Obě jsou vynikající. |
Možnost tisku (L-PBF) | Obecně dobré | Náročnější (vyžaduje odborné znalosti) | Ovlivňuje spolehlivost procesu, možnost vzniku závad a náklady. |
Únavová pevnost | Mírný | Velmi dobře | Odolnost proti porušení při cyklickém zatížení. Velmi důležité. |
Odolnost proti korozi | Dobrý | Středně těžká (může vyžadovat ochranu povrchu) | Důležité pro odolnost v automobilovém prostředí. |
Relativní náklady | Dolní | Vyšší | Významný faktor pro zadávání veřejných zakázek a celkový rozpočet projektu. |
Ideální případ použití | Obecné odlehčení, EV, standardní výkon | Vysoce výkonné, závodní, maximálně odolné potřeby | Přizpůsobení materiálu požadavkům aplikace. |
Export do archů
Volba mezi AlSi10Mg a A7075 pro kovový brzdový pedál AM nakonec zahrnuje kompromis mezi požadavky na výkon, složitostí výroby a rozpočtem. Oba materiály, pokud jsou správně zpracovány pomocí vysoce kvalitních prášků a optimalizovaných parametrů L-PBF, umožňují vytvářet lehké a vysoce výkonné součásti, které výrazně posouvají možnosti konstrukce automobilů. Pro optimální výběr je zásadní konzultace s odborníky na materiály a zkušenými poskytovateli AM služeb.
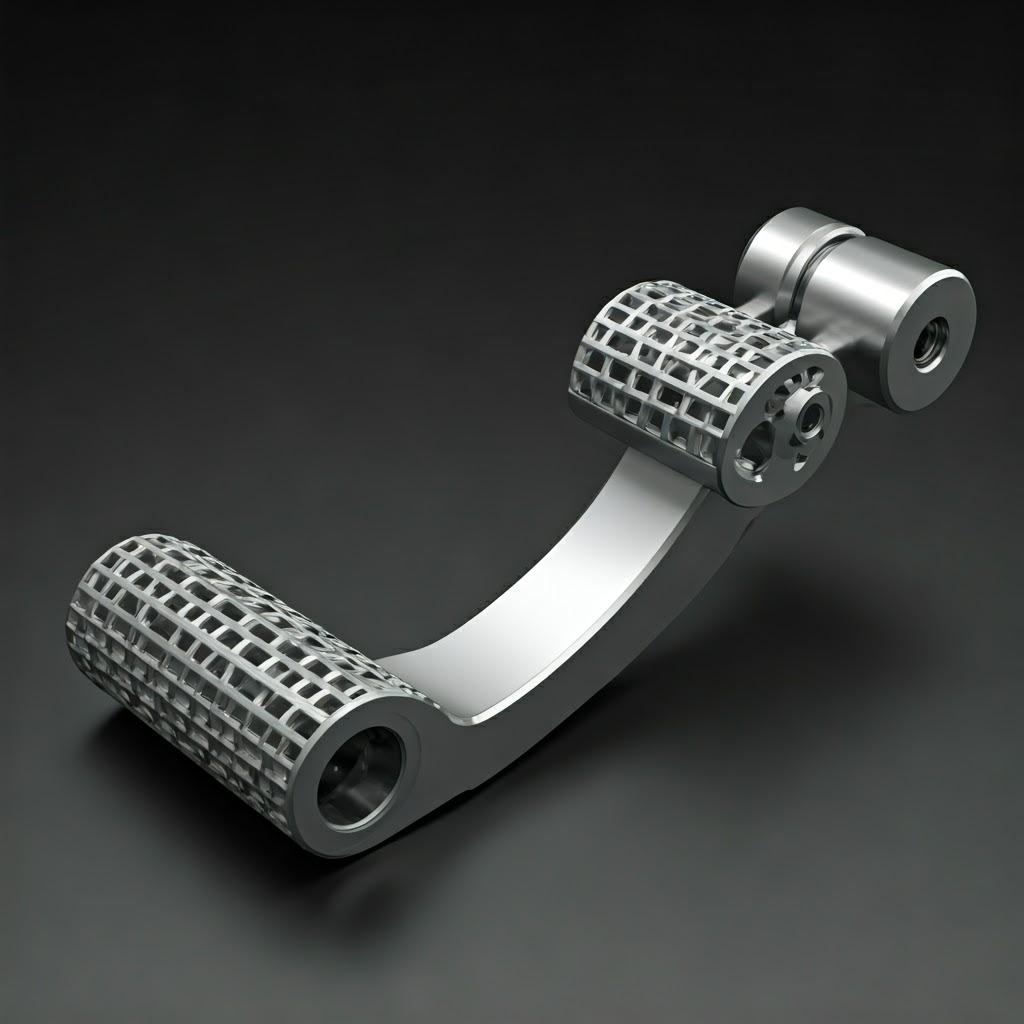
Design pro aditivní výrobu (DfAM): Optimalizace geometrie brzdového pedálu
Pouhým převzetím stávajícího návrhu brzdového pedálu určeného k odlévání nebo kování a jeho odesláním na kovovou 3D tiskárnu lze jen zřídkakdy plně využít potenciál aditivní výroby. Abyste skutečně využili dříve popsané výhody - zejména výrazné odlehčení a zvýšení výkonu - musí konstruktéři přijmout následující opatření Design pro aditivní výrobu (DfAM). DfAM je změna paradigmatu, která spočívá v navrhování komponent s ohledem na možnosti a omezení procesu AM po vrstvách. U kritické součásti, jako je rameno brzdového pedálu, je použití zásad DfAM pro úspěch nezbytné.
Klíčové aspekty DfAM pro kovové brzdové pedály AM zahrnují:
- Optimalizace topologie & Analýza zátěžové cesty: To je často výchozím bodem pro odlehčení. Software pro analýzu konečných prvků (FEA) dokáže určit primární dráhy zatížení pedálu při brzdění. Algoritmy pro optimalizaci topologie pak systematicky odstraňují materiál z oblastí s nízkým namáháním a ponechávají organickou, účinnou strukturu, která optimálně usměrňuje síly. Výsledné konstrukce často vypadají radikálně odlišně od svých tradičních protějšků a vyznačují se hladkými křivkami a kostrbatými tvary.
- Příhradové konstrukce & Strategie výplní: V oblastech vyžadujících tuhost nebo specifické vlastnosti pohlcování energie lze použít vnitřní mřížové struktury. Tyto složité, opakující se geometrické vzory (jako jsou voštinové, krychlové nebo gyroidní struktury) nabízejí:
- Vysoký poměr tuhosti k hmotnosti.
