3D tištěné chladiče pro chlazení elektromotorů
Obsah
Úvod: Revoluce v tepelném managementu elektromotorů pomocí 3D tisku z kovu
Elektromotory jsou hnacími motory moderního průmyslu a pohánějí vše od elektromobilů (EV) a leteckých pohonů až po průmyslové roboty a lékařské přístroje. S rostoucími požadavky na výkon - vyšší hustotou výkonu, vyššími rychlostmi a kompaktnějšími konstrukcemi - se však efektivní řízení tepla stává prvořadým. Přehřívání je hlavní příčinou snížené účinnosti, zkrácené životnosti a katastrofických poruch elektromotorů. Tradiční chladiče, často vyráběné odléváním nebo lisováním, narážejí na omezení při řešení komplexních požadavků na chlazení pokročilých konstrukcí motorů. Zde se uplatní aditivní výroba kovů (AM), resp 3D tisk, se ukazuje jako transformační technologie, která umožňuje vytvářet vysoce optimalizované, komplexní systémy chlazení elektromotoru řešení, která dříve nebylo možné vyrobit.
3D tisk kovů umožňuje konstruktérům vymanit se z omezení konvenční výroby. Namísto odebírání materiálu z bloku se při AM vytvářejí díly vrstvu po vrstvě přímo z digitálního modelu pomocí vysoce výkonných kovových prášků. Tento aditivní přístup otevírá nebývalou konstrukční svobodu a umožňuje vytvářet složité vnitřní chladicí kanály, topologicky optimalizované geometrie a lehké struktury přesně přizpůsobené tepelnému profilu konkrétního elektromotoru. Pro manažery nákupu a inženýry, kteří hledají nejmodernější technologie řešení tepelného managementu, pochopení potenciálu aditivní výroba chladičů je zásadní pro udržení konkurenceschopnosti. Tyto pokročilé komponenty nabízejí vynikající odvod tepla, což umožňuje motorům pracovat chladněji, déle a efektivněji, zejména v náročných podmínkách průmyslové aplikace. Společnosti jako Met3dp, které se specializují jak na pokročilé 3D tisk z kovu zařízení a vysoce kvalitní kovové prášky, stojí v čele této revoluce a poskytuje nástroje a materiály nezbytné pro realizaci těchto tepelných řešení nové generace. Tento posun směrem k AM nepředstavuje jen postupné zlepšování, ale zásadní změnu v přístupu k návrhu a výrobě kritických komponent, jako jsou chladiče elektromotorů.
S rostoucím výkonem motorů a jejich integrací do stísněných prostor se zvyšuje problém účinného odvádění tepla generovaného statorovým vinutím a rotorovým soustrojím. Běžné chladiče, obvykle s rovnými žebry připevněnými k základní desce, se spoléhají především na maximalizaci plochy vystavené chladicímu médiu (vzduchu nebo kapalině). I když jsou do určité míry účinné, jejich výkon je často omezen samotným výrobním procesem. Vytlačování omezuje tvary a konstrukce žeber, zatímco odlévání může způsobit pórovitost a omezit geometrickou složitost a minimální velikost prvků. Obrábění složitých tvarů z masivních bloků je možné, ale často neúměrně nákladné a neekonomické.
3D tisk kovů tyto překážky překonává tím, že umožňuje:
- Bezkonkurenční geometrická složitost: Technologie AM dokáže vytvářet organické tvary, složité mřížkové struktury a konformní chladicí kanály, které přesně kopírují obrysy součástí motoru. To umožňuje přímý a účinný odvod tepla z horkých míst.
- Optimalizace topologie: Pomocí výpočetní analýzy lze optimalizovat konstrukci tak, aby byl materiál umístěn pouze tam, kde je to z konstrukčního nebo tepelného hlediska nezbytné, což vede k výrazně lehčím součástem se stejným nebo lepším chladicím výkonem.
- Konsolidace částí: Více komponent sestavy tepelného managementu (např. chladič, montážní držáky, průtokové rozdělovače) lze potenciálně konsolidovat do jediného 3D tištěného dílu, čímž se sníží čas montáže, potenciální místa úniku a celková složitost systému.
- Rychlé prototypování a iterace: Konstrukční změny lze rychle implementovat a testovat bez nutnosti nákladných úprav nástrojů, což urychluje vývojové cykly nových řešení chlazení motorů.
- Použití pokročilých materiálů: Procesy AM mohou efektivně pracovat s materiály optimalizovanými pro tepelnou vodivost a pevnost, jako jsou specifické slitiny mědi a hliníku, které by bylo obtížné nebo nákladné zpracovávat tradičními metodami.
Podnikům zapojeným do dodavatelského řetězce elektromotorů - od dodavatelů součástek až po výrobce originálního vybavení (OEM) - nabízí využití technologie AM pro chladiče z kovu výraznou konkurenční výhodu. Usnadňuje vývoj výkonnějších, spolehlivějších a potenciálně nákladově efektivnějších elektromotorů, které splňují přísné požadavky průmyslových odvětví, jako je automobilový průmysl (zejména elektromobily), letecký průmysl, robotika a vysoce výkonná výpočetní technika. Odborníci na veřejné zakázky, kteří hledají spolehlivé dodavatelé AM kovů schopné vyrábět vysoce kvalitní a složité chladiče z materiálů, jako je měď, chrom, zirkon (CuCrZr) nebo hliník, křemík, hořčík (AlSi10Mg), se stále častěji obracejí na specializované dodavatele, kteří rozumí jak procesu tisku, tak kritickým požadavkům na aplikace. Integrace návrhu založeného na simulaci s pokročilými výrobními možnostmi slibuje budoucnost, kdy budou ze systémů elektromotorů systematicky odstraňována úzká místa z hlediska tepelné ochrany.
K čemu se používají 3D tištěné chladiče elektromotorů?
Aplikace pro 3D tištěné chladiče elektromotorů zahrnují širokou škálu průmyslových odvětví, kde je důležitý vysoký výkon, účinnost a spolehlivost. Díky schopnosti vytvářet vlastní, vysoce účinná chladicí řešení je technologie AM z kovu obzvláště cenná ve scénářích, kde konvenční chladiče nedostačují kvůli nedostatku místa, hmotnostním omezením nebo extrémnímu tepelnému zatížení. Mezi klíčové oblasti použití patří:
- Elektrická vozidla (EV) a automobilový průmysl:
- Trakční motory: Hlavní hnací motory elektromobilů produkují značné množství tepla, zejména při vysoké akceleraci nebo rekuperačním brzdění. Tepelný management elektromobilů je rozhodující pro dojezd, výkon a výdrž baterie. 3D tištěné chladiče se složitými vnitřními kanály pro kapalinové chlazení nebo optimalizované struktury žeber pro chlazení vzduchem mohou výrazně zlepšit odvod tepla v kompaktních sestavách pohonných jednotek. Umožňují konstrukci motorů s vyšší hustotou výkonu, což přispívá k odlehčení a účinnosti vozidla.
- Palubní nabíječky a měniče: Součásti výkonové elektroniky vyžadují také robustní chlazení. Pro optimální tepelný výkon lze do těchto jednotek přímo integrovat vlastní 3D tištěné chladicí desky nebo chladiče.
- Motorsport: V závodních aplikacích se počítá každý gram a maximální výkon je zásadní. Topologicky optimalizované, lehké 3D tištěné chladiče poskytují konkurenční výhodu tím, že zajišťují maximální účinnost motorů v extrémních podmínkách.
- Letectví a obrana:
- Ovládací systémy: Elektromotory pohánějí letové řídicí plochy, podvozek a další důležité systémy. Spolehlivost je prvořadá a komponenty musí odolávat náročným provozním podmínkám (kolísání teploty, vibrace). Součásti leteckých motorů často vyžadují lehké, vysoce odolné materiály a optimalizovaný tepelný management. 3D tištěné chladiče, často vyrobené ze specializovaných hliníkových nebo měděných slitin, tyto požadavky splňují a nabízejí přizpůsobené chlazení v těsně zabalených prostorech pro avioniku.
- Pohon dronu: Motory s vysokou hustotou výkonu v dronech a bezpilotních letadlech významně využívají lehká a účinná řešení chlazení. 3D tištěné chladiče umožňují delší dobu letu a vyšší nosnost.
- Chlazení radaru a elektroniky: Pozemní a vzdušné elektronické systémy produkují značné množství tepla. Vlastní chladiče AM poskytují účinné tepelné cesty.
- Průmyslová automatizace a robotika:
- Servomotory a pohony: Přesné pohyby v robotice a automatizovaných montážních linkách jsou závislé na motorech, které pracují konzistentně. Přehřátí může vést k chybám při polohování a zkrácení životnosti součástek. Chlazení průmyslové automatizace řešení využívající 3D tištěné chladiče zajišťují tepelnou stabilitu, zvyšují přesnost a dobu provozu.
- Motory s vysokým točivým momentem: Motory používané v těžkých zdvihacích nebo nepřetržitě pracujících strojích vytvářejí značné množství tepla. AM umožňuje použití robustních chladičů integrovaných přímo do skříně motoru nebo chladicího systému.
- Výrobní zařízení: Motory v CNC strojích, dopravníky a další tovární zařízení těží z lepšího tepelného managementu, který poskytují 3D tištěná řešení na zakázku.
- Lékařské přístroje:
- Chirurgické roboty a nástroje: Motory v lékařské robotice vyžadují přesné řízení a vysokou spolehlivost. Často je nutné kompaktní a účinné chlazení, takže ideální řešení představují chladiče vytištěné na 3D tiskárně.
- Lékařské zobrazovací zařízení (MRI/CT skenery): Součásti těchto systémů mohou využívat motory, které vyžadují specifické profily tepelného managementu, dosažitelné pomocí speciálních chladičů AM.
- Vysoce výkonná výpočetní technika a elektronika:
- Kapalinové chladicí systémy: Nejedná se sice o elektromotory, ale principy platí. 3D tisk umožňuje vytvářet složité chladicí desky a rozdělovače pro přímé kapalinové chlazení výkonných procesorů a elektroniky a posouvat tak hranice výkonu.
Proč je přizpůsobení důležité:
Klíčovou výhodou těchto aplikací je možnost vytvářet řešení chladičů na zakázku. Na rozdíl od hotových chladičů mohou být 3D tištěné verze:
- Dokonale konformní: Jsou navrženy tak, aby přesně odpovídaly tvaru skříně motoru nebo specifickým horkým místům.
- Integrované: V kombinaci s dalšími funkčními prvky, jako jsou držáky nebo přípojky kapalin.
- Optimalizováno: Přizpůsobené pro specifické průtoky (chlazení kapalinou) nebo proudění vzduchu (chlazení vzduchem).
- Odlehčené: Využití optimalizace topologie a mřížkových struktur ke snížení hmotnosti bez snížení tepelného výkonu.
Manažeři pro zadávání veřejných zakázek vysoce výkonné chlazení motoru komponenty by si měly uvědomit, že 3D tisk z kovu nabízí cestu k řešením, která nejsou jen náhradou tradičních dílů, ale významným vylepšením, umožňujícím vyšší výkon a větší flexibilitu konstrukce v mnoha náročných odvětvích. Identifikace výrobci chladičů s osvědčenými odbornými znalostmi v oblasti AM je klíčem k efektivnímu využití této technologie.
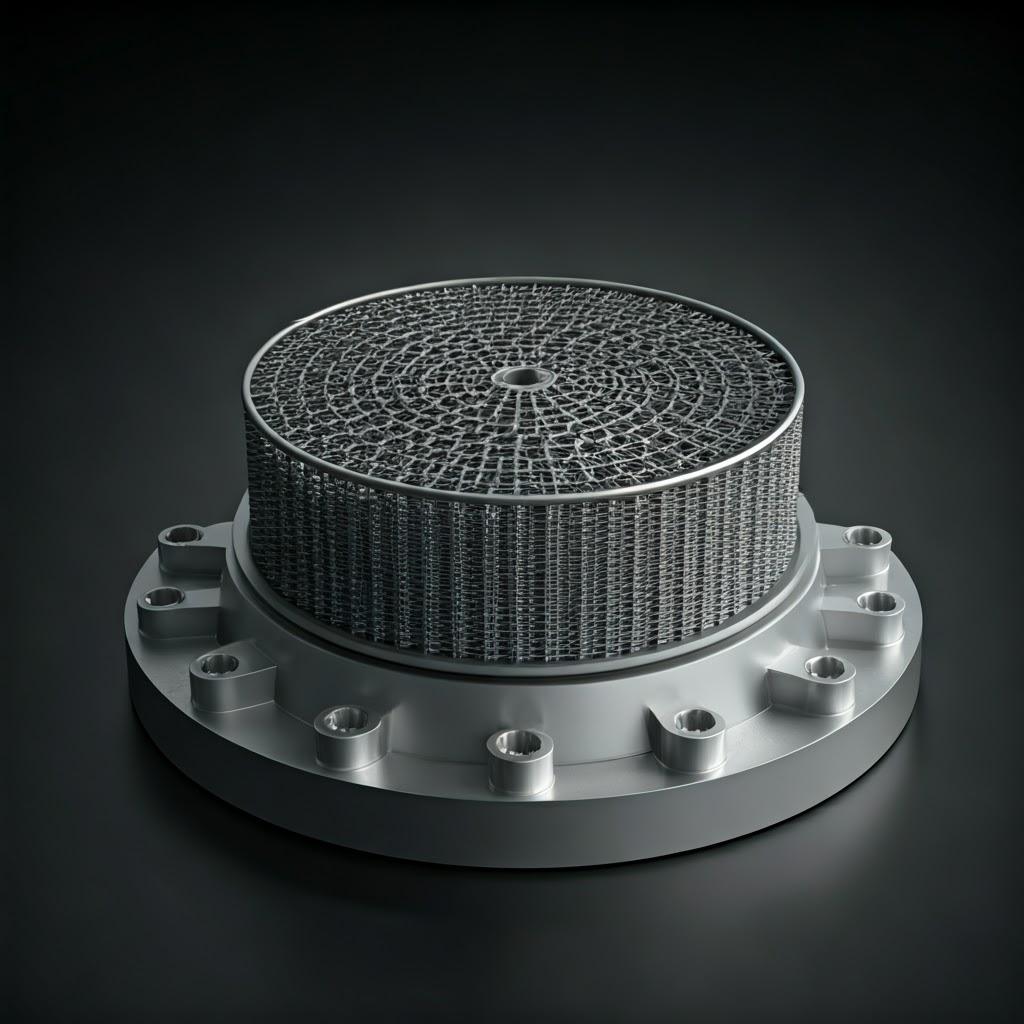
Proč používat 3D tisk z kovu pro chladiče elektromotorů? Aditivní výhoda
Výběr aditivní výroby kovů (AM) pro výrobu chladičů elektromotorů není jen o přijetí nové technologie, ale o využití výrazných výhod, které přímo řeší omezení tradičních výrobních metod (jako je odlévání, vytlačování a obrábění) v kontextu pokročilého tepelného managementu. Pro inženýry, kteří navrhují elektromotory nové generace, a specialisty na nákup vysoce výkonných komponent je pochopení těchto výhod zásadní pro přijímání informovaných rozhodnutí. Výhoda aditivních technologií se projevuje ve vynikajícím výkonu, nižší hmotnosti, rychlejších vývojových cyklech a rozšířených možnostech konstrukce.