- Zvýšený potenciál absorpce energie (důležité z hlediska odolnosti proti nárazu).
- Zlepšený odvod tepla v případě potřeby.
- Flexibilita konstrukce pro vyladění místní tuhosti. Návrh efektivních mřížek však vyžaduje také zvážení odstranění prášku po tisku.
- Minimální rozměry prvků & Tloušťka stěny: Procesy AM mají omezení týkající se minimální velikosti prvků (otvorů, čepů) a nejtenčích stěn, které mohou spolehlivě vyrobit. U L-PBF s hliníkovými slitinami je minimální tloušťka stěny obvykle kolem 0,4-0,8 mm, v závislosti na stroji a geometrii. Konstrukce musí tyto limity respektovat, aby byla zajištěna tisknutelnost a strukturální integrita. Příliš tenké profily se mohou během tisku nebo používání deformovat nebo selhat.
- Strategie orientace na budování: Významný vliv má způsob orientace dílu na konstrukční platformě:
- Podpůrné struktury: Ovlivňuje množství, umístění a odstranitelnost podpěr. Strmější převisy (obvykle >45 stupňů od vodorovné roviny) vyžadují podpěru.
- Povrchová úprava: Povrchy směřující vzhůru a svislé povrchy mají obecně lepší povrchovou úpravu než povrchy směřující dolů.
- Mechanické vlastnosti: Anizotropie (směrová změna vlastností) se může vyskytnout u dílů AM, i když je obecně méně výrazná u kovů než u polymerů. Orientace může být zvolena tak, aby byl směr nejsilnější síly v souladu s osou primárního zatížení.
- Doba výstavby & Náklady: Vyšší postavy obvykle potřebují více času. Vměstnání více dílů na jednu konstrukční desku snižuje náklady na jeden díl, což ovlivňuje rozhodování o objemová výroba.
- Návrh podpůrné konstrukce & Minimalizace: Podpěry jsou v kovovém AM často nutným zlem. Ukotvují díl na konstrukční desce, zabraňují deformacím a podpírají převislé prvky. Spotřebovávají však další materiál, prodlužují dobu tisku, vyžadují odstranění (významný krok následného zpracování) a mohou na povrchu zanechat stopy. Správná praxe DfAM zahrnuje:
- Minimalizace převisů a navrhování samonosných úhlů tam, kde je to možné (obvykle do 45 stupňů).
- Navrhování dostatečně pevných, ale snadno přístupných a odstranitelných podpěr (např. pomocí kuželových nebo děrovaných konstrukcí).
- Zvažte, kde jsou přípustné podpěrné značky, a podle toho díl orientujte.
- Navrhování pro následné zpracování & Inspection: Kritické prvky, které vyžadují přísné tolerance nebo specifickou povrchovou úpravu (např. otvory pro čepy nebo montážní body senzorů), by měly být navrženy s dodatečným materiálem (“obráběcí materiál”), aby bylo možné po tisku provést přesnou úpravu pomocí CNC obrábění. Rovněž by se měl zvážit přístup pro kontrolní nástroje (jako jsou sondy CMM nebo skenery NDT).
Efektivní využití DfAM vyžaduje hlubokou znalost zvoleného procesu AM (např. L-PBF) a chování materiálu. Spolupráce se zkušenými poskytovateli služeb AM, kteří nabízejí odborné znalosti v oblasti DfAM, může výrazně zkrátit křivku učení a vést k optimalizovanějším a vyrobitelnějším konstrukcím, které zajistí, že komponenty budou splňovat přísné požadavky výrobní normy.
Dosažitelné tolerance, povrchová úprava a rozměrová přesnost
Inženýři a zadávání veřejných zakázek odborníci zvyklí na přísné tolerance a hladké povrchy tradičního obrábění musí pochopit možnosti a nuance aditivní výroby kovů, pokud jde o rozměrovou přesnost a kvalitu povrchu. Ačkoli lze pomocí AM obrábění kovů vyrábět velmi složité díly, obvykle vyžaduje následné zpracování, aby se dosáhlo velmi vysoké přesnosti potřebné pro určité prvky na rameni brzdového pedálu.
Zde je přehled toho, co můžete očekávat:
- Typické tolerance: U procesů L-PBF s hliníkovými slitinami, jako je AlSi10Mg nebo A7075, se přesnost rozměrů po vytištění často pohybuje v rozmezí +/- 0,1 mm až +/- 0,3 mm nebo +/- 0,1 % až 0,3 % rozměru, podle toho, která hodnota je vyšší. Obecné tolerance lze často vztáhnout k normám, jako je ISO 2768-m (střední) nebo -f (jemné) pro lineární a úhlové rozměry, ale to je velmi závislé na geometrii dílu, velikosti, orientaci a řízení procesu. Dosažení těsnějších tolerancí obvykle vyžaduje sekundární obráběcí operace.
- Faktory ovlivňující přesnost: Na konečné rozměrové přesnosti dílu AM se podílí několik faktorů:
- Kalibrace stroje: Pravidelná kalibrace systému laserového skeneru a stavební platformy je zásadní.
- Parametry procesu: Výkon laseru, rychlost skenování, tloušťka vrstvy a strategie šrafování ovlivňují dynamiku taveniny a tuhnutí, což má vliv na rozměrovou stabilitu.
- Tepelné namáhání: Rychlé cykly zahřívání a ochlazování, které jsou pro L-PBF typické, vyvolávají vnitřní pnutí, která mohou způsobit deformaci nebo zkroucení, zejména u velkých nebo složitých dílů. Účinné řízení teploty a odstraňování pnutí po zpracování jsou rozhodující.
- Geometrie dílu & Velikost: Větší díly a složité geometrie s různými průřezy jsou náchylnější k odchylkám.
- Podpůrné struktury: Způsob podepření dílu ovlivňuje jeho stabilitu během sestavování a případné deformace po vyjmutí.
- Následné zpracování: Tepelné zpracování s uvolněním napětí může způsobit drobné rozměrové změny, se kterými je třeba počítat. Obrábění samozřejmě zvyšuje přesnost, ale pouze u obrobených prvků.
- Povrchová úprava podle stavu: Vrstvová povaha AM vede k charakteristické struktuře povrchu. Drsnost povrchu (Ra) hliníkových dílů z L-PBF se obvykle pohybuje v rozmezí od 6 µm do 20 µm (přibližně 240-800 µin).
- Svislé stěny: Obecně nabízí nejhladší povrchovou úpravu.
- Povrchy směřující vzhůru: Mírně drsnější kvůli odstupňování vrstev.
- Povrchy směřující dolů: Bývají nejhrubší, zejména ty, které vyžadují podpěry, protože rozhraní mezi podpěrou a dílem může být nepravidelné.
- Důsledky: Tato povrchová úprava je často přijatelná pro nekritické povrchy, ale obvykle je nedostatečná pro rozhraní ložisek, těsnicí povrchy nebo oblasti vyžadující hladkou hmatovou zpětnou vazbu.
- Požadavky na sekundární obrábění: U ramene brzdového pedálu vyžadují některé prvky téměř vždy následné CNC obrábění, aby byly splněny funkční požadavky:
- Otvory pro čepy: Pro hladký chod a interakci s pouzdry nebo ložisky je nutný přesný průměr, zaoblení a povrchová úprava.
- Montážní otvory/rozhraní: Vyžadují přesné umístění a rozměry pro montáž na přepážku nebo pedálovou skříň.
- Rozhraní pedálových podložek: Může vyžadovat specifickou rovinnost nebo vlastnosti pro bezpečné upevnění podložky pedálu.
- Montážní body senzoru: V případě potřeby je často třeba přesně určit jejich polohu a geometrii.
- Kontrola kvality & Inspekce: Zajištění rozměrové integrity vyžaduje robustní kontrola kvality opatření. Obvykle se jedná o 3D skenování nebo kontrolu souřadnicovým měřicím strojem (CMM), která porovnává finální díl s původním modelem CAD a technickými výkresy. Metody nedestruktivního testování (NDT) mohou být také použity ke kontrole vnitřních vad, které by mohly ovlivnit integritu konstrukce, což je zásadní pro distributoři komponentů zaručuje kvalitu dílů.
Pochopení těchto faktorů umožňuje konstruktérům vhodně navrhovat díly (např. přidáním obráběcího materiálu) a stanovit realistická očekávání ohledně tolerancí a povrchových úprav dosažitelných přímo v procesu AM oproti těm, které vyžadují sekundární operace.
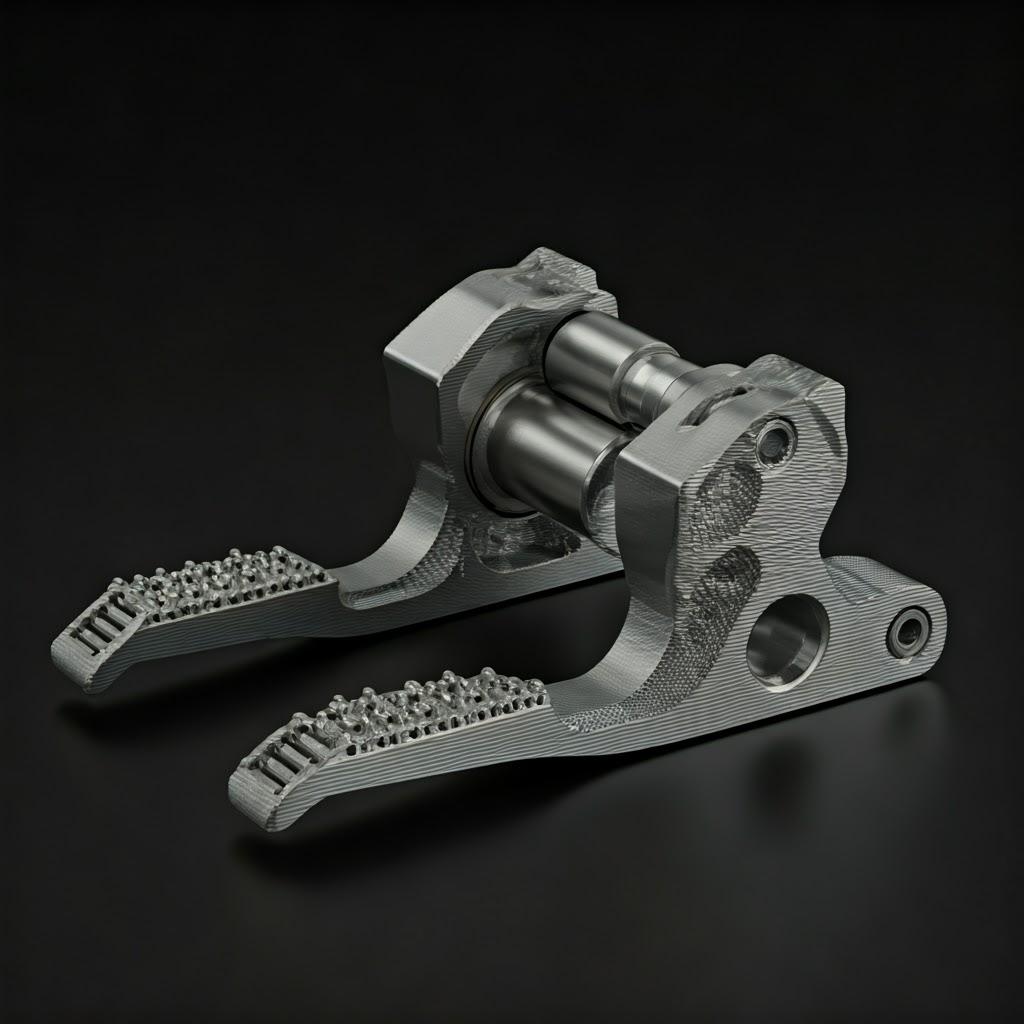
Základní kroky následného zpracování kovových brzdových pedálů AM
Kovový 3D tištěný díl je po vyjmutí z tiskárny jen zřídka připraven ke konečnému použití, zejména pro náročné automobilové aplikace, jako je brzdový pedál. K dosažení potřebných vlastností materiálu, rozměrové přesnosti, povrchové úpravy a celkové kvality je zapotřebí řada zásadních kroků následného zpracování. Zanedbání těchto kroků může ohrozit výkon a bezpečnost součásti.
Typický pracovní postup následného zpracování ramene brzdového pedálu z hliníkové slitiny L-PBF zahrnuje:
- Úleva od stresu / tepelné ošetření: To je pravděpodobně nejdůležitější krok pro hliníkové díly AM.
- Účel: Rychlé cykly ohřevu/chlazení při L-PBF vytvářejí v dílu značná zbytková napětí. Tato napětí mohou způsobit deformaci po vyjmutí z konstrukční desky nebo dokonce vést k předčasnému selhání při zatížení. Tepelné zpracování tato napětí zmírňuje a homogenizuje mikrostrukturu materiálu. U slitin, jako je AlSi10Mg a zejména A7075, jsou pro dosažení požadované vysoké pevnosti a tvrdosti nezbytné specifické cykly tepelného zpracování (jako je temperace T6 zahrnující rozpouštění, kalení a umělé stárnutí).