Zde je přehled důvodů, proč je kovový 3D tisk stále více preferovanou metodou pro náročné aplikace chladičů:
- Bezkonkurenční volnost návrhu pro složité geometrie:
- Problém s tradičními metodami: Vytlačování omezuje konstrukce na 2,5D tvary s rovnými žebry. Odlévání umožňuje větší složitost, ale bez složitého (a nákladného) nástrojového vybavení se potýká s tenkými stěnami, složitými vnitřními kanály a podřezáváním. Obrábění složitých vnitřních prvků je často nemožné nebo vyžaduje sestavení více dílů.
- Výhoda AM: 3D tisk vytváří díly vrstvu po vrstvě, což umožňuje vytvářet vysoce kvalitní díly složité geometrie chladičů. To zahrnuje:
- Vnitřní chladicí kanály: Důmyslné, hladce zakřivené kanály pro chlazení kapalinou mohou být integrovány přímo do těla chladiče a kopírují obrysy zdrojů tepla motoru pro dosažení maximální účinnosti.
- Trojnásobně periodické minimální plochy (TPMS) & mřížkové struktury: Tyto složité porézní struktury nabízejí obrovský poměr povrchu k objemu, což je ideální pro zlepšení konvektivního přenosu tepla v aplikacích chlazených vzduchem i kapalinou. Jejich tradiční výroba je prakticky nemožná.
- Tvarové návrhy: Chladiče lze tvarovat tak, aby dokonale obepínaly skříň motoru nebo konkrétní součásti, minimalizovaly tepelný odpor a zlepšily odvod tepla.
- Optimalizované tvary ploutví: Ploutve lze navrhovat s proměnlivou tloušťkou, zakřivením a hustotou, přesně vyladěné pomocí simulace pro optimální proudění vzduchu nebo interakci s proudící kapalinou.
- Optimalizace topologie a odlehčení:
- Problém s tradičními metodami: Konstrukce jsou často nadměrně konstruovány s rovnoměrným rozložením materiálu, protože odstranění materiálu přesně tam, kde není potřeba, je obtížné nebo nákladné.
- Výhoda AM:Optimalizace topologie software dokáže analyzovat tepelné a konstrukční zatížení chladiče a algoritmicky určit nejefektivnější rozložení materiálu. Technologie AM pak dokáže vyrobit tyto optimalizované, často organicky vypadající konstrukce. To vede k:
- Výrazné snížení hmotnosti: Odstranění nepotřebného materiálu výrazně snižuje hmotnost součástek, což je důležité v leteckém a automobilovém průmyslu (zejména u elektrických vozidel) a v robotice.
- Úspora materiálu: Méně použitého materiálu znamená nižší náklady na suroviny, což je důležité zejména při použití dražších vysoce vodivých slitin, jako je měď.
- Vylepšený výkon systému: Lehčí komponenty přispívají k lepší celkové dynamice a účinnosti systému (např. větší dojezd vozidla, rychlejší pohyby robota).
- Zvýšená tepelná účinnost:
- Problém s tradičními metodami: Konstrukční omezení často vedou k neoptimálním tepelným cestám a nižší celkové kapacitě odvodu tepla při daném objemu nebo hmotnosti. Spojení více částí (např. základní desky a žeber) přináší tepelný kontaktní odpor.
- Výhoda AM: Schopnost vytvářet složité vnitřní struktury, konformní konstrukce a integrovat prvky, jako jsou turbulátory nebo optimalizovaná pole žeber, vede k tomu, že lepší tepelná účinnost.
- Cílené chlazení: Teplo lze účinněji odvádět z konkrétních horkých míst.
- Větší plocha povrchu: Mřížkové struktury a složité konstrukce žeber maximalizují plochu pro přenos tepla v daném objemu.
- Snížený tepelný odpor: Jednodílná konstrukce eliminuje kontaktní odpor mezi spojovanými díly. Často se uvádí nárůst výkonu o 20-50 % nebo více ve srovnání s tradičně vyráběnými chladiči podobné velikosti.
- Rychlá tvorba prototypů a opakování návrhu:
- Problém s tradičními metodami: Vytváření prototypů často vyžaduje speciální nástroje (formy, zápustky) nebo rozsáhlé nastavení obrábění. Iterace návrhu je pomalá a nákladná, což brání optimalizaci.
- Výhoda AM: AM umožňuje rychlé prototypování chladičů přímo z modelů CAD.
- Rychlost: Funkční kovové prototypy lze často vyrobit během několika dnů, nikoli týdnů či měsíců.
- Efektivita nákladů: Pro prototypy nebo malosériovou výrobu není třeba investovat do nástrojů.
- Flexibilita: Návrhy lze snadno upravovat a znovu tisknout, což inženýrům umožňuje rychle testovat a ověřovat různé strategie chlazení (např. různá provedení kanálů, vzory žeber nebo hustotu mřížky). To výrazně urychluje vývojový cyklus výrobku.
- Konsolidace částí:
- Problém s tradičními metodami: Složité chladicí sestavy často vyžadují více komponent (základna chladiče, žebra, držáky, rozdělovače, konektory), které je třeba vyrobit samostatně a poté je smontovat.
- Výhoda AM: 3D tisk umožňuje sloučit více funkcí do jediného monolitického dílu. Například montážní prvky, vstupní/výstupní otvory pro kapaliny a strukturu výměny tepla lze vytisknout jako jeden kus. Tím se snižuje:
- Doba montáže a náklady na práci.
- Potenciální místa úniku (u kapalinou chlazených systémů).
- Složitost počítání dílů a řízení zásob.
- Celková hmotnost a objem systému.
- Umožnění pokročilých materiálů:
- Problém s tradičními metodami: Některé vysoce výkonné materiály, zejména některé slitiny mědi optimalizované z hlediska tepelné vodivosti a pevnosti, lze obtížně nebo nákladně odlévat nebo přesně obrábět do složitých tvarů.
- Výhoda AM: Procesy fúze v práškovém loži (PBF), jako je selektivní laserové tavení (SLM) nebo tavení elektronovým svazkem (EBM), jsou vhodné pro zpracování řady pokročilých kovových prášků, včetně specializovaných slitiny mědi (např. CuCrZr) a slitiny hliníku (jako AlSi10Mg), přizpůsobené pro tepelné aplikace. Společnosti jako Met3dp využívají pokročilé techniky výroby prášků (např. plynovou atomizaci) k výrobě sférických prášků s vysokou tekutostí, které jsou ideální pro dosažení hustých a vysoce výkonných dílů AM.
Tradiční vs. aditivní výroba chladičů: Srovnávací přehled
Vlastnosti | Tradiční výroba (odlévání, vytlačování, obrábění) | Aditivní výroba kovů (3D tisk) | Výhoda AM |
---|---|---|---|
Geometrická složitost | Omezené (zejména vnitřní funkce) | Velmi vysoká (vnitřní kanály, mřížky, organické tvary) | Umožňuje optimalizované, konformní provedení pro vynikající tepelný výkon. |
Optimalizace topologie | Obtížné / nepraktické | Snadno použitelné | Významný potenciál odlehčení, úspora materiálu. |
Konsolidace částí | Obtížné / vyžaduje montáž | Možnost integrace více funkcí do jednoho dílu | Nižší náklady na montáž, méně netěsných míst, nižší počet dílů. |
Rychlost prototypování | Pomalé (vyžaduje nástroje/nastavení) | Rychle (přímo z CAD) | Urychluje iteraci a ověřování návrhu. |
Náklady na nástroje | Vysoká (zejména u složitých tvarů nebo malých objemů) | Žádný | Cenově výhodné pro zakázkové díly, prototypy a malé až střední objemy. |
Materiálový odpad | Vysoká (obrábění – subtraktivní) | Nízká (aditivní – používá pouze potřebný materiál + recyklovatelný prášek) | Udržitelnější, v některých případech nižší efektivní náklady na materiál. |
Tepelný výkon | Dobré, ale často omezené vyrobitelností | Potenciálně vynikající (optimalizované návrhy, komplexní funkce) | Vyšší schopnost odvodu tepla při dané velikosti/hmotnosti. |
Dodací lhůta (výroba) | Může být rychlý pro velké objemy (vytlačování), pomalý (odlévání) | Mírná, škálovatelná podle kapacity stroje | Konkurenceschopné pro složité díly, potenciálně rychlejší pro malé/střední objemy. |
Možnosti materiálu | Široký sortiment, ale některé slitiny se obtížně zpracovávají | Rozšiřující se sortiment, vyniká specifickými slitinami optimalizovanými pro AM | Umožňuje použití vysoce výkonných slitin Cu/Al pro tepelný management. |
Export do archů
Shrnuto, rozhodnutí použít kovový 3D tisk pro chladiče elektromotorů je dáno potřebou výkonnostních charakteristik, které překračují hranice tradiční výroby. Pro manažery nákupu a inženýry, kteří hodnotí řešení tepelného managementu, nabízí výhoda aditivních technologií přesvědčivou cestu k vytváření lehčích, účinnějších a vysoce přizpůsobených součástí, které jsou nezbytné pro novou generaci elektromotorů. Spolupráce se znalými Poskytovatel služeb metal AM je klíčem k uvolnění tohoto potenciálu.
Doporučené materiály pro 3D tištěné chladiče: CuCrZr & AlSi10Mg Deep Dive
Výběr správného materiálu je zásadní pro výkon každého chladiče, zejména těch, které jsou vyráběny aditivní výrobou kovů. Jeho výběr přímo ovlivňuje tepelnou vodivost, mechanickou pevnost, hmotnost, odolnost proti korozi, možnost tisku a v konečném důsledku i cenu. U 3D tištěných chladičů elektromotorů vynikají dva materiály díky vynikající rovnováze vlastností: Měď, chrom, zirkon (CuCrZr) a Hliník křemík hořčík (AlSi10Mg). Pochopení nuancí těchto slitin je pro inženýry, kteří specifikují komponenty, a manažery nákupu, kteří zajišťují materiály nebo služby, zásadní.
Proč záleží na výběru materiálu u chladičů AM:
- Tepelná vodivost: Hlavní funkcí chladiče je odvádět teplo od zdroje. Vyšší tepelná vodivost umožňuje účinnější přenos tepla.
- Mechanické vlastnosti: Chladič musí odolávat provoznímu namáhání, vibracím a montážním silám. Důležitými faktory jsou pevnost, tvrdost a odolnost proti únavě.
- Hmotnost: Materiály s nižší hustotou přispívají k odlehčení zejména v automobilovém a leteckém průmyslu.
- Možnost tisku: Ne všechny slitiny lze snadno zpracovávat pomocí AM. Kvalitu a proveditelnost tisku ovlivňují faktory jako absorpce laseru, stabilita taveniny, chování při tuhnutí a náchylnost k praskání.
- Následné zpracování: Požadavky na tepelné zpracování, povrchovou úpravu nebo obrábění se u jednotlivých materiálů liší a mají vliv na konečné vlastnosti a náklady.
- Náklady: Náklady na práškové suroviny a složitost/rychlost tiskového procesu ovlivňují konečnou cenu dílu.
Projděme si specifika doporučených prášků:
1. Měď, chrom, zirkon (CuCrZr) – šampion ve vysoké vodivosti
CuCrZr je precipitačně kalitelná slitina mědi, která je známá pro svou vynikající kombinaci vysoké tepelné a elektrické vodivosti, dobré mechanické pevnosti (zejména při zvýšených teplotách) a odolnosti proti měknutí.
- Klíčové vlastnosti a výhody:
- Výjimečná tepelná vodivost: Obvykle >300 W/(m-K) po vhodném tepelném zpracování. To je výrazně vyšší hodnota než u hliníkových slitin a většiny ocelí, což umožňuje vysoce účinný odvod tepla a potenciálně kompaktnější konstrukci chladiče při daném požadavku na chlazení.
- Vysoká elektrická vodivost: Často přesahuje 80 % IACS (International Annealed Copper Standard). Ačkoli pro samotnou funkci chladiče není tak kritická, může být výhodná, pokud součást plní sekundární elektrickou úlohu nebo se nachází v těsné blízkosti vodivých prvků.
- Dobrá mechanická pevnost: Díky srážecímu kalení (tepelnému zpracování) dosahuje slušné pevnosti v tahu a tvrdosti, takže je vhodný pro aplikace s mírným mechanickým zatížením. Zachovává si pevnost lépe při zvýšených teplotách ve srovnání s čistou mědí nebo některými slitinami hliníku.
- Odolnost vůči stresu a relaxaci: Důležité pro udržení upínacích sil, pokud je chladič součástí šroubové sestavy pracující při vyšších teplotách.
- Výzvy a úvahy:
- Možnost tisku: Tisk měděných slitin pomocí laserové technologie PBF může být náročný kvůli vysoké odrazivosti a tepelné vodivosti mědi, což může vést k nestabilním taveninám nebo vyžadovat vysoký výkon laseru. Optimalizace parametrů procesu je rozhodující. Tavení elektronovým svazkem (EBM) může být někdy pro měď výhodné.
- Náklady: Prášky ze slitin mědi jsou obecně dražší než prášky ze slitin hliníku.
- Hustota: Měď je výrazně hustší (~8,9 g/cm³) než hliník (~2,7 g/cm³), takže je méně vhodná pro aplikace, kde je hmotnost naprosto zásadním omezením, pokud ovšem lepší tepelný výkon neumožňuje mnohem menší konstrukci.
- Následné zpracování: K dosažení optimálních vlastností vyžaduje specifické cykly tepelného zpracování (rozpuštění a stárnutí). Náročné může být také odstranění podpory.