- Proces: Díly se obvykle tepelně zpracovávají ještě na konstrukční desce, aby se minimalizovalo jejich zkreslení. Přesný teplotní profil a doba trvání závisí do značné míry na slitině a požadovaných vlastnostech. Znalost metalurgie a protokolů tepelného zpracování materiálů pro AM je nezbytná.
- Vyjmutí dílu ze stavební desky: Po dokončení tepelného zpracování (nebo někdy i dříve, v závislosti na pracovním postupu) je třeba díl oddělit od konstrukční desky.
- Metody: Běžně se k tomu používá elektroerozivní obrábění (EDM) nebo pásová pila. Je třeba dbát na to, aby nedošlo k poškození samotného dílu.
- Odstranění podpůrné konstrukce: Nyní je třeba odstranit podpěry použité při tisku.
- Metody: Může se jednat o pracný proces, který často zahrnuje ruční lámání nebo řezání (pomocí kleští, brusek nebo ručního nářadí), obrábění na CNC nebo někdy drátové elektroerozivní obrábění na obtížně přístupných místech.
- Úvahy: Snadnost odstranění podpory je do značné míry ovlivněna dříve provedenými volbami DfAM. Špatně navržené podpěry lze obtížně čistě odstranit, což může vést k poškození povrchu dílu a zvýšení nákladů.
- Čištění & amp; Odstraňování prášku: Veškerý netavený prášek zachycený ve vnitřních kanálech, mřížkových strukturách nebo složitých geometriích musí být důkladně odstraněn.
- Metody: Obvykle se jedná o tryskání stlačeným vzduchem, tryskání kuličkami nebo čištění ultrazvukem. Ve fázi návrhu je třeba zvážit přístup k čisticím nástrojům. Neúplné odstranění prášku může zvýšit hmotnost a potenciálně ohrozit výkon nebo narušit montáž.
- Povrchová úprava: V závislosti na požadavcích lze použít různé povrchové úpravy:
- Tryskání kuličkami / kuličkování: Vytváří rovnoměrný matný povrch, odstraňuje uvolněné částice a někdy může zlepšit únavovou životnost díky tlakovým zbytkovým napětím (kuličkování).
- Obrábění / vibrační úprava: Vyhlazuje povrchy a hrany pěchováním dílů médiem. Efektivní pro dávkové zpracování, ale hůře kontrolovatelné pro specifické prvky.
- Leštění: Pro dosažení velmi hladkých, reflexních povrchů, často ručně nebo pomocí automatických lešticích nástrojů pro specifické oblasti.
- Eloxování: Elektrochemický proces pro hliník, který vytváří tvrdou, proti korozi odolnou vrstvu oxidu. Lze použít i k barvení. Nezbytný pro A7075 v mnoha aplikacích kvůli jeho mírné odolnosti proti korozi.
- Malování / nátěry: Nanášení specializovaných automobilových barev nebo nátěrů pro estetiku a zvýšenou ochranu životního prostředí.
- CNC obrábění: Jak již bylo uvedeno, obvykle se obrábějí kritické prvky vyžadující malé tolerance (+/- 0,01 až 0,05 mm) a specifickou kvalitu povrchu (Ra < 1,6 µm nebo méně). Tím je zajištěno přesné uložení a funkce čepů, montážních bodů a rozhraní.
- Kontrola a validace: Posledním krokem je důkladná kontrola kvality:
- Rozměrová kontrola: Pomocí souřadnicového měřicího stroje nebo 3D skenování.
- Nedestruktivní zkoušení (NDT): Metody, jako je počítačová tomografie (CT), umožňují kontrolovat vnitřní struktury na přítomnost defektů (pórovitost, praskliny), aniž by došlo k poškození dílu. Lze také použít penetrační zkoušku barvivem nebo ultrazvuk.
- Ověřování vlastností materiálu: Zkušební vzorky vytištěné vedle hlavního dílu pro potvrzení pevnosti v tahu, tvrdosti atd.
Úspěšné zvládnutí těchto kroků následného zpracování vyžaduje specializované vybavení, kvalifikované techniky a přesně definované postupy. Spolupráce s poskytovatelem AM služeb, jako je Met3dp, který rozumí celému pracovnímu postupu od prášku až po hotový díl, včetně nejrůznějších technologií tiskových metod a nezbytných sekundárních operací, má zásadní význam pro dosažení spolehlivých a kvalitních výsledků.
Běžné problémy při tisku brzdových pedálů a strategie pro jejich zmírnění
Ačkoli technologie AM nabízí obrovský potenciál pro automobilové komponenty, jako jsou brzdové pedály, není bez problémů. Uvědomění si těchto potenciálních problémů a zavedení účinných strategií pro jejich zmírnění je klíčem k úspěšnému přijetí, zejména při rozšiřování směrem k objemová výroba.
Zde jsou uvedeny některé běžné problémy, které se vyskytují při tisku brzdových pedálů z hliníkové slitiny pomocí L-PBF:
- Deformace a zkreslení:
- Příčina: Výrazné tepelné gradienty mezi roztaveným materiálem a okolními vrstvami prášku/ztuhlého materiálu vyvolávají napětí, které způsobuje, že se díly (zejména velké, ploché nebo asymetrické) deformují nebo odtahují od konstrukční desky.
- Zmírnění:
- Optimalizovaná orientace: Orientace dílu tak, aby se minimalizovaly velké rovné plochy rovnoběžné s konstrukční deskou a snížila se koncentrace tepelné hmoty.
- Efektivní strategie podpory: Robustní podpěry pevně ukotvují díl a pomáhají odvádět teplo.
- Vytápění stavebních desek: Předehřátí stavební desky snižuje tepelný gradient.
- Řízení procesních parametrů: Jemné doladění parametrů laseru pro řízení tepelného příkonu.
- Tepelné ošetření proti stresu: Důležité pro uvolnění nahromaděného napětí po tisku.
- Řízení zbytkového stresu:
- Příčina: I když je deformace během sestavování kontrolována, zůstává v dílu zablokováno značné zbytkové napětí. To může vést k deformaci po vyjmutí z konstrukční desky nebo podpůrných konstrukcí, nebo dokonce k předčasnému selhání v provozu.
- Zmírnění:
- Povinné tepelné zpracování: Vhodné odlehčení a/nebo ošetření roztokem a cykly stárnutí přizpůsobené konkrétní slitině (AlSi10Mg vs. A7075) jsou neoddiskutovatelné.
- Simulace: Použití softwaru pro simulaci procesů k předvídání akumulace napětí a optimalizaci strategie výroby.
- Složitost odstraňování podpory & Kvalita povrchu:
- Příčina: Podpěry potřebné pro převisy nebo stabilitu lze obtížně čistě odstranit, zejména ze složitých vnitřních geometrií nebo choulostivých prvků. Procesy odstraňování mohou na povrchu dílu zanechat stopy nebo škrábance.
- Zmírnění:
- DfAM pro minimalizaci podpory: Navrhování dílů se samonosnými úhly, kde je to možné.
- Chytrá konstrukce podpory: Použití podpůrných struktur (např. tenkých hrotů, perforací) určených pro snadnější oddělování.
- Strategická orientace: Umístění podpěr na nekritické povrchy, pokud je to možné.
- Vhodné techniky odstraňování: Pomocí pečlivých ručních metod nebo přesného obrábění/EDM. Plánování dokončovacích kroků (tryskání, leštění) k odstranění stop.
- Odstranění prášku z vnitřních prvků:
- Příčina: Složité vnitřní kanály nebo mřížové struktury určené k odlehčení mohou zachycovat netavený kovový prášek.
- Zmírnění:
- DfAM pro únik prášku: Navrhování vnitřních prvků s odtokovými otvory nebo přístupovými místy pro odstraňování prášku.
- Důkladné čisticí postupy: Využití účinných metod, jako jsou vysokotlaké vzduchové/plynové trysky, vibrační stoly a případně čištění rozpouštědly.
- Kontrola: Pokud je to důležité, použijte k ověření úplného odstranění prášku metody, jako je CT skenování.
- Kontrola pórovitosti:
- Příčina: V tištěném materiálu mohou vznikat malé dutiny nebo póry v důsledku zachyceného plynu, keyholingu (nestálost při stlačení páry) nebo nedostatečného spojení mezi vrstvami. Pórovitost může výrazně zhoršit mechanické vlastnosti, zejména únavovou životnost.
- Zmírnění:
- Vysoce kvalitní prášek: Použití prášku s nízkým obsahem vnitřního plynu, řízenou distribucí velikosti částic a vysokou sféricitou (jako jsou částice vyráběné společností Met3dp pomocí pokročilé atomizace).
- Optimalizované parametry tisku: Přesné řízení výkonu laseru, rychlosti skenování, tloušťky vrstvy a strategie šrafování pro zajištění úplného roztavení a tavení.
- Kontrola inertní atmosféry: Udržování prostředí s vysoce čistým inertním plynem (argon nebo dusík) ve stavební komoře, aby se zabránilo oxidaci.
- Monitorování procesů: Využití monitorovacích systémů v reálném čase (monitorování taveniny) k odhalení případných nesrovnalostí.
- Izostatické lisování za tepla (HIP): Krok následného zpracování, při kterém se pomocí vysoké teploty a tlaku uzavírají vnitřní póry (zvyšuje náklady, ale může výrazně zlepšit vlastnosti kritických dílů).
Překonání těchto výzev vyžaduje důsledné řízení procesů, vysoce kvalitní materiály, moderní vybavení a značné technické znalosti. Spolupráce se zkušenými partnery, jako je Met3dp, která je známá svými spolehlivými tiskovými systémy a hlubokými znalostmi v oblasti materiálových věd a optimalizace procesů, poskytuje záruku, že tyto potenciální problémy jsou aktivně řešeny, což vede ke konzistentním a vysoce kvalitním ramenům brzdových pedálů připraveným pro náročné aplikace v automobilovém průmyslu.
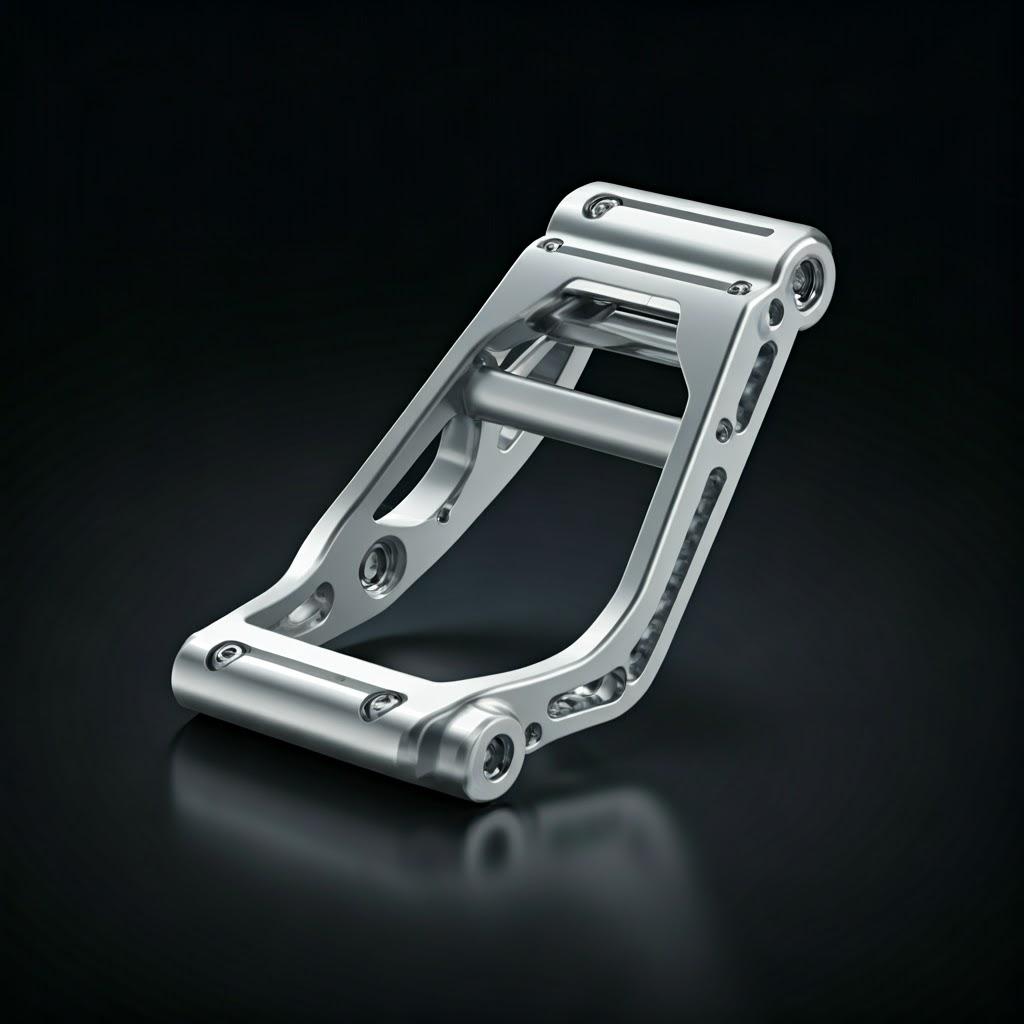
Výběr správného poskytovatele služeb 3D tisku kovů pro automobilové díly
Výběr partnera pro výrobu bezpečnostně důležitých součástí, jako jsou ramena brzdových pedálů, pomocí aditivní výroby je rozhodnutí, které vyžaduje pečlivé zvážení. Ne všichni poskytovatelé AM služeb mají potřebné odborné znalosti, vybavení nebo systémy kvality, aby splnili náročné požadavky automobilového průmyslu. Inženýři a zadávání veřejných zakázek manažeři potřebují robustní hodnocení dodavatelů se zaměřil na několik klíčových kritérií:
- Osvědčené znalosti v oblasti automobilového průmyslu a materiálů: Má poskytovatel prokazatelné zkušenosti s aplikacemi v automobilovém průmyslu a konkrétně se zvolenými materiály (AlSi10Mg, A7075)? Měl by rozumět výkonnostním požadavkům, zkušebním protokolům (např. únavovým zkouškám) a potřebám sledovatelnosti, které jsou v tomto odvětví běžné. Vyhledejte případové studie nebo reference týkající se konstrukčních automobilových součástí.