- Typické aplikace: Náročné aplikace vyžadující maximální tepelný výkon v omezeném objemu, chlazení vysoce výkonné elektroniky, výměníky tepla s omezeným prostorem, indukční cívky, odporové svařovací elektrody (využívající i elektrickou vodivost). Ideální pro vysoce výkonné chlazení motoru kde je tepelná zátěž extrémní.
- Výhoda Met3dp: Pro úspěšný tisk je zásadní získávání vysoce kvalitního prášku CuCrZr. Společnost Met3dp využívá pokročilé techniky plynové atomizace k výrobě sférických prášků CuCrZr s vynikající tekutostí a konzistentní distribucí velikosti částic, optimalizovaných pro procesy AM. Jejich odborné znalosti zajišťují, že prášky splňují přísné požadavky na hustotu a výkon v náročných tepelných aplikacích.
2. Hliník, křemík, hořčík (AlSi10Mg) – univerzální lehký materiál
AlSi10Mg je jednou z nejběžnějších a nejpoužívanějších hliníkových slitin používaných v kovové AM. Je to v podstatě slitina odlitků upravená pro aditivní výrobu, která nabízí dobrou rovnováhu tepelných vlastností, mechanické pevnosti, nízké hmotnosti a vynikající tisknutelnosti.
- Klíčové vlastnosti a výhody:
- Dobrá tepelná vodivost: I když je výrazně nižší než CuCrZr (obvykle v rozmezí 120-150 W/(m-K) po odlehčení napětí/tepelném zpracování), je stále podstatně lepší než oceli nebo titanové slitiny a dostačující pro mnoho aplikací chlazení motorů.
- Vynikající tisknutelnost: AlSi10Mg se poměrně snadno zpracovává pomocí laserové fúze v práškovém loži (LPBF/SLM). Má dobrou absorpci laseru a vytváří stabilní taveniny, což umožňuje spolehlivou výrobu jemných prvků a složitých geometrií.
- Nízká hustota: Díky hustotě přibližně 2,68 g/cm³ je ideální pro odlehčení aplikace v automobilovém a leteckém průmyslu a robotice.
- Dobrý poměr pevnosti a hmotnosti: Po vytištění nabízí slušné mechanické vlastnosti (mez kluzu, pevnost v tahu), které lze dále upravit tepelným zpracováním (např. T6).
- Odolnost proti korozi: Vykazuje dobrou odolnost proti atmosférické korozi.
- Efektivita nákladů: Prášky ze slitin hliníku jsou obecně levnější než slitiny mědi a rychlejší a zavedenější tiskové procesy přispívají k nižším celkovým nákladům na díl.
- Výzvy a úvahy:
- Nižší tepelná vodivost: Nelze použít pro slitiny mědi, kde je vyžadován extrémní tepelný tok nebo minimální teplotní spád. Chladiče mohou být ve srovnání s ekvivalentem CuCrZr při stejném tepelném zatížení větší.
- Nižší výkon při vysokých teplotách: Mechanické vlastnosti se výrazněji zhoršují při zvýšených teplotách ve srovnání s CuCrZr.
- Anizotropie: As-printed AlSi10Mg díly mohou vykazovat anizotropní mechanické vlastnosti (různá pevnost v závislosti na směru sestavení), což je třeba zohlednit při návrhu a může to vyžadovat specifické tepelné zpracování.
- Typické aplikace: Široká škála chladičů, u kterých je třeba najít dobrý poměr mezi výkonem, hmotností a cenou. Ideální pro Tepelný management elektromobilů komponenty (kryty motorů s integrovaným chlazením, chladiče měničů), součásti leteckých motorů tam, kde je hmotnost kritická, komponenty dronů a obecně chlazení průmyslové automatizace.
- Výhoda Met3dp: Met3dp poskytuje vysoce kvalitní prášek AlSi10Mg vhodný pro náročné aplikace. Jejich důraz na sféricitu prášku a řízenou distribuci velikosti částic zajišťuje dobrou hustotu a tekutost práškového lože, což vede k robustním a spolehlivým tištěným dílům. Jejich zkušenosti s různými tiskových metod jim umožňuje poradit s optimálními procesními parametry pro dosažení požadované hustoty a mechanických vlastností AlSi10Mg.
Průvodce výběrem materiálu: CuCrZr vs. AlSi10Mg pro chladiče
Vlastnosti | CuCrZr | AlSi 10Mg | Kritéria výběru |
---|---|---|---|
Tepelná vodivost | Vynikající (>300 W/(m-K)) | Dobrý (120-150 W/(m-K)) | Zvolte CuCrZr pro nejvyšší tepelný tok, minimální nárůst teploty a kompaktní provedení. |
Hustota | Vysoká (~8,9 g/cm³) | Nízká (~2,7 g/cm³) | Pro kritické aplikace odlehčování zvolte AlSi10Mg. |
Tisknutelnost (Laser PBF) | Náročné (odrazivost, vodivost) | Vynikající (dobře zavedený proces) | AlSi10Mg je obecně jednodušší/rychlejší spolehlivě tisknout. |
Mechanická pevnost | Dobrý (zejména při vysokých teplotách) | Dobrý (vynikající poměr pevnosti k hmotnosti) | Posuzujte na základě požadavků na provozní teplotu a zatížení. |
Náklady na suroviny | Vysoký | Mírný | AlSi10Mg nabízí nižší základní náklady na materiál. |
Následné zpracování (tepelné zpracování) | Požadováno (srážkové vytvrzování) | Volitelné/doporučené (úleva od stresu/T6) | Vezměte v úvahu složitost a náklady na tepelné zpracování. |
Primární výhoda | Maximální tepelný výkon | Lehká & Všestrannost | Přizpůsobte přínos nejkritičtějšímu požadavku aplikace. |
Export do archů
Závěr o materiálech:
Volba mezi CuCrZr a AlSi10Mg závisí do značné míry na specifických požadavcích elektromotoru a jeho provozním prostředí.
- Zvolte CuCrZr, když: Je zapotřebí absolutně maximální tepelný výkon, prostor je velmi omezený, provozní teploty jsou zvýšené a hmotnost je ve srovnání s odvodem tepla druhořadá.
- AlSi10Mg zvolte, když: Hlavním faktorem je nízká hmotnost, dobrý tepelný výkon, důležitá je cenová efektivita a je třeba spolehlivě tisknout složité geometrie.
Zásadní je spolupráce se znalým partnerem pro aditivní výrobu, jako je Met3dp, který rozumí jak materiálům, tak tiskovým procesům. Může vám poskytnout poradenství při výběru materiálu, optimalizaci konstrukce pro zvolený materiál a zajistit použití vysoce kvalitních materiálů optimalizovaných pro AM tisk kovové prášky pro výrobu spolehlivých a vysoce výkonných 3D tištěných chladičů přizpůsobených vašim specifickým potřebám chlazení elektromotorů. Manažeři veřejných zakázek, kteří hledají velkoobchod nebo hromadné dodávky těchto prášků nebo hotových součástí by měli hledat dodavatele s důkladnou kontrolou kvality a sledovatelností materiálu.
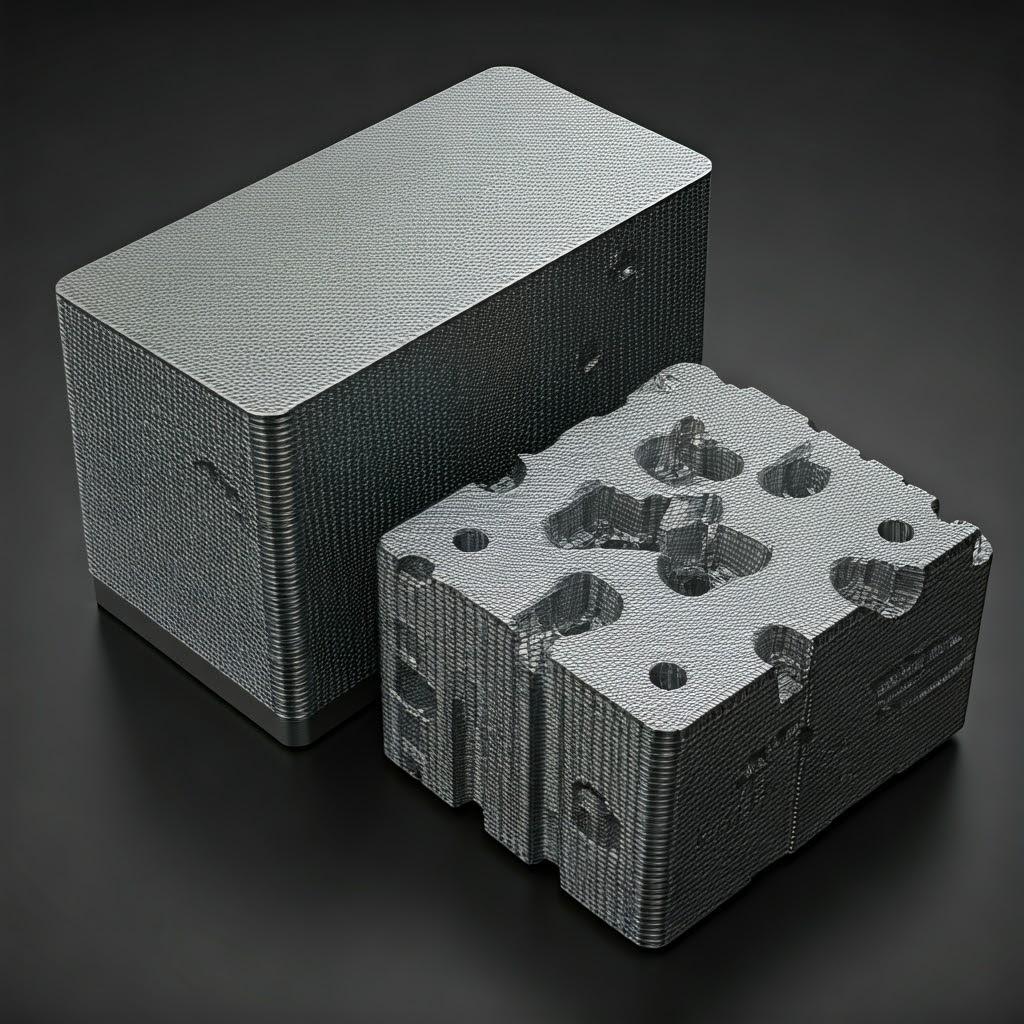
Úvahy o návrhu aditivně vyráběných chladičů
Skutečný potenciál kovového 3D tisku pro chladiče elektromotorů se odkrývá díky inteligentnímu designu - konkrétně designu pro aditivní výrobu (DfAM). Prostá replikace tradičně navrženého chladiče pomocí AM často přináší minimální výhody a může být dokonce kontraproduktivní. DfAM zahrnuje přehodnocení architektury součásti od základu s cílem využít jedinečné možnosti výroby po vrstvách, přičemž se zaměřuje na maximalizaci tepelného výkonu, minimalizaci hmotnosti a zajištění vyrobitelnosti. Inženýři a konstruktéři vytvářející průmyslové konstrukce chladičů pro AM musí zohlednit několik klíčových faktorů nad rámec těch, které jsou typické pro konvenční metody.
1. Přijměte geometrickou svobodu: Za hranice ploutví a bloků
- Optimalizace topologie (TO): Jedná se pravděpodobně o nejmocnější nástroj v arzenálu DfAM pro chladiče.
- Proces: Definujte návrhový prostor (maximální přípustný objem), nenávrhové oblasti (rozhraní, montážní body), zatěžovací stavy (tepelné zatížení, konstrukční síly), cíle (minimalizace hmotnosti, minimalizace tepelného odporu) a omezení (maximální napětí, minimální velikost prvku). Software TO pak iterativně odstraňuje materiál z oblastí s nízkým namáháním/malým vlivem a zanechává optimalizovanou, často organicky vypadající strukturu.
- Výhody: Významné odlehčení (běžné je snížení o 30-70 % ve srovnání se základními konstrukcemi) při zachování nebo dokonce zlepšení tepelných a konstrukčních vlastností. Snižuje spotřebu materiálu a dobu tisku.
- Nástroje: Software jako Altair Inspire, nTopology, Autodesk Fusion 360, Dassault Systèmes CATIA/SOLIDWORKS nabízí moduly TO.
- Úvahy: Optimalizované tvary může být složité čistě vymodelovat pro tisk; vyžaduje to pečlivé zpřesnění sítě a někdy i ruční přetvoření na základě výsledků TO. Ujistěte se, že optimalizace zohledňuje výrobní omezení (např. minimální velikost tisknutelného prvku, úhly převisu).
- Mřížkové struktury & Trojnásobně periodické minimální plochy (TPMS):
- Koncept: Místo pevného materiálu nahraďte vnitřní objemy nebo struktury žeber porézními, opakujícími se jednotkovými buňkami (mřížkami) nebo matematicky definovanými povrchy (TPMS jako Gyroid, Schwarz P, Diamond).
- Výhody: Drasticky zvyšuje poměr plochy k objemu, čímž zlepšuje konvekční přenos tepla pro chlazení vzduchem i kapalinou. Umožňuje řízenou pórovitost a charakteristiky proudění kapaliny. Vynikající pro odlehčení. Struktury TPMS nabízejí hladké, samonosné povrchy, které mohou být výhodné pro proudění kapalin a snížení koncentrace napětí ve srovnání s mřížkami na bázi vzpěr.
- Design: Zvolte typ, velikost a tloušťku vzpěry/stěny jednotkové buňky na základě požadovaného tepelného výkonu, průtoku kapaliny (tlakové ztráty), konstrukčních požadavků a možnosti tisku. Odstupňované mřížky (s různou hustotou) mohou dále optimalizovat výkon.
- Použití: Ideální pro vytváření vysoce účinných zón výměny tepla v chladicích deskách s kapalinovým chlazením nebo pro maximalizaci konvekce vzduchu v chladičích s nucenou nebo přirozenou konvekcí.
- Konformní chladicí kanály:
- Koncept: U kapalinou chlazených chladičů jsou vnitřní kanály navrženy tak, aby přesně kopírovaly obrysy součástí, které vytvářejí teplo (např. stator motoru, vinutí).
- Výhody: Minimalizuje vzdálenost, kterou musí teplo urazit, snižuje tepelný odpor, eliminuje horká místa a umožňuje rovnoměrnější chlazení ve srovnání s tradičními vrtanými nebo frézovanými kanály. Umožňuje chlazení v dříve nepřístupných oblastech.
- Pravidla pro navrhování: Zvažte průměr kanálu (vyvážení průtoku a tlakové ztráty), minimální tloušťku stěny mezi kanály a vnějšími povrchy, dosažitelné poloměry zakřivení (vyhnutí se ostrým ohybům) a integraci vstupních/výstupních otvorů. Hladké vnitřní povrchy jsou žádoucí pro minimalizaci tlakové ztráty.
2. Navrhování pro vyrobitelnost (The “A” in DfAM)
- Minimalizace podpůrných konstrukcí: V procesech PBF (Powder Bed Fusion) (jako je SLM/LPBF) jsou často nutné podpůrné konstrukce, které slouží k ukotvení dílů na konstrukční desce, k podepření převislých prvků (typicky úhly pod 45 stupňů od vodorovné roviny) a k odvodu tepla. Prodlužují však dobu tisku, spotřebovávají materiál, vyžadují následné zpracování pro odstranění a mohou poškodit povrch.
- Strategie:
- Orientace: Optimalizujte orientaci dílů na konstrukční desce, abyste minimalizovali rozsah a složitost převisů.
- Samonosné úhly: Pokud je to možné, navrhněte prvky s úhly většími než 45 stupňů.
- Interní kanály: Kanály navrhněte s průřezem ve tvaru slzy nebo kosočtverce namísto kruhového, aby byly samonosné.
- Obětní funkce: Zahrnout prvky určené k pozdějšímu opracování, které mohou sloužit jako podpěry během tisku.
- Přístupnost: Zajistěte, aby byly nosné konstrukce přístupné pro snadné odstranění (ručně nebo obráběním).
- Strategie:
- Tloušťka stěny a velikost prvků:
- Minimální požadavky: Existují praktické limity pro spolehlivý tisk tenkých stěn nebo jemných prvků. To závisí na materiálu (např. AlSi10Mg obecně umožňuje jemnější rysy než CuCrZr kvůli stabilitě taveniny), velikosti laserového bodu nebo charakteristikách paprsku a procesních parametrech. Typická minimální tloušťka stěny by mohla být 0,3-0,5 mm, ale to je třeba ověřit u výrobce Poskytovatel služeb metal AM.
- Maximální hodnoty: Velmi tlusté masivní profily mohou kumulovat zbytkové napětí a potenciálně vést k deformaci nebo praskání. Začlenění vnitřních dutin nebo mřížkových struktur může tento problém zmírnit.
- Důslednost: Vyhněte se náhlým změnám průřezu, které mohou zhoršit tepelné namáhání. Používejte velkorysé kuželosečky a poloměry.
- Řízení zbytkového stresu: Tepelné cykly během tisku vytvářejí vnitřní pnutí.
- Dopad designu: Ostré rohy, velké rovné plochy rovnoběžné s konstrukční deskou a rychlé změny geometrie mohou zvýšit zbytkové napětí. Při návrhu na tyto faktory myslete.
- Zmírnění: Klíčové jsou správné podpůrné strategie, optimalizovaná orientace a tepelné úpravy po tisku (o nichž bude řeč později).
3. Návrh řízený simulací:
- CFD (výpočetní dynamika tekutin): Zásadní pro optimalizaci výkonu chladiče. Simulujte proudění kapaliny (vzduchu nebo kapaliny) přes geometrii chladiče a předpovídejte tlakové ztráty, rozložení proudění, rychlostní profily a koeficienty přestupu tepla. Iterujte návrhy na základě výsledků CFD, abyste maximalizovali účinnost chlazení.
- Analýza konečných prvků (FEA): Analyzujte tepelné namáhání, mechanické namáhání při zatížení a vibrační odezvu. Zajistěte, aby konstrukce odolala provozním podmínkám. Metoda konečných prvků je také klíčová pro nastavení a validaci optimalizace topologie.
- Simulace procesu sestavování: Specializovaný software dokáže simulovat samotný proces výroby AM a předpovídat potenciální problémy, jako je zkreslení, přehřátí převisů nebo pády lopatek (rušení recoateru). To umožňuje preventivní úpravy konstrukce nebo optimalizaci parametrů sestavení a podpěr.
4. Úvahy o specifických materiálech:
- CuCrZr: Vysoká tepelná vodivost znamená, že se teplo rychle šíří, což může vyžadovat robustnější podpůrné konstrukce pro řízení tepla během stavby. Jeho odrazivost může vyžadovat specifické parametry nebo strategie laseru. Konstrukce by měly zohledňovat objemové změny během tepelného zpracování při srážkovém kalení.
- AlSi10Mg: Obecně je tisk šetrnější. Nižší bod tání a dobrá absorpce laseru umožňují vyšší rychlost sestavování a potenciálně jemnější rysy. Při návrhu je třeba zvážit potřebu odlehčení od napětí nebo tepelného zpracování T6 pro dosažení požadovaných vlastností a rozměrové stability.
Služby a odbornost DfAM:
Úspěšné provedení těchto konstrukčních úvah často vyžaduje specializované znalosti. Spolupráce se společností, která nabízí komplexní 3D tisk z kovu řešení, jako je Met3dp, mohou být neocenitelná. Disponují odbornými znalostmi v oblasti principů DfAM, chování materiálů, simulací a optimalizace procesů a pomáhají klientům převést požadavky na výkon do tisknutelných, vysoce výkonných návrhů chladičů. Efektivní Služby DfAM překlenout mezeru mezi konceptem a úspěšnou aditivní výrobou.
Souhrnná tabulka: Klíčové úvahy DfAM pro chladiče AM
Úvaha | Klíčové akce a techniky | Benefit |
---|---|---|
Geometrická svoboda | Optimalizace topologie, mřížkové struktury/TPMS, konformní chladicí kanály | Maximalizace výkonu (tepelného/strukturálního), Odlehčení, Jedinečná funkčnost |
Minimalizace podpory | Optimalizace orientace, návrh samonosných úhlů/kanálů, zajištění přístupnosti | Zkrácení doby tisku/nákladů, Zjednodušení následného zpracování, Zlepšení povrchové úpravy |
Funkce/velikost stěny | Dodržujte minimální/maximální limity tisku, Zajistěte postupné přechody, Používejte filety | Zajištění tisknutelnosti, Zachování strukturální integrity, Snížení koncentrace napětí |
Zbytkové napětí | Vyhněte se velkým plochám/ostrým rohům, optimalizujte podpěry, naplánujte tepelné zpracování pro snížení napětí | Zabránit deformaci/praskání, Zajistit rozměrovou stabilitu |
Simulace | Použití CFD pro tepelné/teplotní vlastnosti, FEA pro konstrukční/tepelné namáhání, simulace stavby | Optimalizace návrhu před tiskem, předvídání výkonu, zmírnění chyb při sestavování |
Výběr materiálu | Návrh podle specifické potiskovatelnosti materiálu, tepelného chování a potřeb následného zpracování | Zajištění úspěšného tisku a dosažení požadovaných konečných vlastností |
Export do archů
Přijetím těchto zásad DfAM mohou výrobci plně využít výhod kovového 3D tisku a vytvořit chladiče elektromotorů nové generace, které svou účinností, hmotností a integrací předčí své tradiční protějšky.
Dosažitelná tolerance, povrchová úprava a rozměrová přesnost 3D tištěných chladičů
Přestože 3D tisk z kovu nabízí neuvěřitelnou geometrickou volnost, je pro konstruktéry a manažery nákupu zásadní mít realistická očekávání ohledně dosažitelných rozměrových tolerancí, povrchové úpravy a celkové přesnosti vytištěných dílů. Tyto faktory přímo ovlivňují uložení chladiče, jeho montáž, propojení s ostatními součástmi a případně i jeho fluidní dynamiku. Pochopení typických schopností a ovlivňujících faktorů procesů, jako je laserová fúze v práškovém loži (LPBF) a tavení elektronovým svazkem (EBM), je zásadní při specifikaci přesné komponenty AM.
1. Rozměrové tolerance:
- Obecná očekávání: Obecně platí, že u procesů PBF lze obvykle dosáhnout tolerancí srovnatelných s investičním litím kovů. Obecné tolerance se často uvádějí v rozmezí ±0,1 mm až ±0,2 mm pro prvních 25 mm a ±0,05 mm až ±0,1 mm pro každých dalších 25 mm, to však do značné míry závisí na konkrétní geometrii, velikosti, materiálu, kalibraci stroje a procesních parametrech.
- Normy ISO: Specifické toleranční normy pro AM se vyvíjejí, ale někteří výrobci se odvolávají na obecné toleranční normy, jako je ISO 2768 (střední ‘m’ nebo jemné ‘f’ třídy), jako na výchozí bod, ale specifické odchylky pro AM jsou běžné. Konkrétní požadavky na tolerance je nejlepší projednat s poskytovatelem AM služeb.
- Faktory ovlivňující toleranci:
- Kalibrace stroje: Přesnost systému polohování laserového/elektronového paprsku, kalibrace skeneru a kontrola tloušťky vrstvy.
- Vlastnosti materiálu: Tepelná roztažnost/smršťování při zahřívání a ochlazování, smršťování při tuhnutí a ochlazování na pokojovou teplotu. Různé slitiny se chovají různě.
- Tepelné namáhání: Zbytková napětí vzniklá během procesu mohou způsobit deformace a zkreslení, což ovlivní konečné rozměry.
- Geometrie dílu & Velikost: Větší díly a složité geometrie s různými průřezy je obecně obtížnější udržet v přísných tolerancích kvůli kumulativnímu napětí a tepelným vlivům.
- Podpůrné struktury: Způsob podepření dílu ovlivňuje jeho stabilitu během sestavování a případné deformace při demontáži.
- Orientace na stavbu: Směr, kterým je prvek vytvořen vzhledem k vrstvám, může ovlivnit jeho rozměrovou přesnost.
- Následné zpracování: Tepelné zpracování s uvolněním napětí může způsobit drobné rozměrové změny. Pro kritické tolerance jsou často nutné obráběcí operace.
- Kritické rozměry: U prvků, které vyžadují větší tolerance, než je možné dosáhnout ve stavu po sestavení (např. styčné plochy, uložení ložisek, připojení portů), se obvykle používá sekundární CNC obrábění. Pro tyto prvky je zásadní zahrnout do návrhu AM dodatečný materiál (přídavek na obrábění nebo zásoby). Jasně definujte kritické rozměry a tolerance pomocí geometrického dimenzování a tolerování (GD&T) na výkresech.
2. Povrchová úprava (drsnost):
- Drsnost povrchu podle stavu: Povrchová úprava kovových dílů vyrobených metodou AM je ze své podstaty drsnější než povrch obrobený. Je ovlivněn velikostí částic prášku, tloušťkou vrstvy, dynamikou taveniny a orientací konstrukce.
- Typické hodnoty (Ra):
- Boční stěny (svislé): Často hladší, Ra obvykle 6-15 µm.
- Horní plochy (směrem nahoru): Může být relativně hladký v závislosti na parametrech taveniny, Ra 5-12 µm.
- Spodní plochy (směrem dolů/podporované): Bývají nejhrubší v důsledku interakce s nosičem nebo částečného přilnutí roztaveného prášku, Ra se může pohybovat od 15 µm do více než 30 µm.
- Interní kanály: Často se obtížně dokončují po tisku a zachovávají si vyšší drsnost. To má vliv na pokles tlaku v kanálech pro kapaliny.
- Schodišťový efekt: Zakřivené nebo šikmé povrchy vytvořené po vrstvách vykazují charakteristický “schodovitý” efekt, který přispívá k drsnosti. Tenčí vrstvy tento efekt snižují, ale prodlužují dobu vytváření.
- Typické hodnoty (Ra):
- Zlepšení povrchové úpravy: Pokud je požadován hladší povrch z estetických důvodů, z důvodu zvýšení únavové životnosti nebo z důvodu dynamiky tekutin (snížení tření/poklesu tlaku v kanálech), používají se různé techniky následného zpracování:
- Tryskání abrazivem (kuličkové/ pískové): Poskytuje jednotný matný povrch, odstraňuje sypký pudr. Ra obvykle 5-10 µm.
- Třískové/vibrační dokončování: Používá média k vyhlazení povrchů a hran, zvláště efektivní pro dávky menších dílů.
- CNC obrábění: Poskytuje nejlepší kvalitu povrchu a přesnost pro specifické prvky.
- Leštění (ruční nebo automatické): Lze dosáhnout velmi hladkého, zrcadlového povrchu (Ra < 1 µm), ale je často pracný a závislý na geometrii.
- Elektrolytické leštění: Elektrochemický proces, který odstraňuje malou vrstvu materiálu a vyhlazuje povrchy, zvláště účinný u složitých tvarů a vnitřních kanálků, pokud lze řídit tok elektrolytu.
3. Rozměrová přesnost & Kontrola kvality:
- Ověření: Zajištění shody finálního dílu se specifikacemi vyžaduje robustní kontrola kvality tisku na kov postupy.
- 3D skenování: Bezkontaktní optické skenery (laserové nebo se strukturovaným světlem) porovnávají konečnou geometrii dílu s původním modelem CAD a vytvářejí mapu odchylek. Užitečné pro složité tvary.
- Souřadnicové měřicí stroje (CMM): Hmatová sonda umožňuje velmi přesné měření specifických prvků a rozměrů, což je nezbytné pro ověřování kritických tolerancí.
- Monitorování procesů: Monitorování taveniny, ukládání vrstev a tepelných podmínek v průběhu výroby na místě může poskytnout včasné informace o možných problémech s kvalitou.
- Nedestruktivní zkoušení (NDT): Techniky, jako je počítačová tomografie (CT), umožňují kontrolovat vnitřní vlastnosti a odhalovat vady, jako je pórovitost, aniž by došlo k poškození dílu.
- Dosažení vysoké přesnosti:
- Spolupráce: Úzká spolupráce mezi projektantem a poskytovatelem služeb AM (jako je Met3dp, který se zaměřuje na přesnost a spolehlivost) je klíčová. Projednejte kritické prvky, tolerance a vztažné souřadnice již na začátku procesu.
- Optimalizované nastavení sestavení: Pečlivé plánování orientace dílů, strategie podpory a parametrů sestavení.
- Charakteristika materiálu: Porozumění specifickému smršťování a tepelnému chování vybrané šarže prášku.
- Plánování následného zpracování: Navrhování s potřebným obráběcím materiálem a plánování vhodných kroků pro odlehčení napětí a dokončovací práce.