- Příslušné certifikáty kvality: Hledejte alespoň certifikaci ISO 9001, která označuje spolehlivý systém řízení kvality. Pro dodavatele, kteří se zaměřují na sériovou výrobu v automobilovém průmyslu, jsou velmi žádoucí certifikace jako IATF 16949 (nebo prokázaný pokrok směrem k ní), což znamená dodržování přísných norem kvality v automobilovém průmyslu.
- Kontrola kvality materiálu: Jak poskytovatel zajišťuje kvalitu a konzistenci používaných kovových prášků? Má zavedeny kontrolní mechanismy pro získávání prášků, manipulaci s nimi, jejich skladování a recyklaci (je-li to relevantní)? Konzistentní kvalita prášku je základem pro dosažení opakovatelných mechanických vlastností. Poskytovatelé, kteří vyrábějí i vlastní prášky, jako je Met3dp, mají v této oblasti často výhodu díky přímé kontrole vlastností prášků.
- Technologie & Kapacita: Má poskytovatel správné vybavení (např. stroje L-PBF průmyslové třídy vhodné pro hliníkové slitiny) a dostatečnou kapacitu? Zvažte velikost jeho strojového parku, možnosti sestavení obálky a schopnost škálovat výrobu v případě potřeby pro nízké až střední výrobní kapacity objemová výroba běží. Zahrnuje jejich technologické portfolio v případě potřeby doplňkové procesy? Například společnost Met3dp nabízí špičkové schopnosti v oblasti tiskáren L-PBF a SEBM (Selective Electron Beam Melting), což ukazuje šíři technologických znalostí.
- Engineering & DfAM Support: Může poskytovatel nabídnout cenné informace o designu pro aditivní výrobu (DfAM)? Společná optimalizace návrhu může výrazně zlepšit výkonnost dílů, snížit náklady a zefektivnit výrobu. Hledejte partnery s kvalifikovanými aplikačními inženýry, kteří mohou váš tým vést.
- Možnosti následného zpracování: Má poskytovatel vlastní nebo přísně řízené externí kapacity pro všechny nezbytné kroky následného zpracování (tepelné zpracování specifické pro hliníkové slitiny AM, přesné obrábění, povrchová úprava, kontrola NDT)? Vertikálně integrovaný přístup často zjednodušuje logistiku a zajišťuje odpovědnost.
- Umístění, logistika a komunikace: Zvažte polohu poskytovatele vzhledem k vašim potřebám, typickou přepravu dodací lhůtya jejich komunikační schopnosti. Jasné komunikační kanály jsou pro řízení složitých projektů zásadní.
Vyhodnocení potenciálních partnerů podle těchto kritérií vám pomůže zajistit výběr dodavatele, který je schopen dodávat vysoce kvalitní a spolehlivá kovová ramena brzdových pedálů AM, která splňují vaše specifikace. Společnosti jako např Met3dp, se sídlem v čínském městě Čching-tao, zaujímá pozici předního poskytovatele komplexních řešení aditivní výroby. Díky desítkám let společných zkušeností, pokročilým systémům práškové výroby (využívajícím technologie plynové atomizace a PREP), špičkové přesnosti tisku a zaměření na kritické díly pro letecký, lékařský a automobilový průmysl představují typ schopného partnera, který je pro takto náročné aplikace vyžadován. Můžete se dozvědět více O společnosti Met3dp a jejich závazek ke kvalitě a inovacím.
Porozumění nákladovým faktorům a dodacím lhůtám pro brzdové pedály AM
Jedním z hlavních hledisek pro každý tým inženýrů nebo dodavatelů, který hodnotí nový výrobní proces, jsou náklady a doba realizace. Aditivní výroba kovů má ve srovnání s tradičními metodami, jako je odlévání nebo kování, odlišnou strukturu nákladů.
Hlavní faktory ovlivňující náklady na kovové brzdové pedály AM:
- Typ materiálu & Spotřeba: Významným faktorem je cena samotného kovového prášku. Vysokopevnostní slitiny jako A7075 jsou obvykle dražší než standardní AlSi10Mg. Celkový objem použitého materiálu (včetně podpůrných konstrukcí) přímo ovlivňuje náklady. Efektivní DfAM a optimalizace topologie pomáhají minimalizovat spotřebu materiálu.
- Čas stroje (čas sestavení): Stroje L-PBF jsou drahým majetkem a jejich provozní doba je hlavní složkou nákladů. Doba sestavení závisí na:
- Část Výška: Vyšším dílům to trvá déle.
- Část Svazek & Složitost: Více materiálu k roztavení vyžaduje více času. Složité geometrie mohou vyžadovat nižší rychlost skenování pro zajištění přesnosti.
- Počet dílů na sestavení: Maximalizace počtu dílů tištěných současně na jedné sestavovací desce snižuje čas stroje přidělený na jeden díl.
- Objem podpůrné konstrukce & Odstranění: Materiál použitý na podpěry zvyšuje náklady a práce/čas potřebný na jejich odstranění představuje významný náklad na následné zpracování. Optimalizovaná konstrukce minimalizuje potřebu podpěr.
- Intenzita následného zpracování: Každý krok zvyšuje náklady:
- Tepelné zpracování: Čas a spotřeba energie v peci.
- Obrábění: Doba seřízení a obrábění kritických prvků.
- Povrchová úprava: práce a spotřební materiál pro tryskání, leštění, eloxování atd.
- Kontrola: Kontrola NDT a CMM vyžaduje specializované vybavení a kvalifikovanou obsluhu.
- Objednávkové množství: Ačkoli se AM vyhýbá nákladům na nástroje, náklady na jeden díl jsou méně citlivé na množství než u metod hromadné výroby. Nicméně, množstevní slevy jsou často k dispozici pro větší B2B zakázky díky efektivitě nastavení, dávkovému zpracování a optimalizovanému využití stavebních desek. Diskutujte o potenciálu velkoobchodní poptávky přímo u poskytovatele.
- Engineering & Nastavení: Počáteční konzultace návrhu, optimalizace DfAM a příprava tiskových souborů mohou zahrnovat počáteční technické poplatky, zejména u složitých projektů.
Typické dodací lhůty:
Dodací lhůty dílů vyrobených metodou AM jsou výrazně kratší než u tradičních metod vyžadujících výrobu nástrojů, zejména u prototypů a malých objemů. Je však třeba provést více kroků:
- Citace & Design Review: 1-5 pracovních dnů (v závislosti na složitosti a rychlosti reakce poskytovatele).
- Příprava tisku (Nastavení souboru): 0.5-2 pracovní dny.
- Tisk: 1-4 dny (velmi závisí na velikosti, složitosti a počtu dílů na sestavení).
- Chlazení: Několik hodin až celý den ve stroji nebo na stanici pro odstraňování konstrukcí.
- Následné zpracování: 2-10 pracovních dnů (často se jedná o nejdelší fázi, která zahrnuje cykly tepelného zpracování, odstranění podpěr, nastavení obrábění, dokončovací práce a kontrolní fronty).
- Doprava: Záleží na lokalitě a způsobu dopravy.
Celkově lze očekávat, že doba dodání se bude pohybovat od 1 až 4 týdny pro typický projekt kovového brzdového pedálu AM, který do značné míry závisí na výše uvedených faktorech. To je podstatně rychlejší než měsíce, které jsou často potřebné pro tradiční vývoj nástrojů a počáteční výrobu dílů. Přesné analýza nákladů a odhady doby realizace vyžadují předložení konkrétního návrhu (modelu CAD a technického výkresu) potenciálním dodavatelům k podrobné cenové nabídce.
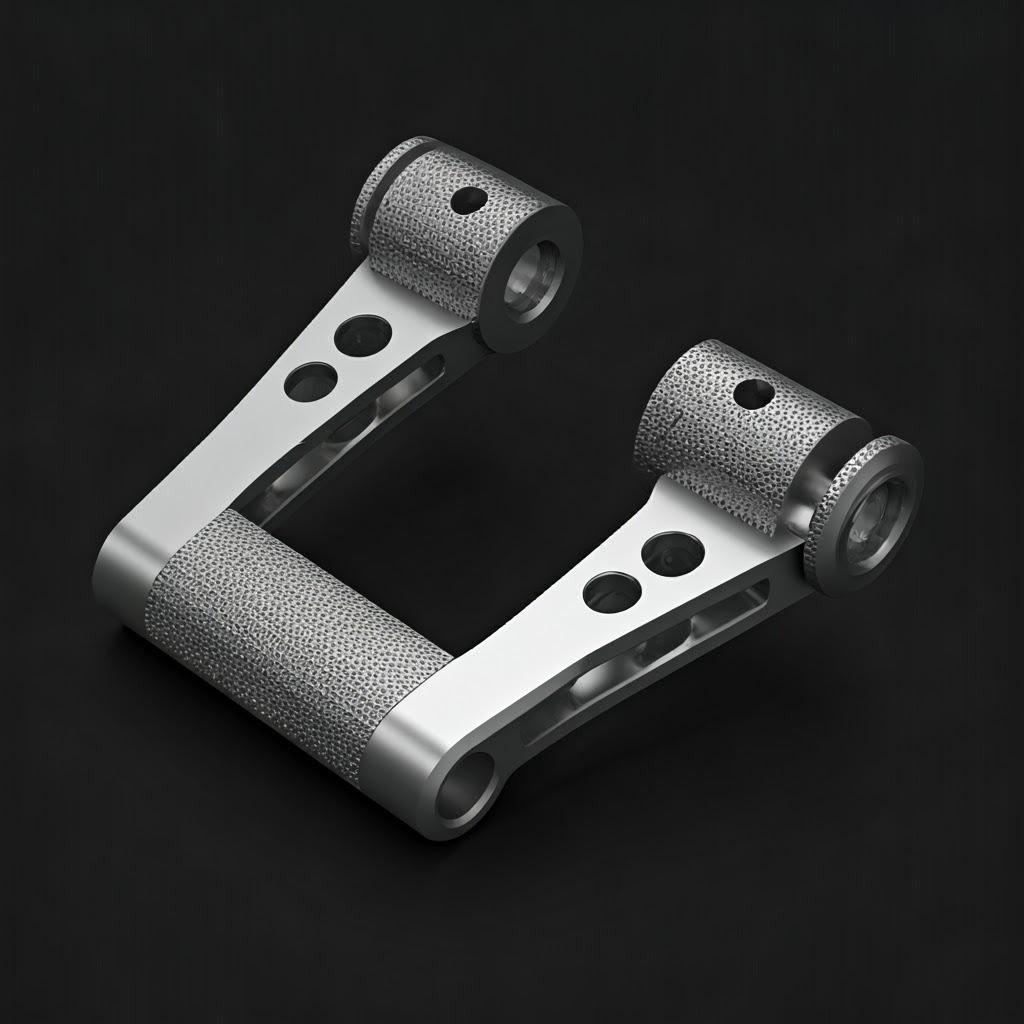
Často kladené otázky (FAQ)
- Otázka 1: Jsou 3D tištěné kovové brzdové pedály dostatečně pevné a bezpečné pro použití v automobilovém průmyslu?
- A: Rozhodně, pokud jsou správně navrženy, vyrobeny a ověřeny. Použití vysokopevnostních slitin, jako je AlSi10Mg nebo A7075, v kombinaci s optimalizací topologie a správnými principy DfAM vede k dílům, které mohou splnit nebo překročit požadavky na pevnost a tuhost tradičních součástí. Zásadní význam má důsledná kontrola procesu během tisku, vhodné tepelné zpracování a důkladná kontrola NDT (např. CT), která zajistí integritu materiálu a absenci kritických vad. Rozsáhlé simulace (FEA) a fyzikální zkoušky (statické zatěžovací zkoušky, únavové zkoušky) jsou standardními validačními kroky před zavedením do jakéhokoli sériového vozidla.