Souhrnná tabulka: Tolerance & Povrchová úprava kovových AM chladičů
Parametr | Typický rozsah ve stavu po dokončení | Ovlivňující faktory | Možnosti dodatečného zpracování | Úvahy |
---|---|---|---|---|
Rozměrová tolerance | ±0,1 až ±0,2 mm (počáteční) + další na délku | Stroj, materiál, geometrie, velikost, podpěry, orientace, tepelné namáhání | CNC obrábění (pro kritické prvky) | Zadejte kritické tolerance pomocí GD&T; Přidejte obráběcí materiál. |
Drsnost povrchu (Ra) | 5-30+ µm (velmi variabilní podle orientace povrchu) | Velikost prášku, tloušťka vrstvy, bazén taveniny, orientace, podpory | Tryskání, otryskávání, obrábění, leštění, elektrolytické leštění | Drsnost ovlivňuje průtok kapaliny (pokles tlaku); vnitřní kanály se obtížně dokončují. |
Rozměrová přesnost | Závisí na kontrolních faktorech | Kalibrace, řízení procesu, konzistence materiálu, stabilita po zpracování | 3D skenování, kontrola CMM, NDT (CT skenování) | Vyžaduje důkladnou kontrolu kvality; klíčová je spolupráce s poskytovatelem. |
Export do archů
Manažeři nákupu a inženýři, kteří zadávají 3D tištěné chladiče, by měli jasně sdělit své požadavky na tolerance a povrchovou úpravu. Ačkoli AM nabízí geometrickou volnost, dosažení přísných tolerancí a velmi hladké povrchové úpravy často vyžaduje zahrnutí kroků následného zpracování, jako je CNC obrábění, do výrobního plánu a rozpočtu. Spolupráce se zkušeným dodavatelem zajistí, že tyto požadavky budou pochopeny a splněny prostřednictvím optimalizovaného tisku a vhodných dokončovacích technik.
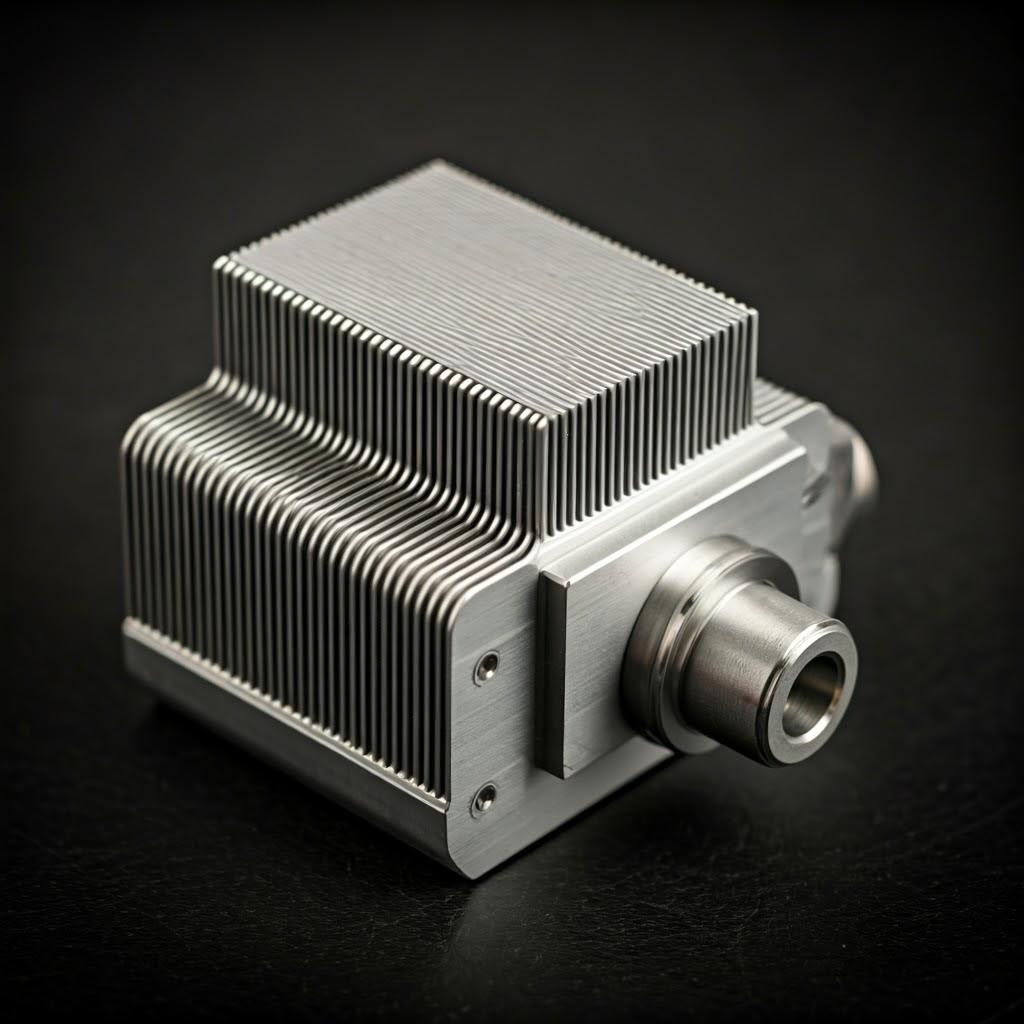
Základní kroky následného zpracování 3D tištěných kovových chladičů
Výroba kovového chladiče pomocí aditivní výroby nekončí, když se tiskárna zastaví. Součástka, která je čerstvě po vyjmutí z konstrukční desky, vyžaduje řadu nezbytných kroků následného zpracování, aby se z ní stala funkční a spolehlivá součástka splňující výkonnostní a kvalitativní specifikace. Tyto kroky jsou rozhodující pro uvolnění vnitřních pnutí, dosažení konečných rozměrů a povrchové úpravy, odstranění dočasných podpůrných struktur a optimalizaci vlastností materiálu. Pochopení tohoto pracovního postupu je zásadní pro přesný odhad nákladů, dodacích lhůt a zajištění toho, aby finální chladič fungoval tak, jak má.
Typický postup následného zpracování kovových AM chladičů (zejména při použití LPBF) zahrnuje:
- Odstranění prášku / zbavení prášku:
- Proces: Jakmile stavební komora vychladne, sejme se stavební deska s připojeným dílem (díly). Volný neroztavený prášek, který obklopuje díl a může být uvnitř dílu, je třeba opatrně odstranit. To se obvykle provádí pomocí vakuových systémů, kartáčů a stlačeného vzduchu v kontrolovaném prostředí, aby se cenný kovový prášek zachytil a mohl být znovu použit.
- Důležitost: Zajišťuje, aby žádný volný prášek nepřekážel v dalších krocích nebo nezůstával zachycený ve vnitřních kanálech (což je důležité pro průtok tekutiny). Důkladné čištění je nezbytné.
- Tepelné zpracování pro uvolnění napětí (často se provádí na stavební desce):
- Proces: V důsledku rychlých cyklů ohřevu a chlazení během tisku vznikají v dílu značná zbytková napětí. Aby se zabránilo deformaci nebo praskání při vyřezávání dílu z konstrukční desky, často se provádí tepelné zpracování pro uvolnění napětí před stěhování. Celá konstrukční deska s dílem (díly) se vloží do pece a zahřeje se na určitou teplotu (nižší než teplota stárnutí nebo žíhání, např. ~300 °C pro AlSi10Mg, vyšší pro CuCrZr, ale nižší než teplota rozpouštění), po určitou dobu se udržuje a poté se pomalu ochlazuje. Obvykle je nutná inertní atmosféra (argon, dusík), aby se zabránilo oxidaci.
- Důležitost: Snižuje vnitřní pnutí, čímž výrazně zlepšuje rozměrovou stabilitu pro další kroky a zabraňuje neočekávanému kroucení. Kritické pro zachování přesnosti.
- Vyjmutí dílu ze stavební desky:
- Proces: Díl odlehčený od napětí je třeba oddělit od stavební desky. Mezi běžné metody patří:
- Drátové elektroerozivní obrábění (EDM): Přesná metoda, vhodná pro složitá nebo jemná rozhraní, minimální mechanické namáhání.
- Pásová pila: Rychlejší a ekonomičtější metoda vhodná pro jednodušší rozhraní, ale přináší větší mechanickou sílu.
- Obrábění: Lze použít i frézování nebo soustružení.
- Důležitost: Uvolní jednotlivou část pro další zpracování. Zvolená metoda závisí na geometrii dílu, materiálu, požadované přesnosti v základně a na ceně.
- Proces: Díl odlehčený od napětí je třeba oddělit od stavební desky. Mezi běžné metody patří:
- Odstranění podpůrné konstrukce:
- Proces: Dočasné podpůrné konstrukce vytištěné pro ukotvení dílu a podpůrné převisy musí být odstraněny. To může být pracné.
- Ruční odstranění: Lámání nebo odřezávání podpěr pomocí ručního nářadí (kleště, štípací kleště). Možné u přístupných, slabších podpěr.
- CNC obrábění: Frézování nebo broušení podpěr, často vyžadované u robustních podpěr nebo kritických povrchů, kde došlo ke kontaktu s podpěrou.
- EDM: V některých případech lze použít pro nepřístupné vnitřní podpěry.
- Důležitost: Zásadní pro dosažení konečné geometrie a funkce dílu. Špatně odstraněné podpěry mohou zanechat stopy, ovlivnit tolerance nebo zablokovat vnitřní kanály. Klíčovou zásadou DfAM je konstrukce pro odstranění podpěr (DfSR).
- Proces: Dočasné podpůrné konstrukce vytištěné pro ukotvení dílu a podpůrné převisy musí být odstraněny. To může být pracné.
- Tepelné zpracování zlepšující vlastnosti (v závislosti na materiálu):
- Proces: Na rozdíl od odlehčování napětí je cílem tohoto kroku dosáhnout konečné požadované mikrostruktury a mechanických vlastností materiálu. Konkrétní cyklus závisí do značné míry na slitině:
- CuCrZr (srážkové kalení): Vyžaduje dvoufázový proces: 1) Žíhání roztoků: Zahřátí na vysokou teplotu (~950-1000 °C) za účelem rozpuštění chromu a zirkonia v měděné matrici a následné rychlé ochlazení. 2) Stárnutí: Přehřátí na nižší teplotu (~450-500 °C) po určitou dobu, aby se vytvořily precipitáty Cr a Zr, které výrazně zvyšují tvrdost, pevnost a tepelnou vodivost. Klíčové je přesné řízení teploty a času. Vyžaduje se inertní atmosféra.
- AlSi10Mg (úprava T6): Často zahrnuje: 1) Řešení Ošetření: Zahřívání (~520-540 °C) k rozpuštění sraženin Mg₂Si. 2) Kalení: Rychlé chlazení (vodou nebo polymerem) pro zachycení prvků v roztoku. 3) Umělé stárnutí: Přehřátím (~160-180 °C) se vysráží jemné částice Mg₂Si, čímž se zvýší pevnost a tvrdost. Odlehčení napětí může být dostačující, pokud je potřeba pouze rozměrová stabilita, nikoli špičková pevnost.
- Důležitost: Přizpůsobí vlastnosti materiálu (pevnost, tvrdost, vodivost, tažnost) požadavkům aplikace. To je často povinné pro dosažení datových vlastností slitin, jako je CuCrZr. Specializované stránky služby tepelného zpracování AM je zapotřebí poskytovatelů nebo vlastních kalibrovaných pecí.
- Proces: Na rozdíl od odlehčování napětí je cílem tohoto kroku dosáhnout konečné požadované mikrostruktury a mechanických vlastností materiálu. Konkrétní cyklus závisí do značné míry na slitině:
- Povrchová úprava & Povrchová úprava:
- Proces: V závislosti na požadavcích mohou být použity různé dokončovací kroky:
- Obrábění: CNC frézování nebo soustružení pro dosažení přísných tolerancí na styčných plochách, těsnicích plochách nebo připojeních portů. Vyžaduje pečlivý návrh přípravků pro potenciálně složité tvary AM.
- Tryskání abrazivem (kuličkami/pískem): Vytváří jednotný matný povrch, čistí povrchy.
- Obrábění / vibrační úprava: Vyhlazuje povrchy a hrany, odstraňuje otřepy.
- Leštění: Dosahuje hladkých povrchů s nízkým obsahem radiačního záření ve specifických oblastech.
- Eloxování (pro hliník): Zlepšuje odolnost proti korozi a opotřebení, může být dekorativní.
- Pokovování (nikl atd.): Může zvýšit odolnost proti opotřebení, ochranu proti korozi nebo pájitelnost.
- Důležitost: Dosáhne konečných rozměrových specifikací, požadované struktury povrchu (pro estetiku, tok nebo kontakt) a v případě potřeby přidá ochranné vrstvy.
- Proces: V závislosti na požadavcích mohou být použity různé dokončovací kroky:
- Čištění a kontrola:
- Proces: Závěrečné čištění za účelem odstranění veškerých obráběcích kapalin, tryskacích prostředků nebo zbytků. Komplexní kontrola pomocí metod, jako jsou souřadnicové měřicí přístroje, 3D skenování, vizuální kontroly a případně NDT (například CT skenování pro ověření vnitřních kanálů nebo detekci vad), zajistí, že díl před expedicí splňuje všechny specifikace.
- Důležitost: Zaručuje kvalitu dílů, rozměrovou přesnost a čistotu požadovanou pro danou aplikaci, což je obzvláště důležité u součástí, které přenášejí kapaliny.
Shrnutí pracovního postupu:
Build Plate -> Depowdering -> Stress Relief -> Part Removal -> Support Removal -> Heat Treatment (Properties) -> Finishing/Machining -> Cleaning & Inspection -> Final Part
Úvahy o zadávání veřejných zakázek:
Při pořizování 3D tištěných chladičů se musí manažeři nákupu ujistit, že potenciální dodavatelé mají potřebné vlastní kapacity nebo kvalifikované partnery pro všechny požadované kroky následného zpracování. Náklady a doba realizace spojené s těmito kroky mohou být značné a musí být zohledněny v celkovém rozsahu projektu. Vertikálně integrovaný dodavatel, jako je Met3dp, s odbornými znalostmi zahrnujícími prášky, tisk a případně koordinaci nezbytného následného zpracování, může tento složitý pracovní postup zefektivnit.
Běžné problémy při 3D tisku chladičů a strategie jejich řešení
Přestože aditivní výroba kovů otevírá neuvěřitelné možnosti pro konstrukci a výkon chladičů, není tento proces bez problémů. Pochopení potenciálních úskalí a zavedení účinných strategií jejich zmírnění je zásadní pro zajištění úspěšných konstrukcí, dosažení požadované kvality a zachování nákladové efektivity. Inženýři navrhující díly a manažeři nákupu vybírající dodavatele by si měli být těchto běžných problémů vědomi.