- Otázka 2: Jaká je cena brzdového pedálu AM ve srovnání s tradičně vyráběným pedálem?
- A: To do značné míry závisí na objemu a složitosti výroby. Pro prototypy a malosériovou výrobu (desítky až stovky dílů) je AM často cenově výhodnější, protože odpadají vysoké počáteční náklady na výrobu nástrojů (odlévací formy, kovací formy). Pro hromadnou výrobu (tisíce nebo miliony dílů) tradiční metody obvykle dosahují nižších nákladů na jeden díl díky úsporám z rozsahu. Díl vyrobený metodou AM však může umožnit úspory na úrovni systému díky odlehčení (lepší palivová/energetická účinnost) nebo konsolidaci dílů (snížení nákladů na montáž), které kompenzují vyšší cenu na díl. Často je vyžadována analýza celkových nákladů na vlastnictví.
- Otázka 3: Jakou únavovou životnost lze očekávat u hliníkového ramena brzdového pedálu AM?
- A: Únavová životnost je vynikající, zejména u dílů vytištěných pomocí vysoce kvalitního prášku, optimalizovaných parametrů a vhodného následného zpracování. Vysokopevnostní slitiny, jako je A7075, mají ze své podstaty dobrou únavovou odolnost. Kontrola procesu s cílem minimalizovat pórovitost je kritická, protože vnitřní defekty mohou působit jako místa iniciace únavy. Postprocesní kroky, jako je izostatické lisování za tepla (HIP), sice zvyšují náklady, ale mohou dále zvýšit únavovou životnost uzavřením vnitřních pórů. Svou roli hraje také povrchová úprava a zbytková napětí. Při správném návrhu a výrobě lze brzdové pedály AM navrhnout tak, aby splňovaly nebo překračovaly náročné požadavky na únavovou životnost v automobilovém průmyslu.
- Otázka 4: Lze dosáhnout stejné povrchové úpravy jako u odlitku nebo kovaného dílu?
- A: Povrchová úprava dílu z L-PBF po vytištění je obvykle drsnější (Ra 6-20 µm) než povrch obrobený nebo dokonce hladký povrch odlitku/kovu. Nicméně díky technikám následného zpracování, jako je otryskávání kuličkami, bubnování, leštění nebo obrábění, lze u specifických povrchů dosáhnout povrchové úpravy, která je srovnatelná nebo dokonce lepší než u tradičních metod. Kritické oblasti, jako jsou otvory čepů, se obvykle opracovávají tak, aby se dosáhlo požadované hladké povrchové úpravy (např. Ra < 1,6 µm nebo nižší). Nekritické povrchy si mohou zachovat povrchovou úpravu jako po otryskání nebo mohou být lakovány/anodizovány. Požadovaná povrchová úprava každého povrchu by měla být uvedena v technickém výkresu pro produkt.
Závěr: Urychlení inovací v automobilovém průmyslu pomocí optimalizovaných brzdových pedálů AM
Neustálá snaha o odlehčení, výkon a efektivitu v automobilovém průmyslu vyžaduje inovativní výrobní řešení. Aditivní výroba kovů, konkrétně L-PBF s využitím pokročilých hliníkových slitin, jako jsou AlSi10Mg a A7075, nabízí účinnou cestu k výrobě ramen brzdových pedálů nové generace. Tím, že AM odpoutává konstruktéry od tradičních omezení, umožňuje vytvářet topologicky optimalizované, komplexní a výrazně lehčí součásti, aniž by byla ohrožena pevnost nebo bezpečnost.
Prozkoumali jsme zajímavé aplikace, zásadní význam návrhu pro aditivní výrobu (DfAM), nuance výběru materiálu a nezbytné kroky následného zpracování, které jsou nutné k dosažení dílů připravených k výrobě. Pochopení dosažitelných tolerancí, zvládnutí potenciálních problémů a pečlivý výběr správného výrobního partnera - to vše jsou klíčové prvky úspěchu.
Tato cesta zahrnuje využití pokročilých materiálů a procesů, zavedení přísné kontroly kvality a často úzkou spolupráci s odborníky na AM. Společnosti jako např Met3dp stojí v čele této technologické vlny a nabízí nejen nejmodernější tiskové zařízení (včetně systémů SEBM a L-PBF) a vysoce výkonné kovové prášky vyráběné pomocí nejmodernějších atomizačních technik, ale také komplexní odborné znalosti potřebné pro zvládnutí složitostí průmyslové aditivní výroby. Jejich závazek umožnit výrobu nové generace z nich činí ideálního partnera pro automobilové společnosti, které chtějí využít sílu AM.
Pro inženýry a manažery veřejných zakázek, kteří se snaží posunout hranice designu a výkonu vozidel, představuje technologie AM pro kov hmatatelnou příležitost. Odlehčení kritických součástí, jako jsou ramena brzdových pedálů, přímo přispívá ke zlepšení dynamiky vozidla, prodloužení dojezdu elektromobilů a celkové účinnosti systému.
Jste připraveni prozkoumat, jak může aditivní výroba kovů změnit vaše automobilové komponenty? Návštěva Met3dp.com nebo se ještě dnes obraťte na jejich tým, abyste prodiskutovali své projektové požadavky a zjistili, jak mohou jejich pokročilé prášky, tiskové systémy a služby vývoje aplikací urychlit dosažení cílů vaší organizace v oblasti aditivní výroby.
Sdílet na
MET3DP Technology Co., LTD je předním poskytovatelem řešení aditivní výroby se sídlem v Qingdao v Číně. Naše společnost se specializuje na zařízení pro 3D tisk a vysoce výkonné kovové prášky pro průmyslové aplikace.
Dotaz k získání nejlepší ceny a přizpůsobeného řešení pro vaše podnikání!
Související články
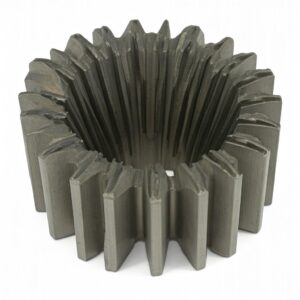
Vysoce výkonné segmenty lopatek trysek: Revoluce v účinnosti turbín díky 3D tisku z kovu
Přečtěte si více "O Met3DP
Nedávná aktualizace
Náš produkt
KONTAKTUJTE NÁS
Nějaké otázky? Pošlete nám zprávu hned teď! Po obdržení vaší zprávy obsloužíme vaši žádost s celým týmem.
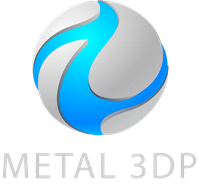
Kovové prášky pro 3D tisk a aditivní výrobu