1. Deformace a zkreslení:
- Výzva: Výrazné teplotní gradienty během procesu tavení a tuhnutí po vrstvách vyvolávají v dílu zbytková napětí. Pokud tato napětí překročí mez kluzu materiálu nebo kotevní sílu podpěr, může se díl deformovat, zkroutit nebo dokonce oddělit od konstrukční desky. Zvláště náchylné jsou velké rovné plochy.
- Příčiny: Vysoké tepelné gradienty, nedostatečná podpora, velké průřezové plochy, nevhodné strategie skenování, vlastnosti materiálu (vysoká tepelná roztažnost).
- Strategie zmírnění dopadů:
- Optimalizovaná orientace: Orientace dílu tak, aby se minimalizovaly velké rovné plochy rovnoběžné s konstrukční deskou a snížila se koncentrace tepelné hmoty.
- Robustní podpůrné struktury: Použití dobře navržených podpěr (hustota, typ, umístění) pro pevné ukotvení dílu a účinné odvádění tepla. Zvažte tepelné podpěry speciálně navržené pro odvod tepla.
- Vytápění stavebních desek: Předehřívání konstrukční desky (běžné u LPBF, nezbytné u EBM) snižuje tepelné gradienty mezi dílem a deskou.
- Optimalizovaná strategie skenování: Používání specifických vzorů skenování laserem/paprskem (např. ostrovní skenování, šachovnicové vzory) pro řízení distribuce tepla a snížení lokálního nárůstu napětí.
- Úprava designu: Přidání žeber nebo zvlnění na velké rovné plochy, čímž se sníží náhlé změny tloušťky.
- Tepelné ošetření proti stresu: Provedení tohoto kroku před vyjmutím dílu má zásadní význam pro stabilizaci součásti (jak bylo uvedeno výše).
2. Pórovitost:
- Výzva: Přítomnost malých dutin nebo pórů v tištěném materiálu zhoršuje jeho hustotu, mechanické vlastnosti (zejména únavovou pevnost) a případně i tepelnou vodivost. Pórovitost může být vnitřní nebo povrchová.
- Příčiny:
- Problémy s procesními parametry: Nesprávný výkon laseru/paprsku, rychlost skenování nebo zaostření mohou vést k neúplnému roztavení (pórovitost bez fúze) nebo ke keyholingu (pórovitost způsobená zachycením plynu).
- Kvalita prášku: Nekvalitní prášek s nepravidelnými tvary, vnitřní pórovitostí nebo satelity může bránit rovnoměrnému roztírání a tavení prášku. Znečištěný prášek (např. vlhkostí) může při tavení uvolňovat plyn. Získávání vysoce kvalitní kovové prášky od renomovaných dodavatelů, jako je Met3dp, kteří využívají pokročilou atomizaci a kontrolu kvality.
- Zachycení plynu: Problémy se stínícím plynem (nesprávný průtok, kontaminace) mohou do bazénu taveniny propustit atmosférické plyny. Přispívat mohou i plyny rozpuštěné v prášku.
- Strategie zmírnění dopadů:
- Optimalizace parametrů: Vývoj a používání validovaných procesních parametrů specifických pro materiál, stroj a geometrii. To vyžaduje značné odborné znalosti.
- Kontrola kvality prášku: Použití vysoce kvalitního sférického prášku s dobrou tekutostí a nízkým obsahem vnitřního plynu. Zavedení správných protokolů pro manipulaci s práškem, jeho skladování a recyklaci.
- Řízení stínicího plynu: Zajištění inertního stínicího plynu vysoké čistoty (argonu nebo dusíku) s vhodnými průtoky a sledováním hladiny kyslíku v komoře.
- Izostatické lisování za tepla (HIP): Následný krok zpracování zahrnující vysoký tlak a teplotu k uzavření vnitřních pórů. Účinné, ale zvyšuje náklady a dobu realizace. Často se vyžaduje u kritických leteckých nebo lékařských součástí.
3. Obtíže při odstraňování podpůrné konstrukce:
- Výzva: Podpěry musí být dostatečně pevné, aby během tisku plnily svou funkci, ale zároveň se po tisku snadno odstraňovaly, aniž by poškodily povrch dílu nebo zanechaly nepřístupné zbytky, zejména ve složitých vnitřních kanálech.
- Příčiny: Příliš robustní konstrukce podpěr, špatná přístupnost, příliš silné přitmelení podpěr k dílu, choulostivé prvky dílu v blízkosti podpěr.
- Strategie zmírnění dopadů:
- DfAM pro snížení podpory: Navrhování dílů se samonosnými úhly (>45°) a optimalizace orientace pro minimalizaci potřeby podpěr.
- Chytrá konstrukce podpory: Použití typů podpěr (např. stromové podpěry, blokové podpěry se specifickými vrstvami rozhraní), které vyvažují pevnost a možnost demontáže. Softwarové nástroje nabízejí různé strategie.
- Plánování přístupnosti: Zajištění přístupu nástrojů (ručních nebo CNC) k podpěrám pro jejich demontáž.
- Výběr materiálu: Z některých materiálů se podpěry odstraňují snadněji než z jiných.
- Techniky následného zpracování: Použití vhodných metod odstraňování (ruční, obrábění, případně elektroerozivní obrábění).
4. Krakování (tuhnutí nebo kapalinové krakování):
- Výzva: Trhliny mohou vznikat během tuhnutí nebo v tepelně ovlivněné zóně v důsledku vysokého tepelného namáhání, zejména u slitin náchylných k trhání za tepla nebo ke vzniku kapalinových trhlin (jako jsou některé vysokopevnostní slitiny hliníku nebo niklu; méně časté, ale možné u AlSi10Mg za neoptimálních podmínek).
- Příčiny: Náchylnost materiálu, vysoké tepelné gradienty, vysoké zbytkové napětí, geometrie dílu (ostré rohy, rychlé změny tloušťky).
- Strategie zmírnění dopadů:
- Optimalizace parametrů: Jemné doladění parametrů laseru/paprsku pro řízení rychlosti chlazení.
- Řízení teploty ohřevu stavební desky / komory: Snížení tepelných gradientů.
- Úprava strategie skenování: Řízení přívodu tepla a akumulace stresu.
- Výběr/úprava slitiny: Volba slitin méně náchylných k praskání nebo použití modifikovaných složení, pokud je to možné.
- Změny designu: Používání krojů/radiů, vyhýbání se problematickým geometriím.
5. Problémy s povrchovou úpravou:
- Výzva: Dosažení požadované povrchové úpravy mohou bránit faktory vlastní procesu PBF.
- Schodiště: Nevyhnutelné na zakřivených/úhlových plochách kvůli vrstvení.
- Částečně roztavený prášek: Částice prášku volně ulpívající na povrchu směřujícím dolů nebo na bočních stěnách.
- Tvorba strusky: Tvorba oxidů nebo výtrysk taveniny vytvářející nedokonalosti povrchu.
- Strategie zmírnění dopadů:
- Optimalizace orientace: Budování kritických ploch vertikálně nebo jako horních ploch, kde je to možné.
- Tloušťka tenčí vrstvy: Snižuje počet kroků po schodech, ale prodlužuje dobu sestavení.
- Optimalizace parametrů: Přesné nastavení parametrů bazénu taveniny pro minimalizaci přilnavosti prášku a strusky.
- Následné zpracování: Použití vhodných dokončovacích technik (tryskání, otryskávání, obrábění, leštění) podle potřeby.
6. Zajištění kvality a konzistence:
- Výzva: Zajištění konzistentní kvality a vlastností jednotlivých dílů a šarží vyžaduje důslednou kontrolu a validaci procesu.
- Příčiny: Změny v kvalitě prášku, odchylky při kalibraci stroje, nestálé atmosférické podmínky, odchylky při následném zpracování.
- Strategie zmírnění dopadů:
- Robustní systém řízení kvality (QMS): Implementace normy ISO 9001 nebo norem specifických pro dané odvětví (AS9100 pro letecký průmysl).
- Monitorování procesů: Využití nástrojů pro monitorování in-situ ke sledování podmínek stavby.
- Sledovatelnost materiálu & Testování: Přísná kontrola šarží prášku, včetně testování vlastností.
- Kalibrace a údržba strojů: Pravidelné plány pro zajištění přesnosti stroje.
- Standardizované postupy: Zdokumentované postupy pro tisk a všechny kroky následného zpracování.
- Závěrečná kontrola & Testování: Komplexní rozměrové kontroly, nedestruktivní zkoušení a případné destruktivní zkoušky na vzorcích.
Úspěšné zvládnutí těchto výzev vyžaduje kombinaci správných konstrukčních postupů (DfAM), pečlivého výběru materiálu a manipulace s ním, přesné kontroly procesu, vhodného následného zpracování a robustní konstrukce zajištění kvality tisku na kov protokoly. Spolupráce se zkušeným poskytovatelem AM, který tyto potenciální problémy aktivně řeší, je pro manažery nákupu, kteří usilují o spolehlivou výrobu vysoce kvalitních 3D tištěných chladičů, klíčová.
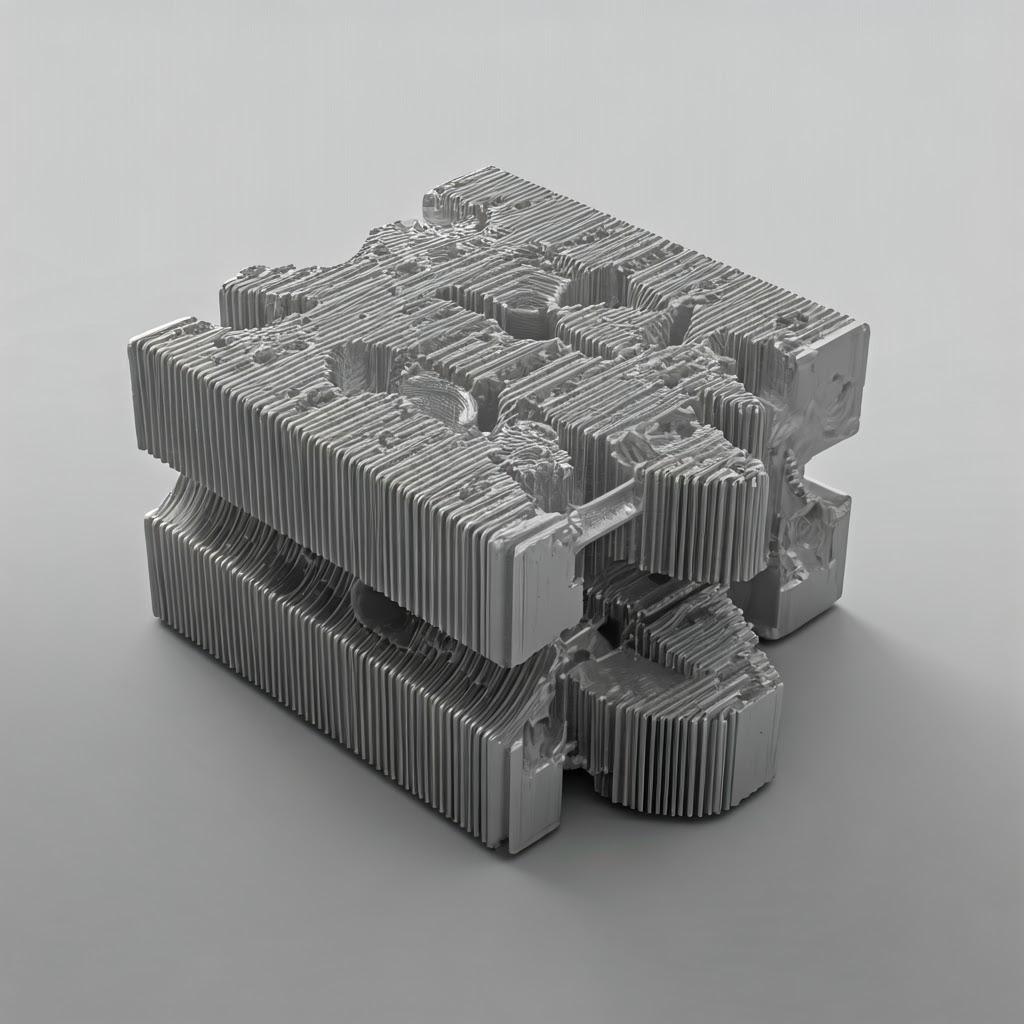
Jak vybrat správného poskytovatele služeb 3D tisku kovů pro chladiče
Výběr správného výrobního partnera je při implementaci 3D tištěných chladičů stejně důležitý jako výběr konstrukce a materiálu. Jedinečné požadavky na výrobu složitých komponent tepelného managementu pomocí aditivní výroby vyžadují specifické odborné znalosti a schopnosti. Pro manažery nákupu a inženýrské týmy, které se pouštějí do kvalifikace dodavatele AM kovů, je pro zajištění kvality, spolehlivosti a hodnoty nezbytný důkladný proces hodnocení. Výběr nevhodného dodavatele může vést ke zpoždění projektu, překročení rozpočtu a nekvalitním dílům, které nesplňují požadavky na výkon.
Zde jsou klíčová kritéria, která je třeba při výběru hodnotit poskytovatel služeb 3D tisku kovů pro chladiče elektromotorů:
1. Technické znalosti a technická podpora:
- Znalosti tepelného managementu: Rozumí poskytovatel principům přenosu tepla, dynamice kapalin a specifickým problémům chlazení elektromotorů? Může nabídnout poradenství DfAM přizpůsobené tepelnému výkonu?
- Hloubka vědy o materiálech: Mají prokazatelné zkušenosti s konkrétními slitinami, které potřebujete (CuCrZr, AlSi10Mg)? Rozumí nuancím tisku těchto materiálů a potřebnému následnému zpracování (zejména tepelnému zpracování) pro dosažení optimálních vlastností?
- Schopnost DfAM: Mohou vám pomoci s návrhem pro aditivní výrobu, včetně optimalizace topologie, generování mřížky, strategie podpory a simulace (CFD/FEA)?
- Řešení problémů: Mají zkušenosti s řešením problémů složitých sestav AM a hledáním řešení?
2. Vybavení, technologie & Kapacita:
- Portfolio strojů: Jaké typy strojů pro AM obrábění kovů provozují (např. LPBF, EBM)? Jsou tyto stroje vhodné pro zvolený materiál a velikost dílu? Mají moderní, dobře udržované a kalibrované vybavení? Společnost Met3dp například klade důraz na své špičkový objem, přesnost a spolehlivost tisku.
- Objem sestavení: Mohou jejich stroje vyhovět velikosti vašeho chladiče?
- Kapacita & amp; Škálovatelnost: Mají dostatečnou kapacitu strojů, aby zvládly vaše potřeby při výrobě prototypů a případně i při výrobě v malém nebo středním objemu? Jaká je jejich typická doba nevyřízených zakázek nebo fronty?
3. Materiálové schopnosti & Kontrola kvality:
- Získávání prášku a manipulace s ním: Získávají vysoce kvalitní prášky od renomovaných dodavatelů, nebo si je jako Met3dp vyrábějí sami pomocí pokročilých metod, jako je např technologie atomizace plynu a PREP? Jaké jsou jejich postupy pro kontrolu kvality prášku, manipulaci, skladování a sledovatelnost?
- Materiálové znalosti: Mohou prokázat úspěšné výtisky a zdokumentované vlastnosti materiálů CuCrZr a AlSi10Mg?
- Vývoj parametrů: Mají validované, optimalizované procesní parametry pro požadované materiály?
4. Možnosti následného zpracování:
- Komplexní pracovní postup: Dokáží řídit celý řetězec následného zpracování buď vlastními silami, nebo prostřednictvím přísně kvalifikovaných partnerů? To zahrnuje:
- Odlehčování napětí & razítko; tepelné zpracování (zásadně důležité: kalibrované pece, řízené atmosféry, ověřené cykly pro srážecí kalení/T6).
- Přesný díl a upnutí; odstranění podpory (elektroerozivní obrábění, pásová pila, obrábění).
- CNC obrábění (pro kritické tolerance a prvky).
- Povrchová úprava (tryskání, omílání, leštění atd.).
- Čištění & amp; Kontrola.
- Integrované služby: Poskytovatel, který nabízí kompletní sadu služeb, zjednodušuje dodavatelský řetězec a zajišťuje lepší kontrolu procesů.
5. Systém řízení kvality (QMS) & Certifikace:
- Formální QMS: Pracují podle certifikovaného systému řízení jakosti, jako je ISO 9001?
- Certifikace specifické pro dané odvětví: Jsou certifikovány pro příslušná odvětví (např. AS9100 pro letecký průmysl, ISO 13485 pro zdravotnictví)? Ačkoli tyto certifikace nejsou u průmyslových chladičů vždy vyžadovány, svědčí o vysoké úrovni řízení procesů a přísnosti.
- Dokumentace: Mohou poskytnout certifikace materiálu, certifikáty shody, inspekční zprávy a úplnou sledovatelnost?
6. Zkušenosti & Dosavadní výsledky:
- Relevantní projekty: Vyráběli úspěšně díly podobné složitosti, materiálu a použití (tepelné komponenty, díly pro automobilový/letecký/průmyslový průmysl)? Mohou poskytnout případové studie nebo reference?
- Roky v podnikání: Jak dlouho se specializují na AM kovy?
7. Komunikace, podpora & řízení projektů:
- Reakce: Reagují rychle na dotazy a poskytují technickou zpětnou vazbu?
- Jasná komunikace: Je komunikace profesionální, jasná a technicky správná?
- Řízení projektů: Mají strukturovaný přístup k řízení projektů, poskytování aktualizací a řešení případných problémů?
8. Náklady, doba realizace & Hodnota:
- Transparentní citování: Jsou jejich ceny jasné a podrobné, s rozdělením nákladů (materiál, strojní čas, práce, následné zpracování)?
- Konkurenční ceny: Jsou ceny konkurenceschopné vzhledem k trhu, s ohledem na kvalitu a nabízené služby? Dávejte si pozor na nabídky, které se zdají být příliš nízké, protože by mohly znamenat kompromisy v kvalitě nebo nezbytném následném zpracování.
- Spolehlivé dodací lhůty: Mohou poskytnout realistické odhady dodacích lhůt a prokázat, že je v minulosti dodržovali?
- Celková hodnota: Zvažte celkovou nabídku hodnoty, včetně odborných znalostí, kvality, spolehlivosti, podpory a zmírnění rizik, nejen jednotkovou cenu.
Souhrnná tabulka hodnocení:
Kritéria | Klíčové otázky | Úroveň důležitosti |
---|---|---|
Technické znalosti | Rozumíte termálnímu/DfAM? Hloubka materiálové vědy? Simulační schopnosti? | Velmi vysoká |
Vybavení & Technologie | Vhodné stroje? Objem stavby? Kalibrace? Kapacita/skalovatelnost? | Vysoký |
Materiálové schopnosti | Prokázané zkušenosti s CuCrZr/AlSi10Mg? Kontrola kvality prášku & manipulace? Optimalizace parametrů? | Velmi vysoká |
Následné zpracování | Vlastní/partnerské kapacity pro tepelné zpracování, obrábění, dokončovací práce, kontrolu? Integrovaný pracovní postup? | Velmi vysoká |
Systém kvality/certifikace | ISO 9001? Průmyslové certifikáty (AS9100)? Sledovatelnost? Dokumentace? | Vysoký |
Zkušenosti & Dosavadní výsledky | Dokončené podobné projekty? Zkušenosti v oboru? Případové studie/reference? | Vysoký |
Komunikace & amp; Podpora | Reakce? Srozumitelnost? Technická podpora? Projektové řízení? | Středně vysoké |
Náklady, doba realizace & hodnota | Transparentní ceny? Konkurenční? Spolehlivé dodací lhůty? Celková nabídka hodnoty? | Vysoký |
Export do archů
Výběr správného partner pro aditivní výrobu je strategické rozhodnutí. Společnosti jako Met3dp, které nabízejí komplexní řešení aditivní výroby zahrnující pokročilé tiskárny, vysoce kvalitní prášky a hluboké aplikační znalosti, představují typ vertikálně integrovaného partnera, který může snížit riziko zavádění AM pro kritické komponenty, jako jsou chladiče elektromotorů. Proveďte důkladnou prověrku, položte podrobné otázky a případně začněte s pilotním projektem, abyste ověřili schopnosti dodavatele, než se zavážete k větší sériové výrobě.
Pochopení nákladových faktorů a dodacích lhůt pro 3D tištěné chladiče
3D tisk z kovu umožňuje vytvářet chladiče s vynikajícím výkonem, ale pro plánování projektu, sestavování rozpočtu a řízení očekávání je zásadní pochopit související strukturu nákladů a typické dodací lhůty. Na rozdíl od tradiční výroby, kde u malých objemů často dominují náklady na nástroje, jsou náklady na AM přímo vázány na spotřebu materiálu, strojní čas a náročné následné zpracování.
Klíčové faktory nákladů na chladiče AM z kovu:
- Náklady na materiál:
- Cena prášku: Náklady na kilogram kovového prášku se výrazně liší podle slitiny. Slitiny mědi jako CuCrZr jsou podstatně dražší než slitiny hliníku jako AlSi10Mg. Vezměte v úvahu výkyvy na trhu.
- Část Objem: Skutečný objem finálního dílu přímo určuje množství spotřebovaného prášku. Klíčovou roli zde hraje optimalizace topologie a mřížkové struktury, které mohou snížit spotřebu materiálu ve srovnání s pevnými konstrukcemi.
- Objem podpůrné struktury: Na nákladech se podílí i materiál použitý na nosné konstrukce. Efektivní DfAM je minimalizuje.
- Práškový odpad/recyklace: Prášek lze sice recyklovat, ale v průběhu cyklů dochází ke ztrátám a degradaci, což se promítá do efektivních nákladů na materiál vypočítaných poskytovateli služeb.
- Strojový čas:
- Doba výstavby: To je často největší složka nákladů. Závisí na:
- Výška dílu (osa Z): Primárním motorem je tisk po vrstvách.
- Objem/hustota dílu: Větší nebo hustší díly vyžadují více naneseného materiálu na jednu vrstvu.
- Tloušťka vrstvy: Tenčí vrstvy zlepšují rozlišení, ale výrazně prodlužují dobu sestavení.
- Strategie skenování: Složité vzory skenování pro řízení napětí nebo jemných rysů mohou trvat déle.
- Počet dílů na sestavení: Efektivní vnoření více dílů na konstrukční desku lépe využívá strojní čas, čímž se snižují náklady na jeden díl velkoobjemová výroba AM.
- Provozní náklady stroje: Amortizace drahého AM zařízení, spotřeba energie (lasery/elektronové paprsky spotřebovávají značný výkon), spotřeba inertního plynu, údržba.
- Doba výstavby: To je často největší složka nákladů. Závisí na:
- Náklady na pracovní sílu:
- Nastavení a demontáž: Příprava stavební úlohy, nakládání prášku, vyjmutí stavební desky, počáteční čištění.
- Depowdering: Opatrně odstraňte uvolněný prášek z dílů.
- Práce po zpracování: Ta může být značná:
- Ruční odstranění podpory.
- Nastavení a provoz pro cykly tepelného zpracování.
- Nastavení a obsluha CNC obrábění.
- Ruční dokončovací práce (leštění, odstraňování otřepů).
- Úkoly inspekce a kontroly kvality.
- Náklady na následné zpracování (kromě mzdových nákladů):
- Tepelné zpracování: Doba pece, spotřeba energie, náklady na inertní plyn. Specifické cykly pro CuCrZr nebo AlSi10Mg vyžadují přesnou kontrolu.
- Obrábění: Čas potřebný pro CNC obrábění, náklady na nástroje, návrh/výroba přípravků, pokud jsou potřeba pro složité tvary.
- Dokončovací práce: Náklady na spotřební materiál (tryskací média, lešticí směsi), použití specializovaného zařízení (např. elektrolytické leštění).
- HIP (pokud je vyžadován): Lisování za tepla je nákladný proces, který se obvykle zadává specializovaným dodavatelům.
- Kontrolní nástroje: Náklady spojené s používáním souřadnicových měřicích strojů, 3D skenerů a zařízení NDT.
- Design & Engineering:
- DfAM & Simulace: Optimalizace návrhu pomocí optimalizace topologie, mřížkových struktur a simulace může výrazně snížit spotřebu materiálu a dobu tisku, a tím snížit výrobní náklady.
- Složitost: Vysoce složité návrhy mohou vyžadovat sofistikovanější plánování sestavení a případně větší podporu, což mírně zvyšuje nároky na nastavení a následné zpracování. AM však zvládá složitost mnohem hospodárněji než tradiční metody.
- Množství & Velikost dávky:
- Úspory z rozsahu: AM vykazuje úspory z rozsahu, ale jinak než metody hromadné výroby. Zřizovací náklady se amortizují v průběhu celé série. Plné stavební desky jsou nákladově efektivnější než částečně naplněné. Náklady na jeden díl obecně klesají s objemem, ale tento vztah je méně strmý než u metod zahrnujících tvrdé nástroje.
Srovnání nákladů (koncepční):
Vlastnosti | Kov AM (např. LPBF) | Tradiční (např. CNC obrábění ze sochorů) | Tradiční (např. tlakové lití) |
---|---|---|---|
Zpracování složitosti | Vynikající (náklady jsou méně citlivé na složitost) | Dobrý (náklady výrazně rostou se složitostí) | Spravedlivé (omezené možnostmi nástrojů) |
Náklady na nástroje | Žádný | Žádné (ale mohou být účtovány náklady na upevnění) | Velmi vysoká |
Náklady na díl (nízký objem) | Mírná až vysoká | Vysoká (zejména u složitých dílů) | Zakázaně vysoká |
Náklady na díl (vysoký objem) | Mírný (omezený pokles) | Mírný (výrazný pokles oproti nízkému objemu) | Velmi nízká (po amortizaci nástrojů) |
Materiálový odpad | Nízký | Vysoká (subtraktivní) | Nízká (proces odlévání) |
Sladké místo | Komplexní geometrie, Zakázkové díly, Prototypy, Low-Med Vol. | Středně složité díly, Středně vysoký objem. | Jednoduché až středně složité tvary, Velmi vysoký objem. |
Export do archů
Faktory doby realizace:
Doba realizace 3D tištěného chladiče je součtem několika fází:
- Citování & Zpracování objednávek: 1-5 dní (v závislosti na složitosti a reakci poskytovatele).
- Posouzení návrhu & Příprava stavby: 1-3 dny (kontroly DfAM, podpůrná strategie, vnořování, krájení).
- Čas fronty stroje: Velmi variabilní (0 dní až několik týdnů v závislosti na počtu nevyřízených žádostí).
- Doba tisku: Hodiny až několik dní (v závislosti na výšce dílu, objemu a množství).
- Chlazení & amp; Odprašování: 0.5-1 den.
- Následné zpracování: Velmi variabilní:
- Úleva od stresu: ~1 den (včetně doby pece).
- Odstranění dílu/podpory: Hodiny až dny (v závislosti na složitosti/metodě).
- Tepelné zpracování (vlastnosti): 1-3 dny (včetně cyklů v peci).
- Obrábění: Dny až týdny (v závislosti na složitosti a dostupnosti dílny).
- Dokončení: hodiny až dny.
- Kontrola: Hodiny až dny.
- Doprava: 1 den až 1 týden a více (v závislosti na lokalitě a způsobu).
Typické rozmezí dodací lhůty:
- Prototypy (jednoduché následné zpracování): 1-3 týdny běžné.
- Prototypy (komplexní následné zpracování/obrábění): 3-6 týdnů+.
- Výrobní šarže: Velmi závisí na množství a složitosti, vyžaduje pečlivé plánování s poskytovatelem. Může se pohybovat v rozmezí týdnů až měsíců.
- Expediční služby AM: Mnozí poskytovatelé nabízejí rychlejší zpracování za příplatek, často díky upřednostnění pozice ve frontě a případné optimalizaci kroků sestavení/následného zpracování, pokud je to možné.
Porozumění těmto nákladovým faktorům a složkám doby realizace umožňuje přesnější plánování a sestavování rozpočtu projektu. Spolupracujte s potenciálními dodavatelé AM kovů brzy získat realistické nabídky a časové harmonogramy na základě vaší konkrétní konstrukce chladiče a požadavků. Zohledněte celý pracovní postup, zejména následné zpracování, protože významně ovlivňuje náklady i dodací lhůty dodavatelský řetězec AM.
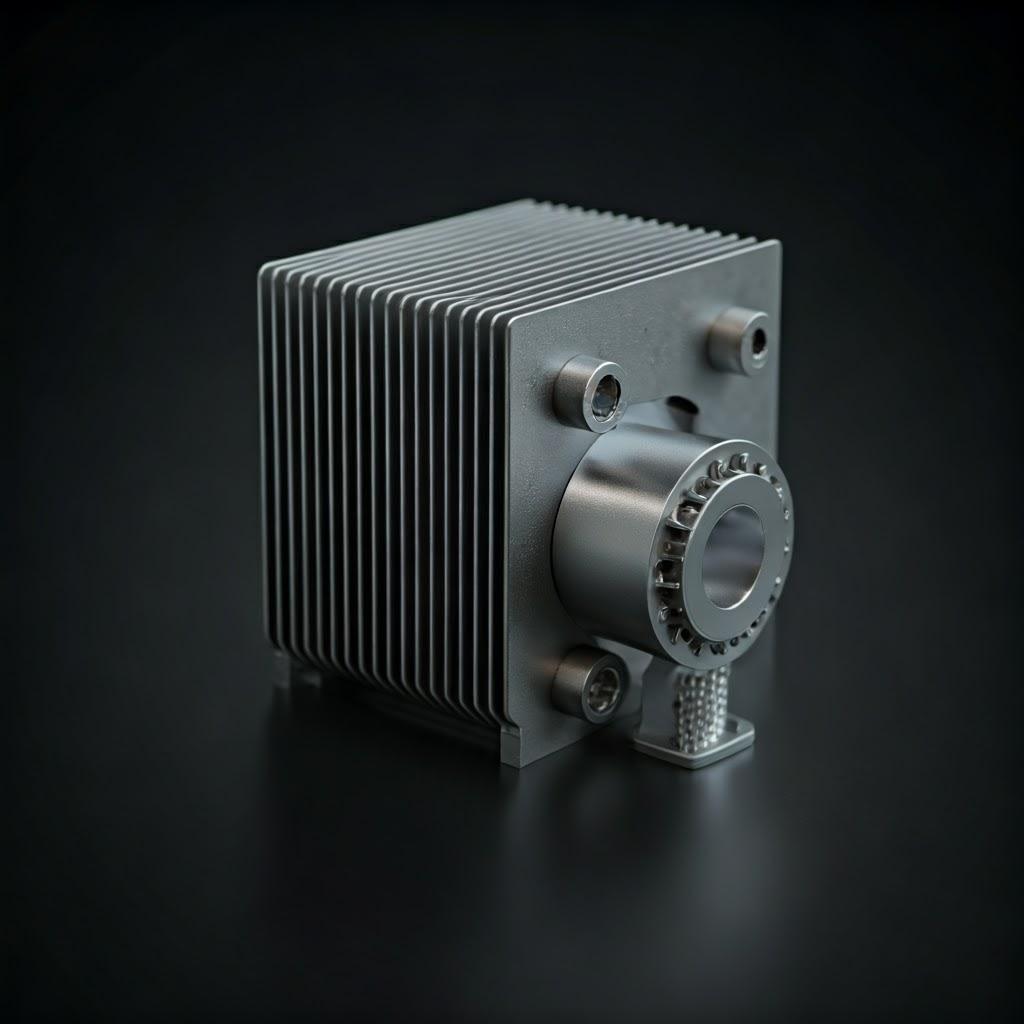
Často kladené otázky (FAQ) o 3D tištěných chladičích elektromotorů
Zde jsou odpovědi na některé časté otázky inženýrů a manažerů nákupu týkající se použití aditivní výroby kovů pro chladiče elektromotorů:
- Jaký je výkon 3D tištěných chladičů v porovnání s tradičními (obráběnými, litými, lisovanými)?
- Často je to výrazně lepší, zejména u složitých návrhů. Technologie AM umožňuje vytvářet geometrie, které tradiční metody neumožňují, jako jsou topologicky optimalizované tvary, vnitřní mřížkové struktury a konformní chladicí kanály. Tyto vlastnosti mohou vést k:
- Vyšší tepelná účinnost: Lepší odvod tepla při stejné velikosti/hmotnosti.
- Nižší hmotnost: Dosažení stejného nebo lepšího chlazení s menším množstvím materiálu/hmotnosti.
- Vylepšená integrace: Kombinace funkcí chladiče s montážními nebo konstrukčními prvky.
- Míra zlepšení závisí do značné míry na využití zásad DfAM. Jednoduchá replikace tradičního návrhu může mít jen malý přínos, zatímco plně optimalizovaný návrh AM může přinést výrazné zvýšení výkonu (např. v případových studiích se často uvádí zlepšení tepelného odporu o 20-50 % nebo více).
- Často je to výrazně lepší, zejména u složitých návrhů. Technologie AM umožňuje vytvářet geometrie, které tradiční metody neumožňují, jako jsou topologicky optimalizované tvary, vnitřní mřížkové struktury a konformní chladicí kanály. Tyto vlastnosti mohou vést k:
- Jsou 3D tištěné kovové chladiče odolné a spolehlivé pro náročné aplikace, jako je automobilový nebo letecký průmysl?
- Ano, pokud jsou správně navrženy, vyrobeny a následně zpracovány.
- Vlastnosti materiálu: Kovové díly AM vyrobené ze slitin, jako je AlSi10Mg nebo CuCrZr, mohou dosáhnout mechanických vlastností (pevnost, tvrdost, odolnost proti únavě) srovnatelných nebo někdy i převyšujících vlastnosti odlitků, zejména po vhodném tepelném zpracování (např. T6 pro AlSi10Mg, srážecí kalení pro CuCrZr).
- Hustota: Správně řízené procesy AM dosahují téměř plné hustoty (>99,5 %, často >99,9 %) a minimalizují pórovitost, která by mohla ohrozit integritu. HIP lze použít pro kritické aplikace k odstranění zbývajících dutin.
- Kontrola kvality: Renomovaní poskytovatelé služeb provádějí přísnou kontrolu kvality, včetně testování materiálu, sledování procesů, kontroly rozměrů (CMM, 3D skenování) a NDT (např. CT skenování), aby zajistili, že díly splňují specifikace a nevykazují kritické vady.
- Spolehlivost závisí na výběru správného materiálu, optimalizaci návrhu pro AM, zajištění vysoce kvalitního tisku a provedení nezbytného následného zpracování a validace.
- Ano, pokud jsou správně navrženy, vyrobeny a následně zpracovány.
- Jaký je typický rozdíl v ceně chladiče AM a srovnatelného tradičně vyráběného chladiče?
- Závisí do značné míry na složitost a objem.
- Vysoká složitost / nízký objem: Pro velmi složité geometrie (např. optimalizovaná topologie, vnitřní kanály, mřížky) nebo zakázkové kusy/prototypy/malé objemy, AM je často výrazně levnější protože se vyhýbá vysokým nákladům na nástroje (odlévání) nebo rozsáhlému nastavení víceosého obrábění a plýtvání materiálem (CNC).
- Jednoduchá geometrie / velký objem: Pro jednoduché konstrukce (jako jsou základní extrudované nebo lité žebrované chladiče) vyráběné ve velkém množství, tradiční metody jsou obvykle mnohem levnější díky nižším nákladům na jeden díl po amortizaci nástrojů nebo díky vysokorychlostnímu obrábění/extruzi.
- Bod přechodu: Existuje určitý bod, kdy se náklady stávají srovnatelnými. Jeho určení vyžaduje specifické vyčíslení na základě konstrukce a množství dílů. Hodnota AM’často spočívá ve zvýšení výkonu a odlehčení, které ospravedlňují potenciálně vyšší jednotkové náklady.
- Závisí do značné míry na složitost a objem.
- Lze efektivně čistit a zbavovat prášku vnitřní kanály nebo složité mřížkové struktury v chladičích AM?
- Ano, ale vyžaduje to pečlivý návrh a kontrolu procesu.
- Depowdering: Klíčové je účinné odstranění prášku ihned po tisku pomocí optimalizované orientace, vibrací, stlačeného vzduchu a někdy i specializovaného vybavení.
- Design for Depowdering: Návrh vnitřních kanálů s dostatečným průměrem, hladkými cestami a případně přístupovými otvory usnadňuje odstraňování prášku. Vyhněte se “prachovým pastem” - uzavřeným dutinám bez možnosti úniku.
- Kontrola: K ověření průchodnosti vnitřních kanálů lze použít techniky, jako je testování průtoku vzduchu, proplachování nebo dokonce CT vyšetření.
- Materiál: Sypnost prášku (ovlivněná sféricitou a distribucí velikosti částic, na kterou se zaměřují výrobci prášků, jako je Met3dp) má vliv na snadnost práškování.
- Ano, ale vyžaduje to pečlivý návrh a kontrolu procesu.
- Jaké informace potřebuje poskytovatel služeb v oblasti AM technologií, aby mohl poskytnout přesnou cenovou nabídku na 3D tištěný chladič?
- Chcete-li získat co nejpřesnější nabídku, uveďte co nejvíce podrobností:
- 3D model CAD: STEP nebo STL (často se dává přednost formátu STEP, protože obsahuje více dat).
- Specifikace materiálu: Jasně uveďte požadovanou slitinu (např. CuCrZr, AlSi10Mg) a všechny požadované materiálové normy.
- Technické kreslení (doporučené): Uveďte kritické rozměry, tolerance GD&T, požadavky na povrchovou úpravu (hodnoty Ra pro konkrétní povrchy) a případné specifické kontrolní poznámky.
- Množství: Počet požadovaných dílů (prototyp vs. výrobní objemy).
- Požadavky na následné zpracování: Uveďte požadované tepelné zpracování (odlehčení, T6, srážkové kalení), potřeby obrábění (zvýraznění kritických prvků), povrchové úpravy a jakékoli zvláštní požadavky na čištění nebo povrchovou úpravu.
- Kontext aplikace: Stručně popište aplikaci (např. chlazení elektromotoru, letecký pohon) a klíčové požadavky na výkon (tepelné zatížení, provozní teplota, konstrukční zatížení), pokud je to možné, protože to pomůže poskytovateli pochopit kontext a kritičnost.
- Požadovaná osvědčení/dokumentace: Uveďte všechny potřebné certifikáty materiálu, certifikáty CofC nebo inspekční zprávy.
- Chcete-li získat co nejpřesnější nabídku, uveďte co nejvíce podrobností:
Poskytnutí komplexních informací předem umožňuje dodavatel AM kovů přesně posoudit proveditelnost výroby, odhadnout náklady na všechny kroky procesu a poskytnout spolehlivou dobu realizace.
Závěr: Budoucnost chlazení vysoce výkonných elektromotorů je aditivní
Neustálá snaha o vyšší hustotu výkonu, vyšší účinnost a nižší hmotnost elektromotorů v průmyslových odvětvích, jako je automobilový průmysl, letectví a průmyslová automatizace, vyžaduje změnu paradigmatu v oblasti tepelného managementu. Tradiční řešení chlazení stále častěji narážejí na výkonnostní bariéry dané výrobními omezeními. Aditivní výroba kovů se stává mocným nástrojem, který nabízí nebývalou konstrukční svobodu pro vytváření vysoce optimalizovaných, lehkých a komplexních chladičů, které byly dříve nepředstavitelné.
S využitím principů DfAM, jako je optimalizace topologie, konformní chladicí kanály a složité mřížkové struktury, mohou inženýři navrhovat 3D tištěné chladiče z vysoce výkonných materiálů, jako jsou CuCrZr a AlSi10Mg, které poskytují vynikající tepelný výkon přesně přizpůsobený potřebám motoru. Schopnost konsolidovat díly, rychle vytvářet prototypy a dosáhnout výrazného odlehčení dále upevňuje výhodu AM’ pro náročné aplikace. I když existují problémy, pochopení chování materiálu, nuancí procesu, zásadních kroků následného zpracování a důkladná kontrola kvality umožňují tyto překážky překonat.
Pro úspěšnou implementaci této technologie je nejdůležitější výběr správného výrobního partnera - partnera s hlubokými technickými znalostmi, pokročilým vybavením, přísnými systémy kvality a prokazatelnými zkušenostmi s příslušnými materiály a aplikacemi. Faktory, jako jsou náklady a doba realizace, je třeba pečlivě zvážit a vyvážit přínosy výkonu s rozpočtem a časovým plánem projektu.
Cesta k aditivní výrobě kritických součástí, jako jsou chladiče, představuje více než jen přijetí nové výrobní techniky; jde o přijetí nového způsobu myšlení o designu a výkonu. S tím, jak tato technologie stále dozrává a věda o materiálech postupuje, je kovový 3D tisk připraven stát se nepostradatelným nástrojem při vývoji elektromotorů nové generace, který umožní chladnější provoz, delší životnost a rozšířené možnosti. Společnosti, které hledají konkurenční výhodu v pokročilý tepelný management musí prozkoumat potenciál AM. Spolupráce s lídrem v oboru může tuto cestu urychlit.
Met3dp poskytuje komplexní Přídavná řešení Met3dp, zahrnující tiskárny SEBM, pokročilé kovové prášky vyráběné pomocí špičkových technik v oboru a služby vývoje aplikací. Díky desítkám let společných zkušeností dodává společnost Met3dp špičkové systémy a materiály umožňující výrobu nové generace. Kontaktujte společnost Met3dp a prozkoumejte, jak její schopnosti mohou podpořit cíle vaší organizace v oblasti aditivní výroby a revolučně změnit váš přístup k chlazení elektromotorů.
Sdílet na
MET3DP Technology Co., LTD je předním poskytovatelem řešení aditivní výroby se sídlem v Qingdao v Číně. Naše společnost se specializuje na zařízení pro 3D tisk a vysoce výkonné kovové prášky pro průmyslové aplikace.
Dotaz k získání nejlepší ceny a přizpůsobeného řešení pro vaše podnikání!
Související články
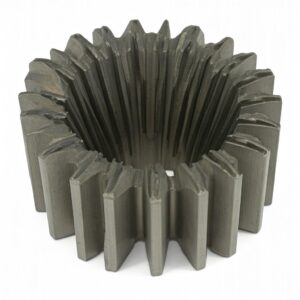
Vysoce výkonné segmenty lopatek trysek: Revoluce v účinnosti turbín díky 3D tisku z kovu
Přečtěte si více "O Met3DP
Nedávná aktualizace
Náš produkt
KONTAKTUJTE NÁS
Nějaké otázky? Pošlete nám zprávu hned teď! Po obdržení vaší zprávy obsloužíme vaši žádost s celým týmem.
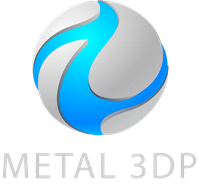
Kovové prášky pro 3D tisk a aditivní výrobu